Синтез газ получение – “СИНТЕЗ-ГАЗ 2 Синтез-газ – смесь оксида углерода с водородом в различных соотношениях ОБЩИЕ СВЕДЕНИЯ Синтез-газ является одним из главных источников сырья.”. Скачать бесплатно и без регистрации.
Способ получения синтез-газа
Изобретение относится к области неорганической химии и может быть использовано для получения синтез-газа. Углеводородное сырье, содержащее метан, пропускают через реактор, в верхней части которого необязательно расположен катализатор, имеющий активность при окислении углеводородного сырья, и через слой катализатора парового риформинга. При этом катализаторы находятся в непосредственном контакте со стороной мембраны, проницаемой для кислорода. Выходная область слоя катализатора парового риформинга не имеет контакта с мембраной. Изобретение позволяет получить газ заданного состава и снизить рабочие температуры процесса. 4 ил.
Изобретение относится к способу получения синтез-газа, содержащего в основном Н2 и СО, для производства метанола, аммиака, процессов Фишера-Тропша, для запитки твердооксидных топливных элементов.
В настоящее время большинство известных способов производства синтез-газа базируется на предварительной конверсии природного газа, основным компонентом которого является метан (см. B.C.Арутюнов, О.В.Крылов. Окислительные превращения метана. М.: Наука, 1978, 361 с.).
Синтез-газ в основном получают паровой конверсией метана (ПКМ):
Эта реакция сильно эндотермическая, и для ее протекания необходимо подведение тепла. Для того чтобы избежать выделения сажи на катализаторе, реакцию проводят при большем количестве водяного пара при соотношении Н2О/СН4 больше 2. Это требует дополнительного подведения тепла на парогенерацию, которое также требуется и для поддержания температуры реактора около 900°С. Чтобы поддерживать необходимые тепловые условия для процесса ПКМ дополнительно сжигают еще около 50% природного газа. Реже синтез-газ получают углекислотной конверсией метана (УКМ):
Эта реакция еще более эндотермическая.
Снижение себестоимости синтез-газа достигается за счет окислительной конверсии метана, а именно путем парциального окисления метана (ПОМ):
Для протекания этой реакции не требуется подвода тепла, а значит, дополнительного сжигания углеводородного сырья, кроме того, синтез-газ, получаемый по этому способу, имеет отношение Н2/СО, близкое к 2, и может быть использован при синтезе метанола и/или синтетического жидкого топлива по реакции Фишера-Тропша.
Таким образом, если при получении синтез-газа отношение Н2/СО сильно отличается от 2, это приводит к повышенным энергоматериальным затратам. Например, корректировка состава синтез-газа, получаемого в процессе ПКМ, до соотношения Н2/СО=2 достигается введением диоксида углерода CO2.
Для снижения энергозатрат и получения синтез-газа с отношением Н2/СО, близким к 2, известен способ (Патент RU 2228901, С01В 3/38, 2004), в котором синтез-газ получают в двухстадийном процессе. На первой ступени первой стадии происходит некаталитическое парциальное окисление с температурой 1400-1800°С с получением в синтез-газе неравновесного содержания H
К основным недостаткам данного способа производства синтез-газа относятся:
– необходимость большого количества кислорода (O2:СН4=0.76-0.84), получение которого является энергоемким производством, требующим дорогостоящего оборудования;
– высокая температура процессов, проходящих на первой стадии, что требует использования дорогостоящих спецматериалов;
– необходимость дополнительного оборудования, например камеры смешивания и коррекции состава синтез-газа, фильтра из специальных материалов для улавливания сажи, образовавшейся на первой стадии.
Наиболее близким по технической сущности способом к заявляемому техническому решению является способ получения газа, обогащенного водородом и/или оксидом углерода (Патент RU 2248931, МПК С01В 3/26, 2005). Синтез-газ получают путем автотермического реформинга с водяным паром углеводородного сырья, которое пропускают через слой катализатора реформинга с водяным паром и в который подают кислород через мембрану, проницаемую для кислорода, с последующим удалением конечного продукта из этого слоя. Причем способ характеризуется тем, что углеводородное сырье пропускают через слой катализатора, во входной области которого содержится катализатор, имеющий пониженную активность или совсем не имеющий активности в реформинге с водяным паром и имеющий активность в окислении углеводородного сырья. Улучшение характеристик процесса достигается путем контроля градиента температуры в реакторе.
Добавление воды к метану в любом количестве приводит к тому, что отношение Н2/СО становится выше 2. Поэтому такой синтез-газ не может быть прямо использован при синтезе метанола и/или синтетического жидкого топлива по реакции Фишера-Тропша, и требуется дополнительная коррекция его состава.
К недостаткам известного способа производства синтез-газа относятся:
– необходимость использования большого количества водяного пара на проведение автотермического реформинга, что приводит к существенному градиенту температуры по длине мембраны за счет снижения температуры в нижней части мембраны вследствие протекания эндотермических реакций паровой и углекислотной конверсии метана, что в свою очередь приводит к уменьшению удельного потока кислорода через мембрану;
– повышенное отношение Н2/СО>2 (около 2.3) в конвертированном газе после автотермического реформинга, что не позволяет использовать получаемый синтез-газ при синтезе метанола и/или синтетического жидкого топлива без дополнительной коррекции состава.
Таким образом, перед авторами стояла задача разработать способ получения синтез-газа, который наряду с возможностью получения заданного состава газа по основным компонентам Н2 и СО в диапазоне отношений Н2/СО от 1.8 до 2.0 является более технологичным за счет снижения рабочих температур и исключения использования водяного пара.
Поставленная задача решена в предлагаемом способе получения синтез-газа, обогащенного водородом и моноксидом углерода, путем пропускания углеводородного сырья, содержащего метан, через катализатор, верхний слой которого имеет активность при окислении углеводородного сырья, а нижний слой является катализатором парового реформинга, в который подают кислород через проницаемую для кислорода мембрану, при этом катализатор находится в непосредственном контакте со стороной мембраны, проницаемой для кислорода, в котором углеводородное сырье пропускают через катализатор, необязательно имеющий верхний слой, а выходная область слоя катализатора парового реформинга не имеет контакта с мембраной.
Предлагаемый способ позволяет получить синтез-газ, содержащий в основном Н2 и СО, для производства метанола, аммиака, процессов Фишера-Тропша, для запитки твердооксидных топливных элементов. Способ включает две стадии: стадию 1) парциального окисления метана и стадию 2) конверсии остаточного метана продуктами стадии 1) на катализаторе парового реформинга в отсутствие его контакта с проницаемой для кислорода мембраной, то есть в отсутствие кислорода, поступающего через мембрану. Стадию 1) проводят при мольном соотношении кислорода и метана, примерно равным 0.6-0.7, путем каталитического или некаталитического парциального окисления метана кислородом, который подают через мембрану со смешанной кислород-ионной и электронной проводимостью. Затем на стадии 2) дополнительно протекает конверсия метана продуктами стадии 1). Причем углеводородное сырье на стадии 1) пропускают через слой катализатора, находящийся в контакте с мембраной, и во входной области которого необязательно содержится катализатор, имеющий повышенную активность при окислении углеводородного сырья. Остаточный метан и продукты стадии 1) пропускают через слой катализатора парового реформинга, который не находится в контакте с кислородной мембраной.
Кислород в реактор поступает путем его сепарации из воздуха через керамическую мембрану со смешанной кислород-ионной и электронной проводимостью. При использовании керамических мембран из материалов со смешанной проводимостью по ионам кислорода и электронам выделение кислорода из воздуха протекает самопроизвольно за счет разницы парциальных давлений кислорода на мембране. Перенос кислорода внутри мембраны осуществляется не в молекулярной форме, а в виде ионов. Электронейтральность мембраны достигается за счет встречного потока электронов.
Поток кислорода в условиях разницы парциальных давлений (р′ и р”) кислорода с разных сторон мембраны определяется как:
где σион – кислородная проводимость, σэл – электронная проводимость, р(O2) -парциальное давление кислорода в газовой фазе, Т – температура, R – газовая постоянная, F – число Фарадея, L – толщина мембраны.
Градиент давления кислорода в условиях реактора парциального окисления метана задается воздухом и продуктами окисления метана. Из уравнения (4) видно, что поток кислорода через мембрану определяется не только градиентом давления кислорода, но сильно зависит от величины кислородной и электронной проводимости, которые находятся в прямой зависимости от состава материала и температуры. Таким образом, поток кислорода может существенно изменяться (в десятки раз) не только в зависимости от градиента давления кислорода, но и от изменения температуры. Исследования, проведенные авторами, позволили определить условия, при которых температура по длине мембраны остается практически постоянной, что позволяет получить значительный поток кислорода по всей длине мембраны при умеренной температуре поверхности мембраны (850-950°С).
Предлагаемый способ может быть осуществлен следующим образом (см. Фиг.1а и 1б).
Метан (1) и воздух (5) поступают в реактор (2) раздельно при комнатной температуре. В высокотемпературной зоне реактора метан и воздух разделены мембраной (4), выполненной из материала со смешанной кислород-ионной и электронной проводимостью, например, состава La1-XSrXFe1-yCryO3, где 0,4≤x≤0,6; 0≤у≤0,4. Ту часть высокотемпературной зоны реактора, в которую вводят метан, загружают катализатором реформинга с водяным паром (6), например, состава 5-15 мас.% Ni/Al2O3 и необязательно катализатором окисления углеводородного сырья (7) (см. Фиг.1а) состава, например, 5-15 мас.% Mn2O3/Al2O3
Практически полная конверсия остаточного метана достигается в объеме катализатора парового реформинга, который не имеет контакта с кислородной мембраной (см. Фиг.1а и 1б).
Предлагаемый способ позволяет существенно снизить рабочие температуры по сравнению с известными процессами. Кроме того, получение синтез-газа с содержанием основных компонентов Н2 и СО в диапазоне отношений Н2/СО от 1.8 до 2.0 не требует дополнительного расхода углеводородного сырья для поддержания рабочих температур в реакторе.
Предлагаемое техническое решение иллюстрируется следующими примерами.
Пример 1. В реактор (см. Фиг.1а) загружают катализатор парового реформинга состава 10 мас.% Ni/Al2O3 в виде гранул так, что верхняя область катализатора примыкает к внутренней стороне проницаемой для кислорода мембраны, выполненной из материала смешанного проводника состава La0,5Sr0,5FeO3, а выходная область катализатора не имеет контакта с мембраной. Верхнюю часть реактора заполняют катализатором окисления углеводородов состава 10 мас.% Mn2O3/Al2O3 в виде гранул, слой катализатора расположен над слоем катализатора парового реформинга и также примыкает к внутренней стороне проницаемой для кислорода мембраны. Температура в средней части мембраны равна 950°С. Поток метана выбирают таким образом, чтобы поступающий через мембрану кислород обеспечивал мольное соотношение кислорода и метана 0,7:1,0. Получаемый синтез-газ направляют далее в конденсатор. На выходе из конденсатора синтез-газ имеет следующий состав, об.%: Н2-61.8%, СО – 34.4%, CO2 – 2.7%, СН4 – 1.1%. Отношение Н2/СО равно 1.8.
Пример 2. В реактор (см. Фиг.1б) загружают катализатор парового реформинга состава 10 мас.% Ni/ Al2O3 в виде гранул так, что верхняя область катализатора примыкает к внутренней стороне проницаемой для кислорода мембраны, выполненной из материала состава La0,5Sr0,5FeO3, а выходная область катализатора не имеет контакта с мембраной. При этом верхняя часть реактора не заполнена катализатором. Температура в средней части мембраны равна 850°С. Поток метана выбирают таким образом, чтобы поступающий через мембрану кислород обеспечивал мольное соотношение кислорода и метана 0,58:1,0. Получаемый синтез-газ направляют далее в конденсатор. На выходе из конденсатора синтез-газ имеет следующий состав, об.%: Н2 – 64.2%, СО – 32.3%, CO2 – 2.1%, CH4 – 1.4%. Отношение Н2/СО равно 1.99.
Нижеприведенные примеры иллюстрируют ухудшение достигаемого технического результата в случае несоблюдения предлагаемых условий получения синтез-газа.
Пример 3. В реактор (см. Фиг.2) загружают катализатор парового реформинга состава 10 мас.% Ni/Al2O3 в виде гранул так, что катализатор примыкает к внутренней стороне проницаемой для кислорода мембраны, выполненной из материала состава La0,5Sr0,5FeO3, и высота слоя катализатора равна длине мембраны. Верхнюю часть реактора заполняют катализатором окисления углеводородов состава 10 мас.% Mn2O3/Al2O3 в виде гранул, слой катализатора расположен над слоем катализатора парового реформинга и также плотно примыкает к внутренней стороне проницаемой для кислорода мембраны. Температура в средней части мембраны равна 900°С. Поток метана выбирают таким образом, чтобы поступающий через мембрану кислород обеспечивал мольное соотношение кислорода и метана 0,71:1,0. Получаемый синтез-газ направляют далее в конденсатор. На выходе из конденсатора синтез-газ имеет следующий состав, об.%: Н2 – 60.0%, СО – 33.2%, CO2 – 4.0%, СН4 – 2.8%. Отношение Н2/СО равно 1.8.
Увеличение содержания в синтез-газе метана указывает, что в условиях примера 3 метан не успевает прореагировать с водой и СO2, которые образуются в процессе окисления, в результате чего конверсия метана понижается.
Пример 4. В реактор (см. Фиг.3) загружают катализатор парового реформинга состава 10 мас.% Ni/Al2O3 в виде гранул на уровне верхнего среза мембраны так, что верхняя область катализатора примыкает к внутренней стороне проницаемой для кислорода мембраны, выполненной из материала смешанного проводника состава La0,5Sr0,5FeO3, а выходная область катализатора не имеет контакта с мембраной. Температура в средней части мембраны равна 900°С. Поток метана выбирают таким образом, чтобы поступающий через мембрану кислород обеспечивал мольное соотношение кислорода и метана 0,68:1,0. Получаемый синтез-газ направляют далее в конденсатор. На выходе из конденсатора синтез-газ имеет следующий состав, об.%: Н2 – 65.5%, СО – 28.5%, CO2 – 5.8%, СН4 – 0.2%. Отношение Н2/СО равно 2.3.
Полученное соотношение Н2/СО, равное 2.3, указывает, что метан частично разложился с образованием водорода и сажи. Действительно, при осмотре реактора в верхней части катализатора присутствует значительное количество сажи.
Таким образом, авторами предлагается технологически простой способ получения синтез-газа, обогащенного водородом и монооксидом углерода, обеспечивающий практически полную конверсию метана, содержащегося в углеводородном сырье. Способ позволяет снизить температуры процесса (850-950°С – в предлагаемом; 1200-1400°С – в известном) и полностью исключить подачу в реактор водяного пара и образование сажи.
Способ получения синтез-газа путем пропускания углеводородного сырья, содержащего метан, через реактор, в верхней части которого необязательно расположен катализатор, имеющий активность при окислении углеводородного сырья, и через слой катализатора парового риформинга, при этом катализаторы находятся в непосредственном контакте со стороной мембраны, проницаемой для кислорода, отличающийся тем, что выходная область слоя катализатора парового риформинга не имеет контакта с мембраной.
www.findpatent.ru
описание работы реактора синтез газа, генератора синтез газа, один из вариантов моей конструкции.
Реактор генераторного газа или синтез газа, по сути это одно и тоже просто в процессе получения синтез газа мы имеем еще и водород, сам же реактор дополняется только лишь подводкой пара в зону реакции.Что мы видим в сравнении с теплотворностью метана (природного газа)
Метан в районе 8000-8500 ккал/м3
Генераторный газ – 1000-1350 ккал/м3
Синтез газ- до 2700 ккал/м3
Если разбить на зоны, весь процесс происходящий в реакторе, то мы увидим зону окисления воздушным дутьем, это зона горения, зону раскаленного углерода где происходит реакция восстановления СО2 в СО и реакцию где пар превращается в СО и Н2 , выше же получаем зону нагрева сырья, то есть там как раз идет пиролиз и выделение летучих которые вместе с СО и Н2 создают газовую смесь, которую можно отправить на дизель генератор. Но при отправке в реактор Фишера Тропша для получения синтетических топлив нужно “промывать” газ где получим отходы, для реактора оптимальный вариант обуглероженная древесина, торф- из них получаем чистый синтез газ без смол отходов.
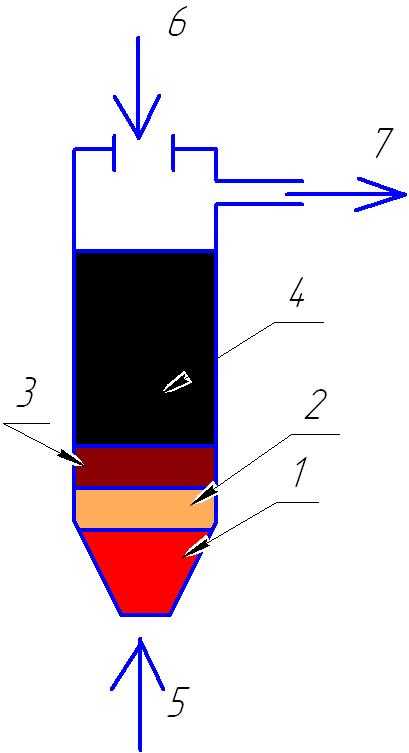
Данная схема показывает зоны реакции и принцип работы реактора.
- Зона горения сырья.
- зона раскаленного углерода, где происходит восстановление СО2 в СО и разложение Н2О на СО и Н2.
- Зона пиролиза, то есть так как кислород сгорает в зоне 1 то в зоне 3 идет реакция нагрева без кислорода, то есть пиролиз и возгонка летучих –
4. Сырье.
5. Паровоздушное дутьё.
6. Загрузка сырья.
7. выход генераторного газа, либо синтез газа, либо смеси синтез газа с летучими, зависит от конструкции сырья.
Далее, сам реактор должен состоять из реактора системы золоудаления и системы очистки полученного газа.
Система золоудаления, довольно сложный момент и зависит от сырья, сырье при сгорании которого получается рассыпчатая зола выводится сквозь колосники вниз в водяной затвор, а часть с потоком газа где проходя через циклон осаждается в золоуловителе. Данный момент прошел испытания практически, и показал что золоудаление по такой системе работает эффективно без сбоев.
Далее, система очистки получаемого газа состоит из вертикальной трубы где в противоток газу идет водяной душ, и очищает газ от вкраплений мелкой золы, остатков пара и смол, а так же если смешивать воду с щелочью, известковать её то можно снизить кислотность газа.
Реактор может запускаться автономно используя минимум энергии, то есть от какого то небольшого генератора тока, для этого подходит схема отработанная мной на реакторе где весь процесс обеспечивается маломощным вентилятором высокого давления, 2.5 квт, 220 вольт, который соединен с частотным преобразователем который дает возможность изменять производительность вентилятора, т.е. подачу воздуха, которая нужна для того что определить оптимальный вариант подачи воздуха в реактор. НО!!!! При использовании данной схемы сырье должно быть кусковым, то есть при работа вентилятора воздух должен проходить сквозь сырье, а это может дать кусковое сырье но не коем случае не пылевидное или очень мелкое смешанное с пылью, которое не даст прохода воздуха при такой мощности вентилятора. Если мы все же используем более мелкое и пылевидное сырье, тогда вентилятор должен быть мощнее, и конечно потребление электроэнергии будет выше, и принцип работы уже будет в “кипящем слое”.
При переработке сырья типа древесины, сланцев , торфа, и т.д мы получаем парогазовую смесь смешанную с синтез газом, так как в зоне 3 протекает в принципе низкотемпературный пиролиз, и чем больше парогазовой смеси дает сырье, тем с одной стороны больше теплотворность газа, но с другой стороны при охлаждении его мы получаем жидкие сконденсированные продукты. Поэтому конструкция должна предусматривать если очистку и охлаждение синтез газа то и отвод и удаления сконденсированных продуктов, разделение их от вкраплений золы, разделения от воды в варианте скруббера и так далее..то есть от применяемого сырья зависит не только золоудаление но и конечный продукт и возможно дополнительные узлы очистки, охлаждения, разделения, отстаивания, чистки, обслуживания. Поэтому и писал выше что оптимальный вариант для получения чистого синтетического газа это обуглероженный продукт, где все смолы уже отсутствуют.
Варианты конструкции.
На данном этапе определяемся по конструкции самого реактора и системе очистки газа, тут несколько моментов, первое, ручная загрузка реактора, либо механическая, ручная выгрузка золы , либо механическая. Для того чтобы определится описываю момент загрузки сырья в реактор.
- Простейший способ: В процессе работы частотным преобразователем устанавливается минимальная скорость производительность вентилятора и открывается верхний люк реактора куда в ручную загружается сырье, метод простой но требует остановки реактора на момент загрузки что ведет к остановки и дизель генератора, и требует увеличения объема самого реактора чтобы как можно меньше было остановок, данный реактор дает безостановочную работу в районе 3.5-4.5 часа , так же продолжительность работы реактора зависит и от сырья, влажности сырья, максимальная влажность сырья не должна превышать 30- 40 процентов, пуск системы должен происходить на сырье влажностью не более 20 процентов.
- Следующий способ это шнековая подача, тут надо знать размер кусков сырья, шнек подачи для такого оборудования делается под заказ, но по сути его можно установить после того как испытали систему, если он нужен.
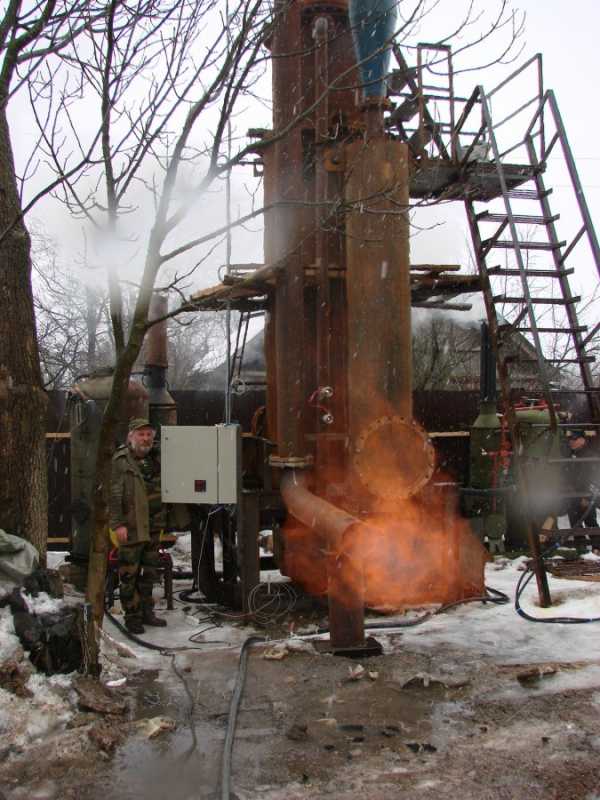
Данный реактор без системы тонкой очистки газа в действии, пламя это горит синтез газ, мощность данного реактора 07 МВт.
Загрузка реактора сырьем через люк, который расположен в верхней части реактора.
Пуск реактора, через люк укладываются дрова, зажигаются, включается дутье вентилятором, люк закрывается, рабочее же сырье засыпается через верхний люк.
Парогенератор который так же работает на твердом топливе и обеспечивает реактор паром для получения синтез газа.
Внутренняя часть реактора.
Данный реактор синтез газа
потребляет:
1. обуглероженной древесины (древесного угля)- 110-120 кг в час.
2. Пара – замеров не былло.
3. Электричество- вентилятор высокого давления 2.5 квт потребления в час.
Получаем 0.7 МВт приблизительно тепловой энергии.
электрической возможно получить 150-200 квт. при присоединении ДВС с электрогенератором.
Ну и получение синтетических жидких топлив при работе с реактором Фишера Тропша на катализаторах.
видео работы реактора синтез газа:
Ну немножко информации из “Технологии лесохимических производств , издательство”Лесная промышленность “, Москва 1970 год
А.К. Славянский, Ф.А.Медников.
Как видите из приведенных выше сканов , данные газогенераторы сложнее, я пошел по пути использования обуглероженного сырья… то есть у меня меньше аппаратного обеспечения для очисти генераторного газа либо синтез газа, хотя возможно проектирование и изготовление и на щепе… конечно и на другом сырье.
ну и тут еще немного информации: http://suslovm.narod.ru/Gazogenerator.html
немного добавлю сканов, пришлось срочно сделать предварительные наброски газогенератора для Донецка, пока считал, нашел у себя еще литературку, может кому пригодится:
Ну и вот предварительная предпроектная схемка недорогого реактора сравнительно, мощностью 1.5 мегаватта с потреблением сырья по углероду 200 кг в час.
ну а ниже схема небольшого газогенератора для так скажем бытовых нужд,
Ну вот дорогие друзья, коллеги и товарищи… добавлю немножко интересного материала, добавляю сканы чтобы было понятно что это не моя отсебятина:
Обложка справочника:
Москва , “Лесная промышленность” 1990 год.
ну вот как бы, наслаждайтесь!
Одна из последних установок- испытания.
Принципиальная схема реактора синтез газа из метана, метан это природный газ, при конверсии его в синтез газ, процент водорода получаем больше, синтез газ из метана интересен восстанвлением руды в железо, получение метанола и так далее…
Тел: +7-911-281-95-62 – основной мобильный.
Суслов Михаил Борисович,
ООО “Экосинтез”, Санкт-Петербург.
Электронная почта для связи: [email protected]
Сайт:
http://suslovm.ucoz.ru/
{C}{C}{C}
<div><img src=”//mc.yandex.ru/watch/25503512″ alt=”” /></div>
suslovm.livejournal.com
ООО “Экосинтез” – Газогенератор, генератор синтез газа. Получение генераторного газа, синтез газа.
Реактор генераторного газа или синтез газа, по сути это одно и тоже просто в процессе получения синтез газа мы имеем еще и водород, сам же реактор дополняется только лишь подводкой пара в зону реакции. Что мы видим в сравнении с теплотворностью метана (природного газа) Метан в районе 8000-8500 ккал/м3 Генераторный газ – 1000-1350 ккал/м3 Синтез газ- до 2700 ккал/м3 Если разбить на зоны, весь процесс происходящий в реакторе, то мы увидим зону окисления воздушным дутьем, это зона горения, зону раскаленного углерода где происходит реакция восстановления СО2 в СО и реакцию где пар превращается в СО и Н2 , выше же получаем зону нагрева сырья, то есть там как раз идет пиролиз и выделение летучих которые вместе с СО и Н2 создают газовую смесь, которую можно отправить на дизель генератор. Но при отправке в реактор Фишера Тропша для получения синтетических топлив нужно “промывать” газ где получим отходы, для реактора оптимальный вариант обуглероженная древесина, торф- из них мы получаем чистый синтез газ без отходов.
.
Данная схема показывает зоны реакции и принцип работы реактора.
1. Зона горения сырья.зона.
2. Зона раскаленного углерода, где происходит восстановление СО2 в СО и разложение Н2О на СО и Н2.
3. Зона пиролиза, то есть так как кислород сгорает в зоне 1 то в зоне 3 идет реакция нагрева без кислорода, то есть пиролиз и возгонка летучих –
в первую очередь метана, этана и этилена и т.д. в зависимости от сырья…
4. Сырье.
5. Паровоздушное дутьё.
6. Загрузка сырья.
7. выход генераторного газа, либо синтез газа, либо смеси синтез газа с летучими, зависит от конструкции сырья.
Далее, сам реактор должен состоять из реактора системы золоудаления и системы очистки полученного газа. Система золоудаления, довольно сложный момент и зависит от сырья, сырье при сгорании которого получается рассыпчатая зола выводится сквозь колосники вниз в водяной затвор, а часть с потоком газа где проходя через циклон осаждается в золоуловителе. Данный момент прошел испытания практически, и показал что золоудаление по такой системе работает эффективно без сбоев. Далее, система очистки получаемого газа состоит из вертикальной трубы где в противоток газу идет водяной душ, и очищает газ от вкраплений мелкой золы, остатков пара и смол, а так же если смешивать воду с щелочью, известковать её то можно снизить кислотность газа. Реактор может запускаться автономно используя минимум энергии, то есть от какого то небольшого генератора тока, для этого подходит схема отработанная мной на реакторе где весь процесс обеспечивается маломощным вентилятором высокого давления, 2.5 квт, 220 вольт, который соединен с частотным преобразователем который дает возможность изменять производительность вентилятора, т.е. подачу воздуха, которая нужна для того что определить оптимальный вариант подачи воздуха в реактор. НО!!!! При использовании данной схемы сырье должно быть кусковым, то есть при работа вентилятора воздух должен проходить сквозь сырье, а это может дать кусковое сырье но не коем случае не пылевидное или очень мелкое смешанное с пылью, которое не даст прохода воздуха при такой мощности вентилятора. Если мы все же используем более мелкое и пылевидное сырье, тогда вентилятор должен быть мощнее, и конечно потребление электроэнергии будет выше, и принцип работы уже будет в “кипящем слое”. При переработке сырья типа древесины, сланцев , торфа, и т.д мы получаем парогазовую смесь смешанную с синтез газом, так как в зоне 3 протекает в принципе низкотемпературный пиролиз, и чем больше парогазовой смеси дает сырье, тем с одной стороны больше теплотворность газа, но с другой стороны при охлаждении его мы получаем жидкие сконденсированные продукты. Поэтому конструкция должна предусматривать если очистку и охлаждение синтез газа то и отвод и удаления сконденсированных продуктов, разделение их от вкраплений золы, разделения от воды в варианте скруббера и так далее..то есть от применяемого сырья зависит не только золоудаление но и конечный продукт и возможно дополнительные узлы очистки, охлаждения, разделения, отстаивания, чистки, обслуживания. Поэтому и писал выше что оптимальный вариант для получения чистого синтетического газа это обуглероженный продукт, где все смолы уже отсутствуют.
Варианты конструкции. На данном этапе определяемся по конструкции самого реактора и системе очистки газа, тут несколько моментов, первое, ручная загрузка реактора, либо механическая, ручная выгрузка золы , либо механическая. Для того чтобы определится описываю момент загрузки сырья в реактор.
- Простейший способ: В процессе работы частотным преобразователем устанавливается минимальная скорость производительность вентилятора и открывается верхний люк реактора куда в ручную загружается сырье, метод простой но требует остановки реактора на момент загрузки что ведет к остановки и дизель генератора, и требует увеличения объема самого реактора чтобы как можно меньше было остановок, данный реактор дает безостановочную работу в районе 3.5-4.5 часа , так же продолжительность работы реактора зависит и от сырья, влажности сырья, максимальная влажность сырья не должна превышать 30- 40 процентов, пуск системы должен происходить на сырье влажностью не более 20 процентов.
- Следующий способ это шнековая подача, тут надо знать размер кусков сырья, шнек подачи для такого оборудования делается под заказ, но по сути его можно установить после того как испытали систему, если он нужен.
Данный реактор без системы тонкой очистки газа в действии, пламя это горит синтез газ, мощность данного реактора 0.7 МВт.
Загрузка реактора сырьем через люк, который расположен в верхней части реактора.
Пуск реактора, через люк укладываются дрова, зажигаются, включается дутье вентилятором, люк закрывается, рабочее же сырье засыпается через верхний люк.
Парогенератор который так же работает на твердом топливе и обеспечивает реактор паром для получения синтез газа.
Внутренняя часть реактора.
Данный реактор синтез газа потребляет: 1. обуглероженной древесины (древесного угля)- 110-120 кг в час. 2. Пара – замеров не былло. 3. Электричество- вентилятор высокого давления 2.5 квт потребления в час. Получаем 0.7 МВт приблизительно тепловой энергии. электрической возможно получить 150-200 квт. при присоединении ДВС с электрогенератором. Ну и получение синтетических жидких топлив при работе с реактором Фишера Тропша на катализаторах.
видео работы реактора синтез газа:
Ну немножко информации из “Технологии лесохимических производств , издательство”Лесная промышленность “, Москва 1970 год А.К. Славянский, Ф.А.Медников.
Как видите из приведенных выше сканов , данные газогенераторы сложнее, я пошел по пути использования обуглероженного сырья… то есть у меня меньше аппаратного обеспечения для очисти генераторного газа либо синтез газа, хотя возможно проектирование и изготовление и на щепе… конечно и на другом сырье.
Немного добавлю сканов, специально разместил титульный лист справочника , что бы было понятно, как давно человечество занимается этим направлением – получение энергетики таким вот способом!
Ну и вот предварительная предпроектная схемка недорогого реактора сравнительно, мощностью 1.5 мегаватта с потреблением сырья по углероду 200 кг в час.
ну а ниже схема небольшого газогенератора для так скажем бытовых нужд,данный газогенератор можно спроектировать от 1.5 до 3 метров высотой, и он может питать ДВС который будет крутить электрогенератор или водяной насос, либо расположен в кузове грузовика.
Ну а тут компактная схема газогенератора для питания ДВС .
1. Газогенератор (бункер)
2. Съемная часть бункера.
3. Реактор газогенератора.
4. Расширитель зольник газогенератора.
5. Парогенератор на твердом топливе типа РИ 5 м.
6. Контейнер 20 футовый размер 6058х2438х2915(высота)
7. Вентилятор высокого давления газогенератора.
8. Вентилятор охлаждения системы фильтрации газа.
9. Шнек подающий топливо в газогенератор.
10. Шнек удаляющий золу с газогенератора.
11. Шкаф управления .
12. Фланцы соединяющие сборный бункер.
13. Блок грубых фильтров системы фильтрации генераторного газа.
14. фильтрующий элемент с возможностью механической очистки и промывания.
15. Фильтр тонкой очистки генераторного газа, с удалением влаги.
16. Пространство контейнера куда укладываются шнеки и съемная часть бункера, инструмент, соединяющие шланги.
2. Принцип работы установки.
Контейнер(6) устанавливается на ровную площадку, открываются технологические люки, монтируется съемная часть бункера(2), шнеки(9,10).
В реактор газогенератора (3) закладывается легко поджигаемое топливо, типа сухой щепы, поджигается через открытое технологическое отверстие, вентилятор поддува(7) пускается на минимальный ход. После того как щепа разгорается идет подача топлива в бункер(1, 2) через шнек(9) до полной загрузки. А далее после устойчивого горения прибавить ход вентилятора(7) и засыпать полный бункер.
В подающий шнек(9) загружается топливо и подается в бункер до полной загрузки, мерная часть – сам бункер
шнека.
Шнек выгружающий(10) закрыт.(На рисунке шнеки изображены схематически.)
Так же запускается парогенератор ( описание эксплуатации парогенератора в инструкции по эксплуатации парогенератора.)
Поступление пара в реактор регулируется вентилем, излишки пара уходят в атмосферу.
Рабочий режим газогенератора считать при протекании стабильной незатухающей реакции с выходом нужного к-ва газа и нужной его калорийности в пределах норм. К-во газа регулируется частотным преобразователем, который определяет обороты вентилятора поддува (7) и находится в шкафу управления(11). Калорийность при добавлении пара увеличивается но при избытке возможна затухающая реакция.
Принцип работы газогенератора состоит в том что топливо загружается в приемный бункер(9) и попадает в реактор газогенератора(3), где происходит реакция восстановления СО2 в СО плюс при добавлении пара разложение воды на водород и кислород,, а так же уменьшение доли азота, что дает дополнительную калорийность газа. И чем больше газа нужно получить тем стабильнее реакция. Калорийность газа следующая: Генераторный газ до 990 ккал м3, синтез газ(смешанный газ) до 1630 ккал на м3.
После получения (восстановительная реакция) газа в ректоре газогенератора(3) газ поступает в зольник расширитель(4), куда так же поступает и зола с реактора газогенератора (3). Зола выгружается с помощью шнека (10), а газ поступает в блок грубой очистки ( 13), где фильтра связаны с собой последовательно, фильтры (14)выемные с возможностью очистки. После грубой очистки газ поступает в фильтр тонкой очистки газа (15), где дополнительно очищается и обезвоживается и далее поступает на ДВС либо другому потребителю.
Ну а это газогенераторный ЗиЛ 130, т.е. машина едет на дровах:
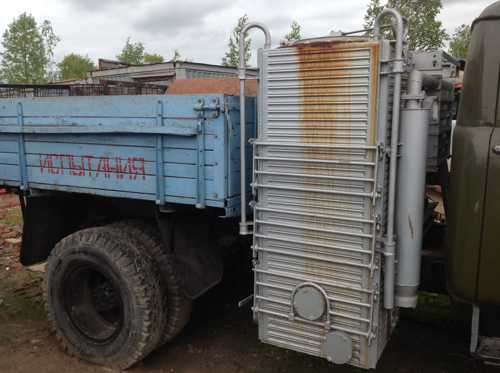
Ну вот дорогие друзья, коллеги и товарищи… добавлю немножко интересного материала, добавляю сканы чтобы было понятно что это не моя отсебятина: Обложка справочника:
Москва , “Лесная промышленность” 1990 год.
ну вот как бы, наслаждайтесь!
тел: 8-911-281-95-62 Суслов Михаил Борисович, ООО “Экосинтез”, Санкт-Петербург. Электронная почта для связи: [email protected]
suslovm.ucoz.ru
Синтез газ для производства метанола получают взаимодействием
Свойства метанола и его применение
Метанол по значению и масштабам производства является одним из важнейших многотоннажных продуктов, выпускаемых современной химической промышленностью.
Он широко применяется для получения пластических масс, синтетических волокон, синтетического каучука. Высокой растворимостью газов в метаноле широко пользуются в промышленности, применяя метанол и его растворы в качестве поглотителя для извлечения примесей из технологических газов. Метиловый спирт – важный вид сырья для получения формальдегида, ингибиторов, антидетонационных смесей, антифризов, лаков, красок и других продуктов. В чистом виде применяется как высокооктановая добавка к топливу.
Метанол (метиловый спирт) СН3ОН представляет бесцветную легкоподвижную жидкость с температурой кипения 650С, температурой кристаллизации –97.90С и плотностью 0.792 т/м3. Критическая температура метанола 239.650С. Метанол горюч. Температура вспышки 80С, пределы взрываемости паров в воздухе 5.5-36.5%. Метанол смешивается во всех отношениях с водой, спиртами, бензолом, ацетоном и др. органическими растворителями. Пары сухого метанола образуют с воздухом взрывчатые смеси. Метанол токсичен, вызывает отравление через органы дыхания, кожу и при приеме внутрь, действуя на нервную и сосудистую систему. ПДК составляет 5 мг/м3. Прием внутрь 5-10 см3 приводит к тяжелому отравлению, вызывает слепоту, доза 30 см3 – смертельна. Метанол – сильный яд кумулятивного действия, оказывает также слабое наркотическое действие.
Методы получения.
Долгое время метанол получали исключительно сухой перегонкой древесины. Этот способ достаточно трудоемкий и дорогой, так как из 1м3 березовых дров можно получит лишь 5-6кг метанола. Производство метанола синтезом из оксида углерода и водорода впервые было организовано в Германии в 1923г.
Метанол получают различными методами, отличающимися исходным сырьем, способами его переработки в технологический газ, а также условиями проведения синтеза метанола. В н.в. основной способ получения метанола – синтез из оксида углерода и водорода (эта смесь называется синтез-газом). Смесь окиси углерода и водорода производят путем конверсии метана.
Синтез метанола по физико-химическим условиям его проведения и по технологическому оформлению аналогичен синтезу аммиака. Как азото-водородную смесь, так и синтез-газ можно получить конверсией природного газа. В обоих процессах взаимодействие смесей тщательно очищенных газов происходит в присутствии катализатора. Из-за малого выхода конечных продуктов и тот и другой процессы являются непрерывно циклическими, причем реакцию никогда не ведут до полного превращения. Такая аналогия дала возможность вести оба синтеза на подобных установках, которые монтируют в составе одного завода.
Исходным сырьем в процессе синтеза метанола является газ после паро-кислородной конверсии метана, а также технический водород, применяемый для регулирования соотношения Н2:СО. К составу сырья предъявляются общин требования: наличие примесей – СН4 0.5%, СО2 2.2%, Н2S 2.0 мг/м3, карбонилы железа 3.0 мг/м3.
Процесс получения метанола состоит из следующих стадий:
1. Парокислородной конверсии природного газа в шахтном конверторе.
2. Очистке конвертированного газа от углекислоты до получения газа с функционалом
f = (Н2 –СО2) /(СО +СО2) =2.05 -2.20
3. Осушке конвертированного газа на алюмогеле.
4. Компримировании свежего газа до давления не более 9.3 МПа.
5. Синтез метанола – сырца.
6. Ректификация метанола – сырца.
1. Паро-кислородная конверсия метана.
Процесс получения технологического газа ведется в одну стадию методом паро-кислородной конверсии метана в шахтном конверторе на никелевых катализаторах при температуре 850-12000С.
Процесс протекает по следующим реакциям:
СН4 +2О2 ↔ СО2 +2Н2О (3.1.1)
СН4 + 0.5О2 ↔СО +2Н2 (3.1.2)
СН4 +Н2О ↔ СО +3Н2 (3.1.3)
СН4 +СО2 ↔ 2СО +2Н2 (3.1.4)
СО +2Н2О ↔СО2 +Н2 (3.1.5)
Равновесный состав конвертированного газа зависит от температуры и давления процесса, а также состава исходной смеси, объема и типа катализатора. В свободном объеме над слоем катализатора протекает кислородная конверсия метана по реакциям (3.1.1) и (3.1.2) –экзотермический процесс.
За счет тепла выделившегося в результате протекания данных реакций, в слое катализатора идет паровая и кислородная конверсия метана и углеводородов с увеличением объема и поглощением тепла по реакциям (3.1.3) и (3.1.4) – эндотермический процесс.
Конвертированный газ с объемной долей компонентов: Н2 н/м 63%, СО н/б 19.5%, СО н/м 14%, СН4 0.4-1.5% поступает в трубное пространство котла-утилизатора, отдавая тепло на получение насыщенного пара, теплообменник, подогревая исходную парогазовую смесь, далее охлаждается в холодильниках и направляется на моноэтаноламиновую очистку от СО2.
2. Моноэтаноламиновая очистка конвертированного газа.
Очистка конвертированного газа – процесс удаления СО2, заключается в химической и физической абсорбции СО2 водным раствором моноэтаноламиана МЭА для обеспечения объемной доли СО2 в конвертированном газе н/б 12%.
Процесс очистки протекает по следующим реакциям
2RNН2 +СО2 +Н2О ↔(RNН3)2СО3 (3.1.6)
(RNН3)2СО3 +СО2 +Н2О ↔2RNН3НСО3 (3.1.7)
где R– (НО–СН2-СН3).
Конвертированный газ подается в абсорбер, орошаемый раствором МЭА, который поглощает избыток СО2. Раствор МЭА идет на регенерацию и после удаления из него СО2 возвращается в абсорбер, а конвертированный газ направляется на стадию осушки.
3. Осушка конвертированного газа.
Осушка происходит на неподвижном слое адсорбента – алюмогеле, обладающем свойством поглощать влагу из газа и кислые газы, в т.ч. СО2. Регенерация насыщенного влагой алюмогеля прояизводится продувкой слоя алюмогеля горячим азотом. Процесс осушки проходит в адсорбере заполненном алюмогелем, поглощающим влагу до точки росы -500С. Осушенный конвертированный газ очищается от уносимой алюмогелевой пыли в фильтрах и направляется на компрессию.
4. Компримирование конвертированного газа.
Процесс производится на трехступенчатых компрессорах до давления н/б 9.3 МПа. Затем газ подается на стадию синтеза.
5. Синтез метанола –сырца.
Основные реакции процесса обратимые и экзотермические:
СО + 2Н2 ↔ СН3ОН + 90.7 кДж/моль (3.1.8)
СО2 + 3Н2 ↔ СН3ОН + Н2О+ 49.5 кДж/моль (3.1.9)
Кроме этих реакций протекает и реакция эндотермическая – взаимодействие диоксида углерода и водорода
СО2 + 3Н2 ↔ СО + Н2О — 41.1 кДж/моль (3.1.10)
Одновременно с образованием метанола могут идти и реакции образования диметилового эфира, органических кислот, альдегидов, кетонов, сложных эфиров.
Вода образуется во всех реакциях. Образующиеся побочные продукты в метаноле-сырце определяют как схему получения метанола–ректификата из метанола-сырца, так и качество конечного продукта. Наличие микропримесей и их массовая концентрация в метаноле-сырце зависят от сырья и его подготовки, от катализатора, от технологических параметров процесса.
При выборе параметров процесса руководствуются не только качеством метанола-сырца, но и экономическими факторами. Исходя из этого принят процесс синтеза метанола при температуре н/б 2800С и избыточном давлении н/б 9.0МПа, с функционалом 2.05-2.2 (функционал – отношение разности объемных долей водорода и диоксида углерода к сумме объемных долей оксида и диоксида углерода в свежем синтез-газе) на цинк-медь-алюминиевом катализаторе.
Метанол-сырец, полученный при данных условиях, отвечает требованиям, предъявляемым к нему, как к сырью для получения высококачественного метанола-ректификата.
Установлено, что синтез метанола из оксида углерода и водорода протекает лишь в присутствии воды или кислородсодержащих соединений. На выход метанола-сырца оказывают влияние следующие технологические факторы: давление процесса; температура; объемная скорость газа; соотношение объемных долей компонентов свежего газа, наличие примесей; активность катализатора.
Давление процесса
Согласно принципу Ле-Шателье повышение давления сдвигает равновесие вправо и увеличивает выход метанола-сырца, массовой доли высших спиртов и эфиров в метаноле, уменьшается массовая доля парафинов. Синтез метанола по реакциям (8 и 9) протекает с уменьшением объема, а восстановление диоксида углерода, реакция (10) – без его изменения. В связи с этим повышение давления способствует более глубокой переработке оксидов углерода. Для низкотемпературного синтеза наиболее эффективен диапазон избыточных давлений 4.9-19.6 МПА. При дальнейшем росте давления равновесная концентрация метанола увеличивается незначительно.
Температура.
Согласно принципу Ле-Шателье повышение температуры сдвигает равновесие реакции влево и уменьшает выход метанола. При повышении температуры производительность всех катализаторов проходит через максимум. Рабочая температура синтеза зависит от активности катализатора: чем активнее катализатор, тем при более низкой температуре образуется метанол с приемлемой для промышленных условий скоростью.
С ростом температуры равновесная концентрация метанола в смеси снижается (реакции 8 и 9 идут с выделение тепла), но скорость достижения равновесия увеличивается. Если равновесие не было достигнуто, то небольшое повышение температуры увеличит выход метанола, в случае, если равновесие было достигнуто, повышение температуры снизит выход метанола.
Температуру в слое катализатора надо поддерживать на возможно более низком уровне, при условии обеспечения производительности по метанолу. Оптимальными температурами синтеза метанола при избыточном давлении 8.6-9.0 МПа являются температуры 205-2680С.
В отсутствии катализатора метанол практически не образуется. Применяемые в промышленности катализаторы проявляют активность только при определенных температурах. Степень превращения исходной газовой смеси в метанол за один проход через катализатор практически невелика -6-7%. Для увеличения общего выхода метанола непрореагировавшую газовую смесь после выделения из нее образовавшегося спирта возвращают в колонну синтеза, добавляя свежий газ, т.е. проводят процесс по непрерывной циклической схеме.
Объемная скорость.
С увеличением объемной скорости газа масса метанола, получаемая с единицы объема катализатора, увеличивается, и, за счет уменьшения времени контакта, уменьшается массовая концентрация примесей. Оптимальная объемная скорость составляет (18-20)*103ч-1. При больших объемных скоростях достигается более равномерное распределение температуры в массе катализатора и предотвращаются его перегревы.
Состав свежего газа.
Исходя из стехиометрических коэффициентов реакций (8 и 9), соотношение объемных долей в исходном газе водорода к оксиду углерода составляет (Н2:СО) =2, а (Н2:СО2)=3. Практикой установлено, что газ для синтеза метанола должен содержать компоненты в соотношении близком к стехиометрии и иметь функционал f =2.01-2.18.
Для получения указанного соотношения в большинстве случаев состав синтез-газа после стадии конверсии метана необходимо корректировать отмывкой от СО2. Избыток СО2, сверх необходимого для процесса минимума, является поставщиком избыточного кислорода, который выводится из процесса в виде воды. Извлечение избытка СО2 из конвертированного газа приводит к увеличению объемной доли инертов, а это снижает выход метанола, т.к. снижается парциальное давление реагирующих компонентов. Увеличение соотношения способствует снижению массовых концентраций примесей.
Наличие примесей в исходном газе.
Сера в любом виде токсична для катализатора синтеза метанола. Отравление серой выражается в необратимой потере активности катализатора. Массовая концентрация сероводорода в конвертированном газе должна быть н/б 0.00015 мг/дм3. Сера в свежий газ попадает из природного газа и компрессорного масла, попадание масла в циркуляционный газ может привести к отравлению катализатора. Парафины могут образовываться в ходе реакции при температуре менее 2050С и более 2800С, а также при наличии пентакарбонилов железа. Наличие парафинов в метаноле может привести к забивке арматуры, трубопроводов.
Активность, селективность и другие свойства катализатора.
Активность катализатора уменьшается с увеличением срока службы катализатора, а при наличии вредных примесей в газе, нарушениях технологического режима. Фирмой–изготовителем катализатора определяются оптимальные условия восстановления и работы для каждого типа катализатора, а также гарантии по содержанию примесей в метаноле–сырце при соблюдении установленных условий.
Технологическая схема агрегатов синтеза метанола.
Многочисленные процессы синтеза метанола включают три обязательные стадии: очистка синтез-газа от сернистых соединений, масла, пентакарбонилов железа; собственно синтез и очистка; и ректификация метанола. В остальном технологические схемы отличаются аппаратурным оформлением и параметрами процесса. Все они могут быть разделены на три группы:
1 Синтез при высоком давлении проводится на цинк-хромовом катализаторе при температуре 370-4200С и давлении 20-30 МПА.
2 Синтез при низком давлении проводится на цинк-медь-хромовых катализаторах при Т=250-3000С и давлении 5-10 МПа. Использование в этой схеме низкотемпературных катализаторов, активных при более низком давлении, позволяет снизить энергозатраты на сжатие газа и уменьшить степень рециркуляции непрореагировавшего сырья.
3 Синтез в трехфазной системе «газ-жидкость – твердый катализатор», проводимый в суспензии из тонкодисперсного катализатора и инертной жидкости, через которую барботируется синтез-газ.
Полученный метанол-сырец очищают от кислот, сложных эфиров, высших спиртов, пентакарбонила железа, что в сочетании с последующей ректификацией позволяет получить чистый метиловый спирт. Основным аппаратом в синтезе метанола служит реактор (колонна синтеза) – контактный аппарат, конструкция которого зависит от способа отвода тепла и принципа осуществления процесса синтеза.
Технологический процесс получения метанола из оксида углерода и водорода включает ряд операций, обязательных для любой технологической схемы синтеза. Газ предварительно очищается от карбонила железа, сернистых соединений, подогревается до температуры начала реакции и поступает в реактор синтеза метанола. По выходе из зоны катализа из газов выделяется образовавшийся метанол, что достигается охлаждением смеси, которая затем сжимается до давления синтеза и возвращается в процесс. Функциональная схема производства метанола приведена на риунке.
Рис. 3.1.1 Функциональная схема синтеза метанола
Дата публикования: 2014-10-16; Прочитано: 5086 | Нарушение авторского права страницы
studopedia.org — Студопедия.Орг — 2014-2018 год.(0.005 с)…
Высшие кислородсодержащие кислоты химических элементов третьего периода, их состав и сравнительная характеристика свойств.
Общая характеристика высокомолекулярных соединений: состав, строение, реакции, лежащие в основе их получения (на примере полиэтилена или синтетического каучука).
Задача. Определите массу карбоната магния, прореагировавшего с соляной кислотой, если при этом получено 8,96 л оксида углерода (IV), что составляет 80% от теоретически возможного выхода.
Общие способы получения металлов.
Справочник химика 21
Практическое значение электролиза на примере солей бескислородных кислот.
Виды синтетических каучуков, их свойства и применение.
Дата публикования: 2014-10-16; Прочитано: 5087 | Нарушение авторского права страницы
studopedia.org — Студопедия.Орг — 2014-2018 год.(0.005 с)…
Промышленное получение метанола и этанола
Метанол получают из синтез-газа (катализатор – Cr2O3, ZnO; 350oC, 210 атм):
CO + 2 h3 → СН3ОН
Этанол получают прямой гидратацией этилена (катализатор – Н3РО4, SiO2; 300 oC):
CН2=CН2 + Н2О → СН3СН2ОН
или в присутствии концентрированной серной кислоты (непрямая гидратация):
CН2=CН2 + Н2О → СН3СН2ОSO3H → СН3СН2ОН
Этиловый спирт также получают ферментативным гидролизом углеводов – брожением глюкозы с помощью дрожжей рода Saccharomyces и бактерий рода Zimomonas
C6Н12О6 → 2 СН3СН2ОН + 2 СО2
9) Двухатомные спирты получают гидроксилированием производных этилена – окислением в водной среде, приводящее к образованию α-гликолей
гидратацией α-окисей алкенов:
гидролизом дигалогенпроизводных или галогензамещенных спиртов слабым раствором щелочи:
СlCh3Ch3Cl + 2 NaOH ¾® НOCh3Ch3OH + 2 NaCl
СlCh3Ch3Ch3Ch3OH + NaOH ¾® НOCh3Ch3Ch3Ch3ОН
10) Глицеринсинтезируют либо из пропилена по следующим схемам:
│ ↑
│________ Сl2 __________Ch3–CH–Ch3 _________________│
│ │ │
OH OH OH
или в результате гидролиза жиров в кислой или в щелочной среде:
Синтезы фенолов
а) В промышленности обычно получают фенол по методу Хока – окислением изопропилбензола (метод Хока)
б) Фенолы могут быть получены сплавлением натриевых солей ароматических сульфокислот с гидроксидами щелочных металлов
в) В жестких условиях (350 0С и повышенном давлении) реакцией замещения галогена в арилгалогенидах на гидроксигруппу
в) Гидролизом солей арилдиазония
Физические свойства.Эти свойства спиртов зависят от строения углеводородного радикала и положения гидроксильной группы. Первые представители гомологического ряда спиртов – это жидкости, высшие спирты – твердые вещества.Спирты и фенолы имеют более высокие температуры кипения и плавления,чем соответствующие им углеводороды и галогенопроизводные. Это объясняется тем, что молекулы спиртов ассоциированы за счет образования водородных связей.
:O–Н …. :O–Н …. :O–Н
½ ½ ½
Ассоциаты спиртов имеют следующее строение: R R R
Ассоциация молекул спиртов за счет водородных связей определяется высокой полярностью связи О–Н из-за сильного различия в электроотрицатель-ности атомов кислорода и водорода. Энергия водородной связи (Н….О) составляет 20 кДж/моль, т.е. существенно меньше, чем ковалентной связи Н-О (460 кДж/моль). Тем не менее разрушение водородных связей, которое должно предшествовать испарению веществ при кипении, требует определенных энергетических затрат, что и выражается в повышении температуры кипения. Многоатомные спирты в еще большей степени ассоциированы, т. к. содержат большее число гидроксильных групп, участвующих в образовании водородных связей. Благодаря этому они обладают еще более высокими температурами кипения, а также повышенной растворимостью в воде.
Спирты нормального строения кипят при более высокой температуре, чем разветвленные. Низшие спирты (метанол, этанол, пропанолы) смешиваются с водой в любых соотношениях.
Тема 3.1 Технология производства метанола
С ростом молярной массы растворимость спиртов в воде резко падает. Высшие спирты не растворяются в воде. Растворимость спиртов с разветвленной структурой выше, чем у спиртов, содержащих нормальные радикалы.
Дата добавления: 2017-09-19; просмотров: 607;
ПОСМОТРЕТЬ ЕЩЕ:
magictemple.ru
Способ получения синтез-газа | Банк патентов
Изобретение относится к области неорганической химии и может быть использовано для получения синтез-газа. Углеводородное сырье, содержащее метан, пропускают через реактор, в верхней части которого необязательно расположен катализатор, имеющий активность при окислении углеводородного сырья, и через слой катализатора парового риформинга. При этом катализаторы находятся в непосредственном контакте со стороной мембраны, проницаемой для кислорода. Выходная область слоя катализатора парового риформинга не имеет контакта с мембраной. Изобретение позволяет получить газ заданного состава и снизить рабочие температуры процесса. 4 ил.
Изобретение относится к способу получения синтез-газа, содержащего в основном Н2 и СО, для производства метанола, аммиака, процессов Фишера-Тропша, для запитки твердооксидных топливных элементов.
В настоящее время большинство известных способов производства синтез-газа базируется на предварительной конверсии природного газа, основным компонентом которого является метан (см. B.C.Арутюнов, О.В.Крылов. Окислительные превращения метана. М.: Наука, 1978, 361 с.).
Синтез-газ в основном получают паровой конверсией метана (ПКМ):
Эта реакция сильно эндотермическая, и для ее протекания необходимо подведение тепла. Для того чтобы избежать выделения сажи на катализаторе, реакцию проводят при большем количестве водяного пара при соотношении Н2О/СН4 больше 2. Это требует дополнительного подведения тепла на парогенерацию, которое также требуется и для поддержания температуры реактора около 900°С. Чтобы поддерживать необходимые тепловые условия для процесса ПКМ дополнительно сжигают еще около 50% природного газа. Реже синтез-газ получают углекислотной конверсией метана (УКМ):
Эта реакция еще более эндотермическая.
Снижение себестоимости синтез-газа достигается за счет окислительной конверсии метана, а именно путем парциального окисления метана (ПОМ):
Для протекания этой реакции не требуется подвода тепла, а значит, дополнительного сжигания углеводородного сырья, кроме того, синтез-газ, получаемый по этому способу, имеет отношение Н2/СО, близкое к 2, и может быть использован при синтезе метанола и/или синтетического жидкого топлива по реакции Фишера-Тропша.
Таким образом, если при получении синтез-газа отношение Н2/СО сильно отличается от 2, это приводит к повышенным энергоматериальным затратам. Например, корректировка состава синтез-газа, получаемого в процессе ПКМ, до соотношения Н2/СО=2 достигается введением диоксида углерода CO2.
Для снижения энергозатрат и получения синтез-газа с отношением Н2/СО, близким к 2, известен способ (Патент RU 2228901, С01В 3/38, 2004), в котором синтез-газ получают в двухстадийном процессе. На первой ступени первой стадии происходит некаталитическое парциальное окисление с температурой 1400-1800°С с получением в синтез-газе неравновесного содержания H2O и CO2 и мольного отношения Н2/СО=1.4-1.8. Во вторую ступень первой стадии подается корректирующая часть CO2 и H2O или H2O и СН4. На выходе из второй ступени первой стадии устанавливается температура 1100-1500°С. На второй стадии происходит конверсия остаточного метана продуктами первой стадии на катализаторе.
К основным недостаткам данного способа производства синтез-газа относятся:
– необходимость большого количества кислорода (O2:СН4=0.76-0.84), получение которого является энергоемким производством, требующим дорогостоящего оборудования;
– высокая температура процессов, проходящих на первой стадии, что требует использования дорогостоящих спецматериалов;
– необходимость дополнительного оборудования, например камеры смешивания и коррекции состава синтез-газа, фильтра из специальных материалов для улавливания сажи, образовавшейся на первой стадии.
Наиболее близким по технической сущности способом к заявляемому техническому решению является способ получения газа, обогащенного водородом и/или оксидом углерода (Патент RU 2248931, МПК С01В 3/26, 2005). Синтез-газ получают путем автотермического реформинга с водяным паром углеводородного сырья, которое пропускают через слой катализатора реформинга с водяным паром и в который подают кислород через мембрану, проницаемую для кислорода, с последующим удалением конечного продукта из этого слоя. Причем способ характеризуется тем, что углеводородное сырье пропускают через слой катализатора, во входной области которого содержится катализатор, имеющий пониженную активность или совсем не имеющий активности в реформинге с водяным паром и имеющий активность в окислении углеводородного сырья. Улучшение характеристик процесса достигается путем контроля градиента температуры в реакторе.
Добавление воды к метану в любом количестве приводит к тому, что отношение Н2/СО становится выше 2. Поэтому такой синтез-газ не может быть прямо использован при синтезе метанола и/или синтетического жидкого топлива по реакции Фишера-Тропша, и требуется дополнительная коррекция его состава.
К недостаткам известного способа производства синтез-газа относятся:
– необходимость использования большого количества водяного пара на проведение автотермического реформинга, что приводит к существенному градиенту температуры по длине мембраны за счет снижения температуры в нижней части мембраны вследствие протекания эндотермических реакций паровой и углекислотной конверсии метана, что в свою очередь приводит к уменьшению удельного потока кислорода через мембрану;
– повышенное отношение Н2/СО>2 (около 2.3) в конвертированном газе после автотермического реформинга, что не позволяет использовать получаемый синтез-газ при синтезе метанола и/или синтетического жидкого топлива без дополнительной коррекции состава.
Таким образом, перед авторами стояла задача разработать способ получения синтез-газа, который наряду с возможностью получения заданного состава газа по основным компонентам Н2 и СО в диапазоне отношений Н2/СО от 1.8 до 2.0 является более технологичным за счет снижения рабочих температур и исключения использования водяного пара.
Поставленная задача решена в предлагаемом способе получения синтез-газа, обогащенного водородом и моноксидом углерода, путем пропускания углеводородного сырья, содержащего метан, через катализатор, верхний слой которого имеет активность при окислении углеводородного сырья, а нижний слой является катализатором парового реформинга, в который подают кислород через проницаемую для кислорода мембрану, при этом катализатор находится в непосредственном контакте со стороной мембраны, проницаемой для кислорода, в котором углеводородное сырье пропускают через катализатор, необязательно имеющий верхний слой, а выходная область слоя катализатора парового реформинга не имеет контакта с мембраной.
Предлагаемый способ позволяет получить синтез-газ, содержащий в основном Н2 и СО, для производства метанола, аммиака, процессов Фишера-Тропша, для запитки твердооксидных топливных элементов. Способ включает две стадии: стадию 1) парциального окисления метана и стадию 2) конверсии остаточного метана продуктами стадии 1) на катализаторе парового реформинга в отсутствие его контакта с проницаемой для кислорода мембраной, то есть в отсутствие кислорода, поступающего через мембрану. Стадию 1) проводят при мольном соотношении кислорода и метана, примерно равным 0.6-0.7, путем каталитического или некаталитического парциального окисления метана кислородом, который подают через мембрану со смешанной кислород-ионной и электронной проводимостью. Затем на стадии 2) дополнительно протекает конверсия метана продуктами стадии 1). Причем углеводородное сырье на стадии 1) пропускают через слой катализатора, находящийся в контакте с мембраной, и во входной области которого необязательно содержится катализатор, имеющий повышенную активность при окислении углеводородного сырья. Остаточный метан и продукты стадии 1) пропускают через слой катализатора парового реформинга, который не находится в контакте с кислородной мембраной.
Кислород в реактор поступает путем его сепарации из воздуха через керамическую мембрану со смешанной кислород-ионной и электронной проводимостью. При использовании керамических мембран из материалов со смешанной проводимостью по ионам кислорода и электронам выделение кислорода из воздуха протекает самопроизвольно за счет разницы парциальных давлений кислорода на мембране. Перенос кислорода внутри мембраны осуществляется не в молекулярной форме, а в виде ионов. Электронейтральность мембраны достигается за счет встречного потока электронов.
Поток кислорода в условиях разницы парциальных давлений (р′ и р”) кислорода с разных сторон мембраны определяется как:
где σион – кислородная проводимость, σэл – электронная проводимость, р(O2) -парциальное давление кислорода в газовой фазе, Т – температура, R – газовая постоянная, F – число Фарадея, L – толщина мембраны.
Градиент давления кислорода в условиях реактора парциального окисления метана задается воздухом и продуктами окисления метана. Из уравнения (4) видно, что поток кислорода через мембрану определяется не только градиентом давления кислорода, но сильно зависит от величины кислородной и электронной проводимости, которые находятся в прямой зависимости от состава материала и температуры. Таким образом, поток кислорода может существенно изменяться (в десятки раз) не только в зависимости от градиента давления кислорода, но и от изменения температуры. Исследования, проведенные авторами, позволили определить условия, при которых температура по длине мембраны остается практически постоянной, что позволяет получить значительный поток кислорода по всей длине мембраны при умеренной температуре поверхности мембраны (850-950°С).
Предлагаемый способ может быть осуществлен следующим образом (см. Фиг.1а и 1б).
Метан (1) и воздух (5) поступают в реактор (2) раздельно при комнатной температуре. В высокотемпературной зоне реактора метан и воздух разделены мембраной (4), выполненной из материала со смешанной кислород-ионной и электронной проводимостью, например, состава La1-XSrXFe1-yCryO3, где 0,4≤x≤0,6; 0≤у≤0,4. Ту часть высокотемпературной зоны реактора, в которую вводят метан, загружают катализатором реформинга с водяным паром (6), например, состава 5-15 мас.% Ni/Al2O3 и необязательно катализатором окисления углеводородного сырья (7) (см. Фиг.1а) состава, например, 5-15 мас.% Mn2O3/Al2O3. В случае отсутствия катализатора окисления углеводородного сырья верхняя часть объема реактора остается свободной (см. Фиг.1б). Кислород поступает в это отделение реактора со стороны (3) мембраны, противоположной стороне, которую омывает воздух. Использование мембранного реактора позволяет объединить процессы выделения кислорода из воздуха и окисления углеводородов в единый процесс. Количество метана, подаваемого в реактор, рассчитывают исходя из удельной кислородопроницаемости мембраны, ее площади, температуры в реакторе. Мембрану, выполненную из материала со смешанной кислород-ионной и электронной проводимостью, располагают в высокотемпературной зоне реактора. В верхней части реактора происходит окисление части подаваемого туда метана кислородом, поступающим через проницаемую для кислорода стенку мембраны, с образованием воды и углекислого газа, смешение которых с метаном препятствует образованию сажи. Кроме того, выделяемое тепло идет на нагрев метана и воздуха, поступающих в реактор при комнатной температуре. Распределение тепла в реакторе таково, что температура мембраны лежит в интервале 850-950°С. Благодаря достаточно равномерному распределению температуры по мембране кислород поступает в реактор по всей ее поверхности. Дополнительно тепло получают в результате окисления метана или продуктов его конверсии (водорода и СО) вблизи поверхности мембраны, это тепло идет на поддержание реакций паровой конверсии метана и углекислотной конверсии метана, которые идут, наряду с реакцией окисления, с поглощением тепла. Таким образом, предлагаемый способ позволяет избежать образования сажи, исключив при этом использование водяного пара.
Практически полная конверсия остаточного метана достигается в объеме катализатора парового реформинга, который не имеет контакта с кислородной мембраной (см. Фиг.1а и 1б).
Предлагаемый способ позволяет существенно снизить рабочие температуры по сравнению с известными процессами. Кроме того, получение синтез-газа с содержанием основных компонентов Н2 и СО в диапазоне отношений Н2/СО от 1.8 до 2.0 не требует дополнительного расхода углеводородного сырья для поддержания рабочих температур в реакторе.
Предлагаемое техническое решение иллюстрируется следующими примерами.
Пример 1. В реактор (см. Фиг.1а) загружают катализатор парового реформинга состава 10 мас.% Ni/Al2O3 в виде гранул так, что верхняя область катализатора примыкает к внутренней стороне проницаемой для кислорода мембраны, выполненной из материала смешанного проводника состава La0,5Sr0,5FeO3, а выходная область катализатора не имеет контакта с мембраной. Верхнюю часть реактора заполняют катализатором окисления углеводородов состава 10 мас.% Mn2O3/Al2O3 в виде гранул, слой катализатора расположен над слоем катализатора парового реформинга и также примыкает к внутренней стороне проницаемой для кислорода мембраны. Температура в средней части мембраны равна 950°С. Поток метана выбирают таким образом, чтобы поступающий через мембрану кислород обеспечивал мольное соотношение кислорода и метана 0,7:1,0. Получаемый синтез-газ направляют далее в конденсатор. На выходе из конденсатора синтез-газ имеет следующий состав, об.%: Н2-61.8%, СО – 34.4%, CO2 – 2.7%, СН4 – 1.1%. Отношение Н2/СО равно 1.8.
Пример 2. В реактор (см. Фиг.1б) загружают катализатор парового реформинга состава 10 мас.% Ni/ Al2O3 в виде гранул так, что верхняя область катализатора примыкает к внутренней стороне проницаемой для кислорода мембраны, выполненной из материала состава La0,5Sr0,5FeO3, а выходная область катализатора не имеет контакта с мембраной. При этом верхняя часть реактора не заполнена катализатором. Температура в средней части мембраны равна 850°С. Поток метана выбирают таким образом, чтобы поступающий через мембрану кислород обеспечивал мольное соотношение кислорода и метана 0,58:1,0. Получаемый синтез-газ направляют далее в конденсатор. На выходе из конденсатора синтез-газ имеет следующий состав, об.%: Н2 – 64.2%, СО – 32.3%, CO2 – 2.1%, CH4 – 1.4%. Отношение Н2/СО равно 1.99.
Нижеприведенные примеры иллюстрируют ухудшение достигаемого технического результата в случае несоблюдения предлагаемых условий получения синтез-газа.
Пример 3. В реактор (см. Фиг.2) загружают катализатор парового реформинга состава 10 мас.% Ni/Al2O3 в виде гранул так, что катализатор примыкает к внутренней стороне проницаемой для кислорода мембраны, выполненной из материала состава La0,5Sr0,5FeO3, и высота слоя катализатора равна длине мембраны. Верхнюю часть реактора заполняют катализатором окисления углеводородов состава 10 мас.% Mn2O3/Al2O3 в виде гранул, слой катализатора расположен над слоем катализатора парового реформинга и также плотно примыкает к внутренней стороне проницаемой для кислорода мембраны. Температура в средней части мембраны равна 900°С. Поток метана выбирают таким образом, чтобы поступающий через мембрану кислород обеспечивал мольное соотношение кислорода и метана 0,71:1,0. Получаемый синтез-газ направляют далее в конденсатор. На выходе из конденсатора синтез-газ имеет следующий состав, об.%: Н2 – 60.0%, СО – 33.2%, CO2 – 4.0%, СН4 – 2.8%. Отношение Н2/СО равно 1.8.
Увеличение содержания в синтез-газе метана указывает, что в условиях примера 3 метан не успевает прореагировать с водой и СO2, которые образуются в процессе окисления, в результате чего конверсия метана понижается.
Пример 4. В реактор (см. Фиг.3) загружают катализатор парового реформинга состава 10 мас.% Ni/Al2O3 в виде гранул на уровне верхнего среза мембраны так, что верхняя область катализатора примыкает к внутренней стороне проницаемой для кислорода мембраны, выполненной из материала смешанного проводника состава La0,5Sr0,5FeO3, а выходная область катализатора не имеет контакта с мембраной. Температура в средней части мембраны равна 900°С. Поток метана выбирают таким образом, чтобы поступающий через мембрану кислород обеспечивал мольное соотношение кислорода и метана 0,68:1,0. Получаемый синтез-газ направляют далее в конденсатор. На выходе из конденсатора синтез-газ имеет следующий состав, об.%: Н2 – 65.5%, СО – 28.5%, CO2 – 5.8%, СН4 – 0.2%. Отношение Н2/СО равно 2.3.
Полученное соотношение Н2/СО, равное 2.3, указывает, что метан частично разложился с образованием водорода и сажи. Действительно, при осмотре реактора в верхней части катализатора присутствует значительное количество сажи.
Таким образом, авторами предлагается технологически простой способ получения синтез-газа, обогащенного водородом и монооксидом углерода, обеспечивающий практически полную конверсию метана, содержащегося в углеводородном сырье. Способ позволяет снизить температуры процесса (850-950°С – в предлагаемом; 1200-1400°С – в известном) и полностью исключить подачу в реактор водяного пара и образование сажи.
Формула изобретения
Способ получения синтез-газа путем пропускания углеводородного сырья, содержащего метан, через реактор, в верхней части которого необязательно расположен катализатор, имеющий активность при окислении углеводородного сырья, и через слой катализатора парового риформинга, при этом катализаторы находятся в непосредственном контакте со стороной мембраны, проницаемой для кислорода, отличающийся тем, что выходная область слоя катализатора парового риформинга не имеет контакта с мембраной.
bankpatentov.ru
Сравнительный анализ: методы получения синтез-газа
Методы ТАР-реактора и ИК-спектроскопии показали, что интенсивность линий СО2 после впуска смеси СО2 + СН4 на Rh/γ-Al2 O3 проходит через максимум, а затем образуется СО32─ , так что механизм с участием реакции Будуара весьма вероятен.
Методы ТАР-реактора и ИК-спектроскопии применили также для исследования конверсии смеси СН4 +СО2 на катализаторах ZrO2 и Pt/ZrO2 . Установлено, что селективность образования СО определяется одним и тем же промежуточным веществом и зависит от содержания атомарного кислорода на каталитической поверхности. Оксид ZrO2 ответственен за активацию СО2 , он частично восстанавливается и реокисляется в условиях реакции. Замещение решеточного кислорода в ZrO2 кислородом из СО2 ─ медленная стадия процесса. После импульса СО2 единственными регистрируемыми частицами, которые остаются достаточно долго на поверхности, являются поверхностные ОН-группы. Очевидно, Оадс после активации СО2 реагирует с метаном. Природа Оадс неясна, это могут быть и реакционноспособные ОН- или СО3 -группы. Метан не диссоциирует на ZrO2 , но диссоциирует на Pt/ZrO2 .
Катализатор Pt/ZrO2 активнее, чем платина на других носителях. Возможно, при этом образуется сплав Pt1─x Zr. Предложена следующая схема механизма конверсии на Pt/ZrO2 :
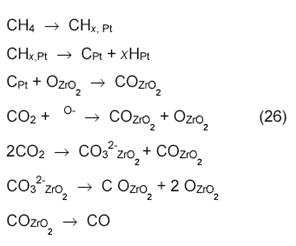
Еще в одной работе с использованием метода ТАР-реактора [18] показано, что не атомы О, а поверхностные ОН-группы реагируют с поверхностными частицами С или СНх :
Однако в большинстве работ ключевыми промежуточными частицами считают адсорбированные атомы кислорода. В работе [13] предполагается корреляция скорости образования СО в смешанной конверсии СН4 +СО2 +Н2 О с прочностью связи металла с Оадс . Такую корреляцию нельзя считать достоверной и даже если она существует, это еще не доказывает, что атомы Оадс являются ключевыми интермедиатами.
Исследование реакции (3) на NiO/MgO при 800 °С (изотопный метод) показало, что в этих условиях на катализаторе присутствуют два типа кислорода: адсорбированный, взаимодействующий с Садс , и решеточный, реагирующий значительно медленнее. Реакция (3) протекает по окислительно-восстановительному механизму.
Окислительно-восстановительный механизм углекислотной конверсии метана на Ni-катализаторах, нанесенных на MgO, принимается и в работах Института химической физики РАН. Окисление Ni и восстановление NiO ускоряется на катализаторе Ni-Cr2 O3 /MgO. Процесс протекает через промежуточное образование шпинели по суммарному стехиометрическому уравнению:
Диссоциация метана происходит, по-видимому, на Ni или NiC, а активация CO2 осуществляется за счет участия кислорода шпинели NiCr2 O4 , вероятно, через промежуточное образование карбоната MgCO3 .
Рассмотрена возможность окислительно-восстановительного механизма углекислотной конверсии метана на системе Pt/CeO2 . Здесь Pt активирует CH4 , а CeO2─x активирует (восстанавливает) CO.
В ряде работ фиксировали образование карбонатов на металлических катализаторах, нанесенных на основные носители. Например, было показано [13], что на Pt/ZrO2 восстановление СО2 происходит через образование карбоната циркония вблизи границы ZrO2 с Pt. Углерод на металле восстанавливает этот карбонат до формиата.
Далее протекают реакции:
Можно предположить, что на разных катализаторах механизм различен: на чистых металлах и на металлах, нанесенных на нейтральные носители типа SiO2 , более вероятна полная диссоциация СН4 и СО2 , а на металлических катализаторах с основными носителями вероятнее промежуточное образование карбоната.
В ИК-спектрах поверхностных соединений, а также после завершения реакции (3), были обнаружены монодентатные и бидентатные комплексные карбонаты, гидрокарбонаты, формиатные комплексы, линейные и мостиковые карбонилы, группы СНх и НСО. Предполагается участие в некоторых механизмах и этих промежуточных веществ. Показано, что атомы Н способствуют разложению карбонатов.
В условиях углекислотной конверсии метана на Pt/TiO2 , Pt/SiO2 , Pt/ZrO2 , Pt/Cr2 O3 преобладающим поверхностным соединением является адсорбированный СО. Обнаружен также СН2 О. По мнению авторов [12], важнейшим интермедиатом на поверхности является СНх О., хотя прямых ИК-спектроскопических подтверждений пока нет. Тем не менее авторы [12,13] считают, что полученные ими данные свидетельствуют в пользу механизма (15) с вероятными стадиями: обратимая диссоциация СН4 с образованием СНх и Н2 , недиссоциативная адсорбция СО2 на носителе, диссоциация адсорбированного СО2 с участием Н на границе металл-носитель, реакция СНх с О (или с ОН) на границе металл-носитель с образованием СНх О. и последующее разложение этого интермедиата с образованием продуктов реакции СО и Н2 .
По ИК-спектроскопическим данным других исследователей [14] на катализаторах Pt/TiO2 и Pt/ZrO2 адсорбция и активация СО2 протекают по механизму обратной конверсии водяного газа (6) на носителе с участием поверхностных ОН-групп. Образуются группы СНх О, а при их разложении ─ СО и Н2 .
Механизм начальных стадий конверсии СН4 +СО2 на никеле, нанесенном на SiO2 , La2 O3 •SiO2 или La2 O3 , изучали импульсным методом отклика [18]. На NiO адсорбция СО2 конкурирует с диссоциацией СН4 . На La2 O3 диоксид углерода адсорбируется с образованием карбонатов и формиатов, которые затем разлагаются с выделением СО и восстановлением кислородных вакансий. Ресурсы О для образования СО из СН4 обеспечиваются за счет перехода кислорода от La2 O3 к Ni. Метан восстанавливает NiO и образует вакансии в La2 O3 .
По данным [10], в случае катализа на NiMgO, промотированном Pt, Pd или Rh, лимитирующей стадией реакции (3) становится диссоциация СО2 или поверхностная реакция СНх + Оадс вместо диссоциации СН4 (для непромотированного NiMgO).
Есть также предположения о промежуточном образовании метильных радикалов. Для выяснения этого механизма на примере конверсии СН4 +СО2 на Rh/SiO2 на катализатор адсорбировали радикалы СН3 , полученные разложением азометана [18]. По ИК-спектрам было установлено, что частицы СН3,адс реагируют с О2 и СО2 из газовой фазы при температуре более 100 °C, поэтому кокс не отлагается на катализаторе. При этой же температуре радикалы СН3,адс разлагаются в вакууме, причем разложение ускоряется под действием СО2 .
Большая часть СН3 адсорбируется на носителе SiO2 , а Rh участвует в дальнейших превращениях. Метан при этой температуре на катализаторе не адсорбируется.
Предполагается протекание следующих реакций:
Существование СН3 -групп в условиях реакции СН4 +СО2 на Ni/SiO2 показано также методами температурно-программируемого восстановления и температурно-программированной реакции (ТПР) [18]. Наблюдалось образование С2 Н6 . Группы СН3 на поверхности могут взаимодействовать с адсорбированными атомами О с образованием групп СНх О. и далее СО и Н2 . Проводилось изучение механизма углеобразования. Установлено, что после диссоциации СО на Ni атомы углерода мигрируют в подповерхностный слой никеля, индуцируя его реконструкцию, удлинение связей Ni─Ni и последующее более глубокое проникновение в металлический кристаллит вплоть до отложения углерода на обратной поверхности кристаллита. Электронно-микроскопическое исследование показало разные свойства углерода, образовавшегося по реакциям (8) и (9). В случае смеси СО+СО2 углерод капсулируется, а из смеси СН4 +Н2 формируются графитовые пластинки и нити. Отсюда следует вывод, что вначале образуется С из СО/СО2 , а вторичный углерод осаждается при диссоциации метана.
Методом температурно-программированного гидрирования после завершения реакции на Ni/MgO были обнаружены две формы углерода: аморфный α-С, гидрирующийся при 270─420 °С и β-С, гидрирующийся выше 600 °С, по-видимому, это графит. Углерод образуется преимущественно на малых частицах никеля.
Проведение температурно-программированного процесса взаимодействия СО и СН4 на катализаторах Ni0,03 Mg0,97 O, 3%Ni/MgO и 3%Ni/Al2 O3 позволило выявить, что углерод образуется как при диспропорционировании СО, так и при диссоциации метана [18]. При
этом происходит быстрое окисление СНх на Ni под действием СО2 . На всех трех изученных катализаторах температура пика взаимодействия С+СО2 одна и та же ─ 550 °С), что указывает на отсутствие взаимодействия между катализатором и осажденным углеродом. На восстановленном катализаторе Ni0,03 Mg0,97 O реакция между СО2 и Ni протекает при температуре на 40 °С ниже, чем на остальных катализаторах. Авторы [18]
приходят к выводу, что возможны два маршрута активации СО2 :
1) на носителе вблизи границы с Ni и 2) на частицах Ni.
Первый маршрут более благоприятен для ингибирования углеобразования.
mirznanii.com
Способ получения синтез-газа при горении и устройство для его осуществления
Изобретения относятся к области переработки углеводородного сырья, а конкретно к окислительной конверсии углеводородных газов в синтез-газ. Способ получения синтез-газа осуществляют в проточном двухкамерном реакторе в турбулентном режиме при горении смеси углеводородного сырья и окислителя. Дополнительно к указанной смеси в проточный реактор подают перегретый водяной пар в количестве 5-20 мас.% по отношению к массе поданного углерода в виде углеводородного сырья. Производят воспламенение трехкомпонентной смеси в камере сгорания струей горячего газа из внешнего источника, давление в котором при воспламенении превышает давление в первой камере. Продукты сгорания из первой камеры реактора через сопло с критическим перепадом давления направляют во вторую камеру и продолжают процесс горения до содержания кислорода в продуктах горения не более 0,3 об.%. Процесс проводят в реакторе горения, который выполнен из двух цилиндрических соосно расположенных камер, между которыми размещено охлаждаемое сопло с сечением, обеспечивающим критический перепад давления между камерами. На входе в первую камеру установлен блок форсунок для подачи компонентов рабочей смеси. В первой камере расположен турбулизатор. На боковой поверхности первой камеры расположено одно или несколько отверстий для ввода струи горячего газа из внешнего источника, давление в котором при воспламенении превышает давление в первой камере, а объем второй камеры превышает объем первой. Изобретения позволяют получить синтез-газ, в котором отношение H2/CO≈2.0, остаточное содержание кислорода не превышает 0,3 об.%, содержание сажи не превышает следовых количеств. 2 н. и 7 з.п. ф-лы, 2 ил.
Изобретение относится к области переработки углеводородного сырья, а конкретно к окислительной конверсии углеводородных газов в синтез-газ.
Известны различные способы получения синтез-газа из углеводородного сырья, в том числе парциальным окислением метана кислородом
CH4+0,5O2=СО+2Н2
Известно изобретение по патенту СССР №1831468, МКИ 5 С01В 3/38, “Способ получения синтез-газа из углеводородного сырья”, которое включает смешение углеводородного сырья и окислителя – кислорода или кислородсодержащего газа или пара и конверсию полученной смеси в присутствии монолитного катализатора при температуре, которая в реакционной зоне не менее чем на 93°С ниже точки самовоспламенения смеси, а скорость ввода смеси в реакционную зону превышает скорость процесса проскока пламени. Известный способ требует использования высокоселективного катализатора. Основным недостатком изобретения по патенту СССР №1831468 является высокая стоимость катализатора, возможность разрушения катализатора за счет локальных перегревов, возможность образования сажи.
Известны также способ и устройство смешанного риформинга СН4+O2+Н2О в реакторе с псевдоожиженным слоем катализатора, по патенту США №5.980.782, МКИ 6 С01В 3/24, 1999 г., в котором газообразные компоненты предварительно подогревают и инжектируют в зону реакции за период, меньший, чем время самовоспламенения, т.е. меньше чем 9 мс, со скоростью от 8 до 333 м/с. Полученный синтез-газ охлаждают и направляют для дальнейшей переработки.
Основным недостатком изобретения по патенту США №5.980.782 является необходимость использования катализатора.
Известен способ получения синтез-газа по патенту РФ №2096313, МКИ 6 С01В 3/36, в котором исключается применение катализаторов. Известный способ осуществляют в следующем порядке:
– предварительно смешивают углеводородное сырье с воздухом до α=0.5-0,8;
– нагревают полученную смесь до температуры 200-450°С;
– подают нагретую смесь в объем цилиндра двигателя внутреннего сгорания компрессионного типа при движении поршня к нижней мертвой точке;
– при сжатии смеси в объеме цилиндра движением поршня к верхней мертвой точке до ее самовоспламенения и получения температуры 1300-2300°С на период 10-2-10-3 осуществляют парциальное окисление углеводородного сырья;
– далее охлаждают полученные продукты процесса окисления, расширяя их при движении поршня к нижней мертвой точке;
– при движении поршня к верхней мертвой точке выводят продукты процесса, содержащие синтез-газ.
Описанный цикл повторяют с частотой, превышающей 350 мин-1. Основным недостатком способа по патенту РФ №2096313 является отсутствие непрерывности процесса получения синтез-газа из-за его цикличности, что снижает производительность процесса.
Известно устройство для получения синтез-газа по патенту РФ №2096313, МКИ 6 С01В 3/36, с помощью которого осуществляют описанный выше способ получения синтез-газа. Устройство основано на двигателе внутреннего сгорания компрессионного типа, цилиндр которого представляет собой замкнутый реакционный объем, в котором помещен поршень. Впускной и выпускной клапаны размещены в зоне верхней мертвой точки цилиндра, при этом впускной клапан связан со смесителем окислителя и углеводородного сырья и устройством их подогрева, а выпускной клапан связан с приемником продуктов окисления. Поршень цилиндра через кривошипно-шатунный механизм связан с приводом.
Описанное устройство для получения синтез-газа работает циклично с частотой движения поршня в цилиндре не менее 350 мин-1. Меньшая частота цикла приводит к относительно меньшей скорости сжатия, которая не обеспечивает самовоспламенения рабочей смеси.
Основным недостатком известного устройства для получения синтез-газа по патенту РФ №2096313 является невозможность обеспечить непрерывность процесса образования синтез-газа, что снижает производительность процесса его получения.
Известен также способ получения синтез-газа по патенту РФ №2120913, МКИ 6 С01В 3/36. Способ получения синтез-газа включает парциальное окисление углеводородного сырья кислородом воздуха в объеме цилиндра двигателя внутреннего сгорания при соотношении количества кислорода к количеству углеводородного сырья α=0,4-0,5. При этом в момент положения поршня в верхней мертвой точке часть смеси углеводородного сырья с воздухом при отношении количества кислорода к количеству углеводородного сырья α=0.8-1.2 в количестве 5-10% от объема исходной смеси изолированно от нее подвергают воспламенению и глубокому окислению. Далее смешивают продукты глубокого окисления с исходной смесью в рабочем объеме цилиндра и воспламеняют ее. Расширяют и охлаждают продукты процесса при движении поршня к нижней мертвой точке, выводят продукты процесса, содержащие синтез-газ, из реакционной зоны при движении поршня к верхней мертвой точке. Затем цикл повторяют. Благодаря тому что в известном способе часть углеводородного сырья с воздухом при α=0.8-1.2 в количестве 5-10% объема исходной смеси при положении поршня в верхней мертвой точке подвергают предварительному воспламенению и глубокому окислению изолированно от основного объема смеси, а затем эту часть впрыскивают высокоэнергетичной струей в основной объем смеси, в рабочем объеме цилиндра исходная смесь подвергается интенсивному перемешиванию и воспламенению, достигается повышение производительности данного способа получения синтез-газа. Основным недостатком известного способа получения синтез-газа по патенту РФ №2120913 является отсутствие непрерывности процесса конверсии из-за его цикличности, что снижает производительность.
Известна установка для получения синтез-газа по патенту РФ №2120913, МКИ 6 С01В 3/36, с помощью которой осуществляют описанный выше способ получения синтез-газа. Установка содержит основанный на двигателе внутреннего сгорания химический реактор сжатия, включающий цилиндр и камеру предварительного воспламенения. В цилиндре размещены поршень и впускной клапан, через который в цилиндр и камеру предварительного воспламенения подают смесь углеводородного сырья с воздухом. На цилиндре установлен выпускной клапан, который предназначен для вывода продуктов процесса. Камера предварительного воспламенения имеет отдельный клапан, через который подают воздух для достижения в камере значения α=0.8-1.2. Объем предварительной камеры воспламенения составляет 5% от объема цилиндра при положении поршня в верхней мертвой точке.
В процессе получения синтез-газа при положении поршня вблизи верхней мертвой точки воздушно-углеводородную смесь указанного состава в камере предварительного воспламенения подвергают воспламенению от искры. Далее высокоэнергетичная струя сильно турбулизованного газа вбрасывается со скоростью около 103 м/с в рабочий объем цилиндра в течение 10-3-10-2 с. В рабочем объеме цилиндра рабочая смесь подвергается смешению с продуктами глубокого окисления и воспламенению, происходит процесс парциального окисления. При движении поршня в цилиндре к нижней мертвой точке происходит расширение продуктов процесса, их охлаждение и закалка. При последующем движении поршня к верхней мертвой точке продукты процесса выводят из цилиндра через выпускной клапан. Подачу в цилиндр и в камеру предварительного воспламенения свежей рабочей смеси производят при движении поршня к нижней мертвой точке и открытии впускных клапанов. Так циклично работает установка и осуществляется способ получения синтез-газа.
Основным недостатком установки для получения синтез-газа по патенту РФ №2120913 является отсутствие возможности достижении непрерывного процесса конверсии углеводородного сырья вследствие его цикличности, что снижает производительность получения синтез-газа, кроме этого, описанная установка недостаточно надежна и долговечна, так как ее работа связана с циклическим движением основных деталей, таких как поршень, кривошип и клапаны.
Известен также способ получения синтез-газа по патенту РФ №2191743, МКИ 7 С01В 3/34, В01J 7/00, принятый в качестве ближайшего аналога заявляемого способа. Способ получения синтез-газа включает смешивание углеводородного сырья с воздухом в соотношении, соответствующем коэффициенту избытка окислителя α меньше 1, принудительное воспламенение воздушно-углеводородной смеси и парциальное окисление углеводородного сырья кислородом воздуха в реакционной зоне, охлаждение с последующим выводом продуктов процесса, содержащих синтез-газ, и введение новой порции углеводородного сырья и воздуха, при этом подогрев углеводородного сырья и воздуха осуществляют при повышенных давлении и температуре, на 50-100°С ниже температуры самовоспламенения их смеси, процесс парциального окисления углеводородного сырья проводят в проточной камере горения, при этом принудительное воспламенение проводят при коэффициенте избытка окислителя α=0,6-0,7, и после прогрева проточной камеры горения отношение кислорода к углеводородному сырью доводят до уровня, соответствующего значению α=0,30-0,56. При этом процесс охлаждения продуктов парциального окисления, выходящих из реакционной зоны, проводят со скоростью не ниже 3000°С/с.
Известно устройство для получения синтез-газа по патенту РФ №2191743, МКИ 7 С01В 3/34, В01J 7/00, принятое в качестве ближайшего аналога устройства для осуществления заявляемого способа. Устройство для получения синтез-газа включает камеру парциального окисления углеводородного сырья кислородом воздуха, смеситель, систему расширения и охлаждения продуктов парциального окисления и вывода синтез-газа. Также оно снабжено системой предварительного подогрева углеводородного сырья и воздуха, регулятором расхода углеводородного сырья. При этом камера парциального окисления углеводородного сырья содержит средство воспламенения и выполнена в виде проточной камеры горения, ко входу которой через антипроскоковую решетку пристыкован смеситель, а к смесителю подключены подводящая труба углеводородного сырья и подводящая труба воздуха, обе указанные подводящие трубы охвачены с зазором рекуператорным патрубком, один конец которого пристыкован к выходу из проточной камеры горения, а другой, открытый, конец сообщается с полостью теплообменника, который образован оболочкой, ограничивающей полость вокруг рекуператорного патрубка. Кроме того, в полости теплообменника расположены трубчатый нагреватель углеводородного сырья и трубчатый нагреватель воздуха. При этом к одному концу трубчатого нагревателя углеводородного сырья подключен регулятор расхода углеводородного сырья, а другой конец через упомянутую подводящую трубу связан со смесителем. Один конец трубчатого нагревателя воздуха подключен к источнику воздуха, а другой конец через подводящую трубу связан со смесителем. Вместе с тем теплообменник снабжен штуцером для вывода из его полости синтез-газа.
Изобретение позволяет повысить производительность процесса.
Основным недостатком способа получения синтез-газа и устройства для его осуществления по патенту РФ №2191743 является осуществление процесса горения в режиме, близком к ламинарному.
Так, при ламинарном режиме горения для получения состава продуктов, близкого к термодинамически равновесному (в том числе для выгорания кислорода), необходимо большое время пребывания в зоне реакции, что приводит к заметному образованию конденсированных продуктов уплотнения углерода, в том числе сажи, и получению основных продуктов процесса водорода и оксида углерода в соотношении ˜1,6, что не соответствует требованиям к синтез-газу для ряда каталитических процессов его переработки, например, в метанол или по методу Фишера-Тропша.
К недостатку также относится описанный в патенте двухстадийный способ воспламенения богатой метано-воздушной смеси, согласно которому сначала подают метано-воздушные смеси с α=0,6-0,7, воспламеняют их от искры, и после прогрева реактора для получения синтез-газа подают богатую метано-воздушную смесь с α=0,30-0,56.
Однако в случае внештатной ситуации, например срыва пламени, искровой поджиг богатых метано-воздушных смесей становится невозможным и процесс надо начинать сначала, т.е. надо вернуться к режиму пуска.
Кроме того, при таком поджиге в продуктах процесса образуется повышенное количество Н2О и CO2, нежелательных при каталитической переработке, например синтез Фишера-Тропша в присутствии железного катализатора.
Предлагаемое изобретение направлено на устранение отмеченных выше недостатков прототипа.
Согласно предлагаемому изобретению поставленная задача решается тем, что в способе получения синтез-газа в проточном реакторе при горении смеси углеводородного сырья и окислителя, взятых в отношении, соответствующем коэффициенту избытка окислителя менее 1. Процесс горения проводят в турбулентном режиме в двухкамерном реакторе, дополнительно к указанной смеси в проточный реактор подают перегретый водяной пар в количестве 5-20 мас.% по отношению к массе поданного углерода в виде углеводородного сырья, что обеспечивает объемное отношение в продуктах процесса Н2/СО≈2,0 и объемное отношение СО/CO2 свыше 4,0, производят воспламенение трехкомпонентной смеси в камере сгорания струей горячего газа из внешнего источника, давление в котором при воспламенении превышает давление в первой камере, при этом продукты сгорания из первой камеры реактора через сопло с критическим перепадом давления направляют во вторую камеру и продолжают процесс горения до содержания кислорода в продуктах горения не более 0,3 об.%.
В качестве углеводородного сырья используют индивидуальные углеводороды алканового ряда, в частности метан, и/или их смеси, очищенные от примесей сернистых соединений.
В качестве окислителя в способе используют газообразный молекулярный кислород и/или его смесь с инертными компонентами, например воздух или обогащенный кислородом воздух.
Поток струи горячего газа от внешнего источника составляет 1-7 об.% по отношению к основному потоку газа, а температура потока струи превышает температуру основного потока газа, причем струю горячего газа подают перпендикулярно оси основного потока газа. Состав газа во внешнем источнике выбирается близким к стехиометрическому для его воспламенения посредством искры от свечи зажигания.
Внешний источник горячего газа выполняет функции поджига основного потока газа и его турбулизации, работая по мере необходимости в режиме дежурного факела.
Время пребывания рабочей смеси в реакторе выбирают в пределах 0,01-1 с.
Предлагаемый способ позволяет получить синтез-газ, в котором отношение основных продуктов процесса Н2/СО≈2.0, остаточное содержание кислорода не превышает 0,3 об.%, содержание сажи не превышает следовых количеств.
Для осуществления способа получения синтез-газа предложено устройство, обеспечивающее проведение процесса горения в турбулентном режиме при стабильной работе реактора.
В устройстве для получения синтез-газа при горении при повышенном давлении реактор выполнен по типу модельного жидкостного ракетного двигателя и состоит из двух цилиндрических соосно расположенных камер, между которыми размещено охлаждаемое сопло с сечением, обеспечивающим критический перепад давления между камерами, что позволяет за критическим сечением сопла организовать зону внезапного расширения, которая защищает дальнейший процесс от случайных выбросов кислорода в продукты реакции, на входе в первую камеру установлен блок форсунок для подачи компонентов рабочей смеси, в первой камере расположен турбулизатор, на боковой поверхности первой камеры расположено одно или несколько отверстий для ввода струи горячего газа из внешнего источника, давление в котором при воспламенении превышает давление в первой камере, а во второй камере, объем которой в несколько раз превышает объем первой, расположена система подогрева компонентов смеси, подаваемых на вход первой камеры. Отверстия расположены в плоскости, перпендикулярной оси реактора под углом 360°/n, где n=1-3.
Устройство позволяет обеспечить протекание процесса в турбулентном режиме и, как следствие, увеличить скорость распространения фронта пламени, что способствует большей термодинамической завершенности процесса.
Общий вид устройства показан на фиг.1, а его разрез – на фиг.2.
Устройство для получения синтез-газа содержит форсуночную головку (1) с двух- или однокомпонентными форсунками, первую камеру (2), охлаждаемое сопло (3), на выходе которого создается сверхкритический перепад давления, и вторую камеру (4). На боковой поверхности первой камеры расположены отверстия для ввода продуктов сгорания из микроЖРД (5), в которых установлены электросвечи (6). Турбулизатор газового потока (7) размещен внутри камеры сгорания ближе к ее середине и может быть выполнен в виде жаропрочной или охлаждаемой решетки. За критическим сечением сопла установлена вторая камера (4), объем которой в несколько раз больше объема первой камеры. Внутри второй камеры размещены теплообменники (8), для подогрева компонентов рабочей смеси перед их подачей в первую камеру.
Предлагаемый способ и работа устройства иллюстрируются следующими примерами.
Пример 1.
После стандартной сероочистки метана исходные компоненты (метан, водяной пар и кислород) под давлением, превосходящим давление в первой камере, нагревают в теплообменниках (8) и подают в форсуночную головку (1) проточного реактора. Воспламенение смеси компонентов в первой камере (2) выполняют при помощи струи горячих продуктов сгорания из жидкостного ракетного двигателя малой тяги (микроЖРД) (5), производительность которого составляет 1-7 об.% от основного потока газа. Смесь горючего и окислителя, подаваемую в микроЖРД, воспламеняют при помощи свечи зажигания (6). Турбулизатор (7) выполнен в виде решетки, конструкция которой позволяет обеспечить скорость потока 35-70 м/с, что в аппарате данной конструкции соответствует числам Рейнольдса, характерным для развитой турбулентности.
В данном эксперименте коэффициент избытка окислителя α метано-кислородной смеси в первой камере составляет 0,35; перегретый водяной пар подают в количестве 5 мас.% по отношению к массе поданного углерода. В микроЖРД подают смесь метана с кислородом, коэффициент избытка окислителя которой составляет 0,8. Расход метано-кислородной смеси через микроЖРД составляет 3 об.% по отношению к расходу газа через блок форсунок (1). Горячую смесь продуктов через охлаждаемое сопло (3) с сечением, обеспечивающим критический перепад давления между камерами, направляют во вторую камеру (4), где происходит за счет внезапного расширения дальнейшее превращение остатков исходных компонентов.
Проводят парциальное окисление метана при давлении в первой камере 54 атм, начальной температуре 570 К и максимальной температуре в реакторе 1600 К. Полученный синтез-газ при поддержании примерно постоянного давления охлаждают с целью выделения из него паров воды до уровня, не превышающего 0,5 об.%. Полученный сухой синтез-газ имеет состав (мол.%): СО – 33,6, Н2 – 61,9, СО2 – 3,4, CH4 – 0,4; O2 – 0,2, сажа – следы, водяной пар – 0,5. В полученном синтез-газе отношение Н2/СО=1,84; отношение СО/CO2=9,9.
Пример 2.
Условия, как в примере 1, за исключением коэффициента избытка окислителя α=0,39 и количества перегретого водяного пара – 20% от массы поданного углерода.
Проводят парциальное окисление метана при давлении в первой камере 54 атм, начальной температуре 520 К и максимальной температуре в реакторе около 1550 К. Полученный синтез-газ при поддержании примерно постоянного давления охлаждают с целью выделения из него паров воды до уровня, не превышающего 0.5 об.%. Полученный сухой синтез-газ имеет состав (мол.%): СО – 32,1, Н2 – 61,4, СО2 – 4,4, СН4 – 1,4; О2 – 0,2, сажа – следы, водяной пар – 0,5. В полученном синтез-газе отношение Н2/СО=1,9; отношение СО/СО2=7,3.
Пример 3.
Условия, как в примере 1, за исключением коэффициента избытка окислителя α=0,36 и количества перегретого водяного пара – 10% от массы поданного углерода.
Проводят парциальное окисление метана при давлении в первой камере 54 атм, начальной температуре 570 К и максимальной температуре в реакторе около 1550 К. Полученный синтез-газ при поддержании примерно постоянного давления охлаждают с целью выделения из него паров воды до уровня, не превышающего 0,5 об.%. Полученный сухой синтез-газ имеет состав (мол.%): СО – 32,0, H2 – 62,0, CO2 – 4,1, CH4 – 1,3; O2 – 0,1, сажа – отсутствует, водяной пар – 0,5. В полученном синтез-газе отношение Н2/СО=1,94; отношение СО/CO2=7,8.
Пример 4.
Условия, как в примере 2, за исключением давления в первой камере устройства, равного 40 атм.
Проводят парциальное окисление метана при начальной температуре 520 К и максимальной температуре в реакторе около 1550 К. Полученный синтез-газ при поддержании примерно постоянного давления охлаждают с целью выделения из него паров воды до уровня, не превышающего 0,5 об.%. Полученный сухой синтез-газ имеет состав (мол.%): СО – 32,1, Н2 – 61,3, CO2 – 4,4, СН4 – 1,5; О2 – 0,2, сажа – следы, водяной пар – 0,5. В полученном синтез-газе отношение Н2/СО=1,9; отношение СО/CO2=7,3.
Пример 5.
Аппаратурное оформление, как в примере 1. Исходное сырье – метан, перегретый водяной пар, окислитель – воздух. Коэффициент избытка окислителя α=0,42, количество перегретого водяного пара – 5% от массы поданного углерода.
Проводят парциальное окисление метана при давлении 50 атм, начальной температуре 570 К и максимальной температуре в реакторе около 1300 К. Полученный синтез-газ при поддержании примерно постоянного давления охлаждают с целью выделения из него паров воды до уровня, не превышающего 0,5 об.%. Полученный сухой синтез-газ имеет состав (мол.%): СО – 13,1, H2 – 24,0, CO2 – 2,5, CH4 – 2,7; O2 – 0,27, сажа + потери – 1,0; водяной пар – 0,5, N2 – до 100. В полученном синтез-газе отношение Н2/СО=1,83; отношение СО/CO2=5,2.
Пример 6
Условия, как в примере 5, за исключением коэффициента избытка окислителя α=0,5 и количества перегретого водяного пара – 15% от массы поданного углерода.
Проводят парциальное окисление метана при давлении 50 атм, начальной температуре 570 К и максимальной температуре в реакторе около 1400 К. Полученный синтез-газ при поддержании примерно постоянного давления охлаждают с целью выделения из него паров воды до уровня, не превышающего 0,5 об.%. Полученный сухой синтез-газ имеет состав (мол.%): СО – 12,8, Н2 – 22,5, CO2 – 3,2, СН4 – 2,5; О2 – 0,25; сажа + потери 0,5; водяной пар – 0,5, N2 – до 100. В полученном синтез-газе отношение Н2/СО=1,76; отношение СО/СО2=4,0.
Пример 7.
Аппаратурное оформление, как в примере 1. Исходное сырье – метан, перегретый водяной пар, окислитель – воздух, обогащенный кислородом (мол.%: О2 – 37, N2 – 63). Коэффициент избытка окислителя α=0,42, количество перегретого водяного пара – 10 мас.% по отношению к массе поданного углерода.
Проводят парциальное окисление метана при давлении 50 атм, начальной температуре 570 К и максимальной температуре в реакторе около 1500 К. Полученный синтез-газ при поддержании примерно постоянного давления охлаждают с целью выделения из него паров воды до уровня, не превышающего 0,5 об.%. Полученный сухой синтез-газ имел состав (мол.%): СО – 24,0, Н2 – 45,6, CO2 – 3,3, СН4 – 2,7; О2 – 0,2; сажа – следы, водяной пар – 0,5, N2 – до 100. В полученном синтез-газе отношение Н2/СО=1,9; отношение СО/CO2=7,3.
Пример 8.
Условия, как в примере 7, за исключением коэффициента избытка окислителя α=0,45 и количества перегретого водяного пара – 15% от массы поданного углерода.
Проводят парциальное окисление метана при давлении 50 атм, начальной температуре 550 К и максимальной температуре в реакторе около 1450 К. Полученный синтез-газ при поддержании примерно постоянного давления охлаждают с целью выделения из него паров воды до уровня, не превышающего 0,5 об.%. Полученный сухой синтез-газ имел состав (мол.%): СО – 23,5, Н2 – 44,8, CO2 – 3,6, СН4 – 2,9; O2 – 0,2; сажа – 0,4; водяной пар – 0,5, N2 – до 100. В полученном синтез-газе отношение Н2/СО=1,9; отношение СО/CO2=6,5.
Пример 9.
Условия, как в примере 1, за исключением состава исходного сырья. В качестве исходного сырья используют углеводородный газ состава (об.%): СН4 – 86,9, C2H6 – 10,1, C2H8 – 3 и перегретый водяной пар в количестве 10% от массы поданного углерода. После осушки был получен синтез-газ состава: СО – 34,9%, Н2 – 60,2%, CO2 – 3,5%, содержание остаточного метана составляет 0,75%; О2 – 0,15%, сажа – следы, водяной пар – 0,5%. В полученном синтез-газе отношение Н2/СО=1,72; отношение СО/СО2=9.9.
Пример 10.
Условия, как в примере 9, за исключением коэффициента избытка окислителя α=0,39 и количества перегретого водяного пара – 20% от массы поданного углерода. После осушки был получен синтез-газ состава: СО – 34,3%, Н2 – 60,0%, CO2 – 3,8%, содержание остаточного метана составляет 1,2%; О2 – 0,20%, сажа – следы, водяной пар – 0,5%. В полученном синтез-газе отношение Н2/СО=1,75; отношение СО/CO2=9,0.
Пример 11.
Условия, как в примере 10, за исключением состава исходного сырья. Окислитель – воздух, коэффициент избытка окислителя 0,45. Подают 8% водяного пара от массы поданного углерода. Состав сухого синтез-газа: СО – 13,3%, H2 – 23,3%, CO2 – 2,9%, содержание остаточного метана составляет 2,4%, O2 – 0,27%, сажа – 0,6%, водяной пар – 0,5%, азот до 100%. В полученном синтез-газе отношение Н2/СО=1,75; отношение СО/СО2=4,6.
1. Способ получения синтез-газа в проточном реакторе при горении смеси углеводородного сырья и окислителя, взятых в соотношении, соответствующем коэффициенту избытка окислителя менее 1, отличающийся тем, что процесс горения проводят в турбулентном режиме в двухкамерном реакторе, дополнительно к указанной смеси в проточный реактор подают перегретый водяной пар в количестве 5-20 мас.% по отношению к массе поданного углерода в виде углеводородного сырья, производят воспламенение трехкомпонентной смеси в камере сгорания струей горячего газа из внешнего источника, давление в котором при воспламенении превышает давление в первой камере, при этом продукты сгорания из первой камеры реактора через сопло с критическим перепадом давления направляют во вторую камеру и продолжают процесс горения до содержания кислорода в продуктах горения не более 0,3 об.%.
2. Способ по п.1, отличающийся тем, что в качестве углеводородного сырья используют индивидуальные углеводороды алканового ряда, в частности метан, и/или их смеси, очищенные от примесей сернистых соединений.
3. Способ по п.1, отличающийся тем, что в качестве окислителя используют газообразный молекулярный кислород и/или его смесь с инертными компонентами.
4. Способ по п.1, отличающийся тем, что при подаче из внешнего источника горячего газа его поток составляет 1-7 об.% по отношению к основному потоку газа, а температура превышает температуру основного потока газа.
5. Способ по пп.1-4, отличающийся тем, что струю горячего газа подают перпендикулярно оси основного потока газа.
6. Способ по п.1, отличающийся тем, что время пребывания смеси в реакторе выбирают в пределах 0,01-1 с.
7. Проточное устройство для получения синтез-газа при горении при повышенном давлении, отличающееся тем, что реактор горения выполнен из двух цилиндрических соосно расположенных камер, между которыми размещено охлаждаемое сопло с сечением, обеспечивающим критический перепад давления между камерами, на входе в первую камеру установлен блок форсунок для подачи компонентов рабочей смеси, в первой камере расположен турбулизатор, на боковой поверхности первой камеры расположено одно или несколько отверстий для ввода струи горячего газа из внешнего источника, давление в котором при воспламенении превышает давление в первой камере, а объем второй камеры превышает объем первой.
8. Устройство по п.7, отличающееся тем, что отверстия для ввода струи горячего газа от внешнего источника расположены в плоскости, перпендикулярной оси реактора под углом 360°/n, где n=1-3.
9. Устройство по п.7, отличающееся тем, что вторая камера снабжена системой подогрева компонентов смеси, подаваемых на вход первой камеры.
www.findpatent.ru
Добавить комментарий