Регенерация отработанных масел – Регенерация отработанных масел Текст научной статьи по специальности «Общие и комплексные проблемы естественных и точных наук»
Восстановление отработанного масла – Основные средства
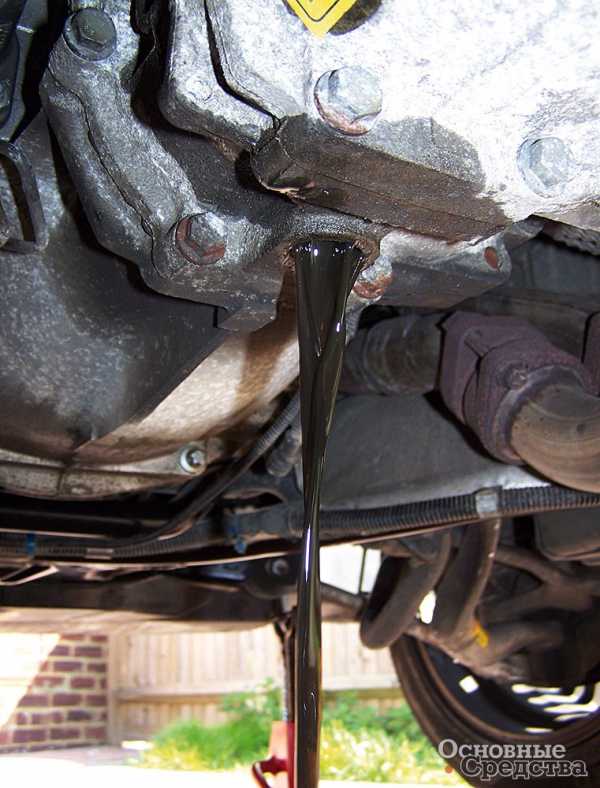
В периоды кризиса остро встают вопросы экономии сырья и материалов, вторичного использования ресурсов, восстановления выработавших ресурс механизмов и материалов.
Растет год от года добыча сырой нефти – главного сырья для производства моторных масел. Только флагман мировой нефтегазовой промышленности компания Exxon Mobil, владеющая 38 нефтеперерабатывающими заводами в 21 стране мира, ежесуточно перерабатывает 6,3 млн. баррелей сырой нефти.
Потребление моторных масел в мире составляет примерно 60 млн. т в условном топливе. И есть данные только о четвертой части этого количества, сообщающие, что после отработки ресурса масло использовано повторно либо переработано или сожжено.
По нашей стране статистика еще печальнее. За год на территории РФ собирается около 1,7 млн. т различных отработанных масел (ОМ). Переработке при этом подвергается до 0,25 млн. т, или 15%, что составляет 3,3% от общего объема потребления.
Для сравнения: в Германии, занимающей первое место в Европе по очистке ОМ, производится сбор и использование около 55% всего объема потребленных свежих масел. Немецкое законодательство в области защиты экологии обязывает производителей масла, чьи производства находятся на территории Германии, добавлять в производимые масла не менее 10% так называемого refining base oil – восстановленного масла. В некоторых европейских странах существует порядок, когда при сдаче отработанного масла сдающий получает свежее масло со скидкой.
О необходимости сбора и переработки ОМ свидетельствует тот факт, что из примерно 100 т нефти получают только 10 т моторного масла, а при переработке 100 т ОМ можно получить более 80 т уже готового к употреблению продукта.
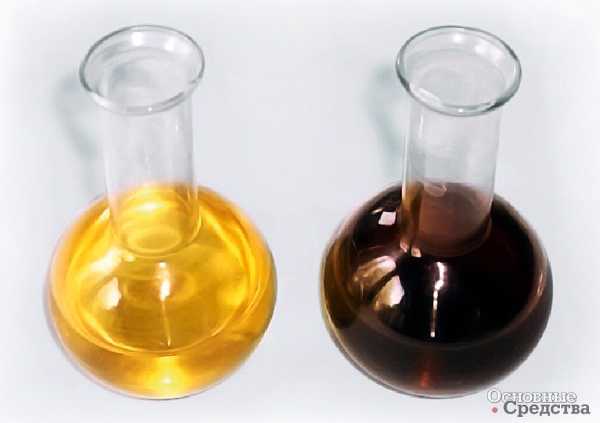
Слили, заменили и что дальше?
В процессе эксплуатации моторных масел в них накапливаются продукты окисления. Это асфальтосмолистые соединения, нагар, лаковые отложения и др. Чтобы предотвратить выпадение осадка этих вредных соединений, в масло вносят моюще-диспергирующие присадки, которые удерживают продукты окисления в коллоидном (взвешенном) состоянии.
Значительное снижение эксплуатационных характеристик моторных масел наступает, когда присадки вырабатывают ресурс. В этот период продукты окисления начинают выпадать в осадок, тем самым вызывая усиленный износ двигателя. Такое состояние моторного масла свидетельствует о необходимости срочно его заменить.
Моторное ОМ относится к категории опасных отходов, является источником загрязнения окружающей среды. Его нельзя сливать в мусорные баки, канализацию или на землю. Из-за присущей вязкости такое масло прилипает ко всему, от песка до оперения птиц. Отработанные масла не растворимы, химически устойчивы и могут содержать токсические химические соединения и тяжелые металлы. В естественных условиях масло разлагается в течение длительного времени. Представьте, что всего 1 л моторного масла может превратить 1 000 000 л питьевой воды в техническую.
Для основного состава транспортных предприятий тема утилизации ОМ – одна из самых злободневных. Организация и содержание пунктов сбора ОМ, хранение, транспортировка, переработка – все это требует финансовых затрат. В реальности незначительную часть ОМ сжигают, а бо’льшую часть все-таки сливают либо на почву, либо в водоемы и канализацию.
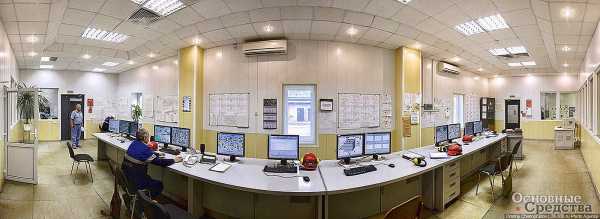
А ведь бережно собранное ОМ, без внесения в него дополнительных загрязнений в виде почвенной и воздушной пыли, воды, топлива, моющих жидкостей и жидкостей не нефтяного происхождения, можно использовать после очистки и восстановления в среднефорсированных двигателях внутреннего сгорания при умеренных нагрузках, в гидравлических системах машин, в коробках передач и трансмиссиях тракторов и автомобилей при умеренных нагрузках, в ходовой части гусеничных тракторов, а также при консервации техники. Современные технологии позволяют получать такой объем смазочного масла из 1 л ОМ, для получения которого при прямом производстве тратится 42 л сырой нефти.
Процесс восстановления отработанного моторного масла в современном понимании включает удаление из него коллоидных веществ, кислот, битумных отложений, механических частиц и химического осадка, удаление газов, водного конденсата, придание восстановленному продукту цвета и запаха оригинала. Однако из существующих и реализованных в настоящее время промышленных процессов восстановления ОМ трудно выделить предпочтительные, все они не лишены как преимуществ, так и изъянов. В каждом конкретном случае при выборе предлагаемой технологии вторичной переработки ОМ необходимо исходить из анализа работы уже действующих прототипов и очень осторожно браться за внедрение новых предложений.
Как переработать?
В зависимости от примененного процесса регенерации получают две-три фракции базовых масел, из которых путем компаундирования и введения присадок получают товарные масла: регенерированные моторные можно использовать как трансмиссионные, гидравлические масла, СОЖ и пластичные смазки, а кроме того, их используют при производстве асфальта.
Обычно при восстановлении в первую очередь механическим путем удаляют свободную воду и твердые частицы. Затем идет теплофизическая фаза – выпаривание, вакуумная перегонка. За этой фазой происходит физико-химическая обработка. Дело в том, что при фильтрации ОМ наблюдается весьма незначительный эффект очистки за счет присутствия многофункциональных присадок, в составе которых есть моющий компонент. Окисные соединения, которые под действием присадок находятся в коллоидном мелкодисперсном состоянии, необходимо с помощью коагулянтов несколько увеличить в объеме, тогда масло становится фильтруемым. Исследования доказали, что оптимальное коагулирование осуществляется в случае применения моноэтаноламина.
На следующем этапе регенерируемое масло подвергают микрофильтрации, пропуская его через мембраны, различающиеся как производительностью, так и термической устойчивостью, поскольку традиционным способом увеличения удельной производительности мембран является снижение вязкости жидкости за счет повышения температуры. Наиболее распространенными являются полимерные мембраны типа МФФК. Они способны отфильтровать около 800 л/(м 2.ч) при диаметре пор 0,07 мкм. Металлокерамические мембраны типа «ТРУМЕМ» являются самыми производительными – при диаметре ячейки 0,07 мкм они пропускают 1000 л/(м2.ч). Для самой тонкой очистки применяют мембраны керамические одноканальные со средним диаметром пор 0,03 мкм. Углеродные одноканальные мембраны осуществляют наиболее грубую очистку: у них диаметр пор 0,1 мкм, зато эти мембраны термически устойчивы до 300 °С.
Высшей целью регенерации является получение масел с характеристиками, превосходящими первоначальные свойства продукта, поступившего на восстановление. Это возможно, но для этого кроме вышеперечисленных этапов обработки ОМ требуется применять химические способы регенерации, связанные с использованием сложного оборудования и большими затратами. Реально же очищенные ОМ обладают достаточным запасом эксплуатационных свойств, обеспечивающих применение в менее нагруженных узлах и агрегатах машин.
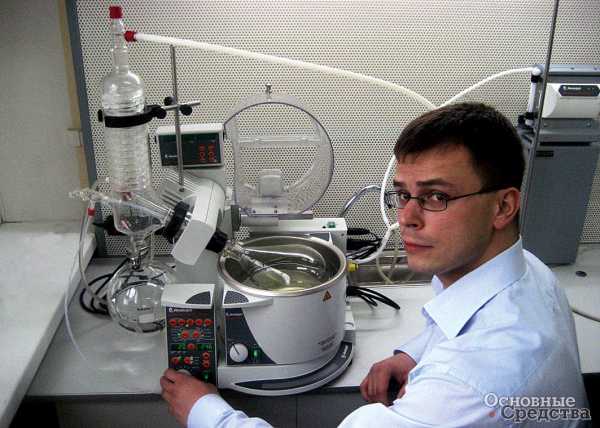
Так что же конкретно?
Наука не стоит на месте. Разработана отечественная технология, получившая название «Мелиоформ», в основе которой процесс лиофобно-сорбиционной сепарации. Метод позволяет очищать и осветлять минеральные моторные масла без применения кислот и щелочей, полностью восстанавливая масляную основу при минимальных затратах.
Еще одна российская разработка – установка УОМ-100. С ее помощью восстанавливается кинематическая вязкость в очищенном масле до 9 мм2/с, а в поступившем ОМ этот показатель не ниже 8,5 мм2/с. Показатель свежего масла по ГОСТу равен 10 мм2/с при 100 °С. Содержание механических примесей после очистки составляет 0,01%, что уже соответствует ГОСТу. А такой важный показатель, как содержание нерастворимого осадка, равен после очистки 0,02% (содержание в ОМ – 0,7%). В результате процесса очистки полученное масло или смесь масел вполне можно использовать как гидравлическое масло, а моторные масла дизельных двигателей подходят для использования на долив в среднефорсированные двигатели. Установка комплектуется также экспресс-лабораторией, контролирующей кинематическую вязкость, загрязненность, диспергирующие-стабилизирующие свойства, содержание воды, плотность и щелочное число полученного продукта. Используя ее, можно проводить внедряемые повсеместно диагностические анализы моторных масел. При этом обслуживают установку всего два человека.
При небольших размерах – 1200х900х1000 мм очень эффективную установку УОМ-3М для очистки ОМ предлагают другие отечественные разработчики. УОМ-3М обеспечивает снижение механических примесей с 0,9% в загрязненном масле до 0,01% в очищенном. При этом в свежем масле по ГОСТу допускается 0,015% механических примесей. Производитель утверждает, что требуется только час для того, чтобы из 100 л загрязненного масла получить 95…98 л продукта. В очищенном масле загрязнений в десятки раз меньше, чем в масле, работающем без такой очистки при рядовой эксплуатации. Очистка освобождает масло от воды, осветляет.
Украинские разработчики предлагают современную серийно выпускаемую установку по регенерации любых типов минеральных масел, в том числе моторных. Причем в технологическом процессе не используются химические вещества, нет вредных отходов, подлежащих опять-таки утилизации. Производительность – от 100 до 250 л/ч по моторным маслам, размеры установки – 1900х1080х1750 мм. Затраты на регенерацию составляют 4 US $/т. Сорбента требуется около 4% от массы масла, а из тонны ОМ получают 950 кг прозрачного, чистого масла.
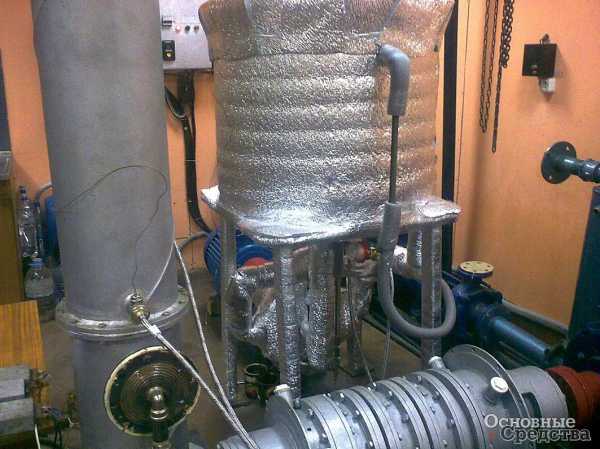
На пунктах техобслуживания автотракторной, дорожной и строительной техники успешно применяются стенды очистки жидкостей серии СОГ (913К1М, 913К1М, 913К1В3, 913КТ1В3). Принцип действия довольно прост – в роторе центрифуги-насоса со спиральной или тарельчатой вставкой осаждаются находящиеся в жидкости даже мельчайшие твердые и жидкие загрязнения, которые нерастворимы и обладают большей, чем очищаемая жидкость, плотностью. Установки компактные, их масса около 140 кг, но осуществляют очистку жидкостей от абразивных загрязнений до 5…10-го класса по ГОСТ 17216–2001 при исходной загрязненности 15…17-го класса. Содержание воды в масле на выходе не выше 0,05% при исходном содержании до 1%.
Глобально решает вопрос использования ОМ комплексная технология в рамках мини-завода по получению так называемого «биодизеля». Это и переработка ОМ, и в конечном итоге обеспечение предприятий агропромышленного комплекса качественным дизельным топливом из собственного сырья. С помощью разработанного нашими конструкторами и технологами оборудования растительные масла и органические жиры перерабатываются в биологическое дизельное топливо, а с помощью другого оборудования из ОМ получают дизтопливо низкого качества. Затем полученные продукты смешивают в пропорции соответственно 20% и 5% с 75% классического дизельного топлива. Такая технология, исходя из производительности мини-завода 2 тыс. куб.м/год, окупает вложения менее чем за год, параллельно решая проблемы 100%-ного использования отработанных материалов. Импортные заводы по производству биотоплива имеют, как правило, мощности 120…500 тыс. т в год, а средняя цена комплекса производительностью 200 тыс. т в год составляет около 25 млн. евро, тогда как наш мини-завод стоит не более $150 тыс. Разработчики утверждают: объем получаемого продукта за единицу времени, а это примерно 1 т/ч, значительно превосходит скорость, которую достигли производители биотоплива стран ЕС, технология которых основана на реакции взаимодействия исходных материалов – масло, щелочь, метанол при высокой температуре нагрева.
А что еще?
Помимо изложенного выше отработанные масла являются высококалорийным топливом, и это огромный теплоэнергетический ресурс. У ОМ калорийность выше, чем у угля и мазутных сортов топлива. Потенциал использования тепловой энергии ОМ сопоставим по величине со всеми потерями в тепловых сетях коммунальных систем теплоснабжения всей страны. Однако использовать потенциал полностью не удается. На заводах «отработку» обезличенно сливают в общую емкость, что недопустимо в условиях предприятий, эксплуатирующих автотехнику. Сбор ОМ из узлов и агрегатов машин должен производиться раздельно, по группам и маркам. В противном случае снижается эффективность горения. Еще хуже, если в такую масляную смесь попадет вода, отходы производства и даже взрывоопасные вещества.
Не выполняется контроль поступающего для централизованного отжига масла. Но самое плохое то, что ОМ сжигают, как правило, в физически и морально устаревших по техническим и экологическим показателям печах, не оборудованных спецавтоматикой горения. При сжигании ОМ используется подмешивание топливных отходов в состав мазута или дизтоплива, что приводит к нарушению норм предельно допустимой концентрации. Тепло сожженного масла не всегда используется рационально и уходит на сброс, что противоречит принципам энергосбережения.
Наиболее экономичным подходом, по всей видимости, является применение автономного оборудования отжига самим эксплуатирующим предприятием, рассчитывающим на собственный ресурс и свои потребности.
os1.ru
способ регенерации отработанных масел – патент РФ 2106398
Изобретение относится к способам регенерации отработанного или свежего загрязненного в процессе транспортирования, хранения и использования смазочного масла и может использоваться на нефтебазах, станциях технического обслуживания автотракторной техники, автотранспортных и других предприятиях, использующих автотракторную технику. Сущность изобретения заключаюется в том, что масло после фильтрации подвергают очистке щелочью и обработке природным адсорбентом “горелая порода” и после центрифугирования из масла дополнительно удаляют механические примеси, воду и легкие углеводороды с последующей очисткой масла в электрогидроциклоне и адсорбере с использованием природного адсорбента “горелая порода”. 3 табл., 4 ил., 3 табл. Изобретение относится к способам регенерации отработанных масел и может быть использовано на нефтебазах, станциях технического обслуживания автотракторной техники, автотранспортных и других предприятиях, применяющих смазочные материалы. Известны способы регенерации отработанных масел (ОМ) от загрязнений с применением химических реагентов (Шишкин П. И. Регенерация отработанных масел. М., Гостоптехиздат, 1960, с.106-110). Недостатком известных способов очистки является их сложность в техническом исполнении в связи с использованием кислот, щелочей, а также с трудностями утилизации отходов. Известен способ регенерации ОМ с применением синтетических цеолитов с высокой избирательной способностью и большой адсорбционной емкостью (Коваленко В. П. и др. Очистка нефтепродуктов от загрязнений. М. Недра, 1990, с. 72-86). Недостатком данного способа является высокая стоимость, что ограничивает их широкое применение. Наиболее близким к предлагаемому способу (прототипом) является способ регенерации ОМ фильтрованием, отстаиванием и очисткой в центробежном поле (SU, авт. свид. N 1174666, кл. F 16 N 39/04,1985). Недостатком данного способа является низкое качество получаемого регенерированного масла. Целью предлагаемого способа является повышение качества отработанных масел после регенерации. Сущность изобретения заключается в том, что масло после фильтрации подвергают очистке щелочью и обработке природным абсорбентом и после центрифугирования из масла дополнительно удаляют механические примеси, воду и легкие углеводороды с последующей очисткой масла в электрогидроциклоне и адсорбере с использованием природного адсорбента. Регенерация отработанного моторного дизельного масла по предлагаемому способу осуществляется следующим образом (фиг.1). Отработанное моторное масло подают через грубый фильтр 1, установленный на заборном шланге, шестеренчатым насосом 2, на второй (щелевой) грубый фильтр 3 и далее в отстойный резервуар 4, снабженный нагревательным (электрическим или паровым) устройством, в котором масло нагревают до температуры 80-85oC, и затем отстаивают в течение 48 часов. После предварительного отстоя и удаления грубых механических примесей и воды регенерируемое масло самотеком через магнитный фильтр 5 сливают в емкость-коагулятор 6 с коническим дном, снабженный нагревательным и перемешивающим (механическим или воздушным) устройствами. В емкости-коагуляторе 6 масло при постоянном перемешивании и температуре 75-80oC обрабатывают 10%-ным водным раствором щелочи. В зависимости от загрязненности, расход водного раствора щелочи для коагуляции может составлять 5-7 % к объему коагулируемого масла. Контроль за ходом процесса коагуляции осуществляют нанесением капли масла на стекло через определенные промежутки времени. Начало коагуляции определяют по образованию укрупненных частиц, видимых на стекле, конец процесса определяют по прекращению роста и количества частиц. При достаточном времени контакта коагулятора с маслом и его концентрации коагуляция завершается в течение 30-40 минут, после чего масло отстаивают. Процесс отстаивания продолжается до 48 час. После спуска отстоя масло самотеком подают в резервуар 7, который по конструктивным особенностям аналогичен резервуару 6. В резервуаре 7 проводят контактную обработку адсорбентом. В качестве адсорбента используют природную отбеливающую глину (по физико-химическим свойствам близкая к гумбрину) Кумертауского месторождения Башкортостана, которая является спутником залежей бурых углей. Структурно-сорбционная способность и химический состав данного минерала показаны на деривотограмме (фиг. 2) и табл. 1. В нагретое масло до температуры 150-200oC при непрерывном и интенсивном перемешивании (1200 об/мин) вводят адсорбент и затем продолжают перемешивание в течение 30-40 мин. Расход адсорбента зависит от его активности и загрязненности масла. Установлено, что расход адсорбента для регенерации отработанного дизельного масла составляет 10-20 % от объема коагулируемого масла. С целью активизации природного адсорбента его предварительно подсушивают в сушилке с паровым обогревом при температуре 200-250oC, а затем измельчают до минимальных размеров (1-2 мм). Далее, после контактной очистки, масло отстаивают при температуре не ниже 75-80oC в течение 10-12 ч и затем сливают в отстой. Масло, очищенное щелочью и обработанное природным адсорбентом, забирается центрифугой 8, где оно дополнительно очищается от воды, механических примесей и возможно оставшихся частиц адсорбентов. После чего насосом 9 масло направляют в устройство для удаления механических примесей, воды и легких углеводородов (далее устройство). Очистку масла в устройстве (фиг.3) осуществляют следующим образом. Нагретое до заданной температуры, например, до 250oC, отработанное масло поступает в межтрубное пространство устройства и далее в щелевой кольцевой канал и вытекает из него с большой скоростью. При обтекании емкости (полусферы) масло поступает в область разрежения и вихревых потоков над емкостью, образованных за счет резкого увеличения площади проходного сечения, в результате чего из очищаемой жидкости испаряются пары воды и легкие углеводородные фракции, которые выводят через патрубок в верхней части крышки и подают в конденсатор-холодильник с емкостью разделения 12. При необходимости создания более грубого разряжения в камере устройства устанавливается эжектор или вакуумный насос 11. Механические примеси, загрязненный абсорбент за счет действия гравитационных сил выпадают внутрь полусферы, из которого затем удаляют по внутреннему трубопроводу. Жидкость, очищенная от механических примесей и загрязненного адсорбента, попадает на перфорированные пороги и продолжает очищаться от паров воды, легких углеводородных фракций (ЛУФ) и далее стекает в кольцевой сборник устройства и затем выводится через отводные патрубки. Особенность рассматриваемого устройства состоит в том, что емкость для сбора механических примесей установлена так, что она имеет возможность вертикального перемещения “вверх-вниз”, что обеспечивает регулирование щелевого зазора, следовательно, и скорости потока жидкости. Далее отработанное масло для более глубокой очистки насосом 13 подают в электрогидроциклон 14. Особенность очистителя-электрогидроциклона 14 состоит в том, что труба сливной камеры (фиг. 4) имеет также возможность вертикального перемещения “вверх-вниз”, что обеспечивает четкое разделение фаз. Кроме того, электрогидроциклон имеет электроды в форме заостренного конуса, куда подводится высокое напряжение порядка 16-24 кВ. Работа гидроциклона осуществляется следующим образом. Очищенную жидкость подают под давлением во входной патрубок. Последний располагается относительно камеры таким образом, что поток жидкости направляется по касательной к сечению корпуса в плоскости входного отверстия, благодаря чему он приобретает вращательное движение. Под действием центробежных сил и электрического поля механические частицы или капельки воды, обладающие большим удельным весом, отбрасываются на стенки корпуса, теряя скорость, частицы скользят по ним вниз по спиральной траектории. Попадая в конусную часть, они осаждаются и выводятся через нижний выходной патрубок, а очищенная жидкость отжимается к центру электрогидроциклона и выбрасывается через сливной патрубок. Во время очистки в корпусе устанавливаются два вращающихся потока жидкости: восходящий и нисходящий. Угловая скорость первого потока больше, чем второго, поэтому не успевшие отделиться на первом этапе мелкие частицы выбрасываются из него и также попадают на стенки очистителя. Таким образом, жидкость подвергается двойной очистке: предварительной при движении ее вниз и окончательной в восходящем потоке. При предварительной очистке жидкости процесс интенсифицируется электрическим полем. Механизм удаления частиц загрязнения в электрическом поле обусловлен наличием двойного электрического слоя на поверхности частиц, состоящих из высокополярных молекул и их ассоциатов. В электрическом поле такие частицы движутся к электродам. Механизм коалесценции воды в электрическом поле объясняется перераспределением нейтральных зарядов эмульгированных капель воды в диполи, которые ориентируются вдоль силовых линий поля, притягиваются друг к другу и агрегируются. Достаточно крупные капли воды выпадают в отстойную зону. Кроме индуциированных зарядов, капли и частицы при соприкосновении с электродами могут приобретать собственные заряды, под влиянием которых происходит интенсивная миграция частиц загрязнений от электрода к электроду. Этот процесс при оптимальных условиях также приводит к дальнейшей коагуляции частиц загрязнений. Интенсификация процесса удаления загрязнений способствует также и форма электродов и их расположение: электрод в форме заостренного клина обеспечивает создание большей напряженности электрического поля; расположение электродов касательно под углом 15oC обеспечивает повторный выброс не отделившихся мелких примесей в зоне размещения электродов. Интенсификация процесса очистки отработанных масел от механических примесей и воды достигается, кроме того, возможностью регулирования частоты высокого напряжения, оптимальным меж электродным расстоянием (5-7 мм), а также регулированием уровня входного отверстия сливного патрубка. Не исключается также и такое предположение, что под действием разряда тока высокого напряжения и частоты происходят процессы электроионизации, приводящие к некоторой стабилизации вязкостных характеристик, а также к уменьшению непредельных соединений по следующей схеме реакцииФизическое описание суммарного поля воздействия на загрязнения: центробежного, электрического, ионизационного и других полей возможно изложить только лишь формулой общего вида
Е=Ец+Еэ+Еи+…+Еi,
где
Ец – центробежное поле;
Еэ – электрическое поле;
Еи – ионизационное поле;
Еi – другие неизвестные и неизученные поля. Естественно, при отсутствии единого взгляда на механизм действия суммарных полей различной природы полное объяснение всех явлений процесса наука дать пока не в состоянии, хотя, как известно, действие отдельных силовых полей описываются соответствующими формулами. Из сливной трубы электрогидроциклона 14 масло насосом 15 подается для доочистки в адсорбер 16. В качестве адсорбента в предлагаемом способе также является природный адсорбент Кумертауского месторождения Башкортостана и далее масло проходит фильтр тонкой очистки 17 и подается в емкость регенерированного масла 18. Удаленные механические примеси, загрязненный адсорбент поступают в сборник шлама 19 и утилизируются. Пример. Отработанное масло (проба 1) с массовым содержанием,%: мехпримесей 0,528; воды – 0,03; золы – 1,12; коксуемостью 2,70 в количестве 0,3 м3 после грубой фильтрации нагревают, отстаивают, защелачивают, коагулируют природным сорбентом и далее нагревают до 250oC и подают в устройство для дополнительной очистки от механических примесей, загрязненной глины и воды. Вода и ЛУФ из устройства охлаждаются в конденсаторе-холодильнике, разделяются и утилизируются. Более глубокую очистку ОМ производят электроциклоном, адсорбцией и фильтрацией фильтром тонкой очистки. Вода, механические примеси, загрязнения и отработанная глина удаляются в специальный сборник и утилизируются. В результате очистки получают ОМ со следующими качественными показателями: мехпримеси – отс.; вода – отс.; зола – 0,81; коксуемость -0,99. Другие примеры и сравнительные результаты приведены в табл. 2 и 3. Анализ данных в табл. 2 и 3 показывает, что предлагаемый способ эффективней прототипа. Из данных табл. 2 и 3 следует, что механические примеси и вода удаляются полностью, коксуемость уменьшается на 10-30 %, содержание золы снижается на 7-25% по сравнению с прототипом. Таким образом, в предлагаемом способе регенерации отработанных масел принята комбинация различных способов с разработкой и применением модифицированных технических средств, позволяющих интенсифицировать процесс очистки отработанных масел. Предлагаемая технологическая схема способа регенерации может работать полностью или частично. При выборе комбинации методов учитывается характер и природа продуктов старения отработанных масел и требования, предъявляемые к регенерированным маслам. Располагая этими данными, можно определить физико-химические свойства масла, требующие исправления и, следовательно, выбрать соответствующий способ его восстановления или регенерации. Режим работы свежих масел и характер претерпеваемых ими изменений в процессе эксплуатации настолько разнообразны, что в каждом случае к выбору оптимального метода регенерации необходимо подходить аналитически. Опытно-промышленные испытания показали хорошую сходимость с результатами лабораторных исследований. Предлагаемый способ особенно легко реализуется при раздельном методе сбора ОМ по сортам (А, Б, В, Г, Д, Е) и непосредственно на местах их потребления. Установка проста в изготовлении и эксплуатации и может быть смонтирована непосредственно в местах применения масел из табельного оборудования и агрегатов, например, насосов НШ-5, центрифуги двигателя ЯМЗ- 238, корпуса фильтра ТФЧ, однако и требует некоторых сил и средств для изготовления вышеуказанных модернизированных технических средств. Предлагаемый способ может использоваться на нефтебазах, станциях технического обслуживания автотракторной техники и других предприятиях, использующих автотранспортную технику. Источники информации. 1. Шишкин П.И., Брай И.В. Регенерация отработанных масел. – М.: Химия, 1970 – 301 с. 2. Коваленко В.П., Турчанин В.Е., Очистка нефтепродуктов от загрязнений. – М.: Недра, 1990 – 160 с. 3. Авт. св. N 1174666, кл. F 16 N 39.04, БИ N 31, 1985 (прототип).
ФОРМУЛА ИЗОБРЕТЕНИЯ
Способ регенерации отработанных масел путем нагревания, фильтрации и центрифугирования, отличающийся тем, что масло после фильтрации подвергают очистке щелочью и обработке природным адсорбентом, и после центрифугирования из масла дополнительно удаляют механические примеси, воду и легкие углеводороды с последующей очисткой масла в электрогидроциклоне и адсорбере с использованием природного адсорбента.www.freepatent.ru
Регенерация отработанных минеральных Масел
ПЕРЕРАБОТКА ОТХОДОВ ПРОИЗВОДСТВА
Основную часть нефтеотходов, образующихся на промышленных и транспортных предприятиях, составляют минеральные масла. На рис. 15.3 приведены источники образования и направления утилизации отработанных масел. Масла применяются в узлах трения различных машин и механизмов для снижения коэффициента трения и износа поверхностей трущихся деталей. Смазочные масла образуют на их поверхности микропленку толщиной в десятые доли микрона, которая позволяет уменьшить износ деталей в сотни раз. Общая масса минеральных масел, поступающих в отходы в течение года во всем мире, оценивается в 40 млн. т. Из них только 20 млн. т собирается, а подвергается переработке не более 2 млн. т, что составляет не более 5% от количества образующихся отходов (табл. 15.3).
Таблица 15.3 Образование и потребление отработанных масел в некоторых странах, тыс. т/год
|
Как видно из данных табл. 15.3, отношение к отработанным маслам разное. Наиболее прогрессивные страны подвергают переработке до 30 – 38% отработанных масел, обеспечивая при этом высокую полноту их сбора, а также качество товарной продукции. Как правило, это страны, не имеющие своих источников нефтепродуктов и закупающие их за рубежом.
Образование отходов минеральных масел связано с тем, что в процессе работы машин и механизмов масло окисляется, загрязняется продуктами износа деталей, металлической стружкой и пылью. При этом происходит изменение физико-химических свойств масел ниже допустимых пределов. Наиболее загрязненными оказываются масла, слитые из картеров двигателей внутреннего сгорания.
Рис. 1S.3. Источники образования и направления утилизации отработанных масел |
Неутилизированные отработанные масла наносят непоправимый ущерб окружающей среде, отравляя воду, воздух и почву. Некоторые из них обладают канцерогенными свойствами и длительно не распадаются в естественных условиях.
В то же время отработанные масла являются сырьем для производства вторичных материалов и должны собираться с целью регенерации. По данным специалистов, выход качественных вторичных масел из отработанных составляет 60-80%, в то время как при переработке сырой нефти выход товарных масел не превышает 10%. Так, в Канаде нефтеперерабатывающая фирма “Эссо” поставляет на рынок масла, содержащие 50% регенерированных продуктов. Во Франции собирается для рекуперации ежегодно до 200 тыс. т отработанных масел. Однако в связи с тем, что затраты на регенерацию превышают стоимость свежеприготовленных масел, регенерированный продукт становится неконкурентоспособным. Выход из создавшегося положения состоит в том, что государство законодательно обязывает поставщиков смазочных масел использовать в их составе до 15% регенерированных продуктов.
В странах ЕС установлены жесткие нормы контроля за образованием и использованием отработанных масел. Любая деятельность, связанная с накоплением, транспортировкой и утилизацией отработанных масел в этих странах лицензируется. В нашей стране работы по сбору и утилизации отработанных масел ведутся с 1930 г., когда их порядок был определен приказом ВСНХ. В более поздние годы сбор и использование отработанных нефтепродуктов организовывались ВО “Вторнефтепродукт” при Госснабе СССР. В 80-х годах в стране был достигнут высокий уровень сбора и утилизации отработанных масел, который к началу 90-х годов достиг 1700 тыс. т/год. Однако в последние годы сбор и утилизация отработанных масел неуклонно снижаются (в 1994 г. сбор составил 470 тыс. т). Это приводит к все более негативному влиянию на окружающую среду.
Согласно ГОСТ 21046-86 “Нефтепродукты отработанные. Общие технические условия” отработанные нефтепродукты подразделяются на масла моторные отработанные (ММО) (в том числе трансмиссионные), масла индустриальные отработанные (МИО) и смеси нефтепродуктов отработанных (СНО).
По свойствам отработанные нефтепродукты должны соответствовать требованиям, приведенным в табл. 15.4.
Таблица 15.4 Требования к отработанным нефтепродуктам, поступающим на регенерацию
|
Временным положением о системе обращения с нефтеотходами, введенным постановлением Правительства г. Москвы с 01.01.98, Установлены шесть категорий нефтеотходов.
К 1-, 2- и 3-й категориям относятся различные масла и их смеси, пригодные для переработки или использования. К 4-й категории отнесена смесь нефтеотходов, также пригодная для переработки или использования. 5-я категория объединяет нефтеотходы, непригодные для переработки с целью дальнейшего использования и подлежащие экологически обоснованному уничтожению. К 6-й категории отнесены опасные нефтеотходы, содержащие особо токсичные компоненты (полихлорированные бифенилы, терфенилы и др.). Эти отходы должны уничтожаться на специальных установках. Согласно постановлению от 18.10.97 № 807 предприятия, осуществляющие прием, переработку и уничтожение отработанных нефтепродуктов, обязаны иметь лицензию на право проведения этих работ, а сами работы выполнять по экологически обоснованным технологиям при максимальном вовлечении нефтеотходов в хозяйственный оборот в качестве вторичных материальных ресурсов.
Методы регенерации отработанных масел подразделяются на физические, физико-химические, химические и комбинированные.
К физическим методам относятся отстаивание, центрифугирование, фильтрация, перегонка.
Отстаивание – наиболее простой и дешевый способ отделения от отработанных масел большей части воды и примесей крупных твердых частиц, осуществляется в отстойниках различной геометрии. Центрифугирование также позволяет отделить воду и твердые частицы от масла; процесс выполняется с помощью центрифуг периодического или непрерывного действия, не требует больших затрат времени и энергии. Фильтрация позволяет отделить от масла дисперсные частицы практически любых размеров, а также воду; выполняется на различных фильтрах, например фильтр-прессах.
Более прогрессивны ленточные, барабанные и дисковые вакуум – фильтры, работающие в непрерывном режиме. Фильтрующими элементами являются пористые материалы: текстиль, бумага, картон и др. Для отделения воды от масла иногда применяют сепарирующие центрифуги.
Перегонка позволяет отделить от масла легколетучие фракции, в частности бензин, попадающий в масло при неисправном двигателе. Еще более эффективна вакуумная перегонка, при которой получают в качестве дистиллята высококачественные базовые масла. Перегонка может осуществляться в несколько стадий с использованием тонкопленочного испарителя. Остаточное давление в системе составляет 8-12 кПа, температура на первой стадии составляет 218 – 260 °С, на заключительной 325 – 345 °С. Реализация метода требует специального оборудования, значительных капитальных и текущих затрат и может быть осуществлена на специализированных предприятиях.
Очень часто в регенерационной установке сочетаются несколько физических методов, например магнитная сепарация металлических частиц и фильтрация с помощью центрифуги.
Интересный опыт регенерации отработанных масел физическими методами накоплен финской фирмой “Экокем”. Отработанные масла собираются с промышленных предприятий, станций технического обслуживания автомобилей, автозаправочных станций и т. п. При переработке сначала методом центрифугирования из масла выделяют металлы и другие взвешенные частицы, затем масло фильтруют и обезвоживают. Для изготовления из образовавшегося “сырого” масла продукта, пригодного для использования в качестве смазочного материала, в него добавляют соответствующие присадки. Фирма “Экокем” на неспециализированном предприятии регенерирует в год 50 тыс. т отработанных масел.
К физико-химическим методам относятся коагуляция, адсорбция и экстракция, т. е. методы, основанные на использовании поверхностно-активных веществ, адсорбентов, экстрагентов и т. п.
Коагуляция позволяет очистить отработанное масло от загрязнений путем коагулирования (укрупнения) частиц. Для этих целей применяют электролиты, поверхностно-активные вещества, некоторые высокомолекулярные соединения с гидрофильными свойствами и др.
Наиболее эффективным коагулянтом является метасиликат натрия. В промышленности при очистке масел применяют 30%-ные (масс.) водные растворы этого соединения. Расход его составляет 5% (масс.) от отработанного дизельного масла и 3 % от отработанного индустриального масла. На процесс влияют интенсивность и продолжительность перемешивания, температура масла и другие факторы. Адсорбция используется для окончательной очистки и проводится с помощью отбеливающей глины, силикагеля, алюмосиликатов и других веществ. Для осуществления процесса необходимо специальное оборудование: периодические или непрерывные адсорберы. Экстракция применяется для разделения на фракции отработанных масел с помощью селективных растворителей, т. е. таких веществ, которые способны избирательно растворять те или иные компоненты смеси. В частности, экстракционная очистка отработанных масел проводится с помощью пропана, который растворяет собственно масло и не растворяет асфальто-смолистые вещества, образовавшиеся при его эксплуатации и старении.
К химическим методам регенерации масел относятся очистка отработанных масел с помощью кислоты или щелочи, а также осушка и гидрогенизация.
Осушка производится с помощью негашеной извести и других водопоглощающих веществ, а гидрогенизация – путем обработки масла водородом на поверхности катализатора. В результате гидрогенизации непредельные углеводороды превращаются в предельные, что приводит к очистке масла от примесей и повышению его стабильности при эксплуатации. Эта технология требует значительных капитальных и текущих затрат.
Комбинированные методы регенерации заключаются в сочетании нескольких названных выше приемов очистки.
Технология, разработанная специалистами Белградского нефтеперерабатывающего завода и основанная на комбинации различных методов, включает следующие стадии переработки отработанных минеральных масел: термическую обработку, экстракцию растворителем, каталитическую гидрообработку и вакуумную перегонку. При термической обработке из отработанного масла удаляются вода и легкие фракции и агломерируются продукты деструкции масла. При экстракции растворителем из масла удаляются отработавшие ресурс добавки и продукты распада масел, образовавшиеся при их эксплуатации.
Во время каталитической гидрообработки масло стабилизируется перед последующей перегонкой на вакуумной установке. Тяжелые фракции, оставшиеся после дистилляции, а также легкий дистиллят используются как добавка к битумам или в качестве топлива. Полученные в результате дистилляции масла не уступают по качеству первичному базовому продукту и после добавления необходимых присадок, загустителей и других компонентов являются ценной товарной продукцией.
В ряде случаев для регенерации отработанные масла смешиваются с сырой нефтью и полученную смесь перерабатывают по полной технологической схеме. Метод прост, но высокая зольность и содержащиеся в масле присадки отрицательно влияют на работу технологического оборудования. Поэтому его применение допустимо только в очень ограниченных количествах (не более 1% отработанных масел от сырой нефти).
При массовой регенерации масел, когда смешиваются масла различных марок, необходимо полное удаление всех видов присадок, даже тех, которые не полностью исчерпали свой ресурс.
Отечественной промышленностью выпускается ряд комплектных установок для регенерации различных масел. Среди них есть промышленные стационарные установки с большой производительностью и небольшие установки, предназначенные для очистки масел на транспортных и промышленных предприятиях.
В связи с сокращением объемов сдачи отработанных масел предприятиям ГАО “Вторнефтепродукт”, особую актуальность приобрела очистка и регенерация масел на местах их образования. Поэтому особый интерес представляют регенерационные установки небольшой мощности, работающие в периодическом режиме. В табл. 15.5 приведены характеристики некоторых регенерационных установок для очистки различных масел.
Работа установки УПТМ-8К основана на использовании физических и физико-химических методов регенерации: фильтрации, коагуляции, отстаивания, выпаривания (рис. 15.4). В процессе работы установки отработанное масло насосом 2 через фильтр грубой очистки 1 и теплообменник 27 подается в электропечь 16, в которой нагревается до 200 °С, и далее поступает в испаритель 17, где из масла удаляются вода и легколетучие фракции. Затем масло с помощью насоса 26 поступает в смеситель 14, куда из емкости 10 Насосом 13 подается 20%-ный раствор коагулянта в количестве 2 – 3% от массы поступающего на переработку масла. Перемешанное с коагулянтом масло поступает в автоклав-отстойник 15, где происходит отстаивание продукта и удаление коагулированных частиц. Затем из автоклава-отстойника масло поступает во второй испаритель 23 для удаления следов воды. С нижней его части масло насосом 24 через теплообменник 27 и холодильник 28 перекачивается в контактную мешалку 6, а затем – в фильтр-пресс 9 для проведения контактной доочистки отбеливающей глиной и удаления механических примесей с размером частиц более 1-2 мкм. Очищенное масло паступает в двухсекционную емкость 5, откуда насосом 4 перекачивается в емкости регенерированного масла либо возвращается на повторную очистку. Для получения технологических масел предусмотрен фильтр тонкой очистки 29. В этом случае масло после испарителя 23, минуя контактную мешалку 6 и фильтр-пресс 9, подается на фильтр тонкой очистки 29, затем – в двухсекционную емкость 5, откуда перекачивается в резервуары регенерированного масла.
Таблица 15.5
|
Технические характеристики установок для регенерации отработанных масел |
МЕТАСИЛИКАТ НАТРИЯ |
МАСЛО РЕГЕНЕРИРОВАННОЕ |
Рис. 15.4. Функциональная схема установки УПТМ-8К: |
1- фильтр грубой очистки; 2, 8, 13, 24, 26 – насос-дозатор НД; 3 – агрегат электронасосный; 4 – узел выдачи готовой продукции; 5 – емкость двухсекционная; 6 – Мешалка контактная; 7 – насос плунжерный; 9 – фильтр-пресс; 10 – емкость приготовления коагулянта; 11 – насос ХМ; 12 – фильтр грубой очистки; 14 – смеситель; 15 – автоклав-отстойник; 16 – электропечь; 17 – испаритель; 18 – насос вакуумный BBHl-1,5; 19 – сборник отгона; 20, 21 – холодильник-конденсатор; 22 – Адсорбер; 23 – испаритель; 25 – холодильник; 27 – теплообменник; 28 — холодильник;
29 – фильтр тонкой очистки
Установка УРММ-50, предназначенная для регенерации моторных масел, позволяет также перерабатывать в полноценные продукты индустриальные и турбинные отработанные масла. Работа установки основана на последовательном сочетании методов коагуляции, отстаивания, фильтрации и адсорбции. В ее состав входит следующее оборудование: емкость для приготовления коагулянта, мешалка-отстойник, фильтр-водоотделитель, фильтры грубой и тонкой очистки масла, насосы, расходные и накопительные емкост
msd.com.ua
Регенерация отработанных масел
Методы регенерации отработанных масел
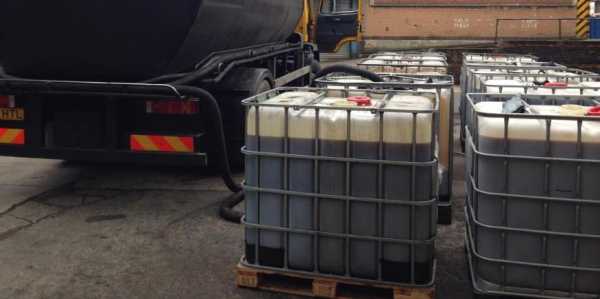
В течение срока использования моторных и индустриальных масел в них начинают накапливаться продукты окисления, загрязнения и др. примеси, которые резко снижают качество масел. Масла с загрязняющими примесями должны быть заменены свежими. Отработанные масла собирают и подвергают регенерации с целью сохранения сырья – это экономически выгодно.
В зависимости от процесса регенерации получают 2-3 фракции базовых масел, из которых компаундированием и введением присадок могут быть приготовлены товарные масла (моторные, трансмиссионные, гидравлические), а также СОЖ и пластичные смазки. Средний выход регенерированного масла из отработанного, содержащего около 2-4 % твердых загрязняющих примесей, воду и до 10 % топлива, составляет 70-85 % в зависимости от применяемого способа регенерации.
Для восстановления отработанных масел применяются разнообразные технологические операции, основанные на физических, физико-химических и химических процессах. Они заключаются в обработке масел с целью удаления из них продуктов старения и загрязнения.
В качестве технологических процессов обычно соблюдается следующая последовательность методов:
- Механический: для удаления из масла свободной воды и твердых загрязнений
- Теплофизический: выпаривание, вакуумная перегонка
- Физико-химический: коагуляция, адсорбция
Если этого недостаточно, используются химические способы регенерации масел, связанные с применением более сложного оборудования и, соответственно, большими затратами.
Физические методы позволяют удалять из масел твердые частицы загрязнений, микрокапли воды и, частично, смолистые и коксообразные вещества, выпаривание – легкокипящие примеси. Масла обрабатываются в силовом поле с использованием гравитационных, центробежных, электрических, магнитных и вибрационных сил, производится фильтрование, водная промывка и вакуумная дистилляция. К физическим методам очистки отработанных масел относятся также различные массо- и теплообменные процессы, которые применяются для удаления из масла продуктов окисления углеводородов, воды и легкокипящих фракций.
Отст
www.mirsmazok.ru
Способ регенерации отработанных нефтяных масел и их смесей
Использование: регенерация отработанных нефтяных масел и их смесей. Сущность: обработка отработанных нефтяных масел и их смесей 15-20%-ным водным раствором метасиликата натрия с модулем 0,5-0,9 в количестве 5-7% от массы отработанного масла при перемешивании в течение 25-30 мин с отстаиванием, центрифугированием и последующим вакуумированием при 80-90oС и остаточном давлении 100 мм рт.ст. в течение 20-30 мин. Технический результат: способ позволяет повысить чистоту регенерированного масла по упрощенной технологии. 1 табл.
Изобретение относится к регенерации отработанных нефтяных масел и их смесей и может быть использовано во всех отраслях народного хозяйства, применяющих смазочные масла – автомобильные, дизельные, индустриальные, трансформаторные и др., а также гидрожидкости.
Восстановление свойств отработанных масел, особенно моторных, связано с определенными трудностями, которые вызваны присутствием в них тонкодисперсных и агрегативно устойчивых продуктов загрязнения и износа поверхностей трения. Присадки, добавляемые в товарные масла для улучшения их эксплуатационных свойств, осложняют процесс регенерации присутствием моющих компонентов. Если сырьем для регенерации служит смесь моторных или индустриальных масел, многое зависит от качества сбора. В этих случаях необходима предварительная обработка активными веществами с последующим отстоем, фильтрацией, адсорбцией и другими стадиями процесса. В результате может быть получен базовый продукт для дальнейшего его использования по назначению. Для регенерации отработанных нефтяных масел применяют различные способы очистки. При физических способах очистки (отстой, сепарация, фильтрация) из отработанных масел удаляют механические примеси. Химические способы включают кислотную и щелочную очистку, требующую промывку водой от электролита, что дополнительно обводняет масло, ухудшая его качество. Регенерацию отработанных масел также осуществляют на адсорбентах (естественных и искусственных) при повышенных температурах. Используют адсорбент с влажностью 7-10%. Обработку адсорбентом проводят в неоднородном электрическом поле переменного тока в присутствии полиметилсилоксановой жидкости (SU 875845 А, 1981). Перколяционная очистка отработанных индустриальных масел кислотно-активированными сорбентами также дает положительный результат (SU 1162869 А, 1985). Для осуществления этих способов регенерации требуются дорогостоящие активированные сорбенты и сложное аппаратурное оформление. Однако при этом не достигается высокая степень очистки без предварительной обработки сырья разделяющим агентом. Известен способ регенерации отработанных масел, заключающийся в добавлении в нагретую до 90oС смесь разделяющего агента – металлической соли динонилнафталинсульфокислоты с последующим отстоем и разделением образующихся слоев (DE 2507270 А, 1977). В качестве разделяющего агента при регенерации отработанных нефтяных масел используют также водные растворы неорганических солей карбоната натрия, тринатрийфосфата с последующим разделением образующихся слоев (FR 2307035 А, 1976), а также аминоспиртов например, моно-, ди-, триэтаноламина, 3-аминобутанола, 1,1-амино-2-пропанола в количестве 0,5-1 мас. % в зависимости от количества исходного сырья (SU 522227 А, 1976) или смесь аминоспирта с изопропиловым спиртом (RU 2076898 С1, 1997). Однако применяемые для восстановления свойств отработанных нефтяных масел известные разделяющие агенты являются неэффективными, оставляют в маслах сильнощелочную или сильнокислую реакцию, что влечет за собой необходимость их дополнительной обработки. Кроме того, они не позволяют удалить тонкодисперсные примеси и продукты окисления, находящиеся в коллоидном состоянии. Более эффективным является использование ортофосфорной кислоты (RU 2094450 С1, 1997) или смеси ее с органической кислотой (RU 2153527 С1, 2000), позволяющих очистить индустриальные масла до степени осветления 93-97%, а при дальнейшей обработке осушителями – до 98-99%. Также достаточно эффективной является обработка отработанных масел 30-50%-ным водным раствором карбамида при давлении 0,6-1,0 МПа с последующим направлением обработанного масла в дросселирующее устройство, отстаиванием и центрифугированием (RU 2078127 С1, 1997). Однако и эти способы оставляют в маслах достаточно сильную кислую или щелочную реакцию, а также достаточно большое содержание смолистых веществ. Недостатками известных способов регенерации нефтяных масел является также сложность технологии, обусловленная необходимостью использования труднодоступных кислот, ухудшающих к тому же экологию, и многостадийность стадии очистки вследствие необходимости использования осушителей для получения товарного индустриального масла, а также обработка исходного масла под давлением и в дросселирующем устройстве. Известен способ регенерации отработанных промышленных масел металлургических производств обработкой их водным раствором метасиликата натрия в количестве 0,6-1,2% от массы масла с кислотным числом до 3 мг КОН/г или смесью его с водным раствором карбоната натрия при 80-85oС и перемешивании в течение 30 мин (SU 979496 А, 1982). Поскольку по известному техническому решению регенерации подвергали маслосодержащие производственные отходы металлургического производства, то отходы содержали большое количество кислых стоков, а для регенерации использовали 40-50%-ный раствор метасиликата натрия с модулем не ниже 1. Позволяя снизить в отработанных промышленных стоках количество загрязнений, известный способ при использовании его для регенерации отработанных нефтяных масел является неэффективным, т.к. не позволяет получить очищенные нефтяные масла на уровне товарного по всем необходимым показателям. Ближайшим аналогом заявленного способа является способ регенерации отработанных нефтяных масел, в частности смазочных масел, нагреванием до 80-90oС и обработкой при этой температуре и перемешивании в смеси с 0,01-0,6% от массы масла водным раствором соли щелочного металла, в качестве которого используют 6%-ный раствор метасиликата натрия с последующим добавлением 10-20%-ного раствора мыла в количестве 0,01-0,50% от массы масла и коагулянта – 5-10%-ного водного раствора полиакриламида, или карбоксиметилцеллюлозы, или неонола К 2125-20, взятого в количестве 0,01-0,30% от массы масла с последующим отстаиванием и фильтрацией (RU 2133262 С1, 1999). Недостатком известного способа являются сложность технологии, обусловленная многостадийностью и длительностью обработки отработанного масла, составляющей 60-100 мин, а также использование большого числа химических реагентов, что ухудшает экологию. Задачей настоящего изобретения является регенерация отработанных масел или смеси масел по упрощенной технологии. Согласно изобретению предлагается способ регенерации отработанных нефтяных масел и их смесей обработкой их 15-20%-ным водным раствором метасиликата натрия с модулем 0,5-0,9 в количестве 5-7% от массы отработанного масла при температуре 75-85oС и перемешивании в течение 25-30 мин с последующим отстаиванием, центрифугированием, вакуумированием при 80-90oС и остаточном давлении 100 мм рт. ст. в течение 20-30 мин и фильтрацией. Очищаемое масло (после отстоя и разделения) подвергают вакуумной дегазации с целью удаления растворенных в масле газов и легкокипящих продуктов окисления. Для получения определенных марок масел, когда сырьем являются индивидуальные отработанные масла (собранные отдельно), технологический процесс предусматривает следующие дополнительные стадии: центрифугирование, адсорбцию, фильтрацию, смешение с присадками. Процесс регенерации проводят в цилиндрическом реакторе с конусным днищем, снабженном обогревающим и перемешивающим устройствами, с нижним сливом водогрязевого шлама. Сырье (отработанное масло) после грубой фильтрации закачивают в реактор, нагревают до температуры 75-85oС, дозировано подают в него при перемешивании водный раствор метасиликата натрия заданной концентрации. Перемешивание полученной массы длится 20-30 мин, после чего проводят отстой при температуре 30-40oС в течение 10-12 мин. Появление четкой границы отстоя позволяет слить шлам полностью. Отслоенное масло (через центрифугу) подают на дегазацию в вакуумный реактор, где в течение 20-30 мин при температуре 80-90oС и остаточном давлении 100 мм рт. ст. происходит удаление растворенных отработанных газов, следов воды и легкорастворимых окисленных продуктов. Согласно описанной технологии были подвергнуты регенерации образцы отработанных моторных, индустриальных и смеси моторных масел с исходными показателями качества. Пример 1. Отработанное моторное масло марки М-10 Гк обработано 20%-ным водным раствором метасиликата натрия с модулем 0,5 в количестве 7% от веса масла при температуре 85oС и перемешивании в течение 25-30 мин. После отстоя и центрифугирования масло подвергали вакуумированию при температуре 90oС и остаточном давлении 100 мм рт.ст. в течение 20 мин. Адсорбционная очистка и фильтрация завершали процесс регенерации основы. Компаундированием с присадками получено регенерированное масло М-10 Гк, соответствующее по качеству показателям ГОСТа. Выход готового продукта составил 85%. Пример 2. Регенерации подвергали отработанное индустриальное масло ИГП-38. Отработанное масло обрабатывали 15%-ным водным раствором метасиликата натрия с модулем 0,7 в количестве 5% при температуре 75-80oС и перемешивании в течение 30 мин. После отстаивания, центрифугирования и вакуумирования при 80oС и остаточном давлении 100 мм рт.ст. в течение 30 мин, фильтрации и смешения с присадками получено масло на уровне товарного. Выход готового продукта – 90%. Использование метасиликата натрия с модулем 0,9 приводит к аналогичному результату. Использование метасиликата натрия с модулем 1 нецелесообразно, т.к. приводит к повышенной щелочной реакции. Пример 3. В качестве сырья использовали смесь моторных масел (группа ММО). Регенерацию проводили по технологии, приведенной в примере 1. Получена основа регенерированного моторного (карбюраторного) масла с вязкостью при 100oС порядка 8 сст., которая после смешивания с соответствующими присадками может быть использована по определенному назначению. Выход готового продукта – 75%. Физико-химические характеристики образцов отработанных и регенерированных масел по примерам 1, 2, 3 приведены в таблице. Использование предложенного способа для регенерации масел и их смесей позволяет снизить кислотное число до 0,08-0,1 мг КОН/г (против 0,25-0,5 мг КОН/мг по известному способу SU 979496), а содержание смолистых веществ – до 2,0-2,5% (против 4,1-4,5% по известному способу SU 979496). В соответствии с данными таблицы регенерированное моторное масло М-10 Гк по качеству соответствует показателям ГОСТ 8581, регенерированное масло ИГП-39 может быть использовано в качестве рабочей жидкости для гидравлических систем, а регенерированная смесь моторных масел может быть использована как база для дальнейшего смешения с присадками в производстве смазочных масел.Формула изобретения
Способ регенерации отработанных нефтяных масел и их смесей обработкой водным раствором метасиликата натрия при температуре 75-85oС при перемешивании с последующим отстаиванием и фильтрацией, отличающийся тем, что обработку ведут с использованием 15-20%-ного водного раствора метасиликата натрия с модулем 0,5-0,9 в количестве 5-7% от массы отработанного масла при перемешивании в течение 25-30 мин, после отстаивания масло подвергают центрифугированию, а после центрифугирования масло подвергают вакуумированию при температуре 80-90oС и остаточном давлении 100 мм рт.ст. в течение 20-30 мин.РИСУНКИ
Рисунок 1www.findpatent.ru
Способ регенерации | Цель | Технологические особенности |
Физико-механические способы | ||
Отстаивание | Удаление твердых примесей, капель воды, смолистых и коксообразных веществ | Способ основан на процессе естественного осаждения механических частиц и воды под действием силы тяжести и разницы в плотности веществ |
Выпаривание, вакуумная дистилляция | Удаление легкокипящих примесей | Способ основан на изменении температуры масла, либо при вакуумной дистилляции на испарении легкокипящих веществ в среде вакуума |
Фильтрация | Удаление частиц механических примесей, смолистых и коксообразных веществ | Способ основан на фильтрации масел через сетчатые или пористые фильтрующие элементы. Фильтрующими материалами могут выступать металлические и пластмассовые сетки, войлок, ткань, бумага, керамика |
Центробежная очистка | Удаление механических примесей и воды | Способ основан на разделении различных фракций неоднородных смесей под действием центробежной силы в центрифугах. |
Физико-химические способы | ||
Коагуляция | и селективное растворение содержащихся в масле загрязнений | Способ основан на укрупнении частиц загрязняющих веществ, находящихся мелкодисперсном состоянии, что достигается с помощью специальных веществ – коагулятов |
Адсорбция | Удаление мелкодисперсных частиц | Способ основан на способности адсорбентов, удерживать загрязняющие продукты на своей поверхности и на поверхности и в порах. Адсорбентами могут быть вещества как природного (глины, бокситы, природные цеолиты) так и искусственного (окись алюминия, алюмосиликатные соединения)происхождения |
Ионно-обменная очистка | Удаление мелкодисперсных частиц | Способ основан на способности ионитов (ионно-обменных смол) задерживать загрязнения, диссоциирующие в растворенном состоянии на ионы |
Селективная очистка | Удаление кислотных загрязнений, и некоторых других химических соединений, ухудшающих вязкостно-температурные свойства масел | Способ основан свойстве отдельных веществ загрязняющих масло (кислородных, сернистых и азотных соединений) выборочно растворяться под действием определенных реактивов |
Химические способы | ||
Сернокислотная очистка | Удаление химических загрязнений | Способ основан на взаимодействии веществ, загрязняющих отработанное масло, и вводимых в это масло серной кислоты |
Гидрогенизация | Удаление химических загрязнений | Способ основан на взаимодействии веществ, загрязняющих отработанное масло с водородом |
sil-trans-form.ru
Регенерация – отработанное масло – Большая Энциклопедия Нефти и Газа, статья, страница 1
Регенерация – отработанное масло
Cтраница 1
Регенерация отработанных масел проводится следующим образом. В сырьевую емкость для отработанного масла вводится коагулятор ( до 3 %), масло перемешивается при температуре около 70 С. Затем отработанное коагулятором масло поступает в емкость для нейтрализации кислых продуктов основной средой, например кальцинированной содой, с последующей промывкой водой. Промытое масло в виде эмульсии подается в печь для отгона горючего, после чего оно контактирует с адсорбентом, а затем подается на фильтрацию, которая благодаря применению коагуляторов, протекает весьма эффективно. [1]
Регенерация отработанных масел дает не только большую экономию средств, но и освобождает большое количество нефти для производства не менее ценных нефтепродуктов, а также значи – тельно сокращает транспортировку свежих масел с нефтеперера – батывающих заводов к местам потребления. [2]
Регенерация отработанного масла имеет целью восстановление последнего. Фактически, однако, всякая регенерация представляет собой не восстановление продуктов распада и окисления углеводородов, а удаление их из масла вместе с примесями механического порядка. Следовательно, вопрос о глубине регенерации сводится только к тому в какой степени применяемая технология переработки обеспечивает удаление из масла продуктов его старения в различных стадиях их образования. [3]
Регенерация отработанных масел из газогенераторных двигателей может быть осуществлена на ЦКФ после предварительной обработки масла на установке 3 % жидкого стекла ( удельного веса 1 8) при температуре масла 90 и 15-мин. [4]
Регенерация отработанных масел по этой схеме происходит следующим образом. Масло из отстойника ( на рисунке не показано) забирается скальчатым насосом 2 и подается в конденсатор-теплообменник 5 труба в трубе. Одновременно перед скальчатым насосом в приемный трубопровод через дозатор 1 из водяного бачка 4, подается вода. Количество воды, подаваемой в масло, обычно берется 40 – 50 % от количества находящегося в масле-горючего. [5]
Регенерация отработанных масел является одним из лучших способов сохранения масляных – ресурсов. [6]
Регенерация отработанных масел с помощью простого отставания от воды и шлама в подогреваемых отстойниках недостаточна. Регенерированные таким способом масла не могут быть снова использованы в качестве масел для двигателя. Для хорошей регенерации масел требуются специальное оборудование и квалифицированные кадры. [7]
Регенерация отработанных масел достигается обработкой их адсорбентами, в частности коллоидально раздробленным графитом. С помощью меченой кислоты показано, что такая обработка удаляет только 40 % присутствующего количества кислоты. Далее установлено, что некоторые комбинации органических кислот с другими органическими соединениями вызывают высокую электропроводность изоляционных масел. [8]
Регенерация отработанных масел на этой установке заключается в основном в нагреве их до требуемой температуры ( 115 – 125 С для обводненных и 70 – 80 С для необводненных), обработке отбеливающей глиной в мешалке и последующей фильтрации. Предварительно отстоенное отработанное масло сырьевым насосом подают из отстойника в дополнительную емкость. Отсюда оно за-качивается скальчатым насосом в электропечь, где нагревается до температуры, обеспечивающей удаление воды. [10]
Регенерация отработанных масел с применением контактной очистки используется в США, Индии, Англии, Германии и во многих других странах. [11]
Регенерация отработанных масел ВМ-4 в зависимости от содержания в них воды осуществляется следующим образом. [13]
Регенерацию отработанных масел производят предприятия Глав-нефтеснабсбыта. [14]
Для регенерации отработанных масел разработано большое количество различных аппаратов и установок, начиная от простейших с ручным управлением типа ВИМЭ-Б ( 1942 г.) и кончая современными установками, полностью автоматизированными, использующими глубокий вакуум и электрическое поле. [15]
Страницы: 1 2 3 4
www.ngpedia.ru
Добавить комментарий