Зубья ковшей экскаваторов – Зубья экскаватора в России. Сравнить цены, купить потребительские товары на маркетплейсе Tiu.ru
Ремонт ковша экскаватора. Важные аспекты. Мнение экспертов
23.08.2018
Со стороны может показаться, что ковш экскаватора — изделие простое: большая металлическая лопата с зубьями, никаких хитростей! Однако производители этого оборудования могут часами рассказывать об особенностях его устройства.
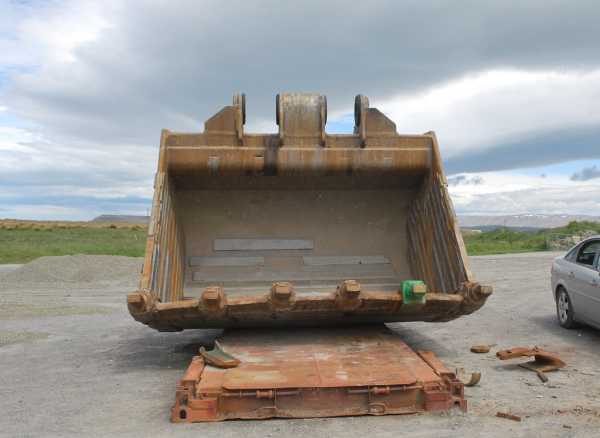
Многолетней опыт работы экскаваторов, тесты, замеры и испытания выявили элементы ковша, которые в процессе работы практически не страдают от контакта с грунтом, а также те, которые принимают удар на себя. Исходя из этих данных и создаётся ковш: для разных его частей используются разные материалы, используется специфическая защита.
Режущая кромка ковша — один из элементов, подверженных наибольшему износу.
Работа с этой частью ковша — целая наука. Задача, разумеется, одна — увеличить интервалы обслуживания и из-бежать незапланированных простоев экскаватора вследствие ремонта оборудования.
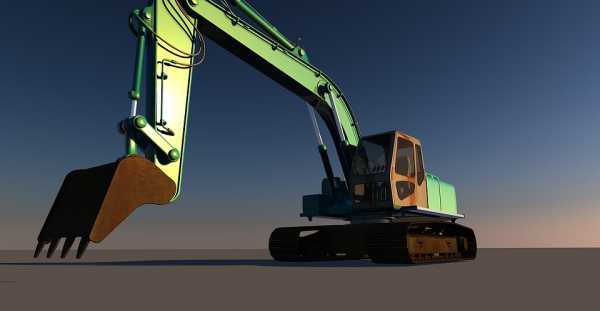
«Основной составляющей износа является абразивное воздействие грунта на режущую кромку навесного оборудования карьерной техники. Твёрдость грунта, из-за наличия в нём кремния, составляет порядка 1000 ед. по Викерсу, в то время как большинство металлов, применяемых для изготовления режущей кромки, имеют твёрдость 300-400 ед.
Самые высокие показатели — это 600 ед.
Очевидно, что при многоцикличной нагрузке режущая кромка будет подвержена истиранию», — объясняет инженер-конструктор ООО «УгольМашСервис» Илья Деблов.
«Конструкция ковша ведь геометрически понятна: если взглянуть на то, как ковш входит в породу, очевидны его элементы, которые в наибольшей степени подвержены истиранию.
На эти участки ставится дополнительная защита, которая является расходным материалом», — добавляет начальник отдела маркетинга машиностроительной группы «КРАНЭКС» Сергей Комолов.
Особый подход
Разумеется, владельцы техники заинтересованы в том, чтобы элементы машины, пусть даже и расходные материалы, ходили как можно дольше. Производители серьёзно подошли к вопросу режущих кромок, и сегодня есть несколько типовых решений повышения износостойкости ковша.
Главную роль, конечно же, отдают качеству металла, который используют для изготовления режущих кромок.
Обычные конструкционные стали не годятся — их ведь разрабатывали для совершенно иных условий работы. Ещё со времён СССР для создания режущих кромок применяли стали с высоким содержанием углерода. Эксперты отмечают, что по твёрдости претензий к ним нет, но вот под воздействием низких температур — а российские месторождения нередко находятся именно на сервере — стали становятся хрупкими.
Говоря о современных материалах, эксперты, как правило, называют шведскую сталь Hardox либо её аналоги. Причём, аналоги должны быть европейскими, китайские стали доверия не вызывают. Важно, чтобы твёрдость материала составляла от 400 до 600 НВ.
«Это класс сталей, разработанных специально для использования в качестве режущих кромок и защитных элементов ковшей. На данный момент они обладают лучшими характеристиками, и именно их используют в своём производстве лидеры индустрии.
Стоит отметить, что ковши их этих сталей при сохранении всех эксплуатационных характеристик имеют более низкий вес, что в целом увеличивает ресурс базовой машины. Данный тип сталей приобретает свои свойства за счёт химического состава (пакета присадок) и особой технологии закалки», — подчёркивает руководитель направления ООО «Компания Традиция К» Алексей Пахомов.
«Сталь Hardox имеет гладкую молекулярную структуру из-за наименьших долей вредных компонентов. При использовании данной стали уменьшается риск образования самого опасного вида трещин — микротрещин. Наша компания работает только с этим материалом», — согласен технический директор ООО «Решке рус» Антон Шагин.
Дополнительная броня
Но одним грамотным выбором стали дело не ограничивается.
Специалист «УгольМашСервис» наглядно продемонстрировал, что даже самая твёрдая сталь уступает грунту, с которым экскаватору приходится работать. Поэтому специалисты дополнительно усиливают режущую кромку дополнительной защитой в виде накладок из высокопрочной стали, межзубьевой защитой, скальными адаптерами и коронкамии.
Все эти защитные элементы являются сменными — за счёт этого упрощается обслуживание ковша.
«Увеличение твёрдости всей режущей кромки нецелесообразно ввиду увеличения, как её цены, так и увеличению хрупкости.
В связи с этим на режущую кромку устанавливаются сменные зубья и межзубьевая защита. При необходимости дополнительно устанавливаются футеровочные пластины из износостойкого металла.
Зубья ковша увеличивают сосредоточенную нагрузку на грунт, что облегчает копание»,— рассказывает Илья Деблов.
Эксперт уточняет, что даже материалы, которые применяются для изготовления зубьев, подвержены абразивному износу при контакте с грунтом.
«Износ зуба и несвоевременная его замена приведёт к постепенному износу самой режущей кромки. Истирание рабочей поверхности приведёт к деформации посадочных мест под установку зубьев, что в свою очередь ведёт к разбалтыванию крепления и последующему излому зуба»,— предупреждает специалист «УгольМашСервис».
«Зубья ковша разрыхляют грунт и облегчают внедрение ковша, минимизируя износ режущей кромки. Залогом надёжности для зубьев являются коронки.
Наши специалисты используют шведские коронки COMBI. Ресурс коронки зависит от массы самой коронки: масса коронок COMBI превышает массу аналогов, что и способствуют большему сроку службы данных коронок. Кроме высокой износостойкости, коронки отличаются индикатором износа, предупреждающим поломку деталей, что также значительно уменьшает вероятность износа режущей кромки.
На ковши для техники от 120 тонн, работающей на горно-обогатительных комбинатах, наша компания устанавливает литые режущие кромки компании СQMS, удачно прошедшие испытания в России. За счёт их эксплуатационных характеристик увеличивается срок службы ковша, соответственно уменьшается стоимость и время обслуживания», — рассказывают о своём опыте Антон Шагин.
Ручная работа
Понятное дело, что в процессе эксплуатации материал истирается, и рано или поздно возникает необходимость замены конструктивных элементов.
Но есть ещё и такое явление, как возникновение трещин на режущей кромке. Здесь вопрос уже не к производителю оборудования (в очень редких случаях причиной могут стать ошибки в отливке стали), а к специалистам, его эксплуатирующим.
«Причиной быстрого износа ножа (режущей кромки) может стать неправильная эксплуатация. Очень важно подбирать ножи в соответствии с определённым характером грунта и для различных климатических условий. Например, твердосплавные ножи отлично убирают снежный покров, а для «ударных работ» в карьере хорошо подойдут скальные ножи (усиленные)», — комментирует директор компании-производителя ножей отвала ООО «Азимут» («ЗиМ») Оксана Камальдинова.
Илья Деблов отметил ещё и возможные климатические факторы износа элементов оборудования.
«Под влиянием погодных условий — дождя, снега — происходит окисление металла. При перепаде температур вода замерзает и снова тает, а это приводит к увеличению количества и размера микротрещин в металле. В целом условия Крайнего Севера — для техники непростые. Увеличивается хладнохрупкость металла. В условиях вечной мерзлоты особое внимание стоит уделять подготовке забоев к буровзрывными работами для облегчения копания»,— отмечает специалист.
Мнение
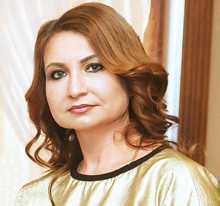
«В каталоге нашей компании большой ассортимент ножей, зубьев и стоек для отечественной и импортной спецтехники, из различных видов сталей.
Есть бронированные ножи, твердосплавные ножи, резцовые ножи, перфорированные ножи и ножи с наплавкой из сормайта.
Каждый из них произведён с термической обработкой на высокотехнологичном оборудовании.
Техническая грамотность наших специалистов позволяет потребителю сориентироваться в выборе оптимального ножа для тех или иных видов работ и сделать правильный выбор» — Оксана Камальдинова, директор ООО «Азимут».
.
«Срок службы режущей кромки во многом зависит от мастерства машиниста экскаватора: копает ли он рукоятью, подворачивает ли стрелу — эти нюансы имеют значения. Да и вообще, мне доводилось видеть, как ковш используют в качестве стенобитного орудия, о каком продолжительном сроке службы тут можно говорить», — подчёркивает Сергей Комолов.
«Довольно часто причиной поломки режущей кромки является нарушение правил эксплуатации оборудования, а также проведённый ранее некачественный ремонт — без соблюдения технологий и при использовании материалов, не подходящих для высоких нагрузок на излом, разрыв или трение»,— уточняет Алексей Пахомов.
Региональный менеджер MTG в СНГ, Монголии и Финляндии Вилле Хяккинен объяснил, что значит «неправильный ремонт». Когда потребитель пытается решить задачу самостоятельно, он порой не учитывает специфики работы со сталью, и в результате — элемент ковша получает повреждения.
«Например, угольный разрез, температура на улице — минус 15 градусов. Если производить сварку без нагрева, без подготовительных процедур, то металл может потрескаться. Поэтому имеет смысл обращаться к производителям, как минимум, за советом.
Наши партнёры из компании «Профессионал» дают такие консультации своим клиентам: выдают соответствующий документ, где прописан температурный режим, как его измерять, как производить процесс сварки и так далее.
Есть возможность воспользоваться услугами мобильного сервиса – это особенно актуально, когда речь идёт о дорогостоящем оборудовании», — рекомендует специалист.
Мнение
«Современные износостойкие стали хорошо свариваются, однако для этого необходимо чёткое соблюдение всех технологических нюансов. Ремонт ковшей представляет собой замену изношенных элементов на новые. В некоторых случаях эти работы можно осуществить прямо на объекте, в других — необходимо везти оборудование в сервис. Специалисты нашей компании выполняют работы как в стенах сервисного центра, так и на объекте заказчика»- Алексей Пахомов, руководитель направления ООО «Компания Традиция К».
Ремонтировать или менять?
И классический вопрос владельцев техники: менять элемент, который по большому счёту, является расходным материалом, или есть возможность «подлатать» кромку, увеличив срок её службы?
Эксперты говорят, что всё определяется на месте, и главное слово за механиком, ответственным за работоспособное состояние техники. Если обнаружены дефекты, к «больной кромке» приглашается специалист по ремонтам.
В основе диагностики — визуальный осмотр: выявляются деформированные и изношенные элементы, трещины, сколы. Специалист составляет ведомость дефектов, на основе которой разрабатывается технологическая карта ремонта, в которой описываются материалы, операции, сроки выполнения.
После согласования двумя сторонами данной ведомости приступают к ремонту.
Режущую кромку очищают от грязи; трещины разделывают, заваривают, зачищают. Заменяют изношенные зубья, срезают и устанавливают новые футеровочные пластины. После завершения ремонта работа принимается механиком.
«Если на режущей кромке появилась трещина, можно попытаться её отремонтировать. Для этого трещину нужно раскрыть, сварить, а потом зашлифовать. Кроме сварки никаких способов решения проблемы не существует», — уточнил Вилле Хяккинен.
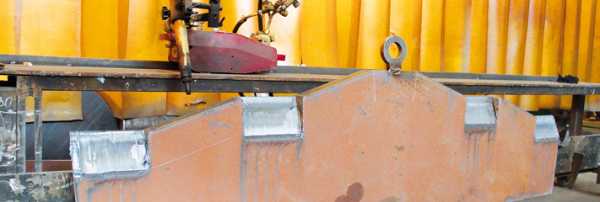
«Целесообразность ремонта определяется исходя из отношения цены новой режущей кромки к затратам, повлекшим как сам ремонт, так и простой оборудования в год. Если годовые затраты превышают стоимость новой режущей кромки, необходимо режущую кромку заменить на новую», — подытоживает Илья Деблов.
Текст: Анна Кучумова
dprom.online
Зуб ковша экскаватора
Изобретение относится к землеройной технике, а именно к одноковшовым карьерным экскаваторам циклического действия, и может быть использовано в горнодобывающей промышленности и строительстве для разрушения и выемки пород и грунтов любой прочности после, либо без предварительного рыхления.
Уровень техники
В нашей стране преимущественное распространение имеют цельные зубья, изготавливаемые литьем или штамповкой. Среди цельнолитых зубьев наиболее часто встречаются зубья с простейшими симметричными треугольными или слабоизогнутыми профилями, зубья со сложными криволинейными профилями встречаются реже. При этом зубья с криволинейными профилями лучше соответствуют рабочему процессу ковша и оказываются более эффективными и долговечными. Литые зубья изготавливают из стали 110Г13Л, которая обладает уникальным свойством – большим сопротивлением истиранию при наклепе. Для изготовления штампованных зубьев используют дорогие сложнолегированные стали.
Известен цельнолитой зуб ковша экскаватора, включающий хвостовик, клинообразную рабочую часть, образованную верхней и нижней криволинейными гранями, формируемыми сопряженными цилиндрическими поверхностями, и снабженную ребрами жесткости и режущей частью, смещенной относительно продольной оси зуба вверх, а на боковых гранях рабочей части выполнены козырьки в виде уголков [1]. Ребра жесткости также формируются сопряженными цилиндрическими поверхностями. Предполагается, что использование зуба данной формы позволяет увеличить срок службы зуба и передней стенки ковша экскаватора за счет уменьшения их износа.
Однако такая форма зуба хотя и позволяет несколько снизить износ и увеличить срок службы, но при стачивании зуба происходит резкое затупление, например, по приведенному чертежу, при стачивании всего 1/5 длины рабочей части режущая кромка затупляется в 2-3 раза, дальнейший износ еще больше затупляет зуб. Режущая часть смещена относительно продольной оси зуба вверх, что приводит к повышенному трению и износу нижней (задней) грани рабочей части и нижних ребер. Рабочая часть зуба примерно на половине длины со стороны режущей кромки не имеет ребер и прочность обеспечивается за счет увеличения толщины, зуб приходится делать чрезмерно массивным и трудно обеспечить высокое качество металла при литье и термообработке. Хвостовик зуба имеет тонкие опорные части постоянной толщины, которые легко отламываются при неизбежном в эксплуатации ослаблении крепления зуба на передней стенке ковша экскаватора. В общем, зуб данной конструкции представляется чрезмерно тяжелым, масса зуба дополнительно увеличивается за счет боковых козырьков, что затрудняет монтаж зубьев при замене. Тем не менее, увеличение массы не приводит к соответствующему повышению эксплуатационных характеристик (снижению износа и повышению срока службы зуба).
Наиболее близким к изобретению по технической сущности и достигаемому результату является зуб ковша экскаватора, включающий клинообразную рабочую часть и хвостовую часть с гнездом, открытым сзади и охватывающим посадочную часть передней стенки ковша. Зуб имеет также короткую, но массивную, переходную часть, служащую для сопряжения рабочей и хвостовой частей. Рабочая часть выполнена с острым углом 10-15° между выпуклой верхней и вогнутой нижней криволинейными гранями, при этом радиусы цилиндрических поверхностей, формирующих верхнюю и нижнюю грани рабочей части и нижние ребра, принимаются одинаковыми. Режущая часть смещена относительно продольной оси зуба вниз на величину, составляющую 0,10-0,14 от длины рабочей части зуба, радиус ее цилиндрической поверхности равен 20 мм. В теле зуба в месте сопряжения рабочей части с хвостовой (в переходной части) предусмотрена полость в виде усадочной раковины, не выходящей на рабочую поверхность [2]. Использование зубьев данной формы позволило увеличить износостойкость и срок службы и уменьшить вероятность внезапной поломки. Зубья были изготовлены в большом количестве и успешно используются в карьерах ГОК.
Однако при массовом изготовлении и эксплуатации выявились и недостатки этой конструкции зуба. Ширина рабочей части представляется недостаточной, т.к. интенсивный износ идет не только по передней и задней граням рабочей части, но и по боковым граням. Передняя криволинейная грань рабочей части зуба истирается быстрее, чем предполагалось из-за того, что ее профиль чрезмерно выпуклый. Выполнение режущей кромки рабочей части зуба малым радиусом 20 мм ослабляет рабочую часть. При литье, как и при других техпроцессах, значения технологических параметров могут колебаться, и при неблагоприятном сочетании отклонений этих параметров нет гарантии в точном расположении усадочной раковины, что приводит к выбраковке зубьев.
Раскрытие изобретения
Целью изобретения является повышение эффективности рабочих органов карьерных экскаваторов при одновременном сокращении эксплуатационных затрат.
Техническими результатами являются повышение износостойкости и срока службы, уменьшение вероятности внезапной поломки, улучшение технологичности при литье и термообработке.
Указанная цель и результаты достигаются зубом ковша, выполненным в соответствии с формулой изобретения, при комплексном решении вопросов служебного соответствия и технологичности.
Краткое описание чертежей
Признаки и преимущества настоящего изобретения будут более очевидными из нижеприведенного описания технической сущности его осуществления со ссылкой на прилагаемые чертежи со сквозной системой обозначений, на которых:
– на фиг. 1 изображен предлагаемый зуб ковша, вид сбоку,
– на фиг. 2 изображен зуб ковша, вид сверху,
– на фиг. 3 изображен зуб ковша, разрез по А-А,
– на фиг. 4 изображен зуб ковша, сечение по Б-Б,
– на фиг. 5 изображен зуб ковша, сечение по В-В.
Осуществление изобретения
Конструкция предлагаемого цельнолитого зуба ковша подробно представлена на фиг. 1-5. Зуб состоит из клинообразной рабочей части, короткой переходной части и хвостовой части с гнездом, открытым сзади и охватывающим посадочную часть передней стенки ковша. Ширина рабочей и переходной частей зуба больше на 40 мм, чем ширина хвостовой части. Клинообразная рабочая часть зуба образована выпуклой передней гранью I и вогнутой задней гранью 2, плавно сопрягающимися на конце клина по цилиндрической поверхности, являющейся режущей частью (кромкой) 3. Режущая кромка смещена относительно продольной оси зуба вниз. Радиус цилиндрической поверхности, формирующей вогнутую заднюю грань 2 рабочей части для зубьев длиной 1250-1510 мм равен R1≅1000 мм, а радиусы цилиндрических поверхностей, формирующих выпуклую переднюю грань 1 принимаются в пропорции R2=(2,5-3,0)⋅R1. По задней грани рабочая часть снабжена двумя широкими периферийными ребрами жесткости 4, радиус которых R3≅(1,25-1,35)⋅R1|.
Переходная часть зуба служит для сопряжения рабочей части с хвостовой. Для уменьшения толщины тела зуба в переходной части выполнена внутренняя полость 5, по форме в продольном сечении соответствующая форме наружной поверхности, смещенная относительно продольной оси зуба вверх на 20-25 мм, при этом толщина сечения зуба со стороны передней грани (сверху) сохраняется несколько больше, чем со стороны задней грани (снизу). Такое размещение полости 5 обеспечивает равные прочность и жесткость верхней и нижней стенок переходной части зуба со стороны передней грани и задней грани с учетом того, что снизу имеются ребра жесткости 4.
Хвостовая часть зуба также снабжена периферийными ребрами сверху и снизу. С целью повышения прочности и жесткости на верхней стенке 7 хвостовой части зуба выполнены ребра 6 переменной ширины с увеличением ее в сторону переходной части зуба. Верхняя 7 и нижняя 8 стенки хвостовой части зуба в промежутке между ребрами имеют прямоугольные площадки 9, здесь выполнены 2 сквозных отверстия 10 для крепления зуба на передней стенке ковша. Жесткость хвостовой части несколько увеличивается наличием ребра 11 между верхней 7 и нижней 8 стенками хвостовой части в месте сопряжения этой части с переходной частью зуба, ширина ребра соответствует ширине прорези на передней стенке ковша.
Зуб ковша выполнен литым из износостойкой аустенитной стали 110Г13Л. Поэтому в его конструкции учтены требования литейной технологии: в местах с максимальной толщиной стенок выполнены полости и выборки, для повышения жесткости используются ребра. В конструкции зуба также учтено требование хорошей прокаливаемости при термообработке.
Для закрепления зубьев на передней стенке ковша в стенках хвостовой части выполняют сквозные цилиндрические отверстия 12, аналогичные отверстия предусмотрены и в передней стенке ковша. При установке зуб надевается гнездом хвостовой части на переднюю стенку ковша и в указанные отверстия вставляют прутки соответствующего диаметра, затем прутки загибают сверху и снизу. При этом небольшой натяг в соединении зуб-ковш создается при установке зуба.
Зубья работают следующим образом. При опускании ковша зубья внедряются в разрушаемый (или предварительно разрушенный взрывом) массив породы или грунт. Разрушаемая порода перемещается вдоль верхней (передней) грани зубьев и передней стенки ковша, постепенно наполняя ковш экскаватора. Ковш поворачивают, отделяя часть породы от массива, и переносят к месту разгрузки. При внедрении в породу и повороте ковша верхняя 1 и нижняя (задняя) грани 2 и режущая кромка 3 интенсивно истираются о породу под действием абразива и ударов.
За счет использования рабочей части в виде острого клина с режущей кромкой в предлагаемой конструкции снижаются напорные усилия при внедрении зуба в породу. Силы трения и износ передней и задней граней значительно уменьшаются при их рациональном профилировании. Долговечность зуба повышается при увеличении ширины рабочей части. Износостойкость также повышается за счет высокого качества металла во всех частях зуба после литья и термообработки, этому способствует точное расположение полости в переходной части зуба.
Конструкцию зубьев и технологию их изготовления отрабатывали в производственных условиях, сравнительные промышленные испытания проведены в 2014-16 г.г. для большой серии зубьев. Значительно понизился уровень брака при литье зубьев. При использовании зубьев предлагаемой конструкции в условиях участка №1 Лебединского ГОК на прочных горных породах средняя наработка горной породы для зубьев предлагаемой конструкции больше в 1,4-1,6 раза, чем наработка для зубьев по патенту РФ №2107779 (прототипу). Отмечено также снижение вероятности поломки зубьев.
Источники информации
1. Зуб ковша экскаватора. Патент РФ МПК Е02F 9/28 №2107779. – Заявл. 14.06.96. – Опубл. 27.03.98. Авторы: Сычев К.К., Ершов Г.У., Ивочкин В.А.
2. Зуб ковша экскаватора. Патент РФ МПК Е02F 9/28 №2184814. – Заявл. 13.02.2001 г. – Опубл. 10.07.2002 г. Авторы: Соколов Г.А., Чернышев С.В., Рубина О.Ф.
Зуб ковша экскаватора, выполненный цельнолитым и содержащий клинообразную рабочую часть, массивную переходную часть и хвостовую часть с гнездом, открытым сзади и охватывающим посадочную часть передней станки ковша, причем рабочая часть образована выпуклой верхней и вогнутой нижней криволинейными гранями, формируемыми сопряженными цилиндрическими поверхностями, снабжена продольными ребрами на задней грани и имеет закругленную режущую кромку, смещенную относительно продольной оси зуба вниз, а хвостовая часть снабжена продольными ребрами сверху и снизу, отличающийся тем, что ширина рабочей и переходной частей зуба больше на 40 мм, чем ширина хвостовой части, радиус цилиндрической поверхности, формирующей вогнутую нижнюю грань рабочей части, принимается для зубьев длиной 1250-1510 мм равным R=1000 мм, радиусы цилиндрических поверхностей, формирующих выпуклую переднюю грань, – в пропорции R=(2,5-3,0)⋅R, а формирующих ребра на задней грани рабочей части, – R=(1,25-1,35)⋅R1, в переходной части зуба выполнена внутренняя полость, открытая сзади и смещенная относительно продольной оси зуба вверх на 20-25 мм, при этом толщина сечения переходной части зуба со стороны передней грани несколько больше, чем со стороны задней грани, а верхние ребра на хвостовой части зуба выполнены переменной ширины с увеличением ее в сторону переходной части.edrid.ru
Зуб ковша экскаватора (варианты) и способ его изготовления
Изобретение относится к конструктивным элементам экскаваторов и других землеройных машин, а именно к деталям их рабочих органов и к способам их изготовления. Зуб ковша экскаватора состоит из адаптера, хвостовик которого имеет соответствующие прорези для крепления на ковше экскаватора. На противоположном конце адаптера имеется направляющий выступ, на котором надет и закреплен демпфер. На выступе могут быть выполнены пазы для размещения в них соответствующих выступов демпфера. На наконечнике адаптера расположена коронка, внутренняя поверхность которой имеет форму, сопрягающуюся с наружной поверхностью передней части демпфера. Варианты конструкции зуба предусматривают различные соединения коронки и демпфера. Соединение может быть осуществлено посредством тугой посадки и образования неразъемного соединения за счет зацепления зубцов, выполненных на соединяющихся поверхностях, или за счет размещения в зазоре между соединяемыми поверхностями слоя легкоплавкого металла, или путем наплавки второго слоя металла. Способ изготовления зуба по третьему варианту предусматривает осуществление наплавки методом литья металла в форму, в которую предварительно введен наконечник демпфера. Изобретение обеспечивает повышение надежности конструкции, экономичности и долговечности при эксплуатации. 4 с. и 9 з.п.ф-лы, 3 ил.
Группа изобретений относится к конструктивным элементам экскаваторов и других землеройных машин, а именно к деталям из рабочих органов и к способам их изготовления.
Известен составной зуб для землеройной машины [1], включающий коронку и адаптер. Адаптер имеет сужающийся конец, образующий выступ, а коронка имеет соответствующей формы полость. Соединение коронки и адаптера осуществляется механическим путем с помощью эластичного клина, который устанавливается в специальные овальные отверстия. Составной зуб достаточно прост в изготовлении, однако имеет ненадежное соединение, а коронка, выполненная из износостойкой стали, имеет излишне массивную форму. В процессе эксплуатации ковша экскаватора коронка изнашивается и требуется ее постоянная замена. Таким образом, дорогая износостойкая сталь используется нерационально, что увеличивает эксплуатационные расходы. Другой известный составной зуб [2] имеет менее металлоемкую форму коронки, что с одной стороны удешевляет конструкцию, однако с другой стороны тонкие стенки коронки и длинный посадочный выступ делают конструкцию ненадежной. В процессе эксплуатации может разрушиться не только коронка, но и сам адаптер. Соединение деталей зуба осуществляется также с помощью штифта и является ненадежным. Известны более сложные конструкции зуба. Так, узел крепления зуба рабочего органа землеройной машины [3] предусматривает соединение составных частей с помощью муфты, расположенный на заднем конце удлиненного корпуса коронки и охватывающей головку адаптера. Сопрягающиеся поверхности адаптера и коронки имеют сложную конфигурацию с впадинами и выступами, что делает всю конструкцию нетехнологичной в изготовлении. Наиболее близким к заявляемому устройству является узел крепления зуба ковша экскаватора [4], принятый за прототип устройства. Зуб [4] состоит из адаптера, имеющего на конце направляющий клинообразный выступ с округлыми впадинами, на котором при помощи штифта установлена коронка из износостойкого материала. Коронка имеет удлиненную клинообразную форму. Ее внутренняя поверхность имеет форму, сопрягающуюся с наружной концевой поверхностью адаптера, и дополнительно снабжена округлыми выступами, фиксирующими положение коронки на адаптере. Зуб снабжен дополнительным рабочим элементом в виде крышки, установленной на специальной направляющей и защищающей верхнюю часть адаптера. На крышке со стороны коронки выполнены ребра, которые являются дополнительными фиксаторами взаимного положения указанных элементов. Таким образом, рабочий орган зуба состоит из двух взаимодействующих элементов: коронки и крышки, выполненных из износостойкой стали, что усложняет и удорожает конструкцию. Кроме того, значительная часть коронки не является рабочей, а служит только для закрепления ее на адаптере, т.е. часть износостойкой стали не используется по назначению. Наличие сквозного канала (для установки штифта) на концевой части адаптера также уменьшает надежность зуба в целом, т. е. может привести в процессе эксплуатации к разрушению адаптера. Известны различные способы изготовления зуба ковша экскаватора, при этом операцией, определяющей ресурсные характеристики зуба, является операция соединения коронки и адаптера. Традиционно соединение осуществляется механическим путем с помощью клиньев, штифтов и муфт, как это описано в [1-4]. При этом простота соединения является несомненным преимуществом, однако такие соединения, как отмечалось, не обладают достаточной надежностью, что приводит к преждевременным поломкам зуба в месте соединения коронки и адаптера. Другим известным способом изготовления зуба является способ [5], в котором между поверхностью полости в задней части коронки землеройного зуба и внешней поверхностью передней части адаптера располагают размягчающийся при нагреве полимерный материал и нагревают его до температуры размягчения. Застывший слой полимера обеспечивает сравнительно прочное соединение деталей зуба в результате адгезионного взаимодействия. После износа коронки опять нагревают материал до температуры размягчения и заменяют изношенную коронку на новую. Способ прост в реализации, однако полимерный материал, соединяющий коронку с адаптером, не обладает достаточной жесткостью и высокими адгезионными свойствами, обеспечивающими надежное крепление коронки на адаптере, а следовательно, надежную работу зуба. В основу изобретения поставлена задача создания простой и надежной конструкции зуба для ковша экскаватора, экономичной с точки зрения использования износостойкой и долговечной при эксплуатации стали коронки. Способ изготовления такого зуба должен обеспечивать надежное соединение между собой его элементов. Поставленная задача решается тремя вариантами конструкции зуба и способом изготовления третьего варианта зуба. В первом варианте поставленная задача решается тем, что в зубе ковша экскаватора, включающем адаптер, на конце которого имеется направляющий выступ, рабочий орган, состоящий из двух элементов, одним из которых является коронка, выполненная из износостойкого материала, и фиксатор, согласно изобретению второй элемент рабочего органа выполнен в виде соосно расположенного демпфера, задняя часть которого закреплена на направляющем выступе адаптера, а передняя часть выполнена в виде сужающегося наконечника с зубчатой поверхностью, на котором закреплена коронка, внутренняя поверхность которой имеет форму, сопрягающуюся с наружной поверхностью наконечника демпфера, с обеспечением возможности их неразъемного соединения путем зацепления зубцов. Во втором варианте поставленная задача решается тем, что в зубе ковша экскаватора, включающем адаптер, на конце которого имеется направляющий выступ, рабочий орган, состоящий из двух элементов, одним из которых является коронка, выполненная из износостойкого материала, и фиксатор, согласно изобретению второй элемент рабочего органа выполнен в виде соосно расположенного демпфера, его задняя часть закреплена на направляющем выступе адаптера, а передняя часть выполнена в виде сужающегося наконечника с переменным рельефом боковых поверхностей, где закреплена коронка, внутренняя поверхность которой имеет форму, сопрягающуюся с наружной поверхностью наконечника демпфера, а в зазоре между указанными поверхностями расположен слой застывшего металла. В третьем варианте поставленная задача решается тем, что в зубе ковша экскаватора, включающем адаптер, на конце которого имеется направляющий выступ, рабочий орган, состоящий из двух элементов, одним из которых является коронка, выполненная из износостойкого материала, и фиксатор, согласно изобретению второй элемент рабочего органа выполнен в виде соосно расположенного демпфера, задняя часть которого закреплена на направляющем выступе адаптера, а передняя часть выполнена в виде сужающегося наконечника с переменным рельефом боковых поверхностей, на котором посредством наплавки выполнена коронка. В качестве материала демпфера во всех вариантах используют сталь конструкционной марки с ударной вязкостью не менее 1,0 МДж/м2 и условным пределом текучести, лежащим в пределах 0,3-0,8 условного предела текучести материала коронки, но не превышающим 0,7 условного предела текучести материала адаптера. Наилучший результат достигается, когда направляющий выступ адаптера имеет H-образное поперечное сечение, а задняя часть демпфера снабжена двумя выступами прямоугольного сечения, установленными в пазы между полками H-образного направляющего выступа адаптера. При этом целесообразно фиксатор выполнить в виде скобы, охватывающей сверху демпфер и закрепленной на полках H-образного выступа адаптера. Поставленная задача решается также способом изготовления зуба по третьему варианту, включающем формирование внутренней поверхности коронки по форме наружной поверхности направляющего выступа демпфера и закрепление коронки зуба на направляющем выступе посредством образования адгезионного взаимодействия, в котором согласно изобретению в качестве направляющего выступа используют переднюю часть демпфера, выполненную в виде сужающегося наконечника с переменным рельефом боковых поверхностей, а коронку изготавливают методом заливки расплавленного износостойкого материала в форму, в рабочей зоне которой предварительно размещают переднюю часть демпфера, затем демпфер с наплавленной коронкой охлаждают до комнатной температуры и закрепляют с помощью фиксатора заднюю часть демпфера на направляющем выступе адаптера. На фиг. 1 представлен зуб, первый вариант, вид сбоку, сверху и сечение; на фиг. 2 – зуб, второй вариант, коронка в сборе с демпфером; на фиг. 3 – зуб, третий вариант, коронка в сборе с демпфером. Зуб ковша экскаватора состоит из адаптера 1, хвостовик которого имеет соответствующие прорези для крепления на ковше экскаватора. На противоположном конце адаптера имеется направляющий выступ 2, на который надет и закреплен демпфер 3. Направляющий выступ 2 может иметь различную форму, однако целесообразно для обеспечения прочности конструкции выполнить в нем пазы, в которые могут быть жестко установлены соответствующие выступы демпфера (соединение по типу гнездо – вилка). Экспериментально установлено, что выполнение выступа 2 в виде профиля, имеющего H-образное поперечное сечение, и двух выступов 4 на задней части демпфера, имеющих прямоугольное сечение шириной, равной расстоянию между боковыми полками 5 на адаптере, позволяет обеспечить максимальную жесткость конструкции при минимальной длине выступов. Фиксацию взаимного положения деталей целесообразно осуществлять с помощью охватывающих конструкцию элементов, например, с помощью фиксатора 6 – имеющего форму скобы, размещенной над задней частью демпфера и закрепленной на полках 5 с помощью винтов 7. При этом скоба 6 имеет профилированное сечение и заглублена в тело выступа адаптера. На наконечнике демпфера расположена коронка 8, внутренняя поверхность которой имеет форму, сопрягающуюся с наружной поверхностью передней части демпфера. Наружная поверхность передней части демпфера выполнена в виде сужающегося наконечника. При этом форма выполнения наконечника может быть пирамидо-, конусо-, клинообразной или иной сложной формы, имеющей выступы и впадины, т. е. имеющей переменный рельеф боковой поверхности, например, в виде ступеней, зубцов (гребенки) и т.д. Одна из таких (наиболее простых) пирамидообразных форм с переменным углом схождения граней представлена на фиг. 2, другая – с зубчатой поверхностью передней части демпфера и соответственно зубчатой внутренней поверхностью коронки – на фиг. 1. Заявляемые варианты решают одну задачу принципиально одним и тем же путем, отличие заключается в конструкционных особенностях, обусловленных способом крепления коронки зуба на демпфере. Конструкция первого варианта зуба предусматривает наличие зубцов на поверхности сужающегося наконечника демпфера и соответствующих по форме зубцов на внутренней поверхности коронки. Неразъемное соединение указанных элементов может быть осуществлено с помощью тугой прессовой посадки. При приложении осевого усилия зубцы на демпфере вследствие упругости его материала подвергаются некоторому изгибу во внутрь, достаточному для того, чтобы зайти в зацепление с зубчатым рельефом коронки с образованием неразъемного соединения. При этом локальная пластическая деформация приводит к образованию адгезионных связей. Во втором варианте в зазоре между наружной поверхностью наконечника демпфера 3 и внутренней поверхностью коронки 8 расположен слой 9 легкоплавкого застывшего металла, например, свинца. При этом свинец в расплавленном виде заливают в щель, а затем он застывает, образуя соединение. Рекомендуется во время сборки коронки 8 и демпфера 3 поместить между ними пластинки свинца, затем нагреть узел до расплавления свинца, после остывания которого получается прочное неразъемное соединение. Слой 9 застывшего металла играет роль прочного уплотнителя. В третьем варианте изобретения коронка 8 выполнена посредством наплавки на демпфере 3 и весь узел является конструктивно единым биметаллическим элементом. При этом позиция 10 на фиг. 3 обозначает зону взаимного сплавления, т.е. переходный металлический слой. Установлено, что наилучший результат достигается не только конструктивными особенностями устройства, но и используемым материалом для изготовления демпфера. Для эффективной работы демпфера и возможности простого монтажа материал должен удовлетворять определенным требованиям по ударной вязкости и прочностным свойствам. Во всех вариантах реализации конструкции зуба в качестве материала демпфера используют сталь конструкционной марки с ударной вязкостью не менее 1 МДж/м2 и условным пределом текучести, лежащем в пределах 0,3-0,8 условного предела текучести материала коронки, но не более 0,7 условного предела текучести материала адаптера. При уменьшении ударной вязкости ниже 1 МДж/м2 в процессе эксплуатации происходит хрупкое разрушение демпфера в месте закрепления его к адаптеру. При изготовлении демпфера из стали с условным пределом текучести, меньшим 0,3 условного предела текучести материала коронки, происходит пластическая деформация демпфера (изгиб) и зуб приобретает нерабочую форму. Увеличение условного предела текучести выше заявляемого предела может привести к разрушению коронки в процессе ее монтажа и в процессе эксплуатации (разрушение передней части), а также необратимой пластической деформации адаптера во время эксплуатации зуба. Устройство работает следующим образом. В процессе внедрения ковша экскаватора в породу на коронку, демпфер и адаптер со стороны породы действуют сжимающие и изгибающие усилия, а коронка при внедрении в породу подвергается абразивному износу. При движении ковша экскаватора действующая на коронку распределенная нагрузка передается на наконечник демпфера и компенсируется его изгибающим моментом в зоне крепления демпфера к адаптеру (в зоне “вилки”). В процессе износа коронки не происходит хрупкого разрушения рабочего органа, а при полном абразивном износе коронки осуществляют замену сборного узла демпфер – коронка. При этом адаптер остается в рабочем состоянии, пригодном для повторного использования. Согласно способу реализации третьего варианта конструкции зуба коронку получают методом литья в форму, изготовленную в соответствии с наружной конфигурацией коронки. Устанавливают форму в ее рабочую зону (предпочтительно сверху), вводят демпфер его передней частью, т.е. вводят наконечник, заливают форму расплавленным износостойким металлом, например, инструментальной быстрорежущей сталью, затем осуществляют регламентированное охлаждение до комнатной температуры и вынимают демпфер с наплавленной коронкой. В случае необходимости производят термообработку узла в сборе. После этого демпфер закрепляют на выступе адаптера с помощью фиксатора. При такой технологии изготовления зуба внутренняя поверхность коронки повторяет рельеф наконечника демпфера и входит с ним в плотное соединение. В процессе остывания в форме возникают дополнительные сжимающие напряжения вследствие различных коэффициентов линейного расширения материалов. Ввиду того, что наконечник имеет развитую боковую поверхность, в зоне контакта демпфера с жидким металлом коронки образуются локальные металлические связи (на выступах), которые усиливают адгезионные связи. Таким образом, зуб имеет во всех вариантах простую конструкцию, технологичную в изготовлении, экономичную с точки зрения использования дорогостоящей стали коронки и надежную в процессе эксплуатации. При неизбежном абразивном износе легко и быстро можно осуществить замену сборного или составного элемента, при этом не требуется замена адаптера, так как существенно повышается срок его службы. Способы изготовления зуба просты и обеспечивают надежное соединение. Изобретение найдет промышленное применение на карьерных экскаваторах различных моделей. Источники информации: 1. Заявка ЕПВ 0531603, МКИ E 02 F 9/28. 2. Патент Швейцарии 679939, МКИ E 02 F 9/28. 3. Патент СССР 1838524, МКИ E 02 F 9/28. 4. Патент Великобритании 2252577, МКИ E 02 F 9/28 (прототип устройства). 5. Акц. заявка Японии 5-24293, МКИ E 02 F 9/28 (прототип способа).Формула изобретения
1. Зуб ковша экскаватора, включающий адаптер, на конце которого имеется направляющий выступ, рабочий орган, состоящий из двух элементов, одним из которых является коронка, выполненная из износостойкого материала, и фиксатор, отличающийся тем, что второй элемент рабочего органа выполнен в виде соосно расположенного демпфера, задняя часть которого закреплена на направляющем выступе адаптера, а передняя часть выполнена в виде сужающегося наконечника с зубчатой поверхностью, на котором закреплена коронка, внутренняя поверхность которой имеет форму, сопрягающуюся с наружной поверхностью наконечника демпфера, с обеспечением возможности их неразъемного соединения путем зацепления зубцов. 2. Зуб по п.1, отличающийся тем, что в качестве материала демпфера используют сталь конструкционной марки с ударной вязкостью, не превышающей 1 МДж/м2 и условным пределом текучести, лежащим в пределах 0,3-0,8 условного предела текучести материала коронки, но не превышающим 0,7 условного предела текучести материала адаптера. 3. Зуб по п.1, отличающийся тем, что направляющий выступ адаптера имеет Н-образное поперечное сечение, а задняя часть демпфера снабжена двумя выступами прямоугольного сечения, установленными в пазы между полками Н-образного направляющего выступа адаптера. 4. Зуб по п. 3, отличающийся тем, что фиксатор выполнен в виде скобы, охватывающей сверху демпфер и закрепленной на полках Н-образного выступа адаптера. 5. Зуб ковша экскаватора, включающий адаптер, на конце которого имеется направляющий выступ, рабочий орган, состоящий из двух элементов, одним из которых является коронка, выполненная из износостойкого материала, и фиксатор, отличающийся тем, что второй элемент рабочего органа выполнен в виде соосно расположенного демпфера, задняя часть которого закреплена на направляющем выступе адаптера, а передняя часть выполнена в виде сужающегося наконечника с переменным рельефом боковых поверхностей, на котором закреплена коронка, внутренняя поверхность которой имеет форму, сопрягающуюся с наружной поверхностью наконечника демпфера, а в зазоре между указанными поверхностями расположен слой застывшего металла. 6. Зуб по п.5, отличающийся тем, что в качестве материала демпфера используют сталь конструкционной марки с ударной вязкостью, не превышающей 1 МДж/м2, и условным пределом текучести, лежащим в пределах 0,3-0,8 условного предела текучести материала коронки, но не превышающим 0,7 условного предела текучести материала адаптера. 7. Зуб по п.5, отличающийся тем, что направляющий выступ адаптера имеет Н-образное поперечное сечение, а задняя часть демпфера снабжена двумя выступами прямоугольного сечения, установленными в пазы между полками Н-образного направляющего выступа адаптера. 8. Зуб по п. 7, отличающийся тем, что фиксатор выполнен в виде скобы, охватывающей сверху демпфер и закрепленной на полках Н-образного выступа адаптера. 9. Зуб ковша экскаватора, включающий адаптер, на конце которого имеется направляющий выступ, рабочий орган, состоящий из двух элементов, одним из которых является коронка, выполненная из износостойкого материала, и фиксатор, отличающийся тем, что второй элемент рабочего органа выполнен в виде соосно расположенного демпфера, задняя часть которого закреплена на направляющем выступе адаптера, а передняя часть выполнена в виде сужающегося наконечника с переменным рельефом боковых поверхностей, на котором посредством наплавки выполнена коронка. 10. Зуб по п.9, отличающийся тем, что в качестве материала демпфера используют сталь конструкционной марки с ударной вязкостью, не превышающей 1 МДж/м2 и условным пределом текучести, лежащим в пределах 0,3-0,8 условного предела текучести материала коронки, но не превышающим 0,7 условного предела текучести материала адаптера. 11. Зуб по п.9, отличающийся тем, что направляющий выступ адаптера имеет Н-образное поперечное сечение, а задняя часть демпфера снабжена двумя выступами прямоугольного сечения, установленными в пазы между полками Н-образного направляющего выступа адаптера. 12. Зуб по п.11, отличающийся тем, что фиксатор выполнен в виде скобы, охватывающей сверху демпфер и закрепленной ан полках Н-образного выступа адаптера. 13. Способ изготовления зуба землеройной машины, включающий формирование внутренней поверхности коронки по форме наружной поверхности направляющего выступа демпфера и закрепление коронки зуба на направляющем выступе посредством образования адгезионного взаимодействия, отличающийся тем, что в качестве направляющего выступа используют переднюю часть демпфера, которую выполняют в виде сужающегося наконечника с переменным рельефом боковых поверхностей, а коронку изготавливают методом литья расплавленного износостойкого материала в форму, в рабочей зоне которой предварительно размещают переднюю часть демпфера, затем демпфер с наплавленной коронкой охлаждают до комнатной температуры и закрепляют с помощью фиксатора заднюю часть демпфера на направляющем выступе адаптера.РИСУНКИ
Рисунок 1, Рисунок 2, Рисунок 3findpatent.ru
Продукция и технологии ESCO – для повышения износостойкости и сроков службы ковшей карьерных экскаваторов
Евгений Чупа, директор по региональным продажам, ООО «Первая Сервисно-Техническая Компания»
А.Д. Табарин, региональный менеджер СНГ, ESCO Frameries (Бельгия)
Каждое горнодобывающее предприятие, парк выемочно-погрузочного оборудования которого представлен мехлопатами карьерного типа, сталкиваются с необходимостью периодической, в зависимости от абразивности, твёрдости, трещиноватости и кусковатости вскрышных пород и полезных ископаемых, замены изношенных зубьев ковшей, а рано или поздно – и полной замены самого ковша на новый.
Как известно из практики, в процессе наполнения ковша экскаватора горной массой наибольшему износу (истиранием и ударом) подвергаются, прежде всего, зубья, закреплённые на режущей кромке передней стенки ковша, затем – внутренняя и наружная поверхности передней стенки и её режущей кромки (за исключением их частей, закрытых зубьями). Также интенсивно истираются передние кромки и часть внутренних и наружных поверхностей боковых стенок ковша. Внутренние поверхности задней стенки ковша и его днища всегда подвергаются меньшему износу как ударом, так и истиранием.
Отметим, что одна из отличительных особенностей практики эксплуатации экскаваторов-мехлопат в российских карьерах заключается в том, что технологической нормой считалось никак не защищать ковши от износа, а лишь, периодически заменять зубья, использовать ковш до его полного износа с последующей заменой на новый. Т.е. считалось нецелесообразным предпринимать какие-либо специальные способы и меры конструктивно-технической защиты ковшей от абразивного износа его поверхностей.
И только в последние годы, благодаря появлению на российском рынке зарубежных разработок, технологий и практического опыта в данном направлении, у горнодобывающих предприятий, появилась реальная возможность эффективного осуществления мер защиты на всех типах выемочнопогрузочного, транспортного, и вспомогательного оборудования. Операции по замене изношенных зубьев ковша в целом всегда сопряжены не только с необходимостью остановки работы экскаватора, но и требуют значительных финансовых и временных затрат на их приобретение, доставку в забой и оплату труда сервисно-ремонтных бригад.
Принимая во внимание устойчивую тенденцию по переоснащению российских карьеров экскаваторами большой единичной мощности – как с реечным, так и с канатным напорными механизмами, а также – гидравлическими лопатами – с ковшами вместимостью от 15–25 до 45–50 м3, можно с уверенностью утверждать, что каждая минута непроизводительного использования, а тем более простоя такой машины, будет лишь источником дополнительного ущерба для предприятия. Для снижения подобных потерь времени и вызванных ими материальных ущербов на зарубежных карьерах давно и в широких масштабах используются технология и продукция ESCO Corporation (США).
С 2009 г. компания подготовила адаптацию своего продукта для российского рынка – систему ESCO SV2 (рис. 1) для экскаваторов типа ЭКГ-5, ЭКГ-8, ЭКГ-10 и ЭШ 10/70.
Достоинства и преимущества использования продукции ESCO обусловлены оригинальностью её конструктивного исполнения. В отличие от стандартной моноблочной конструкции зубьев, используемых, на ковшах указанных экскаваторов, система зубьев SV2 представляет собой двухкомпонентную структуру, в основе которой – адаптер и съёмный (сменяемый) наконечник-коронка (рис. 2). В соответствии с таким структурным решением адаптер (1), укрепляемый с помощью шпилек на режущей кромке передней стенки ковша мехлопаты, имеет утолщённый прочный нос, на который насаживается съёмная коронка (2). Жёсткая фиксация коронки на адаптере осуществляется с помощью фиксатора (3). Для защиты фиксатора от повреждений при выемке грунта предусмотрена прочная литая крышка-накладка (4).
Адаптер при его изготовлении отливается с точными размерами посадочного места, соответствующими режущей кромке конкретного типа ковша. Поэтому он легко и быстро монтируется на ковше без каких-либо подгонок. Массивный и прочный нос обеспечивает полный и стабильный, по площади стыкуемых деталей, контакт с посадочным местом коронки. Боковая запорная система обеспечивает надёжное удержание коронки на адаптере в течение всего срока эксплуатации, а также лёгкость установки/извлечения фиксатора и его полную защищённость от повреждения кусками горных пород при работе экскаватора.
Съёмная коронка из стали ESCO E12K555HBN выполняется меньшего размера поперечного сечения, но большей длиной. Это обеспечивает зубу большую прочность изнашиваемой рабочей части. Вместе с тем, коронка, благодаря более тонкому рабочему профилю, остаётся постоянно заострённой до полного своего износа. Благодаря универсальности посадочного места на один и тот же адаптер могут быть установлены коронки различной конфигурации, в зависимости от изменений условий карьера или места работы экскаватора.
Конструкция накладки обеспечивает лёгкость и точность её закрепления вверху передней части адаптера, и снятия ее при очередной замене коронки.
Кроме того, накладка принимает часть истирающих и ударных нагрузок горных пород при черпании их ковшом и, благодаря своей толщине и приподнятости над остальной частью адаптера, ослабляет силовое воздействие на тело адаптера и на фиксатор, в конечном итоге, способствуя увеличению сроков службы деталей.
Самая малая по размерам и собственной массе деталь системы зубьев SV2 – фиксатор – играет, тем не менее, ключевую роль в обеспечении работоспособности всей конструкции. Выполненный в виде трёхгранной удлинённой пирамиды фиксатор, устанавливаемый в точные направляющие адаптера и коронки, надёжно и прочно фиксирует их защёлкой в рабочем положении.
Рассматривая экономику использования моноблочных и двухкомпонентных зубьев, отметим, что зубья моноблочной конструкции изнашиваются на 30% своей массы, а около 70% массы моноблочного зуба направляется в переплавку. В свою очередь, в зубьях двухкомпонентной конструкции ESCO изнашивается 72–75% массы съёмного наконечника (коронки). И лишь 25–28% массы остаётся неиспользованной и отправляется на переплавку. В общем, отношение суммарной массы использованных наконечников к массе адаптера зуба SV2 конструкции ESCO может достигать 12:1. Эксплуатационно-технологические преимущества зубьев системы ESCO приведены в таблице.
Сравнение эксплуатационно,технологических характеристик моноблочных зубьев с двухкомпонентными зубьями ESCO
Характеристика, технологический фактор | Значение характеристики и фактора | Примечания | |
элементов зубьев системы ESCO | моноблочного зуба российского производства | ||
1. Качество обработки и точность подгонки к режущей кромке ковша | – адаптера зуба – до 2 мм; – наконечника зуба (коронки) – максимально 5 мм |
Зуба – более 10 мм | Плотно подогнанные элементы зуба и режущей кромки ковша способствуют меньшему износу сопряжённых поверхностей и гаранти руют более длительный срок службы зубьев |
2. Продолжительность и трудоёмкость операции по замене комплекта зубьев | – не более 0,5 час; – масса отдельного элемента зуба 30–60 кг |
– 1час и более; – масса зуба от 125 до 200 кг |
Время на замену комплекта ESCO – не более половины времени на замену моноблочных зубьев. Комплекты ESCO заменяются от 4 до 8 раз реже, что повышает коэффициент технической готовности и долю времени производительного использования экскаватора. Безопасность труда персонала повышается, т.к. при замене изношенных наконечников зубьев не используется кувалда, и с использованием физической силы рабочего перемещаются элементы массой не более 60 кг |
3. Тип стали, используемой для изготовления зубьев и ковшей | Низколегированная сталь | Марганцовистая сталь | см. Примечания к фактору 3 |
Примечания к фактору 3:
Необходимо отдельно отметить влияние типа стали на эксплуатационные свойства компонентов ковша мехлопаты. Марганцовистая сталь, из которой изготавливаются зубья и элементы ковша российских экскаваторов, характеризуется начальной твёрдостью 180–220 HB. При работе зубьев в результате ударов о грунт при черпании ковша твёрдость поверхностного слоя металла может достигать 450 HB (благодаря эффекту «наклёпа»). По мере разрушения упрочнённого наклёпом слоя поверхности зубьев, усилению подвергается и нижележащий слой металла. Такая цикличность «упрочнениеразрушениеупрочнение» слоёв металла повторяется до полного износа зубьев, и их замены на новые.
Низколегированная сталь ESCO, используемая для изготовления съёмных наконечников зубьев, имеет прочность до 550 HB (в среднем – 534 HB), но на всю толщину металла. Благодаря этому, в тяжёлых железорудных забоях коронки служат до 4–5 раз дольше, чем российские моноблочные зубья.
Рабочие поверхности ковшей отечественных экскаваторов, изготавливаемых из марганцовистых сталей, остаются незащищёнными от истирающих нагрузок. Для защиты таких поверхностей ковшей ESCO выпускает пластины и биметаллические компоненты с покрытиями из сплавов твёрдостью до 700 HB.
Наглядным представляется сравнение габаритных параметров моноблочной и двухкомпонентной системы ESCO, для ЭКГ10 (рис. 3).
Новый моноблочный зуб (см. рис. 3а) имеет полную массу 190 кг, а новый изнашиваемый и периодически заменяемая коронка двухкомпонентного зуба 75 SV2 имеет массу 60 кг.
Изношенный моноблочный зуб (см. рис.3б) имеет вес 135 кг, а коронка двухкомпонентного зуба 75 SV2 – 15 кг.
На сегодня системы зубьев SV2 используются на мехлопатах угольных карьеров ОАО «УК «Кузбассразрезуголь» и ОАО «СУЭК». Результатам использования зубьев системы ESCO на экскаваторах этих крупнейших в России компаний будет посвящена отдельная статья.
Здесь мы хотим высказать лишь основные соображения относительно некоторых «скрытых» достоинств системы и методики оценки экономической целесообразности её применения:
1. Одно из главных достоинств системы состоит в том, что благодаря двухкомпонентной конструкции и применяемому в ней сплаву, система имеет гораздо более продолжительный срок службы и требует значительно меньшего времени и ресурсов для замены коронки, чем моноблочный зуб.
2. Специалисты-технологи и механики горного предприятия могут легко определить, что будет разумнее и экономически выгоднее: часто заменять зубья и реже ковш, или, используя системы защиты ESCO, работать с единственным, установленным на заводе, ковшом мехлопаты.
3. Потери ресурса рабочего времени экскаваторов при частой замене зубьев и ковшей, а значит – производительности карьера и финансовых средств на её восстановление в обоих вариантах – легко подсчитать. Вывод о рациональности и экономичности предпочтения варианта с продукцией ESCO становится особенно очевидным после изучения статистических данных о наработках каждого экскаватора и продолжительности суммарных простоев по причине замены изношенных зубьев и самого ковша.
4. Актуален вопрос транспортной составляющей при поставке зубьев для труднодоступных и удаленных регионов РФ (как стоимости так и сроков).
Журнал “Горная Промышленность” №6 (100) 2011, стр.41
mining-media.ru
Зубья ковша экскаватора | Производителя
Контактная форма
Наименование: Зубья ковша экскаватора
Совместимость с техникой: Экскаваторы, бульдозеры и т.д.
Материал: Легированная сталь
Возможность изготовления под заказ: Да, в соответствии с образцами или чертежами клиента
Модель экскаватора: По запросу клиента
Мы можем изготовить зубья ковша для экскаваторов следующих марок:
Иностранные производители: Komatsu, DOOSAN, Kobelco, CAT, Hyundai, Volvo, Liebherr, Hitachi и другие.
Китайские производители: Yuchai, SEM, SANY, SDLG, Foton Lovol, LiuGong, XGMA, ChengGong (CG), LonKing, Sunward, DEGONG, ZOOMLION и т.д.
Применение
Зубья ковша являются одними из наиболее изнашиваемых деталей экскаватора. Зуб состоит из адаптера и коронки и крепится к режущей кромке ковша при помощи пальцевого соединения. Качество зубьев играет первостепенную роль в эффективности землеройных работ, и мы гарантируем, что износостойкие и оптимально заточенные зубья для ковшей экскаваторов от HANDY прослужат долго и обеспечат высокую производительность труда.
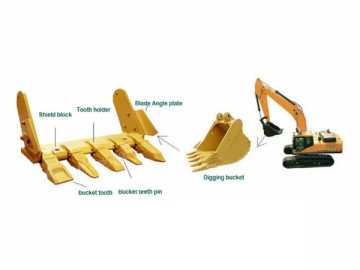
Образцы изделий
Зуб ковша для экскаватора Komatsu PC400(14152HS)
Зуб ковша для экскаватора CAT E200B(IU3302RC)
Зуб ковша для экскаватора Komatsu PC400(14152HS)
Зуб ковша для экскаватора Volvo EC210
Характеристики
1. Высокая износостойкость и эффективность при выполнении землеройных работ.
2. Оптимизированная форма зуба позволяет поддерживать остроту коронки более продолжительное время и облегчает процесс копания.
3. Надежный адаптер для прочной фиксации зуба на режущей кромке ковша при помощи пальцевого соединения.
4. Высокая усталостная прочность, твердость и устойчивость к деформациям.
5. Простота в обслуживании и замене.
Почему именно HANDY
Наиболее выгодные цены;
Запчасти для экскаваторов производятся из высококачественного никельхромистого или высокохромистого чугуна.
Возможность самовывоза продукции;
Продукция сертифицирована по системе CE и ISO.
Упаковка | Ящики из композитного материала |
Срок доставки | 15 дней |
www.etwinternational.ru
О целесообразности изготовления зубьев ковшей экскаваторов из стали 110Г13Л
Санкт-Петербургский государственный горный университет, г. Санкт-Петербург
В.И. Болобов, А.П. Баталов, Ю.В. Лыков, B.C. Бочков
УДК 669.14.018.29.004.62/.63
Считается [1-3], что в условиях трения, сопровождаемого большим удельным давлением и ударами, сталь 110Г13Л(сталь Гадфильда) обладает аномально высокой износоустойчивостью. Это объясняется её повышенной способностью увеличивать твердость, а следовательно, как обычно считают [3], и сопротивление износу с увеличением степени пластической деформации (рис. 1) значительно большей, чем у обычных сталей с такой же исходной твердостью.
Рис. 1. Влияние степени пластической деформации на твердость стали 110Г13Л (1)
по сравнению со сталью 40 (2) [1 ]
По этой причине до настоящего времени сталь 110Г13Л остается одним из основных конструкционных материалов для изготовления элементов горнодобывающего и горно-обогатительного оборудования, работающих в контакте с породой при значительных напряжениях и динамических нагрузках: зубьев ковшей экскаваторов, футеровок шаровых мельниц, бил и щек дробилок.
В то же время, как показывает практика, ряд указанных элементов, например зубья ковшей экскаваторов из стали 110Г13Л, показывают в условиях эксплуатации явно недостаточную износостойкость. Например, по имеющимся у авторов сведениям, при добыче гранита на ГОК «Семиреченское карьероуправление» комплект зубьев экскаватора ЭКГ-5 уже после добычи 20 тыс. м3породы, что соответствует всего 1,5-2 суткам непрерывной работы, изнашивается и требует замены. Продолжительность работы зубьев по медно-никелевой породе в условиях ГМК «Норильский никель» не намного превышает (3-5 суток) эту величину [4]. Приведенные данные ставят под сомнение положительное влияние повышенной способности к наклепу стали 110Г13Л на износостойкость материала в условиях работы зубьев ковшей экскаваторов и целесообразность их изготовления из этой стали для этих условий. Подобной точки зрения, в частности, придерживаются и авторы работы [5], не видя преимуществ стали Гадфильда при изготовлении зубьев по сравнению с термически обработанной сталью Ст. 6.
Некоторое прояснение в указанных вопросах могут дать результаты, полученные авторами на ГОК «Семиреченское карьероуправление» по визуальному осмотру зубьев с начальной твердостью ~ 33-38 HRC(НВ3110-3530 МПа) после их работы по граниту, в котором наиболее твердый породообразующий минерал – кварц имеет микротвердость – 10000 МПа [6], а также по замеру твердости различных участков зуба до и после эксплуатации.
В соответствии с результатами осмотра оказалось, что вид поверхностей нижней и верхней частей зубьев после работы различен. Если поверхность верхней части зубьев гладкая и блестящая с отдельными редкими царапинами (рис. 2а),то нижней – тёмная и шершавая, вся испещренная глубокими царапинами параллельными направлению движения зуба (рис. 2б). Такие виды поверхности характерны для ударно-абразивного (верх) и чисто абразивного (низ) видов износа, соответственно.
Рис. 2. Общий вид верхней (а) и нижней (б)поверхностей зуба и отдельных их точек
Как показали наблюдения за работой зубьев, быстрому износу подвергается только нижняя их поверхность, в то время как верхняя с заметной скоростью не изнашивается. По этой причине по принятой на карьере практике для увеличения срока службы зубьев их периодически переставляют, поворачивая на 180°, меняя местами верхнюю и нижнюю стороны зубьев.
Измерение твердости зуба проводили с использованиемпортативного твердомера ТКМ-459, индентор (алмазный наконечник) которого закреплен на конце металлического стержня, колеблющегося под действием пьезоэлемента с резонансной частотой. При внедрении наконечника в металл на ту или иную глубину, зависящую от твердости металла, изменяется частота колебаний стержня, что и фиксируется прибором.
В соответствии с измерениями оказалось, что твердость стали 110Г13Л во всех точках рабочей поверхности как верхней, так и нижней частей зуба практически одинакова и составляет ~ 50-55 HRC(НВ4810-5600 МПа), что существенно превышает твердость материала зуба до эксплуатации. (Несколько отличающиеся данные получены в работе [7] для условий работы зубьев на каменно-щебеночном карьере: твердость стали на вершине зуба в процессе эксплуатации достигает НВ4200 МПа и снижается по мере удаления от вершины (на 80 мм) до твердости (НВ2050 МПа)). Это обстоятельство может свидетельствовать о том, что в процессе работы зуба материал обеих его сторон претерпевает существенный наклеп: на верхней стороне зуба – в результате ударов крупных фрагментов гранита при их перекатывании в ковше при погрузке и выгрузке, на нижней, как можно предположить, – из-за пластической деформации металла при его царапании о породу. Последнее предположение основывается на результатах исследований [5], показывающих, что при абразивном изнашивании стали 110Г13Л о кварцевый песок микротвердость дна и стенок царапины достигает 800 HV(НВ7220 МПа).
Суммируя результаты визуальных наблюдений и измерения твердости, можно заключить, что, хотя в процессе работы обе стороны зуба подвергаются интенсивному наклепу, его влияние на износостойкость верхней и нижней поверхностей зуба сказывается различно: в условиях ударно-абразивного износа, имеющего место на верхней стороне зуба, наклеп существенно замедляет скорость разрушения стали, в случае же абразивного вида износа, наблюдаемого в условиях работы нижней стороны зуба, наличие наклепа на скорости разрушения стали 110Г13Л практически не сказывается. При этом не повышает износостойкости стали Гадфильда в случае абразивного износа и то обстоятельство, что трение нижней поверхности зуба о породу сопровождается значительными удельными нагрузками.
Такое заключение подтверждается результатами ряда исследований, в частности [8], в которых показано, что наличие наклепа на износостойкости стали Гадфильда в условиях абразивного изнашивания практически не сказывается, в том числе, и при наличии значительных нагрузок на материал. В то же время известно [9], что поверхностное деформирование, способствующее наклепу, является эффективным способом повышения износостойкости металлических материалов при ударно- абразивном изнашивании.
Таким образом, уникальная способность к наклепу стали 110Г13Л благоприятно сказывается на повышении износостойкости верхней поверхности зуба и никак не сказывается на износостойкости нижней. А так как срок службы зуба лимитирует быстрый износ нижней его стороны, изготовление зубьев ковшей экскаваторов из дорогостоящей стали Гадфильда вряд ли можно считать целесообразным.
***
Гуляев А.П.Металловедение. М.: Металлургия, 1986. 544 с.
Марганцовистая сталь. Пер. с англ. Б.А. Белоуса под ред. М.Е. Блантера. М.: Металлургиздат, 1959. 94 с.
Давыдов Н.Г.Высокомарганцевая сталь. М.: «Металлургия», 1979. 176 с.
Шамоня В.П.Долговечность зубьев ковшей экскаваторов ЭКГ-8 в условиях Норильска / В.П. Шамоня, А.И. Михайловский, В.А. Ковальчук, Б.М. Благих // «Горный журнал», № 7, 1966. Стр. 53-56.
Львов П.Н.Износостойкость деталей строительных и дорожных машин. М.: «Машгиз», 1962. 89 с.
Тененбаум М.М.Износостойкость деталей и долговечность горных. М.: ГН-ТИЛ по ГД, 1960,246 с.
ЯмшановП.ИУпрочнение отливок из стали 110Г13Л энергией взрыва / П.И. Ямшанов, Р.З. Кац, В.И. Силантьев, А.К. Копысова, Т.Ф. Пирогова // «Литейное производство», № 9, 1975. Стр. 17-18.
Болобов В.И.О возможности повышения износостойкости стали Гадфильда наклепом в условиях работы футеровок шаровых мельниц / В.И. Болобов, B.C. Бочков // Современные проблемы машиностроения: труды VI Международной научно- технической конференции / Томский политехнический университет. – Томск: Изд-во Томского политехнического университета, 2011. Стр. 42-46.
Маляров П.В.Основы интенсификации процессов рудоподготовки: Монография. – Ростов-на-Дону: ООО «Ростиздат», 2004. – 320 с.
fela-nk.ru
Зуб ковша экскаватора и способ его изготовления
Изобретение относится к области машиностроения, в частности к конструкции зубьев ковшей экскаваторов. Техническая задача – повышение срока службы и эффекта самозатачивания за счет расположения в стальной основе мелких деталей из износостойкого чугуна. В острие зуба устанавливаются вставки параллелепипедной формы, далее по рабочей плоскости – вставки цилиндрической формы. Вставки из износостойкого чугуна за счет теневого эффекта сдерживают стальную основу от интенсивного абразивного износа и тем самым обеспечивают увеличение срока службы. Так как износостойкие вставки располагаются только на одной из рабочих поверхностей, то другая (противоположная) подвергается более интенсивному износу, что в конечном итоге обеспечивает остроту зуба в процессе его эксплуатации (т.е. затачивание). Освоение такой конструкции зуба ковша и способа его изготовления позволит существенно в 2 и более раза повысить срок службы и обеспечить надежность работы оборудования (экскаваторов). 2 н. и 2 з.п. ф-лы, 4 ил.
Изобретение относится к области машиностроения, в частности к конструкции зубьев ковшей экскаваторов.
Зубья ковшей экскаваторов в процессе эксплуатации подвергаются абразивному износу с наличием динамических нагрузок. Изнашивание происходит преимущественно в виде микро- и макрорезания. При разработке скальных грунтов комплект зубьев ковшей экскаваторов интенсивно изнашивается и срок их службы из высокомарганцовистой стали 110Г13Л не превышает 5-10 дней [1].
Работа экскаваторов с изношенными зубьями снижает производительность и повышает износ машины, приводит к дополнительным затратам на замену изношенных деталей.
Известен зуб ковша экскаватора [2], содержащий для повышения износоустойчивости и обеспечения самозатачивания твердосплавную вставку, смонтированную в средней его части по продольной оси.
Недостатком указанной конструкции является то, что она не обеспечивает защиту от износа рабочих поверхностей зуба, а защищает лишь его переднюю часть и сердцевину.
Известен также зуб ковша экскаватора, содержащий вставки из износостойкого чугуна, установленные на рабочих поверхностях, подвергаемых абразивному износу [3].
Армирование зубьев ковшей экскаваторов крупными износостойкими пластинами позволяет повысить стойкость на 20-25%, в зависимости от условий работы.
Данная конструкция взята авторами за прототип.
Существенным недостатком таких зубьев, с крупными пластинами из износостойкого чугуна, является недостаточная механическая прочность пластин.
В процессе эксплуатации при ударах о скальный грунт происходит разрушение пластин из хрупкого износостойкого чугуна и их последующее выкрашивание, после чего возрастает интенсивность абразивного износа. Срок службы при этом резко снижается и не удовлетворяет требованиям эксплуатационников.
Целью настоящего изобретения является увеличение срока службы зуба ковша и обеспечение эффекта самозатачивания.
Поставленная цель достигается тем, что в конструкцию зуба включены вставки из износостойкого чугуна в виде отдельных деталей параллелепипедной и цилиндрической формы с обратной конусностью и расположены по рабочим поверхностям в стальной основе.
Параллелепипедной формы вставки располагаются в острие зуба в один ряд с интервалом 0,5-1,5 их ширины, а далее следуют равномерно расставленные цилиндрические вставки в рядах с межцентровым расстоянием друг от друга, равным 1,5-3,0 диаметра вставки.
Предлагаемое техническое решение позволяет повысить удароустойчивость вставок из износостойкого чугуна, так как они выполнены в виде мелких деталей.
Каждый отдельный элемент (вставка с малыми размерами), расположенный в пластичной стальной основе, за счет своих малых линейных размеров делает их практически неуязвимыми для разрушения при ударных нагрузках.
Вставки предложенной конструкции, выполненные из износостойкого чугуна, позволяют защитить рабочую поверхность зуба от абразивного износа за счет теневого эффекта на протяжении всего периода истирания вставок по толщине.
В дальнейшем, после износа вставок, процесс абразивного изнашивания протекает, как в обычных, не армированных деталях.
Параллелепипедная форма износостойких вставок принята с целью максимальной защиты рабочей поверхности у острия зуба.
Защита остальной (ровной) поверхности осуществляется вставками цилиндрической формы, как наиболее рациональной, обеспечивающей наименьшие внутренние напряжения и повышенную трещинноустойчивость при литье, что повышает эксплуатационные свойства и надежность зуба.
При расположении износостойких вставок на одной из рабочих поверхностей зуба ковша позволяет создать дополнительный эффект самозатачивания.
Поддержание зуба ковша экскаватора в заостренном состоянии способствует снижению затрат и повышению производительности оборудования.
На фиг.1 представлен зуб ковша экскаватора, армированный вставками из износостойкого чугуна (разрез по А-А).
Зуб ковша состоит из корпуса (1) и хвостовика (2), выполненных из стали (основы), и вставок параллелепипедной (3) и цилиндрической (4) форм, изготовленных из износостойкого чугуна.
На фиг.2 представлен зуб ковша экскаватора со стороны износостойких вставок (вид сверху).
Износостойкие вставки параллелепипедной формы располагаются на передней режущей кромке зуба (у острия) в один ряд с интервалом 0,5-1,5 ширины вставки, длина и толщина которой определяются конструктивно и не превышают 2-3-кратной ее ширины.
Цилиндрические вставки расположены равномерно в рядах с межцентровым расстоянием, равным 1,5-3,0 диаметра вставки.
Такое расположение износостойких вставок обеспечивает защиту стальной основы от абразивного износа за счет использования теневого эффекта.
Использование зубьев ковшей экскаваторов предложенной конструкции позволит повысить удароустойчивость вставок и абразивную износостойкость, что приведет к существенному повышению срока службы изделия.
Известен способ изготовления зуба ковша [3] с упрочнением рабочей поверхности путем поверхностного легирования.
Способ заключается в том, что в полость литейной формы проставляются вставки, изготовленные из порошков ферросплавов с жидким стеклом. При заливке формы сталью ферросплавы расплавляются и легируют поверхностный рабочий слой отливки.
Легирование специальными ферросплавами упрочняет рабочую поверхность, делает ее более износостойкой. Стойкость таких зубьев повышалась на 30-40%, что явно недостаточно.
Известен также способ изготовления зубьев ковша с упрочнением рабочей поверхности вставкой из износостойкого чугуна [3].
Способ изготовления заключается в том, что в литейную форму при отливке зуба устанавливается пластина из износостойкого чугуна и примыкает к поверхности, подлежащей упрочнению. В готовую форму заливают сталь (основа отливки) и получают отливку зуба, армированного пластиной из износостойкого чугуна.
Данный способ изготовления принят за прототип.
Целью настоящего изобретения является существенное повышение срока службы зуба ковша экскаватора с обеспечением эффекта самозатачивания.
Поставленная цель достигается тем, что изготовление зуба осуществляется в процессе литья из стали с использованием мелких вставок из износостойкого чугуна параллелепипедной и цилиндрической форм цельнолитой конструкции с элементом крепления в литейной форме.
Предлагаемый способ изготовления зуба отличается от известного тем, что предварительно отлитые из износостойкого чугуна вставки (3) и (4), см. фиг.3, в виде мелких деталей параллелепипедной и цилиндрической формы цельнолитой конструкции проставляют в нижнюю полуформу и фиксируют с помощью элементов крепления по одной или двум рабочим поверхностям (фиг.4, разрез Б-Б).
Вставки параллелепипедной формы располагают на участке, образующем острие зуба, в один ряд с интервалом 0,5-1,5 их ширины, а цилиндрические в продолжение рабочей поверхности в рядах с межцентровым расстоянием, равным 1,5-3,0 диаметра вставок.
Для выполнения внутренней полости отверстий в полуформу устанавливают песчаный стержень (7).
После простановки в нижнюю полуформу износостойких вставок и песчаного стержня ее накрывают верхней полуформой (8) с элементом литниковой системы.
Собранная литейная форма через литниковую систему (9) заливается жидкой сталью.
Закристаллизовавшуюся армированную отливку в дальнейшем подвергают выбивке из формы, удалению стержня, очистке от пригара, обрубке облоев и удалению заусениц.
После этого армированную отливку зуба подвергают термообработке (закалке) с целью придания пластических свойств основе металла и дополнительного увеличения износостойкости чугунным вставкам и зубу в целом.
Такая конструкция зуба и способ его изготовления позволяют создать за счет теневого эффекта износостойкую деталь, способную выдерживать большие динамические нагрузки в сочетании с высокой абразивной стойкостью.
ЛИТЕРАТУРА
1. Ю.Д.Новомейский, В.И.Глазков. Высокомарганцовистая аустенитная сталь 110Г13Л. М.: Металлургия, 1969 г.
2. А.С.№334344.
3. Э.Б.Тен, К.Б.Бикшенов. Повышение срока службы литых зубьев ковшей карьерных экскаваторов. “Литейное производство”, 1981, №10, с.18-19.
1. Зуб ковша экскаватора, включающий корпус, хвостовик, выполненные из стали, и вставку, отличающийся тем, что вставка выполнена в виде мелких деталей из износостойкого чугуна параллелепипедной и цилиндрической формы с обратной конусностью и расположенных внутри стальной основы по рабочим поверхностям, причем вставки параллелепипедной формы расположены в острие зуба в один ряд с интервалом 0,5-1,5 их ширины, а цилиндрические – равномерно на остальной рабочей поверхности в рядах с межцентровым расстоянием, равным 1,5-3,0 диаметрам вставок.
2. Зуб ковша экскаватора по п.1, отличающийся тем, что износостойкие вставки параллелепипедной формы имеют размер 20×30×10 мм, а цилиндрические – диаметр 30 мм.
3. Способ изготовления зуба ковша экскаватора, содержащего стальную основу и износостойкую вставку, согласно которому в литейную форму при отливке зуба устанавливают износостойкую вставку, в литейную форму заливают стальную основу, после чего армированную отливку зуба удаляют из литейной формы и производят термообработку, отличающийся тем, что предварительно отлитые из износостойкого чугуна вставки в виде мелких деталей параллелепипедной и цилиндрической формы цельнолитой конструкции проставляют в нижнюю полуформу и фиксируют с помощью элементов крепления по одной или двум рабочим поверхностям, при этом вставки параллелепипедной формы располагают на участке, образующем острие зуба, в один ряд с интервалом 0,5-1,5 их ширины, а цилиндрические – в продолжении рабочей поверхности в рядах с межцентровым расстоянием, равным 1,5-3,0 диаметрам вставок, причем для выполнения внутренней полости отверстий в отливке зуба устанавливают песчаный стержень, а после простановки в нижнюю полуформу износостойких вставок и песчаного стержня накрывают нижнюю полуформу верхней, после чего готовая литейная форма заливается через литниковую систему жидкой сталью, после чего закристаллизовавшуюся армированную отливку зуба удаляют из литейной формы и производят операции по выбивке стержня, очистке от пригара и заточки заусениц и заливов.
4. Способ изготовления зуба ковша экскаватора по п.3, отличающийся тем, что износостойкие вставки параллелепипедной формы изготавливают размером 20×30×10 мм, а цилиндрические – диаметром 30 мм.
findpatent.ru
Добавить комментарий