Горный экскаватор – Обзор экскаваторного парка горных предприятий – Основные средства
Новые возможностиРазработка крепких горных пород гидравлическими экскаваторами
С внедрением объемного гидропривода в экскаваторостроении появилась возможность создавать более прогрессивные конструктивно-компоновочные схемы рабочего оборудования. Была введена дополнительная степень свободы ковша, система раскрытия и др. Рабочее оборудование гидравлического экскаватора в виде манипулятора имеет неоспоримые технологические преимущества перед традиционной схемой рабочего оборудования канатных механических лопат. Манипулятор, в определенной степени представляющий собой механическую руку, позволяет проводить качественную экскавацию грунта, в том числе разборку устойчивых массивов. Именно возможность разборки устойчивого массива еще расширяет область применения гидравлических экскаваторов, например при разработке пород повышенной крепости без предварительного рыхления.
На горных предприятиях основным способом рыхления крепких горных пород перед экскавацией является проведение буровзрывных работ. На протяжении многих лет разработчики, пытаясь найти альтернативу взрывному рыхлению, предлагают различные способы механического воздействия на породный массив, однако, как показывает практика, эффективной альтернативы взрывному рыхлению пока нет. Тем не менее повысить порог крепости отрабатываемых горных пород без взрывного рыхления вполне возможно, и гидравлические экскаваторы позволяют это делать.
Применительно к экскаваторам можно утверждать, что эффективное резание массива происходит при разработке относительно слабых пород (глины, бурый уголь, мягкие грунты при промерзании на глубину не более 1 м и др.) с пределом прочности на сжатие до 10 МПа. Разработка экскаватором более крепких пород резанием уже нецелесообразна. Возрастающие усилия вынуждают уменьшать толщину «стружки», ковш начинает просто царапать поверхность забоя, наполняемость ковша резко снижается, растет износ инструмента и нагрузка на узлы машины.
Структура породного массива не всегда однородна. В нем могут существовать системы трещин, слоистость, которые разбивают массив на отдельности – блоки разного размера. Это особенно присуще осадочным породам, таким как известняк, доломит, мергель – в них трещины возникли при уменьшении объема горных пород при «усыхании». Естественно, что по границам трещин и слоев связи значительно ослаблены и массив можно разбирать по уже существующим отдельностям. Рабочее оборудование гидравлического экскаватора благодаря дополнительной степени свободы ковша позволяет вырывать данные отдельности из массива, т. е. разбирать забой без предварительной взрывной подготовки.
Эксплуатационная масса, т | 284 |
Вместимость ковша «прямая лопата», м3 | 16,0 |
Вместимость ковша «обратная лопата», м3 | 17,0 |
При соответствующих геологических условиях (крупность блоков-отдельностей, крепость связей и крепость породы) применение мощных гидравлических экскаваторов для безвзрывной выемки может быть весьма целесообразным. Примером может служить карьер известняка в Альмендингене (Германия), где добывают сырье для местного цементного завода. Экскаватор RH-120-E «обратная лопата» производства Terex O&K, оборудован специально изготовленным скальным ковшом вместимостью 8,4 м
Экскаватор располагается на кровле уступа, высота которого 5 м, погрузка осуществляется в самосвалы грузоподъемностью 85 т. Производительность экскаватора – около 840 т/ч, расход топлива – 121,3 л/ч. Плотность известняка находится в пределах 2,0…2,2 т/м3. Раньше при проведении взрывных работ на этом участке расход взрывчатки составлял 120…140 г/т.
Ковш состоит из сварного корпуса, внутри дополнительно вварена перегородка, добавляющая жесткости всей конструкции. На режущей кромке установлены 4 зуба. Зубья по центру ковша выдвинуты вперед относительно боковых и играют роль рыхлителей. Вместимость ковша значительно уменьшена в первую очередь для снижения нагрузки на рабочее оборудование и увеличения усилия на режущей кромке. Снижение производительности экскаватора в данном случае больше связано с крепостью породы и скоростью наполнения ковша, чем с его вместимостью.
«Обратная лопата» конструктивно больше подходит для разбора не взорванного забоя, так как позволяет разгружать ковш опрокидыванием и не требует челюстного раствора, как у «прямой лопаты». Для таких условий ковш должен быть значительно более жестким, устройство разгрузки здесь нежелательно, а с точки зрения кинематики движения ковша значимых преимуществ у «обратной лопаты» не имеется.
Успешная работа этой машины на относительно крепких известняках обеспечивается прежде всего неоднородностью массива, слоистостью и наличием системы эндогенных трещин, а также размерами отдельностей. Однако такой опыт не дает гарантии успешной работы подобных машин на других месторождениях известняка. Важно учитывать технологическую цепочку дальнейшей переработки добываемого ископаемого. Например, если речь идет о вскрышных работах и фракционный состав горной массы не имеет значения, то мощными экскаваторами можно разбирать крупноблочные массивы на негабариты и вывозить их в отвал. А если добываемая масса подлежит дальнейшему дроблению и измельчению и размер кусков уже имеет важное значение, то экскавация должна проводится без образования негабарита.
Эксплуатационная масса, т | 186,5 |
Вместимость ковша «прямая лопата», м3 | 11,0…5,0 |
Вместимость ковша «обратная лопата», м3 | 4,4…12,0 |
В прошлом году на карьере Щуровского цементного завода была внедрена безвзрывная технология разработки карбонатного массива Приокского месторождения с использованием гидравлического экскаватора «обратная лопата» Hitachi EX1900 (мощность двигателя 765 кВт). В этом массиве существует несколько систем вертикальных эндогенных трещин и слоистость, при этом слои известняка перемежаются слоями мергелей и доломитов. Трещины в массиве составляют сложные секущие друг друга сети (ширина от долей миллиметра до 1 см). Частота трещин увеличивается с уменьшением мощности пласта. Размер отдельностей, образованных трещинами, составляет от 300 мм до 1,2 м.
Экскаватор был оснащен специально изготовленным скальным ковшом с пятью зубьями и центральной перегородкой. Перегородка плавно переходит в центральный зуб-рыхлитель, который выступает вперед на 1 м относительно других зубьев. Кроме этого на торцы боковых стенок и в пространство между зубьями режущей кромки ковша установлены предохранительные плоские зубья (в виде лопаток). Вместимость ковша – 6 м3.
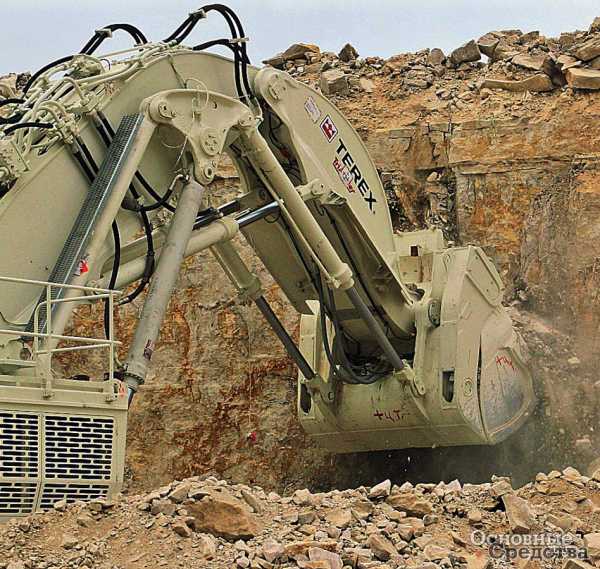
Несмотря на геологические предпосылки (наличие системы трещин и слоистости), испытания показали низкую эффективность новой технологии. Экскаватор работал в режиме перегрузки, что вызывало периодические отказы оборудования, повреждения шарниров стрелы и рукояти. Масса машины оказалась недостаточной для стабилизации во время черпания, гусеницы скользили по поверхности уступа при внедрении ковша. В то же самое время выход негабарита (более 800 мм) составлял менее 2%, а фракция от 32 до 300 мм составляла более 70% от всего объема выработанной горной массы.
Эксплуатационная масса, т | 170 |
Вместимость ковша «прямая лопата», м3 | 10,0 |
Вместимость ковша «обратная лопата», м3 | 10,0 |
Весной этого года на известняковом карьере Жигулёвского комбината строительных материалов – Яблоновском месторождении карбонатных пород провели испытания по внедрению безвзрывной технологии с иcпользованием двух гидравлических экскаваторов RH-90 Terex O&K «прямая лопата». Экскаваторы были оборудованы стандартными скальными ковшами вместимостью 8 м 3.
В геологическом строении месторождения представлены различные по составу ярусы с переслойками известняков и доломитов. Изначально планировалось отрабатывать третий пласт известняков (крепость 7…8 по шкале М.М. Протодьяконова, плотность 2,3 т/м3). Ранее при взрывании данного известняка расход взрывчатки составлял 500 г/м3 (сравните с расходом взрывчатки на карьере в Германии около 300 г/м3). В течение первых дней после запуска экскаваторов в работу разработка проходила удовлетворительно ввиду наличия перебура, оставшегося после предыдущего взрывания. Но по мере завершения отработки ослабленного слоя нагрузки на машины резко возросли, и экскаваторы стали не справляться с разборкой забоя. Ситуация развивалась по «щуровскому» сценарию, оборудование начало отказывать, в частности начали выходить из строя шарнирные соединения рабочего оборудования. Ковш стал «царапать» поверхность забоя, для его наполнения требовалось многократно «сдирать» некое подобие породной стружки значительно удлиняя тем самым продолжительность рабочего цикла.
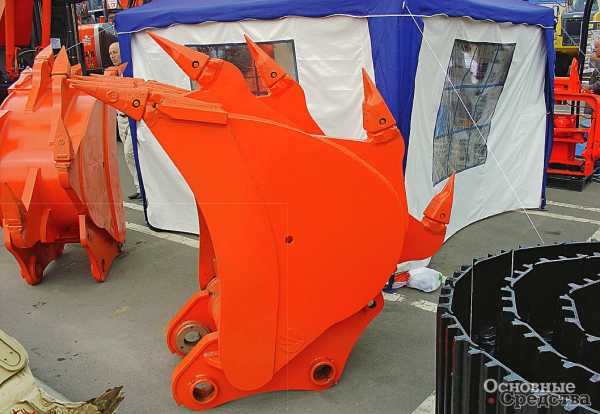
В настоящий момент отработка известняка проводится при взрывном «встряхивании» массива с расходом взрывчатки 120 г/м3. Встряхивание порождает систему трещин в массиве, что позволяет вести качественную экскавацию. Второй экскаватор используется на отработке скальной вскрыши, составленной пермским доломитом. Крепость f = 4…5 по шкале М.М. Протодьяконова, также с предварительным взрывным встряхиванием.
Опыт показывает, что внедрение безвзрывной технологии с применением экскаваторов рабочей массой менее 300 т неэффективно. Обе модели экскаваторов RH-90 и EX1900 являются слишком легкими для такого вида работ.
Для создания нужного усилия на режущей кромке ковша необходимо уменьшать площадь контакта рабочих поверхностей с забоем, т. е. уменьшать число зубьев при одновременном их усилении и сохранении оптимального шага установки. С учетом сохранения базового силового оборудования машины это ведет к уменьшению геометрических размеров самого ковша, а значит, его вместимость в среднем сокращается более чем вдвое. Это условие не было выполнено на RH-90, где использовался стандартный скальный ковш. Перед внедрением подобных технологий необходимо детально изучить структуру массива планируемых к разработке пород. Уже на этой стадии можно оценить, насколько эффективно будет справляться экскаватор с такими породами, предугадать примерный фракционный состав материала после экскавации. Следует учитывать и снижение срока эксплуатации экскаватора, так как разборка не взорванного забоя приводит к работе машины в сверхнагруженном режиме и износ оборудования многократно усиливается. Только трезво взвесив все «за» и «против», можно принимать решение о внедрении новой технологии.
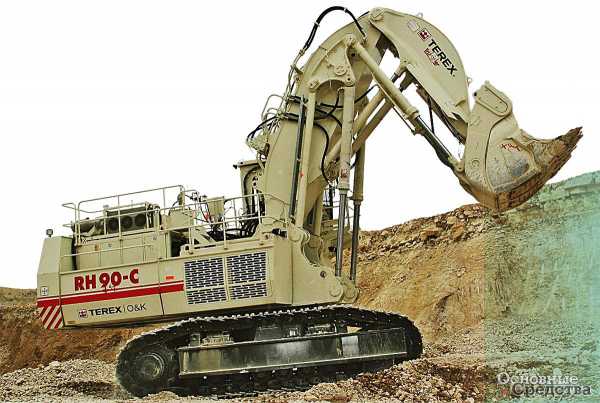
os1.ru
Горный гидравлический экскаватор CAT 6020B с безопасной простой эксплуатацией и удобным обслуживанием
В статье представлен обзор принципиально нового проекта горного гидравлического экскаватора CAT 6020B с современной кабиной, усовершенствованной гидравликой, автоматической системой смазки, диагностическими средствами поиска и устранения неисправностей и другими полезными возможностями.
Горный гидравлический экскаватор Cat 6020B – новая модель в линейке горных гидравлических экскаваторов Cat. Отличительная особенность принципиально нового экскаватора – это его улучшенные характеристики, он допускает полезную нагрузку в 22 тонны, имеет эксплуатационную массу 224 тонны и подходит для внедорожного самосвала Cat 777G, обеспечивая оптимизированную загрузку и транспортировку.
Модель 6020B была анонсирована в прошлом году и после обширных испытаний в полевых условиях скоро скоро поступит в продажу. Главным в конструции экскаватора являются простота и надежность, достигнутые без ущерба для безопасности. “Требования к машине были сформулированы с помощью службы обратной связи “Голос клиента”. Все решения, все детали проекта были основаны на сотнях комментариев, которые мы получили в течение нашего исследования мнений клиентов, — объяснила Анита Рассверм, менеджер по внедрению новых продуктов для 6020B. — При ознакомлении с этим вкладом клиентов были определены три общие темы. Клиенты хотели бы иметь машину, которая является безопасной, простой и надежной. Именно это мы заложили в проект и можем видеть во всей машине”.
Модель 6020B имеет новую, современную кабину и рабочее место оператора с самой высокой обзорностью в своем классе, которая достигается применением большого напольного окна, широкого ветрового стекла и боковых окон. Открывается прямая видимость на гусеничные ленты и дно раскопа, что упрощает работу оператора при перестановке экскаватора и загрузке самосвалов. Новаторский проект кабины включает также два дополнительных сиденья для инструктора и наблюдателя. В экскаваторах с размерами этого класса трехместная кабина установлена впервые.
“С нашими тремя испытательными машинами работали операторы трех горнодобывающих компаний из трех разных стран, и все они приспособились к 6020B очень быстро, независимо от предыдущего опыта работы на другом оборудовании, — сказал Стив Малони, инструктор по обучению операторов Caterpillar. — Трехместная кабина позволяла мне обучать одновременно двух операторов, поэтому этот процесс проходил более эффективно.
Кроме того, сиденье инструктора расположено выше, поэтому обзор области выемки грунта становится беспрепятственным, а это очень важно при обучении операторов на новом оборудовании”.
Высокая производительность и простое обслуживание CAT 6020B
Модульная конструкция с модулем энергетической установки, прошедшим сквозной контроль, обеспечивает свободный доступ к компонентам и непревзойденное удобство обслуживания. Кроме того, модульный проект упрощает доставку и сборку 6020B в поле. В конфигурации предусмотрен единственный двигатель, что также упрощает обслуживание. Двигатель Cat C32 ACERT™ на 778 кВт (1043 л. с.) приводит в действие усовершенствованную гидравлику, которая обеспечивает ведущую в отрасли эффективность системы.
Новаторская, защищенная заявками на патенты технология размещения выделенных насосов обеспечивает управление гидронасосами, что позволяет сократить потери энергии и увеличить экономию топлива. Кроме того, выделенные насосы прокачивают гидравлическое масло через контур охлаждения для поддержания оптимальной температуры масла и обеспечения работы машины даже в наиболее сложных климатических условиях и областях применения.
“Это гибкая, быстрая машина, — сказал Рил Моро, помощник главного диспетчера золотого рудника Rosebel, Суринам (на этом горном предприятии прошел испытания опытный образец 6020B). — Она позволяет нам получить высокую производительность и необходимую продуктивность. Экономическая эффективность, топливная эффективность, полная мощность — все это мы получили от 6020B”.
Кроме того, в модели 6020B предусмотрено применение автоматической системы смазки для сокращения времени обслуживания и обеспечения долговечности. Насос с гидравлическим приводом подает смазку в подшипник механизма поворота платформы, подшипник коробки передач механизма поворота платформы и во все точки поворота конструкции.
Экскаватор Cat 6020B имеет конфигурацию в виде обратной лопаты и создает превосходные усилия копания для достижения высокой производительности. В нем применяется стандартный размер ковша на 12 м3. Ковш для скальных пород Cat MultiPlus™ подходит для стандартных областей применения с каменистыми породами и грунтом, а ковши для скальных пород с высокой абразионной стойкостью в большей степени защищены для работы с плотной горной породой, при сложных условиях заглубления. Имеется также угольный ковш. Зубья ковша Cat, устанавливаемые без применения молота, спроектированы специально для 6020B и позволяют достичь оптимальной производительности. Достаточно просто повернуть зуб на 180 градусов, после чего происходит его блокирование или разблокирование, поэтому установка и снятие происходят безопасно и быстро.
“Если работа осуществляется непрерывно в три смены, наиболее важным фактором становится надежность, а производительность занимает по важности второе место. Создается впечатление, что эта машина отвечает заданным критериям и подходит для нас”, — сказал Арто Хартикайнен, генеральный директор E. Hartikainen Oy, Финляндия. Подрядчик по горнодобыче провел полевые испытания опытного образца 6020B.
Технология управления экскаватором CAT 6020B
Модель 6020B спроектирована для поддержки четырех наборов возможностей системы Cat MineStar™ — наиболее полного пакета технологических продуктов, предоставляемых для горнодобывающей промышленности. Набор возможностей Detect включает видеокамеры и более совершенные технологии применения датчиков, что позволяет повысить информированность операторов, Terrain обеспечивает управление загрузкой. Fleet предоставляет возможности отслеживания, назначения и формирования производственной отчетности, а Health формирует отчеты о состоянии машины и предоставляет диагностические средства.
Модель 6020B не только обеспечивает применение системы MineStar, но и оснащена стандартными диагностическими средствами и функциями поиска и устранения неисправностей, поддерживаемыми ее бортовой системой управления, в которой используются все установленные на машине датчики для отслеживания эксплуатационных данных, регистрации неисправностей, а также подачи оператору звуковых и визуальных уведомлений. Тем самым обеспечивается наиболее раннее обнаружение неисправностей, а также своевременное планирование обслуживания и помощь для быстрого ремонта.
Для получения более подробной информации о горных гидравлических экскаваторах CAT 6020B обратитесь к региональному дилеру Cat.
Технические характеристики горного экскаватора CAT 6020B
КОНФИГУРАЦИЯ / МОДЕЛЬ ДВИГАТЕЛЯ |
CAT C32 ACERT |
---|---|
Диапазон полезной мощности, л.с. (кВт) |
1043 (778) |
Эксплуатационная масса, тонн |
224 |
Полезная нагрузка, тонн |
22 |
Объем ковша, м3 |
12 |
По материалам: http://www.cat.com/ru_RU/ (Номер выпуска: 580PR14)
www.eltehstroy.spb.ru
характеристики, на которые стоит обратить внимание при выборе
На сегодняшний день промышленность просто не может обойтись без использования тяжёлой спецтехники. Они используются для работ в больших карьерах по добыче ископаемых. Горные экскаваторы активно используются на всех стадиях разработки открытых карьеров. Их стихия – это погрузка породы на грузовой транспорт, отвал породы, разработка карьера. Также данная техника широко используется внутри складских помещений для перемещения тяжёлых и габаритных грузов. В данных машинах есть удлинённая оснастка, для поднятия грузов выше уровня конструкции самой техники (штабилёр).
В конструкцию горных экскаваторов заложено множество преимуществ, таких как: управляемость, маневренность, надменная прочность. Также все они имеют упрощённую конструкцию, благодаря которой можно осуществлять ремонт в полевых условиях. Использовав качественные металлы в несущих конструкциях и защищённую механическую часть, инженеры вложили в данные машины большой потенциал, и их можно использовать в самых суровых климатических условиях. Машинист имеет прекрасный обзор благодаря удобно расположенной кабине в самой высшей точке конструкции.
Экскаваторы оснащены электронными системами управления, которые действуют по принципу тристоронних преобразователей. Благодаря этому происходит плавное переключение всех главных приводов по бесступенчатому принципу. Также данная система управления выдает самые наилучшие характеристики, по типу от генератора к двигателю. Все системы данных экскаваторов сконструированы в соответствии с новыми стандартами безопасности и имеют современные механизмы блокировок. Из-за продуманного размещения блоков тристоронних преобразователей можно легко получить доступ к каждому из них, что упрощает ремонт и профилактический осмотр.
Экскаватор поворотного типа имеет гусеничную ходовую часть, которая состоит из звёздочки, редуктора, гидравлического привода для системы торможения и специальных муфт, обеспечивающих плавность хода. Сердцем данной техники, придающим крутящий эффект всей ходовой части, служит электромотор. Надежный пневматический привод обеспечивает поворот всех механизмов, продувку, торможение и т.д. Питает всю пневмосистему очень производительный компрессор, обеспечивающий высокое давление. Экскаватор тормозит благодаря гидравлической системе, а также участвует в работе по переключению гусениц. Основные части узлов гидросистемы расположены в задней части.
Грузоподъемность данных машин зависит от многих факторов, таких как: расположение центра тяжести, мощность гидравлики, а также размеров и веса. Специалисты сайта http://stk-parts.ru/ рекомендуют рассчитывать нагрузку по формуле: чем массивнее конструкция, тем больше груза может поднять экскаватор.
Все технические показатели регламентированы нормами SAE. Как корпус, так и все подвижные соединения изготовлены из высокопрочного металла. Конструкция разработана с учётом максимальной производительности агрегатов и минимальной потери передаваемой энергии по шарнирной системе. Также они отличаются повышенным комфортом, как для машиниста, так и для обслуживающего персонала.
inyoutube.net
Шагающие драглайны – Журнал Горная промышленность
А.В. Груздев, технический директор дивизиона «Горное оборудование» ООО «Уралмаш – Инжиниринг» И.Н. Сандригайло, доцент, к.т.н., Уральский государственный горный университет
Многолетний опыт эксплуатации крупных шагающих экскаваторов-драглайнов на горных предприятиях мира свидетельствует о высокой эффективности этих машин.
К важнейшим их преимуществам следует отнести возможность осуществления не только выемки, но и доставки пород в ковше непосредственно во внутренние отвалы за счет большой длины стрелы. При этом, благодаря возможности экскавации как нижним, так и верхним черпанием обеспечивается разработка месторождений с большой мощностью вскрыши и высокими уступами, а низкое удельное давление на грунт при работе и передвижении позволяет осуществлять эксплуатацию экскаватора при низкой несущей способности грунтов.
Эти особенности крупных драглайнов, наряду с высокой производительностью и надежностью, обеспечили значительное их распространение на карьерах и разрезах мира. Cегодня в России находится в эксплуатации 91 крупный драглайн с ковшом вместимостью от 15 до 100 м3 и длиной стрелы 90-100 м. Все эти машины выпущены Уралмашзаводом, входящим в настоящее время в ЗАО Машиностроительная корпорация «Уралмаш» (МК «Уралмаш»).
Только на угледобывающих предприятиях Российской Федерации, где драглайны эксплуатируются более пятидесяти лет, ими по бестранспортным схемам перемещается около 30% от общего объема всех вскрышных пород.
За пределами России 243 крупных драглайна работают на горных предприятиях 12 стран мира, перемещая каждый год 3360 млн. м3 горной массы. Наибольшие парки таких машин эксплуатируется в США, Австралии, ЮАР, Канаде и Индии. Только в одних США 101 крупный драглайн ежегодно переваливает 1450 млн. м3 горной массы.
Основными тенденциями в развитии драглайнов длительное время являлось увеличение вместимости ковша и длины стрелы. Однако, в последние годы направление по созданию все более крупных драглайнов, по-видимому, исчерпало свои возможности, что определяется экономической целесообразностью. Дальнейшее развитие этого вида техники связано с совершенствованием ее конструкции. Это, в первую очередь, объясняется тем, что увеличенные затраты на особо крупные экскаваторы-драглайны не компенсируются пропорциональным возрастанием их производительности за границами некоторого предельного значения мощности машины.
На сегодняшний день крупные шагающие экскаваторы-драглайны выпускают только три производителя в мире. Это МК «Уралмаш», находящаяся в России, и американские фирмы Bucyrus и P&H.
Являясь одним из крупнейших в мире производителей шагающих драглайнов, Уралмашзавод с 1949 года выпустил и поставил на горные предприятия более 250 крупных машин с ковшом вместимостью от 11 до 100 м3 и длиной стрелы от 65 до 100 м. Эти экскаваторы нашли широкое применение на открытых разработках угля, железных и марганцевых руд, бокситов и горно-химического сырья.
Десятки шагающих экскаваторов были поставлены в Индию, Монголию, КНДР и страны СНГ, где они зарекомендовали себя как высокопроизводительные, надежные машины, хорошо приспособленные для работы в любых климатических и горно-геологических условиях.
Накопленный опыт использования крупных шагающих экскаваторов Уралмашзавода показал, что при бестранспортных системах разработки их применение позволяет в 2-3 раза снизить затраты на производство 1 м3 вскрыши и в 3-4 раза уменьшить трудоемкость вскрышных работ.
Высокие технологические параметры шагающих драглайнов, производимых МК «Уралмаш», обеспечиваются рядом оригинальных конструкторских решений. К ним относятся:
– трехгранная стрела из трубчатых поясов, соединенных между собой распорками из труб и вантами из предварительно натянутых канатов. По сравнению со стрелами решетчатой конструкции, применяемыми другими экскава-торостроительными фирмами, трехгранные вантовые стрелы Уралмашзавода имеют меньшую массу, проще в изготовлении и монтаже;
– гидравлический механизм шагания, имеющий меньшую массу по сравнению с механическим ходом и обеспечивающий возможность изменения длины шага и плавность передвижения, что снижает динамические нагрузки на металлоконструкции и другие узлы экскаватора при его перемещении;
– сравнительно невысокая поворотная платформа, образующая с надстройкой единую пространственную силовую конструкцию и отличающаяся меньшей массой и значительно меньшим объемом сварочных работ при монтаже экскаватора.
Драглайны оснащены автоматической централизованной системой смазки, обеспечивающей долговечность механизмов и узлов экскаватора с минимальными потерями мощности на трение и позволяющей экономично расходовать смазочные материалы. Информационно-диагностическая система на микропроцессорной базе позволяет контролировать расход электроэнергии, загрузку и наличие вентиляционного потока электрических машин, температуру подшипников и обмоток возбуждения, наладочные параметры.
На Уралмашзаводе создан один из крупнейших в мире драглайнов ЭШ-100.100, работавший на разрезе «Назаровский» с 1977 года. Масса машины -10300 т, вместимость ковша – 100 м3, а длина стрелы – 100 м. При его создании, монтаже и эксплуатации решены многие сложные научно-технические и производственные проблемы.
В 1993 году на разрезе «Тулунский» запущен в эксплуатацию второй по величине шагающий экскаватор, изготовленный Уралмашзаводом – ЭШ65.100 с ковшом вместимостью 65 м3 и длиной стрелы 100 м. Уже в первый же год эксплуатации его производительность составила 10 млн. м3 горной массы. Экскаватор оснащен гидравлическим механизмом шагания с полным отрывом опорной рамы от грунта посредством четырех подъемных цилиндров, опирающихся на скользящие опоры. Экскаватор при массе 5450 т показал хорошую проходимость при движении по слабым грунтам. В 1999 году на УЗТМ изготовлен и поставлен на разрез «Му-гунский» новый крупный шагающий экскаватор ЭШ-40.100 с ковшом вместимостью 40 м3 и длиной стрелы 100 м.
С 2003 года в Монголии на разрезе «Шивээ-Овоо» эксплуатируется новый драглайн ЭШ-25.90. Экскаватор снабжен самой современной цифровой системой управления, информационно-диагностической системой и системой смазки фирмы Lincoln (Германия).
Регулярным спросом пользуется экскаватор ЭШ-20.90, сменивший хорошо зарекомендовавший себя в работе на отечественных и зарубежных горных предприятиях драглайн ЭШ-15.90А. Высокая эффективность применения данных машин определила их широкое использование при добыче угля и руд. В эксплуатации на горных предприятиях сегодня находится 61 драглайн ЭШ-20.90.
В связи с потребностью российских горных предприятий в шагающих экскаваторах с ковшами вместимостью 10-11 м3 и стрелой 70-75 м МК «Уралмаш» разработана новая модель экскаватора ЭШ-11.75, имеющая повышенную надежность и проходимость за счет более прочного рабочего оборудования, более низкого удельного давления на грунт при работе и передвижении. Экскаватор имеет трехгранную ван-товую стрелу, электромеханический ход и скорость передвижения до 200 м/час. Первый такой драглайн уже в течение 6 лет успешно работает в ЗАО «Надеждинское» (ОАО «Лен-золото»). Второй ЭШ-11.75 эксплуатируется на разрезе «Степной» компании «Русский уголь», а третий – на разрезе «Майкубенский» в Республике Казахстан.
В последние годы разработаны проекты шагающих экскаваторов нового поколения. Сформирован ряд базовых моделей. Учитывая потребность горнодобывающих отраслей, предложены также модификации базовых моделей – экскаваторы с удлиненными стрелами при несколько меньшей вместимости ковша и экскаваторы с пониженным давлением на грунт. Применение экскаваторов с удлиненными стрелами обеспечивает снижение затрат на вскрышные работы за счет уменьшения коэффициента переэкскавации при бестранспортной системе разработки. Модификация экскаваторов с пониженным на 20-25% давлением может более эффективно использоваться на слабых грунтах и при отвалообразовании.
Новые технические решения, применяемые при создании шагающих экскаваторов-драглайнов, обеспечили снижение эксплуатационных издержек и энергозатрат на экскавацию при значительном росте производительности и эффективности их применения. Всего на сегодняшний день МК «Уралмаш» предлагает 13 типоразмеров шагающих экскаваторов и 6 их вариантов с пониженным давлением на грунт.
При высоком техническом уровне, экскаваторы-драглайны, производимые МК «Уралмаш», выгодно отличаются конкурентной ценой от машин аналогичного класса зарубежных производителей.
Журнал “Горная Промышленность” №5 (81) 2008, стр.6
mining-media.ru
Основные тенденции на рынке экскаваторного оборудования и новая линейка экскаваторов ООО «ИЗ КАРТЭКС» для горнодобывающей промышленности
А.В. Самолазов, Заместитель Генерального директора по развитию ООО «ИЗ-КАРТЭКС»
Т.В. Донченко, к.т.н., Начальник управления маркетинга ООО «ИЗ-КАРТЭКС»
Рынок экскаваторного оборудования России и стран СНГ отличается от рынков крупнейших сырьевых стран мира – США, Австралии, Канады, Бразилии, Чили, Перу, Индонезии и других. Это касается, прежде всего, типоразмеров и вместимости ковшей карьерных экскаваторов. Тенденция сохранения ведущей роли карьерных электрических экскаваторов с ковшом вместимостью 8–15 м3 на большинстве действующих предприятий по добыче руд чёрных и цветных металлов, горно-химического и строительного сырья России и СНГ отличается от зарубежного опыта, где в этом типоразмере основной объем закупок приходится на гидравлические экскаваторы.
Немаловажными и зачастую определяющими факторами является неудовлетворительное качество подготовки горной массы к выемке, отступление от соответствующих проектных показателей, низкий уровень сервисного сопровождения горных машин, что в совокупности делает неэффективным, а в ряде случаев и просто невозможным эксплуатацию гидравлических экскаваторов на основной выемке горных пород III–V категорий по трудности экскавации. Опыт работы гидравлических экскаваторов на Костомукшском, Ковдорском, Оленегорском ГОКах, железорудных предприятиях Украины, Навоийском и Алмалыкском ГМК, ряда угольных предприятий РФ показывает, что в таких условиях гидравлические экскаваторы, обладающие меньшей массой и менее прочными металлоконструкциями, по сравнению с их электромеханическими аналогами, быстро разрушаются, экспоненциально возрастают затраты на ремонт, и их эксплуатация становится убыточной.
Экскаватор ЭКГ8И на Нерюнгринском угольном разрезе (ОАО «Якутуголь»)
Превалирующий парк карьерных гусеничных экскаваторов крупных горнодобывающих предприятий и компаний средней мощности на территории России, Украины, Казахстана и Узбекистана составляют экскаваторы с вместимостью ковша 8–15 м3 производства ООО «ИЗ-КАРТЭКС» (Ижорские заводы – Карьерные тяжёлые экскаваторы).
ИЗ-КАРТЭКС является крупнейшим поставщиком карьерных электрических экскаваторов на территории России и стран СНГ, производство которых осуществляется с 1957 года. За этот период произведено и поставлено свыше 3000 карьерных электрических экскаваторов, из которых более 1200 находятся в эксплуатации. К ним относятся известные экскаваторы типа «прямая механическая лопата» ЭКГC8И, ЭКГC6,3УС, ЭКГC4У, ЭКГC10, ЭКГC8УС, ЭКГC5У, ЭКГC15, ЭКГC12УС, ЭКГC8У, составляющие основу парка выемочно-погрузочного оборудования крупнейших горнодобывающих предприятий России и основных добывающих стран СНГ – Украины, Казахстана и Узбекистана.
Экскаватор ЭКГ10 на угольном разрезе «Чаханур» (Китай)
Основные причины, объясняющие сложившиеся отличия коньюнктуры экскаваторного рынка РФ и СНГ от мировых рыночных тенденций:
• Длительный период стагнации российской промышленности, в том числе тяжёлого машиностроения, в результате перехода от плановой экономики к рыночной модели в период 1990–2000 гг. В эти годы фактически прекратилось развитие компании и модельного ряда в силу невостребованности рынком.
• Элементы системы разработки большинства крупных месторождений спроектированы под экскаваторы с вместимостью ковша до 15 м3 и автосамосвалы грузоподъёмностью до 140 т.
• Консерватизм проектных организаций, закладывающих в большинство действующих и новых проектов горнотранспортное оборудование уже эксплуатируемых и распространённых типоразмеров. За последние 25 лет в эксплуатацию не было введено ни одно крупное месторождение твёрдых полезных ископаемых.
• Консерватизм производственнотехнического персонала и руководителей горного сектора горнодобывающих предприятий, готовящих решение по необходимости приобретения горного оборудования.
• Отсутствие на рынке экскаваторов российского производства с вместимостью ковша более 15 м3 и опыта их эксплуатации.
Потребителями продукции компании ИЗ-КАРТЭКС являются горнодобывающие предприятия, ведущие разработку месторождений твёрдых полезных ископаемых открытым способом – железной руды, угля, меди, золота, алмазов, бокситов, апатита, асбеста, строительных материалов и пр.
Многие железорудные предприятия России и СНГ заявляют о реновации своих парков и рассматривают экскаваторы класса 18–20 м3, как основную и перспективную выемочно-погрузочную единицу. То же самое касается ряда угольных разрезов средней мощности. Это объясняется тем, что для повышения эффективности горных работ и формирования рациональных ЭАК этим предприятиям достаточно увеличить вместимость ковша и довести её до оптимальной, то есть той, которая, исходя из мирового практического опыта и теоретических исследований, позволяет достичь оптимального уровня издержек и себестоимости выемочно-погрузочных и транспортных работ. Как известно, оптимальное соотношение между вместимостью транспортного сосуда и вместимостью ковша экскаватора находится в диапазоне от 3 до 5, то есть погрузка одного автосамосвала должна производиться экскаватором за 3–5 циклов.
Экскаватор ЭКГ15 на меднорудном карьере «Эрдэнэт» (Монголия)
Для этого, не меняя транспортное звено и параметры элементов системы разработки (ширина рабочих площадок, ширина транспортных берм), необходимо «подтянуть» вместимость ковша экскаватора от современной 10 до 18–20 м3, обеспечивающих оптимальную загрузку превалирующего парка транспортных средств горной отрасли РФ и стран СНГ.
Таким образом, одной из ключевых тенденцией на передовых горных предприятиях России и СНГ является их эволюционный переход с экскаваторов класса 8–10 м3, имеющих высокий физический износ, на экскаваторы класса 18–20 м3.
До 2008 г. основной объём продаж осуществлялся на железорудные предприятия России, Украины и Казахстана. Мировой финансовый кризис привёл к резкому падению платёжеспособности на традиционных рынках чёрной металлургии и смещению спроса на более стабильные рынки угля и цветной металлургии. Так, в 2010 г. доля поставок на железорудные предприятия упала с 65 до 24%, а на предприятия по добыче угля и цветных металлов выросла, соответственно, до 39 и 33% (см. рис.).
Однако следует отметить, что крупные горные предприятия проявляют интерес к более мощным и современным экскаваторам. На рынке происходит смещение спроса к экскаваторам с вместимостью ковша 20–45 м3 и более. Начиная с 1980-х годов, на отдельных крупных разрезах страны эксплуатируются экскаваторы Marion 201М и 204М с ковшами 16 и 24 м3, P&H 2300 (21 м3), затем Marion 301М (40 м3), P&H 2800 (32–35 м3), Bucyrus 495HD (42 м3), P&H 4100 (57 м3). Сегодня угольщики являются ключевыми потребителями горного оборудования и для компании ИЗ-КАРТЭКС важно следовать требованиям этого рынка.
Открытым способом добывается практически весь энергетический уголь и около 15% коксующегося. В соответствии с пересмотренной энергетической стратегией России намечен рост добычи угля и увеличение его доли в топливно-энергетическом балансе России с ростом удельного веса открытого способа добычи с 65 до 80%. Намеченные рубежи приведут к росту потребности в карьерных экскаваторах. Осваиваются и планируются к освоению новые крупные угольные месторождения – Эльгинское, Никольское и др., что также приведёт к росту спроса на карьерные экскаваторы.
В последние годы основным спросом в мировой горной промышленности пользуются электрические экскаваторы, имеющие вместимость стандартного ковша 42–60 м3. На сегодня в мире насчитывается более 200 таких экскаваторов. В перспективе можно ожидать создание карьерных экскаваторов с вместимостью ковша до 70–80 и даже 100 м3, способных эффективно работать с автосамосвалами грузоподъемностью 400–600 и более тонн. О технической возможности налаживания производства таких самосвалов в ближайшие десятилетия уже упоминают некоторые производители. Создание же мехлопат с ковшами до 100 м3 пока сдерживается отсутствием производства соответствующих средств карьерного транспорта.
В связи с этим можно сделать вывод о том, что рабочие параметры карьерных экскаваторов на современном этапе приблизились к рациональному пределу и в настоящее время дальнейшее повышение их производительности и эффективности возможно путем совершенствования конструкции, внедрения новых средств автоматики в управление и диагностику машин.
Структура парка мощных карьеров изменяется в сторону увеличения доли крупных типоразмеров экскаваторов, что обусловлено увеличением эффективности горных работ при росте единичной грузоподъёмности и производительности горнотранспортного оборудования. Причём, несмотря на превалирующие мировые продажи и значительный интерес, проявляемый к гидравлическим машинам, крупные горные предприятия в сегменте «более 30 м3» отдают предпочтение электрическим экскаваторам-мехлопатам.
По мнению зарубежных специалистов, применение карьерных экскаваторов типа «прямая механическая лопата» целесообразно при разработке крупноблочных пород, не склонных к самообрушению после их взрывного рыхления, валовой выемке полезных ископаемых, при сроке службы карьера более 15 лет, высоте уступа более 10 метров, наличии на карьере электрического питания и при незначительных перемещениях экскаваторов по рабочей зоне карьеров.
В 2007–2008 гг. в компании ИЗ-КАРТЭКС на основе анализа тенденций развития горного производства и карьерного транспорта в России, СНГ и мире была разработана стратегия производства новой линейки карьерных экскаваторов четырёх типоразмерных групп.Экскаватор ЭКГ12К на Оленегорском карьере (ОАО «Олкон»)
Как известно, в мире существует две основные концепции конструктивного исполнения напорного механизма электромеханических экскаваторов – реечная и канатная.
Каждое исполнение рабочего оборудования имеет свои достоинства и недостатки. В 2008 г компания Bucyrus предложила третий вариант, пока не получивший массового распространения, – гидравлический напор. С точки зрения технологии ведения горных работ конструктивное исполнение напорного механизма экскаваторов не принципиально, однако одни заказчики предпочитают реечные экскаваторы, другие – канатные.
Учитывая данную особенность рынка, компания ИЗКАРТЭКС выбрала стратегию производства унифицированных экскаваторов (см. табл.): в зависимости от предпочтений заказчика экскаваторы могут поставляться с канатным (К) либо реечным (Р) исполнением рабочего оборудования в рамках единой базовой платформы. Модели экскаваторов отличаются только рабочим оборудованием (ковш, стрела, рукоять), устанавливаемым в кронштейне поворотной платформы. Узлы экскаваторов унифицированы на 80%.
В компании работает инжиниринговый центр, оснащенный новейшей компьютерной техникой и программными продуктами. На базе 3D-проектирования и пакета Unigraphics разрабатываются все новые модели экскаваторов, а также осуществляется модернизация серийного горного оборудования.Карьерный экскаватор ЭКГ50 (проект)
Основные решения, повышающие технический уровень экскаваторов ИЗ-КАРТЭКС нового поколения, состоят в следующем:
• Применение 3D-проектирования, что в сочетании с использованием современных высокопрочных сталей обеспечивает увеличение надежности и долговечности узлов.
• Возможность погрузки большегрузных самосвалов грузоподъемностью 90–360 т.
• Сокращение номенклатуры запчастей за счет высокой степени унификации экскаваторов с канатным и реечным механизмами напора.
• Увеличение ресурса редукторов до капитального ремонта – 50 тыс. часов.
• Увеличение ресурса роликового круга – до 12–15 лет. Круг с коническими роликами и установкой на осях роликов из специального материала, не требующих смазки втулок.
• Увеличение ресурса вантовой подвески стрелы – до 5–6 лет.
• Кабинный модуль повышенной комфортности с помещением для отдыха, санузлом и улучшенной обзорностью рабочей зоны и трассы передвижения.
• Долговечность и экономичность электрооборудования. Возможность применения более экономичного электропривода переменного тока.
• Улучшенный доступ к механизмам, расширение зоны обслуживания и проходов для обслуживающего персонала.
• Модульная фильтровентиляционная установка повышенной производительности.
• Комплексная система пожаротушения.
• Информационно-диагностическая система.
• Централизованная автоматическая система смазки с применением современных смазок.
• Новый оригинальный эстетический дизайн.
Монтаж экскаватора ЭКГ32Р на Краснобродском разрезе (ОАО «УК «Кузбассразрезуголь»)
За период 2000–2011 гг. ИЗ-КАРТЭКС поставил на горнодобывающие предприятия России, стран СНГ и Дальнего Зарубежья 270 карьерных экскаваторов и 15 буровых станков. Компания ИЗ-КАРТЭКС поставила перед собой цель активного продвижения экскаваторов класса 18–60 м3 в угольную отрасль страны за счёт повышения технического уровня машин, улучшения потребительских свойств и существенно более низких капитальных затрат на приобретение и эксплуатационных расходов своих экскаваторов.
Журнал “Горная Промышленность” №4 (98) 2011, стр.6
mining-media.ru
Высокопроизводительные экскаваторы ОАО «Уралмаш» для открытых горных работ
ОАО «Уралмаш» является одной из крупнейших в мире фирм по проектированию и производству выемочно-погрузочного оборудования для открытых горных разработок.
Начиная с 1947 года, Уралмашзавод выпустил более 12500 карьерных экскаваторов пятнадцати различных типов с ковшами вместимостью от 3 до 30 м3. Они эксплуатируются на многих предприятиях России, государств СНГ, а также Индии, Германии, Китая, Югославии, Турции, Египта, Румынии и других стран. Всего более 1600 машин было экспортировано в 22 страны мира.
Техническая концепция карьерных экскаваторов, производимых ОАО «Уралмаш», — двухбалочная рукоять и реечный напор, обеспечивают их эффективную эксплуатацию даже в самых тяжелых условиях.
Специалистам в области открытых горных работ хорошо известен надежный, высокопроизводительный экскаватор ЭКГ-5А с ковшом вместимостью 5.2 м3. Начав выпуск этой модели в 1980 году, завод изготовил их более 5000. Сегодня этот экскаватор, представляющий собой дальнейшее развитие всемирно известной модели ЭКГ-4,6Б, успешно применяется на открытых горных разработках, на строительстве гидротехнических сооружений, промышленных объектов, железных дорог в России, СНГ и странах дальнего зарубежья от тропиков до северных широт.
Для более полного удовлетворения потребности горных предприятий на базе ЭКГ-5А в последние годы создан ряд модификаций.
ЭКГ-5В — экскаватор с пневмоударными зубьями, встроенными в ковш, позволяющий производить выемку трещиноватых пород средней крепости и мерзлых грунтов без предварительного буровзрывного рыхления. В настоящее время выпущены и находятся в эксплуатации шесть экскаваторов ЭКГ-5В. Опыт их использования на карьерах показал, что применение данного экскаватора обеспечивает проведение селективной выемки на сложноструктурных месторождениях, снижение потерь и разубоживания, уменьшение затрат на разработку и вредного воздействия на окружающую среду за счет исключения необходимости проведения буровзрывных работ. В отличие от других новых видов оборудования для безвзрывной выемки крепких пород (машин послойного фрезерования, компактных роторных экскаваторов и т.п.) внедрение данного экскаватора на действующих предприятиях не требует коренного изменения технологии отработки месторождения. При использовании ЭКГ-5В его обслуживание и ремонт могут осуществляться на той же ремонтной базе, что и эксплуатирующихся сегодня ЭКГ-5А.
ЭКГ-5Д — экскаватор с дизель-электрическим приводом. Автономность питания позволяет использовать данную машину в районах с плохо развитой инфраструктурой, при отсутствии систем энергоснабжения.
ЭКГ-4УС — экскаватор с удлиненным рабочим оборудованием, позволяющий отрабатывать уступы повышенной высоты.
ЭДГ-3,2.30 — гусеничный драглайн с ковшом вместимостью 3.2 м3 и стрелой длиной 30 метров, предназначенный для использования на карьерах малой и средней мощности, а также выполнения вспомогательных работ на крупных карьерах.
ОАО «Уралмаш» также освоило производство карьерных экскаваторов большой единичной мощности с ковшом вместимостью 20 м3. С 1979 года выпущено 20 машин ЭКГ-20 и ЭКГ-20А, успешно эксплуатирующихся на разрезе «Нерюнгринский» в Якутии и разрезах Южного Кузбасса. В настоящее время с учетом опыта их работы создан проект модернизированного варианта ЭКГ-20А1. Это высокопроизводительная мощная машина, предназначенная для погрузки скальных пород в транспортные средства большой грузоподъемности. Экскаватор ЭКГ-20 специально спроектирован для использования в экстремальных горно-геологических и климатических условиях, что отразилось на выборе его общей компоновки, конструктивных решениях отдельных узлов, в применяемых материалах, наличии специальных систем и устройств, обеспечивающих надежную работу машины при температурах окружающего воздуха до минус 50 градусов. Конструктивное исполнение этого экскаватора отличается простотой, обеспечивает создание больших рабочих усилий, придает машине высокую маневренность и облегчает управление ею. Передовые экскаваторные бригады, эксплуатирующие ЭКГ-20, достигли на вскрышных работах годовой производительности более 4?млн. м3 горной массы.
В 1995 году ОАО «Уралмаш» выпустило и поставило ОАО «Карельский окатыш» новый карьерный экскаватор ЭКГ-12 с ковшом вместимостью 12 м3. Сменные ковши этой машины для тяжелых и легких пород имеют вместимость соответственно, 10, 14 и 16 м3. В конструкции ЭКГ-12 нашли применение последние достижения отечественного и зарубежного экскаваторостроения. Реечный напор с двухбалочной рукоятью и беспалиспастной подвеской ковша, а также двухгусеничная ходовая тележка с раздельным приводом на каждую гусеницу обеспечивают машине надежную высокопроизводительную работу даже в самых тяжелых условиях. Как показал опыт, в этом случае ЭКГ-12 предпочтительнее экскаваторов с канатным напором. Схема подвески стрелы, позволяющая опускать ее до горизонтального уровня и поднимать в рабочее положение без использования дополнительных грузоподъемных устройств и кранов, значительно облегчает обслуживание машины. Экскаватор ЭКГ-12 оптимально сочетается с автосамосвалами грузоподъемностью 80-120 тонн, а также думпкарами грузоподъемностью 105-180 тонн, применяемыми в настоящее время на многих крупных и средних карьерах.
На базе ЭКГ-12 созданы его модификации:
ЭКГ-12В — экскаватор с встроенными в ковш пневмоударными зубьями, позволяющий осуществлять выемку пород без предварительного взрывного рыхления;
ЭДГ-8.50 — гусеничный драглайн с ковшом вместимостью 8 м3 и длиной стрелы 50 метров. Применение таких машин для погрузки горной массы непосредственно в транспортные средства позволяет осуществлять разработку месторождения с уступами повышенной высоты, ускорить проходку вскрывающих выработок, сократить длину транспортных модификаций.
Опыт эксплуатации экскаватора ЭКГ-12 на карьере «Костомукшского РУ» ОАО «Карельский окатыш» показал высокую эффективность его работы в сложных горногеологических и климатических условиях, и в настоящее время в монтаже на разрезе «Междуреченский» находится второй экскаватор ЭКГ-12 с ковшом вместимостью 14 м3.
В последние два десятилетия в мировом экскаваторостроении преобладающей является тенденция к созданию и внедрению крупных гидравлических экскаваторов с оборудованием прямой и обратной лопаты.
Основные преимущества этих машин перед механическими лопатами заключаются в меньшей массе при одинаковой вместимости ковша, большем усилии копания, реализуемом на зубьях, возможности вести селективную выемку за счет управления рабочим органом по всей траектории его движения и высокой мобильности.
Лидером в производстве тяжелых гидравлических экскаваторов в России и государствах СНГ является ОАО «Уралмаш». Начиная с 1978 года, Уралмашзаводом были спроектированы и изготовлены опытные образцы гидравлических экскаваторов ЭГ-12, ЭГ-12А, ЭГ-20 с ковшами вместимостью 12 и 20 м3. Их испытания, проводившиеся на разрезе «Кедровский» в Кузбассе, подтвердили правильность основных конструктивных решений.
Было установлено, что отечественная концепция карьерного гидравлического экскаваторостроения, ориентированная на создание машин с комбинированным электрогидравлическим приводом главных механизмов, просторным кузовом, позволяющим обслуживать механизмы экскаватора в суровых климатических условиях, имеет значительные преимущества перед зарубежными аналогами, в конструкции которых прослеживается влияние традиций универсальных строительных экскаваторов. Электрический привод ходового и поворотного механизмов рабочего оборудования почти в два раза снижает удельную энергоемкость процесса экскавации по сравнению с испытанными зарубежными аналогами.
Многие технические решения и предложения, разработанные специалистами ОАО «Уралмаш» при создании гидравлических карьерных экскаваторов, находятся на самом современном уровне и не имеют аналогов за рубежом. К ним можно отнести разработки по системам рекуперации энергии, системам стабилизации рабочих режимов, системам фильтрации и охлаждения рабочей жидкости гидропривода.
В последние годы в ОАО «Уралмаш» создан карьерный гидравлический экскаватор ЭГО-4 с рабочим оборудованием типа обратная лопата, отечественным комплектующим оборудованием и гидравлическим управлением, а также выполнен рабочий проект экскаватора ЭГО-4А с импортным комплектующим оборудованием и электрическим управлением. Обе машины имеют автономный дизельный привод и вместимость ковша 4 м3. На базе ЭГО-4 разрабатывается прямая лопата ЭГ-6, имеющая как дизельный, так и электрический привод. Чтобы увеличить технические возможности этой машины, в ее ковше вместимостью 6 м3 предусмотрены активные зубья, имеющие гидропривод.
С 1949 года Уралмашзавод выпустил и поставил на горные предприятия более 240 крупных шагающих экскаваторов-драглайнов с ковшом вместимостью от 14 до 100 м3 и длиной стрелы от 65 до 100 метров. Эти экскаваторы нашли широкое применение на открытых разработках угля, железной и марганцевой руды, горно-химического сырья. 13 шагающих экскаваторов было поставлено на экспорт в дальнее зарубежье, где они зарекомендовали себя как высокопроизводительные, надежные машины, хорошо приспособленные для работы в любых климатических и горно-геологических условиях.
Накопленный опыт использования крупных шагающих экскаваторов производства ОАО «Уралмаш» показал, что при бестранспортных системах разработки их применение позволяет в 2–3 раза снизить затраты на производство 1?м3 вскрыши и в 3–4 раза уменьшить трудоемкость вскрышных работ.
В последние годы в ОАО «Уралмаш» разработаны проекты шагающих экскаваторов нового поколения. Сформирован ряд базовых моделей. Учитывая потребность горнодобывающих отраслей, предложены также модификации базовых моделей — экскаваторы с удлиненными стрелами при несколько меньшей вместимости ковша и экскаваторы с пониженным удельным давлением на грунт. Применение экскаваторов с удлиненными стрелами обеспечивает снижение затрат на вскрышные работы за счет уменьшения коэффициента переэкскавации при бестранспортной системе разработки. Модификация экскаваторов с пониженным на 20–25% давлением может более эффективно использоваться на слабых грунтах и при отвалообразовании.
Новые технические решения, применяемые при создании шагающих экскаваторов-драглайнов, обеспечили снижение эксплуатационных издержек и энергозатрат на экскавацию при значительном росте производительности и эффективности их применения.
На Уралмашзаводе создан один из крупнейших в мире экскаваторов-драглайнов ЭШ-100.100, эксплуатирующийся на разрезе «Назаровский» с 1977 года. Масса машины составляет 10300 тонн, вместимость ковша 100 м3, а длина стрелы 100 метров. При его создании, монтаже и эксплуатации решены многие сложные научно-технические и производственные проблемы.
В 1993 году на угольном разрезе «Тулунский» запущен в эксплуатацию второй по величине шагающий экскаватор, изготовленный ОАО «Уралмаш», ЭШ 65.100 с ковшом вместимостью 65 м3 и длиной стрелы 100 метров. Уже в первый год эксплуатации его производительность составила 10?млн.?м3 горной массы. Экскаватор оснащен гидравлическим механизмом шагания с полным отрывом опорной рамы от грунта посредством четырех подъемных цилиндров, опирающихся на скользящие опоры. Экскаватор при массе 5450 тонн показал хорошую проходимость при движении по слабым грунтам.
В настоящее время серийно выпускается экскаватор ЭШ 20.90, сменивший хорошо зарекомендовавший себя в работе на отечественных и зарубежных горных предприятиях драглайн ЭШ 15.90А. Высокая эффективность применения данных машин определила их широкое использование при добыче угля и руд. В эксплуатации на горных предприятиях сегодня находится 61 драглайн ЭШ 20.90.
В последние годы ряд российских предприятий и ведомств обращались в ОАО «Уралмаш» с просьбами о поставке на производство шагающих экскаваторов с ковшом вместимостью 10–11 м3 и длиной стрелы 70–75 метров. В связи с этим разработана новая модель экскаватора ЭШ 11.75, имеющая повышенную надежность и проходимость за счет более прочного рабочего оборудования, более низкого удельного давления на грунт при работе и передвижении. Экскаватор имеет трехгранную вантовую стрелу, электромеханический ход и скорость передвижения до 200 метров в час.
В 1999 году в ОАО «Уралмаш» будет изготовлен новый крупный шагающий экскаватор ЭШ 40.100 с ковшом вместимостью 40 м3 и длиной стрелы 100 метров для Мугунского угольного разреза ОАО «Востсибуголь».
Всего на сегодняшний день ОАО «Уралмаш» предлагает 13 типоразмеров шагающих экскаваторов и 6 их вариантов с пониженным давлением на грунт. Имея высокий технический уровень, экскаваторы-драглайны, производимые ОАО «Уралмаш», отличаются от машин аналогичного класса зарубежных производителей значительно более низкой ценой, не говоря уже о различиях в стоимости их доставки к месту эксплуатации и затратах, связанных с обеспечением запчастями в период эксплуатации.
В случае, если от горных предприятий будут получены заказы на поставку шагающих экскаваторов с иными параметрами, то рабочие чертежи на требуемую заказчиком модификацию могут быть оперативно разработаны.
Главной задачей экскаваторостроителей в условиях рынка является максимальное удовлетворение требований потребителей. Большой опыт, накопленный ОАО «Уралмаш» в области экскаваторостроения, авторитет завода у горняков, высокий творческий потенциал его конструкторов, исследователей и производственников позволяют успешно справиться с решением этой задачи.
Журнал “Горная Промышленность” №3 1999
mining-media.ru
Опыт эксплуатации канатных и гидравлических экскаваторов в условиях карьера Мурунтау
П.А.Шеметов, к.т.н., начальник карьера Мурунтау (Навоийский ГМК)
С.К.Рубцов, к.т.н., начальник лаборатории А.Г.Шлыков, к.т.н., старший научный сотрудник (ВНИПИпромтехнологии)
Карьер Мурунтау Навоийского ГМК – высокопроизводительное золоторудное предприятие, глубина которого достигает 450 м и постоянно увеличивается, что приводит к сокращению рабочих зон и, соответственно, к повышенной концентрации на ограниченной площади горнотранспортного оборудования. В условиях ограничения рабочих зон и увеличения насыщения в них выемочно-погрузочного и другого оборудования происходит снижение производительности экскаваторов за счет организационно-технических причин, вызванных несвоевременной подачей автосамосвалов и скоростью их движения, а также необходимостью частого переноса ЛЭП. Поэтому в данных условиях применение мобильной и автономной, не зависящей от энергоснабжения, выемочно-погрузочной техники с большой единичной мощностью, в частности, гидравлических экскаваторов (ЭГ), вполне оправдано. Преимущества ЭГ в части автономности и маневренности позволяют наиболее эффективно их использовать в сочетании с большегрузными автосамосвалами в стесненных условиях отработки забоев, при широком диапазоне изменения свойств горных пород, сложном строе нии рудных тел и неравномерности распределения полезного ископаемого в горном массиве.
На карьере эксплуатируются 16 канатных экскаваторов шести типоразмеров (ЭКГ4У, ЭКГ8УС, ЭКГ8И, ЭКГ10, ЭКГ12.5, ЭКГ15), которые используются на вскрышных и добычных работах, для заоткоски бортов карьера, на перегрузочных пунктах карьера (ППК). Начиная с 1995 г. введены в эксплуатацию гидравлические экскаваторы: САТ5230 (2 шт.), Rh270 (2 шт.) и ЕХ3500 (1 шт.) фирм Caterpillar (США), Orenstein & Koppel (Германия) и Hitachi (Япония) с емкостью ковша до 15 м3, а с августа 2003 г. – два электрогидравлических экскаватора Rh300 с емкостью ковша 20 м3. При этом у 15 экскаваторов ЭКГ и 4-х экскаваторов ЭГ (кроме RH-170 №5) превышен срок амортизации.
Анализ конструктивных и технологических данных гидравлических экскаваторов показывает, что они практичес ки сопоставимы друг с другом по геометрическим и энергосиловым параметрам. Основными отличиями ЭГ по сравнению с канатными ЭКГ являются автономность в работе и шарнирное сочленение рукояти ковша со стрелой.
Шарнирное сочленение рукояти ковша со стрелой уменьшает радиус черпания, поэтому гидравлические экскаваторы в процессе работы располагаются ближе к откосу уступа по сравнению с электрическими канат ными. Так, например, если у экскава тора ЭКГ15 максимальная высота черпания (16.4 м) в 1.4 раза меньше радиуса черпания (22.6 м), то у гидравлических экскаваторов эти параметры сопоставимы и составляют 15-17 м. В результате, безопасность работы ЭГ (в частности, исключение образования козырьков, нависей и т.п.) обуславливает более высокую степень дробления в забоях, отрабатываемых ЭГ.
Результаты совместной эксплуатации канатных и гидравлических экскаваторов за последние годы в условиях карьера Мурунтау позволили провести оценку эффективности их работы с целью выявления наиболее перспективной модели, сокращения номенклатуры применяемого выемочно-погрузочного оборудования и определения его наиболее эффективного сочетания с транспортным оборудованием для обеспечения оптимальной производительности экскаваторно-автомобильного комплекса. Для сравнения с ЭГ принят наиболее близкий по емкости ковша канатный экскаватор ЭКГ15 (табл. 1).
За время эксплуатации ЭГ ими отгружено 115.3 млн. м3 горной массы, из них – 12.3 млн. м3 – экскаваторами Rh300.
Обеспечение экскаваторов автосамосвалами при выемке горной массы осуществляется с учетом текущих потребностей в руде заданного качества, поскольку управление содержанием в товарной руде начинается с экскаваторных забоев, в связи с чем в зависимости от конкретной ситуации экскаваторы обслуживаются автосамосвалами на 30-100%. Потери рабочего времени на аварийные простои составили 20-25% (рис. 1), причем, как показывает динамика их изменения, при увеличении срока службы они возрастают. Наименьшие простои у САТ5230 (в среднем 7950 час), наибольшие – у экскаватора ЕХ3500 (9300 час), у Rh270 9020 час. Наибольшие простои ЕХ3500 обусловлены более сложным по сравнению с другими ЭГ конструктивным исполнением и, соответственно, сложностью проведения ремонтных работ. За тот же период простои канатного экскаватора ЭКГ15 составили 5640 час, что на 40% меньше, чем у ЕХ3500 и на 29% меньше, чем у САТ5230.
Табл. 1 Основные показатели работы экскаваторов за 1999-2003 гг.
Показатели |
САТ-5230 |
ЕХ-3500 |
RH-170 |
RH-200* |
ЭКГ-15 |
Количество экскаваторов |
2 |
1 |
2 |
2 |
1 |
Геометрическая емкость ковша, м3 |
15.1 |
13.7 |
14.8 |
20.6 |
15.0 |
Объем отгруженной горной массы, тыс. м3 |
21760 |
13370 |
22310 |
3330 |
12460 |
Аварийные простои, час |
15900 |
9300 |
18040 |
340 |
5640 |
Производительность, м3/ч |
510 |
585 |
560 |
577 |
480 |
Удельный расход топлива, кг/м3 |
0.29 |
0.35 |
0.28 |
||
Коэффициент использования |
0.47 |
0.59 |
0.46 |
0.79 |
0.59 |
* RH-200 введены в эксплуатацию в августе 2003 г.
Экскаваторы
Рис. 1 Аварийные простои экскаваторов за период 1999-2003 гг.
Основные характерные причины аварийных простоев ЭГ – это отказы гидроцилиндров ковша, рукояти, стрелы, разрыв шлангов высокого давления, выход из строя двигателей и др. Общими неисправностями для всех экскаваторов являются:
– разрыв шлангов высокого давления, трещины в гидробаках, выход из строя насосов, обрыв шпилек головок цилиндров двигателя;
– экскаваторы САТ5230 и Rh270 имеют нетехнологичную конструкцию упоров на рукояти для ограничения действия ковша и даже из-за небольшой неточности их установки на заводе неравномерно распределяются нагрузки на каждый из упоров, в результате чего возникают трещины в металлоконструкциях.
Анализ работы ЭГ и характерных простоев позволил выявить наиболее слабые детали и узлы с малой наработкой и наладить их производство непосредственно в условиях Навоийского машиностроительного завода (НМЗ), в частности, наиболее подверженных износу сменных элементов ковшей, зубьев, режущих кромок, протекторов. В результате этого предприятие отказалось от закупок за рубежом сменных элементов ковшей, так как стоимость аналогичных изделий собственного производства значительно ниже и не уступает зарубежным по стойкости. Освоен выпуск практически всех сменных элементов ковша САТ5230, а также унифицированного зуба для Rh270 и ЕХ3500.
Динамика изменения коэффициента использования гидравлических экскаваторов (Ки) показывает, что их работа не отличается стабильностью. Разброс показателей Ки для одного типа экскаватора в различные годы достигал 15-20%. Наибольшая стабильность в работе отмечается у экскаваторов ЕХ3500 и Rh270 №4. Значительные аварийные простои, вызванные выходом из строя главного двигателя САТ5230 №2 в 1999 г., практически привели к остановке экскаватора (Ки = 0.06). Аналогичная ситуация наблюдалась в 2003г. с экскаватором Rh270 №5 (Ки = 0.04), который отработал в забое всего один месяц (228 час).
Рис. 2 Среднее значение коэффициента использования за период 1999-2003 гг.
По результатам эксплуатации ЭГ за 1999-2003 гг. величина Кине превышает 0.59-0.47 (рис. 2). Значения Ки для экскаваторов САТ5230 и Rh270 практически одинаковы – 0.47 и 0.46, соответственно, у ЕХ3500 – 0.59, что в среднем на 27% выше. Следует заметить, что Киэлектрогидравлических экскаваторов Rh300, введенных в эксплуатацию в 2003г., достаточно высок и составил 0.79. Работа канатного экскаватора ЭКГ15 отличается достаточной надежностью. За последние 5 лет изменение Ки составило всего 10% (Ки = 0.6 в 1999 г. до 0.54 в 2003 г.), а среднее значение Ки за данный период 0.59, что выше, чем у экскаваторов САТ5230 и Rh270.
Применение на карьере Мурунтау гидравлических экскаваторов с большой единичной мощностью и вместимостью ковша в сочетании с большегрузными самосвалами позволило в первые годы их эксплуатации обеспечить высокие темпы добычи и рост производительности при сокращении общего парка выемочно-погрузочного оборудования при увеличивающейся глубине карьера.
Рис. 3 Приведенные затраты на содержание экскаваторов за период 2000-2004 гг.
Анализ основных показателей работы ЭГ, их достоинств и недостатков не позволяет дать однозначную оценку о преимуществе одного какого-либо типа экскаватора. Однако, по большинству рассматриваемых параметров (объемам горной массы, производительности, коэффициенту использования и др.) лучшие показатели имеют экскаваторы ЕХ3500 фирмы Hitachi и САТ5230 фирмы Caterpillar. В настоящее время оборудование фирмы Caterpillar широко используется в условиях карьера (грейдеры, бульдозеры, погрузчики), которые имеют много унифицированных и взаимозаменяемых с экскаваторами узлов и деталей, что позволяет более оперативно решать вопросы по их обслуживанию и ремонту.
Оценивая работу канатных экскаваторов ЭКГ15, можно заключить, что по многим параметрам отличие в показателях незначительно, а по некоторым показателям ЭКГ15 да же превосходят характеристики гидравлических экскаваторов. Канатные экскаваторы этого типа проще в изготовлении и обслуживании, они дешевле гидравлических и не требуют сложной ремонтной базы. Соответственно дешевле запасные части, которые более доступны по стоимости при отсутствии на них дефицита.
Согласно действующим Единым правилам безопасности при разработке взорванных пород канатными экскаваторами, высота уступа Ну не должна превышать полуторную максимальную высоту копания экскаватора hon™* или Нч1Ш1, так как hon™* = для канатных экскаваторов.
По конструктивной схеме гидравлические экскаваторы при отработке забоя не могут реализовать максимальную кинематическую высоту копания = Нчт_ указанную в технической характеристике экскаватора. Как видно из рис. 3, на котором приведена сопоставительная оценка зон копания на примере канатного (ЭКГ 20) и гидравлического (ЭГ20) экскаваторов, непосредственно в контакте с забоем ковш гидравлического экскаватора может находиться до высоты, равной (0.65-0.75) houm,*, которая на 25-35% меньше паспортной величины г^^. Эту фактическую высоту контакта ковша ЭГ с откосом забоя называют приведенной высотой копания экскаватора h’^^, т.е. h’,,,,,,^^0.7-0.75 • ho,,™ [1, 2]. В связи с этим при отработке ЭГ уступов без применения взрывных работ максимальная высота забоя и уступа составляет Ну = h’,,,,,,^ или Ну = 0.7-0.75 •Н,,^.
В случае разработки взорванных пород с различными значениями коэффициента разрыхления (Кр) и среднего размера взорванного куска (d,,) превышение возможной высоты отрабатываемого забоя (Hmax) над приведенной высотой приведено в табл. 2 [2].
Экспериментальными работами по оценке качества дробления пород карьера Мурунтау установлено, что величина среднего размера куска взорванных пород находится в пределах 14.5-28 см. В связи с этим из данных табл. 3 пред ставляется возможным в случае использования в карьере гидравлических экскаваторов принять относительное значение высоты забоя для ЭГ равным Hmax/1.6 • h’,^^ = 1.6. Тогда максимальная высота взорванного забоя для ЭГ равна Ну = Hmax = 1.6 • h’^^ = 1.6 • 0.7 • Н,^ = 1.12 Н,^.
С учетом изложенного и на основе паспортных технических параметров экскаваторов выполнено сравнение возможных высот взорванных забоев для канатных и гидравлических экскаваторов, используемых на карьере (табл. 3).
Из анализа данных, приведенных в табл. 3, видно, что при взрывании 15 м уступа и Кр = 1.3 (Ну = 19.0 м) только ЕХ3500 в состоянии отработать взорванный уступ, для остальных типов ЭГ необходимо разделение взорванного уступа на подуступы. В случае применения канатных экскаваторов такой проблемы не существует. Из изложенного видно, что шарнирное сочленение рукояти ковша со стрелой у гидравлических экскаваторов ограничивает высоту разрабатываемого забоя.
Рассматривая работу выемочно-погрузочного комплекса, в т.ч. ЭГ, за все время их эксплуатации, можно отметить, что в начальный период производительность экскаваторов
была достаточной для обеспечения запланированных объемов работ. В дальнейшем, по мере окончания гарантийного срока обслуживания и износа оборудования, материальные и трудовые затраты на поддержание экскаваторов в работоспособном состоянии возрастают за счет закупки запасных частей и увеличения затрат времени на выполнение ремонтных работ.
Проведенная технико-экономическая оценка показывает, что после 6-7 лет работы ЭГ существенно падает экономическая целесообразность дальнейшей их эксплуатации, т.к. снижается производительность и увеличиваются затраты на текущие и капитальные ремонты, которые перекрывают средства амортизационных отчислений.
Экскаватор ЭКГ15 – более ремонтопригоден чем ЭГ, т.к. не требует при производстве ремонтных работ (изготовлении новых деталей) такого класса чистоты обработки поверхностей, как для гидравлических систем. По этой причине нет возможности ремонта (восстановления) деталей ЭГ на имеющемся станочном оборудовании в ремонтной службе предприятия. Кроме того, для ремонта ЭГ необходимо содержание отдельного специализированного участка со специальным оборудованием, инструментом и приспособлениями.
За последние годы объем экскавации ЭКГ находится практически на одном уровне (17-18 млн. м3/год). Значительные аварийные простои ЭГ привели к падению объемов выемки горной массы в 2003 г. по сравнению с другими периодами времени. Производительность ЭГ на протяжении последних трех лет остается невысокой и если бы не ввод в эксплуатацию двух Rh300, то производительность карьера в 2004 г. не превысила бы 25-26 млн. м3 (объем выемки горной массы в 2004 г. составил 34.7 млн. м3).
Данное обстоятельство подтверждает вывод о том, что потенциал повышения производительности имеющегося экскаваторного парка полностью исчерпан. Необходимо его обновление, причем не за счет увеличения количества, а за счет ввода в эксплуатацию наиболее производительной техники.
Табл. 3 Возможная высота разрабатываемых забоев для ЭКГ и ЭГ
Модель |
Коэффициент |
Кусковатость взорванной горной массы ()ср, см |
Высота черпания Нч.тах, м |
Выс ота забоя (уступа) , м |
|
экскаватора |
разрыхления Кр |
без БВР, м |
с БВР, м |
||
Кан атные экскаваторы |
|||||
Ну – Нч.тах |
Ну – 1,5-Нч.тах |
||||
ЭКГ-10 |
13.5 |
13.0 |
20.0 |
||
ЭКГ-12,5 |
1.25- 1.35 |
20-10 |
15.5 |
15.0 |
22.0 |
ЭКГ-15 |
16.4 |
16.0 |
24.0 |
||
ЭКГ-20 |
17.8 |
17.5 |
26.0 |
||
Ну – 0,7-Нч.тах |
Ну – 1,12Нч.тах |
||||
RH-170 |
16.0 |
11.0 |
18.0 |
||
EX-3500 |
1.25-1.35 |
20-70 |
17.2 |
12.0 |
19.0 |
CAT-5230 |
14.8 |
10.5 |
16.5 |
||
RH-200 |
15.2 |
10.6 |
17.0 |
Табл. 2 Рекомендуемые относительные значения высоты забоев для ЭГ при различных свойствах взорванной горной массы
Взорванная горная масса, Кр |
Угол взорванного забоя, град. |
||||
При кусковатости ()ср, см |
Выход негабаритных |
||||
5-12 |
20-Ю |
40-60 |
кусков (5-8%) |
||
Связная Кр – 1.02-1.15 |
75-87 |
1.1 5 |
1. 1 |
1.05 |
1. 0 |
Связносыпучая Кр – 1.2-1.35 |
60-80 |
1. 9 |
1. 6 |
1.35 |
1.05 |
Связносыпучая Кр – 1.3-1.4 |
50-70 |
2.7 |
2.1 |
1. 7 |
1. 1 |
Сыпучая Кр – 1.4-1.5 |
32-50 |
3.8 |
3.5 |
3.2 |
– |
Рис. 4 Изменение аварийных простоев экскаваторов за период 1996-2004 гг.
Рис. 5 Изменение приведенной производительности
экскаватора в зависимости от срока его службы
Приведенные затраты на содержание экскаваторов с увеличением срока использования возрастают, причем эти затраты для ЭГ более чем в три раза превышают затраты на ЭКГ15 (рис. 4). Из-за изношенности оборудования за период эксплуатации возросли аварийные простои экскаваторов (рис. 5), причем наибольшее увеличение характерно для ЭГ; для ЭКГ15 за рассматриваемый период аварийные простои в среднем остаются на одном уровне, что свидетельствует о более надежной их работе. Аварийные простои являются одной из основных причин снижения производительности, особенно это наблюдается у ЭГ (рис. 6), где интенсивность уменьшения производительности по сравнению с ЭКГ15 более значительная. Если в первые годы эксплуатации производительность ЭГ была выше на 30-35%, чем у ЭКГ15, то при увеличении срока службы это отличие составляет всего 10-15%.
Несмотря на большие валютные затраты для ремонта и поддержания ЭГ в работоспособном состоянии (до 800 тыс. долл.), тенденция снижения их производительности не уменьшается, что в конечном итоге увеличивает себестоимость экскавации 1 м3 горной массы, почти в два раза превышая себестоимость погрузки ЭКГ15, которая остается прак тически неизменной на протяжении последних лет (рис. 7). При этом значительную долю в увеличении себестоимости экскавации ЭГ составляет расход дизтоплива (рис. 8), объем которого возрастает из-за физического износа дизельных двигателей, причем увеличение расхода особенно наблюдается после проведения ремонтных работ двигателей.
Невысокая надежность физически изношенных ЭГ не позволяет их использовать в настоящее время на ответ ственных направлениях и участках работ, т.к. возрастают риски срыва плановой выемки и погрузки горной массы, что влечет за собой необходимость в дополнительных пе регонах экскаваторов в карьере.
Оценивая результаты эксплуатации ЭГ на карьере Мурунтау в течение 1996-2004 гг., можно заключить, что на сегодняшний день дизельные гидравлические экскаваторы фактически утратили те преимущества (высокую мобиль ность и автономность; возможность лучшей селективной выемки горной массы из массива; производительность) пе ред канатными, ради которых они приобретались и использовались, несмотря на более высокие эксплуатационные затраты.
Рис. 6 Изменение себестоимости экскавации горной массы
Рис. 7 Изменение удельного расхода дизельного топлива
гидравлическим экскаватором с начала эксплуатации
Принимая во внимание окончание срока амортизации ЭГ, представляется целесообразным с целью унификации экска ваторного парка сократить типажный ряд ЭГ, используя при этом наиболее эффективное сочетание комплексов выемоч но-погрузочного и транспортного оборудования. В перспективе целесообразно выемочно-погрузочное оборудование карьера Мурунтау ориентировать на экскаваторы: ЭКГ15 в карьере и складах; ЭКГ8У – для выполнения работ в приконтурных зонах при постановке бортов карьера в предельное положение; ЭКГ10 на ППК, как наиболее соответствующих по своим параметрам железнодорожным думпкарам В105. На участках, требующих высокой концентрации и интенсивного ведения горных работ в значительных объемах (верхние горизонты юго-западной и восточной части карьера), предусматривается использование электрогидравличес ких экскаваторов большой единичной мощности Rh300.
Таким образом, эффективность использования экскаваторного парка определяется комплексом взаимосвязанных факторов, основными из которых являются технические возможности экскаватора, технологические параметры взорванной горной массы, соотношение высоты забоя и паспортной характеристики оборудования, обеспеченность забоев автотранспортом, а также стоимостные показатели работы экскаваторов.
ЛИТЕРАТУРА:
1. Беляков Ю.И. Выемочно-погрузочныеработы на карьерах. М., Недра, 1987,208 с.
2. Беляков Ю.И. Проектирование экскаваторных работ. М., Недра, 1983, 350 с.
Журнал “Горная Промышленность” №5 2005
mining-media.ru
Добавить комментарий