Термообработка втулки: Закалка втулки. Термообработка втулки ★★★
Термическая обработка ✔ стали ✔ металлов ✔ виды ✔ свойства.
Что такое термообработка и зачем она нужна?
Термическая обработка (термообработка, ТО) — процесс тепловой обработки изделий из металлов и сплавов с целью изменения их структуры и свойств в заданном направлении, заключающийся в нагреве с заданной скоростью до определенной температуры, выдержке в течение определённого времени и последующем охлаждении с заданной скоростью до более низкой температуры.
Задача термообработки — путем нагрева и охлаждения вызвать необратимое изменение свойств вследствие необратимого изменения структуры. Термообработка является одним из важнейших этапов технологического процесса производства металлических изделий. Это одна из самых ответственных и, несмотря на кажущуюся простоту, одна из самых сложных и браконосных операций при изготовлении металлической продукции.
Термообработку применяют как промежуточную операцию для улучшения технологических свойств (обрабатываемости давлением, резанием и др. ) и как окончательную операцию для придания металлу или сплаву такого комплекса механических (а в ряде случаев и физико-химических свойств), который обеспечивает необходимые эксплуатационные характеристики изделия.
Без термообработки невозможно обеспечить достижение надлежащих эксплуатационных характеристик — достаточно сказать, что стандартная для большинства инструментов термообработка (закалка с низким отпуском) повышает твердость и прочность изделий в 3-4 раза!
Еще сложнее обстоит дело с износостойкостью: даже детали, термообработанные по разным режимам на одинаковую твердость и прочность, могут различаться по износостойкости в 1,5-3 раза из-за различий в микроструктуре (по этой причине для ответственных деталей в чертежах оговариваются требования не только к механическим свойствам, но и к микроструктуре).
По указанным причинам термообработка является важнейшим процессом при изготовлении ответственных металлических изделий.
Основные типы термообработки
Термическая обработка подразделяется на три основных типа: собственно термическую (ТО), химико-термическую (ХТО) и деформационно-термическую.
- Собственно термическая обработка предусматривает только температурно-временное воздействие на металл или сплав.
- В том случае, когда при термообработке целенаправленно изменяется химический состав поверхностных слоев металла (сплава), то такая обработка называется химико-термической.
- А если наряду с термическим производится еще и деформационное воздействие, приводящее к в изменению структуры, то такая обработка называется деформационно-термической (её виды: термомеханическая — ТМО, механотермическая — МТО и др.). На рис. 1 приведена краткая классификационная схема основных видов термической обработки металлов и сплавов.
Виды и особенности собственно термической обработки
Собственно термическая обработка включает в себя следующие основные виды:
- Отжиг 1-го рода
- Отжиг 2-го рода
- Закалку с полиморфным превращением
- Закалку без полиморфного превращения
- Отпуск
- Старение
Их используют как для сталей, так и для цветных металлов и сплавов. Каждый из этих видов термообработки подразделяют на разновидности, специфические для различных сплавов.
Особенности отжига I рода
Отжиг I рода — нагрев до определённой температуры металла или сплава, находящегося в нестабильном состоянии в результате предшествовавшей обработки, с целью приведения его в более стабильное состояние — например, для гомогенизации, снятия внутренних напряжений, рекристаллизации.
Основные его подвиды: гомогенизирующий отжиг, релаксационный отжиг (он же — отжиг для снятия внутренних напряжений), дорекристаллизационный отжиг, рекристаллизационный отжиг.
В ООО «Технопарк Импульс» из указанных подвидов применяется главным образом релаксационный отжиг I рода с целью снятия напряжений после электросварки и после некоторых операций механической обработки (шлифовки, полировки) — этот вид отжига.
Особенности отжига II рода
Отжиг II рода (или фазовая перекристаллизация) — нагрев выше температуры полиморфного превращения с последующим непрерывным (неизотермическим) или ступенчатым (изотермическим) охлаждением для получения стабильного структурного состояния сплава.
Обязательным условием неизотермического отжига является достаточно медленное охлаждение, тогда как при изотермическом отжиге это условие необязательно.
Напротив, в ряде случаев рекомендовано максимально быстрое охлаждение металла до температуры изотермической выдержки (например, такой вид отжига, как патентирование, предусматривает максимально быстрое охлаждение до температуры, при которой скорость полиморфного превращения максимальна, с последующей изотермической выдержкой при данной температуре).
Разновидностью полного неизотермического отжига II рода является нормализация (охлаждение на спокойном воздухе). В ООО «Технопарк Импульс» для ответственных изделий из доэвтектоидных сталей в качестве предварительной термообработки (перед последующей закалкой) применяется преимущественно изотермический отжиг (либо нормализация с последующим высоким отпуском, которая приводит к получению почти такой же структуры), а для ответственных изделий из заэвтектоидных сталей — сфероидизирующий отжиг.
Для менее ответственных изделий из доэвтектоидных сталей применяется преимущественно неизотермический отжиг (преимущественно с целью улучшения обрабатываемости при последующей механической обработке).
Особенности закалки с полиморфным превращением
Закалка с полиморфным превращением — нагрев выше температуры поли¬морфного превращения с последующим достаточно быстрым охлаждением для получения структурно-неустойчивого состояния (в ряде случаев — фиксации устойчивого высокотемпературного состояния).
Закалка с полиморфным превращением применяется для подавляющего большинства марок стали. В результате закалки происходят т.н. мартенситное и/или бейнитное превращения.
Мартенситное превращение (МП) — полиморфное превращение, при котором структурный переход высокотемпературной фазы с гранецентрированной кубической (ГЦК) решеткой (аустенита) в низкотемпературную фазу с объемноцентрированной кубической (ОЦК) решёткой (мартенсит) происходит путём их упорядоченного перемещения, причем относительные смещения соседних атомов малы по сравнению с межатомным расстоянием.
Мартенситное превращение протекает в определённом интервале температур, зависящем преимущественно от состава стали или сплава (температура начала мартенситного превращения обозначается как МН, а температура конца мартенситного превращения — как МК).
Бейнитное (промежуточное) превращение (БП) — полиморфное превращение, протекающее выше температуры начала мартенситного превращения МН, при котором изменение взаимного расположения атомов кристалла из ГЦК-фазы в ОЦК-фазу (бейнит) происходит посредством преобразования сдвига.
Бейнит, при сопоставимых с мартенситом твердости и прочности, обладает гораздо более высокой ударной вязкостью, поэтому для многих изделий, где требуется сочетание высоких прочности и пластичности, получение данной структуры является предпочтительным.
До недавнего времени о мартенситном и бейнитном превращениях говорили только применительно к сталям, однако в последние десятилетия обнаружено существование мартенситного превращения в некоторых сплавах на основе титана, никеля и др.
Виды закалки с полиморфным превращением
В промышленности применяются следующие виды закалки с полиморфным превращением:
- Закалка с непрерывным охлаждением в одной среде (воде, водных растворах полимеров либо неорганических солей, в масле).
Это самый простой и распространённый вид закалки, но он часто сопряжен либо с получением пониженных механических свойств (как правило, при закалке в масле или растворах полимеров), либо с повышенными значениями закалочных деформаций и риском образования закалочных трещин (как правило, при закалке в воде и водных растворах неорганических солей).По этой причине в ООО «Технопарк Импульс», как правило, применяется только непрерывная закалка в масле и реже — в растворах полимеров, причем преимущественно для изделий небольшого сечения.
- Прерывистая закалка (закалка в двух средах) с быстрым охлаждением (в воде) до температур выше МН и последующим более медленным охлаждением (в масле или на воздухе) в интервале МН — МК.
По этой причине в ООО «Технопарк Импульс» прерывистая закалка (через воду в масло) как правило, применяется только для изделий сравнительно простой формы, причём время выдержки в каждой из сред высчитывается для каждого изделия индивидуально и использованием специализированной программы. - Закалка с самоотпуском заключается в том, что изделие погружается в закалочную среду на ограниченное время с таким расчётом, чтобы температура поверхности была существенно ниже МН, а температура сердцевины — выше МН, за счёт чего после извлечения изделия из закалочного бака произошло выравнивание температуры по сечению изделия, приводящее к самоотпуску поверхностных слоёв изделия.
Данный способ закалки резко снижает закалочные напряжения и тем самым уменьшает значения закалочных деформаций и риск образования закалочных трещин. Главную сложность представляет собой точный подбор времени выдержки в каждой из сред (особенно для изделий переменного сечения).
По этой причине в ООО «Технопарк Импульс» закалка с самоотпуском (с охлаждением в растворе полимера) как правило, применяется только для изделий сравнительно простой формы, причём время выдержки в каждой из сред высчитывается для каждого изделия индивидуально и использованием специализированной программы, а температура самоотпуска контролируется пирометром, и в случае превышения заданной температуры изделие повторно погружается в закалочный бак (при этом закалка через воду в масло преимущественно применяется для изделий среднего размера, а закалка с самоотпуском — для крупногабаритных изделий). - Закалка купанием отличается от закалки с самоотпуском тем, что изделие погружается в закалочную среду на ограниченное время и затем выносится на воздух для выравнивания температуры по сечению не один раз, а неоднократно. Главную сложность представляет собой точный подбор времени выдержки в каждой из сред (особенно для изделий переменного сечения).
- Ступенчатая закалка с охлаждением в горячей среде с температурой немного выше МН (как правило, расплаве селитры либо щелочи) с кратковременной (во избежание бейнитного превращения аустенита) выдержкой для выравнивания температуры по сечению и последующим охлаждением на воздухе.
Данный способ закалки обеспечивает минимизацию закалочных деформаций и уменьшение внутренних напряжений почти до нуля, но применяется в ООО «Технопарк Импульс» только для изделий небольшого размера либо из сталей высокой прокаливаемости, поскольку скорость охлаждения в расплаве селитры не выше, чем в масле.
- Изотермическая закалка проводится по той же схеме, что и ступенчатая — с единственным различием, что выдержка в горячей среде проводится значительно дольше для обеспечения бейнитного превращения аустенита.
- Q-M-B закалка (двухступенчатая мартенситно-бейнитная) проводится по той же схеме, что и изотермическая — с тем отличием, что охлаждение производится в горячей среде с температурой на 10.
..90 оС ниже МН с целью образования в структуре изделия 15…50 % мартенсита, а затем переносится в горячую среду с температурой немного выше МН для обеспечения бейнитного превращения остаточного аустенита.
Во многих случаях данная структура изделия является оптимальной, однако ввиду технической сложности (необходимости наличия двух закалочных ванн с разной температурой) данный способ закалки применяется только для самых ответственных изделий.
- Q-n-P закалка (закалка с перераспределением углерода) проводится по той же схеме, что и Q-M-B закалка — с тем отличием, что охлаждение производится в горячей среде с температурой на 80…120 оС ниже МН с целью образования в структуре изделия 75…80 % мартенсита.
Затем процесс переносится в отпускную печь с температурой немного выше МН для обеспечения перераспределения углерода (из мартенсита в остаточный аустенит) и стабилизации остаточного аустенита и выдерживается в течение непродолжительного времени (5…30 минут).
Важным преимуществом перед Q-M-B закалкой является возможность применения вместо расплавленной селитры горячего масла, а также существенное сокращение длительности производственного цикла.Перераспределение углерода при выдержке в отпускной печи обеспечивается только для кремнистых сталей, поэтому в ООО «Технопарк Импульс» Q-n-P закалка применяется ограниченно (только для изделий из сталей 30ХГСА, 6ХС и т.п. марок).
- Закалка с обработкой холодом (криогенная обработка) заключается в том, что после охлаждения стали до комнатной температуры производится ее дополнительное охлаждение до температур ниже 0 °С (по возможности — ниже МК).
Данный способ термообработки применяется для высокоуглеродистых и/или высоколегированных сталей, у которых точка МК лежит значительно ниже нуля, с целью максимально полного превращения остаточного аустенита.В ООО «Технопарк Импульс» закалка с обработкой холодом (в жидком азоте либо смеси спирта с твердой углекислотой) применяется ограниченно (только для изделий из инструментальных сталей типа ХВГ и ШХ15, а также для особо ответственных цементированных изделий).
Различия между закалкой и отжигом
Принципиальное различие между закалкой и отжигом заключается в том, что для фиксации структурно-неустойчивого состояния охлаждение при закалке должно осуществляться со скоростью больше критической.
Критическая скорость закалки — минимальная скорость охлаждения, при которой подавляются диффузионные превращения, и аустенит превращается в мартенсит. Критическая скорость закалки зависит прежде всего от химического состава сплава и, в определенной степени, от температуры закалки.
Для некоторых высоколегированных сталей (например, быстрорежущих или цементированных) критическая скорость столь мала, что закалка протекает даже при охлаждении на спокойном воздухе — и в этом случае процесс именуется не нормализацией (которая является разновидностью отжига), а воздушной закалкой.
Отпуск в термообработке: особенности и виды
Отпуск — нагрев закаленного (с полиморфным превращением) сплава до температуры не выше точки полиморфного превращения для получения более термически стабильного состояния.
После закалки сталь приобретает структуру, состоящую из мартенсита и остаточного аустенита (в ряде случаев — также бейнита), которые являются неравновесными фазами и при последующем нагреве претерпевают превращения. Кроме того, в закаленных заэвтектоидных сталях присутствует вторичный цементит, который не испытывает превращений.
В термообработке выделяют три вида отпуска.
Низкий отпуск
Так называется процесс нагрева закаленной стали до 150 — 350 °С, при котором происходит выделение углерода из мартенсита (образование мартенсита отпуска), образование карбидной фазы (ε-карбида и/или цементита), превращение остаточного аустенита в нижний бейнит и частичное снятие внутренних напряжений.
Данный вид отпуска применяется для изделий, от которых требуется сохранение высокой твёрдости и прочности (в ООО «Технопарк Импульс» он применяется главным образом для пик и бойков).
Средний отпуск
Это процесс нагрева закаленной стали до 350 — 500 °С, в результате которого происходит распад мартенсита на феррито-цементитную смесь (троостит отпуска) и более глубокое снятие внутренних напряжений.
Данный вид отпуска применяется для изделий, от которых требуется сохранение высокой прочности и упругости при наличии умеренной пластичности (в ООО «Технопарк Импульс» он применяется главным образом для пальцев, стяжек и т. п. крепежа с классом прочности 10.9 и 12.9).
Высокий отпуск
Этот процесс подразумевает нагрев закаленной стали до 500 — 700 °С, который сопровождается распадом мартенсита на феррито-цементитную смесь (сорбит отпуска), дисперсионным твердением сталей, практичеки полным снятием внутренних напряжений.
Данный вид отпуска применяется для изделий, от которых требуется наличие высокой пластичности и ударной вязкости при сохранении сравнительно высокой прочности (в ООО «Технопарк Импульс» он применяется главным образом для втулок, гильз и крепежа с классом прочности 8.8 и 9.8).
Особенности закалки без полиморфного превращения
Закалка без полиморфного превращения — нагрев до температур, вызывающих структурные изменения (чаще всего для растворения избыточной фазы) с последующим быстрым охлаждением для получения структурно-неустойчивого состояния — пересыщенного твердого раствора.
Закалка без полиморфного превращения применяется преимущественно для сплавов цветных металлов (алюминиевых, медных, никелевых, титановых и др. ) и лишь для немногих марок стали (преимущественно аустенитных — нержавеющих хромоникелевых типа Х18Н8 и износостойких высокомарганцевых типа 110Г13). В ООО «Технопарк Импульс» он применяется главным образом изделий из нержавеющих сталей типа Х18Н8, Х18Н10Т и т.п., а также изделий из медных и алюминиевых сплавов.
Старение в термообработке: что это и для чего?
Старение — нагрев или длительная выдержка при комнатной температуре — т.н. естественное старение, вызывающий превращения в закаленном без полиморфного превращения сплаве с целью либо упрочнения сплавов (за счёт дисперсионного твердения), либо разупрочнения (за счёт приближения сплава к более равновесному состоянию.
В ООО «Технопарк Импульс» такой способ применяется главным образом для изделий из медных и алюминиевых сплавов.
Что такое химико-термическая обработка?
Химико-термическая обработка (ХТО) заключается в сочетании термического и химического воздействия с целью изменения химического состава, структуры и свойств поверхностного слоя изделия.
Она включает диффузионное насыщение неметаллами (углеродом, азотом, бором, серой, кремнием и кислородом), диффузионное насыщение металлами (диффузионная металлизация — алюминием, хромом, бериллием, титаном, цинком, медью и др.), диффузионное удаление примесей (углерода, кислорода, водорода).
Диффузионное насыщение классифицируется по насыщающему элементу — углероду (цементация), азоту (азотирование), бору (борирование) и т.п. В ряде случаев применяется одновременное насыщение несколькими элементами (например, хромоалитирование — насыщение хромом и алюминием, цианирование и нитроцементация — насыщение углеродом и азотом). ХТО может применяться как окончательная или как предварительная операция перед последующей упрочняющей термической обработкой.
Как правило, скорость диффузии неметаллов существенно выше, чем металлов, поэтому в тех случаях, когда требуется получение достаточно толстых диффузионных слоёв, обычно используется насыщение неметаллами. По этой причине В ООО «Технопарк Импульс» применяются, главным образом, наиболее распространенные из методов ХТО — цементация, нитроцементация, азотирование и карбонитрация. Данные виды ХТО существенно повышают твердость, износостойкость и задиростойкость изделий.
Деформационно-термическая обработка: особенности и виды
Разные виды деформационно-термической обработки разделяются в за-висимости от характера фазовых превращений и способа деформации, причем существенное значение имеет, до или после деформации происходит превращение, а также выше или ниже температуры рекристаллизации производилась деформация.
Если фазовое превращение происходит до деформации, такой вид обработки именуется механотермической обработкой (МТО). Одним из наиболее распространённых видов МТО является холодное волочение проволоки после патентирования. В ООО «Технопарк Импульс» из методов МТО применяется преимущественно алмазное выглаживание.
Если же превращение происходит во время или после деформации, такой вид обработки именуется термомеханической обработкой (ТМО). В зависимости от температуры деформации, различают высокотемпературную ТМО (ВТМО), при которой деформация производится выше температуры полиморфного превращения, и низкотемпературную ТМО (НТМО).
При этом деформация производится ниже температуры полиморфного превращения, но выше температуры мартенситного превращения. В ООО «Технопарк Импульс» ТМО не применяется, поэтому нет смысла останавливаться на нем более подробно.
Вы можете задать специалистам компании Технопарк «Импульс» любой интересующий вас вопрос
Термообработка изделий
Дополнительные услуги: | Термическая обработка изделийТермическая обработка (термообработка) стали, цветных металлов — процесс изменения структуры стали, цветных металлов, сплавов при нагревании и последующем охлаждении с определенной скоростью. Термическая обработка (термообработка) приводит к существенным изменениям свойств стали, цветных металлов, сплавов. Виды термической обработки сталиОтжигОтжиг — термическая обработка (термообработка) металла, при которой производится нагревание металла, а затем медленное охлаждение. Эта термообработка (т. е. отжиг) бывает разных видов (вид отжига зависит от температуры нагрева, скорости охлаждения металла). ЗакалкаЗакалка — термическая обработка (термообработка) стали, сплавов, основанная на перекристаллизации стали (сплавов) при нагреве до температуры выше критической; после достаточной выдержки при критической температуре для завершения термической обработки следует быстрое охлаждение. Закаленная сталь (сплав) имеет неравновесную структуру, поэтому применим другой вид термообработки — отпуск. ОтпускОтпуск — термическая обработка (термообработка) стали, сплавов, проводимая после закалки для уменьшения или снятия остаточных напряжений в стали и сплавах, повышающая вязкость, уменьшающая твердость и хрупкость металла. НормализацияНормализация — термическая обработка (термообработка), схожая с отжигом. Различия этих термообработок (нормализации и отжига) состоит в том, что при нормализации сталь охлаждается на воздухе (при отжиге — в печи). Нагрев заготовкиНагрев заготовки — ответственная операция. От правильности ее проведения зависят качество изделия, производительность труда. Необходимо знать, что в процессе нагрева металл меняет свою структуру, свойства и характеристику поверхностного слоя и в результате от взаимодействия металла с воздухом атмосферы, и на поверхности образуется окалина, толщина слоя окалины зависит от температуры и продолжительности нагрева, химического состава металла. Стали окисляются наиболее интенсивно при нагреве больше 900°С, при нагреве в 1000°С окисляемость увеличивается в 2 раза, а при 1200°С — в 5 раз. Хромоникелевые стали называют жаростойкими потому, что они практически не окисляются. Легированные стали образуют плотный, но не толстый слой окалины, который защищает металл от дальнейшего окисления и не растрескивается при ковке. Углеродистые стали при нагреве теряют углерод с поверхностного слоя в 2-4 мм. Это грозит металлу уменьшением прочности, твердости стали и ухудшается закаливание. Особенно пагубно обезуглероживание для поковок небольших размеров с последующей закалкой. Заготовки из углеродистой стали с сечением до 100 мм можно быстро нагревать и потому их кладут холодными, без предварительного прогрева, в печь, где температура 1300°С. Во избежание появлений трещин высоколегированные и высокоуглеродистые стали необходимо нагревать медленно. При перегреве металл приобретает крупнозернистую структуру и его пластичность снижается. Поэтому необходимо обращаться к диаграмме «железо-углерод», где определены температуры для начала и конца ковки. Однако перегрев заготовки можно при необходимости исправить методом термической обработки, но на это требуется дополнительное время и энергия. ПережогПережог — неисправимый брак. При ковке изделий из низкоуглеродистых сталей требуется меньше число нагревов, чем при ковке подобного изделия из высокоуглеродистой или легированной стали. При нагреве металла требуется следить за температурой нагрева, временем нагрева и температурой конца нагрева. При увеличении времени нагрева — слой окалины растет, а при интенсивном, быстром нагреве могут появиться трещины. Известно из опыта, что на древесном угле заготовка 10-20 мм в диаметре нагревается до ковочной температуры за 3-4 минуты, а заготовки диаметром 40-50 мм прогревают 15-25 минут, отслеживая цвет каления. Химико-термическая обработкаХимико-термическая обработка (ХТО) стали — совокупность операций термической обработки с насыщением поверхности изделия различными элементами (углерод, азот, алюминий, кремний, хром и др. Поверхностное насыщение стали металлами (хром, алюминий, кремний и др.), образующими с железом твердые растворы замещения, более энергоемко и длительнее, чем насыщение азотом и углеродом, образующими с железом твердые растворы внедрения. При этом диффузия элементов легче протекает в решетке альфа-железо, чем в более плотноупакованной решетке гамма-железо. Химико-термическая обработка повышает твердость, износостойкость, кавитационную, коррозионную стойкость. Химико-термическая обработка, создавая на поверхности изделий благоприятные остаточные напряжения сжатия, увеличивает надежность, долговечность. Цементация сталиЦементация стали — химико-термическая обработка поверхностным насыщением малоуглеродистой (С<0,2%) или легированных сталей при температурах 900…950°С — твердым (цементация твердым карбюризатором), а при 850…900°С — газообразным (газовая цементация) углеродом с последующей закалкой и отпуском. Детали, предназначенные для цементации, сначала очищают. Поверхности не подлежащие науглероживанию, покрывают специальными предохранительными противоцементными обмазками. 1-ый состав простейшей обмазки: огнеупорная глина с добавлением 10% асбестового порошка, вода. Смесь разводят до консистенции густой сметаны и наносят на нужные участки поверхности изделия. После высыхания обмазки можно производить дальнейшую цементацию изделия. 2-ой состав применяемой обмазки: каолин — 25%, тальк — 50%: вода — 25%. Разводят эту смесь жидким стеклом или силикатным клеем. Цементацию делают после полного высыхания обмазки. Вещества, которые входят в состав обмазки, называют карбюризаторами. Они бывают твердые, жидкие и газообразные. В условиях домашней небольшой мастерской удобнее осуществлять цементацию с помощью пасты. Это цементация в твердом карбюризаторе. В состав пасты входят: сажа — 55%, кальцинированная сода — 30%, щавелевокислый натрий — 15%, вода для образования сметанообразной массы. Пасту наносят на нужные участки изделия, дают высохнуть. Затем изделие помещают в печь, выдерживая при температуре 900-920°С в течение 2-2,5 часов. При использовании такой пасты цементация обеспечивает толщину науглероженного слоя 0,7-0,8 мм. Жидкостная цементация также возможна в небольшой мастерской при наличии печи-ванной, в которой и происходит науглероживание инструментов и других изделий. В состав жидкости входят: сода — 75-85%, 10-15% хлористого натрия, 6-10% карбида кремния. Печь-ванну наполняют этим составом и погружают изделие или инструмент. Процесс протекает при температуре 850-860°С в течение 1,5-2 часов; толщина науглероженного слоя достигает при этом 0,3-0,4 мм. Газовую цементацию производят в смеси раскаленных газов, содержащих метан, окись углерода в специальных камерах при температуре 900-950°С и только в производственных условиях. Азотирование сталиАзотирование стали — химико-термическая обработка поверхностным насыщением стали азотом путем длительной выдержки ее при нагреве до б00…650°С в атмосфере аммиака NН3. Азотированные стали обладают очень высокой твердостью (азот образует различные соединения с железом, алюминием, хромом и другими элементами, обладающие большей твердостью, чем карбиды). Азотированные стали обладают повышенной сопротивляемостью коррозии в таких средах, как атмосфера, вода, пар. Азотированные стали сохраняют высокую твердость, в отличие от цементованных, до сравнительно высоких температур (500…520°С). Азотированные изделия не коробятся при охлаждении, так как температура азотирования ниже, чем цементации. Азотирование сталей широко применяют в машиностроении для повышения твердости, износостойкости, предела выносливости и коррозионной стойкости ответственных деталей, например, зубчатых колес, валов, гильз цилиндров. Нитроцементация (цианирование) сталиНитроцементация (цианирование) стали — химико-термическая обработка с одновременным поверхностным насыщением изделий азотом и углеродом при повышенных температурах с последующими закалкой и отпуском для повышения износо- и коррозионной устойчивости, а также усталостной прочности. Нитроцементация может проводиться в газовой среде при температуре 840..860°С — нитроцианирование, в жидкой среде — при температуре 820…950°С — жидкостное цианирование в расплавленных солях, содержащих группу NaCN. Нитроцементация эффективна для инструментальных (в частности, быстрорежущих) сталей; она используется для деталей сложной конфигурации, склонных к короблению. Однако, поскольку этот процесс связан с использованием токсичных цианистых солей, он не нашел широкого распространения. Борирование сталиБорирование стали — химико-термическая обработка насыщением поверхностных слоев стальных изделий бором при температурах 900…950°С. Цинкование (Zn), алюминирование (Аl), хромирование (Сr), силицирование (Si) сталейЦинкование (Zn), алюминирование (Аl), хромирование (Сr), силицирование (Si) сталей выполняются аналогично цементации с целью придания изделиям из стали некоторых ценных свойств: жаростойкости, износостойкости, коррозионной устойчивости. В настоящее время все большее распространение получают процессы многокомпонентного диффузионного насыщения Термомеханическая обработка (ТМО) сталиТермомеханическая обработка (ТМО) стали — совокупность операций термической обработки с пластической деформацией, которая проводится либо выше критических точек (ВТМО), либо при температуре переохлажденного (500… 700°С) аустенита (НТМО). 270 МПа). Формирование структуры стали при ТМО происходит в условиях повышенной плотности и оптимального распределения дислокаций. Окончательными операциями ТМО являются немедленная закалка во избежании развития рекристаллизации и низкотемпературный (Т=100…300 °С) отпуск. Термомеханическая обработка с последующими закалкой и отпуском позволяют получить очень высокую прочность ( s= 2200…3000 МПа) при хорошей пластичности (d = 6…8%, y= 50…60%) и вязкости. В практических целях большее распространение получила ВТМО, обеспечивающая наряду с высокой прочностью хорошее сопротивление усталости, высокую работу распространения трещин, а также сниженные критическую температуру хрупкости, чувствительность к концентраторам напряжений и необратимую отпускную хрупкость. ВТМО осуществляется в цехах прокатного производства на металлургических заводах, например, при упрочнении прутков для штанг, рессорных полос, труб и пружин. Отпуск сталиОтпуск стали смягчает действие закалки, уменьшает или снимает остаточные напряжения, повышает вязкость, уменьшает твердость и хрупкость стали. Отпуск производится путем нагрева деталей, закаленных на мартенсит до температуры ниже критической. При этом в зависимости от температуры нагрева могут быть получены состояния мартенсита, тростита или сорбита отпуска. Эти состояния несколько отличаются от соответственных состояний закалки по структуре и свойствам: при закалке цементит (в троостите и сорбите) получается в форме удлиненных пластинок, как в пластинчатом перлите. А при отпуске он получается зернистым, или точечным, как в зернистом перлите. Преимуществом точечной структуры является более благоприятное сочетание прочности и пластичности. При одинаковом химическом составе и одинаковой твердости сталь с точечной структурой имеет значительно более высокое относительное сужение, ударную вязкость, повышенное удлинение и предел текучести по сравнению со сталью с пластинчатой структурой. Отпуск разделяют на низкий, средний и высокий в зависимости от температуры нагрева. Для определения температуры при отпуске изделия пользуются таблицей цветов побежалости.
Тонкая пленка окислов железа, придающая металлу различные быстро меняющиеся цвета — от светло-желтого до серого. При низком отпуске (нагрев до температуры 200-300° ) в структуре стали в основном остается мартенсит, который, однако, изменяется решетку. Кроме того, начинается выделение карбидов железа из твердого раствора углерода в альфа-железе и начальное скопление их небольшими группами. Это влечет за собой некоторое уменьшение твердости и увеличение пластических и вязких свойств стали, а также уменьшение внутренних напряжений в деталях. Для низкого отпуска детали выдерживают в течение определенного времени обычно в масляных или соляных ваннах. Если для низкого отпуска детали нагревают на воздухе, то для контроля температуры часто пользуются цветами побежалости, появляющимися на поверхности детали.
Появление этих цветов связано с интерференцией белого света в пленках окисла железа, возникающих на поверхности детали при ее нагреве. При среднем (нагрев в пределах 300-500°) и высоком (500-700°) отпуске сталь из состояния мартенсита переходит соответственно в состояние тростита или сорбита. Чем выше отпуск, тем меньше твердость отпущенной стали и тем больше ее пластичность и вязкость. При высоком отпуске сталь получает наилучшее сочетание механических свойств, повышение прочности, пластичности и вязкости, поэтому высокий отпуск стали после закалки ее на мартенсит назначают для кузнечных штампов, пружин, рессор, а высокий — для многих деталей, подверженных действию высоких напряжений (например, осей автомобилей, шатунов двигателей). Для некоторых марок стали отпуск производят после нормализации. Этот относится к мелкозернистой легированной доэвтектоидной стали (особенно никелевой), имеющий высокую вязкость и поэтому плохую обрабатываемость режущим инструментом. Для улучшения обрабатываемости производят нормализацию стали при повышенной температуре (до 950-970°), в результате чего она приобретает крупную структуру (определяющую лучшую обрабатываемость) и одновременно повышенную твердость (ввиду малой критической скорости закалки никелевой стали). С целью уменьшения твердости производят высокий отпуск этой стали. Дефекты закалкиК дефектам закалки относятся:
Главная причина трещин и поводки — неравномерное изменение объема детали при нагреве и, особенно, при резком охлаждении. Другая причина — увеличение объема при закалке на мартенсит. Трещины возникают потому, что напряжения при неравномерном изменении объема в отдельных местах детали превышают прочность металла в этих местах. Лучшим способом уменьшения напряжений является медленное охлаждение около температуры мартенситного превращения. Коробление (или поводка)возникает также от напряжений в результате неравномерного охлаждения и проявляется в искривлениях деталей. Если эти искривления невелики, они могут быть исправлены, например, шлифованием. Трещины и коробление могут быть предотвращены предварительным отжигом деталей, равномерным и постепенным нагревом их, а также применением ступенчатой и изотермической закалки. Обезуглероживание стали с поверхности — результат выгорания углерода при высоком и продолжительном нагреве детали в окислительной среде. Для предотвращения обезуглероживания детали нагревают в восстановительной или нейтральной среде (восстановительное пламя, муфельные печи, нагрев в жидких средах). Образование окалины на поверхности изделия приводит к угару металла, деформации. Это уменьшает теплопроводность и, стало быть, понижает скорость нагрева изделия в печи, затрудняет механическую обработку. Выгоревший с поверхности металла углерод делает изделия обезуглероженным с пониженными прочностными характеристиками, с затрудненной механической обработкой. Интенсивность, с которой происходит окисление и обезуглерожевание, зависит от температуры нагрева, т. е. чем больше нагрев, тем быстрее идут процессы. Образование окалины при нагреве можно избежать, если под закалку применить пасту, состоящую из жидкого стекла — 100 г, огнеупорной глины — 75 г, графита — 25 г, буры — 14 г, карборунда — 30 г, воды — 100 г. Пасту наносят на изделие и дают ей высохнуть, затем нагревают изделие обычным способом. После закалки его промывают в горячем содовом растворе. Для предупреждения образования окалины на инструментах быстрорежущей стали применяют покрытие бурой. Для этого нагретый до 850°С инструмент погружают в насыщенный водный раствор или порошок буры Антикоррозионная обработка изделий после термической обработкиПосле термической обработки, связанной с применением солей, щелочей, воды и прочих веществ, могущих вызывать при длительном хранении изделий коррозию, следует провести антикоррозионную обработку стальных изделий, заключающуюся в том, что очищенные, промытые и высушенные изделия погружают на 5 минут в 20 – 30% водный раствор нитрита натрия, после чего заворачивают в пропитанную этим же раствором бумагу. Закажите продукцию и услуги по телефону +7 (343-9) 39-97-79 |
Термическая обработка болтов и крепежных изделий. Цель термообработки
Высокопрочные или термообработанные крепежные изделия часто требуются для того, чтобы выдерживать растягивающие, сдвигающие или комбинированные нагрузки на болтовые соединения в сложных условиях. Для многих сложных применений требуются высокопрочные крепежные детали, чтобы выдерживать высокие напряжения растяжения и сдвига, создаваемые нагрузками, приложенными к болтовому или скрепленному соединению.
Высокопрочные или термообработанные крепежные детали Нефтегазовые, нефтехимические, химические и энергетические установки содержат котлы, сосуды напорных трубопроводов, клапаны и технологическое оборудование, требующие высокопрочных болтовых соединений для обеспечения герметичности фланцевых соединений, фитингов и закрытия. Термообработанные болты необходимы для того, чтобы выдерживать растягивающие напряжения внутри болтов. Промышленные смесители высокой мощности и приводные валы насосов часто требуют более высокой прочности на сдвиг, обеспечиваемой термообработанными болтами или штифтами.
Строительные анкерные болты, такие как J-образные болты, L-образные болты или вставные клиновые анкеры, для крепления оборудования или элементов конструкции к бетонным подушкам или фундаментам. Конструкционные анкерные болты изготавливаются из углеродистой или полностью термообработанной среднелегированной стали.
Критические по скольжению или фрикционные соединения основаны на сжимающей силе болтов, возникающей при прессовании. Для крепления компонентов конструкции в строительном проекте требуются крепежные детали ASTM A325 или ASTM A490 в сильно нагруженных конструкциях, таких как здания с элементами из высокопрочной стали. Конструкционные болты из мягкой углеродистой стали с меньшей прочностью в соответствии с ASTM A307 можно использовать для крепления статически нагруженных конструкций с легкими элементами.
Термообработанные крепежные детали также необходимы в двигателях, транспортных средствах и гидравлических системах, где болты и крепежные детали подвергаются высоким нагрузкам. Например, высокопрочная головка, блок и другие болтовые соединения на больших дизельных судовых и грузовых двигателях подвергаются высокому крутящему моменту или предварительному напряжению для обеспечения герметичности прокладок. Гидравлические фланцевые соединения высокого давления и четырех болтов (SAE J518) скрепляются закаленными болтами. Четырехболтовые соединения используются в гидравлических системах самолетов, морских нефтяных вышек, большегрузных судов, железнодорожных вагонов, промышленных прессов и формовочных машин. Полностью термообработанные U-образные болты можно найти в тяжелых внедорожниках, карьерных самосвалах и лесозаготовительных прицепах для крепления листовых рессор или других компонентов.
Механические нагрузки и напряжения являются одним из аспектов выбора крепежа. Соображения окружающей среды, такие как температура и коррозионная среда, являются дополнительным фактором, влияющим на проект. В высококоррозионных средах с низкими напряжениями могут потребоваться крепежные детали из нержавеющей стали. Для конструкций, подверженных воздействию низких температур, могут потребоваться болты ASTM A320. ASTM A193 предоставляет спецификации для болтов из легированной и нержавеющей стали для работы при высоких температурах.
Около 90 процентов крепежных изделий изготавливаются из стали, и требуемый уровень прочности обычно достигается в стальных крепежных изделиях с использованием процессов закалки и отпуска. Соответственно, термины «высокая прочность» с «термообработкой» или «закалкой» часто смешиваются с миром крепежных изделий. Однако термическая обработка включает в себя широкий спектр процессов. Некоторые термообработки, такие как отжиг, смягчают металл, в то время как другие затвердевают и укрепляются. Термическая обработка отжигом используется для снятия остаточного напряжения, удаления холодной обработки и растворения легирующего элемента или сегрегации и получения более однородного материала.
Высокоуглеродистые стали можно закаливать, в то время как низкоуглеродистые стали считаются непрокаливаемыми. Сталь в низкопрочных крепежных изделиях ASTM A307 или SAE Grade 2 представляет собой низкоуглеродистую марку, такую как AISI 1018 или 1020. Крепеж из аустенитной нержавеющей стали марки 304 или 316 содержит мало углерода и поэтому не может быть упрочнен термической обработкой. Некоторые марки мартенситной нержавеющей стали, такие как марки B6 и B5 ASTM A193, могут быть упрочнены с помощью термической обработки с закалкой и отпуском. Марки B5 и B6 используются в условиях высоких температур и высокого давления, а также в специальных целях. Термическая обработка болтов из нержавеющей стали используется для растворения грубых частиц карбида хрома, что может снизить коррозионную стойкость и ударную вязкость. Обработка крепежных изделий из нержавеющей стали раствором карбида может улучшить криогенную или низкотемпературную ударную вязкость и является частью спецификации ASTM A320. АСТМ А325, АСТМ А490 Крепеж SAE класса 5 и SAE класса 8 изготавливается из высокоуглеродистой простой или легированной стали, которая может быть закалена в процессе закалки и отпуска. Термообработанные болты класса 8 по SAE имеют вдвое большую минимальную прочность на растяжение, чем болты класса 2 по SAE.
В процессе закалки с отпуском стальные крепежные детали сначала нагревают до температуры, при которой их структура превращается в аустенит, а затем закаливают или быстро охлаждают в воде, масле или воздухе до кристаллической структуры которые превращаются в мартенсит. Затем крепежные изделия из мартенситной стали нагревают при промежуточной температуре отпуска, чтобы превратить мартенсит в феррит с очень тонкой дисперсией цементита. Стали, медленно охлаждаемые от температур аустенизации, а также неупрочняемые малоуглеродистые стали образуют более мягкую, более грубую перлитную структуру из феррита и карбидов железа (цементит). Скорость охлаждения должна быть достаточно высокой, чтобы избежать образования перлита.
Даже среди закаливаемых сталей степень прокаливаемости зависит от содержания углерода и легирующих элементов, таких как хром, молибден, марганец, кремний, ванадий и никель, которые замедляют образование феррита и сдвигают носовую часть стали. перлита, чтобы начать формирование кривой вправо (рис. 4). Прокаливаемость влияет на то, насколько глубоко в материале произойдут изменения твердости в процессе термообработки. Стальные сплавы с более высоким содержанием углерода и легирующих элементов могут подвергаться сквозной закалке, и превращения будут происходить по всей детали даже при более низких скоростях охлаждения, что снижает остаточное напряжение и деформацию при термообработке. В сплавах с более низкой прокаливаемостью закалка будет происходить только частично вглубь сплава от поверхности.
Процесс поверхностного упрочнения В то время как упрочняющая термообработка повышает прочность материала крепежа, закаленные сплавы имеют пониженную пластичность, что означает, что они разрушатся при меньших напряжениях или деформации по сравнению с отожженными крепежными изделиями. Цементация – это процесс упрочнения поверхностного или «корпусного» слоя низкоуглеродистых и легированных сталей. Сталь сначала подвергается науглероживанию или карбонитрированию для увеличения содержания углерода во внешнем слое, или обработанные болты класса SAE 8 имеют вдвое большую минимальную прочность на растяжение, чем болты класса 2 по SAE. В процессе закалки и отпуска стальные крепежные изделия сначала нагревают до температуры, при которой их структура превращается в аустенит, а затем закаливают или быстро охлаждают в воде, масле или воздухе до кристаллических структур, которые превращаются в мартенсит. Затем крепежные изделия из мартенситной стали нагревают при промежуточной температуре отпуска, чтобы превратить мартенсит в феррит с очень тонкой дисперсией цементита. Стали, медленно охлаждаемые от температур аустенизации, а также неупрочняемые малоуглеродистые стали образуют более мягкую, более грубую перлитную структуру из феррита и карбидов железа (цементит). Скорость охлаждения должна быть достаточно высокой, чтобы избежать образования перлита.
Даже среди закаливаемых сталей степень прокаливаемости зависит от содержания углерода и легирующих элементов, таких как хром, молибден, марганец, кремний, ванадий и никель, которые замедляют образование феррита и смещают вершину перлита, чтобы начать формирование кривой вправо ( Рисунок 4). Прокаливаемость влияет на то, насколько глубоко в материале произойдут изменения твердости в процессе термообработки. Стальные сплавы с более высоким содержанием углерода и легирующих элементов могут подвергаться сквозной закалке, и превращения будут происходить по всей детали даже при более низких скоростях охлаждения, что снижает остаточное напряжение и деформацию при термообработке. В сплавах с более низкой прокаливаемостью закалка будет происходить только частично вглубь сплава от поверхности. В то время как упрочняющая термообработка увеличивает прочность материала крепежа, закаленные сплавы имеют пониженную пластичность, что означает, что они будут ломаться при меньших напряжениях или деформации по сравнению с отожженными крепежными элементами.
Цементация – это процесс упрочнения поверхностного или «корпусного» слоя низкоуглеродистых и легированных сталей. Сталь сначала науглероживается или азотируется для увеличения содержания углерода во внешнем слое или корпусе 9.0003
Штифт или крепежная деталь из науглероженной стали затем закаляются обычным способом в процессе закалки и отпуска. В результате крепеж имеет мягкую, прочную внутреннюю сердцевину из низкоуглеродистой стали с внешней поверхностью из цементируемой высокоуглеродистой стали. Закаленная поверхность устойчива к истиранию, износу или порезам. Мягкий и прочный внутренний стержень предотвращает защелкивание или срезание крепежных деталей. Штифты и винты для листового металла часто используют цементированные поверхности. Болты, скобы и другое оборудование для замков часто закаляются, потому что их нелегко распилить, и они обладают прочностью, чтобы противостоять разрушению от удара молотком.
Хотя крепежные детали из высокопрочной стали являются критическим элементом и средством реализации многих передовых конструкций и высокотехнологичных механических конструкций, необходимо соблюдать осторожность при использовании крепежных деталей из закаленной стали. Высокопрочные крепежные изделия с твердостью по Роквеллу С выше 35 подвержены водородному охрупчиванию. Водородное охрупчивание вызывает потерю или частичную потерю пластичности закаленной стали, что может привести к внезапным, катастрофическим и преждевременным отказам крепежа в полевых условиях. Следует избегать воздействия водорода во время обработки или применения в полевых условиях. Атомарный водород может поглощаться стальными крепежными элементами во время процессов фосфатирования, травления (кислотной очистки или удаления окалины), гальваники и гальванического цинкования. Хотя рекомендуются альтернативные защитные покрытия, для удаления остаточного водорода после металлизации или электрохимических процессов можно использовать термическую обработку водородом. ASTM F1941 Стандартная спецификация для электроосажденных покрытий на механических крепежных деталях, дюймовых и метрических единицах, требует водородного нагрева. Водородный отжиг следует проводить через несколько часов после нанесения покрытия, обычно при температуре от 350° до 450° F в течение от двух до 24 часов. Воздействие кислого газа (сероводорода) в окружающей среде, гальваническая коррозия и даже пар высокого давления в полевых условиях могут вызвать «внешнее или экологическое водородное охрупчивание». Минимизация начального количества водорода в стали может помочь избежать этих проблем. Гальванической коррозии из-за приложенных токов или пар разнородных материалов (например, стали, используемой для болтового соединения алюминия или медно-латунных сплавов) можно избежать, изолируя крепежные детали непроводящими шайбами или втулками или выбирая совместимые материалы.
Перегрев во время обработки (в ваннах высокотемпературного цинкования), монтажа (прихватка, пайка) и применения в полевых условиях (реактор, печь и т. д.) может привести к отжигу или размягчению закаленного застежка, если температура и время при температуре чрезмерны. ASTM F2329 требует испытания механических свойств, если процесс цинкования происходит при температурах, превышающих температуру отпуска стального сплава. Хорошо известным примером того, как температура влияет на прочность болта, является сравнение низкоуглеродистой бористой стали SAE J429.болты марки 8.2 к болтам из среднеуглеродистой стали марки 8. Оба сорта имеют сходные свойства при испытаниях при комнатной температуре. Более низкая температура отпуска (650°F) борсодержащей стали не позволяет использовать болты класса 8.2 при более высоких температурах. Болты из легированной стали класса 8 имеют температуру отпуска 800°F, что позволяет использовать их при более высоких температурах.
Болты, подвергнутые термообработке, прочнее, но не являются неразрушимыми. Неправильное использование крепежных элементов могло привести к их поломке и даже выходу из строя всего узла, оборудования или конструкции. Чрезмерная затяжка закаленных болтов выше предела их прочности на кручение может привести к поломке. Недостаточно затянутые крепежные детали могут привести к преждевременному выходу из строя из-за истирания, фреттинг-усталости или изменения нагрузки и внутренних напряжений в крепежных элементах. Как и в случае любой резьбовой системы крепления, необходимо применять соответствующий уровень крутящего момента, чтобы в полной мере использовать уровни прочности болта. Если с закаленным болтом используется мягкая, необработанная гайка, то в гайке может произойти преждевременный выход из строя. В болтовых соединениях ASTM A563 или ASTM A19Следует использовать гайки класса 4 для тяжелых условий эксплуатации с уровнями прочности, сравнимыми с выбранными высокопрочными болтами или совместимыми с ними (рис. 5). Болты с термообработкой не предназначены для использования в резьбовых отверстиях, поскольку стальные пластины или конструктивные элементы обычно изготавливаются из мягкой углеродистой стали или незакаленной легированной стали.
При использовании резьбовых шпилек материал с резьбовым отверстием должен иметь уровень прочности, совместимый с термообработанным крепежным элементом. Шайбы также должны соответствовать спецификациям ASTM F436 для шайб из закаленной стали.
Заключение
Использование термообработанных крепежных деталей в конструкции может обеспечить структурные преимущества. Тем не менее, термообработанные болты будут иметь более высокую стоимость по сравнению с болтами из незакаленной низкоуглеродистой стали. Отказ оборудования вполне возможен, если термообработанные или высокопрочные болты заменяются более мягкими болтами во время капитального ремонта, модернизации или модернизации.
При техническом обслуживании и ремонте следует обращать внимание на маркировку болтов при замене изношенных, поврежденных или заржавевших болтов. Если головка болта заржавела или повреждена до такой степени, что маркировка не читается, следует обратиться к руководству по оборудованию или поставщику оборудования для получения надлежащих спецификаций крепежа. Если бы болты были в точке отказа в проекте ремонта, то было бы неплохо обратиться к руководству по оборудованию, строительным спецификациям или OEM для получения правильных классов болтов. Если маркировка не видна, руководства утеряны, а производитель неизвестен или закрыт, то в крайнем случае испытание болта на твердость может показать, подвергались ли заменяемые крепежные детали термообработке. Дополнительная информация доступна на веб-сайте Bayou City Bolt. Bayou City Bolt and Supply может найти термообработанные крепежные материалы, отвечающие требованиям самых тяжелых условий эксплуатации.
Процесс термической обработки тонкостенной направляющей втулки_PTJ Blog
В центральной передаче нового полногидравлического бульдозера производства нашей компании установлена направляющая втулка. Эта часть взаимодействует с фланцевой пластиной, играя направляющую и фиксирующую роль.
Из-за более высокой точности сопоставления и более высокой твердости для повышения износостойкости, а также из-за того, что эта деталь является тонкостенной (5 мм), термообработка легко деформируется, а термообработка сложнее. В данной статье предлагается несколько схем термической обработки данного изделия, анализируется и обсуждается каждая схема, и выбирается наиболее рациональный процесс термической обработки.
1. Обзор направляющей втулки
Название детали: направляющая втулка, материал конструкции: ZG35SiMn, деталь P требует индукционной закалки, глубина закаленного слоя: 1,5 ~ 2,5 мм, твердость поверхности: 52 ~ 60HRC.
Маршрут процесса проектирования этой детали: литье → нормализация → черновая обработка → закалка и отпуск → чистовая обработка → индукционная закалка → шлифование внутренних и внешних кругов. Эта деталь представляет собой тонкостенную деталь с толщиной стенки около 5 мм. Зона термического влияния большая при индукционной термообработке, а деформация после индукционной термообработки большая, а некоторые части имеют эллиптическую форму. Из-за большой деформации глубина закаленного слоя в некоторых местах после шлифовки недостаточна, что не может удовлетворить требованиям эксплуатации. Химический состав этого изделия приведен в таблице 1, что соответствует требованиям к химическому составу ZG35SiMn. Перед индукционной термообработкой в каждом процессе не возникает проблем.
2. Обнаружение
Чтобы уменьшить зону термического влияния, разработана специальная охлаждающая рубашка с распылением воды по внешнему кругу, и вода распыляется для охлаждения внешнего круга, соответствующего нагревательной части, во время нагрева, чтобы уменьшить диффузию тепла и зону термического влияния для уменьшения деформации. . После многих испытаний проблема деформации не была решена. Регулировка потока охлаждающей воды, давления, частоты индукционной закалки, мощности и других настроек по-прежнему не может решить проблему деформации.
Выберите части с большей деформацией для вскрытия. Результаты вскрытия показаны на рис. 2 и рис. 3. Глубина поверхностного упрочненного слоя после шлифовки составляет всего 0,603 мм, что не соответствует требованиям. Металлографическая структура: отпущенный мартенсит + феррит, поверхностная твердость 54~56HRC, размер зерна 9 классов, твердость сердцевины 315HBW.
Процесс индукционной закалки не может удовлетворить проектные требования, и многочисленные корректировки параметров процесса и инструментов не могут решить проблему. Дизайнеры и технологический персонал нашей компании неоднократно обсуждали разработку двух решений:
(1) Материал детали заменен на 20CrMnTi, и для повышения износостойкости используется науглероживание. Технологический маршрут: вырубка → ковка → нормализация → обработка → науглероживание прямая закалка → шлифование внутреннего и внешнего кругов; поверхностная твердость: 58 ~ 63HRC, глубина закаленного слоя 1,5~2,5 мм, размер зерна закаленного слоя ≥8 класса, остаточный аустенит ≤20%, карбид ≤3 класса.
(2) Материал детали — ZG35SiMn, для повышения износостойкости используется термообработка ионным азотированием. Маршрут процесса: вырубка → ковка → нормализация → обработка → отпуск → обработка → шлифование внутреннего и внешнего круга → ионное азотирование. Твердость поверхности ≥613HV1, глубина азотированного слоя ≥0,3 мм, уровень рыхлости азотированного слоя ≤3, уровень азотирования азотированного слоя ≤3.
3. Тест
Для вышеуказанных двух технологических схем наша компания изготовила 20 образцов и провела технологические испытания.
(1) Испытание процесса науглероживания
В соответствии с материалом заготовки, структурой и соответствующими техническими требованиями определяется процесс науглероживания направляющей втулки.
Деформацию выявляли до и после прямой термической обработки науглероживания. Проблема большой деформации все еще существует, возникает эллиптическая деформация, и проблема деформации не может быть устранена после шлифования.
(2) Испытание процесса ионного азотирования
В соответствии с материалом заготовки, структурой и соответствующими техническими требованиями определяется процесс термообработки ионного азотирования направляющей втулки. .
Проверялся внутренний диаметр направляющей втулки до и после ионного азотирования. Результат сравнения показан в таблице 4. Деформация значительно снижена и соответствует требованиям.
4. Вывод
Путем сравнения трех вышеуказанных мер было обнаружено, что процесс ионного азотирования может значительно уменьшить деформацию заготовки. Благодаря проверке установки основная машина работает в течение 2000 часов без каких-либо отзывов о качестве направляющей втулки; направляющая втулка снимается через 2000 часов, а слой износа очень мал. Это можно почти игнорировать.
Ссылка на эту статью:Процесс термообработки тонкостенной направляющей втулки
Заявление о перепечатке: Если нет особых указаний, все статьи на этом сайте являются оригинальными. Пожалуйста, укажите источник для перепечатки: https://www.cncmachiningptj.com/, спасибо!
PTJ® предоставляет полный спектр услуг по обработке фарфора с ЧПУ Custom Precision. Сертификация ISO 9001: 2015 и AS-9100. 3-, 4- и 5-осевая высокоточная обработка
CNC-обработка услуги, включая фрезерование, обработка листового металла по спецификациям заказчика, возможность обработки металлических и пластиковых деталей с допуском +/- 0,005 мм.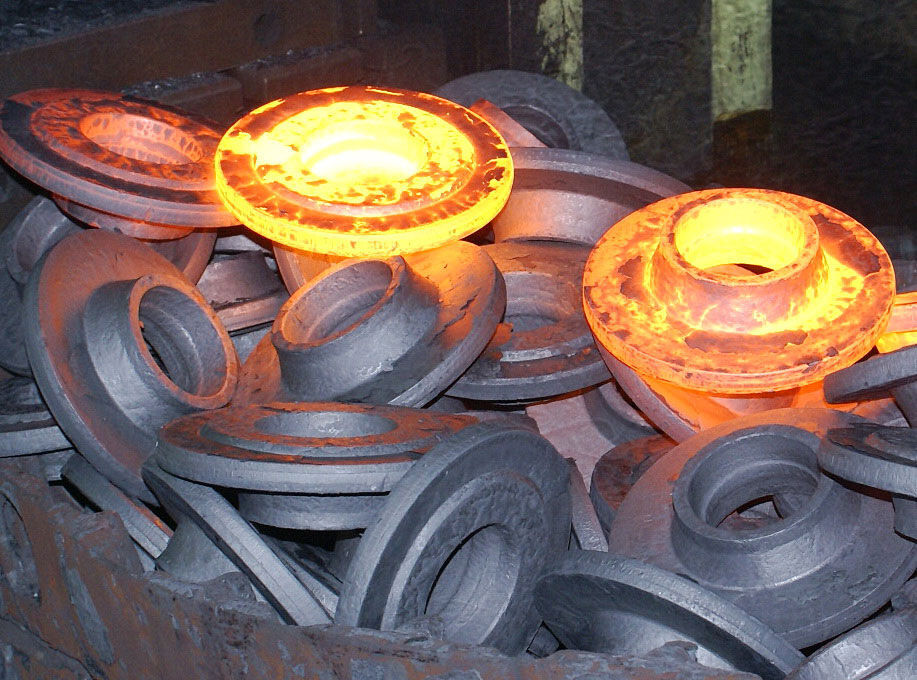
Добавить комментарий