Синтез газ получение: Синтез-газ – Что такое Синтез-газ?
Синтез-газ – Что такое Синтез-газ?
30634
Синтез-газ — смесь монооксида углерода и водорода.
Синтез-газ – смесь монооксида углерода и водорода.Получение синтез-газа является первой стадией превращения природного газа и угля не только в жидкие топлива, но и химические продукты.
В промышленности синтез-газ получают паровой конверсией метана, парциальным окислением метана, газификацией угля.
Эти способы обладают высокой себестоимостью.
Применение катализаторов означает осуществление на поверхности катализатора ряда химических превращений.
Этот метод зарекомендовал себя как более эффективный и дешевый.
В зависимости от способа получения соотношение CO:Н
В зависимости от применяемого сырья и вида конверсии (водяным паром или нестехиометрическим количеством О2) соотношение компонентов в газовой смеси изменяется в широких пределах:
- СН4 + Н2О : СО + 3Н2
- СН4 + ½O2 : СО + 2Н2
- -СН2-+ Н2О:СО + 2Н2
- -СН2-+ ½O2 :СО + Н2
По наиболее распространенному методу Лурги получают сырой газ следующего состава:
- 15-18% СО,
- 38-40% Н2,
- 9-11% СН4,
- 30-32% СО2;
- с повышением температуры увеличивается доля СО,
- с возрастанием давления – Н2 и СН4.
Примесями могут быть инертные газы (N2 и др. ) и Н2S, если сырье содержало серу.
Синтез-газ очищают от Н2S и СО2 селективными растворителями; соотношение между СО и Н2 регулируют, если необходимо, конверсией оксида углерода водяным паром.
Синтез-газ получают также наряду с целевым продуктом ацетиленом при окислительном пиролизе природного газа.
Синтез-газ. Риформинг. Необходимая стехиометрия — Нефтянка
Сердце технологии синтетических топлив — это синтез Фишера-Тропша. Но синтез Фишера-Тропша не превращает в синтетическую нефть или другие углеводороды сырье непосредственно, ни уголь, ни газ, ни биомассы. Необходим так называемый синтез-газ. Синтез-газ — это смесь водорода и монооксида углерода, он же угарный газ, как любят вкратце говорить химики h3 и CO. Вот соотношение водорода и оксида углерода — это штука, к которой очень чувствительны катализаторы Фишера-Тропша.
Так как соотношение водорода и оксида углерода — это соотношение водорода и углерода в продукте в конечном счёте, нужно, чтобы она держалась весьма узких рамках, и для некоторых катализаторов диапазон, в котором они согласны работать, очень узкий. Так называемая стехиометрия синтез-газа связана с составом стехиометрии продукта. В целом это соотношение колеблется в районе двух, но может быть от 1,5–2,5. Есть катализаторы, которые работают только в интервале от 2,10 до 2,15. И момент этот, как оказалось, очень тонкий, особенно учитывая то, что технологии получения синтез-газа, как оказалось, дают нередко синтез-газ совсем не той стехиометрии, который нужен для Фишера-Тропша.
Синтез Фишера-Тропша не единственная химическая технология, потребляющая синтез-газ. Могу назвать производства синтетических спиртов самых разных, в том числе самое массовое производство метанола, производство аммиака, то есть основа производства минеральных удобрений. Производство водорода. Они все основаны сначала на получении синтез-газа, а потом на его переработке конечный продукт. И требования по стехиометрии у всех свои, поэтому вопрос оптимальной технологии получения синтез газ стоял и стоит очень остро.
Тем более что на сегодняшний день это самая дорогая часть установки синтетического топлива. Если в первом поколении получение синтез-газа занимало где-то треть от всей установки, во втором поколении чуть больше половины, то в четвёртом поколении это три четверти, а то и больше, потому что, благодаря достижениям четвёртого поколения, сильно сократились расходы на синтез Фишера-Тропша и дальнейшую переработку. А получение синтез-газа, чаще всего его называют риформинг, осталось прежним. И оставшись прежним, оно тем не менее, требует тонкой настройки и правильного подбора, встраивания в общую схему предприятий синтетического топлива.
Что в этой связи на сегодняшний день существует, если говорить о переработке газа? Прежде всего, есть технология так называемого парового риформинга. Это когда при температуре около 900° природный газ реагирует с водяным паром на специальном катализаторе, обычно никелевом, и из него получается синтез газ, точнее так называемый конвертированный газ, который чистят и превращают в синтез-газ. Метод разработан в 1958-м году как промышленный, с тех пор очень хорошо распространился. 1000 единиц по всему миру. Все, как любят говорить в промышленности, коммерчески доступно, но есть две вещи. Во-первых, паровой риформинг сам по себе дает синтез-газ в соотношении водород/СО не меньше 3, а то и 5, а надо 2. Куда-то надо деть лишний водород.
Есть патент одной уважаемой западной компании, которая предлагает лишний водород извлекать при помощи мембран и сжигать. Это прекрасная идея, но только с экономикой такого процесса будет плохо. Это гарантированно, потому что на водород уходит огромное количество природного газа изначального, и это плохая идея.
Есть другая технология — автотермический риформинг. Это когда в одном реакторе к природному газу подмешивается не только пар, но и кислород. Происходит такое горения влажного газа, или горение во влажном кислороде, как хотите. Там тоже присутствует катализатор, в результате получается довольно просто синтез-газ сразу нужного соотношения, то есть автотермический риформинг дает сотношение водород/СО около двух. Это замечательно, но есть пара «но» как обычно. Одно «но» — это то, что необходим кислород. А раз необходимо кислород, нужна кислородная станция, которая этот кислород производит из воздуха или путём разжижения (криогенная станция). И важно то, что эта кислородная станция дороже самого риформера. Преимущества в значительной степени нивелируются.
Существует ещё риформинг кислорода. Он сейчас находится в состоянии разработки. Одним из разработчиков является как раз компания «ИНФРА Технологии», хотя некоторые крупные компании уже вышли на рынок с промышленными решениями, но пока единичными.
Из невозможности получить правильную стехиометрию методом парового риформинга выходят по-разному. В Катаре, например, на одном из заводов есть риформинг того и другого типа. Синтез-газ смешивается, и стехиометрия получается вполне себе приемлемая. Можно в паровой риформер, который, напомню, дает слишком большое соотношение водород/СО, инжектировать агент, который будет уменьшать это соотношение, например, углекислоту. Это иногда называют пароуглекислотный риформинг. Это очень хорошо работает. Этот прием применяется в частности компанией «ИНФРА Технологии» в наших промышленных установках небольшого размера.
Должен сказать, что одной из важнейших проблем риформинга является переносимость изменения состава природного газа на входе и возможность перерабатывать жирные газы. Компании, которые предлагают промышленные решение риформинга, они, как правило, исходят из того, что необходимо строить на больших предприятиях, имеющих доступ к трубопроводному газа установки, дающие синтез-газ для разных целей.
Это может являться препятствием, например, для переработки попутного газа нефтедобычи. Мало того что они жирные, у них ещё в состав постоянно меняется в ходе добычи. И если кто-то хочет разработать технологию пригодную для того, чтобы её использовать для утилизации попутного газа, он должен об этом позаботиться.
И мы в компании «ИНФРА Технологии» об этом позаботились. Разработали такое решение для нашего пароуглекислотного риформинга, которое позволяет перерабатывать попутный газ в очень широком диапазоне составов и даже гибко реагировать на изменение этого состава. Причём скорость реакции составляет 30–40 минут. Состав газа на самом деле так быстро не меняется.
Владимир Мордкович
Навигация по записям
Альтернативные энергоносители из углеводородных газов
Владимир АРУТЮНОВЧлен НАН Республики Армения, профессор,
д. х. н., главный научный сотрудник,
Федеральный исследовательский центр химической физики им. Н.Н. Семенова РАН, Институт проблем химической физики РАН
e-mail: [email protected]
Введение
Обильные ресурсы природного газа, включая его нетрадиционные разновидности, такие как сланцевый газ и газовые гидраты, позволяют рассматривать их как долговременную базу мировой энергетики. Существенным сырьевым ресурсом энергетики остается попутный нефтяной газ (ПНГ), мировой объем факельного сжигания которого, несмотря на все предпринимаемые усилия и законодательные меры, не снижается уже многие годы, оставаясь на уровне 140 млрд кубометров.
Источник: esys.org
Методы конверсии природного газа в жидкие углеводороды и более привлекательные виды газомоторного топлива хорошо известны, однако существующие технологии пока малопривлекательны для практического применения, особенно в отечественных условиях и для малотоннажных производств [1, 2]. Причина в том, что конверсия метана, основного компонента природных и попутных газов, в другие химические продукты – крайне сложный и энергозатратный процесс. При нормальных условиях метан – наиболее стабильный углеводород, обладающий очень прочными химическими связями, разрыв которых требует больших затрат энергии. Это основная причина серьезного различия традиционных нефтехимических процессов, в которых преобладают разрыв и изомеризация относительно слабых С–С и С-Н связей в жидких углеводородах, и газохимии, начальным процессом в которой является разрыв очень прочной С-Н связи в молекуле метана. Химическая переработка всех остальных углеводородов, начиная уже с этана, требует значительно меньших усилий, и может быть отнесена к хорошо освоенным традиционным нефтехимическим процессам.
Сложность реализации первой стадии активации метана заставляет прибегать к обходным путям его конверсии, наиболее эффективным из которых оказалась его предварительная конверсия в синтез-газ – смесь молекул Н2 и СО, для которой давно разработаны эффективные каталитические процессы превращения в метанол, синтетические жидкие углеводороды (СЖУ, синтетическая нефть) и другие продукты. Главное преимущество такого пути в том, что при определенных условиях метан может быть практически полностью превращен в синтез-газ, но это требует высоких (~900оС) температур, а следовательно, значительных энергозатрат.
Традиционные процессы на основе синтез-газа
Практически все современные промышленные технологии превращения природного газа в химические продукты, за исключением процессов галоидирования и сульфидирования, основаны на его предварительной конверсии в синтез-газ. Затем уже из синтез-газа получают такие крупнотоннажные химические продукты, как аммиак, водород, метанол и синтетические жидкие углеводороды, которые сейчас рассматриваются как потенциальные альтернативные энергоносители. Конверсия природного газа в синтез-газ – наиболее сложная и затратная стадия современных газохимических процессов, на которую приходится до 60–70 % всех затрат на получение целевых продуктов. Высокие затраты на эту стадию являются основным фактором, сдерживающим развитие современной газохимии.
Наиболее распространенным промышленным процессом, на основе которого сейчас производится более 80 % синтез-газа, является паровая конверсия метана.
СН4 + Н2О <−> СО + 3Н2
∆Н = +226 кДж/моль
Этот сильно эндотермический процесс, в котором получают богатый водородом синтез-газ с отношением Н2/СО = 3, начал широко внедряться в промышленных масштабах с 1960‑х гг., когда в качестве исходного сырья вместо угля стали использовать природный газ. Паровая конверсия обычно проводится с использованием относительно недорогих никелевых катализаторов при температурах 800–1000оС, давлениях выше 2 МПа и высоком отношении Н2О/СН4 = 2,5–3,0 и более для снижения зауглероживания катализатора. Процесс проводят в трубчатых печах с внешним обогревом реакционных труб, заполненных нанесенным металлическим катализатором (рис. 1).
Рис. 1. Разрез риформера фирмы LurgiВедущими компаниями-разработчиками процесса паровой конверсии являются Howe-Baker (США), Haldor Topsoe (Дания), Foster Wheeler Corp. (США), Technip (Франция), Lurgi (Германия) и ряд других, конструкции реакторных печей (риформеров) которых различаются в основном схемами нагрева реакторных труб с катализатором. Тепло отходящих дымовых газов используется для производства пара, а также для предварительного подогрева сырья и воздуха, подаваемого на горелки. Если в составе сырья много тяжелых гомологов метана, приводящих к ускоренному зауглероживанию катализатора, то в схему процесса включают реактор предварительного риформинга, в котором при температуре до 600оС проводят паровую конверсию тяжелых гомологов метана в метан и частично в синтез-газ.
Перспективным направлением в технологии паровой конверсии природного газа, особенно с точки зрения снижения эмиссии основного парникового газа СО2, является использование в качестве источника тепла высокотемпературных гелиевых атомных реакторов (ВТГР) – нового типа универсальных атомных источников энергии, способных вырабатывать тепло с температурой до 1000 °C. С участием концерна «Росэнергоатом» разработан проект установки с модульным реактором МГР-Т из серии ВТГР для производства водорода и электричества (тепловая мощность блока – 600 МВт). Реактор испытан в технологии комбинированной выработки высокопотенциального тепла с температурой теплоносителя на выходе из реактора 950–1000оС и электроэнергии с эффективностью газотурбинного цикла преобразования энергии 48 %. Высокопотенциальное тепло, получаемое в реакторе, отводится теплоносителем первого контура (гелием), имеющим на выходе из реактора температуру 950оС. Это тепло передается конвертируемой парогазовой смеси в химико-технологической части установки в высокотемпературных теплообменниках. Оставшаяся тепловая энергия в блоке преобразования энергии преобразуется в электрическую энергию в прямом газотурбинном цикле. Из общей тепловой мощности реактора, составляющей 600 МВт, 160 МВт идет на процесс паровой конверсии метана и 435 МВт – на производство электроэнергии. Расчетный срок службы реактора составляет 60 лет.
Другая промышленная технология конверсии природного газа в синтез-газ – парциальное окисление (окислительная конверсия) – была разработана в начале 1950‑х гг. Это слабо экзотермический процесс, не требующий дополнительного подвода тепла.
СН4 + 0,5О2 <−> СО + 2Н2
∆Н = -44 кДж/моль
Как правило, процесс осуществляют при давлении 30–100 атм в небольшом избытке чистого кислорода по сравнению со стехиометрией реакции, чтобы обеспечить более полную конверсию и достижение необходимой для реакции температуры, что приводит к образованию некоторого количества продуктов глубокого окисления СО2 и Н2О. Окислительная конверсия метана может протекать как в присутствии катализатора, так и без него. Для некаталитического процесса необходимы температуры 1200–15000С и давления 2,5–8 МПа, при которых достигается полная конверсия углеводородов и предотвращается сажеобразование. Термическая эффективность процесса достигает 60–75 %. В каталитическом процессе обычно используют никелевый или родиевый катализатор, чаще всего на цеолитах ZSM‑5. При этом возможны более мягкие условия (800–9000С, 2,5–3,5 МПа), что позволяет использовать технологию в малотоннажных процессах, а также повышает ее мобильность.
1 – монтажные люки; 2 – корпус конвертора; 3 – теплоизоляция; 4 – смеситель;
5 – термопары; 6 – свободное пространство над катализатором; 7 – катализатор крупнокусковой на магнезите; 8 – катализатор ГИАП‑3–6Н; 9 – высокоглиноземистый огнеупор; 10 – перфорированный свод.
На практике часто используют комбинированную парокислородную конверсию метана. Помимо снижения энергозатрат, это позволяет получать синтез-газ с соотношением Н2/СО2 »2, наиболее благоприятным для синтеза метанола и продуктов Фишера-Тропша. Такой процесс успешно реализован на крупнейшем в мире предприятии по производству синтетических жидких углеводородов Perl GTL компании Shell в Катаре. Главными недостатками технологии парциального окисления природного газа являются большие капиталовложения в установки по разделению воздуха, а также заметное образование сажи, которую необходимо удалять. Существуют также проблемы взрывобезопасности процесса. Помимо высоких температур и давлений для достижения высокого выхода синтез-газа необходимо обеспечивать низкое соотношение О2/СН4 = 0,6–0,7, то есть работать с очень богатыми смесями, соотношение метана и кислорода в которых фактически лежит вне области воспламенения для нормальных условий, что крайне сложно. Коммерциализацию процесса парциального окисления метана затрудняют также большие размеры реакторов. Ведущими разработчиками и лицензиарами технологии парциального окисления метана являются компании Shell и Chevron Texaco.
Популярной промышленной технологией конверсии природного газа становится автотермический риформинг (АТР) – комбинация экзотермической реакции гомогенного парциального окисления и эндотермической реакции парового риформинга, энергию для осуществления которой получают за счет парциального и полного окисления части углеводородного сырья в том же реакторе. Пионером и наиболее активным разработчиком этого процесса с 1960‑х гг. является датская компания Haldor Topsoe [3].
Основные показатели различных промышленных методов получения синтез-газа представлены в табл. 1 и на рис. 3.
ПР – паровой риформинг; КР – комбинированный риформинг; АТР – автотермический риформинг [4]
Таблица 1. Показатели различных процессов получения синтез-газа [4]При небольшой производительности установок (до 300 тыс. м3/ч) их относительная стоимость для всех процессов примерно одинакова. С увеличением мощности стоимость всех процессов растет линейно, но для парового риформинга этот рост заметно круче. Поэтому при мощности в 1,5 млн м3/ч относительная стоимость парового риформинга почти в два раза выше, чем автотермического.
Наиболее крупнотоннажным продуктом (более 180 млн т/год), производимым на основе синтез-газа, является аммиак – основа производства азотных удобрений для современного высокопродуктивного сельского хозяйства. Хотя аммиак уже давно рассматривается как потенциальное транспортное топливо [5], а также источник получения водорода [6], серьезные проблемы, возникающие при его практическом использовании, пока сдерживают развитие данного направления.
Более очевидны перспективы использования для этих целей другого продукта, получаемого из синтез-газа – метанола. В настоящее время метанол – продукт газохимии с наиболее динамично растущим объемом производства. В мире более 90 заводов, производящих метанол, с суммарной установленной мощностью около 110 млн т/год. Его мировое производство превысило 80 млн т/год, а к 2025 г. прогнозируется достижение уровня в 120 млн т/год. Особенно быстрыми темпами производство метанола развивается в Китае, который обеспечивает почти половину его мирового производства. Объем производства метанола в России – 4,4 млн т/год. Метанол – универсальный продукт, который может заменить нефть во многих нефтехимических процессах, и универсальное топливо, которое можно использовать практически во всех типах двигателей внутреннего сгорания (ДВС), а также как топливо для газовых турбин и котельное топливо. Наконец, метанол – наиболее удобный жидкий носитель водорода. Водород для питания двигателей внутреннего сгорания или топливных элементов может быть получен из метанола непосредственно на борту транспортного средства при его относительно мягкой паровой каталитической конверсии.
На промышленном уровне уже давно освоен и процесс превращения синтез-газа в жидкие синтетические углеводороды (синтез Фишера-Тропша), способные заменить природную нефть [3]. Фракционный состав образующихся продуктов зависит главным образом от температуры процесса и природы используемого катализатора, и определяется коэффициентом α, отражающим соотношение констант скоростей роста и обрыва углеводородной цепи на катализаторе. Обычно он весьма широк, от метана до углеводородов C50 и выше (рис. 4).
В мире существуют несколько крупных предприятий по производству жидких углеводородов на основе конверсии природного газа в синтез-газ и последующего синтеза Фишера-Тропша, то есть схеме, называемой технологией GTL (Gas to Liquid), суммарной производительностью около 10 млн т/год, а также ряд небольших пилотных установок различных компаний. Основной продукцией GTL предприятий, реализованных на основе технологии компании Shell (Perl GTL в Катаре и Bintulu GTL в Малайзии), является дизельное топливо. Предприятия, реализованные на основе GTL технологии компании Sasol (Oryx GTL в Катаре, Escravos GTL в Нигерии и ряд других) производят более широкий спектр продукции, включающей помимо дизельного топлива бензин, олефины и оксигенаты. В Китае и ЮАР действуют предприятия, производящие синтетические жидкие углеводороды по аналогичной схеме, но использующие в качестве сырья для получения синтез-газа уголь (Coal to Liquid, CTL-технологии).
Основной проблемой современных GTL предприятий является их технологическая сложность и высокие затраты на стадию превращения природного газа в синтез-газ, на которую приходится до 60 % всех затрат. Удельные капвложения в такие предприятия превышают 200 тыс. долл. за баррель ежедневной продукции, что в несколько раз превышает типовые капвложения в нефтеперерабатывающие предприятия. Поэтому после падения цен на нефть привлекательность таких предприятий резко упала (рис. 5), и в настоящее время при цене нефти на уровне 50–60 долл./баррель строительство новых подобных предприятий не планируется. Необходимо отметить, что, согласно оценкам специалистов ВНИИГАЗ, при реализации подобных предприятий в отечественных условиях удельные капзатраты будут примерно в два раза выше, чем для условий Мексиканского или Персидского заливов.
Альтернативные технологии конверсии метана в синтез-газ
Принципиальным недостатком современных сложных технологий GTL является то, что они непригодны для реализации в средне- и малотоннажном варианте, в то время как подавляющая часть перспективных традиционных и особенно нетрадиционных источников углеводородных газов относится именно к этой категории. Поэтому во всем мире ведется разработка альтернативных технологий GTL. Основной упор делается на создание более простых и компактных процессов получения синтез-газа. Уже предложен и испытывается ряд принципиально новых процессов, включая процессы на основе окисления природного газа на керамических мембранах, процессы в микроканальных реакторах, процессы фильтрационного горения, окисление метана при миллисекундных временах контакта, процессы на основе энергетических и электрохимических технологий [3]. Пока ни одна из этих технологий не реализована в промышленном масштабе, но интенсивные работы ведутся во многих странах. Мы лишь коротко отметим недавно разработанный нами метод матричной конверсии, который позволяет проводить процесс в автотермическом режиме без использования внешних источников тепла или энергии, не требует катализаторов и обеспечивает удельную объемную производительность по синтез-газу на порядок выше, чем паровая конверсия. Процесс позволяет использовать углеводородные газы практически любого состава и происхождения, а его рентабельность слабо зависит от объема перерабатываемого газа [8].
Прямые методы конверсии метана в химические продукты
Высокие затраты на получение синтез-газа стимулируют интерес к прямым процессам превращения основного компонента природного газа – метана – в химические продукты и жидкое топливо, не требующим его предварительной конверсии в синтез-газ. Наиболее привлекательным направлением остается окислительная конденсация метана в этилен – процесс, который был открыт в начале 1980‑х и породил большие надежды на создание эффективных химических методов переработки метана. Так как этилен является базовым соединением для производства большого числа продуктов современной нефтегазохимии, такой процесс позволил бы полностью решить проблему химической переработки природного газа. За прошедшее время его исследованию были посвящены тысячи работ, но достигнуть уровня коммерциализации процесса пока так и не удалось [3]. Экономически более выгодным процессом превращения метана в этилен и далее продукты на его основе оказался многостадийный путь с последовательным превращением метана в синтез-газ, затем метанол и далее превращением метанола в этилен на цеолитных катализаторах [3].
Источник: tecedu.academy
В настоящее время в Китае работает уже несколько таких заводов.
Другим методом прямого превращения метана в химические продукты является его парциальное (частичное) окисление в метанол, образующийся как промежуточный продукт неполного окисления метана при большом недостатке кислорода. Метод был предложен еще в начале прошлого века и применялся как промышленный, но из-за низкой конверсии метана за проход и невысокой селективности образования метанола уступил процессу на основе синтез-газа. Хотя в последнее время удалось значительно повысить его показатели, он остается привлекательным в основном для малотоннажных процессов, для которых определяющую роль играют его простота и низкие капзатраты [3].
Использование ПНГ в энергетике
Главная причина неполного использования ПНГ и продолжающегося во всем мире его факельного сжигания – отсутствие рентабельных малотоннажных технологий переработки углеводородных газов [1, 2], которые позволяли бы перерабатывать ПНГ непосредственно на месте добычи. В настоящее время единственный безубыточный способ утилизации ПНГ удаленных месторождений, особенно в специфических условиях российских нефтедобывающих регионов – выработка электроэнергии и тепла для собственных нужд. До 30 % энергии сжигаемого ПНГ могло бы использоваться для удовлетворения потребности в энергии самих нефтяных промыслов, что позволило бы значительно сократить объем северного завоза жидкого топлива. Однако для этого необходимо предварительно тем или иным способом извлечь или преобразовать значительную часть содержащихся в ПНГ гомологов метана. Даже незначительная примесь более тяжелых алканов с низкими октановыми числами (ОЧ) и метановыми числами (МЧ) и высокой низшей теплотой сгорания Qн делает ПНГ склонным к детонации и не позволяет достигать номинальной мощности газопоршневого двигателя (ГПД), вынуждая работать со снижением нагрузки (дерейтингом) на 20–30 % и более, а также приводит к его быстрому выходу из строя в результате образования смолистых отложений. А существующие методы сепарации тяжелых компонентов из ПНГ требуют сложного оборудования и высоких энергозатрат и не окупаются для энергоустановок малой и средней (до 10–20 МВт) мощности [9].
Для превращения ПНГ в кондиционное газомоторное топливо, удовлетворяющее требованиям производителей газопоршневых электростанций небольшой мощности, нами был разработан метод селективного окислительного крекинга гомологов метана непосредственно в самом ПНГ [9, 10]. Окислительный крекинг позволяет обеспечить 82–85 %-ю конверсию этана и практически полную конверсию всех более тяжелых углеводородов. Суммарная конверсия гомологов метана составляет 92–95 %. Основными продуктами конверсии являются этилен, монооксид углерода, водород и метан. Метод селективного оксикрекинга позволяет на 11–19 пунктов поднять метановое число смеси и на 6–8 МДж/м3 снизить низшую теплоту сгорания, доведя оба эти показателя до значений, рекомендуемых производителями для устойчивой эксплуатации газопоршневых машин, то есть получить из ПНГ топливный газ, удовлетворяющий требованиям, предъявляемым производителями ГПД.
Получение водорода
Принятое в 2015 году Парижское соглашение по климату провозгласило своей целью разработку и реализацию стратегии снижения эмиссии парниковых газов, прежде всего СО2, за счет снижения доли углеводородных источников в мировом энергобалансе. Достигнуть это предполагается в основном за счет перехода на возобновляемые источники энергии, однако их реальный потенциал значительно ниже даже текущих потребностей мировой энергетики [11], и на обозримый период все серьезные прогнозы отводят им долю всего в несколько процентов мирового энергобаланса [12]. Поэтому неудивительно, что в последнее время основным направлением усилий по снижению «углеродного следа» энергетики провозглашен ускоренный переход на водородную энергетику, т. е. более широкое использование водорода в качестве энергоносителя для производства энергии, коммунального сектора и транспорта. Россия активно присоединяется к этим усилиям. Распоряжением Правительства РФ от 12 октября 2020 г. № 2634‑р утвержден План мероприятий (дорожная карта) по развитию водородной энергетики до 2024 года. План направлен на увеличение производства и расширение сферы применения водорода в качестве экологически чистого энергоносителя, а также вхождение страны в число мировых лидеров по его производству и экспорту.
Основным промышленным методом получения водорода остается и в обозримом будущем будет оставаться его выделение из синтез-газа, получаемого паровой конверсией природного газа (~80 % производства Н2) и угля (~20 % производства Н2). На долю возобновляемых источников приходится много меньше 1 % его мирового производства, а стоимость такого водорода минимум в 3 раза выше получаемого паровой конверсией. Поэтому помимо пока еще очень далеких от практически приемлемых решений вопросов хранения, транспортировки и распределения больших объемов водорода, фундаментальная проблема водородной энергетики – снижение затрат на получение водорода, прежде всего, на конверсию углеводородных газов в синтез-газ.
Учитывая нерешенные пока проблемы транспортировки и хранения больших объемов водорода, наиболее разумным подходом, особенно для транспортного сектора, может стать его распределенное малотоннажное производство из сетевого природного газа или легко транспортируемого жидкого углеводородного сырья непосредственно в местах потребления. Основой такого распределенного производства водорода мог бы стать метод матричной конверсии природного газа в синтез-газ [8], на базе которого может быть также организовано распределенное производство метанола, синтетических жидких углеводородов, аммиака и других потенциальных альтернативных энергоносителей и жидких источников получения водорода.
Заключение
Современная газохимия предлагает широкий набор уже освоенных промышленностью и потенциальных технологий превращения углеводородных газов различного состава и происхождения в более удобные или экологически приемлемые жидкие и газообразные энергоносители. Однако экономическая эффективность большинства этих технологий пока недостаточна для конкуренции получаемых из природного газа альтернативных энергоносителей с традиционными видами жидкого нефтяного топлива. Поэтому важнейшей проблемой перехода на такие энергоносители становится развитие технологической базы газохимии.
Работа выполнена в рамках Программы фундаментальных научных исследований государственных академий наук, тема ФИЦ ХФ РАН 0082-2019-0014, номер госрегистрации AAAA-A20-120020590084-9 и тема ИПХФ РАН 0089-2019-0018, номер госрегистрации АААА-А19-119022690098-3.
Метан получение синтез-газа – Справочник химика 21
В качестве исходного сырья, используемого для получения синтез-газа посредством парового риформинга, могут применяться природный газ (в основном метан с несколькими процентами высококипящих углеводородов), легкий бензин (в основном бутан с некоторым количеством бутена и высококипящих углеводородов) и, наконец, легкие нефтяные дистиллаты.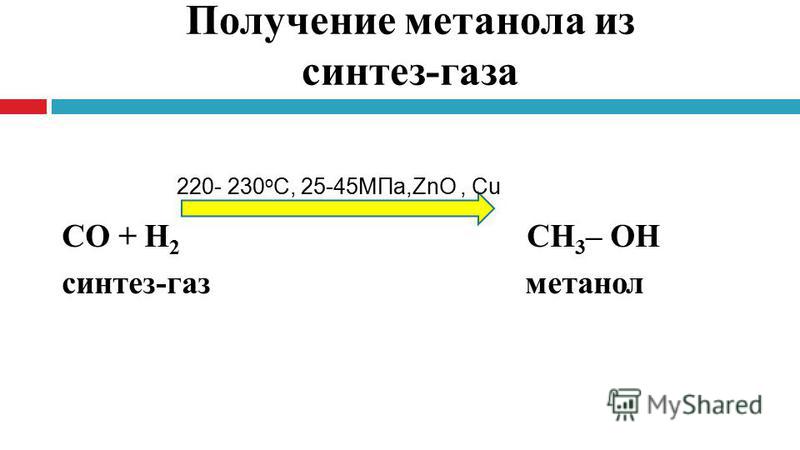
Наиболее экономичным сырьем для получения синтез-газа является метан. [c.101]
В качестве источника сырья для производства продуктов нефтехимической промышленности стали использовать метан из природного газа. Конверсией метана с водяным паром или реакцией с кислородом получали газ синтеза (смесь окиси углерода и водорода) и водород. Таким образом, метан из природного газа стал одним из исходных продуктов для получения синтетического метилового спирта и синтетического аммиака. Синтез аммиака был разработан в Германии непосредственно перед первой мировой войной, за ним последовало развитие процесса производства синтетического метанола в обоих случаях исходным сырьем служил каменный уголь. Подобно этому и паро-метановый и метано-кислородный процессы получения газа синтеза имеют европейское происхождение, при этом в качестве сырья используется метан, являющийся побочным продуктом в процессах разделения коксового газа или при гидрогенизации угля. [c.21]
Если основной целью является получение синтез-газа с различным соотношением На СО, можно увеличить содержание СО добавлением в реакционную смесь СОа. Это смещает равновесие в сторону образования СО с другой стороны, при высоких температурах СОа вступает с метаном в следующую сильно эндотермическую реакцию [c.213]
Применение. Метан находит широкое применение. Его используют как газообразное, очень калорийное топливо. Кроме того, метан является ценным сырьем для получения производных. Огромные количества метана подвергают конверсии (превращению) в синтез-газ (смесь СО и Нг). Для этого метан либо с парами воды пропускают над никелевым катализатором при 700—800°С (конверсия водяным паром), либо подвергают неполному окислению кислородом при 1400—1500° С (кислородная конверсия) [c. 300]
Продукты окисления. Неполное окисление углеводородов и углеводородных смесей всегда было исключительно интересным объектом исследования. Сложность этой проблемы объясняется двумя причинами во-первых, сама реакция окисления является трудноуправляемой и, во-вторых, — реакционная смесь содержит бесчисленное множество соединений самых различных классов. Из всех процессов неполного окисления углеводородов наиболее хорошо изученным и освоенным является получение синтез-газа (смеси СО п водорода) для производства метанола и для оксосинтеза [300]. Сырьем для этого процесса служит метан (природный газ) в смеси с 95 %-ным кислородом. Очистка продукта реакции от СО позволяет также получать водород (в смеси с азотом) для синтеза аммиака (301—305]. [c.584]
Если бы метан удалось окислить непосредственно в формальдегид и метанол, то можно было бы отказаться от дорогостоящих и энергоемких стадий получения синтез-газа и метанола.

Для получения синтез-газа, содержащего водород и окись углерода в объемном соотношении 2 1 (используют его для синтеза метанола), производят конверсию метана с водяным паром или с кислородом затем из с.меси удаляют двуокись углерода. Попутный нефтяной газ и газы нефтепереработки, состоящие из метана и этана с примесью пропана, можно также подвергать конверсии гомологи метана конвертируются легче, чем метан. [c.251]
Не оставляя этого метода конверсии, промышленность Германии использовала также и другой способ получения синтез-газа из метана, получивший название процесса К У. При этом методе метан и кислород после предварительного подогрева подвергают неполному сжиганию при высокой температуре (700—1000°) над никелевым катализатором. Происходящая реакция может быть выражена уравнением [c.195]
На рис. 56 показана технологическая схема получения синтез-газа конверсией метана водяным паром. Метан нагревают в теплообменнике 3 до 400 С контактными газами, отходящими из трубчатой печи (конвертора 1) и направляется в смеситель 2. Одновременно в смеситель 2 из теплообменника 4 подается водяной пар при температуре 400 °С. Полученную паро-газовую смесь направляют в конвертор 1. В трубы конвертора, выполненные из жароупорной стали и обогреваемые снаружи, помещают никелевый катализатор (высота слоя 7 м). [c.163]
Характеристики катализаторов конверсии углеводородов во многом зависят от качества исходного сырья. В Советском Союзе для получения синтез-газов и водорода преимущественно используется природный газ, содержащий метан с примесью гомологов до С5 (табл, 11,5). В газе, поступающем из магистрального газопровода, может содержаться 50—200 г/м газового конденсата ( Сз) с точкой росы при давлении до 3,5 МПа порядка (—20)—(—23) С. После местной очистки содержание конденсата не должно превышать 15—60 г/м (в зависимости от сезона). В большинстве случаев в [c.62]
Различие между реакциями I и II заключается в том, что при температуре реакции Ст — твердое вещество, а С Нт — газообразное. В настоящее время основным углеводородом, используемым в качестве сырья, является метан. Температуру получения синтез-газа выбирают из кинетических соображений она не превышает 1500 К. [c.317]
Получение синтез-газа в двигателе внутреннего сгорания показано на рис. Сырьем служит смесь природного газа (метана) с кислородом мольное соотношение кислорода и метана от 0,7 до 1,0. Специально сконструированный восьмицилиндровый двигатель со степенью сжатия, равной 7, имеет рабочий объем 42 л. Наилучшие результаты были получены при температуре 550 °С и соотношении кислород метан, равном 0,8. Выхлопные газы при этом содержат 58% водорода и 35% окиси углерода. Через 1000 ч работы в цилиндрах двигателя наблюдалось незначительное коксообразование. Сравнение этого процесса с процессами частичного сжигания и конверсии с водяным паром показало, что синтез-газ, полученный в двигателе внутреннего сгорания, дешевле. [c.82]
Приближение к равновесию АТ всегда положительная величина, если для получения синтез-газа риформингу подвергается метан или нафта (хотя она может быть отрицательной, когда из нафты получают город-ские газы, богатые метаном), а низкие значения ДТ (например, менее 20° С) соответствуют высокой каталитической активности. На приближение к равновесию влияют объемная скорость (производительность), соотношение пар газ и, в меньшей степени, температура и давление. Для оценки АТ необходимо очень точно определять рабочие условия. В области обычных параметров первичного риформинга (при температурах до 800° С и давлениях до 31,64 ат) катализатор 57-1 дает приближение, равное 10—15° С. Подобные же рассуждения применимы к катализатору 46-1 риформинга нафты, но в этом случае суш,ествует дополнительное требование — полный риформинг исходной нафты. [c.107]
Наиболее эффективным процессом получения синтез-газа является конверсия метана паро-кислородной смесью. Тепло, необходимое для этого процесса, обеспечивается за счет полного окисления части метана. При этом образуются СОг и НгО, которые взаимодействуют с продуктами конверсии и исходным метаном, образуя СО и Нг. При паро-кислородной конверсии не требуются жаропрочные стали, катализатор не отравляется сернистыми соединениями и требования к сырью менее жесткие (можно использовать газы любого состава). Капиталовложения меньше, чем при конверсии в трубчатых печах, однако эксплуатационные расходы более высоки из-за относительно высокой стоимости кислорода. Технологическая схема паро-кислородной конверсии приведена на рис. И1.11. [c.164]
По назначению процесса для получение заменителя природного газа (8МО), обогащенного метаном для получение синтез газа, имеющего в составе преимущественно СО и Н2 в различных соотношениях.
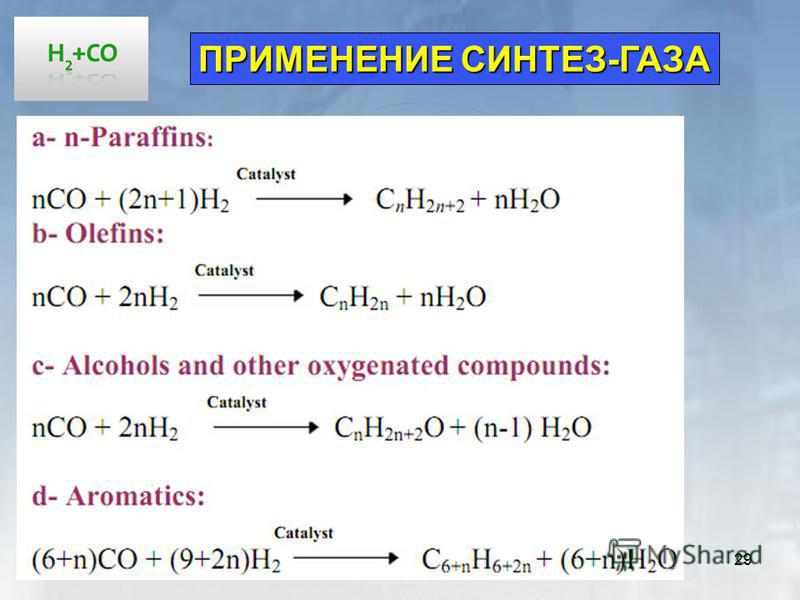
Получение синтез-газа путем газификации угля является громоздким процессом. В связи с этим в последнее время все больше развиваются процессы получения синтез-газа на основе природных газов, содержащих метан. [c.335]
По этому способу метанол получают при 5 МПа, а в качестве исходного сырья для получения синтез-газа используют метан, тяжелые нефтяные остатки, уголь. [c.125]
Основными компонентами природного газа являются метан, сероводород, диоксид углерода. Данные о некоторых реакциях СО2, получении водорода и синтез-газа из СН4, взаимодействии метана с насыщенными (диспропорционирование) и ненасыщенными (крекинг) углеводородами приведены выше. Ниже рассмотрены термодинамические характеристики процесса утилизации сероводорода — процесса Клауса и синтезов на основе метана. [c.349]
Последняя ступень получения синтез-газа — метанирование— превращение остаточных окислов углерода в метан взаимодействием с водородом. Реакцию проводят при температуре 288 400°С в реакторе со стационарным слоем никелевого катализатора. [c.19]
По технологии фирмы Лурги метанол получают под давлением 5,0 МПа, используя в качестве исходного сырья для получения синтез-газа метан, тяжелые нефтяные остатки, уголь. На рис. 4.4 представлена схема процесса, исходным сырьем для которого служат нефтяные остатки. [c.310]
Реактор для получения синтез-газа путем парциального окисления метана. Получение синтез-газа состоит из двух стадий экзотермической реакции сгорания метана в кислороде и взаимодействия этих продуктов с оставшимся метаном по эндотермической реакции. Реакционная камера 2 для проведения процесса в гомогенной фазе устанавливается сбоку от разделенной на части печи I (рис. [c.623]
До настоящего времени метан коксового газа использовался в основном для получения синтез-газа и метанола, но это производство пока ограничено масштабами единичных установок. В отдельных случаях коксохимический метан используется для промышленного производства ацетилена и сажи [91]. Вместе с тем, наличие крупных ресурсов метана в коксовом газе отечественной коксохимической промышленности дает основания для того, чтобы изыскивать новые направления химического использования этого газа с целью получения важных для народного хозяйства продуктов. [c.48]
Синтез-газ (от процесса получения ацетилена) и метан, предварительно увлажненные в сатурационной башне, орошаемой горячей водой, подогреваются до 450° С, смешиваются с кислородом в соотношении 1,5 1 и поступают в конвертор метана, где происходит конверсия метана с кислородом и паром на никелевом катализаторе при 1100° С и давлении 0,6—0,7 ат. Содержание метана по выходе из конвертора не должно превышать 0,3—0,5%. Конвертированный газ увлажняется впрыскиванием конденсата и добавлением пара до соотношения пар газ—0,68 1, охлаждается свежим синтез-газом до 400°С и подается в конвертор окиси углерода, где при 500° С взаимодействует с паром на железо-хромовом катализаторе до содержания окиси углерода в конвертированном газе около-4%. Затем охлажденный до 30°С газ очищается от двуокиси углерода абсорбцией водным раствором моноэтаноламина в насадочных скрубберах в две ступени при давлении 0,15 и 30 ат. [c.335]
Процесс получения ацетилена методом неполного сжигания, в котором сырьем являются метан из природного газа и 90—95% ный кислород, эксплуатируется в промышленном масштабе в США, Италии, а также в Германии. В этом процессе на каждую весовую часть ацетилена получают не менее 2 весовых частей газа синтеза (00 + На), поэтому описанный процесс применяют там, где одновременно имеется производство синтетического аммиака или синтетического метанола. Такое применение смеси СО и Иг более выгодно, чем использование ее в качестве энергетического топлива. Метод частичного сожжения углеводородного сырья можно рассматривать как вариант метано-кислородного процесса (гл. 3), в котором часть метана превращается в весьма ценный ацетилен. [c.279]
Для получения синтез-газа может быть успешно использован также метан природных газов, который превран ается в смесь окиси углерода и водо1рода или каталитически по уравнению СН4 + Н20 —> СО ЗН2, или неполным сжиганием в кислороде. Следовательно, удается из простейшего парафина — метана — получить его высокомолекулярные гомологи. В результате имеем наиболее четко выраженный процесс синтеза, в ходе которого сложные молекулы образуются из простейших составляющих компонентов. [c.70]
Эффективность процесса получения синтез-газа увеличивается, если обычному процессу риформинга с паром предшествует риформинг на никелевом катализаторе при низком содержании пара в смеси (как в процессе БАСФ — Лурги Рикатро ). В результате риформинга при низком содержании пара образуется газовая смесь, богатая метаном, которая при риформин-ге с паром на традиционном катализаторе превраш,ается в синтез-газ с благоприятным для синтеза метанола отношением, [c.223]
Превращение биомассы в топлива, пригодные для непосредственного использования, осуществляется термохимическими или биохимическими процессами. К термохимическим процессам переработки относятся прямое сжигание, пиролиз, газификация и экстракция масел, к биохимическим — ферментация и анаэробное разложение. Перед переработкой биомасса обычно проходит стадии подготовки, включающие измельчение, сущку и др. При переработке биомассы в моторные топлива наибольший интерес представляет газификация с получением синтез-газа (преобразуемого затем в метанол или углеводороды), а также ферментация с получением этанола. Процесс получения синтез-газа во многом аналогичен газификации угля (см. раздел 3.2). При газификации древесины при 300 °С в присутствии кислорода образуется в основном диоксид углерода. При повышении температуры до 600 °С получают смесь, в которой помимо СОг присутствуют водород, оксид углерода, метан, пары спиртов, органических кислот и высших углеводородов. Выход газообразных продуктов при этом не превышает обычно 40% (масс.) на сырье. В связи с меньшими энергетической плотностью и теплотой сгорания биомассы газификация ее менее эффективна, чем газификация угля. Поэтому, несмотря на проводимые во многих странах исследовательские и конструкторские [c.121]
Любые газообразные углеводороды (в частности, метан), содержащиеся в водороде, который в дальнейшем используется для получения аммиака, не изменяются при пропускании через катализатор синтеза аммиака. Поскольку непрореагировавшие газы возвращаются в цикл, газообразные углеводороды накапливаются и снижают парциальное давление водорода. При получении синтез-газа для производства аммиака концентрацию углеводородов снижают до 0,2- 0,5%, На стадии конверсии природного газа водяным паром образующийся в первичном реакторе газ может содержать 5-10% метана. Этот газ смешивают с определенным количеством воздуха (синтез-газ должен содержать азот) и пропускают смесь над катализатором вторичной высокотемпературной конверсии. Этот катализатор находится в адиабатическом реакторе, футированном тугоплавкими материалами. Поскольку реакция конверсии экзотермическая, температура в реакторе поднимается до [c.166]
По технологии фирмы Lurgi метанол получают при 5 МПа, а в качестве исходного сырья для получения синтез-газа используют метан, тяжелые нефтяные остатки, уголь. На рис. 8.23 представлена схема процесса, исходным сырьем для которого служат нефтяные остатки. Окисление углеводородного сырья ведут в присутствии водяного пара при 1400—1450 °С и 5,5— 6 МПа и получают смесь Н2 и СО (1 1) с примесью СО2, СН4 и сажи. Тепло отходящих газов используют для получения пара высокого давления. Синтез-газ отмывают от сажи, очищают от сернистых соединений и подвергают переработке для получения газа нужного состава. Под давлением 5—5,5 МПа газ подогревают в теплообменнике и без дополнительного компримирования вводят в реактор синтеза. Синтез метанола ведут при 250— 260 °С при этом на 1 кг метанола получают 1,4 кг пара высокого давления. Выходящую из реактора газовую смесь охлаж- [c.316]
Сырьем для производства исходных мономеров для получения синтетического каучука служат этиловый спирт, пентаны, нормальный изобутан, метан (для синтеза изопрена), этан, низкооктановый бензин. Характерным изменением в структуре сырья для получения синтетического каучука является увеличение доли изобутана, пентанов, бутан-бутиленовой фракции с иефтеперерабатываю-. щих предприятий, а также фракции С4 газов пиролиза. [c.53]
Очищенная азотоводородная смесь, вводимая в цикл синтеза, может содержать, в зависимости от исходного сырья п способа получения синтез-газа, большие или меньшие количества аргона и метана. Из смешанного водяного газа получается чистый синтез-газ, содержащий в сз мме около 0,4—0,5% аргона и метана, причем метана обычно содержится немногим больше, чем аргона. Водород, полученный конверсией метана, может содержать 1% и более метана, азот, полз чаемый ректификацией воздуха, обычно очень чист. Аргон и метан являются инертными газами в процессе синтеза аммиака, но присутствие их нежелательно, так как они постепенно накапливаются в циркуляционном газе. При полной герметизации аппаратуры только небольшое количество циркуляиио нного газа выводится из цикла (в результате растворения газа в сепараторах жидким аммиаком). Вследствие этого Содержание аргона и метана в газе значительно возрастает, что приводит к уменьшению парциальных давленнй азота и водорода и к снижению производительности установки синтеза аммиака. [c.539]
КОНВЕРСИЯ ГАЗОВ (лат. сопуег-510 — превращение) — процесс переработки газов с целью изменения состава исходной газовой смеси. Конвертируют метан и его производные или оксид углерода для получения водорода или его смесей с оксидом углерода — так называемый синтез-газ, который используют для синтеза органических веществ, в качестве газа-восстановителя в металлургии или для получения чистого водорода. [c.133]
На этой стадии процесса ВМ постоянно рассчитывает оптимальную температуру и соотношение пар-углеводород с целью обеспечения максимальной конверсии углеводорода при минимальной стоимости пара и топлива, что позволяет снизить себестоимость получения водорода и уменьшить уровень инертных составляющих, таких как неконвертирован-ный метан, в синтез-газе. При этом ВМ учитывает уменьшение срока службы катализатора при повышении температуры конверсии. [c.558]
МЕТАН СН4 — первый член гомологического ряда предельных углеводородов, Бесцветный газ, не имеющий запаха, малорастворим в воде. М. образуется в природе при разложении органических веществ без доступа воздуха на дне болот, в каменноугольных залежах (отсюда другое название М.— болотный, нли рудничный газ). В большом количестве М, образуется при коксовании каменного угля, гидрировании угля, нефти. В лаборатории М. получают действием воды на карбид алюминия. Л, — главная составная часть природных горючих газов. М. легче воздуха, смеси М. с воздухом взрывоопасны, М. горит бледным синим пламенем. М, широко используется в промышленности и быту как топливо, для получения водяного и синтез-газа, применяемых для органического синтеза углеводородов с большой молекулярной массой, спиртов, ацетилена, сажи, хлористого метила, хлорбро . метана, ни-грометака, цианистоводородной кислоты и др. [c.160]
Применение кислорода позволяет упростить процесс получения синтез-газа, так как вследствие положительного теплового эффекта суммарной реакции отпадает необходимость использования сложных контактных печей с внешним обогревом. По одному из вариантов этого метода экзотермическую реакцию сгорания метана в кислороде и эндотермические реакции разложения метана водяным паром и двуокисью углерода проводят раздельно. Сначала метан разбавляют водяным паром (чтобы предотвратить образование взрывчатой газовой смеси) и к подогретому газу постепенно добав- [c.336]
Фирма “Снампрожетти” предложила получать МТБЭ (метил-mpem-бутиловый эфир) и другие эфиры в многостадийном процессе, используя в качестве сырья только метан и кислород [179]. Процесс состоит из стадий 1) получение синтез-газа 2) синтез метанола и высших спиртов, главным образом изобутанола 3) отделение метанола от высших спиртов 4) дегидратация высших спиртов в олефины [c.123]
В коксохимической промышленности Франции, где глубокая химическая переработка коксового газа получила наибольшее развитие, на основе метана коксового газа вырабатывают широкий ассортимент продуктов. На центральном перерабатывающем заводе в Мазенгарбе (район угольного бассейна Нор э Па-де-Кале) метан коксового газа подвергается крекингу с получением синтез-газа последний используется для производства метанола и его производных. Часть синтез-газа направляется на синтез аммиака. Производство метанола на заводе было организовано в 1928 г., а к 1964 г. мощность установки составляла 40 тыс. т, т. е. более Vg общего производства в то время метанола в стране (ПО тыс. т). На этом же заводе строится новая установка синтеза метанола производительностью 60 тыс. т в год. На основе метанола завод производит форм- [c.48]
Синтез углеводородов по Фишеру-Тропшу, так же как и другие виды синтеза на основе окиси углерода и водорода, базируется на ианользовании смесей окиси углерода и водорода, легко получаемых в производстве водяного газа. Для получения водяного газа могут быть использованы каменные и бурые угли, а также все виды топлива, способные к газификации. Каталитической конверсией с водяным паром в смесь окиси углерода с водородом могут быть переведены также и газообразные углеводороды и в первую очередь метан. [c.75]
Кислород предварительно подогревают до 315° и затем в смеси с нагретым до 650° природным гаэом под давлением 20—21 ат подают в футерованную камеру сгорания, где проходит реакция и развивается температура примераю 1350°. Продукты реакции направляются затем в котел-утилизатор, где они охлаждаются до 315° с получением примерно 45-атмосферного пара. После этого синтез-газ проходит теплообменник, холодильник и, наконец, промыватель для удаления сажи. При конверсии природного газа, не являющегося чистым метаном, получается газ с соотношением СО Нг примерно 1 1.8 [18]. [c.78]
Затем в США был освоен процесс на основе соединений родия и иода, когда давление синтеза составляет всего 0,1—0,5 МПа, а выход уксусной кислоты достигает 99% по метанолу. Этот метод получения уксусной кислоты позволяет базировать ее производство на метане или на малодефицитных углеводородах (углеводород—)-синтез-газ— -метанол— уксусная кислота) и на угле (уголь— -водяной газ—>-метанол— -кислота). По некоторым оценкам, он является самым экономичным нз способов получения уксусной кислоты. [c.543]
Количество тех или иных побочных соединений в продукциои-ной смеси зависит от температуры, давления, состава исходной газовой смеси, селективности и состояния катализатора. Наиболее существенными примесями являются метан и диметиловый эфир. По сравиению со всеми побочными процессами (а) — (е) получение метилового спирта идет с максимальным уменьшением объема, поэтому Б соответствии с принципом Ле Шателье повышение давления сдвигает равновесие в сторону образования метилового спирта. Так как процесс экзотермичен, то при повышении температуры равновесие сдвигается влево и равновесная степень превращения синтез-газа в метиловый спирт уменьшается. В то же время при недостаточно высоких температурах скорость процесса чрезвычайно мала. Поэтому в промышленности процесс ведут в узком интервале температур с колебаниями в 20—30°С. Константа равновесия основной реакции [c.165]
Найден новый подход к созданию эффективных катализаторов для получения синтез-газа
Ученые из Института общей и неорганической химии им. Н.С. Курнакова РАН, Химического факультета Московского государственного университета им. М.В. Ломоносова и Российского государственного университета нефти и газа им. И.М. Губкина разработали оригинальную, экспрессную и эффективную методику получения никелата лантана, который является перспективным материалом для создания катализаторов получения синтез-газа. Работа поддержана Российским научным фондом (грант № 20-13-00138). Результаты работы опубликованы в журнале Applied Organometallic Chemistry.
Сложные оксиды – оксиды, образованные двумя и более металлами – используются в составе самых различных материалов, например, катализаторов, сенсоров, магнитных материалов и адсорбентов. Например, одним из наиболее перспективных направлений исследования никелата лантана (LaNiO3) является создание на его основе эффективных и дешевых катализаторов углекислотной конверсии метана в синтез-газ (смесь CO+H2) – важнейший промежуточный продукт промышленного получения водорода, метанола и углеводородов.
Помимо возможности эффективного получения синтез-газа, огромный интерес к процессу углекислотной конверсии метана обусловлен утилизацией углекислого газа и метана – двух наиболее вредоносных парниковых газов. Поэтому дальнейшее развитие методов получения катализаторов на основе никелата лантана является актуальной и важной задачей.
Классический метод получения материалов на основе никелата лантана заключается во взаимодействии соответствующих индивидуальных оксидов лантана и никеля в результате длительного нагрева при температурах порядка 800-900 °С. В связи с этим особое значение приобретает разработка альтернативных, более экспрессных и простых методов получения никелата лантана и материалов на его основе.
Именно такой подход был предложен российскими учеными. В его основе – образование никелата лантана в результате термического разложения координационных соединений, содержащих лантан и никель в заданном соотношении (1:1).
Исследование комментирует старший научный сотрудник Лаборатории магнитных материалов ИОНХ РАН, кандидат химических наук Андрей Гавриков: «Преимущество нашего метода заключается в том, что равномерное распределение ионов лантана и никеля по объему обеспечивается уже на этапе получения координационных соединений. Таким образом, задача получения никелата лантана фактически сводится к тому, чтобы “убрать лишнее”, то есть органические фрагменты комплексов, в процессе их термического разложения. Это, в свою очередь, требует гораздо меньших время- и энергозатрат по сравнению с классическим методом. Так, длительность получения никелата лантана по нашей методике сокращена сразу в несколько раз.
Важным преимуществом предложенного метода, помимо простоты и экспрессности, являются высокие величины удельной поверхности полученных материалов. С учетом высокого, близкого к 100%, содержания никелата лантана, это определяет их высокую каталитическую активность в процессе углекислотной конверсии метана. Так, выходы синтез-газа при использовании новых катализаторов доходят до практически количественных значений (99%), т.е. существенно превышают аналогичные величины, полученные при использовании большинства других катализаторов. Важнейшим преимуществом полученных систем является их низкая стоимость по сравнению с катализаторами, сопоставимыми по эффективности, но содержащими чрезвычайно дорогие благородные металлы (например, родий). Результаты исследования будут использованы для дальнейшего развития подходов к получению эффективных гетерогенных катализаторов получения синтез-газа и других важных процессов.
21 мая 2020 г. | |||
Органические вещества.![]() | Химия 11 класс | 30 минут | Пяткова Ольга Борисовна, старший преподаватель кафедры естественно-математических дисциплин, ГБУ ДПО ЧИППКРО |
Органические вещества. Кислородосодержащие соединения | Химия 11 класс | 30 минут | Пяткова Ольга Борисовна, старший преподаватель кафедры естественно-математических дисциплин, ГБУ ДПО ЧИППКРО |
15 мая 2020 г. | |||
Итоговая видеоконсультация по химии | Химия 9 класс | 30 минут | Пяткова Ольга Борисовна, старший преподаватель кафедры естественно-математических дисциплин, ГБУ ДПО ЧИППКРО |
12 мая 2020 г. | |||
Генетическая связь между классами неорганических соединений | Химия 11 класс | 30 минут | Пяткова Ольга Борисовна, старший преподаватель кафедры естественно-математических дисциплин, ГБУ ДПО ЧИППКРО |
Кислоты неорганические и органические | Химия 11 класс | 30 минут | Пяткова Ольга Борисовна, старший преподаватель кафедры естественно-математических дисциплин, ГБУ ДПО ЧИППКРО |
5 мая 2020 г.![]() | |||
Электролиз растворов и расплавов. Применение электролиза в промышленности | Химия 11 класс | 30 минут | Пяткова Ольга Борисовна, старший преподаватель кафедры естественно-математических дисциплин, ГБУ ДПО ЧИППКРО |
Неметаллы | Химия 11 класс | 30 минут | Пяткова Ольга Борисовна, старший преподаватель кафедры естественно-математических дисциплин, ГБУ ДПО ЧИППКРО |
29 апреля 2020 г. | |||
Окислительно-восстановительные реакции в природе, производственных процессах и жизнедеятельности организмов | Химия 11 класс | 30 минут | Пяткова Ольга Борисовна, старший преподаватель кафедры естественно-математических дисциплин, ГБУ ДПО ЧИППКРО |
Свойства простых веществ – металлов главных и побочных подгрупп | Химия 11 класс | 30 минут | Пяткова Ольга Борисовна, старший преподаватель кафедры естественно-математических дисциплин, ГБУ ДПО ЧИППКРО |
Урок 1.![]() | Химия 9 класс | 30 минут | Пяткова Ольга Борисовна, старший преподаватель кафедры естественно-математических дисциплин, ГБУ ДПО ЧИППКРО |
Урок 2. Обобщение знаний. Электроотрицательность. Степень окисления | Химия 9 класс | 30 минут | Пяткова Ольга Борисовна, старший преподаватель кафедры естественно-математических дисциплин, ГБУ ДПО ЧИППКРО |
6 апреля 2020 г. | |||
Общая характеристика элементов IVА-группы | Химия 11 класс | 30 минут | Пяткова Ольга Борисовна, старший преподаватель кафедры естественно-математических дисциплин, ГБУ ДПО ЧИППКРО |
Периодическая система химических элементов Д.И. Менделеева. Строение атома и вещества. | Химия 9 класс | 30 минут | Пяткова Ольга Борисовна, старший преподаватель кафедры естественно-математических дисциплин, ГБУ ДПО ЧИППКРО |
Классификация химических реакций по различным признакам.![]() | Химия 9 класс | 30 минут | Пяткова Ольга Борисовна, старший преподаватель кафедры естественно-математических дисциплин, ГБУ ДПО ЧИППКРО |
Способ получения синтез-газа
Изобретение относится к способу утилизации газов доменного процесса и производства кокса.
Синтез-газы являются газовыми смесями, которые используются в реакциях синтеза и состоят преимущественно из монооксида углерода и водорода. Для некоторых комбинаций CO/H2 на основе их происхождения или применения были приняты специальные обозначения, такие как водяной газ, крекинг-газ, метанольный синтез-газ или оксогаз. Синтез-газ может служить в качестве смеси исходных веществ для производства жидких топлив. Так, синтез-газ используется, например, в способе Фишера-Тропша для производства дизельного топлива. Бензиновые топлива могут производиться MTG-способом (Methanol To Gasoline), при котором синтез-газ сначала превращается в метанол, который на дальнейших этапах преобразуется в бензин.
В принципе, для получения синтез-газа могут применяться все углеродсодержащие вещества. К ним относятся как ископаемые топлива, такие как уголь, нефть и природный газ, так и другие материалы, например пластик, торф, древесина или биомасса, такая как городские или сельскохозяйственные отходы. Если применяются твердые вещества, то они сначала должны быть подвергнуты дорогостоящему измельчению, чтобы за счет частичного окисления или дегидрирования можно было получить неочищенный синтез-газ. На последующих этапах он затем подготавливается. Все эти меры приводят к высоким капиталовложениям, которые являются препятствием для производства жидких топлив из синтез-газа.
Из ЕР 0200880 A2 известно, что конвертерный газ с высоким содержанием СО от доменного процесса смешивается с коксовым газом с высоким содержанием водорода и смесь используется в качестве синтез-газа для синтеза метанола. В известном способе коксовый газ сначала подается к установке короткоцикловой безнагревной адсорбции (КБА-установка), в которой отделяется примерно 83% содержащегося в коксовом газе водорода. Содержащий углеводороды остаточный газ сжимается, освобождается на ступени очистки от каталитических ядов, затем подвергается конверсии и расщепляется в паровом риформере с помощью водорода в CO, CO2 и H2. Крекинг-газ смешивается с предварительно отделенным водородом и необходимым для получения стехиометрического синтез-газа количеством конвертерного газа и используется в качестве метанольного синтез-газа. Для описанной подготовки коксового газа необходимы дополнительные установки, связанные с соответствующими капиталовложениями и эксплуатационными расходами.
Задачей изобретения является сокращение затрат на оборудование и эксплуатационных расходов на получение синтез-газа.
Объектом изобретения и решением этой задачи является способ утилизации азов доменного процесса и производства кокса, включающий разделение коксового газа, образующегося при коксовании угля, на водород и содержащий углеводороды поток остаточного газа, при этом отделенный от коксового газа водород вводится в богатый монооксидом углерода поток синтез-газа, полученного из колошникового газа доменного процесса, а содержащий углеводороды поток остаточного газа вводится в доменный процесс в качестве топлива.
Возвращенный в доменный процесс поток остаточного газа представляет собой богатый метаном и СО газ. Углеводороды используются в доменном процессе в качестве топлива. Введенная с остаточным газом в доменный процесс доля СО приводит к повышению удаляемого из доменной печи колошникового газа, используемого для производства синтез-газа. Предложенный способ является энергоэффективным и не требует дополнительных этапов подготовки или установок.
В коксовую печь подается уголь, который при исключении воздуха нагревается более чем до 1000°С. При этом летучие компоненты угля удаляются. Они образуют коксовый газ. Если используются несколько коксовых печей, то образующиеся неочищенные газы объединяются в сборном трубопроводе. Перед дальнейшим использованием, т.е. перед разделением на водород и содержащий углеводороды поток остаточного газа, коксовый газ обессмоливается и обессеривается, а также освобождается от аммиака, ароматических веществ и нафталина. Очищенный коксовый газ (светильный газ) подается преимущественно в КБА-установку, в которой происходит отделение водорода от остаточного газа. КБА-установка может быть выполнена также в виде вакуумной КБА-установки. На напорной стороне адсорбционной установки получают чистый водород. При расширении высвобождается остаточный газ, который содержит метан и монооксид углерода, и в качестве исходного сырья вводится в доменный процесс.
Доменный процесс предназначен для производства синтез-газа. В доменную печь загружаются железные руды и углеродсодержащие восстановители, причем используемое в доменном процессе количество углеродсодержащих восстановителей больше необходимого для получения железа количества топлива. Далее в доменную печь подается технически чистый кислород для получения железа и удаленного в виде колошникового газа, богатого СО, синтез-газа. Дополнительно в доменную печь может подаваться СО и/или водяной пар для управления соотношением СО/H2 в покидающем доменную печь колошниковом газе, причем могут протекать следующие реакции:
C+CO2→2CO
C+H2O↔CO+H2
CO2+H2→CO+H2O
В предложенном способе за счет комбинации коксовального и колошникового газов доменного процесса использовано предпочтительно то, что в коксовой печи получают богатый водородом, а в доменной печи – богатый монооксидом углерода неочищенные газы. Кроме того, коксохимические заводы расположены, как правило, вблизи доменных печей, поскольку кокс требуется для доменного процесса. При осуществлении предлагаемого способа обеспечивается целенаправленная материальная утилизация газообразных побочных продуктов, возникающих при производстве кокса и железа.
Synthesis Gas – обзор
6 КОНВЕРСИЯ УГЛЯ С ИСПОЛЬЗОВАНИЕМ ТЕХНОЛОГИИ FT
Существует несколько различных технологических вариантов конверсии угля в синтез-газ, пригодный для синтеза FT. Все они будут включать в себя ту или иную форму технологии газификации, как обсуждается в главе 4. Уместно сначала получить некоторое представление о соображениях баланса массы и энергии, которые применяются к маршруту конверсии угля. Уголь – это богатое углеродом сырье, которое различается по составу, например.г. отношение углерода к водороду, но идеализированный случай чистого углеродного сырья можно использовать в качестве отправной точки для получения некоторых фундаментальных представлений о процессе. Таким образом, превращение углерода в олефиновые углеводороды может быть исследовано с использованием баланса масс и термодинамических соображений следующим образом:
Реакция баланса масс для идеальной паровой газификации:
- –
Газификация: 1,5C + 2h3O → CO + 2h3 + 0,5CO2
- –
FT: CO + 2h3 → (-Ch3 -) + h3O
(Обратите внимание, что эффективность угля составляет 67%)
Термодинамика для этой идеальной газификации следующая:
- –
ΔH = 158 кДж (эндотермическая реакция)
- –
ΔG = 104 кДж (реакция термодинамически невозможна)
Измените газификацию, чтобы сделать ее термодинамически возможной, добавив кислород:
- –
Газификация: 1.77 + 2h3O + 0,27 O2 → CO + 2h3 + 0,77CO2
(КПД по углероду снижается до 56%)
Термодинамика «возможной» газификации:
- –
ΔG = −2 кДж (реакция термодинамически возможна т.
е. ΔG 〈0)
- –
ΔH = 51 кДж (реакция все еще эндотермическая)
В настоящее время в действительности наиболее эффективным методом обеспечения тепла для эндотермической реакции является сжигание дополнительного углерода с кислородом на месте.Это приводит к следующим массовым балансам:
C + 4/3 h3O → 2/3 CO + 4/3 h3 + 1/3 CO2 → 2/3 (−Ch3−) + 2/3 h3O + 1/3 CO2. ↑ ↓ 1/3 C + 1/3 O2 → 1/3 CO2 120 кДж4 / 3 C + 4/3 h3O + 1/3 O2 → 2/3 O2 + 4/3 h3 + 2/3 CO2 → 2/3 (−Ch3−) + 2/3 h3O + 2/3 CO2 + 120 кДж ¯
Используя два атома углерода в качестве исходной основы, вышеуказанный баланс масс принимает вид:
2C + 2 h3O + 1/2 O2 → CO + 2h3 + CO2 → (−Ch3 -) + h3O + CO2 + 108 кДж
(КПД по углероду снижается до 50%, а термический КПД продукта / сырья составляет около 75%)
Вышеприведенное уравнение также можно изменить, уменьшив количество пара, подаваемого в газификатор, до дают:
2C + h3O + 1/2 O2 → 2CO + h3 → (−Ch3 -) + CO2 + 240 кДж
Однако в этой модифицированной реакции, которая дает синтез-газ с более низким соотношением H 2 / CO, экзотермический Реакция конверсии водяного газа (h3O + CO → h3 + CO2) исключается из стадии газификации, и это требует сжигания дополнительного углерода для образования CO 2 , чтобы закрыть энергетический баланс для этой стадии. Это снижает эффективность использования углерода примерно на 5%, то есть с примерно 50% до примерно 47%. Хорошо это или плохо, зависит от значения, которое может быть получено за счет дополнительного тепла, производимого реакцией конверсии водяного газа, которая теперь имеет место на этапе FT (240 кДж против 180 кДж).
Использованы следующие приблизительные допущения теплосодержания:
C = 400 кДж / моль
CH 4 = 800 кДж / моль
−CH 2 – = 600 кДж / моль
CO = 300 кДж / моль
H 2 = 240 кДж / моль
Предыдущие два уравнения баланса масс по существу иллюстрируют разницу между газификаторами Sasol-Lurgi, которые производят синтез-газ с H 2 / CO отношение близко к 2.0 по сравнению с высокотемпературными газификаторами с увлеченным потоком, которые производят синтез-газ с этим соотношением, близким к 0,5. Хотя есть небольшая разница в теоретической эффективности процесса по выбросам углерода, существуют и другие различия, когда принимаются во внимание практические балансы полезности. Например, энергия требуется для производства пара из воды и отделения кислорода от воздуха. Также с точки зрения капитальных затрат подход Sasol-Lurgi требует большей мощности по выработке пара для газификации и большего удаления диоксида углерода из синтез-газа, а также большего количества очистных сооружений для реакционной воды FT.
Это, очевидно, в высшей степени идеализированный анализ, например, уголь, возможно, лучше представить как CH, а не C. Однако увеличение содержания водорода в топливе не оказывает значительного влияния на термический КПД процесса (с точки зрения энергии в продуктах как доля энергии в корме), хотя это улучшает эффективность использования углерода. Это можно оценить, проанализировав метан в качестве исходного материала:
Ch5 + 1/3 CO2 +2/3 h3O → 4/3 CO + 8/3 h3 → 4/3 (-Ch3-) + 4/3 h3O ↑ ↓ 1/3 Ch5 + 2/3 O2 → 1/3 CO2 + 2/3 h3O 240 кДж4 / 3 Ch5 + 2/3 O2 → 4/3 CO + 8/3 h3 → 4/3 (-Ch3-) + 4/3 h3O + 240 кДж ¯
Использование одной молекулы метана в качестве исходной дает:
Ch5 + 1 / 2O2 → CO + 2 h3 → (−Ch3 -) + h3O + 108 кДж
Углеродная эффективность составляет 100 %, но термический КПД без учета тепла реакции FT все еще составляет 75%.
6.1 Комбинированное производство углеводородной жидкости и электроэнергии
Ниже приводится выдержка из статьи Стейнберга и Нела, опубликованной в FUEL [44]: Любое значимое использование огромных запасов угля в таких местах, как Китай, Индия, Австралия, Юг Африка и США предполагают преобразование в какую-либо другую форму энергии. Уголь в твердом виде имеет высокую плотность энергии и поэтому достаточно удобен в качестве топлива для обогрева. Проблема в том, что связанные с этим загрязняющие вещества сводят на нет какие-либо преимущества по сравнению с другими более чистыми видами топлива.Уголь скорее превращается в другие более чистые формы топлива, такие как жидкие углеводороды, синтетический природный газ (SNG) и электроэнергию. Первоначально эти конверсионные установки просто концентрировали загрязнители на одной крупномасштабной конверсионной площадке, позволяя конечному потребителю энергии получать более чистое топливо. Со временем все больший и больший успех был достигнут в очистке выбросов от крупномасштабных предприятий по переработке угля.
Нельзя избежать одного факта: каждая тонна углерода в добываемом угле рано или поздно упадет до 3.67 тонн углекислого газа в атмосфере (т.е. 44/12 – это соотношение молекулярной / атомной массы углекислого газа и углерода). Хотя некоторое внимание было уделено возможности секвестрации углекислого газа, в настоящее время это не является и, возможно, никогда не будет жизнеспособным вариантом. Конечно, стоимость секвестрации, вероятно, будет способствовать использованию других альтернатив ископаемому топливу, таких как сырая нефть и природный газ, хотя они все еще легко доступны.
Увеличение производства углекислого газа на единицу полезной энергии для угля по сравнению с другими видами топлива неизбежно [45]. Если предположить, что это приемлемо, становится важным обеспечить, чтобы при использовании угля он использовался с максимальной эффективностью.Совместное производство жидких углеводородов и электроэнергии из угля с использованием электростанций комбинированного цикла было предложено как чистый и эффективный подход [15–22].
Угольные электростанции в Южной Африке и других местах производят электроэнергию с одними из самых дешевых в мире, но такое крупномасштабное сжигание угля наносит ущерб окружающей среде. Альтернативный подход заключается в газификации угля для получения синтез-газа с низкой теплотворной способностью, который можно очищать перед сжиганием.Затем этот газ сжигается на электростанции с комбинированным циклом с использованием как паровых, так и газовых турбин для производства электроэнергии. Есть альтернативные варианты использования этого синтез-газа, которые могут предложить возможности, которые являются как экономически более привлекательными, так и приводят к более эффективному использованию угля. Там, где экономика региона зависит от использования угля, есть веские основания для перехода на более эффективные и менее загрязняющие технологии переработки угля по мере их появления.
Синтез-газ также может быть получен из природного газа, и следующее сравнение было опубликовано ранее Shell [45]:
Производство синтез-газа + Фишер-Тропш | Тепловая эффективность * | Относительные капитальные затраты |
---|---|---|
Уголь: 2 (-CH-) + O2 → 2CO + h3 → (-Ch3-) + CO2 | 60% | 200 |
Природный газ: Ch5 + 1/2 O2 → CO + 2h3 → (-Ch3-) + h3O | 80% | 100 |
Это, кажется, рисует мрачную картину использования угля, но игнорирует два фактора. Во-первых, высокая удельная энергия угля позволяет доставлять сырье на конверсионную установку с меньшими затратами. Во-вторых, более низкая энергоэффективность игнорирует возможность преобразовать часть побочного тепла в электроэнергию. (Также анализ в разделе 6 показывает, что при использовании идеализированного подхода, учитывающего реакции паровой газификации, тепловой КПД, выраженный в единицах (теплотворная способность продукта) / (теплотворная способность сырья), как для угля, так и для природного газа, дает один и тот же теоретический максимум. около 75%.)
Потенциальное использование некоторого количества побочного тепла, которое обычно присутствует в горячих выходящих газах из высокотемпературных газификаторов, заключается в генерировании пара для реакции конверсии водяного газа, которая будет проводиться ниже по потоку от газификатора, чтобы изменить указанную выше реакцию конверсии угля, как следующим образом:
h3O + 2CO + h3 → CO + 2h3 + CO2 → (-Ch3 -) + h3O ↓ Удалено
Это становится эквивалентным маршруту природного газа для стадии конверсии синтез-газа, но используется вдвое больше кислорода подготовка синтез-газа и затраты на производство пара и удаление диоксида углерода приводят к дополнительным штрафным затратам. Ясно, что из анализа в разделе 6, где требуется гораздо меньше кислорода, предпочтительно, чтобы паровые реакции происходили внутри газификатора. В реальных приложениях соотношение потребления кислорода высокотемпературными газификаторами и кислородными установками риформинга составляет около 1,7. С другой стороны, газификаторы Sasol-Lurgi с подачей через шток потребляют около четверти количества кислорода, используемого высокотемпературными газификаторами.
Снижение затрат на генерацию пара в некоторой степени сводится на нет тем фактом, что генерация пара требуется в любом случае для отвода тепла, генерируемого реакцией Фишера-Тропша, и для охлаждения горячего синтез-газа, выходящего из газогенератора.Очистка синтез-газа от кислых газов также требуется в любом случае для использования в газовых турбинах для производства электроэнергии.
Концепция производства жидких углеводородов Фишера-Тропша и электроэнергии из синтез-газа, полученного из угля, существует уже довольно давно. Патент 1978 г. от Chevron указал на преимущества использования этой концепции для эффективного управления колебаниями энергопотребления [17]. Министерство энергетики США (DOE) при поддержке исследований, проведенных по контракту MITER Corporation [15, 16] и такими компаниями, как Texaco [18], Air Products [19, 20] и Rentech [21, 22], показало, что реакторная технология LTFT может быть используются вместе с газификаторами угля или нефтяного кокса для совместного производства жидких углеводородов и электроэнергии.Fluor Daniel [46] предложил использовать HTFT для этой цели.
Процесс LTFT [47] и процесс HTFT [1] были описаны в публикации 1999 г. по теме последних достижений в синтезе Фишера-Тропша. Возможно, что комбинированное производство жидких углеводородов и электроэнергии из угля может конкурировать с конверсией природного газа только в жидкие углеводороды. Часто нет спроса на электроэнергию на участке, где находится удаленный природный газ, но есть спрос рядом с потенциальными объектами конверсии угля. Этот подход к конверсии угля был изучен для двух вариантов конверсии Фишера-Тропша, то есть LTFT и HTFT, оба с использованием катализаторов на основе железа.
6.2 Изученные случаи
В обоих случаях предполагалось использование газификатора Texaco для получения синтез-газа следующего состава (мол.%):
h3 | 29,26 |
CO | 37,36 |
CO2 | 13,30 |
Ch5 | 0.16 |
h3O | 19,43 |
Инертный | 0,49 |
Этот состав был получен из брошюры Texaco для угля со следующим составом:
Сухой анализ | ||
Углерод | 78,08 | |
Водород | 5,26 | |
Азот | 0,85 | |
Сера | 0,47 | |
Зола | 7,11 |
Для случая LTFT этот газ подается в двухступенчатую реакторную систему для образования жидких углеводородных продуктов. 83,3% реагентов превращаются с использованием этого подхода. Остаточный газ направляется в газовую турбину для выработки энергии. Другими источниками энергии являются пар, образующийся в процессе охлаждения синтез-газа из газификатора и при отводе тепла, генерируемого в реакторах Фишера-Тропша.
Для случая HTFT аналогичное количество углеводородного продукта может быть произведено за одну стадию с использованием только двух реакторов максимального размера, используемых Sasol на своем предприятии в Секунде, Южная Африка.92,2% реагентов конвертируются с использованием этого конструктивного подхода. В этом случае синтез-газ подвергается реакции конверсии водяного газа перед удалением кислого газа для увеличения отношения водорода к монооксиду углерода в синтез-газе. Было также обнаружено, что это значительно увеличивает требования к коммунальным службам на стадии удаления кислого газа.
Балансы массы и энергии для двух случаев показаны в таблицах 3 и 4. Они не обязательно полностью оптимизированы, но считаются реалистичными для обеспечения справедливой основы для сравнения.
Таблица 3. Баланс массы и энергии для корпуса LTFT
Сводка по потоку сырья | ||||||
---|---|---|---|---|---|---|
Номер потока | Название потока | Расход кг / ч | LHV кДж / кг | LHV | ||
1 | Уголь | 928063 | 30506 | 7864 | ||
2 | Кислород | 951597 | 0 | 0 | 9015 9015 | 0 | 9015
Летний поток газа | ||||||||||||||
---|---|---|---|---|---|---|---|---|---|---|---|---|---|---|
Номер потока | Название потока | Расход, кнм3 / ч | LHV кДж / нм3 | LHV15 MW | 9015 2243 | 9843 | 6133 | |||||||
5 | C02 | 364 | 0 | 0 | ||||||||||
6 | Синтез-газ | 1879 | 11781 | 6148 | ||||||||||
7 | Отводной газ | 695 | 7831 | 1514 | Название потока | баррелей / день | LHV МДж / баррель | LHV MV | Тонна / день (метрическая) | МДж / кг | ||||
8 | 0 | 9 Конденсат 9782090 | 40.![]() | |||||||||||
9 | Воск | 35844 | 5809 | 2410 | 4740 | 43,8 | ||||||||
Всего | 5408214 | 9017 9017 9015 9014 9015|||||||||||||
Stream | LHV MW | % | ||||||||||||
Уголь | 7884 | 100,0 | ||||||||||||
Конденсат | 979 | 12.4 | ||||||||||||
Воск | 2410 | 30,6 | ||||||||||||
Power | 566 | 7,2 | ||||||||||||
Общий | 3955 | Таблица 50000 энергии |
Сводка по потоку | ||||||
---|---|---|---|---|---|---|
Номер потока | Название потока | Расход (кг / ч) | LHV (кДж / кг) | LHV (MW) | 928063 | 30506 | 7864 |
2 | Кислород | 951597 | 0 | 0 | ||
3 | 9014 9015 9015 9015 9015 9015 | Летний поток газа | ||||
Номер потока | Название потока | Расход (кнм3 / ч) | LHV (кДж / нм3) 9 0148 | LHV (МВт) | ||
4 | Неочищенный газ | 2243 | 9843 | 6133 | ||
5 | Shift Gas0 | 9015 9015 9015 9015 9015 9015 9015 9015 9015 9015 9015 9015 9015 9015 9015 9015 9015 | CO 2 | 799 | 0 | 0 |
7 | Синтез-газ | 1881 | 11341 | 5925 | ||
149015 9015 9015 9015 9015 9015 9015 9015 9015 9015 9015 9015 9015 9015 9015 |
Текущий поток жидкости | ||||||
---|---|---|---|---|---|---|
Номер потока | Название потока | баррелей в день | LHV (МДж / баррель) | LHV MV | Тонна / день ( | МДж) МДж|
9 | Декантное масло | 1799 | 6099 | 127 | 249 | 44.![]() |
10 | Стабилизированное легкое масло | 34070 | 4859 | 1918 | 3899 | 42,5 |
11 | Конденсат | 119015 9015 9015 9015 9015 9015 9015 9015 9015|||||
Всего | 60871 | 3233 |
Тепловой КПД | |||||||||||
---|---|---|---|---|---|---|---|---|---|---|---|
Поток | |||||||||||
LHV MW | |||||||||||
Жидкие продукты | 3233 | 41,1 | |||||||||
Power Export | 393 | 5,02 | |||||||||
Общая | 3626 | 46,1 |
Паровая система | ||||
---|---|---|---|---|
Источники насыщенного пара высокого давления | Количество (тонны / ч) | |||
Выход газа котел-утилизатор | 2449 | |||
Утилизация тепла газовой турбины | 814 | |||
Потребители перегретого пара ВД | ||||
Приводы турбины блока разделения воздуха | 58 | |||
Электрогенерирующая турбина | 1046 | |||
Насыщенный пар среднего давления от охлаждения реактора FT | 1607 | |||
Мощность перегретого пара MP601 | Электроэнергия | |||
Другой MP Steam Us В том числе удаление CO 2 | 556 |
Источники электроэнергии | |||||||||||
---|---|---|---|---|---|---|---|---|---|---|---|
Источник | Количество (МВт) | ||||||||||
Паровая турбина 9015 л.![]() | 123 | ||||||||||
Газовая турбина | 309 | ||||||||||
Минус: Внутреннее использование | 100 | ||||||||||
Экспорт чистой энергии | 566 | ||||||||||
Количество (МВт) | |||||||||||
Пароперегреватель высокого давления | 438 | ||||||||||
Пароперегреватель среднего давления | 16 | ||||||||||
Газовая турбина | 1075 | HTFT Utility Balnces
6.![]() Ожидается, что процессы конверсии природного газа будут иметь тепловой КПД в диапазоне от 60 до 66%. При нынешнем состоянии технологий рентабельные объекты будут иметь тепловой коэффициент полезного действия, близкий к 60%. Конверсия угля явно менее эффективна. Кажется, достижима эффективность около 50%. Следовательно, стоимость сырья на единицу энергии должна быть меньше, чтобы компенсировать этот дефицит эффективности. Однако это не нереально. Существующие установки по переработке угля, работающие с КПД около 40%, приносят положительный доход. По сравнению с конверсией природного газа капитальные затраты на конверсию угля, основанные на аналогичных количествах энергетического продукта, выше по ряду причин. Во-первых, это необходимость удаления кислого газа из синтез-газа. Этот этап не требуется для подачи чистого природного газа. Капитальные затраты на производство синтез-газа также значительно выше, в основном из-за более высокой потребности в кислороде (почти в 1,7 раза). При сравнении вариантов HTFT и LTFT становится ясно, что путь LTFT более эффективен при использовании газификатора с увлеченным потоком. Основная причина более низкой эффективности варианта HTFT заключается в том, что стадия удаления кислого газа становится более энергоемкой. Однако, как упоминалось ранее, капитальные затраты на участок LTFT Фишера-Тропша выше.Только подробное исследование, выходящее за рамки данной статьи, сможет определить, может ли более высокая эффективность маршрута LTFT компенсировать более высокие капитальные затраты. Кроме того, анализ в Разделе 6.4 показывает, что сочетание HTFT-синтеза с газификаторами Sasol-Lurgi является привлекательным вариантом с точки зрения термического КПД. Экономический успех фабрики по переработке угля неизбежно будет зависеть от цены, полученной за продукцию. Кажется маловероятным, что цена на жидкие углеводороды будет достаточной для обеспечения надлежащей прибыли на вложенный капитал, в то время как энергетические ресурсы сырой нефти и природного газа все еще легко доступны. Однако, если будет оказана некоторая помощь в покрытии начальных капитальных затрат, преобразование угля в жидкие углеводороды вместе с электроэнергией будет более эффективным вариантом по сравнению с другими вариантами преобразования угля.Эффективность преобразования угля выше при добыче жидких углеводородов, чем при производстве только электроэнергии. 6.4 Конверсия угля с использованием газификаторов Sasol-Lurgi Было проведено исследование с использованием аналогичных допущений для угольной установки, использующей газификаторы Sasol-Lurgi вместо газификаторов с унесенным потоком. Из информации, представленной ниже, можно увидеть, что при использовании синтеза LTFT газификаторы с увлеченным потоком приводят к наивысшему тепловому КПД, примерно 52,5% по сравнению с 49,6% при использовании газификаторов Sasol-Lurgi. Это предполагает использование лучистого охлаждения в котле-утилизаторе. Если используется закалочная конструкция Texaco, то эффективность снижается до 47,9%. Ожидается, что стоимость подготовки синтез-газа с использованием газификаторов Sasol-Lurgi будет меньше, чем при проектировании Texaco с использованием радиационного охлаждения, а газификаторы Sasol-Lurgi имеют лучшие показатели с точки зрения готовности оборудования. В целом наиболее эффективным подходом является использование газификаторов Sasol-Lurgi в сочетании с синтезом HTFT, обеспечивающим общую эффективность около 53,5%. Таблица 7. Обзор потоков для газификации Sasol-Lurgi с синтезом LTFT
Таблица 8. Сводная информация о потоках для газификации Sasol-Lurgi С синтезом HTFT
Таблица 9. Корпус Texco LTFT с более высокой эффективностью турбины, радиационным охладителем и расширением потока угля как lurgi
Если исключить радиантный котел, то есть предполагается, что неочищенный газ будет закален для его охлаждения, результаты изменятся следующим образом: FT Краткое описание продукта
Тепловая эффективность
Существует много нежелательных побочных продуктов процесса газификации Sasol-Lurgi, таких как битум и водный газовый щелок, перерабатываемый на установке Phenosolvan. Кроме того, эти газификаторы не могут работать с мелким углем. Технологическую схему можно значительно упростить, если сточные воды от газификации вместе с другими нежелательными побочными продуктами газификации и мелким углем подавать в газификаторы типа Texaco, работающие параллельно с газификаторами Sasol-Lurgi. 6.5 Сравнение с использованием удаленного природного газа Импорт сжиженного природного газа (СПГ) становится все более популярным в качестве топлива для производства электроэнергии. Маловероятно, что СПГ будет поставляться по цене ниже 3 долларов за ГДж из-за капиталоемкости этой технологии. В настоящее время цена выше этой. Принимая во внимание эффективность преобразования в электричество 60% для природного газа и 40% эффективности преобразования для угля, цена угля, которая приводит к такой же стоимости сырья, составляет 61 доллар за метрическую тонну (с использованием теплотворной способности 30506 кДж / кг). Когда дело доходит до производства жидких углеводородов из угля или природного газа, можно ожидать ценовой диапазон от 0,5 до 1,0 доллара на обедненный природный газ в удаленных местах. Предполагая, что эффективность преобразования составляет 60% для природного газа и 40% для угля, это соответствует цене угля от 10 до 20 долларов за метрическую тонну для угля, имеющего такую же стоимость сырья, как и природный газ.Это соответствует ценам на уголь, доступным в Китае, но ниже, чем преобладающие цены в США. Комбинируя производство углеводородов с производством электроэнергии, эффективность преобразования угля может быть увеличена с примерно 40% до примерно 50%. Это увеличивает указанные выше показатели паритета затрат на сырье на 25%. Согласно Shell [1] капитальные затраты на переработку угля могут быть вдвое больше, чем на переработку природного газа в жидкие углеводороды. Для сравнения, следующие блоки, предложенные в [5]. 3 удаляются, если хвостовой газ Фишера-Тропша подается в газовую турбину для производства электроэнергии:
При таком подходе по-прежнему возможно превышение 80% конверсии реагентов в чистом синтез-газе, поступающем в установку Фишера-Тропша. Добыча жидких углеводородов из угля, как описано выше, имеет два дополнительных преимущества. Во-первых, рынок огромен, и предприятия могут использовать эффект масштаба для очень крупных предприятий, производящих углеводородное топливо вместе с электричеством. Однако огромные капитальные вложения – еще одна причина, по которой, вероятно, потребуется государственная помощь для финансирования такого предприятия по переработке угля. 6.6 Выводы по конверсии угля с использованием фут-технологии Безусловно, конверсия угля в углеводородные жидкости и электричество является экономически привлекательной с точки зрения доходов / денежных затрат. Однако для получения выгоды от эффекта масштаба требуются крупные капитальные вложения, а окупаемость вложенного капитала не является особенно привлекательной. Поэтому ожидается, что эти угольные установки станут реальностью только в том случае, если будет какая-либо форма государственной помощи с начальными капиталовложениями, например, ссуды под низкие проценты.Это будет мотивировано независимостью от импортируемой энергии и более эффективным и чистым использованием местных энергетических ресурсов. Китайское правительство приняло этот подход, и Китай, вероятно, станет пионером этого технологического варианта. Синтез-газ – обзор2.3.1 Биогаз и биометанБиогаз представляет собой смесь горючих газов, образующихся в результате анаэробного сбраживания (AD), биологического процесса, при котором разложение органического субстрата бактериями происходит в анаэробной среде (таблица 2.6). Его продукция осуществляется в основном на свалках ТБО, осадках сточных вод AD, совместном переработке органических фракций ТБО (MSWOF) и на заводах по биогазификации зоотехнических отходов. Таблица 2.6. Состав биогаза [19]
Европа как континент является основным мировым производителем биогаза (около 12 Мтнэ / год), 53% которого вырабатывается в Германии. Только в ЕС-27 ежегодно производится более 1,5 x 10 9 т навоза с общим потенциалом выработки энергии около 830 ПДж [23]. К концу 2014 года в Европе насчитывалось более 17 000 действующих биогазовых установок, с общим производственным потенциалом, оцениваемым к 2020 году в 770 ПДж / год, по сравнению с 92 ПДж / год в 2002 году. в настоящее время Германия и Италия, в то время как Великобритания является крупнейшим производителем биогаза со свалок (84% ее национального производства) [24]. 2.3.1.1 Синтез-газ Синтез-газ – это короткое название продукта газификации, в основном из отходов биомассы, известного как «синтез-газ», состоящего из смеси H 2 , CO и CO 2 , которые могут быть используется в качестве потенциального промежуточного продукта при преобразовании биомассы в топливо.В первую очередь синтез-газ используется для производства других видов топлива, а именно метанола и дизельного топлива. В некоторых промышленных условиях (сталелитейное производство, нефтепереработка и т. Производство дизельного топлива из синтез-газа основано на процессе Фишера-Тропша, серии химических реакций, превращающих CO и H 2 в жидкий углеводород. Метан со свалок может служить сырьем для производства дизельного топлива, технически считающегося биодизелем, поскольку его не получают из ископаемого топлива.Новым применением синтез-газа является непосредственное приведение в действие водородных топливных элементов; водород просто улавливается из газа и очищается для использования в топливных элементах. Конечно, это имеет тенденцию противоречить цели топливных элементов «нулевые выбросы» и поэтому широко не используется за пределами исследований. Произошла ошибка при настройке пользовательского файла cookie Этот сайт использует файлы cookie для повышения производительности. Если ваш браузер не принимает файлы cookie, вы не можете просматривать этот сайт. Настройка вашего браузера для приема файлов cookieСуществует множество причин, по которым cookie не может быть установлен правильно.Ниже приведены наиболее частые причины:
Почему этому сайту требуются файлы cookie?Этот сайт использует файлы cookie для повышения производительности, запоминая, что вы вошли в систему, когда переходите со страницы на страницу.Чтобы предоставить доступ без файлов cookie потребует, чтобы сайт создавал новый сеанс для каждой посещаемой страницы, что замедляет работу системы до неприемлемого уровня. Что сохраняется в файле cookie?Этот сайт не хранит ничего, кроме автоматически сгенерированного идентификатора сеанса в cookie; никакая другая информация не фиксируется. Как правило, в cookie-файлах может храниться только информация, которую вы предоставляете, или выбор, который вы делаете при посещении веб-сайта.Например, сайт
не может определить ваше имя электронной почты, пока вы не введете его. Произошла ошибка при установке пользовательского файла cookieЭтот сайт использует файлы cookie для повышения производительности. Если ваш браузер не принимает файлы cookie, вы не можете просматривать этот сайт. Настройка вашего браузера для приема файлов cookieСуществует множество причин, по которым cookie не может быть установлен правильно.Ниже приведены наиболее частые причины:
Почему этому сайту требуются файлы cookie? Этот сайт использует файлы cookie для повышения производительности, запоминая, что вы вошли в систему, когда переходите со страницы на страницу.Чтобы предоставить доступ без файлов cookie
потребует, чтобы сайт создавал новый сеанс для каждой посещаемой страницы, что замедляет работу системы до неприемлемого уровня. Что сохраняется в файле cookie?Этот сайт не хранит ничего, кроме автоматически сгенерированного идентификатора сеанса в cookie; никакая другая информация не фиксируется. Как правило, в cookie-файлах может храниться только информация, которую вы предоставляете, или выбор, который вы делаете при посещении веб-сайта.Например, сайт не может определить ваше имя электронной почты, пока вы не введете его. Разрешение веб-сайту создавать файлы cookie не дает этому или любому другому сайту доступа к остальной части вашего компьютера, и только сайт, который создал файл cookie, может его прочитать. исследователей из Калифорнийского университета в Лос-Анджелесе помогают разработать усовершенствованный процесс производства синтез-газаИсследователи из Калифорнийского университета в Лос-Анджелесе и других университетов разработали стабильный и экологически безопасный метод производства синтез-газа. Синтез-газ, или сокращенно «синтез-газ», представляет собой промышленный материал, состоящий из монооксида углерода и газообразного водорода. Синтез-газ, полученный из угля, обеспечивает альтернативный способ производства бензина для стран и регионов, не имеющих доступа к нефти, – сказала Эмили Картер, автор статьи, исполнительный вице-канцлер и проректор Калифорнийского университета в Лос-Анджелесе. «Мы берем два очень сильных парниковых газа и превращаем их в синтез-газ», – сказал Картер. Исследователи из Калифорнийского университета в Лос-Анджелесе, а также Калифорнийского университета в Санта-Барбаре и Университета Райса усовершенствовали процесс сухого риформинга, способ производства синтез-газа, сделав его стабильным и более экологически чистым. Новый метод был подробно описан в исследовании, опубликованном в журнале Nature Energy 6 января 2005 года. В настоящее время наиболее распространенным методом производства синтез-газа является паровая конверсия метана, сказал Линан Чжоу, первый автор исследования и научный сотрудник Университета Райса. Эта высокая температура обычно достигается за счет сжигания традиционных ископаемых видов топлива, которые выделяют в атмосферу большое количество углекислого газа, сказал Картер. По ее словам, альтернативный метод, сухой риформинг метана, особенно если он может проводиться при низких температурах, обеспечивает гораздо более экологичный способ производства синтез-газа. В процессе сухого риформинга потребляются диоксид углерода и метан.По словам Картера, углекислый газ можно извлекать из промышленных процессов, таких как производство стали и цемента, а также из электростанций, использующих ископаемое топливо. Метан может улавливаться со свалок, заброшенных газовых скважин и в качестве побочных продуктов человеческой деятельности, такой как разведение крупного рогатого скота, сказала она. Однако текущий сухой риформинг страдает от «закоксовывания», когда углеродные соединения накапливаются и быстро покрывают металлический катализатор реакции, не позволяя процессу продолжаться, сказал Чжоу. Чжоу сказал, что его группа изучила эффекты добавления рутения в катализатор на основе меди. Затем команда разработала катализатор, легированный рутением, в материал с особыми свойствами поверхности, чтобы решить проблему коксования. Согласно исследованию, усовершенствованный процесс стабилен и может длиться около 50 часов. Более того, исследователи обнаружили, что, направляя свет на поверхность нового катализатора, можно значительно снизить температуру, необходимую для начала реакции. Свет также возбуждает атомы водорода и предотвращает их реакцию с атомами кислорода с образованием воды. Это также предотвратило закоксовывание, поскольку атомы углерода вступали в реакцию с кислородом, а не друг с другом. Джон Марк Мартирез, помощник научного сотрудника Калифорнийского университета в Лос-Анджелесе и второй автор статьи, проанализировал реакцию с помощью вычислительных инструментов, имитирующих распределение электронов в молекулах и других химических системах. Мартирез сказал, что моделирование показало, что присутствие рутения может значительно улучшить процесс разрыва углеродно-водородной связи, который является начальным этапом производства синтез-газа. Поскольку частицы рутения тонко распределены по поверхности катализатора, атомы углерода, образовавшиеся в процессе разрыва связей, не могут образовывать богатые углеродом соединения, покрывающие поверхность, сказал Мартирез. Рутений связывает атомы углерода сильнее, чем медь. В результате атомы углерода оставались концентрированными в центрах рутения, удаленных друг от друга, и имели достаточно времени для образования окиси углерода, сказал Мартирез. Анализ показал, что частицы меди могут эффективно поглощать энергию света и направлять собранную энергию в сторону рутениевого участка, чтобы облегчить разрыв связи. Медно-рутениевое соединение также может быть хорошим катализатором для других химических процессов, таких как синтез аммиака, сказал Чжоу. Что такое синтез-газ – информация о биотопливеСинтез-газ – это сокращение от синтез-газа, который представляет собой смесь, состоящую из моноксида углерода, диоксида углерода и водорода. Синтез-газ получают путем газификации углеродсодержащего топлива до газообразного продукта, имеющего некоторую теплотворную способность. Некоторые из примеров производства синтез-газа включают газификацию выбросов угля, выбросы отходов для энергетической газификации и паровой риформинг кокса. Название «синтез-газ» происходит от его использования в качестве промежуточного продукта при производстве синтетического природного газа и для производства аммиака или метанола. Это газ, который можно использовать для синтеза других химических веществ, отсюда и название синтез-газ, которое было сокращено до синтез-газа. Синтез-газ также является промежуточным звеном при создании синтетической нефти для использования в качестве смазочного материала или топлива. Синтез-газ имеет 50% плотности энергии природного газа. Его нельзя сжигать напрямую, но он используется в качестве источника топлива.Другое использование – в качестве промежуточного продукта для производства других химикатов. Производство синтез-газа для использования в качестве сырья в производстве топлива осуществляется путем газификации угля или городских отходов. В этих реакциях углерод соединяется с водой или кислородом с образованием диоксида углерода, монооксида углерода и водорода. Синтез-газ используется в качестве промежуточного продукта в промышленном синтезе аммиака и удобрений. Во время этого процесса метан (из природного газа) соединяется с водой с образованием окиси углерода и водорода. Процесс газификации используется для преобразования любого материала, содержащего углерод, в более длинные углеводородные цепи. Одно из применений синтез-газа – это топливо для производства пара или электричества. Другое применение – это базовый химический строительный блок для многих нефтехимических и нефтеперерабатывающих процессов. Основным сырьем, используемым для газификации (создания синтез-газа), является уголь, материалы на основе нефти или другие материалы, которые могут быть выброшены как отходы.Из этих материалов готовят сырье. Он вводится в газификатор в сухом виде или в виде суспензии. В газификаторе это сырье реагирует в среде с недостатком кислорода с паром при повышенных давлении и температуре. Полученный синтез-газ состоит на 85% из моноксида углерода и водорода и небольших количеств метана и диоксида углерода. Синтез-газ может содержать некоторые следовые элементы примесей, которые удаляются путем дальнейшей обработки и либо восстанавливаются, либо направляются в газогенератор.Например, сера извлекается в элементарной форме или в виде серной кислоты, и обе они могут быть проданы. Синтез-газ – это основной источник серной кислоты. Если синтез-газ содержит значительное количество азота, азот необходимо отделить, чтобы избежать образования оксидов азота, которые являются загрязнителями и способствуют образованию кислотных дождей. Если синтез-газ будет использоваться для выработки электроэнергии, то он обычно используется в качестве топлива в конфигурации выработки электроэнергии IGCC (интегрированный комбинированный цикл газификации).Затем энергия используется фактором, производящим синтез-газ, тем самым снижая эксплуатационные расходы. Существуют коммерчески доступные технологии обработки синтез-газа для производства промышленных газов, удобрений, химикатов, топлива и других продуктов. Производство синтез-газа из различного сырья биомассыИсследовательская статья
Разложение пяти различных образцов биомассы изучалось в горизонтальном лабораторном реакторе.Образцы включали траву альфа, солому, водоросли Posidonea Oceanic, отходы городских и сельскохозяйственных обрезок и отходы обрезки леса. Изучали пиролиз в инертной атмосфере и горение в присутствии кислорода. Использовались разные скорости нагрева за счет изменения скорости подачи. Были проанализированы основные газовые соединения. Результаты экспериментов показывают, что количество образующегося CO ниже у менее плотных частиц. Также обнаружено, что при увеличении скорости подачи образуется больше углеводородов, в частности метана, в то время как производство водорода уменьшается. Образец цитирования: Juan A.Конеса, А. Домене. Производство синтез-газа из различного сырья биомассы [J]. AIMS Energy, 2013, 1 (1): 17-27. DOI: 10.3934 / энергия.2013.1.17 Аннотация Разложение пяти различных образцов биомассы изучалось в горизонтальном лабораторном реакторе. Список литературы
|
Добавить комментарий