Цементобетонные покрытия – Устройство цементобетонных покрытий | roadtm.com
Цементобетонные дороги — плюсы и минусы — журнал За рулем
В мартовском номере ЗР мы рассказывали о дорогах будущего. О том, какие технологии помогут сделать их комфортнее и долговечнее. Одним из эпизодов той заметки стала разработка швейцарской LafargeHolcim, одного из крупнейших в мире производителей цемента. Компания продвигает идею замены в России асфальтобетонных дорожных покрытий цементобетонными. Опять бетонки?
Хочу сразу оговориться, что под такими дорогами мы подразумеваем современное монолитное полотно, ровное и жесткое, а не фрагментированную дорогу, наспех уложенную из бетонных плит, порой со значительными перепадами высот в местах их стыков.
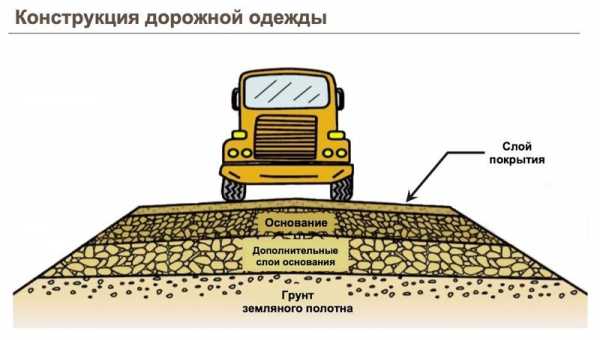
Согласно нашим исследованиям, жизненный цикл цементобетонных автодорог в 3 раза длиннее асфальтобетонных. Первоначально стоимость строительства цементобетонных покрытий на 5–20% дороже асфальтобетонных. Но, если подробно разбирать финансовую составляющую вопроса, расходы на ремонт и эксплуатацию асфальтобетонных покрытий в перспективе жизненного цикла (около 25 лет) таковы, что возведение и эксплуатация альтернативных цементобетонных покрытий обходится на 40–50% дешевле. Особенно цементобетонные покрытия оправдывают себя в условиях высокой интенсивности движения, и/или большой грузонапряженности автомобильных перевозок.
Их опыт

Материалы по теме
Технология строительства дорог с применением цементобетонных покрытий используется в мире уже около 50 лет, она нашла применение в странах с самыми разными климатическими условиями. Например, цементобетонные покрытия распространены в Канаде, стране, очень схожей по климатическим условиям с Россией. И Норвегии, но с оговоркой, что скандинавские страны являются не совсем корректным примером, так как в большей части расположены на территориях с огромными залежами гранита, который они имеют возможность сыпать по 80 см в дорожную одежду. Плюс масштабы страны и, как следствие, логистика минимальны. Если к этому всему добавить скальные грунты, которые по своим свойствам изначально превосходят наши суглинки в десятки раз, то разница между нами становится очевидной. Однако и в скандинавских странах имеется небольшая доля бетонных дорог (от 5 до 13%).
В США и Польше разработаны специальные стандарты, регулирующие технологию. Для нашей страны методика на данный момент является инновационной: она не была широко использована прежде и является альтернативой существующей практике.
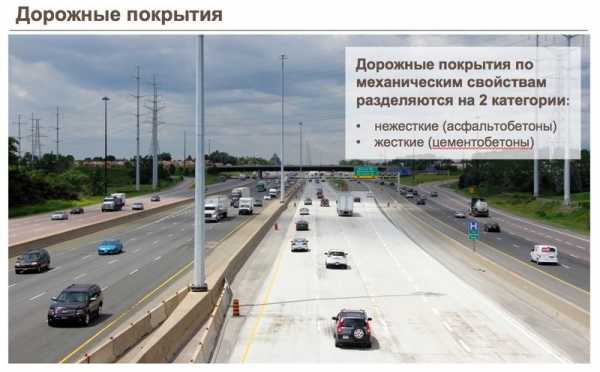
www.zr.ru
Цементобетонное покрытие дорог
Технология не требует применения особых техники и исходных материалов и характеризуется использованием двух асфальтобетонных смесей с очень высокой температурой, а также уплотняющих органов асфальтоукладчика, обеспечивающих виброуплотнение, и катков для запрессовки одной смеси в другую. Зарубежных аналогов таким покрытиям пока нет.
Смеси, разные по структуре, свойствам и назначению, запрессовывают друг в друга в один асфальтобетонный слой в процессе устройства. В нижний слой покрытия укладывают вибролитую смесь (II тип по ТУ), сверху — высокощебенистую смесь. В результате получают экономичное, прочное, ровное, шероховатое плотное дорожное покрытие, устойчивое к колее и трещинам, рассчитанное на самые тяжелые условия движения и имеющее большой срок службы.
Приготовление литой асфальтобетонной смеси из новых материалов в термосемиксере обходится дороже, чем в заводской смесительной установке, на 15—20 %.
Вибролитьевые и литьевые технологии строительства и ремонта асфальтобетонных покрытий открывают новые широкие возможности повышения транс- портно-эксплуатационных характеристик автомобильных дорог. В асфальтовом покрытии в качестве вяжущего материала смеси используется битум, в бетонном — цемент. В некоторых вариантах может применяться композитный материал, когда на бетон кладут асфальт, обеспечивая таким образом качественный нижний слой на многие десятилетия, и меняют каждые лет пять-семь верхний асфальтобетонный, что позволяет создать долговечную и прочную дорогу.
Покрытия из цементобетона устраивают на дорогах I, II и III категорий при большой интенсивности движения (более 3000 автомобилей в сутки). Преимуществами цементобетонных покрытий являются высокая прочность, ровность и в то же время достаточная шероховатость, обеспечивающая хорошее сцепление автомобильных шин с поверхностью дороги.
Цементобетонные покрытия находят все большее применение ввиду своей экономичности и простоты эксплуатации. Производство работ по устройству цементобетонных покрытий почти полностью механизировано.
Цементобетонное покрытие представляет собой плиту из бетона, уложенную на прочное и устойчивое основание. В качестве оснований под бетонные покрытия применяют слои грунта, укрепленные вяжущими, крупнозернистый или среднезернистый песок, щебень, гравий или гравийно-песчаную смесь.
Для предохранения плиты от образования трещин при температурных изменениях устраивают температурные швы. Швы расширения (поперечные), обеспечивающие удлинение плиты, имеют зазор 2,5—3 см и устраиваются через 20—80 м.
Фактически наши дороги требуют ремонта уже через три года после ввода в
эксплуатацию, а затем — ежегодно так называемый ямочный ремонт. А на Западе дороги без ремонта работают десятилетиями!
По статистике, бетонное покрытие, показанное на рис. 2.5, дороже асфальтового в 1,5—2 раза, т. е. примерно на 70—80 %. Асфальтовое требует ухода и ремонта
studfiles.net
Строительство цементобетонных покрытий
Строительные машины и оборудование, справочник
Строительство цементобетонных покрытийКатегория:
Техника при ремонте автомобильных дорог
Строительство цементобетонных покрытий
Технология устройства цементобетонных покрытий состоит из следующих операций: – подготовительные работы; – доставка приготовленной смеси к месту укладки; – распределение смеси; – формирование конструктивного слоя; – уплотнение цементобетонной смеси; – отделка поверхности цементобетонного покрытия; – уход за свежеуложенным бетоном; – устройство швов; – герметизация швов.
К подготовительным работам при устройстве цементобетонных покрытий относятся:
1) установка копирных струн, которые обеспечивают ровность конструктивных слоев дорожной одежды и их плановое и высотное расположение при работе бетоноукл ад очных машин со скользящей опалубкой;
2) установка рельс-форм для работы комплектов машин на рельс-формах;
3) заготовка и установка арматуры и конструкций швов расширения.
Натяжение копирной струны производится с двух сторон для работы бетоноукладчика со скользящей опалубкой. Копирные струны закрепляются в кронштейнах на стойках. Стойки выставляются при помощи теодолита и нивелира на расстоянии друг от друга 4-6 м на криволинейных участках и через 15 м на прямых. Кронштейны крепятся на стойках на высоте 0,5-1,0 м от поверхности нижележащего слоя. Отклонение копирной струны от вертикальных отметок не должно превышать ±3 мм.
Установка рельс-форм — трудоемкая операция, выполняемая при помощи геодезических инструментов и автокрана. Рельс-формы предназначены для движения по ним комплекта машин и одновременно с этим являются опалубкой для бетона.
Рельс-формы должны устанавливаться на спланированное основание шириной не менее 0,5 м с каждой стороны бетонирования (из щебня, гравия или грунта, укрепленного вяжущими материалами) или на уширенное для этого основание под покрытие. Не допускается осадка основания от воздействия бетоноукладочных машин во время укладки. Для этого установленные рельс-формы следует обкатывать наиболее тяжелой машиной комплекта. Отклонение отметок рельс-форм после обкатки не должно превышать +5 мм. Непосредственно перед укладкой бетонной смеси рельс-формы необходимо смазать с внутренней стороны отработанным маслом.
Отделять рельс-формы от бетона следует с помощью приспособлений, обеспечивающих целостность боковых граней и кромок уложенного слоя, не ранее 24 часов после укладки.
При устройстве цементобетонных покрытий на участках высоких насыпей над трубами, на подходах к путепроводам, мостам производится армирование слоя покрытия.
Металлические сетки устанавливаются в проектное положение при помощи сухариков бетона или арматурных закладных деталей.
Доставку приготовленной смеси к месту укладки можно производить различными транспортными средствами, учитывая при этом объем работ и дальность транспортирования. Дальность транспортирования смеси следует рассчитывать с учетом температуры и влажности окружающего воздуха, от которых зависит скорость схватывания цементобетонной смеси. По СНиП 3.06.03.-85 смесь должна быть доставлена к месту производства бетонных работ не позднее чем за 30 минут при температуре воздуха 20-30 °С, 60 минут — при температуре 10-20 °С.
Для контроля выполнения данного условия необходимо вести строгий учет за порядком движения автотранспортных средств, если ЦБЗ обслуживает только данный объект, или каждое транспортное средство должно быть снабжено сопроводительными документами (паспорт смеси), в которых указывается марка цементобетонной смеси, подвижность смеси, время ее приготовления и место укладки. В местах выгрузки необходимо оборудовать моечные пункты для очистки кузовов автомобилей от остатков цементобетонной смеси. Автотранспортные средства должны иметь водонепроницаемый кузов с гладкой, ровной поверхностью.
Неблагоприятно сказывается длительная перевозка на качество подвижных смесей. Подвижные смеси в транспортных средствах без побуждения в пути не рекомендуется перевозить на расстояние свыше 10 км по хорошей дороге и 3 км по плохой. В качестве бетоновозов с побуждением применяют автобетоносмесители. Автобетоносмесители используют также для приготовления бетонной смеси в пути следования к месту укладки.
Дальность возки сухих смесей ограничена по экономическим соображениям расстоянием, на которое можно перевозить готовые бетонные смеси с побуждением (медленное вращение барабана 3-4 об/мин) без ущерба для качества смеси.
При устройстве цементобетонных покрытий наиболее трудоемкими являются операции по распределению, формированию, уплотнению и отделке поверхности цементобетонного покрытия. Для производства этих операций в настоящее время широко используются комплекты бетоноукладочных машин.
Развитие комплектов бетоноукладочных машин происходит по двум направлениям: создание высокопроизводительных бетоноукладочных машин со скользящей опалубкой и бетоноукладочных машин с использованием рельс-форм.
Бетоноукладчики со скользящей опалубкой представляют собой гусеничные машины, предназначенные для непрерывной укладки цементобетонных покрытий при строительстве автомобильных дорог, аэродромов, каналов. Традиционно для этих целей использовались комплекты бетоноукладочных машин ДС-100 и ДС-110 , в настоящее время на наш рынок выходит ряд фирм, предлагающих свои услуги в обновлении парка строительных машин.
Бетоноукладчики со скользящими формами фирмы «Виртген» отличаются высокой экономичностью. Их модульная конструкция позволяет быстро переоборудовать машину в зависимости от предстоящей работы.
Скользящие формы могут быть подвешены между ходовыми механизмами или сбоку методом «офсет» (со смещением). Таким образом можно использовать одну и ту же машину для устройства покрытия шириной 7,5 м и для формирования прикромочного водоотводного лотка, укрепительной полосы, направляющей стенки.
Выгрузка цементобетонной смеси осуществляется непосредственно на основание перед бетоноукладчиком или распределителем бетонной смеси, если основание достаточно прочное для движения автотранспорта. В противном случае выгрузку смеси осуществляют в приемный бункер, находящийся сбоку. Из приемного бункера смесь подается конвейером на шнек распределителя. Шнек распределителя состоит из двух частей, каждая из которых может вращаться в двух направлениях. Благодаря этому обеспечивается равномерное распределение цементобетонной смеси по ширине. Бетоноукладчики со скользящими формами SP 1600 фирмы «Виртген» позволяют формировать двухслойные цементобетонные покрытия за один проход. Один бетоноукладчик применяется для одновременного устройства бетонного слоя основания и бетонного покрытия.
Цементобетонная смесь для устройства основания подается непосредственно на основание перед бетоноукладчиком, а смесь для верхнего слоя це-ментобетонного покрытия подается в приемный бункер, находящийся сбоку или впереди бетоноукладчика. С приемного бункера цементобетонная смесь транспортером подается на рабочий орган, осуществляющий распределение и уплотнение верхнего слоя цементобетонного покрытия. Скользящая опалубка может формировать боковую поверхность слоя ровной или криволинейной для лучшего сцепления между смежными полосами.
Формирование смеси по ширине покрытия осуществляется распределителем бетонной смеси или самим бетоноукладчиком. При применении распределителя бетонная смесь распределяется на заданную ширину с некоторым запасом по толщине на уплотнение. Запас на уплотнение уточняется пробным бетонированием.
Уплотнение цементобетонной смеси и окончательное формирование осуществляется бетоноукладчиком. Для уплотнения смеси бетоноукладчик оснащен глубинными вибраторами, вибробрусьями и выглаживающей плитой.
При вибрации зерна щебня и песка располагаются плотнее, а воздух, имеющийся в смеси, вытесняется наружу. При уплотнении используют разные частоты вибрирования. Низкие частоты способствуют уплотнению более крупных частиц, а высокие — мелких. В этом случае получают плотные бетоны при малой продолжительности вибрирования. Частота колебаний находится в пределах 460-1000 Гц.
Качество виброуплотнения зависит и от продолжительности вибрирования. Оптимальная продолжительность ее зависит от удобоукладываемости смеси и находится в пределах 60-90 секунд.
При виброуплотнении цементобетонных поверхностей часто наблюдается обогащение верхних слоев излишней водой, отжатой из толщи цементобетона. Это может привести к увеличению пористости цементного камня и снижению прочности верхнего слоя.
Для окончательной отделки покрытия в комплект машин по устройству цементобетонных покрытий входит бетоноотделочная машина — трубный финишер. Рабочим органом этой машины является асбоцементная труба, подвешенная к раме машины. Передвигая трубу по свежеуложенному бетону, добиваются выглаживания поверхности. Чтобы не происходило разрушение кромок свежеуложенного покрытия при первых проходах, асбоцементную трубу устанавливают под углом к оси таким образом, чтобы края трубы не доходили до кромок покрытия на 15-20 см.
Для удаления воды, отжатой при вибрировании, на бетоноотделочной машине предусмотрено навешивание влаговпитывающего полотна, например мешковины. В конце рабочей смены мешковину тщательно промывают, очищая от цементного молока. На отделочной машине также имеется навесное оборудование по нанесению бороздок для создания шероховатости. Средняя глубина бороздок шероховатости, определяемая по методу «песчаного пятна», в зависимости от требуемой величины коэффициента сцепления колеса с покрытием должна быть в пределах 0,5-1,5 мм. Фактура обработанного покрытия должна быть однородной.
Следующей технологической операцией является уход за твердеющим бетоном. Эта операция состоит из комплекса мероприятий, обеспечивающих благоприятные условия твердения уложенной в покрытие смеси. Мероприятия включают предупреждение испарения из бетона влаги, необходимой для процесса структурообразования бетона, а также предохранения его от механических повреждений в начальном периоде набора прочности.
Длительность ухода — до набора проектной прочности, но не менее 28 суток.
Для предохранения высыхания бетона дорожных покрытий производят обработку поверхности пленкообразующими материалами, в качестве которых могут применяться помороль (ПМ-86), лак «Этиноль», битумные эмульсии. Битумные эмульсии используются реже, так как создание темной поверхности способствует нагреву покрытия, что вредит на ранних стадиях набора прочности. Для уменьшения нагрева поверхности после образования пленки, покрытие, обработанное битумной эмульсией, следует засыпать слоем песка толщиной 5 см или для осветления поверхности наносят суспензии алюминиевой пудры или известкового раствора.
В настоящее время для ухода за бетоном используют пленкообразующие материалы типа ПМ. Их наносят на бетонную поверхность в количестве не менее 400 г/м2 при температуре воздуха до 25 °С и 600 г/м2 при температуре 25 °С и выше, как правило, в два слоя с интервалом в 20-30 минут.
Пленкообразующие материалы необходимо наносить путем распыления многосопловым распределителем равномерно на всю открытую поверхность плиты (включая и боковые грани) после завершения работ по отделке покрытия.
Пленкообразующие материалы типа ПМ следует наносить после испарения влаги с поверхности бетона (поверхность становится матовой), а водную битумную эмульсию — сразу после окончания отделки поверхности бетонного покрытия.
В случае задержки с нанесением пленкообразующих материалов во избежание высыхания поверхности свежеуложенный бетон необходимо предварительно защитить путем нанесения депрессора испарения влаги. В качестве депрессора испарения влаги следует применять депрессор марки ДСШ при расходе 5-10 г/м2. Допускается применение влажной мешковины. В случае выпадения осадков следует применять рулонные пароводонепроницаемые материалы.
Для уменьшения напряжений, возникающих при сезонных и суточных изменениях температуры воздуха, в цементобетонных покрытиях устанавливаются температурные швы сжатия, расширения и коробления.
При температуре воздуха, превышающей ту, при которой устраивалось покрытие, происходит температурное удлинение плит цементобетонного покрытия, для обеспечения такого удлинения устраивают швы расширения.
Длина бетонного покрытия увеличивается пропорционально расстоянию между швами расширения, коэффициенту температурного расширения бетона и зависит от разности температур покрытия в данный момент и в момент укладки. В швах расширения покрытие разрезают по всей толщине плиты и на всю ширину. Осуществляется это при помощи прокладки из дерева.
При температуре воздуха ниже той, при которой производилась укладка цементобетонной смеси, цементобетонная плита покрытия стремится укоротиться. Швы сжатия допускают укорочение плит цементобетонного покрытия. При сокращении длины плиты силы трения между покрытием и основанием вызывают растягивающие напряжения в цементобетонном покрытии. Швы сжатия позволяют уменьшить эти напряжения и связанную с этим вероятность появления трещин.
В швах сжатия покрытие разрезается по всей ширине на 1/3 – 1/4 толщины, ниже этой прорези и возникает в дальнейшем трещина.
Швы в продольном направлении устраивают при покрытии шире 4,5 м. Этот шов называется продольным швом, или швом коробления, так как он допускает возможность температурного коробления в поперечном направлении и снижает вероятность появления продольных трещин.
Пазы деформационных швов следует нарезать преимущественно в затвердевшем бетоне алмазными дисками при достижении бетоном прочности на сжатие 8-10 МПа. Допускается устройство швов и пазов швов сжатия комбинированным способом: закладка в свежеуложенный бетон эластичной прокладки и нарезка по ней паза в затвердевшем бетоне.
Элемент шва расширения (рис. 4.15) следует перед бетонированием надежно закрепить штырями в соответствии с проектом. До установки в проектное положение дощатую прокладку следует 24 ч вымачивать в воде или смазать со всех сторон разжиженным битумом. Штыри поперечных швов сжатия следует устанавливать в проектное положение до бетонирования покрытия с использованием поддерживающих устройств или втапливать в свежеуложенный бетон вибропогружением.
Рис. 4.15. Типовая конструкция поперечного шва расширения: 1 — арматура; 2 — арматурный корпус; 3 — деревянная прокладка; 4 — битумная обмазка; 5 — пластмассовый колпачок; 6 — резиновый компенсатор
Время начала нарезки пазов швов следует определять на основании данных о прочности бетона и уточнять путем пробной нарезки. При пробной нарезке выкрашивание кромок швов не должно превышать 2-3 мм. При суточных перепадах температуры воздуха менее 12 °С пазы поперечных швов сжатия в покрытии следует нарезать в этот же день. В случае невозможности нарезать все швы подряд из-за недопустимого выкрашивания кромок шва следует устраивать контрольные швы сжатия через три-четыре плиты по двухста-дийному способу: нарезка узкого паза шва одним алмазным диском при достижении прочности бетона на сжатие около 5-7 Мпа и последующая нарезка верхней части шва до проектных размеров при достижении прочности бетона более 10 Мпа. При невозможности устройства контрольных швов по двухста-дийному способу и появлении трещин в покрытии контрольные швы следует устраивать комбинированным способом.
При суточном перепаде температуры воздуха более 12 °С пазы поперечных швов сжатия в покрытии, уложенном до 13-14 ч, следует нарезать в те же сутки. В покрытии, уложенном во второй половине дня, для обеспечения трещиностойкости следует устраивать контрольные поперечные швы через две-три плиты комбинированным способом, а последующую нарезку промежуточных швов производить в затвердевшем бетоне.
При устройстве контрольных поперечных швов комбинированным способом в бетон следует заложить эластичную ленту (прокладку) толщиной 0,2-3,0 мм, а затем по ленте следует нарезать паз шва в затвердевшем бетоне. В качестве эластичной прокладки может использоваться полиэтиленовая лента и другие аналогичные материалы, закладываемые после отделки поверхности бетонного покрытия. Установка ленты по СНиП 3.06.03.-85 не допускается, если бетонная смесь потеряла подвижность и лента не омоноличивается. Лента должна закладываться на глубину не менее 1/4 толщины покрытия и выступать над поверхностью на 0,5-1,0 см.
В конце рабочей смены и в случае вынужденного перерыва работ следует устраивать рабочие поперечные швы, как правило, по типу швов коробления с помощью приставной опалубки. Укладку покрытия от рабочего шва следует продолжать после снятия опалубки и обмазки торца плиты разжиженным битумом или пленкообразующим материалом. Если в данном месте необходим шов расширения, его устраивают на расстоянии одной плиты перед рабочим швом или после него.
Работы по герметизации швов производят в сухую погоду при температуре воздуха не ниже +5 °С. Заполнение швов, нарезанных в свежеуложенном бетоне, производят через 7 суток, а в затвердевшем бетоне — немедленно после их промывки и просушки.
Работы по заполнению деформационных швов мастиками, приготовленными на основе битума, надлежит выполнять в такой последовательности:
а на дно паза шва уложить хлопчатобумажный шнур;
а стенки паза шва смазать разжиженным битумом;
а паз шва заполнить мастикой на 2-3 мм выше уровня покрытия;
□ выступающие над пазом шва излишки мастики срезать острым скребком.
Герметизирующие материалы, приготовленные на основе битума, перед применением необходимо разогреть до температуры 150-180 °С.
Реклама:
Читать далее: Установки для приготовления битумных эмульсий
Категория: – Техника при ремонте автомобильных дорог
Главная → Справочник → Статьи → Форум
stroy-technics.ru
Глава 17. Строительство цементобетонных покрытий и оснований
17.1. Особенности строительства покрытий с применением минеральных вяжущих
Более 2 тысяч лет назад в Римской империи были построены первые дороги с покрытиями на основе минеральных вяжущих, частично сохранившиеся до наших дней. Каждый слой этой дорожной одежды выполнялся из каменных материалов различной крупности, убывающей от нижнего к верхнему слою, скрепленных минеральным вяжущим – известковым или известково-пуццолановым. Верхний слой римской дороги представлял собой жесткое бетонное покрытие, компонентами которого являлись щебень, гравий, песок и вяжущее – смесь извести и пуццоланы.
Первые покрытия из бетона на портландцементе были построены в Англии (г. Эдинбург) в 1866 г. В США первая дорога с бетонным покрытием была построена в Bellefontaine позднее на 25 лет (1891 г.). Массовое строительство таких дорог началось именно в этой стране. К 1912 г. в США имелось 400 км дорог с бетонным покрытием; к 1913 г. эта цифра удвоилась. В 1914 г. уже насчитывалось около 3 тыс. км, а в 1951 г. – 140 тыс. км.
В нашей стране первые участки бетонных покрытий были построены в 1913 г. на улицах Петербурга. В довоенный период (до 1941 г.) в России бетонные покрытия строили в опытном порядке – в небольшом объеме и с применением зарубежных бетоноукладочных машин. Широкое строительство бетонных дорог развернулось в начале 50-х гг. XX столетия с применением первого отечественного комплекта бетоноукладочных машин Д-181, Д-182, Д-195 на рельсовом ходу.
В 70-е гг. в России началось строительство цементобетонных дорожных покрытий с применением машин со скользящей опалубкой на гусеничном ходу. Были закуплены в США бетоноукладочные комплекты высокопроизводительных машин «Автогрейд», которые послужили основой для выпуска отечественных комплектов машин под маркой ДС-100, ДС-110.
В настоящее время в России эксплуатируется более 9 тыс. км автомобильных дорог с цементобетонным покрытием, таких как Москва-Волгоград, Екатеринбург-Челябинск, МКАД, МКАД-Серпухов-Тула, Екатеринбург-Серов, Омск-Новосибирск, МКАД-Кашира, обход г. Коломны и многие другие.
Стабильные транспортно-эксплуатационные показатели и высокая долговечность дают им преимущества перед покрытиями других типов.
Цементобетонные покрытия имеют высокую распределяющую способность и малую величину вертикальных упругих перемещений под нагрузкой автомобилей, незначительный износ вследствие истирания, высокий, малозависящий от увлажнения покрытия, коэффициент сцепления.
Прочностные и деформативные характеристики цементобетона практически не меняются в реально наблюдаемых диапазонах изменения температуры, влажности и скорости нагружения. Его прочность возрастает в течение всего срока службы дорожной одежды, что служит дополнительным резервом долговечности.
Благодаря светлому цвету поверхности цементобетонных покрытий для их освещения требуется на 20 % меньше энергии. На таких покрытиях автомобили расходуют примерно на 5-10 % меньше топлива, чем на асфальтобетонных. Для производства минерального вяжущего (портландцемента) имеются значительно большие сырьевые ресурсы, чем для производства битума. Цементобетонные покрытия устраивают непосредственно на месте строительства из свежеприготовленного бетона по конструктивным слоям.
В зависимости от интенсивности движения, свойств земляного полотна плита из цементобетона может быть неармированной или содержать арматурную сетку, препятствующую раскрытию трещин в случае их возникновения. Толщину плиты назначают по расчету и обычно она колеблется от 18 до 24 см, а иногда до 30 см.
Бетонное покрытие укладывают на искусственное основание из грунта, обработанного цементом, щебня, обработанного вяжущим или из других прочных материалов. Обеспечение необходимой ровности и прочности основания позволяет существенно снизить напряжения в цементобетонном покрытии, повысить его работоспособность. В мировой практике используют в основном две технологии строительства цементобетонных покрытий и оснований: в скользящей опалубке и в рельс-формах.
Во избежание разрушения бетона от совместного действия транспортной нагрузки и колебаний температуры, существенно увеличивающихся с ростом длины плит, в бетонных покрытиях устраивают деформационные швы различного назначения.
В большинстве стран технология устройства поперечных деформационных швов характеризуется нарезкой их пазов в затвердевшем бетоне самоходными многодисковыми машинами-нарезчиками.
Продольные швы в ряде случаев устраивают в свежеуложенном бетоне диском, смонтированным на бетоноотделочной машине. Качество герметизации деформационных швов определяет долговечность цементобетонных покрытий. Для герметизации всех видов швов используют герметики холодного и горячего применения.
Поперечные швы – наиболее уязвимое место бетонных покрытий. Желание избавиться от температурных швов сжатия и расширения привело к созданию непрерывно армированных цементобетонных покрытий.
В последние годы наблюдается тенденция создания дорожных бетонов повышенной прочности и долговечности. Это достигается путем модификации структуры бетона химическими добавками: пластифицирующими, воздухововлекающими и газообразующими. Направленная модификация структуры дорожного бетона позволяет создавать бетоны высокой прочности и морозостойкости при низком водоцементном отношении. Весьма перспективным является применение для строительства дорожных одежд бетонов высокой эксплуатационной надёжности (НРС – High Performance Concrete), имеющих прочность на растяжение при изгибе более 7 МПа и прочность при сжатии 80 МПа и более.
С появлением виброкатков, уплотняющих бетонную смесь до большей плотности и без раскрошивания крупного заполнителя, стало возможным использование бетонных смесей особо жесткой консистенции для строительства автомобильных дорог под тяжелые нагрузки. Отличительной особенностью применения таких смесей является меньший расход цемента по сравнению с традиционными смесями, широкое использование в их составе отходов производства, простота технологии строительства.
Дальнейшее совершенствование технологии строительства и расширение области применения цементобетонных покрытий идет по пути отказа от часто расположенных поперечных швов и повышения стойкости бетона к эксплуатационным воздействиям. Успешно решить проблему обеспечения высокой морозостойкости дорожного бетона позволяют определенные требования к цементобетону и технологии строительных работ (табл. 17.1).
studfiles.net
Конструкция монолитных цементобетонных покрытий
2.6. Толщина бетонных покрытий должна быть, как правило, одинаковой по всей ширине проезжей части. На шестиполосных покрытиях толщину крайних внешних полос допускается увеличивать на 2 см для обеспечения проезда тяжелых автомобилей. Бетонные покрытия могут быть однослойными или при наличии соответствующего технологического оборудования – двухслойными, устраиваемыми методом сращивания слоев с одновременным уплотнением верхнего и нижнего слоев, с толщиной верхнего слоя не менее 6 см.
Толщину бетонных покрытий h определяют расчетом. При использовании для покрытия бетонов, указанных в обязательном приложении 1, классов для нормативной нагрузки 50 кН на колесо минимальную толщину покрытия принимают по табл. 2.1.
Таблица 2.1
Основание | Минимальная толщина, см, покрытия при интенсивности движения расчетной нагрузки, ед/сут на полосу | ||||
более 2000 | 1000 – 2000 | 500 – 1000 | 100 – 500 | менее 100** | |
Бетонное (мелкозернистый бетон, шлакобетон) | 22 | 20 | 18 (16) | 18* (16) | 15* |
Из материалов, укрепленных неорганическими вяжущими | 22 | 20 | 18 (16) | 18* (16) | 15* |
Из щебня, гравия, шлака | – | 22 | 20 (18) | 18* (16) | 16* |
Из песка, песчано-гравийной смеси | – | – | 20 (18) | 18 (16) | 16 |
* Толщина основания в этих случаях может быть на 2 см меньше указанной в п. 2.3. ** Сооружаются при соответствующем технико-экономическом обосновании. Примечания:1. В скобках приведена толщина покрытия для облегченных условий движения. 2. Если в поперечных швах штыри не применяются, толщину покрытия увеличивают на 2 см. |
2.7. В покрытии устраивают продольные и поперечные швы (сжатия и расширения), делящие покрытие на плиты определенной длины и ширины. В конце рабочей смены или при длительных перерывах в бетонировании (более 2 – 4 ч) устраивают рабочие швы по типу швов сжатия и при необходимости швы расширения. Для предохранения покрытия от трещинообразования в раннем возрасте часть швов сжатия устраивают как контрольные и в первую очередь в свежеуложенном бетоне.
В швах предусматривают штыревые соединения. Пазы швов заполняют герметизирующим материалом.
Длину плит lсж (расстояние между поперечными швами сжатия) на укрепленном основании и на устойчивом земляном полотне принимают по расчету, но не более 25h, на земляном полотне с ожидаемыми неравномерными осадками (включая насыпи высотой более 3 м) – 22h, а в местах перехода из выемок в высокие насыпи, в местах примыкания к искусственным сооружениям и в покрытиях шириной 6 м и менее – 20h.
2.8. Продольные швы предусматривают при ширине покрытия более 23h.
Контрольные швы, по конструкции аналогичные швам сжатия, обеспечивающие температурно-усадочную трещиностойкость в раннем возрасте, устраивают через каждые 2 – 3 плиты.
2.9. При устройстве швов расширения руководствуются данными табл. 2.2. Ширину швов расширения (толщину прокладки) принимают равной 3 см.
Таблица 2.2
Ожидаемая для данного района температура нагрева покрытия в летнее время, °С | Толщина покрытия, см | Расстояние между швами расширения, число плит, при температуре воздуха во время бетонирования, °С | ||||
менее 5 | 5 – 10 | 10 – 15 | 15 – 20 | более 20 | ||
Менее 40 | 20 и более | 10 | 10 | -* | – | – |
Менее 20 | 10 | 10 | 10 | -* | – | |
Более 40 | 20 и более | 10 | 10 | 10 | -* | – |
Менее 20 | 10 | 10 | 10 | 10 | – | |
*См. п. 2.11. |
2.10. Для повышения продольной устойчивости, лучшей совместной работы плит, увеличения динамической устойчивости основания и повышения транспортно-эксплуатационных качеств рекомендуется поперечные швы устраивать наклонными в плане или в виде «елочки» с уклоном к перпендикуляру 1:10 (рис. 2.1). Количество штырей в продольном шве рассчитывают с учетом массы соседних плит без штырей в продольном шве.
Рис. 2.1. Варианты расположения швов сжатия в плане для повышения комфортности движения, для уменьшения уступов между плитами (а, б и в), ровности покрытия в жаркое время года (б и в)
2.11. Штыри в продольных и поперечных швах располагают в соответствии с рис. 2.2. Конструкции швов расширения и сжатия принимают по рис. 2.2 и 2.3.
При устройстве покрытий на цементогрунтовом основании толщиной не менее 18 см бетоноукладчиками со скользящими формами и допущении проектной организацией уступов между плитами в поперечных швах высотой до 3 мм (см, расчет основания) допускается в поперечных швах штыри не применять. Толщину покрытия в этом случае увеличивают на 2 см, а швы расширения при температуре бетонирования более 10 °С можно не устраивать.
Рис. 2.2. Расположение штырей в швах покрытий на цементогрунтовом и цементобетонном (а), щебеночном и песчаном (б) основаниях:
1 – шов сжатия; 2 – шов расширения; 3 – продольный шов; 4 – установочные шпильки (Æ 5, l – 13 … 16 см), приваренные к штырям; 5 – изоляция места сварки с помощью специальных колпачков или полиэтиленовой пленки; 6 – заполнитель (при приварке к штырям продольного шва шпилек диаметром 8 – 10 мм (в торец) длина штырей может быть уменьшена до 50 см)
Рис. 2.3. Конструкция шва расширения:
1 – прокладка из выдержанной в воде древесины; 2 – каркас для фиксации прокладки и штырей, свариваемый в кондукторе; 3 – штыри в битумной изоляции, привязываемые к каркасу; 4 – температурный компенсатор (колпачок), обеспечивающий смещение штыря в бетоне не менее чем на 2 см; 5 – заполнитель (герметик)
Для повышения продольной устойчивости рекомендуется в примыкающих к шву расширения швах сжатия, а также в швах сжатия для случаев, отмеченных в табл. 2 звездочкой, применять в нижней части деревянные прокладки треугольного сечения высотой 5 – 6 см.
2.12. При устройстве швов сжатия и расширения не допускается отклонение перекосов и наклонов штырей и прокладок от проектного положения более чем на 1 см. При устройстве пазов швов сжатия и расширения в свежеуложенном бетоне радиус закругления кромок швов не должен превышать 8 мм. Длина зоны обмазки штырей в поперечных швах разжиженным битумом составляет 2/3 длины штырей, толщина обмазки не должна превышать 0,2 мм.
Температурные колпачки, надеваемые на штыри швов расширения, должны обеспечивать свободное смещение штыря в бетоне не менее чем на 2 см.
Штыри в продольных швах устанавливают без битумной обмазки с допущением перекосов не более чем на 5 см.
2.13. Паз швов сжатия может быть в сечении прямоугольным, ступенчатым или с наклонными стенками. Ширина паза швов сжатия может быть от 4 до 15 мм, глубина паза – не менее 0,25h.
Ширина паза над швом расширения принимается равной 33 – 35 мм, глубина до верха доски – 40 – 60 мм.
Расстояние между верхней частью доски шва расширения, снимаемой после бетонирования, и поверхностью сооружаемого покрытия должно быть не менее 10 мм.
Перед мостами и путепроводами устраивают не менее трех швов расширения без штырей и прокладок, шириной по 6 см каждый, через 15 – 30 м друг от друга. Швы заполняют сильно сжимаемым материалом, например песком, обработанным битумом; вверху шва устанавливают готовую резиновую пустотелую или пористую прокладку высотой 6 см.
2.14. Армирование плит по индивидуальным проектам применяется как вариант при тяжелых нагрузках, при слабых основаниях. Для армирования следует применять арматуру периодического профиля диаметром 8 – 16 мм класса А-II в виде отдельных продольных стержней, длина которых меньше длины плиты на 100 – 200 см, или в виде плоских сеток той же длины с продольной арматурой, со средним расходом ее 2,3 – 3,4 кг на 1 м2 покрытия.
При армировании краев покрытия в нижней зоне (на высоте 40 мм от нижней плоскости) двумя стержнями (диаметром 10 – 12 мм, А-II) стержни должны быть короче длины плит на 100 см.
studfiles.net
87. Конструкции и технология устройства цементобетонных покрытий. Строительство предварительно напряженных покрытий.
В мировой практике используются две различные технологии строительства цементобетонных покрытий и оснований: в рельс-формах и скользящей опалубке.
Безрельсовая укладка бетона в покрытия автомобильных дорог основана на применении специальных машин – бетоноукладчиков со скользящими формами, рабочие органы которых выполняют за один проход машины распределение и уплотнение бетонной смеси, отделку поверхности бетона, а также устройство продольного деформационного шва. Полная автоматизация основных процессов укладки, однопроходный режим работы, отказ от трудоемких операций по монтажу и демонтажу рельс – форм позволяют резко повысить эффективность строительных работ: улучшить ровность покрытия, увеличить производительность укладки, снизить стоимость и трудоемкость работ.
Строительство цементобетонных покрытий комплектами машин со скользящими формами может иметь различное количество машин в комплекте. Комплект машин включает:
–профилировщик оснований;
-конвейер-перегружатель;
-распределитель бетонной смеси;
-бетоноукладчик;
-оборудование для заглубления арматуры;
-трубчатый финишер;
-машина для устройства шероховатой поверхности и нанесения пленкообразующих материалов;
-нарезчик швов;
-заливщик швов;
Технологическими условиями, обеспечивающими реализацию преимуществ от применения безрельсовых комплектов машин, являются: ровность и плотность основания; материал основания и его несущая способность; консистенция бетонной смеси; однородность смеси по составу и консистенции как в течение смены, так и пределах замеса; дальность возки бетонной смеси; возможность бесперебойной подачи транспорта к бетоноукладчику, все это определяется поперечным профилем, наличием подъездных путей и съездов, а также возможностью расстановки машин и механизмов на линии. При этом имеется в виду, что, во-первых, отсутствует возможность исправления основания в ходе движения машин; во-вторых, смесь выдерживается в опалубке в течение короткого отрезка времени; в-третьих, гусеничные безрельсовые машины в принципе однопроходные, что исключает возможность последующего исправления покрытия как в местах плохой отделки из-за неоднородности смеси так и в местах вынужденных остановок машины. Последнее обстоятельство следует отметить особо.
По характеру работы бетоноотделочная машина на гусеничном ходу – высокопроизводительная. При рабочей скорости около 1м/мин его сменная производительность составляет не менее 1000 погонных метров покрытия. При ширине укладки 7,5-8 м расход бетонной смеси в смену до 2000 м3. Для совместной работы с такой машиной необходим бетонный завод с часовой производительностью не менее 220-240 м3. Технология на рельс-формах:
1)Подготовка основания. Необходимо иметь достаточно прочное основание, особенно, если большие нагрузки. Как правило, во всех случаях ЗП заканчивают не менее, чем за год до устройства покрытия. Основание может служить: цементогрунтовые, щебеночные, шлаковые, гравийные и песчаные материалы. Основание должна быть не менее на 0,5м шире пр.части для установки рельс-форм.
2)Установка
рельс-форм и их обкатка. Проверяется точность установки
рельс-форм. Она должна быть 5мм.
Обкатка рельс-форм должна производится
самой тяжелой машиной комплекта.
Рельс-формы непосредственно перед
укладкой бетонной смеси необходимо
смазать с внутренней стороны отработанным
маслом.
3)Устройство выравнивающего слоя из необработанных вяжущими песков укладывают на щебеночные и гравийные основания устраивают на всю ширину покрытия. Этот слой, а также песчаное основание профилируют и уплотняют профилировщиками с фрезой или без (с фрезой – уст-во основания из грунта укрепленного цементом).
4)Установка арматуры и прокладок с арматурными штырями в швах расширения. Армирование предусматривают: при устройстве ц/б на песчаных основаниях края плит усиливают продольной арматурой в виде 2 стержней ǿ 12мм; при тяжелом движении на дорогах I и II категорий усиливают арматурными сетками при насыпях на болотах и над трубами или при насыпи выше 3м. Установку арматуры, как и установку закладных деталей швов сжатия и продольного шва, осуществляют до начала бетонирования или в процессе
5)Распределение бетонной смеси. Бетонную смесь следует распределять с помощью распределителя с учетом припуска на уплотнение, величину которого следует устанавливать в зависимости от толщины покрытия и удобоукладываемости смеси и определять при пробном бетонировании. Допускается распределение бетонной смеси бетоноукладчиком в случае выгрузки бетонной смеси на основание.
6)Укладка и уплотнение. Незначительные неровности и мелкие дефекты поверхности покрытия после прохода бетоноукладчика следует исправлять с помощью трубного финишера. Трубы финишера следует слегка увлажнить тонко-распыленной водой через систему орошения. Уплотнение и отделку бетона в покрытии следует производить. как правило, непрерывно, избегая остановок бетоноотделочной машины с включенными вибраторами.
7)Нарезка швов в свежеуложенном бетоне осуществляют спциальным нарезчиком, который движется в потоке машин за бетоноотделочной машиной в 5-10м от нее. После нарезки бетон отделывают в зоне шва.
8)Обработка поверхности бетонного покрытия. Шероховатость бетонного покрытия следует устраивать путем обработки поверхности свежеуложенного бетона мешковиной, щетками, дисковой накаткой и др.
9)Уход за свежеуложенным бетоном. Уход за свежеуложенным бетоном следует осуществлять до момента достижения бетоном проектной прочности, но не менее 28 сут. Для ухода за бетоном следует применять пленкообразующие материалы, которые наносятся на бетонную поверхность в количестве не менее 400 г/м2 при температуре воздуха до 25°С и 600 г/м2 при температуре 25 °С и выше, как правило, в два слоя с интервалом в 20—30 мин. В случае выпадения осадков следует применять рулонные пароводонепроницаемые материалы.
10)Снятие рельс-форм производят не ранее 24 ч после укладки бетонной смеси. Отделять рельс-формы от бетона следует с помощью приспособлений, обеспечивающих целостность боковых граней и кромок плит. После их снятия торцы бетонной плиты обрабатывают битумной эмульсией или другими водонепроницаемыми материалами.
11)Нарезка швов в затвердевшем бетоне производят при наборе прочности бетона 8-10 МПа. При этом осуществляетсЯ пробная нарезка шва и проверка кромок. Если происходит выкрашивание кромки, то нарезка прекращается и необходимо дождаться набора большей прочности.
12)Заливка швов мастикой.
Строительство предварительно напряжённых монолитных
цементобетонных покрытий
Плюс: уменьшение толщины слоя.
2 системы по способу создания преднапряжения и способу работы: 1) подвиж., 2) неподвижн.
Минус: концевые упоры достаточно жесткие; домкратами разжимается по центру уже застывшее покрытие; сложная технология, требующая сложного оборудования; необходимость периодического создания напряжений из-за усадки.
НЕПОДВИЖН: (рис.52а)
1) строятся концевые упоры (разбивочные работы; рытьё котлованов под концевые упоры; изготовление арматурного каркаса; установка опалубки; уст. арматуры; бетонирование концевого упора; уход за бетоном; снятие опалубки; уход за бетоном; обратная засыпка котлована; уплотнение грунта; набор прочности бетона концевых упоров)
2) строительство монолитного напряженного покрытия (подготовка основания; формирование плиты бет. покр. (часто компл. на рельс-формах) специализированным комплектом машин; уход за покрытием; установка домкратов в силовой шов; поэтапное обжате покрытия по мере набора прочности бетона; фиксация проектного положения плит)
(гидродомкрат – прокладки; клинья – омоноличивание, заанкеривание арматуры; пневмодомкрат – металлич. накладки и омонол. шов)
ПОДВИЖН: (сущ. с внешним и внутренним обжатием) (рис.52б,в)
С внешним обжатием осущ. по технологии аналогичной неподвижной. Разница заключается в конструкции силового шва. В подвижн. системе примен. упругий шов. Наиболее широкое распространение получили покрытия с внутренним обжатием, которые могут устр. с напряжением арматуры до бетонирования или после бетонир. и набора прочности бетона.
Струнно-бетонное покр. (рис 53) Возможны различные варианты устр. покр. с созданием напряжения после бнтонирования. а) продольн. б) диагональн. в) по периметру
а
б
в
При устр. покр. из напряженных плит, в частности из стр-бет. плит, на подходах к искусств. сооружению надо обязательно устраивать либо несколько коротких плит со швами расширения, либо швы расширения спец.конструкции (и с легко сжимаемыми прокладками).
а) неподвижная внешнеобжатая
б) подвижная с внешним обжатием
в) подвижная с внтуренним обжатием
Рис. 17.11. Принципиальная схема струнобетонного покрытия:
1 – анкерные упоры; 2 – плиты струнобетонного покрытия; 3 – швы
расширения; 4 – продольные швы между захватками; 5 – песчаное основание;
6 – подшовные плиты
.
studfiles.net
13.Технология строительства монолитных цементобетонных покрытий.
Технология устройства цементобетонных покрытий состоит из следующих операций:
подготовительные работы;
доставка приготовленной смеси к месту укладки;
распределение смеси;
формирование конструктивного слоя;
уплотнение цементобетонной смеси,
отделка поверхности цементобетонного покрытия;
уход за свежеуложенным бетоном;
устройство швов;
герметизация швов.
К подготовительным работам при ус, устройство цементобетонных покрытий относятся:
установка копирных струн, которые обеспечиваю ровность конструктивных слоев дорожной одежды и их плановое и высотное расположение при работе бетоноукладочных машин со скользящей опалубкой;
установка рельсформ для работы комплектов машинна рельсформах;
заготовка и установка арматуры и конструкций швов расширений Натял эние копирной струны производится с двух сторон, (для работы бетоноукладчика со скользящей опалубкой;. Копищщг/ ; струны закрепляются в кронштейнах на ет йках
Конструкция шва расширения приведена на рис.2.15.
Доставку приготовленной смеси к месту укладки можно производить различными транспортными средствами, учитывая при этом объем работ, дальность транспортирования. Дальность транспортирования смеси следует рассчитывать с учетом температуры и влажности окружающего воздуха, от которых зависит ско-оость схватывания цементобетонной смеси. По СНиП 3.06.03.-85 “смесь должна быть доставлена к месту производства бетонных работ не позднее, чем за 30 минут при температуре воздуха 20-,30 °СА 60 минут при температуре 10-20 °С.
Дальность возки сухих смесей ограничена по экономиче-/ ским соображениям расстоянием, на которое можно перевозить ( готовые бетонные смеси с побуждением (медленное вращение барабана 3-4 об/мин) без ущерба для качества смеси При устройстве цементобетонных покрытий наиболее трудо-/ емкими являются операции по распределению, формированию, уплотнению и отделке поверхности цементобетонного покрытия. Для производства этих операций в настоящее время широко используются комплекты бетоноукладочных машин.
Развитие комплектов бетоноукладочных машин происходит по двум направлениям. Это создание высокопроизводительных ч^ бетоноукладочных машин со скользящей опалубкой и бетоноук-ладочных машин с использованием рельсформ.
Следующей технологической операцией является уход затвердеющим бетоном. Эта технологичес сая операция состоит из комплекса мероприятий, обеспечивающих благоприятные условия твердения уложенной в покрытие смеси. Мероприятия включают предупреждение испарения из бетона злаги, необходимой для процесса структурообразования бетона, а также предохранения ч§го от механических повреждений в начальном периоде набора 11рочности.
Длительность ухода —до набора проектной прочности, но не менее 28 суток.
Для предохранения высыхания поверхности бетона дорожных покрытий производят обработку поверхности пленкообразующими материалами, в качестве которых могут применяться \ помороль (ПМ-86), лак «Этиноль», битумные эмульсий
ДлЯ уменьшения напряжений, возникающих при сезоньых / и суточныx изменениях температуры воздуха в цементобетон? ых покрытиях устанавливаются температурные швы сжатия, pacширения и коробления.
При температуре воздуха, превыпающей ту, при которой устраивалось покрытие, происходит температурное удлинение i плит цементобетонного покрытия, для обеспечения такого удлинея устраивают швы расширения.
В швах сжатия покрытие разрезается по всей ширине на
1/3 —1/4 толщины, ниже этой прорези и возникает в дальнейшем трещина.
Швы в продольном направлении устраивают при покрытии шире 4,5 метров. Этот шов носит наименование продольного шва или шва коробления, так как он допускает возможность температурного коробления в поперечном направлении и снижает вероят-.цость появления продольных трещин.
Время начала нарезки пазов швов слодует определять на ос-/ новании данных о прочности бетона и уточнять путем пробной ! нарезки. При пробной нарезке выкрашивание кромок швов не должно превышать 2-3 мм. При суточных перепадах температуры воздуха менее 12 °С пазы поперечных швов сжатия в покрытии следует нарезать в этот же день. В случае i звозможности нарезать все швы подряд из-за недопустимого выкрашивания кромок шва i следует устраивать контрольные швы сжатия через три-четыре плиты по двухстадийному способу: нарезка узкого паза шва од-• ним алмазным диском при достижении прочности бетона на сжатие около 5-7 Мпа и последующая нарезка верхней части шва до проектных размеров при достижении прочности бетона более 10 Мпа. При невозможности устройства чонтрольных швов по двухстадийному способу и появлении трс, цин в покрытии контрольные швы следует устраивать комбинк ^ованным способом.
Работы по заполнению деформационных швов мастиками приготовленными на основе битума, надлежит выполнять в посдовательаости:
на дно паза шва уложить хлопчатобумажный шнур;
стенки паза шва смазать разжиженнь-м битумом:
паз шьа заполнить мастикой на 2-3 м л выше уровня покры тия;
выступающие над пазом шва излишка мастики срезать острым скребке м.
Гермечизирующие материалы, приготовленные на основе битума, перед применением необходимо ра; эгреть до температуры 150-180 °С.
studfiles.net
Добавить комментарий