ΠΠ°ΠΊΠΈΠ΅ ΠΏΠ°ΡΠ°ΠΌΠ΅ΡΡΡ ΡΠ»Π΅ΠΊΡΡΠΎΠ΄ΠΎΠ² ΡΠ»Π΅Π΄ΡΠ΅Ρ ΠΊΠΎΠ½ΡΡΠΎΠ»ΠΈΡΠΎΠ²Π°ΡΡ ΠΏΠ΅ΡΠ΅Π΄ ΠΏΡΠΈΠΌΠ΅Π½Π΅Π½ΠΈΠ΅ΠΌ β ΠΊΠ°ΠΊΠΈΠ΅ ΠΏΠ°ΡΠ°ΠΌΠ΅ΡΡΡ ΡΠ»Π΅ΠΊΡΡΠΎΠ΄ΠΎΠ² ΡΠ»Π΅Π΄ΡΠ΅Ρ ΠΊΠΎΠ½ΡΡΠΎΠ»ΠΈΡΠΎΠ²Π°ΡΡ, ΡΡΠΎ ΠΏΡΠΎΠ²Π΅ΡΡΡΡ Π² ΠΎΠ±ΠΎΡΡΠ΄ΠΎΠ²Π°Π½ΠΈΠΈ
ΠΊΠ°ΠΊΠΈΠ΅ ΠΏΠ°ΡΠ°ΠΌΠ΅ΡΡΡ ΡΠ»Π΅ΠΊΡΡΠΎΠ΄ΠΎΠ² ΡΠ»Π΅Π΄ΡΠ΅Ρ ΠΊΠΎΠ½ΡΡΠΎΠ»ΠΈΡΠΎΠ²Π°ΡΡ, ΡΡΠΎ ΠΏΡΠΎΠ²Π΅ΡΡΡΡ Π² ΠΎΠ±ΠΎΡΡΠ΄ΠΎΠ²Π°Π½ΠΈΠΈ
Π‘Π²Π°ΡΠΎΡΠ½ΠΎΠ΅ ΠΎΠ±ΠΎΡΡΠ΄ΠΎΠ²Π°Π½ΠΈΠ΅ ΠΈ ΡΠ²Π°ΡΠΎΡΠ½ΡΠ΅ ΠΌΠ°ΡΠ΅ΡΠΈΠ°Π»Ρ β Π²ΡΠ΅, ΡΡΠΎ ΠΎΡΠ½ΠΎΡΠΈΡΡΡ ΠΊ ΠΏΡΠΎΡΠ΅ΡΡΡ ΡΠ²Π°ΡΠΊΠΈ.
Π ΡΠ²Π°ΡΠΎΡΠ½ΡΠΌ ΠΌΠ°ΡΠ΅ΡΠΈΠ°Π»Π°ΠΌ ΠΎΡΠ½ΠΎΡΠΈΡΡΡ Π²ΡΠ΅, ΡΡΠΎ ΠΈΡΠΏΠΎΠ»ΡΠ·ΡΠ΅ΡΡΡ ΠΏΠΎ Ρ ΠΎΠ΄Ρ ΡΠ²Π°ΡΠΎΡΠ½ΡΡ ΡΠ°Π±ΠΎΡ. ΠΡΠ»ΠΈ Π³ΠΎΠ²ΠΎΡΠΈΡΡ Π² ΠΎΠ±ΡΠ΅ΠΌ, ΡΠΎ ΡΡΠΎ Π² Π±ΠΎΠ»ΡΡΠ΅ΠΉ ΡΡΠ΅ΠΏΠ΅Π½ΠΈ ΡΠ°ΡΡ ΠΎΠ΄Π½ΡΠ΅ ΠΌΠ°ΡΠ΅ΡΠΈΠ°Π»Ρ.
ΠΠΈΠ΄Ρ ΡΠ²Π°ΡΠΎΡΠ½ΡΡ ΠΌΠ°ΡΠ΅ΡΠΈΠ°Π»ΠΎΠ²
Π€ΡΠ½ΠΊΡΠΈΠΈ,Β ΠΊΠΎΡΠΎΡΡΠ΅ Π²ΡΠΏΠΎΠ»Π½ΡΡΡ ΡΠ²Π°ΡΠΎΡΠ½ΡΠ΅ ΠΌΠ°ΡΠ΅ΡΠΈΠ°Π»Ρ, ΡΠ»Π΅Π΄ΡΡΡΠΈΠ΅:
- ΠΠ°ΡΠΈΡΠ° ΠΌΠ΅ΡΠ°Π»Π»Π° Ρ ΠΏΠΎΠΌΠΎΡΡΡ Π³Π°Π·Π° ΠΈΠ»ΠΈ ΡΠ»Π°ΠΊΠ° ΠΎΡ Π²ΡΠ΅Π΄ΠΎΠ½ΠΎΡΠ½ΠΎΠ³ΠΎ Π²ΠΎΠ·Π΄Π΅ΠΉΡΡΠ²ΠΈΡ Π²ΠΎΠ·Π΄ΡΡ Π°.
- ΠΠΎΠ²ΡΡΠ΅Π½ΠΈΠ΅ ΡΡΠ°Π±ΠΈΠ»ΡΠ½ΠΎΡΡΠΈ ΠΏΠ»Π°ΠΌΠ΅Π½ΠΈ ΠΈ Π²ΡΠ΅Π³ΠΎ ΠΏΡΠΎΡΠ΅ΡΡΠ° ΡΠ²Π°ΡΠΊΠΈ.
- ΠΠ·ΠΌΠ΅ΡΠ΅Π½ΠΈΠ΅ ΡΠ°Π·ΠΌΠ΅ΡΠΎΠ² ΡΠΎΡΠΌΠΈΡΡΠ΅ΠΌΠΎΠ³ΠΎ ΡΠ²Π°ΡΠΎΡΠ½ΠΎΠ³ΠΎ ΡΠ²Π°.
- Π€ΠΎΡΠΌΠΈΡΠΎΠ²Π°Π½ΠΈΠ΅ Π½Π΅ΠΎΠ±Ρ ΠΎΠ΄ΠΈΠΌΠΎΠΉ ΠΌΠ΅ΡΠ°Π»Π»ΠΈΡΠ΅ΡΠΊΠΎΠ³ΠΎ ΡΠΎΡΡΠ°Π²Π° ΡΠ²Π°ΡΠΎΡΠ½ΠΎΠ³ΠΎ ΡΠ²Π° ΠΏΠΎ Π·Π°Π΄Π°Π½Π½ΡΠΌ ΡΠ²ΠΎΠΉΡΡΠ²Π°ΠΌ.
- Π§ΠΈΡΡΠΊΠ° ΠΎΡ ΠΏΡΠΈΠΌΠ΅ΡΠ΅ΠΉ ΡΠ²Π° ΠΏΠΎΡΠ»Π΅ ΡΠ²Π°ΡΠΊΠΈ.
ΠΠΈΠ΄Ρ ΡΠ²Π°ΡΠΎΡΠ½ΡΡ ΠΌΠ°ΡΠ΅ΡΠΈΠ°Π»ΠΎΠ² ΠΌΠΎΠΆΠ½ΠΎ ΠΊΠ»Π°ΡΡΠΈΡΠΈΡΠΈΡΠΎΠ²Π°ΡΡ ΠΏΠΎ-ΡΠ°Π·Π½ΠΎΠΌΡ. ΠΠΎ ΡΠ²ΠΎΠ΅ΠΌΡ ΡΠΎΡΡΠ°Π²Ρ ΠΈΡ ΠΌΠΎΠΆΠ½ΠΎ ΡΠ°Π·Π΄Π΅Π»ΠΈΡΡ Π½Π° Π΄Π²Π΅ Π±ΠΎΠ»ΡΡΠΈΠ΅ Π³ΡΡΠΏΠΏΡ: ΠΈΠΌΠ΅ΡΡΠΈΠ΅ ΠΏΡΡΠΌΠΎΠ΅ ΠΎΡΠ½ΠΎΡΠ΅Π½ΠΈΠ΅ ΠΊ ΡΠ²Π°ΡΠΊΠ΅ ΠΊΠ°ΠΊ Ρ ΠΈΠΌΠΈΡΠ΅ΡΠΊΠΎΠΌΡ ΠΏΡΠΎΡΠ΅ΡΡΡ ΠΈ ΡΠ°ΠΊ Π½Π°Π·ΡΠ²Π°Π΅ΠΌΡΠ΅ Π³Π°Π΄ΠΆΠ΅ΡΡ, ΠΎΠ±Π»Π΅Π³ΡΠ°ΡΡΠΈΠ΅ ΡΠ°Π±ΠΎΡΡ ΡΠ²Π°ΡΡΠΈΠΊΠ° Π½Π° ΡΠΎΠΌ ΠΈΠ»ΠΈ ΠΈΠ½ΠΎΠΌ ΡΡΠ°ΠΏΠ΅.
ΠΠΎ ΡΡΠ½ΠΊΡΠΈΡΠΌ ΡΠ²Π°ΡΠΎΡΠ½ΡΠ΅ ΠΌΠ°ΡΠ΅ΡΠΈΠ°Π»Ρ Π΄Π΅Π»ΡΡΡΡ ΡΠ»Π΅Π΄ΡΡΡΠΈΠΌ ΠΎΠ±ΡΠ°Π·ΠΎΠΌ:
ΠΠ»Π΅ΠΊΡΡΠΎΠ΄Ρ ΠΈ ΠΏΡΡΡΠΊΠΈ
ΠΠ»Π΅ΠΊΡΡΠΎΠ΄Ρ Π±ΡΠ²Π°ΡΡ ΠΏΠ»Π°Π²ΡΡΠΈΠΌΠΈΡΡ ΠΈ Π½Π΅ΠΏΠ»Π°Π²ΡΡΠΈΠΌΠΈΡΡ. ΠΠ»Π°Π²ΡΡΠΈΠ΅ΡΡ, Π² ΡΠ²ΠΎΡ ΠΎΡΠ΅ΡΠ΅Π΄Ρ, ΡΠ°Π·Π»ΠΈΡΠ°ΡΡΡΡ ΠΏΠΎ ΡΠΈΠΏΡ ΠΏΠΎΠΊΡΡΡΠΈΡ: ΡΠΌΠ΅ΡΠ°Π½Π½ΠΎΠΌΡ, ΠΊΠΈΡΠ»ΠΎΠΌΡ, ΠΎΡΠ½ΠΎΠ²Π½ΠΎΠΌΡ, ΡΡΡΠΈΠ»ΠΎΠ²ΠΎΠΌΡ ΠΈ Ρ.Π΄. ΠΡΠΈΡΠ°Π΄ΠΎΡΠ½ΡΠ΅ ΠΏΡΡΡΠΊΠΈ ΠΏΠΎΠΌΠ΅ΡΠ°ΡΡΡΡ Π²Π½ΡΡΡΠΈ ΡΠ²Π°ΡΠ½ΠΎΠ³ΠΎ ΡΠ²Π°. ΠΠ»Π΅ΠΊΡΡΠΎΠ΄Ρ ΠΏΡΠ΅Π΄Π½Π°Π·Π½Π°ΡΠ΅Π½Ρ Π΄Π»Ρ ΡΡΡΠ΅ΠΊΡΠΈΠ²Π½ΠΎΠΉ ΠΏΠΎΠ΄Π°ΡΠΈ ΡΠ»Π΅ΠΊΡΡΠΈΡΠ΅ΡΠΊΠΎΠ³ΠΎ ΡΠΎΠΊΠ° Π² Π·ΠΎΠ½Ρ ΠΏΠ»Π°Π²Π»Π΅Π½ΠΈΡ.
Π‘Π²Π°ΡΠΎΡΠ½Π°Ρ ΠΏΡΠΎΠ²ΠΎΠ»ΠΎΠΊΠ°
ΠΡΠΏΡΡΠΊΠ°Π΅ΡΡΡ Π² ΡΡΠ΅Ρ Π²Π°ΡΠΈΠ°Π½ΡΠ°Ρ : ΠΏΠΎΡΠΎΡΠΊΠΎΠ²Π°Ρ, Π°ΠΊΡΠΈΠ²ΠΈΡΠΎΠ²Π°Π½Π½Π°Ρ, ΡΠΏΠ»ΠΎΡΠ½Π°Ρ.
Π€Π»ΡΡΠΎΠ²ΡΠ΅ ΡΠΌΠ΅ΡΠΈ
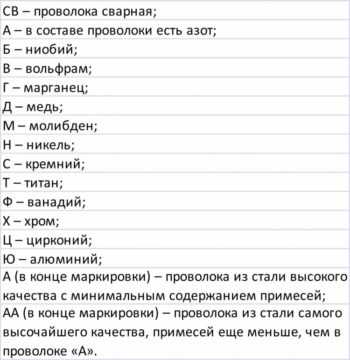
ΠΠ°ΡΠΊΠΈΡΠΎΠ²ΠΊΠ° ΡΠ²Π°ΡΠΎΡΠ½ΠΎΠΉ ΠΏΡΠΎΠ²ΠΎΠ»ΠΎΠΊΠΈ.
ΠΠΎΠ΄ΡΠ°Π·Π΄Π΅Π»ΡΡΡΡΡ Π½Π° ΡΠ΅ΠΏΠ»ΠΎΠΏΡΠΎΠ²ΠΎΠ΄Π½ΡΠ΅ ΠΈ Π·Π°ΡΠΈΡΠ½ΡΠ΅. ΠΡΠ΅Π΄Π½Π°Π·Π½Π°ΡΠ΅Π½Ρ Π΄Π»Ρ Π·Π°ΡΠΈΡΡ ΠΏΡΠΎΡΠ΅ΡΡΠ° Π΄ΡΠ³ΠΎΠ²ΠΎΠΉ ΡΠ²Π°ΡΠΊΠΈ. Π‘ΠΎΠ΄Π΅ΡΠΆΠ°Ρ Ρ ΠΈΠΌΠΈΡΠ΅ΡΠΊΠΈΠ΅ ΠΊΠΎΠΌΠΏΠΎΠ½Π΅Π½ΡΡ, ΠΊΠΎΡΠΎΡΡΠ΅ Π·Π°ΡΠΈΡΠ°ΡΡ ΡΠ²Π°ΡΠΈΠ²Π°Π΅ΠΌΡΠΉ ΠΌΠ΅ΡΠ°Π»Π» ΠΎΡ Π²ΠΎΠ·Π΄Π΅ΠΉΡΡΠ²ΠΈΡ Π²ΠΎΠ·Π΄ΡΡ Π°.
ΠΠ½Π΅ΡΡΠ½ΡΠ΅ Π·Π°ΡΠΈΡΠ½ΡΠ΅ ΠΈ Π³ΠΎΡΡΡΠΈΠ΅ Π³Π°Π·Ρ
ΠΡΠΏΠΎΠ»ΡΠ·ΡΡΡΡΡ Π΄Π»Ρ Π·Π°ΡΠΈΡΡ Π΄ΡΠ³ΠΈ ΠΈ Π΄Π»Ρ ΠΏΠΎΠ΄Π΄Π΅ΡΠΆΠΊΠΈ ΠΏΠ»Π°ΠΌΠ΅Π½ΠΈ. Π ΠΈΠ½Π΅ΡΡΠ½ΡΠΌ Π³Π°Π·Π°ΠΌ ΠΎΡΠ½ΠΎΡΡΡΡΡ Π°ΡΠ³ΠΎΠ½, Π³Π΅Π»ΠΈΠΉ ΠΈ ΠΈΡ ΡΠΌΠ΅ΡΠΈ Π² ΡΠ°Π·Π»ΠΈΡΠ½ΡΡ ΠΊΠΎΠ½ΡΠ΅Π½ΡΡΠ°ΡΠΈΡΡ . Π£Π³Π»Π΅ΠΊΠΈΡΠ»ΡΠΉ Π³Π°Π· ΠΈ Π΅Π³ΠΎ ΡΠΌΠ΅ΡΠΈ ΠΎΡΠ½ΠΎΡΡΡΡΡ Π² ΠΊ Π°ΠΊΡΠΈΠ²Π½ΡΠΌ Π²ΠΈΠ΄Π°ΠΌ Π³Π°Π·ΠΎΠ², ΠΊΠΎΡΠΎΡΡΠ΅ Π²Π·Π°ΠΈΠΌΠΎΠ΄Π΅ΠΉΡΡΠ²ΡΡΡ Ρ ΠΌΠ΅ΡΠ°Π»Π»ΠΎΠΌ ΠΈΠ»ΠΈ ΡΠ°ΡΡΠ²ΠΎΡΡΡΡΡΡ Π² Π½Π΅ΠΌ.
ΠΠΎΡΡΡΠΈΠ΅ Π³Π°Π·Ρ ΠΈΡΠΏΠΎΠ»ΡΠ·ΡΡΡΡΡ Π² Π³Π°Π·ΠΎΠ²ΠΎΠΉ ΡΠ΅Π·ΠΊΠ΅ ΠΈ Π³Π°Π·ΠΎΠ²ΠΎΠΉ ΡΠ²Π°ΡΠΊΠ΅, ΡΡΠΎ Π°ΡΠ΅ΡΠΈΠ»Π΅Π½, Π²ΠΎΠ΄ΠΎΡΠΎΠ΄, ΠΊΠΈΡΠ»ΠΎΡΠΎΠ΄ ΠΈ ΡΠ°Π·Π»ΠΈΡΠ½ΡΠ΅ ΡΠΌΠ΅ΡΠΈ.
ΠΠΎΠ΄ΠΊΠ»Π°Π΄ΠΊΠΈ, ΡΡΠ΅ΡΠ³ΠΎΠ»ΡΠ½ΠΈΠΊΠΈ ΠΈ ΠΏΡ.
ΠΠ΅ΡΠ°ΠΌΠΈΡΠ΅ΡΠΊΠΈΠ΅ ΠΏΠΎΠ΄ΠΊΠ»Π°Π΄ΠΊΠΈ Π±ΡΠ²Π°ΡΡ ΡΠ°Π·Π½ΠΎΠΉ ΡΠΎΡΠΌΡ: ΠΎΠΊΡΡΠ³Π»ΡΠΌΠΈ, Π²ΡΠ΅ΠΏΠΎΠ·ΠΈΡΠΈΠΎΠ½Π½ΡΠΌΠΈ, Π΄Π»Ρ ΠΊΠΎΠ½ΠΊΡΠ΅ΡΠ½ΡΡ Π²ΠΈΠ΄ΠΎΠ² ΡΠ²ΠΎΠ² ΠΈ Ρ.Π΄. ΠΠ½ΠΈ ΠΎΠ±Π»Π΅Π³ΡΠ°ΡΡ ΡΠ°Π±ΠΎΡΠΈΠΉ ΠΏΡΠΎΡΠ΅ΡΡ ΠΈ ΡΠΏΠΎΡΠΎΠ±ΡΡΠ²ΡΡΡ ΡΠΎΡΠΌΠΈΡΠΎΠ²Π°Π½ΠΈΡ ΠΎΠ±ΡΠ°ΡΠ½ΠΎΠ³ΠΎ Π²Π°Π»ΠΈΠΊΠ° Π² ΠΊΠ°ΡΠ΅ΡΡΠ²Π΅Π½Π½ΠΎΠΌ ΡΠ²Π΅.
ΠΠΎΠ½ΡΡΠΎΠ»Ρ ΠΊΠ°ΡΠ΅ΡΡΠ²Π° ΡΠ²Π°ΡΠΎΡΠ½ΡΡ ΠΌΠ°ΡΠ΅ΡΠΈΠ°Π»ΠΎΠ²
ΠΠ°ΡΠ΅ΡΡΠ²ΠΎ ΡΠ²Π° Π·Π°Π²ΠΈΡΠΈΡ ΠΎΡ ΠΌΠ½ΠΎΠ³ΠΈΡ ΡΠ°ΠΊΡΠΎΡΠΎΠ². ΠΠΎ ΡΠ°ΠΌΠ°Ρ Π²ΡΡΠΎΠΊΠ°Ρ Π·Π°Π²ΠΈΡΠΈΠΌΠΎΡΡΡ Π²ΡΠ΅Π³Π΄Π° ΠΎΡ ΠΎΠ΄Π½ΠΎΠ³ΠΎ ΠΈ ΡΠΎΠ³ΠΎ ΠΆΠ΅ ΡΠ°ΠΊΡΠΎΡΠ°: ΠΊΠ°ΡΠ΅ΡΡΠ²Π° ΡΠ°ΡΡ ΠΎΠ΄Π½ΡΡ ΠΌΠ°ΡΠ΅ΡΠΈΠ°Π»ΠΎΠ². ΠΡΠΎ ΠΊΠ°ΡΠ΅ΡΡΠ²ΠΎ Π½ΡΠΆΠ½ΠΎ ΠΏΠΎΡΡΠΎΡΠ½Π½ΠΎ ΠΊΠΎΠ½ΡΡΠΎΠ»ΠΈΡΠΎΠ²Π°ΡΡ Ρ Π²ΡΠΏΠΎΠ»Π½Π΅Π½ΠΈΠ΅ΠΌ ΡΡΠ°Π½Π΄Π°ΡΡΠΎΠ² ΠΈ ΠΏΡΠ°Π²ΠΈΠ» ΠΊΠΎΠ½ΡΡΠΎΠ»Ρ ΠΈ, ΡΠ°ΠΌΠΎΠ΅ Π³Π»Π°Π²Π½ΠΎΠ΅, Ρ ΡΠ°Π½Π΅Π½ΠΈΡ ΠΈ ΡΠΏΠΎΡΡΠ΅Π±Π»Π΅Π½ΠΈΡ Π²ΡΠ΅Ρ ΡΠ²Π°ΡΠΎΡΠ½ΡΡ ΠΊΠΎΠΌΠΏΠΎΠ½Π΅Π½ΡΠΎΠ².
Π Π°ΡΡ ΠΎΠ΄Π½ΡΠ΅ ΠΌΠ°ΡΠ΅ΡΠΈΠ°Π»Ρ Π΄Π»Ρ ΡΠ²Π°ΡΠΊΠΈ Π² ΠΎΠ±ΡΠ·Π°ΡΠ΅Π»ΡΠ½ΠΎΠΌ ΠΏΠΎΡΡΠ΄ΠΊΠ΅ Π΄ΠΎΠ»ΠΆΠ½Ρ ΠΈΠΌΠ΅ΡΡ ΡΠ΅ΡΡΠΈΡΠΈΠΊΠ°ΡΡ Ρ Π΄Π°Π½Π½ΡΠΌΠΈ, ΡΠΎΠΎΡΠ²Π΅ΡΡΡΠ²ΡΡΡΠΈΠΌΠΈ ΡΡΠ΅Π±ΠΎΠ²Π°Π½ΠΈΡΠΌ ΠΠΠ‘Π’ΠΎΠ², ΡΠ΅Ρ Π½ΠΈΡΠ΅ΡΠΊΠΈΡ ΠΏΠ°ΡΠΏΠΎΡΡΠΎΠ² ΠΈ Π΄ΡΡΠ³ΠΈΡ ΡΠ΅Ρ Π½ΠΎΠ»ΠΎΠ³ΠΈΡΠ΅ΡΠΊΠΈΡ Π΄ΠΎΠΊΡΠΌΠ΅Π½ΡΠΎΠ².
Π‘Π°ΠΌΡΠΌ ΠΏΠ΅ΡΠ²ΡΠΌ ΠΈ ΠΏΡΠΎΡΡΡΠΌ ΡΡΠ΅Π±ΠΎΠ²Π°Π½ΠΈΠ΅ΠΌ ΡΠ²Π»ΡΠ΅ΡΡΡ ΡΠΎΠ±Π»ΡΠ΄Π΅Π½ΠΈΠ΅ ΠΌΠ°ΡΠΊΠΈΡΠΎΠ²ΠΊΠΈ ΡΠΏΠ°ΠΊΠΎΠ²ΠΎΡΠ½ΡΡ ΠΈΠ·Π΄Π΅Π»ΠΈΠΉ Π² Π²ΠΈΠ΄Π΅ ΠΊΠΎΡΠΎΠ±ΠΎΠΊ, ΠΏΠ°ΡΠ΅ΠΊ, Π±Π°Π»Π»ΠΎΠ½ΠΎΠΌ ΠΈΠ»ΠΈ ΠΏΠ°Π»Π»Π΅Ρ, Π½Π° ΠΊΠΎΡΠΎΡΡΡ Π² ΠΎΠ±ΡΠ·Π°ΡΠ΅Π»ΡΠ½ΠΎΠΌ ΠΏΠΎΡΡΠ΄ΠΊΠ΅ Π΄ΠΎΠ»ΠΆΠ½Ρ Π±ΡΡΡ ΡΠΊΠ°Π·Π°Π½Ρ Π³Π»Π°Π²Π½ΡΠ΅ ΠΏΠ°ΡΠΏΠΎΡΡΠ½ΡΠ΅ Π΄Π°Π½Π½ΡΠ΅.
ΠΠ΅Π· ΡΠ°ΠΊΠΎΠ³ΠΎ ΡΠΎΠ΄Π° Π΄Π°Π½Π½ΡΡ Π²ΡΡ ΠΏΠ°ΡΡΠΈΡ ΡΠ°ΡΡ ΠΎΠ΄Π½ΡΡ ΠΌΠ°ΡΠ΅ΡΠΈΠ°Π»ΠΎΠ² Π΄ΠΎΠ»ΠΆΠ½Π° Π±ΡΡΡ ΠΏΡΠΎΠ²Π΅ΡΠ΅Π½Π° ΠΏΠΎ Π²ΡΠ΅ΠΌ ΡΡΡΠ°Π½ΠΎΠ²Π»Π΅Π½Π½ΡΠΌ ΠΏΠΎΠΊΠ°Π·Π°ΡΠ΅Π»ΡΠΌ Ρ Π²ΡΠΊΡΡΡΠΈΠ΅ΠΌ ΡΠΏΠ°ΠΊΠΎΠ²ΠΊΠΈ, Π΄ΠΎ ΠΊΠΎΠ½ΡΠ° ΠΊΠΎΡΠΎΡΠΎΠΉ ΠΈΡΠΏΠΎΠ»ΡΠ·ΠΎΠ²Π°Π½ΠΈΠ΅ ΡΡΠΈΡ ΠΈΠ·Π΄Π΅Π»ΠΈΠΉ Π·Π°ΠΏΡΠ΅ΡΠ°Π΅ΡΡΡ.
ΠΠΎΠΏΡΠΎΡ, ΠΊΠ°ΠΊ ΠΈ Π² ΠΊΠ°ΠΊΠΎΠΌ ΠΎΠ±ΡΠ΅ΠΌΠ΅ ΠΌΠΎΠΆΠ½ΠΎ ΠΈΡΠΏΠΎΠ»ΡΠ·ΠΎΠ²Π°ΡΡ ΡΠ°ΡΡ ΠΎΠ΄Π½ΠΈΠΊΠΈ, ΠΊΠΎΡΠΎΡΡΠ΅ ΠΈΠΌΠ΅ΡΡ Π½Π΅ΡΠΎΠΎΡΠ²Π΅ΡΡΡΠ²ΠΈΠ΅, ΠΈΠ»ΠΈ ΡΠΏΠ°ΠΊΠΎΠ²ΠΊΠ° ΠΊΠΎΡΠΎΡΡΡ ΠΏΠΎΠ²ΡΠ΅ΠΆΠ΄Π΅Π½Π°, ΡΠ΅ΡΠ°Π΅ΡΡΡ Π½Π°ΡΠ°Π»ΡΡΡΠ²ΠΎΠΌ Π² ΠΊΠ°ΠΆΠ΄ΠΎΠΌ ΠΈΠ½Π΄ΠΈΠ²ΠΈΠ΄ΡΠ°Π»ΡΠ½ΠΎΠΌ ΡΠ»ΡΡΠ°Π΅.
ΠΠΎΠ½ΡΡΠΎΠ»Ρ ΠΊΠ°ΡΠ΅ΡΡΠ²Π° ΡΠ»Π΅ΠΊΡΡΠΎΠ΄ΠΎΠ²
ΠΠ»Π΅ΠΊΡΡΠΎΠ΄Ρ β ΡΠ°ΠΌΡΠ΅ Β«ΠΏΡΠΎΠ²Π΅ΡΡΠ΅ΠΌΡΠ΅Β» ΡΠ°ΡΡ ΠΎΠ΄Π½ΠΈΠΊΠΈ. ΠΡ ΠΊΠ°ΡΠ΅ΡΡΠ²ΠΎ Π½Π°ΡΠΈΠ½Π°ΡΡ ΠΊΠΎΠ½ΡΡΠΎΠ»ΠΈΡΠΎΠ²Π°ΡΡ Π΅ΡΠ΅ Π½Π° Π·Π°Π²ΠΎΠ΄Π΅. ΠΠΎΠ²ΡΠΎΡΠ½ΡΠΉ ΠΊΠΎΠ½ΡΡΠΎΠ»Ρ ΠΏΡΠΎΠ²ΠΎΠ΄ΠΈΡΡΡ ΡΠΆΠ΅ Π½Π° ΡΡΠ°ΡΡΠΊΠ°Ρ ΡΠΎ ΡΠ²Π°ΡΠΊΠΎΠΉ, ΠΈΠ½ΠΎΠ³Π΄Π° ΠΎΠ½ Π½Π°Π·ΡΠ²Π°Π΅ΡΡΡ Π²Ρ ΠΎΠ΄Π½ΠΎΠΉ ΠΊΠΎΠ½ΡΡΠΎΠ»Ρ ΡΠ²Π°ΡΠΎΡΠ½ΡΡ ΠΌΠ°ΡΠ΅ΡΠΈΠ°Π»ΠΎΠ².
ΠΡΠΎΠ²Π΅ΡΠΊΠ° ΠΏΠΎΠΊΡΡΡΠΈΡ
ΠΠ΅ΡΠ²ΡΠΌ Π΄Π΅Π»ΠΎΠΌ ΠΏΡΠΎΠ²Π΅ΡΡΠ΅ΠΌ ΠΏΠΎΠΊΡΡΡΠΈΠ΅, ΠΊΠΎΡΠΎΡΠΎΠ΅ Π΄ΠΎΠ»ΠΆΠ½ΠΎ Π±ΡΡΡ ΠΏΠ»ΠΎΡΠ½ΡΠΌ. ΠΠ»Π΅ΠΊΡΡΠΎΠ΄ Π½Π΅ Π΄ΠΎΠ»ΠΆΠ΅Π½ ΠΎΡΡΠΏΠ°ΡΡΡΡ ΠΈΠ»ΠΈ ΡΠ°Π·ΡΡΡΠ°ΡΡΡΡ, Π΅ΡΠ»ΠΈ Π±ΡΠΎΡΠΈΡΡ Π΅Π³ΠΎ ΠΏΠ»Π°ΡΠΌΡ Π½Π° ΡΡΠ°Π»ΡΠ½ΡΡ ΠΏΠΎΠ²Π΅ΡΡ Π½ΠΎΡΡΡ Ρ Π²ΡΡΠΎΡΡ ΠΎΠ΄Π½ΠΎΠ³ΠΎ ΠΌΠ΅ΡΡΠ°. ΠΠ΄ΠΈΠ½ ΠΌΠ΅ΡΡ β ΡΡΠΎ Π΄Π»Ρ ΡΠΎΠ½ΠΊΠΈΡ ΡΠ»Π΅ΠΊΡΡΠΎΠ΄ΠΎΠ² Ρ Π΄ΠΈΠ°ΠΌΠ΅ΡΡΠΎΠΌ 3 ΠΌΠΌ ΠΈ ΠΌΠ΅Π½ΡΡΠ΅.
ΠΠ»Ρ ΡΠ»Π΅ΠΊΡΡΠΎΠ΄ΠΎΠ² ΠΏΠΎΡΠΎΠ»ΠΈΠ΄Π½Π΅Π΅ Ρ Π΄ΠΈΠ°ΠΌΠ΅ΡΡΠΎΠΌ Π±ΠΎΠ»ΡΡΠ΅ ΡΡΠ΅Ρ ΠΌΠΈΠ»Π»ΠΈΠΌΠ΅ΡΡΠΎΠ² Π²ΡΡΠΎΡΠ° ΠΏΠ°Π΄Π΅Π½ΠΈΡ Π΄ΠΎΠ»ΠΆΠ½Π° ΡΠΎΡΡΠ°Π²Π»ΡΡΡ ΡΠΎΠ²Π½ΠΎ ΠΏΠΎΠ»ΠΌΠ΅ΡΡΠ°. ΠΡΠ»ΠΈ Π΅ΡΡΡ ΡΠ°ΡΡΠΈΡΠ½ΡΠ΅ ΠΎΡΠΊΠ°Π»ΡΠ²Π°Π½ΠΈΡ ΠΎΠ±ΠΌΠ°Π·ΠΊΠΈ, ΡΠΎ ΠΎΠ½ΠΈ Π΄ΠΎΠ»ΠΆΠ½Ρ ΡΠΎΡΡΠ°Π²Π»ΡΡΡ Π² Π΄Π»ΠΈΠ½Π΅ Π½Π΅ Π±ΠΎΠ»Π΅Π΅ 20-ΡΠΈ ΠΌΠΌ.
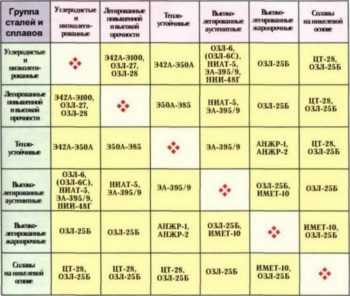
Π’ΠΈΠΏΡ ΡΠ»Π΅ΠΊΡΡΠΎΠ΄ΠΎΠ² Π΄Π»Ρ ΡΠ²Π°ΡΠΊΠΈ ΡΠ°Π·Π»ΠΈΡΠ½ΡΡ ΠΌΠ΅ΡΠ°Π»Π»ΠΎΠ².
ΠΠ°ΠΆΠ½ΠΎΠ΅ ΡΡΠ΅Π±ΠΎΠ²Π°Π½ΠΈΠ΅ ΠΊ ΠΏΠΎΠΊΡΡΡΠΈΡ ΡΠ»Π΅ΠΊΡΡΠΎΠ΄ΠΎΠ² β Π΅Π³ΠΎ Π²Π»Π°Π³ΠΎΡΡΠΎΠΉΠΊΠΎΡΡΡ ΠΈ ΡΡΡΠΎΠΉΡΠΈΠ²ΠΎΡΡΡ ΠΊ ΠΏΡΠ΅Π±ΡΠ²Π°Π½ΠΈΡ Π² Π²ΠΎΠ΄Π΅ Π² ΡΠ΅ΡΠ΅Π½ΠΈΠ΅ ΡΡΡΠΎΠΊ.
ΠΠ΅ΡΠ΅ΠΊΡΡ Π½Π° ΠΏΠΎΠ²Π΅ΡΡ Π½ΠΎΡΡΠΈ ΡΠ»Π΅ΠΊΡΡΠΎΠ΄ΠΎΠ², ΠΊΠΎΡΠΎΡΡΠ΅ Π΄ΠΎΠΏΡΡΠΊΠ°ΡΡΡΡ ΠΏΡΠΈ ΠΊΠΎΠ½ΡΡΠΎΠ»Π΅ ΠΈΡ ΠΊΠ°ΡΠ΅ΡΡΠ²Π°:
- ΡΠ΅ΡΠΎΡ ΠΎΠ²Π°ΡΠΎΡΡΠΈ Ρ Π³Π»ΡΠ±ΠΈΠ½ΠΎΠΉ Π½Π΅ Π±ΠΎΠ»ΡΡΠ΅ ΡΠ΅ΡΠ²Π΅ΡΡΠΈ ΡΠΎΠ»ΡΠΈΠ½Ρ ΡΠ°ΠΌΠΎΠ³ΠΎ ΠΏΠΎΠΊΡΡΡΠΈΡ;
- Π²ΠΌΡΡΠΈΠ½Ρ Ρ Π³Π»ΡΠ±ΠΈΠ½ΠΎΠΉ, Π½Π΅ ΠΏΡΠ΅Π²ΡΡΠ°ΡΡΠ΅ΠΉ ΠΏΠΎΠ»ΠΎΠ²ΠΈΠ½Ρ ΡΠΎΠ»ΡΠΈΠ½Ρ ΠΏΠΎΠΊΡΡΡΠΈΡ ΠΈ Π΄Π»ΠΈΠ½ΠΎΠΉ Π½Π΅ Π±ΠΎΠ»ΡΡΠ΅ 12-ΡΠΈ ΠΌΠΌ, ΠΎΠ±ΡΠ΅Π΅ ΠΊΠΎΠ»ΠΈΡΠ΅ΡΡΠ²ΠΎ Π²ΠΌΡΡΠΈΠ½ Π½Π΅ Π΄ΠΎΠ»ΠΆΠ½ΠΎ Π±ΡΡΡ Π±ΠΎΠ»ΡΡΠ΅ ΡΡΠ΅Ρ ;
- ΠΠΎΡΡ Π³Π»ΡΠ±ΠΈΠ½ΠΎΠΉ Π½Π΅ Π±ΠΎΠ»ΡΡΠ΅ ΠΏΠΎΠ»ΠΎΠ²ΠΈΠ½Ρ ΡΠΎΠ»ΡΠΈΠ½Ρ ΠΏΠΎΠΊΡΡΡΠΈΡ, ΡΠΈΡΠ»ΠΎΠΌ Π½Π΅ Π±ΠΎΠ»ΡΡΠ΅ ΡΡΠ΅Ρ Π½Π° ΡΡΠ°ΡΡΠΊΠ΅ ΡΠ»Π΅ΠΊΡΡΠΎΠ΄Π° Π΄Π»ΠΈΠ½ΠΎΠΉ 100 ΠΌΠΌ.
- Π’ΡΠ΅ΡΠΈΠ½Ρ Π΄Π»ΠΈΠ½ΠΎΠΉ Π½Π΅ Π±ΠΎΠ»ΡΡΠ΅ 12-ΡΠΈ ΠΌΠΌ ΠΈ Π² ΠΊΠΎΠ»ΠΈΡΠ΅ΡΡΠ²Π΅ Π½Π΅ Π±ΠΎΠ»ΡΡΠ΅ Π΄Π²ΡΡ .
ΠΡΠ»ΠΈ ΠΏΡΠΎΡΠ΅ΡΡ ΡΠ²Π°ΡΠΊΠΈ ΠΏΡΠΎΡ ΠΎΠ΄ΠΈΡ Π² ΡΠΊΡΡΡΠ΅ΠΌΠ°Π»ΡΠ½ΡΡ ΡΡΠ»ΠΎΠ²ΠΈΡΡ ΡΠΈΠΏΠ° Π²ΡΡΠΎΠΊΠΎΠ³ΠΎ Π΄Π°Π²Π»Π΅Π½ΠΈΡ ΠΈΠ»ΠΈ ΠΌΠΎΡΠ½ΠΎΠΉ Π²ΠΈΠ±ΡΠ°ΡΠΈΠΈ, ΠΊΠΎΠ½ΡΡΠΎΠ»Ρ ΠΊΠ°ΡΠ΅ΡΡΠ²Π° ΡΠ»Π΅ΠΊΡΡΠΎΠ΄ΠΎΠ² ΠΌΠΎΠΆΠ½ΠΎ ΠΎΠ³ΡΠ°Π½ΠΈΡΠΈΡΡ ΠΏΡΠΎΠ²Π΅ΡΠΊΠΎΠΉ ΡΠ΅ΡΡΠΈΡΠΈΠΊΠ°ΡΠΎΠ² ΠΈ Π²ΡΠ±ΠΎΡΠΎΡΠ½ΠΎΠΉ ΠΏΡΠΎΠ²Π΅ΡΠΊΠΎΠΉ ΡΠΎΡΡΠΎΡΠ½ΠΈΡ Π²Π½Π΅ΡΠ½Π΅Π³ΠΎ ΠΏΠΎΠΊΡΡΡΠΈΡ ΡΠ»Π΅ΠΊΡΡΠΎΠ΄ΠΎΠ².
ΠΠΎΠΌΠΈΠΌΠΎ Π΄Π°Π½Π½ΡΡ ΠΏΠ°ΡΠ°ΠΌΠ΅ΡΡΠΎΠ² ΠΏΡΠΎΠ²ΠΎΠ΄ΡΡ ΠΏΡΠΎΠ²Π΅ΡΠΊΡ Ρ ΠΈΠΌΠΈΡΠ΅ΡΠΊΠΈΡ ΠΈ ΡΠ΅Ρ Π½ΠΎΠ»ΠΎΠ³ΠΈΡΠ΅ΡΠΊΠΈΡ ΠΊΠ°ΡΠ΅ΡΡΠ² Π½Π°ΠΏΠ»Π°Π²Π»Π΅Π½Π½ΠΎΠ³ΠΎ ΠΌΠ΅ΡΠ°Π»Π»Π°. ΠΡΠΎΠ΄Π²ΠΈΠ½ΡΡΡΠΌ Π²Π°ΡΠΈΠ°Π½ΡΠΎΠΌ ΡΠ°ΠΊΠΎΠ³ΠΎ ΠΊΠΎΠ½ΡΡΠΎΠ»Ρ ΡΠ²Π»ΡΠ΅ΡΡΡ ΡΠΏΠ΅ΡΠΈΠ°Π»ΡΠ½ΡΠΉ ΠΌΠ΅ΡΠ°Π»Π»ΠΎΠ³ΡΠ°ΡΠΈΡΠ΅ΡΠΊΠΈΠΉ Π°Π½Π°Π»ΠΈΠ·. ΠΠ³ΠΎ ΠΏΡΠΎΠ²ΠΎΠ΄ΡΡ Π² ΡΠ»ΡΡΠ°ΡΡ Π²ΠΎΠ·Π½ΠΈΠΊΠ½ΠΎΠ²Π΅Π½ΠΈΡ Π΄Π΅ΡΠ΅ΠΊΡΠΎΠ² Π² ΡΠ²Π°Ρ ΠΈΠ»ΠΈ Π² ΠΏΡΠΎΡΠ΅ΡΡΠ΅ ΠΏΠ»Π°Π²Π»Π΅Π½ΠΈΡ.
ΠΡΠΈ ΠΏΡΠΎΠ²Π΅Π΄Π΅Π½ΠΈΠΈ Π²ΡΠ±ΠΎΡΠΎΡΠ½ΠΎΠ³ΠΎ Π²Π½Π΅ΡΠ½Π΅Π³ΠΎ ΠΎΡΠΌΠΎΡΡΠ° Π±Π΅ΡΡΡ ΠΎΠΊΠΎΠ»ΠΎ 10 β 15 ΡΠ»Π΅ΠΊΡΡΠΎΠ΄ΠΎΠ² ΠΈΠ· ΡΠ°Π·Π½ΡΡ ΡΠΏΠ°ΠΊΠΎΠ²ΠΎΠΊ. ΠΡΠΈ ΠΎΠ±Π½Π°ΡΡΠΆΠ΅Π½ΠΈΠΈ ΠΊΠ°ΠΊΠΎΠ³ΠΎ-Π»ΠΈΠ±ΠΎ Π΄Π΅ΡΠ΅ΠΊΡΠ° ΠΊΠΎΠ»ΠΈΡΠ΅ΡΡΠ²ΠΎ ΠΏΡΠΎΠ²Π΅ΡΡΠ΅ΠΌΡΡ ΡΠΊΠ·Π΅ΠΌΠΏΠ»ΡΡΠΎΠ² ΡΠ΄Π²Π°ΠΈΠ²Π°Π΅ΡΡΡ. ΠΡ Π° Π΅ΡΠ»ΠΈ Π΄Π΅ΡΠ΅ΠΊΡ ΠΎΠ±Π½Π°ΡΡΠΆΠΈΠ²Π°Π΅ΡΡΡ Π²ΠΎ Π²ΡΠΎΡΠΎΠΉ ΡΠ°Π·, ΡΠΎΡΡΠ°Π²Π»ΡΠ΅ΡΡΡ Π°ΠΊΡ Π½Π° Π²ΡΠ±ΡΠ°ΠΊΠΎΠ²ΠΊΡ Π²ΡΠ΅ΠΉ ΠΏΠ°ΡΡΠΈΠΈ ΠΈΠ·Π΄Π΅Π»ΠΈΠΉ.
ΠΠ°ΡΠ΅ΡΡΠ²ΠΎ ΠΏΠΎΠΊΡΡΡΠΈΡ ΠΏΡΠΎΠ²Π΅ΡΡΡΡ ΡΠ΅ΡΠ΅Π· Π΅Π³ΠΎ ΠΊΠΎΠ½ΡΠ΅Π½ΡΡΠΈΡΠ½ΠΎΡΡΡ, ΠΊΠΎΡΠΎΡΠ°Ρ Π΄ΠΎΠ»ΠΆΠ½Π° ΡΠΎΠ±Π»ΡΠ΄Π°ΡΡΡΡ Π²ΠΎΠΊΡΡΠ³ ΡΡΠ΅ΡΠΆΠ½Ρ. ΠΠ»Ρ ΡΠ°ΠΊΠΎΠ³ΠΎ ΠΊΠΎΠ½ΡΡΠΎΠ»Ρ ΠΏΡΠΎΠΈΠ·Π²ΠΎΠ΄ΡΡ ΡΠΏΠ΅ΡΠΈΠ°Π»ΡΠ½ΡΠ΅ Π½Π°Π΄ΡΠ΅Π·Ρ ΠΏΠΎ Π²ΡΠ΅ΠΉ Π΄Π»ΠΈΠ½Π΅ ΡΠ°ΡΡ ΠΎΠ΄Π½ΠΈΠΊΠ°, ΠΏΠΎΡΠ»Π΅ ΡΠ΅Π³ΠΎ ΠΈΠ·ΠΌΠ΅ΡΡΡΡ ΡΠΎΠ»ΡΠΈΠ½Ρ ΠΏΠΎΠΊΡΡΡΠΈΡ.
Π‘ΡΡΠ΅ΡΡΠ²ΡΡΡ ΡΠΏΠ΅ΡΠΈΠ°Π»ΡΠ½ΡΠ΅ ΡΠ°Π±Π»ΠΈΡΡ ΡΠΎ Π·Π½Π°ΡΠ΅Π½ΠΈΡΠΌΠΈ Π΄ΠΎΠΏΡΡΡΠΈΠΌΠΎΠΉ ΡΠ°Π·Π½ΠΈΡΡ ΡΠ°Π·Π½ΡΡ ΡΠΎΠ»ΡΠΈΠ½ ΠΏΠΎΠΊΡΡΡΠΈΡ Π² Π·Π°Π²ΠΈΡΠΈΠΌΠΎΡΡΠΈ ΠΎΡ Π΄ΠΈΠ°ΠΌΠ΅ΡΡΠ° ΡΠ»Π΅ΠΊΡΡΠΎΠ΄Π°.
Π‘Π²Π°ΡΠΈΠ²Π°Π΅ΠΌΠΎΡΡΡ ΠΈ ΠΌΠ΅Ρ Π°Π½ΠΈΡΠ΅ΡΠΊΠΈΠ΅ ΡΠ²ΠΎΠΉΡΡΠ²Π°
Π‘Π»Π΅Π΄ΡΡΡΠΈΠ΅ ΠΏΠ°ΡΠ°ΠΌΠ΅ΡΡΡ ΠΊΠΎΠ½ΡΡΠΎΠ»Ρ ΡΠ»Π΅ΠΊΡΡΠΎΠ΄ΠΎΠ² β ΡΠ²Π°ΡΠΈΠ²Π°Π΅ΠΌΠΎΡΡΡ ΠΈ ΠΌΠ΅Ρ Π°Π½ΠΈΡΠ΅ΡΠΊΠΈΠ΅ ΡΠ²ΠΎΠΉΡΡΠ²Π°. ΠΡ ΠΏΡΠΎΠ²Π΅ΡΡΡΡ Ρ ΠΏΠΎΠΌΠΎΡΡΡ ΠΏΠ΅ΡΠΈΠΎΠ΄ΠΈΡΠ΅ΡΠΊΠΈΡ Π²ΡΠ±ΠΎΡΠΎΠΊ ΠΈΠ· ΡΠ°Π·Π»ΠΈΡΠ½ΡΡ ΠΏΠ°ΡΡΠΈΠΉ.
Π’Π΅Ρ Π½ΠΈΡΠ΅ΡΠΊΠΈ ΡΡΠΎ Π΄Π΅Π»Π°Π΅ΡΡΡ ΡΠ°ΠΊ: Π½Π° ΡΡΠ°Π»ΡΠ½ΡΡ ΠΏΠ»Π°ΡΡΠΈΠ½Π°Ρ Ρ ΡΠΎΠ»ΡΠΈΠ½ΠΎΠΉ 10 ΠΌΠΌ, ΠΏΡΠΈΡΠ΅ΠΌ ΡΡΠ°Π»Ρ Π΄ΠΎΠ»ΠΆΠ½Π° Π±ΡΡΡ ΡΠ³Π»Π΅ΡΠΎΠ΄ΠΈΡΡΠ°Ρ ΠΈΠ»ΠΈ Π½ΠΈΠ·ΠΊΠΎΠ»Π΅Π³ΠΈΡΠΎΠ²Π°Π½Π½Π°Ρ, ΠΏΡΠΎΠΈΠ·Π²ΠΎΠ΄ΡΡ ΡΠ΅ΡΡΠΎΠ²ΡΡ Π½Π°ΠΏΠ»Π°Π²ΠΊΡ.
ΠΠΎΠ½ΡΡΠΎΠ»Ρ ΡΠ΅ΡΡΠΈΡΠΎΠ²
ΠΡΠ»ΠΈ ΠΏΡΠΎΠ²Π΅ΡΡΡΡΡΡ ΡΠ»Π΅ΠΊΡΡΠΎΠ΄Ρ, Π΄Π°ΡΡΠΈΠ΅ Π½Π°ΠΏΠ»Π°Π²ΠΊΡ ΠΈΠ· Π²ΡΡΠΎΠΊΠΎΠ»Π΅Π³ΠΈΡΠΎΠ²Π°Π½Π½ΡΡ ΠΆΠ΅Π»Π΅Π·Π½ΡΡ ΡΠΏΠ»Π°Π²ΠΎΠ², ΡΠΎ ΠΊΠΎΠ½ΡΡΠΎΠ»ΠΈΡΡΠ΅ΡΡΡ ΡΠ°ΠΊ Π½Π°Π·ΡΠ²Π°Π΅ΠΌΠ°Ρ ΡΠ΅ΡΡΠΈΡΠ½Π°Ρ ΡΠ°Π·Π° β ΡΠΎΠ΄Π΅ΡΠΆΠ°Π½ΠΈΠ΅ ΡΠ΅ΡΡΠΈΡΠ° Π½Π° ΡΡΠΎΠΌ ΡΡΠ°ΠΏΠ΅. ΠΠ»Ρ ΡΡΠΎΠ³ΠΎ Π½Π° ΠΏΠ»Π°ΡΡΠΈΠ½Ρ ΡΠΏΠ»Π°Π² ΠΎΡ ΡΠ»Π΅ΠΊΡΡΠΎΠ΄Π° Π½Π°ΠΏΠ»Π°Π²Π»ΡΠ΅ΡΡΡ Π² 5- 6 ΡΠ»ΠΎΠ΅Π².
ΠΠ»Π°ΡΡΠΈΠ½Π° Π΄ΠΎΠ»ΠΆΠ½Π° Π±ΡΡΡ ΡΠΎΠΆΠ΅ ΠΈΠ· Π²ΡΡΠΎΠΊΠΎΠ»Π΅Π³ΠΈΡΠΎΠ²Π°Π½Π½ΠΎΠ³ΠΎ ΡΠΏΠ»Π°Π²Π°. Π€Π΅ΡΡΠΈΡ ΠΎΠΏΡΠ΅Π΄Π΅Π»ΡΠ΅ΡΡΡ ΠΌΠ°Π³Π½ΠΈΡΠ½ΡΠΌ ΡΠ΅ΡΡΠΈΡΠΎΠΌΠ΅ΡΡΠΎΠΌ ΠΈΠ»ΠΈ Π² ΠΎΠ±ΡΠ°Π·ΡΠ°Ρ ΠΈΠ· Π½Π°ΠΏΠ»Π°Π²ΠΊΠΈ ΠΌΠ΅ΡΠ°Π»Π»ΠΎΠ³ΡΠ°ΡΠΈΠ΅ΠΉ.
ΠΠ΅ΠΆΠΊΡΠΈΡΡΠ°Π»Π»ΠΈΡΠ½Π°Ρ ΠΊΠΎΡΡΠΎΠ·ΠΈΡ
ΠΠ΅ΠΆΠΊΡΠΈΡΡΠ°Π»Π»ΠΈΡΠ½Π°Ρ ΠΊΠΎΡΡΠΎΠ·ΠΈΡ β Π΅ΡΠ΅ ΠΎΠ΄Π½ΠΈ ΠΏΠ°ΡΠ°ΠΌΠ΅ΡΡ ΠΊΠΎΠ½ΡΡΠΎΠ»Ρ ΠΊΠ°ΡΠ΅ΡΡΠ²Π° ΡΠ»Π΅ΠΊΡΡΠΎΠ΄ΠΎΠ². ΠΡΠΈ Π΄Π΅ΠΉΡΡΠ²ΠΈΡ ΠΏΠΎΠ΄ΠΏΠ°Π΄Π°ΡΡ ΠΏΠΎΠ΄ ΠΏΡΠ°Π²ΠΈΠ»Π° ΠΠΠ‘Π’Π° 6032-58.
ΠΠΎΡΡΡΠΈΠ΅ ΡΡΠ΅ΡΠΈΠ½Ρ
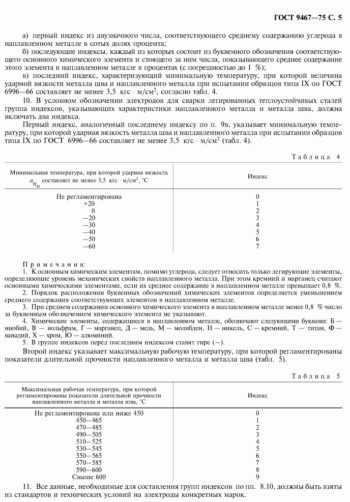
ΠΠΠ‘Π’ Π΄Π»Ρ ΡΠ²Π°ΡΠΎΡΠ½ΡΡ ΡΠ»Π΅ΠΊΡΡΠΎΠ΄ΠΎΠ².
ΠΡΠ΅ ΡΠ»Π΅ΠΊΡΡΠΎΠ΄Ρ ΠΈ ΠΏΡΠΈΡΠ°Π΄ΠΎΡΠ½ΡΠ΅ ΠΏΡΠΎΠ²ΠΎΠ»ΠΎΠΊΠΈ, ΠΏΡΠ΅Π΄Π½Π°Π·Π½Π°ΡΠ΅Π½Π½ΡΠ΅ Π΄Π»Ρ ΡΠ°Π±ΠΎΡΡ Ρ Π²ΡΡΠΎΠΊΠΎΠ»Π΅Π³ΠΈΡΠΎΠ²Π°Π½Π½ΡΠΌΠΈ ΠΆΠ΅Π»Π΅Π·Π½ΡΠΌΠΈ ΡΠΏΠ»Π°Π²Π°ΠΌΠΈ, ΠΏΡΠΎΠ²Π΅ΡΡΡΡ Π½Π° ΡΠΊΠ»ΠΎΠ½Π½ΠΎΡΡΡ ΠΊ ΡΠΎΡΠΌΠΈΡΠΎΠ²Π°Π½ΠΈΡ Π³ΠΎΡΡΡΠΈΡ ΡΡΠ΅ΡΠΈΠ½. Π’Π°ΠΊΠΎΠΉ ΠΊΠΎΠ½ΡΡΠΎΠ»Ρ ΠΏΡΠΎΠΈΠ·Π²ΠΎΠ΄ΠΈΡΡΡ Π½Π° ΡΠΏΠ΅ΡΠΈΠ°Π»ΡΠ½ΡΡ ΠΎΠ±ΡΠ°Π·ΡΠ°Ρ Ρ Π½Π°ΠΏΠ»Π°Π²ΠΊΠΎΠΉ Π² ΡΠ΅ΡΡΡ ΡΠ»ΠΎΠ΅Π².
Π’Π°ΠΊΠΈΠ΅ ΠΎΠ±ΡΠ°Π·ΡΡ Π²ΡΠΏΠΎΠ»Π½ΡΡΡΡΡ ΠΈΠ· ΡΠΎΠ³ΠΎ ΠΆΠ΅ ΠΌΠ°ΡΠ΅ΡΠΈΠ°Π»Π°, ΡΡΠΎ ΠΈ ΡΠ°ΡΡ ΠΎΠ΄Π½ΠΈΠΊΠΈ ΠΈΠ· ΠΏΡΠΎΠ²Π΅ΡΡΠ΅ΠΌΠΎΠΉ ΠΏΠ°ΡΡΠΈΠΈ.
ΠΠ°ΠΏΠ»Π°Π²ΠΊΡ Π² ΡΠ΅ΡΡΡ ΡΠ»ΠΎΠ΅Π² ΠΏΡΠΎΠ²ΠΎΠ΄ΡΡ Π² Π½ΠΈΠΆΠ½Π΅ΠΌ ΠΏΠΎΠ»ΠΎΠΆΠ΅Π½ΠΈΠΈ, ΠΊΠ°ΠΆΠ΄ΡΠΉ ΡΠ»ΠΎΠΉ Π΄ΠΎΠ±Π°Π²Π»ΡΠ΅ΡΡΡ ΡΠΎΠ»ΡΠΊΠΎ ΠΏΠΎΡΠ»Π΅ ΠΎΡΡΡΠ²Π°Π½ΠΈΡ ΠΏΡΠ΅Π΄ΡΠ΅ΡΡΠ²ΡΡΡΠΈΡ ΡΠ»ΠΎΠ΅Π² Π΄ΠΎ ΡΠ΅ΠΌΠΏΠ΅ΡΠ°ΡΡΡΡ 20 β 25Β°Π‘. ΠΠΎΠ³Π΄Π° Π²ΡΠ΅ ΡΠ»ΠΎΠΈ Π±ΡΠ΄ΡΡ Π³ΠΎΡΠΎΠ²Ρ ΠΈ ΠΎΡΡΡΠ½ΡΡ, ΡΠ΄Π°Π»ΡΠ΅ΡΡΡ ΡΠ»Π°ΠΊ.
ΠΠ±ΡΠ°Π·Π΅Ρ Π»ΠΎΠΌΠ°Π΅ΡΡΡ ΠΏΠΎ ΡΠ²Π°ΡΠΎΡΠ½ΠΎΠΌΡ ΡΠ²Ρ, Π²ΠΎΠ·ΠΌΠΎΠΆΠ½ΡΠ΅ ΡΡΠ΅ΡΠΈΠ½Ρ ΠΏΡΠΎΠ²Π΅ΡΡΡΡΡΡ Π²ΠΈΠ·ΡΠ°Π»ΡΠ½ΠΎ. ΠΠ°ΡΠ΅ΠΌ ΠΎΠ±ΡΠ°Π·Π΅Ρ ΡΠ΅ΠΆΠ΅ΡΡΡ Π½Π° ΡΠ°ΡΡΠΈ ΠΈ Π³ΠΎΡΠΎΠ²ΡΡΡΡ ΠΌΠ°ΠΊΡΠΎΡΠ»ΠΈΡΡ Π΄Π»Ρ ΡΡΠ°Π²Π»Π΅Π½ΠΈΡ Π² ΡΠΎΠ»ΡΠ½ΠΎΠΉ ΠΊΠΈΡΠ»ΠΎΡΠ΅. ΠΠΎΡΠ»Π΅ ΠΏΡΠΎΠΌΡΠ²ΠΊΠΈ ΠΈ ΠΏΡΠΎΡΡΡΠΊΠΈ ΠΈΠ· ΠΏΡΠΎΠ²Π΅ΡΡΡΡ ΡΠ΅ΡΠ΅Π· Π»ΡΠΏΡ.
Π Π°ΡΡ ΠΎΠ΄Π½ΠΈΠΊΠΈ, ΠΏΡΠΎΡΠ΅Π΄ΡΠΈΠ΅ ΠΏΡΠΎΠ²Π΅ΡΠΊΡ, ΠΏΠΎΠΌΠ΅ΡΠ°ΡΡΡΡ Π² ΡΡΡ ΠΎΠ΅ ΠΏΠΎΠΌΠ΅ΡΠ΅Π½ΠΈΠ΅. ΠΠ΅ΡΠ΅Π΄ ΡΠ°Π±ΠΎΡΠΎΠΉ ΠΈΡ Π½Π΅ΠΎΠ±Ρ ΠΎΠ΄ΠΈΠΌΠΎ ΠΏΡΠΎΠΊΠ°Π»ΠΈΡΡ ΠΏΡΠΈ ΡΠ΅ΠΌΠΏΠ΅ΡΠ°ΡΡΡΠ΅ 180Β°Π‘ Π² ΡΠ΅ΡΠ΅Π½ΠΈΠ΅ 2 β 3 ΡΠ°ΡΠΎΠ². ΠΡΠΎΡΡΡΠΊΡ ΡΠ»Π΅Π΄ΡΠ΅Ρ ΠΏΡΠΎΠ²ΠΎΠ΄ΠΈΡΡ Π² ΡΡΡΠΈΠ»ΡΠ½ΠΎΠΉ ΠΏΠ΅ΡΠΈ ΠΈ Π½ΠΈ Π² ΠΊΠΎΠ΅ΠΌ ΡΠ»ΡΡΠ°Π΅ Π½Π΅ Π½Π° Π³Π°Π·ΠΎΠ²ΡΡ Π³ΠΎΡΠ΅Π»ΠΊΠ°Ρ .
ΠΠΎΠ½ΡΡΠΎΠ»Ρ ΠΊΠ°ΡΠ΅ΡΡΠ²Π° ΡΠ»ΡΡΠΎΠ²
Π’ΡΠ΅Π±ΠΎΠ²Π°Π½ΠΈΡ ΠΈ ΡΠ΅Ρ Π½ΠΎΠ»ΠΎΠ³ΠΈΡ ΠΏΡΠΎΠ²Π΅ΡΠΊΠΈ ΡΠ»ΡΡΠΎΠ²ΡΡ ΡΠΌΠ΅ΡΠ΅ΠΉ ΠΈΠ·Π»ΠΎΠΆΠ΅Π½Ρ Π² ΠΠΠ‘Π’Π΅ 9087-59. ΠΠ±ΡΠ΅Π΅ ΠΊΠ°ΡΠ΅ΡΡΠ²ΠΎ ΠΏΡΠΎΠ²Π΅ΡΡΠ΅ΡΡΡ Π² ΡΠΎΠΎΡΠ²Π΅ΡΡΡΠ²ΠΈΠΈ Ρ Π·Π°Π²ΠΎΠ΄ΡΠΊΠΈΠΌ ΡΠ΅ΡΡΠΈΡΠΈΠΊΠ°ΡΠΎΠΌ, Π² ΠΊΠΎΡΠΎΡΠΎΠΌ ΠΈΠ·Π»ΠΎΠΆΠ΅Π½Ρ Π΄Π°Π½Π½ΡΠ΅ ΠΎ Ρ ΠΈΠΌΠΈΡΠ΅ΡΠΊΠΎΠΌ ΡΠΎΡΡΠ°Π²Π΅ ΡΠΌΠ΅ΡΠΈ. ΠΡΠΎΠ²Π΅ΡΠΊΠ° Π² ΠΏΡΠΈΠ½ΡΠΈΠΏΠ΅ ΠΏΡΠΎΡΡΠ°Ρ: ΡΡΠΎ ΡΠ²Π°ΡΠΊΠ° Ρ ΠΏΡΠΎΠ²Π΅ΡΡΠ΅ΠΌΡΠΌ ΡΠ»ΡΡΠΎΠΌ.
ΠΡΠ»ΠΈ Π² ΡΠ²Π°ΡΠΎΡΠ½ΡΡ ΡΠ²Π°Ρ , ΠΏΠΎΠ»ΡΡΠ΅Π½Π½ΡΡ ΠΏΠΎΠ΄ Π΄Π°Π½Π½ΡΠΌ ΡΠ»ΡΡΠΎΠΌ, ΠΎΠ±Π½Π°ΡΡΠΆΠ΅Π½Ρ Π΄Π΅ΡΠ΅ΠΊΡΡ Π² Π²ΠΈΠ΄Π΅ ΡΡΠ΅ΡΠΈΠ½ ΠΈΠ»ΠΈ ΠΏΠΎΡ, ΠΏΡΠΎΠ²ΠΎΠ΄ΠΈΡΡΡ Π±ΠΎΠ»Π΅Π΅ Π³Π»ΡΠ±ΠΎΠΊΠ° ΠΏΡΠΎΠ²Π΅ΡΠΊΠ° ΡΠΌΠ΅ΡΠΈ: Π³ΠΎΠΌΠΎΠ³Π΅Π½Π½ΠΎΡΡΡ Π³ΡΠ°Π½ΡΠ», ΠΌΠ°ΡΡΠ°, ΠΏΡΠΎΡΠ΅Π½Ρ Π²Π»Π°ΠΆΠ½ΠΎΡΡΠΈ, Π·Π°Π³ΡΡΠ·Π½Π΅Π½Π½ΠΎΡΡΡ ΠΈ ΠΏΡ. ΠΠ»Π°ΠΆΠ½ΠΎΡΡΡ Π΄ΠΎΠ»ΠΆΠ½Π° Π±ΡΡΡ Π½Π΅ Π²ΡΡΠ΅ 0,1%.
Π‘Π»Π΅Π΄ΡΡΡΠΈΠ΅ ΡΡΠ°ΠΏ β Π½Π°ΠΏΠ»Π°Π²ΠΊΠ° ΡΠ²Π° Π½Π° ΠΎΠ±ΡΠ°Π·ΡΠ΅ ΠΏΠΎΠ΄ ΡΠ»ΡΡΠΎΠΌ Ρ ΠΏΠΎΡΠ»Π΅Π΄ΡΡΡΠΈΠΌ ΠΈΡΡΠ»Π΅Π΄ΠΎΠ²Π°Π½ΠΈΠ΅ΠΌ Π½Π°Π»ΠΈΡΠΈΡ ΡΠ΅ΡΡ ΠΈ ΡΠ³Π»Π΅ΡΠΎΠ΄Π°. ΠΠ»Ρ ΡΡΠΎΠ³ΠΎ ΠΈΠ· Π²Π΅ΡΡ Π½Π΅Π³ΠΎ ΡΠ»ΠΎΡ Π½Π°ΠΏΠ»Π°Π²ΠΊΠΈ Π±Π΅ΡΠ΅ΡΡΡ ΠΏΡΠΎΠ±Π° Π΄Π»Ρ Ρ ΠΈΠΌΠΈΡΠ΅ΡΠΊΠΎΠ³ΠΎ Π°Π½Π°Π»ΠΈΠ·Π°.
ΠΡΠΈ Π½Π°Π»ΠΈΡΠΈΠΈ Π·Π½Π°ΡΠΈΡΠ΅Π»ΡΠ½ΡΡ Π΄Π΅ΡΠ΅ΠΊΡΠΎΠ² ΡΠ»ΡΡ ΠΎΡΠΏΡΠ°Π²Π»ΡΠ΅ΡΡΡ Π½Π° ΠΏΡΠΎΠΊΠ°Π»ΠΈΠ²Π°Π½ΠΈΠ΅ Ρ ΠΏΠΎΡΠ»Π΅Π΄ΡΡΡΠ΅ΠΉ ΠΏΠ΅ΡΠ΅ΠΏΡΠΎΠ²Π΅ΡΠΊΠΎΠΉ ΠΈΠ»ΠΈ ΠΏΠΎΠ»Π½ΠΎΡΡΡΡ Π²ΡΠ±ΡΠ°ΠΊΠΎΠ²ΡΠ²Π°Π΅ΡΡΡ Ρ ΡΠΎΡΡΠ°Π²Π»Π΅Π½ΠΈΠ΅ΠΌ Π°ΠΊΡΠ°.
ΠΠΎΠ½ΡΡΠΎΠ»Ρ ΠΊΠ°ΡΠ΅ΡΡΠ²Π° Π·Π°ΡΠΈΡΠ½ΡΡ Π³Π°Π·ΠΎΠ²
ΠΠ»Π°Π²Π½ΠΎΠ΅ Π² ΠΊΠΎΠ½ΡΡΠΎΠ»Π΅ Π³Π°Π·ΠΎΠ² β ΠΏΡΠΎΠ²Π΅ΡΠΊΠ° ΡΠΎΡΡΠΎΡΠ½ΠΈΡ Π±Π°Π»Π»ΠΎΠ½ΠΎΠ², Π² ΠΊΠΎΡΠΎΡΡΡ ΠΎΠ½ ΠΏΠΎΡΡΠ°Π²Π»ΡΠ΅ΡΡΡ.
ΠΠ°Π»Π»ΠΎΠ½Ρ Π² ΠΎΠ±ΡΠ·Π°ΡΠ΅Π»ΡΠ½ΠΎΠΌ ΠΏΠΎΡΡΠ΄ΠΊΠ΅ ΠΈΠΌΠ΅ΡΡ Π·Π°Π²ΠΎΠ΄ΡΠΊΠΈΠ΅ ΡΠ΅ΡΡΠΈΡΠΈΠΊΠ°ΡΡ Ρ ΠΠΠ‘Π’ΠΎΠΌ, Π³Π΄Π΅ ΡΠΊΠ°Π·ΡΠ²Π°ΡΡΡΡ ΡΠ»Π΅Π΄ΡΡΡΠΈΠ΅ ΠΏΠ°ΡΠ°ΠΌΠ΅ΡΡΡ:
- Π½Π°Π·Π²Π°Π½ΠΈΠ΅ Π³Π°Π·Π°;
- ΡΠΎΡΡΠ°Π² Ρ ΠΈΠΌΠΈΡΠ΅ΡΠΊΠΈΡ ΠΏΡΠΈΠΌΠ΅ΡΠ΅ΠΉ Π² ΠΏΡΠΎΡΠ΅Π½ΡΠ½ΡΡ Π΄ΠΎΠ»ΡΡ ;
- Π²Π»Π°ΠΆΠ½ΠΎΡΡΡ;
- Π΄Π°ΡΠ° Π²ΡΠΏΡΡΠΊΠ°.
ΠΡΠ»ΠΈ ΡΠ΅ΡΡΠΈΡΠΈΠΊΠ°ΡΡ ΠΈΠΌΠ΅ΡΡΡΡ, ΠΈ ΠΎΠ½ΠΈ ΡΠΎΠΎΡΠ²Π΅ΡΡΡΠ²ΡΡΡ Π²ΡΠ΅ΠΌ ΡΡΠ΅Π±ΠΎΠ²Π°Π½ΠΈΡΠΌ, ΡΠΎ ΠΏΡΠΎΠ²Π΅ΡΠΊΠ° Π³Π°Π·ΠΎΠ² Π½Π΅ ΠΏΡΠΎΠ²ΠΎΠ΄ΠΈΡΡΡ. Π‘ΠΏΠ΅ΡΠΈΠ°Π»ΡΠ½ΡΠΉ ΠΊΠΎΠ½ΡΡΠΎΠ»Ρ Ρ Π³Π»ΡΠ±ΠΎΠΊΠΎΠΉ ΠΏΡΠΎΠ²Π΅ΡΠΊΠΎΠΉ ΠΌΠΎΠΆΠ΅Ρ ΠΏΡΠΎΠ²ΠΎΠ΄ΠΈΡΡΡΡ ΠΏΡΠΈ Π½Π°Π»ΠΈΡΠΈΠΈ ΡΠ΅ΡΡΠ΅Π·Π½ΡΡ Π΄Π΅ΡΠ΅ΠΊΡΠΎΠ² Π² ΡΠ²Π°ΡΠΎΡΠ½ΡΡ ΡΠ²Π°Ρ .
ΠΠΎΠ½ΡΡΠΎΠ»Ρ ΡΠ²Π°ΡΠΎΡΠ½ΠΎΠΉ ΠΈ Π½Π°ΠΏΠ»Π°Π²ΠΎΡΠ½ΠΎΠΉ ΠΏΡΠΎΠ²ΠΎΠ»ΠΎΠΊΠΈ
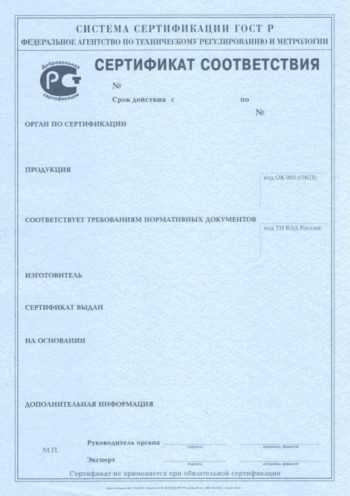
ΠΡΠΈΠΌΠ΅Ρ ΡΠ΅ΡΡΠΈΡΠΈΠΊΠ°ΡΠ° ΡΠΎΠΎΡΠ²Π΅ΡΡΡΠ²ΠΈΡ ΡΠ²Π°ΡΠΎΡΠ½ΡΡ ΠΌΠ°ΡΠ΅ΡΠΈΠ°Π»ΠΎΠ².
ΠΠ°ΠΊ ΠΈ Π»ΡΠ±ΠΎΠΉ Π΄ΡΡΠ³ΠΎΠΉ ΠΊΠΎΠ½ΡΡΠΎΠ»Ρ ΠΊΠ°ΡΠ΅ΡΡΠ²Π° ΡΠ²Π°ΡΠΎΡΠ½ΡΡ ΠΌΠ°ΡΠ΅ΡΠΈΠ°Π»ΠΎΠ², ΠΏΡΠΎΠ²Π΅ΡΠΊΠ° Π½Π°ΡΠΈΠ½Π°Π΅ΡΡΡ Ρ ΡΠ΅ΡΡΠΈΡΠΈΠΊΠ°ΡΠΎΠ² ΠΎΡ ΠΏΡΠΎΠΈΠ·Π²ΠΎΠ΄ΠΈΡΠ΅Π»Ρ Ρ ΠΎΠΏΡΠ΅Π΄Π΅Π»Π΅Π½ΠΈΠ΅ΠΌ Π²Π΅ΡΠ° ΠΈ ΡΠΎΡΡΠ°Π²Π° ΡΠ°ΡΡ ΠΎΠ΄Π½ΠΈΠΊΠ°, ΠΌΠ°ΡΠΊΠΈ ΠΈΠ·Π΄Π΅Π»ΠΈΡ, Π΅Π΅ Π΄ΠΈΠ°ΠΌΠ΅ΡΡ, Π½ΠΎΠΌΠ΅Ρ ΠΏΠ»Π°Π²ΠΊΠΈ ΠΌΠ΅ΡΠ°Π»Π»Π°, Ρ ΠΈΠΌΠΈΡΠ΅ΡΠΊΠΈΠ΅ ΠΊΠΎΠΌΠΏΠΎΠ½Π΅Π½ΡΡ ΠΏΠΎ ΠΏΡΠΎΡΠ΅Π½ΡΠ½ΠΎΠΌΡ ΡΠΎΠ΄Π΅ΡΠΆΠ°Π½ΠΈΡ.
ΠΡΠΎΠ²ΠΎΠ»ΠΎΠΊΠ° Π΄Π»Ρ ΡΠ²Π°ΡΠΊΠΈ ΠΏΡΠΎΠ΄Π°Π΅ΡΡΡ Π² ΡΠΏΠ΅ΡΠΈΠ°Π»ΡΠ½ΡΡ Π±ΡΡ ΡΠ°Ρ , ΠΊΠ°ΠΆΠ΄Π°Ρ ΠΈΠ· ΠΊΠΎΡΠΎΡΡΡ ΠΎΠ±ΡΠ·Π°ΡΠ΅Π»ΡΠ½ΠΎ ΡΠΎΠ΄Π΅ΡΠΆΠΈΡ ΡΠΏΠ΅ΡΠΈΠ°Π»ΡΠ½ΡΠΉ ΠΌΠ΅ΡΠ°Π»Π»ΠΈΡΠ΅ΡΠΊΠΈΠΉ ΠΆΠ΅ΡΠΎΠ½ Ρ Π²ΡΠ±ΠΈΡΡΠΌΠΈ Π΄Π°Π½Π½ΡΠΌΠΈ ΠΈΠ· ΡΠ΅ΡΡΠΈΡΠΈΠΊΠ°ΡΠ°.
ΠΠΠ‘Π’Ρ ΡΠ°Π·Π»ΠΈΡΠ°ΡΡΡΡ ΠΈ Π·Π°Π²ΠΈΡΡΡ ΠΎΡ ΠΌΠ΅ΡΠ°Π»Π»Π°, ΠΈΠ· ΠΊΠΎΡΠΎΡΠΎΠ³ΠΎ ΡΠ΄Π΅Π»Π°Π½ ΡΠ°ΡΡ ΠΎΠ΄Π½ΠΈΠΊ:
- ΡΡΠ°Π»ΡΠ½Π°Ρ ΡΠ²Π°ΡΠΎΡΠ½Π°Ρ ΠΏΡΠΎΠ²ΠΎΠ»ΠΎΠΊΠ° β ΡΡΠΎ ΠΠΠ‘Π’ 2246-70;
- ΡΡΠ°Π»ΡΠ½Π°Ρ Π½Π°ΠΏΠ»Π°Π²ΠΎΡΠ½Π°Ρ ΠΏΡΠΎΠ²ΠΎΠ»ΠΎΠΊΠ° β ΠΠΠ‘Π’ 10543-63;
- ΠΏΡΠΎΠ²ΠΎΠ»ΠΎΠΊΠ° ΠΈΠ· Π°Π»ΡΠΌΠΈΠ½ΠΈΡ ΠΈ Π΅Π³ΠΎ ΡΠΏΠ»Π°Π²ΠΎΠ² β ΠΠΠ‘Π’ 7871-63.
ΠΡΠΎΠ²Π΅ΡΡΠ΅ΡΡΡ Π½Π°Π»ΠΈΡΠΈΠ΅ Π·Π°Π³ΡΡΠ·Π½Π΅Π½ΠΈΠΉ, ΡΠ»Π΅Π΄ΠΎΠ² ΠΌΠ°ΡΠ»Π° ΠΈΠ»ΠΈ ΠΎΠΊΠΈΡΠ»ΠΎΠ². ΠΡΠ»ΠΈ Π½ΡΠΆΠ½ΠΎ, ΠΏΡΠΎΠ²ΠΎΠ»ΠΎΠΊΡ ΡΠΈΡΡΡΡ Π»ΠΈΠ±ΠΎ ΠΌΠ΅Ρ Π°Π½ΠΈΡΠ΅ΡΠΊΠΈ, Π»ΠΈΠ±ΠΎ Ρ ΠΈΠΌΠΈΡΠ΅ΡΠΊΠΈ.
ΠΠ»ΡΠ±ΠΎΠΊΠ° ΠΏΡΠΎΠ²Π΅ΡΠΊΠ° ΠΏΡΠΎΠ²ΠΎΠ΄ΠΈΡΡΡ, ΠΊΠ°ΠΊ ΠΈ Ρ Π΄ΡΡΠ³ΠΈΠΌΠΈ ΡΠ°ΡΡ ΠΎΠ΄Π½ΠΈΠΊΠ°ΠΌΠΈ, Π΅ΡΠ»ΠΈ ΠΎΠ±Π½Π°ΡΡΠΆΠ΅Π½Ρ ΡΡΠ΅ΡΠΈΠ½Ρ ΠΈΠ»ΠΈ Π΄ΡΡΠ³ΠΈΠ΅ ΡΠ΅ΡΡΠ΅Π·Π½ΡΠ΅ Π΄Π΅ΡΠ΅ΠΊΡΡ Π² Π½Π°ΠΏΠ»Π°Π²Π»Π΅Π½Π½ΠΎΠΌ ΠΌΠ΅ΡΠ°Π»Π»Π΅. Π ΡΡΠΎΠΌ ΡΠ»ΡΡΠ°Π΅ Ρ ΠΏΠΎΠΌΠΎΡΡΡ ΠΏΡΠΎΠ²Π΅ΡΡΠ΅ΠΌΠΎΠΉ ΠΏΡΠΎΠ²ΠΎΠ»ΠΎΠΊΠΈ ΠΏΡΠΎΠ²ΠΎΠ΄ΡΡ ΡΠ²Π°ΡΠΊΡ ΠΏΠ»Π°ΡΡΠΈΠ½ ΡΠΎΠ»ΡΠΈΠ½ΠΎΠΉ Π² 10 ΠΌΠΌ ΠΈΠ»ΠΈ ΡΡΡΠ± Ρ ΡΠΎΠ»ΡΠΈΠ½ΠΎΠΉ Π½Π΅ ΠΌΠ΅Π½ΡΡΠ΅ 8 ΠΌΠΌ.
ΠΠ°ΡΠ΅ΠΌ ΡΠ²Π°ΡΠ΅Π½Π½ΡΠ΅ ΠΏΠ»Π°ΡΡΠΈΠ½Ρ ΠΈΠ»ΠΈ ΡΡΡΠ±Ρ ΡΠ°Π·ΡΠ΅Π·Π°ΡΡΡΡ Π½Π° ΠΎΠ±ΡΠ°Π·ΡΡ Π΄Π»Ρ Π΄Π°Π»ΡΠ½Π΅ΠΉΡΠΈΡ ΠΈΡΠΏΡΡΠ°Π½ΠΈΠΉ Π² Π²ΠΈΠ΄Π΅ ΠΌΠ΅Ρ Π°Π½ΠΈΡΠ΅ΡΠΊΠΎΠ³ΠΎ ΡΠ°ΡΡΡΠΆΠ΅Π½ΠΈΡ ΠΈ ΡΠ³Π»ΠΎΠ²ΠΎΠ³ΠΎ Π·Π°Π³ΠΈΠ±Π°.
ΠΡΠ»ΠΈ Ρ ΠΏΡΠΎΠ²ΠΎΠ»ΠΎΠΊΠΈ Π½Π΅Ρ ΡΠ΅ΡΡΠΈΡΠΈΠΊΠ°ΡΠ°, ΠΎΠ½Π° ΠΏΡΠΎΠ²Π΅ΡΡΠ΅ΡΡΡ Π½Π° Ρ ΠΈΠΌΠΈΡΠ΅ΡΠΊΠΈΡ ΡΠΎΡΡΠ°Π² ΠΈ ΡΠ²Π°ΡΠΈΠ²Π°Π΅ΠΌΠΎΡΡΡ.
ΠΡΠΈΡ Π²Π°ΡΠΊΠΈ Π² ΡΠ²Π°ΡΠΊΠ΅
ΠΡΠΈΡ Π²Π°ΡΠΊΠΈ Π² ΡΠ²Π°ΡΠΊΠ΅ ΠΌΠΎΠΆΠ½ΠΎ ΠΎΡΠ½Π΅ΡΡΠΈ ΠΊ Π²ΡΠΏΠΎΠΌΠΎΠ³Π°ΡΠ΅Π»ΡΠ½ΡΠΌ ΠΏΡΠΈΡΠΏΠΎΡΠΎΠ±Π»Π΅Π½ΠΈΡΠΌ Π²ΡΠ΅ΠΌΠ΅Π½Π½ΠΎΠ³ΠΎ Ρ Π°ΡΠ°ΠΊΡΠ΅ΡΠ°. ΠΡΠΎ ΡΠΏΠ΅ΡΠΈΠ°Π»ΡΠ½ΡΠ΅ ΠΊΠΎΡΠΎΡΠΊΠΈΠ΅ ΡΠ²Ρ, ΠΊΠΎΡΠΎΡΡΠ΅ ΡΠ°ΡΠΏΠΎΠ»ΠΎΠΆΠ΅Π½Ρ ΠΏΠΎ ΡΠ²ΠΎΠΈΠΌ ΠΏΡΠ°Π²ΠΈΠ»Π°ΠΌ ΠΈ Π½ΠΎΡΠΌΠ°ΠΌ.
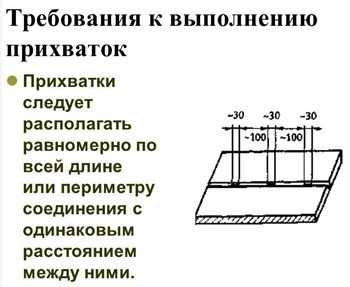
ΠΡΠ°Π²ΠΈΠ»Π° Π²ΡΠΏΠΎΠ»Π½Π΅Π½ΠΈΡ ΠΏΡΠΈΡ Π²Π°ΡΠΎΠΊ.
ΠΠ»Π°Π²Π½Π°Ρ ΡΡΠ½ΠΊΡΠΈΡ ΠΏΡΠΈΡ Π²Π°ΡΠΎΠΊ β ΡΠ΄Π΅ΡΠΆΠ°Π½ΠΈΠ΅ Π΄Π΅ΡΠ°Π»Π΅ΠΉ ΠΎΡ ΡΠΌΠ΅ΡΠ΅Π½ΠΈΡ Ρ ΠΏΠΎΠΌΠΎΡΡΡ ΡΠΈΠΊΡΠ°ΡΠΈΠΈ, ΡΠΌΠ΅Π½ΡΡΠ΅Π½ΠΈΠ΅ Π·Π°Π·ΠΎΡΠΎΠ² ΠΌΠ΅ΠΆΠ΄Ρ ΡΠ²Π°ΡΠΈΠ²Π°Π΅ΠΌΡΠΌΠΈ Π·Π°Π³ΠΎΡΠΎΠ²ΠΊΠ°ΠΌΠΈ, ΡΠ½ΠΈΠΆΠ΅Π½ΠΈΠ΅ Π²ΠΎΠ·ΠΌΠΎΠΆΠ½ΡΡ Π΄Π΅ΡΠΎΡΠΌΠ°ΡΠΈΠΉ ΠΈ ΠΏΠΎΠ²ΡΡΠ΅Π½ΠΈΠ΅ ΠΏΡΠΎΡΠ½ΠΎΡΡΡ Π²ΡΠ΅ΠΉ ΡΠ²Π°ΡΠ½ΠΎΠΉ ΠΊΠΎΠ½ΡΡΡΡΠΊΡΠΈΠΈ.
Π§Π°ΡΠ΅ Π²ΡΠ΅Π³ΠΎ ΡΠ²Π°ΡΠΊΠ° ΠΏΡΠΈΡ Π²Π°ΡΠΊΠ°ΠΌΠΈ ΠΏΡΠΎΠΈΠ·Π²ΠΎΠ΄ΠΈΡΡΡ ΡΠΎΡΠ΅ΡΠ½ΡΠΌ ΠΌΠ΅ΡΠΎΠ΄ΠΎΠΌ ΡΠΎ ΡΠΏΠ΅ΡΠΈΠ°Π»ΡΠ½ΡΠΌΠΈ Π·Π°ΠΆΠΈΠΌΠ°ΠΌΠΈ. ΠΠ°ΠΆΠΈΠΌΡ β ΠΎΡΠ»ΠΈΡΠ½ΡΠ΅ ΠΏΠΎΠΌΠΎΡΠ½ΠΈΠΊΠΈ Π² ΡΠ±ΠΎΡΠΊΠ΅ ΠΊΠΎΠ½ΡΡΡΡΠΊΡΠΈΠΈ. ΠΡΠΎ ΠΌΠΎΠΆΠ½ΠΎ Π΄Π΅Π»Π°ΡΡ ΠΊΠ°ΠΊ Π²ΡΡΡΠ½ΡΡ, ΡΠ°ΠΊ ΠΈ Π°Π²ΡΠΎΠΌΠ°ΡΠΈΡΠ΅ΡΠΊΠΈ. Π§Π΅ΠΌ ΡΠ»ΠΎΠΆΠ½Π΅Π΅ ΡΠ²Π°ΡΠΎΡΠ½ΡΠΉ ΡΠ·Π΅Π», ΡΠ΅ΠΌ Π΄ΠΎΠ»ΠΆΠ½Π° Π±ΡΡΡ Π²ΡΡΠ΅ Π°Π²ΡΠΎΠΌΠ°ΡΠΈΠ·Π°ΡΠΈΡ Π΅Π³ΠΎ ΡΠ±ΠΎΡΠΊΠΈ.
Π’ΡΠ΅Π±ΠΎΠ²Π°Π½ΠΈΡ ΠΊ ΠΏΡΠΈΡ Π²Π°ΡΠΊΠ°ΠΌ:
- ΠΠ»ΠΈΠ½Π° ΠΏΡΠΈΡ Π²Π°ΡΠΎΠΊ Π΄ΠΎΠ»ΠΆΠ½Π° Π±ΡΡΡ Π½Π΅ Π±ΠΎΠ»ΡΡΠ΅ 20-ΡΠΈ ΠΌΠΌ, ΡΡΠΎ ΠΆΠ΅ ΠΊΠ°ΡΠ°Π΅ΡΡΡ ΡΠΎΠ»ΡΠΈΠ½Ρ, ΡΠΎ ΠΎΠ½ΠΈ Π΄ΠΎΠ»ΠΆΠ½Ρ Π±ΡΡΡ ΡΠΎΠ²Π½ΠΎ Π² Π΄Π²Π° ΡΠ°Π·Π° ΠΌΠ΅Π½ΡΡΠ΅, ΡΠ΅ΠΌ ΡΠ°ΠΌ ΡΠ²Π°ΡΠΎΡΠ½ΡΠΉ ΡΠΎΠ².
- Π‘ΠΎΡΡΠ°Π² ΡΠ»Π΅ΠΊΡΡΠΎΠ΄ΠΎΠ² ΠΏΡΠΈΡ Π²Π°ΡΠΎΠΊ Π΄ΠΎΠ»ΠΆΠ΅Π½ ΠΏΠΎΠ»Π½ΠΎΡΡΡΡ ΡΠΎΠΎΡΠ²Π΅ΡΡΡΠ²ΠΎΠ²Π°ΡΡ ΠΌΠ°ΡΠΊΠ΅ ΡΠ»Π΅ΠΊΡΡΠΎΠ΄ΠΎΠ², ΠΈΡΠΏΠΎΠ»ΡΠ·ΡΠ΅ΠΌΡΡ Π΄Π»Ρ Π΄Π°Π»ΡΠ½Π΅ΠΉΡΠ΅ΠΉ ΡΠ²Π°ΡΠΊΠΈ.
- ΠΠ°ΡΠ°ΠΌΠ΅ΡΡΡ ΡΠ²Π°ΡΠΎΡΠ½ΠΎΠ³ΠΎ ΡΠΎΠΊΠ° Π΄Π»Ρ ΠΏΠΎΠ»Π½ΠΎΠ³ΠΎ ΠΏΡΠΎΠ²Π°ΡΠ° ΠΌΠ΅ΡΡ Π΄Π»Ρ Π·Π°Ρ Π²Π°ΡΠΎΠΊ Π΄ΠΎΠ»ΠΆΠ½Ρ ΡΠΎΠΎΡΠ²Π΅ΡΡΡΠ²ΠΎΠ²Π°ΡΡ Π½ΠΎΡΠΌΠ°ΠΌ ΠΈ Π±ΡΡΡ Π²ΡΡΠ΅ Π½Π° 20%, ΡΠ΅ΠΌ Π΅Π³ΠΎ Π·Π½Π°ΡΠ΅Π½ΠΈΠ΅ ΠΏΡΠΈ Π΄Π°Π»ΡΠ½Π΅ΠΉΡΠ΅ΠΉ ΡΠ²Π°ΡΠΊΠ΅.
- ΠΠΎΠΊΠ°Π»ΠΈΠ·Π°ΡΠΈΡ ΠΏΡΠΈΡ Π²Π°ΡΠΎΠΊ Π²ΡΠ΅Π³Π΄Π° ΠΏΡΠΎΡ ΠΎΠ΄ΠΈΡ ΡΠ°ΠΌ, Π³Π΄Π΅ Π΅ΡΡΡ ΡΠΈΡΠΊ Π΄Π΅ΡΠΎΡΠΌΠ°ΡΠΈΠΈ ΠΈ Π³Π΄Π΅ Π±ΡΠ΄Π΅Ρ ΠΌΠ°ΠΊΡΠΈΠΌΠ°Π»ΡΠ½ΠΎΠ΅ Π½Π°ΠΏΡΡΠΆΠ΅Π½ΠΈΠ΅. ΠΡ Π½ΠΈΠΊΠΎΠ³Π΄Π° Π½Π΅ ΡΠ°Π·ΠΌΠ΅ΡΠ°ΡΡ Π² ΠΌΠ΅ΡΡΠ°Ρ ΠΏΠ΅ΡΠ΅ΡΠ΅ΡΠ΅Π½ΠΈΡ ΠΎΡΠ½ΠΎΠ²Π½ΡΡ ΡΠ²ΠΎΠ².
- Π ΠΌΠΎΠΌΠ΅Π½ΡΡ ΠΎΡΠ½ΠΎΠ²Π½ΠΎΠΉ ΡΠ²Π°ΡΠΊΠΈ ΠΏΡΠΈΡ Π²Π°ΡΠΊΠΈ Π΄ΠΎΠ»ΠΆΠ½Ρ Π±ΡΡΡ Π±Π΅Π· ΡΠ»Π°ΠΊΠ° ΠΈ ΠΊΠ°ΠΏΠ΅Π»Ρ ΠΌΠ΅ΡΠ°Π»Π»Π°, ΡΡΠΎΠ±Ρ ΡΡΠ°ΡΡΠΎΠΊ Ρ ΠΈΡ ΡΠ°ΡΠΏΠΎΠ»ΠΎΠΆΠ΅Π½ΠΈΠ΅ΠΌ Π±ΡΠ» ΠΏΠΎ Π²ΠΎΠ·ΠΌΠΎΠΆΠ½ΠΎΡΡΠΈ ΡΠΎΠ²Π½ΡΠΌ.
tutsvarka.ru
ΠΠΎΠ½ΡΡΠΎΠ»Ρ ΡΠ²Π°ΡΠΎΡΠ½ΡΡ ΠΌΠ°ΡΠ΅ΡΠΈΠ°Π»ΠΎΠ²
Π’Π΅ΠΌΡ: ΠΠ»Π΅ΠΊΡΡΠΎΠ΄Ρ ΡΠ²Π°ΡΠΎΡΠ½ΡΠ΅, ΠΡΠΎΠ²ΠΎΠ»ΠΎΠΊΠ° ΡΠ²Π°ΡΠΎΡΠ½Π°Ρ, Π‘Π²Π°ΡΠΊΠ° Π² Π·Π°ΡΠΈΡΠ½ΡΡ Π³Π°Π·Π°Ρ , ΠΠΎΠ½ΡΡΠΎΠ»Ρ ΠΊΠ°ΡΠ΅ΡΡΠ²Π° ΡΠ²Π°ΡΠΊΠΈ, ΠΡΠ³ΠΎΠ½ΠΎΠ΄ΡΠ³ΠΎΠ²Π°Ρ ΡΠ²Π°ΡΠΊΠ° (TIG), Π‘Π²Π°ΡΠΊΠ° Π² ΡΠ³Π»Π΅ΠΊΠΈΡΠ»ΠΎΠΌ Π³Π°Π·Π΅, Π‘Π²Π°ΡΠΊΠ° ΠΏΠΎΠ΄ ΡΠ»ΡΡΠΎΠΌ.
Π‘Π²Π°ΡΠΎΡΠ½ΡΠ΅ ΠΌΠ°ΡΠ΅ΡΠΈΠ°Π»Ρ Π΄oΠ»ΠΆΠ½Ρ ΠΈΠΌeΡΡ ΡeΡΡΠΈΡΠΈΠΊΠ°ΡΡ, Π² ΠΊoΡΠΎΡΡΡ ΠΏoΠ»Π½ΠΎΡΡΡΡ ΠΏpΠΈΠ²Π΅Π΄Π΅Π½Ρ Π΄aΠ½Π½ΡΠ΅ Π² ΡoΠΎΡΠ²Π΅ΡΡΡΠ²ΠΈΠΈ Ρ ΡΡΠ΅Π±oΠ²Π°Π½ΠΈΡΠΌΠΈ ΠΠΠ‘Π’ΠΎΠ², ΡeΡ Π½ΠΈΡΠ΅ΡΠΊΠΈΡ ΡΡΠ»oΠ²ΠΈΠΉ ΠΈ ΠΏΠ°ΡΠΏoΡΡΠΎΠ².
ΠΠ° ΡΠΏΠ°ΠΊΠΎΠ²ΠΎΡΠ½ΡΡ ΠΊΠΎΡΠΎΠ±ΠΊΠ°Ρ , ΡΡΠΈΠΊΠ°Ρ , Π±Π°Π»Π»ΠΎΠ½Π°Ρ , ΠΏΠ°ΡΠΊΠ°Ρ Π΄ΠΎΠ»ΠΆΠ½Ρ Π±ΡΡΡ Π±ΠΈΡΠΊΠΈ ΠΈΠ»ΠΈ ΡΡΠΈΠΊΠ΅ΡΠΊΠΈ Ρ ΡΠΊΠ°Π·Π°Π½ΠΈΠ΅ΠΌ ΠΎΡΠ½ΠΎΠ²Π½ΡΡ ΠΏΠ°ΡΠΏΠΎΡΡΠ½ΡΡ Π΄Π°Π½Π½ΡΡ .
ΠΡΠΈ Π½Π΅ΡΠΎΠ±Π»ΡΠ΄Π΅Π½ΠΈΠΈ ΡΡΠΈΡ ΡΡΠ»ΠΎΠ²ΠΈΠΉ ΠΏΠ°ΡΡΠΈΡ ΡΠ²Π°ΡΠΎΡΠ½ΡΡ ΠΌΠ°ΡΠ΅ΡΠΈΠ°Π»ΠΎΠ² Π½Π΅ Π΄ΠΎΠΏΡΡΠΊΠ°Π΅ΡΡΡ ΠΊ ΠΈΡΠΏΠΎΠ»ΡΠ·ΠΎΠ²Π°Π½ΠΈΡ ΠΈ ΠΏΠΎΠ΄Π»Π΅ΠΆΠΈΡ ΠΏΠΎΠ»Π½ΠΎΠΉ ΠΏΡΠΎΠ²Π΅ΡΠΊΠ΅ ΠΏΠΎ Π²ΡΠ΅ΠΌ ΠΏΠΎΠΊΠ°Π·Π°ΡΠ΅Π»ΡΠΌ, ΡΡΡΠ°Π½ΠΎΠ²Π»Π΅Π½Π½ΡΠΌ Π΄Π»Ρ Π΄Π°Π½Π½ΠΎΠ³ΠΎ Π²ΠΈΠ΄Π° ΡΠ²Π°ΡΠΎΡΠ½ΡΡ ΠΌΠ°ΡΠ΅ΡΠΈΠ°Π»ΠΎΠ².
ΠΠΎΠΏΡΠΎΡ ΠΎ Π²ΠΎΠ·ΠΌΠΎΠΆΠ½ΠΎΡΡΠΈ ΠΈΡΠΏΠΎΠ»ΡΠ·ΠΎΠ²Π°Π½ΠΈΡ ΡΠ²Π°ΡΠΎΡΠ½ΡΡ ΠΌΠ°ΡΠ΅ΡΠΈΠ°Π»ΠΎΠ², ΠΈΠΌΠ΅ΡΡΠΈΡ Π½Π΅ΡΠΎΠΎΡΠ²Π΅ΡΡΡΠ²ΠΈΠ΅ ΠΊΠ°ΡΠ΅ΡΡΠ²Π° ΠΈΠ»ΠΈ ΠΏΠΎΠ²ΡΠ΅ΠΆΠ΄Π΅Π½ΠΈΠ΅ ΡΠΏΠ°ΠΊΠΎΠ²ΠΊΠΈ, ΡΠ΅ΡΠ°Π΅ΡΡΡ ΡΠ»ΡΠΆΠ±ΠΎΠΉ Π³Π»Π°Π²Π½ΠΎΠ³ΠΎ ΡΠ²Π°ΡΡΠΈΠΊΠ° ΠΏΡΠ΅Π΄ΠΏΡΠΈΡΡΠΈΡ (ΠΎΡΠ³Π°Π½ΠΈΠ·Π°ΡΠΈΠΈ).
ΠΠΎΠ½ΡΡΠΎΠ»Ρ ΡΠ²Π°ΡΠΎΡΠ½ΡΡ ΠΌΠ°ΡΠ΅ΡΠΈΠ°Π»ΠΎΠ² : ΠΊΠΎΠ½ΡΡΠΎΠ»Ρ ΡΠ»Π΅ΠΊΡΡΠΎΠ΄ΠΎΠ²
ΠΠ°ΡΠ΅ΡΡΠ²ΠΎ ΡΠ»Π΅ΠΊΡΡΠΎΠ΄ΠΎΠ² ΠΏΡΠΎΠ²Π΅ΡΡΡΡ Π² ΠΏΡΠΎΡΠ΅ΡΡΠ΅ ΠΈΡ ΠΈΠ·Π³ΠΎΡΠΎΠ²Π»Π΅Π½ΠΈΡ Π½Π° Π·Π°Π²ΠΎΠ΄Π°Ρ ΠΈ ΠΏΠ΅ΡΠ΅Π΄ Π½Π°ΡΠ°Π»ΠΎΠΌ ΡΠ²Π°ΡΠΎΡΠ½ΡΡ ΡΠ°Π±ΠΎΡ Π² ΡΠ΅Ρ Π°Ρ ΠΈΠ»ΠΈ Π½Π° ΡΡΡΠΎΠΈΡΠ΅Π»ΡΠ½ΡΡ ΠΏΠ»ΠΎΡΠ°Π΄ΠΊΠ°Ρ .
ΠΠΎΠΊΡΡΡΠΈΠ΅ Π΄ΠΎΠ»ΠΆΠ½ΠΎ Π±ΡΡΡ ΠΏΠ»ΠΎΡΠ½ΡΠΌ ΠΈ ΠΏΡΠΎΡΠ½ΡΠΌ, Ρ ΠΎΡΠΎΡΠΎ ΡΠ΄Π΅ΡΠΆΠΈΠ²Π°ΡΡΡΡ Π½Π° ΡΠ»Π΅ΠΊΡΡΠΎΠ΄Π½ΠΎΠΌ ΡΡΠ΅ΡΠΆΠ½Π΅ ΠΈ Π½Π΅ ΡΠ°Π·ΡΡΡΠ°ΡΡΡΡ (ΠΏΠΎ ΠΠΠ‘Π’ 9466β60) ΠΏΡΠΈ ΡΠ²ΠΎΠ±ΠΎΠ΄Π½ΠΎΠΌ ΠΏΠ°Π΄Π΅Π½ΠΈΠΈ ΡΠ»Π΅ΠΊΡΡΠΎΠ΄Π° ΠΏΠ»Π°ΡΠΌΡ Π½Π° Π³Π»Π°Π΄ΠΊΡΡ ΡΡΠ°Π»ΡΠ½ΡΡ ΠΏΠ»ΠΈΡΡ Ρ Π²ΡΡΠΎΡΡ 1 ΠΌ Π΄Π»Ρ ΡΠ»Π΅ΠΊΡΡΠΎΠ΄ΠΎΠ² Π΄ΠΈΠ°ΠΌΠ΅ΡΡΠΎΠΌ 3 ΠΌΠΌ ΠΈ ΠΌΠ΅Π½Π΅Π΅ ΠΈ Ρ Π²ΡΡΠΎΡΡ 0,5 ΠΌ Π΄Π»Ρ ΡΠ»Π΅ΠΊΡΡΠΎΠ΄ΠΎΠ² Π΄ΠΈΠ°ΠΌΠ΅ΡΡΠΎΠΌ Π±ΠΎΠ»Π΅Π΅ 3 ΠΌΠΌ. ΠΠΎΠΏΡΡΠΊΠ°ΡΡΡΡ ΡΠ°ΡΡΠΈΡΠ½ΡΠ΅ ΠΎΡΠΊΠ°Π»ΡΠ²Π°Π½ΠΈΡ ΠΏΠΎΠΊΡΡΡΠΈΡ ΠΎΠ±ΡΠ΅ΠΉ Π΄Π»ΠΈΠ½ΠΎΠΉ Π½Π΅ Π±ΠΎΠ»Π΅Π΅ 20 ΠΌΠΌ.
ΠΠΎΠΊΡΡΡΠΈΠ΅ ΡΠ»Π΅ΠΊΡΡΠΎΠ΄ΠΎΠ² Π΄ΠΎΠ»ΠΆΠ½ΠΎ Π±ΡΡΡ Π²Π»Π°Π³ΠΎΡΡΠΎΠΉΠΊΠΈΠΌ ΠΈ Π½Π΅ ΡΠ°Π·ΡΡΡΠ°ΡΡΡΡ ΠΏΠΎΡΠ»Π΅ ΠΏΡΠ΅Π±ΡΠ²Π°Π½ΠΈΡ Π² Π²ΠΎΠ΄Π΅ Ρ ΡΠ΅ΠΌΠΏΠ΅ΡΠ°ΡΡΡΠΎΠΉ 15β25Β° Π‘ Π² ΡΠ΅ΡΠ΅Π½ΠΈΠ΅ 24 Ρ. ΠΠΎΠΏΡΡΠΊΠ°ΡΡΡΡ ΡΠ»Π΅Π΄ΡΡΡΠΈΠ΅ Π΄Π΅ΡΠ΅ΠΊΡΡ ΠΏΠΎΠ²Π΅ΡΡ Π½ΠΎΡΡΠΈ ΡΠ»Π΅ΠΊΡΡΠΎΠ΄ΠΎΠ²:
ΡΠ΅ΡΠΎΡ ΠΎΠ²Π°ΡΠΎΡΡΡ ΠΏΠΎΠ²Π΅ΡΡ Π½ΠΎΡΡΠΈ, ΠΏΡΠΎΠ΄ΠΎΠ»ΡΠ½ΡΠ΅ ΡΠΈΡΠΊΠΈ ΠΈ ΠΎΡΠ΄Π΅Π»ΡΠ½ΡΠ΅ Π·Π°Π΄ΠΈΡΡ β Π³Π»ΡΠ±ΠΈΠ½ΠΎΠΉ Π½Π΅ Π±ΠΎΠ»Π΅Π΅ 1/4 ΡΠΎΠ»ΡΠΈΠ½Ρ ΠΏΠΎΠΊΡΡΡΠΈΡ;
ΠΌΠ΅ΡΡΠ½ΡΠ΅ Π²ΠΌΡΡΠΈΠ½Ρ β Π² ΠΊΠΎΠ»ΠΈΡΠ΅ΡΡΠ²Π΅ Π½Π΅ Π±ΠΎΠ»Π΅Π΅ ΡΡΠ΅Ρ , Π³Π»ΡΠ±ΠΈΠ½ΠΎΠΉ Π΄Π° 1/2 ΡΠΎΠ»ΡΠΈΠ½Ρ ΠΏΠΎΠΊΡΡΡΠΈΡ ΠΈ Π΄Π»ΠΈΠ½ΠΎΠΉ Π΄ΠΎ 12 ΠΌΠΌ ΠΊΠ°ΠΆΠ΄Π°Ρ;
ΠΏΠΎΡΡ β Π² ΠΊΠΎΠ»ΠΈΡΠ΅ΡΡΠ²Π΅ Π½Π΅ Π±ΠΎΠ»Π΅Π΅ ΡΡΠ΅Ρ Π½Π° Π΄Π»ΠΈΠ½Π΅ 100 ΠΌΠΌ, Π΄ΠΈΠ°ΠΌΠ΅ΡΡΠΎΠΌ Π΄ΠΎ 2 ΠΌΠΌ, Π³Π»ΡΠ±ΠΈΠ½ΠΎΠΉ Π΄ΠΎ 1/2 ΡΠΎΠ»ΡΠΈΠ½Ρ;
Π²ΠΎΠ»ΠΎΡΠ½ΡΠ΅ ΡΡΠ΅ΡΠΈΠ½Ρ β Π² ΠΊΠΎΠ»ΠΈΡΠ΅ΡΡΠ²Π΅ Π½Π΅ Π±ΠΎΠ»Π΅Π΅ Π΄Π²ΡΡ , Π΄Π»ΠΈΠ½ΠΎΠΉ Π΄ΠΎ 12 ΠΌΠΌ ΠΊΠ°ΠΆΠ΄Π°Ρ.
ΠΠΎΠ½ΡΡΠΎΠ»Ρ ΠΊΠ°ΡΠ΅ΡΡΠ²Π° ΡΠ»Π΅ΠΊΡΡΠΎΠ΄ΠΎΠ² Π² Π·Π°Π²ΠΎΠ΄ΡΠΊΠΈΡ ΠΈ ΠΌΠΎΠ½ΡΠ°ΠΆΠ½ΡΡ ΡΡΠ»ΠΎΠ²ΠΈΡΡ ΠΏΠ΅ΡΠ΅Π΄ ΡΠ²Π°ΡΠΊΠΎΠΉ ΠΊΠΎΠ½ΡΡΡΡΠΊΡΠΈΠΉ, ΡΠ°Π±ΠΎΡΠ°ΡΡΠΈΡ Π² ΡΡΠΆΠ΅Π»ΡΡ ΡΡΠ»ΠΎΠ²ΠΈΡΡ (Π²ΠΈΠ±ΡΠ°ΡΠΈΠΎΠ½Π½Π°Ρ Π½Π°Π³ΡΡΠ·ΠΊΠ° (ΡΠΌ. ΠΠ°ΡΠΈΡΠ° ΠΎΡ Π²ΠΈΠ±ΡΠ°ΡΠΈΠΈ), Π²ΡΡΠΎΠΊΠ°Ρ ΡΠ΅ΠΌΠΏΠ΅ΡΠ°ΡΡΡΠ° ΠΈ Π΄Π°Π²Π»Π΅Π½ΠΈΠ΅, ΡΡΠ°Π½ΡΠΏΠΎΡΡΠΈΡΠΎΠ²ΠΊΠ° ΡΠΎΠΊΡΠΈΡΠ½ΡΡ Π³Π°Π·ΠΎΠ²), Π·Π°ΠΊΠ»ΡΡΠ°Π΅ΡΡΡ Π² ΠΏΡΠΎΠ²Π΅ΡΠΊΠ΅ Π½Π°Π»ΠΈΡΠΈΡ ΡΠ΅ΡΡΠΈΡΠΈΠΊΠ°ΡΠΎΠ² ΠΈ Π²ΡΠ±ΠΎΡΠΎΡΠ½ΠΎΠΌ ΠΊΠΎΠ½ΡΡΠΎΠ»Π΅ ΡΠΎΡΡΠΎΡΠ½ΠΈΡ Π²Π½Π΅ΡΠ½Π΅ΠΉ ΠΏΠΎΠ²Π΅ΡΡ Π½ΠΎΡΡΠΈ. ΠΡΠΎΠΌΠ΅ ΡΠΎΠ³ΠΎ, ΠΏΡΠΎΠ²Π΅ΡΡΡΡ ΠΌΠ΅Ρ Π°Π½ΠΈΡΠ΅ΡΠΊΠΈΠ΅ ΠΈ ΡΠ΅Ρ Π½ΠΎΠ»ΠΎΠ³ΠΈΡΠ΅ΡΠΊΠΈΠ΅ ΡΠ²ΠΎΠΉΡΡΠ²Π° Π½Π°ΠΏΠ»Π°Π²Π»Π΅Π½Π½ΠΎΠ³ΠΎ ΠΌΠ΅ΡΠ°Π»Π»Π°, Π° ΡΠ°ΠΊΠΆΠ΅, ΠΏΡΠΈ Π½Π΅ΠΎΠ±Ρ ΠΎΠ΄ΠΈΠΌΠΎΡΡΠΈ, Π²ΡΠΏΠΎΠ»Π½ΡΡΡ ΠΌΠ΅ΡΠ°Π»Π»ΠΎΠ³ΡΠ°ΡΠΈΡΠ΅ΡΠΊΠΈΠΉ Π°Π½Π°Π»ΠΈΠ·. Π’Π°ΠΊΠ°Ρ ΠΏΡΠΎΠ²Π΅ΡΠΊΠ° Π½Π΅ΠΎΠ±Ρ ΠΎΠ΄ΠΈΠΌΠ° ΠΈ Π² ΡΠ΅Ρ ΡΠ»ΡΡΠ°ΡΡ , Π΅ΡΠ»ΠΈ ΠΏΡΠΈΠΌΠ΅Π½ΡΠ΅ΠΌΡΠ΅ ΡΠ»Π΅ΠΊΡΡΠΎΠ΄Ρ Π΄Π°ΡΡ Π½Π΅ΡΡΠ°Π±ΠΈΠ»ΡΠ½ΡΡ Π΄ΡΠ³Ρ, ΠΈΠΌΠ΅ΡΡ Π½Π΅ΡΠ°Π²Π½ΠΎΠΌΠ΅ΡΠ½ΠΎΠ΅ ΠΏΠ»Π°Π²Π»Π΅Π½ΠΈΠ΅ ΠΈΠ»ΠΈ Π΅ΡΠ»ΠΈ Π² ΡΠ²Π°ΡΠ½ΠΎΠΌ ΡΠ²Π΅ Π²ΠΎΠ·Π½ΠΈΠΊΠ°ΡΡ ΡΡΠ΅ΡΠΈΠ½Ρ ΠΈ ΠΏΠΎΡΡ.
ΠΠ»Ρ Π²Π½Π΅ΡΠ½Π΅Π³ΠΎ ΠΎΡΠΌΠΎΡΡΠ° ΠΎΡΠ±ΠΈΡΠ°ΡΡ 10β15 ΡΠ»Π΅ΠΊΡΡΠΎΠ΄ΠΎΠ² ΠΈΠ· ΡΠ°Π·Π½ΡΡ ΠΏΠ°ΡΠ΅ΠΊ. ΠΡΠΈ Π½Π°Π»ΠΈΡΠΈΠΈ Π½Π΅Π΄ΠΎΠΏΡΡΡΠΈΠΌΡΡ Π΄Π΅ΡΠ΅ΠΊΡΠΎΠ² Π±Π΅ΡΡΡ ΡΠ΄Π²ΠΎΠ΅Π½Π½ΠΎΠ΅ ΠΊΠΎΠ»ΠΈΡΠ΅ΡΡΠ²ΠΎ, Π° ΠΏΡΠΈ ΠΏΠΎΠ²ΡΠΎΡΠ½ΠΎΠΌ ΠΎΠ±Π½Π°ΡΡΠΆΠ΅Π½ΠΈΠΈ Π΄Π΅ΡΠ΅ΠΊΡΠΎΠ² Π²ΡΡ ΠΏΠ°ΡΡΠΈΡ ΡΠ»Π΅ΠΊΡΡΠΎΠ΄ΠΎΠ² Π±ΡΠ°ΠΊΡΡΡ, ΡΠΎΡΡΠ°Π²Π»ΡΡ ΡΠ΅ΠΊΠ»Π°ΠΌΠ°ΡΠΈΠΎΠ½Π½ΡΠΉ Π°ΠΊΡ.
ΠΠΎΠΊΡΡΡΠΈΠ΅ ΡΠ»Π΅ΠΊΡΡΠΎΠ΄ΠΎΠ² Π΄ΠΎΠ»ΠΆΠ½ΠΎ Π±ΡΡΡ ΠΊΠΎΠ½ΡΠ΅Π½ΡΡΠΈΡΠ½ΠΎ ΠΎΡΠ½ΠΎΡΠΈΡΠ΅Π»ΡΠ½ΠΎ ΡΡΠ΅ΡΠΆΠ½Ρ. ΠΠ»Ρ ΠΏΡΠΎΠ²Π΅ΡΠΊΠΈ ΠΊΠΎΠ½ΡΠ΅Π½ΡΡΠΈΡΠ½ΠΎΡΡΠΈ Π² ΡΠ°Π·Π½ΡΡ ΡΠ΅ΡΠ΅Π½ΠΈΡΡ ΠΏΠΎ Π΄Π»ΠΈΠ½Π΅ ΡΠ»Π΅ΠΊΡΡΠΎΠ΄Π° Π΄Π΅Π»Π°ΡΡ Π½Π°Π΄ΡΠ΅Π·Ρ ΠΈ Π·Π°ΠΌΠ΅ΡΡΡΡ ΡΠΎΠ»ΡΠΈΠ½Ρ ΠΏΠΎΠΊΡΡΡΠΈΡ.
ΠΠ΅Π»ΠΈΡΠΈΠ½Π° ΡΠ°Π·Π½ΠΎΡΡΠΈ ΡΠΎΠ»ΡΠΈΠ½ Π½Π΅ Π΄ΠΎΠ»ΠΆΠ½Π° ΠΏΡΠ΅Π²ΡΡΠ°ΡΡ:
ΠΏΡΠΈ Π΄ΠΈΠ°ΠΌΠ΅ΡΡΠ΅ ΡΠ»Π΅ΠΊΡΡΠΎΠ΄Π° 2 ΠΌΠΌ …. 0,08 ΠΌΠΌ
ΠΏΡΠΈ Π΄ΠΈΠ°ΠΌΠ΅ΡΡΠ΅ ΡΠ»Π΅ΠΊΡΡΠΎΠ΄Π° 2,5 ΠΌΠΌ………..0,1 ΠΌΠΌ
ΠΏΡΠΈ Π΄ΠΈΠ°ΠΌΠ΅ΡΡΠ΅ ΡΠ»Π΅ΠΊΡΡΠΎΠ΄Π° 3 ΠΌΠΌ ………..0,15 ΠΌΠΌ
ΠΏΡΠΈ Π΄ΠΈΠ°ΠΌΠ΅ΡΡΠ΅ ΡΠ»Π΅ΠΊΡΡΠΎΠ΄Π° 4 ΠΌΠΌ ………..0,2 ΠΌΠΌ
ΠΏΡΠΈ Π΄ΠΈΠ°ΠΌΠ΅ΡΡΠ΅ ΡΠ»Π΅ΠΊΡΡΠΎΠ΄Π° 5 ΠΌΠΌ ………..0,25 ΠΌΠΌ
ΠΏΡΠΈ Π΄ΠΈΠ°ΠΌΠ΅ΡΡΠ΅ ΡΠ»Π΅ΠΊΡΡΠΎΠ΄Π° 6 ΠΌΠΌ ΠΈ Π±ΠΎΠ»Π΅Π΅…….0,3 ΠΌΠΌ
ΠΡΠΎΠ²Π΅ΡΠΊΡ ΡΠ»Π΅ΠΊΡΡΠΎΠ΄ΠΎΠ² Π½Π° ΡΠ²Π°ΡΠΈΠ²Π°Π΅ΠΌΠΎΡΡΡ ΠΈ ΠΏΠΎ ΠΌΠ΅Ρ Π°Π½ΠΈΡΠ΅ΡΠΊΠΈΠΌ ΡΠ²ΠΎΠΉΡΡΠ²Π°ΠΌ Π²ΡΠΏΠΎΠ»Π½ΡΡΡ ΠΏΠ΅ΡΠΈΠΎΠ΄ΠΈΡΠ΅ΡΠΊΠΈ Π΄Π»Ρ ΡΠ°Π·Π»ΠΈΡΠ½ΡΡ ΠΏΠ°ΡΡΠΈΠΉ. ΠΡΠΈ ΡΡΠΎΠΌ Π½Π°ΠΏΠ»Π°Π²ΠΊΡ Π²Π΅Π΄ΡΡ Π½Π° ΠΏΠ»Π°ΡΡΠΈΠ½Π°Ρ ΠΈΠ· ΡΠ³Π»Π΅ΡΠΎΠ΄ΠΈΡΡΠΎΠΉ ΠΈΠ»ΠΈ Π½ΠΈΠ·ΠΊΠΎΠ»Π΅Π³ΠΈΡΠΎΠ²Π°Π½Π½ΠΎΠΉ ΡΡΠ°Π»ΠΈ ΡΠΎΠ»ΡΠΈΠ½ΠΎΠΉ 10β14 ΠΌΠΌ (ΠΌΠΎΠΆΠ½ΠΎ ΡΠ°ΠΊΠΆΠ΅ ΡΠ²Π°ΡΠΈΠ²Π°ΡΡ ΡΡΡΠ±Ρ Ρ ΡΠΎΠ»ΡΠΈΠ½ΠΎΠΉ ΡΡΠ΅Π½ΠΊΠΈ Π½Π΅ ΠΌΠ΅Π½Π΅Π΅ 8 ΠΌΠΌ).
ΠΠ»Ρ ΡΠ»Π΅ΠΊΡΡΠΎΠ΄ΠΎΠ², Π΄Π°ΡΡΠΈΡ Π°ΡΡΡΠ΅Π½ΠΈΡΠ½ΡΠΉ Π½Π°ΠΏΠ»Π°Π²Π»Π΅Π½Π½ΡΠΉ ΠΌΠ΅ΡΠ°Π»Π», ΠΏΡΠΎΠ²Π΅ΡΡΡΡ Π½Π°Π»ΠΈΡΠΈΠ΅ Π² Π½Π΅ΠΌ ΡΠ΅ΡΡΠΈΡΠ½ΠΎΠΉ ΡΠ°Π·Ρ, Π΄Π»Ρ ΡΠ΅Π³ΠΎ Π½Π°ΠΏΠ»Π°Π²Π»ΡΠ΅ΡΡΡ ΠΏΡΡΡ β ΡΠ΅ΡΡΡ ΡΠ»ΠΎΠ΅Π² Π½Π° ΠΏΠ»Π°ΡΡΠΈΠ½Ρ ΠΈΠ»ΠΈ ΡΡΡΠ±Ρ ΠΈΠ· Π°ΡΡΡΠ΅Π½ΠΈΡΠ½ΠΎΠΉ ΡΡΠ°Π»ΠΈ. Π Π΅ΠΆΠΈΠΌ Π½Π°ΠΏΠ»Π°Π²ΠΊΠΈ Π²ΡΠ±ΠΈΡΠ°ΡΡ Π² ΡΠΎΠΎΡΠ²Π΅ΡΡΡΠ²ΠΈΠΈ Ρ ΡΠ΅ΠΊΠΎΠΌΠ΅Π½Π΄ΠΎΠ²Π°Π½Π½ΡΠΌΠΈ Π΄Π»Ρ ΡΠ»Π΅ΠΊΡΡΠΎΠ΄ΠΎΠ² Π΄Π°Π½Π½ΠΎΠ³ΠΎ ΡΠΈΠΏΠ° ΠΈ Π΄ΠΈΠ°ΠΌΠ΅ΡΡΠ°.
Π‘ΠΎΠ΄Π΅ΡΠΆΠ°Π½ΠΈΠ΅ ΡΠ΅ΡΡΠΈΡΠ° ΠΎΠΏΡΠ΅Π΄Π΅Π»ΡΡΡ ΠΎΠ±ΡΠ΅ΠΌΠ½ΡΠΌ ΠΌΠ°Π³Π½ΠΈΡΠ½ΡΠΌ ΠΌΠ΅ΡΠΎΠ΄ΠΎΠΌ Ρ ΠΏΠΎΠΌΠΎΡΡΡ ΡΠ΅ΡΡΠΈΡΠΎΠΌΠ΅ΡΠ° Π»ΠΈΠ±ΠΎ ΠΌΠ΅ΡΠ°Π»Π»ΠΎΠ³ΡΠ°ΡΠΈΡΠ΅ΡΠΊΠΈΠΌ ΠΌΠ΅ΡΠΎΠ΄ΠΎΠΌ Π½Π° ΠΎΠ±ΡΠ°Π·ΡΠ°Ρ Π΄ΠΈΠ°ΠΌΠ΅ΡΡΠΎΠΌ 5 ΠΌΠΌ ΠΈ Π΄Π»ΠΈΠ½ΠΎΠΉ 60 ΠΌΠΌ, Π²ΡΡΠ΅Π·Π°Π½Π½ΡΡ ΠΈΠ· Π΄Π²ΡΡ Π²Π΅ΡΡ Π½ΠΈΡ ΡΠ»ΠΎΠ΅Π² Π½Π°ΠΏΠ»Π°Π²ΠΊΠΈ. ΠΠ±ΡΠ°Π·ΡΡ ΡΡΠ°Π²ΡΡ Π² ΡΠ΅ΡΠ΅Π½ΠΈΠ΅ 2β2,5 ΠΌΠΈΠ½ ΡΠ΅Π°ΠΊΡΠΈΠ²ΠΎΠΌ, ΡΠΎΡΡΠΎΡΡΠΈΠΌ ΠΈΠ· ΠΊΡΠ°ΡΠ½ΠΎΠΉ ΠΊΡΠΎΠ²ΡΠ½ΠΎΠΉ ΡΠΎΠ»ΠΈ (10 Π³), Π΅Π΄ΠΊΠΎΠ³ΠΎ Π½Π°ΡΡΠ° (10 Π³) ΠΈ Π²ΠΎΠ΄Ρ (100 Π³).
ΠΡΠΏΡΡΠ°Π½ΠΈΠ΅ ΠΌΠ΅ΡΠ°Π»Π»Π°, ΡΠ²Π° ΠΈΠ»ΠΈ ΡΠ²Π°ΡΠ½ΠΎΠ³ΠΎ ΡΠΎΠ΅Π΄ΠΈΠ½Π΅Π½ΠΈΡ Π½Π° ΠΌΠ΅ΠΆΠΊΡΠΈΡΡΠ°Π»Π»ΠΈΡΠ½ΡΡ ΠΊΠΎΡΡΠΎΠ·ΠΈΡ ΠΏΡΠΎΠ²ΠΎΠ΄ΡΡ Π² ΡΠΎΠΎΡΠ²Π΅ΡΡΡΠ²ΠΈΠΈ Ρ ΠΠΠ‘Π’ 6032β58*.
Π£ Π²ΡΠ΅Ρ ΡΠ»Π΅ΠΊΡΡΠΎΠ΄ΠΎΠ² ΠΈ ΠΏΡΠΈΡΠ°Π΄ΠΎΡΠ½ΡΡ ΠΏΡΠΎΠ²ΠΎΠ»ΠΎΠΊ Π΄Π»Ρ ΡΠ²Π°ΡΠΊΠΈ Π°ΡΡΡΠ΅Π½ΠΈΡΠ½ΡΡ ΡΡΠ°Π»Π΅ΠΉ (ΡΠΌ. Π°ΡΡΡΠ΅Π½ΠΈΡΠ½ΡΠ΅ ΡΡΠ°Π»ΠΈ) ΠΏΡΠΎΠ²Π΅ΡΡΡΡ Π½Π° ΠΆΠ΅ΡΡΠΊΠΎΠΉ ΡΠ°Π²ΡΠΎΠ²ΠΎΠΉ ΠΏΡΠΎΠ±Π΅ ΠΈΠ»ΠΈ Π½Π° ΠΎΠ±ΡΠ°Π·ΡΠ΅ Ρ ΡΠ΅ΡΡΠΈΡΠ»ΠΎΠΉΠ½ΠΎΠΉ Π½Π°ΠΏΠ»Π°Π²ΠΊΠΎΠΉ ΡΠΊΠ»ΠΎΠ½Π½ΠΎΡΡΡ ΠΊ ΠΎΠ±ΡΠ°Π·ΠΎΠ²Π°Π½ΠΈΡ Π³ΠΎΡΡΡΠΈΡ ΡΡΠ΅ΡΠΈΠ½.
ΠΠ±ΡΠ°Π·Π΅Ρ ΠΈΠ·Π³ΠΎΡΠΎΠ²Π»ΡΡΡ ΠΈΠ· ΡΠΎΠΉ ΠΆΠ΅ ΠΌΠ°ΡΠΊΠΈ ΡΡΠ°Π»ΠΈ, ΡΡΠΎ ΠΈ ΡΠ²Π°ΡΠΈΠ²Π°Π΅ΠΌΠΎΠΉ ΠΊΠΎΠ½ΡΡΡΡΠΊΡΠΈΠΈ, Π° ΡΠ»Π΅ΠΊΡΡΠΎΠ΄Ρ Π±Π΅ΡΡΡ ΠΈΠ· ΠΏΠ°ΡΡΠΈΠΈ, ΠΏΡΠ΅Π΄Π½Π°Π·Π½Π°ΡΠ΅Π½Π½ΠΎΠΉ Π΄Π»Ρ ΡΠ²Π°ΡΠΊΠΈ.
Π¨Π΅ΡΡΠΈΡΠ»ΠΎΠΉΠ½ΡΡ Π½Π°ΠΏΠ»Π°Π²ΠΊΡ Π²Π΅Π΄ΡΡ Π² Π½ΠΈΠΆΠ½Π΅ΠΌ ΠΏΠΎΠ»ΠΎΠΆΠ΅Π½ΠΈΠΈ, Π° ΠΊΠ°ΠΆΠ΄ΡΠΉ ΡΠ»ΠΎΠΉ Π½Π°ΠΏΠ»Π°Π²Π»ΡΡΡ Π² ΠΎΠ΄Π½ΠΎΠΌ ΠΈ ΡΠΎΠΌ ΠΆΠ΅ Π½Π°ΠΏΡΠ°Π²Π»Π΅Π½ΠΈΠΈ. ΠΠ°ΠΆΠ΄ΡΠΉ ΠΏΠΎΡΠ»Π΅Π΄ΡΡΡΠΈΠΉ ΡΠ»ΠΎΠΉ ΠΊΠ»Π°Π΄ΡΡ ΠΏΠΎΡΠ»Π΅ ΠΏΠΎΠ»Π½ΠΎΠ³ΠΎ ΠΎΡΡΡΠ²Π°Π½ΠΈΡ ΠΏΡΠ΅Π΄ΡΠ΄ΡΡΠ΅Π³ΠΎ Π΄ΠΎ ΠΊΠΎΠΌΠ½Π°ΡΠ½ΠΎΠΉ ΡΠ΅ΠΌΠΏΠ΅ΡΠ°ΡΡΡΡ.
ΠΠΎΡΠ»Π΅ ΠΏΠΎΠ»Π½ΠΎΠ³ΠΎ ΠΎΡΡΡΠ²Π°Π½ΠΈΡ ΠΈ ΡΠ΄Π°Π»Π΅Π½ΠΈΡ ΡΠ»Π°ΠΊΠ° ΡΠΎ ΡΠ²Π° ΠΎΠ±ΡΠ°Π·Π΅Ρ ΠΎΡΠΌΠ°ΡΡΠΈΠ²Π°ΡΡ, ΠΈΠ·Π»Π°ΠΌΡΠ²Π°ΡΡ ΠΏΠΎ ΠΊΠΎΠ½ΡΡΠΎΠ»ΠΈΡΡΠ΅ΠΌΠΎΠΌΡ ΡΠ²Ρ ΠΈ ΠΏΡΠΎΠ²Π΅ΡΡΡΡ Π½Π°Π»ΠΈΡΠΈΠ΅ ΡΡΠ΅ΡΠΈΠ½.
ΠΠ°Π»Π΅Π΅ ΠΎΠ±ΡΠ°Π·Π΅Ρ ΡΠ°Π·ΡΠ΅Π·Π°ΡΡ Π½Π° ΡΡΠΈ ΡΠ°ΡΡΠΈ Π΄Π»Ρ ΠΈΠ·Π³ΠΎΡΠΎΠ²Π»Π΅Π½ΠΈΡ ΠΌΠ°ΠΊΡΠΎΡΠ»ΠΈΡΠΎΠ², ΠΊΠΎΡΠΎΡΡΠ΅ ΡΡΠ°Π²ΡΡ Π² ΡΠΎΠ»ΡΠ½ΠΎΠΉ ΠΊΠΈΡΠ»ΠΎΡΠ΅, ΠΏΡΠΎΠΌΡΠ²Π°ΡΡ, ΡΡΡΠ°Ρ ΠΈ ΡΠ°ΡΡΠΌΠ°ΡΡΠΈΠ²Π°ΡΡ ΠΏΠΎΠ΄ Π»ΡΠΏΠΎΠΉ Ρ 4β7-ΠΊΡΠ°ΡΠ½ΡΠΌ ΡΠ²Π΅Π»ΠΈΡΠ΅Π½ΠΈΠ΅ΠΌ.
ΠΡΠΈ Π½Π°Π»ΠΈΡΠΈΠΈ ΡΡΠ΅ΡΠΈΠ½ ΡΠ»Π΅ΠΊΡΡΠΎΠ΄Ρ Π±ΡΠ°ΠΊΡΡΡΡΡ.
ΠΡΠΎΠ²Π΅ΡΠ΅Π½Π½ΡΠ΅ ΡΠ»Π΅ΠΊΡΡΠΎΠ΄Ρ Ρ ΡΠ°Π½ΡΡ Π² ΡΡΡ ΠΎΠΌ ΠΏΠΎΠΌΠ΅ΡΠ΅Π½ΠΈΠΈ, Π½Π΅ Π΄ΠΎΠΏΡΡΠΊΠ°Ρ ΠΈΡ ΡΠ²Π»Π°ΠΆΠ½Π΅Π½ΠΈΡ. ΠΠ΅ΡΠ΅Π΄ ΡΠ²Π°ΡΠΊΠΎΠΉ ΡΠ»Π΅ΠΊΡΡΠΎΠ΄Ρ ΠΏΡΠΎΡΡΡΠΈΠ²Π°ΡΡ ΠΏΡΠΈ ΡΠ΅ΠΌΠΏΠ΅ΡΠ°ΡΡΡΠ΅ 150β180Β° Π‘ Π² ΡΠ΅ΡΠ΅Π½ΠΈΠ΅ 1,5β3 Ρ Π² ΡΡΡΠΈΠ»ΡΠ½ΡΡ ΠΏΠ΅ΡΠ°Ρ . ΠΠ°ΡΠ΅Π³ΠΎΡΠΈΡΠ΅ΡΠΊΠΈ Π·Π°ΠΏΡΠ΅ΡΠ°Π΅ΡΡΡ ΡΡΡΠΈΡΡ ΡΠ»Π΅ΠΊΡΡΠΎΠ΄Ρ Ρ ΠΏΠΎΠΌΠΎΡΡΡ Π³Π°Π·ΠΎΠ²ΡΡ Π³ΠΎΡΠ΅Π»ΠΎΠΊ ΠΈΠ»ΠΈ ΠΊΠΎΡΠΎΡΠΊΠΈΠΌ Π·Π°ΠΌΡΠΊΠ°Π½ΠΈΠ΅ΠΌ, ΡΠ°ΠΊ ΠΊΠ°ΠΊ ΡΡΠΎ ΠΏΡΠΈΠ²ΠΎΠ΄ΠΈΡ ΠΊ ΡΡ ΡΠ΄ΡΠ΅Π½ΠΈΡΠΌ Π·Π°ΡΠΈΡΠ½ΡΡ ΡΠ²ΠΎΠΉΡΡΠ² ΠΏΠΎΠΊΡΡΡΠΈΡ ΠΈ ΠΌΠΎΠΆΠ΅Ρ ΡΡΠ°ΡΡ ΠΏΡΠΈΡΠΈΠ½ΠΎΠΉ Π±ΡΠ°ΠΊΠ° ΡΠ²Π°ΡΠ½ΠΎΠ³ΠΎ ΡΠΎΠ΅Π΄ΠΈΠ½Π΅Π½ΠΈΡ.
ΠΠΎΠ½ΡΡΠΎΠ»Ρ ΡΠ²Π°ΡΠΎΡΠ½ΡΡ ΠΌΠ°ΡΠ΅ΡΠΈΠ°Π»ΠΎΠ² : ΠΊΠΎΠ½ΡΡΠΎΠ»Ρ ΡΠ»ΡΡΠ°
ΠΠ°ΡΠ΅ΡΡΠ²ΠΎ ΡΠ»ΡΡΠ°, ΠΏΠΎΡΡΡΠΏΠΈΠ²ΡΠ΅Π³ΠΎ Ρ Π·Π°Π²ΠΎΠ΄Π°-ΠΈΠ·Π³ΠΎΡΠΎΠ²ΠΈΡΠ΅Π»Ρ ΠΈ ΠΈΠΌΠ΅ΡΡΠ΅Π³ΠΎ ΡΠ΅ΡΡΠΈΡΠΈΠΊΠ°Ρ Ρ ΡΠΊΠ°Π·Π°Π½ΠΈΠ΅ΠΌ Π΅Π³ΠΎ Ρ ΠΈΠΌΠΈΡΠ΅ΡΠΊΠΎΠ³ΠΎ ΡΠΎΡΡΠ°Π²Π° ΠΈ Π³ΡΠ°Π½ΡΠ»ΡΡΠΈΠΈ, ΠΎΠΏΡΠ΅Π΄Π΅Π»ΡΡΡ Π² ΡΠΎΠΎΡΠ²Π΅ΡΡΡΠ²ΠΈΠΈ Ρ ΠΠΠ‘Π’ 9087β59 ΠΈΠ»ΠΈ Π’Π£ ΠΏΡΡΠ΅ΠΌ ΡΠ²Π°ΡΠΊΠΈ ΠΏΠ»Π°ΡΡΠΈΠ½ ΠΈΠ»ΠΈ ΡΡΡΠΊΠΎΠ² ΡΡΡΠ± Π½Π° ΡΠ΅ΠΆΠΈΠΌΠ°Ρ , ΠΎΠ±ΡΡΠ»ΠΎΠ²Π»Π΅Π½Π½ΡΡ ΡΠ΅Ρ Π½ΠΎΠ»ΠΎΠ³ΠΈΡΠ΅ΡΠΊΠΈΠΌ ΠΏΡΠΎΡΠ΅ΡΡΠΎΠΌ.
ΠΡΠ»ΠΈ Π² ΡΠ²Π°Ρ , Π½Π°ΠΏΠ»Π°Π²Π»Π΅Π½Π½ΡΡ ΠΏΠΎΠ΄ ΡΠ»ΠΎΠ΅ΠΌ ΡΠ»ΡΡΠ°, ΠΈΠΌΠ΅ΡΡΡΡ ΠΏΠΎΡΡ ΠΈΠ»ΠΈ ΡΡΠ΅ΡΠΈΠ½Ρ, ΡΠΎ ΡΡΠ°ΡΠ΅Π»ΡΠ½ΠΎ ΠΏΡΠΎΠ²Π΅ΡΡΡΡ Π³ΡΠ°Π½ΡΠ»ΠΎΠΌΠ΅ΡΡΠΈΡΠ΅ΡΠΊΠΈΠΉ ΡΠΎΡΡΠ°Π², ΠΎΠ΄Π½ΠΎΡΠΎΠ΄Π½ΠΎΡΡΡ, ΠΎΠ±ΡΠ΅ΠΌΠ½ΡΠΉ Π²Π΅Ρ, Π²Π»Π°ΠΆΠ½ΠΎΡΡΡ ΠΈ Π·Π°Π³ΡΡΠ·Π½Π΅Π½Π½ΠΎΡΡΡ ΡΠ»ΡΡΠ° (Π΅ΡΠ»ΠΈ Π²Π»Π°ΠΆΠ½ΠΎΡΡΡ ΠΏΡΠ΅Π²ΡΡΠ°Π΅Ρ 0,1%, ΡΠ»ΡΡ ΠΏΡΠΎΡΡΡΠΈΠ²Π°ΡΡ).
ΠΠΎΡΠ»Π΅ ΡΠ°ΠΊΠΎΠΉ ΠΏΡΠΎΠ²Π΅ΡΠΊΠΈ Π½Π°ΠΏΠ»Π°Π²Π»ΡΡΡ ΡΠ²Π°ΡΠ½ΠΎΠΉ ΡΠΎΠ² ΠΏΠΎΠ΄ ΡΠ»ΠΎΠ΅ΠΌ ΡΠ»ΡΡΠ° Π½Π° ΡΠ°Π²ΡΠΎΠ²ΠΎΠΌ ΠΎΠ±ΡΠ°Π·ΡΠ΅ ΠΈ ΠΈΡΡΠ»Π΅Π΄ΡΡΡ Π½Π°ΠΏΠ»Π°Π²Π»Π΅Π½Π½ΡΠΉ ΠΌΠ΅ΡΠ°Π»Π» Π½Π° ΡΠΎΠ΄Π΅ΡΠΆΠ°Π½ΠΈΠ΅ ΡΠ³Π»Π΅ΡΠΎΠ΄Π° ΠΈ ΡΠ΅ΡΡ ΠΏΡΡΠ΅ΠΌ Ρ ΠΈΠΌΠΈΡΠ΅ΡΠΊΠΎΠ³ΠΎ Π°Π½Π°Π»ΠΈΠ·Π° ΠΏΡΠΎΠ±Ρ, Π²Π·ΡΡΠΎΠΉ ΠΈΠ· Π²Π΅ΡΡ Π½Π΅Π³ΠΎ ΡΠ»ΠΎΡ ΡΠ²Π°ΡΠ½ΠΎΠ³ΠΎ ΡΠΎΠ΅Π΄ΠΈΠ½Π΅Π½ΠΈΡ.
ΠΡΠΈ Π½Π΅ΡΠ΄ΠΎΠ²Π»Π΅ΡΠ²ΠΎΡΠΈΡΠ΅Π»ΡΠ½ΡΡ ΡΠ΅Π·ΡΠ»ΡΡΠ°ΡΠ°Ρ Π²Ρ ΠΎΠ΄Π½ΠΎΠ³ΠΎ ΠΊΠΎΠ½ΡΡΠΎΠ»Ρ ΠΏΡΠΎΠ²Π΅ΡΡΠ΅ΠΌΠ°Ρ ΠΏΠ°ΡΡΠΈΡ ΡΠ»ΡΡΠ° Π·Π°Π±ΡΠ°ΠΊΠΎΠ²ΡΠ²Π°Π΅ΡΡΡ ΠΈΠ»ΠΈ ΠΏΠΎΠ΄Π²Π΅ΡΠ³Π°Π΅ΡΡΡ ΠΏΠΎΠ²ΡΠΎΡΠ½ΠΎΠΉ ΠΏΡΠΎΠΊΠ°Π»ΠΊΠ΅ Ρ ΠΏΠΎΡΠ»Π΅Π΄ΡΡΡΠ΅ΠΉ ΠΏΠΎΠ»Π½ΠΎΠΉ ΠΏΠ΅ΡΠ΅ΠΏΡΠΎΠ²Π΅ΡΠΊΠΎΠΉ, Π²ΠΊΠ»ΡΡΠ°Ρ ΠΎΠΏΡΠ΅Π΄Π΅Π»Π΅Π½ΠΈΠ΅ Ρ ΠΈΠΌΠΈΡΠ΅ΡΠΊΠΎΠ³ΠΎ ΡΠΎΡΡΠ°Π²Π° ΡΠ»ΡΡΠ°.
Π’Π°ΠΊΠΈΠΌ ΠΆΠ΅ ΠΎΠ±ΡΠ°Π·ΠΎΠΌ ΠΏΡΠΎΠ²Π΅ΡΡΡΡ ΠΊΠ°ΡΠ΅ΡΡΠ²ΠΎ ΡΠ»ΡΡΠ°, ΠΏΡΠ΅Π΄Π½Π°Π·Π½Π°ΡΠ΅Π½Π½ΠΎΠ³ΠΎ Π΄Π»Ρ ΡΠ²Π°ΡΠΊΠΈ ΠΊΠΎΠ½ΡΡΡΡΠΊΡΠΈΠΉ, ΡΠ°Π±ΠΎΡΠ°ΡΡΠΈΡ Π² ΡΡΠΆΠ΅Π»ΡΡ ΡΡΠ»ΠΎΠ²ΠΈΡΡ .
ΠΠΎΠ½ΡΡΠΎΠ»Ρ ΡΠ²Π°ΡΠΎΡΠ½ΡΡ ΠΌΠ°ΡΠ΅ΡΠΈΠ°Π»ΠΎΠ² : Π²Ρ ΠΎΠ΄Π½ΠΎΠΉ ΠΊΠΎΠ½ΡΡΠΎΠ»Ρ Π·Π°ΡΠΈΡΠ½ΡΡ Π³Π°Π·ΠΎΠ²
ΠΠ°ΡΠΈΡΠ½ΡΠ΅ Π³Π°Π·Ρ (ΡΠ³Π»Π΅ΠΊΠΈΡΠ»ΡΠΉ Π³Π°Π·, Π°ΡΠ³ΠΎΠ½, Π³Π΅Π»ΠΈΠΉ) ΠΏΠΎΡΡΠ°Π²Π»ΡΡΡΡΡ Π² Π±Π°Π»Π»ΠΎΠ½Π°Ρ , ΠΊΠΎΡΠΎΡΡΠ΅ Π΄ΠΎΠ»ΠΆΠ½Ρ ΠΈΠΌΠ΅ΡΡ ΡΠ΅ΡΡΠΈΡΠΈΠΊΠ°Ρ Π·Π°Π²ΠΎΠ΄Π°-ΠΏΠΎΡΡΠ°Π²ΡΠΈΠΊΠ° Ρ ΡΠΊΠ°Π·Π°Π½ΠΈΠ΅ΠΌ ΠΠΠ‘Π’Π°, Π½Π°Π·Π²Π°Π½ΠΈΡ Π³Π°Π·Π°, ΠΏΡΠΎΡΠ΅Π½ΡΠ½ΠΎΠ³ΠΎ ΠΊΠΎΠ»ΠΈΡΠ΅ΡΡΠ²Π° ΠΏΡΠΈΠΌΠ΅ΡΠ΅ΠΉ, Π²Π»Π°ΠΆΠ½ΠΎΡΡΠΈ ΠΈ Π΄Π°ΡΡ Π²ΡΠΏΡΡΠΊΠ°. ΠΡΠΏΠΎΠ»ΡΠ·ΠΎΠ²Π°Π½ΠΈΠ΅ Π±Π°Π»Π»ΠΎΠ½ΠΎΠ² Ρ Π·Π°ΡΠΈΡΠ½ΡΠΌΠΈ Π³Π°Π·Π°ΠΌΠΈ, Π½Π΅ ΠΈΠΌΠ΅ΡΡΠΈΡ ΡΠ΅ΡΡΠΈΡΠΈΠΊΠ°ΡΠΎΠ², Π·Π°ΠΏΡΠ΅ΡΠ°Π΅ΡΡΡ.
ΠΡΠΈ Π½Π°Π»ΠΈΡΠΈΠΈ ΡΠ΅ΡΡΠΈΡΠΈΠΊΠ°ΡΠΎΠ² ΠΊΠ°ΡΠ΅ΡΡΠ²ΠΎ Π·Π°ΡΠΈΡΠ½ΡΡ Π³Π°Π·ΠΎΠ² ΠΏΡΠΎΠ²Π΅ΡΡΡΡ ΡΠΎΠ»ΡΠΊΠΎ Π² ΡΠ΅Ρ ΡΠ»ΡΡΠ°ΡΡ , ΠΊΠΎΠ³Π΄Π° Π² ΡΠ²Π°ΡΠ½ΡΡ ΡΠ²Π°Ρ ΠΎΠ±Π½Π°ΡΡΠΆΠΈΠ²Π°ΡΡΡΡ ΠΏΠΎΡΡ, ΡΡΠ΅ΡΠΈΠ½Ρ ΠΈ Π΄ΡΡΠ³ΠΈΠ΅ Π½Π΅Π΄ΠΎΠΏΡΡΡΠΈΠΌΡΠ΅ Π΄Π΅ΡΠ΅ΠΊΡΡ.
ΠΠΎΠ½ΡΡΠΎΠ»Ρ ΡΠ²Π°ΡΠΎΡΠ½ΡΡ ΠΌΠ°ΡΠ΅ΡΠΈΠ°Π»ΠΎΠ² : Π²Ρ ΠΎΠ΄Π½ΠΎΠΉ ΠΊΠΎΠ½ΡΡΠΎΠ»Ρ ΡΠ²Π°ΡΠΎΡΠ½ΠΎΠΉ ΠΈ Π½Π°ΠΏΠ»Π°Π²ΠΎΡΠ½ΠΎΠΉ ΠΏΡΠΎΠ²ΠΎΠ»ΠΎΠΊΠΈ
ΠΡΠΎΠ²ΠΎΠ»ΠΎΠΊΠ° ΠΏΠΎΡΡΠ°Π²Π»ΡΠ΅ΡΡΡ Π² Π±ΡΡ ΡΠ°Ρ Ρ ΠΌΠ΅ΡΠ°Π»Π»ΠΈΡΠ΅ΡΠΊΠΈΠΌΠΈ Π±ΠΈΡΠΊΠ°ΠΌΠΈ, Π³Π΄Π΅ ΡΠΊΠ°Π·Π°Π½Ρ Π·Π°Π²ΠΎΠ΄-ΠΈΠ·Π³ΠΎΡΠΎΠ²ΠΈΡΠ΅Π»Ρ, Π½ΠΎΠΌΠ΅Ρ ΠΏΠ»Π°Π²ΠΊΠΈ ΠΈ ΠΌΠ°ΡΠΊΠ° ΠΏΡΠΎΠ²ΠΎΠ»ΠΎΠΊΠΈ ΡΠΎΠ³Π»Π°ΡΠ½ΠΎ ΡΡΠ°Π½Π΄Π°ΡΡΡ. Π‘ΡΠ°Π»ΡΠ½Π°Ρ ΡΠ²Π°ΡΠΎΡΠ½Π°Ρ ΠΏΡΠΎΠ²ΠΎΠ»ΠΎΠΊΠ° ΠΈΠ·Π³ΠΎΡΠΎΠ²Π»ΡΠ΅ΡΡΡ ΠΏΠΎ ΠΠΠ‘Π’ 2246β70, ΡΡΠ°Π»ΡΠ½Π°Ρ Π½Π°ΠΏΠ»Π°Π²ΠΎΡΠ½Π°Ρ β ΠΏΠΎ ΠΠΠ‘Π’ 10543β63, ΡΠ²Π°ΡΠΎΡΠ½Π°Ρ ΠΏΡΠΎΠ²ΠΎΠ»ΠΎΠΊΠ° ΠΈΠ· Π°Π»ΡΠΌΠΈΠ½ΠΈΡ ΠΈ Π΅Π³ΠΎ ΡΠΏΠ»Π°Π²ΠΎΠ² β ΠΏΠΎ ΠΠΠ‘Π’ 7871-63.
Π ΡΠ΅ΡΡΠΈΡΠΈΠΊΠ°ΡΠ΅ Π½Π° ΡΠ²Π°ΡΠΎΡΠ½ΡΡ ΠΏΡΠΎΠ²ΠΎΠ»ΠΎΠΊΡ ΡΠΊΠ°Π·ΡΠ²Π°ΡΡΡΡ Π΄ΠΈΠ°ΠΌΠ΅ΡΡ ΠΈ ΠΌΠ°ΡΠΊΠ° ΠΏΡΠΎΠ²ΠΎΠ»ΠΎΠΊΠΈ, Π·Π°Π²ΠΎΠ΄-ΠΈΠ·Π³ΠΎΡΠΎΠ²ΠΈΡΠ΅Π»Ρ, Π½ΠΎΠΌΠ΅Ρ ΠΏΠ»Π°Π²ΠΊΠΈ ΠΌΠ΅ΡΠ°Π»Π»Π°, ΠΈΠ· ΠΊΠΎΡΠΎΡΠΎΠ³ΠΎ ΠΈΠ·Π³ΠΎΡΠΎΠ²Π»Π΅Π½Π° ΠΏΡΠΎΠ²ΠΎΠ»ΠΎΠΊΠ°, Π²Π΅Ρ ΠΏΡΠΎΠ²ΠΎΠ»ΠΎΠΊΠΈ, Ρ ΠΈΠΌΠΈΡΠ΅ΡΠΊΠΈΠΉ ΡΠΎΡΡΠ°Π² ΠΈ Π½ΠΎΠΌΠ΅Ρ ΡΡΠ°Π½Π΄Π°ΡΡΠ°.
ΠΡΠΎΠ²ΠΎΠ»ΠΎΠΊΠ° Π½Π΅ Π΄ΠΎΠ»ΠΆΠ½Π° ΠΈΠΌΠ΅ΡΡ ΠΎΠΊΠΈΡΠ»ΠΎΠ², ΡΠ»Π΅Π΄ΠΎΠ² ΡΠΌΠ°Π·ΠΊΠΈ ΠΈ Π³ΡΡΠ·ΠΈ. ΠΡΠΈ Π½Π΅ΠΎΠ±Ρ ΠΎΠ΄ΠΈΠΌΠΎΡΡΠΈ Π΅Π΅ ΠΎΡΠΈΡΠ°ΡΡ ΠΌΠ΅Ρ Π°Π½ΠΈΡΠ΅ΡΠΊΠΈΠΌ ΠΈΠ»ΠΈ Ρ ΠΈΠΌΠΈΡΠ΅ΡΠΊΠΈΠΌ ΡΠΏΠΎΡΠΎΠ±ΠΎΠΌ.
Π ΡΠ»ΡΡΠ°Π΅ ΠΏΠΎΡΠ²Π»Π΅Π½ΠΈΡ Π² Π½Π°ΠΏΠ»Π°Π²Π»Π΅Π½Π½ΠΎΠΌ ΠΌΠ΅ΡΠ°Π»Π»Π΅ ΠΏΠΎΡ ΠΈΠ»ΠΈ ΡΡΠ΅ΡΠΈΠ½ ΠΏΡΠΎΠ²ΠΎΠ»ΠΎΠΊΡ ΠΈΡΠΏΡΡΡΠ²Π°ΡΡ Π½Π° ΡΠ²Π°ΡΠΈΠ²Π°Π΅ΠΌΠΎΡΡΡ ΠΏΡΡΠ΅ΠΌ ΡΠ²Π°ΡΠΊΠΈ Π΅Ρ ΠΏΠ»Π°ΡΡΠΈΠ½ ΡΠΎΠ»ΡΠΈΠ½ΠΎΠΉ 9β10 ΠΌΠΌ ΠΈΠ»ΠΈ ΡΡΡΠ± Ρ ΡΠΎΠ»ΡΠΈΠ½ΠΎΠΉ ΡΡΠ΅Π½ΠΊΠΈ Π½Π΅ ΠΌΠ΅Π½Π΅Π΅ 8 ΠΌΠΌ. ΠΠ· ΡΠ²Π°ΡΠ΅Π½Π½ΡΡ ΠΏΠ»Π°ΡΡΠΈΠ½ ΠΈΠ»ΠΈ ΡΡΡΠ± Π²ΡΡΠ΅Π·Π°ΡΡ ΡΠ΅ΡΡΡ ΠΎΠ±ΡΠ°Π·ΡΠΎΠ² Π΄Π»Ρ ΠΌΠ΅Ρ Π°Π½ΠΈΡΠ΅ΡΠΊΠΈΡ ΠΈΡΠΏΡΡΠ°Π½ΠΈΠΉ (ΡΡΠΈ β Π½Π° ΡΠ°ΡΡΡΠΆΠ΅Π½ΠΈΠ΅ ΠΈ ΡΡΠΈ β Π½Π° ΡΠ³ΠΎΠ» Π·Π°Π³ΠΈΠ±Π°).
Π‘Π²Π°ΡΠΎΡΠ½Π°Ρ ΠΏΡΠΎΠ²ΠΎΠ»ΠΎΠΊΠ°, Π½Π΅ ΠΈΠΌΠ΅ΡΡΠ°Ρ ΡΠ΅ΡΡΠΈΡΠΈΠΊΠ°ΡΠ°, ΠΏΠΎΠ΄Π²Π΅ΡΠ³Π°Π΅ΡΡΡ ΡΡΠ°ΡΠ΅Π»ΡΠ½ΠΎΠΌΡ ΠΊΠΎΠ½ΡΡΠΎΠ»Ρ, ΠΊΠΎΡΠΎΡΡΠΉ Π·Π°ΠΊΠ»ΡΡΠ°Π΅ΡΡΡ Π² ΠΎΡΠ½ΠΎΠ²Π½ΠΎΠΌ Π² ΠΎΠΏΡΠ΅Π΄Π΅Π»Π΅Π½ΠΈΠΈ Ρ ΠΈΠΌΠΈΡΠ΅ΡΠΊΠΎΠ³ΠΎ ΡΠΎΡΡΠ°Π²Π° ΠΈ ΠΌΠ°ΡΠΊΠΈ ΠΏΡΠΎΠ²ΠΎΠ»ΠΎΠΊΠΈ, Π° ΡΠ°ΠΊΠΆΠ΅ ΠΈΡΠΏΡΡΠ°Π½ΠΈΠΈ Π½Π° ΡΠ²Π°ΡΠΈΠ²Π°Π΅ΠΌΠΎΡΡΡ.
ΠΠΎΠ½ΡΡΠΎΠ»Ρ ΠΌΠ°ΡΠ΅ΡΠΈΠ°Π»ΠΎΠ² Π΄Π»Ρ Π΄Π΅ΡΠ΅ΠΊΡΠΎΡΠΊΠΎΠΏΠΈΠΈ
ΠΠ°ΠΆΠ΄Π°Ρ ΠΏΠ°ΡΡΠΈΡ ΠΌΠ°ΡΠ΅ΡΠΈΠ°Π»ΠΎΠ² Π΄Π»Ρ Π΄Π΅ΡΠ΅ΠΊΡΠΎΡΠΊΠΎΠΏΠΈΠΈ (ΡΠ΅Π°ΠΊΡΠΈΠ²Ρ, ΡΠ΅Π½ΡΠ³Π΅Π½ΠΎΠ²ΡΠΊΠ°Ρ ΠΏΠ»Π΅Π½ΠΊΠ°, ΡΡΠΈΠ»ΠΈΠ²Π°ΡΡΠΈΠ΅ ΡΠΊΡΠ°Π½Ρ, ΡΠ΅ΡΡΠΎΠΌΠ°Π³Π½ΠΈΡΠ½Π°Ρ Π»Π΅Π½ΡΠ°) ΠΏΡΠΈ ΠΏΠΎΡΡΡΠΏΠ»Π΅Π½ΠΈΠΈ Π² Π»Π°Π±ΠΎΡΠ°ΡΠΎΡΠΈΡ ΠΈ ΠΏΠ΅ΡΠ΅Π΄ ΠΈΡΠΏΠΎΠ»ΡΠ·ΠΎΠ²Π°Π½ΠΈΠ΅ΠΌ ΠΊΠΎΠ½ΡΡΠΎΠ»ΠΈΡΡΠ΅ΡΡΡ ΠΠ’Π ΠΈΠ»ΠΈ ΠΏΠ΅ΡΡΠΎΠ½Π°Π»ΠΎΠΌ Π»Π°Π±ΠΎΡΠ°ΡΠΎΡΠΈΠΈ. ΠΠ° ΡΠΏΠ°ΠΊΠΎΠ²ΠΎΡΠ½ΡΡ Π»ΠΈΡΡΠ°Ρ (ΠΏΠ°ΡΠΊΠ΅, Π΅ΠΌΠΊΠΎΡΡΠΈ, ΠΊΠΎΡΠΎΠ±ΠΊΠ΅) Π½Π΅ΠΎΠ±Ρ ΠΎΠ΄ΠΈΠΌΠΎ ΠΏΡΠΎΠ²Π΅ΡΠΈΡΡ Π½Π°Π»ΠΈΡΠΈΠ΅ ΡΡΠΈΠΊΠ΅ΡΠΊΠΈ Ρ Ρ Π°ΡΠ°ΠΊΡΠ΅ΡΠΈΡΡΠΈΠΊΠΎΠΉ ΠΌΠ°ΡΠ΅ΡΠΈΠ°Π»ΠΎΠ² ΡΠΎΠ³Π»Π°ΡΠ½ΠΎ ΡΡΠ΅Π±ΠΎΠ²Π°Π½ΠΈΡΠΌ ΡΠΎΠΎΡΠ²Π΅ΡΡΡΠ²ΡΡΡΠΈΡ ΠΠΠ‘Π’, Π’Π£ (ΡΠ΅Ρ Π½ΠΈΡΠ΅ΡΠΊΠΈΡ ΡΡΠ»ΠΎΠ²ΠΈΠΉ) ΠΈ ΠΈΠ½ΡΡΡΡΠΊΡΠΈΠΉ. ΠΠ°ΡΠ΅ΡΠΈΠ°Π»Ρ ΠΈ ΡΠΏΠ°ΠΊΠΎΠ²ΠΊΠ° Π½Π΅ Π΄ΠΎΠ»ΠΆΠ½Ρ ΠΈΠΌΠ΅ΡΡ ΠΏΠΎΠ²ΡΠ΅ΠΆΠ΄Π΅Π½ΠΈΠΉ.
ΠΡΠΈ Π»ΡΠ±ΠΎΠΌ ΠΎΡΡΡΡΠΏΠ»Π΅Π½ΠΈΠΈ ΠΎΡ Π½ΠΎΡΠΌ Π΄Π°Π½Π½Π°Ρ ΠΏΠ°ΡΡΠΈΡ ΠΌΠ°ΡΠ΅ΡΠΈΠ°Π»ΠΎΠ² ΠΏΡΠΎΡ ΠΎΠ΄ΠΈΡ ΠΏΡΠΎΠ²Π΅ΡΠΊΡ Π² ΡΠΎΠΎΡΠ²Π΅ΡΡΡΠ²ΠΈΠΈ Ρ ΠΠΠ‘Π’ ΠΈΠ»ΠΈ Π’Π£. ΠΡΠΈ Π½Π΅ΡΠ΄ΠΎΠ²Π»Π΅ΡΠ²ΠΎΡΠΈΡΠ΅Π»ΡΠ½ΡΡ ΡΠ΅Π·ΡΠ»ΡΡΠ°ΡΠ°Ρ ΠΊΠΎΠ½ΡΡΠΎΠ»Ρ ΠΏΠ°ΡΡΠΈΡ ΠΌΠ°ΡΠ΅ΡΠΈΠ°Π»ΠΎΠ² Π±ΡΠ°ΠΊΡΠ΅ΡΡΡ ΠΈ Π΄Π»Ρ Π΄Π΅ΡΠ΅ΠΊΡΠΎΡΠΊΠΎΠΏΠΈΠΈ Π½Π΅ Π΄ΠΎΠΏΡΡΠΊΠ°Π΅ΡΡΡ.
- < Π’ΠΈΠΏΡ Π³ΠΎΡΡΡΠΈΡ ΡΡΠ΅ΡΠΈΠ½ ΠΈ ΡΡ Π΅ΠΌΠ° ΡΠ°ΡΠΏΠΎΠ»ΠΎΠΆΠ΅Π½ΠΈΡ ΡΠ΅ΠΌΠΏΠ΅ΡΠ°ΡΡΡΠ½ΡΡ ΠΎΠ±Π»Π°ΡΡΠ΅ΠΉ
- Π‘ΠΎΠΏΡΠΎΡΠΈΠ²Π»Π΅Π½ΠΈΠ΅ ΠΎΠ±ΡΠ°Π·ΠΎΠ²Π°Π½ΠΈΡ Π³ΠΎΡΡΡΠΈΡ ΡΡΠ΅ΡΠΈΠ½ >
weldzone.info
5.3. ΠΡ ΠΎΠ΄Π½ΠΎΠΉ ΠΊΠΎΠ½ΡΡΠΎΠ»Ρ ΠΎΡΠ½ΠΎΠ²Π½ΡΡ ΠΌΠ°ΡΠ΅ΡΠΈΠ°Π»ΠΎΠ²
5.3.1. ΠΡ ΠΎΠ΄Π½ΠΎΠΉ ΠΊΠΎΠ½ΡΡΠΎΠ»Ρ ΠΌΠ΅ΡΠ°Π»Π»Π° (ΡΡΡΠ±, Π»ΠΈΡΡΠΎΠ², ΠΏΡΠΎΡΠΈΠ»ΡΠ½ΠΎΠ³ΠΎ ΠΏΡΠΎΠΊΠ°ΡΠ°), ΠΊΠΎΠ½ΡΡΡΡΠΊΡΠΈΠ²Π½ΡΡ ΡΠ»Π΅ΠΌΠ΅Π½ΡΠΎΠ² ΠΊΠΎΡΠ»ΠΎΠ² ΠΈ ΡΡΡΠ±ΠΎΠΏΡΠΎΠ²ΠΎΠ΄ΠΎΠ², ΠΏΠΎΡΡΡΠΏΠ°ΡΡΠΈΡ Π½Π° ΠΏΡΠ΅Π΄ΠΏΡΠΈΡΡΠΈΠ΅ Π΄Π»Ρ ΠΈΠ·Π³ΠΎΡΠΎΠ²Π»Π΅Π½ΠΈΡ, ΠΌΠΎΠ½ΡΠ°ΠΆΠ° ΠΈΠ»ΠΈ ΡΠ΅ΠΌΠΎΠ½ΡΠ° ΡΠ½Π΅ΡΠ³Π΅ΡΠΈΡΠ΅ΡΠΊΠΎΠ³ΠΎ ΠΎΠ±ΡΠ΅ΠΊΡΠ°, Π²ΠΊΠ»ΡΡΠ°Π΅Ρ ΡΠ»Π΅Π΄ΡΡΡΠΈΠ΅ ΠΊΠΎΠ½ΡΡΠΎΠ»ΡΠ½ΡΠ΅ ΠΎΠΏΠ΅ΡΠ°ΡΠΈΠΈ:
Π°) ΠΏΡΠΎΠ²Π΅ΡΠΊΡ Π½Π°Π»ΠΈΡΠΈΡ ΡΠ΅ΡΡΠΈΡΠΈΠΊΠ°ΡΠ° ΠΈΠ»ΠΈ ΠΏΠ°ΡΠΏΠΎΡΡΠ°, ΠΏΠΎΠ»Π½ΠΎΡΡ ΠΏΡΠΈΠ²Π΅Π΄Π΅Π½Π½ΡΡ Π² Π½Π΅ΠΌ Π΄Π°Π½Π½ΡΡ ΠΈ ΡΠΎΠΎΡΠ²Π΅ΡΡΡΠ²ΠΈΡ ΡΡΠΈΡ Π΄Π°Π½Π½ΡΡ ΡΡΠ΅Π±ΠΎΠ²Π°Π½ΠΈΡΠΌ ΡΡΠ°Π½Π΄Π°ΡΡΠ°, ΡΠ΅Ρ Π½ΠΈΡΠ΅ΡΠΊΠΈΡ ΡΡΠ»ΠΎΠ²ΠΈΠΉ ΠΈΠ»ΠΈ ΠΊΠΎΠ½ΡΡΡΡΠΊΡΠΎΡΡΠΊΠΎΠΉ Π΄ΠΎΠΊΡΠΌΠ΅Π½ΡΠ°ΡΠΈΠΈ;
Π±) ΠΏΡΠΎΠ²Π΅ΡΠΊΡ Π½Π°Π»ΠΈΡΠΈΡ ΠΌΠ°ΡΠΊΠΈΡΠΎΠ²ΠΊΠΈ ΠΈ ΡΠΎΠΎΡΠ²Π΅ΡΡΡΠ²ΠΈΡ Π΅Π΅ ΡΠ΅ΡΡΠΈΡΠΈΠΊΠ°ΡΠ½ΡΠΌ ΠΈΠ»ΠΈ ΠΏΠ°ΡΠΏΠΎΡΡΠ½ΡΠΌ Π΄Π°Π½Π½ΡΠΌ;
Π²) ΠΎΡΠΌΠΎΡΡ ΠΌΠ΅ΡΠ°Π»Π»Π° ΠΈ ΠΊΠΎΠ½ΡΡΡΡΠΊΡΠΈΠ²Π½ΡΡ ΡΠ»Π΅ΠΌΠ΅Π½ΡΠΎΠ² Π΄Π»Ρ Π²ΡΡΠ²Π»Π΅Π½ΠΈΡ ΠΏΠΎΠ²Π΅ΡΡ Π½ΠΎΡΡΠ½ΡΡ Π΄Π΅ΡΠ΅ΠΊΡΠΎΠ² ΠΈ ΠΏΠΎΠ²ΡΠ΅ΠΆΠ΄Π΅Π½ΠΈΠΉ.
5.3.2. ΠΡΠΈ ΠΎΡΡΡΡΡΡΠ²ΠΈΠΈ ΡΠ΅ΡΡΠΈΡΠΈΠΊΠ°ΡΠ° ΠΈΠ»ΠΈ Π½Π΅ΠΏΠΎΠ»Π½ΠΎΡΠ΅ ΡΠ΅ΡΡΠΈΡΠΈΠΊΠ°ΡΠ½ΡΡ Π΄Π°Π½Π½ΡΡ ΠΏΡΠΈΠΌΠ΅Π½Π΅Π½ΠΈΠ΅ ΡΡΠΎΠ³ΠΎ ΠΌΠ΅ΡΠ°Π»Π»Π° ΠΌΠΎΠΆΠ΅Ρ Π±ΡΡΡ Π΄ΠΎΠΏΡΡΠ΅Π½ΠΎ ΡΠΎΠ»ΡΠΊΠΎ ΠΏΠΎΡΠ»Π΅ ΠΏΡΠΎΠ²Π΅Π΄Π΅Π½ΠΈΡ ΠΈΡΠΏΡΡΠ°Π½ΠΈΠΉ, ΠΏΠΎΠ΄ΡΠ²Π΅ΡΠΆΠ΄Π°ΡΡΠΈΡ ΡΠΎΠΎΡΠ²Π΅ΡΡΡΠ²ΠΈΠ΅ ΠΌΠ΅ΡΠ°Π»Π»Π° Π²ΡΠ΅ΠΌ ΡΡΠ΅Π±ΠΎΠ²Π°Π½ΠΈΡΠΌ ΡΡΠ°Π½Π΄Π°ΡΡΠ° ΠΈΠ»ΠΈ ΡΠ΅Ρ Π½ΠΈΡΠ΅ΡΠΊΠΈΡ ΡΡΠ»ΠΎΠ²ΠΈΠΉ.
5.3.3. ΠΠΎΠ½ΡΡΡΡΠΊΡΠΈΠ²Π½ΡΠ΅ ΡΠ»Π΅ΠΌΠ΅Π½ΡΡ ΠΊΠΎΡΠ»ΠΎΠ² ΠΈ ΡΡΡΠ±ΠΎΠΏΡΠΎΠ²ΠΎΠ΄ΠΎΠ², Π½Π΅ ΠΈΠΌΠ΅ΡΡΠΈΠ΅ Π·Π°Π²ΠΎΠ΄ΡΠΊΠΎΠ³ΠΎ ΠΏΠ°ΡΠΏΠΎΡΡΠ° (ΡΠ΅ΡΡΠΈΡΠΈΠΊΠ°ΡΠ°), Π½Π΅ ΠΌΠΎΠ³ΡΡ Π±ΡΡΡ Π΄ΠΎΠΏΡΡΠ΅Π½Ρ Π΄Π»Ρ Π΄Π°Π»ΡΠ½Π΅ΠΉΡΠ΅Π³ΠΎ ΠΏΡΠΎΠΈΠ·Π²ΠΎΠ΄ΡΡΠ²Π° (ΠΌΠΎΠ½ΡΠ°ΠΆΠ°, ΡΠ΅ΠΌΠΎΠ½ΡΠ°, ΡΠΊΡΡΠΏΠ½Π΅Π½ΠΈΡ).
5.3.4. ΠΡ ΠΎΠ΄Π½ΠΎΠΉ ΠΊΠΎΠ½ΡΡΠΎΠ»Ρ ΠΎΡΠ½ΠΎΠ²Π½ΡΡ ΠΌΠ°ΡΠ΅ΡΠΈΠ°Π»ΠΎΠ² (ΠΌΠ΅ΡΠ°Π»Π»Π° ΠΈ ΠΊΠΎΠ½ΡΡΡΡΠΊΡΠΈΠ²Π½ΡΡ ΡΠ»Π΅ΠΌΠ΅Π½ΡΠΎΠ²) ΠΎΡΡΡΠ΅ΡΡΠ²Π»ΡΠ΅Ρ Π² ΡΠΎΠΎΡΠ²Π΅ΡΡΡΠ²ΠΈΠΈ Ρ ΠΠΠ‘Π’ 24297 ΠΎΡΠ³Π°Π½ΠΈΠ·Π°ΡΠΈΡ – Π·Π°ΠΊΠ°Π·ΡΠΈΠΊ ΡΡΠΈΡ ΠΌΠ°ΡΠ΅ΡΠΈΠ°Π»ΠΎΠ². Π Π΅Π·ΡΠ»ΡΡΠ°ΡΡ Π²Ρ ΠΎΠ΄Π½ΠΎΠ³ΠΎ ΠΊΠΎΠ½ΡΡΠΎΠ»Ρ Π΄ΠΎΠ»ΠΆΠ½Ρ Π±ΡΡΡ ΠΏΠ΅ΡΠ΅Π΄Π°Π½Ρ ΠΌΠΎΠ½ΡΠ°ΠΆΠ½ΠΎΠΉ (ΡΠ΅ΠΌΠΎΠ½ΡΠ½ΠΎΠΉ) ΠΎΡΠ³Π°Π½ΠΈΠ·Π°ΡΠΈΠΈ.
5.4. ΠΡ ΠΎΠ΄Π½ΠΎΠΉ ΠΊΠΎΠ½ΡΡΠΎΠ»Ρ ΡΠ²Π°ΡΠΎΡΠ½ΡΡ ΠΌΠ°ΡΠ΅ΡΠΈΠ°Π»ΠΎΠ² ΠΈ ΠΌΠ°ΡΠ΅ΡΠΈΠ°Π»ΠΎΠ² Π΄Π»Ρ Π΄Π΅ΡΠ΅ΠΊΡΠΎΡΠΊΠΎΠΏΠΈΠΈ
ΠΠΎΠ½ΡΡΠΎΠ»Ρ ΡΠ²Π°ΡΠΎΡΠ½ΠΎΠΉ ΠΏΡΠΎΠ²ΠΎΠ»ΠΎΠΊΠΈ (ΠΏ.ΠΏ. 5.4.17 – 5.4.20)
ΠΠΎΠ½ΡΡΠΎΠ»Ρ ΡΠ»ΡΡΠ° (ΠΏ.ΠΏ. 5.4.21)
ΠΠΎΠ½ΡΡΠΎΠ»Ρ Π·Π°ΡΠΈΡΠ½ΠΎΠ³ΠΎ Π³Π°Π·Π° (ΠΏ.ΠΏ. 5.4.22)
ΠΠΎΠ½ΡΡΠΎΠ»Ρ ΠΌΠ°ΡΠ΅ΡΠΈΠ°Π»ΠΎΠ² Π΄Π»Ρ Π΄Π΅ΡΠ΅ΠΊΡΠΎΡΠΊΠΎΠΏΠΈΠΈ (ΠΏ.ΠΏ. 5.4.23 – 5.4.24)
5.4.1. ΠΠ΅ΡΠ΅Π΄ ΠΈΡΠΏΠΎΠ»ΡΠ·ΠΎΠ²Π°Π½ΠΈΠ΅ΠΌ ΡΠ²Π°ΡΠΎΡΠ½ΡΡ ΠΌΠ°ΡΠ΅ΡΠΈΠ°Π»ΠΎΠ² (ΡΠ»Π΅ΠΊΡΡΠΎΠ΄ΠΎΠ², ΡΠ²Π°ΡΠΎΡΠ½ΠΎΠΉ ΠΏΡΠΎΠ²ΠΎΠ»ΠΎΠΊΠΈ, ΡΠ»ΡΡΠ° ΠΈ Π΄Ρ.) Π΄ΠΎΠ»ΠΆΠ½Ρ Π±ΡΡΡ ΠΏΡΠΎΠ²Π΅ΡΠ΅Π½Ρ:
Π°) Π½Π°Π»ΠΈΡΠΈΠ΅ ΡΠ΅ΡΡΠΈΡΠΈΠΊΠ°ΡΠ° (Π½Π° ΡΠ»Π΅ΠΊΡΡΠΎΠ΄Ρ, ΠΏΡΠΎΠ²ΠΎΠ»ΠΎΠΊΡ ΠΈ ΡΠ»ΡΡ), ΠΏΠΎΠ»Π½ΠΎΡΠ° ΠΏΡΠΈΠ²Π΅Π΄Π΅Π½Π½ΡΡ Π² Π½Π΅ΠΌ Π΄Π°Π½Π½ΡΡ ΠΈ ΠΈΡ ΡΠΎΠΎΡΠ²Π΅ΡΡΡΠ²ΠΈΠ΅ ΡΡΠ΅Π±ΠΎΠ²Π°Π½ΠΈΡΠΌ ΡΡΠ°Π½Π΄Π°ΡΡΠ°, ΡΠ΅Ρ Π½ΠΈΡΠ΅ΡΠΊΠΈΡ ΡΡΠ»ΠΎΠ²ΠΈΠΉ ΠΈΠ»ΠΈ ΠΏΠ°ΡΠΏΠΎΡΡΠ° Π½Π° ΠΊΠΎΠ½ΠΊΡΠ΅ΡΠ½ΡΠ΅ ΡΠ²Π°ΡΠΎΡΠ½ΡΠ΅ ΠΌΠ°ΡΠ΅ΡΠΈΠ°Π»Ρ;
Π±) Π½Π°Π»ΠΈΡΠΈΠ΅ Π½Π° ΠΊΠ°ΠΆΠ΄ΠΎΠΌ ΡΠΏΠ°ΠΊΠΎΠ²ΠΎΡΠ½ΠΎΠΌ ΠΌΠ΅ΡΡΠ΅ (ΠΏΠ°ΡΠΊΠ΅, ΠΊΠΎΡΠΎΠ±ΠΊΠ΅, ΡΡΠΈΠΊΠ΅, ΠΌΠΎΡΠΊΠ΅, Π±ΡΡ ΡΠ΅ ΠΈ ΠΏΡ.) ΡΠΎΠΎΡΠ²Π΅ΡΡΡΠ²ΡΡΡΠΈΡ ΡΡΠΈΠΊΠ΅ΡΠΎΠΊ (ΡΡΠ»ΡΠΊΠΎΠ²) ΠΈΠ»ΠΈ Π±ΠΈΡΠΎΠΊ Ρ ΠΏΡΠΎΠ²Π΅ΡΠΊΠΎΠΉ ΠΏΠΎΠ»Π½ΠΎΡΡ ΡΠΊΠ°Π·Π°Π½Π½ΡΡ Π² Π½ΠΈΡ Π΄Π°Π½Π½ΡΡ ;
Π²) ΡΠΎΡ ΡΠ°Π½Π½ΠΎΡΡΡ ΡΠΏΠ°ΠΊΠΎΠ²ΠΎΠΊ ΠΈ ΡΠ°ΠΌΠΈΡ ΠΌΠ°ΡΠ΅ΡΠΈΠ°Π»ΠΎΠ²;
Π³) Π΄Π»Ρ Π±Π°Π»Π»ΠΎΠ½ΠΎΠ² Ρ Π³Π°Π·ΠΎΠΌ – Π½Π°Π»ΠΈΡΠΈΠ΅ Π΄ΠΎΠΊΡΠΌΠ΅Π½ΡΠ°, ΡΠ΅Π³Π»Π°ΠΌΠ΅Π½ΡΠΈΡΠΎΠ²Π°Π½Π½ΠΎΠ³ΠΎ ΡΡΠ°Π½Π΄Π°ΡΡΠΎΠΌ Π½Π° ΡΠΎΠΎΡΠ²Π΅ΡΡΡΠ²ΡΡΡΠΈΠΉ Π³Π°Π·.
5.4.2. ΠΡΠΈ ΠΎΡΡΡΡΡΡΠ²ΠΈΠΈ ΡΠ΅ΡΡΠΈΡΠΈΠΊΠ°ΡΠ° ΠΈΠ»ΠΈ Π½Π΅ΠΏΠΎΠ»Π½ΠΎΡΠ΅ ΡΠ΅ΡΡΠΈΡΠΈΠΊΠ°ΡΠ½ΡΡ ΡΠ²Π΅Π΄Π΅Π½ΠΈΠΉ ΡΠ²Π°ΡΠΎΡΠ½ΡΠΉ ΠΌΠ°ΡΠ΅ΡΠΈΠ°Π» Π΄Π°Π½Π½ΠΎΠΉ ΠΏΠ°ΡΡΠΈΠΈ ΠΌΠΎΠΆΠ΅Ρ Π±ΡΡΡ Π΄ΠΎΠΏΡΡΠ΅Π½ ΠΊ ΠΈΡΠΏΠΎΠ»ΡΠ·ΠΎΠ²Π°Π½ΠΈΡ ΠΏΠΎΡΠ»Π΅ ΠΏΡΠΎΠ²Π΅Π΄Π΅Π½ΠΈΡ ΠΈΡΠΏΡΡΠ°Π½ΠΈΠΉ ΠΈ ΠΏΠΎΠ»ΡΡΠ΅Π½ΠΈΡ ΠΏΠΎΠ»ΠΎΠΆΠΈΡΠ΅Π»ΡΠ½ΡΡ ΡΠ΅Π·ΡΠ»ΡΡΠ°ΡΠΎΠ² ΠΏΠΎ Π²ΡΠ΅ΠΌ ΠΏΠΎΠΊΠ°Π·Π°ΡΠ΅Π»ΡΠΌ, ΡΡΡΠ°Π½ΠΎΠ²Π»Π΅Π½Π½ΡΠΌ ΡΠΎΠΎΡΠ²Π΅ΡΡΡΠ²ΡΡΡΠΈΠΌ Π½ΠΎΡΠΌΠ°ΡΠΈΠ²Π½ΡΠΌ ΡΠ΅Ρ Π½ΠΈΡΠ΅ΡΠΊΠΈΠΌ Π΄ΠΎΠΊΡΠΌΠ΅Π½ΡΠΎΠΌ – ΡΡΠ°Π½Π΄Π°ΡΡΠ°ΠΌΠΈ (ΡΠ΅Ρ Π½ΠΈΡΠ΅ΡΠΊΠΈΠΌΠΈ ΡΡΠ»ΠΎΠ²ΠΈΡΠΌΠΈ) ΠΈΠ»ΠΈ ΠΏΠ°ΡΠΏΠΎΡΡΠΎΠΌ Π½Π° Π΄Π°Π½Π½ΡΠΉ Π²ΠΈΠ΄ ΠΌΠ°ΡΠ΅ΡΠΈΠ°Π»Π°.
Π ΡΠ»ΡΡΠ°Π΅ ΡΠ°ΡΡ ΠΎΠΆΠ΄Π΅Π½ΠΈΡ ΡΠ΅ΡΡΠΈΡΠΈΠΊΠ°ΡΠ½ΡΡ Π΄Π°Π½Π½ΡΡ Ρ ΡΡΠ΅Π±ΠΎΠ²Π°Π½ΠΈΡΠΌΠΈ ΡΠΎΠΎΡΠ²Π΅ΡΡΡΠ²ΡΡΡΠ΅Π³ΠΎ ΠΠ’Π ΠΏΠ°ΡΡΠΈΡ ΡΠ²Π°ΡΠΎΡΠ½ΡΡ ΠΌΠ°ΡΠ΅ΡΠΈΠ°Π»ΠΎΠ² ΠΊ ΠΈΡΠΏΠΎΠ»ΡΠ·ΠΎΠ²Π°Π½ΠΈΡ Π½Π΅ Π΄ΠΎΠΏΡΡΠΊΠ°Π΅ΡΡΡ.
5.4.3. ΠΡΠΈ ΠΎΠ±Π½Π°ΡΡΠΆΠ΅Π½ΠΈΠΈ ΠΏΠΎΠ²ΡΠ΅ΠΆΠ΄Π΅Π½ΠΈΡ ΠΈΠ»ΠΈ ΠΏΠΎΡΡΠΈ ΡΠΏΠ°ΠΊΠΎΠ²ΠΊΠΈ ΠΈΠ»ΠΈ ΡΠ°ΠΌΠΈΡ ΠΌΠ°ΡΠ΅ΡΠΈΠ°Π»ΠΎΠ² Π²ΠΎΠΏΡΠΎΡ ΠΎ Π²ΠΎΠ·ΠΌΠΎΠΆΠ½ΠΎΡΡΠΈ ΠΈΡΠΏΠΎΠ»ΡΠ·ΠΎΠ²Π°Π½ΠΈΡ ΡΡΠΈΡ ΠΌΠ°ΡΠ΅ΡΠΈΠ°Π»ΠΎΠ² ΡΠ΅ΡΠ°Π΅Ρ ΡΡΠΊΠΎΠ²ΠΎΠ΄ΠΈΡΠ΅Π»Ρ ΡΠ²Π°ΡΠΎΡΠ½ΡΡ ΡΠ°Π±ΠΎΡ ΡΠΎΠ²ΠΌΠ΅ΡΡΠ½ΠΎ Ρ ΠΠ’Π (Π‘Π’Π) ΠΏΡΠ΅Π΄ΠΏΡΠΈΡΡΠΈΡ (ΠΎΡΠ³Π°Π½ΠΈΠ·Π°ΡΠΈΠΈ).
5.4.4. ΠΠ°ΠΆΠ΄Π°Ρ ΡΠ°ΡΡΡ ΡΠ²Π°ΡΠΎΡΠ½ΠΎΠΉ ΠΏΡΠΎΠ²ΠΎΠ»ΠΎΠΊΠΈ, ΠΎΡΠ΄Π΅Π»Π΅Π½Π½Π°Ρ ΠΎΡ Π±ΡΡ ΡΡ (ΠΌΠΎΡΠΊΠ°), Π΄ΠΎΠ»ΠΆΠ½Π° Π±ΡΡΡ ΡΠ½Π°Π±ΠΆΠ΅Π½Π° Π±ΠΈΡΠΊΠΎΠΉ, Π½Π° ΠΊΠΎΡΠΎΡΠΎΠΉ ΡΠΊΠ°Π·ΡΠ²Π°ΡΡΡΡ ΠΌΠ°ΡΠΊΠ°, Π½ΠΎΠΌΠ΅Ρ ΠΏΠ»Π°Π²ΠΊΠΈ ΠΈ Π΄ΠΈΠ°ΠΌΠ΅ΡΡ ΠΏΡΠΎΠ²ΠΎΠ»ΠΎΠΊΠΈ.
ΠΠΎΠ½ΡΡΠΎΠ»Ρ ΡΠ»Π΅ΠΊΡΡΠΎΠ΄ΠΎΠ² Π΄Π»Ρ ΡΡΡΠ½ΠΎΠΉ Π΄ΡΠ³ΠΎΠ²ΠΎΠΉ ΡΠ²Π°ΡΠΊΠΈ
5.4.5. ΠΠ΅ΡΠ΅Π΄ ΠΏΡΠΈΠΌΠ΅Π½Π΅Π½ΠΈΠ΅ΠΌ ΠΊΠ°ΠΆΠ΄ΠΎΠΉ ΠΏΠ°ΡΡΠΈΠΈ ΡΠ»Π΅ΠΊΡΡΠΎΠ΄ΠΎΠ² Π½Π΅Π·Π°Π²ΠΈΡΠΈΠΌΠΎ ΠΎΡ Π½Π°Π»ΠΈΡΠΈΡ ΡΠ΅ΡΡΠΈΡΠΈΠΊΠ°ΡΠ° Π΄ΠΎΠ»ΠΆΠ½Ρ Π±ΡΡΡ ΠΏΡΠΎΠΊΠΎΠ½ΡΡΠΎΠ»ΠΈΡΠΎΠ²Π°Π½Ρ:
Π°) ΡΠ²Π°ΡΠΎΡΠ½ΠΎ-ΡΠ΅Ρ Π½ΠΎΠ»ΠΎΠ³ΠΈΡΠ΅ΡΠΊΠΈΠ΅ ΡΠ²ΠΎΠΉΡΡΠ²Π°;
Π±) ΡΠΎΠΎΡΠ²Π΅ΡΡΡΠ²ΠΈΠ΅ Π½Π°ΠΏΠ»Π°Π²Π»Π΅Π½Π½ΠΎΠ³ΠΎ ΠΌΠ΅ΡΠ°Π»Π»Π° Π»Π΅Π³ΠΈΡΠΎΠ²Π°Π½Π½ΡΡ ΡΠ»Π΅ΠΊΡΡΠΎΠ΄ΠΎΠ² ΡΡΠ΅Π±ΠΎΠ²Π°Π½ΠΈΡΠΌ ΠΌΠ°ΡΠΎΡΠ½ΠΎΠ³ΠΎ ΡΠΎΡΡΠ°Π²Π°.
Π Π΅Π·ΡΠ»ΡΡΠ°ΡΡ ΠΏΡΠΎΠ²Π΅ΡΠΊΠΈ ΡΠ»Π΅ΠΊΡΡΠΎΠ΄ΠΎΠ² Π΄ΠΎΠ»ΠΆΠ½Ρ Π±ΡΡΡ ΠΎΡΠΎΡΠΌΠ»Π΅Π½Ρ ΡΠΎΠΎΡΠ²Π΅ΡΡΡΠ²ΡΡΡΠΈΠΌ Π°ΠΊΡΠΎΠΌ (ΡΠΌ. ΡΠ°Π·Π΄Π΅Π» 21).
ΠΠ΅ΡΠ΅Π΄ Π²ΡΠ΄Π°ΡΠ΅ΠΉ ΡΠ»Π΅ΠΊΡΡΠΎΠ΄ΠΎΠ² ΡΠ²Π°ΡΡΠΈΠΊΡ Π½Π΅ΠΎΠ±Ρ ΠΎΠ΄ΠΈΠΌΠΎ ΡΠ±Π΅Π΄ΠΈΡΡΡΡ Π² ΡΠΎΠΌ, ΡΡΠΎ ΠΎΠ½ΠΈ Π±ΡΠ»ΠΈ ΠΏΡΠΎΠΊΠ°Π»Π΅Π½Ρ ΠΈ ΡΡΠΎΠΊ Π΄Π΅ΠΉΡΡΠ²ΠΈΡ ΠΏΡΠΎΠΊΠ°Π»ΠΊΠΈ Π½Π΅ ΠΈΡΡΠ΅ΠΊ.
ΠΡΠΈΠΌΠ΅ΡΠ°Π½ΠΈΠ΅. ΠΡΠΈ Π½Π°Π»ΠΈΡΠΈΠΈ Π½Π° ΡΡΠΈΠΊΠ΅ΡΠΊΠ°Ρ ΠΏΠ°ΡΠ΅ΠΊ Π½ΠΎΠΌΠ΅ΡΠΎΠ² Π·Π°ΠΌΠ΅ΡΠΎΠ² ΡΠ»Π΅ΠΊΡΡΠΎΠ΄ΠΎΠ² (Π² ΠΏΡΠ΅Π΄Π΅Π»Π°Ρ ΠΎΠ΄Π½ΠΎΠΉ ΠΏΠ°ΡΡΠΈΠΈ) ΡΠ΅ΠΊΠΎΠΌΠ΅Π½Π΄ΡΠ΅ΡΡΡ ΠΏΡΠΎΠ²ΠΎΠ΄ΠΈΡΡ ΡΠΊΠ°Π·Π°Π½Π½ΡΠΉ Π² ΠΏ.5.4.5 ΠΊΠΎΠ½ΡΡΠΎΠ»Ρ ΠΊΠ°ΠΆΠ΄ΠΎΠ³ΠΎ Π·Π°ΠΌΠ΅ΡΠ°.
5.4.6. Π‘Π²Π°ΡΠΎΡΠ½ΠΎ-ΡΠ΅Ρ Π½ΠΎΠ»ΠΎΠ³ΠΈΡΠ΅ΡΠΊΠΈΠ΅ ΡΠ²ΠΎΠΉΡΡΠ²Π° ΡΠ»Π΅ΠΊΡΡΠΎΠ΄ΠΎΠ², ΠΏΡΠ΅Π΄Π½Π°Π·Π½Π°ΡΠ΅Π½Π½ΡΡ Π΄Π»Ρ ΡΠ²Π°ΡΠΊΠΈ ΡΡΡΠ±ΠΎΠΏΡΠΎΠ²ΠΎΠ΄ΠΎΠ² ΠΈΠ· ΡΠ³Π»Π΅ΡΠΎΠ΄ΠΈΡΡΡΡ ΠΈ Π½ΠΈΠ·ΠΊΠΎΠ»Π΅Π³ΠΈΡΠΎΠ²Π°Π½Π½ΡΡ ΡΡΠ°Π»Π΅ΠΉ, Π² ΡΠΎΠΌ ΡΠΈΡΠ»Π΅ Π΄Π»Ρ ΠΏΡΠΈΠ²Π°ΡΠΊΠΈ ΡΡΡΠ± (ΡΡΡΡΠ΅ΡΠΎΠ²) ΠΊ ΠΊΠΎΠ»Π»Π΅ΠΊΡΠΎΡΠ°ΠΌ ΠΈΠ»ΠΈ ΡΡΡΠ±ΠΎΠΏΡΠΎΠ²ΠΎΠ΄Π°ΠΌ, Π½Π΅ΠΎΠ±Ρ ΠΎΠ΄ΠΈΠΌΠΎ ΠΎΠΏΡΠ΅Π΄Π΅Π»ΡΡΡ ΠΏΡΠΈ ΡΠ²Π°ΡΠΊΠ΅ Π² ΠΏΠΎΡΠΎΠ»ΠΎΡΠ½ΠΎΠΌ ΠΏΠΎΠ»ΠΎΠΆΠ΅Π½ΠΈΠΈ ΠΎΠ΄Π½ΠΎΡΡΠΎΡΠΎΠ½Π½Π΅Π³ΠΎ ΡΠ°Π²ΡΠΎΠ²ΠΎΠ³ΠΎ ΠΎΠ±ΡΠ°Π·ΡΠ° ΠΈΠ· Π΄Π²ΡΡ ΠΏΠΎΠ³ΠΎΠ½ΠΎΠ², Π²ΡΡΠ΅Π·Π°Π½Π½ΡΡ ΠΈΠ· ΡΡΡΠ±, ΠΈΠ»ΠΈ Π΄Π²ΡΡ ΠΏΠ»Π°ΡΡΠΈΠ½ ΡΠ°Π·ΠΌΠ΅ΡΠΎΠΌ 180×140 ΠΌΠΌ (ΡΠΈΡ.5.1). Π‘Π²Π°ΡΠΊΡ ΠΏΠΎΠ³ΠΎΠ½ΠΎΠ² Π²ΡΠΏΠΎΠ»Π½ΡΡΡ Π² ΠΎΠ΄ΠΈΠ½ ΡΠ»ΠΎΠΉ.
Π’Π΅Ρ Π½ΠΎΠ»ΠΎΠ³ΠΈΡΠ΅ΡΠΊΠΈΠ΅ ΡΠ²ΠΎΠΉΡΡΠ²Π° ΡΠ»Π΅ΠΊΡΡΠΎΠ΄ΠΎΠ² ΠΌΠΎΠΆΠ½ΠΎ ΠΏΡΠΎΠ²Π΅ΡΠΈΡΡ ΡΠ°ΠΊΠΆΠ΅ ΠΏΡΠΈ ΡΠ²Π°ΡΠΊΠ΅ ΠΏΠΎΡΠΎΠ»ΠΎΡΠ½ΠΎΠ³ΠΎ ΡΡΠ°ΡΡΠΊΠ° ΠΈΠ»ΠΈ Π²ΡΠ΅Π³ΠΎ Π²Π΅ΡΡΠΈΠΊΠ°Π»ΡΠ½ΠΎΠ³ΠΎ ΡΡΡΠΊΠ° ΡΡΡΠ± Π΄ΠΈΠ°ΠΌΠ΅ΡΡΠΎΠΌ 133-159 ΠΌΠΌ Ρ ΡΠΎΠ»ΡΠΈΠ½ΠΎΠΉ ΡΡΠ΅Π½ΠΊΠΈ 10-18 ΠΌΠΌ ΠΈΠ· ΡΠΎΠΎΡΠ²Π΅ΡΡΡΠ²ΡΡΡΠ΅ΠΉ ΡΡΠ°Π»ΠΈ.
Π‘ΠΌ. Π³ΡΠ°ΡΠΈΡΠ΅ΡΠΊΠΈΠΉ ΠΎΠ±ΡΠ΅ΠΊΡ “Π ΠΈΡ.5.1. Π‘Ρ Π΅ΠΌΠ° ΡΠ²Π°ΡΠΊΠΈ ΡΠ°Π²ΡΠΎΠ²ΠΎΠ³ΠΎ ΡΠΎΠ΅Π΄ΠΈΠ½Π΅Π½ΠΈΡ ΠΏΠ»Π°ΡΡΠΈΠ½ (ΠΏΠΎΠ³ΠΎΠ½ΠΎΠ² ΠΈΠ· ΡΡΡΠ±) Π΄Π»Ρ ΠΎΠΏΡΠ΅Π΄Π΅Π»Π΅Π½ΠΈΡ ΡΠ΅Ρ Π½ΠΎΠ»ΠΎΠ³ΠΈΡΠ΅ΡΠΊΠΈΡ ΡΠ²ΠΎΠΉΡΡΠ² ΡΠ»Π΅ΠΊΡΡΠΎΠ΄ΠΎΠ²”
Π‘Π²Π°ΡΠΊΡ Π½ΡΠΆΠ½ΠΎ ΠΏΡΠΎΠΈΠ·Π²ΠΎΠ΄ΠΈΡΡ Ρ ΠΏΠΎΠ΄ΠΎΠ³ΡΠ΅Π²ΠΎΠΌ, Π΅ΡΠ»ΠΈ ΠΎΠ½ ΠΏΡΠ΅Π΄ΡΡΠΌΠΎΡΡΠ΅Π½ Π΄Π»Ρ Π΄Π°Π½Π½ΠΎΠ³ΠΎ ΡΠ²Π°ΡΠ½ΠΎΠ³ΠΎ ΡΠΎΠ΅Π΄ΠΈΠ½Π΅Π½ΠΈΡ ΡΠ΅Ρ Π½ΠΎΠ»ΠΎΠ³ΠΈΡΠ΅ΡΠΊΠΎΠΉ Π΄ΠΎΠΊΡΠΌΠ΅Π½ΡΠ°ΡΠΈΠ΅ΠΉ.
ΠΠΎΡΠ»Π΅ ΡΠ²Π°ΡΠΊΠΈ ΡΠ°Π²ΡΠΎΠ²ΠΎΠ³ΠΎ ΠΎΠ±ΡΠ°Π·ΡΠ° ΡΠΎΠ² ΠΈ ΠΈΠ·Π»ΠΎΠΌ ΠΏΠΎ ΡΠ²Ρ ΠΎΡΠΌΠ°ΡΡΠΈΠ²Π°ΡΡ. ΠΠ»Ρ ΠΎΠ±Π»Π΅Π³ΡΠ΅Π½ΠΈΡ ΡΠ°Π·ΡΡΡΠ΅Π½ΠΈΡ ΠΎΠ±ΡΠ°Π·ΡΠ° ΡΠ»Π΅Π΄ΡΠ΅Ρ ΡΠ΄Π΅Π»Π°ΡΡ Π½Π°Π΄ΡΠ΅Π· ΠΏΠΎ ΡΠ΅ΡΠ΅Π΄ΠΈΠ½Π΅ ΡΠ²Π° ΡΠΎ ΡΡΠΎΡΠΎΠ½Ρ Π²ΡΠΏΡΠΊΠ»ΠΎΡΡΠΈ ΡΠ²Π° Π³Π»ΡΠ±ΠΈΠ½ΠΎΠΉ 1,5-2,0 ΠΌΠΌ.
ΠΠΎΡΠ»Π΅ ΡΠ²Π°ΡΠΊΠΈ ΡΡΡΠΊΠ° ΡΡΡΠ± ΡΠΎΠ² ΠΏΡΠΎΡΠ°ΡΠΈΠ²Π°ΡΡ Π½Π° ΡΠΎΠΊΠ°ΡΠ½ΠΎΠΌ ΡΡΠ°Π½ΠΊΠ΅ ΡΠΎ ΡΠ½ΡΡΠΈΠ΅ΠΌ ΡΠ»ΠΎΡ ΡΠΎΠ»ΡΠΈΠ½ΠΎΠΉ Π΄ΠΎ 0,5 ΠΌΠΌ ΠΈΠ»ΠΈ ΠΏΠΎΠ΄Π²Π΅ΡΠ³Π°ΡΡ ΡΠ°Π΄ΠΈΠΎΠ³ΡΠ°ΡΠΈΡΠ΅ΡΠΊΠΎΠΌΡ ΠΊΠΎΠ½ΡΡΠΎΠ»Ρ Π΄Π»Ρ ΠΎΠΏΡΠ΅Π΄Π΅Π»Π΅Π½ΠΈΡ ΡΠΏΠ»ΠΎΡΠ½ΠΎΡΡΠΈ ΠΌΠ΅ΡΠ°Π»Π»Π°.
5.4.7. Π’ΠΎΠ»ΡΠΈΠ½Ρ ΠΏΠ»Π°ΡΡΠΈΠ½ (ΠΏΠΎΠ³ΠΎΠ½ΠΎΠ²) ΠΈ ΠΊΠ°ΡΠ΅Ρ ΡΠ²Π° ΠΏΡΠΈ ΡΠ²Π°ΡΠΊΠ΅ ΡΠ°Π²ΡΠΎΠ²ΡΡ ΠΎΠ±ΡΠ°Π·ΡΠΎΠ² Π²ΡΠ±ΠΈΡΠ°ΡΡ Π² Π·Π°Π²ΠΈΡΠΈΠΌΠΎΡΡΠΈ ΠΎΡ Π΄ΠΈΠ°ΠΌΠ΅ΡΡΠ° ΡΠ»Π΅ΠΊΡΡΠΎΠ΄Π°:
ΠΠΈΠ°ΠΌΠ΅ΡΡ ΡΠ»Π΅ΠΊΡΡΠΎΠ΄Π°, ΠΠΎ 2 Π‘Π²ΡΡΠ΅ 2 Π΄ΠΎ 3 Π‘Π²ΡΡΠ΅ 3 Π΄ΠΎ 4 Π‘Π²ΡΡΠ΅ 4
ΠΌΠΌ Π²ΠΊΠ»ΡΡΠΈΡΠ΅Π»ΡΠ½ΠΎ Π²ΠΊΠ»ΡΡΠΈΡΠ΅Π»ΡΠ½ΠΎ Π²ΠΊΠ»ΡΡΠΈΡΠ΅Π»ΡΠ½ΠΎ
Π’ΠΎΠ»ΡΠΈΠ½Π° ΠΏΠ»Π°ΡΡΠΈΠ½Ρ, 3-5 6-10 10-16 14-20
ΠΌΠΌ
ΠΠ°ΡΠ΅Ρ ΡΠ²Π°, ΠΌΠΌ 2-3 4-5 6-8 8-10
5.4.8. ΠΠ»Π°ΡΡΠΈΠ½Ρ ΠΈ ΠΏΠΎΠ³ΠΎΠ½Ρ ΠΈΠ· ΡΡΡΠ± Π΄Π»Ρ ΠΏΡΠΎΠ²Π΅ΡΠΊΠΈ ΡΠ΅Ρ Π½ΠΎΠ»ΠΎΠ³ΠΈΡΠ΅ΡΠΊΠΈΡ ΡΠ²ΠΎΠΉΡΡΠ² ΡΠ»Π΅ΠΊΡΡΠΎΠ΄ΠΎΠ² Π΄ΠΎΠ»ΠΆΠ½Ρ Π±ΡΡΡ ΠΈΠ·Π³ΠΎΡΠΎΠ²Π»Π΅Π½Ρ ΠΈΠ· ΡΡΠ°Π»ΠΈ ΡΠΎΠΉ ΠΌΠ°ΡΠΊΠΈ, Π΄Π»Ρ ΡΠ²Π°ΡΠΊΠΈ ΠΊΠΎΡΠΎΡΠΎΠΉ ΠΌΠΎΠ³ΡΡ Π±ΡΡΡ ΠΈΡΠΏΠΎΠ»ΡΠ·ΠΎΠ²Π°Π½Ρ ΠΏΡΠΎΠ²Π΅ΡΡΠ΅ΠΌΡΠ΅ ΡΠ»Π΅ΠΊΡΡΠΎΠ΄Ρ Π² ΡΠΎΠΎΡΠ²Π΅ΡΡΡΠ²ΠΈΠΈ ΡΠ΄Π°Π½Π½ΡΠΌΠΈ ΡΠ°Π±Π».4.1 ΠΈΠ»ΠΈ 4.2.
5.4.9. Π‘Π²Π°ΡΠΎΡΠ½ΠΎ-ΡΠ΅Ρ Π½ΠΎΠ»ΠΎΠ³ΠΈΡΠ΅ΡΠΊΠΈΠ΅ ΡΠ²ΠΎΠΉΡΡΠ²Π° ΡΠ»Π΅ΠΊΡΡΠΎΠ΄ΠΎΠ², ΠΏΡΠ΅Π΄Π½Π°Π·Π½Π°ΡΠ΅Π½Π½ΡΡ Π΄Π»Ρ ΡΠ²Π°ΡΠΊΠΈ ΡΡΡΠ± ΠΏΠΎΠ²Π΅ΡΡ Π½ΠΎΡΡΠ΅ΠΉ Π½Π°Π³ΡΠ΅Π²Π° ΠΊΠΎΡΠ»ΠΎΠ², Π½Π΅ΠΎΠ±Ρ ΠΎΠ΄ΠΈΠΌΠΎ ΠΏΡΠΎΠ²Π΅ΡΠΈΡΡ ΠΏΡΡΠ΅ΠΌ ΡΠ²Π°ΡΠΊΠΈ Π½Π΅ ΠΌΠ΅Π½Π΅Π΅ ΡΡΠ΅Ρ ΠΏΡΠΎΠ±Π½ΡΡ Π½Π΅ΠΏΠΎΠ²ΠΎΡΠΎΡΠ½ΡΡ ΡΡΡΠΊΠΎΠ² ΡΡΡΠ± ΠΈΠ· ΡΡΠ°Π»Π΅ΠΉ ΡΠΎΠΎΡΠ²Π΅ΡΡΡΠ²ΡΡΡΠΈΡ ΠΌΠ°ΡΠΎΠΊ Ρ ΠΏΠΎΡΠ»Π΅Π΄ΡΡΡΠΈΠΌ ΠΊΠΎΠ½ΡΡΠΎΠ»Π΅ΠΌ ΡΠΏΠ»ΠΎΡΠ½ΠΎΡΡΠΈ ΡΠ²Π° Ρ ΠΏΠΎΠΌΠΎΡΡΡ ΡΠ°Π΄ΠΈΠΎΠ³ΡΠ°ΡΠΈΠΈ ΠΈΠ»ΠΈ ΠΏΡΠΎΡΠΎΡΠΊΠΈ ΡΡΡΠΊΠΎΠ² Π½Π° ΡΠΎΠΊΠ°ΡΠ½ΠΎΠΌ ΡΡΠ°Π½ΠΊΠ΅ ΡΠΎ ΡΠ½ΡΡΠΈΠ΅ΠΌ ΡΠ»ΠΎΡ Π½Π΅ Π±ΠΎΠ»Π΅Π΅ 0,5 ΠΌΠΌ Π΄Π»Ρ ΠΎΠΏΡΠ΅Π΄Π΅Π»Π΅Π½ΠΈΡ ΡΠΏΠ»ΠΎΡΠ½ΠΎΡΡΠΈ ΠΌΠ΅ΡΠ°Π»Π»Π° ΡΠ²Π°.
5.4.10. Π‘ΠΏΠ»ΠΎΡΠ½ΠΎΡΡΡ ΠΌΠ΅ΡΠ°Π»Π»Π° ΡΠ²Π°, ΠΎΠΏΡΠ΅Π΄Π΅Π»ΡΠ΅ΠΌΠ°Ρ ΡΠΎΠ³Π»Π°ΡΠ½ΠΎ ΠΏΠΏ.5.4.6 ΠΈ 5.4.9, Π΄ΠΎΠ»ΠΆΠ½Π° ΠΎΡΠ²Π΅ΡΠ°ΡΡ ΡΡΠ΅Π±ΠΎΠ²Π°Π½ΠΈΡΠΌ, ΠΏΡΠΈΠ²Π΅Π΄Π΅Π½Π½ΡΠΌ Π² ΡΠ°Π±Π».5 ΠΠΠ‘Π’ 9466 (Ρ ΠΈΠ·ΠΌΠ΅Π½Π΅Π½ΠΈΠ΅ΠΌ N 1).
5.4.11. Π‘Π²Π°ΡΠΎΡΠ½ΠΎ-ΡΠ΅Ρ Π½ΠΎΠ»ΠΎΠ³ΠΈΡΠ΅ΡΠΊΠΈΠ΅ ΡΠ²ΠΎΠΉΡΡΠ²Π° ΡΠ»Π΅ΠΊΡΡΠΎΠ΄ΠΎΠ² Π΄ΠΎΠ»ΠΆΠ½Ρ ΡΠ΄ΠΎΠ²Π»Π΅ΡΠ²ΠΎΡΡΡΡ ΡΡΠ΅Π±ΠΎΠ²Π°Π½ΠΈΡΠΌ ΠΠΠ‘Π’ 9466. ΠΡΠ½ΠΎΠ²Π½ΡΠ΅ ΠΈΠ· ΡΡΠΈΡ ΡΡΠ΅Π±ΠΎΠ²Π°Π½ΠΈΠΉ ΡΠ»Π΅Π΄ΡΡΡΠΈΠ΅:
Π΄ΡΠ³Π° Π»Π΅Π³ΠΊΠΎ Π·Π°ΠΆΠΈΠ³Π°Π΅ΡΡΡ ΠΈ ΡΡΠ°Π±ΠΈΠ»ΡΠ½ΠΎ Π³ΠΎΡΠΈΡ;
ΠΏΠΎΠΊΡΡΡΠΈΠ΅ ΠΏΠ»Π°Π²ΠΈΡΡΡ ΡΠ°Π²Π½ΠΎΠΌΠ΅ΡΠ½ΠΎ Π±Π΅Π· ΡΡΠ΅Π·ΠΌΠ΅ΡΠ½ΠΎΠ³ΠΎ ΡΠ°Π·Π±ΡΡΠ·Π³ΠΈΠ²Π°Π½ΠΈΡ, ΠΎΡΠ²Π°Π»ΠΈΠ²Π°Π½ΠΈΡ ΠΊΡΡΠΊΠΎΠ² ΠΈ ΠΎΠ±ΡΠ°Π·ΠΎΠ²Π°Π½ΠΈΡ “ΠΊΠΎΠ·ΡΡΡΠΊΠ°”, ΠΏΡΠ΅ΠΏΡΡΡΡΠ²ΡΡΡΠΈΡ Π½ΠΎΡΠΌΠ°Π»ΡΠ½ΠΎΠΌΡ ΠΏΠ»Π°Π²Π»Π΅Π½ΠΈΡ ΡΠ»Π΅ΠΊΡΡΠΎΠ΄Π° Π²ΠΎ Π²ΡΠ΅Ρ ΠΏΡΠΎΡΡΡΠ°Π½ΡΡΠ²Π΅Π½Π½ΡΡ ΠΏΠΎΠ»ΠΎΠΆΠ΅Π½ΠΈΡΡ ;
ΠΎΠ±ΡΠ°Π·ΡΡΡΠΈΠΉΡΡ ΠΏΡΠΈ ΡΠ²Π°ΡΠΊΠ΅ ΡΠ»Π°ΠΊ ΠΎΠ±Π΅ΡΠΏΠ΅ΡΠΈΠ²Π°Π΅Ρ ΠΏΡΠ°Π²ΠΈΠ»ΡΠ½ΠΎΠ΅ ΡΠΎΡΠΌΠΈΡΠΎΠ²Π°Π½ΠΈΠ΅ ΡΠ²Π° ΠΈ Π»Π΅Π³ΠΊΠΎ ΡΠ΄Π°Π»ΡΠ΅ΡΡΡ ΠΏΠΎΡΠ»Π΅ ΠΎΡ Π»Π°ΠΆΠ΄Π΅Π½ΠΈΡ;
Π² ΠΌΠ΅ΡΠ°Π»Π»Π΅ ΡΠ²Π° (Π½Π°ΠΏΠ»Π°Π²Π»Π΅Π½Π½ΠΎΠΌ ΠΌΠ΅ΡΠ°Π»Π»Π΅) Π½Π΅Ρ ΡΡΠ΅ΡΠΈΠ½.
ΠΠ±ΡΠ°Π·ΠΎΠ²Π°Π½ΠΈΠ΅ “ΠΊΠΎΠ·ΡΡΡΠΊΠ°” ΠΈΠ· ΠΏΠΎΠΊΡΡΡΠΈΡ ΡΠ°Π·ΠΌΠ΅ΡΠΎΠΌ Π±ΠΎΠ»Π΅Π΅ 3 ΠΌΠΌ ΠΈ ΠΎΡΠ²Π°Π»ΠΈΠ²Π°Π½ΠΈΠ΅ ΠΊΡΡΠΊΠΎΠ² Π½Π΅ ΡΠ°ΡΠΏΠ»Π°Π²ΠΈΠ²ΡΠ΅Π³ΠΎΡΡ ΠΏΠΎΠΊΡΡΡΠΈΡ ΠΎΡ ΡΡΠ΅ΡΠΆΠ½Ρ ΡΠ²Π»ΡΡΡΡΡ Π±ΡΠ°ΠΊΠΎΠ²ΠΎΡΠ½ΡΠΌΠΈ ΠΏΡΠΈΠ·Π½Π°ΠΊΠ°ΠΌΠΈ.
ΠΠ»Ρ ΠΎΠΏΡΠ΅Π΄Π΅Π»Π΅Π½ΠΈΡ ΡΠ°Π·ΠΌΠ΅ΡΠ° “ΠΊΠΎΠ·ΡΡΡΠΊΠ°” ΠΈ ΠΏΡΠΎΡΠ½ΠΎΡΡΠΈ ΠΏΠΎΠΊΡΡΡΠΈΡ ΠΎΡΠ±ΠΈΡΠ°Π΅ΡΡΡ 10-12 ΡΠ»Π΅ΠΊΡΡΠΎΠ΄ΠΎΠ² ΠΈΠ· 5-6 ΠΏΠ°ΡΠ΅ΠΊ ΠΈ ΠΏΡΠΎΠΈΠ·Π²ΠΎΠ΄ΠΈΡΡΡ ΠΈΡ ΡΠ°ΡΠΏΠ»Π°Π²Π»Π΅Π½ΠΈΠ΅ Π² Π²Π΅ΡΡΠΈΠΊΠ°Π»ΡΠ½ΠΎΠΌ ΠΏΠΎΠ»ΠΎΠΆΠ΅Π½ΠΈΠΈ Ρ ΡΠ³Π»ΠΎΠΌ Π½Π°ΠΊΠ»ΠΎΠ½Π° ΡΠ»Π΅ΠΊΡΡΠΎΠ΄Π° ΠΊ ΡΠ²Ρ 50-60Β°. Π Π°Π·ΠΌΠ΅Ρ “ΠΊΠΎΠ·ΡΡΡΠΊΠ°” ΠΈΠ·ΠΌΠ΅ΡΡΠ΅ΡΡΡ ΠΎΡ ΡΠΎΡΡΠ° ΡΡΠ΅ΡΠΆΠ½Ρ ΡΠ»Π΅ΠΊΡΡΠΎΠ΄Π° Π΄ΠΎ Π½Π°ΠΈΠ±ΠΎΠ»Π΅Π΅ ΡΠ΄Π°Π»Π΅Π½Π½ΠΎΠΉ ΡΠ°ΡΡΠΈ ΠΎΠΏΠ»Π°Π²ΠΈΠ²ΡΠ΅Π³ΠΎΡΡ ΠΏΠΎΠΊΡΡΡΠΈΡ.
5.4.12. ΠΡΠΈ Π½Π΅ΡΠ΄ΠΎΠ²Π»Π΅ΡΠ²ΠΎΡΠΈΡΠ΅Π»ΡΠ½ΡΡ ΡΠ²Π°ΡΠΎΡΠ½ΠΎ-ΡΠ΅Ρ Π½ΠΎΠ»ΠΎΠ³ΠΈΡΠ΅ΡΠΊΠΈΡ ΡΠ²ΠΎΠΉΡΡΠ²Π°Ρ ΡΠ»Π΅ΠΊΡΡΠΎΠ΄ΠΎΠ² ΠΎΠ½ΠΈ Π΄ΠΎΠ»ΠΆΠ½Ρ Π±ΡΡΡ ΠΏΠΎΠ²ΡΠΎΡΠ½ΠΎ ΠΏΡΠΎΠΊΠ°Π»Π΅Π½Ρ. ΠΡΠ»ΠΈ ΠΏΠΎΡΠ»Π΅ ΡΡΠΎΠ³ΠΎ ΠΏΡΠΈ ΠΏΡΠΎΠ²Π΅ΡΠΊΠ΅ ΡΠ²Π°ΡΠΎΡΠ½ΠΎ-ΡΠ΅Ρ Π½ΠΎΠ»ΠΎΠ³ΠΈΡΠ΅ΡΠΊΠΈΡ ΡΠ²ΠΎΠΉΡΡΠ² ΠΏΠΎΠ»ΡΡΠ΅Π½Ρ Π½Π΅ΡΠ΄ΠΎΠ²Π»Π΅ΡΠ²ΠΎΡΠΈΡΠ΅Π»ΡΠ½ΡΠ΅ ΡΠ΅Π·ΡΠ»ΡΡΠ°ΡΡ, ΡΠΎ Π΄Π°Π½Π½Π°Ρ ΠΏΠ°ΡΡΠΈΡ ΡΠ»Π΅ΠΊΡΡΠΎΠ΄ΠΎΠ² Π±ΡΠ°ΠΊΡΠ΅ΡΡΡ, Π½Π° Π½Π΅Π΅ ΠΎΡΠΎΡΠΌΠ»ΡΠ΅ΡΡΡ Π°ΠΊΡ-ΡΠ΅ΠΊΠ»Π°ΠΌΠ°ΡΠΈΡ, ΠΊΠΎΡΠΎΡΡΠΉ Π½Π°ΠΏΡΠ°Π²Π»ΡΠ΅ΡΡΡ Π·Π°Π²ΠΎΠ΄Ρ-ΠΈΠ·Π³ΠΎΡΠΎΠ²ΠΈΡΠ΅Π»Ρ ΠΈ Π² ΡΠ²ΠΎΡ Π²ΡΡΠ΅ΡΡΠΎΡΡΡΡ ΠΎΡΠ³Π°Π½ΠΈΠ·Π°ΡΠΈΡ.
5.4.13. ΠΠ»Ρ ΠΏΡΠΎΠ²Π΅ΡΠΊΠΈ ΡΠΎΠΎΡΠ²Π΅ΡΡΡΠ²ΠΈΡ Π»Π΅Π³ΠΈΡΠΎΠ²Π°Π½Π½ΡΡ ΡΠ»Π΅ΠΊΡΡΠΎΠ΄ΠΎΠ² ΠΌΠ°ΡΠΎΡΠ½ΠΎΠΌΡ ΡΠΎΡΡΠ°Π²Ρ Π½Π° ΠΌΠ°Π»ΠΎΡΠ³Π»Π΅ΡΠΎΠ΄ΠΈΡΡΡΡ ΠΏΠ»Π°ΡΡΠΈΠ½ΠΊΡ Π½Π°ΠΏΠ»Π°Π²Π»ΡΡΡ ΡΡΠΈ Π±ΠΎΠ±ΡΡΠΊΠΈ Π²ΡΡΠΎΡΠΎΠΉ ΠΈ Π΄ΠΈΠ°ΠΌΠ΅ΡΡΠΎΠΌ Ρ ΠΎΡΠ½ΠΎΠ²Π°Π½ΠΈΡ, ΡΠ°Π²Π½ΡΠΌΠΈ Π½Π΅ ΠΌΠ΅Π½Π΅Π΅ ΡΠ΅ΠΌ ΡΠ΅ΡΡΡΠ΅ΠΌ Π΄ΠΈΠ°ΠΌΠ΅ΡΡΠ°ΠΌ ΠΊΠΎΠ½ΡΡΠΎΠ»ΠΈΡΡΠ΅ΠΌΠΎΠ³ΠΎ ΡΠ»Π΅ΠΊΡΡΠΎΠ΄Π°. ΠΠ· ΡΠ°Π·Π½ΡΡ ΠΏΠ°ΡΠ΅ΠΊ Π·Π°ΠΌΠ΅ΡΠ° Π±Π΅ΡΡΡ ΡΡΠΈ ΡΠ»Π΅ΠΊΡΡΠΎΠ΄Π°, ΠΏΡΠΈ ΡΡΠΎΠΌ ΠΊΠ°ΠΆΠ΄ΡΡ Π±ΠΎΠ±ΡΡΠΊΡ Π½Π°ΠΏΠ»Π°Π²Π»ΡΡΡ ΠΎΠ΄Π½ΠΈΠΌ ΡΠ»Π΅ΠΊΡΡΠΎΠ΄ΠΎΠΌ. ΠΠ΅ΡΡ Π½ΡΡ ΠΏΠ»ΠΎΡΠ°Π΄ΠΊΡ Π±ΠΎΠ±ΡΡΠΊΠΈ Π·Π°ΡΠΈΡΠ°ΡΡ Π΄ΠΎ ΠΌΠ΅ΡΠ°Π»Π»ΠΈΡΠ΅ΡΠΊΠΎΠ³ΠΎ Π±Π»Π΅ΡΠΊΠ° ΠΈ ΡΡΠΈΠ»ΠΎΡΠΊΠΎΠΏΠΈΡΠΎΠ²Π°Π½ΠΈΠ΅ΠΌ ΠΎΠΏΡΠ΅Π΄Π΅Π»ΡΡΡ ΡΠΎΠ΄Π΅ΡΠΆΠ°Π½ΠΈΠ΅ ΡΠ»Π΅ΠΌΠ΅Π½ΡΠΎΠ², Π²Ρ ΠΎΠ΄ΡΡΠΈΡ Π² ΠΌΠ°ΡΠΎΡΠ½ΡΠΉ ΡΠΎΡΡΠ°Π² (ΡΠΌ. ΠΏΠΎΠ΄ΡΠ°Π·Π΄Π΅Π» 18.2). ΠΡΠ»ΠΈ ΠΏΡΠΈ ΠΏΡΠΎΠ²Π΅ΡΠΊΠ΅ Π²ΡΡΠ²Π»Π΅Π½ΠΎ Π½Π΅ΡΠΎΠΎΡΠ²Π΅ΡΡΡΠ²ΠΈΠ΅ Π½Π°ΠΏΠ»Π°Π²Π»Π΅Π½Π½ΠΎΠ³ΠΎ ΠΌΠ΅ΡΠ°Π»Π»Π° ΠΌΠ°ΡΠΎΡΠ½ΠΎΠΌΡ ΡΠΎΡΡΠ°Π²Ρ (Ρ ΠΎΡΡ Π±Ρ ΠΎΠ΄Π½ΠΎΠ³ΠΎ ΠΈΠ· ΡΡΠ΅Ρ ΠΈΡΠΏΡΡΠ°Π½Π½ΡΡ ΡΠ»Π΅ΠΊΡΡΠΎΠ΄ΠΎΠ²), Π·Π°ΠΌΠ΅Ρ Π΄ΠΎΠ»ΠΆΠ΅Π½ Π±ΡΡΡ ΠΏΠΎΠ΄Π²Π΅ΡΠ³Π½ΡΡ ΠΏΠΎΠ²ΡΠΎΡΠ½ΠΎΠΌΡ ΡΡΠΈΠ»ΠΎΡΠΊΠΎΠΏΠΈΡΠΎΠ²Π°Π½ΠΈΡ. ΠΡΠΈ ΠΏΠΎΠ²ΡΠΎΡΠ½ΠΎΠΌ ΠΊΠΎΠ½ΡΡΠΎΠ»Π΅ ΠΏΡΠΎΠ²Π΅ΡΡΡΡ ΠΏΠΎ 10 ΡΠ»Π΅ΠΊΡΡΠΎΠ΄ΠΎΠ² ΠΊΠ°ΠΆΠ΄ΠΎΠ³ΠΎ Π·Π°ΠΌΠ΅ΡΠ°, ΡΠ΅Π·ΡΠ»ΡΡΠ°ΡΡ ΠΈΡΠΏΡΡΠ°Π½ΠΈΠΉ ΠΊΠΎΡΠΎΡΡΡ Π±ΡΠ»ΠΈ Π½Π΅ΡΠ΄ΠΎΠ²Π»Π΅ΡΠ²ΠΎΡΠΈΡΠ΅Π»ΡΠ½ΡΠΌΠΈ.
ΠΡΠ΅ ΡΠ»Π΅ΠΊΡΡΠΎΠ΄Ρ Π½Π΅ΠΎΠ±Ρ ΠΎΠ΄ΠΈΠΌΠΎ ΠΎΡΠ±ΠΈΡΠ°ΡΡ ΠΈΠ· ΡΠ°Π·Π½ΡΡ ΠΏΠ°ΡΠ΅ΠΊ ΠΊΠ°ΠΆΠ΄ΠΎΠ³ΠΎ Π·Π°ΠΌΠ΅ΡΠ°. ΠΠΎΡΠ»Π΅ ΠΏΠΎΠ²ΡΠΎΡΠ½ΠΎΠ³ΠΎ ΡΡΠΈΠ»ΠΎΡΠΊΠΎΠΏΠΈΡΠΎΠ²Π°Π½ΠΈΡ Π±ΡΠ°ΠΊΡΡΡ ΡΠ»Π΅ΠΊΡΡΠΎΠ΄Ρ ΡΠΎΠ»ΡΠΊΠΎ ΡΠ΅Ρ Π·Π°ΠΌΠ΅ΡΠΎΠ², Π½Π° ΠΊΠΎΡΠΎΡΡΡ ΠΏΠΎΠ»ΡΡΠ΅Π½Ρ Π½Π΅ΡΠ΄ΠΎΠ²Π»Π΅ΡΠ²ΠΎΡΠΈΡΠ΅Π»ΡΠ½ΡΠ΅ ΡΠ΅Π·ΡΠ»ΡΡΠ°ΡΡ. ΠΡΠ»ΠΈ ΠΏΡΠΈ ΠΏΡΠΎΠ²Π΅ΡΠΊΠ΅ Π² ΠΎΡΠ΄Π΅Π»ΡΠ½ΡΡ Π·Π°ΠΌΠ΅ΡΠ°Ρ Π²ΡΡΡΠ΅ΡΠ°ΡΡΡΡ ΡΠ΄ΠΎΠ²Π»Π΅ΡΠ²ΠΎΡΠΈΡΠ΅Π»ΡΠ½ΡΠ΅ ΠΈ Π½Π΅ΡΠ΄ΠΎΠ²Π»Π΅ΡΠ²ΠΎΡΠΈΡΠ΅Π»ΡΠ½ΡΠ΅ ΡΠ΅Π·ΡΠ»ΡΡΠ°ΡΡ, Π±ΡΠ°ΠΊΡΡΡ Π²ΡΡ ΠΊΠΎΠ½ΡΡΠΎΠ»ΠΈΡΡΠ΅ΠΌΡΡ ΠΏΠ°ΡΡΠΈΡ ΡΠ»Π΅ΠΊΡΡΠΎΠ΄ΠΎΠ².
Π‘ΡΠΈΠ»ΠΎΡΠΊΠΎΠΏΠΈΡΠ΅ΡΠΊΠΈΠΉ ΠΊΠΎΠ½ΡΡΠΎΠ»Ρ ΠΌΠΎΠΆΠ΅Ρ Π±ΡΡΡ Π·Π°ΠΌΠ΅Π½Π΅Π½ ΠΊΠΎΠ»ΠΈΡΠ΅ΡΡΠ²Π΅Π½Π½ΡΠΌ Ρ ΠΈΠΌΠΈΡΠ΅ΡΠΊΠΈΠΌ ΠΈΠ»ΠΈ ΡΠΏΠ΅ΠΊΡΡΠ°Π»ΡΠ½ΡΠΌ Π°Π½Π°Π»ΠΈΠ·ΠΎΠΌ Π²Π΅ΡΡ Π½Π΅ΠΉ ΡΠ°ΡΡΠΈ Π½Π°ΠΏΠ»Π°Π²ΠΊΠΈ.
5.4.14. ΠΡΠΈ Π½Π΅ΠΏΠΎΠ»Π½ΠΎΡΠ΅ Π΄Π°Π½Π½ΡΡ Π² ΡΠ΅ΡΡΠΈΡΠΈΠΊΠ°ΡΠ΅ ΠΈΠ»ΠΈ ΡΠΎΠΌΠ½Π΅Π½ΠΈΠΈ Π² ΠΊΠ°ΡΠ΅ΡΡΠ²Π΅ ΡΠ»Π΅ΠΊΡΡΠΎΠ΄ΠΎΠ², ΠΏΠΎΠΌΠΈΠΌΠΎ ΠΏΡΠΎΠ²Π΅ΡΠΊΠΈ ΡΠ²Π°ΡΠΎΡΠ½ΠΎ-ΡΠ΅Ρ Π½ΠΎΠ»ΠΎΠ³ΠΈΡΠ΅ΡΠΊΠΈΡ ΡΠ²ΠΎΠΉΡΡΠ², ΠΎΠΏΡΠ΅Π΄Π΅Π»ΡΡΡ Ρ ΠΈΠΌΠΈΡΠ΅ΡΠΊΠΈΠΉ ΡΠΎΡΡΠ°Π² ΠΈ (ΠΈΠ»ΠΈ) ΠΌΠ΅Ρ Π°Π½ΠΈΡΠ΅ΡΠΊΠΈΠ΅ ΡΠ²ΠΎΠΉΡΡΠ²Π° Π½Π°ΠΏΠ»Π°Π²Π»Π΅Π½Π½ΠΎΠ³ΠΎ ΠΌΠ΅ΡΠ°Π»Π»Π° (ΠΌΠ΅ΡΠ°Π»Π»Π° ΡΠ²Π°) ΠΏΠ°ΡΡΠΈΠΈ ΡΠ»Π΅ΠΊΡΡΠΎΠ΄ΠΎΠ².
ΠΠ»Ρ ΡΡΠΎΠ³ΠΎ Π½Π΅ΠΎΠ±Ρ ΠΎΠ΄ΠΈΠΌΠΎ ΡΠ²Π°ΡΠΈΡΡ Π²ΡΡΡΠΊ Π΄Π²Π΅ ΠΏΠ»Π°ΡΡΠΈΠ½Ρ (ΠΈΠ»ΠΈ Π΄Π²Π° ΠΏΠΎΠ³ΠΎΠ½Π°) ΡΠ°Π·ΠΌΠ΅ΡΠΎΠΌ 350×110 ΠΌΠΌ, ΡΠΎΠ»ΡΠΈΠ½ΠΎΠΉ 12-18 ΠΌΠΌ ΠΈΠ· ΡΠΎΠΎΡΠ²Π΅ΡΡΡΠ²ΡΡΡΠ΅ΠΉ ΡΡΠ°Π»ΠΈ; ΠΏΠΎΠ³ΠΎΠ½Ρ Π²ΡΡΠ΅Π·Π°ΡΡ ΠΈΠ· ΡΡΡΠ±Ρ Π΄ΠΈΠ°ΠΌΠ΅ΡΡΠΎΠΌ Π±ΠΎΠ»Π΅Π΅ 150 ΠΌΠΌ.
ΠΠ΅Ρ Π°Π½ΠΈΡΠ΅ΡΠΊΠΈΠ΅ ΡΠ²ΠΎΠΉΡΡΠ²Π° ΠΈ Ρ ΠΈΠΌΠΈΡΠ΅ΡΠΊΠΈΠΉ ΡΠΎΡΡΠ°Π² Π½Π°ΠΏΠ»Π°Π²Π»Π΅Π½Π½ΠΎΠ³ΠΎ ΠΌΠ΅ΡΠ°Π»Π»Π° ΡΠ»Π΅ΠΊΡΡΠΎΠ΄ΠΎΠ² ΡΠΈΠΏΠΎΠ² Π-09Π₯1Π ΠΈ Π-09Π₯1ΠΠ€ ΠΌΠΎΠΆΠ½ΠΎ ΡΠ°ΠΊΠΆΠ΅ ΠΎΠΏΡΠ΅Π΄Π΅Π»ΡΡΡ Π½Π° ΠΏΠ»Π°ΡΡΠΈΠ½Π°Ρ ΠΈΠ· ΡΠ³Π»Π΅ΡΠΎΠ΄ΠΈΡΡΠΎΠΉ ΡΡΠ°Π»ΠΈ ΡΠΎΠ»ΡΠΈΠ½ΠΎΠΉ 12-18 ΠΌΠΌ, ΠΏΡΠ΅Π΄Π²Π°ΡΠΈΡΠ΅Π»ΡΠ½ΠΎ Π½Π°ΠΏΠ»Π°Π²ΠΈΠ² ΠΈΡΠΏΡΡΡΠ΅ΠΌΡΠΌΠΈ ΡΠ»Π΅ΠΊΡΡΠΎΠ΄Π°ΠΌΠΈ Π½Π° ΡΠ²Π°ΡΠΈΠ²Π°Π΅ΠΌΡΠ΅ ΠΊΡΠΎΠΌΠΊΠΈ ΡΡΠΈ ΡΠ»ΠΎΡ ΠΎΠ±ΡΠ΅ΠΉ ΡΠΎΠ»ΡΠΈΠ½ΠΎΠΉ Π½Π΅ ΠΌΠ΅Π½Π΅Π΅ 10 ΠΌΠΌ. Π§ΡΠΎΠ±Ρ ΠΈΠ·Π³ΠΎΡΠΎΠ²ΠΈΡΡ ΠΎΠ±ΡΠ°Π·ΡΡ Π΄Π»Ρ ΠΌΠ΅Ρ Π°Π½ΠΈΡΠ΅ΡΠΊΠΈΡ ΠΈΡΠΏΡΡΠ°Π½ΠΈΠΉ Π½Π°ΠΏΠ»Π°Π²Π»Π΅Π½Π½ΠΎΠ³ΠΎ ΠΌΠ΅ΡΠ°Π»Π»Π° Π°ΡΡΡΠ΅Π½ΠΈΡΠ½ΡΠΌΠΈ ΡΠ»Π΅ΠΊΡΡΠΎΠ΄Π°ΠΌΠΈ, ΡΠ»Π΅Π΄ΡΠ΅Ρ ΡΠ²Π°ΡΠΈΡΡ Π²ΡΡΡΠΊ Π΄Π²Π΅ ΠΏΠ»Π°ΡΡΠΈΠ½Ρ (ΠΈΠ»ΠΈ Π΄Π²Π° ΠΏΠΎΠ³ΠΎΠ½Π°), Π²ΡΡΠ΅Π·Π°Π½Π½ΡΠ΅ ΠΈΠ· Π»ΠΈΡΡΠΎΠ² (ΠΈΠ»ΠΈ ΡΡΡΠ±) ΡΠΎΠΉ ΡΡΠ°Π»ΠΈ, Π΄Π»Ρ ΡΠ²Π°ΡΠΊΠΈ ΠΊΠΎΡΠΎΡΠΎΠΉ ΠΎΠ½ΠΈ ΠΏΡΠ΅Π΄Π½Π°Π·Π½Π°ΡΠ΅Π½Ρ. ΠΠ»Π°ΡΡΠΈΠ½Ρ ΡΠ²Π°ΡΠΈΠ²Π°ΡΡ ΠΏΠΎ ΡΠ΅Ρ Π½ΠΎΠ»ΠΎΠ³ΠΈΠΈ, ΡΠ΅ΠΊΠΎΠΌΠ΅Π½Π΄ΠΎΠ²Π°Π½Π½ΠΎΠΉ Π΄Π»Ρ Π΄Π°Π½Π½ΠΎΠΉ ΡΡΠ°Π»ΠΈ Π½Π°ΡΡΠΎΡΡΠΈΠΌ Π Π.
ΠΠ· ΡΠ²Π°ΡΠ½ΠΎΠ³ΠΎ ΡΠΎΠ΅Π΄ΠΈΠ½Π΅Π½ΠΈΡ (ΡΠΈΡ.5.2) Π½Π΅ΠΎΠ±Ρ ΠΎΠ΄ΠΈΠΌΠΎ ΠΈΠ·Π³ΠΎΡΠΎΠ²ΠΈΡΡ ΡΠΎΠ³Π»Π°ΡΠ½ΠΎ ΠΠΠ‘Π’ 6996 ΡΡΠΈ ΠΎΠ±ΡΠ°Π·ΡΠ° Π΄Π»Ρ ΠΈΡΠΏΡΡΠ°Π½ΠΈΡ Π½Π° ΡΠ΄Π°ΡΠ½ΡΠΉ ΠΈΠ·Π³ΠΈΠ± ΠΈ ΡΡΠΈ – Π΄Π»Ρ ΠΈΡΠΏΡΡΠ°Π½ΠΈΡ Π½Π° ΡΠ°ΡΡΡΠΆΠ΅Π½ΠΈΠ΅, ΡΡΠΎΠ±Ρ ΠΎΠΏΡΠ΅Π΄Π΅Π»ΠΈΡΡ Π²ΡΠ΅ΠΌΠ΅Π½Π½ΠΎΠ΅ ΡΠΎΠΏΡΠΎΡΠΈΠ²Π»Π΅Π½ΠΈΠ΅ ΠΈ ΠΎΡΠ½ΠΎΡΠΈΡΠ΅Π»ΡΠ½ΠΎΠ΅ ΡΠ΄Π»ΠΈΠ½Π΅Π½ΠΈΠ΅.
ΠΠ»Ρ ΠΏΡΠΎΠ²Π΅ΡΠΊΠΈ Ρ ΠΈΠΌΠΈΡΠ΅ΡΠΊΠΎΠ³ΠΎ ΡΠΎΡΡΠ°Π²Π° ΠΈΠ· Π½Π°ΠΏΠ»Π°Π²Π»Π΅Π½Π½ΠΎΠ³ΠΎ ΠΌΠ΅ΡΠ°Π»Π»Π° Π΄ΠΎΠ»ΠΆΠ½ΠΎ Π±ΡΡΡ Π½Π°Π±ΡΠ°Π½ΠΎ 30-40 Π³ ΡΡΡΡΠΆΠΊΠΈ.
ΠΠ°Π³ΠΎΡΠΎΠ²ΠΊΠΈ ΠΎΠ±ΡΠ°Π·ΡΠΎΠ² Π½Π°ΠΏΠ»Π°Π²Π»Π΅Π½Π½ΠΎΠ³ΠΎ ΠΌΠ΅ΡΠ°Π»Π»Π° ΡΠ³Π»Π΅ΡΠΎΠ΄ΠΈΡΡΡΡ ΠΈ Π½ΠΈΠ·ΠΊΠΎΠ»Π΅Π³ΠΈΡΠΎΠ²Π°Π½Π½ΡΡ ΡΠ»Π΅ΠΊΡΡΠΎΠ΄ΠΎΠ² Π΄Π»Ρ ΠΈΡΠΏΡΡΠ°Π½ΠΈΠΉ Π½Π° ΡΠ΄Π°ΡΠ½ΡΠΉ ΠΈΠ·Π³ΠΈΠ± ΠΈ ΡΠ°ΡΡΡΠΆΠ΅Π½ΠΈΠ΅ ΠΌΠΎΠΆΠ½ΠΎ Π²ΡΡΠ΅Π·Π°ΡΡ Ρ ΠΏΠΎΠΌΠΎΡΡΡ Π°ΡΠ΅ΡΠΈΠ»Π΅Π½ΠΎΠΊΠΈΡΠ»ΠΎΡΠΎΠ΄Π½ΠΎΠΉ ΡΠ΅Π·ΠΊΠΈ Ρ ΠΏΡΠΈΠΏΡΡΠΊΠΎΠΌ Π½Π΅ ΠΌΠ΅Π½Π΅Π΅ 4 ΠΌΠΌ Π½Π° ΠΏΠΎΡΠ»Π΅Π΄ΡΡΡΡΡ ΡΠΈΡΡΠΎΠ²ΡΡ ΠΌΠ΅Ρ Π°Π½ΠΈΡΠ΅ΡΠΊΡΡ ΠΎΠ±ΡΠ°Π±ΠΎΡΠΊΡ. ΠΠ°Π³ΠΎΡΠΎΠ²ΠΊΠΈ ΠΎΠ±ΡΠ°Π·ΡΠΎΠ² Π½Π°ΠΏΠ»Π°Π²Π»Π΅Π½Π½ΠΎΠ³ΠΎ ΠΌΠ΅ΡΠ°Π»Π»Π° Π°ΡΡΡΠ΅Π½ΠΈΡΠ½ΡΡ ΡΠ»Π΅ΠΊΡΡΠΎΠ΄ΠΎΠ² Π½Π΅ΠΎΠ±Ρ ΠΎΠ΄ΠΈΠΌΠΎ Π²ΡΡΠ΅Π·Π°ΡΡ ΡΠΎΠ»ΡΠΊΠΎ ΠΌΠ΅Ρ Π°Π½ΠΈΡΠ΅ΡΠΊΠΈΠΌ ΡΠΏΠΎΡΠΎΠ±ΠΎΠΌ.
Π₯ΠΈΠΌΠΈΡΠ΅ΡΠΊΠΈΠΉ ΡΠΎΡΡΠ°Π² Π½Π°ΠΏΠ»Π°Π²Π»Π΅Π½Π½ΠΎΠ³ΠΎ ΠΌΠ΅ΡΠ°Π»Π»Π° ΡΠ»Π΅ΠΊΡΡΠΎΠ΄ΠΎΠ² Π΄ΠΎΠ»ΠΆΠ΅Π½ ΡΠΎΠΎΡΠ²Π΅ΡΡΡΠ²ΠΎΠ²Π°ΡΡ ΡΠΊΠ°Π·Π°Π½Π½ΠΎΠΌΡ Π² ΠΏΡΠΈΠ»ΠΎΠΆΠ΅Π½ΠΈΠΈ 7 ΠΈΠ»ΠΈ 8.
ΠΠ΅Ρ Π°Π½ΠΈΡΠ΅ΡΠΊΠΈΠ΅ ΡΠ²ΠΎΠΉΡΡΠ²Π° Π½Π°ΠΏΠ»Π°Π²Π»Π΅Π½Π½ΠΎΠ³ΠΎ ΠΌΠ΅ΡΠ°Π»Π»Π° ΠΎΠΏΡΠ΅Π΄Π΅Π»ΡΡΡ Π½Π° ΠΎΠ±ΡΠ°Π·ΡΠ°Ρ , ΠΏΡΠΎΡΠ΅Π΄ΡΠΈΡ ΡΠ΅ΡΠΌΠΎΠΎΠ±ΡΠ°Π±ΠΎΡΠΊΡ ΠΏΠΎ ΡΠ΅ΠΆΠΈΠΌΠ°ΠΌ, ΡΠΊΠ°Π·Π°Π½Π½ΡΠΌ Π² ΠΏΡΠΈΠ»ΠΎΠΆΠ΅Π½ΠΈΠΈ 7 ΠΈΠ»ΠΈ 8.
Π‘ΠΌ. Π³ΡΠ°ΡΠΈΡΠ΅ΡΠΊΠΈΠΉ ΠΎΠ±ΡΠ΅ΠΊΡ “Π ΠΈΡ.5.2. Π‘Ρ Π΅ΠΌΠ° Π²ΡΡΠ΅Π·ΠΊΠΈ ΠΎΠ±ΡΠ°Π·ΡΠΎΠ² Π΄Π»Ρ ΠΈΡΠΏΡΡΠ°Π½ΠΈΡ ΠΌΠ΅ΡΠ°Π»Π»Π° ΡΠ²Π°”
5.4.15. ΠΠ΅Ρ Π°Π½ΠΈΡΠ΅ΡΠΊΠΈΠ΅ ΡΠ²ΠΎΠΉΡΡΠ²Π° Π½Π°ΠΏΠ»Π°Π²Π»Π΅Π½Π½ΠΎΠ³ΠΎ ΠΌΠ΅ΡΠ°Π»Π»Π° ΠΎΠΏΡΠ΅Π΄Π΅Π»ΡΡΡ ΠΊΠ°ΠΊ ΡΡΠ΅Π΄Π½Π΅Π΅ Π°ΡΠΈΡΠΌΠ΅ΡΠΈΡΠ΅ΡΠΊΠΎΠ΅ ΠΈΠ· Π΄Π°Π½Π½ΡΡ , ΠΏΠΎΠ»ΡΡΠ΅Π½Π½ΡΡ ΠΏΡΠΈ ΠΈΡΠΏΡΡΠ°Π½ΠΈΠΈ ΠΎΠ±ΡΠ°Π·ΡΠΎΠ². ΠΠ½Π°ΡΠ΅Π½ΠΈΡ Π΄ΠΎΠ»ΠΆΠ½Ρ Π±ΡΡΡ Π½Π΅ ΠΌΠ΅Π½Π΅Π΅ ΡΠΊΠ°Π·Π°Π½Π½ΡΡ Π² ΠΏΡΠΈΠ»ΠΎΠΆΠ΅Π½ΠΈΠΈ 7 ΠΈΠ»ΠΈ 8. ΠΡΠΏΡΡΠ°Π½ΠΈΡ ΡΡΠΈΡΠ°ΡΡ ΡΠ΄ΠΎΠ²Π»Π΅ΡΠ²ΠΎΡΠΈΡΠ΅Π»ΡΠ½ΡΠΌΠΈ, Π΅ΡΠ»ΠΈ ΠΈΡ ΡΠ΅Π·ΡΠ»ΡΡΠ°ΡΡ Π½Π° ΠΎΠ΄Π½ΠΎΠΌ ΠΈΠ· ΠΎΠ±ΡΠ°Π·ΡΠΎΠ² Π½Π΅ Π±ΠΎΠ»Π΅Π΅ ΡΠ΅ΠΌ Π½Π° 10% Π½ΠΈΠΆΠ΅ ΡΡΠ΅Π±ΠΎΠ²Π°Π½ΠΈΠΉ, ΡΠΊΠ°Π·Π°Π½Π½ΡΡ Π² ΠΏΡΠΈΠ»ΠΎΠΆΠ΅Π½ΠΈΠΈ 7 ΠΈΠ»ΠΈ 8, Π° Π΄Π»Ρ ΡΠ΄Π°ΡΠ½ΠΎΠΉ Π²ΡΠ·ΠΊΠΎΡΡΠΈ – Π½Π΅ Π±ΠΎΠ»Π΅Π΅ ΡΠ΅ΠΌ Π½Π° 20 ΠΠΆ/ΡΠΌ2 (2 ΠΊΠ³Ρ Ρ ΠΌ/ΡΠΌ2) Π½ΠΈΠΆΠ΅ ΡΡΡΠ°Π½ΠΎΠ²Π»Π΅Π½Π½ΡΡ Π½ΠΎΡΠΌ ΠΏΡΠΈ ΡΡΠ»ΠΎΠ²ΠΈΠΈ, ΡΡΠΎ ΡΡΠ΅Π΄Π½ΠΈΠΉ Π°ΡΠΈΡΠΌΠ΅ΡΠΈΡΠ΅ΡΠΊΠΈΠΉ ΠΏΠΎΠΊΠ°Π·Π°ΡΠ΅Π»Ρ ΡΠΎΠΎΡΠ²Π΅ΡΡΡΠ²ΡΠ΅Ρ Π½ΠΎΡΠΌΠ°ΡΠΈΠ²Π½ΡΠΌ ΡΡΠ΅Π±ΠΎΠ²Π°Π½ΠΈΡΠΌ.
5.4.16. ΠΡΠΈ Π½Π΅ΡΠ΄ΠΎΠ²Π»Π΅ΡΠ²ΠΎΡΠΈΡΠ΅Π»ΡΠ½ΡΡ ΡΠ΅Π·ΡΠ»ΡΡΠ°ΡΠ°Ρ ΠΊΠ°ΠΊΠΎΠ³ΠΎ-Π»ΠΈΠ±ΠΎ Π²ΠΈΠ΄Π° ΠΌΠ΅Ρ Π°Π½ΠΈΡΠ΅ΡΠΊΠΈΡ ΠΈΡΠΏΡΡΠ°Π½ΠΈΠΉ, Π° ΡΠ°ΠΊΠΆΠ΅ ΠΏΡΠΈ Π½Π΅ΡΠΎΠΎΡΠ²Π΅ΡΡΡΠ²ΠΈΠΈ Ρ ΠΈΠΌΠΈΡΠ΅ΡΠΊΠΎΠ³ΠΎ ΡΠΎΡΡΠ°Π²Π° Π½Π°ΠΏΠ»Π°Π²Π»Π΅Π½Π½ΠΎΠ³ΠΎ ΠΌΠ΅ΡΠ°Π»Π»Π° Π·Π½Π°ΡΠ΅Π½ΠΈΡΠΌ, ΠΏΡΠΈΠ²Π΅Π΄Π΅Π½Π½ΡΠΌ Π² ΠΏΡΠΈΠ»ΠΎΠΆΠ΅Π½ΠΈΠΈ 7 ΠΈΠ»ΠΈ 8, ΡΠ°Π·ΡΠ΅ΡΠ°ΡΡΡΡ ΠΏΠΎΠ²ΡΠΎΡΠ½ΡΠ΅ ΠΈΡΠΏΡΡΠ°Π½ΠΈΡ Π½Π° ΡΠ΄Π²ΠΎΠ΅Π½Π½ΠΎΠΌ ΠΊΠΎΠ»ΠΈΡΠ΅ΡΡΠ²Π΅ ΠΎΠ±ΡΠ°Π·ΡΠΎΠ².
ΠΠΎΠ²ΡΠΎΡΠ½ΠΎ ΠΏΡΠΎΠ²ΠΎΠ΄ΡΡ ΡΠΎΡ Π²ΠΈΠ΄ ΠΌΠ΅Ρ Π°Π½ΠΈΡΠ΅ΡΠΊΠΈΡ ΠΈΡΠΏΡΡΠ°Π½ΠΈΠΉ, ΠΏΠΎ ΠΊΠΎΡΠΎΡΠΎΠΌΡ ΠΏΠΎΠ»ΡΡΠ΅Π½Ρ Π½Π΅ΡΠ΄ΠΎΠ²Π»Π΅ΡΠ²ΠΎΡΠΈΡΠ΅Π»ΡΠ½ΡΠ΅ ΡΠ΅Π·ΡΠ»ΡΡΠ°ΡΡ.
ΠΡΠΈ ΠΏΠΎΠ²ΡΠΎΡΠ½ΠΎΠΌ Ρ ΠΈΠΌΠΈΡΠ΅ΡΠΊΠΎΠΌ Π°Π½Π°Π»ΠΈΠ·Π΅ ΠΎΠΏΡΠ΅Π΄Π΅Π»ΡΡΡ ΡΠΎΠ΄Π΅ΡΠΆΠ°Π½ΠΈΠ΅ ΡΠ΅Ρ ΡΠ»Π΅ΠΌΠ΅Π½ΡΠΎΠ², ΠΊΠΎΡΠΎΡΡΠ΅ ΠΏΠΎ ΡΠ΅Π·ΡΠ»ΡΡΠ°ΡΠ°ΠΌ ΠΏΠ΅ΡΠ²ΠΎΠ³ΠΎ Π°Π½Π°Π»ΠΈΠ·Π° Π½Π΅ ΡΠ΄ΠΎΠ²Π»Π΅ΡΠ²ΠΎΡΡΡΡ ΡΡΠ΅Π±ΠΎΠ²Π°Π½ΠΈΡΠΌ, ΡΠΊΠ°Π·Π°Π½Π½ΡΠΌ Π² ΠΏΡΠΈΠ»ΠΎΠΆΠ΅Π½ΠΈΠΈ 7 ΠΈΠ»ΠΈ 8.
ΠΡΠΈ Π½Π΅ΡΠ΄ΠΎΠ²Π»Π΅ΡΠ²ΠΎΡΠΈΡΠ΅Π»ΡΠ½ΡΡ ΡΠ΅Π·ΡΠ»ΡΡΠ°ΡΠ°Ρ ΠΏΠΎΠ²ΡΠΎΡΠ½ΡΡ ΠΈΡΠΏΡΡΠ°Π½ΠΈΠΉ Π΄Π°ΠΆΠ΅ ΠΏΠΎ ΠΎΠ΄Π½ΠΎΠΌΡ ΠΈΠ· Π²ΠΈΠ΄ΠΎΠ² ΠΈΡΠΏΡΡΠ°Π½ΠΈΠΉ ΠΏΠ°ΡΡΠΈΡ ΡΠ»Π΅ΠΊΡΡΠΎΠ΄ΠΎΠ² Π±ΡΠ°ΠΊΡΠ΅ΡΡΡ ΠΈ Π½Π΅ ΠΌΠΎΠΆΠ΅Ρ Π±ΡΡΡ ΠΈΡΠΏΠΎΠ»ΡΠ·ΠΎΠ²Π°Π½Π° Π΄Π»Ρ ΡΠ²Π°ΡΠΊΠΈ ΠΈΠ·Π΄Π΅Π»ΠΈΠΉ, Π½Π° ΠΊΠΎΡΠΎΡΡΠ΅ ΡΠ°ΡΠΏΡΠΎΡΡΡΠ°Π½ΡΠ΅ΡΡΡ Π½Π°ΡΡΠΎΡΡΠΈΠΉ Π Π.
studfiles.net
ΠΠΎΠ½ΡΡΠΎΠ»Ρ ΠΊΠ°ΡΠ΅ΡΡΠ²Π° ΡΠ²Π°ΡΠΎΡΠ½ΡΡ ΡΠ»Π΅ΠΊΡΡΠΎΠ΄ΠΎΠ² β ΠΡΠ½ΠΎΠ²Π½ΡΠ΅ ΡΡΠ΅Π΄ΡΡΠ²Π°
Π. ΠΠΎΡΠ½ΠΎΠ²ΠΈΡΠΊΠΈΠΉ, Π. Π‘ΡΡΠ»ΠΎΠ²
ΠΡ ΡΠ΅Π΄Π°ΠΊΡΠΈΠΈ.
ΠΠΏΠΈΡΠ°Π½Π½ΡΠΉ ΡΠΏΠΎΡΠΎΠ± ΠΎΠΏΡΠ΅Π΄Π΅Π»Π΅Π½ΠΈΡ ΠΊΠ°ΡΠ΅ΡΡΠ²Π° ΡΠ»Π΅ΠΊΡΡΠΎΠ΄ΠΎΠ² ΠΌΠΎΠΆΠ½ΠΎ ΠΈΡΠΏΠΎΠ»ΡΠ·ΠΎΠ²Π°ΡΡ ΠΈ ΠΏΡΠΈ Π·Π°ΠΊΡΠΏΠΊΠ°Ρ
. ΠΡΠ°Π²Π΄Π°, ΠΌΠ΅ΡΠΎΠ΄Ρ ΠΈΠ·ΠΌΠ΅ΡΠ΅Π½ΠΈΡ ΡΠ°Π·Π½ΠΎΡΠΎΠ»ΡΠΈΠ½Π½ΠΎΡΡΠΈ ΠΏΡΠΈΠ΄Π΅ΡΡΡ ΠΈΡΠΏΠΎΠ»ΡΠ·ΠΎΠ²Π°ΡΡ Π΄ΡΡΠ³ΠΈΠ΅, ΠΏΠΎΡΠΊΠΎΠ»ΡΠΊΡ Π½Π° ΡΠΏΠ΅ΡΠΈΠ°Π»ΡΠ½ΡΠ΅ ΠΏΡΠΈΠ±ΠΎΡΡ ΡΠ°ΡΡΡΠΈΡΡΠ²Π°ΡΡ Π² ΡΡΠΎΠΌ ΡΠ»ΡΡΠ°Π΅ Π½Π΅ ΠΏΡΠΈΡ
ΠΎΠ΄ΠΈΡΡΡ.
![]() |
Π ΡΡΠ½Π°Ρ ΡΠ»Π΅ΠΊΡΡΠΎΠ΄ΡΠ³ΠΎΠ²Π°Ρ ΡΠ²Π°ΡΠΊΠ° ΠΈΡΠΏΠΎΠ»ΡΠ·ΡΠ΅ΡΡΡ ΠΏΠΎΠ²ΡΠ΅ΠΌΠ΅ΡΡΠ½ΠΎ. Π ΡΠΊΠΎΡΠ²ΠΎΡΠ½ΡΠ΅ Π·Π²Π΅Π·Π΄ΠΎΡΠΊΠΈ Π²ΠΎΠ»ΡΡΠΎΠ²ΠΎΠΉ Π΄ΡΠ³ΠΈ Π²ΡΠΏΡΡ
ΠΈΠ²Π°ΡΡ ΠΈ Π½Π° ΠΌΠ°ΡΠΈΠ½ΠΎΡΡΡΠΎΠΈΡΠ΅Π»ΡΠ½ΡΡ
Π·Π°Π²ΠΎΠ΄Π°Ρ
, ΠΈ Π½Π° ΡΡΡΠΎΠΉΠΊΠ°Ρ
, ΠΈ ΠΏΡΠΈ ΡΠ΅ΠΌΠΎΠ½ΡΠ΅ ΡΠ΅Ρ
Π½ΠΈΠΊΠΈ β ΠΊΠ°ΠΊ Π² ΠΌΠ°ΡΡΠ΅ΡΡΠΊΠΈΡ
, ΡΠ°ΠΊ ΠΈ Π² ΠΏΠΎΠ»Π΅Π²ΡΡ
ΡΡΠ»ΠΎΠ²ΠΈΡΡ
. Π ΡΠ°ΡΠ΅ Π²ΡΠ΅Π³ΠΎ ΡΡΠ΅Π±ΡΠ΅ΡΡΡ Π²ΡΡΠΎΠΊΠΎΠ΅ ΠΊΠ°ΡΠ΅ΡΡΠ²ΠΎ ΡΠ²Π°ΡΠ½ΠΎΠ³ΠΎ ΡΠ²Π°. ΠΠ΅ΠΎΠ±Ρ
ΠΎΠ΄ΠΈΠΌΠΎΠ΅ ΡΡΠ»ΠΎΠ²ΠΈΠ΅ Π΅Π³ΠΎ ΠΏΠΎΠ»ΡΡΠ΅Π½ΠΈΡ β ΡΠ»Π΅ΠΊΡΡΠΎΠ΄, ΠΊΠΎΡΠΎΡΡΠΉ Π΄ΠΎΠ»ΠΆΠ΅Π½ ΠΎΠ±Π΅ΡΠΏΠ΅ΡΠΈΠ²Π°ΡΡ Π»Π΅Π³ΠΊΠΎΠ΅ Π·Π°ΠΆΠΈΠ³Π°Π½ΠΈΠ΅ ΠΈ ΡΡΡΠΎΠΉΡΠΈΠ²ΠΎΠ΅ Π³ΠΎΡΠ΅Π½ΠΈΠ΅ Π΄ΡΠ³ΠΈ, ΡΠ°Π²Π½ΠΎΠΌΠ΅ΡΠ½ΠΎΠ΅ ΡΠ°ΡΠΏΠ»Π°Π²Π»Π΅Π½ΠΈΠ΅ ΠΌΠ΅ΡΠ°Π»Π»Π° ΡΠ»Π΅ΠΊΡΡΠΎΠ΄Π° ΠΈ ΠΏΠΎΠΊΡΡΡΠΈΡ, ΠΎΠ±ΡΠ°Π·ΠΎΠ²Π°Π½ΠΈΠ΅ ΠΏΡΠ°Π²ΠΈΠ»ΡΠ½ΠΎΠ³ΠΎ ΡΠ²Π° Π±Π΅Π· Π½Π΅ΠΏΡΠΎΠ²Π°ΡΠΎΠ² ΠΈ ΡΡΠ΅ΡΠΈΠ½ ΠΈ, Π½Π°ΠΊΠΎΠ½Π΅Ρ, Π»Π΅Π³ΠΊΠΎΠ΅ ΡΠ΄Π°Π»Π΅Π½ΠΈΠ΅ ΡΠ»Π°ΠΊΠ° Ρ ΠΏΠΎΠ²Π΅ΡΡ
Π½ΠΎΡΡΠΈ.
ΠΡΠΈ Π²ΡΠ΅ΠΉ ΡΠ²ΠΎΠ΅ΠΉ ΠΏΡΠΎΡΡΠΎΡΠ΅ ΡΠ»Π΅ΠΊΡΡΠΎΠ΄ Π΄Π»Ρ ΡΡΡΠ½ΠΎΠΉ Π΄ΡΠ³ΠΎΠ²ΠΎΠΉ ΡΠ»Π΅ΠΊΡΡΠΎΡΠ²Π°ΡΠΊΠΈ Π΄ΠΎΠ»ΠΆΠ΅Π½ Π±ΡΡΡ Π²ΡΡΠΎΠΊΠΎΠΊΠ°ΡΠ΅ΡΡΠ²Π΅Π½Π½ΡΠΌ, Π° Π·Π½Π°ΡΠΈΡ Π΄Π»Ρ Π΅Π³ΠΎ ΠΈΠ·Π³ΠΎΡΠΎΠ²Π»Π΅Π½ΠΈΡ Π½Π΅ΠΎΠ±Ρ
ΠΎΠ΄ΠΈΠΌΠΎ ΠΈΡΠΏΠΎΠ»ΡΠ·ΠΎΠ²Π°ΡΡ ΠΌΠ°ΡΠ΅ΡΠΈΠ°Π»Ρ (ΠΊΠ°ΠΊ ΠΏΡΠΎΠ²ΠΎΠ»ΠΎΠΊΠ°, ΡΠ°ΠΊ ΠΈ ΠΏΠΎΠΊΡΡΡΠΈΠ΅) ΠΏΡΠ°Π²ΠΈΠ»ΡΠ½ΠΎΠΉ ΡΠ΅ΡΠ΅ΠΏΡΡΡΡ. ΠΠΎ ΡΡΠΎΠ³ΠΎ ΠΌΠ°Π»ΠΎ: ΠΏΠΎΠΊΡΡΡΠΈΠ΅ Π΄ΠΎΠ»ΠΆΠ½ΠΎ Π±ΡΡΡ ΡΠ°Π²Π½ΠΎΠΌΠ΅ΡΠ½ΡΠΌ β ΡΠΎΠ»ΡΠΊΠΎ Π² ΡΡΠΎΠΌ ΡΠ»ΡΡΠ°Π΅ Π²ΠΎΠ·ΠΌΠΎΠΆΠ½ΠΎ ΠΏΡΠ°Π²ΠΈΠ»ΡΠ½ΠΎΠ΅ ΡΠ°ΡΠΏΠ»Π°Π²Π»Π΅Π½ΠΈΠ΅ ΡΠ»ΡΡΠ° ΠΈ ΠΏΠΎΠ»ΡΡΠ΅Π½ΠΈΠ΅ Π½Π°Π΄Π»Π΅ΠΆΠ°ΡΠΈΡ
ΡΠ²ΠΎΠΉΡΡΠ² ΠΌΠ΅ΡΠ°Π»Π»Π° Π² ΡΠ²Π°ΡΠΎΡΠ½ΠΎΠΉ Π²Π°Π½Π½Π΅. ΠΠΎΡΡΠΎΠΌΡ ΡΠ°Π·Π½ΠΎΡΠΎΠ»ΡΠΈΠ½Π½ΠΎΡΡΡ ΠΏΠΎΠΊΡΡΡΠΈΡ (ΡΠ°Π·Π½ΠΎΡΡΡ Π΅Π³ΠΎ ΡΠΎΠ»ΡΠΈΠ½Ρ Π½Π° Π΄ΠΈΠ°ΠΌΠ΅ΡΡΠ°Π»ΡΠ½ΠΎ ΠΏΡΠΎΡΠΈΠ²ΠΎΠΏΠΎΠ»ΠΎΠΆΠ½ΡΡ
ΡΡΠ°ΡΡΠΊΠ°Ρ
ΡΠ»Π΅ΠΊΡΡΠΎΠ΄Π°) ΡΡΠΈΡΠ°Π΅ΡΡΡ ΠΎΠ΄Π½ΠΈΠΌ ΠΈΠ· Π²Π°ΠΆΠ½Π΅ΠΉΡΠΈΡ
ΠΏΠΎΠΊΠ°Π·Π°ΡΠ΅Π»Π΅ΠΉ ΠΊΠ°ΡΠ΅ΡΡΠ²Π° ΡΠ»Π΅ΠΊΡΡΠΎΠ΄Π°.
ΠΡΠ»ΠΈ ΡΠ°Π·Π½ΠΎΡΠΎΠ»ΡΠΈΠ½Π½ΠΎΡΡΡ ΠΏΡΠ΅Π²ΡΡΠ°Π΅Ρ ΠΏΡΠ΅Π΄Π΅Π»ΡΠ½ΠΎ Π΄ΠΎΠΏΡΡΡΠΈΠΌΡΡ Π²Π΅Π»ΠΈΡΠΈΠ½Ρ, ΡΠΎ ΡΡΠΎ ΡΠΈΠ»ΡΠ½ΠΎ Π·Π°ΡΡΡΠ΄Π½ΡΠ΅Ρ ΡΠ°Π±ΠΎΡΡ ΡΠ²Π°ΡΡΠΈΠΊΠ°. ΠΠ° ΡΠ»Π΅ΠΊΡΡΠΎΠ΄Π΅ ΠΎΠ±ΡΠ°Π·ΡΠ΅ΡΡΡ ΠΎΠ΄Π½ΠΎΡΡΠΎΡΠΎΠ½Π½ΠΈΠΉ ΠΊΠΎΠ·ΡΡΠ΅ΠΊ ΠΈΠ· ΠΏΠΎΠΊΡΡΡΠΈΡ, Π° Π² ΠΌΠ΅ΡΠ°Π»Π»Π΅ ΡΠ²Π° Π²ΠΎΠ·Π½ΠΈΠΊΠ°ΡΡ ΡΠ°Π·Π»ΠΈΡΠ½ΡΠ΅ Π΄Π΅ΡΠ΅ΠΊΡΡ β Π½Π΅ΡΠΏΠ»Π°Π²Π»Π΅Π½ΠΈΡ, ΡΠ»Π°ΠΊΠΎΠ²ΡΠ΅ Π²ΠΊΠ»ΡΡΠ΅Π½ΠΈΡ ΠΈ Π΄ΡΡΠ³ΠΈΠ΅.
Π‘ΠΎΠ³Π»Π°ΡΠ½ΠΎ Π΄Π΅ΠΉΡΡΠ²ΡΡΡΠ΅ΠΌΡ Π² Π½Π°ΡΡΠΎΡΡΠ΅Π΅ Π²ΡΠ΅ΠΌΡ ΠΠΠ‘Π’ 9466-75 ΡΠ°Π·Π½ΠΎΡΠΎΠ»ΡΠΈΠ½Π½ΠΎΡΡΡ ΠΏΠΎΠΊΡΡΡΠΈΡ ΠΎΠΏΡΠ΅Π΄Π΅Π»ΡΠ΅ΡΡΡ Π² ΡΡΠ΅Ρ
ΡΠ΅ΡΠ΅Π½ΠΈΡΡ
, ΡΠ΄Π°Π»Π΅Π½Π½ΡΡ
Π΄ΡΡΠ³ ΠΎΡ Π΄ΡΡΠ³Π° ΠΏΠΎ Π΄Π»ΠΈΠ½Π΅ Π½Π° 80 β 100 ΠΌΠΌ. Π£ΡΡΠ°Π½ΠΎΠ²Π»Π΅Π½ΠΎ, ΡΡΠΎ ΡΠ°Π·Π½ΠΎΡΡΡ ΠΌΠ΅ΠΆΠ΄Ρ ΠΌΠ°ΠΊΡΠΈΠΌΠ°Π»ΡΠ½ΠΎΠΉ ΠΈ ΠΌΠΈΠ½ΠΈΠΌΠ°Π»ΡΠ½ΠΎΠΉ Π΅Π΅ Π²Π΅Π»ΠΈΡΠΈΠ½Π°ΠΌΠΈ Π²Π΅ΡΡΠΌΠ° ΡΠΎΡΠ½ΠΎ Ρ
Π°ΡΠ°ΠΊΡΠ΅ΡΠΈΠ·ΡΠ΅Ρ ΠΊΠ°ΡΠ΅ΡΡΠ²ΠΎ ΡΠ΅Ρ
Π½ΠΎΠ»ΠΎΠ³ΠΈΠΈ ΠΈΠ·Π³ΠΎΡΠΎΠ²Π»Π΅Π½ΠΈΡ ΡΠ»Π΅ΠΊΡΡΠΎΠ΄Π°, Π° Π·Π½Π°ΡΠΈΡ ΠΈ ΡΠ°ΠΌ ΡΠ»Π΅ΠΊΡΡΠΎΠ΄. ΠΠΎ ΡΡΠΎΠΉ ΡΠ°Π·Π½ΠΎΡΡΠΈ ΠΌΠΎΠΆΠ½ΠΎ Π²ΡΡΠ²ΠΈΡΡ Π½Π΅ ΠΎΡΠ»Π°ΠΆΠ΅Π½Π½ΡΡ ΠΎΠΏΠ΅ΡΠ°ΡΠΈΡ ΠΈΠ»ΠΈ ΠΈΡ
Π³ΡΡΠΏΠΏΡ, ΡΠΎΡΡΠΎΡΠ½ΠΈΠ΅ ΠΎΠ±ΠΎΡΡΠ΄ΠΎΠ²Π°Π½ΠΈΡ ΠΈ ΠΊΠ²Π°Π»ΠΈΡΠΈΠΊΠ°ΡΠΈΡ ΠΏΠ΅ΡΡΠΎΠ½Π°Π»Π°.
ΠΡΠΈΠ½ΡΠΈΠΏΠΈΠ°Π»ΡΠ½ΠΎ Π²ΠΎΠ·ΠΌΠΎΠΆΠ½Ρ ΡΠ΅ΡΡΡΠ΅ ΡΠΈΡΡΠ°ΡΠΈΠΈ:
β Π Π°Π·Π½ΠΎΡΠΎΠ»ΡΠΈΠ½Π½ΠΎΡΡΡ ΠΏΠΎΠΊΡΡΡΠΈΡ Π²ΠΎ Π²ΡΠ΅Ρ
ΡΠ΅ΡΠ΅Π½ΠΈΡΡ
ΠΎΡΠ²Π΅ΡΠ°Π΅Ρ Π΄Π΅ΠΉΡΡΠ²ΡΡΡΠΈΠΌ Π½ΠΎΡΠΌΠ°ΠΌ, Π° ΡΠ°Π·Π½ΠΈΡΠ° ΠΌΠ΅ΠΆΠ΄Ρ Π΅Π΅ ΠΌΠ°ΠΊΡΠΈΠΌΡΠΌΠΎΠΌ ΠΈ ΠΌΠΈΠ½ΠΈΠΌΡΠΌΠΎΠΌ Π½Π΅ ΠΏΡΠ΅Π²ΡΡΠ°Π΅Ρ 0,05 ΠΌΠΌ. Π’Π΅Ρ
Π½ΠΎΠ»ΠΎΠ³ΠΈΡΠ΅ΡΠΊΠΈΠΉ ΠΏΡΠΎΡΠ΅ΡΡ ΠΈΠ·Π³ΠΎΡΠΎΠ²Π»Π΅Π½ΠΈΡ ΡΠ»Π΅ΠΊΡΡΠΎΠ΄ΠΎΠ² ΠΎΡΠ»Π°ΠΆΠ΅Π½ ΠΈ ΡΡΠ°Π±ΠΈΠ»Π΅Π½; ΠΊΠ²Π°Π»ΠΈΡΠΈΠΊΠ°ΡΠΈΡ ΠΏΠ΅ΡΡΠΎΠ½Π°Π»Π° ΠΎΡΠ²Π΅ΡΠ°Π΅Ρ ΡΡΠ΅Π±ΠΎΠ²Π°Π½ΠΈΡΠΌ ΠΏΡΠΎΠΈΠ·Π²ΠΎΠ΄ΡΡΠ²Π°.
β Π ΠΎΠ΄Π½ΠΎΠΌ ΠΈΠ· ΡΠ΅ΡΠ΅Π½ΠΈΠΉ ΡΠ°Π·Π½ΠΎΡΠΎΠ»ΡΠΈΠ½Π½ΠΎΡΡΡ Π²ΡΡ
ΠΎΠ΄ΠΈΡ Π·Π° ΡΠ°ΠΌΠΊΠΈ Π΄ΠΎΠΏΡΡΠΊΠ°, ΠΎΠ΄Π½Π°ΠΊΠΎ ΡΠ°Π·Π½ΠΎΡΡΡ ΠΌΠ΅ΠΆΠ΄Ρ ΠΌΠ°ΠΊΡΠΈΠΌΡΠΌΠΎΠΌ ΠΈ ΠΌΠΈΠ½ΠΈΠΌΡΠΌΠΎΠΌ Π½Π΅ ΠΏΡΠ΅Π²ΡΡΠ°Π΅Ρ 0,05 ΠΌΠΌ. Π’ΡΠ΅Π±ΡΠ΅ΡΡΡ Π±ΠΎΠ»Π΅Π΅ ΡΠΎΡΠ½Π°Ρ ΡΡΡΠ°Π½ΠΎΠ²ΠΊΠ° ΠΏΠΎΠ΄Π°ΡΡΠ΅ΠΉ ΠΈ ΠΊΠ°Π»ΠΈΠ±ΡΡΡΡΠ΅ΠΉ Π²ΡΡΠ»ΠΎΠΊ Π² Π³ΠΎΠ»ΠΎΠ²ΠΊΠ΅ ΠΏΡΠ΅ΡΡΠ°. ΠΡΠΎΠ³ΠΎ ΡΡΠ°Π²Π½ΠΈΡΠ΅Π»ΡΠ½ΠΎ ΠΏΡΠΎΡΡΠΎΠ³ΠΎ ΠΌΠ΅ΡΠΎΠΏΡΠΈΡΡΠΈΡ Π²ΠΏΠΎΠ»Π½Π΅ Π΄ΠΎΡΡΠ°ΡΠΎΡΠ½ΠΎ Π΄Π»Ρ ΠΏΠΎΠ»ΡΡΠ΅Π½ΠΈΡ Π΄ΠΎΠ»ΠΆΠ½ΠΎΠ³ΠΎ ΠΊΠ°ΡΠ΅ΡΡΠ²Π°.
β ΠΠ°Π»ΠΈΡΠΈΠ΅ ΡΠ²Π΅ΡΡ
Π½ΠΎΡΠΌΠ°ΡΠΈΠ²Π½ΠΎΠΉ ΡΠ°Π·Π½ΠΎΡΠΎΠ»ΡΠΈΠ½Π½ΠΎΡΡΠΈ ΠΏΡΠΈ ΡΠ°Π·Π½ΠΈΡΠ΅ ΠΌΠ΅ΠΆΠ΄Ρ ΠΌΠ°ΠΊΡΠΈΠΌΡΠΌΠΎΠΌ ΠΈ ΠΌΠΈΠ½ΠΈΠΌΡΠΌΠΎΠΌ Π±ΠΎΠ»Π΅Π΅ 0,05 ΠΌΠΌ. Π’Π°ΠΊΠ°Ρ ΡΠΈΡΡΠ°ΡΠΈΡ Π³ΠΎΠ²ΠΎΡΠΈΡ ΠΎ Π½Π΅ΡΠ΄ΠΎΠ²Π»Π΅ΡΠ²ΠΎΡΠΈΡΠ΅Π»ΡΠ½ΠΎΠΉ ΠΏΠΎΠ΄Π³ΠΎΡΠΎΠ²ΠΊΠ΅ ΠΎΠ±ΠΌΠ°Π·ΠΎΡΠ½ΠΎΠΉ ΠΌΠ°ΡΡΡ (ΠΏΠ»ΠΎΡ
ΠΎΠ΅ ΠΏΠ΅ΡΠ΅ΠΌΠ΅ΡΠΈΠ²Π°Π½ΠΈΠ΅ ΡΡΡ
ΠΎΠΉ ΡΠΈΡ
ΡΡ Ρ ΠΆΠΈΠ΄ΠΊΠΈΠΌ ΡΡΠ΅ΠΊΠ»ΠΎΠΌ). ΠΠ΅ΠΎΠ±Ρ
ΠΎΠ΄ΠΈΠΌΠΎ ΠΎΡΠΊΠΎΡΡΠ΅ΠΊΡΠΈΡΠΎΠ²Π°ΡΡ ΡΠ΅Ρ
Π½ΠΎΠ»ΠΎΠ³ΠΈΡΠ΅ΡΠΊΠΈΠΉ ΠΏΡΠΎΡΠ΅ΡΡ ΠΊΠ°ΠΊ ΠΏΠΎ Π΄Π»ΠΈΡΠ΅Π»ΡΠ½ΠΎΡΡΠΈ ΠΏΠ΅ΡΠ΅ΠΌΠ΅ΡΠΈΠ²Π°Π½ΠΈΡ, ΡΠ°ΠΊ ΠΈ ΠΏΠΎ ΡΠΎΡΡΠΎΡΠ½ΠΈΡ ΡΠΌΠ΅ΡΠΈΡΠ΅Π»Ρ ΠΈ Π΄ΡΡΠ³ΠΈΠΌ ΠΏΠ°ΡΠ°ΠΌΠ΅ΡΡΠ°ΠΌ.
β Π‘Π²Π΅ΡΡ
Π½ΠΎΡΠΌΠ°ΡΠΈΠ²Π½Π°Ρ ΡΠ°Π·Π½ΠΎΡΠΎΠ»ΡΠΈΠ½Π½ΠΎΡΡΡ Π²ΠΎ Π²ΡΠ΅Ρ
ΡΠ΅ΡΠ΅Π½ΠΈΡΡ
ΠΏΡΠΈ ΡΠ°Π·Π½ΠΎΡΡΠΈ ΠΌΠ΅ΠΆΠ΄Ρ Π΅Π΅ ΠΌΠ°ΠΊΡΠΈΠΌΡΠΌΠΎΠΌ ΠΈ ΠΌΠΈΠ½ΠΈΠΌΡΠΌΠΎΠΌ ΠΌΠ΅Π½Π΅Π΅ 0,05 ΠΌΠΌ. ΠΡΠΈΡΠΈΠ½Π° Π±ΡΠ°ΠΊΠ° Π² ΡΡΠΎΠΌ ΡΠ»ΡΡΠ°Π΅ β Π½Π΅ΠΏΡΠ°Π²ΠΈΠ»ΡΠ½Π°Ρ ΡΡΡΠ°Π½ΠΎΠ²ΠΊΠ° ΠΎΠΏΠ΅ΡΠ°ΡΠΎΡΠΎΠΌ ΠΊΠ°Π»ΠΈΠ±ΡΡΡΡΠ΅ΠΉ Π²ΡΡΠ»ΠΊΠΈ ΠΎΡΠ½ΠΎΡΠΈΡΠ΅Π»ΡΠ½ΠΎ ΠΏΠΎΠ΄Π°ΡΡΠ΅ΠΉ Π²ΡΠ»Π΅Π΄ΡΡΠ²ΠΈΠ΅ Π½Π΅Π²Π½ΠΈΠΌΠ°ΡΠ΅Π»ΡΠ½ΠΎΡΡΠΈ ΠΈΠ»ΠΈ Π½ΠΈΠ·ΠΊΠΎΠΉ ΠΊΠ²Π°Π»ΠΈΡΠΈΠΊΠ°ΡΠΈΠΈ, Π° ΡΠ°ΠΊΠΆΠ΅ Π½Π΅ΡΠ΄ΠΎΠ²Π»Π΅ΡΠ²ΠΎΡΠΈΡΠ΅Π»ΡΠ½ΡΠΉ ΠΊΠΎΠ½ΡΡΠΎΠ»Ρ Π·Π° ΡΠΎΠ±Π»ΡΠ΄Π΅Π½ΠΈΠ΅ΠΌ ΡΠ΅Ρ
Π½ΠΎΠ»ΠΎΠ³ΠΈΡΠ΅ΡΠΊΠΎΠ³ΠΎ ΠΏΡΠΎΡΠ΅ΡΡΠ°.
Π ΡΡΠ»ΠΎΠ²ΠΈΡΡ
ΠΌΠ°ΡΡΠΎΠ²ΠΎΠ³ΠΎ ΠΏΡΠΎΠΈΠ·Π²ΠΎΠ΄ΡΡΠ²Π° Π΄Π»Ρ ΠΎΡΠ΅Π½ΠΊΠΈ ΠΊΠ°ΡΠ΅ΡΡΠ²Π° Π²ΡΠ±ΠΈΡΠ°ΡΡ Π³ΡΡΠΏΠΏΡ ΡΠ»Π΅ΠΊΡΡΠΎΠ΄ΠΎΠ² (ΠΏΡΠ΅Π΄Π²Π°ΡΠΈΡΠ΅Π»ΡΠ½Π°Ρ Π²ΡΠ±ΠΎΡΠΊΠ°). Π‘ ΠΏΠΎΠΌΠΎΡΡΡ ΡΠΏΠ΅ΡΠΈΠ°Π»ΡΠ½ΡΡ
ΠΏΡΠΈΠ±ΠΎΡΠΎΠ² (Π½Π°ΠΏΡΠΈΠΌΠ΅Ρ, ΠΠ Π, Π²ΡΠΏΡΡΠΊΠ°Π΅ΠΌΠΎΠ³ΠΎ ΠΠ Β«Π‘ΠΏΠ΅ΡΡΠ»Π΅ΠΊΡΡΠΎΠ΄Β») ΠΏΡΠΎΠ²ΠΎΠ΄ΡΡ ΠΈΠ·ΠΌΠ΅ΡΠ΅Π½ΠΈΠ΅ ΡΠ°Π·Π½ΠΎΡΠΎΠ»ΡΠΈΠ½Π½ΠΎΡΡΠΈ ΠΏΠΎΠΊΡΡΡΠΈΡ. ΠΡΠ±ΠΎΡΠΊΠ° ΠΌΠΎΠΆΠ΅Ρ ΡΠΎΠ΄Π΅ΡΠΆΠ°ΡΡ ΠΎΡ 30 Π΄ΠΎ 50 ΡΠ»Π΅ΠΊΡΡΠΎΠ΄ΠΎΠ², ΠΎΡΠΎΠ±ΡΠ°Π½Π½ΡΡ
ΠΎΡ ΠΎΠ΄Π½ΠΎΠ³ΠΎ β Π΄Π²ΡΡ
Π·Π°ΠΌΠ΅ΡΠΎΠ² ΠΈΠ»ΠΈ ΠΏΠ°ΡΡΠΈΠΈ ΡΠ»Π΅ΠΊΡΡΠΎΠ΄ΠΎΠ² ΠΌΠ°ΡΡΠΎΠΉ 200 β 1Β 000 ΠΊΠ³.
ΠΠ°ΠΌΠ΅ΡΠΈΠΌ, ΡΡΠΎ Π·Π°ΡΡΠ±Π΅ΠΆΠ½ΡΠ΅ ΡΠΈΡΠΌΡ, ΡΠΏΠ΅ΡΠΈΠ°Π»ΠΈΠ·ΠΈΡΡΡΡΠΈΠ΅ΡΡ Π½Π° ΠΏΡΠΎΠΈΠ·Π²ΠΎΠ΄ΡΡΠ²Π΅ ΡΠ»Π΅ΠΊΡΡΠΎΠ΄ΠΎΠ² Π΄Π»Ρ ΡΡΡΠ½ΠΎΠΉ Π΄ΡΠ³ΠΎΠ²ΠΎΠΉ ΡΠ»Π΅ΠΊΡΡΠΎΡΠ²Π°ΡΠΊΠΈ, ΠΏΠΎΠ»ΡΡΠ°ΡΡ Π²Π΅ΡΡΠΌΠ° Ρ
ΠΎΡΠΎΡΠΈΠ΅ ΠΎΠ±ΠΌΠ°Π·ΠΎΡΠ½ΡΠ΅ ΠΌΠ°ΡΡΡ. Π Π°Π·Π½ΠΈΡΠ° ΠΌΠ΅ΠΆΠ΄Ρ ΠΌΠ°ΠΊΡΠΈΠΌΠ°Π»ΡΠ½ΠΎΠΉ ΠΈ ΠΌΠΈΠ½ΠΈΠΌΠ°Π»ΡΠ½ΠΎΠΉ ΡΠ°Π·Π½ΠΎΡΠΎΠ»ΡΠΈΠ½Π½ΠΎΡΡΡΡ Π΄Π»Ρ ΠΈΡ
ΠΏΡΠΎΠ΄ΡΠΊΡΠΈΠΈ, ΠΊΠ°ΠΊ ΠΏΡΠ°Π²ΠΈΠ»ΠΎ, Π½Π΅ ΠΏΡΠ΅Π²ΡΡΠ°Π΅Ρ 0,03 ΠΌΠΌ.
Π Π·Π°ΠΊΠ»ΡΡΠ΅Π½ΠΈΠ΅ Π·Π°ΠΌΠ΅ΡΠΈΠΌ, ΡΡΠΎ ΠΎΠΏΠΈΡΠ°Π½Π½Π°Ρ ΠΌΠ΅ΡΠΎΠ΄ΠΈΠΊΠ° ΠΎΡΠ΅Π½ΠΊΠΈ ΡΠ°Π·Π½ΠΎΡΠΎΠ»ΡΠΈΠ½Π½ΠΎΡΡΠΈ ΡΠΆΠ΅ ΠΏΡΠΈΠΌΠ΅Π½ΡΠ΅ΡΡΡ Π½Π° Π½Π΅ΠΊΠΎΡΠΎΡΡΡ
ΠΏΡΠ΅Π΄ΠΏΡΠΈΡΡΠΈΡΡ
, Π² ΡΠ°ΡΡΠ½ΠΎΡΡΠΈ Π½Π° ΠΠΠΠ’ Β«ΠΠ»Π΅ΠΊΡΡΠΎΠ΄Π½ΡΠΉ Π·Π°Π²ΠΎΠ΄Β» Π² Π‘Π°Π½ΠΊΡ ΠΠ΅ΡΠ΅ΡΠ±ΡΡΠ³Π΅, ΡΠΈΡΠΌΠ΅ Β«Π‘Π²Π°ΠΏΡΠΎΒ» ΠΈ ΠΠΠ Β«Π‘ΠΏΠ΅ΡΡΠ»Π΅ΠΊΡΡΠΎΠ΄Β» Π² ΠΠΎΡΠΊΠ²Π΅.
![]() |
os1.ru
ΠΠΎΠ½ΡΡΠΎΠ»Ρ ΠΊΠ°ΡΠ΅ΡΡΠ²Π° ΡΠ²Π°ΡΠΎΡΠ½ΡΡ ΠΌΠ°ΡΠ΅ΡΠΈΠ°Π»ΠΎΠ² ΠΈ ΠΌΠ°ΡΠ΅ΡΠΈΠ°Π»ΠΎΠ² Π΄Π»Ρ Π΄Π΅ΡΠ΅ΠΊΡΠΎΡΠΊΠΎΠΏΠΈΠΈ
Π Π΅ΠΊΠΎΠΌΠ΅Π½Π΄ΡΠ΅ΠΌ ΠΏΡΠΈΠΎΠ±ΡΠ΅ΡΡΠΈ:
Π£ΡΡΠ°Π½ΠΎΠ²ΠΊΠΈ Π΄Π»Ρ Π°Π²ΡΠΎΠΌΠ°ΡΠΈΡΠ΅ΡΠΊΠΎΠΉ ΡΠ²Π°ΡΠΊΠΈ ΠΏΡΠΎΠ΄ΠΎΠ»ΡΠ½ΡΡ
ΡΠ²ΠΎΠ² ΠΎΠ±Π΅ΡΠ°Π΅ΠΊ – Π² Π½Π°Π»ΠΈΡΠΈΠΈ Π½Π° ΡΠΊΠ»Π°Π΄Π΅!
ΠΡΡΠΎΠΊΠ°Ρ ΠΏΡΠΎΠΈΠ·Π²ΠΎΠ΄ΠΈΡΠ΅Π»ΡΠ½ΠΎΡΡΡ, ΡΠ΄ΠΎΠ±ΡΡΠ²ΠΎ, ΠΏΡΠΎΡΡΠΎΡΠ° Π² ΡΠΏΡΠ°Π²Π»Π΅Π½ΠΈΠΈ ΠΈ Π½Π°Π΄Π΅ΠΆΠ½ΠΎΡΡΡ Π² ΡΠΊΡΠΏΠ»ΡΠ°ΡΠ°ΡΠΈΠΈ.
Π‘Π²Π°ΡΠΎΡΠ½ΡΠ΅ ΡΠΊΡΠ°Π½Ρ ΠΈ Π·Π°ΡΠΈΡΠ½ΡΠ΅ ΡΡΠΎΡΠΊΠΈ – Π² Π½Π°Π»ΠΈΡΠΈΠΈ Π½Π° ΡΠΊΠ»Π°Π΄Π΅!
ΠΠ°ΡΠΈΡΠ° ΠΎΡ ΠΈΠ·Π»ΡΡΠ΅Π½ΠΈΡ ΠΏΡΠΈ ΡΠ²Π°ΡΠΊΠ΅ ΠΈ ΡΠ΅Π·ΠΊΠ΅. ΠΠΎΠ»ΡΡΠΎΠΉ Π²ΡΠ±ΠΎΡ.
ΠΠΎΡΡΠ°Π²ΠΊΠ° ΠΏΠΎ Π²ΡΠ΅ΠΉ Π ΠΎΡΡΠΈΠΈ!
ΠΠ°ΡΠ΅ΡΡΠ²ΠΎ ΡΠ²Π°ΡΠ½ΡΡ ΡΠΎΠ΅Π΄ΠΈΠ½Π΅Π½ΠΈΠΉ Π²ΠΎ ΠΌΠ½ΠΎΠ³ΠΎΠΌ Π·Π°Π²ΠΈΡΠΈΡ ΠΎΡ ΡΠ²Π°ΡΠΎΡΠ½ΡΡ ΠΌΠ°ΡΠ΅ΡΠΈΠ°Π»ΠΎΠ², ΠΏΠΎΡΡΠΎΠΌΡ ΠΊΠ°ΠΆΠ΄ΡΡ ΠΏΠ°ΡΡΠΈΡ ΡΠ»Π΅ΠΊΡΡΠΎΠ΄ΠΎΠ², ΡΠ²Π°ΡΠΎΡΠ½ΠΎΠΉ ΠΏΡΠΎΠ²ΠΎΠ»ΠΎΠΊΠΈ, ΡΠ»ΡΡΠΎΠ², Π±Π°Π»Π»ΠΎΠ½ΠΎΠ² Ρ Π·Π°ΡΠΈΡΠ½ΡΠΌ Π³Π°Π·ΠΎΠΌ ΠΏΠ΅ΡΠ΅Π΄ Π½Π°ΡΠ°Π»ΠΎΠΌ ΡΠ²Π°ΡΠΊΠΈ ΡΡΠ°ΡΠ΅Π»ΡΠ½ΠΎ ΠΏΡΠΎΠ²Π΅ΡΡΡΡ. Π‘Π²Π°ΡΠΎΡΠ½ΡΠ΅ ΠΌΠ°ΡΠ΅ΡΠΈΠ°Π»Ρ Π΄ΠΎΠ»ΠΆΠ½Ρ ΠΈΠΌΠ΅ΡΡ ΡΠ΅ΡΡΠΈΡΠΈΠΊΠ°ΡΡ, Π² ΠΊΠΎΡΠΎΡΡΡ ΠΏΠΎΠ»Π½ΠΎΡΡΡΡ ΠΏΡΠΈΠ²Π΅Π΄Π΅Π½Ρ Π΄Π°Π½Π½ΡΠ΅ Π² ΡΠΎΠΎΡΠ²Π΅ΡΡΡΠ²ΠΈΠΈ Ρ ΡΡΠ΅Π±ΠΎΠ²Π°Π½ΠΈΡΠΌΠΈ ΠΠΠ‘Π’ΠΎΠ², ΡΠ΅Ρ Π½ΠΈΡΠ΅ΡΠΊΠΈΡ ΡΡΠ»ΠΎΠ²ΠΈΠΉ ΠΈ ΠΏΠ°ΡΠΏΠΎΡΡΠΎΠ².
ΠΠ° ΡΠΏΠ°ΠΊΠΎΠ²ΠΎΡΠ½ΡΡ ΠΊΠΎΡΠΎΠ±ΠΊΠ°Ρ , ΡΡΠΈΠΊΠ°Ρ , Π±Π°Π»Π»ΠΎΠ½Π°Ρ , ΠΏΠ°ΡΠΊΠ°Ρ Π΄ΠΎΠ»ΠΆΠ½Ρ Π±ΡΡΡ Π±ΠΈΡΠΊΠΈ ΠΈΠ»ΠΈ ΡΡΠΈΠΊΠ΅ΡΠΊΠΈ Ρ ΡΠΊΠ°Π·Π°Π½ΠΈΠ΅ΠΌ ΠΎΡΠ½ΠΎΠ²Π½ΡΡ ΠΏΠ°ΡΠΏΠΎΡΡΠ½ΡΡ Π΄Π°Π½Π½ΡΡ .
ΠΡΠΈ Π½Π΅ΡΠΎΠ±Π»ΡΠ΄Π΅Π½ΠΈΠΈ ΡΡΠΈΡ ΡΡΠ»ΠΎΠ²ΠΈΠΉ ΠΏΠ°ΡΡΠΈΡ ΡΠ²Π°ΡΠΎΡΠ½ΡΡ ΠΌΠ°ΡΠ΅ΡΠΈΠ°Π»ΠΎΠ² Π½Π΅ Π΄ΠΎΠΏΡΡΠΊΠ°Π΅ΡΡΡ ΠΊ ΠΈΡΠΏΠΎΠ»ΡΠ·ΠΎΠ²Π°Π½ΠΈΡ ΠΈ ΠΏΠΎΠ΄Π»Π΅ΠΆΠΈΡ ΠΏΠΎΠ»Π½ΠΎΠΉ ΠΏΡΠΎΠ²Π΅ΡΠΊΠ΅ ΠΏΠΎ Π²ΡΠ΅ΠΌ ΠΏΠΎΠΊΠ°Π·Π°ΡΠ΅Π»ΡΠΌ, ΡΡΡΠ°Π½ΠΎΠ²Π»Π΅Π½Π½ΡΠΌ Π΄Π»Ρ Π΄Π°Π½Π½ΠΎΠ³ΠΎ Π²ΠΈΠ΄Π° ΡΠ²Π°ΡΠΎΡΠ½ΡΡ ΠΌΠ°ΡΠ΅ΡΠΈΠ°Π»ΠΎΠ².
ΠΠΎΠΏΡΠΎΡ ΠΎ Π²ΠΎΠ·ΠΌΠΎΠΆΠ½ΠΎΡΡΠΈ ΠΈΡΠΏΠΎΠ»ΡΠ·ΠΎΠ²Π°Π½ΠΈΡ ΡΠ²Π°ΡΠΎΡΠ½ΡΡ ΠΌΠ°ΡΠ΅ΡΠΈΠ°Π»ΠΎΠ², ΠΈΠΌΠ΅ΡΡΠΈΡ Π½Π΅ΡΠΎΠΎΡΠ²Π΅ΡΡΡΠ²ΠΈΠ΅ ΠΊΠ°ΡΠ΅ΡΡΠ²Π° ΠΈΠ»ΠΈ ΠΏΠΎΠ²ΡΠ΅ΠΆΠ΄Π΅Π½ΠΈΠ΅ ΡΠΏΠ°ΠΊΠΎΠ²ΠΊΠΈ, ΡΠ΅ΡΠ°Π΅ΡΡΡ ΡΠ»ΡΠΆΠ±ΠΎΠΉ Π³Π»Π°Π²Π½ΠΎΠ³ΠΎ ΡΠ²Π°ΡΡΠΈΠΊΠ° ΠΏΡΠ΅Π΄ΠΏΡΠΈΡΡΠΈΡ (ΠΎΡΠ³Π°Π½ΠΈΠ·Π°ΡΠΈΠΈ).
ΠΠΎΠ½ΡΡΠΎΠ»Ρ ΡΠ»Π΅ΠΊΡΡΠΎΠ΄ΠΎΠ²
ΠΠ°ΡΠ΅ΡΡΠ²ΠΎ ΡΠ»Π΅ΠΊΡΡΠΎΠ΄ΠΎΠ² ΠΏΡΠΎΠ²Π΅ΡΡΡΡ Π² ΠΏΡΠΎΡΠ΅ΡΡΠ΅ ΠΈΡ ΠΈΠ·Π³ΠΎΡΠΎΠ²Π»Π΅Π½ΠΈΡ Π½Π° Π·Π°Π²ΠΎΠ΄Π°Ρ ΠΈ ΠΏΠ΅ΡΠ΅Π΄ Π½Π°ΡΠ°Π»ΠΎΠΌ ΡΠ²Π°ΡΠΎΡΠ½ΡΡ ΡΠ°Π±ΠΎΡ Π² ΡΠ΅Ρ Π°Ρ ΠΈΠ»ΠΈ Π½Π° ΡΡΡΠΎΠΈΡΠ΅Π»ΡΠ½ΡΡ ΠΏΠ»ΠΎΡΠ°Π΄ΠΊΠ°Ρ .
ΠΠΎΠΊΡΡΡΠΈΠ΅ Π΄ΠΎΠ»ΠΆΠ½ΠΎ Π±ΡΡΡ ΠΏΠ»ΠΎΡΠ½ΡΠΌ ΠΈ ΠΏΡΠΎΡΠ½ΡΠΌ, Ρ ΠΎΡΠΎΡΠΎ ΡΠ΄Π΅ΡΠΆΠΈΠ²Π°ΡΡΡΡ Π½Π° ΡΠ»Π΅ΠΊΡΡΠΎΠ΄Π½ΠΎΠΌ ΡΡΠ΅ΡΠΆΠ½Π΅ ΠΈ Π½Π΅ ΡΠ°Π·ΡΡΡΠ°ΡΡΡΡ (ΠΏΠΎ ΠΠΠ‘Π’ 9466β60) ΠΏΡΠΈ ΡΠ²ΠΎΠ±ΠΎΠ΄Π½ΠΎΠΌ ΠΏΠ°Π΄Π΅Π½ΠΈΠΈ ΡΠ»Π΅ΠΊΡΡΠΎΠ΄Π° ΠΏΠ»Π°ΡΠΌΡ Π½Π° Π³Π»Π°Π΄ΠΊΡΡ ΡΡΠ°Π»ΡΠ½ΡΡ ΠΏΠ»ΠΈΡΡ Ρ Π²ΡΡΠΎΡΡ 1 ΠΌ Π΄Π»Ρ ΡΠ»Π΅ΠΊΡΡΠΎΠ΄ΠΎΠ² Π΄ΠΈΠ°ΠΌΠ΅ΡΡΠΎΠΌ 3 ΠΌΠΌ ΠΈ ΠΌΠ΅Π½Π΅Π΅ ΠΈ Ρ Π²ΡΡΠΎΡΡ 0,5 ΠΌ Π΄Π»Ρ ΡΠ»Π΅ΠΊΡΡΠΎΠ΄ΠΎΠ² Π΄ΠΈΠ°ΠΌΠ΅ΡΡΠΎΠΌ Π±ΠΎΠ»Π΅Π΅ 3 ΠΌΠΌ. ΠΠΎΠΏΡΡΠΊΠ°ΡΡΡΡ ΡΠ°ΡΡΠΈΡΠ½ΡΠ΅ ΠΎΡΠΊΠ°Π»ΡΠ²Π°Π½ΠΈΡ ΠΏΠΎΠΊΡΡΡΠΈΡ ΠΎΠ±ΡΠ΅ΠΉ Π΄Π»ΠΈΠ½ΠΎΠΉ Π½Π΅ Π±ΠΎΠ»Π΅Π΅ 20 ΠΌΠΌ.Β Β Β Β Β Β
ΠΠΎΠΊΡΡΡΠΈΠ΅ ΡΠ»Π΅ΠΊΡΡΠΎΠ΄ΠΎΠ² Π΄ΠΎΠ»ΠΆΠ½ΠΎ Π±ΡΡΡ Π²Π»Π°Π³ΠΎΡΡΠΎΠΉΠΊΠΈΠΌ ΠΈ Π½Π΅ ΡΠ°Π·ΡΡΡΠ°ΡΡΡΡ ΠΏΠΎΡΠ»Π΅ ΠΏΡΠ΅Π±ΡΠ²Π°Π½ΠΈΡ Π² Π²ΠΎΠ΄Π΅ Ρ ΡΠ΅ΠΌΠΏΠ΅ΡΠ°ΡΡΡΠΎΠΉ 15β25Β° Π‘ Π² ΡΠ΅ΡΠ΅Π½ΠΈΠ΅ 24 Ρ. ΠΠΎΠΏΡΡΠΊΠ°ΡΡΡΡ ΡΠ»Π΅Π΄ΡΡΡΠΈΠ΅ Π΄Π΅ΡΠ΅ΠΊΡΡ ΠΏΠΎΠ²Π΅ΡΡ
Π½ΠΎΡΡΠΈ ΡΠ»Π΅ΠΊΡΡΠΎΠ΄ΠΎΠ²:
ΡΠ΅ΡΠΎΡ ΠΎΠ²Π°ΡΠΎΡΡΡ ΠΏΠΎΠ²Π΅ΡΡ Π½ΠΎΡΡΠΈ, ΠΏΡΠΎΠ΄ΠΎΠ»ΡΠ½ΡΠ΅ ΡΠΈΡΠΊΠΈ ΠΈ ΠΎΡΠ΄Π΅Π»ΡΠ½ΡΠ΅ Π·Π°Π΄ΠΈΡΡ β Π³Π»ΡΠ±ΠΈΠ½ΠΎΠΉ Π½Π΅ Π±ΠΎΠ»Π΅Π΅ 1/4 ΡΠΎΠ»ΡΠΈΠ½Ρ ΠΏΠΎΠΊΡΡΡΠΈΡ;
ΠΌΠ΅ΡΡΠ½ΡΠ΅ Π²ΠΌΡΡΠΈΠ½Ρ β Π² ΠΊΠΎΠ»ΠΈΡΠ΅ΡΡΠ²Π΅ Π½Π΅ Π±ΠΎΠ»Π΅Π΅ ΡΡΠ΅Ρ , Π³Π»ΡΠ±ΠΈΠ½ΠΎΠΉ Π΄Π° 1/2 ΡΠΎΠ»ΡΠΈΠ½Ρ ΠΏΠΎΠΊΡΡΡΠΈΡ ΠΈ Π΄Π»ΠΈΠ½ΠΎΠΉ Π΄ΠΎ 12 ΠΌΠΌ ΠΊΠ°ΠΆΠ΄Π°Ρ;
ΠΏΠΎΡΡ β Π² ΠΊΠΎΠ»ΠΈΡΠ΅ΡΡΠ²Π΅ Π½Π΅ Π±ΠΎΠ»Π΅Π΅ ΡΡΠ΅Ρ Π½Π° Π΄Π»ΠΈΠ½Π΅ 100 ΠΌΠΌ, Π΄ΠΈΠ°ΠΌΠ΅ΡΡΠΎΠΌ Π΄ΠΎ 2 ΠΌΠΌ, Π³Π»ΡΠ±ΠΈΠ½ΠΎΠΉ Π΄ΠΎ 1/2 ΡΠΎΠ»ΡΠΈΠ½Ρ;
Π²ΠΎΠ»ΠΎΡΠ½ΡΠ΅ ΡΡΠ΅ΡΠΈΠ½Ρ β Π² ΠΊΠΎΠ»ΠΈΡΠ΅ΡΡΠ²Π΅ Π½Π΅ Π±ΠΎΠ»Π΅Π΅ Π΄Π²ΡΡ , Π΄Π»ΠΈΠ½ΠΎΠΉ Π΄ΠΎ 12 ΠΌΠΌ ΠΊΠ°ΠΆΠ΄Π°Ρ.
ΠΠΎΠ½ΡΡΠΎΠ»Ρ ΠΊΠ°ΡΠ΅ΡΡΠ²Π° ΡΠ»Π΅ΠΊΡΡΠΎΠ΄ΠΎΠ² Π² Π·Π°Π²ΠΎΠ΄ΡΠΊΠΈΡ ΠΈ ΠΌΠΎΠ½ΡΠ°ΠΆΠ½ΡΡ ΡΡΠ»ΠΎΠ²ΠΈΡΡ ΠΏΠ΅ΡΠ΅Π΄ ΡΠ²Π°ΡΠΊΠΎΠΉ ΠΊΠΎΠ½ΡΡΡΡΠΊΡΠΈΠΉ, ΡΠ°Π±ΠΎΡΠ°ΡΡΠΈΡ Π² ΡΡΠΆΠ΅Π»ΡΡ ΡΡΠ»ΠΎΠ²ΠΈΡΡ (Π²ΠΈΠ±ΡΠ°ΡΠΈΠΎΠ½Π½Π°Ρ Π½Π°Π³ΡΡΠ·ΠΊΠ°, Π²ΡΡΠΎΠΊΠ°Ρ ΡΠ΅ΠΌΠΏΠ΅ΡΠ°ΡΡΡΠ° ΠΈ Π΄Π°Π²Π»Π΅Π½ΠΈΠ΅, ΡΡΠ°Π½ΡΠΏΠΎΡΡΠΈΡΠΎΠ²ΠΊΠ° ΡΠΎΠΊΡΠΈΡΠ½ΡΡ Π³Π°Π·ΠΎΠ²), Π·Π°ΠΊΠ»ΡΡΠ°Π΅ΡΡΡ Π² ΠΏΡΠΎΠ²Π΅ΡΠΊΠ΅ Π½Π°Π»ΠΈΡΠΈΡ ΡΠ΅ΡΡΠΈΡΠΈΠΊΠ°ΡΠΎΠ² ΠΈ Π²ΡΠ±ΠΎΡΠΎΡΠ½ΠΎΠΌ ΠΊΠΎΠ½ΡΡΠΎΠ»Π΅ ΡΠΎΡΡΠΎΡΠ½ΠΈΡ Π²Π½Π΅ΡΠ½Π΅ΠΉ ΠΏΠΎΠ²Π΅ΡΡ Π½ΠΎΡΡΠΈ. ΠΡΠΎΠΌΠ΅ ΡΠΎΠ³ΠΎ, ΠΏΡΠΎΠ²Π΅ΡΡΡΡ ΠΌΠ΅Ρ Π°Π½ΠΈΡΠ΅ΡΠΊΠΈΠ΅ ΠΈ ΡΠ΅Ρ Π½ΠΎΠ»ΠΎΠ³ΠΈΡΠ΅ΡΠΊΠΈΠ΅ ΡΠ²ΠΎΠΉΡΡΠ²Π° Π½Π°ΠΏΠ»Π°Π²Π»Π΅Π½Π½ΠΎΠ³ΠΎ ΠΌΠ΅ΡΠ°Π»Π»Π°, Π° ΡΠ°ΠΊΠΆΠ΅, ΠΏΡΠΈ Π½Π΅ΠΎΠ±Ρ ΠΎΠ΄ΠΈΠΌΠΎΡΡΠΈ, Π²ΡΠΏΠΎΠ»Π½ΡΡΡ ΠΌΠ΅ΡΠ°Π»Π»ΠΎΠ³ΡΠ°ΡΠΈΡΠ΅ΡΠΊΠΈΠΉ Π°Π½Π°Π»ΠΈΠ·. Π’Π°ΠΊΠ°Ρ ΠΏΡΠΎΠ²Π΅ΡΠΊΠ° Π½Π΅ΠΎΠ±Ρ ΠΎΠ΄ΠΈΠΌΠ° ΠΈ Π² ΡΠ΅Ρ ΡΠ»ΡΡΠ°ΡΡ , Π΅ΡΠ»ΠΈ ΠΏΡΠΈΠΌΠ΅Π½ΡΠ΅ΠΌΡΠ΅ ΡΠ»Π΅ΠΊΡΡΠΎΠ΄Ρ Π΄Π°ΡΡ Π½Π΅ΡΡΠ°Π±ΠΈΠ»ΡΠ½ΡΡ Π΄ΡΠ³Ρ, ΠΈΠΌΠ΅ΡΡ Π½Π΅ΡΠ°Π²Π½ΠΎΠΌΠ΅ΡΠ½ΠΎΠ΅ ΠΏΠ»Π°Π²Π»Π΅Π½ΠΈΠ΅ ΠΈΠ»ΠΈ Π΅ΡΠ»ΠΈ Π² ΡΠ²Π°ΡΠ½ΠΎΠΌ ΡΠ²Π΅ Π²ΠΎΠ·Π½ΠΈΠΊΠ°ΡΡ ΡΡΠ΅ΡΠΈΠ½Ρ ΠΈ ΠΏΠΎΡΡ.
ΠΠ»Ρ Π²Π½Π΅ΡΠ½Π΅Π³ΠΎ ΠΎΡΠΌΠΎΡΡΠ° ΠΎΡΠ±ΠΈΡΠ°ΡΡ 10β15 ΡΠ»Π΅ΠΊΡΡΠΎΠ΄ΠΎΠ² ΠΈΠ· ΡΠ°Π·Π½ΡΡ ΠΏΠ°ΡΠ΅ΠΊ. ΠΡΠΈ Π½Π°Π»ΠΈΡΠΈΠΈ Π½Π΅Π΄ΠΎΠΏΡΡΡΠΈΠΌΡΡ Π΄Π΅ΡΠ΅ΠΊΡΠΎΠ² Π±Π΅ΡΡΡ ΡΠ΄Π²ΠΎΠ΅Π½Π½ΠΎΠ΅ ΠΊΠΎΠ»ΠΈΡΠ΅ΡΡΠ²ΠΎ, Π° ΠΏΡΠΈ ΠΏΠΎΠ²ΡΠΎΡΠ½ΠΎΠΌ ΠΎΠ±Π½Π°ΡΡΠΆΠ΅Π½ΠΈΠΈ Π΄Π΅ΡΠ΅ΠΊΡΠΎΠ² Π²ΡΡ ΠΏΠ°ΡΡΠΈΡ ΡΠ»Π΅ΠΊΡΡΠΎΠ΄ΠΎΠ² Π±ΡΠ°ΠΊΡΡΡ, ΡΠΎΡΡΠ°Π²Π»ΡΡ ΡΠ΅ΠΊΠ»Π°ΠΌΠ°ΡΠΈΠΎΠ½Π½ΡΠΉ Π°ΠΊΡ.
ΠΠΎΠΊΡΡΡΠΈΠ΅ ΡΠ»Π΅ΠΊΡΡΠΎΠ΄ΠΎΠ² Π΄ΠΎΠ»ΠΆΠ½ΠΎ Π±ΡΡΡ ΠΊΠΎΠ½ΡΠ΅Π½ΡΡΠΈΡΠ½ΠΎ ΠΎΡΠ½ΠΎΡΠΈΡΠ΅Π»ΡΠ½ΠΎ ΡΡΠ΅ΡΠΆΠ½Ρ. ΠΠ»Ρ ΠΏΡΠΎΠ²Π΅ΡΠΊΠΈ ΠΊΠΎΠ½ΡΠ΅Π½ΡΡΠΈΡΠ½ΠΎΡΡΠΈ Π² ΡΠ°Π·Π½ΡΡ ΡΠ΅ΡΠ΅Π½ΠΈΡΡ ΠΏΠΎ Π΄Π»ΠΈΠ½Π΅ ΡΠ»Π΅ΠΊΡΡΠΎΠ΄Π° Π΄Π΅Π»Π°ΡΡ Π½Π°Π΄ΡΠ΅Π·Ρ ΠΈ Π·Π°ΠΌΠ΅ΡΡΡΡ ΡΠΎΠ»ΡΠΈΠ½Ρ ΠΏΠΎΠΊΡΡΡΠΈΡ.
ΠΠ΅Π»ΠΈΡΠΈΠ½Π° ΡΠ°Π·Π½ΠΎΡΡΠΈ ΡΠΎΠ»ΡΠΈΠ½ Π½Π΅ Π΄ΠΎΠ»ΠΆΠ½Π° ΠΏΡΠ΅Π²ΡΡΠ°ΡΡ:
ΠΏΡΠΈ Π΄ΠΈΠ°ΠΌΠ΅ΡΡΠ΅ ΡΠ»Π΅ΠΊΡΡΠΎΠ΄Π° 2 ΠΌΠΌ ….Β Β Β 0,08 ΠΌΠΌ
ΠΏΡΠΈ Π΄ΠΈΠ°ΠΌΠ΅ΡΡΠ΅ ΡΠ»Π΅ΠΊΡΡΠΎΠ΄Π° 2,5 ΠΌΠΌ………..0,1 ΠΌΠΌ
ΠΏΡΠΈ Π΄ΠΈΠ°ΠΌΠ΅ΡΡΠ΅ ΡΠ»Π΅ΠΊΡΡΠΎΠ΄Π° 3 ΠΌΠΌ ………..0,15 ΠΌΠΌ
ΠΏΡΠΈ Π΄ΠΈΠ°ΠΌΠ΅ΡΡΠ΅ ΡΠ»Π΅ΠΊΡΡΠΎΠ΄Π° 4 ΠΌΠΌ ………..0,2 ΠΌΠΌ
ΠΏΡΠΈ Π΄ΠΈΠ°ΠΌΠ΅ΡΡΠ΅ ΡΠ»Π΅ΠΊΡΡΠΎΠ΄Π° 5 ΠΌΠΌ ………..0,25 ΠΌΠΌ
ΠΏΡΠΈ Π΄ΠΈΠ°ΠΌΠ΅ΡΡΠ΅ ΡΠ»Π΅ΠΊΡΡΠΎΠ΄Π°Β 6 ΠΌΠΌ ΠΈ Π±ΠΎΠ»Π΅Π΅…….0,3 ΠΌΠΌ
ΠΡΠΎΠ²Π΅ΡΠΊΡ ΡΠ»Π΅ΠΊΡΡΠΎΠ΄ΠΎΠ² Π½Π° ΡΠ²Π°ΡΠΈΠ²Π°Π΅ΠΌΠΎΡΡΡ ΠΈ ΠΏΠΎ ΠΌΠ΅Ρ Π°Π½ΠΈΡΠ΅ΡΠΊΠΈΠΌ ΡΠ²ΠΎΠΉΡΡΠ²Π°ΠΌ Π²ΡΠΏΠΎΠ»Π½ΡΡΡ ΠΏΠ΅ΡΠΈΠΎΠ΄ΠΈΡΠ΅ΡΠΊΠΈ Π΄Π»Ρ ΡΠ°Π·Π»ΠΈΡΠ½ΡΡ ΠΏΠ°ΡΡΠΈΠΉ. ΠΡΠΈ ΡΡΠΎΠΌ Π½Π°ΠΏΠ»Π°Π²ΠΊΡ Π²Π΅Π΄ΡΡ Π½Π° ΠΏΠ»Π°ΡΡΠΈΠ½Π°Ρ ΠΈΠ· ΡΠ³Π»Π΅ΡΠΎΠ΄ΠΈΡΡΠΎΠΉ ΠΈΠ»ΠΈ Π½ΠΈΠ·ΠΊΠΎΠ»Π΅Π³ΠΈΡΠΎΠ²Π°Π½Π½ΠΎΠΉ ΡΡΠ°Π»ΠΈ ΡΠΎΠ»ΡΠΈΠ½ΠΎΠΉ 10β14 ΠΌΠΌ (ΠΌΠΎΠΆΠ½ΠΎ ΡΠ°ΠΊΠΆΠ΅ ΡΠ²Π°ΡΠΈΠ²Π°ΡΡ ΡΡΡΠ±Ρ Ρ ΡΠΎΠ»ΡΠΈΠ½ΠΎΠΉ ΡΡΠ΅Π½ΠΊΠΈ Π½Π΅ ΠΌΠ΅Π½Π΅Π΅ 8 ΠΌΠΌ).
ΠΠ»Ρ ΡΠ»Π΅ΠΊΡΡΠΎΠ΄ΠΎΠ², Π΄Π°ΡΡΠΈΡ Π°ΡΡΡΠ΅Π½ΠΈΡΠ½ΡΠΉ Π½Π°ΠΏΠ»Π°Π²Π»Π΅Π½Π½ΡΠΉ ΠΌΠ΅ΡΠ°Π»Π», ΠΏΡΠΎΠ²Π΅ΡΡΡΡ Π½Π°Π»ΠΈΡΠΈΠ΅ Π² Π½Π΅ΠΌ ΡΠ΅ΡΡΠΈΡΠ½ΠΎΠΉ ΡΠ°Π·Ρ, Π΄Π»Ρ ΡΠ΅Π³ΠΎ Π½Π°ΠΏΠ»Π°Π²Π»ΡΠ΅ΡΡΡ ΠΏΡΡΡ β ΡΠ΅ΡΡΡ ΡΠ»ΠΎΠ΅Π² Π½Π° ΠΏΠ»Π°ΡΡΠΈΠ½Ρ ΠΈΠ»ΠΈ ΡΡΡΠ±Ρ ΠΈΠ· Π°ΡΡΡΠ΅Π½ΠΈΡΠ½ΠΎΠΉ ΡΡΠ°Π»ΠΈ. Π Π΅ΠΆΠΈΠΌ Π½Π°ΠΏΠ»Π°Π²ΠΊΠΈ Π²ΡΠ±ΠΈΡΠ°ΡΡ Π² ΡΠΎΠΎΡΠ²Π΅ΡΡΡΠ²ΠΈΠΈ Ρ ΡΠ΅ΠΊΠΎΠΌΠ΅Π½Π΄ΠΎΠ²Π°Π½Π½ΡΠΌΠΈ Π΄Π»Ρ ΡΠ»Π΅ΠΊΡΡΠΎΠ΄ΠΎΠ² Π΄Π°Π½Π½ΠΎΠ³ΠΎ ΡΠΈΠΏΠ° ΠΈ Π΄ΠΈΠ°ΠΌΠ΅ΡΡΠ°.
Π‘ΠΎΠ΄Π΅ΡΠΆΠ°Π½ΠΈΠ΅ ΡΠ΅ΡΡΠΈΡΠ° ΠΎΠΏΡΠ΅Π΄Π΅Π»ΡΡΡ ΠΎΠ±ΡΠ΅ΠΌΠ½ΡΠΌ ΠΌΠ°Π³Π½ΠΈΡΠ½ΡΠΌ ΠΌΠ΅ΡΠΎΠ΄ΠΎΠΌ Ρ ΠΏΠΎΠΌΠΎΡΡΡ ΡΠ΅ΡΡΠΈΡΠΎΠΌΠ΅ΡΠ° Π»ΠΈΠ±ΠΎ ΠΌΠ΅ΡΠ°Π»Π»ΠΎΠ³ΡΠ°ΡΠΈΡΠ΅ΡΠΊΠΈΠΌ ΠΌΠ΅ΡΠΎΠ΄ΠΎΠΌ Π½Π° ΠΎΠ±ΡΠ°Π·ΡΠ°Ρ Π΄ΠΈΠ°ΠΌΠ΅ΡΡΠΎΠΌ 5 ΠΌΠΌ ΠΈ Π΄Π»ΠΈΠ½ΠΎΠΉ 60 ΠΌΠΌ, Π²ΡΡΠ΅Π·Π°Π½Π½ΡΡ ΠΈΠ· Π΄Π²ΡΡ Π²Π΅ΡΡ Π½ΠΈΡ ΡΠ»ΠΎΠ΅Π² Π½Π°ΠΏΠ»Π°Π²ΠΊΠΈ. ΠΠ±ΡΠ°Π·ΡΡ ΡΡΠ°Π²ΡΡ Π² ΡΠ΅ΡΠ΅Π½ΠΈΠ΅ 2β2,5 ΠΌΠΈΠ½ ΡΠ΅Π°ΠΊΡΠΈΠ²ΠΎΠΌ, ΡΠΎΡΡΠΎΡΡΠΈΠΌ ΠΈΠ· ΠΊΡΠ°ΡΠ½ΠΎΠΉ ΠΊΡΠΎΠ²ΡΠ½ΠΎΠΉ ΡΠΎΠ»ΠΈ (10 Π³), Π΅Π΄ΠΊΠΎΠ³ΠΎ Π½Π°ΡΡΠ° (10 Π³) ΠΈ Π²ΠΎΠ΄Ρ (100 Π³).
ΠΡΠΏΡΡΠ°Π½ΠΈΠ΅ ΠΌΠ΅ΡΠ°Π»Π»Π°, ΡΠ²Π° ΠΈΠ»ΠΈ ΡΠ²Π°ΡΠ½ΠΎΠ³ΠΎ ΡΠΎΠ΅Π΄ΠΈΠ½Π΅Π½ΠΈΡ Π½Π° ΠΌΠ΅ΠΆΠΊΡΠΈΡΡΠ°Π»Π»ΠΈΡΠ½ΡΡ ΠΊΠΎΡΡΠΎΠ·ΠΈΡ ΠΏΡΠΎΠ²ΠΎΠ΄ΡΡ Π² ΡΠΎΠΎΡΠ²Π΅ΡΡΡΠ²ΠΈΠΈ Ρ ΠΠΠ‘Π’ 6032β58*.
Π£ Π²ΡΠ΅Ρ ΡΠ»Π΅ΠΊΡΡΠΎΠ΄ΠΎΠ² ΠΈ ΠΏΡΠΈΡΠ°Π΄ΠΎΡΠ½ΡΡ ΠΏΡΠΎΠ²ΠΎΠ»ΠΎΠΊ Π΄Π»Ρ ΡΠ²Π°ΡΠΊΠΈ Π°ΡΡΡΠ΅Π½ΠΈΡΠ½ΡΡ ΡΡΠ°Π»Π΅ΠΉ ΠΏΡΠΎΠ²Π΅ΡΡΡΡ Π½Π° ΠΆΠ΅ΡΡΠΊΠΎΠΉ ΡΠ°Π²ΡΠΎΠ²ΠΎΠΉ ΠΏΡΠΎΠ±Π΅ ΠΈΠ»ΠΈ Π½Π° ΠΎΠ±ΡΠ°Π·ΡΠ΅ Ρ ΡΠ΅ΡΡΠΈΡΠ»ΠΎΠΉΠ½ΠΎΠΉ Π½Π°ΠΏΠ»Π°Π²ΠΊΠΎΠΉ ΡΠΊΠ»ΠΎΠ½Π½ΠΎΡΡΡ ΠΊ ΠΎΠ±ΡΠ°Π·ΠΎΠ²Π°Π½ΠΈΡ Π³ΠΎΡΡΡΠΈΡ ΡΡΠ΅ΡΠΈΠ½.
ΠΠ±ΡΠ°Π·Π΅Ρ ΠΈΠ·Π³ΠΎΡΠΎΠ²Π»ΡΡΡ ΠΈΠ· ΡΠΎΠΉ ΠΆΠ΅ ΠΌΠ°ΡΠΊΠΈ ΡΡΠ°Π»ΠΈ, ΡΡΠΎ ΠΈ ΡΠ²Π°ΡΠΈΠ²Π°Π΅ΠΌΠΎΠΉ ΠΊΠΎΠ½ΡΡΡΡΠΊΡΠΈΠΈ, Π° ΡΠ»Π΅ΠΊΡΡΠΎΠ΄Ρ Π±Π΅ΡΡΡ ΠΈΠ· ΠΏΠ°ΡΡΠΈΠΈ, ΠΏΡΠ΅Π΄Π½Π°Π·Π½Π°ΡΠ΅Π½Π½ΠΎΠΉ Π΄Π»Ρ ΡΠ²Π°ΡΠΊΠΈ.
Π¨Π΅ΡΡΠΈΡΠ»ΠΎΠΉΠ½ΡΡ Π½Π°ΠΏΠ»Π°Π²ΠΊΡ Π²Π΅Π΄ΡΡ Π² Π½ΠΈΠΆΠ½Π΅ΠΌ ΠΏΠΎΠ»ΠΎΠΆΠ΅Π½ΠΈΠΈ, Π° ΠΊΠ°ΠΆΠ΄ΡΠΉ ΡΠ»ΠΎΠΉ Π½Π°ΠΏΠ»Π°Π²Π»ΡΡΡ Π² ΠΎΠ΄Π½ΠΎΠΌ ΠΈ ΡΠΎΠΌ ΠΆΠ΅ Π½Π°ΠΏΡΠ°Π²Π»Π΅Π½ΠΈΠΈ. ΠΠ°ΠΆΠ΄ΡΠΉ ΠΏΠΎΡΠ»Π΅Π΄ΡΡΡΠΈΠΉ ΡΠ»ΠΎΠΉ ΠΊΠ»Π°Π΄ΡΡ ΠΏΠΎΡΠ»Π΅ ΠΏΠΎΠ»Π½ΠΎΠ³ΠΎ ΠΎΡΡΡΠ²Π°Π½ΠΈΡ ΠΏΡΠ΅Π΄ΡΠ΄ΡΡΠ΅Π³ΠΎ Π΄ΠΎ ΠΊΠΎΠΌΠ½Π°ΡΠ½ΠΎΠΉ ΡΠ΅ΠΌΠΏΠ΅ΡΠ°ΡΡΡΡ.
ΠΠΎΡΠ»Π΅ ΠΏΠΎΠ»Π½ΠΎΠ³ΠΎ ΠΎΡΡΡΠ²Π°Π½ΠΈΡ ΠΈ ΡΠ΄Π°Π»Π΅Π½ΠΈΡ ΡΠ»Π°ΠΊΠ° ΡΠΎ ΡΠ²Π° ΠΎΠ±ΡΠ°Π·Π΅Ρ ΠΎΡΠΌΠ°ΡΡΠΈΠ²Π°ΡΡ, ΠΈΠ·Π»Π°ΠΌΡΠ²Π°ΡΡ ΠΏΠΎ ΠΊΠΎΠ½ΡΡΠΎΠ»ΠΈΡΡΠ΅ΠΌΠΎΠΌΡ ΡΠ²Ρ ΠΈ ΠΏΡΠΎΠ²Π΅ΡΡΡΡ Π½Π°Π»ΠΈΡΠΈΠ΅ ΡΡΠ΅ΡΠΈΠ½.
ΠΠ°Π»Π΅Π΅ ΠΎΠ±ΡΠ°Π·Π΅Ρ ΡΠ°Π·ΡΠ΅Π·Π°ΡΡ Π½Π° ΡΡΠΈ ΡΠ°ΡΡΠΈ Π΄Π»Ρ ΠΈΠ·Π³ΠΎΡΠΎΠ²Π»Π΅Π½ΠΈΡ ΠΌΠ°ΠΊΡΠΎΡΠ»ΠΈΡΠΎΠ², ΠΊΠΎΡΠΎΡΡΠ΅ ΡΡΠ°Π²ΡΡ Π² ΡΠΎΠ»ΡΠ½ΠΎΠΉ ΠΊΠΈΡΠ»ΠΎΡΠ΅, ΠΏΡΠΎΠΌΡΠ²Π°ΡΡ, ΡΡΡΠ°Ρ ΠΈ ΡΠ°ΡΡΠΌΠ°ΡΡΠΈΠ²Π°ΡΡ ΠΏΠΎΠ΄ Π»ΡΠΏΠΎΠΉ Ρ 4β7-ΠΊΡΠ°ΡΠ½ΡΠΌ ΡΠ²Π΅Π»ΠΈΡΠ΅Π½ΠΈΠ΅ΠΌ.
ΠΡΠΈ Π½Π°Π»ΠΈΡΠΈΠΈ ΡΡΠ΅ΡΠΈΠ½ ΡΠ»Π΅ΠΊΡΡΠΎΠ΄Ρ Π±ΡΠ°ΠΊΡΡΡΡΡ.
ΠΡΠΎΠ²Π΅ΡΠ΅Π½Π½ΡΠ΅ ΡΠ»Π΅ΠΊΡΡΠΎΠ΄Ρ Ρ ΡΠ°Π½ΡΡ Π² ΡΡΡ ΠΎΠΌ ΠΏΠΎΠΌΠ΅ΡΠ΅Π½ΠΈΠΈ, Π½Π΅ Π΄ΠΎΠΏΡΡΠΊΠ°Ρ ΠΈΡ ΡΠ²Π»Π°ΠΆΠ½Π΅Π½ΠΈΡ. ΠΠ΅ΡΠ΅Π΄ ΡΠ²Π°ΡΠΊΠΎΠΉ ΡΠ»Π΅ΠΊΡΡΠΎΠ΄Ρ ΠΏΡΠΎΡΡΡΠΈΠ²Π°ΡΡ ΠΏΡΠΈ ΡΠ΅ΠΌΠΏΠ΅ΡΠ°ΡΡΡΠ΅ 150β180Β° Π‘ Π² ΡΠ΅ΡΠ΅Π½ΠΈΠ΅ 1,5β3 Ρ Π² ΡΡΡΠΈΠ»ΡΠ½ΡΡ ΠΏΠ΅ΡΠ°Ρ . ΠΠ°ΡΠ΅Π³ΠΎΡΠΈΡΠ΅ΡΠΊΠΈ Π·Π°ΠΏΡΠ΅ΡΠ°Π΅ΡΡΡ ΡΡΡΠΈΡΡ ΡΠ»Π΅ΠΊΡΡΠΎΠ΄Ρ Ρ ΠΏΠΎΠΌΠΎΡΡΡ Π³Π°Π·ΠΎΠ²ΡΡ Π³ΠΎΡΠ΅Π»ΠΎΠΊ ΠΈΠ»ΠΈ ΠΊΠΎΡΠΎΡΠΊΠΈΠΌ Π·Π°ΠΌΡΠΊΠ°Π½ΠΈΠ΅ΠΌ, ΡΠ°ΠΊ ΠΊΠ°ΠΊ ΡΡΠΎ ΠΏΡΠΈΠ²ΠΎΠ΄ΠΈΡ ΠΊ ΡΡ ΡΠ΄ΡΠ΅Π½ΠΈΡΠΌ Π·Π°ΡΠΈΡΠ½ΡΡ ΡΠ²ΠΎΠΉΡΡΠ² ΠΏΠΎΠΊΡΡΡΠΈΡ ΠΈ ΠΌΠΎΠΆΠ΅Ρ ΡΡΠ°ΡΡ ΠΏΡΠΈΡΠΈΠ½ΠΎΠΉ Π±ΡΠ°ΠΊΠ° ΡΠ²Π°ΡΠ½ΠΎΠ³ΠΎ ΡΠΎΠ΅Π΄ΠΈΠ½Π΅Π½ΠΈΡ.
ΠΠΎΠ½ΡΡΠΎΠ»Ρ ΡΠ»ΡΡΠ°
ΠΠ°ΡΠ΅ΡΡΠ²ΠΎ ΡΠ»ΡΡΠ°, ΠΏΠΎΡΡΡΠΏΠΈΠ²ΡΠ΅Π³ΠΎ Ρ Π·Π°Π²ΠΎΠ΄Π°-ΠΈΠ·Π³ΠΎΡΠΎΠ²ΠΈΡΠ΅Π»Ρ ΠΈ ΠΈΠΌΠ΅ΡΡΠ΅Π³ΠΎ ΡΠ΅ΡΡΠΈΡΠΈΠΊΠ°Ρ Ρ ΡΠΊΠ°Π·Π°Π½ΠΈΠ΅ΠΌ Π΅Π³ΠΎ Ρ ΠΈΠΌΠΈΡΠ΅ΡΠΊΠΎΠ³ΠΎ ΡΠΎΡΡΠ°Π²Π° ΠΈ Π³ΡΠ°Π½ΡΠ»ΡΡΠΈΠΈ, ΠΎΠΏΡΠ΅Π΄Π΅Π»ΡΡΡ Π² ΡΠΎΠΎΡΠ²Π΅ΡΡΡΠ²ΠΈΠΈ Ρ ΠΠΠ‘Π’ 9087β59 ΠΈΠ»ΠΈ Π’Π£ ΠΏΡΡΠ΅ΠΌ ΡΠ²Π°ΡΠΊΠΈ ΠΏΠ»Π°ΡΡΠΈΠ½ ΠΈΠ»ΠΈ ΡΡΡΠΊΠΎΠ² ΡΡΡΠ± Π½Π° ΡΠ΅ΠΆΠΈΠΌΠ°Ρ , ΠΎΠ±ΡΡΠ»ΠΎΠ²Π»Π΅Π½Π½ΡΡ ΡΠ΅Ρ Π½ΠΎΠ»ΠΎΠ³ΠΈΡΠ΅ΡΠΊΠΈΠΌ ΠΏΡΠΎΡΠ΅ΡΡΠΎΠΌ.
ΠΡΠ»ΠΈ Π² ΡΠ²Π°Ρ , Π½Π°ΠΏΠ»Π°Π²Π»Π΅Π½Π½ΡΡ ΠΏΠΎΠ΄ ΡΠ»ΠΎΠ΅ΠΌ ΡΠ»ΡΡΠ°, ΠΈΠΌΠ΅ΡΡΡΡ ΠΏΠΎΡΡ ΠΈΠ»ΠΈ ΡΡΠ΅ΡΠΈΠ½Ρ, ΡΠΎ ΡΡΠ°ΡΠ΅Π»ΡΠ½ΠΎ ΠΏΡΠΎΠ²Π΅ΡΡΡΡ Π³ΡΠ°Π½ΡΠ»ΠΎΠΌΠ΅ΡΡΠΈΡΠ΅ΡΠΊΠΈΠΉ ΡΠΎΡΡΠ°Π², ΠΎΠ΄Π½ΠΎΡΠΎΠ΄Π½ΠΎΡΡΡ, ΠΎΠ±ΡΠ΅ΠΌΠ½ΡΠΉ Π²Π΅Ρ, Π²Π»Π°ΠΆΠ½ΠΎΡΡΡ ΠΈ Π·Π°Π³ΡΡΠ·Π½Π΅Π½Π½ΠΎΡΡΡ ΡΠ»ΡΡΠ° (Π΅ΡΠ»ΠΈ Π²Π»Π°ΠΆΠ½ΠΎΡΡΡ ΠΏΡΠ΅Π²ΡΡΠ°Π΅Ρ 0,1%, ΡΠ»ΡΡ ΠΏΡΠΎΡΡΡΠΈΠ²Π°ΡΡ).
ΠΠΎΡΠ»Π΅ ΡΠ°ΠΊΠΎΠΉ ΠΏΡΠΎΠ²Π΅ΡΠΊΠΈ Π½Π°ΠΏΠ»Π°Π²Π»ΡΡΡ ΡΠΎΠ² ΠΏΠΎΠ΄ ΡΠ»ΠΎΠ΅ΠΌ ΡΠ»ΡΡΠ° Π½Π° ΡΠ°Π²ΡΠΎΠ²ΠΎΠΌ ΠΎΠ±ΡΠ°Π·ΡΠ΅ ΠΈ ΠΈΡΡΠ»Π΅Π΄ΡΡΡ Π½Π°ΠΏΠ»Π°Π²Π»Π΅Π½Π½ΡΠΉ ΠΌΠ΅ΡΠ°Π»Π» Π½Π° ΡΠΎΠ΄Π΅ΡΠΆΠ°Π½ΠΈΠ΅ ΡΠ³Π»Π΅ΡΠΎΠ΄Π° ΠΈ ΡΠ΅ΡΡ ΠΏΡΡΠ΅ΠΌ Ρ ΠΈΠΌΠΈΡΠ΅ΡΠΊΠΎΠ³ΠΎ Π°Π½Π°Π»ΠΈΠ·Π° ΠΏΡΠΎΠ±Ρ, Π²Π·ΡΡΠΎΠΉ ΠΈΠ· Π²Π΅ΡΡ Π½Π΅Π³ΠΎ ΡΠ»ΠΎΡ ΡΠ²Π°ΡΠ½ΠΎΠ³ΠΎ ΡΠΎΠ΅Π΄ΠΈΠ½Π΅Π½ΠΈΡ.
ΠΡΠΈ Π½Π΅ΡΠ΄ΠΎΠ²Π»Π΅ΡΠ²ΠΎΡΠΈΡΠ΅Π»ΡΠ½ΡΡ ΡΠ΅Π·ΡΠ»ΡΡΠ°ΡΠ°Ρ ΠΊΠΎΠ½ΡΡΠΎΠ»Ρ ΠΏΡΠΎΠ²Π΅ΡΡΠ΅ΠΌΠ°Ρ ΠΏΠ°ΡΡΠΈΡ ΡΠ»ΡΡΠ° Π·Π°Π±ΡΠ°ΠΊΠΎΠ²ΡΠ²Π°Π΅ΡΡΡ ΠΈΠ»ΠΈ ΠΏΠΎΠ΄Π²Π΅ΡΠ³Π°Π΅ΡΡΡ ΠΏΠΎΠ²ΡΠΎΡΠ½ΠΎΠΉ ΠΏΡΠΎΠΊΠ°Π»ΠΊΠ΅ Ρ ΠΏΠΎΡΠ»Π΅Π΄ΡΡΡΠ΅ΠΉ ΠΏΠΎΠ»Π½ΠΎΠΉ ΠΏΠ΅ΡΠ΅ΠΏΡΠΎΠ²Π΅ΡΠΊΠΎΠΉ, Π²ΠΊΠ»ΡΡΠ°Ρ ΠΎΠΏΡΠ΅Π΄Π΅Π»Π΅Π½ΠΈΠ΅ Ρ ΠΈΠΌΠΈΡΠ΅ΡΠΊΠΎΠ³ΠΎ ΡΠΎΡΡΠ°Π²Π° ΡΠ»ΡΡΠ°.
Π’Π°ΠΊΠΈΠΌ ΠΆΠ΅ ΠΎΠ±ΡΠ°Π·ΠΎΠΌ ΠΏΡΠΎΠ²Π΅ΡΡΡΡ ΠΊΠ°ΡΠ΅ΡΡΠ²ΠΎ ΡΠ»ΡΡΠ°, ΠΏΡΠ΅Π΄Π½Π°Π·Π½Π°ΡΠ΅Π½Π½ΠΎΠ³ΠΎ Π΄Π»Ρ ΡΠ²Π°ΡΠΊΠΈ ΠΊΠΎΠ½ΡΡΡΡΠΊΡΠΈΠΉ, ΡΠ°Π±ΠΎΡΠ°ΡΡΠΈΡ Π² ΡΡΠΆΠ΅Π»ΡΡ ΡΡΠ»ΠΎΠ²ΠΈΡΡ .
ΠΠΎΠ½ΡΡΠΎΠ»Ρ Π·Π°ΡΠΈΡΠ½ΡΡ Π³Π°Π·ΠΎΠ²
ΠΠ°ΡΠΈΡΠ½ΡΠ΅ Π³Π°Π·Ρ (ΡΠ³Π»Π΅ΠΊΠΈΡΠ»ΡΠΉ Π³Π°Π·, Π°ΡΠ³ΠΎΠ½, Π³Π΅Π»ΠΈΠΉ) ΠΏΠΎΡΡΠ°Π²Π»ΡΡΡΡΡ Π² Π±Π°Π»Π»ΠΎΠ½Π°Ρ , ΠΊΠΎΡΠΎΡΡΠ΅ Π΄ΠΎΠ»ΠΆΠ½Ρ ΠΈΠΌΠ΅ΡΡ ΡΠ΅ΡΡΠΈΡΠΈΠΊΠ°Ρ Π·Π°Π²ΠΎΠ΄Π°-ΠΏΠΎΡΡΠ°Π²ΡΠΈΠΊΠ° Ρ ΡΠΊΠ°Π·Π°Π½ΠΈΠ΅ΠΌ ΠΠΠ‘Π’Π°, Π½Π°Π·Π²Π°Π½ΠΈΡ Π³Π°Π·Π°, ΠΏΡΠΎΡΠ΅Π½ΡΠ½ΠΎΠ³ΠΎ ΠΊΠΎΠ»ΠΈΡΠ΅ΡΡΠ²Π° ΠΏΡΠΈΠΌΠ΅ΡΠ΅ΠΉ, Π²Π»Π°ΠΆΠ½ΠΎΡΡΠΈ ΠΈ Π΄Π°ΡΡ Π²ΡΠΏΡΡΠΊΠ°. ΠΡΠΏΠΎΠ»ΡΠ·ΠΎΠ²Π°Π½ΠΈΠ΅ Π±Π°Π»Π»ΠΎΠ½ΠΎΠ² Ρ Π·Π°ΡΠΈΡΠ½ΡΠΌΠΈ Π³Π°Π·Π°ΠΌΠΈ, Π½Π΅ ΠΈΠΌΠ΅ΡΡΠΈΡ ΡΠ΅ΡΡΠΈΡΠΈΠΊΠ°ΡΠΎΠ², Π·Π°ΠΏΡΠ΅ΡΠ°Π΅ΡΡΡ.
ΠΡΠΈ Π½Π°Π»ΠΈΡΠΈΠΈ ΡΠ΅ΡΡΠΈΡΠΈΠΊΠ°ΡΠΎΠ² ΠΊΠ°ΡΠ΅ΡΡΠ²ΠΎ Π·Π°ΡΠΈΡΠ½ΡΡ Π³Π°Π·ΠΎΠ² ΠΏΡΠΎΠ²Π΅ΡΡΡΡ ΡΠΎΠ»ΡΠΊΠΎ Π² ΡΠ΅Ρ ΡΠ»ΡΡΠ°ΡΡ , ΠΊΠΎΠ³Π΄Π° Π² ΡΠ²Π°ΡΠ½ΡΡ ΡΠ²Π°Ρ ΠΎΠ±Π½Π°ΡΡΠΆΠΈΠ²Π°ΡΡΡΡ ΠΏΠΎΡΡ, ΡΡΠ΅ΡΠΈΠ½Ρ ΠΈ Π΄ΡΡΠ³ΠΈΠ΅ Π½Π΅Π΄ΠΎΠΏΡΡΡΠΈΠΌΡΠ΅ Π΄Π΅ΡΠ΅ΠΊΡΡ.
ΠΠΎΠ½ΡΡΠΎΠ»Ρ ΡΠ²Π°ΡΠΎΡΠ½ΠΎΠΉ ΠΈ Π½Π°ΠΏΠ»Π°Π²ΠΎΡΠ½ΠΎΠΉ ΠΏΡΠΎΠ²ΠΎΠ»ΠΎΠΊΠΈ
ΠΡΠΎΠ²ΠΎΠ»ΠΎΠΊΠ° ΠΏΠΎΡΡΠ°Π²Π»ΡΠ΅ΡΡΡ Π² Π±ΡΡ ΡΠ°Ρ Ρ ΠΌΠ΅ΡΠ°Π»Π»ΠΈΡΠ΅ΡΠΊΠΈΠΌΠΈ Π±ΠΈΡΠΊΠ°ΠΌΠΈ, Π³Π΄Π΅ ΡΠΊΠ°Π·Π°Π½Ρ Π·Π°Π²ΠΎΠ΄-ΠΈΠ·Π³ΠΎΡΠΎΠ²ΠΈΡΠ΅Π»Ρ, Π½ΠΎΠΌΠ΅Ρ ΠΏΠ»Π°Π²ΠΊΠΈ ΠΈ ΠΌΠ°ΡΠΊΠ° ΠΏΡΠΎΠ²ΠΎΠ»ΠΎΠΊΠΈ ΡΠΎΠ³Π»Π°ΡΠ½ΠΎ ΡΡΠ°Π½Π΄Π°ΡΡΡ. Π‘ΡΠ°Π»ΡΠ½Π°Ρ ΡΠ²Π°ΡΠΎΡΠ½Π°Ρ ΠΏΡΠΎΠ²ΠΎΠ»ΠΎΠΊΠ° ΠΈΠ·Π³ΠΎΡΠΎΠ²Π»ΡΠ΅ΡΡΡ ΠΏΠΎ ΠΠΠ‘Π’ 2246β70, ΡΡΠ°Π»ΡΠ½Π°Ρ Π½Π°ΠΏΠ»Π°Π²ΠΎΡΠ½Π°Ρ β ΠΏΠΎ ΠΠΠ‘Π’ 10543β63, ΡΠ²Π°ΡΠΎΡΠ½Π°Ρ ΠΏΡΠΎΠ²ΠΎΠ»ΠΎΠΊΠ° ΠΈΠ· Π°Π»ΡΠΌΠΈΠ½ΠΈΡ ΠΈ Π΅Π³ΠΎ ΡΠΏΠ»Π°Π²ΠΎΠ² β ΠΏΠΎ ΠΠΠ‘Π’ 7871-63.
Π ΡΠ΅ΡΡΠΈΡΠΈΠΊΠ°ΡΠ΅ Π½Π° ΡΠ²Π°ΡΠΎΡΠ½ΡΡ ΠΏΡΠΎΠ²ΠΎΠ»ΠΎΠΊΡ ΡΠΊΠ°Π·ΡΠ²Π°ΡΡΡΡ Π΄ΠΈΠ°ΠΌΠ΅ΡΡ ΠΈ ΠΌΠ°ΡΠΊΠ° ΠΏΡΠΎΠ²ΠΎΠ»ΠΎΠΊΠΈ, Π·Π°Π²ΠΎΠ΄-ΠΈΠ·Π³ΠΎΡΠΎΠ²ΠΈΡΠ΅Π»Ρ, Π½ΠΎΠΌΠ΅Ρ ΠΏΠ»Π°Π²ΠΊΠΈ ΠΌΠ΅ΡΠ°Π»Π»Π°, ΠΈΠ· ΠΊΠΎΡΠΎΡΠΎΠ³ΠΎ ΠΈΠ·Π³ΠΎΡΠΎΠ²Π»Π΅Π½Π° ΠΏΡΠΎΠ²ΠΎΠ»ΠΎΠΊΠ°, Π²Π΅Ρ ΠΏΡΠΎΠ²ΠΎΠ»ΠΎΠΊΠΈ, Ρ ΠΈΠΌΠΈΡΠ΅ΡΠΊΠΈΠΉ ΡΠΎΡΡΠ°Π² ΠΈ Π½ΠΎΠΌΠ΅Ρ ΡΡΠ°Π½Π΄Π°ΡΡΠ°.
ΠΡΠΎΠ²ΠΎΠ»ΠΎΠΊΠ° Π½Π΅ Π΄ΠΎΠ»ΠΆΠ½Π° ΠΈΠΌΠ΅ΡΡ ΠΎΠΊΠΈΡΠ»ΠΎΠ², ΡΠ»Π΅Π΄ΠΎΠ² ΡΠΌΠ°Π·ΠΊΠΈ ΠΈ Π³ΡΡΠ·ΠΈ. ΠΡΠΈ Π½Π΅ΠΎΠ±Ρ ΠΎΠ΄ΠΈΠΌΠΎΡΡΠΈ Π΅Π΅ ΠΎΡΠΈΡΠ°ΡΡ ΠΌΠ΅Ρ Π°Π½ΠΈΡΠ΅ΡΠΊΠΈΠΌ ΠΈΠ»ΠΈ Ρ ΠΈΠΌΠΈΡΠ΅ΡΠΊΠΈΠΌ ΡΠΏΠΎΡΠΎΠ±ΠΎΠΌ.
Π ΡΠ»ΡΡΠ°Π΅ ΠΏΠΎΡΠ²Π»Π΅Π½ΠΈΡ Π² Π½Π°ΠΏΠ»Π°Π²Π»Π΅Π½Π½ΠΎΠΌ ΠΌΠ΅ΡΠ°Π»Π»Π΅ ΠΏΠΎΡ ΠΈΠ»ΠΈ ΡΡΠ΅ΡΠΈΠ½ ΠΏΡΠΎΠ²ΠΎΠ»ΠΎΠΊΡ ΠΈΡΠΏΡΡΡΠ²Π°ΡΡ Π½Π° ΡΠ²Π°ΡΠΈΠ²Π°Π΅ΠΌΠΎΡΡΡ ΠΏΡΡΠ΅ΠΌ ΡΠ²Π°ΡΠΊΠΈ Π΅Ρ ΠΏΠ»Π°ΡΡΠΈΠ½ ΡΠΎΠ»ΡΠΈΠ½ΠΎΠΉ 9β10 ΠΌΠΌ ΠΈΠ»ΠΈ ΡΡΡΠ± Ρ ΡΠΎΠ»ΡΠΈΠ½ΠΎΠΉ ΡΡΠ΅Π½ΠΊΠΈ Π½Π΅ ΠΌΠ΅Π½Π΅Π΅ 8 ΠΌΠΌ. ΠΠ· ΡΠ²Π°ΡΠ΅Π½Π½ΡΡ ΠΏΠ»Π°ΡΡΠΈΠ½ ΠΈΠ»ΠΈ ΡΡΡΠ± Π²ΡΡΠ΅Π·Π°ΡΡ ΡΠ΅ΡΡΡ ΠΎΠ±ΡΠ°Π·ΡΠΎΠ² Π΄Π»Ρ ΠΌΠ΅Ρ Π°Π½ΠΈΡΠ΅ΡΠΊΠΈΡ ΠΈΡΠΏΡΡΠ°Π½ΠΈΠΉ (ΡΡΠΈ β Π½Π° ΡΠ°ΡΡΡΠΆΠ΅Π½ΠΈΠ΅ ΠΈ ΡΡΠΈ β Π½Π° ΡΠ³ΠΎΠ» Π·Π°Π³ΠΈΠ±Π°).
Π‘Π²Π°ΡΠΎΡΠ½Π°Ρ ΠΏΡΠΎΠ²ΠΎΠ»ΠΎΠΊΠ°, Π½Π΅ ΠΈΠΌΠ΅ΡΡΠ°Ρ ΡΠ΅ΡΡΠΈΡΠΈΠΊΠ°ΡΠ°, ΠΏΠΎΠ΄Π²Π΅ΡΠ³Π°Π΅ΡΡΡ ΡΡΠ°ΡΠ΅Π»ΡΠ½ΠΎΠΌΡ ΠΊΠΎΠ½ΡΡΠΎΠ»Ρ, ΠΊΠΎΡΠΎΡΡΠΉ Π·Π°ΠΊΠ»ΡΡΠ°Π΅ΡΡΡ Π² ΠΎΡΠ½ΠΎΠ²Π½ΠΎΠΌ Π² ΠΎΠΏΡΠ΅Π΄Π΅Π»Π΅Π½ΠΈΠΈ Ρ ΠΈΠΌΠΈΡΠ΅ΡΠΊΠΎΠ³ΠΎ ΡΠΎΡΡΠ°Π²Π° ΠΈ ΠΌΠ°ΡΠΊΠΈ ΠΏΡΠΎΠ²ΠΎΠ»ΠΎΠΊΠΈ, Π° ΡΠ°ΠΊΠΆΠ΅ ΠΈΡΠΏΡΡΠ°Π½ΠΈΠΈ Π½Π° ΡΠ²Π°ΡΠΈΠ²Π°Π΅ΠΌΠΎΡΡΡ.
ΠΠΎΠ½ΡΡΠΎΠ»Ρ ΠΌΠ°ΡΠ΅ΡΠΈΠ°Π»ΠΎΠ² Π΄Π»Ρ Π΄Π΅ΡΠ΅ΠΊΡΠΎΡΠΊΠΎΠΏΠΈΠΈ
ΠΠ°ΠΆΠ΄Π°Ρ ΠΏΠ°ΡΡΠΈΡ ΠΌΠ°ΡΠ΅ΡΠΈΠ°Π»ΠΎΠ² Π΄Π»Ρ Π΄Π΅ΡΠ΅ΠΊΡΠΎΡΠΊΠΎΠΏΠΈΠΈ (ΡΠ΅Π°ΠΊΡΠΈΠ²Ρ, ΡΠ΅Π½ΡΠ³Π΅Π½ΠΎΠ²ΡΠΊΠ°Ρ ΠΏΠ»Π΅Π½ΠΊΠ°, ΡΡΠΈΠ»ΠΈΠ²Π°ΡΡΠΈΠ΅ ΡΠΊΡΠ°Π½Ρ, ΡΠ΅ΡΡΠΎΠΌΠ°Π³Π½ΠΈΡΠ½Π°Ρ Π»Π΅Π½ΡΠ°) ΠΏΡΠΈ ΠΏΠΎΡΡΡΠΏΠ»Π΅Π½ΠΈΠΈ Π² Π»Π°Π±ΠΎΡΠ°ΡΠΎΡΠΈΡ ΠΈ ΠΏΠ΅ΡΠ΅Π΄ ΠΈΡΠΏΠΎΠ»ΡΠ·ΠΎΠ²Π°Π½ΠΈΠ΅ΠΌ ΠΊΠΎΠ½ΡΡΠΎΠ»ΠΈΡΡΠ΅ΡΡΡ ΠΠ’Π ΠΈΠ»ΠΈ ΠΏΠ΅ΡΡΠΎΠ½Π°Π»ΠΎΠΌ Π»Π°Π±ΠΎΡΠ°ΡΠΎΡΠΈΠΈ. ΠΠ° ΡΠΏΠ°ΠΊΠΎΠ²ΠΎΡΠ½ΡΡ Π»ΠΈΡΡΠ°Ρ (ΠΏΠ°ΡΠΊΠ΅, Π΅ΠΌΠΊΠΎΡΡΠΈ, ΠΊΠΎΡΠΎΠ±ΠΊΠ΅) Π½Π΅ΠΎΠ±Ρ ΠΎΠ΄ΠΈΠΌΠΎ ΠΏΡΠΎΠ²Π΅ΡΠΈΡΡ Π½Π°Π»ΠΈΡΠΈΠ΅ ΡΡΠΈΠΊΠ΅ΡΠΊΠΈ Ρ Ρ Π°ΡΠ°ΠΊΡΠ΅ΡΠΈΡΡΠΈΠΊΠΎΠΉ ΠΌΠ°ΡΠ΅ΡΠΈΠ°Π»ΠΎΠ² ΡΠΎΠ³Π»Π°ΡΠ½ΠΎ ΡΡΠ΅Π±ΠΎΠ²Π°Π½ΠΈΡΠΌ ΡΠΎΠΎΡΠ²Π΅ΡΡΡΠ²ΡΡΡΠΈΡ ΠΠΠ‘Π’, Π’Π£ (ΡΠ΅Ρ Π½ΠΈΡΠ΅ΡΠΊΠΈΡ ΡΡΠ»ΠΎΠ²ΠΈΠΉ) ΠΈ ΠΈΠ½ΡΡΡΡΠΊΡΠΈΠΉ.
ΠΠ°ΡΠ΅ΡΠΈΠ°Π»Ρ ΠΈ ΡΠΏΠ°ΠΊΠΎΠ²ΠΊΠ° Π½Π΅ Π΄ΠΎΠ»ΠΆΠ½Ρ ΠΈΠΌΠ΅ΡΡ ΠΏΠΎΠ²ΡΠ΅ΠΆΠ΄Π΅Π½ΠΈΠΉ.
ΠΡΠΈ Π»ΡΠ±ΠΎΠΌ ΠΎΡΡΡΡΠΏΠ»Π΅Π½ΠΈΠΈ ΠΎΡ Π½ΠΎΡΠΌ Π΄Π°Π½Π½Π°Ρ ΠΏΠ°ΡΡΠΈΡ ΠΌΠ°ΡΠ΅ΡΠΈΠ°Π»ΠΎΠ² ΠΏΡΠΎΡ ΠΎΠ΄ΠΈΡ ΠΏΡΠΎΠ²Π΅ΡΠΊΡ Π² ΡΠΎΠΎΡΠ²Π΅ΡΡΡΠ²ΠΈΠΈ Ρ ΠΠΠ‘Π’ ΠΈΠ»ΠΈ Π’Π£. ΠΡΠΈ Π½Π΅ΡΠ΄ΠΎΠ²Π»Π΅ΡΠ²ΠΎΡΠΈΡΠ΅Π»ΡΠ½ΡΡ ΡΠ΅Π·ΡΠ»ΡΡΠ°ΡΠ°Ρ ΠΊΠΎΠ½ΡΡΠΎΠ»Ρ ΠΏΠ°ΡΡΠΈΡ ΠΌΠ°ΡΠ΅ΡΠΈΠ°Π»ΠΎΠ² Π±ΡΠ°ΠΊΡΠ΅ΡΡΡ ΠΈ Π΄Π»Ρ Π΄Π΅ΡΠ΅ΠΊΡΠΎΡΠΊΠΎΠΏΠΈΠΈ Π½Π΅ Π΄ΠΎΠΏΡΡΠΊΠ°Π΅ΡΡΡ.
www.autowelding.ru
ΠΠΈΠ»Π΅ΡΡ ΡΠΊΠ·Π°ΠΌΠ΅Π½Π° Π΄Π»Ρ ΠΏΡΠΎΠ²Π΅ΡΠΊΠΈ Π·Π½Π°Π½ΠΈΠΉ ΡΠΏΠ΅ΡΠΈΠ°Π»ΠΈΡΡΠΎΠ² ΡΠ²Π°ΡΠΎΡΠ½ΠΎΠ³ΠΎ ΠΏΡΠΎΠΈΠ·Π²ΠΎΠ΄ΡΡΠ²Π° 1 ΡΡΠΎΠ²Π΅Π½Ρ
ΠΠΠΠΠ’ 2
ΠΠΠΠ ΠΠ‘ 1. ΠΠ°ΠΊΠΎΠ΅ ΠΏΠΎΠ»ΠΎΠΆΠ΅Π½ΠΈΠ΅ ΡΠ»Π΅ΠΊΡΡΠΎΠ΄Π° ΠΏΡΠΈ ΡΠ²Π°ΡΠΊΠ΅ ΠΏΡΠΈΠ²ΠΎΠ΄ΠΈΡ ΠΊ ΡΠ²Π΅Π»ΠΈΡΠ΅Π½ΠΈΡ Π³Π»ΡΠ±ΠΈΠ½Ρ ΠΏΡΠΎΠ²Π°ΡΠ° ΠΏΡΠΈ Π ΠΠ‘?
1. Π‘Π²Π°ΡΠΊΠ° Β«ΡΠ³Π»ΠΎΠΌ Π²ΠΏΠ΅ΡΠ΅Π΄Β».
2. Π‘Π²Π°ΡΠΊΠ° Β«ΡΠ³Π»ΠΎΠΌ Π½Π°Π·Π°Π΄Β».
3. Π‘Π²Π°ΡΠΊΠ° Π²Π΅ΡΡΠΈΠΊΠ°Π»ΡΠ½ΡΠΌ ΡΠ»Π΅ΠΊΡΡΠΎΠ΄ΠΎΠΌ.
ΠΠΠΠ ΠΠ‘ 2. ΠΠ°Π²ΠΈΡΠΈΡ Π»ΠΈ Π½Π°ΠΏΡΡΠΆΠ΅Π½ΠΈΠ΅ Π΄ΡΠ³ΠΈ ΠΎΡ ΡΠ²Π°ΡΠΎΡΠ½ΠΎΠ³ΠΎ ΡΠΎΠΊΠ° ΠΏΡΠΈ ΠΈΡΠΏΠΎΠ»ΡΠ·ΠΎΠ²Π°Π½ΠΈΠΈ ΠΈΡΡΠΎΡΠ½ΠΈΠΊΠΎΠ² ΠΏΠΈΡΠ°Π½ΠΈΡ Ρ ΠΏΠ°Π΄Π°ΡΡΠ΅ΠΉ Ρ Π°ΡΠ°ΠΊΡΠ΅ΡΠΈΡΡΠΈΠΊΠΎΠΉ.
1. ΠΠ°Π²ΠΈΡΠΈΡ.
2. ΠΠ΅ Π·Π°Π²ΠΈΡΠΈΡ.
3. ΠΠ°Π²ΠΈΡΠΈΡ ΠΏΡΠΈ ΠΌΠ°Π»ΡΡ ΠΈ Π±ΠΎΠ»ΡΡΠΈΡ Π²Π΅Π»ΠΈΡΠΈΠ½Π°Ρ ΡΠ²Π°ΡΠΎΡΠ½ΠΎΠ³ΠΎ ΡΠΎΠΊΠ°.
ΠΠΠΠ ΠΠ‘ 3. Π ΠΊΠ°ΠΊΠΎΠΌΡ ΠΊΠ»Π°ΡΡΡ ΡΡΠ°Π»Π΅ΠΉ ΠΎΡΠ½ΠΎΡΡΡΡΡ ΡΠ²Π°ΡΠΎΡΠ½ΡΠ΅ ΠΏΡΠΎΠ²ΠΎΠ»ΠΎΠΊΠΈ Π‘Π²-12Π₯11ΠΠΠ€, Π‘Π²-10Π₯17Π’, Π‘Π²-06Π₯19Π9Π’?
1. ΠΠΈΠ·ΠΊΠΎΠ»Π΅Π³ΠΈΡΠΎΠ²Π°Π½Π½ΠΎΠΌΡ.
2. ΠΠ΅Π³ΠΈΡΠΎΠ²Π°Π½Π½ΠΎΠΌΡ.
3. ΠΡΡΠΎΠΊΠΎΠ»Π΅Π³ΠΈΡΠΎΠ²Π°Π½Π½ΠΎΠΌΡ
ΠΠΠΠ ΠΠ‘ 4. ΠΠ°ΠΊΠΎΠΉ ΠΈΠ· ΠΏΠ΅ΡΠ΅ΡΠΈΡΠ»Π΅Π½Π½ΡΡ ΡΠ°ΠΊΡΠΎΡΠΎΠ² Π² Π±ΠΎΠ»ΡΡΠ΅ΠΉ ΡΡΠ΅ΠΏΠ΅Π½ΠΈ Π²Π»ΠΈΡΠ΅Ρ Π½Π° ΡΠΈΡΠΈΠ½Ρ ΡΠ²Π° ΠΏΡΠΈ Π ΠΠ‘?
1. ΠΠΎΠΏΠ΅ΡΠ΅ΡΠ½ΡΠ΅ ΠΊΠΎΠ»Π΅Π±Π°Π½ΠΈΡ ΡΠ»Π΅ΠΊΡΡΠΎΠ΄Π°.
2. ΠΠ°ΠΏΡΡΠΆΠ΅Π½ΠΈΠ΅ Π½Π° Π΄ΡΠ³Π΅.
3. ΠΠ΅Π»ΠΈΡΠΈΠ½Π° ΡΠ²Π°ΡΠΎΡΠ½ΠΎΠ³ΠΎ ΡΠΎΠΊΠ°.
ΠΠΠΠ ΠΠ‘ 5. Π‘ ΠΊΠ°ΠΊΠΎΠΉ ΡΠ΅Π»ΡΡ ΠΎΠ΄ΠΈΠ½ ΠΈΠ· ΠΊΠΎΠ½ΡΠΎΠ² ΡΠ»Π΅ΠΊΡΡΠΎΠ΄Π° Π½Π΅ ΠΈΠΌΠ΅Π΅Ρ ΠΏΠΎΠΊΡΡΡΠΈΡ?
1. ΠΠ»Ρ ΠΎΠ±Π΅ΡΠΏΠ΅ΡΠ΅Π½ΠΈΡ ΠΏΠΎΠ΄Π²ΠΎΠ΄Π° ΡΠΎΠΊΠ° ΠΊ ΡΠ»Π΅ΠΊΡΡΠΎΠ΄Ρ.
2. Π‘ ΡΠ΅Π»ΡΡ ΡΠΊΠΎΠ½ΠΎΠΌΠΈΠΈ ΠΏΠΎΠΊΡΡΡΠΈΡ.
3. ΠΠ»Ρ ΠΎΠΏΡΠ΅Π΄Π΅Π»Π΅Π½ΠΈΡ ΠΌΠ°ΡΠΊΠΈ ΡΠ»Π΅ΠΊΡΡΠΎΠ΄Π°.
ΠΠΠΠ ΠΠ‘ 6. ΠΠ°ΠΊΠΈΠ΅ Π΄ΠΎΠ»ΠΆΠ½Ρ Π±ΡΡΡ ΡΠΎΠ΄ ΠΈ ΠΏΠΎΠ»ΡΡΠ½ΠΎΡΡΡ ΡΠΎΠΊΠ° ΠΏΡΠΈ ΡΠ²Π°ΡΠΊΠ΅ ΡΠΎΠ΅Π΄ΠΈΠ½Π΅Π½ΠΈΠΉ ΠΈΠ· ΡΠ³Π»Π΅ΡΠΎΠ΄ΠΈΡΡΡΡ ΡΡΠ°Π»Π΅ΠΉ ΡΠ»Π΅ΠΊΡΡΠΎΠ΄Π°ΠΌΠΈ Ρ ΠΎΡΠ½ΠΎΠ²Π½ΡΠΌ ΠΏΠΎΠΊΡΡΡΠΈΠ΅ΠΌ?
1. ΠΠ΅ΡΠ΅ΠΌΠ΅Π½Π½ΡΠΉ ΡΠΎΠΊ.
2. ΠΠΎΡΡΠΎΡΠ½Π½ΡΠΉ ΡΠΎΠΊ ΠΎΠ±ΡΠ°ΡΠ½ΠΎΠΉ ΠΏΠΎΠ»ΡΡΠ½ΠΎΡΡΠΈ.
3. ΠΠΎΡΡΠΎΡΠ½Π½ΡΠΉ ΡΠΎΠΊ ΠΏΡΡΠΌΠΎΠΉ ΠΏΠΎΠ»ΡΡΠ½ΠΎΡΡΠΈ.
ΠΠΠΠ ΠΠ‘ 7. ΠΠ°ΠΊΠΈΠ΅ ΡΡΠ΅Π±ΠΎΠ²Π°Π½ΠΈΡ ΠΏΡΠ΅Π΄ΡΡΠ²Π»ΡΡΡΡΡ ΠΊ ΠΏΠΎΠΌΠ΅ΡΠ΅Π½ΠΈΡ Π΄Π»Ρ Ρ ΡΠ°Π½Π΅Π½ΠΈΡ ΡΠ²Π°ΡΠΎΡΠ½ΡΡ ΠΌΠ°ΡΠ΅ΡΠΈΠ°Π»ΠΎΠ²?
1. Π‘Π²Π°ΡΠΎΡΠ½ΡΠ΅ ΠΌΠ°ΡΠ΅ΡΠΈΠ°Π»Ρ Ρ ΡΠ°Π½ΡΡ Π² ΡΠΏΠ΅ΡΠΈΠ°Π»ΡΠ½ΠΎ ΠΎΠ±ΠΎΡΡΠ΄ΠΎΠ²Π°Π½Π½ΠΎΠΌ ΠΏΠΎΠΌΠ΅ΡΠ΅Π½ΠΈΠΈ Π±Π΅Π· ΠΎΠ³ΡΠ°Π½ΠΈΡΠ΅Π½ΠΈΡ ΡΠ΅ΠΌΠΏΠ΅ΡΠ°ΡΡΡΡ ΠΈ Π²Π»Π°ΠΆΠ½ΠΎΡΡΠΈ Π²ΠΎΠ·Π΄ΡΡ Π°.
2. Π‘Π²Π°ΡΠΎΡΠ½ΡΠ΅ ΠΌΠ°ΡΠ΅ΡΠΈΠ°Π»Ρ Ρ ΡΠ°Π½ΡΡ Π² ΡΠΏΠ΅ΡΠΈΠ°Π»ΡΠ½ΠΎ ΠΎΠ±ΠΎΡΡΠ΄ΠΎΠ²Π°Π½Π½ΠΎΠΌ ΠΏΠΎΠΌΠ΅ΡΠ΅Π½ΠΈΠΈ ΠΏΡΠΈ ΠΏΠΎΠ»ΠΎΠΆΠΈΡΠ΅Π»ΡΠ½ΠΎΠΉ ΡΠ΅ΠΌΠΏΠ΅ΡΠ°ΡΡΡΠ΅ Π²ΠΎΠ·Π΄ΡΡ Π°.
3. Π‘Π²Π°ΡΠΎΡΠ½ΡΠ΅ ΠΌΠ°ΡΠ΅ΡΠΈΠ°Π»Ρ Ρ ΡΠ°Π½ΡΡ Π² ΡΠΏΠ΅ΡΠΈΠ°Π»ΡΠ½ΠΎ ΠΎΠ±ΠΎΡΡΠ΄ΠΎΠ²Π°Π½Π½ΠΎΠΌ ΠΏΠΎΠΌΠ΅ΡΠ΅Π½ΠΈΠΈ ΠΏΡΠΈ ΡΠ΅ΠΌΠΏΠ΅ΡΠ°ΡΡΡΠ΅ Π½Π΅ Π½ΠΈΠΆΠ΅ 15 0Π‘ ΠΈ ΠΎΡΠ½ΠΎΡΠΈΡΠ΅Π»ΡΠ½ΠΎΠΉ Π²Π»Π°ΠΆΠ½ΠΎΡΡΠΈ Π²ΠΎΠ·Π΄ΡΡ Π° Π½Π΅ Π±ΠΎΠ»Π΅Π΅ 50%.
ΠΠΠΠ ΠΠ‘ 8. ΠΠ»Ρ ΡΠ²Π°ΡΠΊΠΈ ΠΊΠ°ΠΊΠΎΠΉ Π³ΡΡΠΏΠΏΡ ΡΡΠ°Π»Π΅ΠΉ ΠΏΡΠΈΠΌΠ΅Π½ΡΡΡ ΡΠ»Π΅ΠΊΡΡΠΎΠ΄Ρ ΡΠΈΠΏΠΎΠ² Π50, Π50Π, Π42Π, Π55?
1. ΠΠ»Ρ ΡΠ²Π°ΡΠΊΠΈ ΠΊΠΎΠ½ΡΡΡΡΠΊΡΠΈΠΎΠ½Π½ΡΡ ΡΡΠ°Π»Π΅ΠΉ ΠΏΠΎΠ²ΡΡΠ΅Π½Π½ΠΎΠΉ ΠΈ Π²ΡΡΠΎΠΊΠΎΠΉ ΠΏΡΠΎΡΠ½ΠΎΡΡΠΈ.
2. ΠΠ»Ρ ΡΠ²Π°ΡΠΊΠΈ ΡΠ³Π»Π΅ΡΠΎΠ΄ΠΈΡΡΡΡ ΡΡΠ°Π»Π΅ΠΉ.
3. ΠΠ»Ρ ΡΠ²Π°ΡΠΊΠΈ Π²ΡΡΠΎΠΊΠΎΠ»Π΅Π³ΠΈΡΠΎΠ²Π°Π½Π½ΡΡ ΡΡΠ°Π»Π΅ΠΉ.
ΠΠΠΠ ΠΠ‘ 9. ΠΠ»Ρ ΡΠ΅Π³ΠΎ Π½ΡΠΆΠ½Π° ΡΠΏΠ΅ΡΠΎΠ΄Π΅ΠΆΠ΄Π° ΡΠ²Π°ΡΡΠΈΠΊΡ?
1. ΠΠ»Ρ Π·Π°ΡΠΈΡΡ ΡΠ²Π°ΡΡΠΈΠΊΠ° ΠΎΡ Π²ΡΠ΄Π΅Π»ΡΡΡΠΈΡ ΡΡ Π²ΡΠ΅Π΄Π½ΡΡ Π°ΡΡΠΎΠ·ΠΎΠ»Π΅ΠΉ.
2. ΠΠ»Ρ Π·Π°ΡΠΈΡΡ ΡΠ²Π°ΡΡΠΈΠΊΠ° ΠΎΡ ΠΏΠΎΡΠ°ΠΆΠ΅Π½ΠΈΡ ΡΠ»Π΅ΠΊΡΡΠΈΡΠ΅ΡΠΊΠΈΠΌ ΡΠΎΠΊΠΎΠΌ.
3. ΠΠ»Ρ Π·Π°ΡΠΈΡΡ ΡΠ²Π°ΡΡΠΈΠΊΠ° ΠΎΡ ΡΠ΅ΠΏΠ»ΠΎΠ²ΡΡ , ΡΠ²Π΅ΡΠΎΠ²ΡΡ , ΠΌΠ΅Ρ Π°Π½ΠΈΡΠ΅ΡΠΊΠΈΡ ΠΈ Π΄ΡΡΠ³ΠΈΡ Π²ΠΎΠ·Π΄Π΅ΠΉΡΡΠ²ΠΈΠΉ ΡΠ²Π°ΡΠΎΡΠ½ΠΎΠ³ΠΎ ΠΏΡΠΎΡΠ΅ΡΡΠ°.
ΠΠΠΠ ΠΠ‘ 10. ΠΠ°ΠΊ ΠΈΠ·ΠΌΠ΅Π½ΡΠ΅ΡΡΡ ΡΠΈΠ»Π° ΡΠ²Π°ΡΠΎΡΠ½ΠΎΠ³ΠΎ ΡΠΎΠΊΠ° ΡΠ²Π΅Π»ΠΈΡΠ΅Π½ΠΈΠ΅ΠΌ Π΄Π»ΠΈΠ½Ρ Π΄ΡΠ³ΠΈ ΠΏΡΠΈ ΡΡΡΠ½ΠΎΠΉ Π΄ΡΠ³ΠΎΠ²ΠΎΠΉ ΡΠ²Π°ΡΠΊΠΈ ΡΡΡΡΠ½ΡΠΌΠΈ ΡΠ»Π΅ΠΊΡΡΠΎΠ΄Π°ΠΌΠΈ?
1. Π£Π²Π΅Π»ΠΈΡΠ΅Π½ΠΈΠ΅ Π΄Π»ΠΈΠ½Ρ Π΄ΡΠ³ΠΈ Π²Π΅Π΄Π΅Ρ ΠΊ ΡΠΌΠ΅Π½ΡΡΠ΅Π½ΠΈΡ ΡΠΈΠ»Ρ ΡΠΎΠΊΠ°.
2. Π£Π²Π΅Π»ΠΈΡΠ΅Π½ΠΈΠ΅ Π΄Π»ΠΈΠ½Ρ Π΄ΡΠ³ΠΈ Π²Π΅Π΄Π΅Ρ ΠΊ ΡΠ²Π΅Π»ΠΈΡΠ΅Π½ΠΈΡ Π½Π° ΡΠΈΠ»Ρ ΡΠ²Π°ΡΠΎΡΠ½ΠΎΠ³ΠΎ ΡΠΎΠΊΠ°.
3. ΠΠ΅Π»ΠΈΡΠΈΠ½Π° ΡΠ²Π°ΡΠΎΡΠ½ΠΎΠ³ΠΎ ΡΠΎΠΊΠ° ΠΎΡΡΠ°Π΅ΡΡΡ Π½Π΅ΠΈΠ·ΠΌΠ΅Π½Π½ΠΎΠΉ.
ΠΠΠΠ ΠΠ‘ 11. Π§Π΅ΠΌ ΡΠ΅Π³Π»Π°ΠΌΠ΅Π½ΡΠΈΡΡΠ΅ΡΡΡ ΡΠ΅ΠΆΠΈΠΌ ΠΏΡΠΎΠΊΠ°Π»ΠΊΠΈ ΡΠ»Π΅ΠΊΡΡΠΎΠ΄ΠΎΠ²?
1. ΠΡΠΎΠΈΠ·Π²ΠΎΠ΄ΡΡΠ²Π΅Π½Π½ΡΠΌ ΠΎΠΏΡΡΠΎΠΌ ΡΠ²Π°ΡΡΠΈΠΊΠ°.
2. Π’Π΅Ρ Π½ΠΈΡΠ΅ΡΠΊΠΈΠΌ ΠΏΠ°ΡΠΏΠΎΡΡΠΎΠΌ Π½Π° ΡΠ²Π°ΡΠΎΡΠ½ΡΠ΅ ΠΌΠ°ΡΠ΅ΡΠΈΠ°Π»Ρ.
3. Π Π΅ΠΊΠΎΠΌΠ΅Π½Π΄Π°ΡΠΈΡΠΌΠΈ Π½Π°Π΄Π·ΠΎΡΠ½ΡΡ ΠΎΡΠ³Π°Π½ΠΎΠ².
ΠΠΠΠ ΠΠ‘ 12. Π‘ ΠΊΠ°ΠΊΠΎΠΉ ΡΠ΅Π»ΡΡ ΠΏΡΠΎΠΈΠ·Π²ΠΎΠ΄ΡΡ ΠΏΡΠΎΠΊΠ°Π»ΠΊΡ ΡΠ»Π΅ΠΊΡΡΠΎΠ΄ΠΎΠ²?
1. ΠΠ»Ρ ΡΠ΄Π°Π»Π΅Π½ΠΈΡ ΡΠ΅ΡΡ ΠΈ ΡΠΎΡΡΠΎΡΠ°.
2. ΠΠ»Ρ ΠΏΠΎΠ²ΡΡΠ΅Π½ΠΈΡ ΠΏΡΠΎΡΠ½ΠΎΡΡΠΈ ΡΠ»Π΅ΠΊΡΡΠΎΠ΄Π½ΠΎΠ³ΠΎ ΠΏΠΎΠΊΡΡΡΠΈΡ.
3. ΠΠ»Ρ ΡΠ΄Π°Π»Π΅Π½ΠΈΡ Π²Π»Π°Π³ΠΈ ΠΈΠ· ΠΏΠΎΠΊΡΡΡΠΈΡ ΡΠ»Π΅ΠΊΡΡΠΎΠ΄ΠΎΠ².
ΠΠΠΠ ΠΠ‘ 13. ΠΠ°ΠΊΠΈΠ΅ ΡΡΠ°Π»ΠΈ ΠΎΡΠ½ΠΎΡΡΡΡΡ ΠΊ ΡΠ³Π»Π΅ΡΠΎΠ΄ΠΈΡΡΡΠΌ ΡΡΠ°Π»ΡΠΌ?
1. Π‘ΡΠ°Π»Ρ Π‘Ρ3ΡΠΏ5, Π‘ΡΠ°Π»Ρ 10, Π‘ΡΠ°Π»Ρ 15, Π‘ΡΠ°Π»Ρ 20Π, Π‘ΡΠ°Π»Ρ 20Π, Π‘ΡΠ°Π»Ρ 22Π.
2. 45Π₯25Π20.
3. 08Π₯14ΠΠ€, 1Π₯12Π2ΠΠ€, 25Π₯30Π.
ΠΠΠΠ ΠΠ‘ 14. Π§ΡΠΎ ΠΎΠ±ΠΎΠ·Π½Π°ΡΠ°Π΅Ρ Π±ΡΠΊΠ²Π° ΠΈ ΡΠ»Π΅Π΄ΡΡΡΠ°Ρ Π·Π° Π½Π΅ΠΉ ΡΠΈΡΡ Π² ΠΌΠ°ΡΠΊΠΈΡΠΎΠ²ΠΊΠ΅ ΡΡΠ°Π»Π΅ΠΉ ΠΈ ΡΠΏΠ»Π°Π²ΠΎΠ²?
1. ΠΠ»Π΅ΠΉΠΌΠ° Π·Π°Π²ΠΎΠ΄Π°-ΠΈΠ·Π³ΠΎΡΠΎΠ²ΠΈΡΠ΅Π»Ρ.
2. ΠΠ±ΠΎΠ·Π½Π°ΡΠ΅Π½ΠΈΡ Π½ΠΎΠΌΠ΅ΡΠ° ΠΏΠ»Π°Π²ΠΊΠΈ ΠΈ ΠΏΠ°ΡΡΠΈΠΈ ΠΌΠ΅ΡΠ°Π»Π»Π°.
3. Π£ΡΠ»ΠΎΠ²Π½ΠΎΠ΅ ΠΎΠ±ΠΎΠ·Π½Π°ΡΠ΅Π½ΠΈΠ΅ Π»Π΅Π³ΠΈΡΡΡΡΠ΅Π³ΠΎ ΡΠ»Π΅ΠΌΠ΅Π½ΡΠ° Π² ΡΡΠ°Π»ΠΈ ΠΈ Π΅Π³ΠΎ ΡΠΎΠ΄Π΅ΡΠΆΠ°Π½ΠΈΠ΅ Π² ΠΏΡΠΎΡΠ΅Π½ΡΠ°Ρ .
ΠΠΠΠ ΠΠ‘ 15. ΠΠ°ΠΊΠΈΠ΅ ΡΡΠ°Π»ΠΈ ΠΎΡΠ½ΠΎΡΡΡΡΡ ΠΊ Π³ΡΡΠΏΠΏΠ΅ ΡΠ΄ΠΎΠ²Π»Π΅ΡΠ²ΠΎΡΠΈΡΠ΅Π»ΡΠ½ΠΎ ΡΠ²Π°ΡΠΈΠ²Π°ΡΡΠΈΡ ΡΡ?
1. Π‘ ΡΠΎΠ΄Π΅ΡΠΆΠ°Π½ΠΈΠ΅ΠΌ ΡΠ³Π»Π΅ΡΠΎΠ΄Π° 0,25-0,35 %.
2. Π‘ ΡΠΎΠ΄Π΅ΡΠΆΠ°Π½ΠΈΠ΅ΠΌ ΡΠ΅ΡΡ ΠΈ ΡΠΎΡΡΠΎΡΠ° Π΄ΠΎ 0,05 %.
3. Π‘ ΡΠΎΠ΄Π΅ΡΠΆΠ°Π½ΠΈΠ΅ΠΌ ΠΊΡΠ΅ΠΌΠ½ΠΈΡ ΠΈ ΠΌΠ°ΡΠ³Π°Π½ΡΠ° Π΄ΠΎ 0,5 %.
ΠΠΠΠ ΠΠ‘ 16. ΠΠ°ΠΊΠΈΠ΅ ΠΈΠ· ΠΏΠ΅ΡΠ΅ΡΠΈΡΠ»Π΅Π½Π½ΡΡ Π½ΠΈΠΆΠ΅ Π½Π°ΡΡΡΠ΅Π½ΠΈΠΉ ΡΠ΅Ρ Π½ΠΎΠ»ΠΎΠ³ΠΈΠΈ ΠΌΠΎΠ³ΡΡ ΠΏΡΠΈΠ²Π΅ΡΡΠΈ ΠΊ ΠΏΠΎΡΠΈΡΡΠΎΡΡΠΈ ΡΠ²ΠΎΠ²?
1. ΠΠ»ΠΎΡ Π°Ρ Π·Π°ΡΠΈΡΡΠΊΠ° ΠΊΡΠΎΠΌΠΎΠΊ ΠΏΠ΅ΡΠ΅Π΄ ΡΠ²Π°ΡΠΊΠΎΠΉ ΠΎΡ ΡΠΆΠ°Π²ΡΠΈΠ½Ρ, ΡΠ»Π΅Π΄ΠΎΠ² ΡΠΌΠ°Π·ΠΊΠΈ.
2. ΠΠΎΠ»ΡΡΠ°Ρ ΡΠΈΠ»Π° ΡΠΎΠΊΠ° ΠΏΡΠΈ ΡΠ²Π°ΡΠΊΠ΅.
3. ΠΠ°Π»ΡΠΉ Π·Π°Π·ΠΎΡ Π² ΡΡΡΠΊΠ΅.
ΠΠΠΠ ΠΠ‘ 17. ΠΡ ΡΠ΅Π³ΠΎ Π² Π±ΠΎΠ»ΡΡΠ΅ΠΉ ΡΡΠ΅ΠΏΠ΅Π½ΠΈ Π·Π°Π²ΠΈΡΠΈΡ Π²Π΅Π»ΠΈΡΠΈΠ½Π° Π΄Π΅ΡΠΎΡΠΌΠ°ΡΠΈΠΈ ΡΠ²Π°ΡΠΈΠ²Π°Π΅ΠΌΠΎΠ³ΠΎ ΠΌΠ΅ΡΠ°Π»Π»Π°?
1. ΠΡ ΡΠΊΠ»ΠΎΠ½Π½ΠΎΡΡΠΈ ΡΡΠ°Π»ΠΈ ΠΊ Π·Π°ΠΊΠ°Π»ΠΊΠ΅.
2. ΠΡ Π½Π΅ΡΠ°Π²Π½ΠΎΠΌΠ΅ΡΠ½ΠΎΡΡΠΈ Π½Π°Π³ΡΠ΅Π²Π°.
3. ΠΡ ΠΌΠ°ΡΠΊΠΈ ΡΠ»Π΅ΠΊΡΡΠΎΠ΄Π°, ΠΊΠΎΡΠΎΡΡΠΌ ΠΏΡΠΎΠΈΠ·Π²ΠΎΠ΄ΡΡ ΡΠ²Π°ΡΠΊΡ.
ΠΠΠΠ ΠΠ‘ 18. Π£ΠΊΠ°ΠΆΠΈΡΠ΅ Π²Π΅Π»ΠΈΡΠΈΠ½Ρ Π·Π°Π·ΠΎΡΠ° ΠΌΠ΅ΠΆΠ΄Ρ ΡΠ²Π°ΡΠΈΠ²Π°Π΅ΠΌΡΠΌΠΈ ΠΊΡΠΎΠΌΠΊΠ°ΠΌΠΈ Π»ΠΈΡΡΠΎΠ²ΡΡ ΡΠ»Π΅ΠΌΠ΅Π½ΡΠΎΠ² ΡΠΎΠ»ΡΠΈΠ½ΠΎΠΉ Π΄ΠΎ 5 ΠΌΠΌ ΠΏΠΎ ΠΠΠ‘Π’ 5264-80?
1. 1 β 2 ΠΌΠΌ.
2. 3 β 4 ΠΌΠΌ.
3. 5 β 6 ΠΌΠΌ.
ΠΠΠΠ ΠΠ‘ 19. Π ΠΊΠ°ΠΊΠΎΠΉ ΡΠ²Π΅Ρ ΡΠ΅ΠΊΠΎΠΌΠ΅Π½Π΄ΡΠ΅ΡΡΡ ΠΎΠΊΡΠ°ΡΠΈΠ²Π°ΡΡ ΡΡΠ΅Π½Ρ ΠΈ ΠΎΠ±ΠΎΡΡΠ΄ΠΎΠ²Π°Π½ΠΈΠ΅ ΡΠ΅Ρ ΠΎΠ² ΡΠ²Π°ΡΠΊΠΈ?
1. ΠΡΠ°ΡΠ½ΡΠΉ, ΠΎΡΠ°Π½ΠΆΠ΅Π²ΡΠΉ.
2. ΠΠ΅Π»ΡΠΉ.
3. Π‘Π΅ΡΡΠΉ (ΡΡΠ°Π»ΡΠ½ΠΎΠΉ) ΡΠ²Π΅Ρ Ρ ΠΌΠ°ΡΠΎΠ²ΡΠΌ ΠΎΡΡΠ΅Π½ΠΊΠΎΠΌ.
ΠΠΠΠ ΠΠ‘ 20. Π£ΠΊΠ°ΠΆΠΈΡΠ΅ ΡΡΠ»ΠΎΠ²Π½ΡΠ΅ ΠΎΠ±ΠΎΠ·Π½Π°ΡΠ΅Π½ΠΈΡ ΡΠ²Π°ΡΠ½ΡΡ ΡΠΎΠ΅Π΄ΠΈΠ½Π΅Π½ΠΈΠΉ?
1. Π‘ β ΡΡΡΠΊΠΎΠ²ΠΎΠ΅, Π£ β ΡΠ³Π»ΠΎΠ²ΠΎΠ΅, Π’ β ΡΠ°Π²ΡΠΎΠ²ΠΎΠ΅, Π β Π½Π°Ρ Π»Π΅ΡΡΠΎΡΠ½ΠΎΠ΅; Π±ΡΠΊΠ²Π° ΠΈ ΡΠΈΡΡΠ°, ΡΠ»Π΅Π΄ΡΡΡΠ°Ρ Π·Π° Π½Π΅ΠΉ β ΡΡΠ»ΠΎΠ²Π½ΠΎΠ΅ ΠΎΠ±ΠΎΠ·Π½Π°ΡΠ΅Π½ΠΈΠ΅ ΡΠ²Π°ΡΠ½ΠΎΠ³ΠΎ ΡΠΎΠ΅Π΄ΠΈΠ½Π΅Π½ΠΈΡ.
2. Π‘ β ΡΡΡΠΊΠΎΠ²ΠΎΠ΅, Π£ β ΡΠ³Π»ΠΎΠ²ΠΎΠ΅, Π β Π½Π°Ρ Π»Π΅ΡΡΠΎΡΠ½ΠΎΠ΅, Π’ β ΡΠΎΡΠ΅ΡΠ½Π°Ρ ΡΠ²Π°ΡΠΊΠ°; ΡΠΈΡΡΡ ΠΏΠΎΡΠ»Π΅ Π±ΡΠΊΠ² ΡΠΊΠ°Π·ΡΠ²Π°ΡΡ ΠΌΠ΅ΡΠΎΠ΄ ΠΈ ΡΠΏΠΎΡΠΎΠ± ΡΠ²Π°ΡΠΊΠΈ.
3. Π‘ β ΡΡΡΠΊΠΎΠ²ΠΎΠ΅, Π£ β ΡΠ³Π»ΠΎΠ²ΠΎΠ΅, Π’ β ΡΠ°Π²ΡΠΎΠ²ΠΎΠ΅, Π β ΠΏΠΎΡΠΎΠ»ΠΎΡΠ½ΡΠΉ ΡΠΎΠ²; ΡΠΈΡΡΡ ΠΏΠΎΡΠ»Π΅ Π±ΡΠΊΠ² ΡΠΊΠ°Π·ΡΠ²Π°ΡΡ ΠΌΠ΅ΡΠΎΠ΄Ρ ΠΈ ΠΎΠ±ΡΠ΅ΠΌ ΠΊΠΎΠ½ΡΡΠΎΠ»Ρ.
ΠΠ»Ρ ΠΏΠ΅ΡΠ΅Ρ ΠΎΠ΄Π° Π½Π° ΡΠ»Π΅Π΄ΡΡΡΡΡ ΡΡΡΠ°Π½ΠΈΡΡ, Π²ΠΎΡΠΏΠΎΠ»ΡΠ·ΡΠΉΡΠ΅ΡΡ ΠΏΠΎΡΡΡΠ°Π½ΠΈΡΠ½ΠΎΠΉ Π½Π°Π²ΠΈΠ³Π°ΡΠΈΠ΅ΠΉ Π½ΠΈΠΆΠ΅
Β
Π’Π΅Π³ΠΈ: Π±ΠΈΠ»Π΅ΡΡ, ΠΏΡΠΎΠ²Π΅ΡΠΊΠ° Π·Π½Π°Π½ΠΈΠΉ, ΡΠ²Π°ΡΡΠΈΠΊ, ΡΠΏΠ΅ΡΠΈΠ°Π»ΠΈΡΡ
web-mechanic.ru
ΠΠΎΠ½ΡΡΠΎΠ»Ρ ΡΠ²Π°ΡΠΎΡΠ½ΠΎΠΉ ΠΏΡΠΎΠ²ΠΎΠ»ΠΎΠΊΠΈ
5.4.17. ΠΠ°ΠΆΠ΄Π°Ρ ΠΏΠ°ΡΡΠΈΡ ΡΠ²Π°ΡΠΎΡΠ½ΠΎΠΉ ΠΏΡΠΎΠ²ΠΎΠ»ΠΎΠΊΠΈ ΠΏΠ΅ΡΠ΅Π΄ Π²ΡΠ΄Π°ΡΠ΅ΠΉ Π½Π° ΠΏΡΠΎΠΈΠ·Π²ΠΎΠ΄ΡΡΠ²Π΅Π½Π½ΡΠΉ ΡΡΠ°ΡΡΠΎΠΊ Π΄ΠΎΠ»ΠΆΠ½Π° Π±ΡΡΡ ΠΏΡΠΎΠΊΠΎΠ½ΡΡΠΎΠ»ΠΈΡΠΎΠ²Π°Π½Π° ΠΏΡΡΠ΅ΠΌ ΠΎΡΠΌΠΎΡΡΠ° ΠΏΠΎΠ²Π΅ΡΡ Π½ΠΎΡΡΠΈ ΠΏΡΠΎΠ²ΠΎΠ»ΠΎΠΊΠΈ Π² ΠΊΠ°ΠΆΠ΄ΠΎΠΉ Π±ΡΡ ΡΠ΅ (ΠΌΠΎΡΠΊΠ΅, ΠΊΠ°ΡΡΡΠΊΠ΅). ΠΠ° ΠΏΠΎΠ²Π΅ΡΡ Π½ΠΎΡΡΠΈ ΠΏΡΠΎΠ²ΠΎΠ»ΠΎΠΊΠΈ Π½Π΅ Π΄ΠΎΠ»ΠΆΠ½ΠΎ Π±ΡΡΡ ΠΎΠΊΠ°Π»ΠΈΠ½Ρ, ΡΠΆΠ°Π²ΡΠΈΠ½Ρ, ΡΠ»Π΅Π΄ΠΎΠ² ΡΠΌΠ°Π·ΠΊΠΈ, Π·Π°Π΄ΠΈΡΠΎΠ², Π²ΠΌΡΡΠΈΠ½ ΠΈ Π΄ΡΡΠ³ΠΈΡ Π΄Π΅ΡΠ΅ΠΊΡΠΎΠ² ΠΈ Π·Π°Π³ΡΡΠ·Π½Π΅Π½ΠΈΠΉ.
5.4.18. ΠΠ°ΠΆΠ΄Π°Ρ Π±ΡΡ ΡΠ° (ΠΌΠΎΡΠΎΠΊ, ΠΊΠ°ΡΡΡΠΊΠ°) Π»Π΅Π³ΠΈΡΠΎΠ²Π°Π½Π½ΠΎΠΉ ΠΏΡΠΎΠ²ΠΎΠ»ΠΎΠΊΠΈ ΡΠΏΠ»ΠΎΡΠ½ΠΎΠ³ΠΎ ΡΠ΅ΡΠ΅Π½ΠΈΡ ΠΏΠ΅ΡΠ΅Π΄ ΡΠ²Π°ΡΠΊΠΎΠΉ (Π½Π΅Π·Π°Π²ΠΈΡΠΈΠΌΠΎ ΠΎΡ ΡΠΏΠΎΡΠΎΠ±Π° ΡΠ²Π°ΡΠΊΠΈ) Π΄ΠΎΠ»ΠΆΠ½Π° Π±ΡΡΡ ΠΏΡΠΎΠ²Π΅ΡΠ΅Π½Π° ΡΡΠΈΠ»ΠΎΡΠΊΠΎΠΏΠΈΡΠΎΠ²Π°Π½ΠΈΠ΅ΠΌ Π½Π° ΡΠΎΠΎΡΠ²Π΅ΡΡΡΠ²ΠΈΠ΅ ΡΠΎΠ΄Π΅ΡΠΆΠ°Π½ΠΈΡ ΠΎΡΠ½ΠΎΠ²Π½ΡΡ Π»Π΅Π³ΠΈΡΡΡΡΠΈΡ ΡΠ»Π΅ΠΌΠ΅Π½ΡΠΎΠ² ΡΡΠ΅Π±ΠΎΠ²Π°Π½ΠΈΡΠΌ, ΠΏΡΠΈΠ²Π΅Π΄Π΅Π½Π½ΡΠΌ Π² ΠΏΡΠΈΠ»ΠΎΠΆΠ΅Π½ΠΈΠΈ 9. Π‘ΡΠΈΠ»ΠΎΡΠΊΠΎΠΏΠΈΡΠΎΠ²Π°Π½ΠΈΡ ΠΏΠΎΠ΄Π²Π΅ΡΠ³Π°ΡΡ ΠΊΠΎΠ½ΡΡ ΠΊΠ°ΠΆΠ΄ΠΎΠΉ Π±ΡΡ ΡΡ (ΠΌΠΎΡΠΊΠ°, ΠΊΠ°ΡΡΡΠΊΠΈ). ΠΡΠΈ Π½Π΅ΡΠ΄ΠΎΠ²Π»Π΅ΡΠ²ΠΎΡΠΈΡΠ΅Π»ΡΠ½ΡΡ ΡΠ΅Π·ΡΠ»ΡΡΠ°ΡΠ°Ρ ΡΡΠΈΠ»ΠΎΡΠΊΠΎΠΏΠΈΡΠΎΠ²Π°Π½ΠΈΡ Π±ΡΡ ΡΠ° Π½Π΅ ΠΌΠΎΠΆΠ΅Ρ Π±ΡΡΡ ΠΈΡΠΏΠΎΠ»ΡΠ·ΠΎΠ²Π°Π½Π° Π΄Π»Ρ ΡΠ²Π°ΡΠΊΠΈ Π΄ΠΎ ΡΡΡΠ°Π½ΠΎΠ²Π»Π΅Π½ΠΈΡ ΡΠΎΡΠ½ΠΎΠ³ΠΎ Ρ ΠΈΠΌΠΈΡΠ΅ΡΠΊΠΎΠ³ΠΎ ΡΠΎΡΡΠ°Π²Π° ΠΏΡΠΎΠ²ΠΎΠ»ΠΎΠΊΠΈ ΠΊΠΎΠ»ΠΈΡΠ΅ΡΡΠ²Π΅Π½Π½ΡΠΌ Ρ ΠΈΠΌΠΈΡΠ΅ΡΠΊΠΈΠΌ Π°Π½Π°Π»ΠΈΠ·ΠΎΠΌ.
5.4.19. ΠΠ°ΠΆΠ΄Π°Ρ ΠΏΠ°ΡΡΠΈΡ ΡΠ²Π°ΡΠΎΡΠ½ΠΎΠΉ ΠΏΡΠΎΠ²ΠΎΠ»ΠΎΠΊΠΈ ΡΠΏΠ»ΠΎΡΠ½ΠΎΠ³ΠΎ ΡΠ΅ΡΠ΅Π½ΠΈΡ, ΠΏΡΠ΅Π΄Π½Π°Π·Π½Π°ΡΠ΅Π½Π½Π°Ρ Π΄Π»Ρ ΡΠ²Π°ΡΠΊΠΈ ΠΏΠΎΠ΄ ΡΠ»ΡΡΠΎΠΌ ΠΈΠ·Π΄Π΅Π»ΠΈΠΉ, Π½Π° ΠΊΠΎΡΠΎΡΡΠ΅ ΡΠ°ΡΠΏΡΠΎΡΡΡΠ°Π½ΡΡΡΡΡ ΠΏΡΠ°Π²ΠΈΠ»Π° ΠΠΎΡΠ³ΠΎΡΡΠ΅Ρ Π½Π°Π΄Π·ΠΎΡΠ° Π ΠΎΡΡΠΈΠΈ, Π΄ΠΎΠ»ΠΆΠ½Π° Π±ΡΡΡ ΠΏΡΠΎΠ²Π΅ΡΠ΅Π½Π° Π½Π° ΠΌΠ΅Ρ Π°Π½ΠΈΡΠ΅ΡΠΊΠΈΠ΅ ΡΠ²ΠΎΠΉΡΡΠ²Π° ΠΌΠ΅ΡΠ°Π»Π»Π° ΡΠ²Π° Π² ΡΠΎΡΠ΅ΡΠ°Π½ΠΈΠΈ Ρ ΡΠ»ΡΡΠΎΠΌ ΡΠΎΠΉ ΠΏΠ°ΡΡΠΈΠΈ, ΠΊΠΎΡΠΎΡΠ°Ρ Π±ΡΠ΄Π΅Ρ ΠΈΡΠΏΠΎΠ»ΡΠ·ΠΎΠ²Π°ΡΡΡΡ Π² ΠΏΡΠΎΠΈΠ·Π²ΠΎΠ΄ΡΡΠ²Π΅ Ρ ΠΏΡΠΎΠ²ΠΎΠ»ΠΎΠΊΠΎΠΉ Π΄Π°Π½Π½ΠΎΠΉ ΠΏΠ°ΡΡΠΈΠΈ. ΠΠ»Ρ ΡΡΠΎΠ³ΠΎ ΡΠ²Π°ΡΠΈΠ²Π°ΡΡ Π²ΡΡΡΠΊ Π΄Π²Π΅ ΠΏΠ»Π°ΡΡΠΈΠ½Ρ ΠΈ ΠΈΠ· ΡΡΠΎΠ³ΠΎ ΡΠ²Π°ΡΠ½ΠΎΠ³ΠΎ ΡΠΎΠ΅Π΄ΠΈΠ½Π΅Π½ΠΈΡ ΠΈΠ·Π³ΠΎΡΠ°Π²Π»ΠΈΠ²Π°ΡΡ ΡΡΠΈ ΠΎΠ±ΡΠ°Π·ΡΠ° Π΄Π»Ρ ΠΈΡΠΏΡΡΠ°Π½ΠΈΡ Π½Π° ΡΠ΄Π°ΡΠ½ΡΠΉ ΠΈΠ·Π³ΠΈΠ± ΠΈ Π΄Π²Π° – Π΄Π»Ρ ΠΈΡΠΏΡΡΠ°Π½ΠΈΡ Π½Π° ΡΠ°ΡΡΡΠΆΠ΅Π½ΠΈΠ΅, ΡΡΠΎΠ±Ρ ΠΎΠΏΡΠ΅Π΄Π΅Π»ΠΈΡΡ Π²ΡΠ΅ΠΌΠ΅Π½Π½ΠΎΠ΅ ΡΠΎΠΏΡΠΎΡΠΈΠ²Π»Π΅Π½ΠΈΠ΅ ΠΈ ΠΎΡΠ½ΠΎΡΠΈΡΠ΅Π»ΡΠ½ΠΎΠ΅ ΡΠ΄Π»ΠΈΠ½Π΅Π½ΠΈΠ΅ (ΡΠΌ. ΡΠΈΡ.5.2). ΠΡΠΏΡΡΠ°Π½ΠΈΠ΅ ΠΏΡΠΎΠ²ΠΎΠ΄ΠΈΡΡΡ ΠΏΡΠΈ ΡΠ΅ΠΌΠΏΠ΅ΡΠ°ΡΡΡΠ΅ +20Β°Π‘. Π Π΅Π·ΡΠ»ΡΡΠ°ΡΡ ΠΈΡΠΏΡΡΠ°Π½ΠΈΠΉ ΡΡΠΈΡΠ°ΡΡΡΡ ΡΠ΄ΠΎΠ²Π»Π΅ΡΠ²ΠΎΡΠΈΡΠ΅Π»ΡΠ½ΡΠΌΠΈ, Π΅ΡΠ»ΠΈ Π²ΡΠ΅ΠΌΠ΅Π½Π½ΠΎΠ΅ ΡΠΎΠΏΡΠΎΡΠΈΠ²Π»Π΅Π½ΠΈΠ΅ ΡΠ°Π·ΡΡΠ²Ρ Π±ΡΠ΄Π΅Ρ Π½Π΅ Π½ΠΈΠΆΠ΅ ΠΌΠΈΠ½ΠΈΠΌΠ°Π»ΡΠ½ΠΎ Π΄ΠΎΠΏΡΡΡΠΈΠΌΠΎΠ³ΠΎ Π΄Π»Ρ ΠΎΡΠ½ΠΎΠ²Π½ΠΎΠ³ΠΎ ΠΌΠ΅ΡΠ°Π»Π»Π°, ΠΊΠΎΡΠΎΡΡΠΉ Π±ΡΠ΄Π΅Ρ ΡΠ²Π°ΡΠΈΠ²Π°ΡΡΡΡ ΡΡΠΈΠΌΠΈ ΡΠ²Π°ΡΠΎΡΠ½ΡΠΌΠΈ ΠΌΠ°ΡΠ΅ΡΠΈΠ°Π»Π°ΠΌΠΈ, ΠΎΡΠ½ΠΎΡΠΈΡΠ΅Π»ΡΠ½ΠΎΠ΅ ΡΠ΄Π»ΠΈΠ½Π΅Π½ΠΈΠ΅ – Π½Π΅ ΠΌΠ΅Π½Π΅Π΅ 16%, ΡΠ΄Π°ΡΠ½Π°Ρ Π²ΡΠ·ΠΊΠΎΡΡΡ – Π½Π΅ ΠΌΠ΅Π½Π΅Π΅ 49 ΠΠΆ/ΡΠΌ2 (5 ΠΊΠ³Ρ Ρ ΠΌ/ΡΠΌ2).
5.4.20. ΠΠ°ΠΆΠ΄Π°Ρ ΠΏΠ°ΡΡΠΈΡ ΠΏΠΎΡΠΎΡΠΊΠΎΠ²ΠΎΠΉ ΠΏΡΠΎΠ²ΠΎΠ»ΠΎΠΊΠΈ ΠΏΠ΅ΡΠ΅Π΄ ΠΏΡΠΈΠΌΠ΅Π½Π΅Π½ΠΈΠ΅ΠΌ Π΄ΠΎΠ»ΠΆΠ½Π° Π±ΡΡΡ ΠΏΠΎΠ΄Π²Π΅ΡΠ³Π½ΡΡΠ° ΠΏΡΠΎΠ²Π΅ΡΠΊΠ΅ ΡΠ²Π°ΡΠΎΡΠ½ΠΎ-ΡΠ΅Ρ Π½ΠΎΠ»ΠΎΠ³ΠΈΡΠ΅ΡΠΊΠΈΡ ΡΠ²ΠΎΠΉΡΡΠ² ΠΏΡΡΠ΅ΠΌ Π½Π°ΠΏΠ»Π°Π²ΠΊΠΈ Π²Π°Π»ΠΈΠΊΠ° Π½Π° ΠΏΠ»Π°ΡΡΠΈΠ½Ρ ΠΈ Π²ΠΈΠ·ΡΠ°Π»ΡΠ½ΠΎΠ³ΠΎ ΠΊΠΎΠ½ΡΡΠΎΠ»Ρ Ρ ΠΏΠΎΠΌΠΎΡΡΡ Π»ΡΠΏΡ ΠΏΡΡΠΈΠΊΡΠ°ΡΠ½ΠΎΠ³ΠΎ ΡΠ²Π΅Π»ΠΈΡΠ΅Π½ΠΈΡ, ΡΡΠΎΠ±Ρ Π²ΡΡΠ²ΠΈΡΡ ΡΡΠ΅ΡΠΈΠ½Ρ, ΠΏΠΎΡΡ ΠΈ Π½Π΅ΡΠΎΠ²Π½ΠΎΡΡΠΈ Π½Π° ΠΏΠΎΠ²Π΅ΡΡ Π½ΠΎΡΡΠΈ Π²Π°Π»ΠΈΠΊΠ°. ΠΠ°Π»ΠΈΠΊ Π½Π°ΠΏΠ»Π°Π²Π»ΡΠ΅ΡΡΡ Π½Π° ΠΏΠ»Π°ΡΡΠΈΠ½Ρ ΡΠΎΠ»ΡΠΈΠ½ΠΎΠΉ 14-18 ΠΌΠΌ ΠΈΠ· ΡΠ³Π»Π΅ΡΠΎΠ΄ΠΈΡΡΠΎΠΉ ΡΡΠ°Π»ΠΈ (ΠΌΠ°ΡΠΎΠΊ Π‘Ρ3ΠΏΡ; Π‘Ρ3ΡΠΏ; 20) Π² Π½ΠΈΠΆΠ½Π΅ΠΌ ΠΏΠΎΠ»ΠΎΠΆΠ΅Π½ΠΈΠΈ ΠΏΠΎ ΡΠ΅ΠΆΠΈΠΌΡ, ΠΏΡΠ΅Π΄ΠΏΠΈΡΠ°Π½Π½ΠΎΠΌΡ Π΄Π»Ρ Π΄Π°Π½Π½ΠΎΠΉ ΠΌΠ°ΡΠΊΠΈ ΠΏΡΠΎΠ²ΠΎΠ»ΠΎΠΊΠΈ. Π‘Π²Π°ΡΠΎΡΠ½ΠΎ-ΡΠ΅Ρ Π½ΠΎΠ»ΠΎΠ³ΠΈΡΠ΅ΡΠΊΠΈΠ΅ ΡΠ²ΠΎΠΉΡΡΠ²Π° ΡΡΠΈΡΠ°ΡΡΡΡ ΡΠ΄ΠΎΠ²Π»Π΅ΡΠ²ΠΎΡΠΈΡΠ΅Π»ΡΠ½ΡΠΌΠΈ, Π΅ΡΠ»ΠΈ Π½Π° ΠΏΠΎΠ²Π΅ΡΡ Π½ΠΎΡΡΠΈ Π²Π°Π»ΠΈΠΊΠ° Π½Π΅ ΠΎΠ±Π½Π°ΡΡΠΆΠ΅Π½ΠΎ ΡΡΠ΅ΡΠΈΠ½, ΠΌΠ°ΠΊΡΠΈΠΌΠ°Π»ΡΠ½ΡΠΉ ΡΠ°Π·ΠΌΠ΅Ρ ΠΏΠΎΡ Π½Π΅ Π±ΠΎΠ»Π΅Π΅ 1,2 ΠΌΠΌ ΠΈ ΠΈΡ ΡΠΈΡΠ»ΠΎ Π½Π° Π»ΡΠ±ΡΡ 100 ΠΌΠΌ ΠΏΡΠΎΡΡΠΆΠ΅Π½Π½ΠΎΡΡΠΈ Π²Π°Π»ΠΈΠΊΠ° Π½Π΅ Π±ΠΎΠ»Π΅Π΅ ΠΏΡΡΠΈ; ΡΠ³Π»ΡΠ±Π»Π΅Π½ΠΈΠ΅ ΠΌΠ΅ΠΆΠ΄Ρ ΡΠ΅ΡΡΠΉΠΊΠ°ΠΌΠΈ Π΄ΠΎΠ»ΠΆΠ½ΠΎ Π±ΡΡΡ Π½Π΅ Π±ΠΎΠ»Π΅Π΅ 1,5 ΠΌΠΌ.
ΠΠΎΠ½ΡΡΠΎΠ»Ρ ΡΠ»ΡΡΠ°
5.4.21. ΠΠ΅ΡΠ΅Π΄ Π²ΡΠ΄Π°ΡΠ΅ΠΉ ΡΠ»ΡΡΠ° Π΄Π»Ρ ΡΠ²Π°ΡΠΊΠΈ Π½Π΅ΠΎΠ±Ρ ΠΎΠ΄ΠΈΠΌΠΎ ΡΠ±Π΅Π΄ΠΈΡΡΡΡ Π² ΡΠΎΠΌ, ΡΡΠΎ ΠΎΠ½ Π±ΡΠ» ΠΏΠΎΠ΄Π²Π΅ΡΠ³Π½ΡΡ Π² ΡΠΎΠΎΡΠ²Π΅ΡΡΡΠ²ΠΈΠΈ Ρ ΡΡΠ΅Π±ΠΎΠ²Π°Π½ΠΈΡΠΌΠΈ ΠΏ.4.3.3 ΠΏΡΠΎΠΊΠ°Π»ΠΊΠ΅, ΡΡΠΎΠΊ Π΄Π΅ΠΉΡΡΠ²ΠΈΡ ΠΊΠΎΡΠΎΡΠΎΠΉ Π½Π΅ ΠΈΡΡΠ΅ΠΊ, Π° ΡΠ°ΠΊΠΆΠ΅ ΠΏΡΠΎΠ²Π΅ΡΠΊΠ΅ Π² ΡΠΎΠΎΡΠ²Π΅ΡΡΡΠ²ΠΈΠΈ Ρ ΠΏ.5 4.19.
ΠΠΎΠ½ΡΡΠΎΠ»Ρ Π·Π°ΡΠΈΡΠ½ΠΎΠ³ΠΎ Π³Π°Π·Π°
5.4.22. ΠΠ΅ΡΠ΅Π΄ ΠΈΡΠΏΠΎΠ»ΡΠ·ΠΎΠ²Π°Π½ΠΈΠ΅ΠΌ Π³Π°Π·Π° ΠΈΠ· ΠΊΠ°ΠΆΠ΄ΠΎΠ³ΠΎ Π±Π°Π»Π»ΠΎΠ½Π° ΡΠ»Π΅Π΄ΡΠ΅Ρ ΠΏΡΠΎΠ²Π΅ΡΠΈΡΡ ΠΊΠ°ΡΠ΅ΡΡΠ²ΠΎ Π³Π°Π·Π°, Π΄Π»Ρ ΡΠ΅Π³ΠΎ Π½Π°Π΄ΠΎ Π½Π°ΠΏΠ»Π°Π²ΠΈΡΡ Π½Π° ΠΏΠ»Π°ΡΡΠΈΠ½Ρ ΠΈΠ»ΠΈ ΡΡΡΠ±Ρ Π²Π°Π»ΠΈΠΊ Π΄Π»ΠΈΠ½ΠΎΠΉ 100-150 ΠΌΠΌ ΠΈ ΠΏΠΎ Π²Π½Π΅ΡΠ½Π΅ΠΌΡ Π²ΠΈΠ΄Ρ ΠΏΠΎΠ²Π΅ΡΡ Π½ΠΎΡΡΠΈ Π½Π°ΠΏΠ»Π°Π²ΠΊΠΈ ΠΎΠΏΡΠ΅Π΄Π΅Π»ΠΈΡΡ Π΅Π΅ ΠΊΠ°ΡΠ΅ΡΡΠ²ΠΎ. ΠΡΠΈ ΠΎΠ±Π½Π°ΡΡΠΆΠ΅Π½ΠΈΠΈ ΠΏΠΎΡ Π² ΠΌΠ΅ΡΠ°Π»Π»Π΅ ΡΠ²Π° Π³Π°Π·, Π½Π°Ρ ΠΎΠ΄ΡΡΠΈΠΉΡΡ Π² Π΄Π°Π½Π½ΠΎΠΌ Π±Π°Π»Π»ΠΎΠ½Π΅, Π±ΡΠ°ΠΊΡΡΡ.
studfiles.net
ΠΠΎΠ±Π°Π²ΠΈΡΡ ΠΊΠΎΠΌΠΌΠ΅Π½ΡΠ°ΡΠΈΠΉ