Асфальтобетон плотность – ГОСТ 12801-84 Смеси асфальтобетонные дорожные и аэродромные, дегтебетонные дорожные, асфальтобетон и дегтебетон. Методы испытаний
Щебеночно-мастичный асфальтобетон (ЩМА): ГОСТ, свойства и характеристики
Щебеночно-мастичный асфальтобетон – это оптимально подобранный состав минеральных материалов, которые призваны обеспечить конструкции дорожного покрытия высокую водонепроницаемость, сдвигоустойчивость и повышенную шероховатость.
В чем особенность?
Такие асфальтобетонные смеси обладают особой структурой, благодаря которой укладка возможна тонкими слоями. Это позволяет снизить удельный расход материала. Цена сырья для приготовления такого асфальтобетона выше по сравнению с производством традиционного асфальтобетона, однако он не уступает ему в рентабельности.
Государственные стандарты и состав
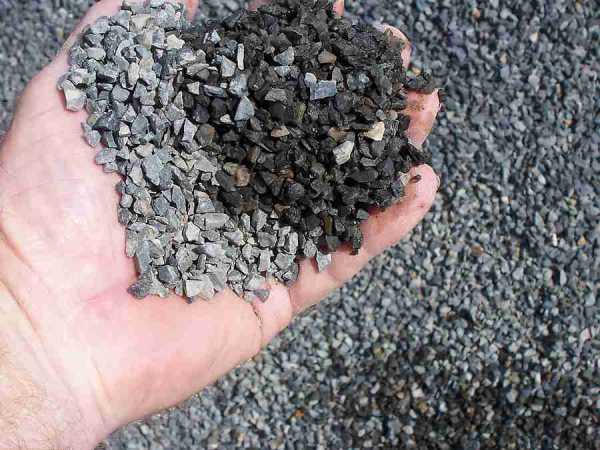
Щебеночно-мастичный асфальтобетон, который изготавливается по ГОСТ 31015-2002, на первый взгляд, можно было бы отнести к группе классических дорожных покрытий, созданных на базе нефти и битумных вяжущих. Однако это не так. Структурными особенностями и компонентным составом эта смесь выделяется среди конкурентов.
Основа материала формируется жестким каркасом из щебня, что и объясняет высокую устойчивость к пластическим деформациям. Внутри содержится большой объем битумного вяжущего, который занимает свободное пространство между заполнителями. Это сокращает остаточную пористость, которая составляет 1% или меньше. Что позволило получить долговечное покрытие, которое в процессе эксплуатации проявляет высокую устойчивость к климатическим и интенсивным транспортным воздействиям.
Основная область использования
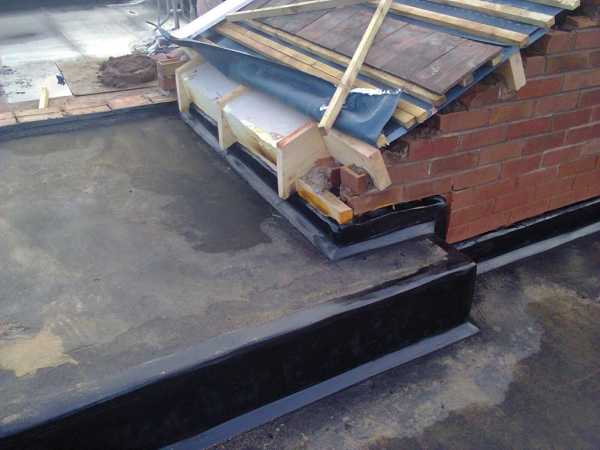
Автомобильные дороги (ГОСТ 31015-2002) обычно устраиваются с применением асфальтобетона. Одной из основных областей использования этого материала является еще и устройство верхних слоев:
- покрытий дорог;
- городских улиц;
- аэродромов;
- площадей.
Использовать состав могут еще и при капитальном ремонте верхних слоев покрытий. Применяется асфальтобетон и для создания долговечных и качественных площадей и площадок.
Основные свойства
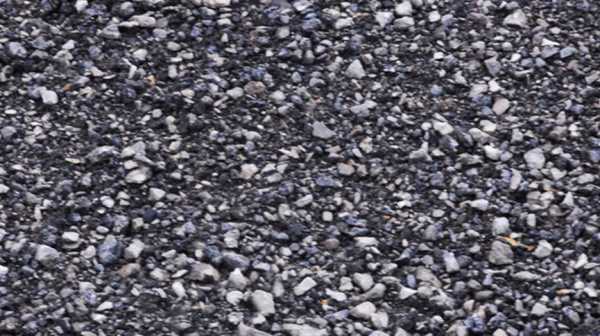
Щебеночно-мастичный асфальтобетон имеет в составе следующие ингредиенты:
- щебень;
- стабилизирующую добавку;
- битум;
- минеральный порошок.
1-й содержится в объеме от 70 до 80%. Что касается битума, его количество по отношению к общей массе может достигать предела в 7,5 %. Если проводить сравнение с обычными асфальтобетонными смесями, описываемая отличается высоким объемом нефтяного битума и щебня.
Для защиты от расслоения и сохранения однородной структуры асфальтобетонную смесь связывают стабилизирующими добавками в виде волокон. Это особенно актуально при осуществлении дорожных работ. В зависимости от того, заполнитель какой фракции используется в производстве, асфальтобетон можно систематизировать по составу.
Если перед вами материал с маркировкой ЩМА 10, это указывает на то, что размер зерен щебня не должен быть больше 10 мм. Наиболее распространенной маркой является асфальтобетон с маркировкой ЩМА 15. Здесь нормируемый размер зерен заполнителя составляет 15 мм. Щебеночно-мастичный асфальтобетон может быть представлен маркировкой ЩМА 20. В данном случае речь идет о составе с максимальным размером зерен до 20 мм.
Смесь вышеописанных марок рекомендована к использованию при изготовлении верхних слоев дорожных покрытий толщиной до 6 см. Такие составы используются на автомагистральных автомобильных дорогах, городских улицах всех категорий в 1 – 5 климатических зонах.
Совет специалиста
Когда дорожно-строительные работы ведутся для устройства аэродромных покрытий, коэффициент сцепления и прочность на сжатие должны быть увеличены на 25 %. Использование такого бетона на скоростных дорогах, которые подвергаются интенсивному движению, позволяет добиться множества преимуществ. Это особенно верно, если проводить сравнение с традиционным асфальтовым покрытием.
Дополнительные свойства
ЩМА, ГОСТ которого был упомянут выше, имеет высокую износостойкость, длительный срок эксплуатации и низкий показатель уровня шума при движении автотранспорта. Покрытие остается стабильным при механических воздействиях, кроме того, оно характеризуется повышенным коэффициентом сцепления шин с поверхностью дороги. Износостойкость при этом не зависит от климатических условий эксплуатации. Срок эксплуатации будет выше в три раза по сравнению с аналогичными покрытиями, используемыми с теми же целями.
Основные характеристики
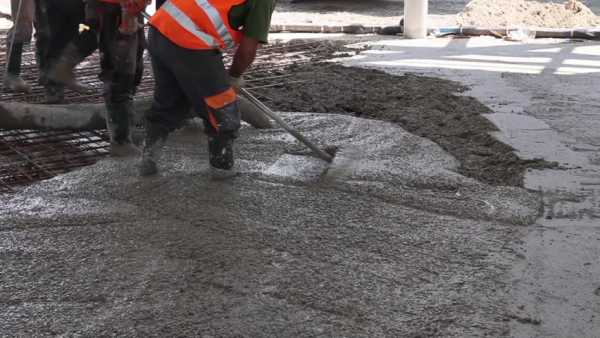
Щебеночно-мастичный асфальтобетон (ЩМА) испытывается по государственным стандартам 12801-98. Согласны им, существуют определенные параметры, которые подлежат изучению, среди них следует выделить:
- предел прочности при сжатии;
- сдвигоустойчивость;
- трещиностойкость.
Предел прочности при сжатии у ЩМА 15 составляет 9 МПа, что верно при температуре в 0 ˚С. Сдвигоустойчивость эквивалентна 0,93. Рассматривая ЩМА 15, вы можете обратить внимание еще и на трещиностойкость. Для этой марки она равна 4,3 МПа.
Истинная плотность этого материала составляет 2,56 т/м3. Нормированная толщина верхнего слоя покрытия – 0,05 м. По ГОСТу ЩМА обладает массой в 0,128 т/м2. Стоимость одного квадратного метра покрытия примерно равна 265 рублям.
Из чего изготавливают?
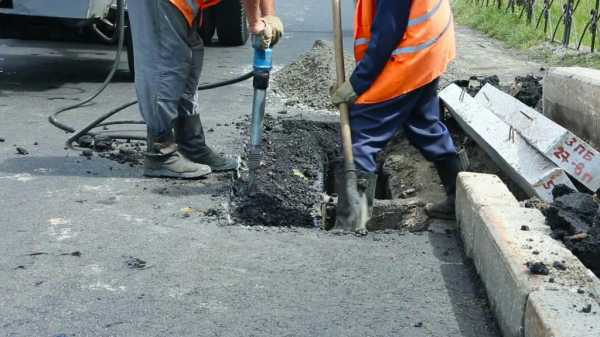
Технология асфальтобетона предусматривает определенные требования для используемых материалов, среди которых следует выделить:
- щебень;
- битумы;
- минеральный порошок;
- стабилизирующую составляющую смесь.
Что касается щебня, то его зерновой состав должен состоять из твердых горных пород. Допустимо использование дробленого материала из металлургических шлаков. Марка должна быть равна 1000 или выше. Форма зерна должна иметь кубовидный тип. По общей массе объем зерен пластинчатой и игольчатой формы не должен превышать 15%.
Морозостойкость щебня должна быть равна F50 или выше. По истираемости значение должно соответствовать марке И—1. Если вы задались вопросом о том, из чего делают асфальт, то должны знать, что в основе содержится еще и битум. Рекомендованы нефтяные битумы, которые соответствуют ГОСТ 22245–90. Использоваться могут и полимерно-битумные вяжущие. В последнем случае должно быть обеспечено требование к показателям стекания битума.
В состав могут не вводится волокнистые стабилизирующие добавки. Все используемые битумы должны иметь достаточное значения сцепления с щебнем. В ином случае необходимо ввести адгезионную присадку катионного типа. Если вы хотите знать, из чего делают асфальт, то вам должно быть известно, что в составе имеется еще и песок. Он должен быть взят из отсева дробления твердых горных пород. Марка песка должна быть равна 1000 или выше. Материал должен соответствовать ГОСТ 8736–93. Объем глинистых частиц в нем не должен быть больше 0,5%.
Минеральный порошок в составе
Дорожно-строительные работы осуществляются с использованием асфальтобетона, в котором есть минеральный порошок. Его характеристики регламентируются ГОСТ 16557-78. Его изготавливают методом дробления известковых горных пород или доломитных пород. Допустимо использование минерального порошка из отсева вулканических горных пород. Фракция частиц не должна быть больше 0,16 мм. Если в составе имеется большое количество битумного вяжущего, это непременно должно повлечь присутствие стабилизирующей добавки. Без этого компонента невозможно получить смесь с физико-механическими свойствами, которые прописаны стандартами.
Стабилизирующая составляющая смесь
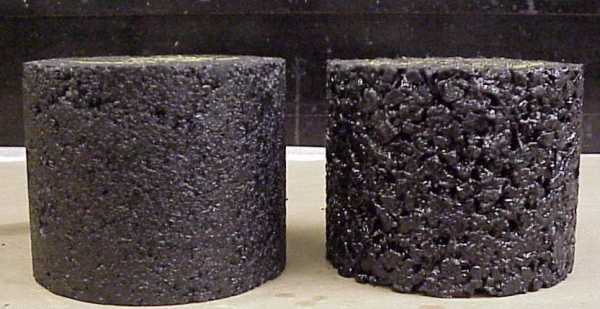
По ГОСТу автомобильные дороги должны укладываться с помощью асфальтобетона, который содержит стабилизирующую составляющую. Ее свойства и вид обладают огромным значением для повышения качества конечного материала, его транспортировки, приготовления и укладки. Добавки являются структурирующими волокнистыми. Они позволяют сохранять однородность и способствуют удержанию горячего битума на поверхности щебня. Это дает возможность исключить расслоение раствора при высоких температурах, которые свойственны процессу укладки.
Свойства и характеристики щебеночно-мастичного асфальтобетона предусматривают в составе наличие стабилизирующих смесей, а именно:
- резиновой крошки;
- полимерных волокон;
- термопластичных полимеров;
- акриловых нитей;
- волокон асбеста;
- минеральных компонентов;
- продуктов на основе кремниевой кислоты;
- целлюлозных волокон.
Благодаря тому, что себестоимость производства довольно низка, а в виде волокон используются целлюлоза и фибра, а также специальные гранулы на их основе, материал в течение долгого времени удерживает битум на поверхности покрытия и исключает расслаивание состава.
Характеристики в соответствии с государственными стандартами
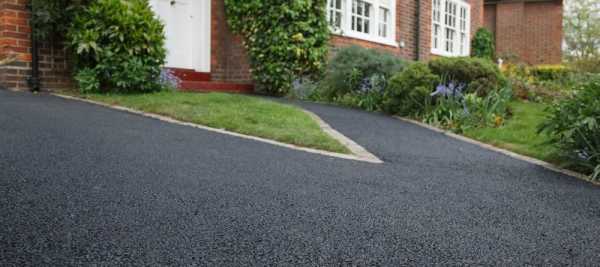
Горячие смеси должны быть устойчивы к расслаиванию, в том числе при хранении и транспортировке. Подобная устойчивость к отслоению обеспечивается стабилизирующими добавками, а оценку этого качества нужно осуществлять по ГОСТ 31015.
Показатель стекания не должен превышать 0,3 % по массе. Когда осуществляется подбор состава смеси, рекомендуется, чтобы показатель стекания вяжущего был равен пределу от 0,1 до 0,2 % по массе. Что касается цвета асфальта, то смесь должна иметь однородный блестящий черный цвет, ей должна быть свойственна однородность, которая оценивается по ГОСТ 12801. Вариация показателя не должно быть больше 0,18 % при температуре в 50 ˚С.
Технология устройства покрытия
Смеси асфальтобетонные и щебеночно-мастичный асфальтобетон должны укладываться в сухую погоду. Если работы ведутся весной, то температура окружающего воздуха не должна быть ниже + 5 ˚С. Осенью этот показатель составляет + 10 ˚С. Основание должно быть сухим и обладать положительной температурой.
В состав работ входят некоторые технологические операции. На первом их этапе осуществляются подготовительные работы. Далее ведется приемка асфальтобетонной смеси и ее выгрузка в бункер асфальтоукладчика, если применяется именно он. Может использоваться и другой механизм. Затем смесь укладывается асфальтоукладчиком и уплотняется катком.
Если работы ведутся с применением горячих асфальтобетонов, их доставляют на место проведения работ самосвалами с чистыми кузовами, которые имеют систему подогрева. Смесь накрывается водонепроницаемым тентом. Укладка должна вестись непрерывными темпами, ее необходимо согласовать с производительностью заводом. Темп работ регламентируется соответствующей документацией и прописывается в проекте производства работ.
Для укладки смеси следует использовать асфальтоукладчики с автоматической системой обеспечения поперечного уклона и ровности покрытия. Для уплотнения покрытий используются дорожные катки, масса которых достигает 18 т. При устройстве покрытий осуществляются подготовительные работы. Они предусматривают установку ограждений и дорожных знаков.
Перед укладкой слоя из горячего асфальтобетона нужно убедиться в ровности и качестве нижележащего покрытия. Основание следует очистить от пыли и грязи, обработав органическим вяжущим на основе битумной эмульсии. С этой целью можно использовать жидкий дорожный битум.
Укладка асфальтобетона ведется без остывших продольных стыков на ширину проезжей части. Количество одновременно работающих укладчиков должно быть назначено с учетом ширины уплотняющих рабочих органов. Шаг между асфальтоукладчиками, работающими одновременно по соседству, не должен быть выше 30 м. Для того чтобы получить ровную поверхность покрытия, необходимо обеспечить постоянную скорость и непрерывность укладки. Первая из упомянутых зависит от равномерности доставки смеси к асфальтоукладчику и обычно варьируется от 2 до 4 м в минуту.
Смесь должна выступать из кузова автомобиля во время укладки максимально равномерно. Для того чтобы добиться слоя постоянной толщины и нужной ровности, следует обеспечивать равномерное давление материала на плиту. В начале смены, когда производится возобновление укладки после перерыва, следует прогреть поперечный стык. Заглаживающая плита при этом устанавливается на ранее уложенное покрытие. Шнековая камера после постепенно наполняется смесью.
В заключение
Цвет асфальта регламентируется государственными стандартами. Но это – не единственная характеристика, на которую следует обращать внимание при оценке качества асфальтобетона. Если состав был изготовлен согласно правилам, то он будет способствовать снижению шума при движении транспорта, прослужит значительно больший срок, будет устойчив к образованию колеи.
fb.ru
Плотность асфальта. Состав асфальта, ГОСТ, марки, характеристики
В качестве одного из самых часто используемых дорожно-строительных материалов сегодня используется асфальт, ГОСТ которого предполагает необходимость соблюдения плотности и состава. На сегодняшний день известно несколько марок, разновидностей и типов данного материала. Основанием для классификации служат не только исходные компоненты, но и соотношение в составе их массовых долей. Подразделяется асфальт по категориям еще и по той причине, что составляющие могут иметь разную фракцию, что касается щебня и песка, а также степень очистки минерального порошка.
Состав
Состав асфальта предполагает наличие:
- гравия;
- щебня;
- песка;
- битума;
- минерального порошка.
Что касается щебня, то некоторые разновидности данного покрытия не предусматривают его использования. Однако щебень или гравий необходимы, если осуществляется асфальтирование территории с учетом сильных кратковременных нагрузок и высокого трафика на покрытие. Упомянутые материалы при этом выступают в роли каркасообразующего защитного элемента.
В качестве обязательного исходного сырья используется минеральный порошок, он содержится в составе любых разновидностей и марок асфальта. Массовая доля этого порошка определяется с учетом требований и задач к вязкости. Если использовать минеральный порошок в большом объеме, то материал получит способность гасить колебания мостовых конструкций, не покрываясь трещинами.
Как было упомянуто выше, песок используется в большинстве марок и типов асфальта. Его качество определяется степенью очистки и способом получения. Материал может быть добыт открытым способом, в этом случае он предусматривает необходимость тщательной очистки. Краеугольным камнем индустрии является битум. Это продукт переработки нефти.
Массовая доля битума в большинстве сортов асфальта не превышает 5%. Однако при необходимости асфальтирование территорий, которые имеют сложный рельеф, битум может применяться в объеме до 10% и больше. Это сырье придает плотность и упругость смеси после затвердевания. Готовый состав легко распределяется по площадке, ведь он обладает текучестью.
Плотность и основные характеристики природного асфальта
Плотность асфальта – это одна из первых характеристик, которая интересует профессионалов и частных застройщиков. Природная его разновидность представляет собой легкоплавкую твердую массу чёрного цвета. На изломе материал может иметь тусклый или блестящий цвет.
Плотность асфальта составляет 1,1 г/см³. Температура плавления может изменяться в пределах от 20 до 100 °С. В составе содержится масло в объеме от 25 до 40%, а также смолисто-асфальтеновое вещество, которое может содержаться в объеме от 60 до 75%. Что касается элементного состава в процентах то он выглядит следующим образом:
- C – 80—85.
- Н – 10—12.
- S – 0,1—10.
- О – 2—3.
Плотность асфальта вам уже известна, однако эта характеристика не является единственной, которая интересует потребителей. Среди прочих особенностей следует выделить способ образования из остатков или фракций нефти в результате испарения лёгких составляющих и окисления под влиянием гипергенеза.
Характеристики искусственного асфальта
Искусственный асфальт еще называется асфальтобетонной смесью. Он представляет собой уплотненный состав из минерального порошка, щебня, битума и песка. Встречается горячий асфальт, который укладывается методом уплотнения при воздействии температуры в 180 °С и больше. Если в процессе производства используется маловязкий битум, то укладка ведется при температуре в пределах от 40 до 80 °С. Если используется жидкий битум, то асфальт является холодным и уплотняется при температуре до -30 °С.
Основные марки асфальта и ГОСТ
Плотность асфальта крупнозернистого была упомянута выше, однако следует знать еще и о том, что процентное содержание ингредиентов в составе влияет на марки и типы асфальта. Сегодня общеприняты три разновидности, которые изготавливаются по ГОСТ 9128-2009. В этих стандартах можно узнать о возможности добавления присадок, которые повышают гидрофобность, морозостойкость, износоустойчивость и гибкость покрытия.
В составе асфальта марки 1 содержатся:
- отсев;
- песок;
- щебень;
- бетон;
- минеральный порошок.
К этому покрытию относятся плотные материалы, в которых содержание щебня может изменяться в пределах от 30 до 60%. Сюда следует отнести высокоплотные, щебеночные высокопористые и пористые асфальты. Асфальт, ГОСТ которого должен быть учтен при производстве, может изготавливаться под маркой 2. В составе данного материала содержатся:
- щебень;
- бетон;
- отсев дробления;
- песок;
- минеральный порошок.
К этой категории следует отнести высокопористые песчаные, пористые, а также плотные асфальты, в которых содержание щебня может изменяться от 30 до 50%, тогда как смесь из отсева дробления и песок может составить объем до 70%.
Плотность асфальта вам уже известна, однако необходимо знать ещё и о том, что существует марка асфальта 3, в ней содержатся:
- отсев дробления;
- песок минеральный;
- порошок битума.
В этом случае речь идет о смесях, щебня и гравия в которых может содержаться в пределах от 30 до 50%. Отсев дробления и песок содержатся в объеме от 30 до 70%.
Описание марок
Плотность асфальта (т/м3) составляет 1,1. Однако это не всё, что следует знать о свойствах. Например, асфальт марки 1 может быть высокопористым или плотным с высоким содержанием щебня. Областью использования данного покрытия выступает дорожное благоустройство и строительство. Что касается асфальта марки 2, то диапазон его плотности остается примерно таким же, но процентное содержание гравия и песка варьируется в широких пределах. Этот асфальт считается самым среднестатистическим. Применяется смесь для возведения автомобильных дорог, обустройства территорий, ремонта покрытий, а также формирования площадок и паркингов.
Заключение
Плотность асфальта (т/м3) составляет 1,1. Но этот параметр не является единственным, который следует знать. Например, стоит упомянуть еще и о месторождении асфальта, которое распространяется на территории бывшего СССР, острове Тринидад, Венесуэлы, Франции и Канады. Смешиваясь с минеральными составляющими, среди которых гравий и песок, материал превращается в мощную кору на поверхности нефтяных озёр. Такое покрытие распространено в районах выхода и неглубокого залегания к поверхности земли нефтеносных пород.
autogear.ru
Многощебенистый асфальтобетон повышенной плотности
6.37. Асфальтобетон повышенной плотности и шероховатости предназначается для устройства верхних слоев покрытий на автомобильных дорогах высоких категорий. Особенно целесообразно его использование в I-IIдорожно-климатических зонах, где верхний слой покрытия должен быть особенно водо- и морозостойким.
По структуре и составу такие асфальтобетоны занимают промежуточное положение между литыми асфальтобетонами и асфальтобетонами, регламентируемыми ГОСТ 9128-84. Покрытие имеет плотность, близкую к плотности покрытий из литого асфальтобетона, но выгодно отличается от них тем, что в процессе строительства не требуется специального оборудования для приготовления, транспортирования и укладки смеси.
Содержание щебня в асфальтобетонной смеси составляет 55-70%, что обеспечивает высокий коэффициент сцепления колеса автомобиля с поверхностью покрытия.
6.38. Для приготовления смесей применяют минеральные и вяжущие материалы, рекомендуемые ГОСТ 9128-84для асфальтобетонных смесей 1 марки, и пески мелкие и очень мелкие по ГОСТ 8736-85. Максимальная плотность асфальтобетона достигается при использовании песков с модулем крупности от 1,5 до 2,0. Наибольшая крупность зерен щебня не должна превышать 20 мм.
Минеральные порошки должны соответствовать требованиям ГОСТ 16557-78. Использование активированных минеральных порошков способствует повышению плотности асфальтобетона и снижению оптимального количества битума.
Зерновой состав минеральной части асфальтобетонов с целью обеспечить максимальную плотность асфальтобетона подбирается по принципу прерывистой гранулометрии.
6.39. При подборе состава смеси сначала определяют такое соотношение между песком и минеральным порошком, при котором пористость их смеси будет минимальной и которое сохранится в составе асфальтобетонной смеси. Количество битума в смеси подбирают таким образом, чтобы образцы, уплотненные комбинированным способом в соответствии с ГОСТ 12801-84, имели показатели физико-механических свойств, приведенные втабл. 14.
При таком подборе состава асфальтобетонных смесей типа А количество битума в них не превышает пределов, рекомендуемых ГОСТ 9128-84, несмотря на повышенное содержание минерального порошка.
Таблица 14
Показатель | Нормативное значение показателя |
Пористость минерального остова, % по объему | 13-16 |
Остаточная пористость, % по объему | |
Водонасыщение, % по объему, не более | 2 |
Предел прочности при сжатии, МПа (кгс/см2) при температуре: | |
20°С, не менее | 2,2 (22) |
50°С, не менее | 0,8 (8) |
0°С, не более | 7 (70) |
Коэффициент водостойкости при длительном водонасыщении, не менее | 0,95 |
Коэффициент заполнения пор битумом | 0,8-0,9 |
6.40. Образцы уплотняют либо комбинированным способом, либо статической нагрузкой 30 МПа через резиновые прокладки между смесью и вкладышем формы толщиной 4-5 мм.
Температура смеси при уплотнении образцов должна соответствовать ГОСТ 12801-84.
6.41. При устройстве верхнего слоя покрытия из многощебенистых асфальтобетонных смесей с повышенной плотностью последние укладывают на нижний слой из асфальтобетонов в соответствии с ГОСТ 9128-84или из других черных смесей, предназначенных для устройства нижних слоев покрытий.
Рекомендуемая толщина верхнего слоя покрытия – от 3,5 до 5,0 см – назначается по расчету.
При использовании в смеси щебня фракции 5-10 мм можно устраивать защитные слои минимальной толщины 1,5-2,0 см.
6.42. Технология устройства слоя покрытия изложена в разд. 5настоящего Пособия, а некоторые ее особенности приведены ниже.
Температура асфальтобетонных смесей в асфальтоукладчике перед укладкой в конструктивный слой должна быть не менее 140°С.
Особое внимание следует уделять устройству продольных и поперечных сопряжений, так как именно они в верхних слоях асфальтобетонных покрытий наиболее подвержены разрушающему воздействию воды. Смесь рекомендуется укладывать на всю ширину проезжей части широкозахватным асфальтоукладчиком или несколькими обычными укладчиками. Опережение одного укладчика относительно другого не должно превышать 30 м.
При устройстве продольных и поперечных сопряжений покрытия нельзя допускать местного накопления щебня, так как это приведет к образованию выбоин и неровностей. Не разрешается распределять по поверхности слоя щебень, оставшийся при ручной заделке продольных сопряжений.
Сопряжения должны быть особенно тщательно уплотнены. При правильном выполнении работ сопряжения визуально незаметны, а плотность самого асфальтобетона такая же, как и на остальных участках покрытия.
Для уплотнения смесей применяют как гладковальцовые катки массой 8-18 т, так и самоходные катки на пневматических шинах массой 16 т.
studfiles.net
Устройство асфальтобетонного покрытия технологическая карта
Определение удельного расхода смеси, кг/ м2.
Исходные данные:
толщина слоя в плотном теле h = 0,04 м;
средняя плотность асфальтобетона р. кг / м3
Плотность асфальтобетона в зависимости от вида смеси приведена в табл. 9
Таблица 9 ~~г^-—
Вид смеси | Плотность смеси, кг/м3 |
Крупнозернистая: | |
плотная | 2340 |
пористая | 2300 |
Мелкозернистая типа А | 2385 |
Б | 2370 |
Песчаная | 2280 |
Литая | 2460 |
На один квадратный метр требуется: ц = И р, кг/м 2; например: ц = 0, 04 2340 = 93,6 кг / м2.
На заданную площадь ( Э ) потребности О) на объекте определится: О = Э я т .
Например, О = 800-93,6 = 421200 кг = 421.2 т , где 800 м2-площадь участка.
Производительность асфальтоукладчика определяется по следующему выражению: Ра = V И Ь р I к , где {например, ДС — 54)
скорость укладки 2,5 м/мин;
Ь толщина слоя асфальтобетона — 0,04 м;
Ь ширина укладываемой полосы 3,75 м; р плотность м.з. асфальтобетона типа Б 2370 кг /м3;
Калькуляция затрат труда на работы по укладке асфальтобетонных смесей приведена в табл. 10
Таблица 10
№ | Обосно вание | Наименование и состав работ | Ед изм. | Объём работ (площадь карты) | Норма времени на ед. изм. чел. ч | Затраты труда на объём, чел. ч. | Состав звена |
1 | Укладка асфальтобетонной смеси врі | /чную. | |||||
ЕНиР | Укладка и разравни ванне а.б. смеси при толщине слоя 50 мм, уборка отходов Переходы рабочих. За вычетом Нпр на розлив вяжущего | 1м2 | 1 | 0,43 | 0,427 | Асфальте бетонщик! 4 разр.-1 3 разр.-З 2 разр.-2 1 разр.-1 | |
2 | Укладка асфальтобетонной смеси асфальтоукладчиком | ||||||
ЕНиР | Приём смеси, укладка, разравнивание, уплотнение смеси, Обработка краёв со смазкой битумом, проверка ровности | 100 м | 0,25 | 1,97 | 0,49 | Машинист 6 разр,-1 | |
3 | Укладка литой аа | »альтобетонной смеси в | ручную | ||||
ЕНир | Разравнивание смеси | 1т 1м3 1м3 !м3 1м3 1м3 | 1 3 10 12 25 | 0,69 0,69 0,43 0,41 0,32 | 0,69 1,71 4,3 4,92 5,25 | Асфальтобетоншики: 3 разр.-1 2 разр 3 |
Материал взял из книги Эксплуатация городских дорог (Н.В. Борисюк)
studik.net
Зачем уплотнять асфальтобетон выше минимальной нормы?
В прежние годы советские, а затем и российские дорожные подрядчики постоянно были озабочены проблемой обеспечения минимально требуемого нормативного коэффициента уплотнения (Ky) асфальтобетона в покрытии дороги. По действующему СНиП 3.06.03-85 степень или коэффициент уплотнения, выражаемый в России в долях 1,0, а в других странах в долях 100%, должен быть не ниже 0,99 или 99% для асфальтобетона из плотных смесей типов А и Б и 0,98 или 98% из плотных смесей типов В, Г и Д, а также для пористых и высокопористых асфальтобетонов, от объемного веса переформованных и уплотненных в лаборатории образцов. Такой объемный вес принимался за 1,0 или 100%.
Отмеченная озабоченность была обусловлена известной и всеми признаваемой технологической отсталостью отечественной дорожной отрасли, несовершенством собственной уплотняющий техники, невозможностью приобрести зарубежные, более эффективные дорожные катки.
В табл. 1 приведены те модели отечественных и зарубежных катков, которые были доступны большинству дорожников и которые использовались ими практически повсеместно в те годы на устройстве асфальтобетонных покрытий. Анализ их уплотняющей способности по современному критерию индекса контактных давлений и технологических возможностей качественно уплотнять асфальтобетон показывает их явную ущербность в функциональном плане.
Таблица 1
|
* Индекс контактных давлений является обобщенной функционально-технологической характеристикой катка, учитывающей весовую нагрузку или общую динамическую силу при вибрации и размеры (ширина, диаметр) каждого вальца.
** Оптимальный слой уплотнения щебенистого асфальтобетона для указанного индекса контактных давлений.
*** На завершающей стадии уплотнения, для которой и создавался ДУ-49Б.
И, конечно же, ожидать от такой техники более высокого качества уплотнения, чем минимально требуемое, было бы, по меньшей мере, наивно и несерьезно. Доказательств этому можно привести достаточно много. Стоит лишь указать, что по результатам двух массовых независимых обследований дорог в европейской части СССР, проведенных СоюздорНИИ, ГипродорНИИ и МАДИ в 60–70-е годы прошедшего столетия, средний срок службы их покрытий составлял примерно две трети от срока службы зарубежных дорог, а в Сибири он вообще часто не превышал 50–55%.
Из-за значительного недоуплотнения покрытий, т.е. наличия фактического брака, доходящего в 80-е годы 20 века до 25–30% даже в таком технически передовом и развитом центре, как Ленинград (табл. 2), они достаточно быстро разрушались, требуя частых и существенных затрат на свои ремонты.
Таблица 2
|
Сегодня в дорожной отрасли России уже другие времена, сами дорожники становятся другими, более опытными и современными в технологическом плане. Их оснащение эффективной техникой, в том числе уплотняющей, постепенно приближается к оснащению зарубежных коллег, они осваивают передовые технологические приемы выполнения асфальтобетонных работ. И главное, свое право на очередной объект они должны завоевывать в конкурентной борьбе, предусматривающей особое отношение к качеству работ и материалов.
Поэтому реализация минимально требуемого Ky асфальтобетона для многих подрядчиков стала не просто трудным обязательством, а фактически даже заурядным делом. Ряд из них добивается хороших, а иногда и очень высоких результатов по качеству уплотнения асфальтобетонных покрытий.
И, тем не менее, даже среди успешных в этом плане подрядчиков порой возникают сомнения и суждения о том, что СНиП формально требует Ky не ниже установленной планки, так зачем стремиться реально перекрывать эту планку, тем более, что логика конкурсных торгов поощряет снижение стоимости контрактных работ и нередко в ущерб их качеству. Объект ведь все равно примут в эксплуатацию, если соблюдены хотя бы минимальные требования СНиП.
Такого сорта дорожники продолжают мыслить и руководствоваться в своей практической деятельности прежними устремлениями и заботами – достичь минимально требуемого качества и все. Хотя имеющиеся потенциальные возможности современных технологий и машин (укладчики, катки) позволяют добиваться значительно более высоких показателей уплотнения асфальтобетона в покрытии, доходящих до 1,01–1,02 (101–102%), а в некоторых случаях и до 1,03 (103%).
Правда, у тех же дорожников появляются вопросы, а иногда и возражения против таких высоких значений коэффициента уплотнения. Мол, что это за показатель, превышающий 100%, и нужно ли, а может быть и вредно, достигать такой высокой плотности?
Очевидно, все эти вопросы, сомнения и возражения требуют определенного их обсуждения и некоторых пояснений. Хотя они давно, неоднократно и профессионально уже освещались российскими практиками и учеными, в том числе такими крупными специалистами в области асфальтобетонной технологии, как Н. Н. Иванов, Н. В. Горелышев, И. В. Королев, Л. Б. Гезенцвей и другие, внесшие существенный и неоценимый вклад в становление и развитие дорожной отрасли.
Высокие значения Ky, превышающие 1,0 или 100%, свидетельствуют, во-первых, о несовершенстве российского метода и средств уплотнения переформованного образца асфальтобетона в лаборатории, во-вторых, об имеющемся запасе или о потенциальных возможностях самого асфальтобетона деформироваться в покрытии более значительно, чем в лабораторной форме (жестком стакане), и, в-третьих, о высокой эффективности используемых сегодня технологических приемов и современных уплотняющих средств в виде разных типов катков.
К сожалению, российские дорожники до сих пор (уже примерно 50 лет, если не больше) для переформовки и для подбора состава асфальтобетона в лаборатории используют обычный, правда, легко доступный гидравлический пресс и жесткий металлический стакан (форму), которые в случае работы со щебенистыми смесями дополняются простейшим вибростолом (амплитуда колебаний 0,35–0,40 мм, частота 50 Гц) для комбинированного уплотнения сначала на вибростоле (3 мин), а затем на прессе при давлении 200 кгс/см2 (3 мин). Если смеси малощебенистые и песчаные, понадобится только пресс, но при давлении 400 кгс/см2. До утверждения в 1970 г действующих сегодня стандартов, приборов и норм уплотнения асфальтобетона достаточно было одного пресса с давлением 300 кгс/см2 при минимально требуемой степени уплотнения дорожного покрытия 0,97 из любых типов смесей.
Общеизвестно из механики грунтов, бетонов и других строительных материалов, что наиболее эффективно и быстро такие материалы деформируются и уплотняются в том случае, когда к ним прикладываются циклические усилия с поочередно повторяющимися нагружениями и разгрузками, как это делают катки на устройстве покрытия или зарубежные лабораторные приборы для уплотнения грунта и асфальтобетона (приборы Проктора, стандартного уплотнения грунта СоюздорНИИ, Маршалла, гиратор и др.), и когда частицам уплотняемого материала предоставляется некоторая свобода или возможность вертикального и горизонтального смещения относительного друг друга.
В жесткой лабораторной форме при непрерывно действующем статическом давлении пресса вместо чередующихся циклов нагрузка-разгрузка частицы асфальтобетонной смеси такой свободы практически не имеют. После некоторой начальной осадки материал образца попадает в зажатое вертикальное положение, хотя его возможности к уменьшению пористости и дальнейшему уплотнению еще не исчерпаны. В итоге объемный вес такого образца оказывается меньше, чем мог бы быть при его уплотнении по методу Маршалла или в гираторе. Поэтому за счет уменьшенного значения знаменателя (объемный вес несколько недоуплотненного образца в лаборатории) и получаются у образцов асфальтобетона из покрытия значения Ky, превышающие 1,0 или 100%.
И ничего в этом страшного или тревожащего, на первый взгляд, нет. Однако с помощью такого уже исчерпавшего себя метода и оборудования ведется подбор и проверка проектируемых составов асфальтобетонных смесей для будущих покрытий дорог, и не исключено, что эти составы будут не соответствовать наилучшим вариантам гранулометрии и физико-механических свойств.
Как известно, с повышением плотности асфальтобетона пористость его минерального остова снижается, и поэтому количество битума для заполнения пор тоже понижается. При подборе гранулометрического состава смеси в лаборатории определяют оптимальный расход битума по максимуму получаемой прочности отформованных образцов на сжатие. Если в лаборатории при использовании существующей методологии с прессом образец оказывается недоуплотненным по сравнению с плотностью в покрытии (вариант, когда Ky>1,0 или >100%), значит оптимум битума для покрытия установлен неверно.
Эксперименты с песчаными смесями показали, что при их уплотнении на прессе (400 кгс/см2) оптимум битума для Ky = 1,0 составил 7,6%, а при уплотнении на гираторе (20 оборотов) получен Ky около 1,02–1,03 и оптимум битума понизился до 6,7%. Хорошая экономия битума (в 1,13–1,14 раза), правда, на песчаном асфальтобетоне. Кроме того, образцы после гиратора оказались прочнее (R20, R50) образцов из-под пресса в 1,11–1,17 раза.
В табл. 3 представлены итоги обработки и осреднения результатов уплотнения различных щебенистых смесей известными лабораторными методами, выполненного в свое время Н. В. Горелышевым и К. Я. Лобзовой, причем за 100% приняты результаты уплотнения таких смесей стандартным для России комбинированным методом (вибрация + статическое сжатие).
Таблица 3
|
Из данных этой таблицы следует, что и комбинированный метод, и чисто статическое сжатие исчерпали все свои возможности к увеличению плотности лабораторного образца и в этом отношении оба они отстали уже не только от зарубежных методов и приборов, но и от катков, работающих на дороге и реализующих Ky>1,0.
Рис. 1. Результат лабораторного уплотнения асфальтобетона 0/11 В65 в приборе Маршалла при различной температуре (проф. Эльк Рихтер, технический институт г. Эрфурта, Германия) |
К тому же у этих отечественных методов и приборов нет возможности варьировать работу уплотнения и оценивать уплотняемость составов смесей, как это делается в методе Маршалла за счет изменения количества ударов трамбовки (рис. 1) или количества оборотов гиратора во вращательном уплотнителе (рис. 2).
Рис. 2. Гироскопический уплотнитель асфальтобетона фирмы Troxler, созданный для реализации федеральной программы SHRP SuperPave (США)
Можно только увеличивать давление пресса, как это произошло в 1970 г., когда 300 кгс/см2 повысили до 400 кгс/см2 и нормативный коэффициент уплотнения Ky(300) = 0,97 подняли до Ky(400) = 0,99 для щебенистых смесей. Любопытно, что в результате таких изменений прежняя норма Ky=0,97 теперь соответствует всего лишь Ky=0,95, что наглядно объясняет низкий уровень качества уплотнения покрытий в 60–70-е годы прошлого века и незначительный срок их службы.
Однако та же табл. 3 показывает нецелесообразность и даже бессмысленность увеличения статического давления свыше 400 кгс/см2 для щебенистых смесей. Во-первых, прирост плотности незначителен, и, во-вторых, и это самое неприятное, с ростом давления сжатия увеличивается дробление щебня в образце, что ведет к искажению всех его показателей.
Теперь вполне очевидно, что дорожная отрасль России фактически подошла к моменту, когда действующему лабораторному методу и его оборудованию оценки качества подбора состава в лаборатории и уплотнения асфальтобетона в покрытии необходимо дать отставку, заменив их более подходящими и современными. Но какими?
Проще всего, не мудрствуя лукаво и не изобретая велосипед, можно было бы перейти на широко применяемый в большинстве стран мира, накопивший огромный опыт своего использования, достаточно доступный и, пожалуй, самый дешевый метод трамбования по Брюсу Маршаллу (незамысловатое оборудование несложно изготовить в любой механической мастерской, в том числе дорожной).
Правда, к наиболее современным все-таки следует отнести метод вращательного уплотнения асфальтобетонного образца на гираторе.
Гирационный уплотнитель лучше и ближе всего моделирует физику и механику процесса деформирования и, соответственно, уплотнения асфальтобетона статическими и вибрационными вальцами катков в слоях покрытия на дороге, и потому он более перспективный. Но в то же время и самый дорогой. И сейчас, очевидно, пока не всем российским дорожникам доступный, как, например, прибор и метод Маршалла.
Вообще в этом плане не следует исключать и перехода на новые принципы оценки качества уплотнения асфальтобетона на дороге, взяв за основу (100%) так называемую «теоретическую плотность», легче и проще определяемую в лабораторных условиях.
В США, к примеру, действует стандарт ASTM D 2041, который рекомендует (не требует и не обязывает, а рекомендует наравне с другими) использовать в качестве показателя степени уплотнения отношение плотности асфальтобетона из покрытия к его истинной («теоретической») плотности. Последняя представляет из себя отношение общей массы минеральных материалов и битума к их объему, легко находимому по закону Архимеда. Фактически «теоретическая плотность» по Д. Райсу (J. Rice) есть плотность асфальтобетона с нулевой пористостью, т.е. плотность двухфазной системы. Поэтому новый Ky асфальтобетонных покрытий, найденный через такую «теоретическую плотность», будет наиболее объективным и не зависящим от особенностей метода или конструкции лабораторного прибора определения той плотности, которую принимают за 100%.
Кстати, всю подобную лабораторную и расчетную процедуру российские дорожные службы давно освоили, определяя остаточную пористость асфальтобетона через показатели средней и истинной его плотности. Ничего не следует объяснять, никого не нужно учить. Осталось только начать движение в сторону внедрения нового Ky.
При переходе на такой принцип оценки качества уплотнения (по остаточной пористости) было бы удобно ввести региональные нормы этого качества, что давно и неоднократно предлагали некоторые дорожные специалисты, понимающие и видящие различия в эксплуатации и поведении асфальтобетонных покрытий, например, в сыром и мягком по климату Северо-Западном или суровом и сухом Сибирском регионах.
Однако этот переход потребует серьезной и большой работы по разработке, обоснованию и практической проверке норм на качество уплотнения асфальтобетона. Следует заметить, что переход не исключит необходимости иметь метод и лабораторное оборудование для подбора наиболее оптимального и эффективного состава асфальтобетона по критериям прочности, сдвигоустойчивости и усталостной долговечности.
Но все это вполне решаемо, о чем свидетельствует опыт дорожников ряда стран, в том числе соседней Финляндии, где качество уплотнения асфальтобетона нормируется по остаточной пористости, а подбор составов асфальтобетона выполняется с использованием гирационного лабораторного уплотнителя (формование тестовых образцов с определением уплотняемости подобранного состава) и проверкой отобранного состава испытательным колесом на образование колеи (оценка сдвигоустойчивости и усталостной долговечности).
Финские нормативы очень жестко и скрупулезно регламентируют методологию и результат подбора гранулометрического состава асфальтобетона для покрытий. Для качества уплотнения эти нормы тоже не кажутся более демократичными и свободными. Во всяком случае, если судить по наличию вилки требуемой средней остаточной пористости 1–4% (при условии, что единичные значения не превысят 5%) для верхних и нижних слоев покрытий дорог I и II категорий. Если эту остаточную пористость обратить в новый Ky, то норма на его минимальное и максимальное значения составит узкую вилку – 96–99% от истинной или «теоретической» плотности. Нужно ли ограничивать максимум Ky?
Российскому дорожнику, понимающему цену каждого 1% (или 0,01) плотности и привыкшему делать все для достижения более высоких ее значений, пока трудно сразу ощутить и осмыслить, что здесь хорошо, а что плохо.
Во всяком случае, концепция финских нормативов (хорошо только то, что попадает в вилку требуемых значений Ky) отличается от концепции российских и ряда зарубежных стран (все хорошо то, что не ниже заданного минимального уровня Ky) и позволяет осуществлять на дороге предельно возможное уплотнение асфальтобетона, превращающее его в материал высокого качества или класса.
Слабое или даже с минимальной нормой уплотнение, как правило, сводит на нет все технологические приемы, направленные на повышение качества и свойств асфальтобетона – использование высокопрочных и более качественных исходных материалов, как например, габбродиабазовый щебень с ухтинским или модифицированным полимерами битумом, тщательный подбор оптимального гранулометрического состава смеси, введение различного рода добавок, увеличение времени перемешивания смеси на АБЗ и др.). Такое низкокачественное уплотнение покрытия ведет к сокращению срока его службы и к росту затрат на его ремонты.
Наилучшим решением следует считать достижение предельно возможной плотности сразу во время устройства покрытия на дороге (но как заставить или простимулировать подрядчика?!), что позволит сформировать оптимальную структуру асфальтобетона с его более высокими прочностными и деформативными свойствами и исключит нежелательную стадию или период покрытия в недостаточно уплотненном состоянии, что раньше допускалось, практиковалось и не только в России. Продолжительность такого вредного периода прямо пропорциональна вязкости битума в асфальтобетоне и поэтому может быть нежелательно затяжной.
Теоретическим пределом такого состояния может служить так называемая максимальная, или истинная («теоретическая»), плотность, выше которой асфальтобетон не уплотнить, но с 0,5–1,5% остаточной пористости для не очень жарких регионов России, подобных Северо-Западному, для которых крайне важна малая пористость уплотненного асфальтобетона и низкая поверхностная водопроницаемость покрытия.
Практическим же пределом может быть та максимальная плотность, дальнейшее повышение которой вызовет резкое увеличение дробимости щебня, превышающее известные 5–6% после обычной укатки покрытия катками. Иногда состояние асфальтобетона с увеличенной дробимостью щебня называют переуплотнением, и его можно зафиксировать по снижению его прочностных показателей, несмотря на некоторое повышение плотности.
По многочисленным экспериментальным данным российских и зарубежных исследований установлено, что увеличение коэффициента уплотнения щебенистого асфальтобетона сверх минимальной нормы на 1% (или на 0,01, если этот коэффициент в долях 1,0) влечет за собой или устойчиво обеспечивает:
- рост прочности на сжатие при +50°C и +20°С в среднем соответственно на 9 и 13%;
- рост прочности на растяжение при изгибе на 8,5%;
- повышение предельной деформации растяжения при изгибе на 21–22%;
- снижение остаточной пористости примерно в 1,15 раза;
- снижение оптимального содержания битума до 0,5% из реального его расхода;
- рост сдвиговой и усталостной прочности примерно в 1,3–1,5 раза.
Влияние качества уплотнения асфальтобетонного покрытия на его усталостную и сдвиговую прочность достаточно убедительно показывают следующие данные, заимствованные из опубликованных графиков упомянутого уже проф. Э. Рихтера (табл. 4).
Таблица 4
|
В некоторых странах допускаемой считается колея глубиной 10 мм, в других – 15 или 20 мм. Если минимально требуемый по нормам коэффициент уплотнения асфальтобетона составляет, к примеру, 98% от максимальной плотности по Маршаллу, то подрядчик, доведя плотность до 100%, увеличит количество проездов испытательного колеса в лаборатории до образования предельно допустимой колеи (10, 15 или 20 мм), а соответственно и срок службы покрытия почти в 3 раза или около этого. Разве будет возражать заказчик? Напротив, следующий контракт он постарается, очевидно, передать именно этому подрядчику.
Как показал проф. Н. В. Горелышев, свойства асфальтобетона можно улучшать и другими мерами помимо уже упомянутых выше – добавлять резину, латекс, ПАВ, использовать активированные материалы, входящие в его состав. Каждая из этих мер достаточно эффективно улучшает ряд одних и не затрагивает или минимально изменяет другие свойства асфальтобетона. Сравнение результатов влияния таких мер на шесть показателей свойств асфальтобетона с влиянием высококачественного (предельного) уплотнения подтверждает высокую эффективность и конкурентоспособность именно этой простой и достаточно дешевой технологической операции по отношению к другим более сложным и дорогим мерам, перечисленным в табл. 5.
Таблица 5
|
Из изложенного вытекает логически ясный ответ на вопрос, сформулированный в заголовке этой публикации. Во всяком случае, в заключение можно обоснованно утверждать, что выполнять сегодня уплотнение асфальтобетонного покрытия на дороге только до минимально требуемых показателей качества – большой дорожный и экономический грех.
library.stroit.ru
Смеси асфальтобетонные горячие: особенности и виды
Асфальтобетон готовится из специального состава с правильными пропорциями специальных компонентов: песка, минерального порошка, щебня разных размеров, а также определенного битума, предназначенного для дорог. Смеси асфальтобетонные используются для обустройства основы и покрытия проезжей части почти в любых условиях. Можно рассмотреть подробнее эти материалы.
Смеси асфальтобетонные разделяют на горячие и холодные по принципу укладки. Первые являются наиболее известными на сегодняшний день и активно используемыми. Их укладка производится при температуре 140-170 градусов Цельсия. Готовая асфальтобетонная смесь горячая доставляется в специальной технике. Она сберегает температуру состава. Когда укладка завершается, производится уплотнение посредством асфальтных катков. После того как состав застынет, получается покрытие, обладающее высоким качеством.
Приготовление смесей осуществляется с использованием вязких битумов. Смесь следует использовать сразу же после приготовления, ей нельзя остывать. При укладке температура асфальта должна быть 120 градусов и более. Такая технология применяется для любых работ и почти во всех широтах. Существуют незначительные особенности. Верхние слои покрытий укладываются с обязательным использованием щебней, фракционность которых составляет 20-40 миллиметров, что оказывает влияние на общую стоимость работ. Горячие смеси асфальтобетонные являются самыми выносливыми на данный момент, чего удается достичь благодаря применению битумов. У такого метода имеется еще одно очень важное достоинство – открытие движения по обработанному участку возможно сразу же после того, как смесь остынет до температуры окружающей среды, то есть на это уходит всего несколько часов. Этого периода хватает для того, чтобы смесь успела пройти формировочную фазу, после чего она полностью готова к эксплуатации.
Если смеси асфальтобетонные выбраны в качестве материала для произведения ремонтных работ на дорожном покрытии, то их состав необходимо выбрать максимально приближенным к составу, подвергаемому ремонту. При глубине дефекта до пяти сантиметров производится укладка в один слой, а при большем размере выбоин следует использовать пару пластов. Поверхности малых площадей требуется уплотнять посредством пневматического оборудования, а более обширные – с использованием виброкатка.
Разные типы асфальтобетонных смесей используются для обустройства аэродромных и дорожных покрытий, гидротехнических сооружений, полов и плоских кровель. Покупка таких материалов должна производиться на предприятиях, работающих со строгим соблюдением всех технологических особенностей их изготовления, а стоимость будет оптимальной. Понятно, что мелкозернистая асфальтобетонная смесь будет стоить дороже, так как она представляет собой более качественный продукт, предназначенный для обустройства очень гладких поверхностей. А вообще, стоимость такого строительного материала зависит от множества факторов, среди которых весьма важными являются качества составляющих, оборудование и технологии, используемые при работе, а также ряд иных факторов.
fb.ru
Добавить комментарий