Микротоннелирование технология при прокладке трубопроводов – Руководство по применению микротоннелепроходческих комплексов и технологий микротоннелирования при строительстве подземных сооружений и прокладке коммуникаций закрытым способом документ, – Руководство
Микротоннелирование – СУ87
Технология
Сущность технологии микротуннелирования состоит в том, что проходка в грунте осуществляется проходческой машиной — щитом, поступательное движение которого обеспечивает мощная домкратная станция, установленная в шахте на глубине, соответствующей требуемой глубине прокладки трубопровода. Усилие домкратной станции передаётся проходческому щиту через став железобетонных труб, который наращивается по мере продвижения щита.
Во время подготовительного периода производится строительство двух шахт — стартовой и приёмной. Диаметры шахт зависят от ряда параметров, но не превышают нескольких метров, а глубина их соответствует глубине прокладки трубопровода. В стартовой шахте устанавливается мощная дом-кратная станция, на которую помещается проходческий щит. С помощью домкратов осуществляется проходка щита в грунте на длину, соответствующую длине применяемых труб продав-ливания, после чего на домкратную станцию помещается последующая труба и процесс повторяется.
Разработка породы при проходке ведётся режущим колесом проходческой машины. Разработанный грунт смешивается с водой, которая по соединительным линиям подаётся питающим насосом в зону режущего колеса. Полученная взвесь транспортным насосом подаётся в отстойник, установленный на поверхности около стартовой шахты.
В отстойнике происходит осадка грунта, после чего вода снова используется в технологическом процессе, а осаженный грунт вывозится. Поэтапное наращивание става труб обеспечивает дальнеишую проходку щита до выхода в приёмную шахту. После этого щит демонтируется, а став труб остаётся в земле. Весь процесс проходки происходит под управлением, осуществляемым из контейнера управления, который установлен на поверхности и оснащён электронной техникой.
Точность проходки обеспечивается применением лазера. Став труб, оставшийся в земле после демонтажа комплекса, является готовым ненапорным трубопроводом либо футляром для прокладки других коммуникаций, например, электрокабелей.
www.su87.ru
Микротоннелирование AVN | Статьи | ТРУБОПРОВОД.рф
Эта технология не требует раскопки традиционных траншей по всей протяженности прокладки труб, что позволяет свести к минимуму воздействие на экологию и привычную жизнедеятельность города в процессе строительства.
Микротоннелирование – это бестраншейный метод строительства коллекторов в условия стесненной городской застройки. Суть данного метода заключается в том, что прокладка труб в грунте производится проходческим микрощитом AVN. Его поступательные движения обеспечивает мощная домкратная станция, которая передаёт толкающее усилие к щиту через колонну железобетонных труб, которая наращивается по мере продвижения вперёд.
Технология микротоннелирования
На подготовительном периоде разрабатываются два котлована (стартовый и приемный). Расстояние между стартовой и приемной шахтами составляет от 50 до 500 м. Домкратная станция устанавливается в стартовом котловане на глубине, необходимой для осуществления прокладки трубопровода. При длине проходки свыше 200 метров используется промежуточная домкратная станция. В плане шахты могут быть круглыми или квадратными. Размеры их сторон до 6 м в зависимости от типа микрощита.
Разработка грунта производится режущим инструментом проходческого щита. Грунт перемешивается с водой (или бентонитовым раствором), которая подаётся в забой по подводящим линиям, а по отводящим линиям полученная взвесь попадает в отстойник, который находится у стартового котлована.
Поэтапное продвижение микрощита вперед заканчивается в приемном котловане, после чего он демонтируется, оставив за собой готовый коллектор. Методом микротоннелирования прокладываются стальные или специальные железобетонные трубы для микротоннелирования (тюбинги).
Навигационная система управления.
Электронна лазерная система управления ELS для прямолинейных участков длиной до 200 метров состоит из трех основных составляющих:
- Лазерная станция;
- Измерительное колесо;
- Мишень.
Для прямолинейных участков длиной от 200 до 400 метров применяется ELS-HWL (электронная лазерная система с гидростатическим водяным уровнем). Поскольку при большой длине проходки внутри трубы может быть разная температура воздуха, это приводит к преломлению лазера, что в свою очередь изменяет направление машины по вертикали. Гидростатический уровень определяет точные данные по выстоте, независимо от температуры.
Для проходки криволинейных участков в микротоннелировании применяется система с гироскопом GNS-P.
Данная система применяется без лазера, с ориентированным на север гироскопом, при внутреннем диаметре трубы от 800мм.
Преимущества микротоннелирования.
Отличительной чертой данного метода является высокая точность проходки, отклонение от проектной оси составляет не более 30мм. Это обеспечивается специальным компьютерным комплексом управления на основе системы лазерного наведения щита.
Микротоннелирование комплексом AVN осуществляется в автоматическом режиме. Вся проходка наблюдается непосредственно оператором, его местонахождение базируется в центре управления микротоннеля.
Технология микротоннелирования помогает прокладывать трубопроводы в разных категориях грунтов: от суглинков и водонасыщенных песков до скальных пород. Так же немаловажным преимущество метода микротоннелирования является высокая скорость проходческих работ – до 15 метров в сутки.
Какие задачи решает микротоннелирование? Область применения.
Данная бестраншейная технология помогает решить ряд важных задач:
- Строительство подземных инженерных коммуникаций в различных населенных пунктах: города, поселки и промышленные зоны;
- Прокладка коммуникаций всех видов: водопровод, канализация, теплоснабжение и прочие;
- Строительство кабельных коллекторов;
- Прокладка труб под автодорогами, железными дорогами, взлётными полосами аэродромов и других встречающимися препятствиями;
В условиях плотной городской застройки, на большой глубине, строительство трубопровода зачастую возможно только с использованием микротоннелей AVN.
Источник:http://dvn-stroy.ru/articles/Mikrotonnelirovanie/
Технология микротоннелирования – СоюзДонСтрой
Микротоннелирование приобретает все большее применение как метод строительства коллекторов бестраншейным способом в крупных городах. Микротоннелирование уже в течение нескольких десятилетий является основным методом строительства коллекторов в странах Европы, Америки, Японии.
Важной особенностью технологии микротоннелирования является высокая точность проходки и постоянный контроль за ее траекторией. Микротонелирование позволяет выполнять задачи по прокладке коммуникаций в сложнейших условиях, где раньше без специальных методов (водопонижение, замораживание и др.) делать было нечего.
ООО “СоюзДонСтрой” выполняет работы микротоннелепроходческими комплексами фирмы “Херренкнехт” AVN, EPB, TBM, 500/800/1200/1500/2000/2500/2850/3000/3600/4000/4500, позволяющим прокладывать стальные и железобетонные футляры наружным диаметром 500/4500 мм на расстояние до 5000 метров без промежуточных шахт в грунтах содержащих валуны и скальные включения.
С поверхности грунта строятся шахты: стартовые и приемные, расстояние между ними может достигать от 50 до 5000 метров, а глубина – порядка от 8 до 100 метров. В плане шахты могут быть круглыми или квадратными с размерами сторон около 5 метров.
Из стартовой шахты рабочий орган микротоннелепроходческого комплекса AVN (микрощит) осуществляет проходку при избыточном давлении воды в забое. Подача воды к режущему рабочему органу AVN и отсос образовавшейся пульпы выполняются насосами, установленными на поверхности грунта рядом со стартовой шахтой. В стартовую шахту подаются также отдельные звенья стальных или железобетонных труб обделки, которые вдавливаются в грунт домкратами, что позволяет осуществлять горизонтальную проходку коллектора.
Корректируют точность проходки с помощью наземной станции управления по лазерному лучу. Все технологические и контрольные функции при микротоннелировании компьютеризованы.
Отработанная пульпа насосами подается в отстойник, вода из которого повторно используется в проходке, а твердый осадок по мере накопления вывозится на свалку.
Микротоннелирование комплексом AVN осуществляется в автоматическом режиме, под контролем операторов, находящихся в блоке управления.
Микротоннелирование представляет собой процесс установки различного рода коммуникаций без вскрытия поверхности. Это очень удобно, так как исключает дополнительные затраты на рытье траншей для прокладывания систем и разрушение верхнего слоя поверхности (асфальта, почвы). Особенно актуальна описываемая возможность для больших городов, где всякого рода ремонтные работы вынуждают занимать большие территории, а значит препятствовать движению как транспорта, так и жителей.
Специальная проходческая машина использует микрощит, который проделывает в грунте скважину необходимого диаметра и на необходимой глубине. Щит приводится в движение за счет мощной домкратной станции, которая располагается в шахте; шахта предварительно сооружается в обязательном порядке на глубине, равной метрике прокладываемого объекта. Первая шахта, стартовая, необходима для погружения в нее домкратов. Именно домкраты обеспечивают проходку щита на длину, соответствующую длине труб, которые продавливают грунт. Земля, остающаяся после работы, смешивается с водой, подающейся питающим насосом режущего колеса. Полученная смесь направляется в отстойник, где грунт оседает и в последующем вывозится из шахты. Максимальная точность работ достигается устройством лазерной навигации.
Использование технологии микротоннелирования
Использование технологии микротоннелирования возможно во многих случаях:
- для строительства футляров для кабелей, нефте- и газопроводов;
- для строительства подземных систем города – водоснабжения, канализации, электро- и теплосетей;
- для оснащения взлетно-посадочных полос, железных дорог и автомагистралей;
- для поддержки тоннелей крупных диаметров;
В последнее время в городском строительстве устойчиво укрепилась тенденция к интегрированной застройке. Постройка новых или реконструкция уже существующих зданий происходит, как правило, в условиях в городской плотной застройки, рядом с соседними сооружениями. Из-за такого подхода сильно ограничивается площадь, на которой могут проводиться работы, и возникают трудности с проведением инженерных коммуникаций к объектам. В таком случае идеальным методом прокладки трубопроводов является микротоннелирование.
Мы оказываем услуги в ЮФО, Центральной России и Крыму, в таких городах как:
- Ростов-на-Дону
- Краснодар
- Ставрополь
- Крым
- Волгоград
- Москва
- Тында
- Минск
- Выборг
- Сочи
- Самара
и стран ближнего зарубежья. По всем вопросам обращайтесь к нашим специалистам по телефонам или по электронной почте в разделе «Контакты».
soyuzdonstroy.ru
Метод микротоннелирования
Микротоннелирование приобретает все большее применение как метод строительства коллекторов бестраншейным способом в крупных городах. Технология микротоннелирование уже в течение нескольких десятилетий является основным методом строительства коллекторов в странах Европы, США, Японии. Важной особенностью технологии – микротоннелирование является высокая точность проходки и постоянный контроль за ее траекторией. Микротоннелирование позволяет выполнять задачи по прокладке коммуникаций в сложнейших условиях, где раньше без специальных методов (водопонижение, замораживание и др.) делать было нечего. Метод позволяет с точностью до нескольких сантиметров прокладывать под землей коллектора большого диаметра.
Работы по строительству инженерных сетей методом горизонтально-направленного бурения скважин производятся в три этапа:
1. Бурение пилотной скважины
2. Расширение пилотной скважины
3. Протаскивание трубопровода в скважину.
Сущность технологии микротоннелирования состоит в том, что проходка в грунте осуществляется проходческой машиной (щитом), поступательное движение которой обеспечивает мощная домкратная станция установленная в шахте на глубине, соответствующей глубине прокладки трубопровода. Быстрая (в среднем скорость проходки 10–15 м/сут.), практически безосадочная (осадки дневной поверхности не превышают 10 мм) и точная (отклонения в пределах 10–20 мм) по направлению прокладка трубопроводов в сочетании с возможностью ведения строительства во всем диапазоне инженерно-технологических и гидрогеологических условий (от слабых водонасыщенных грунтов до крепких скальных пород) без применения каких-либо специальных способов работ (замораживание, водопонижение, химическое закрепление грунтов и т. д.) — вот основные достоинства микротоннелирования. С помощью домкратов осуществляется проходка щита в грунтах на длину, соответствующую длине применяемых труб продавливания, после чего на домкратную станцию помещается последующая труба и процесс повторяется. Разработка грунта при проходке ведется рабочим органом проходческой машины.
Укрепление грунтов
Для повышения несущей способности грунтовых оснований применяют следующие способы искусственного закрепления грунтов:
цементацию и битумизацию
химический
термический
электрический
электрохимический
механический и др.
Цементация — это процесс нагнетания в грунт жидкого цементного раствора или цементного молока по ранее забитым полым сваям. Когда процесс нагнетания заканчивается, сваи вынимают. Цементация подходит только для уплотнения крупных и средних песков.
Химическим способом (силикатизацией) закрепляют песчаные и лёссовые грунты, нагнетая в них химические растворы.
Термическое закрепление заключается в обжиге лёссовых грунтов раскаленными газами, которые подаются в толщу грунта вместе с воздухом через жаропрочные трубы в пробуренных скважинах.
Электрическим способом закрепляют влажные глинистые грунты. Способ заключается в использовании эффекта электроосмоса, для чего через грунт пропускают постоянный электрический ток с напряженностью поля 0,5-1 В/см и плотностью 1-5 А/кв.м. При этом глина осушается, уплотняется и теряет способностью к пучению.
Электрохимический способ отличается от предыдущего тем, что одновременно с электрическим током через трубу, являющуюся катодом, в грунт вводят растворы химических добавок (хлористый кальций и др.). Благодаря этому интенсивность процесса закрепления грунта возрастает.
Механический способ укрепления грунтов имеет следующие разновидности: устройство грунтовых подушек и грунтовых свай, вытрамбовывание котлованов и др.
Устройство грунтовых подушек заключается в замене слабого грунта основания другим, более прочным, для чего слабый грунт удаляют, а на его место насыпают прочный грунт и послойно утрамбовывают.
При устройстве грунтовых свай в слабый грунт забивают сваю-лидер. В полученную после извлечения этой сваи скважину засыпают грунт и послойно уплотняют.
Вытрамбовывание котлованов осуществляют с помощью тяжелых трамбовок, подвешенных на стреле крана. Этот способ менее сложен, чем способ грунтовых подушек, поскольку не требует замены грунта основания.
Уплотнение котлованов значительных размеров может осуществляться гладкими или кулачковыми катками, трамбующими машинами, виброкатками и виброплитами.
Классификация методов укрепления грунтов
Метод | Применяемые материалы и способы воздействия |
Укрепление гранулометрическими добавками | Щебень, гравий, песок, шлаки, глины, суглинки |
Укрепление органическими вяжущими | Битумы твёрдые и жидкие, дёгти, битумные и дегтевые эмульсии и пасты, синтетические смолы, древесные пески и др. |
Укрепление минеральными вяжущими материалами | Цемент, известь, силикат натрия (жидкое стекло) |
Термическая обработка | Местное топливо (дрова, уголь, электрический ток, газ) |
Укрепление солевыми растворами | Хлористый кальций, хлористый натрий и др. |
Электрохимические обработки | Электрический постоянный ток (с применением электролитов) |
Комплексные методы | Органические и минеральные вяжущие с гранулометрическими добавками, органические вяжущие с активными добавками и т. д. |
Известкование грунтов
В 1926 году в Ленинградском дорожно-исследовательском бюро были проведены опыты по известкованию грунтов. В ходе опытов было установлено, что добавки гашёной извести в количестве 5 % от массы грунта уменьшает липкость и пластичность глинистых грунтов и увеличивает сопротивление размоканию. С 1927 по 1931 год под Москвой были проведены опытные работы по укреплению известью глинистых и чернозёмных грунтов [6]. В послевоенный период известкование грунтов получило дальнейшее развитие в работах ДорНИИ, Саратовского автодорожного института и других НИИ. Были разработаны практические рекомендации по внедрению метода известкования грунтов в дорожном строительстве. С 1950 по 1955 год был построен ряд опытных участков дорог, где в качестве оснований, а также покрытий, использовался местный грунт, укреплённый известью. По данным С. А. Морозова [6], известкование дерновоподзолистых грунтов обеспечило во всех опытных участках более высокие показатели прочности образцов на сжатие в водонасыщенном состоянии, чем при укреплении цементом.
Однако известкованные грунты имеют низкую морозоустойчивость, поэтому их надо применять главным образом в основаниях дорожных одежд.
Силикатирование
При взаимодействии жидкого стекла с грунтом образуется гель кремнекислоты, который со временем твердеет (особенно в присутствии катализатора, например, хлористого кальция) и таким образом связывает частицы грунта между собой. Первые производственные опыты по применению жидкого стекла в дорожном строительстве были проведены в 1928 году в Ленинградской области, Белоруссии, Украине и в других регионах [6]. Большой вклад в развитие методов силикатирования грунтов внесли учёные Б. А. Ржаницын и В. В. Аскалонов, которые разработали и теоретически обосновали 2-растворный способ силикатизации песчаных и гравелистых грунтов и 1-растворный способ по укреплению лёссовых грунтов. Оба эти метода нашли широкое применение в метро- и тоннелестроении, а также при укреплении фундаментов и оснований промышленных сооружений. В дорожном строительстве жидкое стекло не получило широкого распространения, за исключением постройки опытных участков, а также силикатирования щебёночных шоссе по методу пропитки и поверхностной обработки. Причина — низкая морозостойкость силикатированных грунтов, а также неудобство в работе в связи с быстрым схватыванием и твердением смеси грунта с силикатом.
Цементация грунтов
Цементно-грунтовая технология основана на смешивании до однородного состояния цемента и естественного грунта при установленном содержании воды и уплотнении с целью придания укреплённому грунту определённых свойств: прочности, устойчивости, морозостойкости и т. д. [4]
Таблица 2. Расход цемента в зависимости от характера грунта
Характер грунта | Расход Цемента | |
% сухого грунта | кг/м3 уплотненного основания | |
Гравийно-песчаный | 4-7 | 80-120 |
Суглинистый песок | 6-10 | 120-160 |
Песок с одним рядом частиц | 8-12 | 150-200 |
Суглинок | 7-12 | 120-200 |
Глина | 10-16 | 180-240 |
При укреплении пластичного суглинка применяют смесь извести (2–3 %) и цемента [4]. Кроме того, для пластичных грунтов проводят испытания на замораживание. При покрытии просёлочных работ цементогрунтом работу производят в несколько этапов.
1 этап. Выравнивание и очистка грунта с целью устранения органических веществ (дёрн, трава, корни и т. п.) и последующая планировка. Если грунт чрезмерно сухой, производят его увлажнение для выравнивания содержания и достижения однородности состава. Распределение цемента и извести по поверхности производят при небольших объёмах ручных работ, или с помощью навесного механизма — «распределитель» вяжущего.
2 этап. Перемешивание. Перемешивание грунта с вяжущим производят в несколько последовательных проходов машины (4–6 раз до получения однородной смеси) (рис. 1). Такая машина снабжена горизонтальными дисками или горизонтальными либо вертикальными лопатками. Обычно толщина цементно-грунтового слоя составляет 15–35 см.
3 этап. Профилирование и уплотнение. Профилирование полотна производят автогрейдерами. После этого грунт уплотняют несколькими проходами пневмо- или виброкатка. Степень уплотнения должна достигнуть не менее 90 % полученного на образце в лаборатории. После уплотнения цементогрунта катком приступают к окончательной планировке дорожного полотна.
4 этап. Завершающим этапом является защита дорожного покрытия пластиковой плёнкой или другим накрывочным материалом с последующим укрытием слоём песка. Подобная защита необходима для того, чтобы избежать испарения воды из обработанной почвы, и, кроме того, для предохранения дорожного полотна от дождя. Примерно такая же технология применяется для укрепления оснований шоссе некоторых типов. Только в этом случае выровненный и спланированный грунт смешивают с песком.
Технология устройства опускных колодцев.
При строительстве сооружений иногда возникает необходимость устройства мощных или глубоко заложенных фундаментов в сложных гидрогеологических условиях. В этом случае прибегают к устройству опускных систем. Опускная система – ограждающая конструкция в виде бетонной, железобетонной или металлической оболочки, погружаемой в грунт, внутри которой создаётся рабочее пространство для ведения строительно-монтажных работ. Опускные системы выполняются в виде опускных колодцев или кессонов. Опускные колодцы – открытые сверху и снизу полые, как правило массивные, конструкции, погружаемые под действием собственного веса по мере удаления из полости грунта. Кессоны – тонкостенные конструкции, имеющие сверху герметичное перекрытие, образующее рабочую камеру с избыточным давлением, позволяющим работать под водой. Технология производства работ у опускных колодцев и кессонов схожая, поэтому рассмотрим только опускные колодцы.
стенка грейфер Схема опускного
колодца
рабочая
камера
слабый грунт
рабочая
нож
песчаные сваи
Производство работ по устройству опускных колодцев разбивается на несколько циклов (строительных технологических комплексов):
1.Устройство основания под ножевую часть.
2.Бетонирование ножевой (опорной) части и
нижнего яруса опускного колодца.
3. Наращивание стенок опускного колодца.
4.Гидроизоляция стенок опускного колодца.
5. Опускание колодца.
6. Бетонирование днища опускного колодца.
Основание под ножевую часть.
При сооружении опускного колодца на слабых или неоднородных грунтах на предварительно спланированную площадку отсыпается песчаная подушка толщиной 0,3- 0,6м или устраиваются буровые песчаные (гравийные) сваи. Песчаные материалы отсыпаются слоями 0,2 м (подушка)…0,5м (сваи) с обязательным уплотнением. Бурение скважин под сваи производится буровыми станками по технологии принятой в ППР. Засыпка песчаной смеси в скважину ведётся через бункер-воронку, после отсыпки смесь увлажняется (для повышения эффекта уплотнения).
Для уменьшения и равномерной передачи на поверхность грунта давления от первого яруса опускного колодца до начала работ по его бетонированию (монтажу) под ножевую часть должно быть подготовлено специальное временное основание в виде деревянных, бетонных, железобетонных подкладок, сегментов, колец или других опорных конструкций.
Поперечные деревянные подкладки укладываются по периметру ножа кольца на предварительно выполненную песчаную подушку. Подкладки могут быть выполнены из окантованных брёвен или брусьев. Длина подкладок (Lп) принимается в зависимости от толщины стен ( Вст )опускного колодца :
Lп = Вст + (0,5…1м),
Железобетонное опорное кольцо выполняется разрезным (участками не более 1,5м) по песчаной подушке. Ширина железобетонного кольца составляет 0,8…1,2м.
Бетонирование опорной части.
Опорная часть опускного колодца является самой ответственной конструкцией, поэтому её изготовление выделяется в отдельный цикл. Конструктивно это нижний ярус колодца с выступом (12…15см), который обеспечивает полость с наружной стороны, которая используется для технологических потребностей (создание тиксотропной рубашки). В любом случае опорная часть изготавливается из монолитного железобетона. Нижний торец колодца (нож) представляет собой стальной скошенный элемент, связанный с арматурой.
Наращивание стенок опускного колодца
После изготовления опорной части производится начальное погружение колодца. В этот период отрабатывается и уточняется технология производства работ и принятая схема механизации.
Дальнейшее наращивание стенок опускного колодца производится в соответствием проектом: путём монолитного бетонирования стенок или монтаж сборных железобетонных элементов.
В зависимости от местных условий и объёмов работ приготовление бетонной смеси может производиться на центральном бетонном заводе или в непосредственной близости от опускного колодца. На современном этапе строительства наиболее предпочтительно применение мобильных бетонных заводов различной производительности и комплектации. Транспортирование смеси производится автобетоновозами или в контейнерах (на небольшое расстояние). Доставка смеси к месту укладки ведётся бетононасосами или кранами в бадьях.
Гидроизоляция стенок
Гидроизоляция стенок опускных колодцев должна выполняться до их опускания. Конструктивно (в зависимости от назначения) гидроизоляция может быть металлическая, торкрет-гидроизоляция, пропиточная синтетическими составами.
Металлическая выполняется с внутренней стороны колодца и при бетонировании может служить опалубкой.
Торкрет-изоляция наносится в несколько слоёв специальными агрегатами (марка цемента не ниже 400) по технологии установленной в ППР.
Пропитка осуществляется в несколько приёмов.
Погружение колодца
Погружение опускных колодцев в грунт является наиболее сложным и ответственным процессом при их строительстве. Перед погружением необходимо провести распалубочные работы, снять колодец с искусственного основания (подкладок), установить землеройное водоотливное и другое специальное оборудование. Последовательность удаления подкладок должна быть такой, чтобы не произошло перекоса кольца. При погружении грунт разрабатывается слоями равномерно по всей площади колодца.
Сухие грунты разрабатываются землеройной техникой внутри колодца и удаляются краном-грейфером или в бадьях. Обводнённые грунты разрабатываются средствами гидромеханизации (землесосом, гидромонитором) или с водоотливом. В этом случае предусматривается система водоотвода с мощными насосами. В практике строительства часто применяют водопонижение иглофильтровыми установками.
Систематический контроль за погружением колодца ведут с помощью рисок, нанесённых на стенки или нивелировочных контрольных реек, закреплённых по концам двух взаимно перпендикулярных диаметров кольца. Колодцы при погружении могут накренятся, поэтому проверку вертикальности следует производить на всех этапах погружения.
С целью уменьшения трения по наружной поверхности стен, возможно, применять способы нагнетания тиксотропного раствора, устройства полимерных покрытий и обмазок (снижают трение на 25…50%).
Кроме способа естественного погружения под действием собственного веса используют более прогрессивный (но более дорогой) способ принудительного погружения с помощью домкратов (вдавливания).
Устройство днища
Устройство днища опускного колодца является завершающей операцией. При сухих грунтах производится бетонирование по щебёночной подготовке и гидроизоляция металлическими листами.
При разработке рыхлых водонасыщенных грунтов возможны наплывы грунта из под ножа, что затрудняет устройство днища. В этом случае вначале устраивают бетонную подушку, укладываемую методами подводного бетонирования: восходящего раствора или вертикально перемещающейся трубы. После набора её бетоном достаточной прочности воду из колодца откачивают и под прикрытием подушки устраивают гидроизоляцию, а затем насухо бетонируют днище.
studfiles.net
Микротоннелирование как метод строительства коллекторов бестраншейным способом
Бестраншейная прокладка труб в Санкт-Петербурге реализуется двумя основными методами: микротоннелированием (продавливанием трубы) и горизонтальным направленным бурением; небольшой объем работ выполняется бурошнековыми установками и проколами с применением домкратных установок или пневмопробойников.
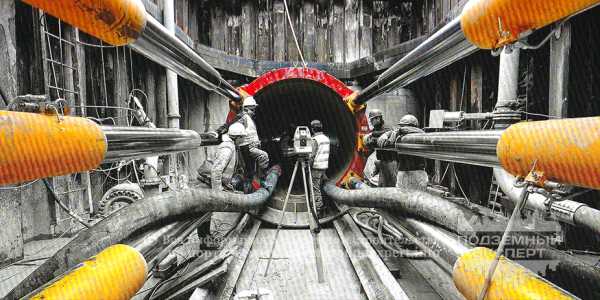
Микротоннелирование, Польша
Источник: Альбом The Wonders of Trenchless Technologies, ISTT
Если говорить о ситуации в мире, то микротоннелирование уже в течение нескольких десятилетий является основным методом строительства коллекторов в странах Европы, США, Японии. Важной особенностью технологии микротоннелирования является высокая точность проходки и постоянный контроль за ее траекторией. Микротоннелирование позволяет выполнять задачи по прокладке коммуникаций в сложнейших условиях, где раньше без специальных методов (водопонижение, замораживание и др.) делать было нечего. Метод позволяет с точностью до нескольких сантиметров прокладывать под землей выработки большого диаметра.
Преимущества технологии очевидны, за 2013 год компания «СТИС» построила 6709 м тоннелей методом микротоннелирования. Кроме ООО «СТИС» микротоннелированием в регионе занимаются еще несколько компаний – это ООО «Тоннельный отряд-4», ЗАО «ПРиСС», ООО «ПиК», которые также располагают оборудованием для строительства микротоннелей.
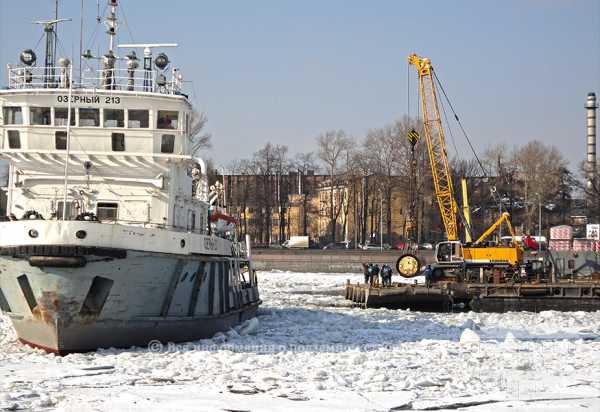
Строительство главного коллектора в Санкт-Петербурге
Преимущества нового оборудования для микротоннелирования
Первые проходки с применением микротоннелей в нашем городе были еще в 1998 году. Для компании «СТИС» активное развитие и строительство началось с 2003 года после приобретения тоннелепроходческого комплекса AVN2000 фирмы «Нerrenknecht». Очевидно, что к этому времени остро назрела необходимость замены старых, еще советских, щитов на современное проходческое оборудование.
Преимущества нового оборудования перед классическими на тот момент щитами было очевидно – это дало компании новый импульс развития. Объемы работ возросли, и скорость проходки иногда составляла до 39 м в день, в то время как традиционный способ с применением специальных методов не позволял выполнять более 90 м в месяц. Преимущества современного проходческого комплекса были доказаны на практике, и технология микротоннелирования получило мощный импульс развития. В экспоненциальном приближении длина построенных ООО «СТИС» тоннелей каждый год увеличивалась вплоть до конца 2013 года.
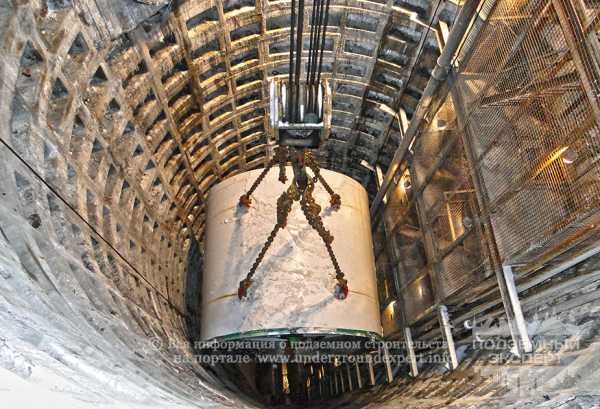
Строительство главного коллектора, Санкт-Петербург
На сегодняшний момент рынок микротоннелирования пребывает не в лучшем состоянии, что связано, в первую очередь, с окончанием масштабного проекта по завершению строительства Главного коллектора Санкт-Петербурга. Однако преимущества технологии и тот факт, что город растет, появляются новые жилые районы, ставит вопрос о строительстве различных тоннелей в разряд актуальных.
Преимущества технологии бестраншейной прокладки трубопроводов
В общепринятом понимании, микротоннелирование – это сооружение тоннеля, основанное на технологии продавливания труб, в котором управление проходческой машиной осуществляется удаленно, с поверхности земли. Диаметр микротоннелей обычно не превышает 2,5 м, но в мире известны случаи, когда диаметр составляет 3 м и более.
Преимущества технологии микротоннелирования можно перечислять долго, но основными являются:
- безопасность работ – нахождение персонала в тоннеле и в щите не предусмотрено;
- высокая скорость строительства, особенно в необводненных грунтах, где строительство котлованов для монтажа и выдачи щита ведется без замораживания;
- высокая точность строительства – 2 см на 1 км тоннеля в плане и профиле;
- отсутствие оседаний поверхности, что позволяет строить тоннели под любыми коммуникациями;
- возможность проходки на глубинах до 30 м;
- возможность проходки в любых грунтах.
Часто технология микротоннелирования применяется в строительстве объектов коммунального хозяйства – самотечных тоннельных коллекторов. Вода в тоннеле должна перемещаться, а для этого необходимо выдерживать проектный уклон на всем протяжении тоннеля. И технология микротоннелирования, в отличие от ГНБ, дает такую возможность: при движении щита оператор контролирует его положение с точностью 1 мм. Поэтому сегодня при строительстве коллекторов альтернативы микротоннелированию нет.
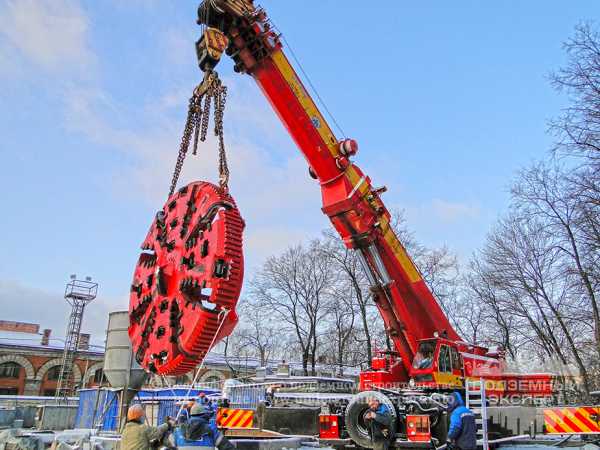
Щит AVN 3700
Раньше, до появления технологии микротоннелирования, тоннели в четвертичных отложениях проходили под избыточным давлением воздуха в призабойном пространстве. В результате вода «отжималась» с поверхности забоя, и он становился устойчивым. Далее грунт разрабатывали и выдавали через ствол на поверхность. Сейчас к таким методам мы уже не вернемся: проходка в кессоне не дает темпа и достаточно сложна в организации работ.
Технические проблемы при сооружении микротоннелей
В процессе строительства возникает немало непредвиденных трудностей, однако, опыт и квалификация специалистов позволяют успешно с ними справляться. Существуют и объективные обстоятельства, к которым можно отнести весьма непростую геологию нашего города. В четвертичных отложениях, где сооружаются микротоннели, мощность и глубина залегания различных геологических слоев чрезвычайно изменчивы и нестабильны на протяжении проходки тоннеля, поэтому зачастую данные изысканий достоверны только в месте пробуренной геологической скважины.
Например, имея проект проходки в супесях, мы планируем сроки и составляем графики работ. Затем начинается проходка, и неожиданно супеси сменяются валунами. Скорость падает с 200 до 20 мм/мин, сроки увеличиваются, и летят графики выполнения работ. То есть существуют объективные причины увеличения сроков выполнения работ.
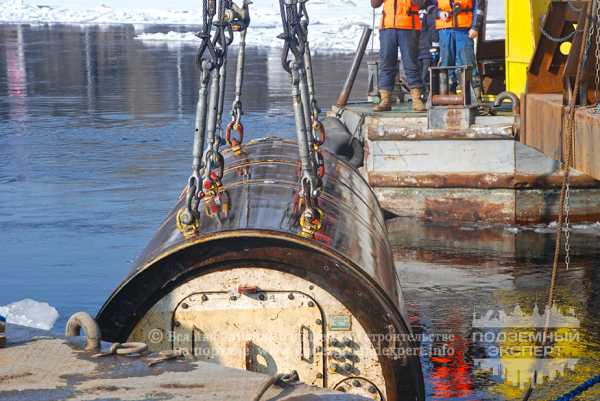
Щит AVN 1600
Другая сложность – это решение задачи: как выдать щит в приемную шахту в водонасыщенных грунтах с давлением воды до 3 бар, не затопив саму шахту. Для этого применяется специально разработанное «резиновое кольцо» – приемное уплотнение. Геометрические параметры этого уплотнения и особенности ведения щита ограничивают точность выхода в ствол: она должна быть не грубее 20 мм при любой длине тоннеля. В свою очередь такие требования обуславливают необходимость высокоточных маркшейдерских измерений с использованием самых передовых методик и оборудования.
В целом, наверное, большинство проблем подземных строителей связано с особенностями инженерно-геологическими условий, в которых ведутся работы. Поэтому очень важно иметь в распоряжении опытный персонал и надежные строительные машины, с которыми возможно успешно реализовывать проекты любой сложности.
инженерные коммуникации, бестраншейные технологии
Расскажите о нашей статье своим друзьям,
поделившись ссылкой в социальной сети
undergroundexpert.info
Прокладка трубопровода: методы и технологии
Развитие промышленности и современного городского хозяйства совершенно невозможно без использования трубопроводов разного назначения. Бесперебойная работа систем отопления водоснабжения, канализации, газовых, нефтяных магистралей и т. д. может быть обеспечена только при условии соблюдений положенных технологий и нормативов во время их прокладки. Способов сборки трубопроводов существует множество.
Какие технологии могут использоваться
Существуют следующие основные методы прокладки трубопроводов:
- Открытый способ предполагает сборку магистралей по опорам, а также в непроходных и проходных коллекторах.
- Закрытый или бестраншейный способ. Предполагает прокладку трубопроводов под землей без предварительного вскрытия грунта.
- Скрытый способ. В этом случае трубы тянутся по вырытым траншеям.
Для сборки магистралей в зависимости от особенностей транспортируемой среды, методов монтажа и внешних условий могут использоваться трубы, изготовленные из разных материалов: бетонные, металлические, пластиковые, керамические, асбестовые. В городах прокладка трубопроводов водоснабжения может производиться в одной траншее с другими коммуникациями (магистралями отопления, кабельными системами и т. д). При этом допускается использование как траншейной, так и канальной технологии.
Особенности открытого способа прокладки трубопроводов
По такой методике может производиться прокладка трубопроводов отопления, водоснабжения, канализации и т. д. Использование под магистрали непроходных каналов в сравнении с траншейным методом имеет одно неоспоримое преимущество. Проложенные в них трубы не подвергаются давлению грунта во время пучения или подвижек, а следовательно, служат дольше. Недостатком этой методики считается затрудненный доступ к магистралям при необходимости их ремонта.
Прокладка трубопровода в проходных каналах обходится дороже. Однако в этом случае специалисты обслуживающих компаний имеют возможность доступа к магистралям без необходимости проведения земляных работ.
Над поверхностью земли трубы обычно прокладывают только в неблагоустроенных районах населенных пунктов, в качестве временных магистралей и т. д. Опорами под них могут служить разного рода бетонные и металлические конструкции, эстакады, стены сооружений и т. д.
Способы прокладки трубопроводов в городах могут быть разными. Но в любом случае магистрали по населенным пунктам тянут вне зоны давления в грунте от сооружений и зданий. Это способствует сохранению фундаментов в случае прорыва. Все подземные городские инженерные коммуникации разделяют на три большие группы: магистральные, транзитные и распределительные. К первой разновидности относятся все основные коммуникационные сети населенного пункта. Транзитные трубопроводы проходят по территории города, но никак в нем не используются. Распределительными называют магистрали, отходящие от основной непосредственно к зданиям.
Скрытый способ прокладки
Строительство трубопроводов по этой методике выполняется чаще всего. Основным преимуществом прокладки труб в траншеях является ее относительная дешевизна. Однако технология сборки в данном случае должна соблюдаться неукоснительно. Ведь доступ к трубам в данном случае затруднен и следует добиться того, чтобы ремонт трубопроводу требовался как можно реже.
Правила проведения работ при скрытой прокладке
Траншеи под магистрали могут использоваться мелкозаглубленные или глубокие. В первом случае закладка трубопровода производится на 50-90 см. При использовании глубокого способа траншеи выкапывают ниже промерзания грунта. Прокладка трубопровода промышленного может производиться на глубине до 5 м. Правила при укладке магистралей соблюдаются такие:
- Если грунт плотный, трубы укладываются непосредственно на него.
- При прокладке на глубине свыше 4 м, либо если трубы изготовлены из не слишком прочного материала, устраивают искусственную подложку. Так же поступают при условии сборки магистралей в сложных гидрогеологических условиях.
- Дно траншей подготавливают таким образом, чтобы трубы соприкасались с ним на всем протяжении. Имеющиеся пустоты засыпают местными грунтами или песком.
- При наличии грунтовых вод в самых низких местах устраивают приямки для их откачки.
Скрытый способ прокладки: особенности технологии
Технология сборки магистралей выбирается в том числе в зависимости от того, трубы из какого материала используются. Полимерные сваривают по нескольку штук (до длины 18-24 м) непосредственно возле объекта хранения, а затем доставляют к месту прокладки. Здесь в летний период времени их собирают в непрерывную нитку, после чего помещают в траншею. Монтаж производится с помощью передвижных сварочных установок. Зимой трубы укладывают в траншею по одной и соединяют склеиванием или с помощью резиновых колец.
Строительство трубопроводов керамических по уклону производят сверху вниз. Перед началом монтажа трубы осматривают на наличие сколов. Соединяют их раструбным методом с уплотнением битумной прядью и устройством замка из цементного раствора. Примерно так же укладываются и бетонные трубы. В качестве уплотнителя в данном случае может использоваться резиновое кольцо.
Асбоцементные магистральные трубопроводы с давлением до 0,6 МПа собирают с применением двухбуртных асбоцементных муфт, а с давлением до 0,9 МПа — с использованием чугунных фланцевых. Безнапорные трубопроводы ведут с применением цилиндрических муфт. Стальные магистрали прокладывают с использованием сварки.
Бестраншейный метод
Прокладка трубопровода этим способом используется в основном при невозможности сборки по скрытой технологии. К примеру, именно так тянут магистрали под оживленными автотрассами, железными дорогами, наружными инженерными коммуникациями и т. д. Существуют следующие методы бестраншейной прокладки трубопроводов:
- проколом;
- продавливанием;
- горизонтальным бурением;
- щитовой проходкой.
Прокладка методом прокола
По этой технологии тянут магистральные трубопроводы на суглинистых и глинистых грунтах. При ее использовании можно прокладывать трубопроводы длиной до 60 м. Заключается эта методика в следующем:
- на трубу надевается стальной наконечник;
- на определенном расстоянии от препятствия выкапывают котлован и устанавливают в него гидравлический домкрат на опорах;
- в котлован опускается труба со вставленной в нее трубой меньшего диаметра – «шомполом»;
- производится поэтапный прокол грунта.
При использовании этой методики земля наружу не вынимается. В процессе прокола она просто уплотняется по окружности трубы.
Метод продавливания и технология щитовой проходки
Эти технологии также довольно-таки часто используются при необходимости сборки трубопроводов под препятствиями. Прокладка трубопровода методом продавливания позволяет преодолевать препятствия длиной до ста метров. Труба в данном случае открытым концом продавливается в грунт. Образующаяся при этом внутри нее земляная пробка удаляется.
Проходческий щит состоит из опорной, ножевой и хвостовой части. Вторая обеспечивает срезание породы и углубление конструкции в массив. Опорная часть имеет вид кольца и предназначена для придания конструкции необходимой жесткости. В хвостовой части расположен пульт управления щитом.
Направленное горизонтальное бурение
Этот метод считается наиболее затратным. Но у него есть одно безусловное преимущество. С использованием такой технологии можно проходить даже самые плотные грунты. Бурение в данном случае производится специальными штангами, соединенными шарнирами. Осуществляться проходка может со скоростью 1,5-19 м/ч. К сожалению, эту технологию нельзя использовать при наличии на участке грунтовых вод.
Таким образом, выбор методики прокладки трубопроводов зависит от особенностей грунта, материала изготовления труб, производственной необходимости. В любом случае технологии сборки магистралей должны соблюдаться в точности. Качественный трубопровод — гарантия бесперебойной работы промышленных предприятий и городских коммунальных сетей.
fb.ru
Микротоннелирование трубопроводов в Москве и области, низкие цены за метр
Прокладка трубопроводов методом микротоннелирования
Микротоннелирование выполняется проходческим щитом с применением домкратной станции, которая устанавливается в шахте на необходимой глубине. Уровень определяется в соответствии с требуемой глубиной прокладки трубопровода.
При микротоннелировании поступательное движение машины обеспечивает домкратная станция. На этапе подготовки разрабатываются котлованы (стартовый и приемный), расстояние между шахтами доходит до 450 м. Размеры сторон определяются типом микрощита.
В нашем распоряжении имеется два вида проходческих шита для микротоннелирования – AVN 1200 и AVN 800.
Разработка грунта производится при помощи режущего инструмента. На поверхности находится отстойник, из которого жидкость по соединительным линиям попадает в призабойную зону. Вода смешивается с грунтом и подается в отстойник, где происходит осадка грунта.
Воду используют в технологических процессах, полученный грунт вывозится. Проходческий щит перемешивает воду с породой, после чего жидкость проходит систему очистки и сепарируется.
При помощи управляемой головки щита регулируется направленность движения. Прокладка труб бестраншейным методом микротоннелирования подходит для работы в районах плотной застройки и на местности, пересеченной транспортными коммуникациями.
Технология микротоннелирования
Технология микротоннелирования — это современная технология по бестраншейной прокладке инженерных коммуникаций. Эта технология в отличие от традиционного ведения работ открытым способом не требует раскопки траншеи по всей трассе прокладки коммуникаций, что позволяет свести к минимуму воздействие на окружающую среду и нарушения в работе транспорта и систем жизнеобеспечения.
Технология микротоннелирования позволяет осуществлять прокладку подземных коммуникаций практически в любых условиях, в том числе и в районах исторической застройки города. Она может использоваться в таких проектах, которые требуют проходов под автострадами, железнодорожными путями, взлётно-посадочными полосами и т.п.
Технология микротоннелирования — это универсальная бестраншейная технология подземного строительства, которая позволяет быстро, эффективно решать задачи, связанные с развитием инфраструктуры города, в том числе и те, которые до настоящего времени не имели экономически оправданного решения.
Сущность технологии микротоннелирования состоит в том, что проходка в грунте осуществляется проходческой машиной — щитом, поступательное движение которого обеспечивает мощная домкратная станция, установленная в шахте на глубине, соответствующей требуемой глубине прокладки трубопровода. Усилие домкратной станции передаётся проходческому щиту через став железобетонных труб, который наращивается по мере продвижения щита.
Во время подготовительного периода производится строительство двух шахт — стартовой и приёмной. Диаметры шахт зависят от ряда параметров, но не превышают нескольких метров, а глубина их соответствует глубине прокладки трубопровода. В стартовой шахте устанавливается мощная домкратная станция, на которую помещается проходческий щит.
С помощью домкратов осуществляется проходка щита в грунте на длину, соответствующую длине применяемых труб продавливания, после чего на домкратную станцию помещается последующая труба и процесс повторяется.
Разработка породы при проходке ведётся режущим колесом проходческой машины. Разработанный грунт смешивается с водой, которая по технологическим трубопроводам насосом подаётся в зону режущего колеса проходческой машины. Полученная взвесь транспортным насосом подаётся в отстойник, установленный на поверхности около стартовой шахты.
В отстойнике происходит осадка грунта, после чего вода снова используется в технологическом процессе, а осаженный грунт вывозится. Поэтапное наращивание става труб обеспечивает дальнейшую проходку щита до выхода его в приёмную шахту.
После этого щит демонтируется, а став труб остаётся в земле. Весь процесс проходки происходит под управлением, осуществляемым из контейнера управления, который установлен на поверхности и оснащён электронной техникой.
Точность проходки обеспечивается применением лазера. Став труб, оставшийся в земле после демонтажа комплекса, является готовым безнапорным трубопроводом либо футляром для прокладки других коммуникаций.
Оборудование для микротоннелирования
Технические параметры
Максимальное расстояние между шахтами — до 200 м.
Средняя скорость проходки —3,0 м/час.
Возможные диаметры труб: 1000 – 3000 мм.
Область применения технологии:
– при строительстве подземных коммуникаций городского назначения — сетей водоснабжения и канализации, коллекторов, газовых, электро- и теплосетей, линий связи;
– при прокладке футляров для электрических кабелей, газо- и нефтепроводов;
– при строительстве под взлётно-посадочными полосами, железными дорогами и автомагистралями;
– при строительстве в районе пересечения влагонасыщенных участков земли;
Отличительные свойства
Во всех случаях применение технологии микротоннелирования имеет убедительные плюсы там, где ведение работ открытым способом затруднено или вообще невозможно.
Преимущества
Значительная экономия за счёт минимума земляных работ при строительстве сетей и сооружений.
Не нарушается движение транспорта, т. е. возможно применение данного метода в условиях плотной городской застройки.
Возможность использования в нестабильных грунтовых условиях.
Меньший риск повреждения существующих коммуникаций по сравнению с открытыми способами прокладки трубопроводов.
Минимальные размеры зоны производства работ, что делает данный метод особо актуальным в условиях выполненного комплексного благоустройства территорий.
Не загрязняет окружающую среду.
ekh77.ru
Добавить комментарий