Π‘Ρ Π΅ΠΌΠ° ΡΡΡΡΠΎΠΉΡΡΠ²Π° ΡΡΠ΅ΠΏΠ½ΠΎΠ³ΠΎ ΡΡΡΡΠΎΠΉΡΡΠ²Π° β Π’ΡΠ³ΠΎΠ²ΠΎ-ΡΡΠ΅ΠΏΠ½ΠΎΠ΅ ΡΡΡΡΠΎΠΉΡΡΠ²ΠΎ Π½Π° ΡΡΠ°ΠΊΡΠΎΡ | ΠΠΎΠ΄ΡΠΎΠ±Π½ΠΎ ΠΎ ΡΡΠ°ΠΊΡΠΎΡΠ°Ρ ΠΈ ΡΠ΅Π»ΡΡΠΊΠΎΡ ΠΎΠ·ΡΠΉΡΡΠ²Π΅Π½Π½ΠΎΠΉ ΡΠ΅Ρ Π½ΠΈΠΊΠ΅
Π‘Ρ Π΅ΠΌΠ° ΠΏΠΎΠ΄ΠΊΠ»ΡΡΠ΅Π½ΠΈΡ ΠΏΡΠΈΡΠ΅ΠΏΠ°, ΡΠ°ΡΠΏΠΈΠ½ΠΎΠ²ΠΊΠ° ΡΠΎΠ·Π΅ΡΠΊΠΈ ΡΠ°ΡΠΊΠΎΠΏΠ°
ΠΠ°ΡΠ° ΠΏΡΠ±Π»ΠΈΠΊΠ°ΡΠΈΠΈ: .
ΠΠ°Π»ΠΈΡΠΈΠ΅ ΡΡΠ³ΠΎΠ²ΠΎΠ³ΠΎ ΡΡΠ΅ΠΏΠ½ΠΎΠ³ΠΎ ΡΡΡΡΠΎΠΉΡΡΠ²Π° (Π’Π‘Π£) Π² Π°Π²ΡΠΎΠΌΠΎΠ±ΠΈΠ»Π΅, ΠΏΠΎΠ·Π²ΠΎΠ»ΡΠ΅Ρ ΡΡΠ°Π½ΡΠΏΠΎΡΡΠΈΡΠΎΠ²Π°ΡΡ Π³ΡΡΠ·Ρ Ρ ΠΏΠΎΠΌΠΎΡΡΡ ΠΏΡΠΈΡΠ΅ΠΏΠ°. ΠΠ΄Π½Π°ΠΊΠΎ ΠΌΠ°Π»ΠΎ ΠΏΡΠΎΡΡΠΎ ΠΏΡΠΈΠΎΠ±ΡΠ΅ΡΡΠΈ ΠΈ ΡΡΡΠ°Π½ΠΎΠ²ΠΈΡΡ Π½Π°ΠΈΠ±ΠΎΠ»Π΅Π΅ ΠΏΠΎΠ΄Ρ ΠΎΠ΄ΡΡΠΈΠΉ Π΄Π»Ρ Π²Π°ΡΠ΅ΠΉ ΠΌΠ°ΡΠΈΠ½Ρ ΡΠ°ΡΠΊΠΎΠΏ, Π΅Π³ΠΎ Π½ΡΠΆΠ½ΠΎ ΡΠ°ΠΊΠΆΠ΅ ΠΏΠΎΠ΄ΠΊΠ»ΡΡΠΈΡΡ. ΠΠ΅Π»ΠΎ Π² ΡΠΎΠΌ, ΡΡΠΎ Π΄Π»Ρ Π±Π΅Π·ΠΎΠΏΠ°ΡΠ½ΠΎΠΉ ΡΠΊΡΠΏΠ»ΡΠ°ΡΠ°ΡΠΈΠΈ ΠΏΡΠΈΡΠ΅ΠΏΠ°, Π½Π° Π½Π΅ΠΌ ΠΎΠ±ΡΠ·Π°ΡΠ΅Π»ΡΠ½ΠΎ Π΄ΠΎΠ»ΠΆΠ½Ρ ΡΠ°Π±ΠΎΡΠ°ΡΡ ΡΠΈΠ³Π½Π°Π»ΡΠ½ΡΠ΅ ΠΎΠ³Π½ΠΈ, ΠΏΠΎΠ·Π²ΠΎΠ»ΡΡΡΠΈΠ΅ Π΄ΡΡΠ³ΠΈΠΌ ΡΡΠ°ΡΡΠ½ΠΈΠΊΠ°ΠΌ Π΄ΠΎΡΠΎΠΆΠ½ΠΎΠ³ΠΎ Π΄Π²ΠΈΠΆΠ΅Π½ΠΈΡ ΠΎΡΠΈΠ΅Π½ΡΠΈΡΠΎΠ²Π°ΡΡΡΡ Π² Π²Π°ΡΠΈΡ Π΄Π΅ΠΉΡΡΠ²ΠΈΡΡ .
ΠΠΎΠ΄ΠΊΠ»ΡΡΠ΅Π½ΠΈΠ΅ ΡΠ»Π΅ΠΊΡΡΠΈΠΊΠΈ ΡΠ°ΡΠΊΠΎΠΏΠ° ΡΠ²ΠΎΠΈΠΌΠΈ ΡΡΠΊΠ°ΠΌΠΈ ΠΌΠΎΠΆΠ½ΠΎ ΠΏΡΠΎΠΈΠ·Π²Π΅ΡΡΠΈ Π±Π΅Π· Π»ΠΈΡΠ½ΠΈΡ Π·Π°ΡΡΠ°Ρ ΠΈ ΡΠΏΠ΅ΡΠΈΠ°Π»ΠΈΠ·ΠΈΡΠΎΠ²Π°Π½Π½ΡΡ ΠΈΠ½ΡΡΡΡΠΌΠ΅Π½ΡΠΎΠ². ΠΠΎΡΡΠ°ΡΠΎΡΠ½ΠΎ Π»ΠΈΡΡ ΡΠ°Π·ΠΎΠ±ΡΠ°ΡΡΡΡ Π² ΡΠΈΠΏΠ΅ ΡΠ°Π·Π²ΠΎΠ΄ΠΊΠΈ ΠΈ ΠΏΡΠΈΠΎΠ±ΡΠ΅ΡΡΠΈ ΡΠΎΠΎΡΠ²Π΅ΡΡΡΠ²ΡΡΡΠΈΠΉ ΠΏΠ΅ΡΠ΅Ρ ΠΎΠ΄Π½ΠΈΠΊ, Π΅ΡΠ»ΠΈ ΠΎΠ½ ΠΏΠΎΡΡΠ΅Π±ΡΠ΅ΡΡΡ.
ΠΠ²ΡΠΎΠΏΠ΅ΠΉΡΠΊΠ°Ρ ΠΈ ΠΎΡΠ΅ΡΠ΅ΡΡΠ²Π΅Π½Π½Π°Ρ ΡΠ°Π·Π²ΠΎΠ΄ΠΊΠ°
ΠΠ° ΡΠ°ΠΌΠΎΠΌ Π’Π‘Π£ ΠΏΠΎΠ΄ Π·Π°ΡΠΈΡΠ½ΠΎΠΉ ΠΊΡΡΡΠΊΠΎΠΉ ΡΠ°ΡΠΏΠΎΠ»ΠΎΠΆΠ΅Π½Π° ΠΎΡΠΎΠ±Π°Ρ ΠΏΠ»ΠΎΡΠ°Π΄ΠΊΠ° – ΡΠΎΠ·Π΅ΡΠΊΠ° ΡΠ°ΡΠΊΠΎΠΏΠ°. Π‘Ρ Π΅ΠΌΠ° Π΅Π΅ ΠΏΠΎΠ΄ΠΊΠ»ΡΡΠ΅Π½ΠΈΡ Π·Π°Π²ΠΈΡΠΈΡ ΠΎΡ ΠΊΠΎΠ»ΠΈΡΠ΅ΡΡΠ²Π° ΠΊΠΎΠ½ΡΠ°ΠΊΡΠΎΠ². ΠΠ±ΡΡΠ½ΠΎ Π½Π° ΠΎΡΠ΅ΡΠ΅ΡΡΠ²Π΅Π½Π½ΡΡ Π°Π²ΡΠΎ ΠΈΡΠΏΠΎΠ»ΡΠ·ΡΡΡΡΡ ΡΠΎΠ·Π΅ΡΠΊΠΈ Π½Π° 7 ΠΊΠΎΠ½ΡΠ°ΠΊΡΠΎΠ², Π° 13-ΠΊΠΎΠ½ΡΠ°ΠΊΡΠ½ΡΠ΅ ΠΈΠ·Π΄Π΅Π»ΠΈΡ Π±ΠΎΠ»ΡΡΠ΅ Ρ Π°ΡΠ°ΠΊΡΠ΅ΡΠ½Ρ ΠΈΠ½ΠΎΠΌΠ°ΡΠΊΠ°ΠΌ ΠΈΠ· ΠΠ²ΡΠΎΠΏΡ ΠΈ Π‘Π¨Π (Π°ΠΌΠ΅ΡΠΈΠΊΠ°Π½ΡΠΊΠΈΠ΅ Π²ΡΠΏΡΡΠΊΠ°ΡΡΡΡ ΡΠ°ΠΊΠΆΠ΅ Ρ 7-ΠΊΠΎΠ½ΡΠ°ΠΊΡΠ½ΡΠΌΠΈ ΡΠΎΠ·Π΅ΡΠΊΠ°ΠΌΠΈ). ΠΠΎ Π±ΠΎΠ»ΡΡΠΎΠΌΡ ΡΡΠ΅ΡΡ ΡΠ°ΡΠΏΠΈΠ½ΠΎΠ²ΠΊΠ° ΡΠ°Π·ΡΠ΅ΠΌΠ° ΡΠ°ΡΠΊΠΎΠΏΠ° ΠΎΡΠ»ΠΈΡΠ°Π΅ΡΡΡ ΡΠΎΠ»ΡΠΊΠΎ Π½Π°Π»ΠΈΡΠΈΠ΅ΠΌ Π΄ΠΎΠΏΠΎΠ»Π½ΠΈΡΠ΅Π»ΡΠ½ΡΡ ΠΏΠΈΠ½ΠΎΠ² Π΄Π»Ρ Π°ΠΊΡΠΈΠ²Π°ΡΠΈΠΈ ΡΠ»Π΅ΠΊΡΡΠΈΡΠ΅ΡΠΊΠΎΠΉ Π½Π°ΡΠΈΠ½ΠΊΠΈ, ΠΊΠΎΡΠΎΡΠ°Ρ ΡΡΡΠ°Π½Π°Π²Π»ΠΈΠ²Π°Π΅ΡΡΡ Π½Π΅ Π² ΠΎΠ±ΡΡΠ½ΡΡ ΠΏΡΠΈΡΠ΅ΠΏΠ°Ρ , Π° Π² ΠΏΠΎΠ»Π½ΠΎΡΠ΅Π½Π½ΡΡ Π΄ΠΎΠΌΠ°Ρ -ΠΏΡΠΈΡΠ΅ΠΏΠ°Ρ . ΠΡΠ»ΠΈ ΠΆΠ΅ ΡΠ΅ΡΡ ΠΈΠ΄Π΅Ρ ΠΎ ΡΡΠ°Π½Π΄Π°ΡΡΠ½ΠΎΠΌ ΡΡΡΡΠΎΠΉΡΡΠ²Π΅ Π΄Π»Ρ ΠΏΠ΅ΡΠ΅Π²ΠΎΠ·ΠΊΠΈ Π²Π΅ΡΠ΅ΠΉ, ΡΠΎ Π΄Π»Ρ Π½Π΅Π³ΠΎ Π±ΠΎΠ»ΡΡΠ΅ ΠΏΠΎΠ΄ΠΎΠΉΠ΄Π΅Ρ ΡΠ°Π·ΡΠ΅ΠΌ ΡΠ°ΡΠΊΠΎΠΏΠ°, ΡΠ°ΡΠΏΠΈΠ½ΠΎΠ²ΠΊΠ° ΠΊΠΎΡΠΎΡΠΎΠ³ΠΎ Π±ΡΠ΄Π΅Ρ ΡΠΎΠΎΡΠ²Π΅ΡΡΡΠ²ΠΎΠ²Π°ΡΡ 7 ΡΠ»Π΅ΠΌΠ΅Π½ΡΠ°ΠΌ.
Π Π°ΡΡΠΌΠΎΡΡΠΈΠΌ Π²Π°ΡΠΈΠ°Π½Ρ Π΅Π²ΡΠΎΠΏΠ΅ΠΉΡΠΊΠΎΠΉ ΡΠ°Π·Π²ΠΎΠ΄ΠΊΠΈ, Π³Π΄Π΅:
ΠΠΎΠ΄ΠΊΠ»ΡΡΠ΅Π½ΠΈΠ΅ ΠΏΡΠΎΠ²ΠΎΠ΄ΠΊΠΈ ΡΠ°ΡΠΊΠΎΠΏΠ° ΠΏΡΠΎΠΈΠ·Π²ΠΎΠ΄ΠΈΡΡΡ ΡΠ°ΠΊΠΆΠ΅ ΠΈ ΠΏΠΎ ΠΎΡΠ΅ΡΠ΅ΡΡΠ²Π΅Π½Π½ΠΎΠΉ ΡΡ Π΅ΠΌΠ΅:
- ΠΠ΅Π²ΡΠΉ ΠΏΠΎΠ²ΠΎΡΠΎΡΠ½ΠΈΠΊ (ΠΆΠ΅Π»ΡΡΠΉ).
- ΠΡΠΎΡΠΈΠ²ΠΎΡΡΠΌΠ°Π½ΠΊΠ° (Π³ΠΎΠ»ΡΠ±ΠΎΠΉ).
- Β«ΠΠ΅ΠΌΠ»ΡΒ».
- ΠΡΠ°Π²ΡΠΉ ΠΏΠΎΠ²ΠΎΡΠΎΡΠ½ΠΈΠΊ (Π·Π΅Π»Π΅Π½ΡΠΉ).
- Π‘Π²ΠΎΠ±ΠΎΠ΄Π½ΡΠΉ.
- Π‘ΡΠΎΠΏ-ΡΠΈΠ³Π½Π°Π»Ρ (ΠΊΠΎΡΠΈΡΠ½Π΅Π²ΡΠΉ).
- ΠΠ°Π±Π°ΡΠΈΡΠ½ΡΠ΅ ΠΎΠ³Π½ΠΈ (ΡΠ΅ΡΠ½ΡΠΉ).
ΠΡΠ»ΠΈ ΡΠ°ΡΠΏΠΈΠ½ΠΎΠ²ΠΊΠ° ΡΠ°ΡΠΊΠΎΠΏΠ° Π½Π΅ ΡΠΎΠΎΡΠ²Π΅ΡΡΡΠ²ΡΠ΅Ρ ΠΏΡΠΈΡΠ΅ΠΏΡ (Π΄ΠΎΠΏΡΡΡΠΈΠΌ, Π²Ρ ΠΏΠ»Π°Π½ΠΈΡΡΠ΅ΡΠ΅ ΡΠΊΡΠΏΠ»ΡΠ°ΡΠΈΡΠΎΠ²Π°ΡΡ ΠΎΡΠ΅ΡΠ΅ΡΡΠ²Π΅Π½Π½ΡΠΉ ΠΏΡΠΈΡΠ΅ΠΏ, ΠΏΠΎΠ΄ΠΊΠ»ΡΡΠΈΠ² Π΅Π³ΠΎ ΠΊ ΠΈΠ½ΠΎΠΌΠ°ΡΠΊΠ΅, ΠΈΠ»ΠΈ Π½Π°ΠΎΠ±ΠΎΡΠΎΡ), ΡΠΎ Π΄ΠΎΡΡΠ°ΡΠΎΡΠ½ΠΎ ΡΠΎΠ»ΡΠΊΠΎ ΠΏΡΠΈΠΎΠ±ΡΠ΅ΡΡΠΈ Π°Π΄Π°ΠΏΡΠ΅Ρ ΠΈ ΠΏΡΠΎΠΈΠ·Π²Π΅ΡΡΠΈ ΠΏΠΎΠ΄ΠΊΠ»ΡΡΠ΅Π½ΠΈΠ΅ ΠΏΠΎ ΠΎΠΏΠΈΡΠ°Π½Π½ΠΎΠΉ Π²ΡΡΠ΅ ΡΡ Π΅ΠΌΠ΅.
ΠΡΠΈΡΠ»ΠΎ Π²ΡΠ΅ΠΌΡ ΠΏΠ΅ΡΠ΅ΠΉΡΠΈ ΠΊ ΠΏΡΠ°ΠΊΡΠΈΡΠ΅ΡΠΊΠΈΠΌ ΡΠ΅ΠΊΠΎΠΌΠ΅Π½Π΄Π°ΡΠΈΡΠΌ, ΠΊΠ°ΡΠ°ΡΡΠΈΠΌΡΡ ΡΠΎΠ³ΠΎ, ΠΊΠ°ΠΊ ΠΏΠΎΠ΄ΠΊΠ»ΡΡΠΈΡΡ ΡΠΎΠ·Π΅ΡΠΊΡ ΡΠ°ΡΠΊΠΎΠΏΠ° ΠΊ Π°Π²ΡΠΎΠΌΠΎΠ±ΠΈΠ»Ρ ΡΠ°ΠΌΠΎΡΡΠΎΡΡΠ΅Π»ΡΠ½ΠΎ.
ΠΠΎΠ΄ΠΊΠ»ΡΡΠ°Π΅ΠΌ ΡΠΎΠ·Π΅ΡΠΊΡ ΡΠ°ΡΠΊΠΎΠΏΠ° ΠΊ ΠΌΠ°ΡΠΈΠ½Π΅
ΠΠ΅ΡΠ΅Π΄ ΡΠ΅ΠΌ, ΠΊΠ°ΠΊ ΠΏΡΠΎΠΈΠ·Π²Π΅ΡΡΠΈ ΠΏΠΎΠ΄ΠΊΠ»ΡΡΠ΅Π½ΠΈΠ΅ ΡΠΎΠ·Π΅ΡΠΊΠΈ ΡΠ°ΡΠΊΠΎΠΏΠ° ΠΊ Π°Π²ΡΠΎΠΌΠΎΠ±ΠΈΠ»Ρ, Π½Π΅ΠΎΠ±Ρ ΠΎΠ΄ΠΈΠΌΠΎ ΡΠ΄ΠΎΡΡΠΎΠ²Π΅ΡΠΈΡΡΡΡ, ΡΡΠΎ Π΅Π΅ ΠΊΠΎΡΠΏΡΡ, ΠΊΡΡΡΠΊΠ° ΠΈ Π·Π°Π³Π»ΡΡΠΊΠ° Π³Π΅ΡΠΌΠ΅ΡΠΈΡΠ½Ρ. ΠΠ»Ρ ΡΡΠΎΠ³ΠΎ ΠΎΠ±Π»Π΅ΠΉΡΠ΅ ΡΡΡ Π΄Π΅ΡΠ°Π»Ρ Π²ΠΎΠ΄ΠΎΠΉ ΠΈ ΠΏΠΎΡΠΌΠΎΡΡΠΈΡΠ΅, Π±ΡΠ΄ΡΡ Π»ΠΈ ΠΏΡΠΎΡΠ΅ΡΠΊΠΈ. ΠΡΠ»ΠΈ ΠΊΠΎΠ½ΡΡΡΡΠΊΡΠΈΡ Π½Π΅ Π³Π΅ΡΠΌΠ΅ΡΠΈΡΠ½Π°, ΡΠΎ ΡΠ»Π°Π±ΡΠ΅ ΠΌΠ΅ΡΡΠ° Π½ΡΠΆΠ½ΠΎ Π±ΡΠ΄Π΅Ρ ΠΎΠ±ΡΠ°Π±ΠΎΡΠ°ΡΡ ΡΠΈΠ»ΠΈΠΊΠΎΠ½ΠΎΠΌ, ΠΏΠΎΡΠ»Π΅ Π·Π°Π²Π΅ΡΡΠ°ΡΡΠ΅Π³ΠΎ ΡΡΠ°ΠΏΠ° ΠΌΠΎΠ½ΡΠ°ΠΆΠ° ΡΠ°ΡΠΊΠΎΠΏΠ°.
Π‘Π°ΠΌΠ° ΡΠΎΠ·Π΅ΡΠΊΠ° ΠΏΠΎΠ΄ΠΊΠ»ΡΡΠ°Π΅ΡΡΡ Π΄Π²ΡΠΌΡ ΡΠΏΠΎΡΠΎΠ±Π°ΠΌΠΈ:
- Π‘ΡΠ°Π½Π΄Π°ΡΡΠ½ΡΠΌ. Π ΡΡΠΎΠΌ ΡΠ»ΡΡΠ°Π΅ Π½Π΅ ΠΏΡΠ΅Π΄ΠΏΠΎΠ»Π°Π³Π°Π΅ΡΡΡ Π½ΠΈΠΊΠ°ΠΊΠΈΡ ΠΈΠ·ΠΌΠ΅Π½Π΅Π½ΠΈΠΉ ΡΠ»Π΅ΠΊΡΡΠΈΡΠ΅ΡΠΊΠΎΠΉ ΡΠΈΡΡΠ΅ΠΌΡ Π°Π²ΡΠΎΠΌΠΎΠ±ΠΈΠ»Ρ. ΠΡΠ»ΠΈ ΠΏΡΠΈΡΠ΅ΠΏ ΠΈ Π’Π‘Π£ ΠΎΠ±Π»Π°Π΄Π°ΡΡ ΡΠΎΠΎΡΠ²Π΅ΡΡΡΠ²ΡΡΡΠΈΠΌΠΈ ΡΠ°Π·ΡΠ΅ΠΌΠ°ΠΌΠΈ, ΡΠΎ ΡΡ Π΅ΠΌΡ Π΄Π»Ρ ΡΠ°ΠΊΠΎΠ³ΠΎ ΠΏΠΎΠ΄ΠΊΠ»ΡΡΠ΅Π½ΠΈΡ Π½Π΅ ΠΏΠΎΡΡΠ΅Π±ΡΠ΅ΡΡΡ β Π΄ΠΎΡΡΠ°ΡΠΎΡΠ½ΠΎ Π²ΡΠ΅Π³ΠΎ Π»ΠΈΡΡ Π²ΡΡΠ°Π²ΠΈΡΡ ΡΠΎΠ·Π΅ΡΠΊΡ Π² Π³Π½Π΅Π·Π΄ΠΎ.
- Π£Π½ΠΈΠ²Π΅ΡΡΠ°Π»ΡΠ½ΡΠΌ. Π ΡΠ»ΡΡΠ°Π΅, ΠΊΠΎΠ³Π΄Π° ΡΠ΅ΡΡ ΠΈΠ΄Π΅Ρ Π½Π΅ ΠΎ ΡΡΠ°ΡΠ½ΠΎΠΌ ΠΎΠ±ΠΎΡΡΠ΄ΠΎΠ²Π°Π½ΠΈΠΈ, Π° ΠΎ ΠΏΡΠΈΠΎΠ±ΡΠ΅ΡΠ΅Π½Π½ΠΎΠΌ Π΄ΠΎΠΏΠΎΠ»Π½ΠΈΡΠ΅Π»ΡΠ½ΠΎ ΡΠ°ΡΠΊΠΎΠΏΠ΅ ΠΈΠ»ΠΈ ΠΏΡΠΈΡΠ΅ΠΏΠ΅, ΡΠΎ ΡΠ°ΡΠ΅ Π²ΡΠ΅Π³ΠΎ ΡΡΠ΅Π±ΡΠ΅ΡΡΡ Π±ΠΎΠ»Π΅Π΅ ΡΠ»ΠΎΠΆΠ½ΠΎΠ΅ ΠΏΠΎΠ΄ΠΊΠ»ΡΡΠ΅Π½ΠΈΠ΅.
ΠΡΠ»ΠΈ ΡΠΎ ΡΡΠ°Π½Π΄Π°ΡΡΠ½ΡΠΌ Π²Π°ΡΠΈΠ°Π½ΡΠΎΠΌ Π²ΡΠ΅ ΠΏΠΎΠ½ΡΡΠ½ΠΎ, ΡΠΎ ΠΏΠΎΠ΄ΠΊΠ»ΡΡΠΈΡΡ ΡΠ°ΡΠΊΠΎΠΏ ΠΊ ΠΏΡΠΎΠ²ΠΎΠ΄ΠΊΠ΅ Π°Π²ΡΠΎΠΌΠΎΠ±ΠΈΠ»Ρ ΡΠ½ΠΈΠ²Π΅ΡΡΠ°Π»ΡΠ½ΡΠΌ ΠΌΠ΅ΡΠΎΠ΄ΠΎΠΌ ΠΌΠΎΠΆΠ½ΠΎ Π΄Π²ΡΠΌΡ Π²Π°ΡΠΈΠ°Π½ΡΠ°ΠΌΠΈ.
ΠΠ°ΡΠΈΠ°Π½Ρ 1
ΠΠ°Π½Π½ΡΠΉ ΠΌΠ΅ΡΠΎΠ΄ ΠΏΠΎΠ΄Ρ ΠΎΠ΄ΠΈΡ Π΄Π»Ρ ΡΠ΅Ρ ΡΠΈΡΡΠ°ΡΠΈΠΉ, ΠΊΠΎΠ³Π΄Π° Π² Π°Π²ΡΠΎΠΌΠΎΠ±ΠΈΠ»Π΅ ΠΎΡΡΡΡΡΡΠ²ΡΠ΅Ρ ΡΠΎΠ²ΡΠ΅ΠΌΠ΅Π½Π½ΡΠΉ Π±Π»ΠΎΠΊ ΡΠΏΡΠ°Π²Π»Π΅Π½ΠΈΡ, ΡΡΠΎ Π΄Π΅Π»Π°Π΅Ρ Π²ΠΎΠ·ΠΌΠΎΠΆΠ½ΡΠΌ ΠΏΠΎΠ΄ΠΊΠ»ΡΡΠΈΡΡ ΠΏΡΠΎΠ²ΠΎΠ΄Π° Π½Π°ΠΏΡΡΠΌΡΡ ΠΊ ΡΠ»Π΅ΠΊΡΡΠΎ-ΡΠ΅ΠΏΠΈ. ΠΡΠΎ ΠΎΠ·Π½Π°ΡΠ°Π΅Ρ ΡΡΠΎ ΠΏΡΠΎΠ²ΠΎΠ΄ΠΊΠ°, ΠΈΠ΄ΡΡΠ°Ρ Ρ ΡΠ°Π·ΡΠ΅ΠΌΠ°, ΠΏΠΎΠ΄ΠΊΠ»ΡΡΠ°Π΅ΡΡΡ ΠΊ ΠΏΡΠΎΠ²ΠΎΠ΄Π°ΠΌ Π·Π°Π΄Π½ΠΈΡ ΡΠ²Π΅ΡΠΎΠ²ΡΡ ΡΠ»Π΅ΠΌΠ΅Π½ΡΠΎΠ².
ΠΠ»Ρ ΡΡΠΎΠ³ΠΎ, ΡΠΏΠ΅ΡΠ²Π°, Π½Π΅ΠΎΠ±Ρ ΠΎΠ΄ΠΈΠΌΠΎ ΠΎΠ±ΡΠ°ΡΠΈΡΡΡΡ ΠΊ ΡΡ Π΅ΠΌΠ΅ ΠΏΠΎΠ΄ΠΊΠ»ΡΡΠ΅Π½ΠΈΡ ΡΠΎΠ·Π΅ΡΠΊΠΈ ΠΏΡΠΈΡΠ΅ΠΏΠ°, ΠΊΠΎΡΠΎΡΡΡ ΠΌΠΎΠΆΠ½ΠΎ Π½Π°ΠΉΡΠΈ Π² ΡΠΎΠΏΡΠΎΠ²ΠΎΠ΄ΠΈΡΠ΅Π»ΡΠ½ΡΡ Π΄ΠΎΠΊΡΠΌΠ΅Π½ΡΠ°Ρ ΠΈ ΠΈΠ½ΡΡΡΡΠΊΡΠΈΡΡ . ΠΠ°Π»Π΅Π΅, ΠΏΡΠΎΠΈΠ·Π²ΠΎΠ΄ΠΈΡΡΡ ΠΏΠΎΠ΄ΠΊΠ»ΡΡΠ΅Π½ΠΈΠ΅ ΡΠ°ΠΌΠΎΠΉ ΡΠΎΠ·Π΅ΡΠΊΠΈ Π² ΠΎΠ±Π»Π°ΡΡΠΈ, Π³Π΄Π΅ ΡΠ°ΡΠΏΠΎΠ»Π°Π³Π°Π΅ΡΡΡ ΠΊΠΎΠ»ΠΎΠ΄ΠΊΠ° ΠΆΠ³ΡΡΠ° Π·Π°Π΄Π½Π΅Π³ΠΎ ΡΠΎΠ½Π°ΡΡ ΠΌΠ°ΡΠΈΠ½Ρ. Π§Π°ΡΠ΅ Π²ΡΠ΅Π³ΠΎ Π² ΡΡΠΎΠΌ ΠΌΠ΅ΡΡΠ΅ ΠΌΠΎΠΆΠ½ΠΎ Π½Π°ΠΉΡΠΈ ΡΠΏΠ΅ΡΠΈΠ°Π»ΡΠ½ΠΎΠ΅ ΡΠ΅Ρ Π½ΠΎΠ»ΠΎΠ³ΠΈΡΠ΅ΡΠΊΠΎΠ΅ ΠΎΠΊΠ½ΠΎ, ΠΏΡΠ΅Π΄ΡΡΠΌΠΎΡΡΠ΅Π½Π½ΠΎΠ΅ ΠΏΡΠΎΠΈΠ·Π²ΠΎΠ΄ΠΈΡΠ΅Π»ΡΠΌΠΈ Ρ ΡΠ΅Π»ΡΡ ΡΠΏΡΠΎΡΡΠΈΡΡ ΠΏΡΠΎΡΠ΅Π΄ΡΡΡ Π·Π°ΠΌΠ΅Π½Ρ ΠΈΡΠΏΠΎΡΡΠ΅Π½Π½ΡΡ Π»Π°ΠΌΠΏΠΎΡΠ΅ΠΊ.
ΠΠΎΠ»Π΅Π·Π½ΠΎ! ΠΡΠΈ ΡΡΠΎΠΌ Ρ Π²Π°Ρ Π΄ΠΎΠ»ΠΆΠ΅Π½ Π±ΡΡΡ Π»ΠΈΡΠ½ΠΈΠΉ ΠΏΡΠΎΠ²ΠΎΠ΄ Π΄Π»Ρ Π²ΡΠΎΡΠΎΠ³ΠΎ ΠΏΠΎΠ²ΠΎΡΠΎΡΠ½ΠΈΠΊΠ°.
ΠΠ»Ρ ΡΠΎΠ³ΠΎ ΡΡΠΎΠ±Ρ ΠΏΠΎΠ΄ΠΊΠ»ΡΡΠΈΡΡ ΡΠΎΠ·Π΅ΡΠΊΡ ΡΠ°ΠΊΠΈΠΌ ΠΎΠ±ΡΠ°Π·ΠΎΠΌ Π²Ρ ΠΌΠΎΠΆΠ΅ΡΠ΅ ΠΈΡΠΏΠΎΠ»ΡΠ·ΠΎΠ²Π°ΡΡ ΠΎΠ±ΠΆΠΈΠΌΠ½ΡΠ΅ ΠΊΠ»ΠΈΠΏΡΡ ΠΈΠ»ΠΈ ΠΏΡΠΎΡΡΠΎ ΡΠ½ΡΡΡ ΠΈΠ·ΠΎΠ»ΡΡΠΈΡ Ρ ΠΏΡΠΎΠ²ΠΎΠ΄ΠΎΠ², ΡΠΎΠ΅Π΄ΠΈΠ½ΠΈΡΡ ΠΈΡ ΠΈ Π·Π°ΠΊΡΠ΅ΠΏΠΈΡΡ ΠΏΠΎΡΡΠ΅Π΄ΡΡΠ²ΠΎΠΌ ΠΏΠ°ΠΉΠΊΠΈ. Π’Π°ΠΊΠΆΠ΅ ΡΡΠΎΠΈΡ ΡΡΠΈΡΡΠ²Π°ΡΡ, ΡΡΠΎ Π΄Π»Ρ ΡΠΎΠ³ΠΎ, ΡΡΠΎΠ±Ρ Π²ΡΠ΅ ΠΏΠΎΠ΄ΠΊΠ»ΡΡΠΈΡΡ ΠΏΡΠ°Π²ΠΈΠ»ΡΠ½ΠΎ, Π»ΡΡΡΠ΅ Π²ΠΎΠΎΡΡΠΆΠΈΡΡΡΡ ΡΡ Π΅ΠΌΠΎΠΉ ΡΠ»Π΅ΠΊΡΡΠΎΠΏΡΠΎΠ²ΠΎΠ΄ΠΊΠΈ ΠΌΠ°ΡΠΈΠ½Ρ.
ΠΠ°ΡΠΈΠ°Π½Ρ 2
ΠΡΠ»ΠΈ ΠΆΠ΅ Π²Ρ ΡΠ²Π»ΡΠ΅ΡΠ΅ΡΡ Π²Π»Π°Π΄Π΅Π»ΡΡΠ΅ΠΌ ΡΠΎΠ²ΡΠ΅ΠΌΠ΅Π½Π½ΠΎΠΉ ΠΈΠ½ΠΎΠΌΠ°ΡΠΊΠΈ, ΡΠΎ, ΡΠΊΠΎΡΠ΅Π΅ Π²ΡΠ΅Π³ΠΎ Π² Π½Π΅ΠΉ ΡΡΡΠ°Π½ΠΎΠ²Π»Π΅Π½Π° Π½Π΅ΠΏΡΠΎΡΡΠ°Ρ ΡΠ»Π΅ΠΊΡΡΠΎΠ½Π½Π°Ρ Π½Π°ΡΠΈΠ½ΠΊΠ°, ΠΊΠΎΡΠΎΡΠ°Ρ Π½Π΅ ΠΏΠΎΠ·Π²ΠΎΠ»ΠΈΡ ΠΏΠΎΠ΄ΠΊΠ»ΡΡΠΈΡΡ ΠΏΡΠΈΡΠ΅ΠΏ ΠΏΠ΅ΡΠ²ΡΠΌ ΠΌΠ΅ΡΠΎΠ΄ΠΎΠΌ. ΠΠ΅Π»ΠΎ Π² ΡΠΎΠΌ, ΡΡΠΎ ΡΡΡΠ°Π½ΠΎΠ²Π»Π΅Π½Π½ΡΠΉ Π±Π»ΠΎΠΊ ΡΠΏΡΠ°Π²Π»Π΅Π½ΠΈΡ ΠΏΠΎΡΡΠΎΡΠ½Π½ΠΎ ΠΊΠΎΠ½ΡΡΠΎΠ»ΠΈΡΡΠ΅Ρ ΠΎΠΏΡΠΈΠΊΡ, ΡΠ°ΡΠΏΠΎΠ»ΠΎΠΆΠ΅Π½Π½ΡΡ Π² Π·Π°Π΄Π½Π΅ΠΉ ΡΠ°ΡΡΠΈ Π°Π²ΡΠΎΠΌΠΎΠ±ΠΈΠ»Ρ. ΠΠ°ΠΊ ΡΠΎΠ»ΡΠΊΠΎ Π² ΡΡΠΎΠΉ ΠΎΠ±Π»Π°ΡΡΠΈ Π½Π°ΡΠ½Π΅ΡΡΡ Π±ΠΎΠ»ΡΡΠ΅Π΅ ΠΏΠΎΡΡΠ΅Π±Π»Π΅Π½ΠΈΠ΅ ΡΠΎΠΊΠ° β ΡΡΠΎ Π±ΡΠ΄Π΅Ρ Π²ΠΎΡΠΏΡΠΈΠ½ΡΡΠΎ ΡΠΈΡΡΠ΅ΠΌΠΎΠΉ ΠΊΠ°ΠΊ ΠΎΡΠΈΠ±ΠΊΠ°.
Π§ΡΠΎΠ±Ρ ΠΈΠ·Π±Π΅ΠΆΠ°ΡΡ ΠΏΠΎΠ΄ΠΎΠ±Π½ΠΎΠΉ ΠΏΡΠΎΠ±Π»Π΅ΠΌΡ ΠΈΡΠΏΠΎΠ»ΡΠ·ΡΠ΅ΡΡΡ Π΄ΠΎΠΏΠΎΠ»Π½ΠΈΡΠ΅Π»ΡΠ½ΡΠΉ ΡΠ»Π΅ΠΌΠ΅Π½Ρ, ΠΊΠΎΡΠΎΡΡΠΉ Π½Π°Π·ΡΠ²Π°Π΅ΡΡΡ Π±Π»ΠΎΠΊΠΎΠΌ ΡΠΎΠ³Π»Π°ΡΠΎΠ²Π°Π½ΠΈΡ. ΠΡΠΎΡ ΠΏΡΠΈΠ±ΠΎΡ ΠΏΠΎΠ΄ΠΊΠ»ΡΡΠ°ΡΡ ΠΊ ΡΡΠ°ΡΠ½ΠΎΠΉ ΡΠ»Π΅ΠΊΡΡΠΈΠΊΠ΅ Π°Π²ΡΠΎΠΌΠΎΠ±ΠΈΠ»Ρ, ΠΈ ΠΎΠ½ ΡΡΠ°Π½ΠΎΠ²ΠΈΡΡΡ ΡΠ²ΠΎΠ΅Π³ΠΎ ΡΠΎΠ΄Π° ΠΏΠΎΡΡΠ΅Π΄Π½ΠΈΠΊΠΎΠΌ, ΠΏΠΎΠ·Π²ΠΎΠ»ΡΡΡΠΈΠΌ Π±Π΅ΡΠΏΡΠ΅ΠΏΡΡΡΡΠ²Π΅Π½Π½ΠΎ ΠΏΠ΅ΡΠ΅Π΄Π°Π²Π°ΡΡ ΡΠΈΠ³Π½Π°Π» Π½Π° ΡΠ²Π΅ΡΠΎΠ²ΡΠ΅ ΡΠ»Π΅ΠΌΠ΅Π½ΡΡ ΠΏΡΠΈΡΠ΅ΠΏΠ°.
ΠΠΎΠ»Π΅Π·Π½ΠΎ! ΠΠ»ΠΎΠΊ ΡΠΏΡΠ°Π²Π»Π΅Π½ΠΈΡ ΡΠ»Π΅ΠΌΠ΅Π½ΡΠ°ΡΠ½ΠΎ Π½Π΅ Π±ΡΠ΄Π΅Ρ Β«Π²ΠΈΠ΄Π΅ΡΡΒ» Π΄ΠΎΠΏΠΎΠ»Π½ΠΈΡΠ΅Π»ΡΠ½ΡΠΉ ΠΈ ΡΠ»Π΅ΠΌΠ΅Π½Ρ, ΡΠΎΠΎΡΠ²Π΅ΡΡΡΠ²Π΅Π½Π½ΠΎ Π½ΠΈΠΊΠ°ΠΊΠΈΡ ΡΠΎΠΎΠ±ΡΠ΅Π½ΠΈΠΉ ΠΎΠ± ΠΎΡΠΈΠ±ΠΊΠ°Ρ Π²ΠΎΠ΄ΠΈΡΠ΅Π»Ρ Π½Π΅ ΠΏΠΎΠ»ΡΡΠΈΡ.
ΠΡΠ»ΠΈ Π²Ρ Π½Π΅ Ρ ΠΎΡΠΈΡΠ΅ ΠΏΠΎΠΊΡΠΏΠ°ΡΡ Π±Π»ΠΎΠΊ ΡΠΎΠ³Π»Π°ΡΠΎΠ²Π°Π½ΠΈΡ, ΡΠΎ ΠΌΠΎΠΆΠ½ΠΎ Π²ΠΎΡΠΏΠΎΠ»ΡΠ·ΠΎΠ²Π°ΡΡΡΡ ΠΌΠ°Π»Π΅Π½ΡΠΊΠΎΠΉ Ρ ΠΈΡΡΠΎΡΡΡΡ β ΠΈΡΠΏΠΎΠ»ΡΠ·ΠΎΠ²Π°ΡΡ ΡΠ΅Π»Π΅. ΠΠ½ΠΎ, ΠΏΠΎ Π±ΠΎΠ»ΡΡΠΎΠΌΡ ΡΡΠ΅ΡΡ, Π±ΡΠ΄Π΅Ρ Π²ΡΠΏΠΎΠ»Π½ΡΡΡ ΡΡΠ½ΠΊΡΠΈΡ ΡΠΏΡΠ°Π²Π»ΡΡΡΠ΅Π³ΠΎ ΡΠ»Π΅ΠΌΠ΅Π½ΡΠ°, ΠΏΠΎΠ΄Π°ΡΡΠ΅Π³ΠΎ Π½Π°ΠΏΡΡΠΆΠ΅Π½ΠΈΠ΅ Π½Π° Π³Π°Π±Π°ΡΠΈΡΠ½ΡΠ΅ ΠΎΠ³Π½ΠΈ ΠΏΡΠΈΡΠ΅ΠΏΠ°. Π’Π°ΠΊΠΆΠ΅ ΡΠ΅Π»Π΅ ΠΌΠΎΠΆΠ½ΠΎ ΡΡΡΠ°Π½ΠΎΠ²ΠΈΡΡ ΠΈ Π΄Π»Ρ ΡΡΠΎΠΏ-ΡΠΈΠ³Π½Π°Π»ΠΎΠ² ΠΈ ΠΏΡΠΎΡΠΈΠ²ΠΎΡΡΠΌΠ°Π½ΠΎΠΊ (Π΅ΡΠ»ΠΈ ΡΠ°ΠΊΠΎΠ²ΡΠ΅ ΡΡΡΠ°Π½ΠΎΠ²Π»Π΅Π½Ρ).
ΠΠΎΡΠ»Π΅ ΡΠΎΠ³ΠΎ ΠΊΠ°ΠΊ Π²Ρ ΠΏΠΎΠ΄ΠΊΠ»ΡΡΠΈΠ»ΠΈ ΠΏΡΠΈΡΠ΅ΠΏ ΠΈ ΠΏΡΠΎΠ²Π΅ΡΠΈΠ»ΠΈ ΡΡΠΎ Π²ΡΠ΅ ΡΠΈΡΡΠ΅ΠΌΡ ΡΠ°Π±ΠΎΡΠ°ΡΡ Π½ΠΎΡΠΌΠ°Π»ΡΠ½ΠΎ, Π° ΠΎΠ³Π½ΠΈ Π³ΠΎΡΡΡ, Π½Π΅ Π·Π°Π±ΡΠ΄ΡΡΠ΅ Π·Π°ΡΠΈΡΠΈΡΡ Π²Π½ΡΡΡΠ΅Π½Π½ΠΈΠ΅ ΡΠ»Π΅ΠΌΠ΅Π½ΡΡ ΠΎΡ Π²Π»Π°Π³ΠΈ. ΠΠ»Ρ Β«Π±ΡΠ΅ΡΠ΅ΠΉΒ» ΠΈΡΠΏΠΎΠ»ΡΠ·ΡΠ΅ΡΡΡ ΡΠΈΠ»ΠΈΠΊΠΎΠ½, Π° Π΄Π»Ρ Π·Π°ΡΠΈΡΡ ΠΊΠΎΠ½ΡΠ°ΠΊΡΠΎΠ² ΠΎΡ ΠΎΠΊΠΈΡΠ»Π΅Π½ΠΈΡ ΠΈΡ ΡΠ΅ΠΊΠΎΠΌΠ΅Π½Π΄ΡΠ΅ΡΡΡ ΠΎΠ±ΡΠ°Π±ΠΎΡΠ°ΡΡ Π³ΡΠ°ΡΠΈΡΠΎΠ²ΠΎΠΉ ΡΠΌΠ°Π·ΠΊΠΎΠΉ.
Π Π·Π°ΠΊΠ»ΡΡΠ΅Π½ΠΈΠΈ
ΠΡΠΈ ΠΏΠΎΠ΄ΠΊΠ»ΡΡΠ΅Π½ΠΈΠΈ ΡΠ°ΡΠΊΠΎΠΏΠ°, Π²Π°ΠΆΠ½ΠΎ ΡΠΎΠΎΡΠ²Π΅ΡΡΡΠ²ΠΎΠ²Π°ΡΡ ΡΡ Π΅ΠΌΠ°ΠΌ, ΡΡΠΎΠ±Ρ Π²ΡΠ΅ ΡΠ»Π΅ΠΌΠ΅Π½ΡΡ ΡΠ°Π±ΠΎΡΠ°Π»ΠΈ ΠΏΡΠ°Π²ΠΈΠ»ΡΠ½ΠΎ. ΠΡΠ»ΠΈ Π²Ρ ΡΠΎΠΌΠ½Π΅Π²Π°Π΅ΡΠ΅ΡΡ Π² ΡΠ²ΠΎΠΈΡ ΡΠΈΠ»Π°Ρ , ΡΠΎ Π»ΡΡΡΠ΅ Π½Π΅ ΡΠΈΡΠΊΠΎΠ²Π°ΡΡ ΠΈ ΠΎΠ±ΡΠ°ΡΠΈΡΡΡΡ ΠΊ ΡΠΏΠ΅ΡΠΈΠ°Π»ΠΈΡΡΠ°ΠΌ, ΠΊΠΎΡΠΎΡΡΠ΅ Π·Π° Π½Π΅Π±ΠΎΠ»ΡΡΡΡ ΠΏΠ»Π°ΡΡ ΡΠ΄Π΅Π»Π°ΡΡ Π²ΡΠ΅ ΡΠΎΠ³Π»Π°ΡΠ½ΠΎ Π²ΡΠ΅ΠΌ ΡΡΠ΅Π±ΠΎΠ²Π°Π½ΠΈΡΠΌ.
avto-moto-shtuchki.ru
ΠΡΠΈΡΠ΅ΠΏΠ½ΠΎΠ΅ ΡΡΡΡΠΎΠΉΡΡΠ²ΠΎ ΡΡΠ°ΠΊΡΠΎΡΠ°. Π‘Ρ Π΅ΠΌΠ° ΠΈ ΡΡΡΠ°Π½ΠΎΠ²ΠΊΠ°
ΠΡΠΈΡΠ΅ΠΏΠ½ΠΎΠ΅ ΡΡΡΡΠΎΠΉΡΡΠ²ΠΎ ΡΡΠ°ΠΊΡΠΎΡΠ° β Π’Π‘Π£-1Π ΠΏΡΠ΅Π΄Π½Π°Π·Π½Π°ΡΠ΅Π½ΠΎ Π΄Π»Ρ ΠΏΡΠΈΡΠΎΠ΅Π΄ΠΈΠ½Π΅Π½ΠΈΡ ΠΊ ΡΡΠ°ΠΊΡΠΎΡΡ ΠΏΡΠΈΡΠ΅ΠΏΠ½ΡΡ ΡΠ΅Π»ΡΡΠΊΠΎΡ ΠΎΠ·ΡΠΉΡΡΠ²Π΅Π½Π½ΡΡ ΠΌΠ°ΡΠΈΠ½ ΠΈ ΠΎΡΡΠ΄ΠΈΠΉ. ΠΡΠΈΡΠ΅ΠΏΠ½ΠΎΠ΅ ΡΡΡΡΠΎΠΉΡΡΠ²ΠΎ ΡΠΌΠΎΠ½ΡΠΈΡΠΎΠ²Π°Π½ΠΎ Π½Π° ΠΌΠ΅Ρ Π°Π½ΠΈΠ·ΠΌΠ΅ Π·Π°Π΄Π½Π΅ΠΉ Π½Π°Π²Π΅ΡΠΊΠΈ ΠΈ ΡΠΎΡΡΠΎΠΈΡ ΠΈΠ· ΠΏΠΎΠΏΠ΅ΡΠ΅ΡΠΈΠ½Ρ, ΠΏΡΠΈΡΠ΅ΠΏΠ½ΠΎΠΉ Π²ΠΈΠ»ΠΊΠΈ, ΡΠΊΠ²ΠΎΡΠ½Ρ ΠΈ Π΄Π²ΡΡ ΠΊΡΠΎΠ½ΡΡΠ΅ΠΉΠ½ΠΎΠ²
Π£ΡΡΡΠΎΠΉΡΡΠ²ΠΎ ΠΏΡΠΈΡΠ΅ΠΏΠ½ΠΎΠ³ΠΎ ΡΡΡΡΠΎΠΉΡΡΠ²Π°
ΠΡΠΈ ΠΎΡΠ³ΡΡΠ·ΠΊΠ΅ ΡΡΠ°ΠΊΡΠΎΡΠΎΠ² Ρ Π·Π°Π²ΠΎΠ΄Π° ΠΊΡΠΎΠ½ΡΡΠ΅ΠΉΠ½Ρ Π·Π°ΠΊΡΠ΅ΠΏΠ»ΡΡΡ Π² ΠΎΡΠ²Π΅ΡΡΡΠΈΡΡ ΠΏΡΠΎΠ΄ΠΎΠ»ΡΠ½ΡΡ ΡΡΠ³, Π° Π½Π° Π½ΠΈΡ Π½Π° Π²ΡΠ΅ΠΌΡ ΡΡΠ°Π½ΡΠΏΠΎΡΡΠΈΡΠΎΠ²Π°Π½ΠΈΡ ΡΡΠ°ΠΊΡΠΎΡΠ° ΡΡΡΠ°Π½Π°Π²Π»ΠΈΠ²Π°ΡΡ Π°Π²ΡΠΎΠΌΠ°ΡΠΈΡΠ΅ΡΠΊΡΡ ΡΡΠ΅ΠΏΠΊΡ. ΠΡΠΈ ΠΏΠΎΠ΄Π³ΠΎΡΠΎΠ²ΠΊΠ΅ ΡΡΠ°ΠΊΡΠΎΡΠ° ΠΊ ΡΠ°Π±ΠΎΡΠ΅ Ρ ΠΏΡΠΈΡΠ΅ΠΏΠ½ΡΠΌΠΈ ΠΌΠ°ΡΠΈΠ½Π°ΠΌΠΈ ΠΊΡΠΎΠ½ΡΡΠ΅ΠΉΠ½Ρ Π΄ΠΎΠ»ΠΆΠ½Ρ Π±ΡΡΡ ΡΡΡΠ°Π½ΠΎΠ²Π»Π΅Π½Ρ Π½Π° ΠΎΡΡ Π²ΠΌΠ΅ΡΡΠΎ ΠΏΡΠΎΠ΄ΠΎΠ»ΡΠ½ΡΡ ΡΡΠ³, Π° ΠΏΡΠΎΠ΄ΠΎΠ»ΡΠ½ΡΠ΅ ΡΡΠ³ΠΈ Π·Π°ΠΊΡΠ΅ΠΏΠ»Π΅Π½Ρ Π½Π° ΠΊΡΠΎΠ½ΡΡΠ΅ΠΉΠ½Π°Ρ ΡΠ΅ΡΠ΅Π· ΡΡΠΈ ΠΎΡΠ½ΠΎΠ²Π½ΡΡ ΠΈΠ»ΠΈ Π΄ΠΎΠΏΠΎΠ»Π½ΠΈΡΠ΅Π»ΡΠ½ΡΡ ΠΎΡΠ²Π΅ΡΡΡΠΈΡ. ΠΠΎΠ»ΡΡ Π΄Π»Ρ ΠΊΡΠ΅ΠΏΠ»Π΅Π½ΠΈΡ ΡΡΠ³ ΠΊ ΠΊΡΠΎΠ½ΡΡΠ΅ΠΉΠ½Π°ΠΌ Π½Π°Ρ ΠΎΠ΄ΡΡΡΡ Π² ΠΠΠΠ΅ ΡΡΠ°ΠΊΡΠΎΡΠ°. Π Π°ΡΠΊΠΎΡΡ ΠΌΠ΅Ρ Π°Π½ΠΈΠ·ΠΌΠ° Π½Π°Π²Π΅ΡΠΊΠΈ ΠΏΡΠΈ ΡΡΠΎΠΌ ΡΠΎΠ΅Π΄ΠΈΠ½ΡΡΡ Ρ ΠΏΡΠΎΠ΄ΠΎΠ»ΡΠ½ΡΠΌΠΈΒ ΡΡΠ³Π°ΠΌΠΈ ΡΠ΅ΡΠ΅Π· ΠΎΡΠ²Π΅ΡΡΡΠΈΡ ΠΈ ΠΊΡΡΠ³Π»ΠΎΠ΅ ΠΎΡΠ²Π΅ΡΡΡΠΈΠ΅ Π² Π²ΠΈΠ»ΠΊΠ°Ρ ΡΠ°ΡΠΊΠΎΡΠΎΠ². ΠΡΠΎΠΌΠ΅ ΡΠΎΠ³ΠΎ, ΡΡΡΠΆΠΊΠΈ Π΄ΠΎΠ»ΠΆΠ½Ρ Π±ΡΡΡ ΠΎΡΡΠΎΠ΅Π΄ΠΈΠ½Π΅Π½Ρ ΠΎΡ ΠΏΡΠΎΠ΄ΠΎΠ»ΡΠ½ΡΡ ΡΡΠ³, ΡΡΡΠ°Π½ΠΎΠ²Π»Π΅Π½Ρ Π² ΠΎΡΠ²Π΅ΡΡΡΠΈΡ Π½Π° ΠΏΠΎΠΏΠ΅ΡΠ΅ΡΠΈΠ½Π΅ (Π΄Π»Ρ ΡΡΡΠΆΠ΅ΠΊ Π²Π½ΡΡΡΠ΅Π½Π½Π΅Π³ΠΎ ΡΠ°ΡΠΏΠΎΠ»ΠΎΠΆΠ΅Π½ΠΈΡ) ΠΈΠ»ΠΈ ΠΎΡΠ²Π΅ΡΡΡΠΈΡ Π½Π° ΠΏΡΠΎΠ΄ΠΎΠ»ΡΠ½ΡΡ ΡΡΠ³Π°Ρ (Π΄Π»Ρ ΡΡΡΠΆΠ΅ΠΊ Π½Π°ΡΡΠΆΠ½ΠΎΠ³ΠΎ ΡΠ°ΡΠΏΠΎΠ»ΠΎΠΆΠ΅Π½ΠΈΡ) ΠΈ ΠΌΠ°ΠΊΡΠΈΠΌΠ°Π»ΡΠ½ΠΎ ΡΠΊΠΎΡΠΎΡΠ΅Π½Ρ Ρ ΡΠ΅ΠΌ, ΡΡΠΎΠ±Ρ ΠΏΡΠΎΠ΄ΠΎΠ»ΡΠ½ΡΠ΅ ΡΡΠ³ΠΈ Π²ΠΌΠ΅ΡΡΠ΅ Ρ ΠΏΠΎΠΏΠ΅ΡΠ΅ΡΠΈΠ½ΠΎΠΉ Π½Π΅ ΠΊΠ°ΡΠ°Π»ΠΈΡΡ Π² ΠΏΠΎΠΏΠ΅ΡΠ΅ΡΠ½ΠΎΠΉ ΠΏΠ»ΠΎΡΠΊΠΎΡΡΠΈ.
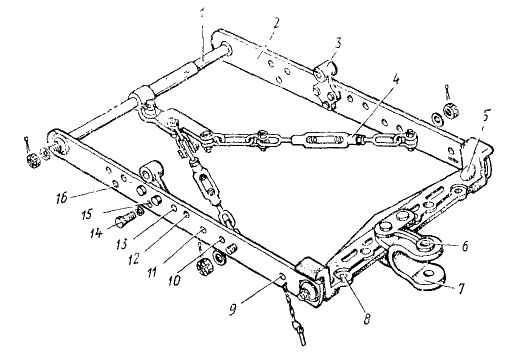
Π‘Π΅Ρ ΠΌΠ° ΠΏΡΠΈΡΠ΅ΠΏΠ½ΠΎΠ³ΠΎ ΡΡΡΡΠΎΠΉΡΡΠ²Π° ΡΡΠ°ΠΊΡΠΎΡΠ°: 1 β ΠΎΡΡ; 2 β ΠΏΡΠΎΠ΄ΠΎΠ»ΡΠ½Π°Ρ ΡΡΠ³Π°; 3 β ΠΊΡΠΎΠ½ΡΡΠ΅ΠΉΠ½; 4 β ΡΡΡΠΆΠΊΠ°; 5 β ΠΏΠΎΠΏΠ΅ΡΠ΅ΡΠΈΠ½Π°; 6 β ΠΎΡΠ²Π΅ΡΡΡΠΈΠ΅ Π΄Π»Ρ ΠΏΡΠΈΡΠΎΠ΅Π΄ΠΈΠ½Π΅Π½ΠΈΡ ΡΠ΅Π»ΡΡΠΊΠΎΡ ΠΎΠ·ΡΠΉΡΡΠ²Π΅Π½Π½ΡΡ ΠΌΠ°ΡΠΈΠ½; 7 β ΠΏΡΠΈΡΠ΅ΠΏΠ½Π°Ρ Π²ΠΈΠ»ΠΊΠ°; 8 β ΠΎΡΠ²Π΅ΡΡΡΠΈΠ΅ Π΄Π»Ρ ΠΏΡΠΈΡΠΎΠ΅Π΄ΠΈΠ½Π΅Π½ΠΈΡ ΡΡΡΠΆΠΊΠΈ; 9 β Π΄ΠΎΠΏΠΎΠ»Π½ΠΈΡΠ΅Π»ΡΠ½ΠΎΠ΅ ΠΎΡΠ²Π΅ΡΡΡΠΈΠ΅; 10,11,12 ΠΈ 13 β ΠΎΡΠ²Π΅ΡΡΡΠΈΡ Π΄Π»Ρ ΠΏΡΠΈΡΠΎΠ΅Π΄ΠΈΠ½Π΅Π½ΠΈΡ ΡΠ°ΡΠΊΠΎΡΠΎΠ²; 14 β Π±ΠΎΠ»Ρ; 15, 16 β ΠΎΡΠ²Π΅ΡΡΡΠΈΡ Π΄Π»Ρ ΠΏΡΠΈΡΠΎΠ΅Π΄ΠΈΠ½Π΅Π½ΠΈΡ ΠΊΡΠΎΠ½ΡΡΠ΅ΠΉΠ½ΠΎΠ².
Π£ΡΡΠ°Π½ΠΎΠ²ΠΊΠ° ΠΏΡΠΈΡΠ΅ΠΏΠ½ΠΎΠ³ΠΎ ΡΡΡΡΠΎΠΉΡΡΠ²Π°
ΠΠΎΠΏΡΡΠΊΠ°Π΅ΡΡΡ ΠΏΡΠΈ ΡΠ°Π±ΠΎΡΠ΅ Ρ ΠΏΡΠΈΡΠ΅ΠΏΠ½ΡΠΌΠΈ ΠΌΠ°ΡΠΈΠ½Π°ΠΌΠΈ Π±Π΅Π· ΠΈΡΠΏΠΎΠ»ΡΠ·ΠΎΠ²Π°Π½ΠΈΡ ΠΠΠ Π½Π΅ ΠΏΠ΅ΡΠ΅ΡΡΠ°Π²Π»ΡΡΡ ΠΏΡΠΎΠ΄ΠΎΠ»ΡΠ½ΡΠ΅ ΡΡΠ³ΠΈ Ρ ΠΎΡΠΈ Π½Π°Π²Π΅ΡΠΊΠΈ Π½Π° ΠΊΡΠΎΠ½ΡΡΠ΅ΠΉΠ½Ρ; ΠΏΠΎ ΠΏΡΠΈ ΡΡΠΎΠΌ ΠΏΡΠΈΡΠ΅ΠΏΠ½Π°Ρ Π²ΠΈΠ»ΠΊΠ° Π΄ΠΎΠ»ΠΆΠ½Π° ΠΎΠ±ΡΠ·Π°ΡΠ΅Π»ΡΠ½ΠΎ Π½Π°Ρ ΠΎΠ΄ΠΈΡΡΡΡ Π½Π° ΠΎΡΠΈ ΡΠΈΠΌΠΌΠ΅ΡΡΠΈΠΈ ΡΡΠ°ΠΊΡΠΎΡΠ°, Π° ΡΡΡΠΆΠΊΠΈ ΠΏΡΠΎΠ΄ΠΎΠ»ΡΠ½ΡΡ ΡΡΠ³ Π΄ΠΎΠ»ΠΆΠ½Ρ Π±ΡΡΡ ΠΌΠ°ΠΊΡΠΈΠΌΠ°Π»ΡΠ½ΠΎ Π½Π°ΡΡΠ½ΡΡΡ.
ΠΡΠ½ΠΎΠ²Π½ΡΠ΅ ΠΎΡΠ²Π΅ΡΡΡΠΈΡ ΠΏΡΠΎΠ΄ΠΎΠ»ΡΠ½ΡΡ ΡΡΠ³ ΠΏΡΠ΅Π΄Π½Π°Π·Π½Π°ΡΠ΅Π½Ρ Π΄Π»Ρ ΠΊΡΠ΅ΠΏΠ»Π΅Π½ΠΈΡ ΡΡΠ³ Π½Π° ΠΊΡΠΎΠ½ΡΡΠ΅ΠΉΠ½Π°Ρ ΠΏΡΠΈ ΡΠ°Π±ΠΎΡΠ΅ ΡΡΠ°ΠΊΡΠΎΡΠ° Ρ ΠΎΡΠ½ΠΎΠ²Π½ΡΠΌΠΈ ΠΏΡΠΈΡΠ΅ΠΏΠ½ΡΠΌΠΈ ΡΠ΅Π»ΡΡΠΊΠΎΡ ΠΎΠ·ΡΠΉΡΡΠ²Π΅Π½Π½ΡΠΌΠΈ ΠΌΠ°ΡΠΈΠ½Π°ΠΌΠΈ, Π² ΡΠΎΠΌ ΡΠΈΡΠ»Π΅ ΠΈ ΠΈΡΠΏΠΎΠ»ΡΠ·ΡΡΡΠΈΠΌΠΈ ΠΏΡΠΈΠ²ΠΎΠ΄ ΠΎΡ ΠΠΠ. ΠΡΠΈ ΡΡΠΎΠΌ ΡΠ°ΡΡΡΠΎΡΠ½ΠΈΠ΅ ΠΎΡ ΠΎΡΠ²Π΅ΡΡΡΠΈΠΈ Π² ΠΏΡΠΈΡΠ΅ΠΏΠ½ΠΎΠΉ Π²ΠΈΠ»ΠΊΠ΅ Π΄ΠΎ ΡΠΎΡΡΠ° ΠΠΠ Π±Π΅Π· ΡΠ΄Π»ΠΈΠ½ΠΈΡΠ΅Π»Ρ ΡΠ°Π²Π½ΠΎ 504 ΠΌΠΌ, Π° Ρ ΡΠ΄Π»ΠΈΠ½ΠΈΡΠ΅Π»Π΅ΠΌ β 394 ΠΌΠΌ. ΠΡΠΈ ΡΡΡΠ°Π½ΠΎΠ²ΠΊΠ΅ ΡΡΠ³ Π½Π° Π΄ΠΎΠΏΠΎΠ»Π½ΠΈΡΠ΅Π»ΡΠ½ΡΠ΅ ΠΎΡΠ²Π΅ΡΡΡΠΈΡ ΡΠ°ΡΡΡΠΎΡΠ½ΠΈΠ΅ ΠΎΡ ΠΎΡΠ²Π΅ΡΡΡΠΈΠΉ Π΄ΠΎ ΡΠΎΡΡΠ° ΠΠΠ Π±Π΅Π· ΡΠ΄Π»ΠΈΠ½ΠΈΡΠ΅Π»Ρ ΡΠ°Π²Π½ΠΎ 624 ΠΌΠΌ, Π° Ρ ΡΠ΄Π»ΠΈΠ½ΠΈΡΠ΅Π»Π΅ΠΌ β 514 ΠΌΠΌ.
tractor-server.ru
Π‘Π΅Π΄Π΅Π»ΡΠ½ΠΎ-ΡΡΠ΅ΠΏΠ½ΠΎΠ΅ ΡΡΡΡΠΎΠΉΡΡΠ²ΠΎ (Π‘Π‘Π£) β ΠΡΠ½ΠΎΠ²Π½ΡΠ΅ ΡΡΠ΅Π΄ΡΡΠ²Π°
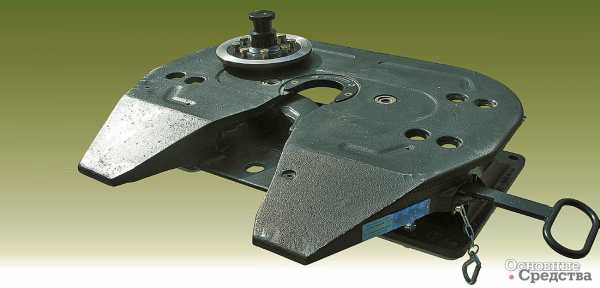
Π. ΠΠ°ΡΠΈΠ»ΡΠ΅Π², ΠΈΠ»Π»ΡΡΡΡΠ°ΡΠΈΠΈ ΠΈΠ· Π°ΡΡ ΠΈΠ²Π° Π°Π²ΡΠΎΡΠ°
Π‘ΠΏΠ΅ΡΠΈΠ°Π»ΠΈΡΡΡ Π½Π΅ΡΠ΅Π΄ΠΊΠΎ Π½Π°Π·ΡΠ²Π°ΡΡ ΡΠ΅Π΄Π΅Π»ΡΠ½ΠΎ-ΡΡΠ΅ΠΏΠ½ΠΎΠ΅ ΡΡΡΡΠΎΠΉΡΡΠ²ΠΎ, ΡΡΡΠ°Π½Π°Π²Π»ΠΈΠ²Π°Π΅ΠΌΠΎΠ΅ Π½Π° Π³ΡΡΠ·ΠΎΠ²ΠΎΠΉ Π°Π²ΡΠΎΠΌΠΎΠ±ΠΈΠ»Ρ-ΡΡΠ³Π°Ρ, Β«ΠΏΡΡΡΠΌ ΠΊΠΎΠ»Π΅ΡΠΎΠΌΒ» (ΠΎΡ Π°Π½Π³Π». fifth wheel). ΠΡΠΎΡ ΡΠ·Π΅Π» ΡΠ²Π»ΡΠ΅ΡΡΡ Π΅Π΄ΠΈΠ½ΡΡΠ²Π΅Π½Π½ΡΠΌ ΠΌΠ΅Ρ Π°Π½ΠΈΡΠ΅ΡΠΊΠΈΠΌ ΡΠ»Π΅ΠΌΠ΅Π½ΡΠΎΠΌ, ΡΠΎΠ΅Π΄ΠΈΠ½ΡΡΡΠΈΠΌ ΡΡΠ³Π°Ρ ΠΈ ΠΏΠΎΠ»ΡΠΏΡΠΈΡΠ΅ΠΏ Π°Π²ΡΠΎΠΏΠΎΠ΅Π·Π΄Π°.
ΠΡΠΎΠΈΠ·Π²ΠΎΠ΄ΡΡΠ²ΠΎ ΡΠ΅Π΄Π΅Π»ΡΠ½ΠΎ-ΡΡΠ΅ΠΏΠ½ΡΡ ΡΡΡΡΠΎΠΉΡΡΠ² (Π‘Π‘Π£) β Π±ΠΈΠ·Π½Π΅Ρ Π΄ΠΎΡ ΠΎΠ΄Π½ΡΠΉ ΠΈ Ρ ΠΎΡΠΎΡΠΎ ΠΎΡΠ²ΠΎΠ΅Π½Π½ΡΠΉ. ΠΠΌ Π·Π°Π½ΠΈΠΌΠ°Π΅ΡΡΡ ΡΠΎΠ»ΠΈΠ΄Π½Π°Ρ Π³ΡΡΠΏΠΏΠ° ΠΊΠΎΠΌΠΏΠ°Π½ΠΈΠΉ: Jost, Rockinger (ΠΠ΅ΡΠΌΠ°Π½ΠΈΡ), Georg Fisher (Π¨Π²Π΅ΠΉΡΠ°ΡΠΈΡ), Crane Fruehauf, York (ΠΠ΅Π»ΠΈΠΊΠΎΠ±ΡΠΈΡΠ°Π½ΠΈΡ), Fontaine Truck Equipment, Fruehauf, Holland Hitch ΠΈ Π΄Ρ. ΠΡΠΏΡΡΠΊΠ°ΡΡ Π‘Π‘Π£ ΠΈ ΠΎΡΠ΅ΡΠ΅ΡΡΠ²Π΅Π½Π½ΡΠ΅ ΠΏΡΠ΅Π΄ΠΏΡΠΈΡΡΠΈΡ.
ΠΠΎΠ½ΡΡΡΡΠΊΡΠΈΡ Π‘Π‘Π£ Π½Π°ΠΏΡΡΠΌΡΡ Π²Π»ΠΈΡΠ΅Ρ Π½Π° ΡΠ°ΠΊΠΈΠ΅ ΡΠΊΡΠΏΠ»ΡΠ°ΡΠ°ΡΠΈΠΎΠ½Π½ΡΠ΅ ΠΊΠ°ΡΠ΅ΡΡΠ²Π° Π°Π²ΡΠΎΠΏΠΎΠ΅Π·Π΄Π°, ΠΊΠ°ΠΊ ΡΠΏΡΠ°Π²Π»ΡΠ΅ΠΌΠΎΡΡΡ, ΡΡΡΠΎΠΉΡΠΈΠ²ΠΎΡΡΡ, ΠΌΠ°Π½Π΅Π²ΡΠ΅Π½Π½ΠΎΡΡΡ, ΠΏΠ»Π°Π²Π½ΠΎΡΡΡ Ρ ΠΎΠ΄Π°, ΠΏΡΠΎΡ ΠΎΠ΄ΠΈΠΌΠΎΡΡΡ, Π½Π°Π΄Π΅ΠΆΠ½ΠΎΡΡΡ, Π±Π΅Π·ΠΎΠΏΠ°ΡΠ½ΠΎΡΡΡ ΠΈ ΡΠΊΠΎΠ½ΠΎΠΌΠΈΡΠ΅ΡΠΊΠΈΠ΅ ΠΏΠΎΠΊΠ°Π·Π°ΡΠ΅Π»ΠΈ. Π ΠΎΠ±ΡΠ΅ΠΌ ΡΠ»ΡΡΠ°Π΅ ΡΠ΅Π΄Π΅Π»ΡΠ½ΠΎ-ΡΡΠ΅ΠΏΠ½ΡΠ΅ ΡΡΡΡΠΎΠΉΡΡΠ²Π° ΡΠΎΡΡΠΎΡΡ ΠΈΠ· ΡΠ°Π·ΡΠ΅ΠΌΠ½ΠΎ-ΡΡΠ΅ΠΏΠ½ΠΎΠΉ ΡΠΈΡΡΠ΅ΠΌΡ, ΠΌΠ΅Ρ Π°Π½ΠΈΠ·ΠΌΠ° Π³ΠΈΠ±ΠΊΠΎΡΡΠΈ ΠΈ Π΄Π΅ΡΠ°Π»Π΅ΠΉ ΠΊΡΠ΅ΠΏΠ»Π΅Π½ΠΈΡ. Π‘ΡΡΠ΅ΡΡΠ²ΡΠ΅Ρ Π΄Π²Π° ΡΠΈΠΏΠ° Π‘Π‘Π£: ΡΠΊΠ²ΠΎΡΠ½Π΅Π²ΡΠ΅ (ΠΏΠ°ΡΠ° ΡΠΊΠ²ΠΎΡΠ΅Π½ΡβΠ·Π°Ρ Π²Π°Ρ) ΠΈ ΡΠΎΠ»ΠΈΠΊΠΎΠ²ΡΠ΅, ΠΈΠ»ΠΈ Π±Π΅ΡΡΠΊΠ²ΠΎΡΠ½Π΅Π²ΡΠ΅ (ΠΏΠ°ΡΠ° ΠΊΡΡΠΊβΡΠΎΠ»ΠΈΠΊ). ΠΠ°ΡΡΠ° Π±ΠΎΠ»ΡΡΠΈΠ½ΡΡΠ²Π° Π‘Π‘Π£ ΡΠΎΡΡΠ°Π²Π»ΡΠ΅Ρ ΠΎΡ 100 Π΄ΠΎ 300 ΠΊΠ³.
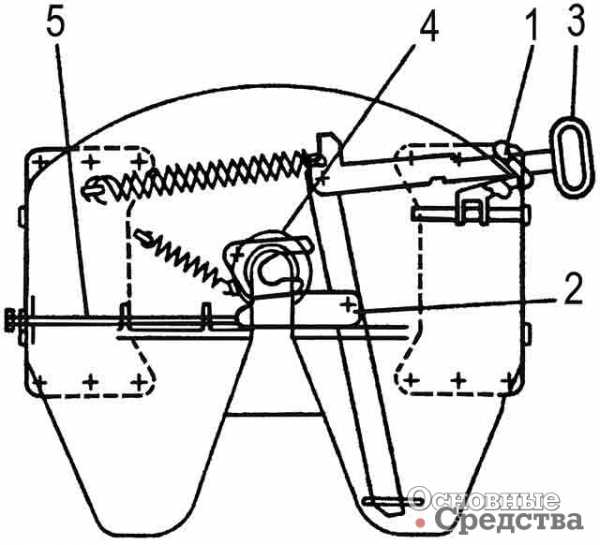
Π¨ΠΊΠ²ΠΎΡΠ½Π΅Π²ΡΠ΅ ΡΡΡΡΠΎΠΉΡΡΠ²Π°
Π Π±ΠΎΠ»ΡΡΠΈΠ½ΡΡΠ²Π΅ ΡΠ΅Π΄Π΅Π»ΡΠ½ΠΎ-ΡΡΠ΅ΠΏΠ½ΡΠ΅ ΡΡΡΡΠΎΠΉΡΡΠ²Π° (ΡΠ²ΡΡΠ΅ 95%) ΠΈΠΌΠ΅ΡΡ ΡΠΊΠ²ΠΎΡΠ½Π΅Π²ΡΡ ΠΊΠΎΠ½ΡΡΡΡΠΊΡΠΈΡ. Π‘ΡΠ΄Π° Π²Ρ ΠΎΠ΄ΡΡ ΠΎΠΏΠΎΡΠ½Π°Ρ ΠΏΠ»ΠΈΡΠ° (ΠΊΡΡΠ³) Ρ ΠΏΡΠΎΡΠ΅Π·ΡΡ (ΡΡΡΡΠ΅ΠΌ) Π² ΡΠ΅Π½ΡΡΠ°Π»ΡΠ½ΠΎΠΉ ΡΠ°ΡΡΠΈ, ΡΡΡΠ°Π½Π°Π²Π»ΠΈΠ²Π°Π΅ΠΌΠ°Ρ Π½Π° ΡΡΠ³Π°ΡΠ΅, ΠΈ ΡΠΊΠ²ΠΎΡΠ΅Π½Ρ, Π·Π°ΠΊΡΠ΅ΠΏΠ»Π΅Π½Π½ΡΠΉ Π½Π° ΠΏΠΎΠ»ΡΠΏΡΠΈΡΠ΅ΠΏΠ΅. ΠΡΠΈ ΡΡΠ΅ΠΏΠΊΠ΅ Π°Π²ΡΠΎΠΏΠΎΠ΅Π·Π΄Π° ΡΠΊΠ²ΠΎΡΠ΅Π½Ρ Π²Ρ ΠΎΠ΄ΠΈΡ Π² ΠΏΡΠΎΡΠ΅Π·Ρ ΠΎΠΏΠΎΡΠ½ΠΎΠΉ ΠΏΠ»ΠΈΡΡ ΠΈ ΡΠΈΠΊΡΠΈΡΡΠ΅ΡΡΡ Π·Π°Ρ Π²Π°ΡΠ°ΠΌΠΈ (ΠΎΠ΄Π½ΠΈΠΌ ΠΈΠ»ΠΈ Π½Π΅ΡΠΊΠΎΠ»ΡΠΊΠΈΠΌΠΈ), ΡΠ°ΡΠ½ΠΈΡΠ½ΠΎ Π·Π°ΠΊΡΠ΅ΠΏΠ»Π΅Π½Π½ΡΠΌΠΈ Π½Π° ΠΏΠ°Π»ΡΡΠ°Ρ . Π’Π°ΠΊ ΠΎΠ±ΡΠ°Π·ΡΠ΅ΡΡΡ ΡΡΠ΅ΠΏΠ½Π°Ρ ΠΏΠ°ΡΠ°. Π¨ΠΊΠ²ΠΎΡΠ½Π΅Π²ΡΠ΅ ΡΡΡΡΠΎΠΉΡΡΠ²Π° ΠΎΠ±ΡΡΠ½ΠΎ Π²ΡΠΏΠΎΠ»Π½ΡΡΡΡΡ ΠΏΠΎΠ»ΡΠ°Π²ΡΠΎΠΌΠ°ΡΠΈΡΠ΅ΡΠΊΠΈΠΌΠΈ (ΡΡΠ΅ΠΏΠΊΠ° Π·Π²Π΅Π½ΡΠ΅Π² Π°Π²ΡΠΎΠΏΠΎΠ΅Π·Π΄Π° ΠΏΡΠΎΠΈΡΡ ΠΎΠ΄ΠΈΡ Π°Π²ΡΠΎΠΌΠ°ΡΠΈΡΠ΅ΡΠΊΠΈ, Π° ΠΏΠΎΠ΄Π³ΠΎΡΠΎΠ²ΠΊΠ° ΠΊ ΡΠ°ΡΡΠ΅ΠΏΠΊΠ΅, Ρ. Π΅. ΡΠ°Π·Π±Π»ΠΎΠΊΠΈΡΠΎΠ²Π°Π½ΠΈΠ΅ Π·Π°ΠΌΠΊΠΎΠ²ΡΡ ΡΡΡΡΠΎΠΉΡΡΠ², β Π²ΡΡΡΠ½ΡΡ). Π§ΡΠΎΠ±Ρ ΠΏΡΠ΅Π΄ΠΎΡΠ²ΡΠ°ΡΠΈΡΡ ΡΠ°ΠΌΠΎΠΏΡΠΎΠΈΠ·Π²ΠΎΠ»ΡΠ½ΡΡ ΡΠ°ΡΡΠ΅ΠΏΠΊΡ, ΡΡΠ°Π²ΡΡ Π½Π΅ ΠΌΠ΅Π½Π΅Π΅ Π΄Π²ΡΡ Π·Π°ΠΌΠΊΠΎΠ²ΡΡ ΡΡΡΡΠΎΠΉΡΡΠ², Π΄Π΅ΠΉΡΡΠ²ΡΡΡΠΈΡ Π½Π΅Π·Π°Π²ΠΈΡΠΈΠΌΠΎ, ΠΏΡΠΈΡΠ΅ΠΌ ΠΎΠ΄Π½ΠΎ ΠΈΠ· Π½ΠΈΡ Ρ ΡΡΡΠ½ΡΠΌ ΡΠΏΡΠ°Π²Π»Π΅Π½ΠΈΠ΅ΠΌ. ΠΠΎΠ»Π½Π°Ρ ΠΌΠ°ΡΡΠ° Π°Π²ΡΠΎΠΏΠΎΠ΅Π·Π΄ΠΎΠ², ΠΎΠ±ΠΎΡΡΠ΄ΠΎΠ²Π°Π½Π½ΡΡ ΠΏΠΎΠ»ΡΠ°Π²ΡΠΎΠΌΠ°ΡΠΈΡΠ΅ΡΠΊΠΈΠΌΠΈ ΡΠΊΠ²ΠΎΡΠ½Π΅Π²ΡΠΌΠΈ ΡΡΡΡΠΎΠΉΡΡΠ²Π°ΠΌΠΈ, Π΄ΠΎΡΡΠΈΠ³Π°Π΅Ρ 100 Ρ ΠΈ Π±ΠΎΠ»Π΅Π΅. Π‘Π΅Π΄Π΅Π»ΡΠ½ΡΠ΅ ΡΡΡΡΠΎΠΉΡΡΠ²Π° ΡΠ°ΠΊΠΎΠ³ΠΎ ΡΠΈΠΏΠ° ΡΠΏΠΎΡΠΎΠ±Π½Ρ Π²ΡΠ΄Π΅ΡΠΆΠΈΠ²Π°ΡΡ Π½Π°Π³ΡΡΠ·ΠΊΠΈ ΠΎΡ 3 Π΄ΠΎ 50 Ρ.
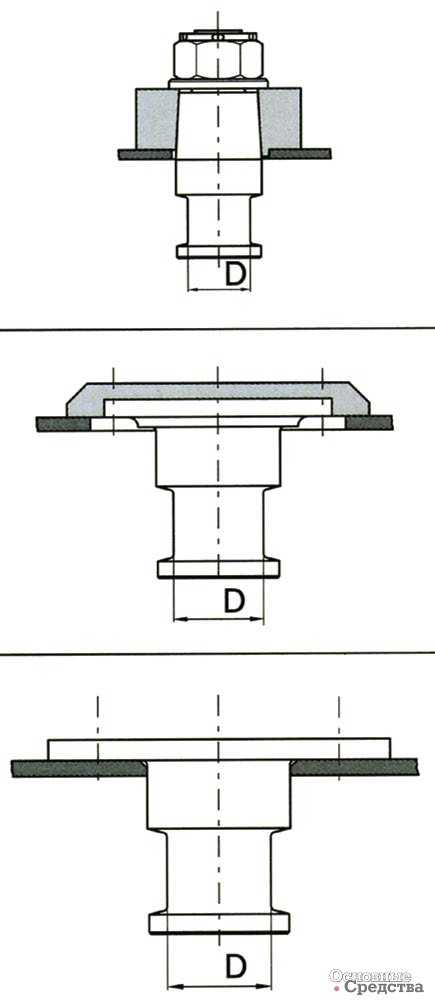
Π‘ΡΠ΅ΠΏΠ½ΠΎΠΉ ΡΠΊΠ²ΠΎΡΠ΅Π½Ρ ΠΊΡΠ΅ΠΏΡΡ Π½Π° ΠΏΠΎΠ»ΡΠΏΡΠΈΡΠ΅ΠΏΠ΅ ΠΌΠ΅ΠΆΠ΄Ρ Π΅Π³ΠΎ ΠΏΠ΅ΡΠ΅Π΄Π½Π΅ΠΉ ΡΡΠ΅Π½ΠΊΠΎΠΉ ΠΈ ΠΎΠΏΠΎΡΠ½ΡΠΌΠΈ ΡΡΡΡΠΎΠΉΡΡΠ²Π°ΠΌΠΈ. ΠΠ°ΠΈΠ±ΠΎΠ»Π΅Π΅ ΡΠ°ΡΠΏΡΠΎΡΡΡΠ°Π½Π΅Π½Ρ Π΄Π²Π° ΡΠΏΠΎΡΠΎΠ±Π° ΡΡΡΠ°Π½ΠΎΠ²ΠΊΠΈ ΡΡΠ΅ΠΏΠ½ΠΎΠ³ΠΎ ΡΠΊΠ²ΠΎΡΠ½Ρ. Π¨ΠΊΠ²ΠΎΡΠ΅Π½Ρ Ρ ΡΠ»Π°Π½ΡΠ΅ΠΌ ΠΊΡΠ΅ΠΏΡΡ ΠΊ ΠΎΠΏΠΎΡΠ½ΠΎΠΌΡ Π»ΠΈΡΡΡ ΠΏΠΎΠ»ΡΠΏΡΠΈΡΠ΅ΠΏΠ° Π·Π°ΠΊΠ»Π΅ΠΏΠΊΠ°ΠΌΠΈ ΠΈΠ»ΠΈ Π±ΠΎΠ»ΡΠ°ΠΌΠΈ, Π° ΡΠΊΠ²ΠΎΡΠ΅Π½Ρ Π±Π΅Π· ΡΠ»Π°Π½ΡΠ° ΡΠΈΠΊΡΠΈΡΡΡΡ ΠΊΠΎΡΠΎΠ½ΡΠ°ΡΠΎΠΉ Π³Π°ΠΉΠΊΠΎΠΉ ΡΠΎ ΡΠΏΠ»ΠΈΠ½ΡΠΎΠΌ.
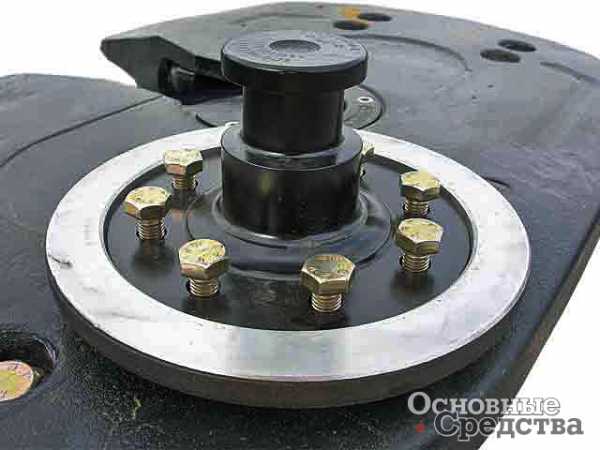
ΠΠ½Π°ΡΠΈΡΠ΅Π»ΡΠ½ΠΎΠ΅ Π²Π½ΠΈΠΌΠ°Π½ΠΈΠ΅ ΡΠ΄Π΅Π»ΡΠ΅ΡΡΡ ΡΠ°ΡΠΏΠΎΠ»ΠΎΠΆΠ΅Π½ΠΈΡ ΡΠ΅Π΄Π΅Π»ΡΠ½ΠΎ-ΡΡΠ΅ΠΏΠ½ΠΎΠ³ΠΎ ΡΡΡΡΠΎΠΉΡΡΠ²Π° ΠΎΡΠ½ΠΎΡΠΈΡΠ΅Π»ΡΠ½ΠΎ Π·Π°Π΄Π½Π΅ΠΉ ΠΎΡΠΈ ΡΡΠ³Π°ΡΠ° ΠΈΠ»ΠΈ ΠΎΡΠΈ Π±Π°Π»Π°Π½ΡΠΈΡΠ° Π·Π°Π΄Π½Π΅ΠΉ ΡΠ΅Π»Π΅ΠΆΠΊΠΈ (ΡΠΌΠ΅ΡΠ΅Π½ΠΈΡ ΡΡΡΡΠΎΠΉΡΡΠ²Π°), ΡΡΠΎ Π½Π΅ΠΎΠ±Ρ ΠΎΠ΄ΠΈΠΌΠΎ Π΄Π»Ρ ΠΏΠΎΠ»Π½ΠΎΠ³ΠΎ ΠΈΡΠΏΠΎΠ»ΡΠ·ΠΎΠ²Π°Π½ΠΈΡ Π³ΡΡΠ·ΠΎΠΏΠΎΠ΄ΡΠ΅ΠΌΠ½ΠΎΡΡΠΈ ΡΠΈΠ½ ΡΡΠ³Π°ΡΠ°, Π° ΡΠ»Π΅Π΄ΠΎΠ²Π°ΡΠ΅Π»ΡΠ½ΠΎ, ΠΈ Π°Π²ΡΠΎΠΏΠΎΠ΅Π·Π΄Π°. ΠΠ°Π½Π½ΠΎΠ΅ ΠΎΠ±ΡΡΠΎΡΡΠ΅Π»ΡΡΡΠ²ΠΎ ΠΎΡΠΎΠ±Π΅Π½Π½ΠΎ Π°ΠΊΡΡΠ°Π»ΡΠ½ΠΎ Π΄Π»Ρ ΠΎΠΏΡΠΈΠΌΠ°Π»ΡΠ½ΠΎΠ³ΠΎ ΡΠ°ΡΠΏΡΠ΅Π΄Π΅Π»Π΅Π½ΠΈΡ Π½Π°Π³ΡΡΠ·ΠΎΠΊ ΠΏΠΎ ΠΎΡΡΠΌ Π½Π°ΠΈΠ±ΠΎΠ»Π΅Π΅ ΡΠ°ΡΠΏΡΠΎΡΡΡΠ°Π½Π΅Π½Π½ΡΡ Π² ΡΠΊΡΠΏΠ»ΡΠ°ΡΠ°ΡΠΈΠΈ ΡΡΠ΅Ρ -, ΡΠ΅ΡΡΡΠ΅Ρ -, ΠΏΡΡΠΈ- ΠΈ ΡΠ΅ΡΡΠΈΠΎΡΠ½ΡΡ ΡΠ΅Π΄Π΅Π»ΡΠ½ΡΡ Π°Π²ΡΠΎΠΏΠΎΠ΅Π·Π΄ΠΎΠ² Ρ ΡΡΠ΅ΡΠΎΠΌ ΡΡΠ΅Π±ΠΎΠ²Π°Π½ΠΈΠΉ Π΄ΠΎΡΠΎΠΆΠ½ΠΎΠ³ΠΎ Π·Π°ΠΊΠΎΠ½ΠΎΠ΄Π°ΡΠ΅Π»ΡΡΡΠ²Π° ΡΠΎΠΉ ΠΈΠ»ΠΈ ΠΈΠ½ΠΎΠΉ ΡΡΡΠ°Π½Ρ, Π²ΠΎ ΠΌΠ½ΠΎΠ³ΠΈΡ ΠΈΠ· ΠΊΠΎΡΠΎΡΡΡ Π½Π°Π³ΡΡΠ·ΠΊΠΈ Π½Π° ΠΎΡΠΈ Π°Π²ΡΠΎΠΌΠΎΠ±ΠΈΠ»Π΅ΠΉ ΠΈ ΠΏΡΠΈΡΠ΅ΠΏΠ½ΠΎΠ³ΠΎ ΡΠΎΡΡΠ°Π²Π° ΠΌΠΎΠ³ΡΡ Π±ΡΡΡ ΡΠ°Π·Π½ΡΠΌΠΈ. ΠΡΠΊΠ»ΡΡΠ΅Π½ΠΈΠ΅ΠΌ ΡΠ²Π»ΡΡΡΡΡ Π½Π΅ΠΊΠΎΡΠΎΡΡΠ΅ ΠΌΠΎΠ΄Π΅Π»ΠΈ Π°Π²ΡΠΎΠ²ΠΎΠ·ΠΎΠ², Π³Π΄Π΅ Π‘Π‘Π£, ΠΈΡΠΏΡΡΡΠ²Π°ΡΡΠ΅Π΅ Π½Π΅Π·Π½Π°ΡΠΈΡΠ΅Π»ΡΠ½ΡΡ Π²Π΅ΡΡΠΈΠΊΠ°Π»ΡΠ½ΡΡ Π½Π°Π³ΡΡΠ·ΠΊΡ, Π΄Π»Ρ ΡΠ°Π·ΠΌΠ΅ΡΠ΅Π½ΠΈΡ Π½Π°Π΄ΡΡΡΠΎΠΉΠΊΠΈ ΡΠΌΠ΅ΡΠ΅Π½ΠΎ Π½Π° ΡΠ°ΠΌΡΠΉ ΠΊΠΎΠ½Π΅Ρ ΡΠ°ΠΌΡ ΡΡΠ³Π°ΡΠ°.
ΠΠ»Π΅ΠΌΠ΅Π½ΡΡ Π‘Π‘Π£
Π Π°Π·ΡΠ΅ΠΌΠ½ΠΎ-ΡΡΠ΅ΠΏΠ½ΠΎΠΉ ΠΌΠ΅Ρ Π°Π½ΠΈΠ·ΠΌ ΠΏΡΠ΅Π΄Π½Π°Π·Π½Π°ΡΠ΅Π½ Π΄Π»Ρ ΠΏΠ΅ΡΠ΅Π΄Π°ΡΠΈ ΡΡΠΈΠ»ΠΈΠΉ ΠΌΠ΅ΠΆΠ΄Ρ Π·Π²Π΅Π½ΡΡΠΌΠΈ Π°Π²ΡΠΎΠΏΠΎΠ΅Π·Π΄Π° ΠΈ ΠΎΠ±Π΅ΡΠΏΠ΅ΡΠΈΠ²Π°Π΅Ρ Π²ΠΎΠ·ΠΌΠΎΠΆΠ½ΠΎΡΡΡ ΠΏΠΎΠ²ΠΎΡΠΎΡΠ° ΠΏΠΎΠ»ΡΠΏΡΠΈΡΠ΅ΠΏΠ° ΠΏΠΎ ΠΎΡΠ½ΠΎΡΠ΅Π½ΠΈΡ ΠΊ ΡΡΠ³Π°ΡΡ Π²ΠΎΠΊΡΡΠ³ ΠΎΡΠΈ ΡΡΠ΅ΠΏΠ½ΠΎΠ³ΠΎ ΡΠΊΠ²ΠΎΡΠ½Ρ Π² Π³ΠΎΡΠΈΠ·ΠΎΠ½ΡΠ°Π»ΡΠ½ΠΎΠΉ ΠΏΠ»ΠΎΡΠΊΠΎΡΡΠΈ.
Π Π°Π·ΡΠ΅ΠΌΠ½ΠΎ-ΡΡΠ΅ΠΏΠ½ΡΠ΅ ΠΌΠ΅Ρ Π°Π½ΠΈΠ·ΠΌΡ ΠΏΠΎΠ΄ΡΠ°Π·Π΄Π΅Π»ΡΡΡΡΡ Π½Π° ΠΏΠΎΠ»ΡΠ°Π²ΡΠΎΠΌΠ°ΡΠΈΡΠ΅ΡΠΊΠΈΠ΅ ΠΈ Π°Π²ΡΠΎΠΌΠ°ΡΠΈΡΠ΅ΡΠΊΠΈΠ΅, Π° ΠΏΠΎ ΡΠΈΡΠ»Ρ Π·Π°Ρ Π²Π°ΡΠΎΠ² β Π½Π° ΠΎΠ΄Π½ΠΎ- ΠΈ Π΄Π²ΡΡ Π·Π°Ρ Π²Π°ΡΠ½ΡΠ΅. ΠΠΎΠ»ΡΡΠ΅ ΡΠ°ΡΠΏΡΠΎΡΡΡΠ°Π½Π΅Π½Ρ Π‘Π‘Π£ Ρ ΠΎΠ΄Π½ΠΎΠ·Π°Ρ Π²Π°ΡΠ½ΡΠΌΠΈ ΡΠ°Π·ΡΠ΅ΠΌΠ½ΠΎ-ΡΡΠ΅ΠΏΠ½ΡΠΌΠΈ ΠΌΠ΅Ρ Π°Π½ΠΈΠ·ΠΌΠ°ΠΌΠΈ. ΠΎΠ½ΠΈ Π±ΠΎΠ»Π΅Π΅ Π½Π°Π΄Π΅ΠΆΠ½Ρ ΠΏΠΎ ΡΡΠ°Π²Π½Π΅Π½ΠΈΡ Ρ Π΄Π²ΡΡ Π·Π°Ρ Π²Π°ΡΠ½ΡΠΌΠΈ ΠΈ ΠΎΡΠ»ΠΈΡΠ°ΡΡΡΡ Π±Π΅Π·ΠΎΠΏΠ°ΡΠ½ΠΎΡΡΡΡ ΠΊΠΎΠ½ΡΡΡΡΠΊΡΠΈΠΈ. Π Π΄Π²ΡΡ Π·Π°Ρ Π²Π°ΡΠ½ΠΎΠΌ ΠΌΠ΅Ρ Π°Π½ΠΈΠ·ΠΌΠ΅ ΡΡΠ³ΠΎΠ²ΡΠ΅ ΠΈ ΡΠΎΡΠΌΠΎΠ·Π½ΡΠ΅ ΡΡΠΈΠ»ΠΈΡ Π²ΠΎΡΠΏΡΠΈΠ½ΠΈΠΌΠ°ΡΡΡΡ ΡΠΎΠ»ΡΠΊΠΎ Π·Π°Ρ Π²Π°ΡΠ°ΠΌΠΈ ΠΈ ΠΏΠ°Π»ΡΡΠ°ΠΌΠΈ, ΡΠΎΠ³Π΄Π° ΠΊΠ°ΠΊ Π² ΠΎΠ΄Π½ΠΎΠ·Π°Ρ Π²Π°ΡΠ½ΠΎΠΉ (Ρ Π·Π°Ρ Π²Π°ΡΠΎΠΌ ΡΠΊΠ²ΠΎΡΠ½Ρ ΠΏΠΎ Π΅Π³ΠΎ Π²Π΅ΡΡ Π½Π΅ΠΌΡ ΠΏΠΎΡΡΡ Ρ Π±ΠΎΠ»ΡΡΠΈΠΌ Π΄ΠΈΠ°ΠΌΠ΅ΡΡΠΎΠΌ) ΡΡΠ³ΠΎΠ²ΡΠ΅ ΡΡΠΈΠ»ΠΈΡ ΠΏΠ΅ΡΠ΅Π΄Π°ΡΡΡΡ Π½Π° ΠΌΠ°ΡΡΠΈΠ²Π½ΡΠΉ Π·Π°ΠΏΠΎΡΠ½ΡΠΉ ΠΊΡΠ»Π°ΠΊ, ΠΏΡΠΈ ΡΡΠΎΠΌ Π·Π°Ρ Π²Π°Ρ ΠΏΠΎΠ΄Π²Π΅ΡΠ³Π°Π΅ΡΡΡ ΡΠΎΠ»ΡΠΊΠΎ ΡΠΆΠΈΠΌΠ°ΡΡΠΈΠΌ ΡΡΠΈΠ»ΠΈΡΠΌ. Π’ΠΎΡΠΌΠΎΠ·Π½ΡΠ΅ ΡΡΠΈΠ»ΠΈΡ ΠΏΠ΅ΡΠ΅Π΄Π°ΡΡΡΡ Π½Π΅ΠΏΠΎΡΡΠ΅Π΄ΡΡΠ²Π΅Π½Π½ΠΎ ΠΎΠΏΠΎΡΠ½ΠΎΠΉ ΠΏΠ»ΠΈΡΠΎΠΉ, ΠΏΡΠΈ ΡΡΠΎΠΌ ΠΏΠ°Π»Π΅Ρ Π·Π°Ρ Π²Π°ΡΠ° ΡΠ°Π·Π³ΡΡΠΆΠ΅Π½ ΠΎΡ ΠΏΡΠΎΠ΄ΠΎΠ»ΡΠ½ΡΡ ΡΡΠΈΠ»ΠΈΠΉ. ΠΠ»Π°Π³ΠΎΠ΄Π°ΡΡ Π·Π°Ρ Π²Π°ΡΡ ΡΠΊΠ²ΠΎΡΠ½Ρ ΠΏΠΎ Π²Π΅ΡΡ Π½Π΅ΠΌΡ ΠΏΠΎΡΡΡ ΡΠΌΠ΅Π½ΡΡΠ°ΡΡΡΡ ΠΈΠ·Π³ΠΈΠ±Π°ΡΡΠΈΠ΅ ΠΌΠΎΠΌΠ΅Π½ΡΡ, Π΄Π΅ΠΉΡΡΠ²ΡΡΡΠΈΠ΅ Π½Π° ΡΠΊΠ²ΠΎΡΠ΅Π½Ρ ΠΈ Π΅Π³ΠΎ ΠΊΡΠ΅ΠΏΠ»Π΅Π½ΠΈΠ΅.
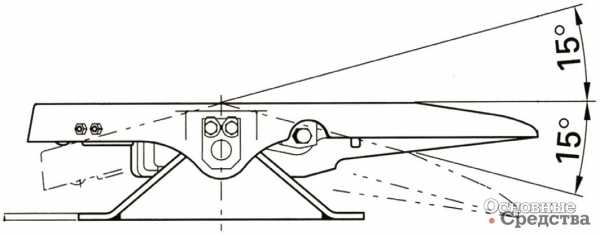
ΠΠΏΠΎΡΠ½ΡΠ΅ ΠΏΠ»ΠΈΡΡ Π‘Π‘Π£ Π²ΡΠΏΠΎΠ»Π½ΡΡΡ Π»ΠΈΠ±ΠΎ Π»ΠΈΡΡΠΌΠΈ, Π»ΠΈΠ±ΠΎ ΡΡΠ°ΠΌΠΏΠΎΡΠ²Π°ΡΠ½ΡΠΌΠΈ. ΠΠΈΡΡΠ΅ ΠΊΠΎΠ½ΡΡΡΡΠΊΡΠΈΠΈ, ΠΎΡΠΎΠ±Π΅Π½Π½ΠΎ ΠΈΠ· ΡΡΠ³ΡΠ½Π° Ρ ΡΠ°ΡΠΎΠ²ΠΈΠ΄Π½ΡΠΌ Π³ΡΠ°ΡΠΈΡΠΎΠΌ, ΠΎΠ±Π»Π°Π΄Π°Ρ Π²ΡΡΠΎΠΊΠΎΠΉ ΠΆΠ΅ΡΡΠΊΠΎΡΡΡΡ ΠΈ ΠΌΠ°Π»ΠΎΠΉ ΠΌΠ°ΡΡΠΎΠΉ, ΡΠ°ΡΠΏΡΠΎΡΡΡΠ°Π½Π΅Π½Ρ ΡΠΈΡΠ΅. ΠΠ»Ρ ΡΠΎΠ²ΡΠ΅ΠΌΠ΅Π½Π½ΡΡ ΡΠ΅Π΄Π΅Π»ΡΠ½ΡΡ ΠΏΠ»ΠΈΡ Ρ Π°ΡΠ°ΠΊΡΠ΅ΡΠ½Ρ ΠΌΠ°ΠΊΡΠΈΠΌΠ°Π»ΡΠ½Π°Ρ ΡΠΈΡΠΈΠ½Π° ΡΡΡΡΡ 400β¦460 ΠΌΠΌ, ΡΠ³ΠΎΠ» ΡΡΡΡΡ 40β¦50Β°, ΡΠ³ΠΎΠ» ΡΠΊΠΎΡΠ° 8β¦15Β°. Π ΡΠΊΠΎΡΡΠΊΠ° ΠΏΡΠΈΠ²ΠΎΠ΄Π° ΡΠ°Π·ΡΠ΅ΠΌΠ½ΠΎ-ΡΡΠ΅ΠΏΠ½ΠΎΠ³ΠΎ ΠΌΠ΅Ρ Π°Π½ΠΈΠ·ΠΌΠ° ΡΠ°ΡΠΏΠΎΠ»ΠΎΠΆΠ΅Π½Π° ΡΠΏΡΠ°Π²Π° ΠΎΡ ΡΠ΅Π΄Π΅Π»ΡΠ½ΠΎ-ΡΡΠ΅ΠΏΠ½ΠΎΠ³ΠΎ ΡΡΡΡΠΎΠΉΡΡΠ²Π°. ΠΠ΅ ΡΡΠ³Π° Π΄Π»Ρ ΡΠ΄ΠΎΠ±ΡΡΠ²Π° Π²ΠΎΠ΄ΠΈΡΠ΅Π»Ρ ΠΌΠΎΠΆΠ΅Ρ Π±ΡΡΡ Π²ΡΠΏΠΎΠ»Π½Π΅Π½Π° ΡΠ°Π·Π½ΠΎΠΉ Π΄Π»ΠΈΠ½Ρ. ΠΠ»Ρ ΡΠ°Π±ΠΎΡΡ Ρ ΡΠ°Π·Π½ΡΠΌΠΈ ΠΏΠΎΠ»ΡΠΏΡΠΈΡΠ΅ΠΏΠ°ΠΌΠΈ Π² ΡΠΎΠ²ΡΠ΅ΠΌΠ΅Π½Π½ΡΡ Π‘Π‘Π£ ΠΏΡΠ΅Π΄ΡΡΠΌΠΎΡΡΠ΅Π½Π° Π²ΠΎΠ·ΠΌΠΎΠΆΠ½ΠΎΡΡΡ ΡΡΡΠ°Π½ΠΎΠ²ΠΊΠΈ Π² ΠΎΠ΄Π½ΠΎΠΉ ΠΈ ΡΠΎΠΉ ΠΆΠ΅ ΠΎΠΏΠΎΡΠ½ΠΎΠΉ ΠΏΠ»ΠΈΡΠ΅ ΡΠΊΠ²ΠΎΡΠ½Π΅ΠΉ Π΄ΠΈΠ°ΠΌΠ΅ΡΡΠΎΠΌ 2 ΠΈΠ»ΠΈ 3,5 Π΄ΡΠΉΠΌΠ°. Π‘ΡΠ΅ΠΏΠ½ΡΠ΅ ΡΠΊΠ²ΠΎΡΠ½ΠΈ ΠΈΠ·Π³ΠΎΡΠ°Π²Π»ΠΈΠ²Π°ΡΡ ΠΈΠ· Π²ΡΡΠΎΠΊΠΎΠΏΡΠΎΡΠ½ΠΎΠΉ ΡΡΠ°Π»ΠΈ, ΠΏΠΎΡΠ»Π΅ ΡΠ΅Π³ΠΎ ΠΏΠΎΠ΄Π²Π΅ΡΠ³Π°ΡΡ ΡΠΏΠ΅ΡΠΈΠ°Π»ΡΠ½ΠΎΠΉ ΡΠ΅ΡΠΌΠΎΠΎΠ±ΡΠ°Π±ΠΎΡΠΊΠ΅ (Π·Π°ΠΊΠ°Π»ΠΊΠ΅) ΠΈ ΡΡΠ°ΡΠ΅Π»ΡΠ½ΠΎ ΠΏΡΠΎΠ²Π΅ΡΡΡΡ Π½Π° ΠΎΡΡΡΡΡΡΠ²ΠΈΠ΅ ΡΡΠ΅ΡΠΈΠ½.
Π‘Π‘Π£ ΡΡΡΠ°Π½Π°Π²Π»ΠΈΠ²Π°ΡΡ Π½Π° ΡΠ°ΠΌΡ ΡΡΠ³Π°ΡΠ° Ρ ΠΏΠΎΠΌΠΎΡΡΡ ΡΠ³ΠΎΠ»ΠΊΠΎΠ²ΡΡ ΠΊΡΠ΅ΠΏΠ΅ΠΆΠ½ΡΡ ΡΠ»Π΅ΠΌΠ΅Π½ΡΠΎΠ² ΠΈΠ»ΠΈ ΠΏΠΎΡΡΠ΅Π΄ΡΡΠ²ΠΎΠΌ ΠΌΠΎΠ½ΡΠ°ΠΆΠ½ΡΡ ΠΏΠ»ΠΈΡ, ΠΈΠΌΠ΅ΡΡΠΈΡ ΡΠ°Π·Π»ΠΈΡΠ½ΡΡ ΠΊΠΎΠ½ΡΠΈΠ³ΡΡΠ°ΡΠΈΡ: ΠΎΡ ΠΏΠ»ΠΎΡΠΊΠΎΠΉ ΠΏΠ»Π°ΡΡΠΈΠ½Ρ Π΄ΠΎ ΠΏΡΠΎΡΡΡΠ°Π½ΡΡΠ²Π΅Π½Π½ΠΎΠΉ ΠΊΠΎΠ½ΡΡΡΡΠΊΡΠΈΠΈ Π²ΡΡΠΎΡΠΎΠΉ Π΄ΠΎ 150 ΠΌΠΌ. Π‘ΡΠΎΠΊ ΡΠ»ΡΠΆΠ±Ρ ΡΠΎΠ²ΡΠ΅ΠΌΠ΅Π½Π½ΡΡ Π‘Π‘Π£ ΡΠΊΠ²ΠΎΡΠ½Π΅Π²ΠΎΠ³ΠΎ ΡΠΈΠΏΠ° Π΄ΠΎΡΡΠΈΠ³Π°Π΅Ρ 1,5β¦2 ΠΌΠ»Π½. ΠΊΠΌ, Ρ. Π΅. ΠΏΡΠΈΠΌΠ΅ΡΠ½ΠΎ ΡΡΠΎΠ»ΡΠΊΠΎ, ΡΠΊΠΎΠ»ΡΠΊΠΎ Π½Π°Ρ ΠΎΠ΄ΠΈΡΡΡ Π² ΡΠΊΡΠΏΠ»ΡΠ°ΡΠ°ΡΠΈΠΈ ΡΡΠ³Π°Ρ.
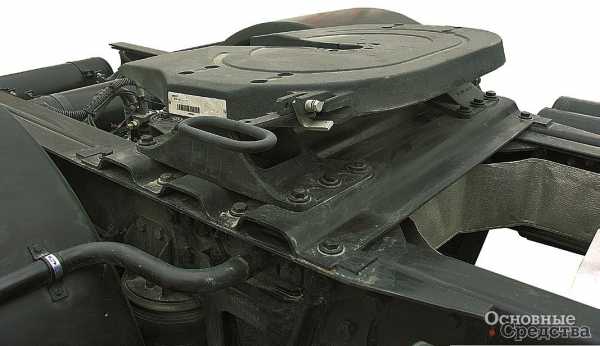
ΠΠΎΡΠΌΠ°ΡΠΈΠ²Π½ΡΠ΅ Π΄ΠΎΠΊΡΠΌΠ΅Π½ΡΡ
Π Π°Π·ΠΌΠ΅ΡΡ ΡΡΠ΅ΠΏΠ½ΡΡ ΡΠΊΠ²ΠΎΡΠ½Π΅ΠΉ ΡΠ΅Π³Π»Π°ΠΌΠ΅Π½ΡΠΈΡΠΎΠ²Π°Π½Ρ. ΠΠΈΠ°ΠΌΠ΅ΡΡ ΡΠΎΠΏΡΡΠ³Π°Π΅ΠΌΠΎΠΉ ΠΏΠΎΠ²Π΅ΡΡ Π½ΠΎΡΡΠΈ ΡΠΊΠ²ΠΎΡΠ½Ρ Π΄ΠΎΠ»ΠΆΠ΅Π½ Π±ΡΡΡ ΡΠ°Π²Π΅Π½ 2 ΠΈΠ»ΠΈ 3,5 Π΄ΡΠΉΠΌΠ° (50,8 ΠΈΠ»ΠΈ 89 ΠΌΠΌ). ΠΡΠ±ΠΎΡ ΠΎΠ΄Π½ΠΎΠ³ΠΎ ΠΈΠ· ΡΡΠΈΡ Π΄Π²ΡΡ ΡΠΈΠΏΠΎΠ² (50 ΠΈΠ»ΠΈ 90) Π·Π°Π²ΠΈΡΠΈΡ ΠΎΡ ΠΏΠΎΠ»Π½ΠΎΠΉ ΠΌΠ°ΡΡΡ Π°Π²ΡΠΎΠΏΠΎΠ΅Π·Π΄Π°, ΠΏΠΎΠ»ΡΠΏΡΠΈΡΠ΅ΠΏΠ° ΠΈ Π²Π΅ΡΡΠΈΠΊΠ°Π»ΡΠ½ΠΎΠΉ Π½Π°Π³ΡΡΠ·ΠΊΠΈ. Π¨ΠΊΠ²ΠΎΡΠ½ΠΈ Γ50,8 ΠΌΠΌ ΡΡΡΠ°Π½Π°Π²Π»ΠΈΠ²Π°ΡΡ Π½Π° ΠΏΠΎΠ»ΡΠΏΡΠΈΡΠ΅ΠΏΡ ΠΏΠΎΠ»Π½ΠΎΠΉ ΠΌΠ°ΡΡΠΎΠΉ Π΄ΠΎ 55 Ρ ΠΈΠ»ΠΈ ΠΏΡΠΈ Π²Π΅ΡΡΠΈΠΊΠ°Π»ΡΠ½ΠΎΠΉ Π½Π°Π³ΡΡΠ·ΠΊΠ΅ Π½Π° Π‘Π‘Π£ Π΄ΠΎ 200 ΠΊΠ. ΠΡΠΈ Π±ΠΎΠ»ΡΡΠΎΠΉ ΠΌΠ°ΡΡΠ΅ (Π½Π°Π³ΡΡΠ·ΠΊΠ΅) ΠΏΡΠΈΠΌΠ΅Π½ΡΡΡ ΡΡΠ΅ΠΏΠ½ΡΠ΅ ΡΠΊΠ²ΠΎΡΠ½ΠΈ Γ89 ΠΌΠΌ. Π Π°Π·ΠΌΠ΅ΡΡ ΡΡΠ΅ΠΏΠ½ΡΡ ΡΠΊΠ²ΠΎΡΠ½Π΅ΠΉ ΡΠΏΠΎΡΡΠ΄ΠΎΡΠ΅Π½Ρ ΠΊΠ°ΠΊ Π½Π°ΡΠΈΠΎΠ½Π°Π»ΡΠ½ΡΠΌΠΈ ΡΡΠ°Π½Π΄Π°ΡΡΠ°ΠΌΠΈ, ΡΠ°ΠΊ ΠΈ ΠΠ΅ΠΆΠ΄ΡΠ½Π°ΡΠΎΠ΄Π½ΠΎΠΉ ΠΎΡΠ³Π°Π½ΠΈΠ·Π°ΡΠΈΠ΅ΠΉ ΠΏΠΎ ΡΡΠ°Π½Π΄Π°ΡΡΠΈΠ·Π°ΡΠΈΠΈ ISΠ. Π Π ΠΎΡΡΠΈΠΈ ΠΏΠΎΠΌΠΈΠΌΠΎ ΡΠΏΠΎΠΌΡΠ½ΡΡΡΡ Π΄ΠΎΠΏΡΡΠΊΠ°Π΅ΡΡΡ ΠΈΡΠΏΠΎΠ»ΡΠ·ΠΎΠ²Π°Π½ΠΈΠ΅ ΡΠΊΠ²ΠΎΡΠ½Π΅ΠΉ Ρ Π΄ΠΈΠ°ΠΌΠ΅ΡΡΠΎΠΌ ΡΠΎΠΏΡΡΠ³Π°Π΅ΠΌΠΎΠΉ ΠΏΠΎΠ²Π΅ΡΡ Π½ΠΎΡΡΠΈ 100 ΠΌΠΌ. ΠΡΡΠΎΡΠ° ΡΠ΅Π΄Π»Π° Π΄Π»Ρ Π‘Π‘Π£ ΡΠΈΠΏΠ° 50 Π½Π΅ Π΄ΠΎΠ»ΠΆΠ½Π° ΠΏΡΠ΅Π²ΡΡΠ°ΡΡ 200 ΠΌΠΌ, Π° Π΄Π»Ρ Π‘Π‘Π£ ΡΠΈΠΏΠ° 90 β 315 ΠΌΠΌ.
Π ΡΡΠ΄Π΅ ΡΡΡΠ°Π½ Π΅ΡΡΡ ΡΡΠ°Π½Π΄Π°ΡΡΡ Π½Π° Π‘Π‘Π£, ΠΎΠ³ΠΎΠ²Π°ΡΠΈΠ²Π°ΡΡΠΈΠ΅ ΠΏΡΠΈΡΠΎΠ΅Π΄ΠΈΠ½ΠΈΡΠ΅Π»ΡΠ½ΡΠ΅ ΡΠ°Π·ΠΌΠ΅ΡΡ Π΄Π»Ρ ΠΊΡΠ΅ΠΏΠ»Π΅Π½ΠΈΡ ΠΊ ΡΠ°ΠΌΠ΅ ΡΡΠ³Π°ΡΠ°. ΠΠ»Ρ Π‘Π‘Π£, ΡΠ°Π±ΠΎΡΠ°ΡΡΠΈΡ Π² ΡΡΠ΅ΠΏΠΊΠ΅ Ρ ΠΏΠΎΠ»ΡΠΏΡΠΈΡΠ΅ΠΏΠ°ΠΌΠΈ, ΡΡΠ΅ΠΏΠ½ΠΎΠΉ ΡΠΊΠ²ΠΎΡΠ΅Π½Ρ ΠΊΠΎΡΠΎΡΡΡ Π²ΡΠΏΠΎΠ»Π½Π΅Π½ ΠΏΠΎ ΠΌΠ΅ΠΆΠ΄ΡΠ½Π°ΡΠΎΠ΄Π½ΠΎΠΌΡ ΡΡΠ°Π½Π΄Π°ΡΡΡ ISΠ 337, ΡΡΡΠ΅ΡΡΠ²ΡΠ΅Ρ ΠΌΠ΅ΠΆΠ΄ΡΠ½Π°ΡΠΎΠ΄Π½ΡΠΉ ΡΡΠ°Π½Π΄Π°ΡΡ ISΠ 3842, ΡΡΡΠ°Π½Π°Π²Π»ΠΈΠ²Π°ΡΡΠΈΠΉ ΡΠΈΡΠ»ΠΎ, Π΄ΠΈΠ°ΠΌΠ΅ΡΡ ΠΈ Π²Π·Π°ΠΈΠΌΠ½ΠΎΠ΅ ΡΠ°ΡΠΏΠΎΠ»ΠΎΠΆΠ΅Π½ΠΈΠ΅ ΠΎΡΠ²Π΅ΡΡΡΠΈΠΉ Π΄Π»Ρ ΠΊΡΠ΅ΠΏΠ»Π΅Π½ΠΈΡ Π‘Π‘Π£ Π½Π° ΡΡΠ³Π°ΡΠ°Ρ .
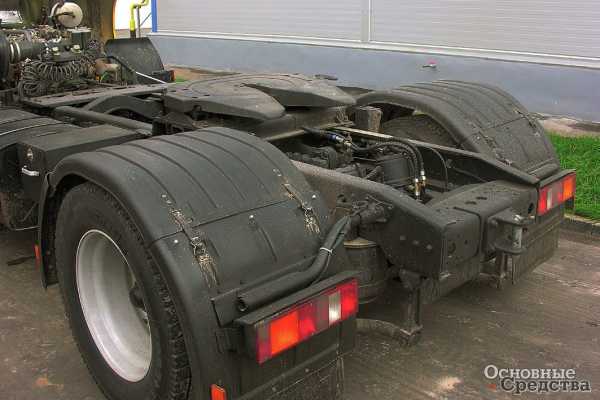
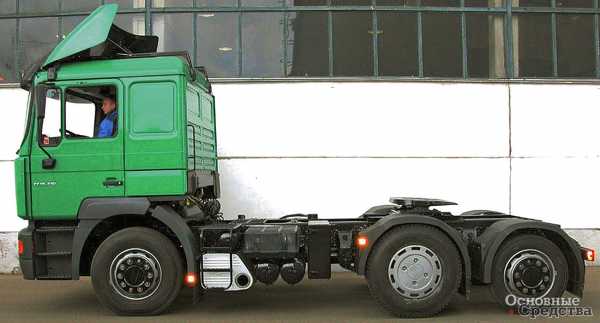
Π ΡΡΡΠ°Π½Π°Ρ ΠΠ²ΡΠΎΡΠΎΡΠ·Π° ΡΠΈΠΏ ΠΏΡΠΈΠΌΠ΅Π½ΡΠ΅ΠΌΡΡ Π‘Π‘Π£ ΠΎΠΏΡΠ΅Π΄Π΅Π»ΡΠ΅ΡΡΡ ΡΠ°ΡΡΠ΅ΡΠ½ΡΠΌ ΠΊΠΎΡΡΡΠΈΡΠΈΠ΅Π½ΡΠΎΠΌ Π½Π°Π³ΡΡΠ·ΠΊΠΈ D. ΠΠ³ΠΎ Π·Π½Π°ΡΠ΅Π½ΠΈΠ΅ Π΄Π»Ρ Π‘Π‘Π£ Π°Π²ΡΠΎΠΏΠΎΠ΅Π·Π΄ΠΎΠ², ΡΠΊΡΠΏΠ»ΡΠ°ΡΠΈΡΡΡΡΠΈΡ ΡΡ Π½Π° Π΄ΠΎΡΠΎΠ³Π°Ρ ΠΎΠ±ΡΠ΅Π³ΠΎ ΠΏΠΎΠ»ΡΠ·ΠΎΠ²Π°Π½ΠΈΡ, ΡΠΎΡΡΠ°Π²Π»ΡΠ΅Ρ Π½Π΅ Π±ΠΎΠ»Π΅Π΅ 162 ΠΊΠ. ΠΠΎΠΊΠ°Π·Π°ΡΠ΅Π»Ρ D Π΄Π»Ρ ΡΠ΅Π΄Π΅Π»ΡΠ½ΡΡ ΡΡΡΡΠΎΠΉΡΡΠ² Π±ΠΎΠ»ΡΡΠΎΠΉ Π³ΡΡΠ·ΠΎΠΏΠΎΠ΄ΡΠ΅ΠΌΠ½ΠΎΡΡΠΈ ΠΌΠΎΠΆΠ΅Ρ Π΄ΠΎΡΡΠΈΠ³Π°ΡΡ 300 ΠΊΠ. ΠΠ°ΠΆΠ½ΠΎΠΉ Ρ Π°ΡΠ°ΠΊΡΠ΅ΡΠΈΡΡΠΈΠΊΠΎΠΉ ΠΊΠΎΠ½ΠΊΡΠ΅ΡΠ½ΠΎΠΉ ΠΌΠΎΠ΄Π΅Π»ΠΈ Π‘Π‘Π£ ΡΠ²Π»ΡΡΡΡΡ ΡΠ°Π·ΠΌΠ΅ΡΡ ΠΏΠ»ΠΎΡΠ°Π΄ΠΈ (ΡΠΈΡΠΈΠ½Ρ) ΠΎΠΏΠΎΡΠ½ΠΎΠΉ ΠΏΠΎΠ²Π΅ΡΡ Π½ΠΎΡΡΠΈ ΡΠ΅Π΄Π΅Π»ΡΠ½ΠΎΠΉ ΠΏΠ»ΠΈΡΡ (24, 34, 36 ΠΈ 40 Π΄ΡΠΉΠΌΠΎΠ²).
Π‘ΡΠ°Π½Π΄Π°ΡΡΡ ΡΠ΅Π»ΠΎΠΉ Π³ΡΡΠΏΠΏΡ Π³ΠΎΡΡΠ΄Π°ΡΡΡΠ², ΠΊΡΠΎΠΌΠ΅ ΡΠΎΠ³ΠΎ, ΡΡΡΠ°Π½Π°Π²Π»ΠΈΠ²Π°ΡΡ ΡΠ³Π»Ρ Π½Π°ΠΊΠ»ΠΎΠ½Π° ΠΎΠΏΠΎΡΠ½ΠΎΠΉ ΠΏΠ»ΠΈΡΡ ΡΠ΅Π΄Π΅Π»ΡΠ½ΠΎ-ΡΡΠ΅ΠΏΠ½ΠΎΠ³ΠΎ ΡΡΡΡΠΎΠΉΡΡΠ²Π° Π²ΠΏΠ΅ΡΠ΅Π΄-Π½Π°Π·Π°Π΄ Π² Π²Π΅ΡΡΠΈΠΊΠ°Π»ΡΠ½ΠΎΠΉ ΠΏΡΠΎΠ΄ΠΎΠ»ΡΠ½ΠΎΠΉ ΠΏΠ»ΠΎΡΠΊΠΎΡΡΠΈ (ΡΠ³Π»Ρ Ξ²1 ΠΈ Ξ²2) ΠΈ ΡΠ³Π»Ρ Π½Π°ΠΊΠ»ΠΎΠ½Π° ΠΎΠΏΠΎΡΠ½ΠΎΠΉ ΠΏΠ»ΠΈΡΡ Π² ΠΎΠ±Π΅ ΡΡΠΎΡΠΎΠ½Ρ Π² Π²Π΅ΡΡΠΈΠΊΠ°Π»ΡΠ½ΠΎΠΉ ΠΏΠΎΠΏΠ΅ΡΠ΅ΡΠ½ΠΎΠΉ ΠΏΠ»ΠΎΡΠΊΠΎΡΡΠΈ (ΡΠ³Π»Ρ Ξ±). ΠΠΎ Π½ΠΎΡΠΌΠ°ΠΌ, ΠΏΡΠΈΠ½ΡΡΡΠΌ Π² ΠΠ²ΡΠΎΡΠΎΡΠ·Π΅, ΡΠ³Π»Ρ Ξ± Π΄ΠΎΠ»ΠΆΠ½Ρ ΡΠΎΡΡΠ°Π²Π»ΡΡΡ Π½Π΅ ΠΌΠ΅Π½Π΅Π΅ Β±8Β°. ΠΠ΅ΠΆΠ΄ΡΠ½Π°ΡΠΎΠ΄Π½ΡΠΉ ΡΡΠ°Π½Π΄Π°ΡΡ ISΠ 1726, ΡΠ°ΡΠΏΡΠΎΡΡΡΠ°Π½ΡΡΡΠΈΠΉΡΡ Π½Π° ΡΡΠ³Π°ΡΠΈ Ρ ΠΏΠΎΠ»ΡΠΏΡΠΈΡΠ΅ΠΏΠ°ΠΌΠΈ, ΠΏΡΠ΅Π΄Π½Π°Π·Π½Π°ΡΠ΅Π½Π½ΡΠΌΠΈ Π΄Π»Ρ ΠΌΠ΅ΠΆΠ΄ΡΠ½Π°ΡΠΎΠ΄Π½ΡΡ ΠΏΠ΅ΡΠ΅Π²ΠΎΠ·ΠΎΠΊ, ΡΡΡΠ°Π½Π°Π²Π»ΠΈΠ²Π°Π΅Ρ Π²Π΅Π»ΠΈΡΠΈΠ½Ρ ΡΠ³Π»Π° Ξ± Π½Π΅ Π±ΠΎΠ»Π΅Π΅ 3Β°, Π° ΡΠ³Π»Π° Ξ² β Π½Π΅ ΠΌΠ΅Π½Π΅Π΅ 8Β°. ΠΠΎΠ½ΡΡΠ½ΠΎ, ΡΡΠΎ ΠΊΠΎΠΌΠΏΠ°Π½ΠΈΠΈ-ΠΈΠ·Π³ΠΎΡΠΎΠ²ΠΈΡΠ΅Π»ΠΈ ΡΠ²ΠΎΠΈΠΌ ΠΊΠ»ΠΈΠ΅Π½ΡΠ°ΠΌ ΠΏΡΠ΅Π΄Π»Π°Π³Π°ΡΡ Π‘Π‘Π£ Ρ Π±ΠΎΠ»Π΅Π΅ Π²ΡΡΠΎΠΊΠΎΠΉ ΠΏΡΠΎΠ΄ΠΎΠ»ΡΠ½ΠΎΠΉ Π³ΠΈΠ±ΠΊΠΎΡΡΡΡ, ΠΏΠΎΡΡΠΎΠΌΡ Π΄ΠΈΠ°ΠΏΠ°Π·ΠΎΠ½ ΠΈΠ·ΠΌΠ΅Π½Π΅Π½ΠΈΡ ΡΠ³Π»Π° Ξ²1 ΡΠΎΡΡΠ°Π²Π»ΡΠ΅Ρ ΠΎΡ 6,5Β° Π΄ΠΎ 29Β°, ΡΠ³Π»Π° Ξ²2 β ΠΎΡ 7,2Β° Π΄ΠΎ 42Β°.
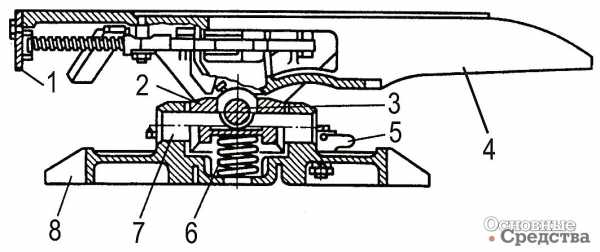
Π ΡΠΈΡΠ»Ρ ΡΡΠ°Π½Π΄Π°ΡΡΠΈΠ·ΠΈΡΡΠ΅ΠΌΡΡ ΡΠ°Π·ΠΌΠ΅ΡΠΎΠ² ΠΎΡΠ½ΠΎΡΡΡΡΡ: ΡΠ°ΡΡΡΠΎΡΠ½ΠΈΠ΅ ΠΎΡ ΠΎΡΠΈ ΠΎΡΠ²Π΅ΡΡΡΠΈΡ Π‘Π‘Π£ ΠΏΠΎΠ΄ ΡΡΠ΅ΠΏΠ½ΠΎΠΉ ΡΠΊΠ²ΠΎΡΠ΅Π½Ρ Π΄ΠΎ Π·Π°Π΄Π½Π΅ΠΉ ΡΡΠ΅Π½ΠΊΠΈ ΠΊΠ°Π±ΠΈΠ½Ρ ΠΈΠ»ΠΈ Π΄ΠΎ ΡΡΡΠ°Π½Π°Π²Π»ΠΈΠ²Π°Π΅ΠΌΡΡ Π·Π° Π½Π΅ΠΉ ΡΠ·Π»ΠΎΠ² ΠΈ Π°Π³ΡΠ΅Π³Π°ΡΠΎΠ² ΡΡΠ³Π°ΡΠ°; ΡΠ°Π΄ΠΈΡΡ Π³Π°Π±Π°ΡΠΈΡΠ° Π·Π°Π΄Π½Π΅ΠΉ ΡΠ°ΡΡΠΈ ΡΡΠ³Π°ΡΠ°; ΡΠ°ΡΡΡΠΎΡΠ½ΠΈΠ΅ ΠΎΡ ΡΡΠ΅ΠΏΠ½ΠΎΠ³ΠΎ ΡΠΊΠ²ΠΎΡΠ½Ρ Π΄ΠΎ Π±Π»ΠΈΠΆΠ°ΠΉΡΠ΅ΠΉ ΡΠ°ΡΡΠΈ ΠΌΠ΅Ρ Π°Π½ΠΈΠ·ΠΌΠ° ΠΎΠΏΠΎΡΠ½ΠΎΠ³ΠΎ ΡΡΡΡΠΎΠΉΡΡΠ²Π° ΠΏΠΎΠ»ΡΠΏΡΠΈΡΠ΅ΠΏΠ°; ΡΠ°Π΄ΠΈΡΡ Π³Π°Π±Π°ΡΠΈΡΠ° ΠΏΠ΅ΡΠ΅Π΄Π½Π΅ΠΉ ΡΠ°ΡΡΠΈ ΠΏΠΎΠ»ΡΠΏΡΠΈΡΠ΅ΠΏΠ°; Π²ΡΡΠΎΡΠ° Π²Π΅ΡΡ Π½Π΅ΠΉ ΠΏΠ»ΠΎΡΠΊΠΎΡΡΠΈ Π‘Π‘Π£ ΡΡΠ³Π°ΡΠ° ΠΏΠΎΠ΄ Π½ΠΎΠΌΠΈΠ½Π°Π»ΡΠ½ΠΎΠΉ Π½Π°Π³ΡΡΠ·ΠΊΠΎΠΉ ΠΎΡ ΡΡΠΎΠ²Π½Ρ Π΄ΠΎΡΠΎΠ³ΠΈ. ΠΡΠ΅ ΡΡΠΈ ΡΠ°Π·ΠΌΠ΅ΡΡ ΠΎΠ³ΠΎΠ²ΠΎΡΠ΅Π½Ρ ΡΠ°ΠΊΠΆΠ΅ ΡΡΠ°Π½Π΄Π°ΡΡΠΎΠΌ ISO 1726. Π¦Π΅Π»ΡΠΉ ΡΡΠ΄ ΠΏΠ°ΡΠ°ΠΌΠ΅ΡΡΠΎΠ² ΡΡΡΠ°Π½Π°Π²Π»ΠΈΠ²Π°Π΅Ρ ΡΡΠ°Π½Π΄Π°ΡΡ ISO 4086.
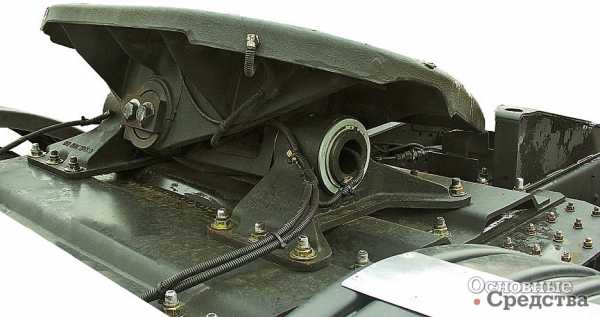
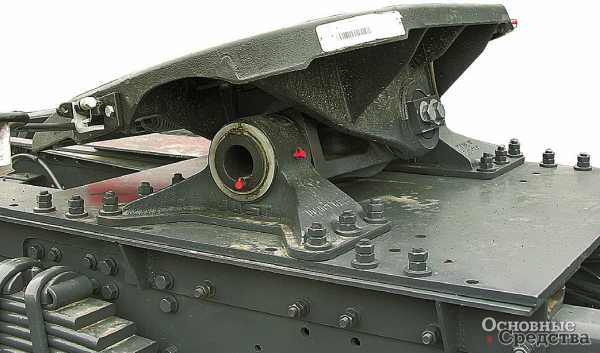
Π£ΡΡΠ°Π½ΠΎΠ²ΠΊΠ° Π‘Π‘Π£ Ρ ΡΡΠ΅ΠΌΡ ΡΡΠ΅ΠΏΠ΅Π½ΡΠΌΠΈ ΡΠ²ΠΎΠ±ΠΎΠ΄Ρ Π½Π° Π±ΠΎΠ»ΡΡΠ΅Π³ΡΡΠ·Π½ΠΎΠΌ ΡΡΠ³Π°ΡΠ΅, Π²ΠΈΠ΄Π½Ρ ΠΏΠΎΠΏΠ΅ΡΠ΅ΡΠ½Π°Ρ ΠΈ ΠΏΡΠΎΠ΄ΠΎΠ»ΡΠ½Π°Ρ ΠΎΡΠΈ ΠΊΠ°ΡΠ°Π½ΠΈΡ
Π‘ΡΠ΅ΠΏΠ΅Π½ΠΈ ΡΠ²ΠΎΠ±ΠΎΠ΄Ρ
ΠΠΎΠ»ΡΠ°Π²ΡΠΎΠΌΠ°ΡΠΈΡΠ΅ΡΠΊΠΈΠ΅ ΡΠΊΠ²ΠΎΡΠ½Π΅Π²ΡΠ΅ ΡΡΠ΅ΠΏΠ½ΡΠ΅ ΡΡΡΡΠΎΠΉΡΡΠ²Π° Π²ΡΠΏΡΡΠΊΠ°ΡΡ Ρ Π΄Π²ΡΠΌΡ ΠΈ ΡΡΠ΅ΠΌΡ ΡΡΠ΅ΠΏΠ΅Π½ΡΠΌΠΈ ΡΠ²ΠΎΠ±ΠΎΠ΄Ρ. Π ΠΏΠ΅ΡΠ²ΠΎΠΌ ΡΠ»ΡΡΠ°Π΅ ΠΎΠ±Π΅ΡΠΏΠ΅ΡΠΈΠ²Π°Π΅ΡΡΡ Π²ΠΎΠ·ΠΌΠΎΠΆΠ½ΠΎΡΡΡ ΠΏΡΠΎΠ΄ΠΎΠ»ΡΠ½ΠΎΠ³ΠΎ ΠΊΠ°ΡΠ°Π½ΠΈΡ ΠΏΠΎΠ»ΡΠΏΡΠΈΡΠ΅ΠΏΠ° ΠΎΡΠ½ΠΎΡΠΈΡΠ΅Π»ΡΠ½ΠΎ ΡΡΠ³Π°ΡΠ° Π½Π° ΠΎΠΏΡΠ΅Π΄Π΅Π»Π΅Π½Π½ΡΠΉ ΡΠ³ΠΎΠ» Ξ² ΠΈ ΠΏΠΎΠ²ΠΎΡΠΎΡ ΠΏΠΎΠ»ΡΠΏΡΠΈΡΠ΅ΠΏΠ° Π²ΠΎΠΊΡΡΠ³ ΠΎΡΠΈ ΡΡΠ΅ΠΏΠ½ΠΎΠ³ΠΎ ΡΠΊΠ²ΠΎΡΠ½Ρ Π² Π³ΠΎΡΠΈΠ·ΠΎΠ½ΡΠ°Π»ΡΠ½ΠΎΠΉ ΠΏΠ»ΠΎΡΠΊΠΎΡΡΠΈ Π½Π° ΡΠ³ΠΎΠ» Π½Π΅ ΠΌΠ΅Π½Π΅Π΅ Β±90Β°. ΠΠΎΠ»ΡΡΠΈΠ½ΡΡΠ²ΠΎ ΡΠ΅Π΄Π΅Π»ΡΠ½ΡΡ ΡΡΠ³Π°ΡΠ΅ΠΉ ΠΎΠ±ΡΠ΅ΡΡΠ°Π½ΡΠΏΠΎΡΡΠ½ΠΎΠ³ΠΎ Π½Π°Π·Π½Π°ΡΠ΅Π½ΠΈΡ, ΡΠΊΡΠΏΠ»ΡΠ°ΡΠΈΡΡΡΡΠΈΠ΅ΡΡ Π² ΠΎΡΠ½ΠΎΠ²Π½ΠΎΠΌ Π½Π° Π΄ΠΎΡΠΎΠ³Π°Ρ Ρ ΡΡΠΎΠ²Π΅ΡΡΠ΅Π½ΡΡΠ²ΠΎΠ²Π°Π½Π½ΡΠΌ ΠΏΠΎΠΊΡΡΡΠΈΠ΅ΠΌ, ΠΎΡΠ½Π°ΡΠ΅Π½ΠΎ Π‘Π‘Π£ Ρ Π΄Π²ΡΠΌΡ ΡΡΠ΅ΠΏΠ΅Π½ΡΠΌΠΈ ΡΠ²ΠΎΠ±ΠΎΠ΄Ρ. ΠΠΎ ΡΡΠ°Π²Π½Π΅Π½ΠΈΡ Ρ ΡΡΠ΅Ρ ΡΡΠ΅ΠΏΠ΅Π½Π½ΡΠΌΠΈ ΡΡΠΈ ΡΡΡΡΠΎΠΉΡΡΠ²Π° ΠΏΠΎΠ²ΡΡΠ°ΡΡ ΡΡΡΠΎΠΉΡΠΈΠ²ΠΎΡΡΡ Π°Π²ΡΠΎΠΏΠΎΠ΅Π·Π΄Π° Π² Π΄Π²ΠΈΠΆΠ΅Π½ΠΈΠΈ, ΠΈΠΌΠ΅ΡΡ ΠΌΠ΅Π½ΡΡΡΡ ΠΌΠ°ΡΡΡ ΠΈ ΠΏΠΎΠ½ΠΈΠΆΠ΅Π½Π½ΡΡ Π³Π°Π±Π°ΡΠΈΡΠ½ΡΡ Π²ΡΡΠΎΡΡ.
Π£ΡΡΡΠΎΠΉΡΡΠ²Π° Ρ ΡΡΠ΅ΠΌΡ ΡΡΠ΅ΠΏΠ΅Π½ΡΠΌΠΈ ΡΠ²ΠΎΠ±ΠΎΠ΄Ρ ΠΎΠ±ΠΎΡΡΠ΄ΠΎΠ²Π°Π½Ρ Π²ΡΠΎΡΠΎΠΉ, Π½ΠΎ ΡΠΆΠ΅ ΠΏΡΠΎΠ΄ΠΎΠ»ΡΠ½ΠΎΠΉ ΠΎΡΡΡ, ΠΊΠΎΡΠΎΡΠ°Ρ Π΄ΠΎΠΏΠΎΠ»Π½ΠΈΡΠ΅Π»ΡΠ½ΠΎ ΠΎΠ±Π΅ΡΠΏΠ΅ΡΠΈΠ²Π°Π΅Ρ Π²ΠΎΠ·ΠΌΠΎΠΆΠ½ΠΎΡΡΡ ΠΏΠΎΠΏΠ΅ΡΠ΅ΡΠ½ΠΎΠ³ΠΎ ΠΊΠ°ΡΠ°Π½ΠΈΡ ΠΏΠΎΠ»ΡΠΏΡΠΈΡΠ΅ΠΏΠ° ΠΎΡΠ½ΠΎΡΠΈΡΠ΅Π»ΡΠ½ΠΎ ΡΡΠ³Π°ΡΠ° Π² ΠΊΠ°ΠΆΠ΄ΡΡ ΡΡΠΎΡΠΎΠ½Ρ Π½Π° ΡΠ³ΠΎΠ» Ξ± Π΄ΠΎ 15Β° Π²ΠΊΠ»ΡΡΠΈΡΠ΅Π»ΡΠ½ΠΎ. ΠΡΠΈ ΡΡΠΎΠΌ ΠΏΠΎΠΏΠ΅ΡΠ΅ΡΠ½Π°Ρ ΠΈ ΠΏΡΠΎΠ΄ΠΎΠ»ΡΠ½Π°Ρ ΠΎΡΠΈ ΠΌΠΎΠ³ΡΡ Π½Π°Ρ ΠΎΠ΄ΠΈΡΡΡΡ Π½Π° ΡΠ°Π·Π½ΠΎΠΉ Π²ΡΡΠΎΡΠ΅ ΠΈΠ»ΠΈ Π½Π° ΠΎΠ΄Π½ΠΎΠΉ Π² ΡΠ°ΠΊ Π½Π°Π·ΡΠ²Π°Π΅ΠΌΠΎΠΌ ΠΊΠ°ΡΠ΄Π°Π½Π½ΠΎΠΌ ΡΠ°ΡΠ½ΠΈΡΠ΅. Π’Π°ΠΊΠΈΠ΅ ΡΠ΅Ρ Π½ΠΈΡΠ΅ΡΠΊΠΈΠ΅ ΡΠ΅ΡΠ΅Π½ΠΈΡ ΠΈΡΠΏΠΎΠ»ΡΠ·ΡΡΡΡΡ Π΄Π»Ρ Π°Π²ΡΠΎΠΏΠΎΠ΅Π·Π΄ΠΎΠ², ΡΠΊΡΠΏΠ»ΡΠ°ΡΠΈΡΡΠ΅ΠΌΡΡ Π½Π° Π±Π΅Π·Π΄ΠΎΡΠΎΠΆΡΠ΅ ΠΈΠ»ΠΈ ΠΏΡΠ΅Π΄Π½Π°Π·Π½Π°ΡΠ΅Π½Π½ΡΡ Π΄Π»Ρ ΠΏΠ΅ΡΠ΅Π²ΠΎΠ·ΠΊΠΈ ΡΡΠΆΠ΅Π»ΠΎΠ²Π΅ΡΠ½ΡΡ Π½Π΅Π΄Π΅Π»ΠΈΠΌΡΡ Π³ΡΡΠ·ΠΎΠ², Π° ΡΠ°ΠΊΠΆΠ΅ Π΄Π»Ρ ΡΡΠ°Π½ΡΠΏΠΎΡΡΠ½ΡΡ ΡΡΠ΅Π΄ΡΡΠ², Π² ΡΠΎΡΡΠ°Π² ΠΊΠΎΡΠΎΡΡΡ Π²Ρ ΠΎΠ΄ΡΡ ΠΏΠΎΠ»ΡΠΏΡΠΈΡΠ΅ΠΏΡ ΠΎΡΠΎΠ±ΠΎ ΠΆΠ΅ΡΡΠΊΠΎΠΉ Π½Π° ΠΊΡΡΡΠ΅Π½ΠΈΠ΅ ΠΊΠΎΠ½ΡΡΡΡΠΊΡΠΈΠΈ (Π½Π°ΠΏΡΠΈΠΌΠ΅Ρ, ΠΊΠΎΡΠΎΡΠΊΠΎΠ±Π°Π·Π½ΡΠ΅ ΠΏΠΎΠ»ΡΠΏΡΠΈΡΠ΅ΠΏΡ, ΠΏΠΎΠ»ΡΠΏΡΠΈΡΠ΅ΠΏΡ-ΡΠ°ΠΌΠΎΡΠ²Π°Π»Ρ, ΠΏΠΎΠ»ΡΠΏΡΠΈΡΠ΅ΠΏΡ-ΡΠΈΡΡΠ΅ΡΠ½Ρ Π½Π΅ΡΡΡΠΈΡ ΠΊΠΎΠ½ΡΡΡΡΠΊΡΠΈΠΉ ΠΈ Ρ. ΠΏ.).
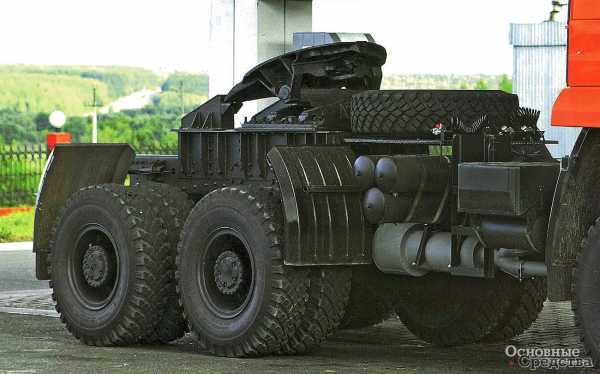
ΠΡΠΏΠΎΠ»ΡΠ·ΠΎΠ²Π°Π½ΠΈΠ΅ Π΄Π»Ρ ΠΏΠ΅ΡΠ΅ΡΠΈΡΠ»Π΅Π½Π½ΡΡ Π²ΡΡΠ΅ Π°Π²ΡΠΎΠΏΠΎΠ΅Π·Π΄ΠΎΠ² ΡΡΡΡΠΎΠΉΡΡΠ² Ρ Π΄Π²ΡΠΌΡ ΡΡΠ΅ΠΏΠ΅Π½ΡΠΌΠΈ ΡΠ²ΠΎΠ±ΠΎΠ΄Ρ ΠΏΡΠΈΠ²ΠΎΠ΄ΠΈΡ ΠΊ ΠΏΠ΅ΡΠ΅Π΄Π°ΡΠ΅ Π½Π° ΡΠ°ΠΌΡ ΡΡΠ³Π°ΡΠ° Π·Π½Π°ΡΠΈΡΠ΅Π»ΡΠ½ΡΡ ΡΠΊΡΡΡΠΈΠ²Π°ΡΡΠΈΡ ΠΌΠΎΠΌΠ΅Π½ΡΠΎΠ², ΡΠΏΠΎΡΠΎΠ±ΡΡΠ²ΡΡΡΠΈΡ Π΅Π΅ Π±ΡΡΡΡΠΎΠΌΡ ΡΠ°Π·ΡΡΡΠ΅Π½ΠΈΡ. ΠΠ°ΠΏΡΠΎΡΠΈΠ², Π‘Π‘Π£ Ρ ΡΡΠ΅ΠΌΡ ΡΡΠ΅ΠΏΠ΅Π½ΡΠΌΠΈ ΡΠ²ΠΎΠ±ΠΎΠ΄Ρ Π»ΠΈΡΠ΅Π½Ρ ΡΡΠΈΡ Π½Π΅Π΄ΠΎΡΡΠ°ΡΠΊΠΎΠ², ΠΎΠ΄Π½Π°ΠΊΠΎ Π°Π²ΡΠΎΠΏΠΎΠ΅Π·Π΄Π° Ρ ΡΠ°ΠΊΠΈΠΌΠΈ ΡΡΡΡΠΎΠΉΡΡΠ²Π°ΠΌΠΈ Π²ΠΎ Π²ΡΠ΅ΠΌΡ Π΄Π²ΠΈΠΆΠ΅Π½ΠΈΡ ΠΌΠ΅Π½Π΅Π΅ ΡΡΡΠΎΠΉΡΠΈΠ²Ρ. ΠΡΡΠ³ΠΎΠΉ Π½Π΅Π΄ΠΎΡΡΠ°ΡΠΎΠΊ Π·Π°ΠΊΠ»ΡΡΠ°Π΅ΡΡΡ Π² ΡΠΎΠΌ, ΡΡΠΎ Π³ΡΡΠΆΠ΅Π½ΡΠΉ ΠΏΠΎΠ»ΡΠΏΡΠΈΡΠ΅ΠΏ ΠΎΠΏΠΈΡΠ°Π΅ΡΡΡ Π½Π° ΡΠ°ΡΠ½ΠΈΡ, ΡΠ΅Π½ΡΡ Π²ΡΠ°ΡΠ΅Π½ΠΈΡ ΠΊΠΎΡΠΎΡΠΎΠ³ΠΎ Π½Π°Ρ ΠΎΠ΄ΠΈΡΡΡ Π½ΠΈΠΆΠ΅ ΡΠ΅Π½ΡΡΠ° ΡΡΠΆΠ΅ΡΡΠΈ ΠΏΠΎΠ»ΡΠΏΡΠΈΡΠ΅ΠΏΠ°. ΠΡΠΈ Π΄Π²ΠΈΠΆΠ΅Π½ΠΈΠΈ Π°Π²ΡΠΎΠΏΠΎΠ΅Π·Π΄Π° Π² ΠΏΠΎΠ²ΠΎΡΠΎΡΠ°Ρ ΡΠ΅Π·ΡΠ»ΡΡΠΈΡΡΡΡΠ°Ρ ΡΠ΅Π½ΡΡΠΎΠ±Π΅ΠΆΠ½Π°Ρ ΡΠΈΠ»Π°, Π΄Π΅ΠΉΡΡΠ²ΡΡΡΠ°Ρ Π² ΡΠ΅Π½ΡΡΠ΅ ΡΡΠΆΠ΅ΡΡΠΈ ΠΏΠΎΠ»ΡΠΏΡΠΈΡΠ΅ΠΏΠ°, ΡΡΡΠ΅ΠΌΠΈΡΡΡ ΠΎΠΏΡΠΎΠΊΠΈΠ½ΡΡΡ ΠΏΠΎΡΠ»Π΅Π΄Π½ΠΈΠΉ, ΡΡΠΎ ΡΠ½ΠΈΠΆΠ°Π΅Ρ ΠΏΠΎΠΏΠ΅ΡΠ΅ΡΠ½ΡΡ ΡΡΡΠΎΠΉΡΠΈΠ²ΠΎΡΡΡ Π°Π²ΡΠΎΠΏΠΎΠ΅Π·Π΄Π° ΠΈ ΠΌΠΎΠΆΠ΅Ρ ΠΏΡΠΈΠ²Π΅ΡΡΠΈ ΠΊ Π°Π²Π°ΡΠΈΠΈ. Π§ΡΠΎΠ±Ρ ΡΡΠΎΠ³ΠΎ Π½Π΅ ΠΏΡΠΎΠ·ΠΎΡΠ»ΠΎ, ΠΈΠ½ΠΎΠ³Π΄Π° ΠΏΡΠΈΠΌΠ΅Π½ΡΡΡ Π‘Π‘Π£ Ρ ΠΌΠ΅Ρ Π°Π½ΠΈΡΠ΅ΡΠΊΠΈΠΌΠΈ ΠΈΠ»ΠΈ Π³ΠΈΠ΄ΡΠ°Π²Π»ΠΈΡΠ΅ΡΠΊΠΈΠΌΠΈ ΡΡΠ°Π±ΠΈΠ»ΠΈΠ·Π°ΡΠΎΡΠ°ΠΌΠΈ. Π Π°Π²ΡΠΎΠΏΠΎΠ΅Π·Π΄Π°Ρ , ΡΠ°Π±ΠΎΡΠ°ΡΡΠΈΡ Π² ΡΡΠΆΠ΅Π»ΡΡ Π΄ΠΎΡΠΎΠΆΠ½ΡΡ ΡΡΠ»ΠΎΠ²ΠΈΡΡ , ΠΏΡΠΈ Π²ΡΠ΅Π·Π΄Π΅ Π½Π° ΠΌΠ°Π³ΠΈΡΡΡΠ°Π»Ρ Ρ ΠΊΠ°ΡΠ΅ΡΡΠ²Π΅Π½Π½ΡΠΌ ΠΏΠΎΠΊΡΡΡΠΈΠ΅ΠΌ ΠΊΠ°ΡΠ°Π½ΠΈΠ΅ ΠΏΠΎΠ»ΡΠΏΡΠΈΡΠ΅ΠΏΠ° Π²ΠΎΠΊΡΡΠ³ ΠΏΡΠΎΠ΄ΠΎΠ»ΡΠ½ΠΎΠΉ ΠΎΡΠΈ ΠΎΠ³ΡΠ°Π½ΠΈΡΠΈΠ²Π°Π΅ΡΡΡ (Β±3Β°) ΡΠΏΠ΅ΡΠΈΠ°Π»ΡΠ½ΡΠΌ ΠΌΠ΅Ρ Π°Π½ΠΈΠ·ΠΌΠΎΠΌ.
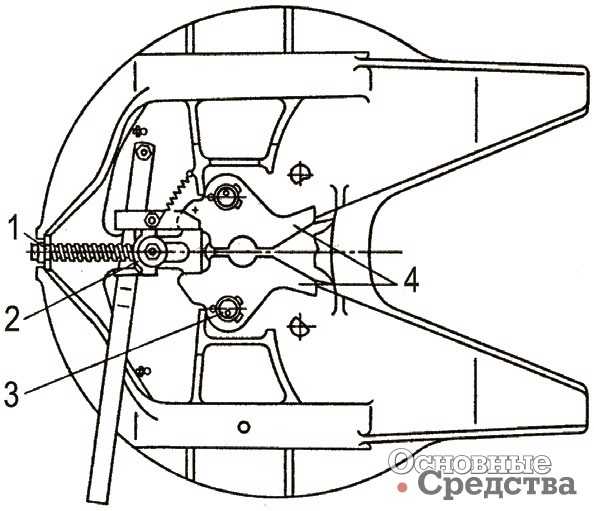
ΠΠΎΠ½ΡΡΡΡΠΊΡΠΈΡ Π‘Π‘Π£ Ρ Π΄Π²ΡΡ Π·Π°Ρ Π²Π°ΡΠ½ΡΠΌ ΡΠ°Π·ΡΠ΅ΠΌΠ½ΠΎ-ΡΡΠ΅ΠΏΠ½ΡΠΌ ΠΌΠ΅Ρ Π°Π½ΠΈΠ·ΠΌΠΎΠΌ: 1 β ΠΏΡΠ΅Π΄ΠΎΡ ΡΠ°Π½ΠΈΡΠ΅Π»Ρ; 2 β Π·Π°ΠΌΠΊΠΎΠ²ΠΎΠ΅ ΡΡΡΡΠΎΠΉΡΡΠ²ΠΎ; 3 β ΠΏΠ°Π»Π΅Ρ Π·Π°Ρ Π²Π°ΡΠ°; 4 β Π·Π°Ρ Π²Π°ΡΡ; 5 β ΡΠ΅Π³ΡΠ»ΠΈΡΠΎΠ²ΠΎΡΠ½ΠΎΠ΅ ΡΡΡΡΠΎΠΉΡΡΠ²ΠΎ; 6 β ΡΡΠ³Π°
ΠΠΌΠ΅ΡΡΡΡ ΠΈ Π΄ΡΡΠ³ΠΈΠ΅ ΡΠ΅ΡΠ΅Π½ΠΈΡ. ΠΡΡΡΡΡ ΡΡΡΠΎΠΉΡΠΈΠ²ΠΎΡΡΡ Π΄Π²ΠΈΠΆΠ΅Π½ΠΈΡ Π°Π²ΡΠΎΠΏΠΎΠ΅Π·Π΄Π° ΠΎΠ±Π΅ΡΠΏΠ΅ΡΠΈΠ²Π°ΡΡ Π‘Π‘Π£ Ρ ΡΡΠ΅ΠΌΡ ΡΡΠ΅ΠΏΠ΅Π½ΡΠΌΠΈ ΡΠ²ΠΎΠ±ΠΎΠ΄Ρ, ΠΊΠΎΡΠΎΡΡΠ΅ ΠΈΠΌΠ΅ΡΡ Β«Π΄ΡΠ³ΠΎΠ²ΠΎΠΉΒ» ΠΌΠ΅Ρ Π°Π½ΠΈΠ·ΠΌ ΠΏΠΎΠΏΠ΅ΡΠ΅ΡΠ½ΠΎΠΉ Π³ΠΈΠ±ΠΊΠΎΡΡΠΈ, ΠΎΠ±Π»Π°Π΄Π°ΡΡΠΈΠΉ ΡΠ²ΠΎΠΉΡΡΠ²ΠΎΠΌ ΡΠ°ΠΌΠΎΡΡΠ°Π±ΠΈΠ»ΠΈΠ·Π°ΡΠΈΠΈ. Π€ΡΠ°Π½ΡΡΠ·ΡΠΊΠ°Ρ ΡΠΈΡΠΌΠ° Coder Ture ΡΠ°Π·ΡΠ°Π±ΠΎΡΠ°Π»Π° ΠΎΡΠΈΠ³ΠΈΠ½Π°Π»ΡΠ½ΠΎΠ΅ ΡΡΠ΅ΡΠΈΡΠ΅ΡΠΊΠΎΠ΅ Π‘Π‘Π£, ΠΏΡΠ΅Π΄Π½Π°Π·Π½Π°ΡΠ΅Π½Π½ΠΎΠ΅ Π΄Π»Ρ ΠΏΠΎΠ²ΡΡΠ΅Π½ΠΈΡ ΡΡΡΠΎΠΉΡΠΈΠ²ΠΎΡΡΠΈ Π°Π²ΡΠΎΠΏΠΎΠ΅Π·Π΄ΠΎΠ² ΠΈ ΠΎΠ±Π»Π°Π΄Π°ΡΡΠ΅Π΅ ΠΏΠΎΠ²ΡΡΠ΅Π½Π½ΠΎΠΉ Π½Π°Π΄Π΅ΠΆΠ½ΠΎΡΡΡΡ, ΠΏΠΎΡΠΊΠΎΠ»ΡΠΊΡ ΠΎΠ½ΠΎ ΡΠΎΡ ΡΠ°Π½ΡΠ΅Ρ ΡΡΠ΅ΠΏΠ»Π΅Π½ΠΈΠ΅ ΡΡΠ³Π°ΡΠ° Ρ ΠΏΠΎΠ»ΡΠΏΡΠΈΡΠ΅ΠΏΠΎΠΌ Π΄Π°ΠΆΠ΅ ΠΏΡΠΈ ΡΠ»ΠΎΠΌΠ°Π½Π½ΠΎΠΌ ΡΠΊΠ²ΠΎΡΠ½Π΅. Π‘ΡΠ΅ΠΏΠ½ΠΎΠΉ ΠΌΠ΅Ρ Π°Π½ΠΈΠ·ΠΌ Π½Π°Ρ ΠΎΠ΄ΠΈΡΡΡ Π² ΡΡΠ΅ΡΠΈΡΠ΅ΡΠΊΠΎΠΌ Π²ΠΎΠ³Π½ΡΡΠΎΠΌ ΠΊΠΎΠΆΡΡ Π΅, Π΄ΠΈΠ°ΠΌΠ΅ΡΡ ΡΡΠ΅ΡΡ Π²ΡΠ±ΡΠ°Π½ ΡΠ°ΠΊ, ΡΡΠΎ ΡΠ΅Π½ΡΡ ΡΡΠ΅ΡΡ ΡΠ°ΡΠΏΠΎΠ»ΠΎΠΆΠ΅Π½ Π²ΡΡΠ΅ ΡΠ΅Π½ΡΡΠ° ΡΡΠΆΠ΅ΡΡΠΈ ΠΏΠΎΠ»ΡΠΏΡΠΈΡΠ΅ΠΏΠ°. ΠΠΎΠ·Π½ΠΈΠΊΠ°ΡΡΠ°Ρ Π² ΠΏΠΎΠ²ΠΎΡΠΎΡΠ°Ρ ΡΠ΅Π½ΡΡΠΎΠ±Π΅ΠΆΠ½Π°Ρ ΡΠΈΠ»Π° ΡΡΡΠ΅ΠΌΠΈΡΡΡ Π½Π°ΠΊΠ»ΠΎΠ½ΠΈΡΡ ΠΏΠΎΠ»ΡΠΏΡΠΈΡΠ΅ΠΏ ΠΊ Π²Π½ΡΡΡΠ΅Π½Π½Π΅ΠΉ ΡΡΠΎΡΠΎΠ½Π΅ Π²ΠΈΡΠ°ΠΆΠ°, Ρ. Π΅. ΠΏΠΎΠ²ΡΡΠ°Π΅Ρ Π΅Π³ΠΎ ΡΡΡΠΎΠΉΡΠΈΠ²ΠΎΡΡΡ. Π‘ΡΠ΅ΠΏΠΊΠ° ΠΎΠΊΡΡΠΆΠ΅Π½Π° ΡΠΏΠ΅ΡΠΈΠ°Π»ΡΠ½ΡΠΌΠΈ ΠΏΡΠΈΠΊΡΠ΅ΠΏΠ»Π΅Π½Π½ΡΠΌΠΈ ΠΊ ΠΏΠΎΠ»ΡΠΏΡΠΈΡΠ΅ΠΏΡ ΠΎΠ³ΡΠ°Π½ΠΈΡΠΈΡΠ΅Π»ΡΠΌΠΈ Π΄Π»Ρ ΡΠΎΡ ΡΠ°Π½Π΅Π½ΠΈΡ Π΅Π³ΠΎ ΡΡΠ΅ΠΏΠ»Π΅Π½ΠΈΡ Ρ ΡΡΠ³Π°ΡΠΎΠΌ Π΄Π°ΠΆΠ΅ ΠΏΡΠΈ ΠΏΠΎΠ»ΠΎΠΌΠΊΠ΅ ΡΠΊΠ²ΠΎΡΠ½Ρ. ΠΠΎΠΌΠΈΠΌΠΎ ΠΏΡΠΎΡΠ΅Π³ΠΎ ΠΎΠΏΠΈΡΠ°Π½Π½Π°Ρ ΠΊΠΎΠ½ΡΡΡΡΠΊΡΠΈΡ ΡΠ°Π·Π³ΡΡΠΆΠ°Π΅Ρ ΡΠ°ΠΌΡ ΠΎΡ ΡΠΊΡΡΡΠΈΠ²Π°ΡΡΠΈΡ ΡΡΠΈΠ»ΠΈΠΉ, ΡΠ°ΠΊ ΠΊΠ°ΠΊ ΠΏΡΠΈ Π½Π°Π΅Π·Π΄Π΅ Π½Π° Π΄ΠΎΡΠΎΠΆΠ½ΡΠ΅ Π½Π΅ΡΠΎΠ²Π½ΠΎΡΡΠΈ ΠΏΠΎΠ»ΡΠΏΡΠΈΡΠ΅ΠΏ ΠΌΠΎΠΆΠ΅Ρ Π½Π°ΠΊΠ»ΠΎΠ½ΡΡΡΡΡ Π² Π»ΡΠ±ΡΡ ΡΡΠΎΡΠΎΠ½Ρ ΠΏΠΎ ΠΎΡΠ½ΠΎΡΠ΅Π½ΠΈΡ ΠΊ ΡΡΠ³Π°ΡΡ.
Π£ΠΏΡΠ°Π²Π»Π΅Π½ΠΈΠ΅ ΡΡΠ΅ΠΏΠΊΠΎΠΉ
ΠΡΠ΅ Π±ΠΎΠ»ΡΡΠ΅Π΅ Π²Π½ΠΈΠΌΠ°Π½ΠΈΠ΅ ΡΠ΄Π΅Π»ΡΠ΅ΡΡΡ Π²ΠΎΠΏΡΠΎΡΠ°ΠΌ Π°Π²ΡΠΎΠΌΠ°ΡΠΈΠ·Π°ΡΠΈΠΈ ΡΠΏΡΠ°Π²Π»Π΅Π½ΠΈΡ ΠΈ Π±Π΅Π·ΠΎΠΏΠ°ΡΠ½ΠΎΡΡΠΈ ΠΏΡΠΈ ΡΡΠ΅ΠΏΠΊΠ΅-ΡΠ°ΡΡΠ΅ΠΏΠΊΠ΅ ΡΡΠ³Π°ΡΠ° Ρ ΠΏΠΎΠ»ΡΠΏΡΠΈΡΠ΅ΠΏΠΎΠΌ. ΠΠ°ΡΠ°ΡΡΡΡ ΠΈΠ·Π³ΠΎΡΠΎΠ²ΠΈΡΠ΅Π»ΠΈ, ΡΡΠΎΠ±Ρ ΠΎΠ±Π»Π΅Π³ΡΠΈΡΡ ΡΠ°Π±ΠΎΡΡ Π²ΠΎΠ΄ΠΈΡΠ΅Π»Ρ, Π²ΡΠΏΡΡΠΊΠ°ΡΡ Π‘Π‘Π£ Ρ ΠΏΠ½Π΅Π²ΠΌΠ°ΡΠΈΡΠ΅ΡΠΊΠΈΠΌΠΈ ΠΏΡΠΈΠ²ΠΎΠ΄Π°ΠΌΠΈ Π΄Π»Ρ Π°Π²ΡΠΎΠΌΠ°ΡΠΈΡΠ΅ΡΠΊΠΎΠΉ ΡΠ°ΡΡΠ΅ΠΏΠΊΠΈ ΠΈ ΡΠ»Π΅ΠΊΡΡΠΈΡΠ΅ΡΠΊΠΈΠΌ Π΄Π°ΡΡΠΈΠΊΠΎΠΌ Π΄Π»Ρ Π΄ΠΈΡΡΠ°Π½ΡΠΈΠΎΠ½Π½ΠΎΠ³ΠΎ ΠΊΠΎΠ½ΡΡΠΎΠ»Ρ Π·Π° ΡΠΎΡΡΠΎΡΠ½ΠΈΠ΅ΠΌ Π‘Π‘Π£. Π’Π°ΠΊΠΈΠ΅ ΠΌΠΎΠ΄Π΅Π»ΠΈ Ρ ΠΏΡΡΠΆΠΈΠ½Π½ΠΎ-ΠΏΠ½Π΅Π²ΠΌΠ°ΡΠΈΡΠ΅ΡΠΊΠΈΠΌ ΡΠΈΠ»ΠΈΠ½Π΄ΡΠΎΠΌ ΡΠΏΡΠ°Π²Π»Π΅Π½ΠΈΡ ΡΠ°Π·ΡΠ΅ΠΌΠ½ΠΎ-ΡΡΠ΅ΠΏΠ½ΡΠΌ ΠΌΠ΅Ρ Π°Π½ΠΈΠ·ΠΌΠΎΠΌ Π΅ΡΡΡ Π² Π°ΡΡΠ΅Π½Π°Π»Π΅ ΠΊΠΎΠΌΠΏΠ°Π½ΠΈΠΉ Fontaine Truck Equipment, ASF ΠΈ Fruehauf.
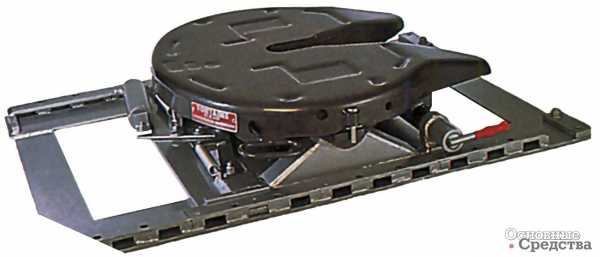
ΠΠ»Ρ ΠΏΠΎΠ²ΡΡΠ΅Π½ΠΈΡ ΡΠ΄ΠΎΠ±ΡΡΠ²Π° ΡΠΏΡΠ°Π²Π»Π΅Π½ΠΈΡ Π‘Π‘Π£ ΡΠΈΡΠΌΠ° Georg Fisher ΠΏΡΠ΅Π΄Π»Π°Π³Π°Π΅Ρ ΡΠ»Π΅ΠΊΡΡΠΎΠ½Π½ΡΡ ΡΠ΅Π½ΡΠΎΡΠ½ΡΡ ΡΠΈΡΡΠ΅ΠΌΡ Π±Π΅Π·ΠΎΠΏΠ°ΡΠ½ΠΎΡΡΠΈ RECCOS, Π΄Π²Π° Π΄Π°ΡΡΠΈΠΊΠ° ΠΊΠΎΡΠΎΡΠΎΠΉ Π½Π΅ΠΏΡΠ΅ΡΡΠ²Π½ΠΎ ΠΊΠΎΠ½ΡΡΠΎΠ»ΠΈΡΡΡΡ Π½Π°Π΄Π΅ΠΆΠ½ΠΎΡΡΡ ΠΈ ΠΏΡΠ°Π²ΠΈΠ»ΡΠ½ΠΎΡΡΡ ΡΡΠ΅ΠΏΠΊΠΈ, Π° Π΅ΡΠ΅ ΠΎΠ΄ΠΈΠ½ ΡΠΈΠΊΡΠΈΡΡΠ΅Ρ ΡΠ°ΡΡΡΠΎΡΠ½ΠΈΠ΅ ΠΌΠ΅ΠΆΠ΄Ρ ΠΏΠ»ΠΈΡΠΎΠΉ ΠΏΠΎΠ»ΡΠΏΡΠΈΡΠ΅ΠΏΠ° ΠΈ ΡΠ΅Π΄Π΅Π»ΡΠ½ΠΎ-ΡΡΠ΅ΠΏΠ½ΡΠΌ ΡΡΡΡΠΎΠΉΡΡΠ²ΠΎΠΌ. ΠΡΠΎΠΈΡΡ ΠΎΠ΄ΡΡΠΈΠ΅ ΠΏΡΠΎΡΠ΅ΡΡΡ, Π² ΡΠΎΠΌ ΡΠΈΡΠ»Π΅ Π½Π΅ΠΏΠΎΠ»Π°Π΄ΠΊΠΈ, Π² Π²ΠΈΠ΄Π΅ Π·Π²ΡΠΊΠΎΠ²ΡΡ ΡΠΈΠ³Π½Π°Π»ΠΎΠ² ΠΈ ΠΈΠ·ΠΎΠ±ΡΠ°ΠΆΠ΅Π½ΠΈΠΉ Π½Π° ΡΠΏΠ΅ΡΠΈΠ°Π»ΡΠ½ΠΎΠΉ ΠΈΠ½ΡΠΎΡΠΌΠ°ΡΠΈΠΎΠ½Π½ΠΎΠΉ ΠΏΠ°Π½Π΅Π»ΠΈ ΠΎΡΠΎΠ±ΡΠ°ΠΆΠ°ΡΡΡΡ Π² ΠΊΠ°Π±ΠΈΠ½Π΅ Π°Π²ΡΠΎΠΌΠΎΠ±ΠΈΠ»Ρ. ΠΠΎΠ΄ΠΈΡΠ΅Π»Ρ, Π½Π΅ ΠΏΠΎΠΊΠΈΠ΄Π°Ρ ΡΠ°Π±ΠΎΡΠ΅Π³ΠΎ ΠΌΠ΅ΡΡΠ°, ΠΌΠΎΠΆΠ΅Ρ ΡΠ»Π΅Π΄ΠΈΡΡ Π·Π° Π²ΡΠ΅ΠΌ ΠΏΡΠΎΡΠ΅ΡΡΠΎΠΌ ΡΡΠ΅ΠΏΠΊΠΈ, ΠΊΠΎΡΠΎΡΠ°Ρ ΠΎΡΡΡΠ΅ΡΡΠ²Π»ΡΠ΅ΡΡΡ Π±ΡΡΡΡΠ΅Π΅ ΠΈ Π½Π°Π΄Π΅ΠΆΠ½Π΅Π΅, ΡΠ΅ΠΌ Π² ΡΡΠ°Π΄ΠΈΡΠΈΠΎΠ½Π½ΡΡ ΠΊΠΎΠ½ΡΡΡΡΠΊΡΠΈΡΡ .
ΠΠ½Π°Π»ΠΎΠ³ΠΈΡΠ½Π°Ρ ΡΠ΅Π½ΡΠΎΡΠ½Π°Ρ ΡΠΈΡΡΠ΅ΠΌΠ° SKS Π΅ΡΡΡ ΠΈ Π² ΠΏΡΠΎΠΈΠ·Π²ΠΎΠ΄ΡΡΠ²Π΅Π½Π½ΠΎΠΉ ΠΏΡΠΎΠ³ΡΠ°ΠΌΠΌΠ΅ ΠΊΠΎΠΌΠΏΠ°Π½ΠΈΠΈ Jost. ΠΠ΄ΠΈΠ½ ΠΈΠ· Π΄Π°ΡΡΠΈΠΊΠΎΠ², Π²Ρ ΠΎΠ΄ΡΡΠΈΡ Π² Π΅Π΅ ΡΠΎΡΡΠ°Π², ΠΊΠΎΠ½ΡΡΠΎΠ»ΠΈΡΡΠ΅Ρ ΠΏΠΎΠ»ΠΎΠΆΠ΅Π½ΠΈΠ΅ Π·Π°ΠΌΠΊΠ° ΡΠ°Π·ΡΠ΅ΠΌΠ½ΠΎ-ΡΡΠ΅ΠΏΠ½ΠΎΠ³ΠΎ ΠΌΠ΅Ρ Π°Π½ΠΈΠ·ΠΌΠ°, Π²ΡΠΎΡΠΎΠΉ Π΄Π°ΡΡΠΈΠΊ ΡΠ»Π΅Π΄ΠΈΡ Π·Π° ΠΏΠΎΠ»ΠΎΠΆΠ΅Π½ΠΈΠ΅ΠΌ ΡΠΊΠ²ΠΎΡΠ½Ρ, ΡΡΠ΅ΡΠΈΠΉ ΡΠΈΠΊΡΠΈΡΡΠ΅Ρ Π²ΡΡΠΎΡΡ Π‘Π‘Π£. Π€ΡΠ½ΠΊΡΠΈΠΎΠ½Π°Π»ΡΠ½ΡΠ΅ Π²ΠΎΠ·ΠΌΠΎΠΆΠ½ΠΎΡΡΠΈ SKS ΠΏΠΎΠ²ΡΡΠ°ΡΡΡΡ Π±Π»Π°Π³ΠΎΠ΄Π°ΡΡ Π½Π°Π»ΠΈΡΠΈΡ ΠΏΠ½Π΅Π²ΠΌΠΎΠΏΡΠΈΠ²ΠΎΠ΄Π° (ΠΏΠ½Π΅Π²ΠΌΠ°ΡΠΈΡΠ΅ΡΠΊΠΈΠΉ ΡΠΈΠ»ΠΈΠ½Π΄Ρ) ΡΠ°ΡΡΠ΅ΠΏΠΊΠΈ Π‘Π‘Π£ Ρ Π΄ΠΈΡΡΠ°Π½ΡΠΈΠΎΠ½Π½ΡΠΌ ΡΠΏΡΠ°Π²Π»Π΅Π½ΠΈΠ΅ΠΌ ΠΈΠ· ΠΊΠ°Π±ΠΈΠ½Ρ ΡΡΠ³Π°ΡΠ°, Π³Π΄Π΅ ΡΡΡΠ°Π½ΠΎΠ²Π»Π΅Π½ ΠΈΠ½ΡΠΎΡΠΌΠ°ΡΠΈΠΎΠ½Π½ΡΠΉ Π΄ΠΈΡΠΏΠ»Π΅ΠΉ.
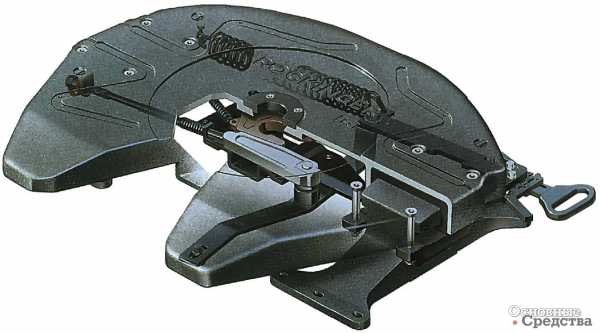
ΠΡΠ΅ Π±ΠΎΠ»Π΅Π΅ Β«ΠΏΡΠΎΠ΄Π²ΠΈΠ½ΡΡΠΎΠΉΒ» ΡΠ²Π»ΡΠ΅ΡΡΡ ΡΠ»Π΅ΠΊΡΡΠΎΠ½Π½Π°Ρ ΡΠΈΡΡΠ΅ΠΌΠ° ΠΊΠΎΠΌΡΠΎΡΡΠ½ΠΎΠΉ ΡΡΠ΅ΠΏΠΊΠΈ KKS ΡΡΠΎΠΉ ΠΆΠ΅ ΡΠΈΡΠΌΡ. Π’ΡΠΈ ΡΠ΅Π½ΡΠΎΡΠ½ΡΡ Π΄Π°ΡΡΠΈΠΊΠ° ΡΠ»Π΅Π΄ΡΡ Π·Π° ΡΠΎΡΡΠΎΡΠ½ΠΈΠ΅ΠΌ Π‘Π‘Π£, ΠΎΠ½ΠΈ ΠΎΠΏΡΠ΅Π΄Π΅Π»ΡΡΡ Π΅Π³ΠΎ Π²ΡΡΠΎΡΡ Ρ Π°Π²ΡΠΎΠΌΠ°ΡΠΈΡΠ΅ΡΠΊΠΈΠΌ Π²ΠΊΠ»ΡΡΠ΅Π½ΠΈΠ΅ΠΌ ΡΠΈΡΡΠ΅ΠΌΡ ΠΏΡΠΈ ΠΎΡΡΡΠ΅ΡΡΠ²Π»Π΅Π½ΠΈΠΈ ΡΡΠ΅ΠΏΠΊΠΈ, ΠΊΠΎΠ½ΡΡΠΎΠ»ΠΈΡΡΡΡ ΠΏΠΎΠ»ΠΎΠΆΠ΅Π½ΠΈΠ΅ ΡΠΊΠ²ΠΎΡΠ½Ρ ΠΈ Π·Π°ΠΌΠΊΠ°. ΠΠ½Π΅Π²ΠΌΠΎΠΏΡΠΈΠ²ΠΎΠ΄ ΠΏΠΎ ΠΊΠΎΠΌΠ°Π½Π΄Π΅ Π²ΠΎΠ΄ΠΈΡΠ΅Π»Ρ ΠΎΡΠΊΡΡΠ²Π°Π΅Ρ Π·Π°ΠΌΠΎΠΊ Π΄Π»Ρ ΡΠ°ΡΡΠ΅ΠΏΠΊΠΈ Π‘Π‘Π£. Π£ΡΡΠ°Π½ΠΎΠ²ΠΊΡ Π½ΡΠΆΠ½ΠΎΠΉ Π²ΡΡΠΎΡΡ ΡΠ°ΡΠΏΠΎΠ»ΠΎΠΆΠ΅Π½ΠΈΡ ΡΠΊΠ²ΠΎΡΠ½Ρ ΠΏΡΠΈ ΡΡΠ΅ΠΏΠΊΠ΅ Π°Π²ΡΠΎΠΌΠ°ΡΠΈΡΠ΅ΡΠΊΠΈ ΠΎΠ±Π΅ΡΠΏΠ΅ΡΠΈΠ²Π°ΡΡ ΠΎΠΏΠΎΡΠ½ΡΠ΅ ΡΡΡΡΠΎΠΉΡΡΠ²Π° ΠΏΠΎΠ»ΡΠΏΡΠΈΡΠ΅ΠΏΠ°, ΡΠ½Π°Π±ΠΆΠ΅Π½Π½ΡΠ΅ ΡΠΎΠ±ΡΡΠ²Π΅Π½Π½ΡΠΌ ΡΠ»Π΅ΠΊΡΡΠΎΠΏΡΠΈΠ²ΠΎΠ΄ΠΎΠΌ. Π ΡΠΊΠΎΡΡΠΊΠ° Π΄Π»Ρ ΡΡΡΠ½ΠΎΠ³ΠΎ ΡΠΏΡΠ°Π²Π»Π΅Π½ΠΈΡ Π΅ΡΡΡ Π² ΠΊΠΎΠΌΠΏΠ»Π΅ΠΊΡΠ΅ ΠΊΠ°ΠΊ ΡΡΡΠ°Ρ ΠΎΠ²ΠΎΡΠ½ΠΎΠ΅ ΡΡΠ΅Π΄ΡΡΠ²ΠΎ. Π¨ΠΊΠ²ΠΎΡΠ΅Π½Ρ ΠΎΡΠ½Π°ΡΠ΅Π½ ΠΏΠΎΠ²ΠΎΡΠΎΡΠ½ΡΠΌ ΠΊΠ»ΠΈΠ½ΠΎΠΌ Ρ Π½Π°Ρ ΠΎΠ΄ΡΡΠΈΠΌΡΡ Π² Π½Π΅ΠΌ ΡΠ°Π·ΡΠ΅ΠΌΠΎΠΌ Π΄Π»Ρ ΡΠ΅Π΄Π»Π°, ΡΠ΅ΡΠ΅Π· ΠΊΠΎΡΠΎΡΡΠΉ ΠΏΠ΅ΡΠ΅Π΄Π°Π΅ΡΡΡ ΡΠΈΠ³Π½Π°Π» ΡΠΏΡΠ°Π²Π»Π΅Π½ΠΈΡ ΠΌΠ΅ΠΆΠ΄Ρ ΡΡΠ³Π°ΡΠΎΠΌ ΠΈ ΠΏΠΎΠ»ΡΠΏΡΠΈΡΠ΅ΠΏΠΎΠΌ. ΠΡΠ»ΡΡ Π΄ΠΈΡΡΠ°Π½ΡΠΈΠΎΠ½Π½ΠΎΠ³ΠΎ ΡΠΏΡΠ°Π²Π»Π΅Π½ΠΈΡ ΠΈ ΠΊΠΎΠ½ΡΡΠΎΠ»Ρ Π²ΡΠΏΠΎΠ»Π½ΡΠ΅ΠΌΡΡ ΠΎΠΏΠ΅ΡΠ°ΡΠΈΠΉ ΡΠ°ΡΠΏΠΎΠ»ΠΎΠΆΠ΅Π½ Π½Π΅ΠΏΠΎΡΡΠ΅Π΄ΡΡΠ²Π΅Π½Π½ΠΎ ΠΏΠ΅ΡΠ΅Π΄ Π²ΠΎΠ΄ΠΈΡΠ΅Π»Π΅ΠΌ. ΠΠ°ΠΊ ΡΠ΅Π·ΡΠ»ΡΡΠ°Ρ ΠΈΡΠΊΠ»ΡΡΠ°Π΅ΡΡΡ ΡΡΡΠ½ΠΎΠΉ ΡΡΡΠ΄ ΠΏΡΠΈ ΠΎΠ±ΡΠ»ΡΠΆΠΈΠ²Π°Π½ΠΈΠΈ Π‘Π‘Π£, ΡΠΎΠΊΡΠ°ΡΠ°Π΅ΡΡΡ Π²ΡΠ΅ΠΌΡ ΡΡΠ΅ΠΏΠΊΠΈ, ΡΠ°ΡΡΠ΅ΠΏΠΊΠΈ, Π° ΡΠ°ΠΊΠΆΠ΅ ΠΈΠ·Π½ΠΎΡ ΠΌΠ΅Ρ Π°Π½ΠΈΠ·ΠΌΠΎΠ², ΠΏΠΎΠ²ΡΡΠ°Π΅ΡΡΡ Π±Π΅Π·ΠΎΠΏΠ°ΡΠ½ΠΎΡΡΡ ΡΠΊΡΠΏΠ»ΡΠ°ΡΠ°ΡΠΈΠΈ Π·Π° ΡΡΠ΅Ρ ΡΠ½ΠΈΠΆΠ΅Π½ΠΈΡ Π²Π΅ΡΠΎΡΡΠ½ΠΎΡΡΠΈ Π½Π΅ΠΏΡΠ°Π²ΠΈΠ»ΡΠ½ΠΎΠΉ ΡΡΠ΅ΠΏΠΊΠΈ, ΡΠ»ΡΡΡΠ°Π΅ΡΡΡ ΠΊΠΎΠ½ΡΡΠΎΠ»Ρ ΡΠΎΡΡΠΎΡΠ½ΠΈΡ Π²ΡΠ΅Ρ ΡΠ»Π΅ΠΌΠ΅Π½ΡΠΎΠ² ΡΠΈΡΡΠ΅ΠΌΡ.
ΠΠ±ΡΡΠ½ΠΎ ΠΏΡΠΈ ΡΠ°Π±ΠΎΡΠ΅ Ρ ΡΠΊΠ²ΠΎΡΠ½Π΅Π²ΡΠΌΠΈ Π‘Π‘Π£ ΠΏΠΎΡΠ»Π΅ ΡΡΠ΅ΠΏΠΊΠΈ ΡΡΠ³Π°ΡΠ° Ρ ΠΏΠΎΠ»ΡΠΏΡΠΈΡΠ΅ΠΏΠΎΠΌ Π²ΠΎΠ΄ΠΈΡΠ΅Π»Ρ Π΄ΠΎΠ»ΠΆΠ΅Π½ ΡΠΎΠ΅Π΄ΠΈΠ½ΠΈΡΡ ΠΈΡ ΡΠΎΡΠΌΠΎΠ·Π½ΡΠ΅ ΠΈ ΡΠ»Π΅ΠΊΡΡΠΈΡΠ΅ΡΠΊΠΈΠ΅ ΠΊΠΎΠΌΠΌΡΠ½ΠΈΠΊΠ°ΡΠΈΠΈ. ΠΠ° ΡΠ΅Π΄Π΅Π»ΡΠ½ΠΎ-ΡΡΠ΅ΠΏΠ½ΡΡ ΡΡΡΡΠΎΠΉΡΡΠ²Π°Ρ , ΡΠΎΠ·Π΄Π°Π½Π½ΡΡ ΡΠΏΠ΅ΡΠΈΠ°Π»ΠΈΡΡΠ°ΠΌΠΈ ΡΠΈΡΠΌΡ Π’ΠΎussaint & HeΞ², ΠΊΠΎΠΌΠΌΡΠ½ΠΈΠΊΠ°ΡΠΈΠΈ Ρ ΠΏΠΎΠΌΠΎΡΡΡ ΠΏΠ΅ΡΠ΅Ρ ΠΎΠ΄Π½ΡΡ ΡΠ»Π΅ΠΌΠ΅Π½ΡΠΎΠ² ΡΠΎΠ΅Π΄ΠΈΠ½ΡΡΡΡΡ Π² ΠΏΡΠΎΡΠ΅ΡΡΠ΅ ΡΡΠ΅ΠΏΠΊΠΈ. ΠΠΎ Π΅Π³ΠΎ Π·Π°Π²Π΅ΡΡΠ΅Π½ΠΈΠΈ Π²ΠΎΠ΄ΠΈΡΠ΅Π»Ρ ΠΈΠ· ΠΊΠ°Π±ΠΈΠ½Ρ ΠΎΡΡΠ°Π΅ΡΡΡ ΡΠΎΠ»ΡΠΊΠΎ Π·Π°ΠΏΠ΅ΡΠ΅ΡΡ ΡΠ΅Π΄Π΅Π»ΡΠ½ΠΎ-ΡΡΠ΅ΠΏΠ½ΠΎΠ΅ ΡΡΡΡΠΎΠΉΡΡΠ²ΠΎ Π΄Π»Ρ Π΄Π°Π»ΡΠ½Π΅ΠΉΡΠ΅Π³ΠΎ Π΄Π²ΠΈΠΆΠ΅Π½ΠΈΡ Π°Π²ΡΠΎΠΏΠΎΠ΅Π·Π΄Π°.
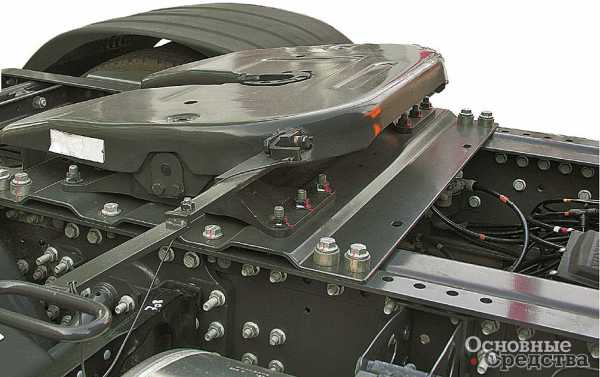
os1.ru
Π‘ΡΠ΅ΠΏΠ½ΡΠ΅ ΡΡΡΡΠΎΠΉΡΡΠ²Π° Π°Π²ΡΠΎΠΌΠΎΠ±ΠΈΠ»ΡΠ½ΡΡ ΠΏΠΎΠ΅Π·Π΄ΠΎΠ² | ΠΠ²ΡΠΎΠΌΠΎΠ±ΠΈΠ»ΡΠ½ΠΎΠ΅
Π‘Π²ΡΠ·Ρ ΠΌΠ΅ΠΆΠ΄Ρ Π·Π²Π΅Π½ΡΡΠΌΠΈ Π°Π²ΡΠΎΠΏΠΎΠ΅Π·Π΄Π° ΠΎΡΡΡΠ΅ΡΡΠ²Π»ΡΠ΅ΡΡΡ Ρ ΠΏΠΎΠΌΠΎΡΡΡ ΡΡΠ΅ΠΏΠ½ΡΡ ΡΡΡΡΠΎΠΉΡΡΠ², ΠΊΠΎΡΠΎΡΡΠ΅ Π²ΠΎΡΠΏΡΠΈΠ½ΠΈΠΌΠ°ΡΡ ΡΠΈΠ»Ρ Π²Π·Π°ΠΈΠΌΠΎΠ΄Π΅ΠΉΡΡΠ²ΠΈΡ, ΠΎΠ±ΡΡΠ»ΠΎΠ²Π»Π΅Π½Π½ΡΠ΅ ΠΎΡΠ½ΠΎΡΠΈΡΠ΅Π»ΡΠ½ΡΠΌΠΈ ΠΏΡΠΎΠ΄ΠΎΠ»ΡΠ½ΡΠΌΠΈ ΠΈ ΠΏΠΎΠΏΠ΅ΡΠ΅ΡΠ½ΡΠΌΠΈ ΠΏΠ΅ΡΠ΅ΠΌΠ΅ΡΠ΅Π½ΠΈΡΠΌΠΈ Π·Π²Π΅Π½ΡΠ΅Π². Π‘ΡΠ΅ΠΏΠ½ΡΠ΅ ΡΡΡΡΠΎΠΉΡΡΠ²Π° Π΄ΠΎΠ»ΠΆΠ½Ρ ΠΎΠ±Π΅ΡΠΏΠ΅ΡΠΈΠ²Π°ΡΡ Π½Π°Π΄Π΅ΠΆΠ½ΠΎΠ΅ ΡΠΎΠ΅Π΄ΠΈΠ½Π΅Π½ΠΈΠ΅ ΡΡΠ³Π°ΡΠ° Ρ ΠΏΡΠΈΡΠ΅ΠΏΠ½ΡΠΌ Π·Π²Π΅Π½ΠΎΠΌ, Π²ΠΎΠ·ΠΌΠΎΠΆΠ½ΠΎΡΡΡ ΠΈΡ ΠΎΡΠ½ΠΎΡΠΈΡΠ΅Π»ΡΠ½ΠΎΠ³ΠΎ ΠΏΠ΅ΡΠ΅ΠΌΠ΅ΡΠ΅Π½ΠΈΡ, ΠΏΠ»Π°Π²Π½ΠΎΡΡΡ ΠΏΠ΅ΡΠ΅Π΄Π°ΡΠΈ ΡΡΠΈΠ»ΠΈΠΉ ΠΎΡ ΡΡΠ³Π°ΡΠ° ΠΊ ΠΏΡΠΈΡΠ΅ΠΏΠ½ΠΎΠΌΡ Π·Π²Π΅Π½Ρ, Π° ΡΠ°ΠΊΠΆΠ΅ Π²ΠΎΠ·ΠΌΠΎΠΆΠ½ΠΎΡΡΡ Π±ΡΡΡΡΠΎΠΉ ΡΡΠ΅ΠΏΠΊΠΈ ΠΈ ΡΠ°ΡΡΠ΅ΠΏΠΊΠΈ.
Π Π·Π°Π²ΠΈΡΠΈΠΌΠΎΡΡΠΈ ΠΎΡ ΠΊΠΎΠΌΠΏΠΎΠ½ΠΎΠ²ΠΊΠΈ Π°Π²ΡΠΎΠΏΠΎΠ΅Π·Π΄Π° ΡΡΠ΅ΠΏΠ½ΡΠ΅ ΡΡΡΡΠΎΠΉΡΡΠ²Π° Π²ΡΠΏΠΎΠ»Π½ΡΡΡ Π² Π²ΠΈΠ΄Π΅ ΡΡΠ³ΠΎΠ²ΠΎ-ΡΡΠ΅ΠΏΠ½ΡΡ ΡΡΡΡΠΎΠΉΡΡΠ² Π΄Π»Ρ ΠΏΡΠΈΡΠ΅ΠΏΠ½ΡΡ Π°Π²ΡΠΎΠΏΠΎΠ΅Π·Π΄ΠΎΠ² ΠΈΠ»ΠΈ Π² Π²ΠΈΠ΄Π΅ ΠΎΠΏΠΎΡΠ½ΠΎ-ΡΡΠ΅ΠΏΠ½ΡΡ ΡΡΡΡΠΎΠΉΡΡΠ² Π΄Π»Ρ ΡΠ΅Π΄Π΅Π»ΡΠ½ΡΡ Π°Π²ΡΠΎΠΏΠΎΠ΅Π·Π΄ΠΎΠ².
Π‘ΡΡΠ΅ΡΡΠ²ΡΡΡ Π΄Π²Π° ΡΠΈΠΏΠ° ΡΡΠ³ΠΎΠ²ΠΎ-ΡΡΠ΅ΠΏΠ½ΡΡ ΡΡΡΡΠΎΠΉΡΡΠ²: ΡΡΠ³ΠΎΠ²ΡΠΉ ΠΊΡΡΠΊ-ΠΏΠ΅ΡΠ»Ρ ΠΈ ΡΡΠ³ΠΎΠ²Π°Ρ Π²ΠΈΠ»ΠΊΠ°-ΠΏΠ΅ΡΠ»Ρ. ΠΠ°ΠΈΠ±ΠΎΠ»Π΅Π΅ ΡΠΈΡΠΎΠΊΠΎΠ΅ ΡΠ°ΡΠΏΡΠΎΡΡΡΠ°Π½Π΅Π½ΠΈΠ΅ ΠΏΠΎΠ»ΡΡΠΈΠ»ΠΈ ΡΡΡΡΠΎΠΉΡΡΠ²Π° ΠΏΠ΅ΡΠ²ΠΎΠ³ΠΎ ΡΠΈΠΏΠ°. ΠΠ½ΠΈ ΡΠΎΡΡΠΎΡΡ ΠΈΠ· ΡΡΠ³ΠΎΠ²ΠΎΠ³ΠΎ ΠΊΡΡΠΊΠ°, ΡΡΡΠ°Π½ΠΎΠ²Π»Π΅Π½Π½ΠΎΠ³ΠΎ Π½Π° ΡΡΠ³Π°ΡΠ΅, ΠΈ ΠΆΠ΅ΡΡΠΊΠΎΠ³ΠΎ Π΄ΡΡΠ»Π° ΡΠΎ ΡΡΠ΅ΠΏΠ½ΠΎΠΉ ΠΏΠ΅ΡΠ»Π΅ΠΉ, ΡΠ²ΡΠ·Π°Π½Π½ΠΎΠ³ΠΎ Ρ ΠΏΡΠΈΡΠ΅ΠΏΠΎΠΌ.
Π ΠΈΡ. Π’ΡΠ³ΠΎΠ²ΡΠΉ ΠΊΡΡΠΊ
Π’ΡΠ³ΠΎΠ²ΡΠΉ ΠΊΡΡΠΊ, ΠΊΠ°ΠΊ ΠΏΡΠ°Π²ΠΈΠ»ΠΎ, ΠΌΠΎΠ½ΡΠΈΡΡΡΡ Π½Π° Π·Π°Π΄Π½Π΅ΠΉ ΠΏΠΎΠΏΠ΅ΡΠ΅ΡΠΈΠ½Π΅ ΡΠ°ΠΌΡ 7. ΠΠ΄Π½Π°ΠΊΠΎ Π½Π° Π½Π΅ΠΊΠΎΡΠΎΡΡΡ Π’Π‘ ΠΎΠ½ ΠΌΠΎΠΆΠ΅Ρ ΡΠ°Π·ΠΌΠ΅ΡΠ°ΡΡΡΡ ΠΈ Π½Π° ΠΏΠ΅ΡΠ΅Π΄Π½ΠΈΡ Π±Π°ΠΌΠΏΠ΅ΡΠ°Ρ ΡΠ°ΠΌΡ. Π’ΡΠ³ΠΎΠ²ΡΠΉ ΠΊΡΡΠΊ Π²ΠΊΠ»ΡΡΠ°Π΅Ρ Π² ΡΠ΅Π±Ρ ΡΠΎΠ±ΡΡΠ²Π΅Π½Π½ΠΎ ΠΊΡΡΠΊ 4, Π½Π°ΠΊΠΈΠ΄Π½ΡΡ Π·Π°ΡΠ΅Π»ΠΊΡ 6 ΠΈ ΠΏΡΠ΅Π΄ΠΎΡ ΡΠ°Π½ΠΈΡΠ΅Π»ΡΠ½ΡΠΉ Π·Π°ΠΌΠΎΠΊ Ρ Π·Π°ΠΏΠΎΡΠ½ΡΠΌ ΡΠΏΠ»ΠΈΠ½ΡΠΎΠΌ 5. ΠΡΠ΅Π΄ΠΎΡ ΡΠ°Π½ΠΈΡΠ΅Π»ΡΠ½ΡΠΉ Π·Π°ΠΌΠΎΠΊ ΠΈ ΡΠΏΠ»ΠΈΠ½Ρ ΠΏΡΠ΅Π΄ΠΎΡΠ²ΡΠ°ΡΠ°ΡΡ ΡΠ°ΠΌΠΎΠΏΡΠΎΠΈΠ·Π²ΠΎΠ»ΡΠ½ΡΡ ΡΠ°ΡΡΠ΅ΠΏΠΊΡ Π°Π²ΡΠΎΠΏΠΎΠ΅Π·Π΄Π° Π²ΠΎ Π²ΡΠ΅ΠΌΡ Π΄Π²ΠΈΠΆΠ΅Π½ΠΈΡ. ΠΠ° ΠΏΠ΅ΡΠ΅Π΄Π½Π΅ΠΌ ΠΊΠΎΠ½ΡΠ΅ ΡΡΠ΅ΡΠΆΠ½Ρ 3 ΠΊΡΡΠΊΠ°, ΡΡΡΠ°Π½ΠΎΠ²Π»Π΅Π½Π½ΠΎΠ³ΠΎ Π²ΠΎ Π²ΡΡΠ»ΠΊΠ΅ 8, Π½Π°Π²ΠΈΠ½ΡΠ΅Π½Π° Π³Π°ΠΉΠΊΠ° 10, ΠΊΠΎΡΠΎΡΠ°Ρ Π²ΠΌΠ΅ΡΡΠ΅ Ρ Π²ΡΡΠ»ΠΊΠΎΠΉ ΠΎΠ±Π΅ΡΠΏΠ΅ΡΠΈΠ²Π°Π΅Ρ ΠΏΡΠ°Π²ΠΈΠ»ΡΠ½ΠΎΠ΅ ΠΏΡΠΎΠ΄ΠΎΠ»ΡΠ½ΠΎΠ΅ ΠΏΠ΅ΡΠ΅ΠΌΠ΅ΡΠ΅Π½ΠΈΠ΅ ΠΊΡΡΠΊΠ°. ΠΠ½ΡΡΡΡ ΠΊΠΎΡΠΏΡΡΠ° 1 Π²ΡΡΠ°Π²Π»Π΅Π½ ΡΠ΅Π·ΠΈΠ½ΠΎΠ²ΡΠΉ ΡΠΏΡΡΠ³ΠΈΠΉ ΡΠ»Π΅ΠΌΠ΅Π½Ρ 2, ΠΎΠ±ΠΆΠΈΠΌΠ°Π΅ΠΌΡΠΉ ΡΠ°ΠΉΠ±Π°ΠΌΠΈ 9 ΠΈ ΠΈΠΌΠ΅ΡΡΠΈΠΉ ΡΠΎΡΠΌΡ Π³ΠΈΠΏΠ΅ΡΠ±ΠΎΠ»ΠΎΠΈΠ΄Π°. ΠΡΠΈ ΡΠΆΠ°ΡΠΈΠΈ ΠΎΠ½ Π²ΡΠΏΡΡΠΈΠ²Π°Π΅ΡΡΡ ΠΈ Π·Π°ΠΏΠΎΠ»Π½ΡΠ΅Ρ ΠΏΡΠΎΡΡΡΠ°Π½ΡΡΠ²ΠΎ Π² ΠΊΠΎΡΠΏΡΡΠ΅. Π Π΄ΡΡΠ³ΠΈΡ ΠΊΠΎΠ½ΡΡΡΡΠΊΡΠΈΡΡ ΡΡΠ³ΠΎΠ²ΡΡ ΠΊΡΡΠΊΠΎΠ² Π² ΠΊΠ°ΡΠ΅ΡΡΠ²Π΅ ΡΠΏΡΡΠ³ΠΈΡ ΡΠ»Π΅ΠΌΠ΅Π½ΡΠΎΠ² ΠΈΡΠΏΠΎΠ»ΡΠ·ΡΡΡ ΠΊΠΎΠ»ΡΡΠ΅Π²ΡΠ΅, Π²ΠΈΠ½ΡΠΎΠ²ΡΠ΅ ΡΠΈΠ»ΠΈΠ½Π΄ΡΠΈΡΠ΅ΡΠΊΠΈΠ΅ ΠΈΠ»ΠΈ ΠΊΠΎΠ½ΠΈΡΠ΅ΡΠΊΠΈΠ΅ ΠΏΡΡΠΆΠΈΠ½Ρ.
Π ΠΊΠ°ΡΠ΅ΡΡΠ²Π΅ ΠΎΠΏΠΎΡΠ½ΠΎ-ΡΡΠ΅ΠΏΠ½ΠΎΠ³ΠΎ ΡΡΡΡΠΎΠΉΡΡΠ²Π° ΡΠ΅Π΄Π΅Π»ΡΠ½ΡΡ Π°Π²ΡΠΎΠΏΠΎΠ΅Π·Π΄ΠΎΠ² Π½Π°ΠΈΠ±ΠΎΠ»Π΅Π΅ ΡΠΈΡΠΎΠΊΠΎ ΠΏΡΠΈΠΌΠ΅Π½ΡΠ΅ΡΡΡ ΠΏΠΎΠ»ΡΠ°Π²ΡΠΎΠΌΠ°ΡΠΈΡΠ΅ΡΠΊΠΎΠ΅ ΡΡΡΡΠΎΠΉΡΡΠ²ΠΎ Ρ ΡΠΈΠΊΡΠ°ΡΠΈΠ΅ΠΉ ΡΡΠ΅ΠΏΠΊΠΈ ΡΠΊΠ²ΠΎΡΠ½Π΅ΠΌ. ΠΠ° ΡΠ°ΠΌΠ΅ ΡΡΠ³Π°ΡΠ° ΡΡΡΠ°Π½ΠΎΠ²Π»Π΅Π½Π° ΠΏΠ»ΠΈΡΠ° 2 Ρ ΡΠ°ΡΠ½ΠΈΡΠ½ΠΎ Π·Π°ΠΊΡΠ΅ΠΏΠ»Π΅Π½Π½ΡΠΌ Π½Π° Π½Π΅ΠΉ ΠΎΠΏΠΎΡΠ½ΡΠΌ ΠΊΡΡΠ³ΠΎΠΌ 3, ΠΈΠΌΠ΅ΡΡΠΈΠΌ ΡΡΡΡΠ΅ 4. ΠΠΏΠΎΡΠ½ΡΠΉ ΠΊΡΡΠ³ ΠΌΠΎΠΆΠ΅Ρ ΠΊΠ°ΡΠ°ΡΡΡΡ Π² ΠΏΡΠΎΠ΄ΠΎΠ»ΡΠ½ΠΎΠΉ ΠΈ ΠΏΠΎΠΏΠ΅ΡΠ΅ΡΠ½ΠΎΠΉ ΠΏΠ»ΠΎΡΠΊΠΎΡΡΡΡ . ΠΠ»Ρ ΠΎΡΠ»Π°Π±Π»Π΅Π½ΠΈΡ ΠΏΠΎΠΏΠ΅ΡΠ΅ΡΠ½ΡΡ ΠΊΠΎΠ»Π΅Π±Π°Π½ΠΈΠΉ ΠΈ ΠΏΠΎΡΠ»Π΅Π΄ΡΡΡΠ΅ΠΉ ΡΡΠ°Π±ΠΈΠ»ΠΈΠ·Π°ΡΠΈΠΈ ΠΏΠΎΠ»ΡΠΏΡΠΈΡΠ΅ΠΏΠ° Π² Π½ΠΎΡΠΌΠ°Π»ΡΠ½ΠΎΠΌ ΠΏΠΎΠ»ΠΎΠΆΠ΅Π½ΠΈΠΈ ΡΠ»ΡΠΆΠ°Ρ Π΄Π²Π΅ ΡΠΈΠ»ΠΈΠ½Π΄ΡΠΈΡΠ΅ΡΠΊΠΈΠ΅ ΠΏΡΡΠΆΠΈΠ½Ρ 5. Π ΡΠ΅Π½ΡΡΠ΅ ΠΎΠΏΠΎΡΠ½ΠΎΠ³ΠΎ ΠΊΡΡΠ³Π° Π½Π° ΠΏΠ°Π»ΡΡΠ°Ρ 7 ΡΠ°ΡΠ½ΠΈΡΠ½ΠΎ Π·Π°ΠΊΡΠ΅ΠΏΠ»Π΅Π½Ρ Π·Π°Ρ Π²Π°ΡΡ 6 ΡΠΊΠ²ΠΎΡΠ½Ρ, ΠΈΠΌΠ΅ΡΡΠΈΠ΅ ΡΠΊΠΎΡΡ Π² ΠΏΠ΅ΡΠ΅Π΄Π½Π΅ΠΉ ΡΠ°ΡΡΠΈ. Π‘ΠΊΠΎΡΡ Π² Π·Π°Π΄Π½Π΅ΠΉ ΡΠ°ΡΡΠΈ Π·Π°Ρ Π²Π°ΡΠΎΠ² ΡΠΎΠ²ΠΏΠ°Π΄Π°ΡΡ ΡΠΎ ΡΠΊΠΎΡΠ°ΠΌΠΈ ΡΡΡΡΡ ΠΎΠΏΠΎΡΠ½ΠΎΠ³ΠΎ ΠΊΡΡΠ³Π°.
Π ΠΈΡ. ΠΠΎΠ»ΡΠ°Π²ΡΠΎΠΌΠ°ΡΠΈΡΠ΅ΡΠΊΠΎΠ΅ ΠΎΠΏΠΎΡΠ½ΠΎ-ΡΡΠ΅ΠΏΠ½ΠΎΠ΅ ΡΡΡΡΠΎΠΉΡΡΠ²ΠΎ Ρ ΡΠΈΠΊΡΠ°ΡΠΈΠ΅ΠΉ ΡΡΠ΅ΠΏΠΊΠΈ ΡΠΊΠ²ΠΎΡΠ½Π΅ΠΌ
Π ΠΏΠ΅ΡΠ΅Π΄Π½Π΅ΠΉ ΡΠ°ΡΡΠΈ Π·Π°Ρ Π²Π°ΡΡ ΠΈΠΌΠ΅ΡΡ ΡΠ°ΡΠΎΠ½Π½ΡΠ΅ Π²ΡΡΠ΅Π·Ρ, Π² ΠΊΠΎΡΠΎΡΡΠ΅ Π²Π΄Π²ΠΈΠ³Π°Π΅ΡΡΡ Π·Π°ΠΌΠΎΠΊ 9. Π Π·Π°ΠΌΠΊΠ΅ ΠΈΠΌΠ΅Π΅ΡΡΡ ΡΡΠ΅ΡΠΆΠ΅Π½Ρ, Π½Π° ΠΊΠΎΡΠΎΡΡΠΉ Π½Π°Π΄Π΅ΡΡ ΠΏΡΡΠΆΠΈΠ½Π° 10 ΠΈ ΡΡΡΠ°Π³ 8 Π·Π°ΠΌΠΊΠ°, Π° ΡΠ°ΠΊΠΆΠ΅ ΠΏΡΠΎΠ΄ΠΎΠ»ΡΠ½ΡΠΉ Π²ΡΡΠ΅Π·, Π² ΠΊΠΎΡΠΎΡΡΠΉ Π²Ρ ΠΎΠ΄ΠΈΡ Π½Π°ΠΏΡΠ°Π²Π»ΡΡΡΠΈΠΉ ΠΏΠ°Π»Π΅Ρ, Π·Π°ΠΊΡΠ΅ΠΏΠ»Π΅Π½Π½ΡΠΉ Π² Π½ΠΈΠΆΠ½Π΅ΠΉ ΡΠ°ΡΡΠΈ ΠΎΠΏΠΎΡΠ½ΠΎΠ³ΠΎ ΠΊΡΡΠ³Π°. ΠΠΎΠ³Π΄Π° ΠΏΠΎΠ»ΡΠΏΡΠΈΡΠ΅ΠΏ ΡΡΠ΅ΠΏΠ»Π΅Π½ Ρ ΡΡΠ³Π°ΡΠΎΠΌ, Π·Π°Ρ Π²Π°ΡΡ 6 ΡΠ²Π΅Π΄Π΅Π½Ρ ΠΈ ΠΎΡ Π²Π°ΡΡΠ²Π°ΡΡ ΡΠΊΠ²ΠΎΡΠ΅Π½Ρ ΠΏΠΎΠ»ΡΠΏΡΠΈΡΠ΅ΠΏΠ°. Π ΡΡΠΎΠΌ ΡΠ»ΡΡΠ°Π΅ ΡΠ°ΡΡΠ΅ΠΏΠΊΠ° Π½Π΅Π²ΠΎΠ·ΠΌΠΎΠΆΠ½Π°, ΡΠ°ΠΊ ΠΊΠ°ΠΊ Π·Π°ΠΌΠΎΠΊ ΠΏΡΠ΅ΠΏΡΡΡΡΠ²ΡΠ΅Ρ ΠΏΠΎΠ²ΠΎΡΠΎΡΡ Π·Π°Ρ Π²Π°ΡΠΎΠ² Π½Π° ΠΏΠ°Π»ΡΡΠ°Ρ .
Π Π°ΡΡΠ΅ΠΏΠΊΠ° Π°Π²ΡΠΎΠΏΠΎΠ΅Π·Π΄Π° ΠΎΡΡΡΠ΅ΡΡΠ²Π»ΡΠ΅ΡΡΡ ΠΎΡΠ²ΠΎΠ΄ΠΎΠΌ Π² ΡΡΠΎΡΠΎΠ½Ρ ΠΏΠ»Π°Π½ΠΊΠΈ 1 ΠΏΡΠ΅Π΄ΠΎΡ ΡΠ°Π½ΠΈΡΠ΅Π»Ρ ΠΈ ΠΏΠ΅ΡΠ΅ΠΌΠ΅ΡΠ΅Π½ΠΈΠ΅ΠΌ Π·Π°ΠΌΠΊΠ° Π²ΠΏΠ΅ΡΠ΅Π΄ ΠΏΡΠΈ ΠΏΠΎΠΌΠΎΡΠΈ ΡΡΡΠ°Π³Π° β ΠΏΡΡΠΆΠΈΠ½Π° 10 ΡΠΆΠΈΠΌΠ°Π΅ΡΡΡ. ΠΠ°ΡΠ΅Π»ΠΊΠ° 11 ΡΠΏΠΈΡΠ°Π΅ΡΡΡ Π² Π²ΡΡΡΡΠΏ Π·Π°ΠΌΠΊΠ° ΠΈ ΡΠ΄Π΅ΡΠΆΠΈΠ²Π°Π΅Ρ Π΅Π³ΠΎ Π² ΠΏΠ΅ΡΠ΅Π΄Π½Π΅ΠΌ ΠΏΠΎΠ»ΠΎΠΆΠ΅Π½ΠΈΠΈ. ΠΡΠΈ ΡΠ°ΡΡΠ΅ΠΏΠΊΠ΅, ΠΊΠΎΠ³Π΄Π° ΡΡΠ³Π°Ρ Π΄Π²ΠΈΠΆΠ΅ΡΡΡ Π²ΠΏΠ΅ΡΠ΅Π΄, ΡΠΊΠ²ΠΎΡΠ΅Π½Ρ ΠΏΠΎΠ»ΡΠΏΡΠΈΡΠ΅ΠΏΠ° ΡΠ²ΠΎΠ±ΠΎΠ΄Π½ΠΎ Π²ΡΡ ΠΎΠ΄ΠΈΡ Π½Π°ΡΡΠΆΡ, ΡΠ°Π·Π΄Π²ΠΈΠ³Π°Ρ Π² ΡΡΠΎΡΠΎΠ½Ρ Π·Π°Ρ Π²Π°ΡΡ. ΠΠ°ΠΌΠΎΠΊ ΠΏΠΎΡΠ»Π΅ ΡΠ°ΡΡΠ΅ΠΏΠΊΠΈ Π²ΠΎΠ·Π²ΡΠ°ΡΠ°Π΅ΡΡΡ Π² ΠΏΠ΅ΡΠ²ΠΎΠ½Π°ΡΠ°Π»ΡΠ½ΠΎΠ΅ ΠΏΠΎΠ»ΠΎΠΆΠ΅Π½ΠΈΠ΅ ΠΈ Π±Π»ΠΎΠΊΠΈΡΡΠ΅Ρ Π·Π°Ρ Π²Π°ΡΡ.
ΠΠ΅ΡΠ΅Π΄ ΡΡΠ΅ΠΏΠΊΠΎΠΉ Π°Π²ΡΠΎΠΏΠΎΠ΅Π·Π΄Π° Π·Π°ΠΌΠΎΠΊ ΠΏΡΠΈ ΠΏΠΎΠΌΠΎΡΠΈ ΡΡΡΠ°Π³Π° ΠΏΠ΅ΡΠ΅ΠΌΠ΅ΡΠ°Π΅ΡΡΡ Π²ΠΏΠ΅ΡΠ΅Π΄, ΠΎΡΠ²ΠΎΠ±ΠΎΠΆΠ΄Π°Ρ Π·Π°Ρ Π²Π°ΡΡ. Π’ΡΠ³Π°Ρ ΠΏΠΎΠ΄Π°Π΅ΡΡΡ Π½Π°Π·Π°Π΄, ΠΈ ΡΠΊΠ²ΠΎΡΠ΅Π½Ρ ΠΏΠΎΠ»ΡΠΏΡΠΈΡΠ΅ΠΏΠ°, ΠΏΠΎΠΏΠ°Π΄Π°Ρ Π² ΡΡΡΡΠ΅ ΠΎΠΏΠΎΡΠ½ΠΎΠ³ΠΎ ΠΊΡΡΠ³Π°, Π½Π°ΠΆΠΈΠΌΠ°Π΅Ρ Π½Π° Π²Π½ΡΡΡΠ΅Π½Π½ΠΈΠ΅ ΡΠΊΠΎΡΡ Π·Π°Ρ Π²Π°ΡΠΎΠ², ΡΠ°Π·Π΄Π²ΠΈΠ³Π°Π΅Ρ ΠΈ ΡΡΡΠ°Π½Π°Π²Π»ΠΈΠ²Π°Π΅Ρ ΠΈΡ Π² ΡΠ°Π±ΠΎΡΠ΅Π΅ ΠΏΠΎΠ»ΠΎΠΆΠ΅Π½ΠΈΠ΅. ΠΠΎΡΠ»Π΅ ΡΡΠΎΠ³ΠΎ Π·Π°ΠΌΠΎΠΊ Π°Π²ΡΠΎΠΌΠ°ΡΠΈΡΠ΅ΡΠΊΠΈ Π²ΠΎΠ·Π²ΡΠ°ΡΠ°Π΅ΡΡΡ Π½Π°Π·Π°Π΄ Ρ Π·Π°Π΄ΠΈΡΠ°Π΅Ρ ΡΡΠ΅ΠΏΠ½ΠΎΠ΅ ΡΡΡΡΠΎΠΉΡΡΠ²ΠΎ. ΠΠ°ΡΠ΅ΠΌ ΠΎΠΏΡΡΠΊΠ°ΡΡ ΠΏΠ»Π°Π½ΠΊΡ 7, ΠΏΡΠ΅Π΄ΡΠΏΡΠ΅ΠΆΠ΄Π°Ρ ΡΠ΅ΠΌ ΡΠ°ΠΌΡΠΌ Π²ΠΎΠ·ΠΌΠΎΠΆΠ½ΠΎΡΡΡ ΠΎΡΠ΅Π²ΠΎΠ³ΠΎ ΠΏΠ΅ΡΠ΅ΠΌΠ΅ΡΠ΅Π½ΠΈΡ Π·Π°ΠΌΠΊΠ° ΠΈ, ΡΠ»Π΅Π΄ΠΎΠ²Π°ΡΠ΅Π»ΡΠ½ΠΎ, ΡΠ°ΡΡΠ΅ΠΏΠΊΡ Π°Π²ΡΠΎΠΏΠΎΠ΅Π·Π΄Π° Π² ΠΏΡΡΠΈ.
Π¦ΠΈΠ»ΠΈΠ½Π΄ΡΠΈΡΠ΅ΡΠΊΠΈΠΉ ΡΠΊΠ²ΠΎΡΠ΅Π½Ρ ΠΏΠΎΠ»ΡΠΏΡΠΈΡΠ΅ΠΏΠ° Π² Π½ΠΈΠΆΠ½Π΅ΠΉ ΡΠ°ΡΡΠΈ ΠΈΠΌΠ΅Π΅Ρ ΡΠ»Π°Π½Π΅Ρ, ΠΏΡΠ΅ΠΏΡΡΡΡΠ²ΡΡΡΠΈΠΉ Π²ΡΡ ΠΎΠ΄Ρ ΡΠΊΠ²ΠΎΡΠ½Ρ ΠΈΠ· Π·Π°ΠΌΠΊΠ° ΠΏΡΠΈ ΠΎΡΠ½ΠΎΡΠΈΡΠ΅Π»ΡΠ½ΡΡ Π²Π΅ΡΡΠΈΠΊΠ°Π»ΡΠ½ΡΡ ΠΏΠ΅ΡΠ΅ΠΌΠ΅ΡΠ΅Π½ΠΈΡΡ Π·Π²Π΅Π½ΡΠ΅Π² Π°Π²ΡΠΎΠΏΠΎΠ΅Π·Π΄Π°.
ustroistvo-avtomobilya.ru
ΠΠΎΠ½ΡΡΡΡΠΊΡΠΈΠΈ ΡΡΠ³ΠΎΠ²ΠΎ-ΡΡΠ΅ΠΏΠ½ΡΡ ΡΡΡΡΠΎΠΉΡΡΠ² β ΠΡΠ½ΠΎΠ²Π½ΡΠ΅ ΡΡΠ΅Π΄ΡΡΠ²Π°
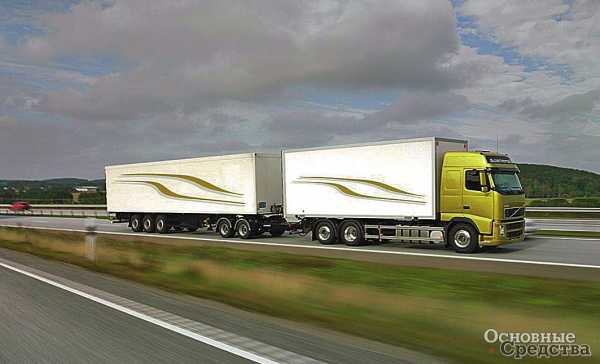
Π. ΠΠ°ΡΠΈΠ»ΡΠ΅Π², ΡΠΎΡΠΎ ΠΈΠ· Π°ΡΡ ΠΈΠ²Π° Π°Π²ΡΠΎΡΠ°
Π Π°Π²ΡΠΎΠΏΠΎΠ΅Π·Π΄Π°Ρ Π΄Π»Ρ ΡΠ°ΡΠ½ΠΈΡΠ½ΠΎΠ³ΠΎ ΡΠΎΠ΅Π΄ΠΈΠ½Π΅Π½ΠΈΡ ΡΡΠ³Π°ΡΠ° ΠΈ ΠΏΡΠΈΡΠ΅ΠΏΠ° ΠΈ Π²ΠΎΠ·ΠΌΠΎΠΆΠ½ΠΎΡΡΠΈ ΠΈΡ Π±ΡΡΡΡΠΎΠΉ ΡΡΠ΅ΠΏΠΊΠΈ-ΡΠ°ΡΡΠ΅ΠΏΠΊΠΈ, Π° ΡΠ°ΠΊΠΆΠ΅ ΠΏΠ΅ΡΠ΅Π΄Π°ΡΠΈ Π²Π΅ΡΡΠΈΠΊΠ°Π»ΡΠ½ΠΎΠΉ ΠΈ ΠΏΡΠΎΠ΄ΠΎΠ»ΡΠ½ΠΎΠΉ Π½Π°Π³ΡΡΠ·ΠΎΠΊ ΠΈΡΠΏΠΎΠ»ΡΠ·ΡΡΡΡΡ ΡΡΠ³ΠΎΠ²ΠΎ-ΡΡΠ΅ΠΏΠ½ΡΠ΅ ΡΡΡΡΠΎΠΉΡΡΠ²Π° ΡΠ°Π·Π»ΠΈΡΠ½ΠΎΠΉ ΠΊΠΎΠ½ΡΡΡΡΠΊΡΠΈΠΈ.
ΠΡΠΏΡΡΠΊΠΎΠΌ ΡΡΠ³ΠΎΠ²ΠΎ-ΡΡΠ΅ΠΏΠ½ΡΡ ΡΡΡΡΠΎΠΉΡΡΠ² (Π’Π‘Π£) Π·Π°Π½ΠΈΠΌΠ°Π΅ΡΡΡ Π·Π½Π°ΡΠΈΡΠ΅Π»ΡΠ½ΠΎΠ΅ ΡΠΈΡΠ»ΠΎ ΠΊΠΎΠΌΠΏΠ°Π½ΠΈΠΉ-ΠΈΠ·Π³ΠΎΡΠΎΠ²ΠΈΡΠ΅Π»Π΅ΠΉ, ΡΡΠ΅Π΄ΠΈ ΠΊΠΎΡΠΎΡΡΡ ΡΠ°ΠΌΡΠ΅ ΠΈΠ·Π²Π΅ΡΡΠ½ΡΠ΅ Jost, Rockinger (c 2001 Π³. Π²Ρ ΠΎΠ΄ΠΈΡ Π² ΡΠΎΡΡΠ°Π² Jost. β ΠΡΠΈΠΌ. ΡΠ΅Π΄.), Ringfeder (Ρ 1997 Π³. Π²Ρ ΠΎΠ΄ΠΈΡ Π² ΡΠΎΡΡΠ°Π² VBG β ΠΡΠΈΠΌ. ΡΠ΅Π΄.), Helmut Buer GmbH & Co. KG (ΠΠ΅ΡΠΌΠ°Π½ΠΈΡ), Georg Fisher (Π¨Π²Π΅ΠΉΡΠ°ΡΠΈΡ), Coder Ture (Π€ΡΠ°Π½ΡΠΈΡ), V. Orlandi (ΠΡΠ°Π»ΠΈΡ), VBG (Π¨Π²Π΅ΡΠΈΡ), York (ΠΠ΅Π»ΠΈΠΊΠΎΠ±ΡΠΈΡΠ°Π½ΠΈΡ), Fontaine Truck Equipment, SAF-Holland, Utility Trailer (Π‘Π¨Π) ΠΈ Π΄Ρ. Π ΡΡΠΎΡ ΡΠΏΠΈΡΠΎΠΊ Π½Π°Π΄ΠΎ Π΄ΠΎΠ±Π°Π²ΠΈΡΡ ΠΈ ΡΠΎΡΡΠΈΠΉΡΠΊΠΈΡ ΠΏΡΠΎΠΈΠ·Π²ΠΎΠ΄ΠΈΡΠ΅Π»Π΅ΠΉ.
Π’ΡΠ³ΠΎΠ²ΠΎ-ΡΡΠ΅ΠΏΠ½ΡΠ΅ ΡΡΡΡΠΎΠΉΡΡΠ²Π° ΡΠ°ΡΡΡΠΈΡΠ°Π½Ρ Π½Π° ΠΏΠ΅ΡΠ΅Π΄Π°ΡΡ Π±ΠΎΠ»ΡΡΠΈΡ ΠΏΡΠΎΠ΄ΠΎΠ»ΡΠ½ΡΡ ΠΈ Π½Π΅Π·Π½Π°ΡΠΈΡΠ΅Π»ΡΠ½ΡΡ Π²Π΅ΡΡΠΈΠΊΠ°Π»ΡΠ½ΡΡ ΡΠΈΠ», ΠΊΠΎΡΠΎΡΡΠ΅ Π½Π΅ Π΄ΠΎΠ»ΠΆΠ½Ρ ΠΏΡΠ΅Π²ΡΡΠ°ΡΡ 10β¦15 ΠΊΠ. ΠΡΠΎ ΡΠ²Π»ΡΠ΅ΡΡΡ ΠΈΡ Π³Π»Π°Π²Π½ΠΎΠΉ ΡΡΠ½ΠΊΡΠΈΠΎΠ½Π°Π»ΡΠ½ΠΎΠΉ ΠΎΡΠΎΠ±Π΅Π½Π½ΠΎΡΡΡΡ. Π’Π°ΠΊΠΈΠ΅ ΠΌΠ΅Ρ Π°Π½ΠΈΠ·ΠΌΡ Π΄ΠΎΠ»ΠΆΠ½Ρ Π±ΡΡΡ Π²ΡΡΠΎΠΊΠΎΠ½Π°Π΄Π΅ΠΆΠ½ΡΠΌΠΈ, ΠΎΠ±Π΅ΡΠΏΠ΅ΡΠΈΠ²Π°ΡΡ ΡΠΎΠΎΡΠ²Π΅ΡΡΡΠ²ΡΡΡΠΈΠ΅ ΡΠ³Π»Ρ ΡΠΊΠ»Π°Π΄ΡΠ²Π°Π½ΠΈΡ Π°Π²ΡΠΎΠΏΠΎΠ΅Π·Π΄Π°, Π²ΠΎΠ·ΠΌΠΎΠΆΠ½ΠΎΡΡΡ Π±ΡΡΡΡΠΎΠΉ ΠΈ Π±Π΅Π·ΠΎΠΏΠ°ΡΠ½ΠΎΠΉ ΡΡΠ΅ΠΏΠΊΠΈ-ΡΠ°ΡΡΠ΅ΠΏΠΊΠΈ, Π°ΠΌΠΎΡΡΠΈΠ·Π°ΡΠΈΡ Π΄ΠΈΠ½Π°ΠΌΠΈΡΠ΅ΡΠΊΠΈΡ Π½Π°Π³ΡΡΠ·ΠΎΠΊ Π²ΠΎ Π²ΡΠ΅ΠΌΡ Π΄Π²ΠΈΠΆΠ΅Π½ΠΈΡ Π°Π²ΡΠΎΠΏΠΎΠ΅Π·Π΄Π°. ΠΡΠΈΠ½ΡΠΈΠΏΠΈΠ°Π»ΡΠ½ΠΎ Π’Π‘Π£ ΡΠΎΡΡΠΎΡΡ ΠΈΠ· ΡΠ°Π·ΡΠ΅ΠΌΠ½ΠΎ-ΡΡΠ΅ΠΏΠ½ΠΎΠ³ΠΎ ΠΈ Π°ΠΌΠΎΡΡΠΈΠ·Π°ΡΠΈΠΎΠ½Π½ΠΎ-ΠΏΠΎΠ³Π»ΠΎΡΠ°ΡΡΠ΅Π³ΠΎ ΠΌΠ΅Ρ Π°Π½ΠΈΠ·ΠΌΠΎΠ², Π° ΡΠ°ΠΊΠΆΠ΅ ΡΠ»Π΅ΠΌΠ΅Π½ΡΠΎΠ² ΠΊΡΠ΅ΠΏΠ»Π΅Π½ΠΈΡ. ΠΠΎΠ½ΡΡΠ½ΠΎ, ΡΡΠΎ ΠΊΠΎΠ½ΡΡΡΡΠΊΡΠΈΠ²Π½ΠΎΠ΅ ΠΈΡΠΏΠΎΠ»Π½Π΅Π½ΠΈΠ΅ ΡΡΠ³ΠΎΠ²ΠΎ-ΡΡΠ΅ΠΏΠ½ΡΡ ΡΡΡΡΠΎΠΉΡΡΠ² ΡΡΡΠ΅ΡΡΠ²Π΅Π½Π½ΠΎ Π²Π»ΠΈΡΠ΅Ρ Π½Π° ΡΠ°ΠΊΠΈΠ΅ Π²Π°ΠΆΠ½Π΅ΠΉΡΠΈΠ΅ ΡΠΊΡΠΏΠ»ΡΠ°ΡΠ°ΡΠΈΠΎΠ½Π½ΡΠ΅ ΠΊΠ°ΡΠ΅ΡΡΠ²Π° Π°Π²ΡΠΎΠΏΠΎΠ΅Π·Π΄Π°, ΠΊΠ°ΠΊ ΡΠΏΡΠ°Π²Π»ΡΠ΅ΠΌΠΎΡΡΡ, ΠΊΡΡΡΠΎΠ²Π°Ρ ΡΡΡΠΎΠΉΡΠΈΠ²ΠΎΡΡΡ, ΠΌΠ°Π½Π΅Π²ΡΠ΅Π½Π½ΠΎΡΡΡ, ΠΏΠ»Π°Π²Π½ΠΎΡΡΡ Ρ ΠΎΠ΄Π°, ΠΏΡΠΎΡ ΠΎΠ΄ΠΈΠΌΠΎΡΡΡ, Π½Π°Π΄Π΅ΠΆΠ½ΠΎΡΡΡ ΠΈ Π±Π΅Π·ΠΎΠΏΠ°ΡΠ½ΠΎΡΡΡ.
ΠΠΎ ΡΠΈΠΏΡ ΡΠ°Π·ΡΠ΅ΠΌΠ½ΠΎ-ΡΡΠ΅ΠΏΠ½ΠΎΠ³ΠΎ ΠΌΠ΅Ρ Π°Π½ΠΈΠ·ΠΌΠ° Π’Π‘Π£ ΠΏΠΎΠ΄ΡΠ°Π·Π΄Π΅Π»ΡΡΡ Π½Π° ΡΡΠΈ ΠΎΡΠ½ΠΎΠ²Π½ΡΡ ΡΠΈΠΏΠ°: ΠΊΡΡΠΊΠΎΠ²ΡΠ΅ (ΠΏΠ°ΡΠ° ΠΊΡΡΠΊβΠΏΠ΅ΡΠ»Ρ), Π²ΠΈΠ»ΠΎΡΠ½ΡΠ΅ ΠΈΠ»ΠΈ ΡΠΊΠ²ΠΎΡΠ½Π΅Π²ΡΠ΅ (ΠΏΠ°ΡΠ° ΡΠΊΠ²ΠΎΡΠ΅Π½ΡβΠΏΠ΅ΡΠ»Ρ) ΠΈ ΡΠ°ΡΠΎΠ²ΡΠ΅ (ΠΏΠ°ΡΠ° ΡΠ°ΡβΠΏΠΎΠ»ΡΡΡΠ΅ΡΠ°). ΠΡΡΠ³ΠΈΠ΅ ΡΠ°Π·Π½ΠΎΠ²ΠΈΠ΄Π½ΠΎΡΡΠΈ Π·Π½Π°ΡΠΈΡΠ΅Π»ΡΠ½ΠΎΠ³ΠΎ ΡΠ°ΡΠΏΡΠΎΡΡΡΠ°Π½Π΅Π½ΠΈΡ Π² ΠΊΠΎΠΌΠΌΠ΅ΡΡΠ΅ΡΠΊΠΎΠΌ Π°Π²ΡΠΎΡΡΠ°Π½ΡΠΏΠΎΡΡΠ΅ Π½Π΅ Π½Π°ΡΠ»ΠΈ, Π° ΠΏΠΎΡΠΎΠΌΡ Π½Π΅ ΡΠ°ΡΡΠΌΠ°ΡΡΠΈΠ²Π°ΡΡΡΡ.
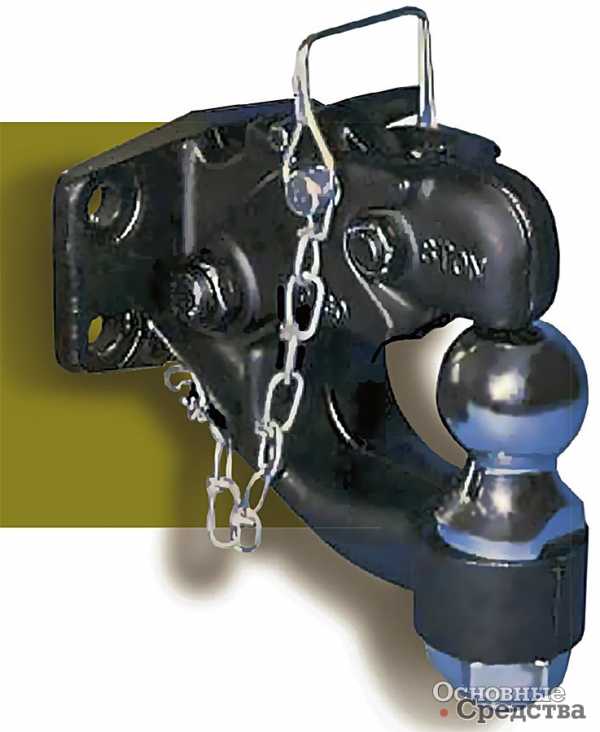
Π’Π‘Π£ ΡΠ°ΡΠΎΠ²ΠΎΠ³ΠΎ ΡΠΈΠΏΠ°
Π’ΡΠ³ΠΎΠ²ΠΎ-ΡΡΠ΅ΠΏΠ½ΡΠ΅ ΡΡΡΡΠΎΠΉΡΡΠ²Π° ΡΠΈΠΏΠ° ΡΠ°ΡβΠΏΠΎΠ»ΡΡΡΠ΅ΡΠ° (ΡΠ°ΡβΠΏΠ΅ΡΠ»Ρ) Π½Π΅ΡΠ΅Π΄ΠΊΠΎ, Ρ ΠΎΡΡ ΠΈ Π½Π΅ΡΠΊΠΎΠ»ΡΠΊΠΎ ΠΎΡΠΈΠ±ΠΎΡΠ½ΠΎ Π½Π°Π·ΡΠ²Π°ΡΡ ΡΠ°ΡΠΊΠΎΠΏΠ°ΠΌΠΈ. ΠΠ½ΠΈ ΡΠ»ΡΠΆΠ°Ρ Π΄Π»Ρ Π±ΡΠΊΡΠΈΡΠΎΠ²ΠΊΠΈ ΡΡΠ°Π½ΡΠΏΠΎΡΡΠ½ΡΠΌ ΡΡΠ΅Π΄ΡΡΠ²ΠΎΠΌ ΠΊΠ°ΡΠ°Π²Π°Π½ΠΎΠ² ΠΈ Π»Π΅Π³ΠΊΠΈΡ ΠΏΡΠΈΡΠ΅ΠΏΠΎΠ² ΠΏΠΎΠ»Π½ΠΎΠΉ ΠΌΠ°ΡΡΠΎΠΉ Π΄ΠΎ 3,5 Ρ. ΠΠΎΠ½ΡΡΡΡΠΊΡΠΈΠ²Π½ΠΎ ΡΠ°ΠΊΠΈΠ΅ ΠΌΠ΅Ρ Π°Π½ΠΈΠ·ΠΌΡ Π²ΡΠΏΠΎΠ»Π½Π΅Π½Ρ Π² Π²ΠΈΠ΄Π΅ ΠΎΠ΄Π½ΠΎΠΎΡΠ½ΡΡ ΠΏΡΠΈΡΠ΅ΠΏΠΎΠ² ΠΈΠ»ΠΈ ΠΏΡΠΈΡΠ΅ΠΏΠΎΠ² ΡΠΎ ΡΠ΄Π²ΠΎΠ΅Π½Π½ΠΎΠΉ ΠΈΠ»ΠΈ ΡΡΠ΅Ρ ΠΎΡΠ½ΠΎΠΉ ΡΠ΅Π½ΡΡΠ°Π»ΡΠ½ΠΎ ΡΠ°ΡΠΏΠΎΠ»ΠΎΠΆΠ΅Π½Π½ΠΎΠΉ ΡΠ΅Π»Π΅ΠΆΠΊΠΎΠΉ. ΠΠ±ΡΡΠ½ΠΎ Π² ΡΠΎΠ»ΠΈ ΡΡΠ³Π°ΡΠ΅ΠΉ Π²ΡΡΡΡΠΏΠ°ΡΡ Π»Π΅Π³ΠΊΠΎΠ²ΡΠ΅ Π°Π²ΡΠΎΠΌΠΎΠ±ΠΈΠ»ΠΈ, ΠΏΠΈΠΊΠ°ΠΏΡ, ΠΌΠΈΠΊΡΠΎΠ°Π²ΡΠΎΠ±ΡΡΡ ΠΈ ΠΌΠ°Π»ΠΎΡΠΎΠ½Π½Π°ΠΆΠ½ΡΠ΅ Π³ΡΡΠ·ΠΎΠ²ΠΈΠΊΠΈ. ΠΡΠ΅ ΡΡΠ΅Π±ΠΎΠ²Π°Π½ΠΈΡ ΠΊ Π’Π‘Π£ ΡΡΠΎΠ³ΠΎ ΡΠΈΠΏΠ° ΠΈΠ·Π»ΠΎΠΆΠ΅Π½Ρ Π² ΡΡΠ°Π½Π΄Π°ΡΡΠ΅ ISO 1103 ΠΈ ΡΠΎΠΎΡΠ²Π΅ΡΡΡΠ²ΡΡΡΠΈΡ ΠΎΡΠ΅ΡΠ΅ΡΡΠ²Π΅Π½Π½ΡΡ ΠΠΠ‘Π’ 28248β89, ΠΠΠ‘Π’ 30600β97 ΠΈ ΠΠ‘Π’ 37.001.096β84.
ΠΠ° Π°Π²ΡΠΎΠΌΠΎΠ±ΠΈΠ»Π΅-ΡΡΠ³Π°ΡΠ΅ ΡΡΡΠ°Π½Π°Π²Π»ΠΈΠ²Π°Π΅ΡΡΡ ΡΡΠ΅ΠΏΠ½ΠΎΠΉ ΡΠ°Ρ (ΠΠΠ‘Π’ 28248 ΠΏΡΠ΅Π΄ΡΡΠΌΠ°ΡΡΠΈΠ²Π°Π΅Ρ Π΅Π΄ΠΈΠ½ΡΡΠ²Π΅Π½Π½ΡΠΉ Π΄ΠΈΠ°ΠΌΠ΅ΡΡ ΡΠ°ΡΠ° β 50 ΠΌΠΌ), Π° Π½Π° Π΄ΡΡΠ»Π΅ Π±ΡΠΊΡΠΈΡΡΠ΅ΠΌΠΎΠ³ΠΎ ΠΏΡΠΈΡΠ΅ΠΏΠ° ΠΌΠΎΠ½ΡΠΈΡΡΠ΅ΡΡΡ ΠΎΡΠ²Π΅ΡΠ½Π°Ρ ΡΡΠ΅ΠΏΠ½Π°Ρ Π³ΠΎΠ»ΠΎΠ²ΠΊΠ° (ΡΡΠ΅ΡΠ°). ΠΠ°ΠΆΠ½ΡΠΌ ΠΌΠΎΠΌΠ΅Π½ΡΠΎΠΌ Π΄Π»Ρ Π²ΡΠ΅ΠΉ ΠΊΠΎΠ½ΡΡΡΡΠΊΡΠΈΠΈ Π’Π‘Π£ ΡΠ²Π»ΡΠ΅ΡΡΡ ΠΊΡΠ΅ΠΏΠ»Π΅Π½ΠΈΠ΅ Π΅Π³ΠΎ ΠΊ ΡΠ°ΠΊΠΈΠΌ ΡΠ»Π΅ΠΌΠ΅Π½ΡΠ°ΠΌ ΠΊΡΠ·ΠΎΠ²Π° ΠΈΠ»ΠΈ ΡΠ°ΠΌΡ ΡΡΠ³Π°ΡΠ°, ΠΊΠΎΡΠΎΡΡΠ΅ Π²ΡΠ΄Π΅ΡΠΆΠ°Ρ Π½Π΅ΠΎΠ±Ρ ΠΎΠ΄ΠΈΠΌΠΎΠ΅ ΡΠΈΡΠ»ΠΎ ΡΠΈΠΊΠ»ΠΎΠ² Π½Π°Π³ΡΡΠΆΠ΅Π½ΠΈΠΉ ΠΏΠ΅ΡΠΈΠΎΠ΄ΠΈΡΠ΅ΡΠΊΠΈΠΌΠΈ Π½Π°Π³ΡΡΠ·ΠΊΠ°ΠΌΠΈ ΠΈ ΠΏΡΠ΅Π΄Π΅Π»ΡΠ½ΡΠ΅ ΡΡΠ°ΡΠΈΡΠ΅ΡΠΊΠΈΠ΅ Π½Π°Π³ΡΡΠ·ΠΊΠΈ. Π‘Π»Π΅Π΄ΠΎΠ²Π°ΡΠ΅Π»ΡΠ½ΠΎ, Π΄ΠΎΡΡΠ°ΡΠΎΡΠ½Π°Ρ Π½Π΅ΡΡΡΠ°Ρ ΡΠΏΠΎΡΠΎΠ±Π½ΠΎΡΡΡ Π’Π‘Π£ ΠΎΠΏΡΠ΅Π΄Π΅Π»ΡΠ΅ΡΡΡ ΠΏΡΠ°Π²ΠΈΠ»ΡΠ½ΡΠΌ Π²ΡΠ±ΠΎΡΠΎΠΌ Π΅Π³ΠΎ ΠΊΠΎΠ½ΡΡΡΡΠΊΡΠΈΠ²Π½ΡΡ ΡΠ°Π·ΠΌΠ΅ΡΠΎΠ², Ρ. Π΅. ΡΠΎΠΎΡΠ²Π΅ΡΡΡΠ²ΠΈΠ΅ΠΌ ΠΏΡΠΎΡΠ½ΠΎΡΡΠΈ ΡΡΡΡΠΎΠΉΡΡΠ²Π° Π½Π°Π³ΡΡΠ·ΠΊΠ°ΠΌ, Π²ΠΎΠ·Π΄Π΅ΠΉΡΡΠ²ΡΡΡΠΈΠΌ Π½Π° Π½Π΅Π³ΠΎ Π² ΠΏΡΠΎΡΠ΅ΡΡΠ΅ ΡΠΊΡΠΏΠ»ΡΠ°ΡΠ°ΡΠΈΠΈ. Π’Π‘Π£ ΡΠ°ΡΠΎΠ²ΠΎΠ³ΠΎ ΡΠΈΠΏΠ° ΡΠΎΠ³Π»Π°ΡΠ½ΠΎ ΡΡΠ΅Π±ΠΎΠ²Π°Π½ΠΈΡΠΌ ΡΡΠ°Π½Π΄Π°ΡΡΠΎΠ² Π΄ΠΎΠ»ΠΆΠ½Ρ ΠΈΡΠΏΡΡΡΠ²Π°ΡΡΡΡ Π½Π° ΡΡΡΠ°Π»ΠΎΡΡΠ½ΡΡ ΠΏΡΠΎΡΠ½ΠΎΡΡΡ ΠΊΠΎΠ½ΡΡΡΡΠΊΡΠΈΠΈ. ΠΠΎΠΌΠΈΠΌΠΎ ΠΌΠ΅Ρ Π°Π½ΠΈΡΠ΅ΡΠΊΠΎΠ³ΠΎ ΡΠΎΠ΅Π΄ΠΈΠ½Π΅Π½ΠΈΡ ΡΡΠ³ΠΎΠ²ΠΎ-ΡΡΠ΅ΠΏΠ½ΠΎΠ΅ ΡΡΡΡΠΎΠΉΡΡΠ²ΠΎ ΠΎΠ±Π΅ΡΠΏΠ΅ΡΠΈΠ²Π°Π΅Ρ ΡΠ»Π΅ΠΊΡΡΠΈΡΠ΅ΡΠΊΠΎΠ΅ ΡΠΎΠ΅Π΄ΠΈΠ½Π΅Π½ΠΈΠ΅ ΡΠ»Π΅ΠΊΡΡΠΎΠΎΠ±ΠΎΡΡΠ΄ΠΎΠ²Π°Π½ΠΈΡ ΡΡΠ³ΠΎΠ²ΠΎΠ³ΠΎ Π°Π²ΡΠΎΠΌΠΎΠ±ΠΈΠ»Ρ Ρ ΠΎΠ±ΠΎΡΡΠ΄ΠΎΠ²Π°Π½ΠΈΠ΅ΠΌ Π±ΡΠΊΡΠΈΡΡΠ΅ΠΌΠΎΠ³ΠΎ ΠΏΡΠΈΡΠ΅ΠΏΠ°.
ΠΡΠΊΡΠΈΡΡΠ΅ΠΌΡΠ΅ ΠΏΡΠΈΡΠ΅ΠΏΡ Π΄Π΅Π»ΡΡΡΡ Π½Π° Π»Π΅Π³ΠΊΠΈΠ΅ ΠΈ ΡΡΠΆΠ΅Π»ΡΠ΅ β ΡΠ°Π·ΡΠ΅ΡΠ΅Π½Π½ΠΎΠΉ ΠΌΠ°ΠΊΡΠΈΠΌΠ°Π»ΡΠ½ΠΎΠΉ ΠΌΠ°ΡΡΠΎΠΉ ΡΠΎΠΎΡΠ²Π΅ΡΡΡΠ²Π΅Π½Π½ΠΎ Π½Π΅ Π±ΠΎΠ»Π΅Π΅ 750 ΠΈ ΡΠ²ΡΡΠ΅ 750 ΠΊΠ³. ΠΠΎ ΡΠΈΠΏΡ ΡΠ°ΡΠ° ΠΈ ΠΊΡΠ΅ΠΏΠ»Π΅Π½ΠΈΡ Π’Π‘Π£ ΡΠ°ΡΠΎΠ²ΠΎΠ³ΠΎ ΡΠΈΠΏΠ° ΡΠ°Π·Π»ΠΈΡΠ°ΡΡΡΡ ΠΏΠΎ ΠΈΡΠΏΠΎΠ»Π½Π΅Π½ΠΈΡΠΌ β Π, Π, Π‘, F, G, H ΠΈ N. ΠΠ°Π»ΠΎΡΠΎΠ½Π½Π°ΠΆΠ½ΡΠ΅ Β«Π‘ΠΎΠ±ΠΎΠ»ΠΈΒ», Β«ΠΠΠΠ΅Π»ΠΈΒ» ΠΈ Β«ΠΡΡΠΊΠΈΒ» Π² Π±ΠΎΠ»ΡΡΠΈΠ½ΡΡΠ²Π΅ ΡΠ»ΡΡΠ°Π΅Π² ΠΊΠΎΠΌΠΏΠ»Π΅ΠΊΡΡΡΡ Π’Π‘Π£ ΡΠΈΠΏΠ° F Π³ΡΡΠ·ΠΎΠΏΠΎΠ΄ΡΠ΅ΠΌΠ½ΠΎΡΡΡΡ Π΄ΠΎ 2 Ρ, ΠΎΡΠ½Π°ΡΠ΅Π½Π½ΡΠΌ ΠΊΠΎΠ²Π°Π½ΡΠΌ ΡΠ°ΡΠΎΠΌ Ρ Π΄Π²ΡΠΌΡ ΠΊΡΠ΅ΠΏΠ΅ΠΆΠ½ΡΠΌΠΈ ΠΎΡΠ²Π΅ΡΡΡΠΈΡΠΌΠΈ.
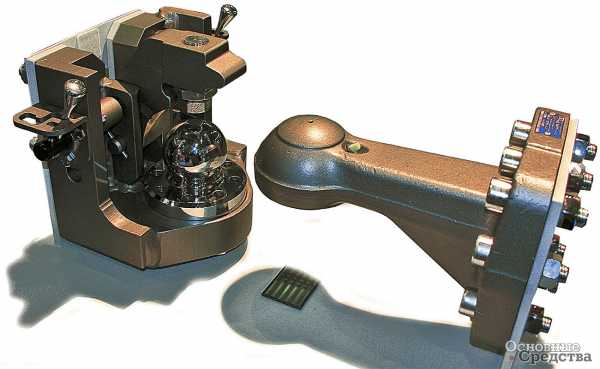
Π’Π‘Π£ ΠΊΡΡΠΊΠΎΠ²ΠΎΠ³ΠΎ ΡΠΈΠΏΠ°
Π Π½Π°ΡΠ΅ΠΉ ΡΡΡΠ°Π½Π΅ ΡΡΡΡΠΎΠΉΡΡΠ²Π° ΡΠΈΠΏΠ° Β«ΠΊΡΡΠΊβΠΏΠ΅ΡΠ»ΡΒ» Π²Π²ΠΈΠ΄Ρ Π΄Π°Π»Π΅ΠΊΠΎ Π½Π΅ ΠΎΠΏΡΠΈΠΌΠ°Π»ΡΠ½ΡΡ Π΄ΠΎΡΠΎΠΆΠ½ΡΡ ΡΡΠ»ΠΎΠ²ΠΈΠΉ ΠΏΡΠΈΠΌΠ΅Π½ΡΡΡ Π½Π°ΠΈΠ±ΠΎΠ»Π΅Π΅ ΡΠΈΡΠΎΠΊΠΎ. Π’Π°ΠΊΠΈΠ΅ Π’Π‘Π£ ΠΎΡΠ»ΠΈΡΠ°ΡΡΡΡ ΠΏΡΠΎΡΡΠΎΡΠΎΠΉ ΠΊΠΎΠ½ΡΡΡΡΠΊΡΠΈΠΈ, Π»Π΅Π³ΠΊΠΎΡΡΡΡ Π² ΠΈΠ·Π³ΠΎΡΠΎΠ²Π»Π΅Π½ΠΈΠΈ, ΠΎΡΠ½ΠΎΡΠΈΡΠ΅Π»ΡΠ½ΠΎ ΠΌΠ°Π»ΠΎΠΉ ΠΌΠ°ΡΡΠΎΠΉ ΠΈ Π±ΠΎΠ»ΡΡΠΈΠΌΠΈ ΡΠ³Π»Π°ΠΌΠΈ Π³ΠΈΠ±ΠΊΠΎΡΡΠΈ. ΠΠΎΡΠ»Π΅Π΄Π½Π΅Π΅ ΠΎΠ±ΡΡΠΎΡΡΠ΅Π»ΡΡΡΠ²ΠΎ Π΄Π΅Π»Π°Π΅Ρ ΠΈΡ Π½Π΅Π·Π°ΠΌΠ΅Π½ΠΈΠΌΡΠΌΠΈ ΠΏΡΠΈ Π΄Π²ΠΈΠΆΠ΅Π½ΠΈΠΈ Π°Π²ΡΠΎΠΏΠΎΠ΅Π·Π΄ΠΎΠ² Π² ΡΡΠΆΠ΅Π»ΡΡ Π΄ΠΎΡΠΎΠΆΠ½ΡΡ ΡΡΠ»ΠΎΠ²ΠΈΡΡ ΠΈ Π½Π° ΠΌΠ΅ΡΡΠ½ΠΎΡΡΠΈ Ρ ΡΠ°Π·Π½ΠΎΠΎΠ±ΡΠ°Π·Π½ΡΠΌ ΡΠ΅Π»ΡΠ΅ΡΠΎΠΌ. ΠΠΏΠΈΡΠ°Π½Π½Π°Ρ ΠΊΠΎΠ½ΡΡΡΡΠΊΡΠΈΡ ΠΏΠΎΠ΄ΡΠ°Π·ΡΠΌΠ΅Π²Π°Π΅Ρ Π½Π°Π»ΠΈΡΠΈΠ΅ Π±ΠΎΠ»ΡΡΠΈΡ Π·Π°Π·ΠΎΡΠΎΠ² (Π΄ΠΎ 10 ΠΌΠΌ) Π² ΡΠΎΠ΅Π΄ΠΈΠ½Π΅Π½ΠΈΠΈ ΠΊΡΡΠΊβΠΏΠ΅ΡΠ»Ρ Π΄Π»Ρ ΠΎΠ±Π»Π΅Π³ΡΠ΅Π½ΠΈΡ ΡΡΠ΅ΠΏΠΊΠΈ-ΡΠ°ΡΡΠ΅ΠΏΠΊΠΈ. ΠΡΠΈ Π·Π°Π·ΠΎΡΡ ΠΏΡΠΈΠ²ΠΎΠ΄ΡΡ ΠΊ ΠΏΠΎΠ²ΡΡΠ΅Π½ΠΈΡ Π΄ΠΈΠ½Π°ΠΌΠΈΡΠ΅ΡΠΊΠΈΡ Π½Π°Π³ΡΡΠ·ΠΎΠΊ ΠΈ ΠΈΠ½ΡΠ΅Π½ΡΠΈΠ²Π½ΠΎΠΌΡ ΠΈΠ·Π½Π°ΡΠΈΠ²Π°Π½ΠΈΡ Π΄Π΅ΡΠ°Π»Π΅ΠΉ ΡΡΡΡΠΎΠΉΡΡΠ²Π° (ΡΠΎΠΏΡΡΠΆΠ΅Π½Π½ΠΎΠΉ ΠΏΠ°ΡΡ), Π° ΡΠ°ΠΊΠΆΠ΅ ΡΠ²Π»ΡΡΡΡΡ ΠΏΡΠΈΡΠΈΠ½ΠΎΠΉ Π²ΡΡ ΠΎΠ΄Π° ΡΡΠ΅ΠΏΠΊΠΈ (ΠΊΡΡΠΊΠ° ΠΈ ΠΏΠ΅ΡΠ»ΠΈ Π΄ΡΡΠ»Π°) ΠΈΠ· ΡΡΡΠΎΡ. ΠΠΎΠ½ΡΡΡΡΠΊΡΠΈΡ ΠΊΡΡΠΊΠΎΠ²ΡΡ ΡΡΡΡΠΎΠΉΡΡΠ² ΠΏΡΠ΅Π΄ΡΡΠΌΠ°ΡΡΠΈΠ²Π°Π΅Ρ, ΠΊΠ°ΠΊ ΠΏΡΠ°Π²ΠΈΠ»ΠΎ, ΡΡΡΠ½ΡΡ ΡΡΠ΅ΠΏΠΊΡ-ΡΠ°ΡΡΠ΅ΠΏΠΊΡ Π·Π²Π΅Π½ΡΠ΅Π² Π°Π²ΡΠΎΠΏΠΎΠ΅Π·Π΄Π°.
Π’ΠΈΠΏΠΎΡΠ°Π·ΠΌΠ΅Ρ ΠΊΡΡΠΊΠΎΠ²ΡΡ Π’Π‘Π£ Π²ΡΠ±ΠΈΡΠ°Π΅ΡΡΡ Π² Π·Π°Π²ΠΈΡΠΈΠΌΠΎΡΡΠΈ ΠΎΡ ΠΏΠΎΠ»Π½ΠΎΠΉ ΠΌΠ°ΡΡΡ ΠΏΡΠΈΡΠ΅ΠΏΠ°. ΠΡΠ½ΠΎΠ²Π½ΡΠ΅ ΠΏΠ°ΡΠ°ΠΌΠ΅ΡΡΡ ΡΠ΅Π³Π»Π°ΠΌΠ΅Π½ΡΠΈΡΡΡΡΡΡ ΠΌΠ΅ΠΆΠ΄ΡΠ½Π°ΡΠΎΠ΄Π½ΡΠΌΠΈ ΡΡΠ°Π½Π΄Π°ΡΡΠ°ΠΌΠΈ ISΠ 1102, ISΠ 3584 ΠΈ ISΠ 8755 Π»ΠΈΠ±ΠΎ Π½Π°ΡΠΈΠΎΠ½Π°Π»ΡΠ½ΡΠΌΠΈ Π½ΠΎΡΠΌΠ°ΡΠΈΠ²Π½ΡΠΌΠΈ Π΄ΠΎΠΊΡΠΌΠ΅Π½ΡΠ°ΠΌΠΈ. Π£ΡΡΡΠΎΠΉΡΡΠ²Π° Β«ΠΊΡΡΠΊβΠΏΠ΅ΡΠ»ΡΒ» Π²ΡΠΏΡΡΠΊΠ°ΡΡ ΠΏΠΎΠ΄ Π²Π½ΡΡΡΠ΅Π½Π½ΠΈΠΉ Π΄ΠΈΠ°ΠΌΠ΅ΡΡ ΠΏΠ΅ΡΠ»ΠΈ 76, 85 ΠΈ 95 ΠΌΠΌ. ΠΠΈΠ°ΠΌΠ΅ΡΡ ΠΏΡΡΡΠΊΠ° ΠΏΠ΅ΡΠ»ΠΈ ΠΏΠ΅ΡΠ²ΠΎΠ³ΠΎ ΡΠΈΠΏΠΎΡΠ°Π·ΠΌΠ΅ΡΠ° ΡΠΎΡΡΠ°Π²Π»ΡΠ΅Ρ 42 ΠΌΠΌ, Π΄Π²ΡΡ ΠΎΡΡΠ°Π»ΡΠ½ΡΡ β ΠΏΠΎ 50 ΠΌΠΌ. Π‘ΡΠ΅ΠΏΠΊΠ° ΡΡΠ³Π°ΡΠ΅ΠΉ ΠΈ ΠΏΡΠΈΡΠ΅ΠΏΠΎΠ², ΠΎΠ±ΠΎΡΡΠ΄ΠΎΠ²Π°Π½Π½ΡΡ ΡΡΠ³ΠΎΠ²ΠΎ-ΡΡΠ΅ΠΏΠ½ΡΠΌΠΈ ΡΡΡΡΠΎΠΉΡΡΠ²Π°ΠΌΠΈ ΡΠ°Π·Π»ΠΈΡΠ½ΠΎΠΉ ΡΠ°Π·ΠΌΠ΅ΡΠ½ΠΎΡΡΠΈ, ΠΎΠ±Π΅ΡΠΏΠ΅ΡΠΈΠ²Π°Π΅ΡΡΡ Π·Π°ΠΌΠ΅Π½ΠΎΠΉ ΡΠΎΠΎΡΠ²Π΅ΡΡΡΠ²ΡΡΡΠΈΡ ΡΠ»Π΅ΠΌΠ΅Π½ΡΠΎΠ² ΡΡΠΈΡ ΠΌΠ΅Ρ Π°Π½ΠΈΠ·ΠΌΠΎΠ² ΠΈΠ»ΠΈ ΡΡΡΠ°Π½ΠΎΠ²ΠΊΠΎΠΉ ΠΏΠ΅ΡΠ΅Ρ ΠΎΠ΄Π½ΡΡ ΡΡΡΡΠΎΠΉΡΡΠ². ΠΠ°ΡΡΠ° Π’Π‘Π£ ΠΊΡΡΠΊΠΎΠ²ΠΎΠ³ΠΎ ΡΠΈΠΏΠ° ΠΎΠ±ΡΡΠ½ΠΎ Π½Π΅ ΠΏΡΠ΅Π²ΡΡΠ°Π΅Ρ 30 ΠΊΠ³.
ΠΠ° ΠΏΡΠ°ΠΊΡΠΈΠΊΠ΅ ΡΡΡΡΠΎΠΉΡΡΠ²ΠΎ Β«ΠΊΡΡΠΊβΠΏΠ΅ΡΠ»ΡΒ» ΠΏΠΎΠ·Π²ΠΎΠ»ΡΠ΅Ρ ΠΎΡΡΡΠ΅ΡΡΠ²Π»ΡΡΡ ΠΏΠΎΠ²ΠΎΡΠΎΡ ΡΡΠ΅ΠΏΠ½ΠΎΠΉ ΠΏΠ΅ΡΠ»ΠΈ Π²ΠΎΠΊΡΡΠ³ Π³ΠΎΡΠΈΠ·ΠΎΠ½ΡΠ°Π»ΡΠ½ΠΎΠΉ ΠΏΡΠΎΠ΄ΠΎΠ»ΡΠ½ΠΎΠΉ ΠΎΡΠΈ ΠΊΡΡΠΊΠ° Π½Π° 360Β°, ΠΏΠΎΠ²ΠΎΡΠΎΡ Π² Π²Π΅ΡΡΠΈΠΊΠ°Π»ΡΠ½ΠΎΠΉ ΠΏΠ»ΠΎΡΠΊΠΎΡΡΠΈ Π½Π° Β±45Β°, ΠΏΠΎΠ²ΠΎΡΠΎΡ Π² Π³ΠΎΡΠΈΠ·ΠΎΠ½ΡΠ°Π»ΡΠ½ΠΎΠΉ ΠΏΠ»ΠΎΡΠΊΠΎΡΡΠΈ Π½Π° Β±90Β°. Π‘ΡΡΠ΅ΡΡΠ²ΡΡΡ ΡΡΡΠ½ΡΠ΅ ΠΈ ΠΏΠΎΠ»ΡΠ°Π²ΡΠΎΠΌΠ°ΡΠΈΡΠ΅ΡΠΊΠΈΠ΅ ΠΊΠΎΠ½ΡΡΡΡΠΊΡΠΈΠΈ ΠΊΡΡΠΊΠΎΠ²ΡΡ ΡΡΠ΅ΠΏΠΎΠΊ. ΠΠΎΡΠ»Π΅Π΄Π½ΠΈΠ΅ ΠΏΠΎΠ»ΡΡΠΈΠ»ΠΈ ΠΌΠ΅Π½ΡΡΠ΅Π΅ ΡΠ°ΡΠΏΡΠΎΡΡΡΠ°Π½Π΅Π½ΠΈΠ΅ ΠΈΠ·-Π·Π° Π±ΠΎΠ»ΡΡΠΎΠΉ ΡΠ»ΠΎΠΆΠ½ΠΎΡΡΠΈ ΠΈ ΡΠ²Π΅Π»ΠΈΡΠ΅Π½Π½ΠΎΠΉ ΠΌΠ°ΡΡΡ.
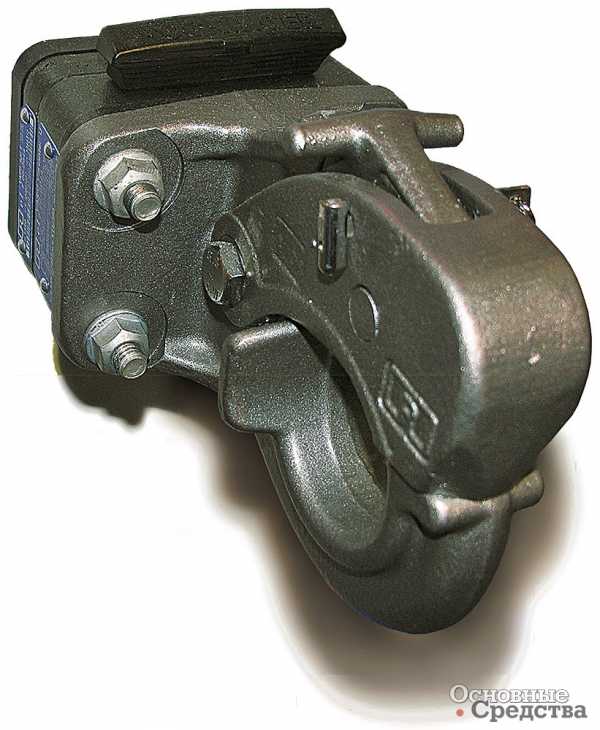
Π Π ΠΎΡΡΠΈΠΈ Π΄Π΅ΠΉΡΡΠ²ΡΠ΅Ρ ΠΠΠ‘Π’ 2349β75. Π Π·Π°Π²ΠΈΡΠΈΠΌΠΎΡΡΠΈ ΠΎΡ ΡΠΈΠΏΠΎΡΠ°Π·ΠΌΠ΅ΡΠ° Π’Π‘Π£ ΡΠ΅Π³Π»Π°ΠΌΠ΅Π½ΡΠΈΡΡΡΡΡΡ Π²ΡΡΠΎΡΠ° ΡΡΡΠ°Π½ΠΎΠ²ΠΊΠΈ Π½Π°Π΄ ΠΎΠΏΠΎΡΠ½ΠΎΠΉ ΠΏΠΎΠ²Π΅ΡΡ Π½ΠΎΡΡΡΡ ΠΈ ΠΏΡΠΈΡΠΎΠ΅Π΄ΠΈΠ½ΠΈΡΠ΅Π»ΡΠ½ΡΠ΅ ΡΠ°Π·ΠΌΠ΅ΡΡ. ΠΠ»Ρ ΠΊΡΡΠΊΠΎΠ²ΡΡ ΡΡΠ΅ΠΏΠΎΠΊ ΡΠΈΠΏΠΎΡΠ°Π·ΠΌΠ΅ΡΠΎΠ² ΠΎΡ 0 Π΄ΠΎ 3 Π³Π΅ΠΎΠΌΠ΅ΡΡΠΈΡΠ΅ΡΠΊΠΈΠ΅ ΠΏΠ°ΡΠ°ΠΌΠ΅ΡΡΡ ΡΠΎΠΏΡΡΠ³Π°Π΅ΠΌΡΡ ΠΏΠΎΠ²Π΅ΡΡ Π½ΠΎΡΡΠ΅ΠΉ Π·Π΅Π²Π° ΠΊΡΡΠΊΠ° ΠΈ ΠΏΠ΅ΡΠ»ΠΈ ΠΎΠ΄ΠΈΠ½Π°ΠΊΠΎΠ²ΡΠ΅ (Π΄ΠΈΠ°ΠΌΠ΅ΡΡ ΠΏΡΡΡΠΊΠ° ΠΏΠ΅ΡΠ»ΠΈ 42 ΠΌΠΌ). Π’ΠΈΠΏΠΎΡΠ°Π·ΠΌΠ΅Ρ 4 ΠΏΡΠ΅Π΄ΡΡΠΌΠ°ΡΡΠΈΠ²Π°Π΅Ρ ΠΏΡΠΈΠΌΠ΅Π½Π΅Π½ΠΈΠ΅ ΠΏΠ΅ΡΠ»ΠΈ ΠΈΠ· ΠΏΡΡΡΠΊΠ° Π΄ΠΈΠ°ΠΌΠ΅ΡΡΠΎΠΌ 45 ΠΌΠΌ. Π‘ΠΎΠ³Π»Π°ΡΠ½ΠΎ ΠΎΡΠ΅ΡΠ΅ΡΡΠ²Π΅Π½Π½ΠΎΠΌΡ ΡΡΠ°Π½Π΄Π°ΡΡΡ ΠΊΡΡΠΊΠΎΠ²ΡΠ΅ ΡΡΡΡΠΎΠΉΡΡΠ²Π° Π΄ΠΎΠ»ΠΆΠ½Ρ ΠΎΠ±Π΅ΡΠΏΠ΅ΡΠΈΠ²Π°ΡΡ ΡΠ³Π»Ρ Π³ΠΈΠ±ΠΊΠΎΡΡΠΈ ΠΎΡΠ½ΠΎΡΠΈΡΠ΅Π»ΡΠ½ΠΎ ΠΏΠΎΠΏΠ΅ΡΠ΅ΡΠ½ΠΎΠΉ ΠΎΡΠΈ, ΠΏΡΠΎΡ ΠΎΠ΄ΡΡΠ΅ΠΉ ΡΠ΅ΡΠ΅Π· Π·Π΅Π² ΠΊΡΡΠΊΠ°, Π½Π΅ ΠΌΠ΅Π½Π΅Π΅ Β±40Β°, ΠΎΡΠ½ΠΎΡΠΈΡΠ΅Π»ΡΠ½ΠΎ Π²Π΅ΡΡΠΈΠΊΠ°Π»ΡΠ½ΠΎΠΉ ΠΎΡΠΈ Β±55Β° (Π΄Π»Ρ Π°Π²ΡΠΎΠΌΠΎΠ±ΠΈΠ»Π΅ΠΉ ΠΎΠ±ΡΠ΅ΡΡΠ°Π½ΡΠΏΠΎΡΡΠ½ΠΎΠ³ΠΎ Π½Π°Π·Π½Π°ΡΠ΅Π½ΠΈΡ Π²ΡΡΠΎΠΊΠΎΠΉ ΠΏΡΠΎΡ ΠΎΠ΄ΠΈΠΌΠΎΡΡΠΈ Π½Π΅ ΠΌΠ΅Π½Π΅Π΅ Β±62Β°) ΠΈ ΠΏΡΠΎΠ΄ΠΎΠ»ΡΠ½ΠΎΠΉ ΠΎΡΠΈ Β±15Β°. ΠΡΡΠΊ Π΄ΠΎΠ»ΠΆΠ΅Π½ ΡΠ²ΠΎΠ±ΠΎΠ΄Π½ΠΎ Π²ΡΠ°ΡΠ°ΡΡΡΡ Π²ΠΎΠΊΡΡΠ³ ΡΠ²ΠΎΠ΅ΠΉ ΠΏΡΠΎΠ΄ΠΎΠ»ΡΠ½ΠΎΠΉ ΠΎΡΠΈ, Π° ΠΏΠΎ Π·Π°ΠΊΠ°Π·Ρ ΠΏΠΎΡΡΠ΅Π±ΠΈΡΠ΅Π»Ρ ΠΎΠ½ ΠΌΠΎΠΆΠ΅Ρ ΡΠ½Π°Π±ΠΆΠ°ΡΡΡΡ ΡΡΠΎΠΏΠΎΡΠ½ΡΠΌΠΈ ΡΡΡΡΠΎΠΉΡΡΠ²Π°ΠΌΠΈ, ΠΏΠΎΠ·Π²ΠΎΠ»ΡΡΡΠΈΠΌΠΈ ΡΠΈΠΊΡΠΈΡΠΎΠ²Π°ΡΡ Π΅Π³ΠΎ ΠΏΡΠΈ ΠΎΡΡΠ΅ΠΏΠ»Π΅Π½Π½ΠΎΠΌ ΠΏΡΠΈΡΠ΅ΠΏΠ΅. ΠΠΎΠ½ΡΡΡΡΠΊΡΠΈΡ Π·Π°ΠΌΠΊΠ° Π΄ΠΎΠ»ΠΆΠ½Π° ΠΈΡΠΊΠ»ΡΡΠ°ΡΡ Π²ΠΎΠ·ΠΌΠΎΠΆΠ½ΠΎΡΡΡ ΡΠ°ΠΌΠΎΡΠ°ΡΡΠ΅ΠΏΠΊΠΈ Π°Π²ΡΠΎΠΏΠΎΠ΅Π·Π΄Π° ΠΏΡΠΈ Π΄Π²ΠΈΠΆΠ΅Π½ΠΈΠΈ, Π° ΡΠ°ΠΊΠΆΠ΅ ΠΈΠΌΠ΅ΡΡ Π½Π΅ ΠΌΠ΅Π½Π΅Π΅ Π΄Π²ΡΡ ΠΏΡΠ΅Π΄ΠΎΡ ΡΠ°Π½ΠΈΡΠ΅Π»ΡΠ½ΡΡ ΠΌΠ΅Ρ Π°Π½ΠΈΠ·ΠΌΠΎΠ², Π΄Π΅ΠΉΡΡΠ²ΡΡΡΠΈΡ Π½Π΅Π·Π°Π²ΠΈΡΠΈΠΌΠΎ ΠΎΠ΄ΠΈΠ½ ΠΎΡ Π΄ΡΡΠ³ΠΎΠ³ΠΎ, ΠΏΡΠΈΡΠ΅ΠΌ Ρ ΠΎΡΡ Π±Ρ ΠΎΠ΄ΠΈΠ½ ΠΈΠ· Π½ΠΈΡ Π½Π΅ Π΄ΠΎΠ»ΠΆΠ΅Π½ Π±ΡΡΡ ΠΏΠΎΠ΄ Π΄Π΅ΠΉΡΡΠ²ΠΈΠ΅ΠΌ ΡΠΈΠ», ΠΏΠΎΡΠ²Π»ΡΡΡΠΈΡ ΡΡ Π²ΠΎ Π²ΡΠ΅ΠΌΡ Π΄Π²ΠΈΠΆΠ΅Π½ΠΈΡ ΡΡΠ°Π½ΡΠΏΠΎΡΡΠ½ΠΎΠ³ΠΎ ΡΡΠ΅Π΄ΡΡΠ²Π°.
ΠΠ»Ρ ΠΏΠ΅ΡΠ²ΡΡ ΡΠ΅ΡΡΡΠ΅Ρ ΠΊΠ°ΡΠ΅Π³ΠΎΡΠΈΠΉ ΡΠΈΠΏΠΎΡΠ°Π·ΠΌΠ΅ΡΠΎΠ² ΠΏΡΠΈΠ½ΡΡ ΠΎΠ΄ΠΈΠ½ ΡΠ°Π·ΠΌΠ΅Ρ Π·Π΅Π²Π°, ΡΠ°Π²Π½ΡΠΉ 48 ΠΌΠΌ, ΡΠ°Π·ΠΌΠ΅Ρ Π³ΡΠ±ΠΊΠΈ β 74 ΠΌΠΌ, ΡΡΠΎ ΠΏΠΎΠ·Π²ΠΎΠ»ΡΠ΅Ρ ΠΏΡΠΈ ΠΊΠΎΠΌΠΏΠ»Π΅ΠΊΡΠ°ΡΠΈΠΈ Π°Π²ΡΠΎΠΏΠΎΠ΅Π·Π΄ΠΎΠ² ΠΈΡΠΏΠΎΠ»ΡΠ·ΠΎΠ²Π°ΡΡ ΡΠΈΡΠΎΠΊΡΡ Π½ΠΎΠΌΠ΅Π½ΠΊΠ»Π°ΡΡΡΡ ΡΡΠ³Π°ΡΠ΅ΠΉ ΠΈ ΠΏΡΠΈΡΠ΅ΠΏΠ½ΠΎΠ³ΠΎ ΡΠΎΡΡΠ°Π²Π°. Π ΠΏΡΡΠΎΠΉ Π³ΡΡΠΏΠΏΠ΅ ΡΠ°Π·ΠΌΠ΅Ρ Π·Π΅Π²Π° ΡΠΎΡΡΠ°Π²Π»ΡΠ΅Ρ 52 ΠΌΠΌ, ΡΠΎΠ³Π΄Π° ΠΊΠ°ΠΊ Π³Π΅ΠΎΠΌΠ΅ΡΡΠΈΡ Π³ΡΠ±ΠΊΠΈ ΠΎΡΡΠ°Π΅ΡΡΡ ΡΠ°ΠΊΠΎΠΉ ΠΆΠ΅.
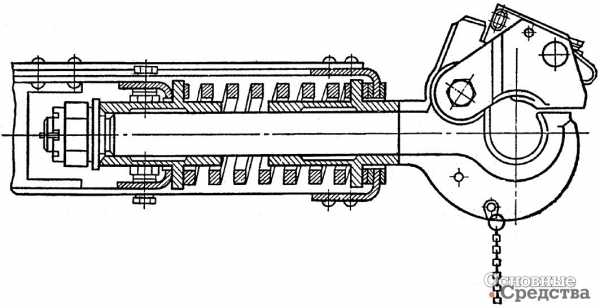
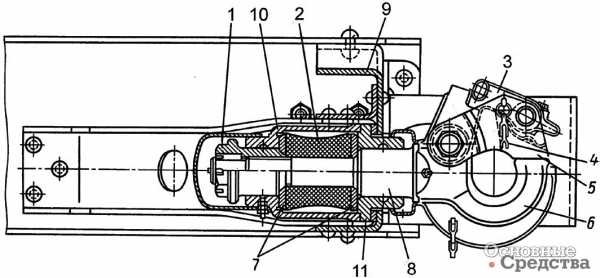
Π‘ΡΠ°Π½Π΄Π°ΡΡΠ½ΠΎΠ΅ ΡΠΎΠ΅Π΄ΠΈΠ½Π΅Π½ΠΈΠ΅ ΠΊΡΡΠΊΠΎΠ²ΠΎΠ³ΠΎ ΡΠΈΠΏΠ°, ΡΠ½Π°Π±ΠΆΠ΅Π½Π½ΠΎΠ΅ Π΄Π²ΡΡΡΠΎΡΠΎΠ½Π½Π΅ΠΉ Π°ΠΌΠΎΡΡΠΈΠ·Π°ΡΠΈΠ΅ΠΉ, ΡΠΎΡΡΠΎΠΈΡ ΠΈΠ· ΡΡΠ³ΠΎΠ²ΠΎΠ³ΠΎ ΠΊΡΡΠΊΠ°, ΡΡΡΠ°Π½ΠΎΠ²Π»Π΅Π½Π½ΠΎΠ³ΠΎ Π½Π° ΡΡΠ³Π°ΡΠ΅, ΠΈ ΠΆΠ΅ΡΡΠΊΠΎΠ³ΠΎ Π΄ΡΡΠ»Π° ΡΠΎ ΡΡΠ΅ΠΏΠ½ΠΎΠΉ ΠΏΠ΅ΡΠ»Π΅ΠΉ, ΡΠ²ΡΠ·Π°Π½Π½ΠΎΠ³ΠΎ Ρ ΠΏΡΠΈΡΠ΅ΠΏΠΎΠΌ. Π’ΡΠ³ΠΎΠ²ΡΠΉ ΠΊΡΡΠΊ ΠΎΠ±ΡΡΠ½ΠΎ ΠΌΠΎΠ½ΡΠΈΡΡΡΡ Π½Π° Π·Π°Π΄Π½Π΅ΠΉ ΠΏΠΎΠΏΠ΅ΡΠ΅ΡΠΈΠ½Π΅ ΡΠ°ΠΌΡ, ΠΎΠ΄Π½Π°ΠΊΠΎ Π½Π° Π½Π΅ΠΊΠΎΡΠΎΡΡΡ Π°Π²ΡΠΎΠΌΠΎΠ±ΠΈΠ»ΡΡ ΠΎΠ½ ΠΌΠΎΠΆΠ΅Ρ Π½Π΅ ΠΌΠ΅Π½Π΅Π΅ ΡΡΡΠ΅ΠΊΡΠΈΠ²Π½ΠΎ Π²ΡΠΏΠΎΠ»Π½ΡΡΡ ΡΠ²ΠΎΡ ΡΡΠ½ΠΊΡΠΈΡ, Π±ΡΠ΄ΡΡΠΈ ΡΠ°ΡΠΏΠΎΠ»ΠΎΠΆΠ΅Π½ Π½Π° ΠΏΠ΅ΡΠ΅Π΄Π½Π΅ΠΌ Π±Π°ΠΌΠΏΠ΅ΡΠ΅ (ΠΏΠΎΠΏΠ΅ΡΠ΅ΡΠΈΠ½Π΅) ΡΠ°ΠΌΡ ΠΈΠ»ΠΈ Π½Π° Π·Π°Π΄Π½Π΅ΠΉ ΠΏΠΎΠΏΠ΅ΡΠ΅ΡΠΈΠ½Π΅ ΠΏΡΠΈΡΠ΅ΠΏΠ° (ΠΏΠΎΠ»ΡΠΏΡΠΈΡΠ΅ΠΏΠ°) Π΄Π»Ρ Π±ΡΠΊΡΠΈΡΠΎΠ²ΠΊΠΈ Π²ΡΠΎΡΠΎΠ³ΠΎ ΠΏΡΠΈΡΠ΅ΠΏΠ°. Π‘ΠΈΡΡΠ΅ΠΌΠ° Β«ΠΊΡΡΠΊβΠΏΠ΅ΡΠ»ΡΒ» ΡΠΎΡΡΠΎΠΈΡ ΠΈΠ· ΡΠΎΠ±ΡΡΠ²Π΅Π½Π½ΠΎ ΠΊΡΡΠΊΠ°, Π½Π°ΠΊΠΈΠ΄Π½ΠΎΠΉ Π·Π°ΡΠ΅Π»ΠΊΠΈ, ΠΏΡΠ΅Π΄ΠΎΡ ΡΠ°Π½ΠΈΡΠ΅Π»ΡΠ½ΠΎΠ³ΠΎ Π·Π°ΠΌΠΊΠ° Ρ Π·Π°ΠΏΠΎΡΠ½ΡΠΌ ΡΠΏΠ»ΠΈΠ½ΡΠΎΠΌ. ΠΠ°Π»ΠΈΡΠΈΠ΅ ΠΏΡΠ΅Π΄ΠΎΡ ΡΠ°Π½ΠΈΡΠ΅Π»ΡΠ½ΠΎΠ³ΠΎ Π·Π°ΠΌΠΊΠ° ΠΈ ΡΠΏΠ»ΠΈΠ½ΡΠ° ΠΏΡΠ΅Π΄ΠΎΡΠ²ΡΠ°ΡΠ°ΡΡ ΡΠ°ΠΌΠΎΠΏΡΠΎΠΈΠ·Π²ΠΎΠ»ΡΠ½ΡΡ ΡΠ°ΡΡΠ΅ΠΏΠΊΡ Π°Π²ΡΠΎΠΏΠΎΠ΅Π·Π΄Π° Π²ΠΎ Π²ΡΠ΅ΠΌΡ Π΄Π²ΠΈΠΆΠ΅Π½ΠΈΡ. ΠΠ° ΠΏΠ΅ΡΠ΅Π΄Π½Π΅ΠΌ ΠΊΠΎΠ½ΡΠ΅ ΡΡΠ΅ΡΠΆΠ½Ρ ΠΊΡΡΠΊΠ°, ΡΡΡΠ°Π½ΠΎΠ²Π»Π΅Π½Π½ΠΎΠ³ΠΎ Π²ΠΎ Π²ΡΡΠ»ΠΊΠ΅, Π½Π°Π²ΠΈΠ½ΡΠ΅Π½Π° Π³Π°ΠΉΠΊΠ°, ΠΊΠΎΡΠΎΡΠ°Ρ ΡΠΎ Π²ΡΡΠ»ΠΊΠΎΠΉ ΠΎΠ±Π΅ΡΠΏΠ΅ΡΠΈΠ²Π°Π΅Ρ ΠΏΡΠ°Π²ΠΈΠ»ΡΠ½ΠΎΠ΅ ΠΏΡΠΎΠ΄ΠΎΠ»ΡΠ½ΠΎΠ΅ ΠΏΠ΅ΡΠ΅ΠΌΠ΅ΡΠ΅Π½ΠΈΠ΅ ΠΊΡΡΠΊΠ°. ΠΠ½ΡΡΡΠΈ ΠΊΠΎΡΠΏΡΡΠ° Π²ΡΡΠ°Π²Π»Π΅Π½ ΡΠ΅Π·ΠΈΠ½ΠΎΠ²ΡΠΉ ΡΠΏΡΡΠ³ΠΈΠΉ ΡΠ»Π΅ΠΌΠ΅Π½Ρ Π² ΡΠΎΡΠΌΠ΅ Π³ΠΈΠΏΠ΅ΡΠ±ΠΎΠ»ΠΎΠΈΠ΄Π°, ΠΎΠ±ΠΆΠΈΠΌΠ°Π΅ΠΌΡΠΉ ΡΠ°ΠΉΠ±Π°ΠΌΠΈ. ΠΡΠΈ ΡΠΆΠ°ΡΠΈΠΈ ΠΎΠ½ ΠΈΠ·ΠΌΠ΅Π½ΡΠ΅Ρ ΡΠΎΡΠΌΡ ΡΠ°ΠΊΠΈΠΌ ΠΎΠ±ΡΠ°Π·ΠΎΠΌ, ΡΡΠΎ Π·Π°ΠΏΠΎΠ»Π½ΡΠ΅Ρ ΠΏΡΠΎΡΡΡΠ°Π½ΡΡΠ²ΠΎ Π² ΠΊΠΎΡΠΏΡΡΠ΅. Π Π΄ΡΡΠ³ΠΈΡ ΠΊΠΎΠ½ΡΡΡΡΠΊΡΠΈΡΡ ΡΡΠ³ΠΎΠ²ΡΡ ΠΊΡΡΠΊΠΎΠ² Π² ΠΊΠ°ΡΠ΅ΡΡΠ²Π΅ ΡΠΏΡΡΠ³ΠΈΡ ΡΠ»Π΅ΠΌΠ΅Π½ΡΠΎΠ² ΠΈΡΠΏΠΎΠ»ΡΠ·ΡΡΡΡΡ ΠΊΠΎΠ»ΡΡΠ΅Π²ΡΠ΅, Π²ΠΈΠ½ΡΠΎΠ²ΡΠ΅ ΡΠΈΠ»ΠΈΠ½Π΄ΡΠΈΡΠ΅ΡΠΊΠΈΠ΅ ΠΈΠ»ΠΈ ΠΊΠΎΠ½ΠΈΡΠ΅ΡΠΊΠΈΠ΅ ΠΏΡΡΠΆΠΈΠ½Ρ.
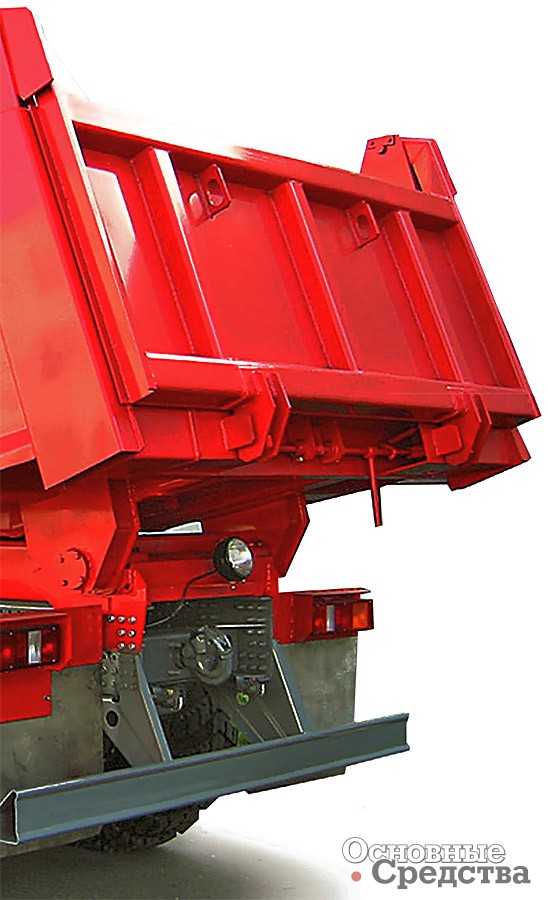
Π ΠΏΡΠΎΡΠ΅ΡΡΠ΅ ΡΠΊΡΠΏΠ»ΡΠ°ΡΠ°ΡΠΈΠΈ Π³Π°ΠΉΠΊΡ Π½Π΅Π»ΡΠ·Ρ ΠΈΡΠΏΠΎΠ»ΡΠ·ΠΎΠ²Π°ΡΡ Π΄Π»Ρ ΡΠ΅Π³ΡΠ»ΠΈΡΠΎΠ²ΠΊΠΈ ΠΎΡΠ΅Π²ΠΎΠ³ΠΎ ΠΏΠ΅ΡΠ΅ΠΌΠ΅ΡΠ΅Π½ΠΈΡ ΠΊΡΡΠΊΠ°, ΡΠ°ΠΊ ΠΊΠ°ΠΊ Π΅Π΅ Π½Π°Π²Π΅ΡΡΡΠ²Π°Π½ΠΈΠ΅-ΡΠ²Π΅ΡΡΡΠ²Π°Π½ΠΈΠ΅ ΠΏΡΠΈΠ²ΠΎΠ΄ΠΈΡ ΠΊ ΡΠ²Π΅Π»ΠΈΡΠ΅Π½ΠΈΡ ΠΎΡΠ΅Π²ΠΎΠ³ΠΎ ΠΏΠ΅ΡΠ΅ΠΌΠ΅ΡΠ΅Π½ΠΈΡ ΠΊΡΡΠΊΠ°. ΠΡΠΈ ΠΏΠΎΡΠ²Π»Π΅Π½ΠΈΠΈ ΡΡΠ°Π΄ΠΊΠΈ ΡΠ΅Π·ΠΈΠ½ΠΎΠ²ΠΎΠ³ΠΎ Π±ΡΡΠ΅ΡΠ° ΡΡΡΠ°Π½Π°Π²Π»ΠΈΠ²Π°ΡΡ Π΄ΠΎΠΏΠΎΠ»Π½ΠΈΡΠ΅Π»ΡΠ½ΡΠ΅ ΠΊΠΎΠ»ΡΡΠ΅Π²ΡΠ΅ ΠΏΡΠΎΠΊΠ»Π°Π΄ΠΊΠΈ ΠΌΠ΅ΠΆΠ΄Ρ ΡΠ»Π°Π½ΡΠ°ΠΌΠΈ ΠΈ ΡΠ΅Π·ΠΈΠ½ΠΎΠ²ΡΠΌ Π±ΡΡΠ΅ΡΠΎΠΌ. ΠΡΠΈΠΌΠ΅Π½Π΅Π½ΠΈΠ΅ ΡΡΠ΅ΠΏΠ½ΠΎΠΉ ΠΏΠ΅ΡΠ»ΠΈ ΠΏΡΠΈΡΠ΅ΠΏΠΎΠ² Ρ ΠΌΠ΅Π½ΡΡΠΈΠΌ ΡΠ΅ΡΠ΅Π½ΠΈΠ΅ΠΌ ΡΠ²Π΅Π»ΠΈΡΠΈΠ²Π°Π΅Ρ ΠΈΠ·Π½ΠΎΡ ΠΈ ΡΠΎΠΊΡΠ°ΡΠ°Π΅Ρ ΡΡΠΎΠΊ ΡΠ»ΡΠΆΠ±Ρ Π’Π‘Π£, Π° ΡΠ°ΠΊΠΆΠ΅ Π·Π°Π΄Π½Π΅ΠΉ ΠΏΠΎΠΏΠ΅ΡΠ΅ΡΠΈΠ½Ρ ΡΠ°ΠΌΡ Π°Π²ΡΠΎΠΌΠΎΠ±ΠΈΠ»Ρ.
ΠΠ΅ΡΠΌΠΎΡΡΡ Π½Π° ΠΏΡΠΈΡΡΡΠΈΠ΅ ΡΡΠ΅ΠΏΠ½ΡΠΌ ΡΡΡΡΠΎΠΉΡΡΠ²Π°ΠΌ ΡΠΈΠΏΠ° Β«ΠΊΡΡΠΊβΠΏΠ΅ΡΠ»ΡΒ» Π½Π΅Π΄ΠΎΡΡΠ°ΡΠΊΠ°ΠΌ, Π²ΡΠ΅ Π²Π΅Π΄ΡΡΠΈΠ΅ ΠΈΠ·Π³ΠΎΡΠΎΠ²ΠΈΡΠ΅Π»ΠΈ ΡΠ°ΠΊΠΎΠ³ΠΎ ΡΠΎΠ΄Π° ΠΏΡΠΎΠ΄ΡΠΊΡΠΈΠΈ ΠΏΡΠΎΠ΄ΠΎΠ»ΠΆΠ°ΡΡ ΠΈΡ ΡΠΎΠ²Π΅ΡΡΠ΅Π½ΡΡΠ²ΠΎΠ²Π°ΡΡ ΠΈ Π²ΡΠΏΡΡΠΊΠ°ΡΡ. ΠΡΡΠΊΠΎΠ²ΡΠ΅ ΡΡΡΡΠΎΠΉΡΡΠ²Π° ΠΎΡΠ»ΠΈΡΠ°ΡΡΡΡ Π±ΠΎΠ»ΡΡΠΈΠΌ ΡΠ°Π·Π½ΠΎΠΎΠ±ΡΠ°Π·ΠΈΠ΅ΠΌ ΠΈΡΠΏΠΎΠ»Π½Π΅Π½ΠΈΠΉ ΠΊΠ°ΠΊ ΡΠ°ΠΌΠΎΠ³ΠΎ ΠΊΡΡΠΊΠ°, ΡΠ°ΠΊ ΠΈ Π·Π°ΠΌΠΊΠ°. ΠΠ»Ρ ΠΎΡΡΡΠ΅ΡΡΠ²Π»Π΅Π½ΠΈΡ Π±Π΅Π·Π·Π°Π·ΠΎΡΠ½ΠΎΠΉ ΡΡΠ΅ΠΏΠΊΠΈ ΡΡΠ΄ ΡΠΈΡΠΌ ΡΠ°Π·ΡΠ°Π±ΠΎΡΠ°Π»ΠΈ ΡΠΏΠ΅ΡΠΈΠ°Π»ΡΠ½ΡΠ΅ ΠΊΠΎΠ½ΡΡΡΡΠΊΡΠΈΠΈ Π’Π‘Π£ ΡΠΈΠΏΠ° Β«ΠΊΡΡΠΊβΠΏΠ΅ΡΠ»ΡΒ», Π² ΠΊΠΎΡΠΎΡΡΡ Π·Π°Π·ΠΎΡ ΠΌΠΎΠΆΠ΅Ρ Π²ΡΠ±ΠΈΡΠ°ΡΡΡΡ Π°Π²ΡΠΎΠΌΠ°ΡΠΈΡΠ΅ΡΠΊΠΈ Ρ ΠΏΠΎΠΌΠΎΡΡΡ ΠΊΠΎΠ½ΠΈΡΠ΅ΡΠΊΠΈΡ ΡΠΎΠ»ΠΈΠΊΠΎΠ² (ΡΠΈΡΠΌΠ° Coder Ture) Π»ΠΈΠ±ΠΎ Ρ ΠΏΠΎΠΌΠΎΡΡΡ ΠΏΡΡΠΆΠΈΠ½ ΠΈΠ»ΠΈ ΠΏΠ½Π΅Π²ΠΌΠ°ΡΠΈΡΠ΅ΡΠΊΠΈΡ ΡΡΡΡΠΎΠΉΡΡΠ² ΠΏΠΎ ΠΏΡΠΈΠ½ΡΠΈΠΏΡ Β«Π±Π΅Π·Π·Π°Π·ΠΎΡΠ½ΡΠΉ ΠΊΡΡΠΊΒ» ΠΈΠ»ΠΈ Β«Π±Π΅Π·Π·Π°Π·ΠΎΡΠ½Π°Ρ ΠΏΠ΅ΡΠ»ΡΒ» (ΡΠΈΡΠΌΠ° Utility Trailer). ΠΠ½Π°Π»ΠΎΠ³ΠΈΡΠ½ΡΠ΅ ΡΠΈΡΡΠ΅ΠΌΡ Π΄Π»Ρ ΠΊΡΡΠΊΠΎΠ²ΡΡ Π’Π‘Π£ Π²ΡΠΏΡΡΠΊΠ°ΡΡ ΠΊΠΎΠΌΠΏΠ°Π½ΠΈΠΈ V. Orlandi ΠΈ SAF-Holland. ΠΠ½ΠΈ ΠΎΡΠ½Π°ΡΠ΅Π½Ρ ΠΏΠ½Π΅Π²ΠΌΠΎΠΏΡΠΈΠ²ΠΎΠ΄ΠΎΠΌ, Π°Π²ΡΠΎΠΌΠ°ΡΠΈΡΠ΅ΡΠΊΠΈ Π²ΡΠ±ΠΈΡΠ°ΡΡΠΈΠΌ Π·Π°Π·ΠΎΡ Π² Π·Π°ΠΌΠΊΠ΅ ΡΡΡΡΠΎΠΉΡΡΠ²Π°. Π ΠΊΠ°ΡΠ΅ΡΡΠ²Π΅ ΡΠΈΠ»ΠΎΠ²ΠΎΠ³ΠΎ ΡΠ»Π΅ΠΌΠ΅Π½ΡΠ° ΠΈΡΠΏΠΎΠ»ΡΠ·ΡΠ΅ΡΡΡ ΠΏΠ½Π΅Π²ΠΌΠ°ΡΠΈΡΠ΅ΡΠΊΠ°Ρ ΠΊΠ°ΠΌΠ΅ΡΠ° Ρ ΠΏΠΎΠ΄Π²ΠΈΠΆΠ½ΡΠΌ ΡΡΠΎΠΊΠΎΠΌ, ΡΠΌΠΎΠ½ΡΠΈΡΠΎΠ²Π°Π½Π½Π°Ρ Ρ ΡΡΠ»ΡΠ½ΠΎΠΉ ΡΡΠΎΡΠΎΠ½Ρ Π·Π°Π΄Π½Π΅ΠΉ ΠΏΠΎΠΏΠ΅ΡΠ΅ΡΠΈΠ½Ρ ΡΠ°ΠΌΡ. Π’Π΅ΠΌ Π½Π΅ ΠΌΠ΅Π½Π΅Π΅ Π±Π΅Π·Π·Π°Π·ΠΎΡΠ½ΡΠ΅ ΡΡΠ΅ΠΏΠΊΠΈ Π½Π΅ Π½Π°ΡΠ»ΠΈ ΡΠΈΡΠΎΠΊΠΎΠ³ΠΎ ΠΏΡΠΈΠΌΠ΅Π½Π΅Π½ΠΈΡ ΠΏΠΎ ΠΏΡΠΈΡΠΈΠ½Π΅ Π·Π½Π°ΡΠΈΡΠ΅Π»ΡΠ½ΠΎΠ³ΠΎ ΡΡΠ»ΠΎΠΆΠ½Π΅Π½ΠΈΡ ΠΊΠΎΠ½ΡΡΡΡΠΊΡΠΈΠΈ ΠΈ ΠΎΠ±ΡΠ»ΡΠΆΠΈΠ²Π°Π½ΠΈΡ, Π° ΡΠ°ΠΊΠΆΠ΅ ΡΠ²Π΅Π»ΠΈΡΠ΅Π½ΠΈΡ ΡΠΎΠ±ΡΡΠ²Π΅Π½Π½ΠΎΠΉ ΠΌΠ°ΡΡΡ (Π΄ΠΎ 60 ΠΊΠ³).
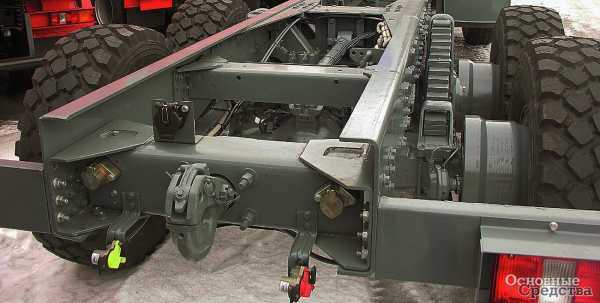
os1.ru
ΠΡΠΈΡΠ΅ΠΏΠ½ΡΠ΅ ΡΡΡΡΠΎΠΉΡΡΠ²Π° ΡΡΠ°ΠΊΡΠΎΡΠΎΠ²
Π‘ΡΡΠΎΠΈΡΠ΅Π»ΡΠ½ΡΠ΅ ΠΌΠ°ΡΠΈΠ½Ρ ΠΈ ΠΎΠ±ΠΎΡΡΠ΄ΠΎΠ²Π°Π½ΠΈΠ΅, ΡΠΏΡΠ°Π²ΠΎΡΠ½ΠΈΠΊ
ΠΠ°ΡΠ΅Π³ΠΎΡΠΈΡ:
Β Β Β ΠΠ²ΡΠΎΠΌΠΎΠ±ΠΈΠ»ΠΈ ΠΈ ΡΡΠ°ΠΊΡΠΎΡΠ°
ΠΡΠΈΡΠ΅ΠΏΠ½ΡΠ΅ ΡΡΡΡΠΎΠΉΡΡΠ²Π°Β ΡΡΠ°ΠΊΡΠΎΡΠΎΠ²
ΠΡΠΈΡΠ΅ΠΏΠ½ΡΠ΅ ΡΡΡΡΠΎΠΉΡΡΠ²Π° ΡΡΠ°ΠΊΡΠΎΡΠΎΠ² ΠΎΠ±Π΅ΡΠΏΠ΅ΡΠΈΠ²Π°ΡΡ Π²ΠΎΠ·ΠΌΠΎΠΆΠ½ΠΎΡΡΡ ΠΈΡΠΏΠΎΠ»ΡΠ·ΠΎΠ²Π°Π½ΠΈΡ ΠΏΠΎΡΠ»Π΅Π΄Π½ΠΈΡ Π΄Π»Ρ Π±ΡΠΊΡΠΈΡΠΎΠ²ΠΊΠΈ ΡΠ°Π·Π»ΠΈΡΠ½ΡΡ ΠΌΠ°ΡΠΈΠ½ ΠΈ ΠΏΡΠΈΡΠ΅ΠΏΠΎΠ². ΠΡΠΈΡΠ΅ΠΏΠ½ΠΎΠ΅ ΡΡΡΡΠΎΠΉΡΡΠ²ΠΎ ΡΠ»ΡΠΆΠΈΡ Π΄Π»Ρ ΡΠΎΠ΅Π΄ΠΈΠ½Π΅Π½ΠΈΡ ΡΡΠ°ΠΊΡΠΎΡΠ° Ρ ΠΏΡΠΈΡΠ΅ΠΏΠ½ΡΠΌΠΈ ΠΈ ΠΏΠΎΠ»ΡΠ½Π°Π²Π΅ΡΠ½ΡΠΌΠΈ ΠΌΠ°ΡΠΈΠ½Π°ΠΌΠΈ, ΠΎΡΡΠ΄ΠΈΡΠΌΠΈ ΠΈ ΠΏΡΠΈΡΠ΅ΠΏΠ°ΠΌΠΈ, ΡΠ°Π·ΠΌΠ΅ΡΠ°Π΅ΠΌΡΠΌΠΈ ΠΏΠΎΠ·Π°Π΄ΠΈ ΠΎΡΠΈ Π²Π΅Π΄ΡΡΠΈΡ ΠΊΠΎΠ»Π΅Ρ (Π·Π²Π΅Π·Π΄ΠΎΡΠ΅ΠΊ) ΡΡΠ°ΠΊΡΠΎΡΠ°. Π’ΠΎΡΠΊΠ°, Π² ΠΊΠΎΡΠΎΡΠΎΠΉ ΠΏΡΠΈΡΠ΅ΠΏΠ½ΠΎΠ΅ ΡΡΡΡΠΎΠΉΡΡΠ²ΠΎ ΡΡΠ°ΠΊΡΠΎΡΠ° ΡΠΎΠ΅Π΄ΠΈΠ½ΡΠ΅ΡΡΡ Ρ ΠΏΡΠΈΡΠ΅ΠΏΠ½ΡΠΌ ΡΡΡΡΠΎΠΉΡΡΠ²ΠΎΠΌ ΠΌΠ°ΡΠΈΠ½Ρ, ΠΎΡΡΠ΄ΠΈΡ ΠΈΠ»ΠΈ ΠΏΡΠΈΡΠ΅ΠΏΠ°, ΡΠ²Π»ΡΠ΅ΡΡΡ ΡΠΎΡΠΊΠΎΠΉ ΠΏΡΠΈΠ»ΠΎΠΆΠ΅Π½ΠΈΡ ΡΡΠ³ΠΎΠ²ΠΎΠ³ΠΎ ΡΡΠΈΠ»ΠΈΡ ΠΈ Π½Π°Π·ΡΠ²Π°Π΅ΡΡΡ ΡΠΎΡΠΊΠΎΠΉ ΠΏΡΠΈΡΠ΅ΠΏΠ°.
ΠΠ»Ρ ΠΏΡΠ°Π²ΠΈΠ»ΡΠ½ΠΎΠΉ ΡΡΠ΅ΠΏΠΊΠΈ ΡΡΠ°ΠΊΡΠΎΡΠ° Ρ ΠΏΡΠΈΡΠ΅ΠΏΠ½ΡΠΌ ΡΡΡΡΠΎΠΉΡΡΠ²ΠΎΠΌ Π½Π΅ΠΎΠ±Ρ ΠΎΠ΄ΠΈΠΌΠΎ, ΡΡΠΎΠ±Ρ ΠΏΠΎΠ»ΠΎΠΆΠ΅Π½ΠΈΠ΅ ΡΠΎΡΠΊΠΈ ΠΏΡΠΈΡΠ΅ΠΏΠ° ΠΌΠΎΠΆΠ½ΠΎ Π±ΡΠ»ΠΎ ΡΠ΅Π³ΡΠ»ΠΈΡΠΎΠ²Π°ΡΡ Π² Π²Π΅ΡΡΠΈΠΊΠ°Π»ΡΠ½ΠΎΠΉ ΠΈ Π³ΠΎΡΠΈΠ·ΠΎΠ½ ΡΠ°Π»ΡΠ½ΠΎΠΉ ΠΏΠ»ΠΎΡΠΊΠΎΡΡΡΡ . ΠΡΠΈΡΠ΅ΠΏΠ½ΡΠ΅ ΡΡΡΡΠΎΠΉΡΡΠ²Π° Π²ΡΠ΅Ρ ΡΡΠ°ΠΊΡΠΎΡΠΎΠ² ΡΠ΅Π³ΡΠ»ΠΈΡΡΡΡΡΡ ΠΏΠΎ ΡΠΈΡΠΈΠ½Π΅, Π° Ρ Π±ΠΎΠ»ΡΡΠΈΠ½ΡΡΠ²Π° ΠΈΠ· Π½ΠΈΡ ΠΈ ΠΏΠΎ Π²ΡΡΠΎΡΠ΅.
ΠΡΠΈΡΠ΅ΠΏΠ½ΡΠ΅ ΡΡΡΡΠΎΠΉΡΡΠ²Π° ΠΏΠΎΠ΄ΡΠ°Π·Π΄Π΅Π»ΡΡΡΡΡ Π½Π° ΠΏΡΠΈΡΠ΅ΠΏΠ½ΡΠ΅ ΡΠΊΠΎΠ±Ρ, ΠΊΠΎΡΠΎΡΡΠ΅ ΠΏΡΠ΅Π΄Π½Π°Π·Π½Π°ΡΠ΅Π½Ρ Π΄Π»Ρ ΡΠΎΠ΅Π΄ΠΈΠ½Π΅Π½ΠΈΡ Ρ ΡΡΠ°ΠΊΡΠΎΡΠΎΠΌ ΠΌΠ°ΡΠΈΠ½ ΠΈ ΠΎΡΡΠ΄ΠΈΠΉ, ΠΈ ΡΡΠ³ΠΎΠ²ΠΎ-ΡΡΠ΅ΠΏΠ½ΡΠ΅ ΠΏΡΠΈΠ±ΠΎΡΡ, ΡΠ»ΡΠΆΠ°ΡΠΈΠ΅ Π΄Π»Ρ ΠΏΡΠΈΡΠΎΠ΅Π΄ΠΈΠ½Π΅Π½ΠΈΡ Π΄Π²ΡΡ - ΠΈ ΠΎΠ΄Π½ΠΎΠΎΡΠ½ΡΡ ΠΏΡΠΈΡΠ΅ΠΏΠΎΠ².
ΠΡΠΈΡΠ΅ΠΏΠ½ΡΠ΅ ΡΠΊΠΎΠ±Ρ ΡΡΠ°ΠΊΡΠΎΡΠΎΠ² Π±ΡΠ²Π°ΡΡ ΠΎΠ±ΡΡΠ½ΠΎΠ³ΠΎ ΠΈ ΠΌΠ°ΡΡΠ½ΠΈΠΊΠΎΠ²ΠΎΠ³ΠΎ ΡΠΈΠΏΠ°. ΠΡΠ½ΠΎΠ²Π½ΡΠΌ ΠΎΡΠ»ΠΈΡΠΈΠ΅ΠΌ ΠΏΡΠΈΡΠ΅ΠΏΠ½ΠΎΠ³ΠΎ ΡΡΡΡΠΎΠΉΡΡΠ²Π° ΠΌΠ°ΡΡΠ½ΠΈΠΊΠΎΠ²ΠΎΠ³ΠΎ ΡΠΈΠΏΠ° ΡΠ²Π»ΡΠ΅ΡΡΡ ΡΠΎ, ΡΡΠΎ ΠΎΡΡ ΠΊΡΠ΅ΠΏΠ»Π΅Π½ΠΈΡ ΠΏΡΠΈΡΠ΅ΠΏΠ½ΠΎΠΉ ΡΠΊΠΎΠ±Ρ Π²ΡΠ½Π΅ΡΠ΅Π½Π° Π²ΠΏΠ΅ΡΠ΅Π΄ ΠΎΡ ΠΎΡΠΈ Π²Π΅Π΄ΡΡΠΈΡ ΠΊΠΎΠ»Π΅Ρ, Π±Π»ΠΈΠΆΠ΅ ΠΊ ΡΠ΅ΡΠ΅Π΄ΠΈΠ½Π΅ ΠΎΠΏΠΎΡΠ½ΡΡ ΠΏΠΎΠ²Π΅ΡΡ Π½ΠΎΡΡΠ΅ΠΉ Π³ΡΡΠ΅Π½ΠΈΡΡ. ΠΡΠΎ ΡΠ²Π΅Π»ΠΈΡΠΈΠ²Π°Π΅Ρ ΡΡΡΠΎΠΉΡΠΈΠ²ΠΎΡΡΡ ΡΡΠ°ΠΊΡΠΎΡΠ° ΠΈ ΡΠΌΠ΅Π½ΡΡΠ°Π΅Ρ ΠΌΠΎΠΌΠ΅Π½Ρ ΡΠΎΠΏΡΠΎΡΠΈΠ²Π»Π΅Π½ΠΈΡ ΠΏΠΎΠ²ΠΎΡΠΎΡΡ.
ΠΠ° ΡΡΠ°ΠΊΡΠΎΡΠ°Ρ MT3-80 ΠΈ ΠT3-8 ΠΏΡΠΈΡΠ΅ΠΏΠ½ΠΎΠ΅ ΡΡΡΡΠΎΠΉΡΡ-Π² ΠΎ ΡΠΎΡΡΠΎΠΈΡ ΠΈΠ· ΠΎΠ±ΡΡΠ½ΠΎΠΉ ΡΠΊΠΎΠ±Ρ (ΡΠΈΡ. 248, Π°). ΠΏΡΠΈΡΠ΅ΠΏΠ½ΠΎΠΉ Π²ΠΈΠ»ΠΊΠΈ, ΡΠΊΠ²ΠΎΡΠ½Ρ ΠΈ Π΄Π²ΡΡ ΠΏΠ°Π»ΡΡΠ΅Π². Π£ΡΡΡΠΎΠΉΡΡΠ²ΠΎ ΡΡΡΠ°Π½Π°Π²Π»ΠΈΠ²Π°Π΅ΡΡΡ Π² ΠΎΠ±ΠΎΠΉΠΌΡ ΠΏΠ΅ΡΠ΅Π΄Π½ΠΈΡ ΠΊΠΎΠ½ΡΠΎΠ² ΠΏΡΠΎΠ΄ΠΎΠ»ΡΠ½ΡΡ ΡΡΠ³ ΠΌΠ΅Ρ Π°Π½ΠΈΠ·ΠΌΠ° Π½Π°Π²Π΅ΡΠΊΠΈ ΠΈ ΠΊΡΠ΅ΠΏΠΈΡΡΡ ΠΊ ΠΏΡΠΎΠ΄ΠΎΠ»ΡΠ½ΡΠΌ ΡΡΠ³Π°ΠΌ ΠΏΡΠΎΡΡΠΈΠ½Π°ΠΌΠΈ ΠΎΠ³ΡΠ°Π½ΠΈΡΠΈΡΠ΅Π»ΡΠ½ΡΡ ΡΡΡΠΆΠ΅ΠΊ. Π ΡΡΠΎΠΉ ΠΊΠΎΠ½ΡΡΡΡΠΊΡΠΈΠΈ ΡΠΊΠΎΠ±Π° ΠΌΠΎΠΆΠ΅Ρ ΠΏΠ΅ΡΠ΅ΠΌΠ΅ΡΠ°ΡΡΡΡ Π³ΠΈΠ΄ΡΠ°Π²Π»ΠΈΡΠ΅ΡΠΊΠΈΠΌ ΠΏΡΠΈΠ²ΠΎΠ΄ΠΎΠΌ Π² Π²Π΅ΡΡΠΈΠΊΠ°Π»ΡΠ½ΠΎΠΉ ΠΏΠ»ΠΎΡΠΊΠΎΡΡΠΈ. Π’ΠΎΡΠΊΠ° ΠΏΡΠΈΡΠ΅ΠΏΠ° ΠΏΠΎ ΡΠΈΡΠΈΠ½Π΅ ΡΠ΅Π³ΡΠ»ΠΈΡΡΠ΅ΡΡΡ ΠΏΠ΅ΡΠ΅ΡΡΠ°Π½ΠΎΠ²ΠΊΠΎΠΉ ΠΏΠ°Π»ΡΡΠ΅Π² Ρ Π²ΠΈΠ»ΠΊΠΎΠΉ Π² ΡΠ°Π·Π½ΡΠ΅ ΠΎΡΠ²Π΅ΡΡΡΠΈΡ ΡΠΊΠΎΠ±Ρ.
ΠΠ° ΡΡΠ°ΠΊΡΠΎΡΠ°Ρ Π’-100Π, Π’-130 ΠΈ Π΄ΡΡΠ³ΠΈΡ ΠΏΡΠΈΡΠ΅ΠΏΠ½ΠΎΠ΅ ΡΡΡΡΠΎΠΉΡΡΠ²ΠΎ ΡΠΎΠ΅Π΄ΠΈΠ½Π΅Π½ΡΠ΅ΡΡΡ Ρ ΠΎΡΡΠΎΠ²ΠΎΠΌ ΡΡΠ°ΠΊΡΠΎΡΠ° ΠΈ ΡΠΎΡΡΠΎΠΈΡ ΠΈΠ· ΡΠΊΠΎΠ±Ρ ΠΌΠ°ΡΡΠ½ΠΈΠΊΠΎΠ²ΠΎΠ³ΠΎ ΡΠΈΠΏΠ° (ΡΠΈΡ. 248, Π±), ΡΠΊΡΠ΅ΠΏΠ»Π΅Π½Π½ΠΎΠΉ Π½Π° ΠΊΡΠΎΠ½ΡΡΠ΅ΠΉΠ½Π°Ρ , ΡΠ°ΡΠ½ΠΈΡΠ½ΠΎ Π·Π°ΠΊΡΠ΅ΠΏΠ»Π΅Π½Π½ΠΎΠΉ ΠΎΠ΄Π½ΠΈΠΌ ΠΊΠΎΠ½ΡΠΎΠΌ Π½Π° ΠΎΡΠΈ Π² ΠΏΠ΅ΡΠ΅Π΄Π½Π΅ΠΌ ΠΊΡΠΎΠ½ΡΡΠ΅ΠΉΠ½Π΅, ΠΈ ΡΡΡΡΠ΅ΠΉ, ΡΠ΄Π΅ΡΠΆΠΈΠ²Π°Π΅ΠΌΡΡ Π½Π° ΡΠ΅ΡΡΠ³Π΅ Π·Π°ΠΌΠΊΠ°ΠΌΠΈ. ΠΠΎΡΡΠ΅Π΄ΡΡΠ²ΠΎΠΌ ΡΡΡΡΡ Π²ΠΈΠ»ΠΊΠ° ΠΌΠΎΠΆΠ΅Ρ Π±ΡΡΡ Π·Π°ΠΊΡΠ΅ΠΏΠ»Π΅Π½Π° Π² ΠΏΡΡΠΈ ΡΠ°Π·Π»ΠΈΡΠ½ΡΡ ΠΏΠΎΠ»ΠΎΠΆΠ΅Π½ΠΈΡΡ , ΡΠ΅ΠΌ ΠΈ Π΄ΠΎΡΡΠΈΠ³Π°Π΅ΡΡΡ ΡΠ΅Π³ΡΠ»ΠΈΡΠΎΠ²ΠΊΠ° ΡΠΎΡΠΊΠΈ ΠΏΡΠΈΡΠ΅ΠΏΠ° ΠΏΠΎ ΡΠΈΡΠΈΠ½Π΅.
Π ΠΈΡ. 248. ΠΡΠΈΡΠ΅ΠΏΠ½ΡΠ΅ ΡΡΡΡΠΎΠΉΡΡΠ²Π° ΡΡΠ°ΠΊΡΠΎΡΠΎΠ²
Π ΠΈΡ. 249. ΠΠΈΠ΄ΡΠΎΡΠΈΡΠΈΡΠΎΠ²Π°Π½Π½ΡΠΉ ΠΊΡΡΠΊ ΡΡΠ°ΠΊΡΠΎΡΠ°
ΠΡΠΈΡΠ΅ΠΏΠ½ΠΎΠ΅ ΡΡΡΡΠΎΠΉΡΡΠ²ΠΎ, ΠΏΡΠ΅Π΄Π½Π°Π·Π½Π°ΡΠ΅Π½Π½ΠΎΠ΅ Π΄Π»Ρ ΡΡΠ΅ΠΏΠΊΠΈ ΡΡΠ°ΠΊΡΠΎΡΠ° Ρ Π΄ΡΡΠ»ΠΎΠΌ ΠΏΡΠΈΡΠ΅ΠΏΠ°, Π½Π°Π·ΡΠ²Π°Π΅ΡΡΡ Π±ΡΠΊΡΠΈΡΠ½ΡΠΌ ΡΡΡΡΠΎΠΉΡΡΠ²ΠΎΠΌ (ΠΏΡΠΈΡΠ΅ΠΏΠ½ΡΠΌ ΠΊΡΡΠΊΠΎΠΌ).
ΠΠ»Ρ ΡΡΠ΅ΠΏΠΊΠΈ ΡΡΠ°ΠΊΡΠΎΡΠ° Ρ ΠΎΠ΄Π½ΠΎΠΎΡΠ½ΡΠΌ ΠΏΡΠΈΡΠ΅ΠΏΠΎΠΌ ΠΊΠΎΠ»Π΅ΡΠ½ΡΠ΅ ΡΡΠ°ΠΊΡΠΎΡΡ ΠΎΠ±ΠΎΡΡΠ΄ΡΡΡΡΡ Π³ΠΈΠ΄ΡΠΎΡΠΈΡΠΈΡΠΎΠ²Π°Π½Π½ΡΠΌΠΈ ΠΊΡΡΠΊΠ°ΠΌΠΈ, ΠΏΡΠΈΠ²ΠΎΠ΄ΠΈΠΌΡΠΌΠΈ Π² Π΄Π΅ΠΉΡΡΠ²ΠΈΠ΅ ΡΠΈΠ»ΠΎΠ²ΡΠΌ ΡΠΈΠ»ΠΈΠ½Π΄ΡΠΎΠΌ (ΡΠΈΡ. 249) Π³ΠΈΠ΄ΡΠ°Π²Π»ΠΈΡΠ΅ΡΠΊΠΎΠΉ ΡΠΈΡΡΠ΅ΠΌΡ. ΠΡΡΠΊ ΠΏΡΠΈΠΊΡΠ΅ΠΏΠ»Π΅Π½ ΠΊ ΡΠ΅ΡΡΠ³Π΅ ΠΈ ΡΠ°ΡΠΊΠΎΡΠ°ΠΌΠΈ ΡΠΎΠ΅Π΄ΠΈΠ½Π΅Π½ Ρ ΠΏΠΎΠ΄Π²Π΅ΡΠ½ΡΠΌΠΈ ΡΡΡΠ°Π³Π°ΠΌΠΈ 2. ΠΠΎΠΊΠΎΠ²ΠΎΠ΅ ΡΠ°ΡΠΊΠ°ΡΠΈΠ²Π°Π½ΠΈΠ΅ ΠΊΡΡΠΊΠ° ΠΏΡΠ΅Π΄ΡΠΏΡΠ΅ΠΆΠ΄Π°Π΅ΡΡΡ Π±Π»ΠΎΠΊΠΈΡΠΎΠ²ΠΎΡΠ½ΡΠΌΠΈ ΡΡΠ³Π°ΠΌΠΈ, ΠΏΡΠΈΠΊΡΠ΅ΠΏΠ»Π΅Π½Π½ΡΠΌΠΈ ΠΊ ΠΊΡΠΎΠ½ΡΡΠ΅ΠΉΠ½Π°ΠΌ ΠΊΠ°ΡΡΠ΅ΡΠΎΠ² ΠΊΠΎΠ½Π΅ΡΠ½ΠΎΠΉ ΠΏΠ΅ΡΠ΅Π΄Π°ΡΠΈ ΡΡΠ°ΠΊΡΠΎΡΠ°. ΠΠ°ΡΠ΅Π»ΠΊΠ° ΠΏΠΎΠ΄ Π΄Π΅ΠΉΡΡΠ²ΠΈΠ΅ΠΌ ΠΏΡΡΠΆΠΈΠ½Ρ Π·Π°ΠΏΠΈΡΠ°Π΅Ρ Π·Π΅Π² ΠΊΡΡΠΊΠ°, ΠΏΡΠ΅Π΄ΡΠΏΡΠ΅ΠΆΠ΄Π°Ρ ΡΡΠΈΠΌ ΡΠ°Π·ΡΠ΅Π΄ΠΈΠ½Π΅Π½ΠΈΠ΅ ΠΊΡΡΠΊΠ° Ρ Π΄ΡΡΠ»ΠΎΠΌ.
Π ΠΈΡ. 250. ΠΡΠΊΡΠΈΡΠ½ΡΠ΅ ΠΊΡΡΠΊΠΈ ΡΡΠ°ΠΊΡΠΎΡΠΎΠ²
ΠΠΈΠ΄ΡΠΎΡΠΈΡΠΈΡΠΎΠ²Π°Π½Π½ΡΠ΅ ΠΊΡΡΠΊΠΈ ΠΏΠΎΠ·Π²ΠΎΠ»ΡΡΡ ΡΠΎΠ΅Π΄ΠΈΠ½ΠΈΡΡ ΡΡΠ°ΠΊΡΠΎΡ Ρ ΠΏΡΠΈΡΠ΅ΠΏΠΎΠΌ Π½Π΅ΠΏΠΎΡΡΠ΅Π΄ΡΡΠ²Π΅Π½Π½ΠΎ ΠΈΠ· ΠΊΠ°Π±ΠΈΠ½Ρ ΡΡΠ°ΠΊΡΠΎΡΠ°, ΡΡΠΎ ΠΎΠ±Π΅ΡΠΏΠ΅ΡΠΈΠ²Π°Π΅Ρ Π±Π΅Π·ΠΎΠΏΠ°ΡΠ½ΠΎΡΡΡ, Π»Π΅Π³ΠΊΠΎΡΡΡ ΠΈ Π±ΡΡΡΡΠΎΡΡ ΡΡΠ΅ΠΏΠΊΠΈ.
ΠΡΠΈΡΠ΅ΠΏΠ½ΠΎΠ΅ ΡΡΡΡΠΎΠΉΡΡΠ²ΠΎ ΡΡΠ°ΠΊΡΠΎΡΠΎΠ² ΠΏΡΠ΅Π΄ΡΡΠ°Π²Π»ΡΠ΅Ρ ΡΠΎΠ±ΠΎΠΉ Π±ΡΠΊΡΠΈΡΠ½ΡΠΉ ΠΊΡΡΠΊ, ΡΠΊΡΠ΅ΠΏΠ»Π΅Π½Π½ΡΠΉ Π½Π° Π·Π°Π΄Π½Π΅ΠΉ ΡΠ°ΡΡΠΈ ΡΠ°ΠΌΡ, ΠΈ, ΠΊΠ°ΠΊ ΠΏΡΠ°Π²ΠΈΠ»ΠΎ, ΡΠ²Π»ΡΠ΅ΡΡΡ Π½Π΅ΡΠ΅Π³ΡΠ»ΠΈΡΡΠ΅ΠΌΡΠΌ. ΠΠ»Ρ ΡΠΌΡΠ³ΡΠ΅Π½ΠΈΡ ΡΠΎΠ»ΡΠΊΠΎΠ² ΠΏΡΠΈ ΡΡΠΎΠ³Π°Π½ΠΈΠΈ Ρ ΠΌΠ΅ΡΡΠ°, ΡΠΎΡΠΌΠΎΠΆΠ΅Π½ΠΈΠΈ ΠΈ ΡΠ΅Π·ΠΊΠΎΠΌ ΠΈΠ·ΠΌΠ΅Π½Π΅Π½ΠΈΠΈ ΡΠΊΠΎΡΠΎΡΡΠΈ Π΄Π²ΠΈΠΆΠ΅Π½ΠΈΡ Π² ΠΏΡΠΈΡΠ΅ΠΏΠ½ΠΎΠ΅ ΡΡΡΡΠΎΠΉΡΡΠ²ΠΎ Π²Π²Π΅Π΄Π΅Π½ ΡΠΏΡΡΠ³ΠΈΠΉ ΡΠ»Π΅ΠΌΠ΅Π½Ρ β ΡΠΏΠΈΡΠ°Π»ΡΠ½Π°Ρ ΠΏΡΡΠΆΠΈΠ½Π° ΠΈΠ»ΠΈ ΡΠ΅Π·ΠΈΠ½ΠΎΠ²ΡΠΉ Π±ΡΡΠ΅Ρ.
ΠΠΎΠ½ΡΡΡΡΠΊΡΠΈΡ ΡΠ°Π·Π»ΠΈΡΠ½ΡΡ Π±ΡΠΊΡΠΈΡΠ½ΡΡ ΠΊΡΡΠΊΠΎΠ² Π½Π΅ΠΊΠΎΡΠΎΡΡΡ ΡΡΠ°ΠΊΡΠΎΡΠΎΠ² ΠΏΠΎΠΊΠ°Π·Π°Π½Π° Π½Π° ΡΠΈΡ. 250.
Π§ΠΈΡΠ°ΡΡ Π΄Π°Π»Π΅Π΅: ΠΠ°Π²Π΅ΡΠ½ΡΠ΅ ΡΡΡΡΠΎΠΉΡΡΠ²Π° ΡΡΠ°ΠΊΡΠΎΡΠΎΠ²
ΠΠ°ΡΠ΅Π³ΠΎΡΠΈΡ: – ΠΠ²ΡΠΎΠΌΠΎΠ±ΠΈΠ»ΠΈ ΠΈ ΡΡΠ°ΠΊΡΠΎΡΠ°
ΠΠ»Π°Π²Π½Π°Ρ β Π‘ΠΏΡΠ°Π²ΠΎΡΠ½ΠΈΠΊ β Π‘ΡΠ°ΡΡΠΈ β Π€ΠΎΡΡΠΌ
stroy-technics.ru
Π Π°ΠΌΠ° ΠΈ ΡΡΠ³ΠΎΠ²ΠΎ-ΡΡΠ΅ΠΏΠ½ΠΎΠ΅ ΡΡΡΡΠΎΠΉΡΡΠ²ΠΎ
Π‘ΡΡΠΎΠΈΡΠ΅Π»ΡΠ½ΡΠ΅ ΠΌΠ°ΡΠΈΠ½Ρ ΠΈ ΠΎΠ±ΠΎΡΡΠ΄ΠΎΠ²Π°Π½ΠΈΠ΅, ΡΠΏΡΠ°Π²ΠΎΡΠ½ΠΈΠΊ
ΠΠ°ΡΠ΅Π³ΠΎΡΠΈΡ:
Β Β Β Π’Π΅Ρ Π½ΠΈΡΠ΅ΡΠΊΠΎΠ΅ ΠΎΠ±ΡΠ»ΡΠΆΠΈΠ²Π°Π½ΠΈΠ΅ Π°Π²ΡΠΎΠΌΠΎΠ±ΠΈΠ»Π΅ΠΉ
Π Π°ΠΌΠ° ΠΈ ΡΡΠ³ΠΎΠ²ΠΎ-ΡΡΠ΅ΠΏΠ½ΠΎΠ΅Β ΡΡΡΡΠΎΠΉΡΡΠ²ΠΎ
Π Π°ΠΌΠ° ΡΠ²Π»ΡΠ΅ΡΡΡ Π½Π΅ΡΡΡΠ΅ΠΉ ΡΠΈΡΡΠ΅ΠΌΠΎΠΉ Π°Π²ΡΠΎΠΌΠΎΠ±ΠΈΠ»Ρ. ΠΠ½Π° Π²ΠΎΡΠΏΡΠΈΠ½ΠΈΠΌΠ°Π΅Ρ Π²ΡΠ΅ Π½Π°Π³ΡΡΠ·ΠΊΠΈ, Π²ΠΎΠ·Π½ΠΈΠΊΠ°ΡΡΠΈΠ΅ ΠΏΡΠΈ Π΄Π²ΠΈΠΆΠ΅Π½ΠΈΠΈ Π°Π²ΡΠΎΠΌΠΎΠ±ΠΈΠ»Ρ, ΠΈ ΡΠ»ΡΠΆΠΈΡ ΠΎΡΠ½ΠΎΠ²Π°Π½ΠΈΠ΅ΠΌ, Π½Π° ΠΊΠΎΡΠΎΡΠΎΠΌ ΠΌΠΎΠ½ΡΠΈΡΡΡΡ Π΄Π²ΠΈΠ³Π°ΡΠ΅Π»Ρ, Π°Π³ΡΠ΅Π³Π°ΡΡ ΡΡΠ°Π½ΡΠΌΠΈΡΡΠΈΠΈ, ΠΌΠ΅Ρ Π°Π½ΠΈΠ·ΠΌΡ ΠΎΡΠ³Π°Π½ΠΎΠ² ΡΠΏΡΠ°Π²Π»Π΅Π½ΠΈΡ, Π΄ΠΎΠΏΠΎΠ»Π½ΠΈΡΠ΅Π»ΡΠ½ΠΎΠ΅ ΠΈ ΡΠΏΠ΅ΡΠΈΠ°Π»ΡΠ½ΠΎΠ΅ ΠΎΠ±ΠΎΡΡΠ΄ΠΎΠ²Π°Π½ΠΈΠ΅, Π° ΡΠ°ΠΊΠΆΠ΅ ΠΊΠ°Π±ΠΈΠ½Ρ, ΠΊΡΠ·ΠΎΠ² ΠΈΠ»ΠΈ Π³ΡΡΠ·ΠΎ-Π½Π΅ΡΡΡΡΡ Π΅ΠΌΠΊΠΎΡΡΡ (ΡΠΈΡΡΠ΅ΡΠ½Ρ).
ΠΡΠ΅ Π³ΡΡΠ·ΠΎΠ²ΡΠ΅ Π°Π²ΡΠΎΠΌΠΎΠ±ΠΈΠ»ΠΈ ΠΈ Π»Π΅Π³ΠΊΠΎΠ²ΡΠ΅ Π°Π²ΡΠΎΠΌΠΎΠ±ΠΈΠ»ΠΈ Ρ Π±ΠΎΠ»ΡΡΠΈΠΌ (ΠΎΠ±ΡΡΠ½ΠΎ Π±ΠΎΠ»Π΅Π΅ 3,5 Π») ΡΠ°Π±ΠΎΡΠΈΠΌ ΠΎΠ±ΡΠ΅ΠΌΠΎΠΌ ΡΠΈΠ»ΠΈΠ½Π΄ΡΠΎΠ² Π΄Π²ΠΈΠ³Π°ΡΠ΅Π»Ρ ΠΈΠΌΠ΅ΡΡ ΡΠ°ΠΌΡ. ΠΠ° Π»Π΅Π³ΠΊΠΎΠ²ΡΡ Π°Π²ΡΠΎΠΌΠΎΠ±ΠΈΠ»ΡΡ ΠΎΡΠΎΠ±ΠΎ ΠΌΠ°Π»ΠΎΠ³ΠΎ ΠΈ ΠΌΠ°Π»ΠΎΠ³ΠΎ ΠΊΠ»Π°ΡΡΠΎΠ² ΠΈ Π°Π²ΡΠΎΠ±ΡΡΠ°Ρ ΡΠ°ΠΌΠ° ΠΎΡΡΡΡΡΡΠ²ΡΠ΅Ρ, Π΅Π΅ ΡΡΠ½ΠΊΡΠΈΠΈ Π²ΡΠΏΠΎΠ»Π½ΡΠ΅Ρ Π½Π΅ΡΡΡΠΈΠΉ ΠΊΡΠ·ΠΎΠ².
Π Π°ΠΌΡ. Π Π·Π°Π²ΠΈΡΠΈΠΌΠΎΡΡΠΈ ΠΎΡ ΠΊΠΎΠ½ΡΡΡΡΠΊΡΠΈΠΈ ΡΠ°ΠΌΡ (ΡΠΈΡ. 15.1) Π΄Π΅Π»ΡΡΡΡ Π½Π° Π»ΠΎΠ½ΠΆΠ΅ΡΠΎΠ½Π½ΡΠ΅ (Π»Π΅ΡΡΠ½ΠΈΡΠ½ΡΠ΅) ΠΈ ΡΠ΅Π½ΡΡΠ°Π»ΡΠ½ΡΠ΅ (Ρ ΡΠ΅Π±ΡΠΎΠ²ΡΠ΅). ΠΠ°ΠΈΠ±ΠΎΠ»ΡΡΠ΅Π΅ ΡΠ°ΡΠΏΡΠΎΡΡΡΠ°Π½Π΅Π½ΠΈΠ΅ Π² Π°Π²ΡΠΎΠΌΠΎΠ±ΠΈΠ»Π΅ΡΡΡΠΎΠ΅Π½ΠΈΠΈ ΠΏΠΎΠ»ΡΡΠΈΠ»ΠΈ ΠΏΠ΅ΡΠ²ΡΠ΅ ΠΈΠ· Π½ΠΈΡ .
ΠΠΎΠ½ΠΆΠ΅ΡΠΎΠ½Π½Π°Ρ ΡΠ°ΠΌΠ° Π³ΡΡΠ·ΠΎΠ²ΡΡ Π°Π²ΡΠΎΠΌΠΎΠ±ΠΈΠ»Π΅ΠΉ (ΡΠΈΡ. 15.1, Π°) ΡΠΎΡΡΠΎΠΈΡ ΠΈΠ· Π΄Π²ΡΡ ΠΏΡΠΎΠ΄ΠΎΠ»ΡΠ½ΡΡ Π±Π°Π»ΠΎΠΊ β Π»ΠΎΠ½ΠΆΠ΅ΡΠΎΠ½ΠΎΠ² β ΠΏΠ΅ΡΠ΅ΠΌΠ΅Π½Π½ΠΎΠ³ΠΎ ΡΠ΅ΡΠ΅Π½ΠΈΡ ΠΈ Π½Π΅ΡΠΊΠΎΠ»ΡΠΊΠΈΡ ΠΏΠΎΠΏΠ΅ΡΠ΅ΡΠΈΠ½. ΠΠΎΠ½ΠΆΠ΅ΡΠΎΠ½Ρ ΡΠ°ΠΌΡ ΠΌΠΎΠ³ΡΡ ΡΡ ΠΎΠ΄ΠΈΡΡΡΡ Π² ΠΏΠ΅ΡΠ΅Π΄Π½Π΅ΠΉ ΡΠ°ΡΡΠΈ (Π°Π²ΡΠΎΠΌΠΎΠ±ΠΈΠ»ΠΈ ΠΠΠ) ΠΈΠ»ΠΈ ΡΠ°ΡΠΏΠΎΠ»Π°Π³Π°ΡΡΡΡ ΠΏΠ°ΡΠ°Π»Π»Π΅Π»ΡΠ½ΠΎ ΠΎΠ΄ΠΈΠ½ Π΄ΡΡΠ³ΠΎΠΌΡ (Π°Π²ΡΠΎΠΌΠΎΠ±ΠΈΠ»ΠΈ ΠΠΠ). Π‘ΠΏΠ΅ΡΠ΅Π΄ΠΈ ΠΊ Π»ΠΎΠ½ΠΆΠ΅ΡΠΎΠ½Π°ΠΌ ΠΊΡΠ΅ΠΏΡΡΡΡ Π±ΡΠΊΡΠΈΡΠ½ΡΠ΅ ΠΊΡΡΠΊΠΈ ΠΈ ΠΏΠ΅ΡΠ΅Π΄Π½ΠΈΠΉ Π±ΡΡΠ΅Ρ, ΠΏΡΠ΅Π΄ΠΎΡ ΡΠ°Π½ΡΡΡΠΈΠΉ Π°Π²ΡΠΎΠΌΠΎΠ±ΠΈΠ»Ρ ΠΎΡ ΠΏΠΎΠ²ΡΠ΅ΠΆΠ΄Π΅Π½ΠΈΠΉ.
ΠΠ° ΠΏΠ΅ΡΠ²ΠΎΠΉ ΠΏΠΎΠΏΠ΅ΡΠ΅ΡΠΈΠ½Π΅ ΡΠ°ΠΌΡ ΠΊΡΠ΅ΠΏΡΡΡΡ ΡΠ°Π΄ΠΈΠ°ΡΠΎΡ ΠΈ ΠΏΠ΅ΡΠ΅Π΄Π½ΠΈΠ΅ ΠΎΠΏΠΎΡΡ (ΠΎΠ΄Π½Π° ΠΈΠ»ΠΈ Π΄Π²Π΅) Π΄Π²ΠΈΠ³Π°ΡΠ΅Π»Ρ, Π·Π°Π΄Π½ΠΈΠ΅ Π΅Π³ΠΎ ΠΎΠΏΠΎΡΡ β ΠΊΡΠΎΠ½ΡΡΠ΅ΠΉΠ½Ρ β ΠΏΡΠΈΠΊΠ»Π΅ΠΏΠ°Π½Ρ ΠΊ Π»ΠΎΠ½ΠΆΠ΅ΡΠΎΠ½Π°ΠΌ. ΠΠ΅ΡΠ΅Π΄Π½ΠΈΠ΅ ΡΠ΅ΡΡΠΎΡΡ ΡΡΡΠ°Π½Π°Π²Π»ΠΈΠ²Π°ΡΡ Π½Π° ΠΊΡΠΎΠ½ΡΡΠ΅ΠΉΠ½Π°Ρ . Π Π΅Π·ΠΈΠ½ΠΎΠ²ΡΠ΅ Π±ΡΡΠ΅ΡΠ° ΠΏΡΠ΅Π΄ΠΎΡ ΡΠ°Π½ΡΡΡ Π»ΠΎΠ½ΠΆΠ΅ΡΠΎΠ½Ρ ΠΎΡ ΡΠ΄Π°ΡΠΎΠ². ΠΠ΅ΠΆΠ΄Ρ ΠΊΡΠΎΠ½ΡΡΠ΅ΠΉΠ½Π°ΠΌΠΈ ΡΠ΅ΡΡΠΎΡ Π½Π° Π»Π΅Π²ΠΎΠΌ Π»ΠΎΠ½ΠΆΠ΅ΡΠΎΠ½Π΅ ΠΊΡΠ΅ΠΏΠΈΡΡΡ ΠΊΡΠΎΠ½ΡΡΠ΅ΠΉΠ½ Π΄Π»Ρ ΠΊΡΠ΅ΠΏΠ»Π΅Π½ΠΈΡ ΠΊΠ°ΡΡΠ΅ΡΠ° ΡΡΠ»Π΅Π²ΠΎΠ³ΠΎ ΠΌΠ΅Ρ Π°Π½ΠΈΠ·ΠΌΠ°.
Π ΠΈΡ. 15.1. ΠΠ²ΡΠΎΠΌΠΎΠ±ΠΈΠ»ΡΠ½ΡΠ΅ ΡΠ°ΠΌΡ:
Π°βΠ»ΠΎΠ½ΠΆΠ΅ΡΠΎΠ½Π½Π°Ρ; Π±βΡΠ΅Π½ΡΡΠ°Π»ΡΠ½Π°Ρ
ΠΠ° Π²ΡΠΎΡΠΎΠΉ ΠΏΠΎΠΏΠ΅ΡΠ΅ΡΠΈΠ½Π΅ ΡΠ°ΠΌΡ ΡΠ½ΠΈΠ·Ρ ΠΊΡΠ΅ΠΏΠΈΡΡΡ ΠΏΡΠΎΠΌΠ΅ΠΆΡΡΠΎΡΠ½Π°Ρ ΠΎΠΏΠΎΡΠ° ΠΊΠ°ΡΠ΄Π°Π½Π½ΠΎΠΉ ΠΏΠ΅ΡΠ΅Π΄Π°ΡΠΈ. Π Π·Π°Π΄Π½Π΅ΠΉ ΡΠ°ΡΡΠΈ ΡΠ°ΠΌΡ Π½Π° Π»ΠΎΠ½ΠΆΠ΅ΡΠΎΠ½Π°Ρ ΡΠ°ΡΠΏΠΎΠ»ΠΎΠΆΠ΅Π½Ρ ΠΊΡΠΎΠ½ΡΡΠ΅ΠΉΠ½Ρ Π΄Π»Ρ ΠΊΡΠ΅ΠΏΠ»Π΅Π½ΠΈΡ Π·Π°Π΄Π½ΠΈΡ ΡΠ΅ΡΡΠΎΡ ΠΈ ΠΊΡΠΎΠ½ΡΡΠ΅ΠΉΠ½Ρ, ΡΠ»ΡΠΆΠ°ΡΠΈΠ΅ ΠΎΠΏΠΎΡΠ°ΠΌΠΈ Π΄Π»Ρ ΠΊΠΎΠ½ΡΠΎΠ² Π΄ΠΎΠΏΠΎΠ»Π½ΠΈΡΠ΅Π»ΡΠ½ΡΡ ΡΠ΅ΡΡΠΎΡ.
ΠΠ° Π»Π΅Π²ΠΎΠΌ Π»ΠΎΠ½ΠΆΠ΅ΡΠΎΠ½Π΅ ΡΠ°ΠΌΡ ΠΈΠΌΠ΅Π΅ΡΡΡ Π³Π½Π΅Π·Π΄ΠΎ Π΄Π»Ρ ΠΊΡΠ΅ΠΏΠ»Π΅Π½ΠΈΡ Π°ΠΊΠΊΡΠΌΡΠ»ΡΡΠΎΡΠ½ΠΎΠΉ Π±Π°ΡΠ°ΡΠ΅ΠΈ, Π° Π½Π° ΠΏΡΠ°Π²ΠΎΠΌ β ΠΎΡΠΊΠΈΠ΄Π½ΠΎΠΉ ΠΊΡΠΎΠ½ΡΡΠ΅ΠΉΠ½ Π·Π°ΠΏΠ°ΡΠ½ΠΎΠ³ΠΎ ΠΊΠΎΠ»Π΅ΡΠ°. ΠΡΠΎΠ½ΡΡΠ΅ΠΉΠ½Ρ ΡΠ»ΡΠΆΠ°Ρ Π΄Π»Ρ ΠΊΡΠ΅ΠΏΠ»Π΅Π½ΠΈΡ ΠΏΠ»Π°ΡΡΠΎΡΠΌΡ, Π° ΠΊΡΠΎΠ½ΡΡΠ΅ΠΉΠ½ β Π΄Π»Ρ ΡΠΈΠΊΡΠ°ΡΠΈΠΈ ΠΏΠΎΠ»ΠΎΠΆΠ΅Π½ΠΈΡ ΠΏΡΡΠΊΠΎΠ²ΠΎΠΉ ΡΡΠΊΠΎΡΡΠΊΠΈ. ΠΠ° Π·Π°Π΄Π½Π΅ΠΉ ΠΏΠΎΠΏΠ΅ΡΠ΅ΡΠΈΠ½Π΅ ΡΠ°ΡΠΏΠΎΠ»ΠΎΠΆΠ΅Π½ΠΎ ΡΡΠ³ΠΎΠ²ΠΎ-ΡΡΠ΅ΠΏΠ½ΠΎΠ΅ ΡΡΡΡΠΎΠΉΡΡΠ²ΠΎ, Π° Π½Π° Π·Π°Π΄Π½Π΅ΠΌ ΠΊΠΎΠ½ΡΠ΅ ΠΏΡΠ°Π²ΠΎΠ³ΠΎ Π»ΠΎΠ½ΠΆΠ΅ΡΠΎΠ½Π° β ΠΊΡΠΎΠ½ΡΡΠ΅ΠΉΠ½ ΡΠΊΠ°Π·Π°ΡΠ΅Π»Ρ ΠΏΠΎΠ²ΠΎΡΠΎΡΠ°.
ΠΠ° Π»Π΅Π³ΠΊΠΎΠ²ΡΡ Π°Π²ΡΠΎΠΌΠΎΠ±ΠΈΠ»ΡΡ ΡΠ΅ΠΌΠ΅ΠΉΡΡΠ²Π° Β«ΠΠΎΡΠΊΠ²ΠΈΡΒ» ΠΈ ΠΠΠ Π² ΠΏΠ΅ΡΠ΅Π΄Π½Π΅ΠΉ ΡΠ°ΡΡΠΈ ΠΊΡΠ·ΠΎΠ²Π° ΡΡΡΠ°Π½ΠΎΠ²Π»Π΅Π½Π° ΠΏΠΎΠ»ΡΡΠ°ΠΌΠ° (ΠΏΠΎΠ΄ΡΠ°ΠΌΠ½ΠΈΠΊ), ΠΏΡΠΈΠΊΡΠ΅ΠΏΠ»Π΅Π½Π½Π°Ρ Π±ΠΎΠ»ΡΠ°ΠΌΠΈ ΠΊ ΠΏΠΎΠ»Ρ ΠΊΡΠ·ΠΎΠ²Π°. Π Π½Π΅ΠΉ ΠΊΡΠ΅ΠΏΠΈΡΡΡ Π΄Π²ΠΈΠ³Π°ΡΠ΅Π»Ρ Π² ΡΠ±ΠΎΡΠ΅ ΡΠΎ ΡΡΠ΅ΠΏΠ»Π΅Π½ΠΈΠ΅ΠΌ ΠΈ ΠΊΠΎΡΠΎΠ±ΠΊΠΎΠΉ ΠΏΠ΅ΡΠ΅Π΄Π°Ρ.
Π¦Π΅Π½ΡΡΠ°Π»ΡΠ½Π°Ρ ΡΠ°ΠΌΠ° (ΡΠΈΡ. 15.1, Π±) ΡΠΎΡΡΠΎΠΈΡ ΠΈΠ· ΡΠ΅Π½ΡΡΠ°Π»ΡΠ½ΠΎΠΉ Π½Π΅ΡΡΡΠ΅ΠΉ Π±Π°Π»ΠΊΠΈ Ρ ΠΏΠΎΠΏΠ΅ΡΠ΅ΡΠΈΠ½Π°ΠΌΠΈ. ΠΠ΅ΡΡΡΠ°Ρ Π±Π°Π»ΠΊΠ° ΠΌΠΎΠΆΠ΅Ρ ΠΈΠΌΠ΅ΡΡ ΠΊΡΡΠ³Π»ΠΎΠ΅ ΠΈΠ»ΠΈ ΡΠ²Π΅Π»Π»Π΅ΡΠ½ΠΎΠ΅ ΡΠ΅ΡΠ΅Π½ΠΈΠ΅. Π Π½Π΅ΠΊΠΎΡΠΎΡΡΡ ΡΠ»ΡΡΠ°ΡΡ ΡΠ°ΠΌΠ° ΠΎΠ±ΡΡΠ·ΡΠ΅ΡΡΡ Π² ΡΠ΅Π·ΡΠ»ΡΡΠ°ΡΠ΅ ΡΠΎΠ΅Π΄ΠΈΠ½Π΅Π½ΠΈΡ ΡΠΏΠ΅ΡΠΈΠ°Π»ΡΠ½ΡΠΌΠΈ ΠΏΠ°ΡΡΡΠ±ΠΊΠ°ΠΌΠΈ ΠΊΠ°ΡΡΠ΅ΡΠ° ΡΠ°Π·Π΄Π°ΡΠΎΡΠ½ΠΎΠΉ ΠΊΠΎΡΠΎΠ±ΠΊΠΈ ΠΈ ΠΊΠ°ΡΡΠ΅ΡΠΎΠ² Π³Π»Π°Π²Π½ΡΡ ΠΏΠ΅ΡΠ΅Π΄Π°Ρ. ΠΠ΅ΠΆΠ΄Ρ ΡΠ»Π°Π½ΡΠ°ΠΌΠΈ ΠΏΠ°ΡΡΡΠ±ΠΊΠΎΠ² ΠΈ ΠΊΠ°ΡΡΠ΅ΡΠΎΠ² ΡΡΡΠ°Π½ΠΎΠ²Π»Π΅Π½Ρ ΠΏΠΎΠΏΠ΅ΡΠ΅ΡΠΈΠ½Ρ, ΡΠ»ΡΠΆΠ°ΡΠΈΠ΅ ΠΎΠΏΠΎΡΠ°ΠΌΠΈ Π΄Π²ΠΈΠ³Π°ΡΠ΅Π»Ρ, ΠΊΠ°Π±ΠΈΠ½Ρ, ΠΊΡΠ·ΠΎΠ²Π° ΠΈ Π΄ΡΡΠ³ΠΈΡ Π°Π³ΡΠ΅Π³Π°ΡΠΎΠ². Π’Π°ΠΊΠΈΠ΅ ΡΠ°ΠΌΡ ΠΎΠ±Π»Π°Π΄Π°ΡΡ Π²ΡΡΠΎΠΊΠΎΠΉ ΠΏΡΠΎΡΠ½ΠΎΡΡΡΡ Π½Π° ΠΈΠ·Π³ΠΈΠ±, Π½ΠΎ ΠΈΠ·-Π·Π° ΡΠ»ΠΎΠΆΠ½ΠΎΡΡΠΈ ΠΈΡ ΠΈΠ·Π³ΠΎΡΠΎΠ²Π»Π΅Π½ΠΈΡ ΡΠΈΡΠΎΠΊΠΎΠ³ΠΎ ΡΠ°ΡΠΏΡΠΎΡΡΡΠ°Π½Π΅Π½ΠΈΡ Π² ΠΎΡΠ΅ΡΠ΅ΡΡΠ²Π΅Π½Π½ΠΎΠΌ ΠΈ Π·Π°ΡΡΠ±Π΅ΠΆΠ½ΠΎΠΌ Π°Π²ΡΠΎΠΌΠΎΠ±ΠΈΠ»Π΅ΡΡΡΠΎΠ΅Π½ΠΈΠΈ ΠΎΠ½ΠΈ Π½Π΅ ΠΏΠΎΠ»ΡΡΠΈΠ»ΠΈ.
Π’ΡΠ³ΠΎΠ²ΠΎ-ΡΡΠ΅ΠΏΠ½ΠΎΠ΅ ΡΡΡΡΠΎΠΉΡΡΠ²ΠΎ. ΠΡΠΎ ΡΡΡΡΠΎΠΉΡΡΠ²ΠΎ ΠΏΡΠ΅Π΄Π½Π°Π·Π½Π°ΡΠ΅Π½ΠΎ Π΄Π»Ρ ΡΡΠ΅ΠΏΠΊΠΈ Π°Π²ΡΠΎΠΌΠΎΠ±ΠΈΠ»Π΅ΠΉ-ΡΡΠ³Π°ΡΠ΅ΠΉ Ρ ΠΏΡΠΈΡΠ΅ΠΏΠ°ΠΌΠΈ ΠΈ ΡΠ³Π»Π°ΠΆΠΈΠ²Π°Π½ΠΈΡ ΠΎΡΠ΅Π²ΡΡ ΡΠΎΠ»ΡΠΊΠΎΠ² Π² ΠΎΠ±ΠΎΠΈΡ Π½Π°ΠΏΡΠ°Π²Π»Π΅Π½ΠΈΡΡ , Π²ΠΎΠ·Π½ΠΈΠΊΠ°ΡΡΠΈΡ ΠΏΡΠΈ Π΄Π²ΠΈΠΆΠ΅Π½ΠΈΠΈ Π°Π²ΡΠΎΠΏΠΎΠ΅Π·Π΄Π°. Π’ΡΠ³ΠΎΠ²ΠΎ-ΡΡΠ΅ΠΏΠ½ΠΎΠ΅ ΡΡΡΡΠΎΠΉΡΡΠ²ΠΎ (ΡΠΈΡ. 15.2) ΠΏΡΠ΅Π΄ΡΡΠ°Π²Π»ΡΠ΅Ρ ΡΠΎΠ±ΠΎΠΉ ΡΡΠ°Π»ΡΠ½ΠΎΠΉ ΠΊΠΎΠ²Π°Π½Π½ΡΠΉ ΠΊΡΡΠΊ, Π½Π° ΡΡΠ΅ΡΠΆΠ½Π΅ ΠΊΠΎΡΠΎΡΠΎΠ³ΠΎ ΠΌΠ΅ΠΆΠ΄Ρ Π΄Π²ΡΠΌΡ ΡΠΏΠΎΡΠ½ΡΠΌΠΈ ΡΠ°ΠΉΠ±Π°ΠΌΠΈ ΠΈ ΡΡΡΠ°Π½ΠΎΠ²Π»Π΅Π½ ΡΠ΅Π·ΠΈΠ½ΠΎΠ²ΡΠΉ ΡΠΏΡΡΠ³ΠΈΠΉ ΡΠ»Π΅ΠΌΠ΅Π½Ρ-Π±ΡΡΠ΅Ρ,β ΠΏΠΎΠ΄ΠΆΠΈΠΌΠ°Π΅ΠΌΡΠΉ Π³Π°ΠΉΠΊΠΎΠΉ. Π‘ΡΠ΅ΡΠΆΠ΅Π½Ρ ΠΊΡΡΠΊΠ° Π² ΡΠ±ΠΎΡΠ΅ Ρ Π±ΡΡΠ΅ΡΠΎΠΌ ΠΏΠΎΠΌΠ΅ΡΠ΅Π½ Π² ΠΊΠΎΡΠΏΡΡΠ΅, ΠΊΠΎΡΠΎΡΡΠΉ Π²ΠΌΠ΅ΡΡΠ΅ Ρ ΠΊΡΡΡΠΊΠΎΠΉ Π±ΠΎΠ»ΡΠ°ΠΌΠΈ ΠΏΡΠΈΠΊΡΠ΅ΠΏΠ»Π΅Π½ ΠΊ Π·Π°Π΄Π½Π΅ΠΉ ΠΏΠΎΠΏΠ΅ΡΠ΅ΡΠΈΠ½Π΅ ΡΠ°ΠΌΡ. ΠΡΡΡΡΠΏΠ°ΡΡΠΈΠΉ ΠΈΠ· ΡΡΠ°ΠΊΠ°Π½Π° ΠΊΠΎΠ½Π΅Ρ ΡΡΠ΅ΡΠΆΠ½Ρ Ρ Π·Π°ΡΠΏΠ»ΠΈΠ½ΡΠΎΠ²Π°Π½Π½ΠΎΠΉ Π½Π° Π½Π΅ΠΌ Π³Π°ΠΉΠΊΠΎΠΉ Π·Π°ΠΊΡΡΠ²Π°Π΅ΡΡΡ ΠΊΠΎΠ»ΠΏΠ°ΠΊΠΎΠΌ.
Π ΠΈΡ. 15.2. Π’ΡΠ³ΠΎΠ²ΠΎ-ΡΡΠ΅ΠΏΠ½ΠΎΠ΅ ΡΡΡΡΠΎΠΉΡΡΠ²ΠΎ
ΠΠ°ΡΠ΅Π»ΠΊΠ° ΠΊΡΡΠΊΠ° Π·Π°ΡΡΠΎΠΏΠΎΡΠ΅Π½Π° ΡΠΎΠ±Π°ΡΠΊΠΎΠΉ, ΡΡΡΠ°Π½ΠΎΠ²Π»Π΅Π½Π½ΠΎΠΉ Π½Π° ΠΎΡΠΈ, Π° ΡΠ°ΠΊΠΆΠ΅ ΡΠΏΠ»ΠΈΠ½ΡΠΎΠΌ, ΡΠΎΠ΅Π΄ΠΈΠ½Π΅Π½Π½ΡΠΌ ΡΠ΅ΠΏΠΎΡΠΊΠΎΠΉ ΠΈ Π²Ρ ΠΎΠ΄ΡΡΠΈΠΌ Π² ΠΎΡΠ²Π΅ΡΡΡΠΈΠ΅ ΡΠΎΠ±Π°ΡΠΊΠΈ.
Π§ΠΈΡΠ°ΡΡ Π΄Π°Π»Π΅Π΅: ΠΠ΅ΡΠ΅Π΄Π½ΠΈΠΉ ΡΠΏΡΠ°Π²Π»ΡΠ΅ΠΌΡΠΉ ΠΌΠΎΡΡ ΠΈ ΡΠ³Π»Ρ ΡΡΡΠ°Π½ΠΎΠ²ΠΊΠΈ ΠΊΠΎΠ»Π΅Ρ
ΠΠ°ΡΠ΅Π³ΠΎΡΠΈΡ: – Π’Π΅Ρ Π½ΠΈΡΠ΅ΡΠΊΠΎΠ΅ ΠΎΠ±ΡΠ»ΡΠΆΠΈΠ²Π°Π½ΠΈΠ΅ Π°Π²ΡΠΎΠΌΠΎΠ±ΠΈΠ»Π΅ΠΉ
ΠΠ»Π°Π²Π½Π°Ρ β Π‘ΠΏΡΠ°Π²ΠΎΡΠ½ΠΈΠΊ β Π‘ΡΠ°ΡΡΠΈ β Π€ΠΎΡΡΠΌ
stroy-technics.ru
ΠΠΎΠ±Π°Π²ΠΈΡΡ ΠΊΠΎΠΌΠΌΠ΅Π½ΡΠ°ΡΠΈΠΉ