Манипуляторы ручные – Виды промышленных манипуляторов, типы промышленных манипуляторов, Купить вакуумный подъёмник, цена вакуумного подъёмника, стоимость вакуумного подъёмника, универсальный промышленный манипулятор купить, производственный манипулятор цена, промышленный манипулятор стоимость, вакуумное переместительное устройство, интеллектуальные манипуляторы с автоматической балансировкой веса
«Ручной» манипулятор / Хабр
Как-то раз, во время обучения на втором курсе университета, передо мной была поставлена задача: стряпать что-нибудь «этакое», дабы подтвердить высокое звание «будущего инженера-робототехника». На этой пафосной ноте я отправился в глубины сознания для поиска идей. После непродолжительного путешествия появилась мысль об устройстве, теорией создания которого хочу поделиться с общественностью.Суть разработки такая. Рассмотрим обычный, скажем, 5-ти осевой манипулятор (кинематическая структурная схема изображена на рисунке ниже). Его возможности при перемещении в пространстве широки: он способен совершать движения в 5-ти координатах, причём одновременно, т.е. 3 координаты по трём осям XYZ и вращение вокруг двух из них. В таком случае рабочий элемент манипулятора способен занять любое положение в рабочем пространстве и вместе с этим сохранить требуемую ориентацию рабочего органа (не считая поворот рабочего элемента вокруг собственной оси).
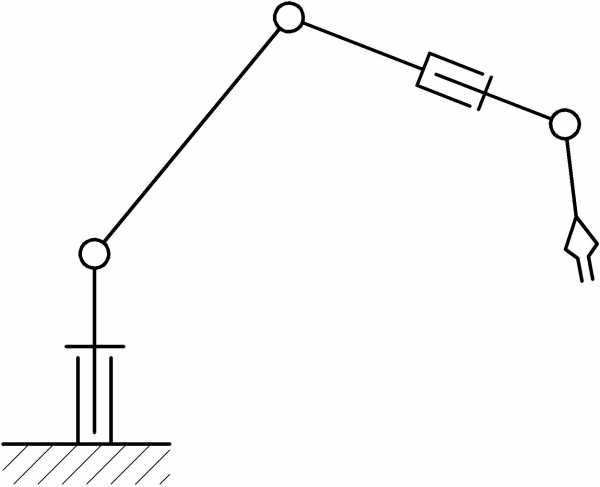
Данная конструкция относится к манипуляторам антропоморфного типа и поэтому способна, приближённо конечно, воспроизводить движение человеческой руки. Рассуждая над этим тезисом как раз пришла мысль, что интересно бы сделать так, чтобы манипулятор дистанционно мог копировать движения моей руки в реальном времени. Чтобы я просто одевал на руку сенсор, считывающий перемещения руки (как линейные, так и угловые), и эта механическая штука будет повторять их вслед за мной. Как манипулятор может выполнять функции перемещения и ориентирования рабочего органа, так и с помощью руки человек может перемещать и ориентировать свою ладонь, следовательно эти два процесса схожи и их можно представить как один общий процесс — захват движения руки манипулятором в реальном времени.Раскатал губу
Забегая вперед, скажу, что удалось только реализовать захват ориентирующего движения ладони, т.е. я мог управлять ориентации рабочего органа, но не его линейным перемещением в пространстве.
На этом формулировка задачи завершена. Теперь проведём анализ задания (не поворачивается язык назвать это «техническим заданием»). Необходимо разработать два, конструктивно независимых устройства: непосредственно сам манипулятор и устройство отслеживания движения, которое крепиться на руку. Затем последует трудоёмкий процесс создания математических описаний, составления алгоритма и написания программного обеспечения. Делим проект на три части:
1. Разработка манипулятора
2. Разработка устройства для отслеживания перемещения руки
3. Всё остальное
Вкратце о каждом из этапов:
- Здесь всё тривиально… В САПР проектируем конструкцию, выполняем чертежи деталей и изготавливаем, после собираем. Затем рассчитываем кинематику и пишем собственное программное обеспечение, которое скроет низкоуровневые обращения к приводам.
- На этом этапе определяемся с типом сенсоров, проектируем принципиальную схему, изготавливаем печатную плату, разрабатываем алгоритм определения положения в пространстве, пишем ПО.
- Собственно, ради чего были предыдущие этапы – заставить манипулятор слушаться хозяина. Здесь разрабатываю алгоритм конвертации координат в рабочее поле манипулятора.
1. Разработка манипулятора
В этом проекте, как было сказано выше, используем манипулятор с 5-ю степенями свободы. Такое количество степеней свободы достаточно, т.к. в их число входит три линейных перемещения и два вращательных. Последние два необходимы для ориентации рабочего органа, поскольку направление РО в пространстве можно задавать в виде вектора, а вектор определённо можно восстановить из двух углов поворота (не учитывая длины). В таком случае нам необходимо пять обобщённых координат, равное числу осей.
Звенья манипулятора связаны вращательными кинематическими парами пятого класса. Конструкция манипулятора стандартная для своего типа (кинематическая схема представлена в начале статьи). Имеет в составе неподвижную станину, с которой связана базовая система координат, поворотную стойку, к которой крепятся остальные подвижные звенья, соединённый в цепь. К конечному звену (фланцу) крепиться рабочий орган, в данном случае его имитация в виде стрелообразного указателя (см. изображение ниже).
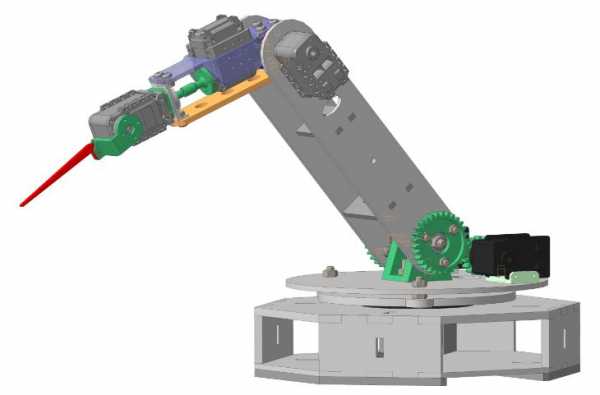
ЗD–модель построена в САПР «Компас 3D». Материал деталей – фанера 4 мм и PLA для пластиковых деталей. Детали из фанеры вырезались на лазерном станке, детали из пластика печатались на 3d-принтере. В качестве приводов осей используются цифровые сервоприводы Dynamixel AX-12. Внешний вид манипулятора напоминает одного гнусного насекомого, от которого он получил прозвище «Комар».
Математическое описание кинематики
На этом этапе необходимо рассчитать прямую и обратную кинематику манипулятора. Прямая задача состоит в том, чтобы по известным значениям обобщённых координат (в данном случае углы поворота звеньев) определить положения звеньев относительно некоторой базовой системы координат. Обратная ей задача называется обратной или инверсной кинематикой, заключается в определении параметров обобщённых координат для достижения желаемой позиции и ориентации рабочего органа манипулятора.
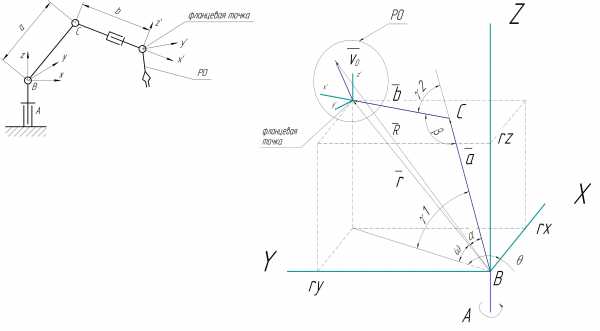
Требуемую позицию изображаем радиус-вектором . Здесь стоит пояснить, почему вектор проведён до фланцевой точки, а не до конечной точки РО. Поскольку ориентация рабочего органа нам известна заранее (я её сам определяю согласно некоторым требованиям), то необходимо, чтобы фланцевая точка оказалась в нужном месте, указанное как вектор . Этот вектор получается вычитанием из радиус-вектора , проведённого к конечное точки РО, вектора его ориентации , относительно БСК, т.е:
Рассмотрим переход фланцевой точки в нужное положение. Оно осуществляется поворотам звеньев a и b (их я изобразил в виде векторов) в шарнирах A, B и C. Начало базовой системы координат (БСК) поместим в точку шарнира B. Ось вращения шарнира A направлена вдоль оси Z, оси B и C направлены перпендикулярно Z.
Когда всё формальности соблюдены, перейдём к сути. Для решения обратной задачи кинематики я использовал геометрический подход в силу простоты конструкции манипулятора. Из геометрии видно, что вектор равен сумме векторов звеньев и . Углы , , — углы поворота звеньев А, В и С соответственно.
Рассмотрим треугольник, ограниченный векторами , и . Из этого треугольника по теореме косинусов найдём углы и . Пусть длины векторов будут равны:
Запишем теорему косинусов относительно искомых углов:
Выразим углы и :
Из геометрической схемы видно, что:
Тогда:
Окончательно, переход от линейной координаты к углам поворота звеньев осуществляется формулами:
Теперь, когда переместили фланцевую точку в требуемое положение надо правильно сориентировать рабочий орган. Чтобы это сделать, необходимо знать координаты вектора относительно фланцевой точки, т.е. координаты в базисе локальной системы координат (ЛСК) – , начало которой расположено в фланцевой точке манипулятора.
Вектор направлен по звену b, вектор – вдоль оси шарнирного соединения f1.
Для нахождения базиса определим матрицу перехода от БСК (с базисом ) и ЛСК. Эта матрица получается путём комбинации поворотов в шарнирах A, B и C:
где
Т.к. матрица является единичной, тогда:
Знающему читателю
Знающий читатель может здесь найти схожесть с представлением Денавита – Хартенберга для решения прямой задачи кинематики. Да, это оно, упрощённое до нельзя и с моими небольшими изменениями. Здесь я не использую однородные преобразования, не учитываю конструктивные особенности, как угловое и линейное смещение осей и т.д. Просто я так спроектировал конструкцию, чтобы там отсутствовали вышеперечисленные лишние параметры, оставив только являющиеся обобщенными координатами.
Матрица вычисляется путём перемножения матриц поворота вокруг оси на угол.
Зададим функцию, которая вычисляет эту матрицу:
Ось берётся в виде вектора как столбец матрицы, полученной предыдущими поворотам, а углы уже рассчитаны выше.
В итоге получаем:
Пусть вектор рабочего органа в БСК . Тогда справедливо равенство:
Отсюда выразим – вектор рабочего органа в базисе , т.е. относительно фланцевой точки:
Теперь, зная вектор РО, можно рассчитать углы поворота ориентирующих осей f1 и f2
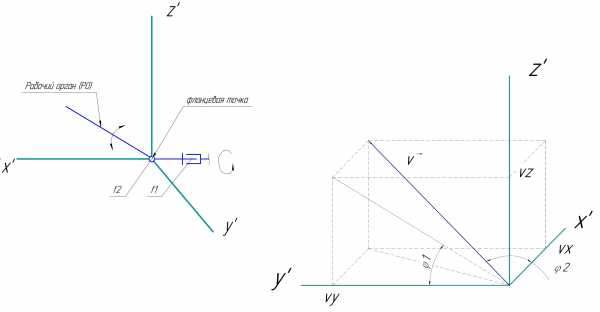
Чтобы переместить РО в заданную позицию, требуется совершить поворот на углы и . Из рисунка видно, что
где — длина рабочего органа,
— координаты вектора .
Программное обеспечение манипулятора разделено на два уровня, верхний и нижний. Верхний уровень написан в Matlab в виде библиотеки и различными командами-методами, нижний – на микроконтроллере Atmega328. Задача верхнего уровня состоит в том, чтобы сформулировать команды, отсылаемые на микроконтроллер. Его задача получить команду и в соответствии с ней установить приводы в нужное положение. В таком виде система управления оказалась надёжной (пока что…) и удобной в использовании.
Почему Matlab?Изюминка, как по мне, языка Matlab в том, что операции с матрицами там происходят как обычные алгебраические соотношения, и не надо городить вложенных циклов как это делается, например, в языке C. Плюс в Matlab доступна практически любая «возжеланная» математическая операция, что доставляет огромное счастье.
Формулировка команды и отправка со стороны верхнего уровня происходит следующим образом: пользователь в командном окне Matlab вызывает функцию из библиотеки (например, функцию простого перемещения в точку), указывает необходимые аргументы (обычно это координаты и ориентация РО). После по изложенным выше математическим соображения, записанных в библиотеку, вычисляются углы поворота осей и при необходимости скорости вращения. После по простенькому протоколу собираем команду и шлём её на микроконтроллер нижнего уровня по последовательному COM – порту. Пару слов о написанной библиотеке. В её распоряжении есть следующие функции:
- функции создания соединения по последовательному интерфейсу
- функции перемещения
- в точку, с постоянной скоростью всех приводов
- в точку, с конечным остановом всех приводов (скорость привода подбирается в пропорции от собственного и самого большого угла поворота. Таким образом в конце подхода к точке заканчивают движение все приводы)
- в точку, с плавным перемещение каждого привода (в этом случае график скорости выглядит как трапеция с участками разгона, постоянной скорости и торможения) График
- в точку, по вручную заданным углам поворота осей и скорости вращения
Список функций можно конечно расширить, но достаточно было и этого функционала для решения непосредственно той задачи, для которой манипулятор и проектировался.
На видео продемонстрирована работа манипулятора.
2. Разработка устройства для отслеживания перемещения руки
Переходим к следующему этапу. Здесь потребуется спроектировать специальное устройство, которое может отслеживать в реальном времени положение в пространстве ладони. Также этот процесс носит название «захват движения». Для осуществления задуманного я решил использовать бесплатформенную инерциальную навигационную систему (БИНС) на основе трёх датчиков: гироскопа, акселлерометра и магнитометра. Связка этих датчиков называется IMU – сенсор (в переводе и есть то самое БИНС).
Сперва я спроектировал печатную плату с необходимым мне функционалом, на которой я разместил эти три датчика. В качестве обрабатывающего контроллера я выбрал (точнее взял что было) микроконтроллер Atmega2560. Сенсоры использовал распространённые и дешёвые на китайском рынке. Это спаренные датчики трёхосные гироскоп и акселерометр MPU6050 и магнитометр HMC5883l.
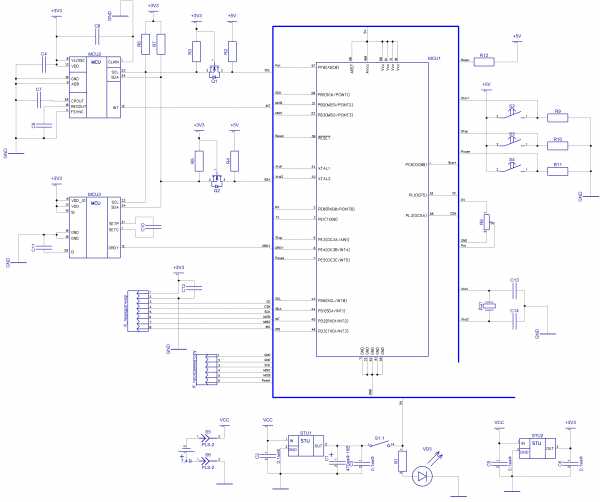
Фото готовой платы
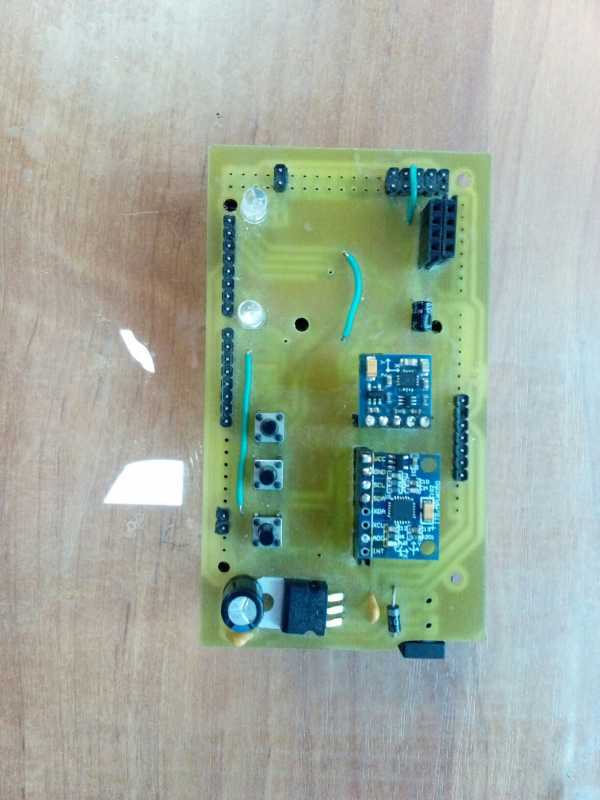
Алгоритм расчёта положения в пространстве достаточно прост: вначале определяем ориентацию в виде базиса локальной системы координат (ЛСК), которая связана с датчиками, а в конечном итоге с ладонью руки.
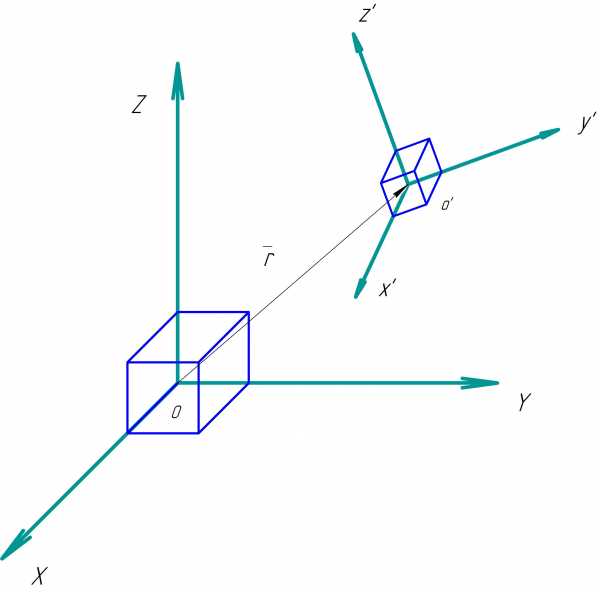
Ориентацию определяем относительно начальной системы координат (НСК), что по сути является начальным положением устройства в момент включения питания. Базисы НСК и ЛСК состоят вектор-столбцов её орт:
Они связаны соотношением:
Где – матрица перехода, она же матрица вращения в пространстве. Базис НСК будем считать единичной матрицей. Следовательно.
После, вектор ускорения , который известен относительно ЛСК, необходимо определить в НСК. Это делается путём умножения вектора-столбца ускорения на базис ЛСК:
Затем полученный вектор ускорения два раза интегрируем по времени и получаем расстояние, т.е. координаты:
Первые попытки реализации этого алгоритма были весьма наивны… Наивность была в том, что я посчитал возможным только по данным гироскопа, используя дискретное интегрирование, получить матрицу поворота вокруг оси. Осью в данном случае можно рассматривать как псевдовектор угловой скорости, компоненты которого (проекции на оси) и есть выходные данные с датчика гироскопа. А угол в свою очередь получается интегрированием модуля вектора. Первоначальный задор и энтузиазм пропал, когда я увидел чудовищный по величине, так называемый «дрейф нуля», вызванный накапливающейся ошибкой из-за погрешности дискретного интегрирования и собственного шума датчика. Ещё тогда у меня появились мысли, что по данным акселерометра, который в состоянии покоя показывает вектор, обратный вектору ускорения свободного падения (далее в тексте вектор гравитации), можно делать корректировку матрицы, но и здесь появляется неопределённость, связанная с тем, что корректировка возможно только с точностью до поворота угла вокруг оси Z. Корректировка будет полноценна в том случае, если будет возможным восстановить матрицу поворота альтернативным способом, т.е. без применения данных гироскопа.Особо интересующимсяОсобо интересующимся поясню. Почему нельзя по акселерометру восстановить матрицу поворота? Точнее недостаточно данных. Как нам известно, вектор гравитации направлен всегда к центру планеты, а, следовательно, перпендикулярен поверхности Земли. Поскольку мы связываем начальную систему координат, например, со столом, так что плоскость XY параллельная поверхности стола, который в свою очередь параллелен (с некоторой условностью) полу, а пол в свою очередь параллелен плоскости основания здания, которая обычно является касательной плоскостью к поверхности Земли. Отсюда делаем вывод, что показания акселерометра в состоянии покоя (или при равномерном движении) говорят нам о положении оси ЛСК, относительно НСК. На этом полезность этих данных исчерпывается, т.к. вращение вокруг оси не изменят саму ось , но изменяет две остальные оси и . Следовательно показания акселерометра не изменятся и тогда положение будет не определено.
Тогда необходимо использовать ещё один фактор, по которому возможно будет сделать полноценную корректировку положения. Этим фактором является магнитное поле Земли, которое наряду с гравитацией в отдельной взятой точке планеты не меняются со временем (в краткосрочной перспективе конечно). Его измеряем при помощи вышеупомянутого датчика HMC5883l. В таком случае мы имеем два вектора, которых достаточно, чтобы относительно них определить положение в пространстве.
Теперь возникает закономерный вопрос – «как это сделать?». После неудачных попыток ответить на это вопрошание самостоятельно я полез в интернет, где нашёл нужную мне информацию. Задача определения ориентации в пространстве по данным трёх измерений (угловая скорость, вектор гравитации и вектор магнитного поля) встаёт также при проектировании любительских летательных аппаратов (например коптеры), поэтому эта задача не раз решалась различными методами. Один из популярных методов – это так называемый фильтр Маджвика (Sebastian O.H. Madgwick). Прочитав оригинальную статью и не поняв англицкого, я обратился к замечательному переводу (спасибо автору за проделанный труд). Пока углублялся в изучении статьи у меня всё чаще и чаще возникала мысль о том, чтобы всё-таки попробовать написать свой алгоритм фильтра определения положения, учитывая, что к этому моменту мой уровень познаний в этой области заметно повысился. Хотя бы ради интереса «изобрести велосипед»! И я его «изобрёл». Ниже привожу свои рассуждения.
В алгоритме используются показания все трёх датчиков. Напомню, задача алгоритма – вычисление ориентации объекта и компенсация дрейфа нуля гироскопа, учитывая данный пары акселерометра и магнитометра. В качестве математического инструмента, описывающего положение, используется кватернион, т.к. он удобен в плане построения и оптимизация алгоритма и требует меньше математических операций для его расчёта в отличие от матриц. Кватернион вращения в пространстве выглядит следующим образом:
Зная ось вращения, описанное нормированным вектором , и угол (откуда они берутся сказано выше) можно рассчитать кватернион:
Тогда, используя только показания гироскопа, на каждой итерации цикла будем рассчитывать текущее значение кватерниона по выражению:
Здесь – кватернион в данный момент времени. Индекс G сверху говорит о том, что это значение относится к измеренному относительно показаний гироскопа, т.е. угловой скорости; – значение кватерниона в предыдущий момент времени; –изменение положение за один шаг измерений, можно сказать дискретное изменение положения на угол за – период дискретизации, выраженное кватернионом вращения (*).
Следующий этап вычислений – нахождение матрицы поворота исходя из данных пары датчиков акселерометра и магнитометра. Конкретно, рассматриваем вектор гравитации и вектор индукции магнитного поля Земли, которые, как это было сказано выше, статичны относительно Земли и связанной с ней НСК. Здесь тезис такой: зная значения гравитации и индукции в базисе ЛСК и НСК можно рассчитать матрицу перехода (поворота) от НСК к ЛСК и кватернион вращения в пространстве.
Обозначим через нормированный начальный вектор гравитации. Его можно принять таким:
Через обозначаем нормированный начальный вектор магнитной индукции:
Также требуется третий вектор , который связан с этими двумя. Он получается векторным умножением на :
Теперь формируется матрица , которая характеризует начальной положение, т.е. НСК, поскольку в начальный момент времени ЛСК совпадает с НСК. Матрица получается из компонентов векторов , и :
Аналогично, но уже на каждой итерации цикла, создаётся подобная матрица , где – текущий нормированный вектор магнитной индукции, – текущий нормированный вектор гравитации, . Эта матрица характеризует положение ЛСК, т.к. эти вектора известны в системе координат датчиков, которая совпадает с ЛСК. Тогда, зная обе матрицы, можно записать такое уравнение:
Оно связывает две матрицы, найденные при разных обстоятельствах. Учитывая выражение и то, что базис – единичная матрица, получим:
Отсюда выразим матрицу перехода :
Первый множитель, как можно понять, рассчитывается только один раз в самом начале алгоритма, и не требует пересчёта в процессе работы. Второй множитель формируется довольно таки легко и не принуждённо на каждой итерации цикла.
После, когда найдена матрица перехода, преобразуем её в кватернион (алгоритм конвертации из матрицы в кватернион вещь публичная и приводить здесь его не буду).
В итоге нам известны два кватерниона, найденные независимо друг от друга. И для совмещения результатов я применил простенький комплементарный фильтр с коэффициентом , который берётся из диапазона от 0 до 1:
В результате получаем кватернион, в котором находится актуальная информация о положении в пространстве устройства с модулем БИНС.
«Велосипед» поехал… Алгоритм работал, но в некоторых положениях вёл себя несколько не адекватно, что в принципе не мешало, но и не давало повода думать о нём положительно. Свой спортивный интерес я удовлетворил, и теперь можно обратиться к готовым решениям, более качественным. Тогда я вновь вернулся к статье Себастьяна Маджвика и решил использовать его алгоритм, благо, что этот замечательный человек опубликовал все исходники на сайте проекта. В архиве были исходный коды на разных языках, в том числе и на языке Matlab. Этот факт повлиял на моё решение отказать от идеи делать все вычисления на микроконтроллере (тем паче что он 8-ми битный) и писать программу уже на компьютере в среде Matlab. Микроконтроллер используется только для опрашивания датчиков и отсылку данных на ПК (похожая ситуация и с манипулятором). В таком случае основной программный код, который подвергается изменениям и отладке, базируется в среде Matlab, что весьма удобно в процессе работы.
Хорошо, ориентацию, заданную кватернионом, мы получили. Что дальше по плану? А далее следует нахождение линейных координат объекта по данным акселерометра. Что ж, здесь лучше просто констатировать, что невозможно с нужной точностью по акселерометру определить координаты. Даже хотя бы находить изменение положения, которое было бы адекватным! Конечно, были попытки решить эту задачу, но в режиме реального времени находить координаты не получалось. Почему? Потому, что двойное дискретное интегрирование зашумленных показаний датчика приводила только к полёту в стратосферу, причём с бешеной скоростью, но никак не к положительному результату. Поэтому обозначенный в начале пункта алгоритм я обрезал до момента нахождения ориентации, и на этом остановился.
3. Всё остальное
Итак, вот я подобрался к заключительному этапу проектирования, вдоволь наигравшись с манипулятором и навертевшись IMU-сенсором. Работая над двумя предыдущими этапами я уже чётко представлял, как всё будет работать и по какому алгоритму. Поэтому с этим этапом я расправился достаточно быстро. Поскольку известна только ориентация ладони, то работаем непосредственно с рабочим органом, который требуется соответственно ориентировать. РО может принять любое направление, если оно не нарушает рабочую зону (вращаться на все 360 не получиться).
В пункте про разработку манипулятора вектор РО задавался вручную, и уже после находились углы поворота приводов. Так вот, этот вектор и нужно определить исходя из ориентации ладони руки. Ориентацию можно выразить базисом
habr.com
Ручной манипулятор – Большая Энциклопедия Нефти и Газа, статья, страница 1
Ручной манипулятор
Cтраница 1
Ручной манипулятор ( модель 2) представляет собой координатный копирующий манипулятор с ручным приводом, предназначенный для дистанционной работы с легкими предметами ( до 15 фунтов) в полугорячих камерах. Это гибкий в применении и сравнительно недорогой инструмент. Небольшая ширина манипулятора, равная всего 6 дюймам, позволяет снимать его для использования в других камерах, оборудованных направляющими. [1]
Ручные манипуляторы отличаются разнообразием, и каждый из них предназначен для выполнения одной или нескольких несложных операций. [3]
Разработан ручной манипулятор съема сапог, и на его основе разрабатывается автоматический манипулятор съема и обрубки верха сапога. Конвейер перемещает каретки с сапогами к манипулятору съема, захват манипулятора берет пару сапог и совершает движение по кривой, необходимой для съема сапога. В позиции съема сапоги захватываются роботом и передаются в обрубочную машину. После окончания обрубки робот переставляет пару сапог на ленточный конвейер, который перемещает сапоги к рабочему месту обрезчиц и браковщиц. [4]
К ручным манипуляторам относится и джойстик ( joystick), представляющий собой подвижную рукоять с одной или двумя кнопками, при помощи которой можно позиционировать указатель на экране дисплея. Кнопки имеют то же назначение, что и клавиши мыши. Джойстик чаще используется в бытовых ПЭВМ, в первую очередь для игровых применений. [5]
Исходными данными для расчета ручного манипулятора являются вес изделия, положение центра тяжести по отношению к оси вращения стола ( фиг. [6]
Работа без применения необходимых ( в зависимости от характера эксперимента) защитных средств: ручных манипуляторов, защитных экранов из соответствующего материала, обеспечивающих получение дозы облучения, меньше предельно допустимой, сухих камер. [7]
Манипуляторы для установки свариваемого изделия в положение, удобное для сварки швов, показаны на рис. 46 – ручной манипулятор и на рис. 47 – универсальный установочный для изделий весом до 1200 кг. Манипулятор имеет поворотный стол 1 на консоли 2, механизм наклона консоли 3, главный вал 4 с редуктором 5, колонку 6 со штоком 9, гидравлический домкрат 7 и тумбу 8 на опорной раме. [9]
Таким образом, термином робот, как он трактуется на Западе ( и в этой книге), не охватываются такие устройства, как дистанционно управляемые манипуляторы ( телеоператоры), искусственные конечности, основанные на принципах бионики, или протезы, поскольку эти устройства управляются человеком, хотя они и основаны на той же технологии, что и роботы. Отнесение японцами к роботам устройств типа взять-положить и ручных манипуляторов серьезно затрудняет сравнение статистики производства и использование роботов в Японии, Западной Европе и США. [10]
Наибольшей популярностью среди пользователей персональных компьютеров пользуется командный процессор Norton Commander фирмы Peter Norton Computing, Inc. Распространяемая в настоящее время фирмой версия командного процессора 3.0 позволяет либо работать в обычном режиме ввода команд в командной строке, либо с помощью оконно-ориентированного интерфейса, дающего возможность использовать ручной манипулятор мышь, непосредственно выполнять наиболее употребительные команды управления файловой системой – просматривать графическое представление структуры и содержимое каталогов на дисках, выбирать новый текущий каталог, искать, копировать, перемещать и удалять группы файлов, запускать исполняемые программы. В Norton Commander имеется встроенный текстовый редактор, в котором можно быстро откорректировать небольшие файлы. Командный процессор также позволяет обмениваться данными между двумя компьютерами. Для неопытных пользователей предусмотрена возможность получения справочной информации. [11]
По вертикали груз уравновешивается приводом, а по горизонтали перемещается вручную. Это позволяет оператору легко перемещать груз в любом пространственном направлении. Но есть ручные манипуляторы и с приводами во всех степенях подвижности, в которые поступают сигналы управления от управляющей рукоятки при произвольном пространственном перемещении груза рукой оператора. Отдельный управляемый оператором привод может устанавливаться для вращения всего манипулятора вокруг колонны, на которой он крепится. [13]
Вытяжные шкафы и боксы изготовляются из легко моющихся материалов. Присоединение их к вентиляционной системе осуществляется через специальный фильтр. В передней стенке шкафов и боксов вмонтированы перчатки или ручные манипуляторы. Передняя стенка шкафов подъемная или раздвижная, боксов – стационарная. [15]
Страницы: 1 2
www.ngpedia.ru
Манипулятор (механизм) — Википедия
Материал из Википедии — свободной энциклопедии
Текущая версия страницы пока не проверялась опытными участниками и может значительно отличаться от версии, проверенной 11 декабря 2016; проверки требуют 7 правок. Текущая версия страницы пока не проверялась опытными участниками и может значительно отличаться от версии, проверенной 11 декабря 2016; проверки требуют 7 правок. У этого термина существуют и другие значения, см. Манипулятор.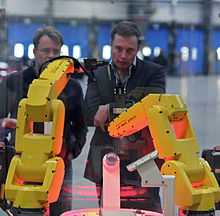
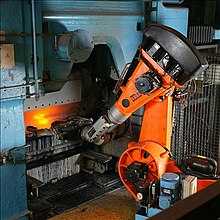
Манипуля́тор — механизм для управления пространственным положением орудий, объектов труда и конструкционных узлов и элементов. Это значение закрепилось за словом с середины XX века, благодаря применению сложных механизмов для манипулирования опасными объектами в атомной промышленности. Используется для перемещения различных грузов, получил широкое развитие в современном обществе.
ru.wikipedia.org
Ручные манипуляторы | Инструмент, проверенный временем
В ручном манипуляторе (фиг. 288) должны быть осуществлены два основных движения: вращение стола вокруг своей оси и наклон стола в вертикальной плоскости.
Механизм поворота (фиг. 289 и 290) с двумя цапфами /, опирающимися на подшипники скольжения, укрепляется на стойке станины. Цапфы 1 укреплены в специальном корпусе 2, служащем опорой для вертикального вала 3 и основанием для ручного червячного привода 4. На валу 3 на шпонке насажена сварная планшайба. Вал смонтирован на двух роликовых конических подшипниках. На верхнем конце этого вата на шпонке насажено червячное колесо 5, получающее движение от червяка, приводимого от рукоятки. Червяк — самотормозящий, что обеспечивает неподвижность стола при отсутствии внешнего усилия на рукоятке. Для крепления свариваемых изделий на планшайбе стола сделаны пазы. Наклон стола осуществляется червячной самотормозящей парой б и цилиндрической парой, состоящей из приводной шестерни 7, сидящей 220
тал горизонтален Стол наклонен на 90° |
Случай II. Вал на подшипниках скольжения.
Осевое усилие воспринимается пятой
20 В
М = (G-f — Q) fr0 — f — — jj-frx — стол горизонтален;
М = (Л/’ — ф N) frx — стол наклонен на 90°;
где /— коэфициент прения скольжения;
г0 — средний радиус пяты, воспринимающей усилие, действующее на планшайбу, в см; гл — радиус вала в см;
г’ — средний радиус пяты, воспринимающей усилие, действующее, от планшайбы, в см.
Определив наибольшее значение М при данной конструкции опор, вычисляют передаточное число механизма.
Принимая усилие рабочего на рукоятке длиной /. равным К, имеем
Мр = KL,
тогда требуемое передаточное число
/ = _Л_
Щл •
г;—к. п. д. всех передаточных звеньев от рукоятки к планшайбе
= ‘Чі’Чг»
пт]х — к. п. д. подшипников;
т(, — к. п. д. зубчатых или червячных пар.
Для червячной самотормозящей пары к. п. д. всегда меньше 0,5. К. п. д. червячной пары
_ tg — «р ~ tg(¥+ р) ’
где ф — угол подъема винтовой линии; р — угол трения.
Кроме того можно написать
Лк
п-г.
я2—число оборотов планшайбы;
«х — число оборотов вала рукоятки.
Для ручных механизмов, предназначаемых для установочных движений, пг должно лежать в пределах 3—5 об/мин, а л, — в пределах 45 — 60 об, мин.
Таким образом, значение і = 9 ч — 20.
Границы применения ручных поворотных механизмов можно установить по следующим соображениям.
Например, для II случая, їіри / = 0,1, г0 = 8 см, о = 20 см, Н = 30 см, г1 — 5 см. для диапазона допускаемых усилий рабочего 10—25 кг получаем предельные значения Q + О для горизонтального положения стола в пределах 750 — 1900 кг
Определив по конструктивной схеме приближенный вес вращающихся частей планшайбы, можно определить грузоподъемность механизма.
15 Б. А. Таубер 2684
Размеры передач определяются по общепринятым формулам, исходя ив расчета на прочность по крутящему моменту, передаваемому соответствующими валами.
Механизм наклона стола. Необходимый для наклона стола крутящий момент на оси цапфы будет равен для трех рассмотренных выше положений планшайбы:
а) наклон по часовой стрелке (фиг. 291, а)
М = Мі + Мтр, где
Мг = G 8,
Mmp=(G+Q+q)f%,
здесь q — вес траверсы и цапф в кг,
d — диаметр цапф в см.
Очевидно, что наклон против часовой стрелки более благоприятен, так как М = М — Мг.
б) Наклон (подъем) против часовой стрелки (фиг. 291, б)
м = мх + мтр,
где
Мх = G (а + I) + QI,
Мтр — по предыдущему.
в) Наклон (подъем) против часовой стрелки (фиг. 291, в)
М = Щ + Мтр,
где
Мх n G (а + /) cos 45° + Ql cos 45°,
Мтр — по предыдущему.
Очевидно, что расчетным является положение, когда стол наклонен на 90е.
П’римечание: а) при значительном весе кроншейна узла крепления червяка механизма поворота, самого червяка и рукоятки их вес д’олжен быть учтен при определении необходимого момента для поворота; б) вес узлов упорных подшипников принят одинаковым и из расчета исключен.
Аналогично предыдущему, полагая момент, создаваемый рабочим на рукоятке длины L, равным
М = KL кгем,
при я = 135° и времени наклона t время одного оборота
<360°
число оборотов в минуту
л, = -— об/мин,
Го
тогда число оборотов рукоятки механизма наклона
пх =« л2г об/мин.
б) Ручные кантователи
Ручные кантователи могут быть сборочными, сварочными, или сборочно-сварочными.
На фиг. 292 приведен механизм, предназначенный для сборки балок и колонн Н-образного сечения.
Сварка изделий производится вне сборочного механизма /на сварочной установке.
Сборочный механизм состоит из рамы корытообразной формы 1, по середине которой приварен двутавр 2, являющийся опорой для стенки свариваемого изделия. В нескольких местах по длине в двутавре 2 сделаны вырезы, в которые вварены сухари 3 (фиг. 293), вдоль которых могут перемещаться уширители 4. Уширители могут раздвигаться в разные стороны, создавая устойчивые опоры для стенок свариваемого изделия.
Габарит по высоте’свариваемого изделия устанавливается выдвижными упорами 5 и винтовыми упорами 6.
В полученный габарит устанавливаются пояса собираемого изделия; они опираются на полку угольника 7, связанного жестко с двумя винтовыми домкратами 8.
Для перемещения угольника 7 в нижней части двутавра 2 сделаны вырезы. Стенка изделия зажимается с помощью отводных перекладин 9, вращающихся на оси 10. Оси запираются в двух горизонтальных упорах 11, приваренных к стойкам 12.
В теле перекладин 9 вмонтированы винтовые домкраты 13, зажимающие стенки изделия через съемные стойки 14. После зажима элементов изделия производится прихватка сверху стенки к поясам, а затем поворот на 180° редуктором с ручным приводом. При повороте снимаются предохранительные тяги 15 (фиг. 294), соединяющие раму механизма со стойкой.
После поворота тяги 15 снова устанавливаются и производится прихватка поясов со стенкой с другой стороны. Затем сборочный механизм снова поворачивают в первоначальное положение. Для выемки балки ослабляют винты домкратов 13, отводят перекладины 9 вдоль стенок рамы 1 и снимают стойки 14. Если червяк редуктора сделан самотормозящим, надобность в предохранительных тягах отпадает.
Сварка балок может осуществляться также на специальном поворотном механизме, показанном на фиг. 295.
Он выполнен по типу поворотных механизмов с опорой несущей рамы на концевых цапфах.
Рама механизма состоит из двух жестких сварных двутавровых балок 1, соединенных в торцах через листы 2 поворотными траверсами 3.
Вид по стрелке Д |
Фиг. 292. Ручной кантователь. |
В каждой балке 1 в нескольких местах симметрично относительно продольной оси сделаны отверстия, в которые вставляются трубчатые штыри 4 (фиг. 296), служащие опорой для свариваемого изделия.
Количество и расположение штырей определяются размерами балок, подлежащих сварке.
Для свариваемого изделия в механизме создается опорный трехсторонний контур, составленный по нижней плоскости из штырей, а с боков — двумя рядами выдвижных упоров 6. Упоры скользят в прорезях Стенок сварных балок 1 и перемещаются вдоль ребер 6 для установки
Фиг. 295. Поворотный механизм для сварки балок. |
необходимого размера по высоте балок. Закрепление упоров производится болтами.
Порядок работы при установке изделия и сварке следующий: в нижние отверстия боковых стенок несущих балок 1, соответствующие данному размеру свариваемого изделия, вставляются штыри, затем устанавливаются на необходимый размер и закрепляются выдвижные упоры.
В полученный трехсторонний контур укладывается собранная на прихватках подлежащая сварке балка. Затем производится сварка двух верхних швов. После этого вставляются штыри по верху свариваемой балки и закрепляются.
по но по ДВ
Таким образом, свариваемая балка оказывается зажатой со всех сторон.
Затем ручным червячным приводом механизм поворачивается на 180°, после чего убираются верхние штыри и производится сварка еще двух швов.
Приводной вал поворотного механизма крепится к траверсе 3.
Поворотные траверсы 3 состоят из двух швеллеров 7 (фиг. 297) с вваренными фланцами 8, связанные шпонками с валом 9, опирающимся на две шариковые опоры 10.
Вал 9 соединяется через муфту 11 с червячным редуктором 12.
Червяк редуктора должен быть самотормозящим, что позволяет остановить раму механизма в любом желаемом положении и делает экспло — атацию безопасной. Опоры механизма должны быть тщательно выверены как по высоте, так и по продольной оси.
Механизм с пневмоприжимами, предназначенный для сборки и сварки крупных металлоконструкций Н-образного сечения, приведен на фиг. 298. Сварка может производиться вручную, либо на установке для автоматической сварки продольных швов.
Рама сборочно-сварочного механизма состоит из двух балок таврового сечения 1 и 2.
К обоим торцам балок приварены прямоугольные цапфы, которые входят в швеллеры, образующие концевые траверсы 3. Цапфы через
подшипник 4 и гайки J опираются на вал, имеющий правую и левую винтовые нарезки (фиг. 299). Балки крепятся к подшипникам и гайкам болтами 7. При вращении штурвала 8 гайки с балками перемещаются симметрично относительно продольной оси. Этим достигается установка продольных балок на размер, соответствующий высоте собираемого изделия.
В горизонтальной плоскости изделие зажимается пневмоприжимами.9, вмонтированными в вертикальные стенки балок (фиг. 300). Число прижимов и расстояние между ними определяются размерами собираемого изделия.
Для укладывания горизонтальных поясов собираемой Н-образной балки служат опоры 10. Опора состоит из набора пластин 11 разной толщины, сидящих на пальце. Пластины могут быть .повернуты вокруг пальца вдоль балок / и 2, либо поперек их.
Пластины помещены в коробке, привариваемой к вертикальной стенке балок. Набранные на определенный размер, они запираются шпингалетом 13.
При поперечном положении они образуют опору для горизонтальных полок собираемого изделия.
Число повернутых пластин и их толщина зависят от расстояния от оси конструкции механизма до кромки горизонтальных листов изделия.
Вертикальный лист собираемой балки укладывается на ряд упоров винтовых прижимов 14 и сверху зажимается рядом противоположных
прижимов. Винтовые упоры состоят из вертикальной трубы 15, в которой помещен винт 16, связанный с опорной гайкой 17: Ход гайки 17 незначителен.
При прохождении сварочною аппараіа верхние прижимы последовательно убираются.
После зажима с боков пневмоприжимами и в вертикальной плоскости винтовыми прижимами Н-образная балка готова для наложения продольных швов.
Для придания раме механизма большей жесткости ее балки соединяются раздвижными и поворотными стяжками 18. При проходе сварочного аппарата стяжки последовательно убираются, а после прохода аппарата снова крепятся.
В положение „лодочка” свариваемое изделие устанавливается поворотом концевых траверс 3. Для этого в середине через коробку 19 вварена опорная цапфа вала (на стороне привода) и вал (на стороне холостой опоры).
Приводной вал опирается на два шариковых подшипника и через муфту соединен с червячным редуктором. Редуктор приводится в движение рукояткой.
Повернутая рама механизма крепится швеллерами 21 к опорному швеллеру 22 болтами. В горизонтальном положении рама 3 крепится к швеллеру 22 с помощью тяги 23.
После наложения первого шва (фиг. 301) сборочно-сварочный механизм последовательно поворачивают для наложения остальных трех швов, причем процесс закрепления и съема винтовых опор-зажимов производится аналогично.
Для снятия сваренного изделия механизм устанавливается в горизонтальное положение, снимаются стяжки 18, верхние винтовые прижимы 14 и разжимаются пневмоприжимы.
hssco.ru
Настольная робо-рука манипулятор из оргстекла на сервоприводах своими руками или реверс-инжиниринг uArm
Привет, гиктаймс!Хочу поделиться с вами результатами реверс-инжиниринга uArm – простого настольно манипулятора из оргстекла на сервоприводах.
Проект uArm от uFactory собрал средства на кикстартере уже больше двух лет назад. Они с самого начала говорили, что это будет открытый проект, но сразу после окончания компании они не торопились выкладывать исходники. Я хотел просто порезать оргстекло по их чертежам и все, но так как исходников не было и в обозримом будущем не предвиделось, то я принялся повторять конструкцию по фотографиям.
Сейчас моя робо-рука выглядит так:
Работая не спеша за два года я успел сделать четыре версии и получил достаточно много опыта. Описание, историю проекта и все файлы проекта вы сможете найти под катом.
Пробы и ошибки
Начиная работать над чертежами, я хотел не просто повторить uArm, а улучшить его. Мне казалось, что в моих условиях вполне можно обойтись без подшипников. Так же мне не нравилось то, что электроника вращается вместе со всем манипулятором и хотелось упростить конструкцию нижней части шарнира. Плюс я начал рисовать его сразу немного меньше.
С такими входными параметрами я нарисовал первую версию. К сожалению, у меня не сохранилось фотографий той версии манипулятора (который был выполнен в желтом цвете). Ошибки в ней были просто эпичнейшие. Во-первых, ее было почти невозможно собрать. Как правило, механика которую я рисовал до манипулятора, была достаточно простая, и мне не приходилось задумываться о процессе сборки. Но все-таки я его собрал и попробовал запустить, И рука почти не двигалась! Все детли крутились вокруг винтов и, сли я затягивал их так, чтобы было меньше люфтов, она не могла двигаться. Если ослаблял так, чтобы она могла двигаться, появлялись невероятные люфты. В итоге концепт не прожил и трех дней. И приступил к работе над второй версией манипулятора.
Красный был уже вполне пригоден к работе. Он нормально собирался и со смазкой мог двигаться. На нем я смог протестировать софт, но все-таки отсутствие подшипников и большие потери на разных тягах делали его очень слабым.
Затем я забросил работу над проектом на какое-то время, но вскоре принял решении довести его до ума. Я решил использовать более мощные и популярные сервоприводы, увеличить размер и добавить подшипники. Причем я решил, что не буду пытаться сделать сразу все идеально. Я набросал чертежи на скорую руки, не вычерчивая красивых сопряжений и заказал резку из прозрачного оргстекла. На получившемся манипуляторе я смог отладить процесс сборки, выявил места, нуждающиеся в дополнительном укреплении, и научился использовать подшипники.
После того, как я вдоволь наигрался с прозрачным манипулятором, я засел за чертежи финальной белой версии. Итак, сейчас вся механика полностью отлажена, устраивает меня и готов заявить, что больше ничего не хочу менять в этой конструкции:
Меня удручает то, что я не смог привнести ничего принципиально нового в проект uArm. К тому времени, как я начал рисовать финальную версию, они уже выкатили 3D-модели на GrabCad. В итоге я только немного упростил клешню, подготовил файлы в удобном формате и применил очень простые и стандартные комплектующие.
Особенности манипулятора
До появления uArm, настольные манипуляторы подобного класса выглядели достаточно уныло. У них либо не было электроники вообще, либо было какое-нибудь управление с резисторами, либо было свое проприетарное ПО. Во-вторых, они как правило не имели системы параллельных шарниров и сам захват менял свое положение в процессе работы. Если собрать все достоинства моего манипулятора, то получается достаточно длинный список:
- Система тяг, позволяющих разместить мощные я тяжелые двигатели в основании манипулятора, а также удерживающие захват параллельно или перпендикулярно основанию
- Простой набор комплектующих, которые легко купить или вырезать из оргстекла
- Подшипники почти во всех узлах манипулятора
- Простота сборки. Это оказалось действительно сложной задачей. Особенно трудно было продумать процесс сборки основания
- Положение захвата можно менять на 90 градусов
- Открытые исходники и документация. Все подготовлено в доступных форматах. Я дам ссылки для скачивания на 3D-модели, файлы для резки, список материалов, электронику и софт
- Arduino-совместимость. Есть много противников Arduino, но я считаю, что это возможность расширения аудитории. Профессионалы вполне могут написать свой софт на C — это же обычный контроллер от Atmel!
Механика
Для сборки необходимо вырезать детали из оргстекла толщиной 5мм:
… и 3мм:
С меня за резку всех этих деталей взяли около $10.
Основание монтируется на большом подшипнике:
Особенно трудно было продумать основание с точки зрения процесса сборки, но я подглядывал за инженерами из uArm. Качалки сидят на штифте диаметром 6мм. Надо отметить, что тяга локтя у меня держится на П-образном держателе, а у uFactory на Г-образном. Трудно объяснить в чем разница, но я считаю у меня получилось лучше.
Захват собирается отдельно. Он может поворачиваться вокруг своей оси. Сама клешня сидит прямо на валу двигателя:
В конце статьи я дам ссылку на суперподробную инструкцию по сборке в фотографиях. За пару часов можно уверенно все это скрутить, если все необходимое есть под рукой. Также я подготовил 3D-модель в бесплатной программе SketchUp. Её можно скачать, покрутить и посмотреть что и как собрано.
Электроника
Чтобы заставить руку работать достаточно всего навсего подключить пять сервоприводов к Arduino и подать на них питание с хорошего источника. У uArm использованы какие-то двигатели с обратной связью. Я поставил три обычных двигателя MG995 и два маленьких двигателя с металлическим редуктором для управления захватом.
Тут мое повествование тесно сплетается с предыдущими проектами. С некоторых пор я начал преподавать программирование Arduino и для этих целей даже подготовил свою Arduino-совместимую плату. С другой стороны как-то раз мне подвернулась возможность дешево изготовить платы (о чем я тоже писал). В итоге все это закончилось тем, что я использовал для управления манипулятором свою собственную Arduino-совместимую плату и специализированный шилд.
Этот шилд на самом деле очень простой. На нем четыре переменных резистора, две кнопки, пять разъемов для сервопривода и разъем питания. Это очень удобно с точки зрения отладки. Можно загрузить тестовый скетч и записать какой-нибудь макрос для управления или что-нибудь вроде того. Ссылку для скачивания файла платы я тоже дам в конце статьи, но она подготовлена для изготовления с металлизацией отверстий, так что мало пригодна для домашнего производства.
Программирование
Самое интересное, это управление манипулятором с компьютера. У uArm есть удобное приложение для управления манипулятором и протокол для работы с ним. Компьютер отправляет в COM-порт 11 байт. Первый из них всегда 0xFF, второй 0xAA и некоторые из оставшихся — сигналы для сервоприводов. Далее эти данные нормализуются и отдаются на отработку двигателям. У меня сервоприводы подключены к цифровым входам/выходам 9-12, но это легко можно поменять.
Терминальная программа от uArm позволяет изменять пять параметров при управлении мышью. При движении мыши по поверхности изменяется положение манипулятора в плоскости XY. Вращение колесика — изменение высоты. ЛКМ/ПКМ — сжать/разжать клешню. ПКМ + колесико — поворот захвата. На самом деле очень удобно. При желании можно написать любой терминальный софт, который будет общаться с манипулятором по такому же протоколу.
Я не буду здесь приводить скетчи — скачать их можно будет в конце статьи.
Видео работы
И, наконец, само видео работы манипулятора. На нем показано управление мышью, резисторами и по заранее записанной программе.
Ссылки
Файлы для резки оргстекла, 3D-модели, список для покупки, чертежи платы и софт можно скачать в конце моей основной статьи.
Подробная инструкция по сборке в фотографиях (осторожно, траффик).
habr.com
Ручные манипуляторы относительного перемещения
а) “мышь“
Наиболее распространенный ручной манипулятор ввода относительного перемещения “мышь” был изобретен в 1963 г. в Стенфорде. До начала 70-х годов это было устройство с аналоговым сигналом, получаемым за счет переменных сопротивлений, управляемых двумя взаимно перпендикулярно расположенных колесика, вращающихся при движении конструкции по плоскому столу. С 1983 г. фирма Microsoft предложила конструкцию, включающую резинометаллический шарик, передающий свое вращение при движении двум взаимно – перпендикулярным роликам. На корпусе были предусмотрены две кнопки зеленого цвета. Эта мышь была связана кабелем с ПЭВМ через последовательный порт.
современные «мыши» вместо механического вращения шарика используют оптические средства распознавания направления перемещения – так называемые «оптические мыши».
Дорогие версии вместо кабеля используют средства радиосвязи с основным блоком компьютера – Blutooth, что делает их использование более удобным.
б)Трекбол представляет собой «мышь», перевернутую шариком вверх. Вращение шарика осуществляется ладонью оператора, поэтому корпус не перемещается по столу, и не требует много места на столе. На корпусе также имеется несколько кнопок (обычно на боковых сторонах), а сам корпус часто крепится к столу резиновой присоской. Чаще всего, трекбол встраивают в ноутбуки.
в) Джойстик позволяет выполнять очень быстрые перемещения курсора по экрану, но затрудняет тонкую работу с курсором. Поэтому его чаще всего используют для работы с игровыми программами.
Дополнительные устройства ввода (дигитайзер, сканер, видеокамера, мИкрофон)
1)Дигитайзер является устройством ввода абсолютных координат любой точки специального планшета. Используется в профессиональной деятельности, т.к. является дорогим высокоточным устройством. Чаще всего дигитайзеры применяются для переноса в электронный вид (оцифровки) чертежей и географических карт.
Дигитайзер состоит из двух частей – ручного манипулятора с электрическим проводом, намотанным на катушку, прицела и кнопки замыкания цепи катушки и планшета, внутри которого проложены провода в форме петель. При нажатии клавиши, по катушке течет ток, создающий магнитное поле. Это поле вызывает напряжение индукции в петлях планшета, тем большее, чем ближе петли к центру катушки манипулятора.
2)Сканер – это устройство для ввода в ПК текстовой или графической информации (черно-белой и цветной) в растровом виде для ее дальнейшей обработки. Сканером создаются файлы растрового формата. Сканирование производится для плоских объектов (обычно листов документов) формата А4, А3 и реже больших размеров.
3)Видеокамера (фотокамера) Основаны на тех же принципах, что и сканеры, но изображение снимается с матрицы, находящейся за объективом камеры. Преимущества – быстрота, простота и отсутствие ограничений на размеры «сканируемых» объектов, недостатки – малая точность и слабое разрешение по сравнению со сканерами.
4)Микрофон -В настоящее время еще нельзя говорить о микрофоне, как об устройстве полноценного ввода данных в ЭВМ, хотя в этом направлении ведутся активные разработки.
Дисплеи
Монитор(дисплей) ПЭВМ служит для вывода на экран текстовой и графической информации. Дисплей и плата видеоадаптера (графическая плата) составляют видеосистему. В видеосистемах применяется аналоговая и цифровая технология получения отображения на экране. Дисплей является системным устройством вывода.
Основными характеристиками дисплея являются:
1. размер экрана (длина диагонали в дюймах). Для ноутбуков – 10 – 15′, для настольных компьютеров – 17 – 19′
2. разрешение экрана – иногда под этим понимается расстояние между соседними пикселями, чаще – максимальное количество строк экрана и число пикселей в строке.
3. глубина (качество) цветопередачи – количество бит на 1 пиксель. В настоящее время – до 32 бит раньше – 24 бита (TRUECOLOR), 16 бит .
4. контрастность и яркость цветов (важно для ЖК-дисплеев), 1:500 -1:1000.
5. предельные углы обзора в вертикальной и горизонтальной плоскостях.
6. потребляемая мощность.
Видеоадаптер – это устройство, управляющее выводом на экран текстовой информации и графических изображений. Видеоадаптер организует интерфейс между ПК и дисплеем.
Принтеры и плоттеры
Принтеры
а) буквопечатающие (барабанные, “сферические”, “ромашки”)
б) матричные (игольчатые, струйные)
в) лазерные
Плоттеры
а) планшетные б) барабанные
infopedia.su
Рука-манипулятор своими руками: как сделать?
Мы рассмотрим, как делается рука-манипулятор своими руками, на промышленных образцах. Сначала будут затронуты общие вопросы, потом технические характеристики результата, детали, а под конец и сам процесс сборки.
В целом и общем
Создание данного устройства в целом не должно вызвать каких-то сложностей. Необходимо будет качественно продумать только возможности механических движений, что будет довольно сложно осуществить с физической точки зрения, чтобы рука-манипулятор выполняла поставленные перед ней задачи.
Технические характеристики результата
Будет рассматриваться образец с параметрами длины/высоты/ширины соответственно 228/380/160 миллиметров. Вес руки-манипулятора, своими руками сделанной, будет составлять примерно 1 килограмм. Для управления используется проводной дистанционный пульт. Ориентировочное время сборки при наличии опыта – около 6-8 часов. Если его нет, то могут уйти дни, недели, а при попустительстве и месяцы, чтобы была собрана рука-манипулятор. Своими руками и одному в таких случаях стоит делать разве что для своего собственного интереса. Для движения составляющих используются коллекторные моторы. Приложив достаточно усилий, можно сделать прибор, который будет поворачиваться на 360 градусов. Также для удобства работы, кроме стандартного инструментария вроде паяльника и припоя, необходимо запастись:
- Удлинёнными плоскогубцами.
- Боковыми кусачками.
- Крестовой отверткой.
- 4-мя батарейками типа D.
Пульт дистанционного управления можно реализовать, используя кнопки и микроконтроллер. При желании сделать дистанционное беспроводное управление элемент контроля действий понадобится и в руке-манипуляторе. В качестве дополнений необходимы будут только устройства (конденсаторы, резисторы, транзисторы), которые позволят стабилизировать схему и передавать по ней в нужные моменты времени ток необходимой величины.
Мелкие детали
Для регуляции количества оборотов можно использовать переходные колесики. Они позволят сделать движение руки-манипулятора плавными.
Также необходимо позаботится о том, чтобы провода не усложняли её движения. Оптимальным будет проложить их внутри конструкции. Можно сделать всё и извне, такой подход сэкономит время, но потенциально может привести к сложностям в перемещении отдельных узлов или всего устройства. А теперь: как сделать манипулятор?
Сборка в общих чертах
Теперь приступаем непосредственно к созданию руки-манипулятора. Начинаем с основания. Необходимо обеспечить возможность поворота устройства во все стороны. Хорошим решением будет его размещение на дисковой платформе, которая приводится во вращение с помощью одного мотора. Чтобы она могла вращаться в обе стороны, существует два варианта:
- Установка двух двигателей. Каждый из них будет отвечать за поворот в конкретную сторону. Когда один работает, второй пребывает в состоянии покоя.
- Установка одного двигателя со схемой, которая сможет заставить его крутится в обе стороны.
Какой из предложенных вариантов выбрать, зависит исключительно от вас. Далее делается основная конструкция. Для комфорта работы необходимо два «сустава». Прикреплённый к платформе должен уметь наклоняться в разные стороны, что решается с помощью двигателей, размещённых в его основании. Ещё один или пару следует разместить в месте локтевого изгиба, чтобы часть захвата можно было перемещать по горизонтальной и вертикальной линии системы координат. Далее, при желании получить максимальные возможности, можно установить ещё двигатель в месте запястья. Далее наиболее необходимое, без чего не представляется рука-манипулятор. Своими руками предстоит сделать само устройство захвата. Тут существует множество вариантов реализации. Можно дать наводку по двум самым популярным:
- Используется только два пальца, которые одновременно сжимают и разжимают объект захвата. Является самой простой реализацией, которая, правда, обычно не может похвастаться значительной грузоподъёмностью.
- Создаётся прототип человеческой руки. Тут для всех пальцев может использоваться один двигатель, с помощью которого будет осуществляться сгиб/разгиб. Но можно сделать и конструкцию сложней. Так, можно к каждому пальцу подсоединить по двигателю и управлять ими отдельно.
Далее остаётся сделать пульт, с помощью которого будет оказываться влияние на отдельные двигатели и темпы их работы. И можно приступать к экспериментам, используя робот-манипулятор, своими руками сделанный.
Возможные схематические изображения результата
Рука-манипулятор своими руками предоставляет широкие возможности для творческих измышлений. Поэтому предоставляются вашему вниманию несколько реализаций, которые можно взять за основу для создания своего собственного устройства подобного предназначения.
Любая представленная схема манипулятора может быть усовершенствована.
Заключение
Важным в робототехнике является то, что практически не существует ограничения по функциональному улучшению. Поэтому при желании создать настоящее произведение искусства не составит труда. Говоря о возможных путях дополнительного улучшения, следует отметить кран-манипулятор. Своими руками сделать такое устройство не составит труда, одновременно оно позволит приучить детей к творческому труду, науке и конструировании. А это в свою очередь позитивно может сказаться на их будущей жизни. Сложно ли будет сделать кран-манипулятор своими руками? Это не так проблемно, как может показаться на первый взгляд. Разве что стоит позаботиться о наличии дополнительных мелких деталей вроде троса и колёс, по которым он будет крутиться.
fb.ru
Добавить комментарий