Система карьер – Система диспетчеризации «КАРЬЕР»: от мониторинга большегрузных автосамосвалов к управлению горно-транспортным комплексом и оптимизации горных работ в карьере
Система диспетчеризации «КАРЬЕР»: от мониторинга большегрузных автосамосвалов к управлению горно-транспортным комплексом и оптимизации горных работ в карьере
Д.Я.Владимиров, А.Ф.Клебанов, «ВИСТ Групп»
А.И.Перепелицын, Федеральная служба по технологическому надзору
Эффективная работа современных горнодобывающих предприятий невозможна без развитого горно-транспортного комплекса (ГТК), включающего в свой состав большое количество машин и оборудования различного назначения (автосамосвалы, топливозаправщики, локомотивы и подвижной состав, экскаваторы, бульдозеры, грейдеры, буровые станки и другое вспомогательное оборудование). Поэтому на предприятиях значительное внимание уделяется увеличению производительности оборудования; организации планомерного его ремонта и обслуживания; обеспечению экономии всех видов материальных ресурсов, снижению расхода топлива, шин; оптимизации загрузки транспортных средств; стабилизации показателей качества руды, поступающей в переработку.
Решение этих задач и обеспечение эффективности эксплуатации ГТК в настоящее время невозможно без использования инженерными и управленческими службами горнодобывающих предприятий современных компьютерных технологий, методов автоматизированного управления технологическими процессами. АСУ ГТК, как часть автоматизированной системы горного предприятия, предназначена для управления выемочно-позрузочным, автомобильным и железнодорожным транспортом и буровыми станками; мониторинга основного и вспомогательного оборудования; управления и контроля объемов и качества руды, поступающей на переработку.
Реализация АСУ ГТК осуществляется, как правило, в три этапа:
1. Управление экскаваторно-автомобильным комплексом, состав которого определяют парк автосамосвалов и топливозаправщиков, а также парк экскаваторов.
2. Управление железнодорожным комплексом, состоящим из тепловозов, электровозов и вспомогательной железнодорожной техники.
3. Управление работой бурового и вспомогательного оборудования, включающего буровые станки, бульдозеры, тракторы и автогрейдеры.
На первом этапе система АСУ ГТК обеспечивает следующие основные функции:
– управление оборудованием в режиме реального времени и управление качеством руды при погрузке и ее разгрузке на складе;
– контроль движения руды, вскрыши и в целом горной массы, контроль соблюдения маршрутов движения, а также загрузки автосамосвалов;
– мониторинг работы двигателей и узлов автосамосвалов, эксплуатации шин, заправок и расхода топлива, времени технического обслуживания оборудования и т.д.
На втором этапе формирования АСУ ГТК добавляется возможность мониторинга местоположения железнодорожного транспорта, его погрузки и выгрузки, простоев и количества отгруженных думпкаров, а также контроля соблюдения скоростных режимов поездов, расхода топлива тепловозами, объемов и качества руды, подаваемой на дробильно-обогатительную фабрику, что позволяет оперативно получать цифровую транспортную модель карьера по участкам железнодорожных путей и итоговый график движения технологических поездов за смену).
На третьем этапе достигается возможность самонаведения буровых станков на проектную точку без предварительной маркшейдерской выноски, передачи координат пробуренных скважин в маркшейдерскую службу и бюро буро-взрывных работ для возможности своевременной корректировки проектов на бурение и взрыв, а также проводится мониторинг и контроль в реальном масштабе времени как параметров процесса бурения, так и технического состояния буровых станков.
Система диспетчеризации горно-транспортного оборудования «КАРЬЕР», разработанная российской компанией «ВИСТ Групп», внедряется на горных предприятиях России и СНГ с 1999 года. Изначально, на первых объектах внедрения (Полтавский ГОК, ЗАО «Черниговец») [1], система «КАРЬЕР» решала задачи мониторинга большегрузных автосамосвалов, т.е. слежения в режиме реального времени за состоянием самосвала (загрузкой, расходом топлива, скоростью, местоположением), учета этих параметров, а также простоев и нарушений технологических режимов эксплуатации автосамосвала. Эти работы проводились совместно с РУПП «Белорусский автомобильный завод». Дальнейшее развитие системы диспетчеризации «КАРЬЕР» направлено на создание на горном предприятии полнофункциональной системы управления горно-транспортным комплексом.
Модернизация системы идет по следующим направлениям:
– развитие бортового оборудования транспортно-погрузочного комплекса;
– развитие программного обеспечения диспетчерского центра;
– развитие средств организации передачи данных в диспетчерский центр.
Рассмотрим кратко основные результаты, достигнутые в этих направлениях.
Бортовое оборудование
Система контроля загрузки и топлива СКЗиТ [1, 2], устанавливаемая на автосамосвалы грузоподъемностью 55–220 т непосредственно на заводе «БЕЛАЗ», интегрируется с другими бортовыми электронными системами управления и контроля состояния автосамосвала. В первую очередь это относится к Системе управления тяговым электроприводом [2] (СУТЭП), а также к системам диагностики основных узлов и агрегатов самосвала (контроль работы дизеля, давления в шинах и др.) (рис. 1). Такая интеграция позволяет качественно усовершенствовать алгоритмы работы систем, по сравнению с их автономным функционированием. Например, для более точного управления работой тяговым электроприводом необходима информация о загрузке автосамосвала, уклоне дороги при его движении, которая передается от СКЗиТ непосредственно в СУТЭП. Передача данных осуществляется по CAN-интерфейсу, которым оснащены бортовые контроллеры СКЗ 02.01 и СУТЭП. Подход к интеграции СКЗиТ и других бортовых электронных комплексов c помощью CAN-интерфейса является общим для развития электронных систем автосамосвала БелАЗ. При этом предусмотренное программно-аппаратное расширение СКЗ 02.01 радионавигационным блоком с встроенным GPS приемником (платой РНБ) – системой, управляющей передачей данных по выделенному радиоканалу, – делает возможным передачу информации от датчиков СУТЭП и систем диагностики непосредственно в диспетчерский центр, сохранение этой информации на сервере системы «КАРЬЕР» и последующую организацию автоматизированного рабочего места механика автобазы (АРМ-М) (рис. 2). Работа автосамосвала БелАЗ-75131 с интегрированными системами СКЗиТ и СУТЭП и непрерывной передачей данных в диспетчерский центр была продемонстрирована в январе 2004 г. на совещании потребителей РУПП «Белорусский автомобильный завод».
Система диспетчеризации «КАРЬЕР» допускает работу с самосвалами других производителей, также оснащенных электронными системами контроля и диагностики. Так, в июле 2004 г. в состав диспетчерской системы на Полтавском ГОКе были включены автосамосвалы Komatsu HD-785 и HD-1200 (рис. 3). Бортовой контроллер PLC II, установленный на этих самосвалах, был соединен по RS-232 с СКЗ 02.01, оснащенным блоком РНБ. Дальнейшее согласование протоколов обмена данными между СКЗ 02.01 и PLC II сделало возможным передачу в диспетчерские центры рудоуправления и автобазы Полтавского ГОКа информации о загрузке, расходе топлива (самосвалы оснащались дополнительно датчиком уровня топлива в баке УТ-90), а также местоположении парка автосамосвалов Komatsu, аналогично информации, передаваемой от автосамосвалов БелАЗ.
До 2004 года система СКЗиТ, вследствие конструктивных особенностей автосамосвалов БелАЗ, могла быть установлена на самосвалах грузоподъемностью от 55 т и выше. Для определения степени загрузки самосвала в этой системе используется методика интегрированного вычисления веса груза по давлению в газомаслонаполненных амортизаторах подвески, измеренному высокоточными электронными датчиками давления (WIKA). При этом конструкция автосамосвалов БелАЗ грузоподъемностью 30–45 тонн, оснащенных шестью двухкамерными подвесками, не позволяла распространить на них указанную выше методику определения загрузки.
С целью преодоления этих ограничений в 2003–2004 гг. была разработана и опробована в заводских и натурных условиях система контроля загрузки, адаптированная для автосамосвалов БелАЗ грузоподъемностью 30 – 45 тонн и основанная на применении датчиков силы, монтируемых непосредственно на технологических «пальцах» подвески (рис. 4). Было установлено, что для определения загрузки с точностью до 1.5% достаточно получение информации от 4-х датчиков силы и показаний инклинометра (ИК-02) – датчика продольного крена, который также как и в случае определения загрузки для большегрузных автосамосвалов, вносит существенные коррективы в работу алгоритмов.
Направление развития бортового оборудования для реализации второго и третьего этапов создания АСУ ГТК (управление железнодорожным транспортом, буровым и вспомогательным оборудованием) определяется функциями, которые должна выполнять система на этих этапах. В большинстве случаев эти функции сводятся к мониторингу в режиме реального времени местоположения и состояния оборудования (информация о начале и завершении погрузки, выгрузки, движении, простоях и т.п.), соблюдения скоростных режимов, а также контролю за уровнем и расходом топлива. Эти задачи решаются установкой на транспортные средства СКЗ 02.01 с блоком РНБ и монтажом дополнительных датчиков состояния транспортных средств. Так, в проекте, реализуемом «ВИСТ Групп» в ЗАО «Черниговец», для определения расхода топлива на тепловозах устанавливаются как датчики уровня топлива поплавкового типа, аналогичные датчикам СКЗиТ автосамосвалов (УТ-90, УТ-60), так и расходомеры (СДМ). Для определения полезной работы транспортных средств (например, бульдозеров, грейдеров) может быть использована методика, основанная на определении комплексного показателя по датчикам позиционирования (GPS), датчику моточасов, расходомеру и датчику нагрузки на отвал, аналогичному описанному выше датчику силы, применяемому для определения загрузки малых БелАЗов. Следует отметить, что универсальность разработанного датчика силы (ДЗ-20) делает возможным его применение для определения загрузки практически любого грузоперевозящего транспортного средства. Например, в настоящее время рассматривается возможность применения этого датчика и других элементов системы «КАРЬЕР» для диспетчеризации и слежения за работой зарядных машин на базе КрАЗа и MAN, а также технологического транспорта ГМК «Норильский Никель».
Исключением от перечисленных выше «традиционных» задач мониторинга оборудования является задача самонаведения бурового станка на проектную точку скважины. Эта задача, также как и задача определения координат экскаватора с дециметровой точностью в плане и по высоте, может быть решена только при оснащении оборудования системами высокоточного позиционирования (СВП). Состав бортового оборудования, а также оборудования диспетчерского центра в этом случае существенно модифицируется. Вместо блока РНБ, обеспечивающего точность определения координат мобильного объекта порядка 3–5 метров в плане, необходимо использовать двухантенный GPS приемник и систему передачи данных RTK (рис. 5). Эволюцию развития системы диспетчеризации «КАРЬЕР» в связи с увеличением парка транспортных средств и требованиями к точности позиционирования экскаваторов и бурстанков иллюстрирует рис. 6., на котором схематично отражены этапы перехода системы от мониторинга большегрузных автосамосвалов к полному управлению горно-транспортным комплексом угольного разреза «Черниговский» в Кузбассе (отмеченные на рис. 6 системы видеонаблюдения и мониторинга технического состояния оборудования (МТСО), а также проблемы интеграции системы «КАРЬЕР» с АСУП «Галактика» и системой геологического моделирования и планирования горных работ выходят за рамки рассматриваемых в данной статье вопросов).
Программное обеспечение диспетчерского центра
Расширение функциональных возможностей программного обеспечения диспетчерского центра достигается за счет постоянного наращивания числа специализированных автоматизированных рабочих мест, которое происходит при расширении круга пользователей системы (функциональных служб горного предприятия) при переходе к полномасштабному управлению горно-транспортным комплексом. Так, если на первом этапе программное обеспечение диспетчерского центра включает в себя пять автоматизированных рабочих места пользователя, а именно: АРМ горного диспетчера, АРМ диспетчера автобазы, АРМ маркшейдера, АРМ системного администратора и АРМ технического директора, то к моменту завершения третьего этапа диспетчерский центр (понимаемый как распределенная информационная среда) может быть оснащен дополнительно АРМ начальника смены рудоуправления, АРМ производственного отдела рудоуправления, АРМ бюро буро-взрывных работ, АРМ начальника смены бурового участка, АРМ поездного диспетчера управления железнодорожным транспортом (рис. 7), АРМ службы ГСМ, АРМ инженера ТО, АРМ геологоразведочного отдела, АРМ производственного отдела разреза, АРМ директора по производству.
Вовлечение в систему управления горно-транспортного комплекса новых пользователей, охватывающих практически все организационно-технические службы комбината, невозможно без постоянного развития гибкости системы, повышения ее функциональности и удобства работы, что реализуется благодаря специальной многокомпонентной структуре программного обеспечения и применению новых технологий программирования. Программное обеспечение сервера приложений с помощью специально разработанной технологии UMP.NET обрабатывает входную информацию, как полученную от мобильных объектов, так и введенную пользователями, результаты этой обработки сохраняются в базе данных. При этом на сервере базы данных ORACLE хранится вся информация о работе оборудования, включая полную историю движения и показаний датчиков каждого мобильного объекта; данные о рейсах, в том числе расстояние транспортировки, массу и вид перевезенного груза; данные об остановках и нарушениях скоростного режима, итоговая информация по смене и суткам, и т. д. Программное обеспечение рабочих мест, построенное на базе нашего программного продукта XRTL Explorer, взаимодействует с базой данных через сервер приложений.
Таким образом, создание компонент UMP.NET и XRTL Explorer дает возможность пользователям по своему желанию самостоятельно разрабатывать и изменять функциональность системы диспетчеризации.
Управление горно-транспортным комплексом невозможно без развития методов автоматизированного диспетчерования оборудования и производственных процессов горного предприятия. В первую очередь это относится к оптимизации работы автомобильно-экскаваторным комплексом. С целью вычисления оптимального распределения автосамосвалов по маршрутам (экскаваторам и пунктам разгрузки) в соответствии с заданными критериями оптимизации, в частности, для поддержания определенного процентного содержания полезных компонентов при шихтовке, разработаны принципы работы модуля оптимизации горных работ в карьере.
Модуль «Оптимизация горных работ» предоставляет возможность использования большого количества критериев опти
mining-media.ru
Система диспетчеризации «КАРЬЕР»: от мониторинга большегрузных автосамосвалов к управлению горно-транспортным комплексом и оптимизации горных работ в карьере
Д.Я.Владимиров, А.Ф.Клебанов, «ВИСТ Групп»
А.И.Перепелицын, Федеральная служба по технологическому надзору
Эффективная работа современных горнодобывающих предприятий невозможна без развитого горно-транспортного комплекса (ГТК), включающего в свой состав большое количество машин и оборудования различного назначения (автосамосвалы, топливозаправщики, локомотивы и подвижной состав, экскаваторы, бульдозеры, грейдеры, буровые станки и другое вспомогательное оборудование). Поэтому на предприятиях значительное внимание уделяется увеличению производительности оборудования; организации планомерного его ремонта и обслуживания; обеспечению экономии всех видов материальных ресурсов, снижению расхода топлива, шин; оптимизации загрузки транспортных средств; стабилизации показателей качества руды, поступающей в переработку.
Решение этих задач и обеспечение эффективности эксплуатации ГТК в настоящее время невозможно без использования инженерными и управленческими службами горнодобывающих предприятий современных компьютерных технологий, методов автоматизированного управления технологическими процессами. АСУ ГТК, как часть автоматизированной системы горного предприятия, предназначена для управления выемочно-позрузочным, автомобильным и железнодорожным транспортом и буровыми станками; мониторинга основного и вспомогательного оборудования; управления и контроля объемов и качества руды, поступающей на переработку.
Реализация АСУ ГТК осуществляется, как правило, в три этапа:
1. Управление экскаваторно-автомобильным комплексом, состав которого определяют парк автосамосвалов и топливозаправщиков, а также парк экскаваторов.
2. Управление железнодорожным комплексом, состоящим из тепловозов, электровозов и вспомогательной железнодорожной техники.
3. Управление работой бурового и вспомогательного оборудования, включающего буровые станки, бульдозеры, тракторы и автогрейдеры.
На первом этапе система АСУ ГТК обеспечивает следующие основные функции:
– управление оборудованием в режиме реального времени и управление качеством руды при погрузке и ее разгрузке на складе;
– контроль движения руды, вскрыши и в целом горной массы, контроль соблюдения маршрутов движения, а также загрузки автосамосвалов;
– мониторинг работы двигателей и узлов автосамосвалов, эксплуатации шин, заправок и расхода топлива, времени технического обслуживания оборудования и т.д.
На втором этапе формирования АСУ ГТК добавляется возможность мониторинга местоположения железнодорожного транспорта, его погрузки и выгрузки, простоев и количества отгруженных думпкаров, а также контроля соблюдения скоростных режимов поездов, расхода топлива тепловозами, объемов и качества руды, подаваемой на дробильно-обогатительную фабрику, что позволяет оперативно получать цифровую транспортную модель карьера по участкам железнодорожных путей и итоговый график движения технологических поездов за смену).
На третьем этапе достигается возможность самонаведения буровых станков на проектную точку без предварительной маркшейдерской выноски, передачи координат пробуренных скважин в маркшейдерскую службу и бюро буро-взрывных работ для возможности своевременной корректировки проектов на бурение и взрыв, а также проводится мониторинг и контроль в реальном масштабе времени как параметров процесса бурения, так и технического состояния буровых станков.
Система диспетчеризации горно-транспортного оборудования «КАРЬЕР», разработанная российской компанией «ВИСТ Групп», внедряется на горных предприятиях России и СНГ с 1999 года. Изначально, на первых объектах внедрения (Полтавский ГОК, ЗАО «Черниговец») [1], система «КАРЬЕР» решала задачи мониторинга большегрузных автосамосвалов, т.е. слежения в режиме реального времени за состоянием самосвала (загрузкой, расходом топлива, скоростью, местоположением), учета этих параметров, а также простоев и нарушений технологических режимов эксплуатации автосамосвала. Эти работы проводились совместно с РУПП «Белорусский автомобильный завод». Дальнейшее развитие системы диспетчеризации «КАРЬЕР» направлено на создание на горном предприятии полнофункциональной системы управления горно-транспортным комплексом.
Модернизация системы идет по следующим направлениям:
– развитие бортового оборудования транспортно-погрузочного комплекса;
– развитие программного обеспечения диспетчерского центра;
– развитие средств организации передачи данных в диспетчерский центр.
Рассмотрим кратко основные результаты, достигнутые в этих направлениях.
Бортовое оборудование
Система контроля загрузки и топлива СКЗиТ [1, 2], устанавливаемая на автосамосвалы грузоподъемностью 55–220 т непосредственно на заводе «БЕЛАЗ», интегрируется с другими бортовыми электронными системами управления и контроля состояния автосамосвала. В первую очередь это относится к Системе управления тяговым электроприводом [2] (СУТЭП), а также к системам диагностики основных узлов и агрегатов самосвала (контроль работы дизеля, давления в шинах и др.) (рис. 1). Такая интеграция позволяет качественно усовершенствовать алгоритмы работы систем, по сравнению с их автономным функционированием. Например, для более точного управления работой тяговым электроприводом необходима информация о загрузке автосамосвала, уклоне дороги при его движении, которая передается от СКЗиТ непосредственно в СУТЭП. Передача данных осуществляется по CAN-интерфейсу, которым оснащены бортовые контроллеры СКЗ 02.01 и СУТЭП. Подход к интеграции СКЗиТ и других бортовых электронных комплексов c помощью CAN-интерфейса является общим для развития электронных систем автосамосвала БелАЗ. При этом предусмотренное программно-аппаратное расширение СКЗ 02.01 радионавигационным блоком с встроенным GPS приемником (платой РНБ) – системой, управляющей передачей данных по выделенному радиоканалу, – делает возможным передачу информации от датчиков СУТЭП и систем диагностики непосредственно в диспетчерский центр, сохранение этой информации на сервере системы «КАРЬЕР» и последующую организацию автоматизированного рабочего места механика автобазы (АРМ-М) (рис. 2). Работа автосамосвала БелАЗ-75131 с интегрированными системами СКЗиТ и СУТЭП и непрерывной передачей данных в диспетчерский центр была продемонстрирована в январе 2004 г. на совещании потребителей РУПП «Белорусский автомобильный завод».
Система диспетчеризации «КАРЬЕР» допускает работу с самосвалами других производителей, также оснащенных электронными системами контроля и диагностики. Так, в июле 2004 г. в состав диспетчерской системы на Полтавском ГОКе были включены автосамосвалы Komatsu HD-785 и HD-1200 (рис. 3). Бортовой контроллер PLC II, установленный на этих самосвалах, был соединен по RS-232 с СКЗ 02.01, оснащенным блоком РНБ. Дальнейшее согласование протоколов обмена данными между СКЗ 02.01 и PLC II сделало возможным передачу в диспетчерские центры рудоуправления и автобазы Полтавского ГОКа информации о загрузке, расходе топлива (самосвалы оснащались дополнительно датчиком уровня топлива в баке УТ-90), а также местоположении парка автосамосвалов Komatsu, аналогично информации, передаваемой от автосамосвалов БелАЗ.
До 2004 года система СКЗиТ, вследствие конструктивных особенностей автосамосвалов БелАЗ, могла быть установлена на самосвалах грузоподъемностью от 55 т и выше. Для определения степени загрузки самосвала в этой системе используется методика интегрированного вычисления веса груза по давлению в газомаслонаполненных амортизаторах подвески, измеренному высокоточными электронными датчиками давления (WIKA). При этом конструкция автосамосвалов БелАЗ грузоподъемностью 30–45 тонн, оснащенных шестью двухкамерными подвесками, не позволяла распространить на них указанную выше методику определения загрузки.
С целью преодоления этих ограничений в 2003–2004 гг. была разработана и опробована в заводских и натурных условиях система контроля загрузки, адаптированная для автосамосвалов БелАЗ грузоподъемностью 30 – 45 тонн и основанная на применении датчиков силы, монтируемых непосредственно на технологических «пальцах» подвески (рис. 4). Было установлено, что для определения загрузки с точностью до 1.5% достаточно получение информации от 4-х датчиков силы и показаний инклинометра (ИК-02) – датчика продольного крена, который также как и в случае определения загрузки для большегрузных автосамосвалов, вносит существенные коррективы в работу алгоритмов.
Направление развития бортового оборудования для реализации второго и третьего этапов создания АСУ ГТК (управление железнодорожным транспортом, буровым и вспомогательным оборудованием) определяется функциями, которые должна выполнять система на этих этапах. В большинстве случаев эти функции сводятся к мониторингу в режиме реального времени местоположения и состояния оборудования (информация о начале и завершении погрузки, выгрузки, движении, простоях и т.п.), соблюдения скоростных режимов, а также контролю за уровнем и расходом топлива. Эти задачи решаются установкой на транспортные средства СКЗ 02.01 с блоком РНБ и монтажом дополнительных датчиков состояния транспортных средств. Так, в проекте, реализуемом «ВИСТ Групп» в ЗАО «Черниговец», для определения расхода топлива на тепловозах устанавливаются как датчики уровня топлива поплавкового типа, аналогичные датчикам СКЗиТ автосамосвалов (УТ-90, УТ-60), так и расходомеры (СДМ). Для определения полезной работы транспортных средств (например, бульдозеров, грейдеров) может быть использована методика, основанная на определении комплексного показателя по датчикам позиционирования (GPS), датчику моточасов, расходомеру и датчику нагрузки на отвал, аналогичному описанному выше датчику силы, применяемому для определения загрузки малых БелАЗов. Следует отметить, что универсальность разработанного датчика силы (ДЗ-20) делает возможным его применение для определения загрузки практически любого грузоперевозящего транспортного средства. Например, в настоящее время рассматривается возможность применения этого датчика и других элементов системы «КАРЬЕР» для диспетчеризации и слежения за работой зарядных машин на базе КрАЗа и MAN, а также технологического транспорта ГМК «Норильский Никель».
Исключением от перечисленных выше «традиционных» задач мониторинга оборудования является задача самонаведения бурового станка на проектную точку скважины. Эта задача, также как и задача определения координат экскаватора с дециметровой точностью в плане и по высоте, может быть решена только при оснащении оборудования системами высокоточного позиционирования (СВП). Состав бортового оборудования, а также оборудования диспетчерского центра в этом случае существенно модифицируется. Вместо блока РНБ, обеспечивающего точность определения координат мобильного объекта порядка 3–5 метров в плане, необходимо использовать двухантенный GPS приемник и систему передачи данных RTK (рис. 5). Эволюцию развития системы диспетчеризации «КАРЬЕР» в связи с увеличением парка транспортных средств и требованиями к точности позиционирования экскаваторов и бурстанков иллюстрирует рис. 6., на котором схематично отражены этапы перехода системы от мониторинга большегрузных автосамосвалов к полному управлению горно-транспортным комплексом угольного разреза «Черниговский» в Кузбассе (отмеченные на рис. 6 системы видеонаблюдения и мониторинга технического состояния оборудования (МТСО), а также проблемы интеграции системы «КАРЬЕР» с АСУП «Галактика» и системой геологического моделирования и планирования горных работ выходят за рамки рассматриваемых в данной статье вопросов).
Программное обеспечение диспетчерского центра
Расширение функциональных возможностей программного обеспечения диспетчерского центра достигается за счет постоянного наращивания числа специализированных автоматизированных рабочих мест, которое происходит при расширении круга пользователей системы (функциональных служб горного предприятия) при переходе к полномасштабному управлению горно-транспортным комплексом. Так, если на первом этапе программное обеспечение диспетчерского центра включает в себя пять автоматизированных рабочих места пользователя, а именно: АРМ горного диспетчера, АРМ диспетчера автобазы, АРМ маркшейдера, АРМ системного администратора и АРМ технического директора, то к моменту завершения третьего этапа диспетчерский центр (понимаемый как распределенная информационная среда) может быть оснащен дополнительно АРМ начальника смены рудоуправления, АРМ производственного отдела рудоуправления, АРМ бюро буро-взрывных работ, АРМ начальника смены бурового участка, АРМ поездного диспетчера управления железнодорожным транспортом (рис. 7), АРМ службы ГСМ, АРМ инженера ТО, АРМ геологоразведочного отдела, АРМ производственного отдела разреза, АРМ директора по производству.
Вовлечение в систему управления горно-транспортного комплекса новых пользователей, охватывающих практически все организационно-технические службы комбината, невозможно без постоянного развития гибкости системы, повышения ее функциональности и удобства работы, что реализуется благодаря специальной многокомпонентной структуре программного обеспечения и применению новых технологий программирования. Программное обеспечение сервера приложений с помощью специально разработанной технологии UMP.NET обрабатывает входную информацию, как полученную от мобильных объектов, так и введенную пользователями, результаты этой обработки сохраняются в базе данных. При этом на сервере базы данных ORACLE хранится вся информация о работе оборудования, включая полную историю движения и показаний датчиков каждого мобильного объекта; данные о рейсах, в том числе расстояние транспортировки, массу и вид перевезенного груза; данные об остановках и нарушениях скоростного режима, итоговая информация по смене и суткам, и т. д. Программное обеспечение рабочих мест, построенное на базе нашего программного продукта XRTL Explorer, взаимодействует с базой данных через сервер приложений.
Таким образом, создание компонент UMP.NET и XRTL Explorer дает возможность пользователям по своему желанию самостоятельно разрабатывать и изменять функциональность системы диспетчеризации.
Управление горно-транспортным комплексом невозможно без развития методов автоматизированного диспетчерования оборудования и производственных процессов горного предприятия. В первую очередь это относится к оптимизации работы автомобильно-экскаваторным комплексом. С целью вычисления оптимального распределения автосамосвалов по маршрутам (экскаваторам и пунктам разгрузки) в соотве
mining-media.ru
Системы управления горнотранспортным комплексом – Союз горных инженеров. Информационный портал, посвященный добыче угля, руды и прочих полезных ископаемых.
На долю открытого способа разработки в мировой горной промышленности приходится почти 73% общих объемов от добычи полезных ископаемых. В России подобным методом добывается порядка 90% железных руд, свыше 70% руд цветных металлов, примерно 60% угля. По мере увеличения глубины карьеров доля финансовых затрат на все виды транспорта доходит приблизительно до 55–60% себестоимости в общей добычи полезного ископаемого. Поэтому вопросы развития и совершенствования транспорта в карьерах считаются одними из основных при открытых горных разработках. Какова в этом процессе роль информационных систем для горнотранспортного комплекса?
автор статьи: Саркис Папазян
Дальнейшее развитие открытого метода разработки будет сопровождаться увеличением глубины и сложностью транспортирования сырья и материалов. Определяющим при этом считается показатель глубины карьеров. Самый глубокий, например, среди угольных разрезов ― это Коркинский, чья проектная глубина составляет 630 м, достигнутая же ― свыше 450 м. Такие крупные угольные разрезы, как Кедровский и Междуреченский, или им. 50-летия Октября, уже достигли глубины 250 и более метров при проектной в 300-360 м.
Не будем вдаваться в анализ влияния различных факторов на показатели работ транспортного комплекса при росте глубины карьеров, приведем лишь ориентировочные цифры снижения производительности транспорта при понижении горных работ примерно на 100 м: для автосамосвалов подобное снижение составляет около 25-39%, для локомотивосоставов ― примерно 8,5-20%. Как же выходить из такого положения? Обратимся к опыту известных мировых компаний, работающих в сфере горнодобывающей промышленности.
Модели диспетчеризации для открытых работ
Одним из важнейших факторов повышения производительности работ, как показывает анализ стратегических мер, предпринятых в горнодобывающих отраслях развитых стран, стало совершенствование управления грузопотоками за счет внедрения в карьерах автоматизированных систем управления горнотранспортным комплексом (АСУ ГТК). Как показывает практика, наилучший результат в этой сфере достигается с использованием системы диспетчерского управления (диспетчеризации). Она основывается на технологии космической навигации ― это GPS, ― позволяющей с достаточно высокой точностью выявлять координаты движущихся транспортных средств с применением спутниковых радиосигналов, при помощи компьютерной обработки постоянно отображать положение различных машин, оптимизировать маршруты транспортных единиц.
Специалисты считают наиболее интересным в этой сфере инноваций опыт американских компаний. Можно выделить несколько наиболее значимых типов информационных систем для управления транспортным комплексом в карьерах из числа появившихся в последнее время.
Информационная система под названием «Dispatch», разработка известной компании Modular Mining Systems, была внедрена на карьере Tiron.
Она действует в реальном масштабе времени, считается динамической, имеет возможность непрерывно управлять транспортными единицами для выбора наиболее оптимального маршрута. Оптимизация различных маршрутов производится согласно выбранной установке путем использования методов линейного программирования. Такая система функционирует с помощью спутниковой навигации. Все данные отображаются на специальном дисплее в очень удобной графической форме.
За счет применения системы Dispatch производительность на погрузочно-транспортном комплексе увеличилась в среднем примерно на 11%. Система исключает неправильное назначение транспортных единиц за счет всестороннего контроля на дисплеях. В настоящее время разработками компании Modular Mining Systems уже воспользовались свыше ста карьеров.
Система автоматического управления для автосамосвалов (САУА), разработка компании Unit Rig Equipment.
Она имеет в своем комплекте дорожное оборудование, которое включает подземный кабель с глубиною заложения приблизительно 0,5 м и ряд блоков управления. По кабелю периодически подаются сигналы, что управляют скоростью, направлениями движения, разгрузкой машин и другими параметрами. Система определяет расстояние между автосамосвалами, местонахождение каждой машины отображается на главном диспетчерском табло.
Экономичность данной системы проверялась на меднорудном карьере в США, где работали десять экскаваторов и более 50 автосамосвалов. Время эффективной работы экскаваторов увеличилось на 7%, коэффициент использования автомашин вырос на 25%.
Информационная система на медно-рудном карьере вблизи г. Туссон.
Для фиксирования передвижения автосамосвалов используются контрольные точки, из которых вся информация поступает на диспетчерский пункт. Туда же со всех экскаваторов поступает информация о начале и об окончании погрузки. Маршрут следования машин передается водителю на специальное цифровое табло.
Специфика системы заключается в определении способов «оптимизации» линейного программирования: постановка задач изменяется в соответствии с климатическими условиями, календарным планом и числом задействованных мобильных средств. Практика свидетельствует, что при этом производительность транспортных единиц повышается в среднем на 20%.
Для отечественного карьерного транспорта
Как обстоят дела с внедрением информационных систем на российском карьерном транспорте? Отечественные системы диспетчеризации горнотранспортного комплекса (ГТК) предназначены тоже для автоматизированного управления грузопотоками на горных предприятиях. Их особенность же заключается в том, что они достаточно большое внимание уделяют вопросам экономии топлива.
Информационную систему «КАРЬЕР» разработали опытные специалисты компании «ВИСТ Групп». Она успешно внедрена и функционирует почти на 40 горнодобывающих предприятиях РФ, Казахстана, Монголии и др. стран. На данный момент систему диспетчеризации под названием «Карьер» выбрали крупные рудные и угледобывающие компании, которые входят в структуры холдингов Мечел, Северсталь, Эрдэнэт, Сибуглемет и др. Система может адаптироваться к условиям эксплуатации и требованиям заказчика, благодаря чему ее пользователь получает наиболее оптимальный для себя инструмент.
Окупаемость такой системы диспетчеризации достигается благодаря максимальной производительности использования транспорта в течение смены и оптимизации грузопотоков. Обратимся к примеру. Разрез «Черниговец» производственного объединения «Кемеровоуголь» является одним из самых крупных разрезов на севере Кузбасса. Компания в полном объеме внедрила систему диспетчеризации. К ней подключили автосамосвалы и экскаваторы, бульдозеры и иной технологический транспорт. Регулярная передача данных производится на базе радиомодемов УКВ-диапазона. В компании уже переходят к проекту по совершенствованию системы приема и отправки данных с применением стандарта с индексом WI-FI, в связи с чем во всей зоне проведения горных работ обеспечивается высокоскоростная передача данных. Новинка позволит передавать значительный объем различных диагностических данных, видео- и аудиоинформацию, подключать к системе диспетчеризации еще большее количество горнотранспортной техники. Ее использование совместно с действующими системами высокоточной спутниковой навигации ГЛОНАСС/GPS будет решать все необходимые задачи по корректировке грузопотоков.
Система диспетчеризации «КАРЬЕР» в данный момент используется и в СУЭК на разрезах Восточно-Бейский, Заречный, Тугнуйский и др. Например, Восточно-Бейский разрез в своей работе достаточно успешно использует особый модуль автоматической диспетчеризации системы «КАРЬЕР». Данный модуль по оптимизации позволяет автоматически отправлять автосамосвалы после каждой разгрузки к тому экскаватору, где его работа окажется максимально эффективной. Диспетчер подбирает в меню оптимальный вариант, и система начинает в автоматическом режиме распределять автосамосвалы в соответствии с заранее выбранными критериями работы.
Система диспетчеризации «Карьер» предназначается не только для проведения мониторинга, но и для оперативного управления и контроля горнотранспортного комплекса, всестороннего анализа производственных показателей и иных процессов по добыче полезных ископаемых в карьерах, ― говорит руководитель проекта «КАРЬЕР», компания «ВИСТ Групп», Д. В. Горевой. «Пользователям предлагается достаточно широкий набор функций, которые дают возможность решать самые актуальные для горного транспорта задачи. Информационные системы нашей компании позволяют повысить производительность работ на карьерном транспорте примерно на 15-20% и вести безопасную добычу и транспортировку различных полезных ископаемых в тяжелых и труднодоступных по климатическим условиям регионах Сибири и Крайнего Севера».
Одна из принципиально новых функций, выполняемых отечественными системами диспетчеризации, ― это анализ и контроль полного цикла по движению топлива ― от приема до расхода. Пример для иллюстрации этого положения возьмем из опыта организации работ в подразделениях золотодобывающей компании «Полюс». С целью реализации контроля ГСМ одна из известных в мире компаний по разработке информационных моделей Wenco интегрировала в свои системы, внедренные на Олимпиадинском ГОКе, весьма высокоточные топливные датчики от компании Omnicomm. После этого на ГОКе возросла не только эффективность использования автотранспорта и качество управления транспортными потоками, но и снизился расход топлива, например самосвалами, примерно на 10%.
Системы контроля и анализа расхода топлива были установлены более чем на ста единицах основного горного транспорта, среди которых карьерные автосамосвалы Caterpillar 777D и Caterpillar 777F, Komatsu HD785-5 и БелАЗ-7540-А, различные модели грузовиков КАМАЗ…
Очень важным результатом такого анализа данных стало определение действительного расхода топлива по всем типам машин. Выяснилось, что каждая единица транспорта одного и того же типа расходует различное количество горючего. Такие факты объясняются разным состоянием двигателей и топливной системы, разным сроком эксплуатации машин и даже спецификой условий работы и стилем управления водителя. Полученные информационной системой данные дали возможность скорректировать нормативы по расходу горючего и достигнуть существенной экономии по данной статье.
Кроме статистики по заправкам и сливам ГСМ система предоставляет общие данные по пробегу автотранспорта, расходу горючего на один моточас, времени работы и простоя. Такого рода данные позволяют выявлять оптимальные режимы для загрузки техники, пресекать разного характера простои, мотивировать персонал предприятия в соответствии с объемами действительно выполненной работы. Бесспорно, АСУ ГТК ― достаточно эффективная технология для повышения рентабельности горнодобывающего предприятия.
Ориентиры на будущее
В последнее время на российском рынке появилось немало компаний, в том числе и сибирских, которые стали разрабатывать различного типа информационные системы для горнотранспортного комплекса. Так, текущим летом НПП «Томская электронная компания» представила в своей экспозиции на XXI Международной специализированной выставке технологий по горным разработкам под названием «Уголь России и Майнинг» новые средства по бортовому оснащению локомотива при использовании этой машины в карьерах в составе автоматизированной системы по диспетчеризации и учета производства.
В базовый набор оснащения локомотивов марок ТЭМ -2М, ТГМ-4, ОПЭ-1АМ, НП-1 и др. входит серийно изготовляемая на предприятии продукция:
• бортовой навигационный контроллер, который осуществляет сбор, обработку и передачу всей технологической информации в базу данных;
• блок ввода и вывода, предназначенный для первичного сбора и преобразования сигналов;
• антенный блок для приема и передачи информации;
• карточка машиниста для чтения и записи различной технологической информации;
• комплект монтажных принадлежностей.
Дополнительно в набор бортового оснащения локомотива могут входить КИП и других производителей, что рекомендованы и адаптированы НПП «ТЭК» для использования в АСУ ГТК. Данная информационная система может заинтересовать потенциальных покупателей и тем, что состав оборудования и устройств системы определяется и потом согласуется с заказчиком еще на этапе проектирования.
***
Подводя итог разговору, можно смело сказать, что в текущее время работу современного горнодобывающего предприятия сложно даже представить без применения информационных систем на производстве. Многие процессы по добыче и перевозке полезных ископаемых с помощью, например, диспетчеризации уже автоматизированы, значительная часть ключевых управленческих решений принимается именно на основе информации из такой системы. Цель установок АСУ ГТК ― это оптимальное управление грузопотоками, полный учет и контроль работы горнотранспортного комплекса, мониторинг эксплуатационных режимов машин и в конечном счете ― снижение производственных издержек и повышение всего объема добычи полезного ископаемого.
Кроме того, хочется отметить еще и то, что развитие информационных систем в настоящий момент продвигается в сторону их роботизации по управлению процессами перевозок на открытых горных работах. Такие проекты и разработки уже получили поддержку от Фонда «Сколково», ведущих горнодобывающих предприятий и Ростехнадзора. Таким образом, сегодня есть все основания считать, что дальнейшее развитие АСУ ГТК позволит добывающим предприятиям значительно увеличить экономическую эффективность работ, в том числе и на горнотранспортном комплексе.
Спецвыпуск журнала «Промышленные страницы Сибири» «Добывающая промышленность»
Информация взята с сайта: http://www.epps.ru/journal
2643* Новости рассылаются в виде подборок каждую неделю
www.mining-portal.ru
Автоматизированные системы управления горно-транспортным оборудованием
Особенности и перспективы применения на предприятиях ОАО «Сибирская угольная энергетическая компания» (СУЭК)
К.Н. Трубецкой, академик РАН
В.В. Рашевский, к.э.н., Генеральный директор ОАО «СУЭК» Д.Я. Владимиров, Генеральный директор ООО «ВИСТ Групп»
А.Ф. Клебанов, к.т.н., директор по горным технологиям ООО «ВИСТ Групп»
ОАО «Сибирская угольная энергетическая компания» (СУЭК) – крупнейшее в России угольное объединение и единственная отечественная компания, входящая в десятку лидеров мирового угольного рынка по объемам добычи угля. Компания обеспечивает около 30% поставок энергетического угля на внутреннем рынке и примерно 20% российского угольного экспорта. Филиалы и дочерние предприятия СУЭК расположены в Красноярском, Приморском и Хабаровском краях, Иркутской, Читинской и Кемеровской областях, в Бурятии и Хакасии. Более половины предприятий компании добывают уголь открытым способом. При этом на долю открытого способа приходится примерно 60% добычи. Такой удельный вес открытого способа добычи угля будет сохраняться и в будущем. Между тем с увеличением глубины угольных разрезов и усложнением горно-геологических условий добычи затраты на эксплуатацию карьерного транспорта могут превышать 50% от себестоимости добычи. Поэтому повышение эффективности карьерного автотранспорта имеет существенное значение для компании.
В 2006 году специалисты компании провели анализ эффективности использования карьерных автосамосвалов, работающих на предприятиях СУЭК. Оценивались различные показатели работы этой техники и в результате был выявлен ряд проблемных моментов. Оказалось, что на различных предприятиях расход топлива по одним и тем же моделям самосвалов может различаться на 70% при сопоставимых горно-геологических условиях. Также было установлено, что грузоподъемность самосвалов по породе на некоторых предприятиях используется только на две трети, причем самой распространенной проблемой является невозможность оценки недогруза или перегруза. И в целом исследование показало, что коэффициент использования карьерных самосвалов в среднем по компании составляет всего 50%.
Таким образом, проведенный анализ показал, что основными проблемами использования самосвалов в компании является «нецелевое» использование топлива (расходы компании на приобретение дизельного топлива составляют около 40% от всех затрат на материально-технические ресурсы), низкий коэффициент использования грузоподъемности, простои техники. Отсутствие весового контроля непосредственно при погрузке и средств оперативной оценки скорости самосвала, состояния автодороги ведет к преждевременному износу узлов и агрегатов карьерных самосвалов.
Совокупность перечисленных факторов, значительно снижающих эффективность использования дорогостоящей карьерной техники, убедительно доказывает необходимость скорейшего внедрения на предприятиях компании автоматизированной системы оперативного контроля и управления горно-транспортным оборудованием.
Компания СУЭК провела конкурс среди компаний-разработчиков специализированных информационных систем диспетчерского управления для горных предприятий. В конкурсе приняли участие как зарубежные производители -Modular Mining Systems (США) и Wenco International Mining System (Канада), так и отечественные – ЗАО «Союзтехноком» и ООО «ВИСТ Групп». Удовлетворяющей всем предъявляемым критериям (а их было 19) была признана система управления горно-транспортными комплексами «КАРЬЕР» (разработчик – ООО «ВИСТ Групп»).
Областью применения системы «КАРЬЕР» является диспетчеризация горно-транспортного оборудования: автосамосвалов, экскаваторов, бульдозеров, топливозаправщиков и другой техники, занятой на выемочно-погрузочных работах и в процессах транспортирования горной массы.
Целью внедрения Системы является повышение производительности горно-транспортного комплекса за счет оперативного контроля и оптимизации производственных процессов. Система оперативного диспетчерского управления горно-транспортным оборудованием «КАРЬЕР» внедряется в первую очередь в Иркутском филиале СУЭК на одном из крупнейших разрезов компании -«Тугнуйском» и в Кемеровской области на разрезе «Заречный».
На Тугнуйском разрезе бортовое оборудование установлено на автосамосвалы БелАЗ грузоподъемностью от 30 до 130 т (30 автосамосвалов), топливозаправщики МАЗ и КамАЗ, экскаваторы ЭКГ и ЭШ, бульдозеры, вспомогательный технологический автотранспорт (техпомощь, тягач, поливочная и др.), буровые станки.
Программно-аппаратный комплекс системы «КАРЬЕР» состоит из бортового оборудования, устанавливаемого на мобильных объектах, и диспетчерского центра, включающего радиооборудование, серверы и программное обеспечение. Данные телеметрии с мобильных объектов (информация о загрузке, уровне топлива, координатах, скорости и т.д.) поступают в диспетчерский центр для обработки и хранения. Из диспетчерского центра на мобильные объекты передаются текстовые сообщения от диспетчера, которые появляются на индикаторной панели в кабине водителя. Структурная схема Системы представлена на рис. 1.
Функциональность программного обеспечения системы «КАРЬЕР» включает набор базовых и вспомогательных модулей, состав которых определяется конкретными задачами предприятия.
На Тугнуйском разрезе установлены базовый функциональный модуль, модуль контроля работы бульдозера, модуль контроля работы топливозаправщика, модуль технической готовности самосвалов, модуль аналитики, модуль учета работы шин, модуль учета наработки основных агрегатов самосвалов, модуль автоматической диспетчеризации.
Таким образом, пользователи Системы получают в свое распоряжение набор средств управления работой горнотранспортного комплекса, которые предназначены для повышения производительности комплекса и обеспечения плановых качественных характеристик добычи: механизм всплывающих сообщений о нарушениях работы, механизм контроля плановой и фактической производительности (рис. 2), механизм графического представления графика движения самосвалов, картографическое представление информации (рис. 3).
Существенно повышает эффективность работы Системы использование модуля оптимизации движения самосвалов, который может применяться как для первоначального распределения машин в начале смены, так и для автоматического их перераспределения в течение смены в зависимости от текущей ситуации в карьере. Модуль выполняет новый расчет оптимального маршрута движения самосвала каждый раз при наступлении ключевого события (например, разгрузка самосвала), используя ряд критериев. Выбор критериев зависит от задач, которые стоят перед предприятием. Так, например, в качестве возможных критериев могут быть выбраны достижение максимальной производительности, поддержание заданного качества угля на пункте разгрузки и т.д.
Система позволяет также осуществлять удаленную диагностику основных узлов и агрегатов автосамосвалов, экскаваторов и других мобильных объектов, например диагностику двигателя автосамосвала, контроль давления в шинах, контроль состояния электрооборудования экскаватора, управление тяговым электроприводом и др.
Рабочие места (РМ) пользователей могут произвольно формироваться администратором Системы. На Тугнуйском разрезе планируется выделение РМ автодиспетчера (выдача наряда на смену для самосвалов, управление в течение смены, учет работы автотранспорта), РМ горного диспетчера (контроль работы экскаваторов), РМ оператора по выпуску водителей на линию, РМ оператора по учету ГСМ, РМ механика автобазы и др.
Система предоставляет руководству и техническим службам разрезов большие возможности по анализу данных о работе оборудования в карьере. Важной особенностью Системы является ее открытость для модификации имеющихся экранных форм и отчетов и создания новых. Для хранения данных используется база данных Oracle.
Систему планируется внедрить в эксплуатацию за 9 месяцев. Экономический эффект будет получен за счет сокращения затрат на приобретение нового и замену старого оборудования, уменьшения эксплуатационных годовых расходов и получения дополнительной прибыли от увеличения объема добычи. Расчетный срок окупаемости Системы составляет 11 месяцев с момента запуска Системы.
В рамках внедрения системы управления горно-транспортным комплексом «КАРЬЕР» на разрезе «Заречный» оборудованы более 20 самосвалов БелАЗ грузоподъемностью 45 и 55 т, бульдозеры, экскаваторы ЭКГ и ЭШ. Структура Системы и набор функциональных модулей для решения задач управления аналогичны описанным выше для Тугнуй-ского разреза.
В 2008 г. систему «КАРЬЕР» предполагается внедрить на всех угольных разрезах компании.
Естественным образом возникает вопрос об интеграции системы «КАРЬЕР» с уже функционирующими в компании информационными системами. На рис. 4 представлен один из возможных вариантов построения интегрированной системы компании на базе информационных систем различного уровня (включая и систему «КАРЬЕР»).
Представленная схема предполагает построение интегрированной системы на базе разнородных подсистем или модулей, осуществляющих тем не менее взаимосвязанную обработку информации. Системы должны условно (не обязательно территориально) состоять из двух уровней: уровня сбора информации и уровня контроля и анализа информации. При этом подсистемы или отдельные модули системы должны отвечать согласованным требованиям по интеграции в единую систему.
Уровень сбора информации представлен различными системами и модулями, относящимися к уровню MES (АСУП), к которым относятся такие системы, как система автоматизированного управления «КАРЬЕР», системы учета качества и количества угля на угольных складах разрезов и шахт, а также угля, поступающего на обогатительную фабрику, выходящего с фабрики в вагоны или на склад, отгружаемого потребителю, находящегося на пути к потребителю. Каждая из внедряемых систем должна предоставлять Web-сервисы с доступом к базам данных.
На уровне контроля и анализа информации в каждом филиале устанавливается сервер, на котором реализуется хранилище данных. Для каждого филиала разрабатывается структура данных на сервере и регламент сбора информации. Для визуализации данных, сохраненных на сервере, используется как готовое программное обеспечение (ПО для анализа данных Business Objects, Cognas и т.п.), так и специально разработанное (может основываться на решениях SAP: SAP BI/BW и SAP xMII).
Система анализа работы предприятий и филиалов, построенная на базе SAP BI/BW, позволяет получать различные отчеты по работе предприятий, филиалов и холдинга в целом. Применение данной системы позволяет проводить интеллектуальный анализ данных, контролировать ключевые показатели эффективности (KPI) и т.д.
Использование системы оперативного контроля показателей производственного процесса (на базе SAP xMII) позволяет осуществлять интеграцию различных систем MES-уровня, оперативное отображение производственных показателей, а также оперативный контроль предприятий со стороны холдинга.
Кроме того, средствами SAP ERP могут быть реализованы такие функции, как, например, контроль производственных и экономических показателей работы, планирование поставок угля, учет готовой продукции на всех этапах перемещения от склада до покупателя и др.
Таким образом, внедрение автоматизированной системы управления горно-транспортными комплексами «КАРЬЕР» на разрезах ОАО «СУЭК» и последующая ее интеграция с другими функционирующими на предприятии информационными системами с целью создания единой информационной системы позволят существенно повысить эффективность управления производством на предприятиях Компании.
Журнал “Горная Промышленность” №6 2007, стр.12
mining-media.ru
Cистемы дробления и транспортировки горных пород в карьерах
Phil Morriss, вице-президент горно-технической службы компании Sandvik Mining and Construction (SMC)
Andrew Hustrulid, специалист по конвейерным системам компании SMC
Андрей Макеев, менеджер по системам транспортировки сыпучих материалов компании SMC
Специалистами компании Sandvik подготовлена серия публикаций, в которых раскрываются возможности компании по техническому и экономическому обоснованию применения систем циклично-поточной технологии (ЦПТ), а также представляется оборудование, спроектированное и изготовленное компанией для этих систем.
Как известно, системы ЦПТ требуют достаточно больших капитальных вложений, поэтому на этапе проектирования особенно важно дать правильную экономико-технологическую оценку всего проекта в целом с учетом себестоимости товарной продукции и срока окупаемости инвестируемых средств. В настоящее время компания не только в состоянии разработать, произвести и ввести в эксплуатацию все необходимое оборудования для систем ЦПТ, но также помочь в оценке возможностей и рентабельности применения этой системы в конкретных горно-технологических условиях, в том числе при реконструкции горного предприятия.
В настоящей статье рассматриваются факторы, которые необходимо учитывать при начальной стадии оценки целесообразности применения систем ЦПТ в условиях конкретного месторождения.
Факторы, определяющие применение ЦПТ
Срок отработки карьера
По исследованиям специалистов компании Sandvik, нормативно ожидаемый срок службы системы ЦПТ составляет 150 тыс. час. или 20 лет, хотя в некоторых конкретных условиях затраты могут окупиться раньше. Во избежание убытков, при использовании оборудования системы ЦПТ проектный срок службы карьера должен составлять не менее 10 лет.
Схема разработки карьера, производительность оборудования и объёмы горной массы, транспортируемой системой ЦПТ
Необходим четкий погодовой план горных работ с положением выработок на определенных этапах развития карьера.
На основе календарного плана разработки месторождения определяются не только годовые объемы разрабатываемых и транспортируемых горных пород, но и места размещения элементов системы ЦПТ на каждом этапе развития карьера, а также схема и график их переноса в новое положение. При этом устанавливается, в какой мере перемещение в новое положение элементов системы ЦПТ повлияет на протяженность горных выработок и фронта работ и, прежде всего, на дальность транспортирования горной массы из забоев до дробильного пункта автосамосвалами по внутрикарьерным дорогам. И, например, необходимо определить, смогут ли экскаваторные забои обеспечить необходимые объемы горной массы для дробления и загрузки конвейерных линий при изменении, после переноса дробилки, дальности транспортирования и неизменном количестве автосамосвалов, обслуживающих забои?
По данным компании Sandvik, наилучшие технико-экономические показатели работы системы ЦПТ достигаются при транспортировании не менее 80–90% горной массы карьера.
Эта доля может упасть ниже 50% в сложных горно-геологических условиях месторождения. Понятно: чем большая доля горной массы перерабатывается системой ЦПТ, тем быстрее возвращаются вложенные в нее инвестиции. Когда имеют место большие первоначальные капитальные затраты и малые объемы горной массы, перерабатываемой системой ЦПТ, возникают затруднения с возвратом инвестиций (в связи с ростом срока окупаемости капиталовложений).
Передвижная дробильная станция (вскрышные породы)
производительностью 5500 т/час (Таиланд)
Производительность системы ЦПТ
На этой стадии проектирования необходимо очень тщательно рассчитать производительность всей цепочки оборудования: экскаватора в забое; автотранспорта от забоя до бункера дробильного узла; перегрузочного устройства, откуда горная масса поступает в полувагоны или на конвейерный транспорт, ведущий к отвалообразователю.
Очень важно, чтобы производительность дробилок была кратна планируемой производительности забойного экскаватора. Например, если в забоях работают экскаваторы с производительностью около 4000 т/ч, то дробилка производительностью 10000 т/ч – явно не подходит. Также важно, чтобы была соблюдена пропорция между средней производительностью за короткий и длительный периоды. При этом необходимо выдержать условие: производительность дробилки не должна превышать долговременную среднюю производительность карьера.
Соотношение цен на энергоносители и стоимость рабочей силы
При выборе технологии разработки месторождения и типа механизации рабочих процессов в карьере необходимо провести анализ чувствительности технико-экономических показателей всего проекта к изменению стоимости дизельного топлива, электроэнергии, рабочей силы и учетной банковской ставки, в конечном итоге влияющих на рентабельность системы ЦПТ. Очевидно, что повышение стоимости дизельного топлива и рабочей силы только повышает сравнительную выгодность системы ЦПТ, в то время как повышение стоимости электроэнергии и учетной банковской ставки оказывает противоположное влияние.
В соответствии с динамикой изменения мировых цен на нефть и нефтепродукты наиболее крутой наклон имеет кривая стоимости дизельного топлива. Это означает, что окупаемость средств, инвестированных в технологию разработки месторождения с использованием только автотранспорта – менее прогнозируема, чем при использовании системы ЦПТ, работающей на электроприводах.
Количество литотипов транспортируемой горной массы Наибольшая эффективность использования системы ЦПТ достигается при транспортировании только одного типа горной массы: скальной или мягкой вскрыши, углей и рудной массы без различия по сорту и качеству.
В карьерах, где необходимо обеспечивать селективные грузопотоки (три и более вида пород и полезных ископаемых), эффективность применения ЦПТ резко снижается.
Конечно, применение современных компьютерных технологий может оптимизировать режим селективной подачи горной массы на конвейеры. Но необходимо учитывать, что раздельная подача двух типов вскрышных пород или полезного ископаемого в дробильную установку не фиксируется компьютерами. Хотя, в настоящее время, с помощью системы диспетчеризации горно-транспортного комплекса возможно решение даже и такой задачи. Но все это повлечет за собой увеличение капитальных вложений в систему ЦПТ и более четких расчетов по организации работы всей системы транспортирования горной массы.
Установка конвейеров в стационарное положение Однозначно можно утверждать, что установка в стационарное положение максимального количества конвейеров с самого начала разработки месторождения значительно увеличивает эффективность применения ЦПТ.
Влияние крепости пород на производительность и стоимость системы
Принципиально важное значение для эффективности функционирования всей системы ЦПТ имеет правильность выбора типа дробилок, соответствующих прочности разрабатываемых горных пород. При переработке мягких и легкодробимых горных пород гораздо легче достичь номинальной производительности системы ЦПТ.
Для таких видов горных пород больше всего подходят валковые дробилки, применение которых снизит как капитальные, так и эксплуатационные расходы. Компания Sandvik располагает широкой линейкой моделей дробильного оборудования для решения всевозможных задач по оптимизации процесса дробления как мягких, так и твердых пород c крупностью исходного куска до 1200 мм.
Периодичность переноса дробильных установок
Расчеты и опыт Sandvik показывают: чтобы достичь приемлемой эксплуатационной готовности системы ЦПТ дробильные установки следует переносить в новое положение не чаще, чем один-два раза в год. Хотя, чем чаще перенос, тем меньше шаг переноса по вертикали (по высоте рабочей зоны карьера) дробильной установки. Соответственно, тем меньше расстояние транспортирования автосамосвалами из забоев до бункера дробилки, тем меньше высота подъема груженого самосвала. Все это приводит к повышению производительности автосамосвалов и сокращению их рабочего парка.
Для ускорения передвижения дробильных и транспортных элементов ЦПТ и сокращения общих простоев оборудования системы, компания Sandvik предлагает модельный ряд специальных гусеничных транспортеров и перегрузочных модулей. Применение этих типов оборудования позволит существенно повысить эффективность применения системы ЦПТ в целом.
Возможность нисходящей транспортировки горной массы Общеизвестно, что нисходящее перемещение любых грузов средствами транспорта всегда менее энергоёмко и дешевле, чем по горизонтальной поверхности и, тем более, вверх на подъем. Кроме того, нисходящие конвейеры во время работы способны генерировать электроэнергию, рекуперируя ее в энергосети, что в конечном итоге приводит к значительному снижению общих эксплуатационных затрат на транспортирование горной массы.
Организация отвалообразования в системе ЦПТ
При конвейерном транспорте горных пород их складирование в отвалах (или в складах некондиционных полезных ископаемых) осуществляется с помощью отвалообразователей различного типа. В целях снижения общих расходов на раздельное, по литотипам, складирование вскрышных пород в отвалах и некондиционных полезных ископаемых в спецотвалах (техногенных месторождениях) необходимо предусмотреть такие схемы их развития, при которых объемы работ по перемещению отвальных конвейеров были бы сведены до минимума, при соответствующем уменьшении расходов на их обустройство и обслуживание после переноса.
Отвалообразователь PA100-1600/25+35 (Индия)
Надо помнить, что раздельная укладка различных типов горных пород в отвалы приводит к усложнению их конфигурации и схемы размещения конвейерных лент, что в конечном итоге может свести до недопустимого минимума эффективность применения ЦПТ.
В настоящее время Sandvik может предложить различные типы и способы складирования при отвалообразовании, начиная от простого снятия грунта с отвального конвейера с помощью разгрузочной тележки и передачей его на приемную консоль ленточного отвалообразователя, и заканчивая применением роторных экскаваторов на приеме мягких пород с перегрузкой их в отвал или на конвейер отвалообразователя, с полным моделированием процесса и расчетом всех необходимых рабочих параметров оборудования.
Практические проблемы планирования горных работ
Проектирование системы ЦПТ
На большинстве горных предприятий оперативное планирование горных работ осуществляется с использованием программного обеспечения Whittle™, позволяющего оптимизировать конфигурацию и положение уступов и бортов карьера. Для угольных карьеров – наиболее типична линейная конфигурация уступов и бортов, поэтому они больше всего подходят для применения систем ЦПТ.
Система ЦПТ и конфигурация, составленная с помощью
программного обеспечения Whittle™
Проблемы, возникающие при работе с программным обеспечением Whittle™, оперирующим единичным выемочным (добычным) блоком, на основе к
mining-media.ru
Системы автоматизации и диспетчеризации для горных предприятий и карьеров
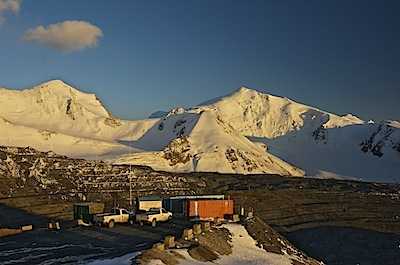
В 2004 году мы одними из первых в стране начали заниматься внедрением и обслуживанием автоматизированных систем управления на открытых горных карьерах.
Среди наших клиентов крупнейшие предприятия в горной отрасли России и СНГ – АК «АЛРОСА», ЗАО «Полюс», Ferrexpo, Altyntau.
Наша работа заключается в том, чтобы найти наиболее эффективное и наименее затратное решение по автоматизации горного производства, чтобы, затратив минимум средств, можно было получить полное оперативное управление производством и максимальное снижение непроизводительных издержек с дальнейшим повышением производительности.
В решениях мы используем передовые, не имеющие аналогов в мире, проверенные технологии:
- Система связи Motorola MESH – мы раньше всех в СНГ начали эксплуатировать эти сети и наработали огромный опыт
- Система управления горно-транспортным комплексом (АСУ ГТК) Wenco – это полнофункциональный горно-транспортный комплекс, разработанный в Канаде, по совершенству программного обеспечения, удобству использования являющийся мировым лидером. Для российских предприятий по нашей инициативе специально был добавлен новый функционал, чтобы учесть специфику российских горных работ
- Система высокоточного позиционирования экскаваторной выемки Wenco – комплекс высокоточного позиционирования для экскаваторов и погрузчиков с прямой и обратной лопатой является наиболее точным продуктом среди подобных на рынке. Предоставляет операторам визуальное подтверждение о типо-сорте и качестве руды, позволяет проводить контроль качества в процессе выемки и погрузки.
- Управление буровзрывным комлексом – система высокоточной навигации на скважины с последующей фиксацией координат и глубины, мониторинг параметров бурения для определения твердости пород и последующего вывода рекомендации по заряду блока.
- Оборудование высокоточной навигации канадской компании Novatel – в наших решениях мы применяем высококачественные навигационные платы Novatel, позволяющие определять координаты в условиях карьера с сантиметровой точностью
Мы ответственно подходим к нашей работе и доводим каждое внедрение до конца до получения максимального эффекта.
На российских предприятиях можно отметить следующие положительные эффекты от внедрения систем АСУ ГТК:
- Увеличение добычи
- Повышение эффективности использования оборудования
- Повышение качества технического обслуживания техники
- Достижение выбранных задач
- Гибкое управление производством
- Увеличение срока эксплуатации шин
- Уменьшение разубоживания
- Улучшение точности исполнения планов обуривания Подробнее…
wenco.ru
С места в «карьер». Компания «ВИСТ Групп» провела первую конференцию пользователей системы диспетчеризации «КАРЬЕР»
12-15 сентября 2005 г. в подмосковном пансионате «Голицыно» прошла «Первая конференция пользователей системы диспетчеризации «КАРЬЕР», организованная компанией «ВИСТ Групп».
В конференции приняли участие более 20 компаний из России и стран СНГ, среди которых были как пользователи Системы, так и компании, пока только рассматривающие возможность оборудования системой автоматизации своих добывающих предприятий: АК «АЛРОСА», ОАО «Полтавский ГОК» (Украина), ОАО «Ингулецкий ГОК» (Украина), ОАО «Разрез «Киселевский», ОАО «Угольная компания «Южный Кузбасс», ОАО «Томусинская автобаза», ОАО «Высочайший», СП «ЭРДЭНЭТ» (Монголия), ОАО «Ураласбест», ЗАО «Черниговец» и др. Средства массовой информации были представлены журналом «Горная промышленность», любезно приглашенным руководством ООО «ВИСТ Групп».
Открывая конференцию, Генеральный директор ООО «ВИСТ Групп» Д.Я.Владимиров отметил, что компания работает на рынке информационных услуг более 15 лет и на сегодняшний день обладает богатым опытом разработки информационных систем и реализации сложных комплексных решений для различных задач целого ряда отраслей промышленности, в т.ч. горнодобывающей. ООО «ВИСТ Групп» осуществляет разработку и внедрение для конкретных условий предприятий систем диспетчиризации транспортных средств, систем геологического моделирования, проектирования, планирования и оптимизации горных работ, проводит горно-геологический консалтинг, поставляет компьютерное и периферийное оборудование, сетевое оборудование.
Участниками конференции были заслушаны доклады и выступления специалистов, имеющих самое непосредственное отношение к внедрению системы диспетчеризации «КАРЬЕР» на предприятиях горнодобывающей отрасли – разработчиков Системы и ее компонентов и непосредственно пользователей Системы, чей опыт ее эксплуатации вызвал не меньший интерес у аудитории, чем информация о новых разработках.
Заместитель генерального директора ООО «ВИСТ Групп» А.Ф.Клебанов в своем докладе остановился на истории создания и перспективах развития системы диспетчеризации
горно-транспортного оборудования «КАРЬЕР», а руководитель отдела внедрения ООО «ВИСТ Групп» Н. Одинцев рассказал о новых функциональных возможностях Системы. Он отметил, что на сегодняшний день функциональность системы диспетчеризации «КАРЬЕР» значительно расширена новыми модулями (модуль оптимизации, модуль геологии, модуль управления ж.-д. транспортом, модуль управления заправками и др.), позволяющими оптимизировать работу всего горно-транспортного комплекса предприятия.
«…Внедряя автоматизированную систему диспетчеризации мы ожидаем повышение производительности парка горных машин, снижение потребления дизельного топлива, а, главное, повышение ответственности персонала и общей культуры производства…»
С.Е. Малышев, Заместитель генерального директора по экономике и финансам ОАО «Угольная компания «Южный Кузбасс»
Не менее значимыми для пользователей, присутствующих на Конференции были и доклады, посвященные вопросам организации технической поддержки Системы и отдельных ее компонентов (СУТЭП и СКЗиТ). В рамках конференции были широко освещены вопросы качества дороги диагностики состояния подвески транспортных средств разработки– бортового оборудования для экскаваторов и бульдозеров, организационно-технические аспекты внедрения Системы на предприятиях, достижения и направления развития систем диспетчеризации на предприятиях Кемеровской области, сертификации, стандартизации и лицензирования Системы.
«…Использование системы позволило увеличить загрузку каждого автосамосвала и снизить расход дизельного топлива.»
А.И. Логачев, Директор по транспорту ОАО «Ингулецкии ГОК»
Отдельно на конференции была представлена цифровая геологическая модель месторождения, использование которой значительно повышает эффективность эксплуатации системы «КАРЬЕР». Такая модель может быть построена с помощью горно-геологической системы GEMS, о принципах функционирования которой в своем докладе рассказала руководитель горно-геологической группы ООО «ВИСТ Групп» Ольга Стагурова. В своем докладе она отметила, что в системе диспетчеризации «КАРЬЕР» используется блочная модель содержания полезного компонента, которая особенно актуальна для предприятий, перед которыми остро стоит проблема контроля качества руды. От стратегического ежегодного/ежеквартального/ежемесячного планирования горных работ, которое осуществляется в системе
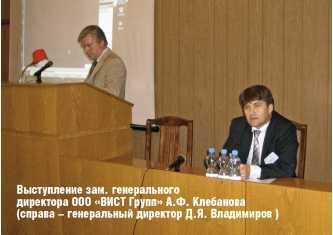
GEMS, система диспетчеризации «КАРЬЕР» позволяет перейти к планированию показателей добычи на уровне «сутки/смена» и произвести оптимизацию работы горно-транспортного оборудования.
С докладами выступили не только специалисты ООО «ВИСТ Групп», отвечающие за внедрение Системы на предприятиях, но и представители компаний, являющихся партнерами ООО «ВИСТ Групп» в области разработки и внедрения системы диспетчеризации «КАРЬЕР»: РУПП «Белорусский автомобильный завод» (БЕЛАЗ), ГУП «Холтрон», ЗАО «САГА Инк.», Motorola, Oracle.
Продемонстрированный на конференции фильм о внедрении системы диспетчеризации на Ингулецком ГОКе позволил участникам мероприятия увидеть Систему в работе.
Важной составляющей конференции стали выступления пользователей Системы, которые вызвали большой интерес
у представителей тех предприятий, где система автоматизации горно-транспортного комплекса еще не применялась. Участники конференции получили уникальную возможность побеседовать с разработчиками Системы и ее компо нентов без посредников. В рамках круглого стола было поднято много вопросов, актуальных как для предприятий, уже использующих систему диспетчеризации «КАРЬЕР», так и для тех, кто еще только принимает решение о необходимости внедрения системы автоматизации горных работ.
Конференция прошла в теплой дружеской атмосфере. Участники отметили высокий уровень организации мероприятия и информативность представленных докладов. Интерес, проявленный к конференции и к системе диспетчеризации «КАРЬЕР», лишний раз доказывает актуальность и востребованность данного продукта на рынке России и стран СНГ, поэтому ООО «ВИСТ Групп» планирует сделать данное мероприятие ежегодным.
Материалы подготовили: В.А. Галкин, А.И. Макеева
Журнал “Горная Промышленность” №5 2005
mining-media.ru
Добавить комментарий