Получение синтез газ: Синтез-газ – Что такое Синтез-газ?
Создан метод получения чистого топлива из воздуха и солнечного света
Свежий номер
РГ-Неделя
Родина
Тематические приложения
Союз
Свежий номер
Общество
31.05.2022 20:59
Поделиться
Сергей Деменко
О создании установки для получения метанола почти из ничего – из воздуха и солнечного света – сообщили многие мировые СМИ. А статья швейцарских и германских инженеров опубликована в самом престижном издании Nature. То, что вытекает из аппарата, авторы скромно называют “капельным топливом”. Что, впрочем, понятно: единственный прототип производит около литра метанола в месяц. Но у разработчиков большие амбиции. Они утверждают, что, используя подобные устройства, можно полностью удовлетворить мировую потребность в авиационном керосине. Для этого потребуется покрыть такими установками около 45 тысяч квадратных километров Сахары, что составляет лишь полпроцента ее площади.
Как же работает этот чудо-аппарат? Неужели появляется шанс получить почти бесплатное, абсолютно чистое зеленое топливо? Подчеркнем, что помимо воды и воздуха требуется еще один ингредиент – оксид металла церия. Сначала он разогревается мощным потоком солнечного света до 1500 градусов Цельсия, и церий освобождается от кислорода. Параллельно из воздуха извлекается СО2. Теперь надо, чтобы он прореагировал с водой для образования синтез-газа. Но сама по себе такая реакция не идет. И вот тут-то и нужен восстановленный, лишенный кислорода церий. В его присутствии, а также при высокой температуре от солнечного концентратора, углекислый газ вступает в реакцию с водой. В итоге получается синтез-газ, а это уже сырье, из которого можно произвести метанол и другие виды топлива.
Кто-то скажет, что сам по себе оксид церия настолько дорог, что и эта бесплатная технология напоминает суп из топора, что топливо из воздуха будет намного дороже традиционного. Авторы не спорят, но утверждают, что снизить стоимость “воздушного” топлива в будущем смогут только масштабирование производства и – самое главное – политическая поддержка проекта. И, как показывает нынешняя ситуация вокруг “зеленой повестки”, таким идеям вполне могут дать “зеленую улицу”. А деньги возьмут из “углеродного налога”, который изымут с тех стран, которых объявят злостными загрязнителями.
Комментарий
Антон Максимов, член-корреспондент РАН, директор Института нефтехимического синтеза РАН:
– В принципе, все стадии этой технологии хорошо известны. В чем новизна? Авторы нашли решение, как эти стадии объединить в единую систему. А вот здесь уже много нюансов. Это легко сказать, применить в реакции оксид церия. Мало того, что он дорогой. Главное, что для проведения реакции он должен выдержать много циклов нагрева и охлаждений. Для этого создана специальная керамика. Но способна ли она устоять против 20-40 тысяч температурных ударов? Пока неясно. Кроме того, для удаления кислорода в аппарате надо сильно понизить давление. А значит, потребуется довольно много энергии. Еще больше ее надо для извлечения углекислого газа из воздуха. Наконец, для разбавления газа применяется дорогой аргон, что также серьезно повышает цену “бесплатного топлива”. Если сейчас все корректно подсчитать, то оно может оказаться “золотым”. Вообще, сегодня в мире разрабатывают самые разные способы получения синтез-газа, чтобы затем его превратить в топливо. Например, в нашем институте мы его производим в реакции СО2 и водорода, который извлекается из воды с помощью электролиза. Пока получаемое топливо и у нас, и в других лабораториях намного дороже, чем традиционное.
Российская газета – Федеральный выпуск: №116(8764)
Поделиться
Наука
СИНТЕТИЧЕСКИЙ БЕНЗИН | Наука и жизнь
Без нефтяного моторного топлива – бензина, керосина, дизельного топлива – современную цивилизацию представить себе просто невозможно. На нем работают двигатели автомобилей, самолетов, ракет. Однако запасы нефти в недрах земли ограничены, и совсем скоро человечество столкнется со всеобщей нехваткой бензина. Но впадать в отчаяние рано: закат нефтяной эры вовсе не означает гибель современной цивилизации. Альтернатива нефтяным моторным топливам есть: ученые разработали методы получения высококачественного моторного топлива из природного газа, угля и другого ненефтяного сырья.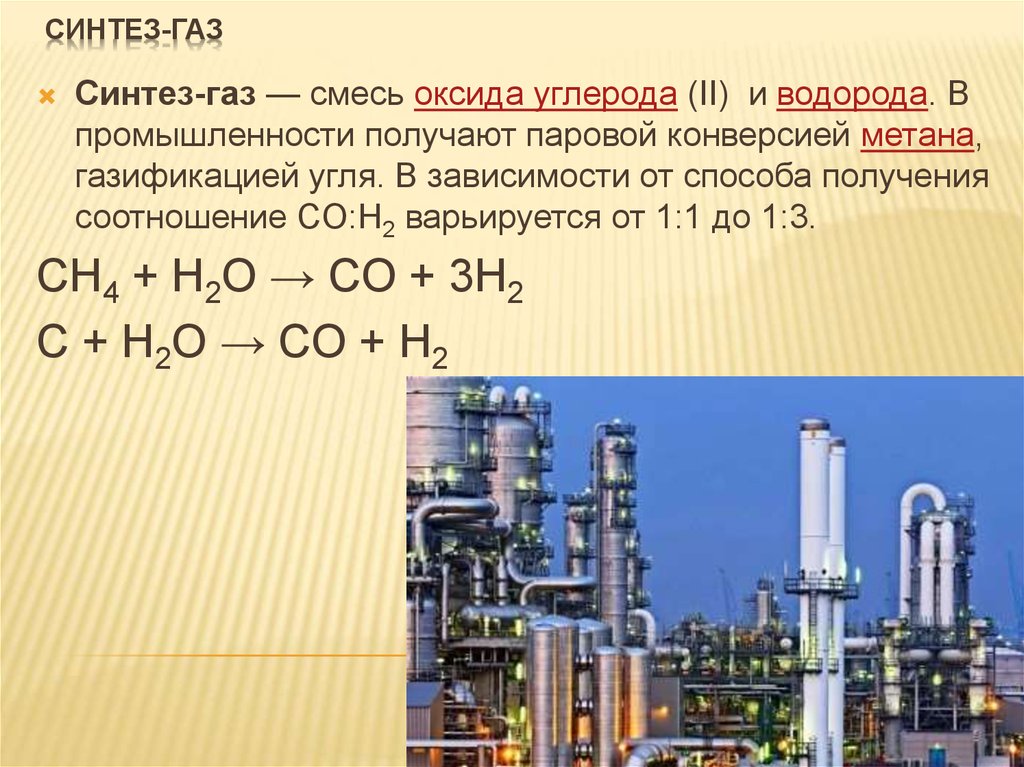
Генератор получения синтез-газа из природного газа, построенный в Институте высоких температур РАН совместно с Институтом нефтехимического синтеза РАН.
Генератор синтез-газа.
Вице-президент РАН, директор Института нефтехимического синтеза им. А. В. Топчиева РАН академик Николай Альфредович Платэ в дни работы Первого московского международного химического саммита.
Смесь окиси углерода и водорода (синтез-газ), из которого в промышленности синтезируют топливные углеводороды, можно получить пропусканием водяного пара через раскаленный кокс (газификация угля) и конверсией природного газа – метана.
Получение моторного топлива из ненефтяного углеводородного сырья.
Процесс синтеза топливных углеводородов через диметиловый эфир (ДМЭ).
Схема химического реактора для получения синтез-газа при горении смеси метана и воздуха при высоких температурах. Подобные реакторы конструируются по принципу ракетного двигателя.
‹
›
Открыть в полном размере
Промышленная добыча нефти началась более 150 лет назад. За прошедшие с тех пор полтора века человечество уже израсходовало более половины нефтяных запасов. Вначале нефть использовалась в качестве источника тепловой энергии, теперь это стало экономически невыгодно. С наступлением автомобильной эры продукты фракционирования нефти в основном применяются в качестве моторного топлива. К 2010 году запасы нефтяных месторождений в значительной степени истощатся, соответственно возрастет стоимость добычи нефти и мир вплотную столкнется с проблемой использования альтернативных (ненефтяных) источников получения бензина и других видов топлива.
По своему химическому составу нефть – смесь углеводородов (алканов и циклоалканов). Кроме того, она содержит метан и некоторые сернистые и азотистые примеси. Бензин – легкокипящая фракция нефти, содержащая короткоцепочечные углеводороды с 5-9 атомами. Это основной вид моторного топлива для легковых автомобилей и небольших самолетов. Керосины более вязкие и тяжелые, чем бензин: они состоят из углеводородов с 10-16 атомами углерода. Керосин стал основным видом топлива для реактивных самолетов и ракетных двигателей. Газойль – более тяжелая фракция, чем керосин. Дизельное топливо для двигателей, установленных на тепловозах, грузовиках, тракторах, содержит смесь фракций керосина и газойля. Истощение природных нефтяных месторождений вовсе не грозит человечеству тотальным дефицитом моторного топлива. Вещества, по химическому составу похожие на бензин, керосин или дизельное топливо, вполне можно получить из углеродного сырья ненефтяного происхождения. Химики решили эту задачу еще в 1926 году, когда немецкие ученые Ф.
Интересно, что во время Второй мировой войны синтетическое топливо, полученное из угля, практически полностью покрывало потребности немецкой авиации. Работы по получению бензина из бурого угля до войны велись и в Советском Союзе, но до промышленного производства дело не дошло. В послевоенные годы цены на нефть упали, и потребность в синтетическом бензине и других топливных углеводородах на какое-то время отпала. Теперь же в связи с уменьшением нефтяных запасов планеты исследования в этой области химии переживают свое “второе рождение”.
Качественного природного угля на планете осталось не так уж много. Внимание ученых привлек природный и попутный газ, огромное количество которого при нефтедобыче просто уходит в атмосферу. Производство синтетического жидкого топлива из природного газа очень выгодно экономически, поскольку газ трудно транспортировать: на его перевозку обычно затрачивается от 30 до 50% стоимости готового продукта. Превращение газа прямо на месторождении в жидкие компоненты значительно снизит объем капиталовложений, затрачиваемых на его переработку.
Существующие технологии позволяют перерабатывать природный газ в высококачественные бензин и дизельное топливо через стадию образования метанола. Производство по такой схеме довольно удобно, поскольку все реакции протекают в одном реакторе. Но эта цепочка химических превращений требует больших затрат энергии. В результате полученный синтетический бензин в 1,8-2,0 раза дороже “нефтяного”.
Российские ученые из московского Института нефтехимического синтеза РАН разработали более рентабельную схему. Они предлагают получать синтетический бензин не через стадию образования метанола, а из другого промежуточного вещества – диметилового эфира (ДМЭ). Это нетрудно сделать, увеличив долю окиси углерода в синтез-газе. Важно то, что ДМЭ можно использовать как экологически чистое топливо для двигателей внутреннего сгорания. Он хорош тем, что полностью укладывается в рамки самых жестких европейских требований по содержанию твердых частиц в автомобильных выхлопах. По теплотворной способности ДМЭ уступает традиционному дизельному топливу – пропану и бутану, но его цетановое число гораздо выше: для обычного дизельного топлива оно 40-55, а для ДМЭ – 55-60.
В присутствии специально разработанных катализаторов ДМЭ превращается в очень неплохой бензин с октановым числом 92. Вредных примесей в нем меньше, чем в нефтяном топливе. Такой синтетический бензин вполне конкурентоспособен даже на европейском рынке. Новый способ получения синтетического топлива намного экономичнее и эффективнее классического “метанольного”. В Институте высоких температур совместно с Институтом нефтехимического синтеза РАН создан генератор синтез-газа, представля ющий собой немного модифицированный дизельный двигатель. На входе – природный газ метан, который в генераторе превращается в синтез-газ. Далее синтез-газ в присутствии специально разработанных катализаторов преобразуется в топливные углеводороды. Поворотом крана можно запустить производство необходимого конечного продукта и по желанию получить на выходе метанол, ДМЭ, смесь углеводородов, аналогичных дизельному топливу, синтетический бензин.
Чем выше температура реакции превращения метана в синтез-газ, тем выше производительность реактора. Обычные технологии не могут справиться с задачей проведения реакции при высоких температурах. Тут на помощь приходят ракетные технологии. Наиболее перспективной разработкой последних лет можно назвать новый высокотемпературный генератор синтез-газа, созданный при участии Института нефтехимического синтеза РАН в Приморске на опытном полигоне ракетно-космической корпорации “Энергия”. Генератор создан по образу и подобию ракетного двигателя, поэтому его оболочка устойчива к воздействию высоких температур. Полученный в реакторе синтез-газ последовательно преобразовывается по новой эффективной схеме, описанной выше, в ДМЭ и бензин.
Моторные топлива, полученные из природного газа, не дороже продуктов переработки нефти, а по качеству даже их превосходят. Так что после окончательного истощения нефтяных месторождений “пробки” на дорогах не уменьшатся.
Иллюстрация “Генератор синтез-газа”.
Генератор синтез-газа для окисления природного газа при высоких температурах, построенный на опытном полигоне ракетно-космической корпорации “Энергия” в Приморске при участии Института нефтехимического синтеза им. А. В. Топчиева РАН по технологии, используемой при строительстве ракетных двигателей.
Иллюстрация “Получение моторного топлива из ненефтяного углеводородного сырья”.
Получение моторного топлива из ненефтяного углеводородного сырья: угля, биомассы, биогаза и природного газа. Схемы переработки сырья близки: на первой стадии происходит превращение в синтез-газ (смесь монооксида углерода и водорода), затем синтез-газ перерабатывают в метанол (традиционная схема) или в диметиловый эфир (ДМЭ) (схема, разработанная в Институте нефтехимического синтеза РАН), которые превращаются в моторное топливо (бензин, дизельное топливо).
Иллюстрация “Процесс синтеза топливных углеводородов через диметиловый эфир (ДМЭ)”.
Синтетический бензин, полученный по традиционной схеме промышленной переработки природного газа в топливные углеводороды через стадию образования метанола, в два раза дороже “нефтяного”. Процесс синтеза топливных углеводородов через диметиловый эфир (ДМЭ), разработанный в Институте нефтехимического синтеза РАН, намного эффективнее и экономичнее традиционной “метанольной” схемы производства синтетических моторных топлив.
10.3. Преобразование синтез-газа в метанол
Метанол является важным первичным химическим продуктом, используемым в качестве химического сырья для производства ряда важных промышленных химикатов, прежде всего уксусной кислоты, формальдегида, метилметакрилата и метил-трет-бутилового эфира (МТБЭ). Метанол также используется непосредственно в качестве топлива или в топливных смесях (например, в M85, состоящем из 85% метанола и 15% бензина). В качестве топлива метанол можно использовать для запуска быстродействующих турбин внутреннего сгорания, снижающих пиковые нагрузки; заменять или смешивать с бензином для приведения в действие транспортных средств; для преобразования в бензин с помощью процесса ExxonMobil превращения метанола в бензин (MTG); или для преобразования в диметиловый эфир (ДМЭ) для питания дизельных двигателей.
Большая часть метанола производится из синтез-газа. Около 55-65% мирового производства метанола используют в качестве сырья природный газ, около 30-35% – уголь, а остальное – коксовый газ и другое сырье. (Альварадо М. Обзор индустрии метанола, 35-я Всемирная конференция по метанолу, Берлин, Германия, 2017 г.). В 2021 году мировое производство метанола достигло 107 миллионов метрических тонн.
Химия технологических процессов
Каталитическая конверсия водорода (H 2 ) и монооксида углерода (CO) из синтез-газа, полученного из угля, в метанол может осуществляться с помощью обычных газофазных процессов или с использованием жидкофазного метанола (LPMEOH™) процесс, разработанный Air Products and Chemicals. Интересующие реакции:
2 H 2 + CO → CH 3 OH |
CO 2 + 3 H 2 → CH 3 OH + H 2 O |
CO + H 2 O → CO2 + H 2 |
Все три реакции сильно экзотермичны. В обычном промышленном газофазном процессе конверсия осуществляется в реакторах с неподвижным слоем при высоком давлении. В зависимости от поставщика катализатора реакция синтеза обычно проводится при манометрическом давлении от 600 до 1700 фунтов на кв. дюйм и температуре от 400 до 600°F. Значительная рециркуляция технологического газа H 2 насыщенный газ сдерживает повышение температуры в адиабатическом реакторе. Концентрация CO на входе в реактор обычно ограничивается примерно 10-15% после разбавления рециркулируемым H 2 .
Каталитические системы, используемые для синтеза метанола, обычно представляют собой смеси меди, оксида цинка, оксида алюминия и оксида магния. Недавние достижения также привели к возможному новому катализатору, состоящему из углерода, азота и платины. Этот катализатор основан на более раннем катализаторе, созданном доктором Роем Перианой из Исследовательского института Скриппса. Этот новый катализатор представляет собой твердый материал, взвешенный в серной кислоте для облегчения катализа. Материал легко перерабатывается, так как его можно отфильтровать от кислоты.
Из трех реакций синтеза метанола последняя является хорошо известной реакцией конверсии водяного газа (WGS). Поскольку отношение H 2 / CO в синтетическом газе из шлакообразующих газификаторов обычно находится в диапазоне от 0,3 до 1, для достижения стехиометрического соотношения H 2 / CO, равного 2, для полной конверсии в метанол требуется значительная конверсия водяного газа.
Примеры технологий и установок:
Производство метанола из синтез-газа представляет собой коммерчески продемонстрированную технологию, использующую в качестве сырья как природный газ, так и уголь. Современные заводы по производству метанола мирового класса обычно имеют мощность порядка 2000–2500 метрических тонн в день (т/сутки). Предлагаются более крупномасштабные (5000 т/сутки) однолинейные технологии производства метанола. Основные поставщики технологий включают:
- Хальдор Топсе
- Казале
- Инженерная корпорация Тойо
- Лурги Хеми ГмбХ
- Джонсон Матти/Дэви
- Уде
С 2011 по 2014 год на нескольких новых заводах по газификации угля или лигнита в Китае были запущены мощности синтез-газа для производства метанола мощностью почти 11 ГВт.
Ссылки/дополнительная литература
|
Жидкое топливо
- Бензин и дизельное топливо
- Синтез Фишера-Тропша
- Конверсия синтез-газа в метанол
- Конфигурации процесса производства метанола
- Процесс LPMEOH™
- Преобразование метанола в бензин
- Процессы непрямого сжижения
- Процессы прямого сжижения
- Министерство энергетики США поддержало исследования и разработки в области синтеза жидкого топлива/усовершенствованного топлива
5.

Рисунок реакций и превращений газификации иллюстрирует концепцию газификации угля и указывает полученный состав синтез-газа. Это может значительно варьироваться в зависимости от сырья и задействованного процесса газификации; однако обычно синтетический газ содержит от 30 до 60% монооксида углерода (CO), от 25 до 30% водорода (H 2 ), от 0 до 5 % метана (CH 4 ), от 5 до 15 % диоксида углерода (CO 2 ), плюс меньшее или большее количество водяного пара, меньшее количество соединений серы сероводород (H 2 S), карбонилсульфид (COS) и, наконец, некоторое количество аммиака и других следовых примесей.
Состав синтез-газа реки Вабаш
В следующей таблице показан рабочий состав синтез-газа для проекта газификации угля на реке Вабаш за четырехлетний демонстрационный период с 19с 96 по 1999 год.
Год | 1996 | 1997 | 1998 | 1999 | ||||
Концентрация | Низкий | Высокий | Низкий | Высокий | Низкий | Высокий | Низкий | Высокий |
Водород, % | 32,87 | 34,21 | 32,90 | 34,40 | 32,71 | 33,82 | 32,31 | 33,44 |
Углекислый газ, % | 14,89 | 17.![]() | 16,60 | 16,90 | 14,92 | 16.06 | 15,25 | 16,22 |
Окись углерода, % | 42,34 | 46.03 | 42,20 | 46,70 | 44,25 | 46,73 | 44,44 | 46,31 |
Метан, % | 1,26 | 1,99 | 1,04 | 2,02 | 1,90 | 2,09 | 1,88 | 2,17 |
Сероводород, ppmv | 17,28 | 83,36 | 43.08 | 106,50 | 23,48 | 107,2 | 86,32 | 106,0 |
Карбонилсульфид, объемные части на миллион | 36,26 | 162,13 | 22,59 | 111,80 | 9.03 | 36,63 | 11.36 | 24,22 |
Теплота сгорания, Btu/sef (HHV) | 256 | 280 | 254 | 283 | 268 | 284 | 267 | 280 |
Завод в Вабаше, использующий технологию газификации E-Gas™, в течение этого периода работал на различных видах топлива, включая два разных типа угля и нефтяной кокс. Состав синтез-газа оставался относительно постоянным, несмотря на изменения в составе угля. Хотя газификатор способен работать с широким спектром сырья, отклонения от угля, используемого в качестве проектной основы для системы, могут снизить производство синтез-газа и пара (различия в производстве будут зависеть от подачи угля и от того, насколько он отличается от расчетного сырья). . Внезапные изменения в сырье могут также вызвать сбои в других процессах предприятия. Сингаз Н 2 :отношение CO относительно высокое (>0,7), типичное для системы газификации с подачей суспензии. Высокие уровни COS в первые годы эксплуатации были результатом проблем с установкой COS-гидролиза (в частности, отравление катализатора микроэлементами и хлоридами и ухудшение площади поверхности из-за перегрева). Эти проблемы были устранены в ходе проекта 1 .
Изменчивость состава синтез-газа
В связанной таблице обобщаются данные нескольких демонстраций, анализов и отчетов о составе синтез-газа на различных газификаторах и типах угольного сырья, показывающие большие различия, которые возникают. При изучении этой таблицы следует проявлять осторожность, поскольку многие факторы могут быть упущены, что оказывает существенное влияние на производимый синтетический газ. Например, для точной детализации воздействия на состав синтез-газа потребуется подробный отчет об используемом угле (окончательный и предварительный анализ). Режим работы газификатора, рабочие условия и т. д. также должны быть указаны (например, газификатор GE может работать в трех различных режимах: полное охлаждение, радиационное и конвективное охлаждение, радиационное охлаждение с последующим частичным охлаждением — синтез-газ может у каждого по разному). Таким образом, эта таблица служит общим обзором и недостаточно детализирована для проектной работы. См. связанные источники для получения информации о разработке этой таблицы.
Данные показывают, что широкий диапазон составов синтетического газа может быть получен путем изменения типа газификатора, исходного сырья и рабочих параметров. Типичный процесс проектирования газификационной установки включает в себя выбор легкодоступного сырья для потенциальной площадки установки и подходящей технологии газификации, а затем использование вариантов последующих процессов для оптимизации состава синтез-газа для получения желаемого конечного продукта.
Добавить комментарий