Синтез газ – Использование – синтез-газ – Большая Энциклопедия Нефти и Газа, статья, страница 1
способы получения, производство, состав и применение
История человечества знает довольно много примеров, когда в силу необходимости рождались кардинально новые подходы к решению существующих жизненно важных проблем. Например, в Германии в промежуток между первой и второй мировыми войнами, лишенной доступа к крупным нефтяным источникам, назревал серьезный дефицит топлива, которое было необходимо для функционирования гражданской и военной техники.
Располагая существенными запасами ископаемого угля, Германия начала искать пути его трансформации в жидкое топливо, пригодное для двигателей внутреннего сгорания. Эта проблему удалось решить благодаря усилиям превосходных химиков, из которых отдельного упоминания заслуживает Франц Фишер, директор Института кайзера Вильгельма по исследованию угля.
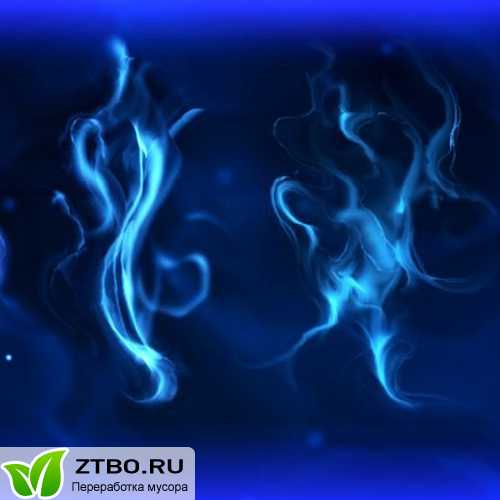
В 1926 году Ф. Фишер и Г. Тропш опубликовали работу “О прямом синтезе нефтяных углеводородов при нормальном давлении”, где сообщалось, что при восстановлении монооксида углерода водородом при нормальном атмосферном давлении в присутствии катализаторов при температуре в 270 градусов по шкале Цельсия можно получить жидкие и твердые гомологи метана.
Так на свет появился знаменитый способ синтеза углеводородов из монооксида углерода, называемый с тех пор методом Фишера-Тропша. Благодаря данному методу смесь водорода и угарного газа в различных соотношениях может легко быть получена как из каменного угля, так и из любого другого сырья, содержащего углерод. Полученную в результате данного процесса смесь газов начали называть синтез-газом.
Состав синтез-газа
Как мы уже упомянули выше, в состав синтез-газа входят такие вещества как CO и h3. В зависимости от метода получения синтез-газа соотношение CO:Н2 в нем варьируется от 1:1 до 1:3. В прямой зависимости от применяемого сырья и метода его соотношение компонентов в синтез-газе изменяется в широких пределах. Как правило, процентное содержание веществ в сыром неочищенном синтез-газе следующее:
- CO – 15-18%
- h3 – 38-40%
- Ch5 – 9-11%
- CO2 – 30-32%
Стоит заметить, что данное соотношение является весьма приблизительным, поскольку повышением температуры в процессе синтеза можно увеличить количество СО, а увеличив давление можно повысить содержание Н2 и СН4.
Также, помимо данных веществ синтез-газ может содержать и другие вещества – инертные газы (N2) и серосодержащие соединения (h3S), если исходное сырье содержало серу. От не нужного присутствия в синтез-газе таких веществ как углекислый газ и сера избавляются путем очистки селективными растворителями.
Способы получения синтез-газа
Первым известным человечеству способом получения синтез-газа была газификация каменного угля. Данный способ был осуществлен в Англии еще в 30-е годы XIX века, и во многих странах мира до 50-х годов XX века. Впоследствии данная методика была вытеснена методами, основанными на использовании нефти и природного газа. Однако в связи с существенным сокращением мировых нефтяных ресурсов, значение процесса газификации каменного угля снова стало возрастать. К тому же, благодаря такому необходимому процессу как переработка ТБО, ученые научились добывать синтез-газ из новых, нетрадиционных источников.
Сегодня существуют три основных метода получения синтез-газа.
1. Газификация угля. Данный процесс основан на взаимодействии каменного угля с водяным паром и происходит по формуле:
C + h3O → h3 + CO.
Данная реакция является эндотермической, и равновесие при температуре 900-1000 по шкале Цельсия сдвигается вправо. Разработаны различные технологические процессы, использующие парокислородное дутье, благодаря которому наряду с упомянутой реакцией параллельно протекает экзотермическая реакция сгорания угля, которая обеспечивает необходимый тепловой баланс. Ее формула:
C + 1/2O2 → CO.
2. Конверсия метана. Данная реакция взаимодействия водяного пара и метана проводится при повышенной температуре (800-900 градусов) и давлении при присутствии никелевых катализаторов (Ni-Al2O3). Формула данного процесса:
Ch5 + h3O → CO + 3h3 .
Также в качестве сырья в данном способе вместо метана можно использовать любое сырье, содержащее углеводород.
3. Парциальное окисление углеводородов. Данный процесс, происходящий при температурах выше 1300 градусов заключается в термическом окислении углеводородов. Формула данной реакции:
Cnh3n + 2 + 1/2nO2 → nCO + (n + 1)h3 .
Данный способ применим к любому сырью, содержащему углеводороды но наиболее часто используется высококипящая фракция нефти – мазут.
Производство синтез-газа
Сегодня производство синтез-газа постоянно совершенствуется, поскольку востребованность данного сырья неизменно растет с каждым годом. В настоящее время учеными разрабатываются проекты подземной газификации угля, то есть планируется, что получение синтез-газа будет происходить непосредственно в пласте угля глубоко под землей. Интересен тот факт, что подобную идею уже высказывал известнейший русский ученый Д.И. Менделеев, причем более 150 лет назад.
Также благодаря современным разработкам сегодня синтез-газ научились получать газификацией не только угля и нефти, но и более нетрадиционных источников углерода, вплоть до бытовых и сельскохозяйственных отходов. Таким образом, сегодня мусороперерабатывающие заводы способны добывать такое ценное сырье как синтез газ в процессе утилизации отходов.
Применение синтез-газа
Сегодня синтез-газ используется в химической промышленности для получения различного сырья. Кроме этого, он также используется в качестве экологически чистого источника тепла и энергии. Сжигая синтез-газ можно получить достаточно большое количество тепла, которое можно использовать в самых различных целях.
Кроме этого, синтез газ используется в качестве исходного сырья для метилового спирта и синтетического жидкого топлива, которое по своим характеристикам ни в чем не уступает традиционному.
- Комментарии к статье
- Вконтакте
ztbo.ru
газ – это… Что такое Синтез-газ?
Синтез-газ — смесь монооксида углерода и водорода. В промышленности получают паровой конверсией метана, парциальным окислением метана, газификацией угля. В зависимости от способа получения соотношение CO:Н2 варьируется от 1:1 до 1:3.
В зависимости от применяемого сырья и вида конверсии (водяным паром или нестехиометрическим количеством О2) соотношение компонентов в газовой смеси изменяется в широких пределах:
Это соотношение определяется также методом и условиями газификации углей. По наиболее распространенному методу Лурги получают сырой газ след, состава: 15-18% СО, 38-40% Н2, 9-11% СН4
Синтез-газ получают также наряду с целевым продуктом ацетиленом при окислительном пиролизе природного газа.
В азотной промышленности синтез-газ называют смесь N2 и Н2, применяемую в синтезе аммиака.
Применение
Основные области использования: получение монооксида углерода и водорода, производство метанола, оксосинтез, синтез Фишера-Тропша.
См. также
dic.academic.ru
Получение синтез-газа
Первым способом получения синтез-газа была газификация каменного угля, которая была осуществлена еще в 30-е годы XIX века в Англии с целью получения горючих газов: водорода, метана, монооксида углерода. Этот процесс широко использовался во многих странах до середины 50-х годов XX века, а затем был вытеснен методами, основанными на использовании природного газа и нефти. Однако в связи с сокращением нефтяных ресурсов значение процесса газификации снова стало возрастать. В настоящее время существуют три основных промышленных метода получения синтез-газа. 1. Газификация угля. Процесс основан на взаимодействии угля с водяным паром:C + H2O = H2 + CO.
Эта реакция является эндотермической, равновесие сдвигается вправо при температурах 900-1000°С. Разработаны технологические процессы, использующие парокислородное дутье, при котором наряду с упомянутой реакцией протекает экзотермическая реакция сгорания угля, обеспечивающая нужный тепловой баланс:
C + 1/2O2 = CO.
2. Конверсия метана. Реакция взаимодействия метана с водяным паром проводится в присутствии никелевых катализаторов (Ni-Al2O3) при повышенных температурах (800-900°С) и давлении:
CH4 + H2O = CO + 3H2.
В качестве сырья вместо метана может быть использовано любое углеводородное сырье. 3. Парциальное окисление углеводородов. Процесс заключается в неполном термическом окислении углеводородов при температурах выше 1300°С:
CnH2n+2 + 1/2nO2 = nCO + (n + 1)H2.
Способ применим к любому углеводородному сырью, но наиболее часто в промышленности используют высококипящую фракцию нефти – мазут. Соотношение СО : Н2 существенно зависит от применяемого способа получения синтез-газа. При газификации угля и парциальном окислении это соотношение близко к 1 : 1, тогда как при конверсии метана соотношение СО : Н 2 составляет 1 : 3. В настоящее время разрабатываются проекты подземной газификации, то есть газификации угля непосредственно в пласте. Интересно, что эта идея была высказана Д.И. Менделеевым более 100 лет назад. В перспективе синтез-газ будут получать газификацией не только угля, но и других источников углерода вплоть до городских и сельскохозяйственных отходов.
Монооксид углерода, карбонилы металлов и правило 18 электронов
Многочисленные
синтезы на базе монооксида углерода и
водорода представляют громадный как
практический, так и теоретический
интерес, так как позволяют из двух
простейших веществ получать ценнейшие
органические соединения. И здесь
определяющую роль играет катализ
переходными металлами, которые способны
активировать инертные молекулы СО и
Н2.
Активация молекул – это перевод их в
более реакционноспособное состояние.
Особо следует отметить, что в превращениях
синтез-газа широкое развитие получил
новый тип катализа – катализ комплексами
переходных металлов или металлокомплексный
катализ (см. статью О.Н. Темкина
[4]). Так
ли инертна молекула СО? Представления
об инертности монооксида углерода носят
условный характер. Еще в 1890 году Монд
получил из металлического никеля и
монооксида углерода первое карбонильное
соединение металла, летучую жидкость
с температурой кипения 43°С – Ni(CO)
При этом происходит не только s-взаимодействие за счет свободной пары электронов углерода, но и p-взаимодействие за счет передачи электронов с d-орбитали металла на энергетически доступные вакантные орбитали углерода:
studfiles.net
Автомобиль на твёрдом газе — синтез газ для автомобиля
Вы можете ознакомиться с изобретениями Николая Егина
Данный сайт остается как память об изобретателе
Важная информация об авторских свидетельствах
Автомобиль на твердом газе — синтез газ для автомобиля
Мысль о том, что простое сжигание нефти и её продуктов равнозначно отоплению печи ассигнациями, была высказана ещё Менделеевым на заре эра автомобиля. Справедливость сказанного мы ощущаем практически, когда резко сокращается добыча нефти, а цены на бензин и дизельное топливо стремительно растут. Неудивительно, что в создавшихся условиях начался широкий поиск альтернативных источников энергии для транспорта. Накоплен большой практический опыт эксплуатации карбюраторных и дизельных ДВС на сжатом и сжиженном природном газе, а также на коксовом или синтез — газе. Однако природный газ быстро дорожает, поэтому оправдан интерес к последнему.
Этот газ содержит до 70% водорода, а также оксид углерода и метан, что обеспечивает их высокую калорийность и экологическую чистоту продуктов сгорания. Синтез — газ производится металлическими и химическими предприятиями в больших объёмах и в качестве «попутного» не где не используется, а, как правило, сжигается в факелах. Кроме того, синтез — газ является продуктом конверсии метанола, что определяет его широкие возможности получения и использование на транспорте.
Испытания по использованию синтез — газа в качестве основного и дополнительного топлива для ДВС с внешним смесеобразованием показали, что уровень токсичности отработавших газов в обоях случаях оказался практически таким же, как при работе ДВС на водороде. Таким образом, использование синтез — газа экономически и экологически выгодно, особенно для транспорта больших городов. К сожалению, на пути широкого использования газов на автотранспорте серьёзные, а для ряда регионов непреодолимые трудности. Дело в том, что синтез — газ, как и природных приходится закачивать в болоны под высоким давлением или сжижать, что требует сети дорогостоящих заправочных станций. На автомобиль приходится устанавливать громоздкие и тяжёлые болоны, редуктор высокого и низкого давления, испарители, смесители, многочисленные вентили и клапаны — ненадёжную и капризную газовую арматуру.
При полном переходе на газ затрудняется запуск холодного двигателя, а главное, снижается пробег между заправками. Естественно, быстрее расходуется сжатый газ, чем сжиженный, но ни тот, ни другой не запасёшь в дорогу и не достанешь в пути следования. Именно это наталкивает на мысль о том, что было бы здорово получить «твёрдый» газ, который не требует баллонов и запас которого легко можно возить с собой. Поскольку удельный вес такого фантастического газа будет больше, чем сжиженного, то пробег между заправками значительно возрастёт.
Практические поиски и экспериментальные работы, проведённые в лаборатории Рязанской городской станции техников, убедительно доказали, что не чего фантастического в идее получения твёрдого синтез — газа нет. Более того, оказалось, что для его производства не надо создавать новые производства и технологии. Почти шестьдесят лет назад группа учёных и инженеров получила Сталинскую премию за производства технического углерода. Этим продуктом является не что иное, как газовая сажа, которая образуется при сжигание газов в печах с недостаточным содержанием кислорода воздуха. Прошло более половины века, а не чего более простого и надёжного ещё не придумали. Техническая сажа выпускается промышленным тоннажём и не заменима при производстве автомобильных шин, автоэмалей, в полиграфической промышленности. Таким образом, отходящие и бросовые газы многочисленных производств можно легко концентрировать в твёрдую фазу, которая не вызывает сложности при получении, хранении и транспортировки. Однако возникает вопрос, каким образом технический углерод можно трансформировать в синтез — газ на транспортном средстве. Решить эту проблему оказалась достаточно просто. Из курса химии известно, что углерод является не только отличным топливом, но и мощным восстановителем. Другими словами, углерод возвращает к активной жизни многие элементы, вступившие в прочное взаимодействие при окислительной реакции. Например, вода является продуктом окисления водорода кислородом и образует очень прочные соединения. Но если водяной пар пропустить через раскалённый до 750С и более углерод, то проявляются восстановительные свойства углерода. В результате образуется синтез — газ, состоящий примерно на 50% водорода и 50% оксида углерода. Данная восстановительная реакция является эндотермической, то есть идёт с поглощением тепла, а углерод выполняет роль активного катализатора, который расщепляет молекулы воды на водород и кислород, и сам участвует в реакции, образуя с кислородом горючей газ — оксид углерода.
Многочисленные эксперименты, проведённые ещё 1989 году, показали, что для образования синтез — газа вода и углерод расходуется в соотношении 4:3. Таким образом, запас «твёрдого» газа на борту автомобиля не превышает нескольких килограммов на расстояние в 500 км при экономии бензина более 50%. Воду можно добавлять в пути следования, а необходимое тепло брать от выхлопных газов и из системы охлаждения ДВС (а.с. и патенты №1321872, № 1578373, №1659248, №1744286).
Кроме решения проблемы перевозки газа в концентрированном твёрдом виде, решение обеспечивает экологически чистый выхлоп ДВС и гасит факелы многочисленных химических производств, так как техническая сажа становится товаром. Более того, в технический углерод легко переработать многочисленные промышленные отходы, например всё те же шины, для производства которых столь необходима сажа. Сотни миллионов старых покрышек наполняют свалки и ждут экологически чистого и экономически выгодного решения их утилизации.
Очень важным является и тот факт, что для работы на твёрдом газе автомобиль не требует переоборудования ДВС и его систем. Просто на выпускном коллекторе устанавливается малогабаритная реакционная камера из жаропрочной стали или чугуна с теплообменником. Первая трубка соединяется с водяным бачком или радиатором, а вторая отводит синтез — газ на карбюратор или во впускной коллектор для дизельных ДВС. При этом в карбюраторе используется жиклёр с сечением отверстия менее чем в 2 раза, а в дизельном ТНВД (топливный насос высокого давления) регулируют рейку привода на меньшую производительность. Такое устройство обеспечивает не только экономию основного топлива более 50%, но снижает температуру выхлопных газов, их токсичность и шумность, что устраняет прогорание корпуса глушителя.
Кстати о глушителях. Именно в их корпусах собирается много сажи от неполного сгорания топлива, а «лишняя» сажа в виде дыма и копоти выделяется в атмосферу и загрязняет её ядовитым смогом. Теперь сажа становится товарным топливом , которое вылетает на ветер. Это меня ситуацию коренным образом. Ни один рачительный хозяин не допустит потерь жизненно необходимых энергоносителей. Мы так же не явились исключением, поэтому разработали сменный фильтрующей элемент из минеральной ваты, например стекловаты, который устанавливается в штатный корпус глушителя и собирает более 90% сажи, но не создаёт динамического сопротивления выхлопным газам (а.с. и патенты №1188343, №1763685). Использование такого фильтра обеспечивает для работы ДВС даже с сильно изношенными деталями поршневой группы экологическую чистоту, кроме того, запасает не сгоревшую рабочую смесь в виде твёрдого газа. Когда сменный фильтр полностью насыщается сажей, то его заменяют на чистый, а загрязнённый, как вы догадываетесь, устанавливают в реакционную камеру. Размеры подобраны таким образом, что из фильтра глушителя элемент превращается в источник синтез — газа. Когда первый фильтр в камере полностью очищается от сажи (стекловолокно в реакцию не вступает), а второй фильтр в глушителе заполняется техническим углеродом, то их меняют местами. Таким образом, циркуляция углеродного топлива в двигателе приобретает почти идеальный замкнутый цикл, что обеспечивает максимальную экономию топлива и экологическую чистоту транспорта.
Предложенные изобретения удачно вписываются в концепцию ведущих зарубежных фирм, использующих возобновляемые виды топлива, например, метанол, спирты, масла и их смеси, в том числе биогаз. Сжигание каждого вида топлива в ДВС сопряжено со многими трудностями: у них различная теплотворная способность, необходимая степень сжатия, полнота сгорания и т.д. Кроме того, технические спирты и метанол токсичны при хранении, а растительное масло и биогаз содержат примеси, которые не нужны в цилиндрах ДВС.
Используя наши решения, можно перевести любые виды возобновляемых топлив в единую форму — технический углерод. При этом тепло от их сгорания можно использовать в производственных и бытовых целях, а полученный топливный концентрат для самых различных транспортных средств, добывающих и перерабатывающих агрегатов, различных силовых и энергетических установок. Карбюраторные и дизельные ДВС становятся всетопливными, причём работают на унифицированном твёрдом топливе, не требуя дополнительных регулировок, зависящих от свойства каждого сходного топливного компонента.
Автомобильный термохимический реактор синтез газа успешно работает не только на саже — техническом углероде, но и на более тяжёлых фракциях, например, каменном угле, кокосовой крошке, древесном угле и различных обугленных органических отходах. Для получения углерода можно использовать отходы деревообработки: ветки, опилки, а также стебли листьев сорняков и различных отходов сельскохозяйственных культур, например, стебли и шелуху подсолнечников, стержни кукурузных початков и др. Углерод полностью преобразуется в синтез — газ, а незначительное количество шлаков и примесей остаётся в виде золы в реакторе и не попадает в цилиндры. После 3-4-х заправок золу удаляют из камеры вручную или при помощи пылесоса. Техническое обслуживание занимает несколько минут, после чего устройство заправляется свежей порцией сажи или угля и готово к эксплуатации. Авторы готовы оказать содействие во внедрение и лицензирование.
Все представленные на сайте изобретения имеют авторские свидетельства на изобретение, чертежи и конструкторскую документацию. Автор – Николай Егин.
Важная информация об авторских свидетельствах
nlegin.ru
Сравнительный анализ: методы получения синтез-газа
Министерство образования Российской Федерации
Московская государственная академия тонкой химической
технологии им. М.В. Ломоносова
Кафедра Технологии нефтехимического синтеза
и искусственного жидкого топлива
АТТЕСТАЦИОННАЯ РАБОТА
на соискание степени бакалавра по направлению
550800 «Химическая технология и биотехнология»
Тема: Сравнительный анализ: методы получения синтез-газа
Заведующий кафедрой,
д. х. н., проф. Третьяков В. Ф.
Руководитель,
ст. преп. Антонюк С. Н.
Дипломант, студент группы ХТ-406
Сысоев М. М.
Москва, 2003 г.
Содержание
1. Введение
2. Способы получения синтез-газа
3. Газификация угля
3.1 Тенденции развития и новые инженерные решения в газификации угля
3.2 Взгляд на углепереработку сквозь десятилетия
3.3 Инженерные разработки за прошедшее столетие
3.4 Аппаратурно-техническое оформление процесса
4. Конверсия метана в синтез-газ
4.1 Термодинамика процесса
4.2 Кинетика углекислотной конверсии метана
4.3 Механизм конверсии смеси CH4 + CO2
4.4 Катализаторы углекислотной конверсии метана
4.5 Технология конверсии метана
5. Синтез Фишера-Тропша
5.1 Выбор катализаторов
6. Альтернативный способ получения синтез-газа
6.1 Термохимическая конверсия биомассы
6.2 Биотехнологическая конверсия биомассы
7. Продукты, получаемые на основе синтез-газа
8. Выводы
9. Используемая литература
1. Введение
История знает немало примеров, когда в силу острой необходимости рождались новые оригинальные подходы к решению давно существующих жизненно важных проблем. Так, в предвоенной Германии, лишенной доступа к нефтяным источникам, назревал жесткий дефицит топлива, необходимого для функционирования мощной военной техники. Располагая значительными запасами ископаемого угля, Германия была вынуждена искать пути его превращения в жидкое топливо. Эта проблема была успешно решена усилиями превосходных химиков, из которых, прежде всего следует упомянуть Франца Фишера, директора Института кайзера Вильгельма по изучению угля.
В 1926 году была опубликована работа Ф. Фишера и Г. Тропша “О прямом синтезе нефтяных углеводородов при обыкновенном давлении”, в которой сообщалось, что при восстановлении водородом монооксида углерода при атмосферном давлении в присутствии различных катализаторов (железо – оксид цинка или кобальт – оксид хрома) при 270 о С получаются жидкие и даже твердые гомологи метана.
Так возник знаменитый синтез углеводородов из монооксида углерода и водорода, называемый с тех пор синтезом Фишера-Тропша. Смесь CO и H2 в различных соотношениях, называемая синтез-газом, легко может быть получена как из угля, так и из любого другого углеродсодержащего сырья.
Следует отметить, что к моменту разработки синтеза Фишера-Тропша существовал другой способ получения жидкого топлива – не из синтез-газа, а непосредственно из угля прямой гидрогенизацией. В этой области значительных успехов добился также немецкий химик Ф. Бергиус, который в 1911 году получил из угля бензин. Справедливости ради подчеркнем, что синтез Фишера-Тропша возник не на пустом месте – к тому времени существовали научные предпосылки, которые базировались на достижениях органической химии и гетерогенного катализа. Еще в 1902 году П. Сабатье и Ж. Сандеран впервые получили метан из СО и H2 . В 1908 году Е. Орлов открыл, что при пропускании монооксида углерода и водорода над катализатором, состоящим из никеля и палладия, нанесенных на уголь, образуется этилен.
Промышленность искусственного жидкого топлива достигла наибольшего подъема в годы второй мировой войны. Достаточно сказать, что синтетическое топливо почти полностью покрывало потребности Германии в авиационном бензине. После 1945 года в связи с бурным развитием нефтедобычи и падением цен на нефть отпала необходимость синтеза жидких топлив из СО и Н2 . Наступил нефтехимический бум. Однако в 1973 году разразился нефтяной кризис – нефтедобывающие страны ОПЕК (Организация стран – экспортеров нефти – Organization of Petroleum Exporting Countries) резко повысили цены на сырую нефть, и мировое сообщество вынуждено было осознать реальную угрозу истощения в обозримые сроки дешевых и доступных нефтяных ресурсов. Энергетический шок 70-х годов возродил интерес ученых и промышленников к использованию альтернативного нефти сырья, и здесь первое место, бесспорно, принадлежит углю. Мировые запасы угля огромны, они, по различным оценкам, более чем в 50 раз превосходят нефтяные ресурсы, и их может хватить на сотни лет. Нет никаких сомнений, что в обозримом будущем использование синтез-газа будет играть ключевую роль не только и не столько для производства “угольных” топлив (здесь трудно пока конкурировать с нефтяным топливом), но, прежде всего для целей органического синтеза. В настоящее время в промышленном масштабе по методу Фишера-Тропша получают бензин, газойль и парафины только в Южной Африке. На установках фирмы “Sasol” производят около 5 млн. т. в год жидких углеводородов.
Отражением интенсификации исследований по синтезам на основе СО и Н2 является резкое возрастание публикаций, посвященных химии одноуглеродных молекул (так называемая С1-химия). С 1984 года начал издаваться международный журнал “C1-Molecule Chemistry”. Таким образом, мы являемся свидетелями наступающего ренессанса в истории углехимии. Рассмотрим некоторые пути превращения синтез-газа, приводящие к получению как углеводородов, так и некоторых ценных кислородсодержащих соединений. Важнейшая роль в превращениях СО принадлежит гетерогенному и гомогенному катализу [1-3].
2. Способы получения синтез-газа
Первым способом получения синтез-газа была газификация каменного угля, которая была осуществлена еще в 30-е годы XIX века в Англии с целью получения горючих газов: водорода, метана, монооксида углерода. Этот процесс широко использовался во многих странах до середины 50-х годов XX века, а затем был вытеснен методами, основанными на использовании природного газа и нефти. Однако в связи с сокращением нефтяных ресурсов значение процесса газификации снова стало возрастать.
В настоящее время существуют три основных промышленных метода получения синтез-газа[34].
1. Газификация угля. Процесс основан на взаимодействии угля с водяным паром:
C + H2 O ↔ H2 + CO
Эта реакция является эндотермической, равновесие сдвигается вправо при температурах 900-1000 о С. Разработаны технологические процессы, использующие парокислородное дутье, при котором наряду с упомянутой реакцией протекает экзотермическая реакция сгорания угля, обеспечивающая нужный тепловой баланс:
C + 1/2O2 ↔CO
2. Конверсия метана. Реакция взаимодействия метана с водяным паром проводится в присутствии никелевых катализаторов (Ni-Al2 O3 ) при повышенных температурах (800-900 о С) и давлении:
CH4 + H2 O → CO + 3H2
В качестве сырья вместо метана может быть использовано любое углеводородное сырье.
3. Парциальное окисление углеводородов. Процесс заключается в неполном термическом окислении углеводородов при температурах выше 1300 о С:
Cn H2n+ 2 + 1/2nO2 → nCO + (n + 1)H2
Способ применим к любому углеводородному сырью, но наиболее часто в промышленности используют высококипящую фракцию нефти – мазут.
Соотношение СО : Н2 существенно зависит от применяемого способа получения синтез-газа. При газификации угля и парциальном окислении это соотношение близко к 1 : 1, тогда как при конверсии метана соотношение СО : Н2 составляет 1 : 3. В настоящее время разрабатываются проекты подземной газификации, то есть газификации угля непосредственно в пласте. Интересно, что эта идея была высказана Д.И. Менделеевым более 100 лет назад. В перспективе синтез-газ будут получать газификацией не только угля, но и других источников углерода вплоть до городских и сельскохозяйственных отходов.
3. Газификация угля
Газификация — высокотемпературный процесс взаимодействия углерода топлива с окислителями, проводимый с целью получения горючих газов (Н2 , СО, СН4 ). В качестве окислителей, которые иногда называют газифицирующими агентами, используют кислород (или обогащенный им воздух), водяной пар, диоксид углерода либо смеси указанных веществ. В зависимости от соотношения исходных реагентов, температуры, продолжительности реакции и других факторов можно получать газовые смеси самого разного состава.
3.1 Тенденции развития и новые инженерные решения в газификации угля
Впервые промышленная реализация газификации твердых топлив была осуществлена в 1835 г в Великобритании. К 50-м годам XIX в. практически во всех крупных и средних городах Европы и Северной Америки действовали газовые заводы для производства отопительного, бытового и светильного газа [4]. К середине XX в этот процесс получил широкое развитие в большинстве промышленных стран мира. Например, в СССР в 50-е годы работало свыше 350 газогенераторных станций, на которых было установлено около 2500 газогенераторов. Эти станции вырабатывали ежегодно 35 млрд. м3 энергетических и технологических газов. Это был “золотой век” газификации угля. Начиная с 60-х годов XIX в., все более серьезную конкуренцию углю начинает оказывать нефть. В начале 1960-х годов разработка месторождений дешевой нефти на Ближнем Востоке и в Западной Сибири привела практически к полной ликвидации этой отрасли промышленности. Как известно, в последующие 20—25 лет в мировом энергетическом балансе происходили изменения, обусловленные ростом добычи и потребления нефти, попутных и природных газов. Вследствие этого конкурентоспособность искусственных энергетических и технологических газов, получаемых из твердых топлив, резко снизилась, и их производство практически повсеместно было прекращено. Сохранились лишь небольшие островки в уникальных регионах. Например, в ЮАР углепереработка (главным образом на основе газификации угля) стала крупной промышленным сектором из-за эмбарго на поставку нефти. Началось триумфальное шествие нефти. Однако уже в 1972 г. оно омрачилось первым “энергетическим кризисом”, который по существу был спровоцирован на политической основе странами-участниками ОПЕК. Мировые цены на нефть подскочили с 5-7 до 24 долл. США за баррель (1 т сырой нефти сорта Brent ≈ 8,06 баррелей), и стало ясно, что углепереработку списывать в архив рано, так как в большинстве развитых стран много угля и мало или совсем нет нефти.
mirznanii.com
Синтез-газ — Википедия (с комментариями)
Материал из Википедии — свободной энциклопедии
Синтез-газ — смесь монооксида углерода и водорода. В промышленности получают паровой конверсией метана, парциальным окислением метана, газификацией угля. В зависимости от способа получения соотношение CO:Н2 варьируется от 1:1 до 1:3.
Соотношение компонентов в синтез-газе колеблется в широком диапазоне, поскольку зависит как от применяемого сырья, так и от вида конверсии – водяным паром или кислородом:
- <math>\mathsf{CH_4 + H_2O \rightarrow CO + 3H_2}</math>
- <math>\mathsf{2CH_4 + O_2 \rightarrow 2CO + 4H_2}</math>
- <math>\mathsf{\text{-}CH_2\text{-} + H_2O \rightarrow CO + 2H_2}</math>
- <math>\mathsf{2 \text{-}CH_2\text{-} + O_2 \rightarrow 2CO + 2H_2}</math>
Соотношение компонентов зависит также от метода и условий газификации углей. Наибольшее распространение имеет метод Лурги, по которому получается сырой газ состав: 15-18 % СО, 38-40 % Н2, 9-11 % СН4, 30-32 % СО2. При повышении температуры возрастает содержание оксида углерода, при повышении давления — водорода и метана. При этом наличествуют примеси инертных газов (N2 и др.) и сероводорода, если в сырье были серосодержащие продукты. Синтез-газ проходит очистку сероводорода и диоксида углерода при помощи селективных растворителей. Соотношение между СО и Н2 при необходимости меняют конверсией оксида углерода водяным паром.
Синтез-газ получают попутно с ацетиленом в процессах окислительного пиролиза природного газа.
В азотной промышленности под синтез-газом понимается смесь азота и водорода, которая используется в процессе получения аммиака.
Применение
Основными сферами применения синтез-газа является получение оксида углерода и водорода, синтез метанола, оксосинтез, синтез Фишера-Тропша.
См. также
Напишите отзыв о статье “Синтез-газ”
Литература
- Химическая энциклопедия / Редкол.: Кнунянц И.Л. и др.. — М.: Советская энциклопедия, 1995. — Т. 4 (Пол-Три). — 639 с. — ISBN 5-82270-092-4.
Отрывок, характеризующий Синтез-газ
Когда на другой день утром государь сказал собравшимся у него офицерам: «Вы спасли не одну Россию; вы спасли Европу», – все уже тогда поняли, что война не кончена.Один Кутузов не хотел понимать этого и открыто говорил свое мнение о том, что новая война не может улучшить положение и увеличить славу России, а только может ухудшить ее положение и уменьшить ту высшую степень славы, на которой, по его мнению, теперь стояла Россия. Он старался доказать государю невозможность набрания новых войск; говорил о тяжелом положении населений, о возможности неудач и т. п.
При таком настроении фельдмаршал, естественно, представлялся только помехой и тормозом предстоящей войны.
Для избежания столкновений со стариком сам собою нашелся выход, состоящий в том, чтобы, как в Аустерлице и как в начале кампании при Барклае, вынуть из под главнокомандующего, не тревожа его, не объявляя ему о том, ту почву власти, на которой он стоял, и перенести ее к самому государю.
С этою целью понемногу переформировался штаб, и вся существенная сила штаба Кутузова была уничтожена и перенесена к государю. Толь, Коновницын, Ермолов – получили другие назначения. Все громко говорили, что фельдмаршал стал очень слаб и расстроен здоровьем.
Ему надо было быть слабым здоровьем, для того чтобы передать свое место тому, кто заступал его. И действительно, здоровье его было слабо.
Как естественно, и просто, и постепенно явился Кутузов из Турции в казенную палату Петербурга собирать ополчение и потом в армию, именно тогда, когда он был необходим, точно так же естественно, постепенно и просто теперь, когда роль Кутузова была сыграна, на место его явился новый, требовавшийся деятель.
Война 1812 го года, кроме своего дорогого русскому сердцу народного значения, должна была иметь другое – европейское.
За движением народов с запада на восток должно было последовать движение народов с востока на запад, и для этой новой войны нужен был новый деятель, имеющий другие, чем Кутузов, свойства, взгляды, движимый другими побуждениями.
wiki-org.ru
газ – Большая Энциклопедия Нефти и Газа, статья, страница 1
Синтез-газ
Cтраница 1
Синтез-газ получают также при газификации угля, кокса, древесных отходов посредством кислородного или парового дутья, а также при паровом риформинге природного газа, СНГ или дистиллята. [1]
Синтез-газ может быть получен из любых производственны. Такой состав водяного газа позволяет использовать его непосредственно для синтеза над железными катализаторами. В случае необходимости повышения концентрации окиси углерода в водяном газе в газогенераторе применяют кислородно-углекислотнос дутье вместо паровоздушного или паро-кислородного. [2]
Синтез-газ, вместо с газообразными и жидкими продуктами, выходит из реактора первой ступени и направляется в насадочпые скрубберы, охлаждаемые водой, где происходит охлаждение и конденсация части полученного продукта в виде конденсат-ног о масла. Пары бензина и углеводороды С3 – С4 ( г аз о л ь), не конденсирующиеся в этих условиях, улавливаются из газа адсорбцией на активированном угле. Газ, выходящий из адсорберов, подается в реактор второй ступени синтеза. Выделение продуктов реакции производится тем же путем, что и в первой ступени. Остаточный газ, разбавленный на 80 % инертными неактивными примесями, не может служить для синтеза и сжигается в топках. [3]
Синтез-газ часто подвергают дополнительной переработке с целью изменения его состава в соответствии с требованиями потребителей. [4]
Синтез-газ из сепаратора 4 направляется в пррмыватель 9, в-котором охлаждается и насыщается влагой до точки росы 82 С; После промывателя 9 газ разветвляется. Один его поток в ка честве целевого газа пропускается через скруббер 10 и отводится из установки. Другой поток при помощи газодувки 11 нагнетается в один из переключаемых регенераторов 8, в котором температура циркуляционного газа повышается – до 1300 С. [6]
Синтез-газ может быть получен и в трубчатых печах. В этом случае ( в отличие от схемы производства технического водорода) в качестве окислителя используется смесь водяного пара и углекислоты. Технологическая схема получения синтез-газа в трубчатых печах аналогична схеме производства водорода с тем отличием, что газы реакции после трубчатой печи и устройства для использования их физического тепла направляются сразу на конечное охлаждение и на отмывку от СОа. Полученная при этом углекислота используется в смеси с водяным паром для конверсии углеводородов. [7]
Синтез-газ выходит из генераторов при 700 – 800 С, проходит системы утилизации тепла, очистки от смол, сернистых сое-дений и СО2; после этого его направляют потребителю. [8]
Синтез-газ сжатый в компрессоре ( 7) подается в смесители ( 4), где смешивается с горячим циркуляционным газом и поступает в реактор 6 на полки со слоями катализатора. [10]
Синтез-газ нужно тщательно очищать от всех примесей. [11]
Синтез-газ из холодильника 7 поступает в абсорбер 8, орошаемый охлажденным водным раствором этаноламинов. Раствор с низа абсорбера подогревается в теплообменнике / / обратным этанол-амином и поступает в десорбер 10, куб которого обогревается глухим паром. При нагревании двуокись углерода выделяется и ее отводят с верха десорбера. [12]
Синтез-газ поступает снизу, поддерживая катализатор во взвешенном состоянии. Отвод тепла осуществляется с помощью водного конденсата, при испарении которого в охлаждающих трубах генерируется пар высокого давления. В другой системе того же типа охлаждение достигается путем циркуляции масла через выносной холодильник. В этих случаях требуется поверхность теплопередачи в 4 – 5 раз меньшая, чем при синтезе в газовой фазе. Эти типы реакторов аналогичны используемым для жидкофазного гидрирования ( рис. 127, а и б, стр. [13]
Синтез-газ поступает в такие ( змеевикозые) реакторы сверху через крышку с прорезями, равномерно распределяется по реакционному пространств1 / и выходит снизу через откидную решетку в коллектор. Для выгрузки катализатора открывают откидную решетку. Загрузка его производится сверху после снятия крышки. [14]
Синтез-газ, используемый для получения метанола и для оксосинтеза, представляет собой смесь водорода и окиси углерода. Производство синтез-газа является также промежуточной стадией процесса получения водорода. Синтез-газ можно получить некаталитически, в частности при взаимодействии кислорода и водяного пара с углем, коксом или жидкими углеводородами. Мы рассмотрим только каталитические процессы. К ним близки также процессы получения газов для синтеза аммиака и процессы получения восстановительных газов ( защитных атмосфер) для металлургии. [15]
Страницы: 1 2 3 4
www.ngpedia.ru
Добавить комментарий