Получение синтез газ – Synthesis gas – an alternative way of obtaining
Synthesis gas – an alternative way of obtaining
Synthesis gas – an alternative method of processing natural gas and associated oil.
Absolutely new, efficient and low cost alternative method of processing natural or associated gas into synthesis gas. Relatively small reactors for producing synthesis gas, suitable for transport, which can be installed near the gas and oil fields.
The synthesis gas
Description of the problem
Traditional methods for producing synthesis gas
Alternative Preparation
Benefits
The synthesis gas:
The synthesis gas (sigaz) – gas mixture, the main components are CO (oxide carbon) and n2 (hydrogen). Depending on the method of producing synthesis gas ratio of CO:n2 it ranges from 1:1 to 1:3. In direct proportion to the raw materials used and the method of its component ratio in the synthesis gas varies widely. Usually, the percentage of substances in the raw crude synthesis gas include:
- CO – 15-18%
- h3 – 38-40%
- Ch5 – 9-11%
- CO2 – 30-32%
It is worth noting, that this ratio is very rough, because the temperature increase in the synthesis process can be increased amount of CO, and increasing the pressure can increase the content of H2 and CH4.
Also, syngas addition of these substances may contain other substances – inert gas (N2) and sulfur-containing compounds (h3S), if the feedstock containing sulfur. From the unnecessary presence of the synthesis gas substances such as the carbonic Heating sulfur disposed of by purification.
Description of the problem:
In Russia, mainly associated oil gas is burned. According to the calculations of the Ministry of Natural Resources, because of this country annually loses over 139 billion rubles. Besides, burning harms ecology. The solution to this problem lies in the effective processing of natural gas and associated oil – found an alternative way – the synthesis gas.
Traditional methods for producing synthesis gas:
There are several methods for producing synthesis gas.
Traditionally, it is produced from natural gas (methane), interacting with steam. This reaction between water vapor and methane is carried out at an elevated temperature (800-900 degrees) and pressure in the presence of nickel catalysts. The formula of this process:
Ch5 + h3O → CO + 3h3 .
But dowry production method has a large negative – for the implementation of this process requires large amounts of heat, which is obtained by burning large quantities of natural gas with carbon dioxide emissions weighty in atmosphere. It is expensive, and a negative impact on the environment.
Another method – the production of synthesis gas by oxidation of methane with oxygen. But pure oxygen is an expensive product, which leads to a sharp increase in the cost of manufacturing a synthesis gas.
Alternative Preparation:
Absolutely new, alternative, efficient and low cost method of obtaining consists in the production of synthesis gas based on a ceramic membrane reactors with mixed oxygen and electron conducting. This allows to combine the release of oxygen from the air, and oxidation of methane in a single process. This more compact technology, than conventional (reacting methane with water), to avoid the explosion of oxygen by reacting with methane. Relatively small reactors for producing synthesis gas, suitable for transport, which can be installed near the gas and oil fields, that allows the use of associated petroleum gas and on the spot to get out of it diesel, methanol, paraffin e pr. raw materials for chemical industry.
Benefits:
– economy,
– environmental friendliness,
– mobility.
RECOMMENDATIONS FOR THE USE OF TECHNOLOGY
CALL: +7-908-918-03-57
or use the search analogue technologies:
The unique technology SEARCH
or write to us here…
card site
To come in check in
Victor PotekhinI received a question regarding pyrolysis plants for MSW incineration. answered. In particular, explained, that there are different pyrolysis installation: for combustion 1-4 hazard class and the rest. Accordingly, different technologies and prices.
2018-05-18 11:06:55Victor PotekhinWe receive a lot of requests for purchase of various goods. We do not sell or produce. But we maintain relationships with manufacturers and can recommend, give advice.
2018-05-18 11:08:11Victor PotekhinArrived in question hydroponnomu green feed. answered: we do not sell it. Asked to leave the application in the comments to, to its producers have fulfilled this request.
We receive a lot of questions about technology. Please ask these questions below in the comments to records.
2018-05-23 07:24:36Andrey-245Not quite clear. This battery can not be charged at all or something? How many volts it produces? Where to buy? And is it possible to connect such series-parallel, collecting a normal battery, eg, for electric vehicle?
2018-08-23 10:09:48SergeyShefgood afternoon! Interesting the above installation. How can it be ordered ? What are the terms of cooperation from the author?
2018-08-27 17:07:42Victor PotekhinSergei, throw a link here to install. Or e-mail me [email protected]
2018-08-27 18:52:14SergeyShefI have asked you, how and where it can be bought?
2018-08-27 21:07:41SergeyShefWho made the sample, that you in the photo and whether to make to order?
2018-08-27 21:10:05Victor Potekhincan not understand, that during installation. throw off the link here
2018-08-27 23:15:16Victor PotekhinWe do not possess such information
2018-08-28 21:45:17NPC-soundgood afternoon! SergeyShef product similar to, It is represented title, and in principle, any article of the LTCC technology can be made at our factory JSC “NPC “SpetsElektronSistemy”. We are in g. Moscow. You can write me an email [email protected]
2018-08-29 18:41:34NPC-soundIn our production there are probably the most complete set of equipment in Russia, which allows 3D micro, including LTCC technology, in a closed loop, from incoming inspection of materials, all intermediate production processes …
2018-08-29 18:47:20JahanCryogels for plant growth and development under adverse conditions. who produce, how to find, to buy?
you can buy from the manufacturer
2018-09-01 20:58:09Andrey-245Hello, Victor. I asked the question (2018-08-23) I meant about carbon battery, which serves as a 100 years old.
2018-09-18 12:15:33Victor Potekhinall information, that is, on the battery, It is written in the corresponding article.
2018-09-18 20:47:11Victor PotekhinTo get information about site technology manufacturers, write the bottom of the page – in FaceBook comments
2018-09-29 20:58:40DenssikAll the good days! I’m head of the center which developed the robot, on all matters concerning cooperation can write to the post office [email protected]
2018-10-03 17:19:46Victor PotekhinDenssik, Write pzhl about any work in question?
2018-10-03 19:10:33DS-Surfer If anyone there interested in “COMPLEX WATER BY hydrowave”, I beg to contact me: [email protected] Sergei.The settings are made and implemented. 2018-11-07 12:23:40vasagov
good afternoon.
I am interested in the technology of processing of APG.
Please send your contact information to [email protected]
To post messages in the chat you need to login
syngas
the synthesis gas
production of synthesis gas
methanol synthesis from synthesis gas
carbon dioxide synthesis gas
methane synthesis gas
the synthesis gas
ammonia synthesis gas
preparation of methanol from synthesis gas
synthesis gas reaction
the synthesis gas compressor
synthesis gas water
coal syngas
synthesis gas reactor
the use of synthesis gas
synthesis gas plant
protein synthesis gas
fuel gas synthesis synthesis
the use of synthesis gas
syngas prepared from
syngas preparation and use
ester synthesis gas
syngas composition
Synthesis gas purification
syngas formula
gas and syngas
syngas kursovaya
gasoline synthesis gas
industrial production of methanol synthesis gas
obtaining coal syngas
synthesis gas properties
Recycling synthesis gas
syngas production of methanol used
conversion methane synthesis gas
synthesis gas for producing methanol is produced by reacting
the production of methanol from synthesis gas
methods for producing synthesis gas
Carbohydrate synthesis carbon dioxide water
synthesis gas generators
Synthesis gas is a mixture of
methods for producing synthesis gas
production of synthesis gas of natural gas
producing synthesis gas technology
syngas from wood
production of synthesis gas from methane
TNK synthesis gaz 32
apparatus for producing synthesis gas
Unlike the synthesis gas
physical properties of the synthesis gas
accident centrifugal compressor synthesis gas
factor demand 738
comments powered by HyperCommentsПолучение синтез-газа из смешанных твердых отходов
Одним из основных преимуществ газификации для конверсии отходов является то, что этот процесс требует небольшой предварительной обработки или сортировки исходных материалов. В настоящее время, во многих процессах газификации пластиковые и резиновые отходы перерабатываются одновременно с другими твердыми отходами. В этой статье описываются некоторые процессы, которые используются в настоящее время для газификации смешанных твердых отходов.
Один из известных процессов основан на высокотемпературной газификации для конверсии твердых отходов, таких как муниципальные твердые отходы, осадок сточных вод, остатки производства, пластмассовые отходы, и т. д. Сырье газифицируется при давлениях до 30 атмосфер и температурах от 800 до 1100 С в псевдо-сжиженном слое с кислородом или воздухом, подаваемыми в газификатор с помощью шнекового питателя. Использование воздуха или кислорода зависит от требуемого качества добываемого газа. Продукты представляют собой синтез-газ и остаток, содержащий непрореагировавший углерод и золу, которые удаляют с помощью шнека, расположенного в нижней части газификатора. Детальный анализ полученных продуктов на демонстрационных заводах показал, что диоксины и другие опасные смечи отсутствуют, и считается, что это связано с наличием восстановительной среды в газификаторе. По сравнению с обычными процессами сжигания отходов этот метод приводит к образованию меньшего объема углекислого газа.
Экспериментальные заводы работают и собирают информацию с середины 1980-х годов, разрабатывая процессы газификации отходов при условиях атмосферного давления. Газификация сырья данного метода происходит в циркулирующем псевдо-сжиженном слое работающих при атмосферном давлении и температурах в диапазоне 850-900 С с воздухом в качестве кислорода и флюидизирующего агента. Газ, выходящий из газификатора, подают во второй реактор где он контактирует с псевдо-сжиженным слоем соединяясь с более легкими компонентами с помощью катализатора. Образующийся HC1 поглощается кальцинированным доломитом с образованием CaCl2, который далее удаляется в нисходящем фильтре.
Процесс термической-селекции – еще одна интересная альтернатива, разработанная для получения газа из отходов. Отходы сначала сжимаются и уплотняются, чтобы увеличить объемную плотность, удалить воздух внутри отходов и гомогенизировать материал. Впоследствии отходы подают в канал пиролиза, где он дегазируются и термически разлагаются, при постепенном увеличении температуры до 600 С и временем протекания реакции около 2 часов. Продукты пиролиза поступают в газификатор, где они реагируют с кислородом и паром. Органические компоненты превращают в синтез-газ, который выходит из реактора при 1200 С, в то время как неорганическая часть превращается в жидкую фазу расплава в нижней части газификатора при 2000 С, и медленно течет в гомогенизационный реактор. Время пребывания газовой фазы в газификаторе составляет около 2-4 с, тогда как жидкая расплавленная фаза остается на время около 5 мин. Синтез-газ подвергается резкому охлаждению при контакте с водой чтобы предотвратить возможное образование диоксинов, фуранов и других нежелательных органических соединений, а также для поглощения большей части присутствующего HCl. Дальнейшая очистка и обработка применяется к синтез-газу для удаления мелких частиц, h3S, воды пара и т. д.
Другие процессы газификации, разработанные для преобразования различных типов отходов, были описаны во множестве литературы, тогда как наиболее релевантные коммерчески подходящие процессы описаны в большинстве случаев в патентах, а также их можно найти в работах Хофмана.
Другие процессы частичного окисления отходов пластика и отходов каучука
Частичное и контролируемое окисление полиолефиновых отходов пластиков используется для сшивания полимеров и повышения их физических свойств, улучшения их технологичности. Существует ряд публикаций по обработке полиэтилена и полипропилена различными пероксидами, которые обычно приводят к увеличению температуры плавления полимера и сужение молекулярно-массового распределения. С другой стороны, в термической деградации полиолефинов, хорошо известно, что наличие низкого количества кислорода ускоряет разложение полимера, тогда как при более высоком содержании кислорода повышается выработка углекислого газа и воды.
Ученые разработали способ окислительного разложения вулканизированного отхода каучука путем обработки органическим гидропероксидом под мягкими условиями реакции. Его можно применять как на натуральным, так и к синтетическим отходам каучука, и можно использовать широкий спектр органических пероксидов (трет-бутилгидропероксид, кумолгидропероксид, гидропероксид диизопропилбензола и т. д.). Гидропероксид контактируют с вулканизированным каучуком в пропорции от 1 до 5 в присутствие галогенированных углеводородов в качестве растворителей и Cu как катализатора окисления. Реакция протекает при температурах около 40 С и ускоряется подачей воздуха или кислорода. В этих условиях общее разложение каучука может быть достигнуто после нескольких часов реакции. Несколько возможных использований получаемого остатка после переработки предлагается учеными: технологическое масло, как добавка к производству новой резины, модификатор для асфальта и т. д.
Гебауэр и Хофманн предложили метод переработки пластика разложением путем термического окисления. Обработка полиолефинов кислородом при относительно низкой температуре (130-180 С) вызывает быструю деградацию полимеров для получения восковых окислов. Одной из основных проблем этого метода является дисперсия и контакт кислорода с высоковязким расплавленным полимером. По мнению авторов, полученные материалы обладают интересными свойствами для различных применений.
Совершенно иной подход к методу окислительной деполимеризации отходов, предложенный другими учеными заключается в разрушении полимера путем его селективного частичного окисления кислородом в сверхкритической водной смеси или в смеси воды вблизи сверхкритических условий, что приводит к высокому выход исходного мономера. По мнению авторов, этот процесс может быть успешно применен как для конденсационных, так и для аддитивных полимеров, таких как ПВХ, изотактического полипропилена и полистирола. Полимеры быстро доводятся до расплавленного состояния при критической температуре 374 С и давлении 218 атмосфер при контакте с водой, после чего в реактор вводят кислород. Под этими условиями, кислород полностью смешивается с водой, в то время как полимер набухает и частично растворяется, что приводит к образованию псевдооднородной смеси. Два типа реакции имеют место в этой системе: разложение полимера по цепному разрыву и общее окисление. Чтобы уменьшить влияние последнего процесса окисления, относительно небольшие количества кислорода вводятся в реактор, только для протекания самой реакции. Деградация происходит очень быстро, причем большая часть отходов полимера полностью превращается в газ в течение времени пребывания до 3 мин, и при этом присутствие катализатора не требуется.
Типичные продукты окисления полимера в условиях сверхкритической воды включают соответствующие мономеры, димеры, триммеры и другие олигомеры, имеющие до 8 повторных групп, а также углекислого газа, воды и небольшого количества легких углеводородов. Если отходы полимера содержат органические добавки, они также подвергаются окислительной деградации, тогда как неорганические добавки и примеси, присутствующие в исходном полимере, обычно не растворяются в сверхкритической жидкостной смеси и легко отделяют от продукта реакции в виде осадка.
При окислительной деполимеризации изотактического полипропилена основными продуктами являются пропилен, метан, этилен и уксусная кислота. Производные пропилена составляют до 65%. Аналогично, окислительный полистирол при деградации в сверхкритических условиях воды приводит к получению таких продуктов, как метан, этилен, пропилен, изобутен, пропан, бутан, бензол, толуол, этилбензол и стирол. Более сложная деградация происходит, когда этот процесс применяется к отходам поливинилхлорида. В этом случае, полимеризация ПВХ при сверхкритических условиях протекает в соответствии с механизмом, состоящим из четырех этапов: дегидрохлорирование и частичное окисление, дегидрохлорирование и разрушение цепи, дегидрохлорирование и полное окисление и гидрохлорирование. В продуктах реакции обнаружены высокие выходы винилхлорида, 1,1-дихлорэтана и 1,2-дихлорэтана, особенно при коротком времени реакции, тогда как более длительные реакции благоприятствуют продуктам общего окисления. Другие продукты включают хлорметан, хлорэтан и 1,2-дихлорпропан.
В еще одном патенте процесс переработки отходов каучука был расширен до окислительной развязки каучука в сверхкритических условиях. Как натуральные, так и синтетические, вулканизованные и не вулканизированные каучуки были предварительно обработаны, чтобы получить смесь низших алканов, алкенов, диенов, ароматических соединений, спиртов, карбоновых кислот, альдегидов и кетонов. Кроме того, небольшие количества каучуковых фрагментов, диоксида углерода, воды, серы и оксидов азота и галогениды кислот также могут быть образованы в зависимости от вида сырого каучука. Реакция протекает при критической температуре в присутствии кислорода. В этих условиях резиновые полимеры очень быстро разрушаются. происходит разрыве цепи (обрыв углеродсодержащих углеродных связей) и девулканизация вулканизированного каучука (обрыв серосодержащей и углерод-серой связей), а также полное окисление в углерод двуокисью и водой. Предлагается, чтобы полученные продукты могли бы использоваться в качестве топлива с последующей модернизацией или без нее для получения топлива более высокого качества, а также для производства различных химических веществ путем разделения компонентов.
Выводы
Газификация пластмассовых отходов путем обработки кислородом, воздухом, паром или смесями этих веществ является эффективным методом деградации, который дает синтез-газ и твердый остаток в качестве основных продуктов. Газификацию можно рассматривать как процесс рециркуляции сырья для пластмассовых отходов, при условии, что полученный синтез-газ используется для получения метанола, аммиака, углеводородов, оксигенированных соединений вместо просто использования его в качестве топливного газа. Основным преимуществом газификации является возможность обработки сложных смесей без какой-либо предыдущей стадии разделения. Таким образом, во многих случаях пластмассы газифицируются при смешивании с другими твердыми отходами. Основные недостатки связаны с последующими процессами очистки, которые необходимы для получения синтез-газа с качеством и композицией, подходящими для химического синтеза. Более того, экономическая жизнеспособность большинства химических процессов, начиная с синтез-газа, сильно зависит от их применения на крупномасштабных установках, расположенных вблизи объектов, в которых отходы превращаются в газ. Другие возможные окислительные обработки для рециркуляции исходного сырья из пластмассовых и резиновых отходов включают частичное окисление органическими пероксидами и разложение реакцией с кислородом путем термического окисления или в условиях сверхкритической воды. Однако эти последние альтернативы до сих пор не были широко исследованы. Процесс экспериментов и разработок продолжается.
Вы можете подать объявление отходы полипропилена
mirothodov.ru
Сравнительный анализ: методы получения синтез-газа
CO2 ─ 8-15% (об.)
CH4 ─ 0,5% (об.)
N2 и Ar ─ 0,5-1% (об.)
Очищают от CO2 через абсорбцию под давлением, хемосорбцию водным раствором моноэтаноламина или карбоната калия.
Наверх газ поступает в абсорбер 9, где поглощается CO2 , а очищенный газ направляется к потребителю. Насыщенный абсорбент подогревается в теплообменнике 10 горячим регенерированным раствором и направляется в десорбер 11, с низа которого абсорбент направляется через т/о 10 вновь на поглощение CO2 в абсорбер 9. CO2 с верха 11 компримируют до соответствующего давления и возвращают на конверсию, смешивая перед т/о 2 с природным газом и водяным паром.
Расход на 1 м3 синтез-газа составляет:
Природный газ ─ 0,35 – 0,40 м3 ,
Технический O2 ─ 0,2 м3 ,
и в зависимости от применяемого
давления и добавки CO2 ≈ 0,2 – 0,8 кг водяного пара.
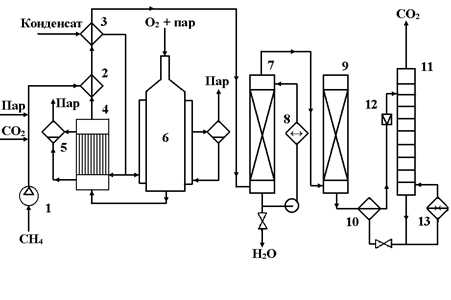
Рис. 15. Технологическая схема окислительной конверсии природного газа при высоком давлении
1 – турбокомпрессор; 2, 3, 10 – теплообменники; 4 – котел-утилизатор; 5 – паросборники; 6 – конвертор; 7 скруббер; 8 – холодильник; 9 – абсорбер; 11 – десорбер; 12 – дроссельный вентиль; 13 – кипятильник.
За рубежом развитие процессов паровой и углекислотной конверсии метана направлено несколько в другую сторону. На рис. 16 показаны принципиальные технологические схемы конверсии метана с паром для получения водорода и комбинированного парового/углекислотного риформинга для производства синтез-газа.
Установка риформинга обычно включает от 40 до 400 трубок (длина 6 ─ 12 м, диаметр 70 ─ 160 мм, толщина стенок 10 ─ 20 м), которые установлены вертикально в прямоугольной печи. Трубки заполняются катализатором, обычно формованным в виде небольших цилиндров или колец Рашига. Реактор обогревается горелками, которые могут размещаться внизу, сбоку или сверху печи. Топливо сжигается в радиационной секции печи. Отходящие дымовые газы (после обогрева реактора). Проходят через конвекционную секцию, где охлаждаются за счет отдачи тепла жидкостным и паровым потокам, включая пар, необходимый для реакции, исходный водяной поток и потоки для производства пара.
Дальнейший технологический маршрут синтез-газа зависит от выбранного процесса его вторичной переработки (получение H2 , CO, оксосинтез, синтез аммиака и т.д.). Для получения водорода газ направляют в реактор конверсии водяного газа и поглотительный реактор переменного давления (см. рис.16а). Если требуется получить CO, то используется технологическая схема, включающая секцию удаления CO2 и установку низкотемпературного разделения (т.н. «холодный ящик»). Выделяемый диоксид углерода повторно используется в процесс риформинга. Если в этом случае желательно также получить H2 в качестве продукта, то установку снабжают блоком PSA (Pressure-Swing-Adsorption) (см. рис. 16).
В таблице 6 представлены некоторые характеристик процессов конверсии метана.
Таблица 6
Сравнительные технико-экономические показатели процессов получения синтез-газа.
Таблица 6 (окончание)
Технико-экономические показатели.
5. Синтез Фишера-Тропша
Метод Фишера – Тропша по превращению метана в более тяжелые углеводороды был разработан в 1923 г. и реализован в промышленности Германии в 1940-х годах.
Почти все авиационное топливо в этой стране во время второй мировой войны производилось с помощью синтеза Фишера – Тропша из каменного угля. Впоследствии от этого способа изготовления моторных топлив отказались, так как топливо, получаемое при переработке нефти, до последнего времени было экономически более выгодным.
При получении жидкого топлива на основе синтеза Фишера – Тропша разнообразные соединения углерода (природный газ, каменный и бурый уголь, тяжелые фракции нефти, отходы деревообработки) конвертируют в синтез-газ (смесь СО и Н2 ), а затем он превращается в синтетическую «сырую нефть» – синтнефть. Это – смесь углеводородов, которая при последующей переработке разделяется на различные виды практически экологически чистого топлива, свободного от примесей соединений серы и азота. Достаточно добавить 10% искусственного топлива в обычное дизельное, чтобы продукты сгорания дизтоплива стали соответствовать экологическим нормам. [28]
Еще более эффективной представляется конверсия газа в дорогостоящие продукты тонкого органического синтеза.
Конверсию газа в моторное топливо можно в целом представить как превращение метана в более тяжелые углеводороды:
2nСН4 + 1/2nО2 = Сn Н2n + nН2 О
Из материального баланса брутто-реакции следует, что массовый выход конечного продукта не может превышать 89%.
Реакция напрямую неосуществима. Конверсия газа в жидкое топливо (КГЖ) проходит через ряд технологических стадий (рис.17). При этом в зависимости от того, какой конечный продукт необходимо получить, выбирается тот или иной вариант процесса.
Синтез Фишера-Тропша может рассматриваться как реакция восстановительной олигомеризации монооксида углерода, при которой образуются углерод-углеродные связи, и в общем виде она представляет собой сложную комбинацию ряда гетерогенных реакций, которую можно представить суммарными уравнениями:
nCO + 2nH2 → (CH2 )n + nH2 O,
2nCO + nH2 → (CH2 )n + nCO2 .
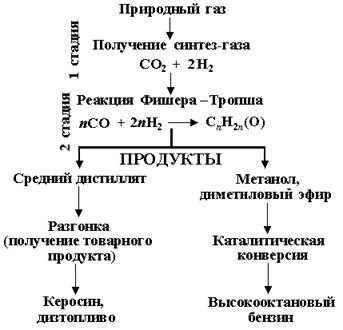
Рис. 17. Принципиальная схема конверсии синтез-газа в жидкие продукты (топливо).
Продуктами реакции являются алканы, алкены и кислородсодержащие соединения, то есть образуется сложная смесь продуктов, характерная для реакции полимеризации. Первичными продуктами синтеза Фишера-Тропша являются a- и b-олефины, которые превращаются в алканы в результате последующего гидрирования. Природа применяемого катализатора, температура, соотношение СО и Н2 существенно сказываются на распределении продуктов. Так, при использовании железных катализаторов велика доля олефинов, тогда как в случае кобальтовых катализаторов, обладающих гидрирующей активностью, преимущественно образуются насыщенные углеводороды. [2]
В настоящее время в качестве катализаторов синтеза Фишера-Тропша в зависимости от поставленных задач (повышение выхода бензиновой фракции, увеличение выхода низших олефинов и др.) используются как высокодисперсные железные катализаторы, нанесенные на оксиды алюминия, кремния и магния, так и биметаллические катализаторы: железо-марганцевые, железо-молибденовые и др. [34]
За 70 лет с момента открытия синтеза не утихают споры по поводу механизма реакции. В настоящее время рассматриваются три различных механизма. Первый механизм, называемый карбидным, впервые предложенный Фишером и Тропшем и в дальнейшем нашедший поддержку у других исследователей, предполагает образование С-С-связей в результате олигомеризации метиленовых фрагментов на поверхности катализатора. На первой стадии происходит адсорбция СО и образуется поверхностный карбид, а кислород превращается в воду или СО2 :
На второй стадии поверхностный карбид гидрируется с образованием фрагментов СНx (х = 1-3):
Удлинение цепи происходит в результате реакции поверхностных метила и метилена и далее путем внедрения метиленовых групп идет рост цепи:
mirznanii.com
Сравнительный анализ: методы получения синтез-газа
Стадия обрыва цепи происходит в результате десорбции алкена с поверхности катализатора:
Второй механизм, названный гидроксикарбеновым, предполагает также гидрирование координированного на металле СО с образованием поверхностных гидроксикарбеновых фрагментов, в результате конденсации которых и происходит образование С-С-связей:
Третий механизм, который можно назвать механизмом внедрения, предполагает образование С-С-связей в результате внедрения СО по связи металл-углерод (о способности СО к внедрению по связи металл-алкил говорилось выше):
Накоплен достаточно богатый экспериментальный материал, свидетельствующий в пользу того или иного варианта механизма, однако приходится констатировать, что к настоящему моменту невозможно сделать однозначный выбор между ними. Можно предположить, что в связи с большой важностью синтеза Фишера-Тропша исследования в этом направлении будут интенсивно продолжаться и мы станем свидетелями новых воззрений на механизмы протекающих реакций [3].
5.1 Выбор катализаторов
Состав конечных продуктов зависит от катализатора, температуры и соотношения СО и Н2 .
На металлоокисном катализаторе получают метанол с примесью этанола и диметилового эфира. Это основной процесс получения метанола в мире, обычная мощность метанольных заводов составляет около 0,5 млн. т в год (Новомосковское ПО «АЗОТ»; кобальтовый катализатор).
Для производства моторных топлив метанол перерабатывается в диметиловый эфир и далее в смесь разветвленных предельных углеводородов (процесс Mobil GTG в Мауи, Новая Зеландия; кобальтовый катализатор)[19].
На кобальтово-цинковых катализаторах, обладающих гидрирующей активностью, получают смесь линейных алканов (процесс AGC-211 в Бинтулу, Малайзия) [20].
На железном катализаторе получают смесь линейных и разветвленных алканов и алкенов (перспективный процесс Рентех).
На кобальтовых или родиевых катализаторах при давлении выше 10 МПа и температуре в диапазоне 140 – 180 °С алкены взаимодействуют с синтез-газом и превращаются в альдегиды – важнейшие полупродукты в производстве спиртов, карбоновых кислот, аминов, многоатомных спиртов и др. Мировое производство альдегидов по такой технологии (оксосинтез) достигает 7 млн т в год [14].
Одно из важных современных направлений научного поиска в области синтеза Фишера – Тропша состоит в получении кислородсодержащих продуктов. Введение таких соединений в количестве 1 % в дизельное топливо снижает содержание сажи в продуктах сгорания на 4 – 10%.
6. Альтернативный способ получения синтез-газа
Современные проблемы энергетики могут быть решены только при рациональном использовании всех существующих на Земле и околоземном пространстве источников топлива и энергии [29]. Среди них биомасса, как постоянно возобновляемый источник топлива, занимает существенное место [32].
Биомасса – термин, объединяющий все органические вещества растительного и животного происхождения. Биомасса делится на первичную (растения, животные, микроорганизмы и т.д.) и вторичную – отходы при переработке первичной биомассы и продукты жизнедеятельности человека и животных. В свою очередь отходы также делятся на первичные – отходы при переработке первичной биомассы (солома, ботва, опилки, щепа, спиртовая барда и т.д.) и вторичные – продукты физиологического обмена животных и человека.
Ежегодное количество органических отходов по разным отраслям народного хозяйства России составляет более 390 млн. т. Сельскохозяйственное производство дает 250 млн. т, из них 150 млн. т приходится на животноводство и птицеводство, 100 млн. т -на растениеводство. Лесо- и деревопереработка дают 700 млн. т, твердые бытовые отходы городов – 60 млн. т, коммунальных стоков – 10 млн. т (все приведенные значения даются на абсолютно сухое вещество.
Энергия, запасенная в первичной и вторичной биомассе может конвертироваться в технически удобные виды топлива или энергии несколькими путями.
1. Получение растительных углеводородов (растительные масла, высокомолекулярные жирные кислоты и их эфиры, предельные и непредельные углеводороды и т.д.). Например, для южных регионов России это может быть рапсовое масло, добавляемое к дизельному топливу.
2. Термохимическая конверсия биомассы (твердой, до 60%) в топливо: прямое сжигание, пиролиз, газификация, сжижение, фест-пиролиз.
3. Биотехнологическая конверсия биомассы (при влажности от 75 % и выше) в топливо: низкоатомные спирты, жирные кислоты, биогаз.
В зависимости от влажности биомасса перерабатывается термохимическими или биологическими способами. Биомасса с низкой влажностью (сельскохозяйственные и городские твердые отходы) перерабатываются термохимическими процессами: прямым сжиганием, газификацией пиролизом, ожижением, гидролизом. В результате получают водяной пар, электроэнергию, топливный газ, водород (метанол), жидкое топливо, газ, древесный уголь, глюкоза.
Биомасса с высокой влажностью (сточные воды, бытовые отходы, продукты гидролиза органических остатков) перерабатываются биологическими процессами: анаэробная переработка, этанольная ферментация, ацетонобутанольная ферментация. В результате этих процессов получают биогаз (СН4 , СО2 ), органические кислоты, этанол, ацетон, бутанол. Различие физико-химических свойств биомассы обусловливает выбор термохимического или биологического процесса ее переработки.
6.1 Термохимическая конверсия биомассы
Прямое сжигание является одним из самых широко применяемых методов переработки биомассы (древесины и древесных отходов, соломы, городских твердых отходов и др.).
Топливо, вырабатываемое из городских твердых отходов, используют в сочетании с углем на небольших электростанциях.
Наиболее перспективными и все более широко применяемыми процессами превращения биомассы в различные виды энергии являются термохимическая газификация, этанольная ферментация и анаэробная переработка. Из термохимических процессов переработки биомассы наибольшее внимание в настоящее время привлекают такие, как газификация, пиролиз и сжижение, в результате которых получают жидкие и газообразные топлива, имеющие значительно большую энергоемкость, чем биомасса. Все эти процессы протекают при высокой температуре, а иногда и при высоком давлении.
Газификация древесины и другого лигноцеллюлозного сырья в течение многих лет является одним из основных методов производства низкокалорийного топливного газа. Топливный газ может быть непосредственно использован в котельных, обжигательных печах и разного вида топках, а после охлаждения, очистки и осушки – в качестве топлива в двигателях внутреннего сгорания. Состав получаемых при газификации газов зависит от природы применяемого сырья, типа окислителя, температуры процесса и давления. Наибольшую ценность представляет среднекалорийный газ, особенно синтез-газ (в основном состоящий из СО и Н2 ). При газификации древесины получают синтез-газ, который по составу идентичен синтез-газу, вырабатываемому газификацией угля, паровой конверсией природного газа и др.
Пиролиз биомассы осуществляется при ее нагревании в отсутствии кислорода с образованием жидкого топлива, газов и древесного угля. Выход продуктов пиролиза зависит от условий проведения процесса и типа сырья. В свою очередь, условия процесса определяются природой сырья, заданными продуктами производства.
Широкую известность получил процесс превращения биомассы в жидкое топливо пиролизом со ступенчатым испарением, где в качестве сырья используются твердые городские отходы, древесная кора и др.
Основными технологическими узлами установки являются отделения для предварительной обработки древесины, производства синтез-газа, реакторное и секция для разделения продуктов ожижения. В отделении для предварительной обработки древесины биомасса (в виде древесной щепы) высушивается, измельчается и смешивается с рециркулирующей частью производимого жидкого топлива. Полученная суспензия нагревается до 200 о С и под давлением 23 МПа подается в реактор, где в присутствии раствора углекислого натрия в качестве катализатора и смеси газов оксида углерода и водорода (поступающего из отделения производства синтез-газа после очистки последнего от СО2 и Н2 О) при температуре 340 о С и давлении 23МПа происходит ожижение биомассы.
Неочищенная жидкая фракция содержит, кроме образовавшегося жидкого топлива, непрореагировавшую древесину, катализатор и нерастворимые твердые вещества, для очистки от которых она направляется в сепараторное отделение. Извлеченные из неочищенного жидкого топлива твердые вещества и водорастворимый катализатор возвращают в систему. Общий тепловой КПД промышленной установки (с учетом всех потерь) составляет 50-60 %.
Один из методов переработки целлюлозной биомассы (например, соломы) – гидролиз минеральными кислотами с образованием глюкозы и ксилозы, которые в дальнейшем могут быть подвергнуты ферментации в целях производства различных органических химикатов, включая этанол, кислоты, бутанол и ацетон. С точки зрения получения заменителей жидкого и газообразного ископаемого топлива наибольший интерес представляет технология переработки биомассы с образованием в качестве конечных продуктов этанола, метанола, синтетического природного газа и биогаза.
Основными преимуществами превращения биомассы методом термохимической газификации являются высокие эффективность и скорость превращения. К недостаткам процесса относится возможность переработки сырья только с низким содержанием влаги, а также высокие температура и давление, сложные техническое оформление и управление процессом.
mirznanii.com
Получение дизельного топлива из синтез газа
Получение дизельного топлива из синтез газа
Синтез-газ – это промежуточный продукт, получаемый в результате переработки углеводородного сырья. Технологии его получения известны достаточно давно, но они не получали применения, вследствие дешевизны и доступности нефти. Ограниченность нефтяных запасов заставила специалистов вспомнить о технологиях , позволяющих заменить традиционно используемый тип сырья на альтернативные. В качестве вариантов альтернативного сырья были названы газ и уголь. Это связано с тем что, так называемые «подтвержденные месторождения» этих ископаемых углеводородов в настоящий момент достаточно велики и намного превышают нефтяные. Единственная проблема , которую необходимо решить , это найти эффективный способ переработки угля и природного газа в обычные нефтепродукты – бензин и дизельное топливо. Именно это обстоятельство стимулирует исследования по совершенствованию существующих способов производства синтез-газа. Капитальные и эксплуатационные затраты на производство Синтез-газа составляют до 60 – 70 % от всех капиталовложений в производство. Поэтому перспективы развития промышленности и конкурентоспособность того или иного производства базирующегося на синтезе через Синтез-газ зависят от эффективности технологии получения последнего. Для различных технологических процессов требования к качеству Синтез-газа различно. Прежде всего, это касается оптимального соотношения Н2/СО2, величина которой сильно колеблется. Кроме того, существенное значение имеют примеси в Синтез-газе, которые могут изменять эффективность дальнейших стадий процесса и отравлять катализаторы.
Получение синтез газа
Получение синтез-газа является первой стадией превращения природного газа и угля не только в жидкие топлива, но и химические продукты. Помимо упомянутых бензина и дизельного топлива, из синтез-газа производят: ароматические соединения, метанол, уксусную кислоту, аммиак, олефеины и другие соединения, которые используются в качестве сырья в химической промышленности. Синтез-газ представляет собой смесь окиси углерода и водорода. Существует много способов для его производства, например с помощью паровой конверсии или окислением метана. Эти способы обладают высокой себестоимостью. Применение катализаторов означает осуществление на поверхности катализатора ряда химических превращений, этот метод зарекомендовал себя как более эффективный и дешевый. Эта технология стала основой для создания бортового генератора синтез-газа для автомобилей.
Первым способом получения синтез-газа была газификация каменного угля, которая была осуществлена еще в 30-е годы XIX века в Англии с целью получения горючих газов: водорода, метана, монооксида углерода. Этот процесс широко использовался во многих странах до середины 50-х годов XX века, а затем был вытеснен методами, основанными на использовании природного газа и нефти. Однако в связи с сокращением нефтяных ресурсов значение процесса газификации снова стало возрастать. В настоящее время существуют три основных промышленных метода получения синтез-газа:
1. Газификация угля. Процесс основан на взаимодействии угля с водяным паром: C + h3O h3 + CO. Эта реакция является эндотермической, равновесие сдвигается вправо при температурах 900-1000?С. Разработаны технологические процессы, использующие парокислородное дутье, при котором наряду с упомянутой реакцией протекает экзотермическая реакция сгорания угля, обеспечивающая нужный тепловой баланс: C + 1/2O2 CO.
2. Конверсия метана. Реакция взаимодействия метана с водяным паром проводится в присутствии никелевых катализаторов (Ni-Al2O3) при повышенных температурах (800-900?С) и давлении: Ch5 + h3O CO + 3h3 . В качестве сырья вместо метана может быть использовано любое углеводородное сырье.
3. Парциальное окисление углеводородов. Процесс заключается в неполном термическом окислении углеводородов при температурах выше 1300?С: Cnh3n + 2 + 1/2nO2 nCO + (n + 1)h3 . Способ применим к любому углеводородному сырью, но наиболее часто в промышленности используют высококипящую фракцию нефти – мазут.
Соотношение СО : Н2 существенно зависит от применяемого способа получения синтез-газа. При газификации угля и парциальном окислении это соотношение близко к 1 : 1, тогда как при конверсии метана соотношение СО : Н2 составляет 1 : 3. В настоящее время разрабатываются проекты подземной газификации, то есть газификации угля непосредственно в пласте. Интересно, что эта идея была высказана Д.И. Менделеевым более 100 лет назад. В перспективе синтез-газ будут получать газификацией не только угля, но и других источников углерода вплоть до городских и сельскохозяйственных отходов.
Получение ДТ из синтез газа
Существующие технологии позволяют перерабатывать природный газ в высококачественные бензин и дизельное топливо через стадию образования метанола. Производство по такой схеме довольно удобно, поскольку все реакции протекают в одном реакторе. Но эта цепочка химических превращений требует больших затрат энергии. В результате полученный синтетический бензин в 1,8-2,0 раза дороже “нефтяного”.
Российские ученые из московского Института нефтехимического синтеза РАН разработали более рентабельную схему. Они предлагают получать синтетический бензин не через стадию образования метанола, а из другого промежуточного вещества – диметилового эфира (ДМЭ). Это нетрудно сделать, увеличив долю окиси углерода в синтез-газе. Важно то, что ДМЭ можно использовать как экологически чистое топливо для двигателей внутреннего сгорания. Он хорош тем, что полностью укладывается в рамки самых жестких европейских требований по содержанию твердых частиц в автомобильных выхлопах. По теплотворной способности ДМЭ уступает традиционному дизельному топливу – пропану и бутану, но его цетановое число гораздо выше: для обычного дизельного топлива оно 40-55, а для ДМЭ – 55-60. Так что преимущество ДМЭ перед дизельным топливом при запуске холодного двигателя очевидно. Кроме того, для горения ДМЭ необходимо меньше кислорода, чем для горения дизельного топлива.
Моторные топлива, полученные из природного газа, не дороже продуктов переработки нефти, а по качеству даже их превосходят. Так что после окончательного истощения нефтяных месторождений “пробки” на дорогах не уменьшатся.
Процесс производства синтетических нефти и дизельного топлива можно условно разделить на три этапа: получение синтез-газа, синтез газо-жидкостной смеси углеводородов (синтез Фишера-Тропша), облагораживание продукта. Получение синтез-газа проводится практически так же, как при производстве метанола. Отличие состоит в том, что через слой катализатора пропускается смесь попутного газа, водяного пара и углекислого газа. А затем синтез-газ необходимо очистить от большей части двуокиси углерода.
Синтез Фишера-Тропша проводится в реакторе в присутствии катализаторов. Полученные в результате синтеза жидкие продукты представляют из себя многокомпонентную смесь углеводородов (преимущественно парафиновых). Третий этап предполагает использование установки для гидрокрекинга и ректификационной колонны для совершенствования продукта. В установке гидрокрекинга происходит расщепление длинных углеводородных молекул на более короткие. В ректификационной колонне производится выделение требуемой фракции.
Синтез Фишера-Тропша
Процесс Фишера—Тропша — это многостадийная химическая реакция: из углеводородов сначала получают так называемый синтез-газ (CO+Н2), а уже из него — такие ценные химические продукты, как метанол или синтетические углеводороды, используемые преимущественно для получения моторных топлив. Эта технология активно развивалась еще в середине прошлого века — тогда на базе переработки угля; теперь же перспективным, логичным направлением ее использования становится переработка газового сырья. Сейчас углеводороды все активнее разрабатывают на шельфе, растет добыча сланцевого газа, при которой скважины имеют относительно короткий период продуктивной жизни, да и месторождения традиционного газа становятся все меньше по запасам. В таких условиях расходы на транспорт и создание соответствующей инфраструктуры, будь то сжижение или поставка по трубопроводам, неизбежно увеличиваются, поэтому переработка сырья на месте на базе процесса Фишера—Тропша становится все более привлекательной.
Смесь монооксида углерода (угарный газ) и водорода называется синтез-газ или сингаз, встречается термин “водяной газ”. Получаемые углеводороды очищают для получения целевого продукта — синтетического бензина. Получение более тяжелых топлив методом Фишера-Тропша очень накладно из за быстрого отравления катализатора. Углекислый газ и монооксид углерода образуются при частичном окислении угля и древесного топлива. Польза от этого процесса преимущественно в его роли в производстве жидких углеводородов или водорода из твёрдого сырья, такого как уголь или твёрдые углеродсодержащие отходы различных видов. Неокислительный пиролиз твёрдого сырья производит сингаз, который может быть напрямую использован в качестве топлива, без преобразования по процессу Фишера – Тропша. Если требуется жидкое, похожее на нефтяное топливо, смазка или парафин, может быть применён процесс Фишера – Тропша. Наконец, если требуется увеличить производство водорода, водяной пар сдвигает равновесие реакции, в результате чего образуются только углекислый газ и водород. Таким образом появилась возможность получать жидкое топливо из газового.
В начале 2006 года в США рассматривались проекты строительства 9 заводов по непрямому сжижению угля суммарной мощностью 90 – 250 тыс. баррелей в день.
Китай планирует инвестировать 15 млрд долл. до 2010—2015 гг. в строительство заводов по производству синтетического топлива из угля. Национальная Комиссия Развития и Реформ (NDRC) заявила, что суммарная мощность заводов по сжижению угля достигнет 16 млн тонн синтетического топлива в год, что составляет 5 % от потребления нефти в 2005 году и 10 % импорта нефти.
Технологии переработки угля в жидкое топливо порождают множество вопросов со стороны экологов. Наиболее серьёзной является проблема выбросов углекислого газа. Последние работы Национальной лаборатории по возобновляемым источникам энергии США (National Renewable Energy Laboratory) показали, что в полном цикле выбросы парниковых газов для произведённых из каменного угля синтетических топлив примерно вдвое выше своего основанного на бензине эквивалента. Выбросы прочих загрязнителей также сильно увеличились, тем не менее, многие из них могут быть собраны в процессе производства. Захоронение углерода было предложено в качестве способа уменьшения выбросов оксида углерода. Закачка CO_2 в нефтяные пласты позволит увеличить добычу нефти и увеличить срок службы месторождений на 20-25 лет, однако использование данной технологии возможно лишь при устойчивых нефтяных ценах выше 50-55 долл. за баррель.
Важной проблемой при производстве синтетического топлива является и высокое потребление воды, уровень которого составляет от 5 до 7 галлонов на каждый галлон полученного топлива.
Уже действуют несколько крупнотоннажных производств такого типа. Гигантский завод на 150 тысяч баррелей в сутки компания Shell строит в Катаре. Реализуется несколько проектов в Китае. Наиболее затратной остается стадия получения синтез-газа, на которую приходится до 70 процентов общих издержек. В принципе подобные западные технологии можно адаптировать и у нас, но в суровых украинских условиях их стоимость возрастает как минимум вдвое. Но если в крупнотоннажных процессах существующие технологии получения синтез-газа еще обеспечивают приемлемый уровень рентабельности, то подобные малотоннажные технологии становятся уже нерентабельными и в промышленных масштабах практически не используются. Вместе с тем для Украины именно они — «горячая» тема, так как они необходимы для утилизации попутного газа, большая часть которого сейчас сжигается в факелах. Если в Штатах действует полторы тысячи заводов по утилизации попутного газа, то к примеру в Росии их – 24, а создание разветвленной инфраструктуры по сбору попутного газа — задача очень дорогостоящая и поэтому не вызывающая у нефтяников большого энтузиазма.
Пик интереса к крупнотоннажной технологии Фишера—Тропша, видимо, уже пройден. Ведущие мировые компании стали активно интересоваться этой темой еще тридцать лет назад и сейчас, имея собственные технологии, планомерно развивают это направление. Малотоннажными технологиями переработки газа крупные зарубежные компании до сих пор мало интересовались, но с началом добычи сланцевого газа в Америке интерес к этой теме заметно повысился.
Водяной газ
Водяной газ (синтез-газ, технологический газ) образуется при взаимодействии раскалённого топлива с водяным паром. Поскольку реакция получения водяного газа эндотермична, то для накопления необходимого для газификации количества тепла слой топлива в генераторе периодически продувают воздухом (полученный при этом воздушный газ является побочным продуктом).
Водяной газ является мало распространенным видом промышленного топлива и производится обычно лишь на газовых заводах, и некоторых крупных химических предприятиях, служит одним из важнейших видов сырья в промышленном органическом синтезе. В качестве так называемого синтез- газа он применяется для получения бензина и метанола. Кроме того, из водяного газа получают водород для синтеза аммиака.
В настоящее время еще не создан практически выгодный способ непрерывного получения водяного газа в одном и том же газогенераторе. Объясняется это тем, что при разложении водяного пара на кислород и водород расходуется больше тепла, чем выделяется при соединении углерода с кислородом. Приходится вести процесс периодически: сначала при помощи воздушного дутья топливо нагревают до раскаленного состояния, затем через тот же генератор продувают пар до тех пор, пока температура не снизится настолько, что получается недоброкачественный газ. Эти периоды процесса называют: первый — периодом горячего (воздушного) дутья и второй — периодом водяного газа.
Периодичность процесса заставляет применять два газогенератора с небольшим газгольдером или один газогенератор с крупным газгольдером. В последнем случае, если газ расходуется в том же количестве, в каком производится, емкость газгольдера может не превышать часовой производительности генератора. Такие установки в настоящее время работают автоматически. Автоматика дает возможность работать с короткими циклами (меньше 2 мин.), в результате чего получается газ однородного состава.
Как правило, водяной газ очищают. Он проходит через сифонный затвор, мокрый скруббер, а также при необходимости — через сероочистку.
Водяной газ богат окисью углерода и поэтому ядовит. Его слабосветящееся пламя имеет синий оттенок, отсюда его второе название — «блаугаз» (синий газ). Это название обычно употребляют для отличия водяного газа от обогащенного водяного газа. Последний получают путем карбюрирования блаугаза для повышения светимости. Теплотворность обогащенного водяного газа составляет около 4900 ккал/нм3. При сжигании водяного газа можно получить самую высокую температуру горения в сравнении с другими распространенными промышленными газами. По этой причине он использовался одно время в большом количестве для сварки. Однако, после того как электросварка повсюду заменила сварку с использованием водяного газа, потребление последнего сократилось. Водяной газ является хорошим топливом, но капитальные затраты на сооружение установок и эксплуатационные расходы при его производстве так высоки, что в настоящее время этим газом пользуются только в крайнем случае.
В России при дешевизне нефтяных продуктов, потребных для освещения (керосина, нефтяного газа и т. п.), ныне водяной газ можно рекомендовать только для таких металлургических заводов, которые могут дешево получать кокс или антрациты. Для этих последних может родиться не только выгода от замены многих реператоров, дающих горючую смесь окиси углерода с азотом одним заводом водяной газа, но и от применения этого последнего к освещению завода (карбюрированием).
b-b.in.ua
Способ получения синтез-газа
Изобретение относится к области химии. Парофазную смесь для получения синтез-газа с молярным отношением Н2О/С, равным, по меньшей мере, 2, которая содержит водяной пар и, по меньшей мере, один углеводород или кислородсодержащий углеводород с точкой кипения в диапазоне от -50 до 370°С при атмосферном давлении, получают путем введения водяного пара в нижнюю часть дистилляционной колонны, а углеводорода или кислородсодержащего углеводорода – в верхнюю часть упомянутой дистилляционной колонны. Изобретение позволяет снизить содержание углерода на катализаторе при производстве синтез-газа из вышеуказанной парофазной смеси. 2 з.п. ф-лы.
Настоящее изобретение относится к производству синтез-газа из (кислородсодержащего) углеводорода с точкой кипения в диапазоне от -50 до 370°C при атмосферном давлении. Изобретение также относится к способу производства метанола из полученного таким образом синтез-газа и способу получения парофазной смеси из водяного пара и (кислородсодержащего) углеводорода, которую можно применять для производства синтез-газа.
Производство биодизельного топлива непрерывно увеличивается. Обычно биодизельное топливо получают из растительных и животных масел и жиров, таких как рапсовое масло, подсолнечное масло, пальмовое масло (пальмоядровое и косточковое), кокосовое масло, соевое масло, кукурузное масло, кулинарный жир, смазочные материалы из жироуловителей и технический (пищевой) жир. При производстве биодизельного топлива образуются большие количества глицерина. Поэтому важно найти для глицерина полезные применения. Одним из таких применений является его применение в качестве исходного сырья для производства синтез-газа.
Одним из способов, применяемых в настоящее время для производства синтез-газа, является паровой реформинг природного газа (метана). Указанный способ включает в себя очистку газа путем гидродесульфуризации, смешение очищенного газа с водяным паром, нагревание полученной смеси в конвективной части установки и проводку полученной смеси над слоем катализатора для производства синтез-газа.
Одним из химических продуктов, который можно получать из синтез-газа, является метанол. Синтез-газ производят на установке для производства метанола; для того чтобы превратить его в метанол, полученный газ подвергают сжатию и затем пропускают через конвертер.
Применение глицерина для производства синтез-газа известно из прототипа (см. публикацию: T. Valliyappan, “Hydrogen or Syn Gas Production from Glycerol Using Pyrolysis and Steam Gasification Processes”, Thesis, University of Saskatchewan, December 2004). В известных способах жидкий глицерин в виде капель вводят в слой катализатора в потоке инертного газа или водяного пара. К сожалению, такой способ приводит к осаждению на катализаторе значительного количества углерода, приводящего к деактивации катализатора.
Согласно патенту США № 4927857 синтез-газ можно получать из углеводородного сырья, включая углеводородное сырье всех типов, а также из спиртов, таких как этанол, метанол и их смеси. Поток исходного материала, который содержит углеводородное сырье, H2O и кислород, подвергают предварительному нагреву, чтобы инициировать каталитическое окисление сырья. Отношение H2O к C находится в диапазоне от 0,5 до 3, а отношение O2 к C – в диапазоне от 0,35 до 0,65.
В Европейском патенте EP 0926096 также описано получение синтез-газа из исходного углеводородного сырья при ступенчатом производстве с применением высокотемпературных мембранных реакторов, в которых используются мембраны со смешанной проводимостью, путем контролируемого взаимодействия углеводородов с кислородом, при котором кислород доставляется непосредственно на место благодаря его проникновению через мембрану со смешанной проводимостью из газа, содержащего кислород, такого как воздух. Отношение H2O к C находится в диапазоне от 0,3 до приблизительно 5.
Задачей настоящего изобретения является разработка способа производства синтез-газа из (кислородсодержащих) углеводородов, таких как глицерин, при котором осаждение углерода на катализаторе уменьшается или даже вовсе отсутствует.
Способ согласно изобретению включает стадии:
a) получения парофазной смеси, содержащей водяной пар и, по меньшей мере, один углеводород или кислородсодержащий углеводород с точкой кипения в диапазоне от -50 до 370°C при атмосферном давлении, в упомянутой парофазной смеси молярное отношение H2O/C равно, по меньшей мере, 2; и
b) каталитической или некаталитической конверсии парофазной смеси в синтез-газ, отличающейся тем, что кислород добавляется только в связанной форме.
Таким образом, в способе по настоящему изобретению (кислородсодержащий) углеводород, например глицерин, не вводится в слой катализатора в виде жидкости. Вместо этого он подается к слою катализатора в виде паров вместе с необходимым количеством водяного пара. Неожиданно было обнаружено, что такой способ приводит к пониженному осаждению углерода на катализаторе.
Кроме того, отсутствует описанное в прототипе добавление кислорода, вместо этого кислород присутствует только в связанной форме.
В патенте США № 4927857, который относится к производству нового катализатора, для конверсии в синтез-газ применяется кислород (O2).
В Европейском патенте EP 0926096 описан мембранный реактор, предназначенный для производства синтез-газа опять-таки с применением кислорода (O2).
Неожиданно, было обнаружено, что в способе согласно изобретению элементарный кислород отсутствует. Кислород поставляется только молекулой воды (водяного пара) или присутствует в кислородсодержащих углеводородах, таких как глицерин.
При прямой конверсии глицерина легко образуются осадки углерода. В настоящем изобретении образование осадков углерода предотвращается с помощью надлежащего количества водяного пара. Добавки газообразного кислорода не требуется.
Парофазная смесь содержит водяной пар и, по меньшей мере, один углеводород или кислородсодержащий углеводород. Указанный углеводород или кислородсодержащий углеводород должен иметь атмосферную точку кипения (то есть точку кипения при атмосферном давлении) в диапазоне от -50 до 370°C, более предпочтительно от 0 до 370°C, еще более предпочтительно от 30 до 370°C и наиболее предпочтительно от 50 до 370°C.
Примерами подходящих углеводородов являются алканы с точкой кипения в упомянутом диапазоне. Предпочтительными алканами являются алканы с 3-7 атомами углерода, такие как пропан, бутан, пентан, гексан и гептан.
Примерами подходящих кислородсодержащих углеводородов являются спирты, включая моноспирты, диолы и триолы, такие как этанол, пропанол, изопропанол, глицерин и гликоли.
Предпочтительно применение кислородсодержащего углеводорода. Более предпочтительно кислородсодержащий углеводород представляет собой глицерин.
Молярное отношение H2O/C в упомянутой парофазной смеси должно составлять, по меньшей мере, 2, предпочтительно, по меньшей мере, 2,5. Молярное отношение H2O/C предпочтительно составляет не более 5, более предпочтительно не более 4 и наиболее предпочтительно – не более 3,2.
Таким образом, когда применяется надлежащее отношение водяного пара к углероду, осаждение углерода можно подавлять или даже предотвращать и, что еще более важно, из процесса также можно исключить газообразный кислород. Фактически кислород в процесс можно поставлять только из молекулы спирта и/или из воды.
Парофазную смесь можно получать, подвергая водяной пар контактированию с (кислородсодержащим) углеводородом в газожидкостной контактной установке, такой как дистилляционная колонна или скруббер. В подходящей дистилляционной колонне потребуется только незначительное количество тарелок. В верхнюю часть колонны вводится концентрированный (кислородсодержащий) углеводород. В нижнюю часть вводится водяной пар. Парофазная смесь удаляется из дистилляционной колонны в верхней части.
Молярное отношение H2O/C в полученной парофазной смеси будет зависеть от (i) температуры и давления водяного пара, который вводится в газожидкостную контактную установку, и (ii) от баланса дистилляции между водяным паром и (кислородсодержащим) углеводородом при таких температуре и давлении. Другими словами, требуемые температура и давление водяного пара будут зависеть от типа применяемого (кислородсодержащего) углеводорода и должны выбираться таким образом, чтобы – при заданном балансе дистилляции – молярное отношение H2O/C получалось равным, по меньшей мере, 2.
Когда в качестве кислородсодержащего углеводорода применяется глицерин, водяной пар предпочтительно имеет давление 10-30 бар, более предпочтительно 15-25 бар и наиболее предпочтительно – приблизительно 20 бар. Температура водяного пара предпочтительно составляет 270-380°C, более предпочтительно 310-360°C и наиболее предпочтительно – приблизительно 340°C.
Из нижней части дистилляционной колонны можно извлекать смесь жидкая вода/(кислородсодержащий) углеводород. Из такой смеси можно выделять (кислородсодержащий) углеводород – например, испарением при пониженном давлении – и возвращать его в верхнюю часть дистилляционной колонны.
Таким образом, производство синтез-газа согласно изобретению можно осуществлять над насадочным материалом, то есть некаталитически или с применением катализатора.
Предпочтительно парофазную смесь конвертируют в синтез-газ каталитически. В предпочтительном варианте осуществления изобретения способ осуществляют путем подачи парофазной смеси в конвективную часть установки парового реформинга. В указанной конвективной части установки парофазную смесь можно смешивать с природным газом и дополнительным водяным паром. Это делает способ очень универсальным, поскольку допускается применение как природного газа, так и глицерина, в зависимости от их доступности. Более того, способ позволяет соединять блок получения парофазной смеси (то есть газожидкостную контактную установку) с конвективной частью имеющейся в наличии установки парового реформинга.
Парофазную смесь можно смешивать с природным газом и водяным паром в любом отношении, при условии, что в полученной смеси (кислородсодержащего) углеводорода, водяного пара и природного газа молярное отношение H2O/C составляет, по меньшей мере, 2.
Предпочтительно, чтобы смесь, покидающая конвективную часть установки, на 10-100 об.% состояла из парофазной смеси. Более предпочтительно, чтобы смесь, покидающая конвективную часть установки, содержала метан и глицерин в молярном отношении метан:глицерин, находящимся в диапазоне от 1:1 до 3:1, более предпочтительно – приблизительно 2:1.
Смесь, покидающая конвективную часть установки, проходит через установку парового реформинга обычным образом, и синтез-газ производится в слое традиционного катализатора парового реформинга. Примерами катализаторов парового реформинга являются нанесенные на подложку катализаторы из Ni, Co, Pt, Pd, Ir, Rh и Ru. С учетом затрат в расчете на единицу активности катализатора обычно предпочтительными являются никелевые катализаторы. Такие никелевые катализаторы обычно добавляют в установку реформинга в форме оксида никеля и восстанавливают до металлического состояния непосредственно перед применением. В качестве подложки для металла можно применять другие материалы-носители, такие как оксид алюминия, оксид магния, диоксид кремния, алюминат кальция или их комбинации. Катализатор может быть, например, в форме гранул, дисков, крупных кусочков или колец. Катализатор может присутствовать в неподвижном слое или кипящем слое или может наноситься на монолитную керамическую подложку.
Слой катализатора обычно работает при температуре в диапазоне от 300 до 1050°C, более предпочтительно от 300 до 950°C и наиболее предпочтительно – от 350 до 850°C.
Полученный синтез-газ можно применять для синтеза различных химических продуктов, таких как метанол, уксусная кислота, метилформиат, этанол, пропанол, изобутанол, этиленгликоль, простой диметиловый эфир и н-бутанол.
В частности, настоящее изобретение также относится к способу производства метанола, который включает в себя стадии (i) получения синтез-газа согласно настоящему изобретению, с последующей (ii) конверсией синтез-газа в метанол. Согласно указанному способу синтез-газ производят, как описано выше, и затем полученный газ подвергают сжатию и конверсии в метанол с применением традиционных способов.
1. Способ получения парофазной смеси для получения синтез-газа с молярным отношением Н2О/С, равным, по меньшей мере, 2, которая содержит водяной пар и, по меньшей мере, один углеводород или кислородсодержащий углеводород с точкой кипения в диапазоне от -50°С до 370°С при атмосферном давлении, при котором водяной пар вводят в нижнюю часть дистилляционной колонны, а (кислородсодержащий) углеводород вводят в верхнюю часть упомянутой дистилляционной колонны.
2. Способ по п.1, при котором кислородсодержащий углеводород представляет собой глицерин, а водяной пар, вводимый в дистилляционную колонну, имеет давление 10-30 бар и температуру 270-380°С.
3. Способ по п.1 или 2, при котором молярное отношение Н2О/С в парофазной смеси находится в диапазоне от 2,5 до 4.
www.findpatent.ru
Синтез-газ получение – Справочник химика 21
Процессы в расплаве являются вариантом газификации угля в режиме уноса. В них уголь и газифицирующий агент подаются на поверхность расплавов металлов, шлаков или солей, которые играют роль теплоносителей. Наиболее перспективен процесс с расплавом железа, поскольку можно использовать имеющиеся в ряде стран свободные мощности кислородных конвертеров в черной металлургии [97]. В данном процессе газогенератором служит полый, футерованный огнеупорным материалом аппарат-конвертер с ванной расплавленного (температура 1400—1600°С) железа. Угольная пыль в смеси с кислородом и водяным паром подается с верха аппарата перпендикулярно поверхности расплава с высокой скоростью. Этот поток как бы сдувает образовавшийся на поверхности расплава шлам и перемешивает расплав, увеличивая поверхность его контакта с углем. Благодаря высокой температуре газификация проходит очень быстро. Степень конверсии углерода достигает 98%, а термический к. п. д. составляет 75— 80%. Предполагается, что железо играет также роль катализатора газификации. При добавлении в расплав извести последняя взаимодействует с серой угля, образуя сульфид кальция, который непрерывно выводится вместе со шлаком. В результате удается освободить синтез-газ от серы, содержащейся в угле, на 95%. Синтез-газ, полученный в процессе с расплавом, содержит 677о (об.) СО и 28% (об.) Нг. Потери железа, которые должны восполняться, составляют 5—15 г/м газа. [c.97]На рис. 12.5 приведена технологическая схема производства метанола по трехфазному методу на медь-цинковом катализаторе из синтез-газа, полученного газификацией каменного угля, производительностью 650 тыс. т в год. [c.267]
В последнее время резко увеличилась потребность в чистой окиси углерода, как сырье для производства полиуретанов и акри-латных пластических масс. Источником сравнительно дешевой окиси углерода может служить синтез-газ, полученный на базе-углеводородов природного и попутного газов. [c.111]
Тепло отходящих газов используют для получения технологического пара. В процессе можно использовать синтез-газ. полученный неполным окислением угля или тяжелых нефтяных остатков в присутствии пара. Этот газ содержит в основном Н2, СО и небольшое количество СО2. После очистки от сернистых соединений состав газа регулируют таким образом, чтобы получить оптимальное соотношение Н2 (СО+СО2), и газ вводят в реактор синтеза без дополнительного компримирования. [c.125]
Получение синтез-газа в двигателе внутреннего сгорания показано на рис. Сырьем служит смесь природного газа (метана) с кислородом мольное соотношение кислорода и метана от 0,7 до 1,0. Специально сконструированный восьмицилиндровый двигатель со степенью сжатия, равной 7, имеет рабочий объем 42 л. Наилучшие результаты были получены при температуре 550 °С и соотношении кислород метан, равном 0,8. Выхлопные газы при этом содержат 58% водорода и 35% окиси углерода. Через 1000 ч работы в цилиндрах двигателя наблюдалось незначительное коксообразование. Сравнение этого процесса с процессами частичного сжигания и конверсии с водяным паром показало, что синтез-газ, полученный в двигателе внутреннего сгорания, дешевле. [c.82]
Сырьем для синтин-процесса является синтез-газ, получение которого описано ранее и который состоит главным образом из окиси углерода и водорода. Этот газ нагревается до температуры 180—210° и пропускается через реакторы, заполненные катализатором, т. е. веществом, которое способствует и ускоряет протекание реакции. В существующем процессе применяют катализатор. [c.242]
Синтетические жидкие топлива производят двумя различными способами прямой гидрогенизацией ТГИ в жидкие продукты и синтезом их на основе синтез-газа, полученного газификацией ТГИ. Схематически это представлено следующим образом (рис. 119). Как видно, второй способ включает промежуточную технологическую стадию — процесс газификации. [c.233]
На основании данных, полученных для катализаторов № 2 и № 3 (см. табл. 4.1), была сделана технико-экономическая оценка процесса применительно к установке мощностью 300 тыс. т этилена в год. Расчеты показали, что себестоимость этилена и пропилена в 2,0—2,5 раза выше себестоимости этилена, производимого по существующей технологии в настоящее время. Меньшая величина относится к синтез-газу, полученному из природного газа, большая — из угля. Необходимо отметить, что в себестоимости 75—80% приходится на сырье. Поэтому производство низших олефинов из синтез-газа в районе добычи угля открытым способом и удаленном от источников нефти может оказаться рентабельным в не очень отдаленном будущем. Кроме того, технико-экономические показатели процесса могут быть улучшены за счет использования образующегося в ходе синтеза диоксида углерода (например, в процессах карбонизации) [241]. [c.306]
Разработанный процесс предназначается в основном для производства метанола для энергетических целей с использованием синтез-газа, полученного газификацией угля. Соответственно, отношение водорода к оксиду углерода в получаемом синтез-газе меньше стехиометрического. Используемая жидкая фаза должна быть стабильной в условиях синтеза — не изменять химического состава и не участвовать в химических взаимодействиях с исходными компонентами и продуктами реакции при повышенных температурах и давлениях. В качестве жидкой фазы можно использовать парафины, циклопарафины, ароматические углеводороды, минеральные масла. Наиболее предпочтительными являются парафины и циклопарафины, обладающие ограниченной смешиваемостью с метанолом. Концентрирование метанола в жидкой фазе замедляет реакцию его образования. Жидкие углеводороды перед использованием в процессе синтеза метанола должны быть обязательно очищены от соединений серы. [c.194]
В табл. 4.1 приведены типичные составы синтез-газа, полученного методом неполного окисления из различного углеводородного сырья. [c.85]
В настоящее время одно из самых перспективных направлений использования синтез-газа — получение из него синтетических моторных топлив. [c.596]
Состав синтез-газа, полученного конверсией с водяным паром углеводородного сырья, в зависимости от состава последнего и условий процесса может несколько изменяться. Содержание водорода в синтез-газе колеблется в пределах 74—80 /о, СО 10—147о, СОз Ю— 15% имеется также некоторое количество непрореагировавших углеводородов. [c.27]
Технология синтеза метанола. Для производства метанола применяют синтез-газ, полученный окислительной конверсией метана водяным паром и имеющий состав, близкий к соотношению С0 Н2=1 2. [c.736]
Синтез-газ, полученный из природного газа, направляют на доохлаждение с целью конденсации воды. Далее синтез-газ долциркуляционным газом н через теплообменник 6, обогреваемый горячим реакционным газом, поступает в два параллельно работающих реактора синтеза метанола 7. Реакторы трубчатого типа охлаждаются циркулирующей в межтрубном пространстве водой. Пар направляется в паросборник 8, куда подается и химически очищенная вода. Конденсат из паросборника вновь поступает в реакторы 7, а водяной пар высокого давления направляется на перегрев и используется в турбинах. Продукты реакции направляются через теплообменник 6, где отдают свое тепло синтез-газу, в конденсатор-холодильник 9 и в газосепаратор 10 для отделения метанола от циркуляционного газа. Последний поступает на прием циркуляционного компрессора 11 вновь направляется в систему синтеза. Часть газа отдувают для удаления поступающих в систему инертных примесей (главным образом метана и азота). Ме-танол-сырец из газосепаратора 10 направляется на ректификацию. [c.337]
Одной из задач введения промоторов в катализатор является уменьшение отравляющего действия ядов, к числу которых относятся СО, СО , О2 и Н О, обычно содержащиеся в синтез-газе (что обусловлено методом его получения). Хлориды и соединения серы также отравляют катализатор, но они значительно реже встречаются в синтез-газе, полученном современными методами. Время жизни катализатора зависит от жесткости условий работы и действия ядов обычно это 3-5 лет, но если катализатор работает под давлением 1000 атм, оно может не превышать 3-4 х месяцев. Отработанный катализатор выбрасывают, так как регенерировать его экономически невыгодно. [c.227]
Широко развивается кооперирование производств азотной промышленности и органического синтеза на базе совместного использования природного сырья (получение из него ацетилена и синтез-газа получение азото-водородной и метанольной газовых смесей), а также использования продукции азотнотукового комбината в качестве основного или вспомогательного сырья для производства органических продуктов. [c.11]
В настоящее время в США около четверти аммиака производят из синтез-газа, полученного методом неполного окисления (остальное вырабатывают каталитической конверсией с водяным паром) [c.70]
Катализаторы синтеза углеводородов являются смешанными они легко отравляются сернистыми соединениями и отдельными ароматическими углеводородами, находящимися в синтез-газе, полученном из угля, в случае его плохой очистки. Поэтому обязательна тщательная предварительная очистка газа от всех веществ, вызывающих частичное или полное отравление катализатора. [c.178]
Пиже приводится примерный состав синтез-газа, полученного в печах внешнего обогрева [c.162]
Сырьем для синтин-процесса является синтез-газ, получение которого описано ранее и который состоит главным образом из [c.203]
Синтез-газ, полученный при окислительном пиролизе метановой фракции, направляется на синтез метанола, который перерабатывается в формальдегид. На базе формальдегида и карбамида организуется производство карбамидных смол. [c.178]
Содержание сернистых соединений в синтез-газе, полученном различными способами, колеблется в довольно широких преде лах [c.174]
По данным отдельных заводов, в синтез-газе, полученном непосредственно из угля в печах с внутренним или внешним обогревом, жидких углеводородов содержится от 0,14 до 0,25 г/нм газа. Главным образом это бензол, толуол, ксилол, на( алин, а также сернистые органические соединения — сероуглерод, тиофен и др. [c.175]
Синтез-газ, полученный из топлива тем или иным способом, подается в газгольдер, откуда он забирается турбогазодувкой и подается на очистку от минеральной и органической серы. После очистки газ охлаждается в скруббере и поступает на компрессию. Компрессия может быть осуществлена двухступенчатым компрессором с приводом от паровой турбины и электромотора. Если синтез проводится с добавкой к газам, после второй и третьей ступеней, водорода, то часть газа после компрессии направляется на конверсию, а основная часть поступает на синтез в первую ступень. Если синтез проводится без добавки водорода на вторую и третью ступени, то синтез-газ весь поступает на синтез в первую ступень. [c.199]
Второй случай — это очистка газа для синтеза аммиака. Даже небольшое количество водяных паров, которое вводится в колонну с газом под большим давлением, является для катализатора ядом. Синтез-газ, полученный низкотемпературным разделением газа, практически не содержит водяных паров, и, следовательно, осушка газа не требуется. Из газов, получаемы другими способами, влага удаляется введением в цикл синтеза свежей азотоводородной смеси до того, как происходит полное сжнжсние ампосле охлаждения газа в сепараторах отделяется очень концентрированная аммиачная вода ( —99,92% аммиака), давление водяного пара лад которой очень незначительно. [c.353]
Производство аммиака в довоенный период основывалось на применени1 синтез-газа, полученного газификацией кокса, и коксового газа от располо жеииых вблизи коксохимических заводов, а также электролитического водо рода. В 50-е годы были открыты крупные месторождения природного газг на Северном Кавказе, Украине, позже—в Средней Азии, Западной Сибир1 а др., возросла его добыча. Это создало предпосылки к использованию при родного газа в качестве сырья для производства аммиака, метанола. [c.420]
В синтез-газах, полученных частичным окислением содержащего серу углеводородного топлива, в качестве важнейшего органического сернистого соединения присутствует сероокись углерода, которая в присутствии некоторых катализаторов легко прелращается в сероводород в результате реакций гидрирования илп гидролиза. Окиспожелезные катализаторы обладают активностью одновременно в реакциях водяного газа и превращения сероокиси углерода в сероводород, тогда как окисные алюмохромовые и алюмо-хром-медные катализаторы можно использовать для избирательного гидролиза сероокиси углерода в присутствии больших количеств окиси углерода. Кроме того, разработаны катализаторы, содержащие окислы меди, хрома и ванадия, для удаления сероводорода п органических сернистых соединении пз синтез-газа. [c.327]
Наряду с водородом получается смесь водорода с окисью углерода, называемая синтез-газом. Синтез-газ применяется для получения метанола и в оксосинтезе. Стоимость синтез-газа, полученного окислительным пиролизом, самая низкая. Так, если ее принять за 100%, то стоимость синтез-газа каталитической конверсией метана с водяным паром составляет 180—250%, а гавификацией кокса — 450—500%. [c.22]
В синтез-газе, полученном газификацией твердого топлива, всегда содержатся благородные газы, прежде всего аргоп (около /78 от количества азота). Аргоп отсутствует только в азоте, полученном сжижением воздуха, так как легко отделяется вследствие более высокой температуры кипения. Следовательно, только синтез-газ, полученный смешением электролитического водорода и азота, не содержит ни метана, ни аргона. [c.125]
Наиболее крупными потребителями кислорода в химической промышленности являются производства ацетилена и синтез-газа, который используют для получения аммиака и оксоиродуктов. Так, в США 40% метилового спирта и 25% аммиака производят из синтез-газа, полученного методом неполного окисления. При этом на 1 т метилового спирта расходуют 0,6 т кислорода, а на 1 т аммиака — 0,8 т кислорода [251]. [c.447]
В промышленных условиях для производства метанола или высших спиртов применяют синтез-газ, полученный смешанной паровой и углекислотной или пароуглекислородной конверсией метана. [c.21]
Нефтехимическая промышленность в качестве сырья использует продукты переработки нефти. Задачи этой отрасли — обеспечение многих оргаиических производств углеводородным сырьем (олефинами, ацетиленом, ароматическими углеводородами, синтез-газом), получение многотоннажяых органических веществ и синтетических полимерных материалов. [c.7]
Помимо сжиженных углеводородов целевыми продуктами газопе-реработки являются моторные топлива, метанол и другие оксигенаты, включая высокооктановые компоненты моторных топлив. Производство жидких моторных топлив из природного газа в ряде стран уже осуществляется в промышленных масштабах. В Новой Зеландии на заводе фирмы “Мобил Ойл” (г. Мотонди) налажено производство синтетических высокооктановых бензинов. Природный газ конвертируют в синтез-газ, а затем полученный из него метанол на цеолитных катализаторах превращают в смесь жидких углеводородов. Производительность установки – 570 тыс. т моторных топлив в год. В Малайзии на заводе фирмы “Шелл” (г. Бинтулу) синтез-газ, полученный некаталитическим высокотемпературным парциальным окислением метана, превращают по реакции Фишера-Тропша в среднедистиллятные фракции и высокомолекулярные парафины. Парафины затем путем [c.17]
Па основе изложенного впервые развиты методы технологической организации промышленных неравновесных химических процессов (получение пленок, порошков, травление, модификация поверхностей материалов и изделий, переработка отходов ряда промышленных производств на синтез-газ, получение карбидов, карбонитридов и т. п.). Это позволило обосновать научно-техни-ческне аспекты оптимизации, устойчивости и управления неравновесными процессами в химической, электронной, металлургической, радиотехнической, стекольной, автомобильной, инструментальной и других отраслях иромышлепностн. [c.42]
Процесс Бенфилд разработан фирмой Юнион Карбайд для извлечения СО2, HjS и OS из высокосернистого природного и других газов, в том числе из водорода и различных синтез-газов, полученных конверсией нефти или газа либо неполным окислением. Процесс нашел широкое применение для очистки отходящих газов нефтепереработки, особенно содержащих кислород, а также для очистки заменителей природного газа. [c.113]
Справочник азотчика Том 1 (1967) — [ c.71 , c.95 , c.172 , c.187 , c.194 ]
Технология связанного азота Синтетический аммиак (1961) — [ c.0 ]
Химия и технология основного органического и нефтехимического синтеза (1971) — [ c.120 ]
Курс технологии связанного азота (1969) — [ c.120 , c.175 , c.182 ]
Технология связанного азота (1966) — [ c.14 , c.18 , c.72 ]
Теория технологических процессов основного органического и нефтехимического синтеза Издание 2 (1975) — [ c.109 ]
Производство мономеров и сырья для нефтехимического синтеза (1973) — [ c.227 , c.246 ]
Справочник азотчика Т 1 (1967) — [ c.71 , c.95 , c.172 , c.187 , c.194 ]
chem21.info
Добавить комментарий