Новые технологии литья металлов: современные и «дедовские» методы в российской промышленности » Главная тема
современные и «дедовские» методы в российской промышленности » Главная тема
Два века назад, когда ещё образовывались первые заводы Петербурга, нынешний «Пролетарский завод» – начинал свою историю, и что интересно – именно с литейного производства. В IXX веке, предприятие называлось – «Александровским литейным заводом», и было знаменито своими изделиями. Помимо прочих государственных заказов, на этом предприятии, были отлиты многие Петербургские памятники культуры и искусству, включая знаменитую решётку Летнего сада, не менее знаменитую колесницу славы (на арке генерального штаба) и чугунных львов на проспекте Обуховской Обороны.
В то время, литьё как декоративных изделий – так и деталей машиностроения, осуществлялось способами «в землю» или «в кокиль». Под кокильным литьём понималась заливка в неподвижную металлическую форму – под действием силы тяжести. А под литьем в землю, подразумевается заливка в форму, из специального песчано-глиняного состава. Стоит отметить, что старые технологии литья – устарели, так как требовали проведения трудозатратных работ, на обработку полученных заготовок (удаление литника, обдирка и шлифовка изделия).
Какими технологиями пользуются передовики нашей промышленности ?
Современные промышленники, имея масштабные сталеплавильные производства, конечно, не льют изделия в землю или в кокиль. Крупнейшие литейно-механические и машиностроительные заводы, пользуются технологиями – в зависимости от имеющегося «на борту» оборудования. Давайте рассмотрим несколько предприятий:
– «Череповецкий литейно-механический завод» (ЧЛМЗ) – практикует центробежное литьё.
– Концерн «КамАЗ» многие изделия получает литьём под давлением, эксплуатируя новый комплекс литья под низким давлением (LPM).
– «Балашихинский литейно-механический завод» (БЛМЗ) – как один из флагманов российского литейного производства, пользуется широкой гаммой существующих новых технологий литья. Основными можно назвать: литье по выплавляемым моделям, в уплотняемые и корковые формы, статическое и центробежное, горячее изостатическое прессование.
– Еще несколько предприятий, таких как АО «Кубаньжелдормаш», Петербургский «Ижора – Машиностроительный комплекс», Тольяттинский «АвтоЛитМаш», используют литьё в формы – из холодно-твердеющих смесей (ХТС).
Технология литья в формы ХТС – перед литьём в землю и в кокиль
Многие предприятия в настоящее время пользуются следующими технологиями литья:
- – В формы ХТС: многоразовые формы из специальных полимерных смол, затвердителей, песка и глины, которые быстро затвердевают без нагрева в печах. Так изготавливают «стержни» для получения полостей в отливках сложной формы.
- – По газифицированным моделям (технология ЛГМ): материал литейных форм при заливке металла газифицируется. Так получают точные отливки из дорогостоящих и труднообрабатываемых материалов (легированные износостойкие, жаропрочные и марганцовистые стали).
- – Под давлением: в пресс-формы, быстро заполняемые жидким металлом, при давлениях 7-700 МПа. Этот способ применяется для цветных металлов с низкой температурой плавления (цинк, олово, медь, магний, свинец) и некоторых сталей. Изделия получаются относительно некрупные – массой от граммов до десятков килограммов.
По мнению некоторых специалистов, «традиционный» способ литья в сырые песчано-глинистые формы, считается пережившим века. И приводят плюсы литья в формы ХТС перед литьём в землю и кокиль:
- – Нет отклонений от размеров получаемой детали, наплывов, литников.
- – Часть чистовых поверхностей можно получить сразу, то есть трудозатраты и время на финишную обработку в разы снижаются. На те поверхности, которые надо будет обрабатывать, даются маленькие припуски – 2-3 мм, и за счёт этого уменьшается масса самой отливки.
- – Почти нет литейных раковин и пор.
- – Короткие сроки изготовления прочной многоразовой оснастки.
Старые методы для мелкосерийных и уникальных деталей
Тем не менее, до сих пор сохранились и заводы с литейными цехами, практикующие старые технологии и гордящиеся своим опытом. Такой опыт передаётся от пожилых специалистов к молодым. Как говорят на производстве ПАО «Пролетарский завод», в литейном деле проблема «что заливать» менее существенна, перед вопросом «куда заливать». На этом заводе, уделяют большое внимание проектированию форм для заливки, и созданию деревянной модельной оснастки. Специалистов, умеющих качественно выполнять эту работу – не много. Если нужно отлить широкую номенклатуру мелкосерийных деталей, для ответственных изделий машиностроения (в том числе, и в рамках гособоронзаказа), иногда требуется изготавливать сложную трудоёмкую литейную форму, ради всего нескольких отливок.
Для чего сохраняются эти, казалось бы, несовременные методы ? Неспециалист в этой области может сделать вывод, что у предприятий, их применяющих, попросту нет денег на модернизацию. Однако, по вышеописанной технологии, изготавливаются рабочие колёса – для конденсатных насосов АЭС, уникальные шнеки – для насосов геотермальных станций, корпусные детали турбокомпрессоров. Предприятие, работающее «по старинке», зачастую лучше других получает отливки из редких сплавов цветных металлов (например, оловянистых и алюминиевых бронз) методом кокильного литья.
Распространённость технологий новых и старых
В настоящее время российские промышленники могут применять как современные технологии литья (ХТС, ЛГМ, ГИП, литьё центробежное и под давлением), так и «старинные» (кокиль, ЛВМ). Для старого способа, зачастую требуется сложное моделирование оснастки (например, деревянной), выполняемое специалистами с уникальным опытом.
Кокильное литьё считается древнерусской технологией, которая возродилась в ХХ веке, на новой научной основе. Технология позволяет выливать изделия – из любых литейных сплавов. А отливаемые детали, могут быть любых размеров, от сковородок – до башен танков.
Применение старых технологий необязательно указывает на устаревание производственных мощностей. Оно бывает связано с заказами деталей – для высокотехнологичных механизмов, в единичном числе или мелкими сериями. Это логичное следствие того, что объёмы современного российского машиностроения в разы меньше, чем 25-30 лет назад, и оно потребляет значительно меньше металла.
Перейти на vk.com и комментировать статью.
под давлением, по выплавляемым моделям и другие
Изготовление металлических изделий методом литья – это широко распространенный способ получения деталей сложной конфигурации без использования дорогостоящего оборудования.
Для литья пригодны такие металлы и сплавы как:
- черные:
- сталь:
- конструкционная;
- легированная;
- чугун:
- серый;
- белый;
- половинчатый;
- сталь:
- цветные:
- медь:
- бронза;
- латунь;
- алюминий:
- силумин;
- дюралюминий;
- магний;
- медь:
- редкоземельные;
- драгоценные.
Для получения деталей определенного качества разрабатываются новые сплавы с различным процентным содержанием компонентов. От их наличия и количества во многом зависит температура плавления и жидкотекучесть расплава.
youtube.com/embed/g2XW80e7Zv4?feature=oembed” frameborder=”0″ allow=”accelerometer; autoplay; encrypted-media; gyroscope; picture-in-picture” allowfullscreen=””/>
Новая технология в литье – прогрессивный способ разливки. Позволяет снизить себестоимость продукции в отличие от конкурирующих предприятий. Кроме издревле известных способов литья в землю или песчано-глинистые формы, для увеличения количества отливок используются неразрушаемые металлические формы – кокили.
Кроме перечисленных способов применяются такие методы литья как:
- под давлением:
- избыточным;
- вакуумическим;
- центробежное;
- в оболочковые формы;
- по моделям:
- выплавляемым;
- газифицируемым;
- точное (прецизионное).
Для литья чугуна с невысоким показателем шероховатости поверхности используются песчано-глинистые формы. Разлив производится как в опочные формы, так и в безопочные.
Использование типа формы зависит от массовости получения отливок. Так, разовые формы разрушаются, чтобы извлечь отливку. Из-за невысокой прочности состава, формы, предназначенные для разлива под небольшим давлением, изготавливаются толстостенными. Благодаря введению специальных связывающих материалов, придающих дополнительную прочность, форма изготавливается небольшой толщины, но с использованием опоки.
Для цветного литья используются более прогрессивные технологии.
Литье алюминия из-за его низкой температуры плавления сопряжено с некоторыми трудностями. Если разлив производится в формы из металла, то под давлением и с использованием специальных смазок, чтобы исключить появление дефектов.
Для получения ровной наружной поверхности и точного размера на изделиях, имеющих форму вращения, не только из алюминиевых, но и из других сплавов, используется центробежное литье. Центробежные силы распределяют расплавленный металл по форме равномерно. К тому же из расплава удаляются излишки воздуха и газов. Далее ознакомимся с некоторыми технологическими способами литейного производства.
По газифицируемым моделям
Получение формы происходит за счет неизвлекаемой модели, и заливка металла производится в неразъемную форму. При этом модель получают из пенопласта вспениванием при высокой температуре. При литье металла в форму, пенопластовая модель полностью выгорает, освобождая внутренний объем.
Если модели для мелких деталей можно получить вспениванием состава, то крупные вырезают из склеенных плит. Резка производится вручную. Для этого используется нихромовая проволока. Поданное напряжение разогревает проволоку, что облегчает резку.
Также модель может вырезаться на фрезерных или гравировальных станках с числовым программным управлением по заданному алгоритму. Подготовленная модель красится и дополнительно покрывается термостойким составом.
Формовка при ЛГМ производится двумя методами. В первом случае для отливок несложных форм используются вибрационные столы, на которых происходит уплотнение формовочной смеси с использованием опок. Затем на опоку укладывается крышка и монтируется литниковый приемник.
Во втором случае, когда изделие имеет сложную геометрию, формовку проводят под вакуумом. Чтобы закрытая форма не разрушилась, она подвергается действию пониженного давления вплоть до окончания заливки. Значение вакуумического давления невелико – порядка 4-5 ГПа.
Заготовки для литья по газифицируемым моделям
Температура разливаемого металла значительно выше, чем начало газификации пенопласта (560 °С). Газы, выделяемые пенопластом, из формы легко удаляются вакуумной системой. При этом отсутствует задымленность рабочей зоны.
В качестве основного достоинства этого метода отмечают высокое качество отливок, которое можно получить литьем в обыкновенный или облицованный кокиль. Возможным это стало из-за того, что форма цельная.
Литье по газифицируемым моделям
На современном этапе литье по выжигаемым моделям применяется для отливки:
- крупных и средних изделий на мелкосерийном производстве;
- заготовок со сложной конфигураций и весом до 50 кг, к которым предъявляются требования повышенной точности размеров, на среднесерийном и крупносерийном производстве.
Под давлением
Технология литья под давлением предполагает быструю подачу расплава в форму путем использования компрессорных или поршневых механизмов. Благодаря автоматизации процесса литье под давлением считается высокопроизводительным.
Таким способом можно получать детали:
- сложной геометрической формы;
- с достаточно тонкими стенками;
- высокой точности;
- с повышенной шероховатостью.
Способ литья под давлением применяется для получения деталей в автомобилестроении. Они получаются небольшого веса, достаточной прочности, что позволяет снизить общую массу агрегата.
Стоит отметить, что метод литья под высоким давлением имеет следующие достоинства:
- возможность получения размеров 9 класса и грубее;
- достигаемая шероховатость поверхности — 1,25 мкм;
- минимальная размер стенок — 0,6 мм;
- минимальным диаметром отверстий — 1 мм;
- формирование наружной резьбы;
- накатки, надписей на внешней стороне.
К недостаткам относят следующее:
- высока цена на сами формы;
- разлив металлов с низкой температурой плавления;
- повышенная вероятность образования внутренних дефектов в виде трещин и напряжений.
Схема литья под давлением
Широкое использование литья алюминия под давлением обусловлено:
- малым значениями температуры в период кристаллизации;
- пластичностью сплава;
- хорошей жидкотекучестью;
- инертностью к химическим реакциям;
- невысоким объемом усадки.
Рассматривая способы технологию поделить следующим образом:
- камера прессования:
- горячая;
- холодная;
- способ разливки:
- горизонтальный;
- вертикальный;
- механизм подачи сплава:
- поршневой;
- компрессорный.
Протекание процесса
Расплав подается в специальную полость. Поршневым пальцем жидкий металл на большой скорости вгоняется во внутреннюю полость пресс-формы. После чего происходит охлаждение без снятия давления. После затвердевания пресс-форма разъединяется, и отливка извлекается. Для облегчения извлечения конструкция оборудуется толкателями.
В кокиль
При литье в кокиль, или в металлические формы, жидкий металл заливают свободно, то есть под действием гравитационных сил. Саму форму изготавливают разборной из двух частей, установленных на плиту. Для получения полостей и отверстий в предусмотренные канавки, в которые укладываются стержни. Для изготовления металлических форм используются стали и чугуны.
Процесс отлива в кокиль
Для удаления газов во время заливки предусматриваются вентиляционные каналы. Чтобы к внутренним поверхностям кокиля не прилипал расплав их облицовывают или красят огнеупорными составами. Толщина покрытия зависит от разливаемого металла и скорости его охлаждения. Перед покрытием полость формы очищается, а затем нагревается до температур 150 °С — 280 °С.
Особенности получения отливок:
- Из-за высокой теплопроводности сплавы в кокиле быстро остывают, поэтому сплавы с малой жидкотекучестью должны иметь максимальную толщину стенок.
Высокая скорость остывания формирует мелкозернистую внутреннюю структуру.
- Металлическая форма неподатлива, поэтому в отливке отсутствуют дефекты, вызываемые остаточными деформациями, а также предотвращает усадку. Получаемая точность заготовок: стали и чугуны – 7-11 класс, цветные сплавы – 5-9 класс.
- Отсутствие пригара.
- Достигаемая шероховатость поверхности соответствует Rz = 40-10 мкм.
- Кокиль – газонепроницаемая конструкция. Вентиляционные каналы и огнеупорные покрытия не могут полностью отвести газы. В связи с этим газовые раковины – это частое явление.
Плюсы литья в кокиль:
- постоянные характеристики для получаемых отливок;
- возможность использования песчаных стержней;
- высокая производительность;
- малое количество производимых операций;
- чистая поверхность готовых изделий;
- механизация работ;
- невысокая квалификация работников.
Отрицательные стороны:
- значительная стоимость формообразующей оснастки;
- ограниченная стойкость форм;
- быстрое остывание расплава.
В кокиль отливаются практически все металлы, но большинство отливок — это чугуны и литейные стали.
В землю
Литье в землю или в формы из смеси песка и глины — самый старый способ получения заготовок из расплавленного металла. Свыше 80% всего литья приходится на него. Отличается простотой и доступностью используемых материалов.
Из древесины изготавливаются модельный и литниковый комплект. После того как модель готова, замешивается формовочная смесь. В состав самой простой входят песок, кварц и глина.
Технология литья в землю
Формовка производится и вручную и на машинах. Ручное изготовление форм применяется при изготовлении разовых или нескольких отливок и считается непродуктивной. Формовка на машинах используется на автоматизированных литейных линиях. Литейные формы состоят из двух половин и являются одноразовыми. После заливки и охлаждения, формы разрушаются. Больше половины отработавшего материала возвращается на формовочную операцию после очищения и восстановления.
Прецизионное литье
Прецизионное литье, обладающее повышенной точностью, применяется уже не одно десятилетие. С его помощью можно изделиям придать любую форму и при этом не увеличивать затраты на производство.
Прецизионное литье металлов характеризуется тем, что отливки имеют:
- любую форму;
- высокую точность;
- минимальные припуски.
Данный способ литья используется при отливке мелких деталей весом от одного грамма до 10 кг.
Современные технологии литья
24.04.2019
Литье – один из древнейших способов обработки металлов. Этим методом получают заготовки для производства товаров в разных отраслях промышленности. Современные технологии литья позволяют получать болванки любой конфигурации, прочности и плотности. Заготовки из металлических сплавов необходимы для работы горнодобывающей, перерабатывающей промышленности, в машиностроительных и дорожностроительных отраслях и т. д.
Специальные способы литья
Подробно о классических и современных видах литья можно узнать здесь: https://amurmetall-lityo.ru/tehnology. К ним относятся стальное, цветное, чугунное.
Современные способы литья:
- центробежное;
- под давлением;
- в тонкостенные одноразовые формы;
- по выплавляемым моделям;
- корковое и другие;
- литье в кокили.
Способ литья под давлением считается самым производительным для фасонных болванок и цветных металлов. Расплавленный металл помещается в форму и кристаллизуется, подвергаясь высокому давлению, которое создают поршневым, газовым методом или вакуумным всасыванием.
Литье по выплавляемым моделям производится по следующей схеме:
- подготавливают одноразовую тонкую керамическую форму;
- в нее заливают металл;
- отливка застывает;
- форму разрушают и изымают готовое изделие.
Корковое или оболочковое литье применяется для отливок массой до 100 кг. Формы готовят из смеси песка и смолы с добавлением растворителя. На внутреннюю поверхность заготовки наносят разделительный состав и скрепляют части струбцинами. Внутрь заготовки заливают металл, оставляют до полного застывания, после чего оболочку разрушают.
Литье в постоянные металлические формы – кокили использует компания ООО «Амурметалл-Литье». Стандартные формы применяются для изготовления большого количества одинаковых отливок при заказе массовых или серийных партий продукции. Перед работой металл подогревают до температуры от 100°С до 300°С, рабочие поверхности кокилей покрывают специальной обмазкой, обеспечивая хорошую отслаиваемость готового изделия. Таким способом изготавливаются запчасти для спецтехники, автомобилей, мотоциклов.
Преимущества современных методов литья
Эти методы позволяют получать отливки максимально четких форм и точных размеров, с хорошими поверхностными характеристиками.

- уменьшение расхода металла при дальнейшей обработке;
- снижение трудоемкости процесса;
- повышение механических свойств самих болванок;
- минимизация потерь при выбраковке;
- практически полное или частичное исключение формовочных материалов;
- сокращение необходимых производственных мощностей и площадей;
- улучшение санитарных условий в цехах;
- повышение КПД каждого из работников и следование нормам ОТ на производстве.
Современные технологии литья основаны на старинных методах обработки металлов. Их используют для производства как традиционных болванок, так и продукции, требующей высокой точности изготовления.
Современные технологии и методы литья металлов в производстве
Работать с металлом человек начал очень давно и с тех пор потребность в этом прочном и удобном в обработке материале только растет. В современном мире металл является наиболее распространенным материалом не только в производстве, но и в быту. Большой спрос на металлические изделия привел к тому, что методы литья постоянно совершенствуются и на сегодняшний день их существует большое количество.
Технологии литья в металлургическом производстве
Метод литья в землю
Одним из самых первых способов изготовления деталей является отливка в землю. Этот метод литья считается самым простым, однако и он требует довольно тщательной подготовки. Она заключается в создании модели будущей отливки, причем размеры должны быть немного большими, чем требуемая деталь, так как при остывании металл немного оседает.
После создания модели начинается подготовка формовочной смеси. Если деталь должна иметь полости, то также подготавливаются стержни и добавочный формовочный состав, которые впоследствии заполняют полые участки детали. После этого опоки разъединяются таким образом, чтобы не нарушить целостность формовочной смеси. После засыхания смеси приступают к непосредственной заливке. Данный вид литья металлов подразумевает заливку расплава либо при помощи ковша, либо конвейерным способом. После этого остывшая отливка проходит финишные операции.
Метод литья в кокиль
Более совершенным методом литья металлов является литье в кокиль. Данная разновидность в большинстве моментов напоминает предыдущую, так как в обоих случаях применяются литейные формы. Отличием является то, что формы выполнены из металла, что в значительной мере упрощает технологический процесс.
К преимуществам данного способа относится возможность применения принудительного охлаждения, а значит и увеличивается скорость изготовления отливок. Используя всего один кокиль можно выпускать сотни деталей, не тратя время на подготовку форм и смесей. К недостаткам стоит отнести то, что данный вид литья металлов подходит только для материалов с хорошей текучестью.
Метод литья под давлением
Для расплавов с низкой текучестью, например, стали применяется метод литья под давлением. Данный метод литья использует сжатый воздух, под действием которого сталь принимает необходимую форму и заполняет все пустоты. Для этого применяются специальные формы, изготовленные из высококачественной стали, а также специальное оборудование для нагнетания воздуха.
Основным преимуществом такого метода литья помимо возможности применения для всех видов металлов является высокая производительность. При этом уменьшается расход сырья, улучшается качество отливок. Чистота поверхности уменьшает количество финишных операций, что уменьшает себестоимость продукции и трудозатраты.
Литьё по газифицируемым (выжигаемым) моделям
Данный способ наиболее распространен в современной металлургии. Преимуществом этого метода литья металлов является отсутствие ограничений отливки по размерам и массе. В качестве формовочной смеси используется кварцевый песок, который после использования может быть подвергнут регенерации для повторного применения. Эта технология существенно увеличивает производительность производства, снижает себестоимость продукции и повышает качество изделий.
Специальные способы получения отливок
Кроме рассмотренных выше существуют и специальные виды литья металлов. Например, по выплавляемым моделям. Суть этого способа изготовления отливок заключается в том, что в опоку устанавливается модель будущей заливки из парафина или воска, после чего промежутки заполняются формовочной смесью. При подаче расплава модель растворяется и металл заполняет весь объем заготовки. Данная технология литья позволяет получать изделия высокого качества, а процесс легко автоматизируется.
Для относительно простых изделий используется технология литья в оболочковые формы. Формовочная смесь состоит из кварцевого песка и смолы. Металлическая модель устанавливается на разогретую поверхность, засыпается формовочной смесью и после спекания смеси получается опока, в которую после пропекания можно заливать расплав.
При изготовлении труб широко применяют центробежный метод литья металлов. Расплав помещается в специальную вращающуюся форму. Под действием центробежных сил расплав равномерно распределяется по форме. Такой способ обеспечивает изготовление деталей с равномерной толщиной стенки.
При электрошлаковом способе получения отливок жидкий металл получается путем воздействия на чушки электродуговыми разрядами. Иногда применяется бездуговой вид литья металлов. В этом случае металл плавится под действием тепла, передаваемого от разогретого шлака, на который воздействуют мощные разряды. В таком случае исключается контакт металла с воздухом.
Для дорогих металлов, таких как золото, титан и другие применяется вакуумная заливка. Металл плавится в вакууме и разливается в формы. Данная технология исключает образование полостей в готовом изделии. Однако масса отливок находится в пределах ста килограмм. Для более крупных деталей применяются вакуумные ковши, из которых в дальнейшем расплав поступает в формы.
На сегодняшний день существует много методов литья металлов. Все они применяются для различных производственных нужд, а конкретная технология зависит от требуемого качества и точности отливок. При этом прогресс не стоит на месте и не исключено, что в ближайшем будущем будут разработаны новые, более совершенные технологии и способы получения отливок металла.
Новые технологии в литейном производстве: литье металлов, Харьков
Инновации в литейном производстве призваны сделать производство отливок более эффективным по затратам сырья, времени, ресурсов, снизить уровень связанных с литейным производством запыленности, задымленности, шума, вибраций, теплового излучения, повысить качество готовой продукции.
Одной из инновационных технологий в литье является криотехнология получения отливок из металла в песчаных формах по ледяным моделям. При таянии ледяной модели вода пропитывает песок, создавая тонкостенную оболочковую форму. Преимуществом метода является исключение из процесса экологически небезопасных органических модельно-формовочных материалов. Ледяные модели как одноразовые дают более точное литье, а цикличность и многократность использования воды (замораживание, таяние модели, испарение при сушке формы) и песка до 90% снижают затраты на приобретение сырья.
Разновидностью литья в разовые песчаные формы по ледяным моделям является литье с вакуумно-пленочной формовкой. Ледяные модели упаковываются в пленку, а сухой песок формы упрочняется вакуумом с помощью вакуум-насоса. Вакуумно-пленочная формовка (ВПФ) – бесшумный и экологически чистый метод производства металлических отливок, так как выделяемые в процессе газы отсасываются вакуумом и утилизируются.
Инновационным является и внедрение нанотехнологий в литье. Путем ввода наноматериалов в расплав достигается изменение качественных характеристик сплавов и готовых отливок, повышаются эксплуатационные свойства отливок из легких сплавов.
Инновации в литейном производстве коснулись и процессов очистки сырья для литья. Так, разработан новый способ рафинирования (очистки от неметаллических включений) металлов и сплавов путем заливки расплавленного металла в расплавленную соль, подверженную вибрации. Поскольку удельный вес соли меньше удельного веса металла, она, проходя сквозь расплавленный металл, очищает его от неметаллических включений и собирается на поверхности металла. Ее потом удаляют, растворяют в воде, неметаллические включения извлекают, воду выпаривают, а соль снова используют для очистки металла.
При таком способе длительность рафинирования металла снижается в 3,5-5 раз, сплавы металлов содержат в 2-3 раза меньше неметаллических включений (при многократной очистке солью достигается полная очистка), расход электроэнергии уменьшается в 1,5-2 раза по сравнению с известными методами рафинирования металлов.
Внедряемые инновации в литейном производстве позволяют купить литье более высокого качества, улучшают условия труда и сберегают окружающую среду от загрязнений.
Современные литейные технологии
Современное литейное производство — сложный технологический метод, при нем заготовки металлических деталей получают с помощью заливания расплавленного металлического сплава в специально подготовленную литейную форму; внутри нее находится полость необходимой конфигурации. После затвердения полученную заготовку извлекают и обрабатывают до нужного состояния. Современная литейная промышленность ставит перед специалистами задачу, при которой получаются максимально соответствующие форме заготовки, требующие минимальных затрат для их доработки.
Литьё в песчаные формы
Это самый малозатратный, при этом весьма грубый метод литья. Благодаря своей дешевизне, способ является наиболее массовым.
Сначала изготавливается литейная модель. Ранее использовали для этих целей дерево, но сегодня гораздо проще выполнить модель с помощью современного 3D-принтера из недорогих полимерных материалов.
Изготовление песчаных форм
Подготовленная модель устанавливается на своеобразной подмодельной плите, сверху на модель надевается ящик без дна (опока). Промежуток между моделью и ближайшими стенками опоки забивается песком или заранее заготовленной смесью песка со специальным связующего. Для сложных вещей используют две полуформы (2 опоки), плоскость их соприкосновения — это место разъема. Модель извлекают, полученные полуформы соединяют и затем производят отливку. Для заливки металла непосредственно в песко-формовочной смеси делают литники – специальные отверстия. По окончании застывания заготовку извлекают, удаляют облой, литники и обрабатывают поверхность до стандартного качества.
В настоящее время литьё в разовые песчаные формы позволило применять вакуумируемые формы, приготовленные из сухого специального песка без применения связующего.
Технология непрерывного литья
При изготовлении отливок непрерывным литьем расплавленное сырье из металлоприемника через графитовый пустотелый полустержень поступает в кристаллизатор с обязательным водным охлаждением, при затвердевании вытягивается специальным устройством. Такие заготовки позднее обрезают по необходимым размерам.
Используют непрерывное литье с целью получения полуфабрикатовиз чугуна, цветных, драг. металлов. Заготовки не могут иметь посторонних включений, пористости, раковин благодаря созданию узконаправленного потока затвердевания металла. Эта особенность делает данный способ непревзойдённым для изготовления качественной проволоки.
Литье по газифицируемым выжигаемым моделям
При методе литья по газифицируемым моделям стала существовать возможность не удалять одноразовую модель из отливочной созданной формы перед заливкой. Либо такие исходники удаляются при помощи выжигания, растворения и др. Благодаря дешевизне пенополистирола этот способ часто применяется для изготовления отливок разного художественного назначения. Его хорошо использовать для единичных экземпляров элементарных отливок, например накладок с несложным орнаментом, фирменных досок и др.
При изготовлении модели гранулы пенополистирола обязательно подвспенивают для активного роста. Далее укладывают сырье в пеноформы и вторично нагревают. При этом начинается реактивный процесс расширения и спекания помещенных гранул, в результате возникшего давления пенополистирол заполняет все пустоты внутри формы. Соединение различных элементов производят простейшим склеиванием, применяя составы, не влияющие агрессивно на химические особенности исходника и полностью выгорающие при нагревании.
Формование газифицируемых моделей необходимо производить в песчано-глинистые, самотвердеющие, жидкостекольные смеси. Большим преимуществом этого прогрессивного метода становится возможность простого формования в песок при отсутствии связующего. При этом песок в формовке не может смешаться с заменяющим модель металлом.
Способ литья в оболочковые формы
Оболочковый способ литья — это технология получения металлических отливок в формах, выполненных по модельной горячей оснастке из специально смешанных песчано-смоляных составов. Такие формы обладают прочностью, податливостью, газопроницаемостью, негигроскопичностью.
Оболочковые формы обладают следующими свойствами: достаточной прочностью, газопроницаемостью, податливостью, негигроскопичностью.
Процесс оболочкового литья начинается с покрытия термореактивной смолой заранее подогретой площадки, на которой установлена обезжиренная металлическая модель. При нагревании первоначальный состав плавится, образуется полутвердая оболочка. С целью удаления избыточной массы смолы форму с модельной плитой переворачивают, позже дополнительно нагревают. После отвердевания оболочку — полуформу удаляют с матрицы, соединяют методом склеивания или же скрепления с другой половиной. Затем помещают готовую оболочковую форму в ранее изготовленную опоку и далее заполняют её плотно формовочной смесью. После заливки такая форма разрушается.
Литье под давлением
При изготовлении полуфабриката литьем под давлением пользуются только металлическими формами, но при этом заливку горячего расплава в подготовленную пресс-форму производят под давлением.
Этот способ является довольно высокопроизводительным, обеспечивая при том высокое качество структуры поверхности. Данным методом обычно льют цветные металлы. Диапазон размеров отливок очень разный — от одного г. до нескольких, а порой и десятков кг. Применяют этот вид литья в основном для различного массового производства пустотелых изделий чаще всего простой конфигурации.
Центробежное литье
Центробежный способ предполагает формирование отливок под резким воздействием возникших сил внутри раскручивающейся формы, свободным методом залитой расплавом. Так производят полуфабрикат из черных и сплавов многих цветных металлов. Сейчас разработаны специализированные установки для бережного центробежного литья драгоценных металлов.
Главным и основным преимуществом представленного способа является непревзойденно высокая, при анализировании с другими видами, плотность получаемой кристаллической структуры используемого металла. Эта особенность придает прекрасные механические свойства требуемым заготовкам.
Данный вид литья возможно производить на машинах с различными осями вращения – вертикальной или же горизонтальной. Для него применяются песчаные, металлические, также оболочковые или формы (опоки) по восковым моделям.
Кокильное литье
Литьем в кокиль принято считать получение заготовки путем заливки расплава в многоразовый металлический кокиль. При этом происходит довольно скорый отвод тепла через высокотеплопроводный материал формы, поэтому поверхность отливки, ее механические особенности получаются значительно более высокого уровня, чем у абсолютного большинства других способов.
Интереснейшей особенностью представленного метода является уникальная возможность множественного использования изготовленной однократно металлической формы. Ее значительная прочность может позволить очень точно копировать конфигурацию поверхности, получая одновременно высочайшее качество металла. Благодаря большой теплопроводности кокиля изделие быстро затвердевает, соответственно увеличивается скорость изготовления полуфабриката.
Метод литья по выплавляемым моделям
Сегодня в художественной промышленности популярнейшим методом становится литьё по выплавляемым моделям. Современная технология представляет собой предварительное изготовление высокоточного образца из любого легкоплавкого материала, зачастую воска. Такую модель заливают специальной смесью – формомассой. После затвердевания из неё вытапливают восковые заготовки, получая литейную форму. В полученные полости необходимо залить расплав. Застывая, он образует заготовки будущих изделий.
Подробное описание литья по выплавляемым моделям наши читатели могут найти в разделе «Технологические процессы на ВЮЗ «Русское серебро». Мы применяем именно этот вид. Сейчас техника литья смогла не только не потерять главенствующей роли в ювелирной промышленности, а напротив, открылись её новые удивительные возможности. Эта тенденция стала необходимейшим связующим звеном между уникальным искусством художника-ювелира и современным ювелирным производством.
Технологии литья металлов – В помощь хозяину
Технологии литья
Изготовление металлических изделий методом литья – это широко распространенный способ получения деталей сложной конфигурации без использования дорогостоящего оборудования. Производители используют различные технологии литья. Благодаря этому детали можно получить такой точности, что не требуется дальнейшая механическая обработка. Автоматизация и механизация технологического процесса позволяет поставить получение отливок на поток.
Для литья пригодны такие металлы и сплавы как:
Для получения деталей определенного качества разрабатываются новые сплавы с различным процентным содержанием компонентов. От их наличия и количества во многом зависит температура плавления и жидкотекучесть расплава.
Новая технология в литье – прогрессивный способ разливки. Позволяет снизить себестоимость продукции в отличие от конкурирующих предприятий. Кроме издревле известных способов литья в землю или песчано-глинистые формы, для увеличения количества отливок используются неразрушаемые металлические формы – кокили.
Кроме перечисленных способов применяются такие методы литья как:
- под давлением:
- избыточным;
- вакуумическим;
- центробежное;
- в оболочковые формы;
- по моделям:
- выплавляемым;
- газифицируемым;
- точное (прецизионное).
Для литья чугуна с невысоким показателем шероховатости поверхности используются песчано-глинистые формы. Разлив производится как в опочные формы, так и в безопочные.
Использование типа формы зависит от массовости получения отливок. Так, разовые формы разрушаются, чтобы извлечь отливку. Из-за невысокой прочности состава, формы, предназначенные для разлива под небольшим давлением, изготавливаются толстостенными. Благодаря введению специальных связывающих материалов, придающих дополнительную прочность, форма изготавливается небольшой толщины, но с использованием опоки.
Для цветного литья используются более прогрессивные технологии.
Литье алюминия из-за его низкой температуры плавления сопряжено с некоторыми трудностями. Если разлив производится в формы из металла, то под давлением и с использованием специальных смазок, чтобы исключить появление дефектов.
Для получения ровной наружной поверхности и точного размера на изделиях, имеющих форму вращения, не только из алюминиевых, но и из других сплавов, используется центробежное литье. Центробежные силы распределяют расплавленный металл по форме равномерно. К тому же из расплава удаляются излишки воздуха и газов. Далее ознакомимся с некоторыми технологическими способами литейного производства.
По газифицируемым моделям
Получение формы происходит за счет неизвлекаемой модели, и заливка металла производится в неразъемную форму. При этом модель получают из пенопласта вспениванием при высокой температуре. При литье металла в форму, пенопластовая модель полностью выгорает, освобождая внутренний объем.
Если модели для мелких деталей можно получить вспениванием состава, то крупные вырезают из склеенных плит. Резка производится вручную. Для этого используется нихромовая проволока. Поданное напряжение разогревает проволоку, что облегчает резку.
Также модель может вырезаться на фрезерных или гравировальных станках с числовым программным управлением по заданному алгоритму. Подготовленная модель красится и дополнительно покрывается термостойким составом.
Формовка при ЛГМ производится двумя методами. В первом случае для отливок несложных форм используются вибрационные столы, на которых происходит уплотнение формовочной смеси с использованием опок. Затем на опоку укладывается крышка и монтируется литниковый приемник.
Во втором случае, когда изделие имеет сложную геометрию, формовку проводят под вакуумом. Чтобы закрытая форма не разрушилась, она подвергается действию пониженного давления вплоть до окончания заливки. Значение вакуумического давления невелико – порядка 4-5 ГПа.
Заготовки для литья по газифицируемым моделям
Температура разливаемого металла значительно выше, чем начало газификации пенопласта (560 °С). Газы, выделяемые пенопластом, из формы легко удаляются вакуумной системой. При этом отсутствует задымленность рабочей зоны.
В качестве основного достоинства этого метода отмечают высокое качество отливок, которое можно получить литьем в обыкновенный или облицованный кокиль. Возможным это стало из-за того, что форма цельная.
Литье по газифицируемым моделям
На современном этапе литье по выжигаемым моделям применяется для отливки:
- крупных и средних изделий на мелкосерийном производстве;
- заготовок со сложной конфигураций и весом до 50 кг, к которым предъявляются требования повышенной точности размеров, на среднесерийном и крупносерийном производстве.
Под давлением
Технология литья под давлением предполагает быструю подачу расплава в форму путем использования компрессорных или поршневых механизмов. Благодаря автоматизации процесса литье под давлением считается высокопроизводительным.
Таким способом можно получать детали:
- сложной геометрической формы;
- с достаточно тонкими стенками;
- высокой точности;
- с повышенной шероховатостью.
Способ литья под давлением применяется для получения деталей в автомобилестроении. Они получаются небольшого веса, достаточной прочности, что позволяет снизить общую массу агрегата.
Стоит отметить, что метод литья под высоким давлением имеет следующие достоинства:
- возможность получения размеров 9 класса и грубее;
- достигаемая шероховатость поверхности — 1,25 мкм;
- минимальная размер стенок — 0,6 мм;
- минимальным диаметром отверстий — 1 мм;
- формирование наружной резьбы;
- накатки, надписей на внешней стороне.
К недостаткам относят следующее:
- высока цена на сами формы;
- разлив металлов с низкой температурой плавления;
- повышенная вероятность образования внутренних дефектов в виде трещин и напряжений.
Схема литья под давлением
Широкое использование литья алюминия под давлением обусловлено:
- малым значениями температуры в период кристаллизации;
- пластичностью сплава;
- хорошей жидкотекучестью;
- инертностью к химическим реакциям;
- невысоким объемом усадки.
Рассматривая способы технологию поделить следующим образом:
- камера прессования:
- горячая;
- холодная;
- способ разливки:
- горизонтальный;
- вертикальный;
- механизм подачи сплава:
- поршневой;
- компрессорный.
Протекание процесса
Расплав подается в специальную полость. Поршневым пальцем жидкий металл на большой скорости вгоняется во внутреннюю полость пресс-формы. После чего происходит охлаждение без снятия давления. После затвердевания пресс-форма разъединяется, и отливка извлекается. Для облегчения извлечения конструкция оборудуется толкателями.
В кокиль
При литье в кокиль, или в металлические формы, жидкий металл заливают свободно, то есть под действием гравитационных сил. Саму форму изготавливают разборной из двух частей, установленных на плиту. Для получения полостей и отверстий в предусмотренные канавки, в которые укладываются стержни. Для изготовления металлических форм используются стали и чугуны.
Процесс отлива в кокиль
Для удаления газов во время заливки предусматриваются вентиляционные каналы. Чтобы к внутренним поверхностям кокиля не прилипал расплав их облицовывают или красят огнеупорными составами. Толщина покрытия зависит от разливаемого металла и скорости его охлаждения. Перед покрытием полость формы очищается, а затем нагревается до температур 150 °С — 280 °С.
Особенности получения отливок:
- Из-за высокой теплопроводности сплавы в кокиле быстро остывают, поэтому сплавы с малой жидкотекучестью должны иметь максимальную толщину стенок.
Высокая скорость остывания формирует мелкозернистую внутреннюю структуру.
- Металлическая форма неподатлива, поэтому в отливке отсутствуют дефекты, вызываемые остаточными деформациями, а также предотвращает усадку. Получаемая точность заготовок: стали и чугуны – 7-11 класс, цветные сплавы – 5-9 класс.
- Отсутствие пригара.
- Достигаемая шероховатость поверхности соответствует Rz = 40-10 мкм.
- Кокиль – газонепроницаемая конструкция. Вентиляционные каналы и огнеупорные покрытия не могут полностью отвести газы. В связи с этим газовые раковины – это частое явление.
- постоянные характеристики для получаемых отливок;
- возможность использования песчаных стержней;
- высокая производительность;
- малое количество производимых операций;
- чистая поверхность готовых изделий;
- механизация работ;
- невысокая квалификация работников.
- значительная стоимость формообразующей оснастки;
- ограниченная стойкость форм;
- быстрое остывание расплава.
В кокиль отливаются практически все металлы, но большинство отливок — это чугуны и литейные стали.
В землю
Литье в землю или в формы из смеси песка и глины — самый старый способ получения заготовок из расплавленного металла. Свыше 80% всего литья приходится на него. Отличается простотой и доступностью используемых материалов.
Из древесины изготавливаются модельный и литниковый комплект. После того как модель готова, замешивается формовочная смесь. В состав самой простой входят песок, кварц и глина.
Технология литья в землю
Формовка производится и вручную и на машинах. Ручное изготовление форм применяется при изготовлении разовых или нескольких отливок и считается непродуктивной. Формовка на машинах используется на автоматизированных литейных линиях. Литейные формы состоят из двух половин и являются одноразовыми. После заливки и охлаждения, формы разрушаются. Больше половины отработавшего материала возвращается на формовочную операцию после очищения и восстановления.
Прецизионное литье
Прецизионное литье, обладающее повышенной точностью, применяется уже не одно десятилетие. С его помощью можно изделиям придать любую форму и при этом не увеличивать затраты на производство.
Прецизионное литье металлов характеризуется тем, что отливки имеют:
- любую форму;
- высокую точность;
- минимальные припуски.
Данный способ литья используется при отливке мелких деталей весом от одного грамма до 10 кг.
Литьё металлов. Методы и способы литья металлов.
Застывая, металл сохраняет форму того сосуда, в который был залит в жидком виде. Эту особенность металла человек использовал при получении изделий способом литья.
Наша страна издавна славилась искусными литейщиками. В Московском Кремле стоят «Царь-пушка» массой 40 т, отлитая Андреем Чоховым в конце XVI в., и «Царь-колокол» массой 200 т, изготовленный знаменитыми литейщиками Иваном и Михаилом Моториными в первой половине XVIII в.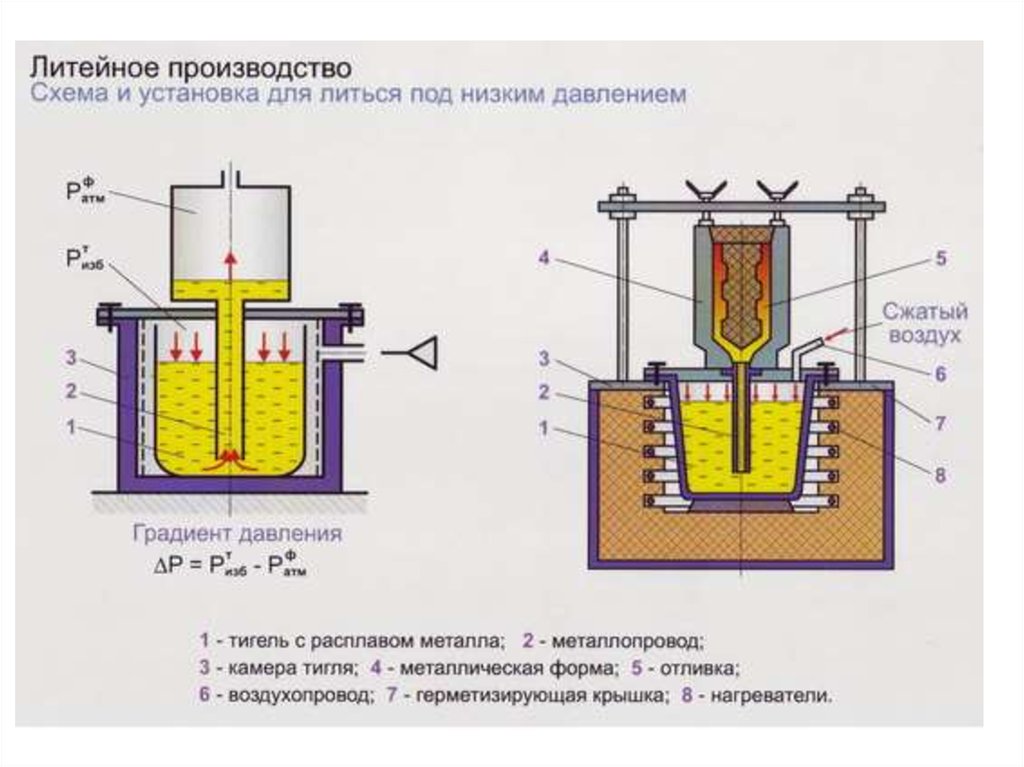
Одно из главных качеств литейного материала — способность растекаться, или жидкотекучесть. Металл или сплав в жидком состоянии должен быть подвижным и невязким, легко заполнять любую сложную форму, быстро проникать в её тончайшие извилины.
Из сплава с хорошей жидкотекучестью можно получить отливку с тонкими стенками. Если металл растекается медленно, то из него тонкостенная отливка не получится: он застынет, прежде чем заполнятся все извилины формы.
Один из лучших литейных материалов — чугун. Он обладает отличной жидкотекучестью. У стали жидкотекучесть меньше, и приходится прибегать к различным ухищрениям, чтобы заставить сталь заполнить всю форму.
Литьё металла в землю.
Самый древний способ литья — литьё в песчано-глинистые формы, или литье в землю. Однако этот способ, хотя его и считают простым, требует большой предварительной работы.
Сначала в модельном цехе из дерева или металла делают модель будущей отливки. Она должна быть несколько большего размера, чем отливка, с учетом усадки металла при охлаждении. Модель (как и будущая форма) разъемная и состоит из двух половинок. В землеприготовительном отделении литейного цеха из земли и различных добавок готовят формовочную смесь. Если у отливки должно быть внутреннее отверстие или полость, то необходимо приготовить еще одну смесь — для стержней. Назначение стержней — заполнить те места в форме, которые в детали соответствуют отверстиям или полостям.

Теперь осталось вынуть из земли деревянную модель. Для этого опоки разъединяют и из каждой вынимают половинки модели. В земле остаются чёткие отпечатки двух половин детали (см. рис.). Их, а также заранее приготовленный стержень покрывают особой краской, чтобы жидкий металл не «пригорел» — не прилип к стенкам формы. В форму вставляют стержень и прорезают в земле канавку, соединяющую отверстие для заливки металла с полостью формы, — литниковый ход. На конец, верхнюю опоку снова кладут на нижнюю, соединяют их, и форма готова. Когда она немного подсохнет, в неё можно заливать металл.
Чугун для литья приготовляют в специальных печах — вагранках. Если отливки стальные, то сталь для них плавят в конвертерах, мартеновских и электрических печах. Для расплавления цветных металлов существуют свои плавильные печи.
Жидкий металл заливают в форму из ковша, который движется вдоль ряда опок, а иногда опоки на конвейере движутся мимо ковша. Когда металл застывает, отливку вынимают из формы. С помощью наждачных станков, пескоструйных или дробеструйных аппаратов отливку очищают от приставшей формовочной земли.
Вместе с тем давно уже появились и успешно используются другие, более совершенные способы литья. Один из них литье в кокиль — металлическую форму (см. рис.), состоящую из двух половин, в одну из них перед заливкой металла вставляют стержни. Затем обе половины кокиля скрепляют между собой и заливают жидкий металл. Здесь он очень быстро затвердевает, и уже через несколько минут можно вынимать деталь и заливать новую порцию металла. С помощью одного кокиля получают сотни и тысячи одинаковых отливок.
Литьё металла в кокиль.
Однако таким способом можно получать отливки только из металлов или сплавов, обладающих хорошей жидкотекучестью. А для стали, например, у которой жидкотекучесть меньше, применяют литье под давлением (см. рис.). Жидкий металл под давлением сжатого воздуха или поршня хорошо заполняет любую сложную форму. Однако обыкновенный кокиль не выдерживает большого давления и разрушается. В связи с этим формы для этого способа литья — пресс-формы — делают из прочной стали. Машины для литья под давлением выпускают по нескольку тысяч отливок за смену.
Литьё по выплавляемым моделям.
Издавна известен способ литья по выплавляемым моделям, сделанным не из дерева или металла, а из легкоплавкого воскообразного (парафин, стеарин) вещества (см. рис.). Такую модель покрывают огнеупорной оболочкой и заформовывают в опоку. Горячий металл расплавляет воск и заполняет оболочку, в точности повторяя форму модели. При этом способе модель не надо извлекать из формы, что позволяет получать очень точные отливки. Кроме того, этот процесс легко автоматизировать.
Литьё в оболочковые формы.
Иногда, когда отливка не требует большой точности, ее получают литьем в оболочковые формы (см. рис.). Их делают из смеси мелкого кварцевого песка с особой порошкообразной смолой. Этой смесью засыпают половинки металлических моделей, установленных на нагретой до 200—250°С металлической плите. Под действием тепла смола расплавляется, обволакивает и скрепляет зерна песка. На модели образуется песчано-смоляная корка. Затем модели вынимают, а плиту с оболочками ставят в печь, где они окончательно затвердевают. Наконец 2 полуформы оболочки соединяют между собой и заливают в полость металл.
Так же широко распространено центробежное литьё, с помощью которого делают отливки, имеющие форму тел вращения, — трубы, шестерни, зубчатые ободы и т. п. Металл заливают во вращающуюся металлическую форму, при вращении он прижимается к стенкам формы, и это позволяет получать отливки высокой точности.
Один из современных способов — электрошлаковое литьё. В этом случае сначала получают жидкий металл методом электрошлакового переплава. Бездуговой переплав металлических электродов осуществляется за счет теплоты, выделяющейся при прохождении электрического тока через расплав электропроводящего шлака. Затем жидкий металл (не соприкасаясь с воздухом) поступает в водоохлаждающий медный кристаллизатор, являющийся литейной формой. Электрошлаковое литье применяется в основном для изготовления сравнительно несложных отливок, например коленчатых валов.
При поставке литых заготовок или готовых изделий специалисты производственного объединения «ПРЕССЛИТМАШ» производят подбор литейной технологиии, оптимально подходящей для каждой конкретной детали. Правильный выбор литейной технологии способен увеличить экономическую рентабельность готового изделия в несколько раз. При выборе технологии отливки каждого конкретного изделия учитывают ряд специфических параметров как самого изделия, так и условий литейного производства.
Заказать отливку из стали, чугуна и цветных металлов вы можете в отделе сбыта по телефону +7(341)297-22-95 или отправив заявку на почту info@presslit. ru
В максимально короткие сроки мы подберём оптимальную литейную технологию и рассчитаем стоимость заказа и сроки поставки отливок.
ОСНОВНЫЕ ЛИТЕЙНЫЕ ТЕХНОЛОГИИ
Литье в землю
литье в ПГС — песчано-глинистые смеси
Литье в ХТС
литье в холодно-твердеющие смеси
Литье ЛГМ
литье по газифицируемым моделям
литье по выплавляемым моделям
Литье ЛПД
литье под давлением
Центробежное литье
центробежное литье
Литье в кокиль
литье в кокиль
Самая массовая технология получения отливок, сочетающая относительную простоту и дешевизну формовки с более грубыми допусками по шероховатости поверхности и точности конфигурации отливки. Применяют для получения отливок 1-3 групп, но при наличии опытных формовщиков и качественной подготовки «земли» (формовочной смеси) возможно получение отливок 4-5 групп.
Технология литья в ХТС, в отличие от литья в ПГС, позволяет получать отливки более высокого качества и с меньшим количеством планируемого литейного брака. Более высокое качество поверхностей и сниженные допуски на мех. обработку отливки существенно увеличивают экономическую рентабельность готового изделия. Модельная оснастка имеет ряд особенностей по сравнению с моделями для ПГС.
Сочетает точность отливок по технологии ЛВМ с низкой себестоимости литья в «землю». Уменьшает трудозатраты, минимизирует производственные отходы.
Газифицируемые (выжигаемые) модели изготавливают из специального полистирола методом спекания в автоклаве или мех. обработки на станках с ЧПУ, также печатают на 3D-принтере из специальных пластиков с малой зольностью.
Литье по выплавляемым моделям позволяет получать отливки самого высокого качества, но особенности технологии и необходимость использования дорогостоящего специализированного оборудования делают выбор технологии ЛВМ оправданным для получения средне- и малосерийных изделий сложной конфигурации с минимальными допусками на обработку поверхностей.
При использовании данного метода литейный сплав ускоренно заполняет литейную форму под воздействием высокого (до 700 МПа) давления.
Отливки отличаются высоким качеством поверхности и точностью формы, но имеют ограничения по сложности формы, толщине стенок, маркам и химическому составу сплавов, что обусловлено особенностями данной технологии.
При литье в кокиль получают отливки с плотным строением, высокими физико-механическими свойствами и хорошей герметичностью.
Технологию применяют при серийном и крупносерийном (массовом) производстве.
При литье в кокиль изготавливают разборную форму (кокиль), в нее и производят заливку. После охлаждения кокиль раскрывают и извлекают полученную отливку.
Эту технологию используют для получения отливок, имеющих форму тел вращения. Метод состоит в том, что расплав заливают в металлическую форму, вращающуюся со скоростью 3000 об/мин. Среди преимуществ метода увеличение процента годного литья, повышенная плотность, возможность биметаллических отливок К недостаткам относятся высокая стоимость оборудования и оснастки.
Методы литья металлов
Способность металла в расплавленном виде заполнять любые полости человек использует уже много лет для изготовления различных изделий.
В наше время существуют различные методы литья металлов, которые отличаются друг от друга технологией, поскольку для каждого материала нужно создать определенные условия, чтобы он мог заполнять все полости заранее подготовленной формы. Это связано с разной жидкотекучестью металлов – параметром, который характеризует способность расплава быстро растекаться.
Рассмотрим подробно, какие методы литья металлов сейчас используются в промышленности, и какие детали или заготовки можно получить при их помощи.
Самые популярные методы литья металлов:
- Литье в землю;
- Литье в кокиль;
- Центробежное литье;
- Электрошлаковое литье;
- Литье под давлением;
- Статическая заливка.
Чтобы понять, в чем заключаются особенности каждого из методов, познакомимся с их технологиями.
Литье металлов в землю
Это процесс знаменит с древних времен, в наши дни он используется преимущественно для изготовления единичных отливок.
Самое главное преимущество технологии литья металла в землю – ее невысокая стоимость, а недостаток – высокая трудоемкость.
Процесс начинается с того, что в специальном цеху изготавливают модель будущей отливки, для этого используют дерево и другие материалы.
Затем готовится формовочная смесь, она содержит в своем составе землю и другие добавки. После этого изготавливается литейная форма, в которую и заливается расплав.
После остывания заготовку извлекают из формы и отправляют на дальнейшую обработку, ее очищают пескоструйным методом или шлифуют, чтобы полностью удалить остатки формовочной земли.
Для такого литья лучше всего подходит чугун, поскольку он имеет отличную жидкотекучесть, также используются и другие металлы.
Литье металла в кокиль
Данный метод литья заключается в том, что форма (кокиль), состоящая из двух частей, одна из которых содержит стержень, соединяется перед началом процесса.
Жидкий металл заливается в форму, там он быстро остывает, и уже через несколько минут получается готовая отливка, которую можно извлекать.
Для этого метода также используются только те материалы, которые обладают хорошей жидкотекучестью, а для других видов подходит литье под давлением.
Литье металла под давлением
Заполнение формы металлом в этом случае осуществляется под высоким давлением воздуха или поршня. Применение давления помогает материалу принимать даже самую сложную конфигурацию формы, заполнять ее тончайшие канавки и повторять все изгибы.
Такие методы литья металлов требуют особенно прочных форм, которые изготавливаются из стали.
Центробежное литье
Для этого способа литья используются формы из песка или металла. Особенность заключается в том, что они вращаются вокруг оси вертикально или горизонтально во время процесса.
Расплав заливается в форму и под действием центробежных сил заполняет ее периферию, затем он затвердевает.
Таким методом целесообразнее всего изготавливать трубы, кольца и подобные элементы.
Электрошлаковое литье
Жидкий металл для этого вида литья получают при помощи электрошлакового переплава.
В качестве литейной формы используется кристаллизатор из меди с водным охлаждением, в него и попадает металл после плавления, не соприкасаясь с воздухом.
Статическая заливка металла
Это самый простой способ, при котором расплав заливается в неподвижную форму до полного ее заполнения. Затем он застывает и извлекается.
Методы литья металлов такого типа позволяют изготавливать отливки самой простой формы.
Достоинства и недостатки технологии литья металлов
Изготовление металлических изделий при помощи литья имеет свои преимущества и недостатки.
К преимуществам можно отнести относительную простоту технологий и высокую производительность, также хорошее качество полученных отливок.
Явными недостатками являются: потребность в применении специальных плавильных печей, большая энергоемкость процессов, невозможность применения метода к определенным видам металла.
Несмотря на это, многие промышленные предприятия пользуются технологией для изготовления самых различных деталей.
Кроме того, в последнее время появились технологии, позволяющие максимально автоматизировать все процессы, что сделало их менее трудоемкими.
Презентация оборудования и технологий для литья металлов на специализированной выставке
На мероприятии международного класса экспоненты из разных стран мира представят новейшие методы литья металлов и других технологий обработки, продемонстрируют оборудование и инструменты, познакомят гостей со своими последними разработками.
Заказать электронные билеты можно прямо сейчас, чтобы не пропустить самое важное событие года в области металлообработки.
Исследования новых технологий
Изобретательность, технологические достижения и новые исследования меняют облик мира литья металлов. Сегодняшняя отрасль более прогрессивна, инновационна, высокотехнологична, сложна, безопасна и чиста. Отрасль формулирует и применяет новейшие разработки в области компьютерного проектирования и моделирования, практики энергоэффективности и процессы и технологии минимизации отходов для улучшения своего имиджа и борьбы с обвинениями в том, что она вызывает загрязнение и создает опасную окружающую среду.
В условиях быстро меняющейся среды и технологий появляются новые продукты и рынки, и, следовательно, ожидается, что спрос на литые металлические компоненты в будущем изменится. Для отрасли важно предвидеть возникающие отраслевые и потребительские требования и разрабатывать инновационные продукты, которые превосходят по качеству и имеют конкурентоспособные цены.
Отрасли потребуются новые методы и процессы для проектирования и создания литых металлических компонентов, которые удовлетворяли бы требовательным спецификациям материалов для новых продуктов.Для обеспечения жизнеспособности индустрии литья металлов в будущем будет важно научиться соответствовать техническим спецификациям и требованиям новых продуктов и рынков.
В области литья металлов ведутся новые технологические исследования с целью обеспечения усовершенствований процесса и технологических инноваций, включая разработки в области литья по выплавляемым моделям, средств компьютерной визуализации для литья под давлением, альтернативных средств литья под давлением.
Промышленность работает над несколькими проблемами, чтобы продемонстрировать, оценить и ускорить новые технологии и научные исследования, которые относятся к различным конкретным потребностям в следующих общих областях –
- Идентификация технологии – Для определения технологических приложений, которые улучшат возможности процессов и материалов в отрасли литья металлов
- Разработка новых технологий – Разработка новых технологий и продуктов для удовлетворения меняющихся требований и спецификаций конкретных приложений.
- Повышение эффективности производства – Повышение эффективности производства с целью контроля производственных затрат, ограничения подверженности колебаниям затрат на электроэнергию и разработки продукции высочайшего качества.
- Разработка приложений – Для демонстрации превосходных экономических и технических преимуществ различных компонентов, спроектированных в виде отливок.
- Управление процессами – Для разработки и производства датчиков управления процессами, которые помогают получать воспроизводимый качественный продукт и снижать производственные затраты.
- Переработка – Для увеличения объемов переработки и повторного использования для внутренних или внешних выгод.
- Контроль загрязнения – Достичь сокращения выбросов в атмосферу и воду и разработать новые технологии и методы, позволяющие избежать загрязнения, а не контролировать и обрабатывать его.
Типы
Новые технологии Исследования обычно проводятся в трех областях –
- Материаловедение
- Технологии производства
- Экологические технологии
Технологии материалов
Исследования в области технологий новых материалов ведутся с основной целью –
- Разработка количественных соотношений между химическим составом сплавов, свойствами и обработкой.
- Установить стандартные методики испытаний материалов.
- Для разработки чистого процесса плавки и переплавки.
- Для разработки методов и процессов для быстрой, точной и неразрушающей оценки химического состава и свойств слитков и отливок.
- Разработать усовершенствованные методы измерения допустимости жидкого металла до обработки.
- Разработать рациональную инициативу по развитию интереса к материаловедению и инженерии.
Технологии производства
Исследования новых производственных технологий ведутся с основными целями –
- Для производства недорогой быстрой оснастки.
- Для улучшения конструкции оснастки, чтобы сократить время вывода отливок на рынок.
- Для создания экономичных и точных по размеру процессов изготовления моделей для литья в песчаные формы.
- Расширьте возможность создания размера / измерения.
- Разобраться в складках при литье алюминия по потерянной пене.
- Чтобы узнать, как на самом деле заполняются формы / матрицы для литья под давлением.
- Для создания математической модели, которая описывает управление процессом и может управлять машиной.
Экологические технологии
Исследования новых экологических технологий проводятся с основными целями –
- Для создания экологически безвредных формовочных материалов со стабильными размерами для литья в песчаные формы.
- Чтобы сформулировать новые способы использования потоков отходов и / или новые методы обработки отходов, чтобы сделать их более пригодными для использования.
- Сформулировать и создать базу данных о выбросах для литейных предприятий, чтобы обучать регулирующих органов.
Отслеживание тенденций в области литья металлов | Foundry Management & Technology
Когда я работаю с компаниями в области маркетинговой стратегии, я задаю два вопроса: « Каковы ваши основные 3 проблемы? »и« Каковы ваши 3 главных возможности? «Что касается проблем, по крайней мере, один из трех ответов обычно не совсем маркетинг: он обычно включает процессы.
По крайней мере одна, а часто и две возможности тоже не совсем маркетинговые. Обычно это связано с целями продаж компании. И меня это никогда не удивляет.
Именно поэтому я формулирую вопросы без слова «маркетинг» как ограничение. У немаркетинговых элементов всегда есть общее: коммуникация , то есть основная функция маркетинга.
Маркетинговый отдел связан с множеством других отделов: обслуживание клиентов, продажи, ИТ, инжиниринг, разработка продуктов, операции, кадры, финансы – и это лишь некоторые из них.Маркетинг требует координации с этими другими отделами, а также обучения у них для создания коммуникационных потоков с клиентами. Можно сказать, что существует множество различных маркетинговых дисциплин – до 41 по некоторым учетным записям – но независимо от того, как вы их считаете, даже когда платформа и конкретное сообщение могут измениться, каждая отдельная маркетинговая дисциплина передает контент об услуге, продукт или бренд.
Большинство маркетинговых дисциплин требуют участия других отделов для создания коммуникации, которая находит отклик у клиентов и потенциальных клиентов.В качестве примеров возьмем некоторые общие маркетинговые дисциплины:
• Бренд работодателя – это обычно координируемый HR результат оперативной потребности в талантах. (Это также может быть обеспечено при поддержке отдела внутренних коммуникаций со стороны отдела маркетинга.)
• Цифровой маркетинг, прямой маркетинг, маркетинг в социальных сетях, традиционный маркетинг и видеомаркетинг – все это может быть охвачено зонтиком «контента», который начинается со знакомства с вашим продуктом / услугой. Вы не можете продавать продукт, о котором не знаете или не знаете, с кем общаетесь.Когда я разрабатываю материалы для любого из этих маркетинговых приложений, я в первую очередь останавливаюсь на обслуживании клиентов, продажах и проектировании (или НИОКР), чтобы узнать, что спрашивают клиенты и потенциальные клиенты, в чем состоят возражения и как наш продукт решает проблему. (Совет для профессионалов: служба поддержки клиентов также является богатым источником историй о выигрышах у клиентов.)
• Маркетинг продуктов часто означает координацию с отделом отдела эксплуатации и проектирования (НИОКР) для получения технической информации, необходимой для каталогов или руководств.В данном случае задача маркетинга – сделать контент доступным и придать ему фирменный вид.
• SEO-маркетинг или голосовой маркетинг могут потребовать некоторой поддержки со стороны ИТ-специалистов для перенастройки серверов или ввода данных по оптимизации вашего веб-сайта для голосового поиска. Также может потребоваться обсуждение с финансовым отделом, чтобы структурировать разумный бюджет для этих усилий. (Или новая категория «расходы».)
• Событийный маркетинг, вероятно, будет делом всех рук, поскольку контент создается техническим и обслуживающим персоналом; Торговый персонал и другие отделы также могут быть частью сферы гостеприимства во время мероприятия.
Спойлер: для большинства возможностей или проблем, которые я узнаю, ответ относится к одной из дисциплин, перечисленных выше. Даже если все 41 вид маркетинга не подходят для B2B, совершенно очевидно, что общение – знание того, о чем вы говорите и с кем – является основой всего маркетинга, а общение обычно является способом решения проблемы или возможности. .
Узнав больше о проблемах и возможностях, я задаю третий вопрос: «Что вы готовы изменить?» Неважно, что представляет собой проблема или возможность, если вы не хотите меняться, вы не сможете их решить.Чтобы зайти так далеко, вам потребовалось то, чем вы занимались; чтобы достичь большего, вы должны быть готовы сделать что-то отличное от того, что делали раньше. Другими словами, вы должны быть готовы к изменениям. Измените то, что вы говорите. Измените способ общения. Измените платформу, которую вы используете для общения. Изменять.
Независимо от того, создаете ли вы единый маркетинговый ход, кампанию или полную маркетинговую стратегию, вы можете начать с ответа на эти три вопроса:
– Каковы ваши основные 3 проблемы?
– Каковы ваши 3 главных возможности?
– Что вы хотите изменить?
Ваши проблемы – это возможности измениться.Ваши возможности – катализаторы перемен. И именно ваши изменения сохраняют актуальность вашего бренда, продукта или услуги для вашего рынка.
Александрия Трусова – менеджер по глобальному маркетингу в Alpha Resources и консультант по маркетингу B2B производителей и других компаний B2B. Свяжитесь с ней по телефону [email protected] или посетите www.truinsightsconsulting.com .
Foundry 4.0 и будущее
Термины Industry 4.0 и Четвертая промышленная революция существуют по крайней мере с 2014 года, но революция продолжается, и новые реализации продолжают входить в отрасли по всему миру.
Отрасль литья металлов переживает свою собственную версию четвертой революции, и все большее число поставщиков, литейных производств и конечных пользователей создают новые способы использования Интернета вещей для более эффективного выполнения своей работы.
Но что на самом деле означает Foundry 4.0?
«Я бы дал определение Foundry 4.0, как что-либо, связанное с новыми возникающими технологиями, процессами, процедурами и системами, которые оказывают социально-экономическое влияние на то, как в настоящее время работают литейные предприятия », – сказал Хидеки Гебкен, технический менеджер Standard Manufacturers Services Limited (Виннипег, Манитоба, Канада).
Как часть Индустрии 4.0, Foundry 4.0 сосредоточена вокруг интеллектуального производства и того, что ждет в будущем с большей вычислительной мощностью, связью, обратной связью и оцифровкой физического мира.
«Мне всегда нравилась концепция, согласно которой производство – это не что иное, как передача полезной« информации о форме »сырьевому материалу», – сказал Рэнди Эрлейн, вице-президент по проектированию Carley Foundry (Блейн, Миннесота).«В Foundry 4.0 мы охватим технологии, которые заставляют информацию о форме перемещаться быстрее, точнее и с меньшими физическими усилиями, поскольку она преобразуется в полезные физические объекты. В случае нашей отрасли это металлические отливки и инструменты ».
Брайан Маккарти, инженер по продажам, Versevo (Хартленд, Висконсин) указывает на то, как литейные цеха по изготовлению моделей участвовали в цифровом производстве с использованием технологий CAD, CAM и ЧПУ с 1980-х годов.
«Мы переняли доступные технологии из других областей производства и сделали их стандартом в нашей отрасли», – сказал он.«В переходный период молодое поколение получало большой отпор со стороны старшего поколения. В следующие 10 лет ситуация будет аналогичной, поскольку молодое поколение преуспевает в технологиях, и в следующие 10 лет потребуется заменить пенсионеров. Для того чтобы отрасль литья металлов могла привлекать молодое поколение (и быть конкурентоспособной), необходимо будет освоить некоторые из передовых производственных возможностей, доступных сегодня, которые используются в других отраслях.”
Foundry 4.0 включает в себя множество аспектов, включая использование робототехники, искусственного интеллекта, автоматизации данных и процессов, а также других новых технологий. Но это также включает в себя то, как цифровое производство повлияет на то, как сотрудники взаимодействуют друг с другом, с оборудованием и клиентами.
«Foundry 4.0 заставляет нас задуматься о будущем: каковы будущие демографические данные, которые повлияют на нашу отрасль, как изменение транспортных тенденций повлияет на тип отливок, которые мы производим, какие новые правила необходимо учитывать в нашей деятельности, какие новые источники энергии будут включены в наш бизнес? » сказал Дэвид Вайс, вице-президент по проектированию и развитию, Eck Industries (Manitowoc, Wisconsin).«Поскольку скорость изменений увеличивается и передовые технологии становятся повсеместными, как мы можем использовать эти инструменты для создания прибыльных и устойчивых литейных предприятий, которые могут работать в далеком будущем?»
Конференция, на которой будут рассмотрены различные способы применения текущих и новых технологий металлургическими компаниями, запланирована на 9-10 июня в Итаске, штат Иллинойс. Конференция Foundry 4.0, организованная Американским обществом литейщиков и членами его различных комитетов, будет охватывать такие ключевые темы, как сбор и управление данными, принятие решений на основе данных, искусственный интеллект, дополненная реальность, виртуальная реальность, носимые технологии, робототехника, автоматизация. , и кибербезопасность, а также связанные с этим вопросы развития, найма и обучения персонала.Конференция будет включать тематические исследования литейного производства, демонстрирующие, как внедрение сбора данных, автоматизации и цифровых технологий изменило и улучшило операции сегодня. Более подробная информация о конференции доступна на сайте www.afsinc.org/conferences/foundry-40.
Щелкните здесь, чтобы просмотреть эту статью в цифровом выпуске Modern Casting за апрель 2020 г.
Аддитивное производство и литье металлов
По данным Американского литейного общества, металлические отливки можно найти в 90% всех товаров длительного пользования, и вы редко находитесь на расстоянии более 10 футов от отливки.Сначала я не поверил, но если почти в каждом автомобиле, грузовике, поезде, тракторе или строительной технике есть отливка, не говоря уже обо всех отливках, имеющихся в нашей инфраструктуре (здания, трубопроводы и т. Д.), Тогда вы понять, почему это число так велико.
Так как же аддитивное производство (AM), один из новейших методов производства, нарушает литье металла, является самым старым методом производства? На самом деле это довольно просто, и оно соответствует тому, что мы обсуждали недавно, а именно гибридным производственным подходам, в которых AM используется для создания приспособлений, приспособлений и / или инструментов (в данном случае песчаных форм и сердечники), которые затем используются для изготовления деталей обычными способами (в данном случае литьем металла).Фактически, 3D-печать песком, вероятно, является одним из самых простых и наименее рискованных способов интеграции AM в производство. Мы знаем, как работает кастинг; все, что мы делаем, – это находим более быстрый и дешевый способ изготовления форм для них, а затем мы отливаем и завершаем детали, как мы это делали на протяжении сотен лет.
Для литья предпочтительным методом AM является распыление связующего – процесс, в котором жидкое связующее используется для «склеивания» материала слой за слоем для создания детали. В этом случае материал, который печатается на 3D-принтере, представляет собой песок, связующее вещество – литейную смолу, а деталь – песчаная форма или стержень формы.Деталь проектируется в САПР как обычно, но вместо того, чтобы превращать ее в узор, твердотельная трехмерная модель инвертируется, чтобы сделать деталь отрицательной. Затем добавляются стояки, литники, направляющие и ворота, и полученная трехмерная твердотельная модель представляет собой саму пресс-форму, которая затем печатается на 3D-принтере с использованием струйной печати связующего.
Системы струйной подачи вяжущего доступны на рынке прямо сейчас. Хотя существует множество вариантов, ExOne и Voxeljet предлагают системы струйной печати связующего, специально предназначенные для 3D-печати на песке. Между тем, новые участники, такие как Viridis3D из EnvisionTEC, объединяют роботизированные манипуляторы и технологию струйной печати связующего для печатных форм и стержней, а также моделей литья по выплавляемым моделям.
Как и большинство процессов AM, использование струйной печати связующего для 3D-печати на песке дает вам новые дизайнерские свободы, которых у вас не было с традиционными процессами литья. Например, вам больше не нужен узор; вы просто распечатываете форму напрямую. Это экономит время, а также означает, что вам больше не нужно беспокоиться об углах уклона и поднутрениях, потому что вам не нужно извлекать шаблон из формы. Более того, стержни можно печатать непосредственно в песчаной форме, что устраняет проблемы соосности, от которых страдает так много отливок.Между тем, стояки и литники могут быть оптимизированы для улучшения потока, поскольку их геометрия не ограничивается способом изготовления пресс-формы. Фактически, результаты, о которых сообщают мои коллеги доктор Гуха Маногаран и доктор Пол Линч из Пенсильванского университета для новых конструкций литников, протестированных с Тони Бадамо и командой Hazelton Casting Co., ошеломляют: снижение дефектов отливок на 99,5%, на 35% уменьшение включений и увеличение механической прочности на 8,4%. Благодаря таким улучшениям, металлическое литье может найти новые применения для компаний, которые ранее отказались от этой технологии.
При стоимости от 0,10 до 0,15 доллара за кубический дюйм, формование песчаных форм и стержней для литья металлов на вяжущем, вероятно, является наиболее экономически эффективным процессом АМ на рынке в настоящее время. Добавьте к этому скорость, с которой можно напечатать форму из песка, не говоря уже об экономии времени за счет отсутствия выкройки, и бизнес-модель литья металла с помощью 3D-печати на песке радикально отличается. Новые конструкции для легковых, грузовых и строительных машин теперь могут быть быстро прототипированы и повторены с использованием функциональных компонентов, изготовленных с помощью 3D-печати на песке, не говоря уже о более сложных геометрических формах, которые позволяет эта форма гибридного производства.
Отрасль литья металлов не может быть известна своей скоростью, но экономика и возможности слишком хороши, чтобы их игнорировать. Теперь вопрос: будете ли вы готовы к быстрой итерации на новых конструкциях и деталях? Если ваши детали сопрягаются с отливками или собираются с ними, вам также будет предложено быстро ответить и выполнить итерацию быстрее, спасибо AM. Между тем, если вы будете обрабатывать или чистить отливки, объем выполняемой работы изменится. Количество итераций будет увеличиваться, но 3D-печать песком также сокращает количество ошибок, переделок и объем необходимой чистовой и механической обработки.Какое влияние это окажет на вашу прибыль?
Новые достижения в области металлического литья
По мере развития технологий производства реактивных двигателей, материалы и технологии обработки материалов идут в ногу со временем.
Design News: Как с годами изменилась технология реактивных двигателей?
Stanley: Технологические разработки реактивного двигателя были направлены на две цели: повышение эффективности и мощности.Одна из тенденций заключалась в повышении температуры внутри турбины – чем выше температура, тем эффективнее сгорает топливо и тем выше мощность на фунт топлива. Как следствие, все внутренние части турбин высокого и низкого давления претерпевают конструктивные изменения, чтобы приспособиться к такому быстрому повышению температуры.
Поток газа при температуре 2600F создает очень агрессивную среду, и достижения в материалах, которые могут выдерживать суровые условия, были огромными: важной разработкой стали отливки с направленной твердостью, в которых границы зерен можно ориентировать определенным образом, чтобы придать сила.Одной из последних разработок в области материалов стал монокристалл металла, из которого можно сделать целую деталь. Очевидное преимущество – отсутствие слабых мест или границ зерен.
Вопрос: Как инженеры справляются с повышением температуры двигателя?
A: Температура газового потока в современных усовершенствованных реактивных двигателях на самом деле выше, чем температура плавления металлов в воздушной фольге. Очевидно, вам нужно беспокоиться об охлаждении.Сегодняшние конструкции воздушной фольги включают очень сложные внутренние охлаждающие камеры, которые направляют горячий воздух от металла. Еще одно направление – разработка покрытий из керамики, циркония и других материалов.
Q: Похоже, что для создания этих очень сложных форм необходимы специальные методы обработки.
A: Один из наиболее важных новых процессов, которые мы разработали здесь, в Howmet, – это вакуумное литье под давлением, которое позволяет нам изготавливать сложные детали до конечной формы.Типичное литье по выплавляемым моделям требует керамической формы и, в зависимости от формы детали, определенной степени механической обработки детали. В этом процессе мы полностью отказались от керамической формы. В основном мы используем вакуумную систему для впрыскивания металла в форму, которая принимает чистую форму. Этот процесс аналогичен литью пластика под давлением, хотя температура здесь намного ниже.
Вопрос: Как это влияет на конструкцию детали?
A: Во-первых, это снизит стоимость.Основная причина в том, что литье под вакуумом – очень эффективный процесс. Эффективность самого лучшего литья по выплавляемым моделям составляет всего около 60%; Эффективность вакуумного литья под давлением составляет около 85%. Это открывает новые возможности для материалов, включая титан.
И, что не менее важно, этот новый процесс позволяет инженерам приступить к разработке деталей, которые намного сложнее по конструкции с точки зрения воздушного потока и оптимизации фактической формы воздушного потока.
Вопрос: Что инженерам нужно знать о технологиях обработки, чтобы создавать успешные проекты?
A: Инженеры много узнают о материалах в школе, но они могут многое узнать о специфике различных процессов.Например, здесь, в Howmet, есть программа обучения инженеров. Это очень адаптированная двухлетняя программа для новых инженеров. Мы также предлагаем программу обучения для наших клиентов, чтобы они лучше понимали проблемы, связанные с обработкой.
Вопрос: Можете ли вы сделать предварительный обзор будущих разработок?
A: Я думаю, что мы увидим эволюцию в том, что касается методов охлаждения этих воздушных пленок по мере их повышения температуры.Одна из рассматриваемых технологий заключается в том, что охлаждение паром – воздух не является очень хорошим проводником тепла, и пар может выделять больше тепла. Мы также увидим больше разработок процессов и материалов.
Джеймс Р. Стэнли Президент и главный исполнительный директор Howmet Castings, Гринвич, Коннектикут Джеймс Р. Стэнли был назначен президентом и главным исполнительным директором Howmet Castings 10 июля 2000 г. До вступления в новую должность он был старшим вице-президентом и главным операционным директором.Стэнли, имеющий степень инженера в области металлургии в Университете Цинциннати, всю свою профессиональную жизнь работал в аэрокосмической отрасли, включая руководящие должности в Textron и GE Aircraft Engine Business Group. Howmet, крупнейший в мире производитель прецизионных отливок, в первую очередь для реактивных самолетов и промышленных газотурбинных двигателей, была первой компанией, которая произвела отливки из воздушной фольги двигателей в 1941 году. |
7 Литейная промышленность | Технологии разделения для отраслей будущего
папок.Влажная очистка, хотя и более эффективна, используется реже из-за сложности и стоимости сушки песка и обезвоживания шлама скруббера перед утилизацией. Усовершенствованные технологии сушки песка и обезвоживания шлама повысят способность отрасли литья металлов утилизировать песок в основной камере (Wood, 1997).
Разгрузочная камера, где отливки извлекаются из изложниц, является источником примерно 50 процентов отработанного песка от операций по разливке металла. Этот отработанный песок представляет собой смесь формовочного песка на глиняной связке и стержневого песка на связующей смоле.В процессе литья большая часть формовочного песка сушится, но в остальном остается неизменной. Однако тонкий слой глины, контактирующий с расплавленным металлом, прокаливается от тепла. Таким образом, отработанный формовочный песок, прошедший литье, содержит кальцинированную глину, которую необходимо удалить перед повторным использованием. Как и песок в помещении, отработанный песок для литейных форм можно утилизировать, используя чистку сухим истиранием с удалением пыли. Влажная очистка используется реже из-за проблем с сушкой и обезвоживанием.
Песок для сердцевины обычно смешивается со смолами, которые действуют как связующие, чтобы гарантировать сохранение формы сердцевины во время литья, несмотря на давление расплавленного металла.Используется много различных связующих, и они обычно окисляются или улетучиваются под воздействием тепла в процессе литья. Если связующие не разрушаются во время литья, они оставляют налипшие остатки, которые могут усложнить утилизацию кернового песка. Более эффективные методы утилизации отработанного песка из цехов по выбрасыванию были бы полезны для промышленности.
Большая часть перерабатываемого песка происходит из цехов по вытяжке. Песок для вытряхивания сначала подвергается измельчению. Металлы и крупные частицы удаляются с помощью магнитов и экранов.Часть этого песка используется повторно. Однако, поскольку отработанный песок для литейных форм нельзя использовать для изготовления стержней, регенерированный песок из вытяжной камеры в сочетании с песком из основного помещения постепенно приводит к накоплению излишков отработанного песка. Некоторое количество отработанного песка, независимо от того, загрязнен он или нет, следует выбрасывать на свалку.
Оставшиеся 30 процентов отработанного песка от металлургического литья поступают в комнату очистки. В настоящее время попытки рекультивации этого песка не предпринимаются. Удаление песка с металлических отливок осуществляется преимущественно дробеструйной очисткой.Во время этого процесса вместе с песком удаляется металлический налет и немного металла размазывается по песчаным поверхностям. Кроме того, металл может истираться с отливки и смешиваться с отработанным песком. Наконец, песчинки можно разбить на более мелкие частицы, иногда изменяя гранулометрический состав песка от желаемого. Доступные технологии рекультивации песка по-прежнему оставляют слишком много загрязненного материала, который необходимо выбросить. Таким образом, рентабельные и действенные методы регенерации песка в помещениях для очистки были бы полезны для промышленности.
Газообразные и водные выбросыОтрасль литья металлов сталкивается с проблемами газообразных и водных выбросов, аналогичными тем, с которыми сталкиваются предприятия алюминиевой и сталелитейной промышленности, но в меньшем масштабе.
различных типов процессов литья, используемых в производстве
Изображение предоставлено: Funtay / Shutterstock.com
Производство отливок – это процесс, при котором жидкий материал, такой как расплавленный металл, заливается в полость специально разработанной формы и дает возможность затвердеть.После затвердевания заготовка вынимается из формы для проведения различных отделочных обработок или для использования в качестве конечного продукта. Методы литья обычно используются для создания сложных твердых и полых форм, а литые изделия находят широкое применение, включая автомобильные компоненты, аэрокосмические детали и т. Д.
Различные виды литья и процесс литья
Хотя литье является одним из старейших известных методов производства, современные достижения в технологии литья привели к появлению широкого спектра специализированных методов литья.Каждый из процессов горячей штамповки, таких как литье под давлением, литье по выплавляемым моделям, гипсовое литье и литье в песчаные формы, дает свои уникальные производственные преимущества. Сравнение преимуществ и недостатков общих типов процессов литья может помочь в выборе метода, наиболее подходящего для данного производственного цикла.
Литье в песчаные формы
Для литья в песчаные формы обычно используются материалы на основе диоксида кремния, такие как синтетический или природный песок. Песок для литья обычно состоит из мелко измельченных сферических зерен, которые можно плотно упаковать в гладкую формовочную поверхность.Отливка спроектирована так, чтобы уменьшить вероятность разрыва, растрескивания или других дефектов, обеспечивая умеренную степень гибкости и усадки во время фазы охлаждения. Песок также можно укрепить, добавив глину, которая помогает частицам более плотно сцепляться. Автомобильные продукты, такие как блоки двигателей, производятся методом литья в песчаные формы.
Литье в песчаные формы включает несколько этапов, включая изготовление моделей, формование, плавление и разливку, а также очистку. Узор – это форма, вокруг которой набивается песок, обычно состоящий из двух частей: рифление и сопротивление.После того, как песок достаточно уплотнен, чтобы воспроизвести узор, колпачок удаляется и узор извлекается. Затем устанавливаются любые дополнительные вставки, называемые стержневыми ящиками, и заменяется колпачок. После заливки и затвердевания металла отливку снимают, очищают от стояков и ворот, которые использовались в процессе заливки, и очищают от прилипшего песка и окалины.
К основным преимуществам литья в песчаные формы относятся:
- Относительно низкие производственные затраты, особенно при малых объемах.
- Возможность изготовления больших компонентов.
- Емкость для литья как черных, так и цветных металлов.
- Низкая стоимость оснастки после литья.
Несмотря на свои преимущества, литье в песчаные формы дает более низкую степень точности, чем альтернативные методы, и может быть трудно отливать в песчаные формы компоненты с заранее определенными размерами и массой. Кроме того, этот процесс имеет тенденцию давать продукты со сравнительно шероховатой поверхностью.
Вы можете использовать платформу Thomas Supplier Discovery Platform, чтобы найти компании по литью в песчаные формы для ваших нужд.
Литье по выплавляемым моделям
Литье по выплавляемым моделям или выплавляемым моделям использует одноразовый восковой узор для каждой отливки. Воск впрыскивается непосредственно в форму, удаляется, затем покрывается огнеупорным материалом и связующим веществом, обычно в несколько этапов для создания толстой оболочки. На общие литники собраны несколько шаблонов. После того, как скорлупа затвердеет, узоры переворачивают и нагревают в печах для удаления воска.Затем расплавленный металл заливается в оставшиеся оболочки, где он затвердевает, принимая форму восковых узоров. Огнеупорная оболочка выламывается, чтобы обнажить законченную отливку. Литье по выплавляемым моделям часто используется для изготовления деталей для автомобильной, энергетической и аэрокосмической промышленности, таких как лопатки турбин. Некоторые из основных преимуществ и недостатков литья по выплавляемым моделям включают:
- Высокая точность и точные результаты размеров.
- Возможность создания тонкостенных деталей сложной геометрии.
- Емкость для литья как черных, так и цветных металлов.
- Относительно качественная обработка поверхности и детализация готовых компонентов.
Несмотря на высокую точность, литье по выплавляемым моделям обычно дороже, чем другие сопоставимые методы литья, и, как правило, рентабельно только тогда, когда нельзя использовать отливки из песка или гипса. Тем не менее, затраты иногда можно компенсировать за счет снижения затрат на обработку и оснастку благодаря качеству поверхности отливок по выплавляемым моделям.
Вы можете использовать платформу Thomas Supplier Discovery Platform для поиска инвестиционных литейных компаний для ваших нужд.
Гипсовая отливка
Литье из гипса аналогично процессу литья в песчаные формы с использованием смеси гипса, упрочняющего состава и воды вместо песка. Штукатурный узор обычно покрывается антиадгезионным составом, чтобы предотвратить его прилипание к форме, а штукатурка способна заполнить любые зазоры вокруг формы. После того, как гипсовый материал был использован для отливки детали, он обычно трескается или образует дефекты, требующие замены на свежий материал.К преимуществам гипсового литья можно отнести:
- Очень гладкая поверхность.
- Возможность отливать сложные формы с тонкими стенками.
- Способность формировать большие детали с меньшими затратами по сравнению с другими процессами, такими как литье по выплавляемым моделям.
- Более высокая точность размеров по сравнению с литьем в песчаные формы.
Этот процесс имеет тенденцию быть более дорогим, чем большинство операций литья в песчаные формы, и может потребовать частой замены гипсового формовочного материала.Обычно это более эффективно и рентабельно, когда важным требованием является качество отделки поверхности. Его применение обычно ограничивается литьем алюминия и сплавов на основе меди.
Вы можете использовать платформу Thomas Supplier Discovery Platform, чтобы найти компании по литью гипса для ваших нужд.
Литье под давлением (процесс литья металла)
Литье под давлением – это метод формования материалов под высоким давлением, обычно с использованием цветных металлов и сплавов, таких как цинк, олово, медь и алюминий.Форма многоразового использования покрыта смазкой, которая помогает регулировать температуру штампа и способствует выталкиванию компонентов. Затем расплавленный металл под высоким давлением впрыскивается в пресс-форму, которое остается непрерывным до тех пор, пока заготовка не затвердеет. Эта вставка под давлением выполняется быстро, предотвращая затвердевание любого сегмента материала перед заливкой. После завершения процесса компонент вынимается из фильеры и удаляются все отходы. Некоторые из основных преимуществ, обеспечиваемых литьем под давлением, включают:
- Минимальные допуски по размерам и форме.
- Высокая стабильность размеров компонентов и унифицированный дизайн.
- Снижение потребности в обработке после литья.
Несмотря на свои преимущества, литье под давлением как процесс литья металла требует относительно высоких затрат на инструмент, что делает его более рентабельным при больших объемах производства. Также может быть трудно обеспечить механические свойства отлитого под давлением компонента, что означает, что эти изделия обычно не функционируют как конструктивные детали. Поскольку формы обычно состоят из двух частей, литье под давлением ограничивается продуктами, которые могут быть извлечены из формы без разрушения формы, как это делается в других процессах литья.
Для получения дополнительной информации о литье под давлением вы можете ознакомиться с нашим руководством по типам литья под давлением, в котором подробно рассматриваются различные типы, сплавы и соображения по выбору конкретной комбинации процесса / сплава.
Центробежное литье
Центробежное литье используется для производства длинных цилиндрических деталей, таких как чугунные трубы, за счет перегрузки, возникающей в прядильной форме. Расплавленный металл, введенный в форму, отбрасывается на внутреннюю поверхность формы, в результате чего отливка может быть без пустот.Первоначально изобретенный как процесс де Лаво с использованием форм с водяным охлаждением, этот метод применяется к симметричным деталям, таким как грунтовая труба и большие стволы орудий, и имеет преимущество изготовления деталей с использованием минимального количества стояков. Для асимметричных деталей, которые нельзя вращать вокруг собственных осей, вариант центробежного литья, называемый литьем под давлением, размещает несколько деталей вокруг общего литника и вращает формы вокруг этой оси. Аналогичная идея применяется к отливке очень больших зубчатых колес и т. Д.В зависимости от отливаемого материала могут использоваться металлические или песчаные формы.
Постоянное литье формы
Литье в постоянную форму имеет сходство с литьем под давлением и центробежным литьем, особенно с использованием многоразовых форм. Они могут быть изготовлены из стали, графита и т. Д. И обычно используются для литья таких материалов, как свинец, цинк, алюминиевые и магниевые сплавы, некоторые виды бронзы и чугун. Это процесс при низком давлении, когда заливка обычно выполняется вручную с использованием нескольких форм на поворотном столе.По мере того как формы вращаются через различные станции, они последовательно покрываются, закрываются, наполняются, открываются и опорожняются. Один из таких методов известен как литье под давлением, при котором форма заполняется, но опорожняется до того, как металл полностью затвердеет. Расплавленный металл выгружается из отливки для получения полой литой оболочки. Похожая идея используется при лепке полых шоколадных изделий, например, пасхальных кроликов. Использование металлических форм способствует более быстрой передаче тепла через форму, позволяя оболочке затвердеть, в то время как ядро остается жидким.
Резюме
В этой статье представлено краткое обсуждение различных типов процессов литья. Для получения дополнительной информации о связанных продуктах или процессах обратитесь к другим нашим руководствам или посетите платформу Thomas Supplier Discovery Platform, чтобы найти потенциальные источники поставок или просмотреть подробную информацию о конкретных продуктах.
Добавить комментарий