Дробилки конусные – Конусная дробилка (ККД, КМД, КСД). Классификация, схема, принцип действия и конструкция
Конусные дробилки. Принцип работы, устройство, конструктивные решения.
Конусные дробилки
Конусные дробилки выгодно отличаются от щековых тем, что процесс дробления породы в них осуществляется непрерывно, т.е. отсутствует холостой ход.
Куски породы раздавливаются в пространстве между двумя коническими поверхностями, образованными подвижным органом и неподвижной конусообразной чашей.
Такая конструкция используется, когда необходимо измельчить руду черных или цветных металлов, а также не очень крупные куски неметаллических руд.
Следует отметить также, что, при прочих равных условиях, лещадность щебня получаемого при помощи конусных дробилок ниже, чем щековых.
Конический рабочий орган совершает вращательно-колебательное (гирационное) движение внутри чаши-основания, измельчая подаваемые в верхнюю загрузочную кольцевую щель породу. Готовый продукт удаляется под действием силы тяжести в нижнее разгрузочное отверстие.
Наглядно рассмотреть принцип работы конусной дробилки можно на приведенном изображении-анимации.
Конструкция конусной дробилки была изобретена давно, в 1877 году, практическое применение было осуществлено лишь в 20-х годах прошлого столетия.
Технологически конусные дробилки подразделяют на дробилки крупного (ККД), среднего (КСД) и мелкого (КМД) дробления. Конструктивное отличие между этими дробилками заключается не только в размерах рабочих органов, но и в соотношении высоты конусов к диаметру основания.
У дробилок крупного дробления такое соотношение выше, т.е. конус узкий и высокий (угол при вершине около 20 град.). Загрузочная щель широкая и позволяет принимать куски породы размером до 1200 мм, например дробилка ККД-1500/300 (здесь 1500 – ширина приемной щели, а 300 – диаметр разгрузочного отверстия).
У конусных дробилок среднего и мелкого дробления угол конической поверхности рабочих органов больше (до 100 град.), т.е. соотношение высоты конуса к диаметру его основания меньше.
Форма дробящей поверхности конусных дробилок не образует правильный конус. На различных ступенях и участках взаимодействия кусков руды с рабочими органами прилагаются разные дробящие нагрузки. Это достигается ступенчатым или плавным изменением угла конической поверхности по высоте конуса.
Основным недостатком дробилок такого типа является повышенная энергоемкость технологии дробления, громоздкость и металлоемкость конструкции. Преимущества – высокая производительность и непрерывный цикл воздействия на дробимый материал.
Проблема попадания между рабочими органами недробимого материала решена при помощи пружинной подвески неподвижной конической чаши к раме. При заклинивании дробилки из-за попадания твердого куска породы, чаша слегка опускается или смещается в сторону, увеличивая тем самым выпускной проем, и недробимый элемент удаляется под действием силы тяжести. Следует отметить, что такая конструкция применяется лишь в конусных дробилках среднего и мелкого дробления.
Среди новаторских решений для конструкций конусных дробилок можно отметить применение в качестве привода подвижной конической головки вибраторов дебалансного типа, сообщающих подвижному дробящему конусу вибрацию, что обеспечивает высокую степень дробления.
Дробилки такого типа называют инерционными конусными дробилками.
К достоинствам такой конструкции можно отнести возможность запуска при загруженном рабочем пространстве, при завале, более высокую производительность и качество дробления.
Среди недостатков – усложнение конструкции, повышение энергопотребления.
В последние годы получают все большее распространение дробилки с гидравлическим регулированием щели, что позволяет упростить настройку размера продукта на выходе (фракции), а также использовать гидравлику в качестве предохранителя (компенсатора) перегрузок, возникающих при попадании в рабочую полость труднодробимого продукта. Подобные дробилки выпускает ряд фирм ФРГ: “Эш-Верке”, “Ведаг”, “Гутехоффнунгсхютте”, а также франко-английская фирма “Баббитлесс” и шведская фирма “Маргардсхаммар”.
Отдельно следует отметить интересное решение конструкторов фирмы “Эш-Верке”, которые разработали уникальную форму неподвижной чаши и подвижного конуса дробилки, получив своеобразный гибрид щековой и конусной дробилок. Внешний вид такой установки представлен на рисунке слева. Верхняя часть загрузочной щели выполнена более полого, что позволяет загружать в щель крупные куски горной массы. На этом участке сопряжения неподвижного и подвижного органов дробилка работает подобно классической щековой. В средней и нижней части чаши и конуса щель сужается, и дробимый продукт измельчается по технологии конусной дробилки. В результате, как уже отмечалось, можно использовать для измельчения крупное сырье, как в щековых дробилках, а на выходе получать щебень кубовидной формы, как в классической конусной дробилке.
Среди прочих конструктивных особенностей конусных дробилок можно отметить применение гидравлических затворов, позволяющих предохранить втулки опор и приводные узлы от попадания грязи и пыли.
***
Мобильные дробилки и дробильные комплексы
granit2006.ru
Конусные дробилки
Материал в конусных дробилках (рис. XVIII -6) измельчается раздавливанием его при сближении поверхностей внутреннего подвижного 1 наружного неподвижного 2 конусов.
Процессы дробления и разгрузки в конусных дробилках отличаются от соответствующих процессов в щековых дробилках непрерывным воздействием на дробимый материал дробящих поверхностей криволинейной формы.
По своему назначению конусные дробилки разделяются на дробилки крупного, среднего и мелкого дробления.В дробилке крупного дробления (рис. XVIII-6, а) крутой подвижный конус приводится в движение вокруг неподвижной оси 3 валом-эксцентриком 4 при помощи конической шестерни 5. Неподвижный конус (чаша) 2 обращен большим основанием кверху.
В дробилке среднего и мелкого дробления (рис. XVIII-6, б) пологий подвижный конус /, закрепленный на вращающемся с помощью эксцентрикового стакана 6 валу 7, расположен внутри неподвижного конуса 2 (обращенного большим основанием вниз). В момент максимального сближения дробящего конуса с чашей такой дробилки создается «параллельная зона» длиной l (рис. XVIII-6, б). Ширина этой зоны определяет размер кусков дробленого продукта.
Рис. XVIII-6. Схемы конусных дробилок:
а — крутоконусной с неподвижной осью; б — пологоконусной с консольным валом; 1 — подвижный конус; 2 — неподвижный конус; 3 — ось; 4 — эксцентриковый вал; 5 — шестерня; 6 — эксцентриковый стакан; 7 — вал.
Дробилки крупного и мелкого дробления могут иметь привод как в виде эксцентрикового вала, так и в виде эксцентрикового стакана. Широко распространены дробилки крупного дробления, в которых подвижный конус приводится в движение также посредством эксцентрикового стакана.
Дробилки крупного дробления (крутоконусные) характеризуются наибольшей шириной загрузочного (верхнего) кольцевого отверстия. Дробленый материал выходит из нижней круговой щели под действием своего веса в месте наибольшего удаления дробящего конуса от чаши. Дробилки среднего и мелкого дробления (пологоконусные) характеризуются размером диаметра основания внутреннего конуса. Разгрузка в такой машине осуществляется под действием сил тяжести, инерции и трения. Корпус конусной дробилки и ее чаша связаны пружинами, позволяющими чаше подниматься вверх, предотвращая тем самым поломку аппарата в случае попадания в него металлических предметов. Внутренняя рабочая поверхность неподвижного конуса и поверхность подвижного конуса футеруются сменными плитами из марганцовистой стали. Регулирование степени измельчения производится подъемом или опусканием чаши.
Конусные дробилки по сравнению со щековыми отличаются высокой1 производительностью (вследствие непрерывного воздействия дробящего усилия на материал), уравновешенной работой (нет необходимости в установке маховика), высокой степенью измельчения (для пологоконусных дробилок).
Недостатками конусных дробилок (в сопоставлении со щековыми) являются: более сложная и дорогая конструкция, большая высота, более сложное обслуживание.
Среднее и мелкое дробление
studfiles.net
Конусные дробилки: основные типы, устройство и принцип работы, технические характеристики, преимущества и применение
Дробилка, работа которой осуществляется с помощью движения конуса и его механическое воздействие на стенки чаши, в которую поступает исходный материал.
Условное обозначение конусных дробилок имеет свою систему, утвержденную российским ГОСТом.
Основные типы дробилок российского производства маркируют так:
- КРД – конусные редукционного дробления.
- ККД – конусные крупного дробления:
- С одним двигателем,
- С двумя двигателями.
- КСД — конусные среднего дробления:
- Грубого дробления,
- Тонкого дробления.
- КМД – конусные мелкого дробления:
- Грубого дробления,
- Тонкого дробления.
Далее могут указываться технические характеристики и вид исполнения (буквенные и цифровые обозначения параметров моделей).
Модели иностранного производства маркируются в соответствие со своими правилами.
Основные классификации
Деление конусных дробилок:
- Для крупного дробления:
- одноприводные,
- двухприводные.
- Для вторичного крупного дробления.
- Для среднего дробления:
- с камерой грубого дробления,
- с камерой тонкого давления.
- Для мелкого дробления:
- с камерой грубого дробления,
- с камерой тонкого давления.
Устройство и принцип работы
Хотя модельный ряд устройств подобного рода и широк, принцип действия всех конусных дробилок одинаков.
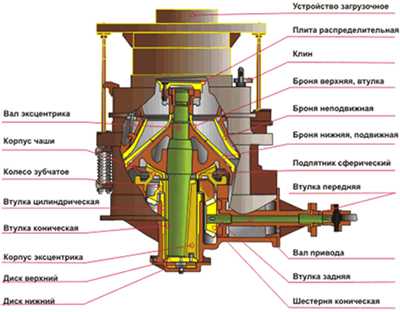
Конусная дробилка представляет собой чашу, в которой установлен вал с жестко закрепленным конусом. Верхняя часть вала закреплена в одной точке, а нижняя находится в специальном эксцентриковом стакане. Электрический двигатель приводит этот стакан движение, а вал, в свою очередь, смещает конус. Дробление материала происходит, когда частицы оказываются между рабочим конусом и стенкой чаши. На исходный материал оказывается огромная сила сжатия, сдвига и удара. В результате чего у частиц разрушается структура и они рассыпаются на более мелкие составляющие. Как только конус удаляется от стенки, измельченный материал под действием силы тяжести перемещается в нижнюю часть резервуара и выводится наружу. Процесс измельчения происходит непрерывно, поэтому такое дробильное оборудование характеризуется высокой производительностью.
Различия в конструкции дробилок для крупного, среднего и мелкого измельчения есть. В первом случае угол конуса при его вершине составляет около 20 градусов (крутой конус). При этом эксцентриситет стакана менее 25 мм. Для среднего и мелкого дробления угол будет составлять около 100 градусов (пологий конус). Эксцентриситет будет в этом случае более 100 мм.
Технические характеристики
Различаются в зависимости от модели. Приведены нижние и верхние границы показателей.
Приемное отверстие — до 300/1500 мм.
Максимальный диаметр частицы исходного материала — до 390 мм.
Ширина выхода – 270 мм.
Производительность – до 3420 м3 в час.
Мощность двигателя – до 800 кВт.
Преимущества и применение
Чаще всего этот тип дробилок применяют для измельчения руды.
Основным преимуществом является большая производительность устройства. Кроме того современные разработки позволяют устанавливать рабочие органы конусных дробилок из таких материалов, что их износостойкость находится на довольно таки приличном уровне.
drobilko.ru
Конусные дробилки — Дробильное оборудование
Содержание статьи
Конусные дробилки имеют множество технических достоинств, что делает устройства данного типа незаменимыми в работе с трудно дробимыми телами. Технологические решения позволяют минимизировать затраты на ремонт и обслуживание конусных измельчителей.Дробилки с конусом диаметром 600, 900 и 1200 мм обычно поставляют в собранном виде, а электродвигатель, клиновые ремни, смазочную систему, пусковую аппаратуру и запасные части — упакованными в ящики. Для дробилок используют армированный фундамент. Под основание дробилки на фундамент подкладывают доски толщиной 60… 70 мм для снижения вибрации.
Масляный бак с масляным насосом и шкаф управления дробилкой устанавливают в защищенном от пыли помещении. Соединение труб при монтаже должно быть надежным во избежание течи масла. Для герметичности трубы соединяют на сурике.
Масса наиболее тяжелых сборочных единиц конусных дробилок, τ — таблица 23.
Сборочные единицы | КСД-1750 и КМД-1750 | КСД-2200 и КМД-2200 |
Станина в сборе с опорным кольцом и пружинами | 22 | 40 |
Дробящий конус | 8-,2 | 18 |
Регулирующее кольцо | 8,8 | 15 |
То же, с кожухом | 10,5 | 18 |
Приводной вал | 1.1 | 2,8 |
Конусные дробилки с диаметром конуса 1750, 2200 мм поставляют в разобранном виде. Монтаж их начинают с установки и подливки фундаментных плит, а если их нет, с установки и подливки станины. Затем монтируют приводной вал, диски подпятника и вал — эксцентрик, проверяют зубчатое зацепление, устанавливают опорную чашу, узел дробящего конуса, устройство регулирования щели, регулирующее кольцо с кожухом, загрузочное устройство и, наконец, привод.
Помещение дробильного цеха оборудуют передвижными грузоподъемными средствами для монтажа и демонтажа сборочных единиц дробилки и вспомогательного оборудования. Грузоподъемность указанных средств необходимо выбирать в соответствии с массой наиболее тяжелых узлов дробилки, значения которой приведены в табл. 23.
Схемы строповки сборочных единиц дробилки:
а —станины, б —дробящего конуса, в — вала эксцентрика, г —опорной чаши, о — приводного вала; Н, h, L, Д — габаритные и монтажные размеры
Качество монтажа во многом зависит от удобства строповки сборочных единиц и деталей оборудования. Особенно это важно для крупных деталей, имеющих точные посадочные поверхности. Поэтому в конструкции сборочных единиц предусмотрены места крепления канатов. Схемы строповки наиболее крупных сборочных единиц конусных дробилок показаны на рис. 101. Обычно сборочную единицу крепят к стропам в таком положении, в котором она будет находиться в конструкции изделия, например горизонтальный вал привода —в горизонтальном положении (рис. 101,(3).
Рис. 102. Выверка станины в сборе с опорным кольцом:
1 — фундаментная плита, 2 —пружина, 3— опорное кольцо, 4— рукав уплотнения, 5 — линейка, 6 — уровень, 7 — цилиндрическая втулка, 8 — станина
Станина
Станина с опорным кольцом 3 (рис. 102) и пружинами 2.
Станина 8 или непосредственно опирается на фундамент, или через специальные фундаментные плиты 1.
При установке непосредственно на фундамент станину выверяют в горизонтальной и вертикальной плоскостях с помощью клиньев высотой около 50 мм (не менее). Правильность установки станины проверяют линейкой 5 с уровнем 6, базируясь на обработанную поверхность под опорную чашу, и по отвесу, базируясь на обработанную поверхность цилиндрической втулки 7, запрессованной в центральном патрубке станины.
Отклонение образующей втулки 7 от вертикали допускается не более 0,3 мм на всю длину втулки. После выверки станину затягивают анкерными болтами и вновь контролируют точность ее выверки. Окончательно (выверенную станину подливают цементным раствором слоем 50 мм. Марка цемента не ниже 250 , затем заливают колодцы фундаментных болтов.
При установке станины на фундаментные плиты 1 их предварительно монтируют и выверяют на фундаменте (рис. 103). Горизонтальность фундаментных плит выверяют по их верхним обработанным поверхностям. Для этого плиты попарно выверяют на клиньях с помощью линейки 2 с уровнем 3. Отклонение от горизонтали допускается не более 0,3 мм на длине обработанной части плит и расстоянии между ними.
После выверки плит затягивают фундаментные болты, крепящие плиты, устанавливают на плиты станину и проверяют отвесом правильность ее установки по образующей цилиндрической втулки (см. рис. 102), а также прилегание подошвы станины к привалочным поверхностям плит (допускаются местные зазоры не более 0,3 мм). Затем окончательно затягивают фундаментные болты и заливают плиты цементным раствором.
Неправильный монтаж станины приводит к одностороннему износу втулки вала-эксцентрика, боковому износу дисков подпятников, эксцентрика, ненормальной работе гидрозатвора.
По окончании монтажа станины промывают резьбу опорного кольца от загрязненной смазки, проверяют действие пружинных масленок опорного кольца шприцем, целостность рукава уплотнения в пазу опорного кольца и затяжку пружин по размеру Я, который должен быть 680 мм для дробилок КМД и 688 — для дробилок КСД.
На упорную резьбу корпуса опорного кольца непосредственно перед вворачиванием в нее корпуса регулирующего кольца наносят пластичную смазку.
Приводной вал
Приводной вал (рис. 104). После разборки, расконсервации, тщательного контроля и устранения обнаруженных повреждений, полученных при транспортировании, приводной вал собирают и смазывают маслом все подвижные поверхности.
Рис. 103. Установка фундаментных плит: 1— фундаментная плита, 2—линейка, 3 — уровень (За …Зг положения уровня), 4— отвесы, 5 —струна; А, Б, Н — установочные размеры
При разборке бронзовые втулки, посаженные на скользящей посадке, обычно не демонтируют. Но если такой демонтаж был произведен, при обратной сборке следят за тем, чтобы не перепутать переднюю и заднюю втулки. Задняя втулка (установлена со стороны электродвигателя), кроме индивидуальной маркировки, отличается от передней неполным по длине пазом для распределения смазки.
После сборки приводного вала замеряют его осевой ход, который должен быть в пределах, указанных на чертеже. При необходимости регулируют его с помощью хомута 7, состоящего из двух полуколец. Перед посадкой вала в станину на его корпус 8 ставят футеровку 4.
Монтируют вал с установленным, но незатянутым конусным диском на переднем фланце (для дробилок с диаметром конуса 2200 мм). На фланце станины при заводской сборке выбивают цифру, обозначающую толщину набора прокладок, которая соответствует правильному осевому положению приводного вала.
Рис. 104. Монтаж приводного вала:
1 — шаблон, 2 — коническая шестерня, 3 — регулировочные прокладки, 4 — футеровка корпуса привода, 5 — маслосборник, 6—полумуфта, 7— хомут, 8 — корпус приводного вала, 9 — втулка приводного вала, 10 — риска
При монтаже приводного вала между средним фланцем его корпуса и фланцем патрубка станины оставляют зазор, примерно равный толщине прокладок. На данном этапе монтажа приводной вал окончательно не фиксируют, так как может потребоваться передвижка его при настройке зубчатого зацепления.
Шестерню 2 устанавливают до упора во фланец втулки приводного вала. Для контроля ее положения определяют расстояние от оси дробилки до начала среза шестерни с помощью шаблона 1 (табл. 24).
Таблица 24. Установочные размеры шестерни приводного вала
Дробилки | Размеры, мм | |||
Д | H | А | Е | |
КСД-1750 КМД-1750 | 530 | 72,5 | 872,43 | 342,43 |
КСД-2200 КМД-2200 | 640 | 120 | 1003,15 | 363,15 |
После монтажа приводного вала между средним фланцем корпуса приводного вала и патрубком станины устанавливают регулировочные прокладки.
Чтобы обеспечить правильную ориентацию смазочных канавок во втулках приводного вала, штифт, запрессованный в патрубке станины, должен войти в отверстие на фланце корпуса приводного вала.
Нижняя крышка станины
До монтажа вала-эксцентрика устанавливают нижнюю крышку станины (с прокладками и тремя нижними дисками) с помощью резьбовой штанги 1 (рис. 105), поставляемой с дробилкой. Предварительно промывают масляную ванну, цилиндрическую втулку и посадочные поверхности станины (после установки нижней крышки станины и дисков подпятника никакие промывки не допускаются).
Сначала в крышку 4 укладывают тщательно проверенные и выровненные прокладки 5 в объеме, указанном в паспорте машины, затем нижний диск 6 облегчением вверх (на нем выбито слово «вверх»). Штифты, запрессованные в крышке, должны попасть в отверстие в нижнем диске 6. Плоские поверхности дисков 7 и 3 обработаны с одинаковой чистотой и точностью, поэтому их устанавливают произвольно. Первым укладывают стальной диск 7, а затем бронзовый 3.
Рис. 105. Монтаж нижней крышки станины:
1 — резьбовая штанга, 2— станина, 3, 6, 7 — диски, 4 — крышка, 5 — прокладки для регулирования зубчатого зацепления
Перед подъемом крышки на ее фланец укладывают картонную прокладку. Поднятую крышку с дисками соединяют болтами с патрубком станины, монтажную штангу вывертывают и сразу перекрывают центральный патрубок станины пыленепроницаемым щитом, чтобы защитить его от загрязнения.
Вал-эксцентрик
Вал-эксцентрик перед монтажом промывают на отдельной площадке и собирают с чисто промытым верхним диском 8 (рис. 106) подпятника, следя за тем, чтобы палец 7 верхнего диска 8 попал в паз вала-эксцентрика 6. Транспортируют вал-эксцентрик на рабочую площадку за литые захваты на зубчатом колесе (см. рис. 101, в).
После этого диск 8 и эксцентрик 6 скрепляют поставляемым с дробилкой специальным приспособлением, состоящим из штанги, накладки и рым-болтов. При посадке эксцентрика на место следят за тем, чтобы зуб колеса без задиров вышел во впадину между зубьями шестерни, а не попал на зуб шестерни.
Рис. 106. Установка конического зацепления:
1 — зубчатое колесо с противовесом, 2 — внешние торцы конических шестерен, 3 — радиальный зазор, 4 — конусный диск, б — коническая шестерня, 6 — эксцентрик, 7 — палец верхнего диска, 8 — верхний диск
После установки эксцентрика регулируют зубчатое зацепление. Для этого между фланцем корпуса приводного вала и фланцем патрубка станины устанавливают прокладки и затягивают приводной вал двумя — четырьмя болтами. Затем проверяют правильность зубчатого зацепления. Зацепление правильно, если торцы 2 зубьев шестерен совмещены, а радиальный 3 и боковой зазоры у большего диаметра соответствуют приведенным в табл. 25.
Радиальный зазор проверяют по отпечатку на свинцовой пластинке, которую укладывают во впадину зуба шестерни 5 приводного вала с ее внешнего торца и прижимают колесом 1 эксцентрика.
Наличие бокового зазора обязательно, так как эксцентрик работает с большими зазорами в цилиндрической втулке и все время прижимается к ней одной стороной. Поэтому центр большой конической шестерни описывает окружность диаметром, равным зазору втулки стакана. Смещение центра вращения вызывает осложнения в зацеплениях и опорах приводного вала.
Установочные размеры зубчатой передачи таблица 25.
Размер дробилки по основанию дробящего конуса, мм | Зазор, мм | |
радиальный | боковой | |
600 и 900 | 3,1 | 0,8 |
1200 | 3.1 | 1.2 |
1750 и 2200 | 5…6 | 1.6 |
Замеряют зазоры в момент, когда противовес колеса находится непосредственно над ведущей шестерней. При отсутствии достаточного бокового зазора («мертвого хода») вставляют прокладки 5 (см. рис. 105) и приподнимают эксцентриковую шестерню.
Рис. 107. Монтаж опорной чаши:
1 — станина, 2 — уплотнительное кольцо, 3 — резиновый воротник, 4 — литой захват, 5 — защитное кольцо, 6 — сферический подпятник, 7 — корпус чаши, в—пробки (место установки отжимных болтов), 9 — шпонка, 10 — затяжной болт
Убедившись в правильности зубчатого зацепления, затягивают остальные болты приводного вала, связывающие корпус приводного вала со станиной, а также конусный диск 4 (см. рис. 106) на переднем фланце корпуса привода, последнее относится к дробилкам с диаметром конуса 2200 мм.
Параллельно с этими работами до монтажа дробящего конуса выполняют разводку смазки по дробилке. По окончании регулировки зацепления и затяжки корпуса приводного вала выверяют положение электродвигателя, при этом несоосность полумуфт приводного вала и электродвигателя должна быть не более 0,2 мм, а перекос — не более 0,5 на длине 1 м.
Опорная чаша
Опорная чаша (рис. 107). Предварительно промывают чашу, прочищают каналы для слива масла, подвода и отвода жидкости из уплотнения, устраняют обнаруженные повреждения и смазывают сферическую поверхность подпятника жидкой смазкой, а посадочные поверхности пластичной. Кольцо с резиновым воротником 3 перед монтажом опорной чаши снимают, отметив его положение. Для установки в дробилку опорную чашу стропуют за четыре литых захвата 4 на ее корпусе 7 (см. рис. 101,г).
Опорная чаша входит в станину 1 (см. рис. 107) плотно, по напряженной посадке, поэтому важно завести ее в посадочное отверстие без перекосов. Для этого на станине дробилок с диаметром конуса 2200 мм применяют отжимные болты, на которые сначала устанавливают чашу. Выворачивая болты, медленно опускают чашу. После захода чаши в посадочное отверстие отжимные болты удаляют, а отверстия закрывают пробками 8. Дальнейшую посадку чаши осуществляют с помощью затяжных болтов 10. При посадке чаши следят за тем, чтобы шпонка 9 станины совпала с лыской на корпусе чаши.
Рис. 108. Насосная установка для пылеуплотнения: 1 — электродвигатель, 2 — насосная установка, 3 — труба подвода жидкости, 4 — слив жидкости при длительных остановках, 5 — патрубок приводного вала, б — слив жидкости, 7 — воронка для контроля слива воды, 8 — бак — отстойник, 9 — перегородка
В дробилках с диаметром конуса 1750 мм конструктивно не предусмотрены затяжные и отжимные болты корпуса опорной чаши, поэтому ее осаживают в станину ударами кувалды через медную выколотку по наружной кольцевой полости. Плотность посадки чаши по горизонтальному стыку проверяют щупом. Допустимы местные зазоры до 0,1 мм суммарной длиной не более 1A окружности.
При монтаже чаши посадочные поверхности станины и чаши оберегают от попадания грязи. Промывать их не допускается ввиду того, что грязь стечет на эксцентрик, втулки и диски подпятника эксцентрика. Удаляют случайно попавшую грязь сухой полотняной тряпкой к периферийным частям опорной чаши. После монтажа чаши сферический подпятник сразу же перекрывают пыленепроницаемым щитом.
После — посадки чаши и затяжки болтов устанавливают кольцо ,с резиновым воротником 3 и подсоединяют трубопроводы подвода и отвода жидкости из гидравлического пылевого уплотнения. Далее проверяют работу гидравлического пылевого уплотнения. В качестве рабочей жидкости применяют воду или в случае работы дробилки при отрицательных температурах — отработанное машинное масло.
Воду подают от системы промышленного водопровода или через уравнительный бак, если напор в водопроводе непостоянный. Подача воды может производиться от специальной насосной установки 2 (рис. 108), если гидросистема работает на оборотной воде по замкнутому циклу.
Места подвода и спуска воды из пылеуплотнения расположены на диаметрально противоположных сторонах кольцевой выточки опорной чаши, что обеспечивает одинаковый уровень воды. Количество поступающей воды в пылеуплотнение регулируют так, чтобы она не выплескивалась через борт затвора. Скорость течения воды в кольцевой выточке должна быть не более 0,005 м/с. Для обеспечения данных условий рекомендуются насосные установки, технические характеристики которых приведены в табл. 26.
Таблица 26. Характеристика насосной установки
Дробилки | Диаметр труб, мм | Вместимость гидросистемы, л | Подача насоса, л/мин | Мощность двигателя насоса, кВт | |
нагнетательной | сливной | ||||
КСД-1200 КМД-1200 | 19 | 32 | 2000 | 20…25 | 0,5 |
КСД-1750 КМД-1750 | 25 | 37 | 2000 | 35…40 | 1 |
КСД-2200 КМД-2200 | 25 | 37 | 2000 | 45…50 | 1 |
Рис. 109. Монтаж подвижного конуса:
1 — эксцентрик, 2 — отражательное кольцо опорной чаши, 3 — воротник гидравлического затвора, 4 — литые захваты, 5 — распределительная тарелка, 6 — главный вал, 7 — бронь подвижного конуса; Л, В — точки, по которым должен скользить вал, соприкасаясь с конусной втулкой эксцентрика, С — зазор между воротником гидравлического затвора и отражательным кольцом
Вода, подаваемая в систему гидравлического уплотнения, должна быть чистой, поэтому при работе на оборотной воде применяют бак-отстойник 8 вместимостью 2000 л. Постоянство подачи воды контролируется визуально по сливной жидкости в воронку 7.
arxipedia.ru
Конусные дробилки |
Конусные дробилки
Измельчение материала в конусных дробилках происходит в результате защемления его кусков и раздавливания между неподвижным конусом и подвижным конусом. Подвижный конус непрерывно совершает круговые движения, удаляясь в одном месте и приближаясь в другом к внутренней поверхности неподвижного конуса. В момент сближения конусов материал раздавливается. В это время с противоположной стороны конусов образуется максимальный зазор, дробленый материал проваливается, а на его место поступают новые порции сырья.
Подвижный конус жестко закреплен на валу. Нижний конец вала входит в эксцентрически расположенное отверстие стакана, вращающегося от привода через пару конических шестерен. При вращении стакан увлекает за собой вал и конус, который при этом совершает вращательно-кача-ющиеся движения, производя дробление материалов. Дробленый продукт ссыпается на наклонный лоток и удаляется из дробилки или непосредственно осыпается под дробилку на транспортерную ленту либо другой вид транспорта.
Непрерывный процесс дробления в конусных дробилках, по сравнению с дробилками щековыми, в которых раздавливание материала происходит периодически, резко улучшает технико-экономические показатели конусной дробилки: повышает производительность, снижает удельный расход электроэнергии (на 1 м3 дробленого продукта).
Примерно так же снижается и металлоемкость конусной дробилки, т. е. вес конструктивных частей ее на единицу провал, подвешенный в центре траверсы . Траверса опирается на неподвижный конус и плотно связана с ним болтами. Неподвижный конус установлен на станину.
Нижний конец вала наклонно вставлен в эксцентричное отверстие стакана. Стакан приводится во вращение от приводного вала дробилки через две конические шестерни. При вращении стакана с эксцентрично расположенным отверстием, в которое вставлен конец вала, конус получает круговое качание. Стакан вращается в подшипнике корпуса дробилки.
Дробящие поверхности конусов дробилки облицованы броневыми плитами из высокомарганцовистой стали.
Исходный материал загружается сверху в полость между конусами, через промежутки в траверсе. Дробленый продукт при выходе из зазора между конусами попадает на наклонный лоток и удаляется из дробилки.
Конусная дробилка с консольным валом имеет станину, на которую устанавливаются все другие части дробилки. Подвижный конус жестко закреплен на дукции, получаемая делением веса дробилки на производительность.
К недостаткам конусных дробилок следует отнести сложность их конструкции, многочисленность деталей и пригодность для дробления только хрупких пород.
Для каждой конусной дробилки существует наивыгодное число колебаний вала (или качания конуса). Уменьшение этого числа снижает производительность дробилки, а увеличение приводит к большему, чем требуется, измельчению материала и повышенному расходу электроэнергии. Не менее важным фактором, влияющим на производительность дробилки, служит степень заполнения материалом ее рабочей емкости. Как недогрузка, так и перегрузка снижают ее производительность. Для ликвидации этого недостатка дробилку загружают равномерно питателем.
По своим конструктивным особенностям различают конусные дробилки: с подвешенным валом и с консольным валом. Принципиальное отличие этих двух типов дробилок не только в конструктивном решении их привода, но и в форме дробящих конусов.
Конусные дробилки с подвешенным валом отличаются высокой производительностью (до 1000 т/ч и более) и применяются они для грубого, иногда для среднего дробления. Дробилки с консольным валом менее производительны. Их применяют для среднего и мелкого дробления. Принципиальных же отличий в конструкциях дробилок разных марок, но одного типа нет и они во многом сходны между собой. Это позволяет ограничиться рассмотрением только одной марки дробилки каждого типа. Конусная дробилка с подвешенным валом состоит из станины, на которой располагаются все другие узлы дробилки.
Для защиты от пыли трущихся поверхностей в месте опирания конуса на сферический подпятник устанавливается пылеотбойное кольцо и устраивается гидравлический затвор в виде кольцевой камеры, через которую непрерывно проходит вода. Воду нужно подавать в систему непрерывно. Поступающая вода не должна содержать механических примесей.
Смазывают конусные дробилки принудительно. Масло к трущимся частям нагнетается насосом и непрерывно циркулирует, очищаясь при этом в фильтрах и охлаждаясь в холодильнике.
Чтобы смазка не вытекала из чаши сферического подпятника дробилки с консольным валом, к торцу чаши плотно крепят маслоотбойное кольцо. Признаком нарушения плотности кольца или засорения каналов, отводящих отработанное масло в отстойник, может служить появление масла в воде, выходящей из гидравлического затвора. Эти неисправности следует немедленно ликвидировать, так как конусная дробилка без обильной систематической смазки может быстро выйти из строя.
midas-beton.ru
Конусная дробилка — Дробильное оборудование
Конусные дробилки применяют для дробления прочных и особопрочных горных пород на различных стадиях дробления.
Главным параметром конусных дробилок является размер основания дробящего конуса. Конусные дробилки классифицируются по крупности дробления: крупного (ККД), среднего (КСД) и мелкого (КМД). Дробилки крупного дробления с шириной загрузочного отверстия 500…1500 мм предназначены для дробления кусков размером 400…1200 мм. Производительность соответственно 200… 2000 м3/ч. Такие дробилки для нерудных материалов применяют редко, поэтому в данной книге они не рассматриваются.
Для нерудных материалов применяют конусные дробилки среднего (КСД) и мелкого дробления (КМД). Дробилки КСД и КМД подразделяют на дробилки грубого (Гр) и тонкого (T) дробления и отличаются формой и размерами камеры дробления (табл. 6).
Технические характеристики конусных дробилок Гр(Т) Таблица 6.
Показатели | КСД-600 СМ-561А) | КСД-900 СМД-120) | КСД-1200 | КСД-1750 | КСД-2200 | КСД-3000 | КМД-1200 | КМД-1750 | КМД-2200 | КМД-3000 |
Диаметр основания дробящего конуса, мм | 600 | 900 | 1200 | 1750 | 2200 | 3000 | 1200 | 1750 | 2200 | 3000 |
Ширина приемной щели на открытой стороне, мм | 75 | 130 | 185 (125) | 250 (200) | 350(275) | 600 (475) | 100 (50) | 130 | 140 (100) | 220 (120) |
Диапазон регулирования ширины выходной щели, мм | 12…35 | 15…40 | 20…25 (10…25) | 25…60 (15…30) | 30.. 60 (15…30) | 50…80 (25…50) | 5…15 (3…12) | 9…20 (5…15) | 10…20 (5…15) | 15…25 (6…20) |
Размер наибольшего куска исходного материала, мм | 60 | 105 | 150 (100) | 200 (160) | 300 (250) | 500 (380) | 80 (40) | 100 | 100 (85) | 180 (100) |
Производительность на материале средней прочности, м3/ч | 12…40 | 30..,70 | 77…115 (42…95) | 170…320 (100.190) | 360…610 (180…360) | 700…1100 (425…850) | 45 (27) | 95…130 (85…110) | 220…260 (170…220) | 360…520 (320…440) |
Мощность главного привода, кВт | 30 | 55 | 75 | 160 | 250 | 500 | 75 | 160 | 250 | 500 |
Масса дробилки, τ | 5,0 | 12,5 | 22 | 55 | 100 | 250 . | 22 | 55 | 100 | 250 |
Габаритные размеры, мм: | ||||||||||
длина | 1800 | 2500 | 3500 | 4400 | 5500 | 7000 | 3500 | 4400 | 5500 | 7000 |
ширина | 1600 | 2000 | 2500 | 3400 | 4300 | 5500 | 2500 | 3400 | 4300 | 5500 |
высота | 1600 | 2400 | 3100 | 4400 | 5100 | 6500 | 3100 | 4400 | 5700 | 7100 |
arxipedia.ru
Конусные дробилки
Процесс изготовления некоторых материалов зачастую требует предварительного дробления составляющих. Для осуществления данной операции возникает необходимость использования специализированного оборудования. Из всего существующего оборудования наиболее функциональными являются конусные дробилки.
Такого рода оборудование широко используется для переработки руды, а также других материалов. Однако материалы, содержащие в своём составе глину в увлажнённом состоянии, или же плитняковую структуру, не подходят для обработки в конусных дробилках. Это обусловлено опасностью повреждения оборудование, а, следовательно, и возникновения необходимости проведения ремонтных работ, зачастую достаточно дорогостоящего устройства.
Устройство конусной дробилки
Для большей устойчивости конусные дробилки снабжены достаточно тяжёлой станиной. Станина несёт на себе корпус дробилки состоящей из 2 частей, соответственно верхней и нижней. Обе части корпуса имеют фланцы и закрепляются болтами. Фланцы являются достаточно важным элементом корпуса, именно поэтому они должны быть выполнены с высокой точностью, так же они служат для центровки обеих частей корпуса относительно станины.
Рабочая часть корпуса оснащается легированной сталью, при этом облицовка выполняется небольшими плитками, данная мера призвана упростить работы по восстановлению рабочей части дробилки. Загрузочная часть оборудования защищена обычной сталью. Фланец верхней части корпуса оснащён траверсой, которая служит для крепления вала подвижного конуса. Вся конструкция при этом имеет защитный кожух.
Конус, осуществляющий процесс дробления так же имеет защиту из легированной стали. В нижней же части корпуса конусных дробилок, расположен патрубок с эксцентриковой системой, которая выполнена в виде стакана с коническим колесом. Сам стакан при этом оснащён баббитовой наплавкой.
Таким образом, создаётся компенсирующая система, для поглощения побочных нагрузок. Подобный эффект обеспечен подшипниками скольжения, в качестве которых выступает соединение эксцентрикового стакана, втулки патрубка и подвижного вала на котором установлен конус.
Распределение веса узла эксцентрика обеспечено системой шайб, на которую собственно и опирается стакан. Для нормальной работы конусных дробилок, необходимо соотношение осей всех узлов согласно нормативной документации.
Принцип действия конусной дробилки
Сам процесс дробления осуществляется непрерывно в независимости от характера дробления (мелкое, среднее или крупное). При детальном сравнении конусных дробилок со щековым аналогом становится очевидным, что щебень в первом случае получается более качественный. Однако стоит заметить, что конструктивно конусные дробилки – оборудование гораздо сложнее, но при этом производительность его выше, при меньших энергозатратах.
Кроме того, конусные дробилки более универсальны и могут быть перенастроены под конкретные рабочие условия. Подобный результат достигается за счёт регулировки эксцентрика, а также рабочей камеры. При правильном использовании оборудования, а также своевременной его чистки и ТО (при этом наиболее часто необходимо заменить некоторые пластины защищающие рабочие части) оно прослужит достаточно длительный срок.
Конусные дробилки, при условии их правильной эксплуатации, за короткий период времени способны окупить вложенные в данное оборудование средства. Данное оборудование способно быстрыми темпами выдавать необходимый продукт, при этом функционируя беспрерывно.
promplace.ru
Добавить комментарий