Регулировка клапанов краз 65055 – Регулировка зазоров клапанов ЯМЗ 238 своими руками
Регулировка зазоров клапанов ЯМЗ 238 своими руками
Дизельные двигатели серии ЯМЗ 238 появились еще в 60 годах прошлого века. Они использованы в грузовых автомобилях Урал, МАЗ, КАМАЗ, КрАЗ, в тракторах К-700. Необходимость регулировки клапанов на ЯМЗ 238 обусловлена высокими температурами и нагрузками, сочетание которых изменяет положение элементов ГРМ относительно друг друга.
Схема устройства ГРМ ЯМЗ 238
Газораспределительный механизм (ГРМ) двигателя ЯМЗ 238 обеспечивает своевременный и полноценный впуск рабочей свечи в цилиндры и выпуск из камеры сгорания отработанных газов. Специфика ГРМ состоит в верхнем расположении системы клапанов, нижней установке распредвала и наличии регулировочного механизма на передающих рычагах (коромыслах). В состав ГРМ входят:
Газораспределительный механизм ЯМЗ 238
- Распределительный вал.
- Толкатели.
- Штанги толкателей.
- Коромысла.
- Клапаны.
Основным рабочим элементом системы является распределительный вал, кулачки которого передают импульсы на толкатели. Те, в свою очередь, воздействуют на клапаны, возвращаемые на исходную позицию при помощи пружин. Регулировка клапанов дизеля ЯМЗ-238 обеспечивает оптимальный режим подачи топливной смеси и полный вывод отработанных газов, что позволяет продлить срок службы двигателя, получить оптимальный расход топлива.
По каким причинам нужно проводить регулировку клапанов
Работа элементов механизма газораспределения происходит в сложных условиях. Помимо высоких механических нагрузок, все детали подвергаются значительному нагреву, вызывающему соответствующее тепловое расширение материала.
Система собрана из нескольких элементов, при изготовлении которых используется металл разных марок. Термическая обработка и химический состав деталей неоднородны, при нагревании точность подгонки искажается. Изменение размеров деталей приводит к нарушению настройки механизма, изменяются параметры тепловых зазоров. При их увеличении появляется специфический стук, режим работы камеры сгорания ухудшается.
Уменьшение зазоров нарушает герметичность контакта клапана и седла, что в конечном счете приводит к прогару. Эти причины приводят к необходимости постоянного наблюдения за состоянием ГРМ и регулировки клапанного механизма при изменении тепловых компенсаторов.
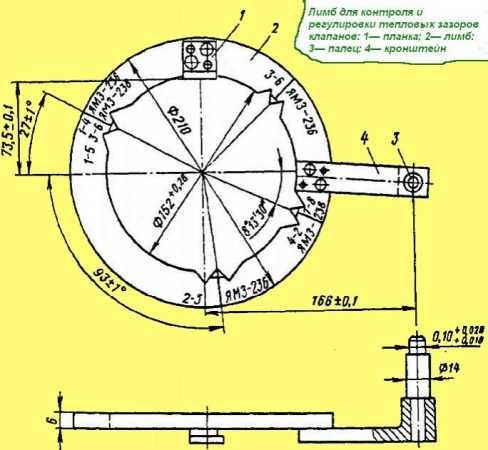
Лимб для контроля и регулировки тепловых зазоров клапанов двигателя ЯМЗ 238
Проверка величин тепловых компенсаторов
Прежде, чем приступить к проверке величин зазоров, следует выполнить некоторые подготовительные действия:
- Отключить подачу топлива, обесточив топливный насос. Для этого следует повернуть вниз скобу кулисы на регуляторе вращения.
- Остудить двигатель до температуры около 20–30°С. Работы начинаются не ранее, чем через час после остановки двигателя.
- Снять крышку с блока клапанов и проверить усилие затяжки на осях коромысел. Оптимальное значение — 120–150 Нм.
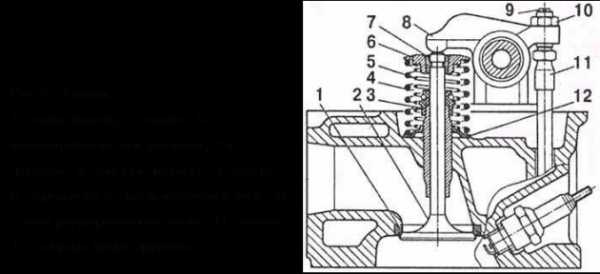
Из чего состоит клапан
Проверка зазора производится в определенном положении цилиндра — на такте сжатия. Номера цилиндров определяются при взгляде со стороны вентилятора (с передней части автомобиля). Ближний цилиндр слева будет первый, справа — пятый.
Положение клапанов регулируется поворотом коленвала по часовой стрелке, если смотреть со стороны передка машины. Движение вала необходимо продолжать до момента полного закрытия впускного клапана. Торец клапана, взаимодействующий с коромыслом, максимально поднимается вверх. После достижения нужного положения необходимо довернуть коленвал еще на треть оборота.
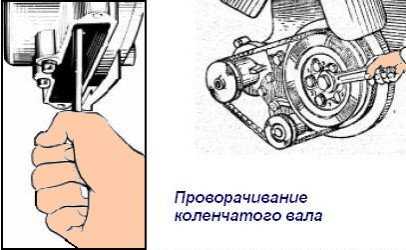
Проворачивание коленчатого вала — один из этапов регулировки клапанов ЯМЗ-238
Паспортная величина зазора составляет 0,25–0,30 мм. Для измерения используются специальные щупы, которые вставляются в зазоры. По усилию, с которым щуп входит в щель, определяется ее размер. При нормальной настройке щуп 0,25 входит достаточно легко, а 0,30 — с усилием.
Проверка и настройка тепловых компенсаторов производится поочередно на всех цилиндрах в последовательности 1–5–4–2–6–3–7–8. Необходимость регулировки зазоров клапанного механизма выявляется путем тщательного обследования каждого из них. Возможно, что вмешательство понадобится лишь на некоторых узлах.
Как проходит регулировка клапанов ЯМЗ-238
Обнаруженные несоответствия в величинах тепловых компенсаторов требуют немедленного исправления. Порядок регулировки клапанов на ЯМЗ 238:
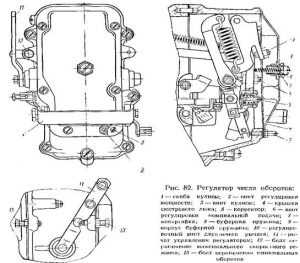
Регулятор числа оборотов ЯМЗ-238
- Отвернуть стопорную гайку регулировочного винта.
- Вставить щуп в зазор.
- Вращая регулировочный винт, добиться оптимальной величины зазора.
- Затянуть колпачковую гайку регулировочного винта, удерживая его в неподвижном состоянии при помощи отвертки.
Во время настройки необходимо прижать коромысла выпускных клапанов к стопорному кольцу, а впускных — к торцу оси (по левой стороне), или в обратном порядке, если регулируются зазоры по правому ряду цилиндров.
После настройки следует еще раз проверить состояние зазоров, запустить двигатель и определить качество работы на слух. При обнаружении характерного стука клапанов всю процедуру необходимо произвести заново.
Видео по теме: Регулировка клапанов ЯМЗ 238
specnavigator.ru
Регулировка клапанов дизеля ЯМЗ-238
Тепловые зазоры в клапанном механизме служат для обеспечения герметичной посадки клапана на седло, при расширении деталей привода клапанов во время работы двигателя.
Величина теплового зазора у впускного и выпускного клапанов устанавливается одинаковой и регулируется в пределах 0,25…0,30 мм.
При повторной проверке зазоров после прокрутки коленчатого вала отрегулированного двигателя возможно изменение их до пределов 0,20…0,35 мм из-за погрешности формы и расположения поверхностей деталей газораспределительного механизма, что является допустимым.
При слишком больших тепловых зазорах уменьшается высота подъема клапанов, вследствие чего ухудшаются наполнение и очистка цилиндров, растут ударные нагрузки и увеличивается износ деталей газораспределительного механизма.
Кроме того, уменьшение зазора в приводе выпускных клапанов может привести к перегреву клапанов и их прогару.
Тепловые зазоры регулировать на холодном двигателе или не ранее, чем через 1 час после его остановки.
При регулировке тепловых зазоров и повторной их проверке коромысла клапанов рекомендуется прижать:
• на головке правого ряда цилиндров коромысла выпускных клапанов к торцу оси, впускных клапанов – к упорной шайбе;
• на головке левого ряда цилиндров коромысла выпускных клапанов к упорной шайбе, впускных клапанов – к торцу оси.
Выпускные клапаны правого ряда цилиндров расположены ближе к вентилятору, левого ряда цилиндров – к маховику.
Последовательность регулировки:
1. Выключить подачу топлива.
2. Отвернуть болты крепления крышек головок цилиндров и снять крышки.
3. Проверить момент затяжки болтов крепления осей коромысел, который должен быть 120…150 Нм (12…15 кгс·м).
4. Проворачивая коленчатый вал по часовой стрелке (при виде со стороны вентилятора) спереди ключом за болт крепления шкива или сзади воротком за маховик через люк в нижней части картера маховика, используя отверстия в маховике (рис. 1), установить момент, когда впускной клапан первого цилиндра полностью поднимется (то есть закроется).
Продолжая вращать коленчатый вал, провернуть его еще примерно на ⅓ оборота (≈120º).
Это положение коленчатого вала соответствует такту сжатия в первом цилиндре и оба клапана этого цилиндра будут закрыты.
5. Проверить щупом зазор между торцом клапана и носком коромысла у впускного и выпускного клапанов первого цилиндра и, при необходимости, отрегулировать.
6. Для регулировки зазоров отвернуть гайку регулировочного винта, вставить в зазор щуп и, вращая винт отверткой (рис. 3), установить зазор 0,25…0,30 мм.
Придерживая винт отверткой, затянуть гайку и проверить величину зазора.
При правильно отрегулированном зазоре щуп толщиной 0,25 мм должен входить при легком нажиме, толщиной 0,30 мм – с усилием.
7. Для регулировки зазоров клапанного механизма остальных цилиндров провертывать коленчатый вал в том же направлении до полного закрытия впускного клапана регулируемого цилиндра и дополнительно еще на ⅓ оборота.
Зазоры регулировать как указано выше (см. п.6).
Регулировку зазоров по цилиндрам рекомендуется проводить в соответствии с порядком их работы.
Порядок работы двигателя по цилиндрам и схема нумерации цилиндров приведена в разделе Основные параметры и характеристики двигателей ЯМЗ-238
8. После окончания регулировки зазоров запустить двигатель и прослушать его работу.
Стуков в клапанном механизме не должно быть.
В случае наличия характерного стука клапанов остановить двигатель и регулировку зазоров повторить.
9. Поставить и закрепить крышки головок цилиндров, проверить состояние прокладок.
В месте прилегания крышек масло не должно подтекать.
autoruk.ru
Двигатель ЯМЗ-238: Регулировка клапанов – Ремонт Своими Руками
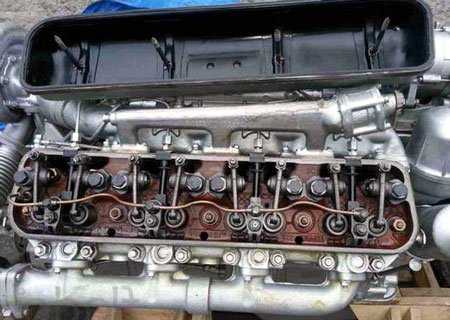
1. Инструмент требующийся для регулировки клапанов
2. Причины регулировки клапанов
3. Регулировка клапанов двигателя ЯМЗ-238
4. Альтернативный метод регулировки клапанов
С регулировкой клапанов на двигателе ЯМЗ-238, встречается основная масса водителей МАЗов. Только те, кто обслуживает свой автомобиль исключительно на станциях технического обслуживания, избегают этой операции.
По регулировке клапанов, написано довольно много рекомендаций и наставлений: от самых простых и незамысловатых до музыкальных. Профессиональные мотористы, регулируют клапана на слух по стуку, который происходит при выборе свободного зазора. Есть также люди, которые регулируют клапана на глаз.
Справедливости ради, стоит отметить, что такие варианты регулировки, если применяет их настоящий специалист, дают хорошие результаты при выставлении зазоров. Однако, описывать подобные методы я не буду, т.к. такими способностями не обладаю, а потому пользуюсь щупом.
1. Инструмент требующийся для регулировки клапанов
Здесь, опишу стандартный метод регулировки клапанов на двигателе ЯМЗ-238. Чтобы выполнить данную операцию, вам понадобится следующий инструмент:
- Ключ на 30 (желательно накидной) с возможностью надеть на него усилитель из трубы;
- Отвертки с широким шлицом;
- Накидной ключ на 17;
- Щуп на 0,25 мм.
Также, желательно иметь канаву для проворачивания коленчатого вала. Однако, если ее нет в наличии, то вполне можно обойтись и без нее, хоть и будет это несколько не удобно.
2. Причины регулировки клапанов
Когда же следует регулировать клапана? Сразу приходит на ум стук в механизме газораспределения. Понятно, что с такими симптомами в первую очередь проверяют тепловые зазоры и регулируют их.
Стоит также произвести регулировку, если после ремонта пройдена первая тысяча километров или если осуществлялась протяжка головки блока.
Нужно следить за пробегом автомобиля и состоянием всего механизма газораспределения. В случае необходимости, регулировать зазоры клапанов через 10-20 тыс. км и всегда помнить, что увеличенные тепловые зазоры ведут к увеличению расхода топлива.
3. Регулировка клапанов двигателя ЯМЗ-238
Теперь, опишу сам порядок регулировки, который у меня выработался. Первым делом, ставим машину на ровное чистое место и достаем инструмент. Поднимаем кабину и откручиваем клапанные крышки клапанов.
Бывает, некоторые болты с барашками не хотят откручиваться от руки, тогда берем газовый ключ или большой рожковый ключ. Мне при такой проблеме, хорошо помогал ступичный трубчатый ключ на 55, который шел в комплекте инструмента на автомобиль.
Далее, берем накидной ключ на 30 с усилителем и залазим под переднюю часть автомобиля. Если клапана на машине регулируются в первый раз, то берем с собой еще и трехгранный напильник.
Порядок нумерации цилиндров двигателей ЯМЗ-236 и ЯМЗ-238
Ищем метку впрыска 1-го цилиндра на шкиве коленчатого вала и на передней части шкива обращенной к радиатору, запиливаем риску напротив метки 1-го цилиндра.Затем, делаем еще одну метку диаметрально напротив первой, а также под 90 градусов к первым двум меткам, ставим еще две метки. Таким образом, мы делим шкив на четыре части под углом 90 градусов.
Теперь, приступаем к выставлению первой заводской метки под 18 градусов и это место на передней плите, следует отчеркнуть хотя бы мелом, т.к. оно еще пригодится.
Вылазим из под машины и проверяем не зажаты ли клапана 1-го цилиндра. Также, убедиться в этом можно по метке топливного насоса, тогда станет понятно, точно ли мы прокрутили двигатель и впрыск находится на 1-ом цилиндре.
Сначала, я тоже так делал и если оказывалось, что впрыск на 6-ом цилиндре, то опять залазил под машину, прокручивал двигатель еще на один оборот и начинал регулировку с 1-го цилиндра в порядке работы двигателя 1-5-4-2-6-3-7-8.
Отрегулировав оба клапана на 1-ом цилиндре, залазим под машину и прокручиваем коленвал так, чтобы вторая риска на шкиве оказалась напротив метки впрыска 1-го цилиндра на блоке. Таким образом, мы повернули коленвал ровно на 90 градусов и можно переходить на левый ряд цилиндров и регулировать следующий по порядку 5-ый цилиндр.
Затем, опять лезем под двигатель, крутим коленвал еще на 90 градусов до совпадения меток и регулируем клапана 4-го цилиндра на правой стороне двигателя. Далее, просто повторяем процесс для всех оставшихся цилиндров в соответствии с порядком работы мотора.
4. Альтернативный метод регулировки клапанов
Парочку раз отрегулировав клапана на двигателе ЯМЗ-238 подобным образом, меня посетила простая мысль и я сократил прокручивание коленвала до точки впрыска 1-го цилиндра.
С этого момента, для меня стало важно просто выставить заводскую метку на шкиве в момент впрыска, после чего, я проверял клапана 1-го цилиндра и если они не были зажаты, то регулировал их, а дальше шел по порядку 1-5-4-2-6-3-7-8. Если же клапана 1-го цилиндра были зажаты, то я начинал регулировку клапанов с 6-го цилиндра, а дальше придерживался порядка 6-3-7-8-1-5-4-2.
Такая мелочь, позволяла лишний раз не залазить под машину и не смотреть на привод топливного насоса, а облегчить процесс регулировки клапанов и немного сократить требующееся на это время.
Кто-то привык регулировать клапана по закрытию одного из них, кто-то регулирует сразу два цилиндра вместе. Спорить о том, какой способ лучше, я не буду. Лично мне, понравился именно порядок регулировки приведенный выше, поэтому им и пользовался.
Автор: Эдуард Залуцкий
capfa.ru
Механизм газораспределения двигателя КрАЗ
Строительные машины и оборудование, справочник
Механизм газораспределения двигателя КрАЗКатегория:
Автомобили КрАЗ
Механизм газораспределения двигателя КрАЗ
Впускной и выпускной клапаны приводятся в действие кулачками распределительного вала через толкатели, штанги толкателя и коромысла. Высота подъема клапанов составляет 13,5 мм. Опускание клапанов осуществляется под действием пружин.
Распределительный вал размещен в средней части блока и приводится во вращение от коленчатого вала двигателя парой цилиндрических шестерен (рис. 18) со спиральным зубом. Боковой зазор в зацеплении находится в пределах от 0,09 до 0,22 мм. Положение шестерен между собой определено метками, выбитыми на их торцах. Распределительный вал изготовлен из стали 45. Он имеет пять опорных шеек диаметром 541o°io5 мм, восемь впускных и восемь выпускных кулачков. Профиль впускных и выпускных кулачков неодинаковый. Поверхности опорных шеек и кулачков вала подвергнуты закалке токами высокой частоты на глубину от 2 до 5 мм до твердости HRC 52—56.
Рис. 16. Порядок затяжки гаек крепления головки цилиндров
Рис. 17. Механизм газораспределения:
1 — коромысло клапана; 2 — ось коромысла; 3— контррайка; 4 — регулировочный винт; 5 — штанга толкателя; 6 — пята толкателя; 7 — ось толкателей; 8 — толкатель; 9— установочный штифт оси коромысла; 10 — болт крепления оси; 11— тарелка пружин клапана; 12 — втулка тарелки; 13 — сухарь крепления клапана; 14 — наружная пружина клапана; 15 — внутренняя пружина; 16 — упорная шайба; 17 — направляющая втулка клапана; 18— впускной клапан; 19 — распределительный вал; 20 — ролик толкателя; 21 — седло выпускного клапана; 22 — выпускной клапан
Рис. 18. Шестерни распределения и привода агрегатов:
1 — ведомая шестерня привода топливного насоса; 2 — шестерня привода вентилятора; 3 — ведущая шестерня привода топливного насоса; 4 — шестерня распределительного вала; 5 — шестерня коленчатого вала; 6 — промежуточная шестерня привода масляного насоса; 7 — ведомая шестерня привода масляного насоса
На переднем конце вала имеется ступица со шпоночной канавкой для установки распределительной шестерни. На резьбовом конце вала сделаны две лыски, предназначенные для фиксации стопорной гайки шестерни.
Ограничение осевых перемещений вала в пределах от 0,121 до 0,265 мм обеспечивается упорным фланцем, изготовленным из листовой стали 65Г и закаленным до твердости HRC 40—45. Упорный фланец устанавливается между шестерней и передней опорной шейкой вала и крепится к переднему торцу блока цилиндров двумя болтами. Болты законтрены от самоотворачивания стопорными шайбами. Упорный фланец одновременно предохраняет от выпадания оси толкателей.
Для обеспечения пульсирующего потока масла к механизмам привода клапанов в передней опорной шейке просверлено сквозное отверстие диаметром 4 мм.
Шестерня распределительного вала изготовлена из стали 40Х с закалкой и отпуском до твердости ИВ 241—286. Она имеет 84 зуба модулем 2,5 мм и углом наклона винтовой линии 20°. Шестерня напрессована на вал, застопорена сегментной шпонкой и закреплена гайкой с замковой шайбой. До октября 1968 г. замковая шайба фиксировалась на распределительном валу усом, входящим в шпоночный паз. С двигателя № 70738 введена фиксация шайбы лысками на резьбовом конце вала, что устранило возможность самоотворачивания гайки.
К шестерне распределительного вала с ее тыльной стороны шестью болтами крепится ведущая шестерня привода топливного насоса, которая центрируется на бурте шестерни распределительного вала.
Впускной клапан изготовлен из жаропрочной стали 4Х10С2М (ЭИ-107), подвергнут закалке с последующим отпуском до твердости HRC 36—40. Торец стержня клапана в месте контакта с коромыслом закален на глубину 2—4 мм до твердости HRC 50—55.
Выпускной клапан 22— сварной, изготовлен из стали 4Х14Н14В2М (ЭИ-69) с последующей закалкой до твердости HRC 25—30. К стержню клапана приварен наконечник, который изготовлен из стали 40ХН и закален на глубину от 2 до 3 мм до твердости HRC 50—57. Диаметр тарелки 48 мм, угол рабочей фаски 91°+30’. Поверхность рабочей фаски наплавлена стеллитом ВЗК, а твердость наплавленного слоя HRC 40—45.
Стержни обоих клапанов графитированы и перемещаются в направляющих втулках, изготовленных Из металлокерамики. Окончательная обработка втулок до внутреннего диаметра 12 мм выполняется после запрессовки их в головку цилиндров. Втулка перед запрессовкой пропитываются веретенным маслом 3 в течение двух часов при температуре 85—95 °С. В процессе работы двигателя стержни клапанов смазываются маслом, вытекающим из сопряжений коромысел.
Каждый клапан прижимается к седлу двумя пружинами в целях увеличения резонансной характеристики.
Наружная пружина 14 имеет правую навивку, внутренняя — левую. Обе пружины изготовлены из проволоки диаметром соответственно 4,8 и 3,5 мм, материал проволоки — сталь 50ХФА.
При нагрузке 25 кгс длина наружной пружины уменьшается до 56 мм, внутренней — до 37 мм. В рабочем положении пружины с одной стороны опираются через шайбу на головку цилиндров, с другой стороны — на тарелку. Через втулку и сухари, входящие в кольцевую канавку на стержне клапана, пружины воздействуют на клапан. Шайбы, тарелки и втулки пружин клапанов изготовлены из стали и подвергнуты цианированию на глубину от 0,1 до 0,2 мм. После термообработки их твердость равна HRC 56, не менее. Сухарь клапана изготовлен из стальной ленты 08 кп.
Конструкция соединения клапана с тарелкой пружин обеспечивает проворачивание клапанов при работе двигателя и способствует постоянной притирке рабочей фаски клапана к его седлу.
Ось состоит из четырех частей (двух крайних и двух средних) и установлена на пяти опорах, сделанных в приливах блока цилиндров. В отверстия этих опор запрессованы чугунные втулки, в которых стыкуются оси. Чтобы толкатели не перемещались по оси, между ними установлены распорные втулки.
На противоположном конце толкателя установлена опорная пята штанги и ролик. Ролик расположен в прорези толкателя и вращается в игольчатом подшипнике на неподвижной оси, запрессованной в отверстие щек прорези толкателя. Над роликом в теле толкателя выполнено отверстие диаметром 18+0’035 мм. Ось отверстия перпендикулярна оси ролика. В отверстие запрессована пята из стали ШХ15, термообработанная до твердости HRC 58—63. Наружный диаметр пяты 18 мм. Пята имеет сферическое углубление радиусом 6 мм, которое служит опорой сферического наконечника штанги 5 толкателя.
Для подачи масла от трущихся поверхностей осей толкателя к рабочей поверхности пяты и через штанги к подшипникам коромысла клапана в теле толкателя и пяты просверлены масляные каналы. Масло для смазки трущихся поверхностей оси толкателя поступает по каналам оси через сверления в передней стенке блока двигателя. Чтобы предотвратить утечку масла, задний конец масляного канала задней оси и передний конец канала передней оси заглушены резьбовыми коническими пробками.
Штанга 5 толкателя представляет собой пустотелый стержень, изготовленный из бесшовной стальной трубы диаметром 12±0,1 мм. Концы штанги выполнены в виде сферы радиусом 6 мм, подвергнуты закалке токами высокой частоты до твердости не менее HRC 52 и прошлифованы. В центре сфер просверлены отверстия для прохода масла через полость штанги к подшипнику коромысла клапана. Верхний сферический конец штанги упирается в сферическое углубление регулировочного винта, нижний — в пяту толкателя.
До апреля 1973 г. штанги толкателей имели специальные наконечники, изготовленные из стали 15ХФ. Сферическая поверхность наконечников подвергалась цементации на глубину от 0,6 до 0,9 мм и последующей закалке до твердости HRC 56—62. После введения штанг новой конструкции взаимозаменяемость со штангами старой конструкции не нарушилась.
Коромысло клапана изготовлено из стали 45. Соотношение плеч коромысла 1 : 1,79. Со стороны короткого плеча в коромысло ввернут регулировочный винт. Противоположный конец коромысла обработан под сферическую площадку радиусом 15 мм и шириной 14 мм. Поверхность площадки закалена на глубину от 2 до 5 мм до твердости HRC 56—63 и отполирована. Через эту площадку передается усилие на торец клапана при работе двигателя.
Коромысло устанавливается на индивидуальной оси и фиксируется на ней упорной шайбой и стопорным кольцом. Ось зафиксирована на головке цилиндров в строго определенном положении и закреплена двумя болтами М16. Точное положение оси коромысла фиксируется двумя установочными штифтами, запрессованными в тело стойки оси. Стойка выполнена как одно целое с осью коромысла. Момент затяжки болтов должен быть от 12 до 15 кгс-м.
Ось коромысла изготавливается из стали, поверхность ее подвергнута закалке токами высокой частоты на глубину от 1,5 до 2,0 мм до твердости HRC 53—58. Диаметр оси равен 25 мм. Подшипниками коромысла являются две бронзовые втулки, запрессованные в отверстие коромысла и обработанные до диаметра 25+о’,оо8 мм. В кольцевом пространстве между втулками просверлен канал, соединяющий его с резьбовым отверстием под регулировочный винт. Это необходимо для подачи масла к подшипникам коромысла.
Регулировочный винт коромысла изготовлен из стали 40Х, подвергнут закалке и отпуску до твердости НЕ 207—241. Его нижний конец имеет сферическое углубление радиусом 6 мм. Внутренняя поверхность углубления закалена токами высокой частоты на глубину от 1,5 до 2,0 мм (твердость не менее HRC 48). Противоположный конец имеет прорезь под отвертку. В теле регулировочного винта выполнены сверления для подачи масла к подшипникам ко-помысла.
Проверка и регулировка тепловых зазоров в клапанном механизме производится на холодном двигателе или спустя 15—20 мин после его остановки. Величина оптимального теплового зазора находится в пределах от 0,25 до 0,30 мм для впускного и выпускного клапанов.
Порядок регулировки тепловых зазоров:
1. Выключить подачу топлива, установив рукоятку ручного управления в крайнее переднее положение.
2. Снять крышки головок цилиндров.
3. Проверить динамометрическим ключом момент затяжки болтов крепления осей коромысел. При необходимости подтянуть болты.
4. Открыть люк картера маховика и с помощью ломика установить маховик меткой «20» против стрелки, закрепленной на картере. Проверить, закрыты ли при этом клапаны 1-го цилиндра (переднего в правом ряду). Если клапаны открыты, провернуть маховик на один оборот, снова установив меткой «20» против стрелки, и после этого повернуть его дополнительно по часовой стрелке (если смотреть со стороны переднего конца коленчатого вала) на 20°. Это положение маховика будет соответствовать ВМТ поршня на такте рабочего хода в 1-м цилиндре. Для ориентации в углах поворота маховика следует помнить, что угол между соседними отверстиями, просверленными в маховике для ломика, составляет 30° (12 отверстий).
5. При помощи щупа проверить зазоры между носками коромысел и торцами впускного и выпускного клапанов 1-го цилиндра и, если необходимо, отрегулировать в следующем порядке: – ослабить гайку, контрящую регулировочный винт на коромысле, придерживая винт отверткой; – вставить в зазор между торцом клапана и носком коромысла щуп толщиной 0,30 мм и вращать винт отверткой до упора носка коромысла в щуп; – придерживая винт отверткой, затянуть контргайку и проверить величину зазора; при правильно отрегулированном зазоре щуп толщиной 0,25 мм должен входить при легком нажиме, а толщиной 0,30 мм — с усилием.
6. При положении поршня 1-го цилиндра в ВТМ на такте рабочего хода можно, не проворачивая коленчатый вал, одновременно отрегулировать зазоры в механизме впускных и выпускных клапанов 5-го и 8-го цилиндров, в которых в этот момент должны быть такты сжатия и оабочего хода соответственно.
7. В остальных цилиндрах можно регулировать зазоры в клапанном механизме в порядке работы цилиндров, но это вызовет большую потерю времени. Целесообразнее после регулировки зазоров в механизме клапанов 1-го, 5-го и 8-го цилиндров провернуть вал на 270° (или на 9 отверстий в маховике) по часовой стрелке и отрегулировать зазоры в механизмах 4-го, 2-го и 6-го цилиндров. Затем снова надо провернуть маховик, но уже на 180° (шесть отверстий в маховике) по часовой стрелке и отрегулировать зазоры в клапанных механизмах 3-го и 7-го цилиндров.
8. После регулировки зазоров пустить двигатель и прослушать его работу. Стук клапанов должен отсутствовать.
9. Установить и закрепить крышки головок цилиндров. В местах прилегания крышек масло не должно подтекать.
Реклама:
Читать далее: Система смазки двигателя КрАЗ
Категория: – Автомобили КрАЗ
Главная → Справочник → Статьи → Форум
stroy-technics.ru
Система тормозов автомобилей Краз-6510, 65055
РЕМОНТ ГРУЗОВЫХ АВТОМОБИЛЕЙ И СПЕЦТЕХНИКИ
Запасные части, техническое обслуживание и регулировки
______________________________________________________________________________________________
Компрессор Краз-6510, 65055
Компрессор поршневого типа, непрямоточный, двухцилиндровый, одноступенчатый, приводится в действие с помощью ремня от шкива вентилятора. Компрессор предназначен для питания пневмосистемы автомобиля сжатым воздухом.
Технические параметры компрессора Краз-65055, 6510
Число цилиндров – 2
Диаметр цилиндров, мм – 72
Ход поршня, мм – 38
Рабочий объем, см3 – 310
Частота вращения, мин1 – 2200
Подача компрессора при 2000 мин”1 и противодавлении 0,75 МПа (7,5
кгс/см2), л/мин – 320
Масса, кг – 19
Для снятия компрессора отпустить болтнатяжитель натяжного устройства и снять ремень. Отвернуть штуцеры и отсоединить трубопроводы, отсоединить воздухопровод подвода воздуха. Отвернуть болты крепления и снять компрессор с автомобиля.
Разборка компрессора Краз-6510, 65101, 65055
Рис. 47. Компрессор Краз-65055, 6510
1-шкив; 2-гайка; 3-шпонка; 4-цилиндр; 5-поршень с шатуном в сборе; 6-плита; 7-головка компрессора; 8-картер; 9-крышка задняя; 10-пружина уплотнителя крышки; 11, 14-подшипники; 12-крышка транспортная; 13-коленчатый вал; 15-крышка передняя
Разборку компрессора проводить в следующем порядке:
Закрепить компрессор в тисках.
Расшплинтовать и отвернуть гайку 2 с шайбой крепления (рис.47) шкива. Снять шкив 1 с помощью пресса и выбить сегментную шпонку из паза.
Вывернуть пробки нагнетательных клапанов, извлечь пружины и клапаны. Квадратным ключом 10×10 мм вывернуть седла клапанов.
Отвернуть гайки шпилек крепления головки компрессора, и осторожно, предварительно отделив прокладку, снять головку 7 блока.
Вынуть из гнезда в блоке пружины и впускные клапаны.
Отвернуть болты и снять патрубок подвода воздуха.
Расшплинтовать и отвернуть гайки болтов крепления крышек шатунов. Снять крышки и вынуть поршни 5 с шатунами из блока цилиндров. Закрепить крышки шатуна. Шатун, крышку и шатунные болты не разукомплектовывать.
Снять поршневые кольца, выбить палец и отсоединить поршни от шатунов.
Отвернуть болты и снять переднюю 15 и заднюю 9 крышки картера.
Вынуть уплотнитель задней крышки с пружиной.
Выбить коленчатый вал 13 из картера 8, с передним подшипником 14 через гнездо переднего подшипника в блоке и с помощью пресса снять передний подшипник с коленчатого вала.
Извлечь стопорное кольцо заднего подшипника и выпрессовать задний подшипник из блока.
Извлечь манжету из гнезда передней крышки.
Отсоединить блок цилиндров от картера 8, отвернуть гайки шпилек, осторожно отделив прокладку.
Детали компрессора промыть, продуть сжатым воздухом и проверить их техническое состояние.
Ускорительный тормозной клапан Краз-6510, 65055
Ускорительный клапан (рис.48) предназначен для подачи сжатого воздуха и затормаживания колес среднего моста при торможении автомобиля рабочей тормозной системой.
Рис. 48. Ускорительный клапан тормозов Краз-65101, 65055
1 – верхний корпус; 2 – поршень; 3, 4 – кольца уплотнительные; 5 – корпус клапана; 6 – пружина; 7 – нижний корпус; 8 – атмосферный вывод; 9 – направляющий колпачок; 10 – упорное кольцо; 11 – выпускной клапан
Вывод А соединен с выводом В перепускного двухмагистрального клапана; С – с выводом четырехконтурного защитного клапана; В – с полостями тормозных камер среднего моста.
Работа ускорительного клапана тормозов Краз-6510, 65055
При отсутствии давления воздуха в выводе А поршень 2 находится в крайнем верхнем положении, впускной клапан 11 закрыт под действием усилия пружины 6, а полости тормозных камер среднего моста сообщены с атмосферой через вывод 8.
При торможении автомобиля рабочей тормозной системой давление сжатого воздуха от верхней и нижней секций тормозного крана подводится через перепускной двухмагистральный клапан 23 к выводу А ускорительного клапана.
Поршень 2 перемещается вниз и перекрывает отверстие, сообщающееся с атмосферой, и открывает клапан 11.
Сжатый воздух, проходя от четырехконтурного защитного клапана через вывод С и открытый клапан 11, заполняет полости тормозных камер среднего моста, подсоединенных к выводу В – происходит торможение.
При отсутствии торможения сжатый воздух из полости над поршнем 2 через двухмагистральный перепускной клапан и атмосферный вывод двухсекционного тормозного крана выпускается в атмосферу.
Поршень 2, перемещаясь вверх, открывает сообщение с атмосферой вывода В, а впускной клапан 11 под действием усилия пружины 6 закрывается и разобщает выводы С и В – автомобиль растормаживается.
Клапан тормозов перепускной двухмагистральный Краз-65101, 65055
Один клапан предназначен для обеспечения подачи сжатого воздуха к ускорительному клапану от двух независимых магистралей секций двухсекционного тормозного крана одновременно или от каждой в отдельности.
Рис. 49. Двухмагистральный перепускной тормозной клапан Краз-65055, 6510
1 – корпус; 2 – мембрана; 3 – крышка; А – к ускорительному клапану; В – к полостям тормозных камер; С – к пневматическому крану
Работа двухмагистрального перепускного клапана
При подводе воздуха к полостям А и С от секций тормозного крана мембрана 2, занимая промежуточное положение, обеспечивает пропуск воздуха в полость В.
В случае снижения давления воздуха в одной из подводящих магистралей мембрана перекрывает поврежденную магистраль (А или С) и обеспечивает поступление воздуха в полость В от исправной магистрали.
Второй клапан 23 расположен на выходе из ресивера контура потребителей и имеет аналогичное значение.
Тормозной кран Краз-6510, 65055 обратного действия с ручным управлением
Предназначен для управления тормозной системой прицепа. Кран (рис.50) установлен на каркасе сиденья водителя с левой стороны.
Рис. 50. Кран тормозной Краз-6510, 65055 обратного действия с ручным управлением
1, 16, 39 – кольцо упорное; 2, 3, 13, 20, 29 – пружина; 4, – шайба опорная; 5, 14, 28 – кольцо О.-образное; 6 – корпус клапана; 7, 8, 10, 19, 24, 25, 26, 34, 36, 41, 42 – шайба; 9 – тарелка пружины; 11 – кольцо клапана; 12 – поршень; 15, 33 – направляющая; 17 – шток; 18 – колпачок направляющий; 21 – рукоятка; 22 – крышка; 23, 30, 40 – штифт; 27 – винт; 31 – кольцо; 32 – ролик; 35 – корпус крана в сборе; 37 – втулка; 38 – стопор; 43 – корпус
К выводу А постоянно подводится сжатый воздух от ресивера контура потребителей через разобщительный кран. В исходном положении сжатый воздух из вывода А через накладное отверстие в корпусе и сверление в поршне 12 проходит в вывод С и далее к клапану управления тормозной системой прицепа с двухпроводным приводом.
При этом сжатый воздух к головке типа «Палм» управляющей магистрали не поступает. При перемещении рукоятки 21 в верхнее положение полости А и С разобщаются.
В этом положении рукоятки 21 сжатый воздух от клапана управления тормозной системой прицепа с двухпроводным приводом поступает к соединительной головке типа «Палм» управляющей магистрали – происходит торможение прицепа (полуприцепа).
Для растормаживания прицепа рукоятку 21 тормозного крана установить в исходное нижнее положение.
Управление тормозной системой прицепа осуществляется с помощью крана управления, установленного с левой стороны каркаса сиденья водителя.
Кран обратного действия, управляет пневматическими тормозными аппаратами, работающими на выпуске воздуха.
Для снятия крана отсоединить трубопроводы и отвернуть гайки болтов крепления.
Разборку тормозного крана Краз-6510, 65055 обратного действия с ручным управлением производить в следующем порядке:
Отвернуть винты крепления и снять крышку 22 (см. рис.50) в сборе с рукояткой 21, снять пружину 20.
Поднять шток 17, вынуть штифт, снять шайбу 19 и колпачок 18 направляющей.
Сжав пружины, снять упорное кольцо, вынуть шток 17 в сборе с направляющей штока 15 и пружиной 13.
Вынуть поршень 12 в сборе и разобрать его, сняв упорное кольцо и вынув пружину, упорную шайбу, клапан 6 и кольцо клапана.
После разборки детали обезжирить и промыть в горячей воде.
Сборку тормозного крана производить в последовательности, обратной разборке, в условиях, исключающих попадание пыли и грязи с учетом следующего:
– Перед сборкой трущиеся поверхности деталей крана смазать тонким слоем смазки.
– Повреждение резиновых деталей при сборке не допускается.
Клапан управления тормозами прицепа Краз-65055, 6510 с двухпроводным приводом
Управление тормозами прицепа (полуприцепа) осуществляется с помощью клапана управления тормозами прицепа с двухпроводным приводом.
Клапан управления тормозами прицепа с двухпроводным приводом имеет 5 выводов. Вывод А (рис.51) соединен с нижней секцией тормозного крана, вывод С – с воздушным ресивером прицепа, вывод D – с краном управления стояночной тормозной системы прицепа, вывод В – с соединительной головкой управляющей магистрали двухпроводного привода тормозов прицепа и выводом А клапана управления тормозами прицепа с однопроводным приводом, вывод Е – с верхней секцией тормозного крана рабочих тормозов.
Рис. 51. Клапан управления тормозами прицепа Краз-65101, 6510, 65055 с двухпроводным приводом
1 – нижний поршень; 2 – выпускное отверстие; 3 – гайка; 4 – нижний корпус; 5 – средний корпус; 6 – средний поршень; 7 – уплотнительное кольцо; 8 – пружина клапана; 9 – тарелка пружины; 10 – пружина верхнего большого поршня; 11 – верхний корпус; 12 – тарелка пружины; 13 – регулировочный винт; 14 – пружина верхнего малого поршня; 15 – верхний малый поршень; 16 – верхний большой поршень; 17 – упорное кольцо; 18 – клапан; 19 – упорное кольцо; 20 – диафрагма; 21 – шайба диафрагмы, I – исходное положение; II – положение при рабочем торможении
При рабочем торможении сжатый воздух от соответствующей секции тормозного крана подводится к выводам А и Е клапана. Сжатый воздух, подведенный к выводу А, перемещает поршни 15 и 16 вниз, сжимая при этом пружину 10, упирается седлом поршня 15 в клапан 18, разобщая полость «В» с атмосферой, и открывает его, сообщая полость «с» с полостью «В».
При этом сжатый воздух проходит в управляющую магистраль прицепа и затормаживает его с интенсивностью, пропорциональной давлению воздуха, подведенному к полости А клапана.
В случае выхода из строя контура рабочих тормозов переднего и среднего мостов, управление тормозами прицепа будет осуществляться от контура тормозов заднего моста через вывод Е.
При отпущенной педали тормоза давление в полостях «d» и «с» одинаковое, клапан 18 сообщает полость «с» с полостью «В», происходит торможение прицепа.
При стояночном или запасном торможении сжатый воздух из вывода D выходит в атмосферу через кран управления стояночной тормозной системой.
Поршень 6 вследствие разности давлений в полостях «с» и «d» перемещается вверх вместе с клапаном 18. Клапан упирается в седло малого поршня 15 и сообщает полость «с» с полостью «В». Сжатый воздух поступает в управляющую магистраль прицепа (полуприцепа) и затормаживает его.
Возможные неисправности в пневмосистеме автомобиля Краз-6510, 65101, 65055
При определении возможных неисправностей в пневмосистеме прежде всего необходимо найти неисправный контур и установить в нем причину, вызвавшую отклонения от нормальной работы пневмопривода.
На аварийное падение давления воздуха в ресиверах контуров тормозов указывают контрольные лампочки на панели приборов. Утечка воздуха в трубопроводах и соединениях проверяется на слух или с помощью мыльной пены, наносимой кистью на проверяемое соединение.
Падение давления сжатого воздуха в ресиверах тормозов при неработающем компрессоре не должно быть более 0,05 МПа (0,5 кгс/см2) от значения нижнего предела, определяемого регулятором давления, в течение: 30 минут при свободном положении органа управления; 15 минут после полного приведения в действие органов управления тормозного привода.
Для устранения утечек воздуха в соединениях допускается применение герметиков.
Регулятор давления воздуха должен обеспечить выключение компрессора при достижении давления, равного 0,8 МПа (8 кгс/см2), и включение компрессора при давлении 0,65 МПа (6,5 кгс/см2).
Тормозная система должна обеспечивать давление воздуха 0,65 – 0,8 МПа (6,5 – 8,0 кгс/см2) в управляющей магистрали двухпроводного привода прицепа.
При плавном приложении усилия к тормозной педали должно обеспечиваться плавное нарастание давления в каждом из контуров рабочих тормозов.
Тормозные камеры Краз-6510, 65055
Тормозные камеры предназначены для передачи усилия на регулировочные рычаги и приведения в действие тормозных механизмов колес передней оси. Устройство тормозной камеры колес передней оси показано на рис.52.
Рис. 52. Камера тормозная Краз-6510, 65055
1 – палец; 2 – вилка; 3 – гайка; 4 – крышка; 5 – мембрана; 6 – шток; 7 – хомут; 8 – пружина; 9 – стакан; А – вывод
Снятие и разборка тормозной камеры Краз-6510, Краз-65101, 65055
Для снятия тормозной камеры отсоединить шланг подвода воздуха, расшплинтовать и вынуть палец 1 (см. рис.52), отвернуть гайки крепления тормозной камеры к кронштейну и снять камеру.
Отвернуть на полтора-два оборота гайку 3, затем вывернуть вилку 2 и гайку 3. Отвернуть гайки болтов хомута 7 и снять хомут. Снять крышку 4, извлечь мембрану 5, пружину 8, стакан 9, шток 6 в сборе с диском.
Сборку и установку камеры производить в последовательности, обратной разборке.
Гайки хомута 7 затянуть моментом силы 0,6 – 1,2 Нм (0,06 – 0,12 кг/см). Гайку 3 – моментом силы 65 – 80 Нм (6,5 – 8 кг/см).
Собранную тормозную камеру испытать на герметичность при давлении воздуха 0,735 МПа (7,35 кгс/см2). При указанном давлении утечка воздуха не должна превышать 4 см3/мин. Произвести несколько раз впуск и выпуск сжатым воздухом из камеры.
При заполнении воздухом тормозной камеры через вывод А шток 6 должен выдвигаться, а при выпуске воздуха – четко возвращаться в исходное положение. Перемещение штока должно быть свободным, без заеданий.
Влагомаслоотделитель с регулятором давления Краз-6510, 65055
Влагомаслоотделитель с регулятором давления предназначен для выделения влаги из сжатого воздуха, автоматического ее слива, а также для регулирования давления сжатого воздуха в заданных пределах. Устройство влагомаслоотделителя показано на рис.53.
Рис. 53. Влагомаслоотделитель Краз-6510, 65101, 65055
1,12 – болт; 2 – планка; 3 – кронштейн; 4, 13, 30 – гайка; 5 – кольцо; 6 – трубка; 7 – кольцо; 8 – пробка; 9 – крышка; 10, 29 – шайба; 11 – пыльник; 14 – болт регулировочный; 15 – шайба; 16 – пружина; 17 – клапан; 18 – корпус наружный; 19 – влагомаслоотделитель с регулятором давления; 20 – О-образное кольцо; 21 – поршень; 22 – кольцо; 23 – шток; 24 – шайба; 25 – пружина; 26 – окно; 27 -клапан; 28 – корпус клапана; 31 – конус; 32 – клапан; 33 – упор; 34 – пружина; 35 – гильза; 36 – пружина; 37 – пружина; 38 – тарелка пружины; 39 – корпус внутренний, 40 – уплотнитель; 41 – О-образное кольцо; 42 – О- образное кольцо; 43 – поршень; 44 – О-образное кольцо; 45 – прокладка
Разборка влагомаслоотделителя с регулятором давления
Для снятия его отсоединить воздухопроводы и отвернуть болты крепления.
Вывернуть четыре болта 12 и снять крышку 9.
Снять прокладку 45 и О-образное кольцо 44.
Снять тарелку пружины 38.
Последовательно вынуть пружины 36, 37, гильзу 35, пружину 34, упор 33, клапан 32.
Снять поршень 43 с кольцами 41, 42.
Снять уплотнитель 40.
Снять внутренний корпус 39 из наружного корпуса 18.
Отвернуть гайку 30.
Последовательно вынуть из корпуса 18: кольцо 20, поршень 21, кольцо 22, шток 23, шайбу 24, пружину 25; окно 26, клапан 27, корпус клапана 28.
После разборки детали необходимо обезжирить и промыть в горячей воде.
Сборку необходимо производить в последовательности, обратной разборке, в условиях, исключающих попадание пыли и грязи, с учетом следующего:
– перед сборкой следует смазать трущиеся поверхности деталей тонким слоем смазки;
– поврежденные резиновые детали заменить новыми.
Защитный четырехконтурный тормозной клапан Краз-6510, 65055
Защитный четырехконтурный клапан тормозов (рис.54) предназначен для разделения контуров пневмопривода и автоматического отключения поврежденного контура с целью сохранения и поддержания заданного давления в исправных контурах.
Рис. 54. Защитный четырехконтурный клапан системы тормоза Краз-6510, 65055
1 – корпус; 2 – шплинт-проволока; 3 – шайба; 4 – клапан; 5 – втулка; 6 – седло; 7 – О-образное кольцо; 8 – поршень; 9 – прокладка; 10 – пружина; 11 – крышка; 12 – болт; 13 – шайба уплотнительная; 14 – шайба регулировочная; 15 – поршень; 16 – пружина клапана; 17 – направляющая
Техническая характеристика четырехконтурного клапана
Конструктивный тип клапана – поршневой
Рабочее давление, МПа (кгс/см2) – 0,65-0,8 (6,5 – 8,0)
Давление начала наполнения через дроссель контуров потребителей, МПа
(кгс/см2) – 0,25 (2,5)
Давление открытия клапанов рабочих контуров, МПа (кгс/см2) – 0,55
(5,5)
Давление, поддерживаемое компрессором в исправных контурах при
неисправности любого контура, МПа (кгс/см2), не менее – 0,68 (6,8)
Давление закрытия клапанов, МПа (кгс/см ), не менее – 0,5
Снятие четырехконтурного защитного клапана с автомобиля производится в такой последовательности:
– Отвернуть накидные гайки трубок всех четырех контуров.
– Отвернуть и снять клапан с ресивера.
Вымыть клапан в дизельном топливе или в керосине и продуть сжатым воздухом. Произвести наружный осмотр клапана, повреждение резьбы не допускается.
Разборка четырехконтурного защитного клапана тормозов производится в такой последовательности:
Зажать клапан в тисках или другом приспособлении.
Отвернуть болт 12 и снять крышку 11.
Снять четыре пружины 10.
Вынуть четыре поршня 8 и 15.
Осмотреть кольца 7 поршней.
Осмотреть седла 6 клапанов.
Поврежденные кольца 7 заменить новыми, поврежденные (растресканные) седла 6 заменить. Сборку клапана произвести в порядке, обратном разборке.
______________________________________________________________________________________
___________________________________________________________________________________________
Другая спецтехника
МТЗ-80
______________________________________________________________________________________
ЯМЗ-236
ЯМЗ-238
Т-130
Т-170
КРАЗ
texav.ru
Проверка и регулировка клапанов – Устройство и техобслуживание – Про МАЗ
Регулировка клапанного механизма сводится к регулировке теплового зазора. Величина теплового зазора у впускных и выпускных клапанов одинакова и равна 0,25-0,3 мм при замере на холодном двигателе.
Для большей точности при регулировке и повторной проверке тепловых зазоров коромысла клапанов рекомендуется прижимать: на головке правого ряда цилиндров коромысла выпускных клапанов к торцу оси, впускных клапанов – к стопорному кольцу; на головке левого ряда цилиндров коромысла выпускных клапанов к стопорному кольцу, впускных клапанов – к торцу оси.
Последовательность регулировки клапанного механизма такая:
- отвернуть барашки крепления крышек головок цилиндров и снять крышки
- проверить момент затяжки болтов крепления осей коромысел, который должен быть 120-150 Н*м (12-15 кгс*м)
- проворачивая коленчатый вал по часовой стрелке (со стороны вентилятора) ключом за болт крепления шкива или ломиком за отверстия в маховике и внимательно наблюдая за движением впускного клапана первого цилиндра, установить момент, когда он полностью поднимется (то есть полностью закроется)
- продолжая вращать коленчатый вал, проверните его еще примерно на 1/3 оборота. В это время в первом цилиндре происходит такт сжатия, и оба клапана этого цилиндра будут закрыты
- проверить щупом зазор между торцом клапана и носком коромысла у впускного и выпускного клапанов первого цилиндра и при необходимости отрегулировать (рис.19)
- для регулировки зазоров отвернуть контргайку регулировочного винта, вставить в зазор щуп и, вращая винт отверткой, установить зазор 0,25-0,30 мм
- придерживая винт отверткой, затяните контргайку и проверьте величину зазора.
- регулировка последующих зазоров осуществляется в последовательности порядка работы цилиндров (ЯМЗ-236: 1-5-4-2-6-3, ЯМЗ-238: 1-5-4-2-6-3-7-8)
- после регулировки зазоров запустить двигатель и проверить его работу.
- при необходимости проверить зазоры
- поставить и закрепить крышки головок цилиндров
- проверить состояние прокладок.
регулировка клапанов
maz-auto.info
Регулировка клапанного механизма ЯМЗ-238Н, ЯМЗ-238Л
Тепловые зазоры клапанного механизма предназначены для обеспечения герметичной посадки клапана на седло при тепловом расширении деталей механизма во время работы двигателя. Величина теплового зазора у впускного клапанов устанавливается одинаковой и регулируется в пределах 0,25 0,30 мм. При проверке на двигателе из-за возможного биения сопрягаемых двигателей распределительного механизма тепловые зазоры должны укладываться в пределы 0,20-0,40 мм. При слишком больших тепловых зазорах уменьшается высота подъема клапанов, вследствие чего ухудшаются наполнение и очистка цилиндров, растут ударные нагрузки и увеличивается износ деталей распределительного механизма. При очень малых зазорах в результате нагрева или износа рабочих фасок клапана и седла головки не обеспечивается герметичность камеры сгорания, двигатель теряет компрессию, перегревается и не развивает полной мощности.
Тепловые зазоры регулировать на холодном двигателе или через 15 минут после его остановки.
При регулировке клапанного механизма и повторной проверке тепловых зазоров коромысла клапанов рекомендуется прижать:
– на головке правого ряда цилиндров коромысла выпускных клапанов к торцу оси, впускных клапанов – к стопорному кольцу;
– на головке левого ряда цилиндров коромысла выпускных клапанов к стопорному кольцу, впускных клапанов – к торцу оси.
Выпускные клапана правого ряда цилиндров расположены к вентилятору, левого ряда цилиндров – к маховику. Последовательность регулировки:
1. Выключить подачу топлива.
2. Отвернуть барашки крепления крышек головок цилиндров и снять крышку.
3. Проверить момент затяжки болтов крепления осей коромысел, который должен быть 120-150 Н•м (12-15 кгс•м).
4. Проворачивая коленчатый вал по часовой стрелке (со стороны вентилятора) ключом за болт крепления шкива (рис.46) или ломиком за отверстия в маховике (рис.47) и внимательно наблюдая за движением впускного клапана первого цилиндра, установить момент, когда он полностью поднимется (т.е. полностью закроется). Продолжая вращать коленчатый вал, провернуть его еще примерно на 1/3 оборота. В это время в первом цилиндре происходит такт сжатия, и оба клапана этого цилиндра будут закрыты.
Рис. 46. Проворачивание коленчатого вала за болт крепления шкива.
Рис. 47. Проворачивание коленчатого вала ломиком за отверстие в маховике.
5. Проверить щупом зазор между торцом клапана и носком коромысла у впускного клапанов первого цилиндра и при необходимости отрегулировать.
6. Для регулировки зазоров отвернуть контргайку регулировочного винта, вставить в зазор щуп, и вращая винт отверткой (рис. 48), установить зазор 0,25-0,30 мм. Придерживая винт отверткой, затянуть контргайку и проверить величину зазора. При правильно отрегулированном зазоре щуп толщиной 0,25 мм должен входить при легком нажиме, толщиной 0,30 мм – с усилием.
Рис. 48. Регулировка зазора клапанного механизма.
7. Для регулировки зазоров клапанного механизма следующего цилиндра провертывать коленчатый вал в направлении вращения до момента полного закрытия впускного клапана регулируемого цилиндра и дополнительно провернуть еще примерно на 1/3 оборота. Регулировать зазоры в каждом цилиндре, как указано выше.
Регулировать клапанные зазоры по цилиндрам рекомендуется в порядке их работы 1-5-4-2-6-3-7-8. Порядок нумерации цилиндров изображен на рис. 2.
8. После регулировки зазоров пустить двигатель и прослушать его работу. При появлении стука клапанов остановить двигатель и вновь проверить зазоры.
9. Поставить и закрепить крышки головок цилиндров, проверить состояние прокладок. В месте прилегания крышек масло не должно подтекать.
banga.ua
Добавить комментарий