Завод вольво в швеции – Шведский завод по сборке двигателей стал первым производством Volvo Cars, не оказывающим влияния на климат
Заводы Volvo Construction Equipment в Швеции и России – Варламов.ру
-=Реклама=- Пост оплачен -=Реклама=-Когда фотографы слышат слово завод, они мечтают увидеть измазанные грязью мускулистые потные спины, блестящие в лучах солнца, пробивающегося из-под затянутых паутиной окошек в крыше кирпичного цеха постройки XVIII века, вырывающие отовсюду струи пара, огромные вращающиеся жернова, снопы искр и реки расплавленного чугуна. Увы, современный машиностроительный завод — это стерильное помещение с белыми стенами, бесконечными роботами и компьютерами. Никакой фотогеничности, как в старые добрые времена. Ситуация осложняется еще тем, что многие процессы происходят за стеклом. Если это покрасочная камера, то оно еще и запотевшее, что ставит крест на съемке. И в конце концов, частенько снимать вообще запрещают.
Мы с Дмитрием Чистопрудовым посмотрели, как собирают строительную технику Volvo. Дмитрий отправился на завод в Швецию, а я в Калужскую область. Вот, что из этого получилось
История компании Volvo Construction Equipment началась более 180 лет назад в Эскилстуне, Швеции. В 1832 году был основал Эскильстунский механический завод. Здесь создавались печатные прессы, молотилки, двигатели и в 1853 первый шведский паровоз. В 1906 году завод выпустил первый шведский паровой каток, в 1913 — первый шведский трактор.
На входе выдают жилетки гаишников и хитрые сандали с металлическим носком и подошвой — в таких можно ходить по гвоздям и ронять коробки передач на ногу. В жилетках человека лучше видно, и это спасает от наезда погрузчиков — они по заводу гоняют весьма резво. На фотографии разноцветные носки Сергея tersan.
В цехах на перекрестках вместо светофоров для погрузчиков развешанны под потолком зеркальные полусферы. Водитель может заглянуть за угол перед поворотом. Полезная штука.
Каждое утро начинается с 15-минутки в комнате для совещаний. Руководители цехов определяют план работ на смену и раздают задания подчиненным. Касок, кстати, не выдают, что меня очень удивило — я раньше ни разу ни гулял по заводам без каски. Их заставляют натягивать даже на нефтебазах, где на голову ничего упасть не может, максимум пролиться.
И вместо обычного нудного инструктажа в полчаса, гид попросил только не заходить на маршруты погрузчиков. При этом завод в этом году должен быть «зиро эксидентс», то есть ни одного пальца, попавшего под молоток. Просто всё организовано так, чтобы опасности для людей нет.
Среди бригад в каждом цехе идет конкурентная борьба за звание лучшей команды завода. Это и дополнительная премия, и гордый переходящий вымпел “пойди и поучись”.
В основном завод выглядит так. Это какие-то большие машины, в которых что-то гудит и делается, но стоит приоткрыть дверцу, как срабатывают датчики безопасности и станок или конвейер останавливается.
Например, загружается в большой станок вот такая стальная заготовка:
А на выходе получается готовый мост, у которого проточены все фланцы, отверстия и так далее.
Или, например, на одном конвейере заготовки подаются в большой станок, на другом выезжают уже готовые обработанные детали.
Танцующие роботы проводят мелкие операции и передают детали от одного станка к другому. В закрытой стеклянной комнатке они берут заготовку, кладут на один станок, который просверливает отверстия, перекладывают на другой станок, где фрезеруются проточки, и так далее. Наблюдать за этим действием можно бесконечно.
Но полностью заменить человека робот пока не может. В цехах сборки специалисты монтируют в корпуса все нужные валы и шестеренки вручную.
На заводе Volvo CE есть два вида сборочных цехов. Один — классический конвейер, где каждый оператор выполняет свою конкретную операцию и пускает деталь дальше. Второй — когда целый узел собирает один человек.
Чрезвычайно интересный момент. Для сбора одной КПП, требуется, скажем, шесть шестеренок, двенадцать сальников, две прокладки, четыре стопорных кольца. Не больше и не меньше. Всё это сборщик получает на специальном катающемся стенде размером с дверь холодильника. Это гарантирует, что он не пропустит ни одной резиночки, а также сильно ускоряет его работу — всё под рукой! На фотографии человек показывает точку старта — какую деталь нужно взять первой. Дальше оператор следует красной линии и берет нужные комплектующие в порядке сборки. Не нужно ничего искать и вспоминать, что и где идет первым. Гениально!
Вопрос: а что, если формировщик этого набора случайно положит лишнюю прокладочку? Ответ — это невозможно, ибо крючок на стенде — специальной длины, на него можно повесить ровно 8 прокладочек, лишняя не влезет, а нехватку сразу заметно — все детали должны быть плотно закреплены.
Стенд с инструментами. Идеальный порядок и тоже ничего лишнего. Надо сказать, что как-то раз я видел ровно такой же стенд и в советском автосервисе — бывают и среди наших механиков зануды и чистюли. Там еще висел плюшевый медвежонок с гвоздём в голове и табличкой на груди «Я взял отвёртку без спроса».
Еще интересно организована поставка комплектующих. Их привозят с других заводов в красивых деревянных ящиках.
Для хранения комплектующих выделена отдельная зона, куда постоянно проносятся погрузчики и что-то привозят и увозят.
К некоторым комплектующим организован доступ через специальную “шайтан-машину”. Из загруженных в неё запчастей она самостоятельно формирует наборы для сборки соответствующих КПП или мостов. То есть отсыпает в одну коробочку четко нужное количество болтов, гаек, шестеренок и подшипников. И, вероятно, заказывает новые поставки, когда заканчиваются резервы.
Вот так выглядят собранные коробки с комплектующими. Их развозят к сборочным постам на специальных грузовиках.
Станция зарядки погрузчиков.
Прекрасный люк!
Конвейер по сборке мостов для сочлененных самосвалов Volvo.
Везде чистота и порядок.
Загрузка готового моста в покрасочную камеру. Пара минут, и мост готов.
Вот еще чрезвычайно крутая штука. Не ноу-хау, конечно, но я, честно, раньше даже не знал, что такое бывает. Итак, как нам идеально сварить один вал из двух половинок? Гениальное по своей простоте решение: сварка трением!
Две половинки вставляют в аппарат типа токарного станка. Одна половинка начинает быстро вращаться. То, что происходит дальше, видно на фотке слева направо.
По мере увеличения частоты вращения свариваемых заготовок при наличии сжимающего давления происходит притирка контактных поверхностей и разрушение жировых, а затем оксидных пленок, присутствующих на них в исходном состоянии. Граничное трение уступает место сухому. В контакт вступают отдельные микровыступы, происходит их деформация и образование ювенильных участков с ненасыщенными связями поверхностных атомов, между которыми мгновенно формируются металлические связи и немедленно разрушаются вследствие относительного движения поверхностей.
Вращение резко останавливается и две половинки становятся единым целым. Затем лишний облой снимается уже обычным токарным станком.
Интересно, что так можно сваривать, например, сталь и алюминий. Или пластик и пластик. Готовые оси:
И еще пара кадров про порядок. Посмотрите, для каждого предмета и оборудования выделена своя зона. Даже у канистры есть свой квадратик синего цвета.
Все ячейки для хранения размечены и промаркерованы. Идеальный порядок!
А теперь перенесемся в Россию. 14 мая 2013 года Volvo Construction Equipment отпраздновала открытие завода по производству экскаваторов в Калужской области.
На заводе 4 основных линии: сборка нижней рамы, верхней рамы, основная линия и линия сборки стрел.
Вначале производится прогонка всех резьб — после морской доставки комплектующих требуется их обработка. Дальше производится сборка главного клапана, прошивка двигателя и установка его на раму.
Дальше на конвейере устанавливают радиатор, нижнюю часть кабины, сидения, рычаги управления.
Запчасти привозят co всего мира, но в основном из Южной Кореи. Двигатели привозят только из Швеции или Германии. Двигатели дизельные, 13-литровые, 283 л/с. Такие же устанавливаются и на грузовики Volvo, только с немного другой прошивкой “мозгов”.
Сборка всей техники проводится сейчас в тестовом режиме и вручную. У каждого оператора есть инструкция по сборке, в которой указано какую деталь куда поставить и какой стороной. А также какое усилие приложить при закручивании соединений. Все болты обрабатываются герметиком.
Конвейер состоит из станций, на каждой из которой установлен столб с пyльтом управления и лапочками-индикаторами. В cлучае ошибки/нехватки деталей/сложностей в работе оператор нажимает на пульте одну из кнопок, соответствующей проблеме и ответственному человеку приходит смска что его вызывают к определенной станции. Также в цехе будут висеть большие плазмы с информацией по конвейеру.
Кстати, в калужском заводе все рабочие ходят в касках.
Линия по сборке нижней рамы.
Я и гусеницы.
Знаете, что это? Это — ленивец. Для того, чтобы его установить, нижняя рама поднимается 26-тонным краном и переворачивается с помощью специальног o переворотного устройства. Ленивец нужен для создания натяжения в гусенице, иначе она свалится.
Готовая нижняя рама весит до 20 тонн!
Готовая верхняя рама, только без кокпита. Церемонию свадьбы застать увы не удалось.
Линия сборки стрел находится отдельно, на ней нa стрелы устанавливается гидравлика, электрика, цилиндры и так далее.
А вот и первый экскаватор Volvo, собранный в России! Всего на предприятии планируется выпуск тяжелых высокопроизводительных экскаваторов Volvo с эксплуатационной массой от 20 до 50т новой серии. Пока завод работает в тестовом режиме и выпускает по 2 экскаватора в день. План — выйти на производство 1500 единиц в год.
Более 90% рабочих на заводе россияне, жители Калужской области. Кроме хорошей зарплаты сотрудники предприятия получают полный соцпакет, трансфер до работы, питание и компенсацию занятий спортом. Также есть возможность обучения и повышения квалификации рабочих.
Большое спасибо компании Volvo CE за интересные экскурсии
Также смотрите, как работает строительная техника Volvo CE в репортаже Дмитрия chistoprudov о тестовом полигоне в Швеции: http://chistoprudov.livejournal.com/131433.html
varlamov.ru
VOLVO ОТКРЫВАЕТ В ШВЕЦИИ НОВЫЙ ЗАВОД ДЛЯ ПРОИЗВОДСТВА СЛЕДУЮЩЕГО ПОКОЛЕНИЯ XC90.
VOLVO ОТКРЫВАЕТ В ШВЕЦИИ НОВЫЙ ЗАВОД ДЛЯ ПРОИЗВОДСТВА СЛЕДУЮЩЕГО ПОКОЛЕНИЯ XC90.
Сегодня Volvo Cars открывает свое новое производственное предприятие площадью 24.000 квадратных метров в Торсланда (Гетеборг), что позволит увеличить объем производства с 200.000 до 300.000 автомобилей в год. Это еще один важный шаг на пути реализации долгосрочной стратегии компании: Volvo Cars планирует выйти на ежегодный объем продаж в 800.000 автомобилей.
Новый кузовной цех будет использоваться для производства нового XC90: сборка нового внедорожника начнется в конце года, а первые автомобили поступят в продажу в первом квартале следующего года. Volvo XC90 станет первой моделью Volvo, созданной на основе новой Архитектуры масштабируемой платформы (SPA). Новая платформа представляет собой гибкую в применении систему, призванную улучшить дизайн, безопасность и обеспечить экономию за счет использования единых комплектующих.
Новый цех открывается в день, когда Volvo отмечает 50-летний юбилей своего завода в Торсланда. Создание нового цеха предусмотрено планом преобразования компании с общим объемом инвестиций в 11 миллиардов долларов США. Почти половина этих средств пойдет на разработку новой архитектуры автомобилей и создание собственной линейки двигателей Drive-E.
“Создание нового кузовного цеха позволит нам увеличить объемы производства на заводе Торсланда с нынешних 200.000 до 300.000 автомобилей в год, – уверен Ларс Вребо (Lars Wrebo), старший вице-президент по закупкам и производству. – Эти инвестиции наглядно показывают, что Volvo Cars нацелена поддерживать и развивать производство в Швеции, и производственные мощности должны находиться вблизи от центров исследований и разработок”.
Президент и генеральный директор Хокан Самуэльссон (Håkan Samuelsson) отметил, что создание нового цеха – это инвестиции в будущее Volvo Cars, а также будущее Гетеборга, где компания работает уже 87 лет.
“Сегодня мы отмечаем 50-летие нашего завода в Торсланда, и сегодня же мы вводим в строй новый цех в Гетеборге, подтверждая наш статус автопроизводителя мирового уровня. Торсланда – это наша штаб-квартира, наш дом”, – добавил он.
Новый цех является самым современным в мире и не только по уровню используемых технологий, но также рабочих процедур, применяемых на производстве. Здесь будут использоваться приблизительно 300 роботов, однако на конвейере уровень автоматизации снизился, и компании удалось повысить качество взаимодействия высококвалифицированных специалистов и роботизированной техники. Снижение количества роботов на производстве позволило снизить объем инвестиций и более оптимально использовать производственные площади.
Для обслуживания роботов на новом предприятии будут работать группы в составе пяти – восьми человек, тогда как в других цехах завода Торсланда роботов обслуживают группы по пятнадцать человек. Работа всех членов таких групп будет тесно взаимосвязана, они должны уметь определить возникшие неполадки, устранить их и произвести необходимое обслуживание оборудования. Такой подход позволит повысить гибкость производственных процессов, сократить вероятность простоев, и в результате повысить эффективность и объемы производства. В новом цехе будут работать около 80 высококвалифицированных рабочих.
Ключевые слова:
Завод, Производство
Опубликованная в данном пресс-релизе и на медиа сайте Volvo Car Group информация может быть изменена в любое время без предварительного уведомления или обязательств. Пожалуйста, для получения наиболее свежей и достоверной для российского рынка информации обращайтесь в пресс-службу Volvo Car Group в России.
www.media.volvocars.com
“ЗАВОДЫ VOLVO CARS В ШВЕЦИИ И БЕЛЬГИИ ИСПОЛЬЗУЮТ ГИДРОЭЛЕКТРОЭНЕРГИЮ
ЗАВОДЫ VOLVO CARS В ШВЕЦИИ И БЕЛЬГИИ
ИСПОЛЬЗУЮТ ГИДРОЭЛЕКТРОЭНЕРГИЮ
Volvo Cars реализует стратегию экологически чистого производства в Европе и переходит на использование гидроэлектроэнергии. Сегодня производственные мощности компании в Швеции и Бельгии получают электроэнергию только с гидроэлектростанций.
“Мы стремимся обеспечить максимальное использование возобновляемых источников энергии, поэтому электроэнергия, выработанная гидроэлектростанциями, рассматривается как наилучшая альтернатива другим видам энергии”, – говорит Магнус Хельстен (Magnus Hellsten), Старший Вице-президент Volvo Cars по производству.
Подразделение закупок Volvo Cars подписало новое соглашение со шведским поставщиком Vattenfall и бельгийской компанией Electrabel, которые будут полностью удовлетворять нужды заводов Volvo Cars в электроэнергии. Поставщики электроэнергии продают сертификаты, которые гарантируют, что вся электроэнергия, поставляемая на заводы Volvo Cars в Швеции и Бельгии, производится гидроэлектростанциями. По условиям соглашения потребность предприятий Volvo Cars в электроэнергии составляет около 1000 ГВт-ч (гигаватт-час).
“Это – часть нашей стратегии, направленной на обеспечение защиты экологии, предусматривая как прямое, так и косвенное воздействие на природу. В будущем мы изучим возможности использования других видов источников энергии для наших производственных заводов, например, газ биологического происхождения и энергия ветра”, – пояснил Магнус Хельстен.
В течение десятилетий Volvo Cars реализует меры, направленные на обеспечение энергетической независимости от нефти
Volvo Cars приступила к поиску других источников энергии отличных от нефти еще 25 лет назад. В 1982 году компания стала использовать остаточное тепло с близлежащих нефтеперерабатывающих заводов в Торсланда. В 1988 году в Volvo Cars стали использовать природный газ, который на сегодняшний день представляет собой единственное топливо для обогрева заводов в Швеции и Бельгии.
“Мы так много сделали в этой сфере, что сегодня мы практически не зависим от нефти. В настоящее время мы прорабатываем пути перехода с природного газа на возобновляемый газ биологического происхождения”, – говорит Михкель Лакс (Mihkel Laks), Директор Volvo Cars по защите окружающей среды.
Системный подход ради обеспечения экономии энергии
Системный подход с целью обеспечения мер по экономии энергии – это еще одно направление в работе Volvo Cars по защите окружающей среды.
“Несмотря на то, что за годы площади, которые мы должны отапливать, удвоились в размерах, мы смогли сохранить расход энергии на прежнем уровне. В действительности, за последние годы мы добились снижения расхода энергии, реализовав ряд удачных проектов”, – пояснил Михкель Лакс.
Одно из недавно проведенных мероприятий в этой области: системный подход в проектировании зданий завода в Торсланда позволил обеспечить около 30 процентов экономии энергии. Кроме этого, удалось улучшить климат внутри заводских помещений.
“Теперь мы внимательно проверяем все наши объекты. Используя меры, предпринятые в процессе выполнения успешных проектов, мы смогли быстро добиться желаемых улучшений”, – добавил Михкель Лакс.
Ключевые слова:
Окружающая среда, О компании
Опубликованная в данном пресс-релизе и на медиа сайте Volvo Car Group информация может быть изменена в любое время без предварительного уведомления или обязательств. Пожалуйста, для получения наиболее свежей и достоверной для российского рынка информации обращайтесь в пресс-службу Volvo Car Group в России.
www.media.volvocars.com
ИСТОРИЧЕСКИЙ ОБЗОР: 1960-1969 – Volvo Car Russia
ИСТОРИЧЕСКИЙ ОБЗОР: 1960 – 1969
1960 год – Volvo представляет совершенно новый автомобиль – спортивную модель P1800
1961 год – в октябре на рынок выходит новый Amazon 121.
1963 год – в июне начинает работу первый сборочный завод Volvo за пределами Швеции – Галифакс, Канада.
1964 год – 24-го апреля открыт новый завод в Торсланда.
1965 год – новый завод открывается в городе Гент, Бельгия.
1966 год – представлен Volvo 144.
1967 год – в конце года Volvo выводит Volvo 145 Estate.
1968 год – на рынок выходит Volvo 164 – престижная версия с эксклюзивной отделкой салона и рулевой системой с гидроусилителем.
1969 год – в новой серии 140 реализованы инновационные решения, Включая подголовники на передних сиденьях, ремни безопасности для трех пассажиров на задних сиденьях и электрический обогрев заднего стекла.
1960
В январе на международной выставке автомобилей в Брюсселе Volvo представила совершенно новую модель Volvo – спортивный автомобиль P1800, который был наконец показан всем желающим “во плоти”. За год до этого события Volvo выпустила фотографии будущего спортивного автомобиля. Двухместное спортивное купе получило совершенно новый двигатель B18B. В течение первых лет новая модель собиралась на заводе в Англии, потому что завод Volvo в Хисинген был перегружен и не позволял наладить сборку еще одной модели.
PV544 и Amazon получили новые коробки переключения передач и сиденья новой конструкции, которые включали новые спинки, обеспечивающие больше пространства для людей на задних сиденьях.
Была учреждена страховая компания Volvia. Владельцы автомобилей Volvo могли продлить страхование своих автомобилей в компании Volvia после того, как у них заканчивалась страховка.
Были внесены усовершенствования в дизайн и конструкцию Volvo Duett, который получил цельное огибающее фронтальную часть лобовое стекло, четырехскоростную КПП и новую панель приборов.
Ремни безопасности стали стандартным оснащением. В тоже время компания прекращает использовать название Duett, а новая модель получила обозначение P210.
Объем годового производства увеличился до 80.000 автомобилей.
СОЗДАННЫЙ ДЛЯ КОМФОРТНОЙ ЕЗДЫ СПОРТИВНЫЙ VOLVO 1800 СТАЛ ЗВЕЗДОЙ ТЕЛЕВИЗИОННОГО СЕРИЛА “СВЯТОЙ”. ГЛАВНЫЙ ГЕРОЙ СЕРИАЛА РОДЖЕР МУР РАЗЪЕЗЖАЛ НА БЕЛОМ VOLVO P1800, ИЗРЯДНО РАЗДРАЖАЯ АВТО ПРОИЗВОДИТЕЛЕЙ ВЕЛИКОБРИТАНИИ. БОЛЕЕ ТОГО, РОДЖЕР МУР МНОГО ЛЕТ САМ ЕЗДИЛ НА VOLVO P1800. НА ВЫСТАВКЕ В КАЛИФОРНИИ В 1961 ГОДУ VOLVO P1800 ПОЛУЧИЛ ГЛАВНУЮ НАГРАДУ ЗА ЛУЧШИЙ ДИЗАЙН. P1800 БЫЛ ОФИЦИАЛЬНЫМ ГОНОЧНЫМ АВТОМОБИЛЕМ НА 24-ЧАСОВЫХ ГОНКАХ НА СОРЕВНОВАНИЯХ В ГОРОДЕ СИБРИНГ, США, В 1963 И 1964.
1961
В мае начинается производство P1800.
PV544 и Amazon получают новый мощный двигатель B18 с двойным карбюратором. Мощность PV544 Sport выросла до 90 л.с. В этих моделях используется электросистема напряжением 12 Вольт и структура ассиметричных фар. Модели, выпускавшиеся осенью, получили новые цвета окраски кузова: светло-коричневый, светло-зеленый, красный, голубой и светло-серый.
В октябре на рынок выходит Amazon 121. Это был двухместный автомобиль, который с начала производства продавался только в Швеции, Норвегии и Дании.
1962
Расширился выбор модификаций Amazon, который теперь включал четырехдверный универсал. Был изменен дизайн задней части автомобиля: задняя дверь была раздельной и включала две секции – верхнюю и нижнюю. Новый универсал комплектовался двигателем B18A и четырехскоростной КПП.
Стоимость новой модели составила 14.475 шведских крон. К февралю было произведено всего 100.000 автомобилей Amazon.
1963
В этом году было предложено совсем немного новых продуктов. Amazon получил низкопрофильные шины, а P1800 стал поставляться с новым двигателем мощностью 108 л.с.
В компании осознавали необходимость местного производства за рубежом, и в июне открылся первый сборочный завод Volvo в городе Галифакс (Канада). Автомобили поставлялись в Галифакс в виде машинокомплектов. На этом заводе ежегодно собиралось несколько тысяч автомобилей Volvo.
Рынок США был самым большим экспортным рынком для Volvo, и Volvo занимала четвертое место среди импортеров автомобильной продукции в США.
Оборот Volvo Group достиг 2.000 миллионов шведских крон. В штате группы компаний насчитывалось более 20.000 служащих.
1964
24-го апреля начал работу новый сборочный завод в Торсланда. Проектная мощность завода составляла 110.000 автомобилей в год в случае работы в одну смену, 150.000 автомобилей в год при частичной двусменной работе и 200.000 при полной загрузке в две смены. Наконец компания получила реальные возможности увеличения объемов производства!
На новом заводе немедленно приступили к сборке Amazon.
Модели 1965 года получили ряд новых функций и элементов, включая передние дисковые тормоза для всех моделей Amazon и сервопривод для тормозной системы в универсалах. Была предложена новая решетка радиатора, штампованные колесные диски и покрытие хромом колпаки ступиц из оцинкованной стали.
Volvo представила новый тип передних сидений, которые были разработаны при участии экспертов из медицины. Новые сиденья обеспечивали правильную посадку, что необходимо было для повышения безопасности вождения автомобиля.
1965
Amazon стал самым популярным автомобилем в Швеции. Компания представляла Amazon и 1800S как модели, не требующие никакой эксплуатационной смазки.
В августе Volvo продемонстрировала новые изменения в дизайне PV544, однако в компании уже было принято решение о прекращении производства этой серии. 20-го октября последний автомобиль серии сошел с конвейера завода в Лундби. Всего же было произведено 440.000 автомобилей этой серии. 280.000 остались в Швеции, а 160.000 ушли на экспорт. Одновременно с окончанием производства 544 серии Volvo представила новую модель Amazon – Favorit. Правда, отличия нового автомобиля от стандартной двухдверной версии были не такими актуальными.
Volvo открыла новый сборочный завод в городе Гент (Бельгия), что позволило Volvo начать работать внутри Европейского Сообщества (прежнее название Европейского Союза) и избежать таможенных барьеров. В течение первого года работы завод в городе Гент произвел около 14.000 автомобилей.
1966
В августе был представлен новый модельный ряд Volvo, на создание которого у инженеров компании ушло много времени. Ранее новой серии было присвоено рабочее название 1400, но на момент выхода новая модель была представлена как Volvo 144. В плане безопасности это был самый передовой автомобиль Volvo. Он получил передние и задние дисковые тормоза, раздельную рулевую колонку и новый блокирующий замок трехточечного ремня безопасности. Кузов автомобиля включал зоны деформации в передней и задней частях. Даже в дверных замках была реализована безопасная конструкция.
Модель 144 предлагала новую двухконтурную трехканальную тормозную систему. Система включала два контура, и если один из них выходил из строя в распоряжении водителя оставалось 80% тормозного усилия. Volvo 144 предлагался с двумя двигателями: B18A мощностью 85 л.с. с горизонтально установленным карбюратором и B18B мощностью 115 л.с. с двумя карбюраторами. Более мощная версия получила название 144S.
Серия 140 также свидетельствовала о введении новой системы названий для моделей Volvo. Первая цифра обозначала модель, вторая показывала количество цилиндров двигателя, а третья – количество дверей. Volvo 144 был превосходно принят средствами массовой информации и покупателями.
Volvo 144 был назван “Автомобилем года в Швеции”.
В этом же году была представлена спортивная модификация Amazon 123GT. На этом автомобиле устанавливался такой же двигатель, которым комплектовался Volvo 1800. Двигатель сочетался с четырехскоростной КПП с повышающей передачей.
1967
Volvo 144 оказался очень успешным и за пределами Швеции, и Volvo отметила свой 40-летний юбилей, демонстрируя отличные результаты. В США модель 144 соответствовала новым требованиям безопасности еще до того, как они были введены. Стандартная версия Volvo 144 в США предлагалась по цене 2.995 долларов.
В июне на рынок вышла двухдверная версия 142S. Эта модель отличалась меньшим весом (и была дешевле) по сравнению с четырехдверной версией.
Позднее в этом же году компания представила универсал Volvo 145. По техническим аспектам этот автомобиль был практически одинаков с другими версиями этой серии. Монолитная задняя дверь крепилась к крыше при помощи петлей и открывалась вверх. На данном этапе в модельном ряду Volvo было три универсала: P210 Duett, Amazon/221 и Volvo 145.
Amazon был оборудован раздельной рулевой колонкой и новым безопасным рулевым колесом, которое складывалось в случае столкновения. Теперь все версии универсалов поставлялись с усилителем тормозной системы.
Начиная с осени все модели с двумя карбюраторами, предназначенные для рынка США, поставлялись с системой контроля отработавших газов.
Производство четырехдверной версии Amazon было прекращено, и на смену Amazon пришла еще более успешная модель Volvo 144.
1968
На рынок вышла престижная версия Volvo 164 с эксклюзивной отделкой салона и гидроусилителем рулевой системы. Volvo 164 комплектовался шестицилиндровым двигателем мощностью 145 л.с. Салон этого автомобиля был более роскошным по сравнению с моделями серии 140. Передняя часть автомобиля была увеличена, что было необходимо для установки более мощного двигателя.
Этот автомобиль развивал максимальную скорость 175 км/ч. Базовая версия Volvo 164 стоила 25.500 шведских крон.
Volvo разработала специально для такси модель Volvo 144 Taxi. Этот автомобиль поставлялся в черном или белом кузове, а двигатель устанавливался с автоматической трансмиссией. Дизайн салона был выполнен для такси.
В августе Volvo представила двигатель B20, который стали устанавливать на моделях Amazon и на автомобилях 140 серии. Этот двигатель представлял собой развитие двигателя B18, он обладал большей мощностью и более высоким крутящим моментом. Двигатель B20 устанавливался с такой же системой контроля отработавших газов, которая предлагалась на моделях Volvo для рынка США еще в предыдущем году.
На Volvo Amazon устанавливалась такая же двухконтурная тормозная система, как и на моделях серии 140. Модель 123GT более не предлагалась на рынке Швеции.
Серия 140 установила новый рекорд продаж. В Швеции это был самый популярный автомобиль. В Великобритании продажи Volvo выросли в течение года на 70%.
В Малайзии было открыто сборочное предприятие, рассчитанное на производство 2.500 автомобилей в год.
1969
В феврале был произведен последний Duett. За годы производства эти универсалы и фургоны стали настоящей легендой.
В качестве преемника Volvo представила универсал с поднятой крышей Volvo 145 Express. В тоже время было прекращено производство универсалов на базе Amazon.
Осенью были представлены обновленные модели серии 140. Новые версии включали подголовники на передних сиденьях, ремни безопасности для трех пассажиров на задних сиденьях и заднее окно с электрической системой обогрева. Нововведения для Amazon были довольно ограничены. В это время в производстве осталась лишь одна двухдверная версия с выбором двух вариантов двигателей.
Volvo приступила к планированию нового испытательного полигона в районе Хеллеред в окрестностях Гетеборга. Полигон должен был разместиться на территории площадью 6 миллионов квадратных метров, а строительные работы должны были завершиться в 1972 году.
Volvo приобрела предприятие Svenska Stålpressnings AB в Улофстрем – эта компания поставляла кузова для автомобилей Volvo начиная с 1927 года.
Опубликованная в данном пресс-релизе и на медиа сайте Volvo Car Group информация может быть изменена в любое время без предварительного уведомления или обязательств. Пожалуйста, для получения наиболее свежей и достоверной для российского рынка информации обращайтесь в пресс-службу Volvo Car Group в России.
www.media.volvocars.com
Шведский завод по сборке двигателей стал первым производством Volvo Cars, не оказывающим влияния на климат
Шведский завод по сборке двигателей стал первым производством Volvo Cars, не оказывающим влияния на климат
С 1 января 2018 г. завод по сборке двигателей Volvo Cars в шведском городе Шёвде перешел на системы теплоснабжения, использующие возобновляемые источники энергии, и стал первым производством компании, не оказывающим влияния на климат.
Новый статус завода в Шёвде — это значительный шаг в реализации стратегии Volvo Cars по глобальному переводу всех своих производственных мощностей в режим, не оказывающий влияния на климат, к 2025 г. Шведский завод компании стал одним из первых подобных автомобильных производств в Европе.
«Наш приоритет на сегодняшний день — повышение энергетической эффективности. Следующий шаг — получение необходимой нам энергии из возобновляемых источников, — говорит Хавьер Варела (Javier Varela), старший вице-президент по производству и логистике Volvo Cars. — Модернизация завода в Шёвде — важная часть наших глобальных действий по минимизации воздействия на окружающую среду. Мы рады быть лидером среди автопроизводителей в вопросах перехода на климатически нейтральное производство».
Новое соглашение между Volvo Cars и локальным поставщиком гарантирует, что источником энергии для теплоснабжения завода в Шёвде послужит сжигание отходов, а также биомассы и биотоплива, произведенных из вторсырья. С 2008 г. производственные мощности в Шёвде, как и другие европейские заводы компании, уже используют электроэнергию, выработанную с использованием возобновляемых ресурсов.
«Этой новостью может гордиться и завод в Шёвде, и Volvo Cars в целом, — говорит Стюарт Темплар (Stuart Templar), директор по устойчивому развитию Volvo Cars. — Забота об окружающей среде — одна из наших фундаментальных ценностей. Наравне с электрификацией всех новых автомобилей Volvo с 2019 г., заводы, не оказывающие влияния на климат, серьезно уменьшат наш углеродный след и помогут предотвратить глобальное изменение климата».
Volvo Cars находится в постоянном поиске новых путей к достижению поставленной на 2025 г. цели. Так, в 2016 г. на заводе в Генте (Бельгия) была представлена централизованная система теплоснабжения, благодаря которой удалось на 40 % снизить выбросы углекислого газа в атмосферу, что равнозначно 15 000 тонн СО2 в год.
«Мы продолжим работать в этом направлении с поставщиками во всех странах, чтобы обеспечить переход наших производств на возобновляемые источники энергии», — пообещал Хавьер Варела.
——————————-
О Volvo Car Group
Компания Volvo существует с 1927 года. Сегодня Volvo — это один из наиболее известных и уважаемых в мире автомобильных брендов. Volvo Cars продает свои автомобили приблизительно в 100 странах, общемировые продажи за 2016 год составили 534 332 автомобиля. Volvo Cars являлась частью компании Volvo Group (Швеция) до 1999 года, когда она была приобретена компанией Ford Motor Company (США). В 2010 году Volvo Cars была приобретена компанией Zhejiang Geely Holding (Китай).
По состоянию на декабрь 2016 года в Volvo Cars работали более 31 000 человек по всему миру. Штаб-квартира Volvo Cars, включая основные подразделения по разработке продукции, маркетингу и управлению компанией, находится в Гётеборге (Швеция). Головной офис Volvo Cars, отвечающий за развитие в Китае, расположен в Шанхае. Основные производственные предприятия компании находятся в Гётеборге (Швеция), Генте (Бельгия), Чэнду и Дацине (Китай). Двигатели для автомобилей Volvo производятся на заводе в Шёвде (Швеция) и Чжанцзякоу (Китай), кузовные комплектующие производятся на заводе в Улофстрёме (Швеция).
Ключевые слова:
Окружающая среда, Завод, Устойчивость
Опубликованная в данном пресс-релизе и на медиа сайте Volvo Car Group информация может быть изменена в любое время без предварительного уведомления или обязательств. Пожалуйста, для получения наиболее свежей и достоверной для российского рынка информации обращайтесь в пресс-службу Volvo Car Group в России.
www.media.volvocars.com
Визит на завод Volvo CE в шведском Браасе – Основные средства
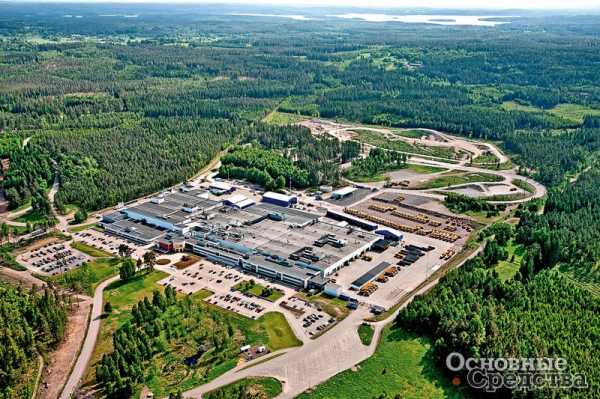
В июне Volvo Construction Equipment организовала поездку журналистов профильных изданий из России, Белоруссии и Казахстана на завод шарнирно-сочлененных самосвалов в Браасе (Швеция). Впечатление о поездке в текущих политико-экономических условиях можно передать одной фразой: завод работает на полную мощность. А это сегодня дорогого стоит.
Завод в Браасе в своем современном виде запущен в 1996 г. Общая площадь заводской территории – 39 000 м2, из них под крышей 30 000 м2. Численность персонала сегодня 850 человек при двухсменной работе пять дней в неделю, участок окраски работает в три смены. При пиковой нагрузке в 2008 г. было задействовано до 1000 человек.
Работники завода преимущественно местные – жители городка Браас и окрестных деревень, так что завод своего рода градообразующее предприятие. В кадровой политике прослеживается царящий в Скандинавии матриархат, то есть при прочих равных условиях на работу принимают женщину. Соответственно при сокращении на улице первым окажется мужчина.
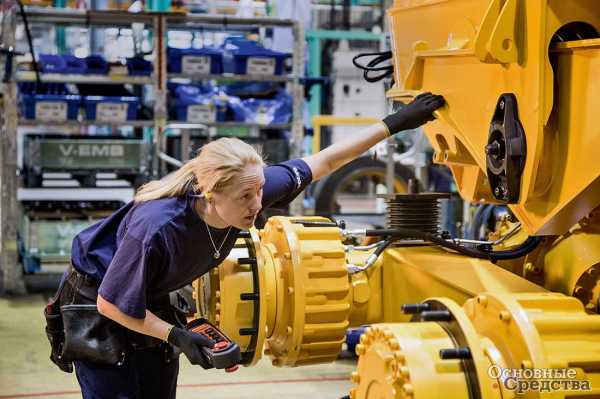
Теоретическая мощность производства – 25 машин в сутки. Сейчас выпускают от 8 до 11 машин. В период расцвета, то есть в первой половине 2008 г., завод выпускал по 75 машин в неделю. Производственный цикл, то есть время, затрачиваемое на изготовление одной машины, около 24 ч. Завод работает под заказ, но некоторое количество самосвалов стандартизированных комплектаций выпускают для склада, чтобы впоследствии с помощью этого запаса компенсировать всплески спроса.
Производство в Браасе включает раскрой металла, сварку передней и задней полурам и кузова, окраску передней и задней полурам и кузова и полную сборку машины. Непосредственно на самом заводе изготавливают переднюю полураму, заднюю полураму и самосвальный кузов. Остальные компоненты поступают с других заводов Volvo – двигатели, КПП, мосты, кабины – и от сторонних производителей.
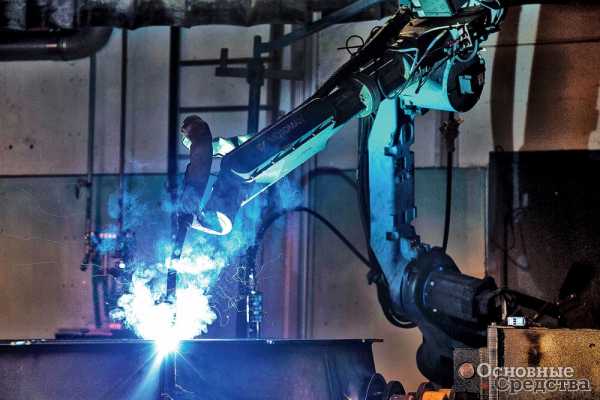
В год завод перерабатывает 250 тыс. т стали. Используют шведскую и финскую листовую сталь размером до 6000х2000 мм. Раскрой металла полностью лазерный, толщина листов – от 6 до 16 мм, точность резки ±0,1 мм на погонный метр. Конструкции рассчитаны так, чтобы максимальная толщина металла не превышала 16 мм и производство не усложнялось. После лазерной резки заготовки не требуют дальнейшей механической обработки, если, конечно, их не нужно гнуть. Гибку заготовок ведут на прессе усилием 640 т на столе длиной 4,5 м.
Готовые детали поступают на сварку. При лазерной резке на кромках сопрягаемых деталей сразу же выполняются выступы высотой 2 мм и впадины для их точной фиксации друг с другом. Детали складывают как «лего» и прихватывают ручной сваркой, затем сваривают роботами, для чего завод оснащен 33 автоматизированными сварочными постами. Вручную варят места, недоступные роботу. Самосвальные кузова изготавливают в различных конфигурациях: с задним бортом, без заднего борта, с износостойкой футеровкой, с высокими бортами, удлиненные.
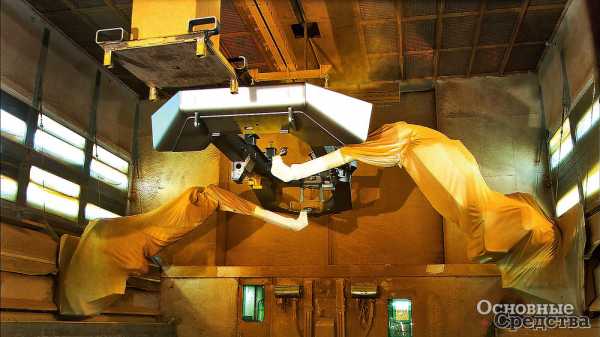
Автоматизированные токарно-фрезерные центры используют для обработки узлов вращения. Самый ответственный узел – шарнирное сочленение поступает в литых заготовках, которые здесь обрабатывают, окрашивают и собирают. Точность и качество сварки и обработки проверяют шаблонами, в случае сомнений применяют рентгеноскопию.
После сварки детали проходят дробеструйную обработку и поступают на окраску. Автоматизированная дробеструйка работает по ночам. Деталь обрабатывается дробью размером 1–1,6 мм в течение 6–12 минут в зависимости от размера детали. Участок окраски был недавно реконструирован – увеличили его пропускную способность, роботизировали и перевели на однослойную окраску двухкомпонентной автомобильной краской без грунтовки. Вручную красят отдельные места, недоступные роботу, и закрашивают повреждения. Толщина красочного слоя 100–150 микрон. Красят, как правило, в фирменные цвета, по заказу возможна другая окраска. В сушильной камере детали выдерживаются 30 минут при 120°, после чего их оставляют охладиться и подают на сборочную линию.
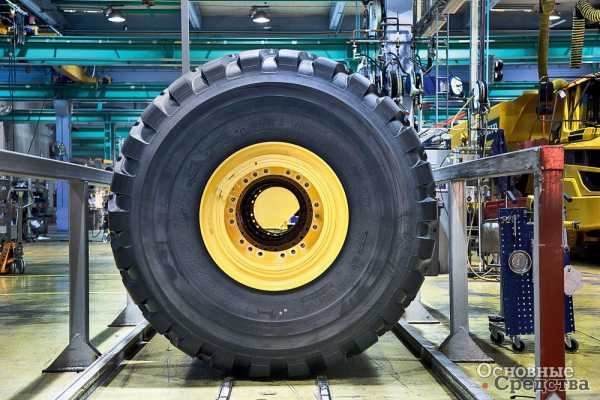
Сборка конвейерная, разбита на участки: установка сочленения, электропроводки, задней дуги, переднего моста, амортизаторов и кабелей, двигателя, КП, гидравлики, рулевого управления. Затем регулировка гидравлики и рулевого управления, установка топливного бака и трубопроводов под радиатором, кабины, крыльев, капота, колес, заправка топливом, маслами и жидкостями. Вдоль конвейера организованы посты подсборки узлов и агрегатов: сочленения, двигателя, кабины и т. д., всего порядка 60 постов. Используют широкую гамму шин: всего 24 вида стандартных шин и более 50 видов специальных шин Bridgestone, Goodyear, Yokohama, Michelin. По окончании сборки каждая машина проходит ходовые испытания в течение 1–1,5 часов на специальном тестовом полигоне.
В производственную программу завода входят самосвалы и шасси для последующего монтажа на них надстроек. Гарантийные обязательства по шасси несет Volvo, по надстройке – ее производитель.
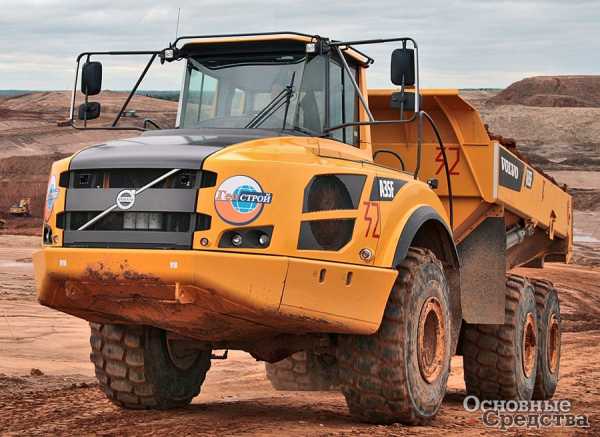
Историческая справка
Годом основания Volvo Construction Equipment считают 1832-й, когда механик и изобретатель Йохан Теофрон Мунктелл открыл механическую мастерскую в городке Эскильстуна, расположенном в 110 км на восток от Стокгольма. Мастерская специализировалась на передовых для своего времени печатных прессах, а также металлообрабатывающих станках, в которых нуждался Королевский ружейный завод. Но Йохану Мунктеллу этого было мало, и в 1853 г. из ворот мастерской выкатили первый шведский паровоз Förstlingen. Многие из изобретений Мунктелла увидели свет уже после того, как он покинул компанию, и даже после его смерти в 1887 г. В 1906 г. компания Munktell представила свою первую строительную машину – паровой каток, а в 1913 г. – первый шведский пропашной трактор.
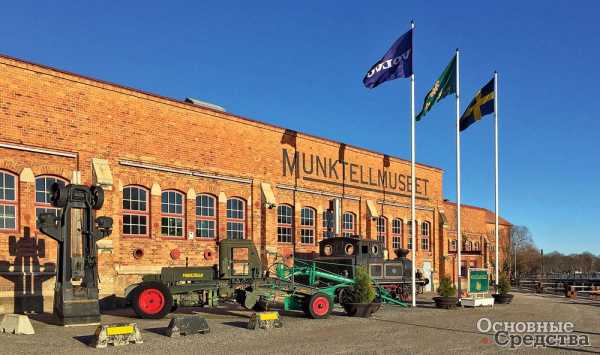
В этот же период создали и развивали собственный бизнес братья Жан и Карл Герхард Болиндеры. В 1844 г. они основали в Стокгольме компанию Kungsholmens Gjutery & Maskin Verkstad. Имя братьев стало известным благодаря проекту первой в мире вооруженной подводной лодки. Вероятно, отсюда у шведов такой интерес к подводным лодкам. В 1883 г. было построено две лодки, которые продали Греции и Турции. В 1893 г. Болиндеры построили первый шведский двигатель внутреннего сгорания – одноцилиндровый двухтактный керосиновый двигатель. После смерти основателей в конце XIX в. компания продолжила развитие моторного направления, которое совпало с расцветом эры ДВС.Обе компании развивались независимо вплоть до Великой Депрессии. В 1929 г. было принято решение о слиянии Bolinders и Munktell. Bolinders перебазировалась в Эскильстуну, и оба партнера начали работать под совместным именем AB Bolinder-Munktell.
Теперь самое время вспомнить о третьем действующем лице, а именно об автомобильной компании Volvo (от лат. volvo – «катать»), созданной двумя годами ранее, в 1927 г., Ассаром Габриэльсоном и Густавом Ларсоном, которая в 1950 г. купила Bolinder-Munktell. Для Bolinder-Munktell (ВМ) это достаточно дружественное поглощение послужило толчком для бурного развития. В 1952 г. ВМ выпустила первый шведский дизельный трактор, воссоздала линейку дизельных двигателей. В 1954 г. совместно с Lundbergs Mekaniska разработали колесный погрузчик h20 на базе трактора BM 35. С него началась линейка колесных погрузчиков Volvo. А в 1966 г. появился первый шарнирно-сочлененный самосвал, такой, каким мы знаем его сегодня.
Предыстория самосвала такова. В 1946 г. братья Леннарт и Карл Линнелли обратились в патентное бюро, чтобы зарегистрировать конструкцию трактора с приводным грузовым прицепом универсального назначения. Трактор был оснащен механизмом отбора мощности, от которого приводился мост прицепа. Их компания Lihnell Vagn AB (LIVAB), основанная в 1949 г., в 1957 г. перебазировалась в Браас, деревню с населением в 2000 жителей на юге Швеции, и приступила производству приводных самосвальных прицепов. Тогда же началось сотрудничество с ВМ, и рынку был предложен «трактор ВМ с самосвальным прицепом». Машина, названная DKD-15 с двухосным прицепом, приводилась трактором ВМ 55, а с 1959 г. – трактором BM 470 и несла на кузове марку LIVAB. Существовал вариант DKD-10 с одноосным прицепом. За ними в 1960 г. последовала модель DD-10 с трактором BM 350 Boxer и в 1964 г. модель DD-1524 с трактором ВМ 473. Двухосный прицеп DD-1524 отличался колесными редукторами и блокировкой дифференциала.
В 1963 г. истек срок действия патента братьев Линнелей, что открыло конкурентам двери в этот сегмент рынка. Доверенные сотрудники Карла Линнеля начали работу над секретным проектом машины для лесной промышленности без передней тракторной оси, с рулевым управлением поворотом полурам и приводом на все четыре колеса. Результат разработок – машина, названная Timber Charlie, была представлена в 1964 г. Таким образом, в руках у LIVAB появилась рабочая концепция рулевого управления поворотом полурам.
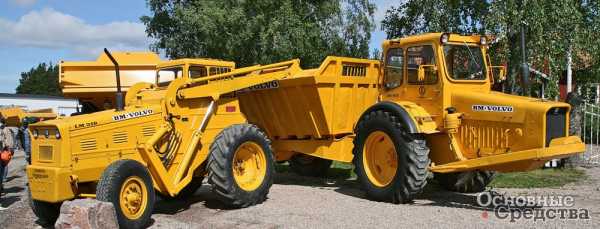
В 1965 г. между LIVAB и BM было заключено более детальное соглашение с разделением ответственности в производстве, маркетинге и сервисе, что усилило интеграцию компаний. Бренд LIVAB заменили на BM-Volvo. Ускорили разработку сочлененного самосвала, построенного на тех же принципах, что и Timber Charlie. Наконец, в 1966 г. представили Gravel Charlie – первый двухосный полноприводный шарнирно-сочлененный самосвал. Шведский рынок благосклонно принял новинку, и к 1969 г. продали более 400 самосвалов этой модели.
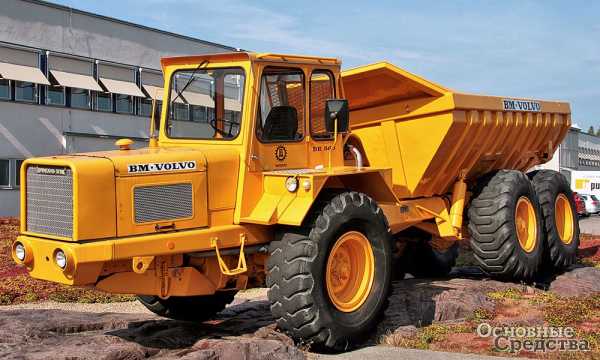
Следующая модель DR 860 грузоподъемностью 15 т увидела свет в 1967 г., и с нею связан вывод сочлененных самосвалов BM-Volvo на международный рынок. За период с 1967 по 1986 гг. выпустили 10 000 самосвалов модели DR 860 и ее модификации DR 861. Преемников DR 860 – модели А20 и А25 запустили в производство в 1985 г., а в 1987 г. расширили модельный ряд самосвалом нового типоразмера А35. Всего к 1992 г. завод выпустил 20 000 самосвалов, производственную мощность нарастили до 900 машин в год. Новое поколение, серию С, поставили на производство в 1993 г., а в 1995 г. вывели на рынок свою самую тяжелую модель А40. Сегодня с конвейера завода Volvo CE в Браасе сходят самосвалы и шасси серии F. В 1981 г. LIVAB полностью потеряла самостоятельность и вошла в состав Volvo BM со статусом производственной единицы.
os1.ru
VOLVO показала журналистам уникальное производство двигателей в Швеции
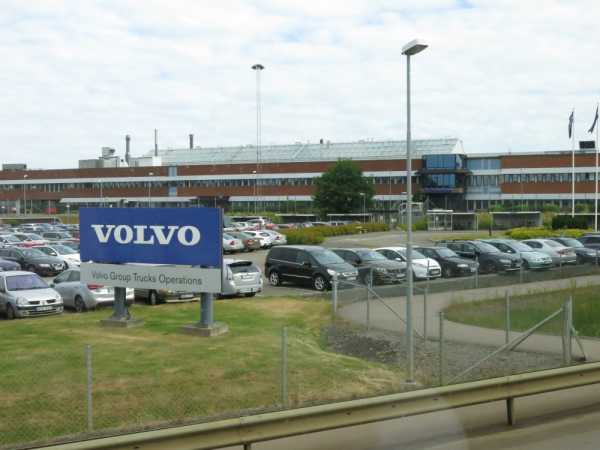
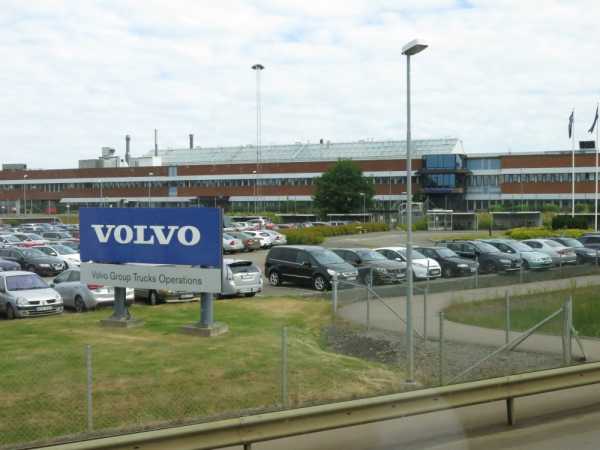
Швеция. Завод по производству двигателей VOLVO. Передает наш спецкор Алексей Невский. Здесь, вблизи небольшого города Шёвде, расположены два завода шведской компании по производству двигателей.
Один из них теперь не принадлежит известному бренду, здесь производятся двигатели для легковых автомобилей. Другой производит их для всей остальной техники, в том числе и принадлежащей самой VOLVO.
Именно на этот завод пригласили российских журналистов по программе пресс-тура. Об истории завода и его современной жизни рассказал журналистам его директор Ене Холтингер.
В частности, он рассказал, что площадь завода составляет 265 тыс. кв. м, за прошлый год здесь произвели 87 тыс. двигателей, из которых 11% составляют двигатели объемом 13 литров, а 89% — 16-литровые двигатели.
С особой гордостью директор отметил, что два завода VOLVO в городе составляют градообразующее предприятие, на котором работает каждый десятый житель города. Только на его заводе работают около трех тысяч человек.
Затем журналисты ознакомились с производством самих двигателей от литья блоков и головок к ним.
Цех по литью и производственные площадки поразили всех чистотой рабочей территории, компактностью и автоматизированностью производства.
Большую часть сборки и литья осуществляют роботы компании АВВ, литье блоков и головок к блокам осуществляют электрические печи, что значительно улучшает экологическое состояние (в отличие от угольных печей — прим. ред.).
Завод выпускает девятнадцать двигателей в час, которые проходят двойное испытание: холодный запуск 19 секунд и горячий в течение часа.
Завод в целом производит двигатели для строительной техники компании, пассажирских автобусов, самосвалов, морских и речных судов. Сегодня, с сожалением отметил директор завода, объем поставляемых в Россию двигателей составляет менее 1%.
Этот рабочий день журналисты из России закончили в Гетеборге, посетив музей компании.
Для справки: первый двигатель здесь был собран в 1907 году, в 1927 году завод приступил к производству серийных двигателей для первых автомобилей компании, в том числе и на первые автобусы.
Для любителей статистики: допустимый или возможный возврат двигателя от потребителя на завод составляет 1 двигатель из одного миллиона. Однако директор, работающий здесь четыре года, не смог вспомнить подобного случая.
От редакции: Администрация завода не рекомендовала фотографировать сборку двигателей, а потому мы не можем вам показать фото этого замечательного производства.
globalsuntech.com
Добавить комментарий