Эксплуатация и обслуживание – Эксплуатация и техническое обслуживание аккумуляторных батарей. Ремонт аккумуляторных батарей. Марки аккумуляторов для автомобилей
Виды технического обслуживания. Техническое обслуживание и ремонт оборудования
Техническое обслуживание – виды работ, выполняемых в промежутке между плановым и внеплановым ремонтом производственного оборудования. Цель – гарантия надежной и беспрерывной работы. Своевременное техническое обслуживание и грамотная эксплуатация значительно снижают затраты на ремонт и вынужденное время простоя.
Задачи технического обслуживания
Можно с уверенностью заявить, что техобслуживание представляет собой определяющее профилактическое действие, которое крайне необходимо для обеспечения непрерывной работы производственного оборудования и механизмов в промежутках времени между запланированными ремонтными манипуляциями. Оно предполагает уход и осуществление контроля над работой машин, их поддержание в исправном рабочем состоянии, плановый техосмотр, чистку, промывку, регулировку, продувку и другой ремонт оборудования.
Отдельные виды технического обслуживания могут проводиться непосредственно на работающем оборудовании с использованием перерывов и выходных дней. При наличии соответствующих разрешений в инструкциях по эксплуатации механизмов и оборудования возможно кратковременное их отключение от электросетей до полной остановки. В таких случаях допускается некоторый простой, но чтобы не прерывались производственный и технологический процессы.
Регламентирующие документы
ГОСТами, регламентирующими применение систем технического обслуживания и ремонт оборудования, являются 18322-78 “Система технического обслуживания и ремонта техники. Термины и определения” и 28.001-83 “Система технического обслуживания и ремонта техники. Основные положения”. Именно эти стандарты определяют классификацию и виды технического обслуживания электрооборудования.
Классификация видов техобслуживания
По этапам эксплуатации ремонт и техническое обслуживание подразделяются на:
- ТО при хранении.
- ТО при перемещении.
- ТО при эксплуатации.
- ТО при ожидании.
По периодичности проведения:
- Периодическое ТО.
- Сезонное ТО.
По условиям эксплуатации:
- ТО в особых условиях.
По регламентации выполнения:
- Регламентированное обслуживание.
- Периодический контроль.
- Постоянный контроль.
- Поточное обслуживание.
- Централизованное обслуживание.
- Децентрализованное обслуживание.
По организации выполнения:
- ТО эксплуатационным персоналом.
- ТО специализированным персоналом.
- ТО эксплуатирующей организацией.
- ТО специализированной организацией.
- ТО заводом-изготовителем.
По методам техобслуживания:
- Поточный метод ТО.
- Централизованный метод ТО.
- Децентрализованный метод ТО.
По исполнительной организации:
- эксплуатационным персоналом,
- специализированным персоналом,
- эксплуатирующей организацией,
- специализированной организацией,
- заводом-изготовителем.
Разделение понятий “текущее” и “плановое” обслуживание
Чтобы избежать проблемного для механиков предприятий вопроса о том, кто именно должен выполнять техническое обслуживание промышленных машин и механизмов, принято разделять понятия “текущее” и “плановое” ТО. В какой-то мере оно включает постоянный контроль оборудования, с кратковременной остановкой или без нее. А с другой стороны, различные виды ТО входят в систему ремонта ТОиР или планово-предупредительного ремонта ППР как элемент плана или как промежуточные мероприятия.
Текущее техническое обслуживание
Различные виды текущего технического обслуживания выполняются собственным производственным персоналом участка или цеха и включают ежечасный и посменный контроль работы оборудования, осмотр, смазку и т.п. С точки зрения количества штатных единиц это разумно и рационально, поскольку не требуется увеличение количества работников ремонтной службы. С другой стороны, такой метод позволяет действующим операторам расширить знания о принципах действия и техническом устройстве промышленного оборудования.
Как правило, текущее ТО оборудования не регламентируется и предполагает:
- четкое исполнение всех правил эксплуатации, которые оговорены технической документацией предприятия-изготовителя;
- регулирование определенного режима работы оборудования и недопущение перегрузок;
- соблюдение температурного режима;
- строгую периодичность смазки в местах, где этого требует техническая документация;
- контроль состояния изношенности механизмов и узлов при визуальном осмотре;
- моментальное отключение электрооборудования при аварийной ситуации.
Плановое техническое обслуживание
Плановое ТО и проведение необходимого ремонта осуществляются квалифицированным, специально обученным персоналом ремонтной бригады. Как правило, плановые работы более объемны, чем текущее техобслуживание, и могут включать работы по разборке целых узлов машин и механизмов. Именно поэтому требуются грамотные специалисты-механики.
Плановый ремонт и техническое обслуживание являются регламентированным видом работ. К нему относят:
- проверку рабочих показателей оборудования;
- наладку и регулирование основных характеристик;
- очистку засоренных рабочих частей оборудования и механизмов;
- замену фильтров и масла;
- выявление нарушений и сбоя в работе оборудования.
Данные об изменениях в работе обслуживаемых механизмов при ТО в обязательном порядке фиксируются: в картах осмотра, ремонтных журналах, в компьютерной базе и т.д.
Очень хорошо зарекомендовали себя технологические карточки техобслуживания, замены смазочного материала, спецификации по расходу материала, когда проводится плановое или текущее обслуживание. С их помощью специалисты-ремонтники легко усваивают информацию о периодичности и перечне необходимых работ.
Поскольку те или иные виды технического обслуживания и ремонта не имеют типового руководства, то основные документы разрабатываются в рамках отдельной системы. Тем более, что для определенного вида промышленного оснащения требуется собственный перечень работ. Для максимального удобства оборудование предприятия разделяют на группы, чтобы облегчить разработку методов ТО для них.
Условное разделение оборудования
Первое разделение осуществляется в соответствии с общим статусом оборудования как части основного оснащения предприятия:
- технологическое;
- электротехническое;
- подъемно-транспортное и др.
Далее разделяется на подгруппы многочисленное технологическое оборудование предприятия, которое представляет наибольший интерес для ремонтной бригады:
- металлорежущее оборудование;
- кузнечнопрессовое оборудование;
- литейное оборудование;
- деревообрабатывающее оборудование и т.д.
Внутри перечисленных видов оборудования намного проще выделять объекты для характеристики и осуществления ремонтных работ, а также те или иные виды технического обслуживания.
Состав работ по группам оборудования
В перечень работ для металлорежущих станков входят:
- оценка износа трущихся деталей;
- подтяжка крепежных и натяжных элементов;
- проверка защитных приспособлений и зажимов;
- определение шума и вибрации;
- регулирование подачи охлаждающих жидкостей и масел и пр.
Некоторые пункты входят и в перечень технического обслуживания для кузнечнопрессового, деревообрабатывающего, литейного оборудования, за исключением специфических особенностей эксплуатации и устройства.
Система технического обслуживания и ремонта
Главной задачей автоматизированных систем, по которым проводятся различные виды ТО, является сокращение расходов по этой статье бюджета предприятия и значительное повышение класса надежности работы машин и механизмов, что способствует уменьшению себестоимости производимой продукции и, соответственно, росту доходов.
В случае проведения ремонта задача меняется, поскольку необходимо максимально сократить не только потери, но и частоту проведения самих работ (независимо от вида и объема). Идеальная схема, к которой стремятся предприятия, – это полный отказ от аварийных ремонтов, которые неизбежно ведут к внеплановым остановкам производства.
Кроме того, эксплуатация и техническое обслуживание, в частности, проведение ремонтных работ, осуществляются в условиях некоторой неопределенности. Даже проведенный мониторинг износа промышленного оснащения и многолетний опыт не могут определить конкретный объем и указать номенклатуру новых запчастей для оборудования. А вот конвейерная система предполагает точное распределение необходимых деталей, которые могут потребоваться со склада на определенный заказ.
Что такое система техобслуживания и ремонта
Система технического обслуживания и ремонта – это комплекс связанных между собой специалистов, технических приспособлений, отчетной и фиксирующей результаты документации. Все они необходимы для поддержания надлежащего состояния промышленного оборудования, определенного ГОСТами.
Все предприятия страны пользуются единой концепцией сохранения рабочих машин и механизмов в состоянии беспрерывной работоспособности, частью которой является применение законодательно утвержденной системы планово-предупредительного ремонта (ППР).
Данная система является полноценным комплексом организационных и технических действий, осуществляемых в плановом режиме, направленных на контроль и обеспечение рабочего состояния имеющихся на балансе предприятия машин и механизмов. Применяется такая система в течение всего срока эксплуатации оборудования при соблюдении указанных заводом-изготовителем режима и условий работы. Точное выполнение всех требований, рекомендаций и инструкций по эксплуатации является обязательным.
Система планово-предупредительных ремонтных работ основана на реализации запланированных периодических осмотров, контроля состояния основного оборудования и носит характер предупредительной меры. Таким образом, комплекс мероприятий, гарантирующих поддержание отличной работоспособности машин и механизмов, выполняется по разработанным месячным и годовым графикам. Последние составляются в расчете на недопустимость и предупреждение неожиданного выхода из строя промышленного оборудования, то есть в расчете на сокращение дополнительных расходов.
Обеспечение системы ТОиР
Внедрение системы планово-предупредительных ремонтов в производство обеспечивается:
- достаточной материально-технической базой и поддержанием определенной периодичности ремонтных работ, сроков выполнения;
- полным объемом выполненного перечня операций техобслуживания, гарантирующих беспрерывную работу машин и оборудования;
- по возможности кратчайшим сроком пребывания вышедшего из строя оборудования в ремонте (особенно капитальном).
Осуществление работ
В зависимости от категории и технологической важности оборудования, а также стабильности производимых процессов и безопасности работников, те или иные виды ремонтных работ могут проводиться в качестве ремонта по неисправному техническому состоянию, регламентированного (планового) ремонта, ремонта по выработанноу сроку или их сочетания.
Ремонт промышленного оборудования допустимо проводить силами предприятий-собственников, которые непосредственно используют его, а также специализированными бригадами заводов-изготовителей или ремонтных предприятий. Приоритеты этих организационных схем для каждого завода расставлены в зависимости от наличия собственных резервов, оснащенности, квалификации ремонтного персонала и финансовой состоятельности. Но каждое промышленное предприятие может на свое усмотрение отдать предпочтение любому методу и форме ППР, максимально соответствующей основным направлениям производства.
Сроки ТО
Виды и сроки технического обслуживания исчисляются сутками или месяцами, и зависит это от сложности и типа промышленного оборудования. Так, к примеру, расчеты для тягового подвижного состава (тепловозов, электровозов и пр.) производятся соответственно средним значениям межремонтных пробегов.
Периодичность, виды и сроки технического обслуживания исчисляются по календарному времени эксплуатации и учитывают техусловия заводов-изготовителей.
Таким образом, в результате небольшого анализа сущности, классификации, видов технического обслуживания промышленного, производственного и технологического оборудования можно сделать вывод о его необходимости, планомерности и обязательном строгом контроле. Именно совокупность этих составляющих позволит предприятиям добиться бесперебойной работы машин и механизмов, что, в свою очередь, способствует экономии бюджета, повышению производительности труда и получению дополнительной прибыли.
fb.ru
Эксплуатация и техническое обслуживание двигателя
Курсовая работа
Эксплуатация и техническое обслуживание двигателя
1. Общая часть
1.1 Введение
Одним из важнейших условий поддержания на высоком уровне эффективности и надёжности двигателей является своевременное обнаружение и предупреждение отказов, возникающих в процессе эксплуатации.
Отрасль знаний, изучающая формы проявления технических состояний, методы и средства обнаружения неисправностей и прогнозирование ресурса работы объекта без его разборки называется диагностикой технического состояния. Технологический процесс определения технического состояния двигателя (агрегата, механизма) без его разборки и заключение о необходимом ремонте или техническом обслуживании (профилактике) называют диагностированием. Диагностирование осуществляют по внешним признакам (люфтам, вибрациям, нагревам и т.д.), несущим информацию о техническом состоянии механизма.
Это позволяет, во-первых, обнаружить скрытые отказы механизма и определить необходимый для их устранения ремонт и, во-вторых, при отсутствии отказов выявить ресурс исправной работы механизма и необходимость в профилактике.
Диагностика двигателей в автотранспортных предприятиях является частью технологического процесса технического обслуживания и ремонта.
Обнаружение и последующее устранение неисправностей и своевременная профилактика позволяют снизить интенсивность процессов изнашивания, повысить вероятность безотказной работы двигателей, а также исключить преждевременный и поздний (аварийный) ремонты их агрегатов. Таким образом, диагностика даёт возможность количественно оценить безотказность и эффективность двигателя и прогнозировать эти свойства в пределах остаточного ресурса или заданной наработки. Задачи диагностики заключаются в том, чтобы поддерживать на высоком уровне надёжность и долговечность двигателей, уменьшать расход запасных частей, эксплуатационных материалов и трудовых затрат на техническое обслуживание и ремонт. В конечном счёте, диагностика служит повышению производительности двигателя и снижению себестоимости перевозочных работ, т.е. повышению его эффективности.
1.2 Характеристика объекта проектирования
Д-2 служит для проведения в принудительном порядке через установленный пробег крепежные, регулированные (по потребности), смазочные, промывочные работы по агрегатам автомобиля, работ по обслуживание систем питания, электрооборудование и шинам автомобиля. Зона располагает площадью 85м2 . Пост работает по 5- дневной рабочей недели в одну смену продолжительностью 8 часов. Время работы поста – с 8.00 до 16.00 с перерывом на обед с 11.00 до 12.00. На посту Д -2 работает
1 диагност. В этой зоне имеются один пожарный щит со средствами пожаротушения и ящик с песком. Технологическое обслуживание в основном соответствует выполняемым работам в объеме Д и требованиям техники безопасности. Суточная программа –0,84 обслуживаний автомобилей ВАЗ и ГАЗ.
2. Расчётно-технологическая часть
2.1 Расчёт годовой производственной программы
Установление нормативов
а)Коэффициент корректирование К1-учитывает категорию эксплуатации К=1 (вторая категория эксплуатации К=1 для всех)
б)Коэффициент К2- коэффициент учитывающий модификации подвижного К2=1.
в)Коэффициент учитывающий природно- климатические условия К3=1 (умеренный климат).
г)Коэффициент учитывающий размеры АТП К4=1.
д)К5- коэффициент учитывающий условия хранения автомобиля К5=1 (если открытая площадь).
Выбор и проектирование периодичности ТО.
Корректирование пробега до ТО1,ТО2 и КР
Средне суточный пробег-250км
Нормативный пробег до ТО1-3000км
L1=L1норм.*К1=3000*1=3000км
L2=L2н.*К1=12000*1=12000км
К1-учитывает категорию эксплуатации К=1 (вторая категория эксплуатации К=1 для всех)
Ео=0,20, ТО1 = 2,50, ТО2=10,10
ТО1 t1=t1*Кто: Кто=К2*К4
t1=2,5*1=2,5чел/час.
ТО2 t2=10,1*1=10,1чел/час.
К2- коэффициент учитывающий модификации подвижного К2=1.
Коэффициент учитывающий размеры АТП К4=1.
άт=_______________1___________________
1+ lcc ( Дор/1000+Дкр/Lкр.ср)
άт =_______________1___________________=0,93
1+250(0,2/1000+17/143000)
Lсс – среднесуточный пробег автомобиля (км)
Дор – число дней простоя /легковые.
Дкр – простой в капитальном ремонте.
Lкр.ср – средневзвешенная величина межремонтного пробега (км).
Lкр.ср=143000. (из таблице Корректирование пробега до ТО1,ТО2 и КР).
Исходя из данных расчётов, принимаем коэффициент тех готовности автомобиля, равным 0,93.
άi=άт*Кп*Драб.г/Дк.д.
άi=0,93*0,95*253/365=0,61.
άт – коэффициент тех готовности автомобиля
Кп- коэффициент учитывающий снижение использование тех. Исправных автомобилей в рабочие дни по эксплуатационным причинам (Кп=0,95).
Драб.г. – число рабочих дней в году (253 дня).
Дк.д. – число календарных дней (365дней).
365 дней вычитаем праздничные и выходные дни.
Исходя из данных расчётов, принимаем коэффициент использования автомобилей, равным 0,61.
Lр.г.=Ai*lcc*Дк.с.*Li
Аi – списочный состав автомобилей одной группы.
Lcc – средне суточный пробег.
Li – Коэффициент использования автомобиля и годового пробега.
Д к. г. – число календарных дней в году (365).
Lр.г. = 50*250*365*0,61=2783125км.
Аi-списочный состав автомобилей одной группы.
Ln.r – годовой пробег автомобиля.
Годовой пробег автомобиля.
Ln1=Ln.r/Ai
Ln1=2783125/50=5562,5км.
Исходя из данных расчётов, принимаем годовой пробег одного автомобиля, равным 5562,5км, а годовой пробег автомобилей равный 2783125км.
Число обслуживаний по парку за год определяется по формуле:
Nкр.г. = Lп.г/Lкр. ср.
Nкр.г – число капитальных ремонтов за год.
Lп.г – общей пробег подвижного состава за год.
Lкр.ср. – средний пробег до капитального ремонта.
N2г.=Lп.г/L2-Nкр.г.
N1г.=Lп.г/L1-(Nкр.г-N2г)
L1 – пробег до ТО
Nкр.г – число капитальных ремонтов за год
Nкр.г=2783125/143000=19,46
N2г=2783125/13000=214,4
N1г=2783125/3250-(119,46-214,4)=922,74
Определение суточной программой по ТО автомобиля.
Nic=Niг/Др.з
Др.з=253 (При 5-ти дневной рабочей недели).
Nic- число обслуживаний за сутки.
Niг-число обслуживаний за год.
N1c=N1г/253
N2c=N2г/253
N1c=922,74/253=3,64 (обслуживание в день).
N2c=214,4/253=0,84 (обслуживание в день).
Исходя из данных расчётов, принимаем суточную программу по ТО = 0,84 обсл/день
Определение годовой трудоемкости работ по участку.
Годовая трудоемкость работ по участку:
Ттр.у = Т тр * Стр.у.
Стр.у – доля трудоемкости работ ТР приходящийся на данный участок.
Т тр – трудоёмкость текущего ремонта по участку.
В трудоемкость работ по конкретному проектируемому участку, может быть включена, трудоемкость вспомогательных работ и подсобных.
Кроме того для небольших АТП может быть объединено несколько цехов в один, для наиболее полной загрузки рабочих, которые будут работать в одном помещении, совмещая несколько профессий, в этом случаи в долю трудоемкости цеховых работ, должны войти, соответствующие доли трудоемкости выполняемые в данном цехе.
Трудоемкость постовых работ диагностика автомобиля легкового.
Трудоёмкость диагностирования.
Тi = 1.2* N2г* тд-2
Tд-2 =t2*k2
t2 = 10,1*1 = 10,1 чел/ч
К2- коэффициент учитывающий модификации подвижного к2 = 1
Тi = 1.2 * 214.4*10.1 = 2177.56 чел/ч.
Тд-2 – трудоёмкость одного диагностирования в объеме поэлементного диагностирования (чел/ч).
N2г – число обслуживаний ТО-1 и ТО-2 за год.
2.2 Расчет числа производственных рабочих
Различают явочные (технологически необходимое) ,число рабочих (Рт) и штатное число рабочих (Рш).
Технологически необходимое явочное число рабочих:
Рт=Тi/Фр.м
Тi-годовой объем работ (трудоемкость) соответствующей зоны ТО, ТР, цеха, поста, или линии диагностирования.
Тi=1,2*N2г*tд=1,2*214.4*10.1=2177,56 чел/час.
Фр.м – годовой производственной фонд времени рабочего места. При 5-ти дневной рабочей недели.
Фр.м= Тсм * (Дкт-Дв-Дп)
Тсм – продолжительность рабочей смены.
Дкт – число календарных дней в году.
Дв – число выходных дней в году.
Дп – число праздничных дней в году.
Штатное число производственных рабочих.
Рш = Тi/Фпр
Фпр – годовой фонд времени одного производственного рабочего.
Ti – трудоёмкость диагностирования.
Фпр = Фр.м – tотп – tуп.
Фр.м – годовой производственный фонд времени рабочего места (ч).
tотп – время отпуска.
tуп – уважительные причины.
tотп=Дотп*Тсм
tотп=24*8.2=196.8 час.
tуп=0,04*(Фрм-tотп)
Iуп= 0,04(2074,6-196,8) = 75.112 час.
Фпр=2074,6-196,8-75,112=1802,688 час.
Рш=2177,56/1802,688=1,2 чел.
Исходя из данных расчётов, принимаем технологически необходимое число производственных рабочих в количестве одного человека.
2.3 Расчет числа постов для зоны диагностирования
Пд1 = Тдi /(Дргд *Тп *Рд *ηп)
Рд -2человека.
mirznanii.com
ПРОИЗВОДСТВЕННАЯ ЭКСПЛУАТАЦИЯ И ОБСЛУЖИВАНИЕ СТАНКОВ
Технологическое оборудование машиностроительных производств
На универсальных станках настройку режимов резания производит станочник непосредственно перед или во время обработки, устанавливая рукоятками частоту вращения шпинделя, подачу и глубину резания.
На специальных и специализированных станках режим резания устанавливается заранее (согласно карте наладки), путем установки сменных колес в цепях главного движения и подач. Наладку завершают регулировкой инструмента на размер и пробными работами.
На большинстве станков при механической обработке на направляющих станины и суппортов образуется мелкая пылевидная стружка, которая оседает на оборудовании, поэтому после каждой смены предусматривается 10—15 мин на уборку. За это время рабочий станочник обязан тщательно очистить оборудование от стружки и грязи. Направляющие необходимо тщательно протереть от охлаждающей жидкости и смазать тонким слоем масла. Доставку масел, долив в резервуар, замену отработанных масел и периодическое смазывание производят по графику. Ежедневное смазывание оборудования и контроль за состоянием системы подачи СОЖ выполняет станочник.
При работе оборудования необходимо также периодически проверять качество изготавливаемых деталей. При ухудшении качества, которое контролируется станочником, он должен произвести подна – ладку оборудования, отрегулировать механизмы станка.
Уход за станками и их обслуживание включает чистку и смазывание, осмотр и контроль состояния механизмов и деталей станков и остастки, гидросистемы, системы смазывания и подачи СОЖ, регулировку и устранение мелких неисправностей. При эксплуатации автоматизированных станков применяют смешанную форму обслуживания: наладку станка производит наладчик, а подналадку — станочник. При этом в функции станочника входят: приемка заготовок и их установка, снятие готовых деталей, оперативное управление, периодический контроль деталей, смена или регулировка режущего инструмента, регулирование подачи СОЖ, контроль за удалением стружки и др.
Уход за гидросистемой оборудования предусматривает контроль температуры масла, которая не должна превышать + 50° С. Первую замену масла в гидросистеме, как правило, производят через 0,5—1 месяц работы, чтобы удалить продукты притирки механизмов. В дальнейшем замену масла производят через 4—6 месяцев. Необходимо систематически контролировать и поддерживать уровень масла, следить за состоянием трубопроводов (во избежание утечки и попадания воздуха в гидросистему), регулярно чистить фильтры.
Уход за электрооборудованием включает в себя ежемесячную очистку аппаратов от грязи и пыли, подтягивание винтовых соединений, контроль плавности перемещений и надежности возврата подвижных частей электроаппаратов в исходное положение. Периодически смазывают приводы аппаратов тонким слоем смазочного материала, не допуская попадания его на контакты. Раз в полгода меняют полярность рабочих контактов у кнопок и выключателей, работающих в цепях постоянного тока, проверяют состояние контактов. При появлении пригара или капель металла на поверхности контактов их слегка зачищают бархатным надфилем.
Особенности эксплуатации станков обязательно указывают в инструкциях. Соблюдение инструкции обеспечит длительную, бесперебойную работу оборудования.
Для устранения неисправностей и восстановления работоспособности станков выполняют их ремонт. Его производят не дожидаясь выхода оборудования из строя. Такой ремонт называют планово-предупредительным ремонтом (ППР). Система ППР металлорежущих станков включает техническое обслуживание, плановый, текущий, средний и капитальный ремонт. При текущем ремонте заменяют поврежденные детали; шпонки, втулки, болты и т. д. При среднем ремонте устраняют неисправности и частично восстанавливают ресурс станка (например, по точности обработки) с заменой или восстановлением составных частей. Капитальный ремонт производят для устранения неисправностей с заменой или восстановлением основных частей, включая базовые элементы для близкого к полному или полного восстановления ресурса станка.
СТАНКИ СВЕРЛ ИЛ ЬНО-РАСТОЧНОЙ ГРУППЫ С ЧПУ
Производим и продаем электроприводы ЭТУ, ЭПУ для двигателей постоянного тока, тел./email +38 050 4571330 / [email protected] Назначение, классификация и конструктивные особенности сверлильных и расточных станков с ЧПУ. Эти станки предназначены …
Повышение эффективности производства
Производим и продаем электроприводы ЭТУ, ЭПУ для двигателей постоянного тока, тел./email +38 050 4571330 / [email protected] Развитие производства во многом определяется техническим прогрессом машиностроения. Увеличение выпуска продукции машиностроения осуществляется за …
МНОГОЦЕЛЕВЫЕ СТАНКИ С ЧПУ
Многоцелевые станки (МС) — это станки, оснащенные УЧПУ и устройством автоматической смены инструментов, предназначенные для комплексной обработки за одну установку корпусных деталей и деталей типа тел вращения. МС выпускают с …
msd.com.ua
7.1.3. Эксплуатация и обслуживание
Для обеспечения безопасного обслуживания, исправного состояния и надежности работы сосудов, работающих под давлением, приказом по АТП назначаются лицо, осуществляющее надзор за сосудами, и лицо, ответственное за их исправное и безопасное действие. Этих работников назначают из числа инженерно-технических. Их знания проверяют в установленном порядке. К обслуживанию сосудов, работающих под давлением, допускаются лица, достигшие 18-летнего возраста, прошедшие производственное обучение, аттестацию в квалификационной комиссии и инструктаж по безопасному обслуживанию сосудов. Лицам, сдавшим испытания, должны быть выданы удостоверения.
Через каждые 12 мес. комиссия, назначаемая приказом по АТП, должна проверять знания персонала. Результаты проверки оформляют протоколом.
На рабочих местах должны быть, вывешены инструкции по режиму работы сосудов и их безопасному обслуживанию, разработанные и утвержденные администрацией АТП совместно с профсоюзным комитетом. Инструкции также выдаются обслуживающему персоналу под расписку.
Сосуд должен быть остановлен в следующих случаях, предусмотренных инструкцией:
повышение давления в сосуде выше разрешенного, несмотря на соблюдение всех требований, указанных в инструкции; неисправность предохранительных клапанов;
обнаружение в основных элементах сосуда трещин, выпучин, значительного утоньшения стенок, припусков или потения в сварных швах, течи в заклепочных и болтовых соединениях, разрыва, прокладок;
возникновение пожара, непосредственно угрожающего сосуду; неисправность манометра и невозможность определить давление по другим приборам;
снижение уровня жидкости ниже допустимого в сосудах с обогревом открытым пламенем;
неисправность или неполное число крепежных деталей крышек и люков;
неисправность указателя уровня жидкости, предохранительных блокировочных устройств, предусмотренных проектом, контрольно-измерительных приборов и средств автоматики.
При эксплуатации баллонов со сжиженными и сжатыми газами следует придерживаться следующих правил. Ни в коем случае не снимать колпак с баллона ударами молотка или других предметов, способных вызвать искры. Если колпак не отвертывается, то в этом случае баллон необходимо возвратить заводу-наполнителю. После снятия колпака и заглушки необходимо проверить: отсутствие на штуцере кислородного баллона видимых следов масла и жиров; исправность присоединительной резьбы на штуцере вентиля; наличие и исправность уплотняющей кожаной прокладки в гнезде присоединительного штуцера ацетиленового баллона.
Перед присоединением редуктора к кислородному баллону необходимо: осмотреть входной штуцер и накидную гайку редуктора и убедиться в исправности резьбы гайки, в отсутствии следов масла и жиров, в наличии и исправности фибровой прокладки и фильтра на входном штуцере редуктора. Пользоваться прокладками из кожи, алюминия, меди вместо фибровых запрещается. Если резьба в накидной гайке редуктора неисправна или неисправен фильтр, то редуктор следует отправить в ремонт. Недопустимо также пользоваться редукторами с неисправными манометрами или просроченными датами испытания.
Запрещается эксплуатировать баллоны, у которых истек срок периодического освидетельствования, отсутствуют установленные клейма, неисправны вентили, поврежден корпус, окраска и надписи не соответствуют требованиям. Цвета окраски баллонов и надписи на них приведены в табл. 29, 30.
На участках, где производится газовая сварка или резка, должно быть не более одного запасного баллона. Баллоны с газом, установленные в помещениях, должны находиться на расстоянии не менее 1 м от радиаторов отопления и других отопительных приборов и печей, а от источников тепла с открытым огнем — не менее 5 м. Наполненные и порожние баллоны должны быть защищены от соприкосновения с токоведущими проводами. Расстояние между баллонами и токоведущими проводами должно быть не менее I м. Расстояние от места газовой сварки и резки до баллонов должно быть не менее 5 м.
Если баллоны хранились в неотапливаемых помещениях или на улице и в холодное время года замерз вентиль, отогревать его разрешается только паром или горячей водой, не имеющей следов масла. Открывать вентили баллонов с ацетиленом и крепить на нем редуктор допускается только специальным ключом.
Газ отбирается из баллонов до остаточного давления не ниже 0,05 МПа, а из баллонов для растворенного ацетилена — не ниже 0,05 и не более 0,1 МПа.
Баллоны с сжатыми или сжиженными газами, установленные в качестве расходных емкостей на автомобилях, должны быть прочно укреплены и герметично присоединены к отходящим трубопроводам.
studfiles.net
Эксплуатация и техническое обслуживание конвейеров
Как только ключевые вопросы, такие, как размещение, маршрут перемещения, тип конвейера и производительность технологического процесса, будут решены, необходимо оценить некоторые другие составные части проекта.
Рассмотрим основные положения, связанные с эксплуатацией конвейеров. Заслуживают внимания следующие вопросы:
Узел привода – элемент всех конвейерных систем. Это механическое устройство, которое с помощью своего электродвигателя приводит в движение конвейерную цепь через червячный или зубчатый передаточные механизмы. Узлы привода с подвижной рамой, которая позволяет двигателю, редуктору и передаточному механизму перемещаться, обычно считаются более предпочтительными по сравнению с узлами привода, в которых используются неподвижные рамы.
Узел привода располагают таким образом, чтобы тяговое усилие прилагалось к секции конвейера с максимальной нагрузкой. Он часто монтируется в местах подъема. Поскольку узлы привода имеют множество движущихся частей и должны смазываться, необходимо, чтобы к ним имелся легкий доступ для обслуживания. Кроме того, узел привода может быть расположен перед моечным агрегатом или между участками загрузки и выгрузки, где присутствует только пустая цепь. Размеры узла привода выбирают на основании максимального расчетного тягового усилия цепи.
Тяговое усилие цепи характеризует то усилие, которое необходимо для обеспечения движения цепи по всей производственной системе. Оно является функцией максимального веса детали, транспортируемой цепью, расстояния между деталями, общей длины цепи, изменений высоты системы. Усилие, создаваемое узлом привода, должно превышать максимальное усилие, которое требуется для движения цепи. Узлы привода могут развивать усилие от 40 до 1400 Н и более, в зависимости от типа и размеров транспортируемых изделий. В некоторых случаях для длинных цепей или больших нагрузок может потребоваться более одного узла привода. В таком случае используется контрольная система распределения тягового усилия между этими узлами привода.
При движении цепей, имеющих большую длину, множество горизонтальных поворотов, изменений высоты, подверженных резким изменениям нагрузки от смешанных деталей или при неудовлетворительной смазке, могут возникать колебания скорости и толчки. Поскольку такие явления могут привести к образованию дефектов покрытия, конвейер следует конструировать таким образом, чтобы устранить или свести к минимуму колебания скорости и толчки в движении цепи в системе нанесения покрытий.
Для каждой замкнутой конвейерной линии требуется устройство для поддержания натяжения цепи, необходимого для оптимальной производительности. Подтягивание цепи необходимо при провисании цепи. Ослабление или провисание цепи может быть вызвано движением деталей вниз при изменении высоты, неравномерной загрузкой цепи или растяжением в результате продолжительного использования. Устройства натяжения цепей бывают следующих типов:
Устройства натяжения цепи следует всегда располагать после узла привода, в непосредственной близости от него.
Во многих случаях требуется, чтобы детали находились на разной выоте при прохождении различных участков производственного процесса. Гибкость, которую обеспечивают конвейерные системы с изменениями высоты, позволяет разместить узлы для загрузки и выгрузки деталей на оптимальной высоте. Детали могут проходить через агрегат подготовки поверхности, камеру нанесения порошка или печь на высоте, желательной для пользователя. Для конвейерных систем с непрерывным движением цепи и свободно-приводных конвейеров эти изменения высоты осуществляются по криволинейным участкам дорожек конвейеров в вертикальной плоскости (см. рис.16). Возможность скольжения деталей при прохождении ленточного конвейера по наклонным участкам нужно обязательно исключить.
Другим средством транспортировки деталей при изменении высоты на ручных или свободно-приводных системах является использование тали. Таль может вертикально поднимать и опускать деталь в установленном месте. В системах транспортировки деталей с непрерывным движением цепи не могут использоваться механизмы подъема/опускания, поскольку деталь поддерживается на непрерывно движущейся конвейерной цепи.
Любой конвейер должен поддерживаться соответствующей опорной конструкцией. Ленточный или цепной конвейер обычно просто присоединяется анкерным креплением к полу производственного помещения или технологическому оборудованию. Различные подвесные конвейеры могут поддерживаться потолочными стальными конструкциями, либо стальными колоннами, поднимающимися с пола, либо комбинацией этих конструкций. Любые потолочные опорные конструкции должны быть прикреплены к стальному каркасу здания.
Для обеспечения безопасности персонала вокруг подвесного конвейера рекомендуется иметь защитное ограждение. Оно требуется в тех случаях, когда просвет под ограждением составляет не менее 2 м. Ограждение служит для защиты персонала, находящегося под конвейером, от падения деталей или крюков, которые могут сорваться с подвесного конвейера.
Ограждение может выполняться из проволочной сетки, сетки из прутьев или листового металла, в зависимости от размеров и массы деталей. Размеры защитного ограждения должны выбираться таким образом, чтобы детали самых больших размеров, свешивающиеся с конвейера, проходили над ограждением с достаточным просветом, включая места горизонтальных поворотов и изменений высоты, с учетом возможного раскачивания и вращения деталей.
Каждый тип конвейерных систем требует смазки для обеспечения нормального функционирования. Недостаток смазки уменьшает срок службы, приводит к неустойчивой работе конвейера, увеличивает необходимое тяговое усилие для движения цепи и вероятность остановки вследствие преждевременного выхода из строя тех или иных частей конвейера.
Ручные конвейеры требуют смазки только тележек и переключателей дорожек. Ленточный конвейер нуждается в смазке подшипников. В конвейерах с непрерывным движением цепи и свободно-приводных смазывают цепи, все движущиеся части, включая соединительные звенья и подшипники. Смазка особенно важна для тех цепей, которые должны переносить детали через моечные участки и печи. Естественно, в каждом конвейере кроме компонентов механизма, несущих нагрузку, в смазке нуждаются редуктор или коробка передач.
В тех случаях, когда конвейер проходит через печь, нужна высокотемпературная консистентная смазка, выбирать ее следует с особой тщательностью. Цепи подвесных конвейеров должны поставляться с масленкой или устройством автоматической смазки. Автоматические масленки наиболее предпочтительны для установок, которые работают строго по таймеру.
Правильно выбранный смазочный материал должен:
Для цепей многих подвесных конвейеров используются некоторые типы жидких смазочных материалов, не высыхающих или высыхающих с образованием твердой пленки, в которых используется дисульфид молибдена или другой материал молибденового типа, наносимый автоматическим устройством. Высыхающие смазки особенно распространены в технологии нанесения покрытий. Состав этих материалов обычно подбирается таким образом, чтобы они содержали не только вещества, снижающие трение, но и смачивающие и смазывающие добавки, а также ингибиторы коррозии. Смазочные материалы в виде сухой тонкой пленки позволяют удалять любые загрязнения с несущих поверхностей конвейера. Смазывающей жидкостью покрывают поверхность (цепи и др.). Она проникает в узкие щели, растекаясь по металлу, и после улетучивания растворителя оставляет тонкую пленку твердого смазочного материала с дисульфидом молибдена.
Этот материал хорошо связывается с микроскопическими неровностями поверхности металла. Образующаяся сухая скользкая пленка способна выдерживать давление до 6800 атм. По мере нарастания сухой пленки несущие поверхности принимают металлический оттенок или блеск. По сравнению с описанными материалами смазочные материалы на жидкой основе не распространены в технологии нанесения покрытий. Они имеют тенденцию к притягиванию пыли и порошка и являются потенциальным источником загрязнения покрытий при отсутствии точного контроля. Нельзя применять смазки на основе силиконов. Они могут отрицательно повлиять на качество покрытий, хотя конвейерные цепи, смазанные ими, могут легко и непрерывно работать при повышенных температурах около 150-200 °С.
Рис.19. Централизованная система подачи смазочного материала:
1 — монорельс;
2 – обратный привод; 3 – двойная ветвь;
4 – трубчатый узел; 5 – закрытая дорожка; 6 — свободный транспортер с обратным приводом;
7 – инвертированный конвейер; 8 — траншейный узел; 9 – линия смазочного материала;
10 — линия подачи электрического питания;
11 — центральная система смазки с емкостью на 200 л
Существует два основных метода нанесения смазочного материала на рабочие и движущиеся конвейерные цепи, а также подшипники тележек. Первый и наиболее часто используемый метод заключается в подаче смазочного материала растворного типа в точно контролируемых количествах в подшипники, точки износа и на поверхности, требующие смазки (рис.19). Второй метод применяется для конвейеров с герметичными подшипниками. Их смазывают консистентной смазкой вручную или автоматически.
Конвейерная система, проходящая через все стадии процесса нанесения покрытия, может загрязняться, что вызывает необходимость ее периодической чистки. С этой целью применяют щеточные очистители. Они предусмотрены для очистки конвейерных цепей, тележек, дорожек и санитарных крюков.
Рис.20. Типичные щеточные очистители конвейеров:
а — закрепление немеханизированного щеточного очистителя на цепи для секций закрытой дорожки;
б – то же для цепи и колес закрытой дорожки; в – механизированный
и г – немеханизированный щеточный очиститель для цепи и тележек двутавровой балки
Щеточные очистители конвейеров могут быть механизированными либо немеханизированными. В механизированных очистителях, монтируемых на дорожке конвейера, обычно используются круглые щетки из проволоки или жесткой пластмассы. Механизированные щеточные очистители могут иметь микропроцессорное управление, так что время и продолжительность очистки могут быть запрограммированы. Все механизированные щетки должны иметь ограждение для сведения к минимуму разбрасывания удаляемых загрязнений и пыли (рис.20).
Немеханизированные щеточные очистители могут быть неподвижными, используемыми для очистки движущейся конвейерной цепи, или прикрепленными к движущемуся конвейеру для очистки поверхностей дорожки конвейера, несущих нагрузку, как это показано на рис.20. Немеханизированные очистители конвейерной цепи и тележек монтируются на дорожке конвейера таким образом, что их щетки приводятся в соприкосновение с различными участками движущейся конвейерной цепи. При движении конвейера щетки вращаются. Усилие, прилагаемое к немеханизированному очистителю конвейера, обычно регулируется пружинами или фрикционной муфтой. Немеханизированные очистители дорожек закрепляются на конвейерных цепях. После прохождения нескольких циклов конвейерной системы их снимают.
Детали, транспортируемые конвейерной системой, должны быть надлежащим образом заземлены. Используется несколько видов заземления. Обычно на рельс конвейера устанавливают медные щетки или приспособления в виде подвижных стержней. Проходя мимо них, подвески деталей соприкасаются со щетками, обеспечивая их соединение с землей.
Другим местом заземления является точка контакта детали с подвеской. Часто пытаются создать универсальное приспособление для подвески, которое обеспечивало бы большую гибкость и меньшую стоимость транспортировки и производства. Но при этом точки контакта детали с приспособлением для подвески, открытые во время нанесения, обрастают порошком и изолируются. Более рациональна конструкция приспособления для подвески с использованием ножевого контакта. В данном методе, как показано на рис.21, приспособление для подвески имеет острую грань в месте соприкосновения с деталью. В процессе транспортировки порошок ссыпается с острия, обнажая контакт. Чем больше нагрузка от детали на приспособление для подвески, тем меньше проблем с заземлением в данной контактной точке, поскольку острая грань легче проходит через слой порошкового материала.
Следующий контактный участок – точка контакта приспособления для подвески с нагрузочным рычагом, транспортером или тележкой. Это соединение не проходит через камеру нанесения порошка, так что вероятность оседания на нем порошка ничтожно мала. И все же полезно учитывать требования проводимости в данных точках путем сведения к минимуму контактов двух плоских поверхностей и применения вместо этого ножевых контактов, где это возможно.
Рис.21. Ножевой (или точечный ) контакт подвески с деталью
(увеличенный вид сбоку в точке подвески детали):
1 – точка контакта; 2 – отверстие для подвески;
3 – деталь; 4 – приспособление для подвески детали
Приспособления для подвески деталей должны часто очищаться для удаления осевшего непроводящего порошка. Крюки, на которые подвешиваются детали, требуют очистки, по крайней мере, один раз в день. В случае нанесения жидких красок для очистки крюки полностью опускают в раствор каустической соды, а в случае порошковых материалов, как правило, используют высокотемпературную печь для выжигания с последующей промывкой водяной струей.
Наконец, нужно отметить, что при избыточной смазке часть ее может попадать в точки контакта, нарушая заземление и приводя к осаждению порошкового материала на детали. Поэтому надлежащая смазка конвейера имеет большое значение для достижения оптимальной производительности конвейера и заземления деталей.
Контроль и обслуживание конвейера осуществляют при постоянном наблюдении, однако существуют вспомогательные средства, облегчающие контроль производительности конвейера и его эксплуатационных характеристик.
Имеется возможность полуавтоматического контроля с помощью системы управления или компьютера. Система управления может сигнализировать о любых ситуациях в ходе работы конвейера, которые являются или могут стать факторами, определяющими производительность конвейера или его потребность в техническом обслуживании. Примером может служить остановка конвейера при отсутствии смазочного материала в резервуаре системы смазки. Другие параметры работы конвейера, которые необходимо контролировать:
Получив сигнал об отклонениях от нормального функционирования или неисправности в работе конвейера, можно принять меры по их устранению без дорогостоящего простоя, вызванного износом или отказом отдельных частей.
vseokraskah.net
эксплуатация и обслуживание – это… Что такое эксплуатация и обслуживание?
- эксплуатация и обслуживание
эксплуатация и обслуживание
—
[А.С.Гольдберг. Англо-русский энергетический словарь. 2006 г.]Тематики
- энергетика в целом
EN
- operations and maintenance
- O&M
Справочник технического переводчика. – Интент. 2009-2013.
- эксплуатация и контроль
- эксплуатация и ремонт
Смотреть что такое “эксплуатация и обслуживание” в других словарях:
ГОСТ Р 53341-2009: Эксплуатация, техническое обслуживание и ремонт железнодорожного подвижного состава. Термины и определения — Терминология ГОСТ Р 53341 2009: Эксплуатация, техническое обслуживание и ремонт железнодорожного подвижного состава. Термины и определения оригинал документа: 53 авторский надзор при эксплуатации и ремонте железнодорожного подвижного состава:… … Словарь-справочник терминов нормативно-технической документации
ГОСТ 27928-88: Машины землеройные. Эксплуатация и обслуживание. Обучение механиков — Терминология ГОСТ 27928 88: Машины землеройные. Эксплуатация и обслуживание. Обучение механиков оригинал документа: 5.2. Второй год обучения 5.2.1. Типовая программа второго года обучения содержит следующие разделы: техническое обслуживание и… … Словарь-справочник терминов нормативно-технической документации
техническая эксплуатация и обслуживание — — [Л.Г.Суменко. Англо русский словарь по информационным технологиям. М.: ГП ЦНИИС, 2003.] Тематики информационные технологии в целом EN operation and maintenance … Справочник технического переводчика
управление, эксплуатация и обслуживание физического уровня — Выполняет функции управления PON, такие как определение дальности, активизация ONU, установление OMCC и передачу аварийных сигналов (МСЭ Т G.984.3). [http://www.iks media.ru/glossary/index.html?glossid=2400324] Тематики электросвязь, основные… … Справочник технического переводчика
эксплуатация — 3.2 эксплуатация: Стадия жизненного цикла изделия (горки), на которой реализуется, поддерживается и восстанавливается его качество (работоспособное состояние). Источник: ГОСТ Р 52604 2006: Аквапарки. Водные горки высотой 2 м и выше. Безопасность… … Словарь-справочник терминов нормативно-технической документации
эксплуатация железнодорожного подвижного состава — 1 эксплуатация железнодорожного подвижного состава: Стадия жизненного цикла железнодорожного подвижного состава, на которой реализуется, поддерживается и восстанавливается его качество. Примечание Эксплуатация включает в себя использование по… … Словарь-справочник терминов нормативно-технической документации
Эксплуатация вычислительных комплексов — ЭКСПЛУАТАЦИЯ ВЫЧИСЛИТЕЛЬНЫХ КОМПЛЕКСОВ, СИСТЕМ И СЕТЕЙ Содержание 1 Ввод 2 Системотехническое обслуживание 3 Настройка операционной системы … Википедия
эксплуатация станка — эксплуатация станка: Использование станка по назначению, техническое обслуживание и ремонт, транспортирование и хранение; Источник: ГОСТ 12.2.009 99: Станки металлообрабатывающие. Общие требования безопасности оригина … Словарь-справочник терминов нормативно-технической документации
Эксплуатация авиационной техники — совокупность процессов использования авиационной техники, поддержания и восстановления её качества на всех этапах её существования (применение и ожидание применения по назначению, транспортирование, хранение, техническое обслуживание, ремонт).… … Энциклопедия техники
Обслуживание оборудования — Эксплуатация, ремонт, наладка и испытание технологического оборудования, а также пусконаладочные работы на нем Источник: РД 34.03.201 97: Правила техники безоп … Словарь-справочник терминов нормативно-технической документации
technical_translator_dictionary.academic.ru
Эксплуатация и обслуживание кранов-манипуляторов – Основные средства
Итак, вы приобрели новую КМУ. Чтобы поставить ее на учет в Ростехнадзоре, надо представить договор на обслуживание приборов безопасности в какой-либо аттестованной сервисной организации. Владельцу же рекомендуется выполнить по крайней мере визуальный осмотр и проверку герметичности гидросистемы, так как возможны повреждения при транспортировке.
Типичные ошибки, которые допускают в эксплуатации
Прежде всего пользователи не читают инструкцию по эксплуатации. Знакомство с КМУ следует начать с ее внимательного изучения, это поможет избежать многих неприятностей.
Самая главная и типичная ошибка в эксплуатации: использование в гидросистеме рабочей жидкости, не рекомендованной производителем. Половина отказов КМУ в эксплуатации происходит из-за этого. Потребители часто не понимают важности характеристик рабочей жидкости и думают, что можно заправить в КМУ любую гидравлическую жидкость.
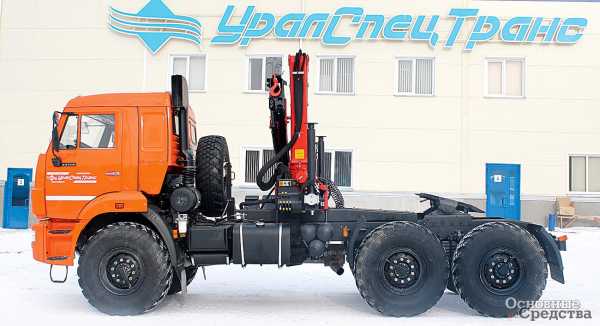
Отсутствие ежедневного и еженедельного техобслуживания – просто-таки бич КМУ. Узлы трения не смазывают, и в них идет повышенный износ. Через год-два такой эксплуатации в соединениях манипулятора возникают огромные люфты: шатаются колонна, секции стрелы, а порой и аутригеры.
Третья проблема – постоянные ошибки операторов при управлении КМУ. Научиться управлять установкой просто, достаточно прочитать инструкцию и попрактиковаться всего несколько минут. У некоторых компаний, продающих манипуляторы, есть услуга – обучение операторов. И тем не менее часто управляют КМУ совершенно неправильно.
При транспортировке КМУ фиксируют в сложенном положении на специальных кронштейнах и упорах стальными пальцами либо пружинными кольцами. Так же фиксируют в транспортном положении аутригеры. Перед началом работы фиксаторы следует снять, стрела должна раскладываться из транспортного положения в определенном порядке, который описан в инструкции. Вначале следует вторую секцию стрелы поджать к первой, сняв с кронштейна, а только затем раскладывают первую секцию. Если этого не сделать, либо кронштейн ломается, либо стрела пружинит соскакивая с него, и падает, разбивая все, что находится ниже.
В процессе работы операторы часто ударяют стрелой по окружающим предметам и даже по кабине, забывают убирать аутригеры и повреждают их при движении. Распространенная ошибка: неправильная работа с грузом, например грузы волокут по земле стрелой. При подъеме груза стрела должна занимать определенные положения (все они описаны в инструкции). В противном случае грузоподъемность стрелы будет значительно ниже ее реальных возможностей, слишком рано срабатывает система защиты от перегрузки. Например, максимальная грузоподъемность достигается при определенном угле между первой секцией стрелы и горизонталью. Кинематика КМУ такова, что при подъеме груза нагрузка на один гидроцилиндр может быть 85%, а на другой только 15%. Нельзя использовать манипулятор не по назначению: упираясь стрелой в землю, приподнимать автомобиль для того, чтобы поменять колеса, либо пытаться вытолкнуть застрявший автомобиль из грязи, упираясь в землю стрелой. При этом механизм КМУ испытывает нагрузки, на которые он не рассчитан, гнутся штоки цилиндров, расшатываются шарниры соединений стрел. Чаще всего страдает гидроцилиндр подъема первой секции стрелы, так как на него приходится самая большая нагрузка. Если гидравлические контуры защищены от перегрузки редукционными клапанами, то механические детали защиты от нештатных нагрузок не имеют.
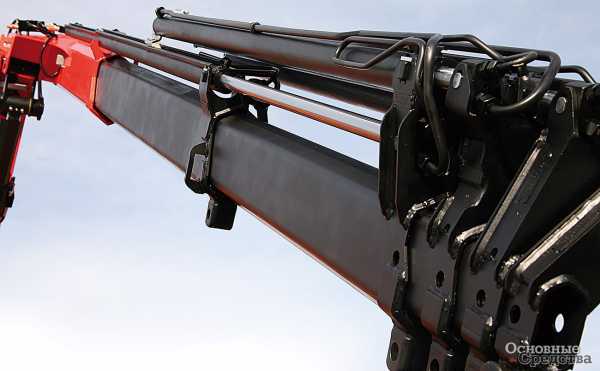
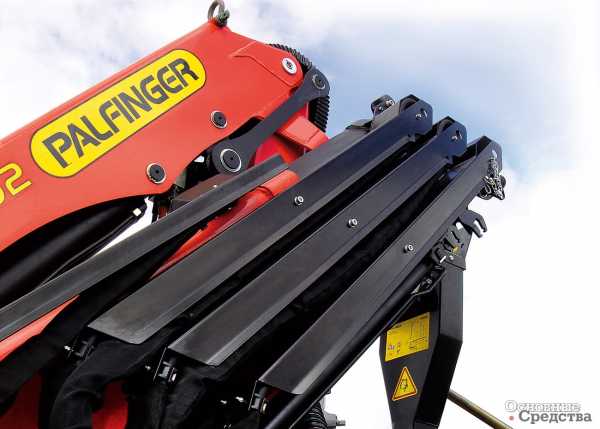
Часто операторы не выставляют опоры на нужную ширину. Это приводит к опрокидыванию установки.
После длительного простоя на морозе гидросистему нужно сначала разогреть: дать насосу поработать на холостом ходу, выполнить несколько движений без нагрузки, погонять жидкость по малому кругу, через бак минут 10…15. Затем медленно, плавно начинать работать с КМУ и проверить выполнение всех функций, не доводя секции стрелы до крайних положений. Летом так тщательно разогревать гидросистему не требуется: раскладывание манипулятора из транспортного положения, выдвижение аутригеров, проверка рабочих функций – эти подготовительные операции позволяют прогреть жидкость.
Если у КМУ нет маслоохладителя, его роль выполняет бак, поэтому бак должен быть достаточно большой вместимости, примерно равной объему, который накачивает насос за 2…3 минуты. Например, если подача насоса 50 л/мин, то вместимость бака должна составлять 100…150 л. К сожалению, бывает, что владельцы используют бак меньшей вместимости, чтобы сэкономить на жидкости. В результате жидкость быстрее стареет, повышается вероятность ее перегрева – недостаточный объем жидкости не успевает охлаждаться во время работы. В результате такой «экономии» компоненты гидросистемы быстрее изнашиваются.
Техническое обслуживание
Предусмотрено техобслуживание КМУ ежедневное, еженедельное, квартальное и т. д. Периодичность указывают в инструкции и в моточасах, и в днях. Приводится карта смазки с указанием способа смазки: под давлением (шприцевание) или нанесение на трущиеся поверхности. Имеются и таблицы рекомендуемых технических жидкостей и смазок. Описывается даже порядок мойки КМУ. Комплекс работ по обслуживанию манипулятора (замена жидкости, фильтров, смазка шарниров) не сложен, при необходимости его может выполнять сам владелец. Ежедневное ТО – это визуальный осмотр КМУ и всего автомобиля. Следует проверить функции установки, особенно работу приборов безопасности. Еженедельное обслуживание включает в себя шприцевание шарниров.
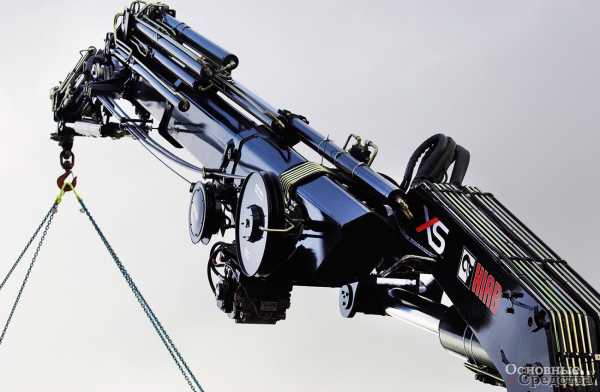
Выполняя ТО, не следует забывать о поворотном механизме. Если он находится в масляной ванне, масло также следует периодически менять. Аутригеры нуждаются лишь в смазке шарнира. Надо следить за состоянием штоков, содержать их в чистоте от грязи, попадающей с дороги. Необходимо следить за чистотой разъемов для подключения гидравлических орудий, так как на рабочую жидкость налипает пыль. Рекомендуется использовать защитные колпачки, а для электрических разъемов применять специальную смазку, так они меньше корродируют от соли на дорогах. На некоторых моделях КМУ имеются охладители масла. Их следует регулярно очищать от пыли и грязи, следить, чтобы ничто не препятствовало доступу воздуха. Обязательно регулярно подтягивают резьбовые соединения деталей крепления манипулятора к надрамнику и т. д., проверяют состояние фиксаторов и пальцев. Моменты затяжки указаны в инструкции.
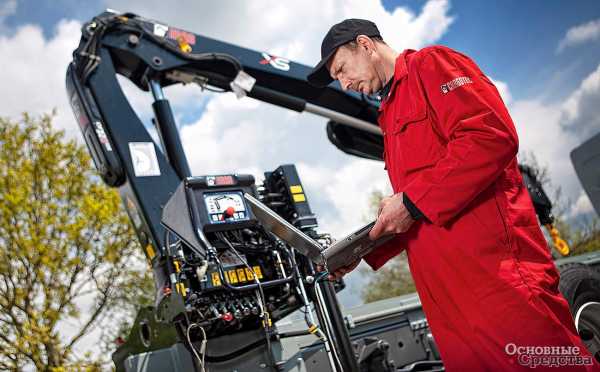
Гидравлическая жидкость
Рекомендуется во время работы следить за температурой жидкости по термометру, совмещенному с датчиком уровня жидкости в баке. Конечно, если температура достигла критической, надо остановить КМУ и дать жидкости остыть. При 100 °С жидкость в значительной степени теряет свои прежде всего смазывающие свойства, начинает интенсивно окисляться.
Следует заменять гидрожидкость не реже раза в год, даже если КМУ работала мало или вообще не работала. Жидкость гигроскопична, она впитывает влагу, это приводит к превращению масла в эмульсию, что крайне опасно для силовых цилиндров и гидрозамков, к коррозии металлических компонентов гидросистемы. При замене жидкости обязательно заменяют и фильтры. В некоторых установках имеется только один фильтр в гидросистеме – сливной, в баке. Если техника работает при более высоких давлениях, требования к очистке масла у нее повышены и в системе устанавливают второй фильтр – в напорной ветви между насосом и гидрораспределителем. В гидросистеме КМУ HIAB с дистанционным управлением, например, устанавливают даже три фильтра.
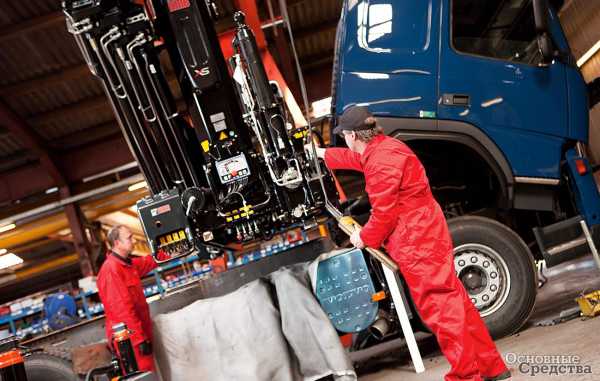
В гидросистеме может быть установлен индикатор засорения фильтра – манометр. При нормальных условиях эксплуатации стрелка манометра практически не меняет своего положения от смены до смены фильтра. Если же стрелка начинает резко уходить в зону повышенного давления, значит, надо обратить внимание на условия эксплуатации. Например, при работе в условиях высокой запыленности (в пустыне, в запыленном складе) следует чаще заменять фильтры и жидкость.
КМУ складывают в транспортное положение, откручивается сливная пробка бака, и жидкость сливается. Заправляют свежую жидкость, устанавливают новый фильтр. Затем рекомендуется несколько раз сложить-разложить манипулятор, чтобы гарантированно заполнить систему. Никаких специальных пробок для выпуска воздуха открывать не надо, так как КМУ имеют гидросистемы открытого типа и весь воздух выходит через сапун бака. Если бак чистый, промывать его нет необходимости. Рекомендуется дополнительно фильтровать жидкость перед заправкой в гидросистему: с помощью несложной установки прокачать насосом жидкость из бочки через фильтр и далее в бак КМУ.
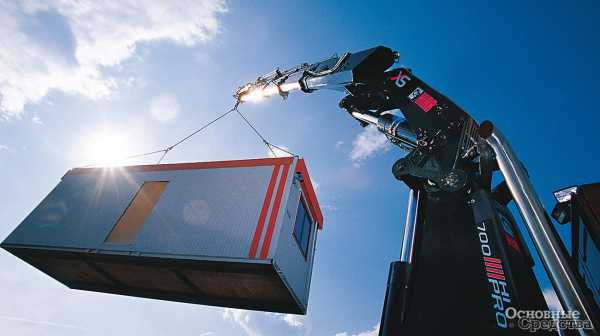
На дне гидробака есть углубление с пробкой, в котором отстаиваются вода и грязь. Этот отстой следует регулярно сливать – раз в неделю. Если отстоя сливается много, необходимо компенсировать убыль жидкости доливом. Доливать следует аккуратно, из чистой посуды и через сетчатый фильтр, чтобы в бак не попала грязь.
В гидросистеме может быть заправлена всесезонная жидкость. Однако при значительной разнице температур воздуха между летним и зимним периодами универсальная жидкость будет не очень хорошо работать, а потому рекомендуется заменять жидкость на летнюю и зимнюю. При выборе зимней жидкости рекомендуется проверить температуру застывания: она должна быть существенно ниже предполагаемых температур окружающей среды, так как вблизи точки застывания жидкость превращается в густую студенистую массу. Слитую сезонную жидкость можно использовать повторно в следующем сезоне, если она еще не потеряла своих свойств.
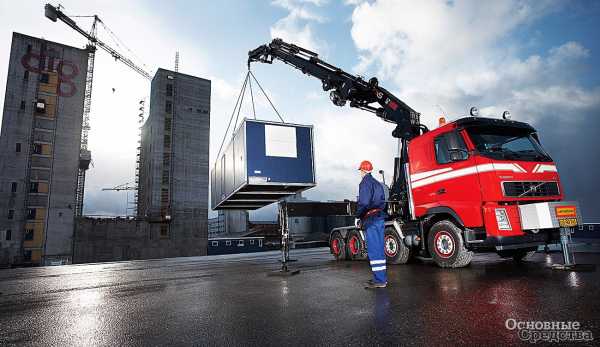
Недопустимо использование летней жидкости в холодный период и зимней жидкости – летом. Летняя жидкость зимой будет слишком густой, и в момент запуска холодного манипулятора возможно превышение давления в системе выше допустимого, насос не справится с прокачкой загустевшей жидкости по системе, возможны поломки насоса или компонентов гидросистемы – уплотнений и шлангов. Замерзшие редукционные клапаны не смогут сбросить давление. Зимняя жидкость в жару будет слишком жидкой. Возможен перегрев гидросистемы, который приведет к выходу ее из строя. От перегрева пересыхают уплотнения гидравлических компонентов, поэтому неизбежно увеличатся утечки, а уменьшенные смазывающие свойства жидкости приводят к задирам в гидроузлах.
Производители КМУ дают рекомендательные таблицы рабочих жидкостей, зимних, летних и всесезонных. Тем не менее при подборе жидкости рекомендуется дополнительно проконсультироваться с производителем или продавцом жидкости.
Диагностика и ремонт
Рекомендуется с периодичностью, указанной в инструкции, измерять зазор между телескопическими секциями стрелы и пластинами скольжения, а также следить за толщиной опорных пластин скольжения цилиндров. Стрела кладется на землю с небольшим усилием, зазор выбирают и измеряют снизу. Некоторые производители рекомендуют регулярно смазывать трущиеся поверхности, некоторые (в случае когда пластины изготавливаются из полимерных материалов, не требующих смазки) не рекомендуется смазывать, так как на смазку налипает пыль. Необходимо своевременно менять пластины, чтобы люфт между секциями не превышал допустимой величины и перемещения КМУ были более точными. К сожалению, на практике часто пластины скольжения не меняют, пока «металл не начнет скрести по металлу».
Гидроцилиндры – очень долговечный компонент. У КМУ высокого класса и через 10 лет цилиндры обычно не имеют износа и даже «родные» уплотнения еще в хорошем состоянии. Однако рано или поздно приходит пора ремонта. В гарантийный период рекомендуется применять только оригинальные запчасти, чтобы не потерять права на гарантийное обслуживание.
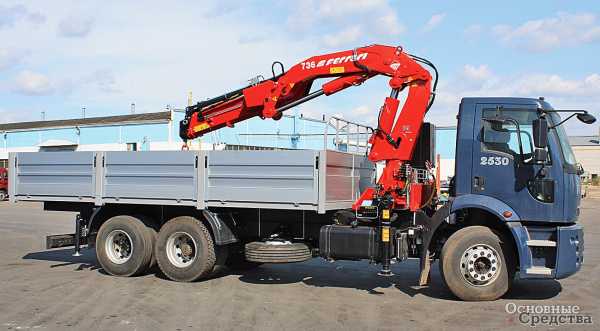
Известно, что ряд деталей производители КМУ закупают у сторонних компаний: это уплотнения, фильтры и т. д. Эти специализированные компании сами поставляют на российский рынок свои изделия (те же фильтры, манжеты), и цена на них, как правило, ниже, чем на «оригинальные». Поэтому в послегарантийный период можно устанавливать такие запчасти без ущерба для производительности КМУ, но только если есть уверенность в их качестве. Однако это относится только к запчастям от проверенных поставщиков и только к расходным материалам – уплотнениям, фильтрам, жидкости.
Если же надо заменить компоненты гидросистемы (гидрораспределители, гидрозамки и т. п.), то не оригинальные поставщики вряд ли смогут предложить что-либо подходящее, потому что у каждого производителя свои характеристики и конструкции компонентов. К тому же КМУ – источник повышенной опасности, и ставить компонент «наобум» просто опасно.
В электронной системе КМУ причиной отказов в основном бывает нарушение контакта с каким-либо датчиком либо короткое замыкание вследствие повреждения проводов грузом, а также иногда значительные скачки напряжения в бортовой сети автомобиля в зимний период, что особенно актуально для российских грузовиков.
Автор благодарит С. Лосева, специалиста ООО «Карготек Рус», и С. Малинина, специалиста фирмы PM Group S.p.A., за помощь в подготовке статьи
os1.ru
Добавить комментарий